Система турбонаддува — принцип работы турбины, устройство турбокомпрессора автомобиля
Мощность двигателя автомобиля напрямую зависит от того, какое количество топлива и какой объем воздуха поступают в двигатель. Чтобы повысить мощность двигателя, логично увеличить количество этих компонентов.
Просто увеличить количество топлива недостаточно, если при этом не увеличить объем воздуха, необходимого для максимально полного сгорания топлива. Использование турбокомпрессора дает возможность доставить больший объем воздуха в цилиндры, предварительно сжав его.
Принцип работы турбины двигателя таков: в цилиндры под давлением отработанных газов подается сжатый воздух, который вращает крыльчатку. Компрессор, расположенный на одном валу с крыльчаткой, нагнетает давление в цилиндр.
Турбонаддув от выхлопных газов – наиболее эффективная система увеличения мощности двигателя. Использование турбонаддува не увеличивает объем цилиндров и не влияет на частоту вращения коленвала.
Таким образом, помимо увеличения мощности, турбонаддув позволяет рационально расходовать топливо и уменьшить токсичность отработанных газов благодаря тому, что топливо сгорает полностью.
Устройство турбокомпрессора автомобиля
Система турбонаддува используется не только в дизельных, но и в бензиновых двигателях.
Система турбонадува состоит из следующих элементов:
- Турбокомпрессора;
- Интеркулера;
- Перепускного клапана;
- Регулировочного клапана;
- Выпускного коллектора.
Принцип работы турбины дизельного двигателя
Работа дизельной турбины также основана на использовании энергии выхлопных газов.
В общих чертах принцип работы турбины дизеля выглядит так.
От выпускного коллектора выхлопные газы направляются в приемный патрубок турбины, после попадают на крыльчатку, принуждая ее двигаться. С крыльчаткой на одном валу расположен компрессор, который нагнетает давление в цилиндрах.
Основное отличие турбокомпрессорных агрегатов от атмосферных дизелей в том, что здесь в цилиндры воздух подается принудительно и под высоким давлением. Поэтому на цилиндр попадает значительно большее количество воздуха. В сочетании с большим объемом подающегося топлива мы получаем прирост мощности порядка 25%. При этом пропорции воздушно-топливной смеси остаются неизменными.
Чтобы еще больше увеличить объем поступающего в цилиндры воздуха, используется интеркулер – устройство, предназначенное для охлаждения атмосферного воздуха перед подачей его в двигатель. Это позволяет за один цикл подать в цилиндр еще больше воздуха, так как, холодный, он занимает меньше места.
Технология турбонаддува используется в случаях, когда необходимо увеличить мощность мотора и при этом оставить неизменными его размеры и габариты.
Более наглядно схема работы турбины показана в этом видео:
Принцип работы дизельной турбины несколько отличается от работы турбины на бензиновом двигателе.
Отличие работы турбины бензинового двигателя
Основное отличие турбин бензинового двигателя от турбин дизельного в том, что последние раскручиваются с помощью выхлопных газов, температура которых достигает 850 градусов. А турбина бензинового двигателя раскручивается с помощью газов, имеющих температуру от 1000 градусов. Имея одинаковый принцип работы, бензиновая турбина изготовлена из более жароустойчивых сплавов, нежели турбина дизельная.
Само строение бензиновой турбины также имеет некоторые отличия, в частности угол входа, крутка лопаток и т.д. По этой причине не стоит использовать дизельные турбины для наддува бензинового двигателя, впрочем, как и наоборот (подробнее в статье).
Вернутся к списку «Статьи и новости»
Устройство и принцип действия турбокомпрессора авто
Устройство и принцип действия турбокомпрессора направлены на увеличение давления топлива в коллекторе впуска для обеспечения максимального поступление кислорода в камеру, где происходит сгорание.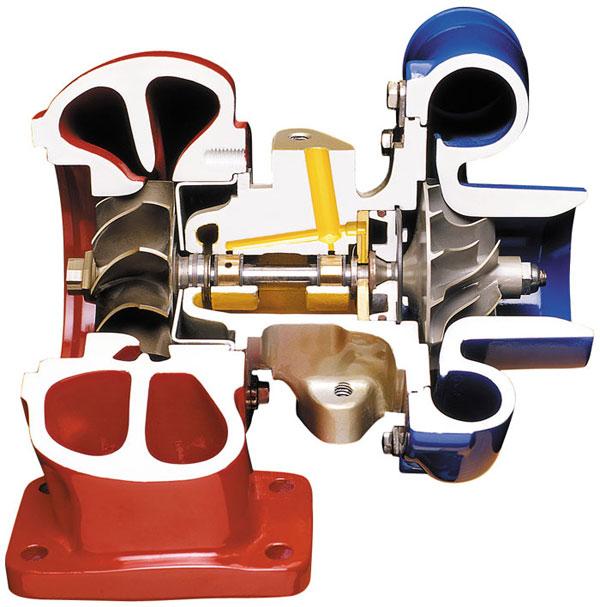
Турбонаддув – принцип работы
Рассмотрим, принцип работы турбины на авто. Поток выхлопных газов поступает из выпускного коллектора в горячую часть турбины, там воздействует на лопасти крыльчатки, приводя ее в движение вместе с валом. На нем закреплена также крыльчатка компрессора, расположенного в холодном отсеке турбины. Она при вращении повышает давление в системе впуска, обеспечивая увеличенное поступление в камеру сжигания топлива и воздуха.
- Улитки компрессора, которая всасывает воздух, а затем нагнетает его в коллектор впуска;
- Улитки, расположенной в горячей части – здесь выхлопные газы заставляют вращать турбину, после чего выбрасываются в систему отработанных газов на выход;
- Крыльчатки компрессора, а также ее аналога в горячей части;
- Шарикоподшипникового картриджа;
- Корпуса, соединяющего улитки, имеющего систему охлаждения и системы подшипников.
Во время работы устройство подвергается значительным термодинамическим нагрузкам. Попадающие в турбину выхлопные газы достигают температуры 900°С, из-за чего ее корпус делают чугунным, причем для отливки используется особая технология. Обороты турбинного вала могут достигать показателя 200 000 об/мин, поэтому в конструкцию устанавливают высокоточные детали, которые тщательно подгоняют и затем балансируют. Также для турбины предъявляются высокие требования к смазочным материалам. Отдельные турбонагнетатели оборудованы так, что система смазки является одновременно охлаждением узла подшипников.
Система охлаждения и устройство турбокомпрессора автомобиля
Охлаждающая система турбокомпрессоров необходима для улучшения передачи тепла от его механизмов и частей. Наиболее распространенные варианты охлаждения деталей — масляный способ и комплексное охлаждение антифризом и маслом. Оба типа имеют свои преимущества, но не лишены и недостатков.
Охлаждение маслом
Достоинства:- Простая конструкция;
- Удешевление турбокомпрессора.
- Меньшая эффективность в сравнении с системой, где выполняется использование антифриза с маслом;
Высокая требовательность к составу масла; - Необходимость часто его менять;
- Требовательность к контролированию температурного режима.
Изначально устройство турбокомпрессора имело только масляное охлаждение, которое быстро достигало высоких температур, проходя через подшипники. Такое масло начинает сразу закипать, возникает эффект коксования, из-за которого забиваются каналы, существенно ограничивая доступ охлаждения и смазки к подшипникам.
В результате подшипники изнашиваются, их заклинивает, необходим дорогостоящий ремонт. У такой неполадки имеется несколько причин:
- Некачественное или не то, которое рекомендовано для двигателя масло;
- Превышение сроков замены масла;
- Неисправности смазочной системы двигателя автомобиля.
Комплексное охлаждение турбины антифризом и маслом
Преимуществом этого варианта становится большая эффективность получаемого охлаждения. Существенный недостаток – усложнение конструкции турбонагнетателей, что повышает их стоимость.Устройство турбонаддува в варианте охлаждения турбин антифризом и маслом более сложное, поскольку в нем имеется отдельный масляный контур, а также система с охлаждающей жидкостью. Зато повышается эффективность работы, устраняются проблемы закипания масла.
Для такого турбонагнетателя масло служит, как и прежде, для охлаждения и смазки подшипников, а антифриз, подаваемый из общей цепи охлаждения двигателя, предотвращает перегрев и не дает закипать маслу. Из-за такой сложности увеличивается цена турбонагнетателя.
Что такое интеркулер на авто?
При работе горячей турбины воздух, нагнетаемый компрессором в ее корпусе, сильно сжимается, отчего происходит его нагрев. Это вызывает нежелательные последствия, поскольку при высокой температуре в воздухе меньше кислорода.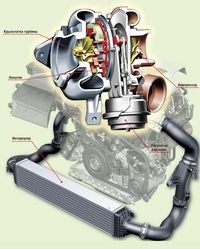
Конструкторы устройства отмечают, что нагрев воздуха далеко не единственная задача, которую им приходится решать при проектировании турбины. Насущной проблемой также становится ее инерционность – задержка реакции двигателя на открытие в коллекторе дроссельной заслонки.
Турбина максимально эффективна, когда достигаются определенные обороты вращения коленчатого вала. Среди автолюбителей даже распространено мнение, что турбонаддув включается только тогда, когда скорость автомобиля достигает определенного значения. Хотя турбина работает постоянно, а значение числа оборотов, при которых ее действие наиболее эффективно, для каждого двигателя индивидуальное.
Отличия твин турбо и битурбо
Решая проблемы устройства турбин, конструкторами была разработана схема, в которой соединились нагнетатели двух компрессоров.
Твинтурбо – это система, в которой несколько одинаковых турбин соединены параллельно. Их задача – повысить давление и объем поступающего воздуха. Система управления включает твин-турбо в момент, когда необходимо получить на повышенных оборотах максимальную мощность.
Подобный компрессор реализован в прославленном японском авто бренда Nissan, который получил имя Skyline Gt-R.
В нем установлен мотор rb26-dett. Аналогичная система, однако, оснащенная одинаковыми небольшими турбинами позволяет получить заметный прирост мощности даже при малых оборотах, при этом поддерживать турбонаддув постоянно.
Последовательное соединение разных турбин получило название «битурбо».
Конструкция сделана так, что при невысоких оборотах функционирует лишь маленькая турбина, которая обеспечивает «отзывчивость» при плавно изменяемой скорости. Если обороты резко возрастают, включается «крупная» турбина». Это позволяет машине получить значительный прирост производительности, причем в любом диапазоне функционирования двигателя.
Инновационные разработки
В числе современных разработок, уже радующих автовладельцев, турбина VGT, у которой лопатки крыльчатки изменяют свой угол наклона, направляя ее в сторону, куда направлены выхлопные газы.
Когда обороты двигателя небольшие, становится более узким пропускное сечение выхода в турбину выхлопных газов, поэтому «выхлоп» получается более быстрым. Чаще эту систему применяют для дизельных агрегатов, но есть разработки и для бензиновых двигателей.
Также к инновационным разработкам относится система twinscroll, где благодаря двойному контуру, по которому совершают обход выхлопные газы, получается, что их энергия вращает общий ротор с компрессором и крыльчаткой.
При этом имеется два варианта реализации:- Выхлопные газы проходят одновременно оба контура и система функционирует как twinturbo.
- Второй тип работает наподобие схемы biturbo – имеется два контура, у которых разная геометрия.
Когда обороты невысокие, выхлопные газы идут по краткому контуру, увеличивающему энергию и скорость благодаря небольшому диаметру. Если обороты повышаются, выхлопные газы поступают в контур, имеющий больший диаметр – при этом рабочее давление сохраняется во впускной системе и отсутствует запор для выхлопных газов. Распределение регулируют механические элементы — клапаны, переключающие потоки.
Сейчас выпускают усовершенствованные турбины, поэтому их популярность возрастает все больше . Турбокомпрессоры перспективны как в плане форсирования моторов, так и потому, что повышают экономичность двигателя, чистоту его выхлопа.
Что такое турбины и для чего они нужны?
Что такое турбины и для чего они нужны?
Основная задача турбин – это повышение мощности двигателя автомобиля. При помощи турбины можно значительно повысить мощность авто.
Принцип работы турбокомпрессора прост: через выпускной коллектор отработанные газы попадают в корпус турбины в которой установлено турбинное колесо, которое приводится в движение. На одной оси с турбинным колесом установлено компрессорное колесо, которое в свою очередь сжимает воздух и падет его в впускной коллектор двигателя. Из всего этого следует, что обороты турбины очень высоки и напрямую зависят от мощности двигателя, скорость вращение турбины достигает 150.000 об/мин и более.
При использовании турбины, в двигатель поступает воздух под высоким давлением, что позволяет увеличиться мощности автомобиля по отношению к объему двигателя и количеству топлива.Наиболее эффективными являются турбокомпрессоры высокого давления. Отличие в конструкции от обычных турбин в том, что турбины повышенного давления имеют клапан, который устраняет избыточное давление на высоких оборотах.Так же большинство турбокомпрессоров оснащены интеркулером.
Основная задача интеркулера – охлаждение воздуха. Так как турбинаработает на больших оборотах, воздух в ней нагревается, тем самым понижается содержание кислорода и плотность воздуха. Интеркулер справляется с этой проблемой. Одной из проблем турбин всегда была небольшая задержка реакции(инерция), но сейчас эти недостатки уже практически устранены. С появлением двух параллельно расположенных турбин, одна из которых предназначена для работы на высоких оборотах, другая на низких, инерция турбины была значительно уменьшена.
Так же, появились турбины, в которых стало возможно изменять угол наклона ротора, что в свою очередь так же позволяет бороться с проблемами связанными с задержкой в реакции. Хорошо уменьшена инерция в турбокомпрессорах с керамическими лопастями ротора, за счет того, что вес их меньше чем у стандартных аналогов.
Принцип работы турбокомпрессора (турбины) его конструкция и типы.
Принцип работы любого турбокомпрессора основан на использовании энергии отработавших выхлопных газов двигателя внутреннего сгорания. Поток выхлопных газов попадает на колесо турбины (закреплённую на валу), тем самым раскручивая её и одновременно с этим раскручивая колесо компрессора, нагнетающего воздух в цилиндры двигателя.
Так как при использовании наддува воздух в цилиндры подаётся принудительно (под давлением), а не только за счёт разрежения, создаваемого поршнем (это разрежение способно взять только определённое количество смеси воздуха с топливом), то в двигатель попадает большая смесь воздуха с топливом. Как следствие, при сгорании увеличивается объём сгораемого топлива с воздухом, образовавшийся газ занимает больший объём и соответственно возникает большая сила, давящая на поршень.
Двигатели внутреннего сгорания снабженные турбокомпрессором более производительные, т.е. меньше удельный эффективный расход топлива (грамм на киловатт-час, г/(кВт•ч)), и выше литровая мощность (мощность, снимаемая с единицы объёма двигателя — кВт/л), что даёт возможность увеличить мощность небольшого мотора без увеличения оборотов двигателя.Вследствие увеличения массы воздуха, сжимаемой в цилиндрах, температура в конце такта сжатия заметно увеличивается и возникает вероятность детонации.
Поэтому, конструкцией двигателей с турбокомпрессором предусмотрена пониженная степень сжатия, применяются высокооктановые марки топлива, а также в системе предусмотрен промежуточный охладитель наддувочного воздуха (интеркулер)- радиатор для охлаждения воздуха. Уменьшение температуры воздуха требуется также и для того, чтобы плотность его не снижалась вследствие нагрева от сжатия после турбины, иначе эффективность всей системы значительно упадёт.
Особенно эффективен турбонаддув у дизельных двигателей тяжёлых грузовиков. Он повышает мощность и крутящий момент при незначительном увеличении расхода топлива. Наиболее мощные (по отношению к мощности двигателя) турбокомпрессоры применяются на тепловозных двигателях. Например на дизеле Д 49 мощностью 4000 л.с. установлен турбокомпрессор мощностью 1100 л.с.Наибольшей (по абсолютной величине) мощностью обладают турбокомпрессоры судовых двигателей, которая достигает 7000 л.с. .Современные турбокомпрессоры можно разделить на два основных типа: 1- с изменяемой геометрией соплового аппарата ( VNT турбокомпрессоры) и 2- без геометрии. Все они в свою очередь могут быть моно, твинскролы (двойные турбины) и т.д.
Профилактика и рекомендации.
При запуске двигателя необходимо дать ему поработать на холостом ходу не менее шестидесяти секунд и прибавлять газ постепенно. Это обеспечивает достаточную смазку движущихся элементов турбины и предохраняет их от преждевременного износа. Чтобы не создавалось низкое давление в двигателе и пропускание паров масла, не эксплуатируйте турбину на холостом ходу более тридцати минут.
Обязательно давайте остыть турбокомпрессору перед выключением зажигания, поскольку быстрое выключение создаст резкий перепад температур в системе. Такие переходы быстро изнашивают любой механизм.
Что касается эксплуатации авто зимой, когда двигатель быстро остывает или после долгого перерыва в работе необходимо сначала провернуть двигатель, и только потом запускать его на холостых оборотах. Это позволит наладить быструю циркуляцию масла и быстро заполнить систему компрессора рабочей жидкостью.
Рекомендуется регулярная диагностика двигателя, особенно если Вы не уверены в качестве дизельного топлива.
По каким признакам можно определить неисправность турбины?
Профессионально это сделать может только опытный мастер, но есть поломки, сразу бросающиеся в глаза. Это повышенный расход масла, синий дым из выхлопной трубы, посторонние шумы в работе мотора.
Как работает турбина на бензиновом двигателе?
Здравствуйте, уважаемые читатели и посетители блога Автогид.ру. Сегодня в статье мы с вами разберёмся и узнаем как работает турбина на бензиновом двигателе. Тема, конечно интересная и в первую очередь для владельцев бензиновых турбированных автомобилей. Зачастую информации о принципе работы и устройстве турбины на бензиновом моторе достаточно мало или она слишком сложна для восприятия обыкновенного человека.
Использование турбины позволяет любому двигателю с малым объёмом увеличить мощность без возрастания расхода топлива и сокращения ресурса эксплуатации. После подключения турбины мотор словно получает невидимый пинок и работает значительно шустрее. Существуют особенности использования бензиновых моторов, оснащённых турбинами.
Их необходимо учитывать для продления срока службы устройства и использования двигателя машины с максимальной эффективностью. Перед тем как говорить о принципе работы турбины на бензиновом двигателе надо узнать историю её появления и широкого использования производителями автомобилей.
История появления турбированного бензинового мотора
Первые двигатели внутреннего сгорания, как и все технические первопроходцы имели очень «сырой» вид и требовали доработки. Время шло и на рынке появлялись надёжные и долговечные модели бензиновых моторов, которые радовали водителей своей неприхотливостью в обслуживании и выносливостью. Требования к моторам среди потребителей возрастали и критерии контролирующих органов ужесточались.
Первоначально развитие бензиновых моторов осуществлялось во многом по экстенсивному пути. Для увеличения мощность двигателя его объём просто увеличивался. Все было отлично если бы не возрастающий пропорционально расход топлива и количество вредных выбросов в окружающую среду. Продолжаться это больше так не могло и перед инженерами и создателями двигателей внутреннего сгорания была поставлена очень непростая задача.
Добиться увеличения мощность ДВС (двигателя внутреннего сгорания) без увеличения объёма мотора и расхода топлива. Решений было предложено большое количество, но выбрано было единственное верное направление развития моторов. Было решено работать над увеличением эффективности образования и сгорания топливно-воздушной смеси в моторе автомобиля.
Единственный верный способ увеличить эффективность сгорания смеси топлива и воздуха – это увеличить поступление воздуха в цилиндры мотора. При этом дополнительный объём воздуха должен был поступать принудительно за счёт создаваемого давления.
Дополнительное количество воздуха значительно усиливало сгорание топлива в цилиндрах мотора и тем самым высвобождая дополнительные мощности при неизменном объёме. Идея простая, но требующая реализации в виде появления устройства для нагнетания воздуха в цилиндры двигателя.
Для решения этой задачи автомобильные инженеры решили опираться на разработки авиационной промышленности. Она уже очень давно использовала турбины. Первые турбированные бензиновые моторы появились на грузовых автомобилях в тридцатых годах прошлого века. Грузовики использующие турбины прибавили в мощности и оптимизировали расход топлива.
Удачный опыт использования турбины как устройства для нагнетания массы воздуха в грузовых машинах подвиг конструкторов и инженеров автомобильной промышленности ускорить движение в этом направлении. Первые автомобили с бензиновыми моторами оснащёнными турбинами начали продаваться на территории США в 60-х годах прошлого века.
Первые модели автомобилей этого типа автолюбители из США встретили настороженно и с подозрительностью. Только через 10 лет в 70-х годах прошлого века их оценили по достоинству и начали активно использовать при создании машин со спортивным уклоном. На серийные модели автомобилей турбины устанавливали в очень малом количестве.
Это было вызвано тем, что первые модели моторов с турбинами оказались очень «прожорливыми» и имели массу прочих мелких недоработок, портящих первое впечатление. Значительный расход топлива не дал возможность наладить широкое производство машин с турбированным моторами. Значительно замедлило внедрение турбин в моторы нефтяной кризис, закончившийся увеличением цен на топливо. Люди стали больше экономить.
Лишь в конце 90-х годов после значительного улучшения конструкции турбины и бензинового мотора в целом удалось изменить ситуацию. Это стало отправной точкой начала эры развития и становления бензиновых турбированных двигателей.
Как работает турбина на бензиновом двигателе?
Турбина бензинового мотора за счёт использования компрессора принудительно нагнетает в цилиндры массу воздуха. Значительно повышается обогащение кислородом топливно-воздушной смеси и улучшается сгораемость бензина. Коэффициент полезного действия существенно возрастает. Эффективность работы мотора увеличивается при неизменно объёме.
Мощность двигателя при использовании турбины возрастает прямо пропорционально количеству сжигаемого за единицу времени бензина. Для обеспечения максимального быстрого сгорания топлива в цилиндрах мотора необходим значительный объём воздуха. Именно его в достаточном количестве направляет турбина за счёт работы компрессора. Он принудительно подаётся в цилиндры, обогащая топливно-воздушную смесь.
Если разрезать турбину бензинового мотора вдоль корпуса можно увидеть следующее рабочие элементы:
Корпус подшипников.
Служит для размещения ротора, представленного валом несущим на себе турбинные и компрессорные кольца, оборудованные лопастями. Именно они при вращении захватывают воздуха и направляют его в цилиндры мотора.
Масляные каналы.
Пронизывают корпус турбины словно кровеносные сосуды на теле человека. Служат для своевременной доставки моторного масла к трущимся и вращающимся элементам. Снижают тем самым износ рабочих элементов бензиновой турбины.
Подшипник скольжения.
Его главная задача обеспечить свободное и плавное вращение ротора турбины с его лопастями для захвата достаточного количества воздуха. Его смазку и охлаждение обеспечивает циркулирующее в турбине моторное масло.
Корпус.
Корпус турбины, имеющий форму улитки обеспечивают защиты от внешних механических воздействий рабочие элементы устройства для нагнетания воздуха.
Привод турбины бензинового мотора осуществляется за счёт подачи отработанного газа энергия которого заставляет ротор вращать лопасти. Сложного в конструкции и работе ничего нет всё понятно и достаточно просто.
При запуске бензинового мотора отработанные газы и цилиндров мотора направляются прямиком в турбину. Они приводят в движение ротор, отдавая ему свою энергию. Далее, через приёмную трубу они поступают в глушитель и выводятся в окружающую среду.
Вал ротора раскручивает колесо компрессора и лопаточное колесо. Они захватывают воздух из окружающей среды, поступающий через воздушный фильтр мотора. Он принудительно подаётся в цилиндры двигателя. Компрессор турбины может повышать давление воздуха до 80%.
Работа турбины бензинового мотора позволяет обогащённую кислородом топливно-воздушную смесь наполнять цилиндры в большом количестве. Объём мотора остаётся неизменным, но его мощность существенно возрастает. В среднем использование турбины даёт возможность увеличить мощность силовой установки машины на 20-30%.
Что необходимо знать для грамотной эксплуатации бензиновой турбины?
Для обеспечения долговечной работы турбины на бензиновом моторе не нужно экономить на количестве и качестве моторного масла. Любители пропускать интервалы замены масла в моторе рано или поздно столкнуться с проблемами и нарушениями в работе турбины. Она очень восприимчива к качеству используемого масла. Дешёвое масло не сможет обеспечить необходимый уровень трения рабочих элементов и они при интенсивном использовании автомобиля достаточно быстро придут в негодность и потребуют замены.
При покупке автомобиля, оснащённого турбиной надо обязательно выполнить замену моторного масла и прочистку всей системы. Смешивать доливая другое масло нельзя, так как оно теряет свои свойства и эффективность его работы стремится к нулю. Полная замена масла позволит избежать вредных воздействий и усилить защиту турбины бензинового мотора.
Есть некоторые особенности эксплуатации мотора, оснащённого турбиной. После длительной поездки на машине двигатель во время остановки сразу глушить не нужно. Необходимо дать ему время поработать на холостых оборотах и немножко остыть. Резкое выключение мотора создаёт температурный перепад отрицательным образом, сказывающийся на прочности и надёжности рабочих элементов турбины мотора.
Преимущества и недостатки турбированного мотора
Главным преимуществом любого бензинового мотора, оснащённого турбиной является увеличение его мощности на 20-30%. При одинаковом объёме с традиционным атмосферным ДВС его мощность выше на треть. Эффективность использования топлива существенно повышается.
Максимальный уровень сгорания топливно-воздушной смеси позволяет существенно снизить выброс загрязняющих веществ в окружающую среду. Максимальное использование турбированных моторов повсеместно настоящая мечта защитника окружающей среды. На этом преимущества турбированного мотора заканчиваются.
Турбированные моторы очень требовательны к качеству используемого топлива и моторного масла. Всё это в совокупности приводит к увеличению расходов на использование автомобиля в долгосрочной перспективе. Обслуживание турбированного мотора потребует от водителя больших расходов денежных средств.
Ремонт турбины требует использования специального оборудования и материалов. Самостоятельно его выполнить очень проблематично. Зачастую век отремонтированной турбины недолог и в конечном итоге потребуется её замена. Это может ощутимо ударить по кошельку владельца машины.
Заключение
Появление турбированных моторов является ещё одной ступенькой развития силовой автомобильных установок. Современные требования к экологической составляющей двигателя существенно ужесточаются и конкуренция между производителями машин обостряется.
Как работает турбокомпрессор
Как работает турбокомпрессорСодержание статьи
- Введение
- Турбокомпрессоры и двигатели
- Устройство турбокомпрессора
- Детали турбокомпрессора
- Использование двух турбокомпрессоров и других турбо деталей
- Узнать больше
- Читайте также » Все статьи про работу двигателя
В этой статье мы узнаем, каким образом турбокомпрессор увеличивает мощность двигателя в жестких условиях эксплуатации. Мы также узнаем о том, как регуляторы давления наддува, керамические лопатки турбины и шариковые подшипники улучшают работу турбокомпрессора. Турбокомпрессоры являются своего рода системой наддува.

Для увеличения мощности двигателя, турбокомпрессор использует выхлопные газы для вращения турбины, которая, в свою очередь, вращает нагнетатель воздуха. Турбина турбокомпрессора вращается со скоростью до 150.000 оборотов в минуту (об/мин) — это примерно в 30 раз быстрее, чем скорость вращения большинства автомобильных двигателей.

Далее мы расскажем о том, как узнать, насколько увеличится мощность двигателя, если установить турбокомпрессор.
Система турбонаддува автомобиля Mitsubishi Lancer Evolution IX.
Турбокомпрессоры и двигатели
Одним из самых эффективных способов увеличения мощности двигателя является увеличение количества сгораемого воздуха и топлива. Для этого можно установить дополнительные цилиндры или увеличить их объем. В некоторых случаях невозможно осуществить эти модификации, поэтому установка турбокомпрессора может стать более простым и компактным способом увеличения мощности, особенно для подержанных автомобилей.
Турбокомпрессоры позволяют двигателю сжигать больше топлива и воздуха благодаря увеличению подачи смеси в цилиндры. Стандартное давление сжатия воздуха турбокомпрессором составляет 6-8 фунт/дюйм2 (0,4 — 0,55 бар). Учитывая, что нормальное атмосферное давление составляет 14,7 фунт/дюйм2 (1 бар), при помощи турбокомпрессора в двигатель поступает на 50% больше воздуха. Следовательно, можно рассчитывать на увеличение мощности двигателя на 50%. Однако, эта технология не идеальна, поэтому мощность увеличивается на 30 — 40%.
Одна причина недостаточной эффективности состоит в том, что энергия, которая вращает турбину, не является свободной. Турбина, установленная в потоке выхлопных газов, создает препятствие для выхода газов. Это означает, что во время такта выпуска двигатель должен преодолеть высокое противодавление. В связи с этим происходит расход энергии работающих цилиндров.
Расположение турбокомпрессора в автомобиле
Устройство турбокомпрессора
Турбокомпрессор крепится к выпускному коллектору двигателя при помощи болтового соединения. Выхлопы из цилиндра вращают турбину, которая работает как газотурбинный двигатель. Турбина при помощи вала соединяется с компрессором, который установлен между воздушным фильтром и впускным коллектором. Компрессор сжимает воздух, поступающий в цилиндры.
Отработанные газы от цилиндра проходят через лопатки турбины, вызывая ее вращение. Чем больше выхлопных газов проходит через лопатки, тем быстрее происходит вращение.
С другой стороны вала, который установлен на турбине, компрессор вводит воздух в цилиндры. Компрессор представляет собой своего рода центробежный насос — он втягивает воздух в центр лопаток и выпускает его под давлением во время вращения.
Для того, чтобы выдержать скорость вращения до 150.000 об/мин, вал турбины должен иметь надежную опору. Большинство подшипников не выдержит такую скорость и взорвется гидростатические подшипники. Такой тип подшипников поддерживает вал на тонком слое масла, которое непрерывно подается. Это обусловлено двумя причинами: Масло охлаждает вал и некоторые другие детали турбокомпрессора и позволяет валу вращаться, снижая трения.
Существует много различных решений, связанных с конструкцией турбокомпрессоров для автомобильных двигателей. На следующей странице мы расскажем о некоторых оптимальных вариантах и рассмотрим, как они влияют на работу двигателя.
Слишком сильное сжатие?
Когда воздух под давлением запускается в цилиндры при помощи турбокомпрессора и затем сжимается поршнями (читайте статью «Как работает автомобильный двигатель» для наглядного описания), существует риск самовозгорания смеси. Возгорание может произойти при сжатии воздуха, т.к. при этом возрастает температура. При высокой температуре может произойти возгорание еще до срабатывания свечи зажигания. Для предотвращения раннего сгорания топлива, автомобили с турбокомпрессором рекомендуется заправлять высокооктановым бензином. Если давление наддува слишком высокое, возможно придется уменьшить степень сжатия двигателя для того, чтобы избежать раннего сгорания топлива. |
Как устанавливается турбокомпрессор
Как турбокомпрессор выглядит изнутри
Детали турбокомпрессора
Одна из основных проблем турбокомпрессоров состоит в том, что они не обеспечивают мгновенный форсированный наддув по нажатию на педаль газа. Турбине требуется несколько секунд для того, чтобы набрать скорость вращения, необходимую для наддува. В результате возникает задержка между временем нажатия на педаль газа и временем начала ускорения автомобиля при срабатывании турбины.
Одним из способов устранения задержки является снижение инерции вращающихся деталей, благодаря снижению их массы. Это способствует более быстрому набору скорости вращения турбины и компрессора и раннему началу наддува. Одним из наиболее надежных способов снижения инерции турбины и компрессора является уменьшение их размеров. Небольшой турбокомпрессор быстрее начнет наддув при низкой скорости работы двигателя, однако он не сможет обеспечить достаточный наддув при больших скоростях двигателя, когда в цилиндры поступает значительные объемы воздуха. Также существует риск слишком быстрого вращения на высоких скоростях двигателя, т.к. при этом через турбину проходит значительный объем выхлопа.
Большой турбокомпрессор может обеспечить сильный наддув при высокой скорости вращения двигателя, однако при этом может наблюдаться сильная задержка наддува, т.к. необходимо определенное время на разгон тяжелой турбины и компрессора. К счастью, существует ряд решений данных проблем.
В большинстве автомобильных турбокомпрессоров используется регулятор давления наддува, который позволяет уменьшить время задержки наддува небольших турбокомпрессоров, предотвращая слишком быстрое вращение при высокой скорости вращения двигателя. Регулятор давления наддува представляет собой клапан, который обеспечивает выпуск выхлопа в обход лопаток турбины. Регулятор давления наддува измеряет давление наддува. Если давление слишком высокое, это означает, что турбина вращается слишком быстро, поэтому регулятор давления наддува выпускает определенное количество выхлопа в обход лопаток для снижения скорости вращения турбины.
В некоторых турбокомпрессорах используются шариковые подшипники вместо гидростатических подшипников для поддержки вала. Но это не обычные шариковые подшипники – это особые подшипники, изготовленные из специального материала, которые могут выдержать скорости и температуры турбокомпрессора. Они снижают трение вала турбины при вращении, как и гидростатические подшипники. Они также позволяют использовать меньший и облегченный вал. Благодаря этому происходит быстрый набор скорости турбокомпрессором, что, в свою очередь, снижает задержку.
Керамические лопатки турбины легче стальных лопаток, которые используются в большинстве турбокомпрессоров. Благодаря этому опять же происходит быстрый набор скорости турбокомпрессором, что снижает задержку.
Турбокомпрессор обеспечивает наддув при большой скорости вращения двигателя.
Использование двух турбокомпрессоров и других турбо деталей
На некоторые двигатели устанавливается два турбокомпрессора разного размера. Малый турбокомпрессор быстрее набирает обороты, снижая тем самым задержку ускорения, а большой обеспечивает больший наддув при высокой скорости вращения двигателя.
Когда воздух сжимается, он нагревается, а при нагревании воздух расширяется. Поэтому повышение давления от турбокомпрессора происходит в результате нагревания воздуха до его впуска в двигатель. Для того, чтобы увеличить мощность двигателя, необходимо впустить в цилиндр как можно больше молекул воздуха, при этом не обязательно сжимать воздух сильнее.
Охладитель воздуха или охладитель наддувочного воздуха является дополнительным устройством, которое выглядит как радиатор, только воздух проходит как внутри, так и снаружи охладителя. При впуске воздух проходит через герметичный канал в охладитель, при этом более холодный воздух подается снаружи по ребрам при помощи вентиляторов охлаждения двигателя.
Охладитель увеличивает мощность двигателя, охлаждая сжатый воздух от компрессора перед его подачей в двигатель. Это значит, что если турбокомпрессор сжимает воздух под давлением 7 фунт/дюйм2 (0,5 бар), охладитель осуществит подачу охлажденного воздуха под давлением 7 фунт/дюйм2 (0,5 бар), который является более плотним и содержит больше молекул, чет теплый воздух.
Турбокомпрессоры также обладают преимуществом на большой высоте, где плотность воздуха ниже. Обычные двигатели будут работать слабее на большой высоте над уровнем моря, т.к. на каждый ход поршня подаваемая масса воздуха будет меньше. Мощность двигателя с турбокомпрессором также снизится, но менее заметно, т.к. разреженный воздух легче сжимать.
В старых автомобилях с карбюраторами автоматически увеличивается подачу топлива в соответствии с увеличением подачи воздуха. В современных автомобилях происходит то же самое. Система впрыска топлива ориентируется на данные датчика кислорода в выхлопе для определения необходимого соотношения топлива и воздуха, так что система автоматически увеличивает подачу топлива при установленном турбокомпрессоре.
При установке мощного турбокомпрессора на двигатель с впрыском топлива, система может не обеспечить необходимое количество топлива — либо программное обеспечение контроллера не допустит, либо инжекторы и насос не смогут осуществить необходимую подачу. В этом случае необходимо осуществлять уже другие модификации для максимального использования преимуществ турбокомпрессора.
Для получения большей информации по турбокомпрессорам, рекомендуем ознакомиться со ссылками на следующей странице.
Mazda RX-8 купе-кабриолет с установленной системой турбонаддува
Источник: https://auto.howstuffworks.com/
Ремонт турбин дизельного и бензинового двигателя: как правильно отремонтировать турбину?
Сегодня огромное количество автовладельцев наслаждаются быстрой ездой на автомобилях с турбированными двигателями. С использованием турбокомпрессора показатель мощности возрастает на 30%, а то и 40%. К сожалению, как и любой механизм, турбина со временем изнашивается. И откладывать ремонт нельзя ни в коем случае. В конце концов это может привести к поломке самого двигателя. В статье мы расскажем, почему возникают неполадки, как их предотвратить, какие этапы включает ремонт и где можно отремонтировать турбину.
Почему может сломаться турбокомпрессор
Турбокомпрессор — это механизм, использующий кинетическую энергию выхлопных газов для сжатия и нагнетания воздуха в цилиндры двигателя. Он устанавливается в выхлопной системе между выпускным коллектором и выхлопной трубой. Турбокомпрессор устанавливают и на бензиновые двигатели, и на дизельные. Разница между ними состоит в температурных режимах работы. Рабочая температура бензиновой турбины выше на 200 градусов, поэтому для ее изготовления используют сплавы большей жаропрочности. По статистике, турбокомпрессор выходит из строя раньше остальных частей двигателя. Это связано с тем, что бесперебойная работа турбины сильно зависит от исправности всех систем автомобиля. При вращении до 250 000 оборотов в минуту и температуре до 1000 градусов она нуждается в безупречной работе систем охлаждения и смазки, топливной и выхлопной системы, системы вентиляции картерных газов. Турбокомпрессор — достаточно надежное устройство, и дефекты в его конструкции сами по себе не появляются. Повреждения, как правило, вызваны следующими причинами:
Некачественное или загрязненное масло. В процессе работы масло очень сильно загрязняется сажей от сгорания топлива. Если двигатель при 5000 оборотах в минуту еще может кратковременно «пережить» грязное масло, то для турбокомпрессора это неизбежная «смерть». Вал и подшипники при вращении испытывают значительную нагрузку, и любая твердая частица оставляет царапины. Для турбированных двигателей необходимо приобретать специальное моторное масло высокого качества. Оно будет создавать хорошую масляную прослойку между валом и подшипниками, что исключит сухое трение и повышенный износ.
Недостаточное количество масла . При уменьшении проходимости масла через турбокомпрессор резко повышается температура внутри корпуса. Из-за этого масло начинает сворачиваться, что в результате приводит к закоксовыванию внутренних лопаток турбины и трубок подачи и слива масла. Это может происходить по причине неисправности масляного насоса, деформации трубок подачи и слива или при недостаточном количестве масла в двигателе.
Попадание инородных частиц . В процессе всасывания компрессорным колесом воздуха в турбину могут попадать посторонние предметы (песок, грязь, мелкие насекомые). Это приводит к постепенной деформации и стачиванию лопастей крыльчатки. Поэтому необходима регулярная и своевременная замена воздушного фильтра. Турбинная крыльчатка может засоряться отколовшимися фрагментами клапанов и свеч накала, кусочками герметика. Такое воздействие оставляет трещины на коллекторе, приводит к дисбалансу ротора, в этом случае отремонтировать турбину двигателя уже практически невозможно.
Засорение выхлопной системы . Для повышения экологичности двигателей на современные автомобили часто устанавливают катализаторы и фильтры. Частой проблемой при наличии такой конструкции является уменьшение выхлопа за счет засорения катализатора. Уменьшение выхлопа создает неблагоприятное давление на вал турбокомпрессора и провоцирует быстрый износ подшипника. Чтобы избежать возникновения таких факторов, нужно менять катализатор каждые 150 000 км.
Несоблюдение условий эксплуатации. Благодаря особенностям своего строения турбокомпрессор очень «любит» масло. Но многие автолюбители допускают большие интервалы между его заменой (в российских условиях рекомендовано менять масло каждые 10 000 км). Также пагубное влияние оказывают так называемые «холодные запуски», когда перед движением автомобиля двигатель не успевает достаточно прогреться и масло не попадает в необходимых количествах на детали турбокомпрессора.
Как отремонтировать турбину: этапы процесса
О неисправности турбокомпрессора могут свидетельствовать увеличенный расход масла, снижение производительности двигателя, посторонние шумы и «нездоровый» черный выхлоп. Ремонт турбин двигателей — задача далеко не простая. Для ее решения необходимо специализированное оборудование и комплексная диагностика. Лучшим вариантом для получения полного анализа неполадок и качественного ремонта будет обращение в квалифицированный автосервис.
В технических центрах процесс ремонта турбокомпрессора состоит из следующих этапов:
- Специалисты проводят полную компьютерную диагностику электронных узлов для выявления ошибок и кодов неисправности с датчиков автомобиля.
- Осматривают турбину для проверки ее целостности; определяют, прослеживаются ли осевой люфт и потеря масла; оценивают состояние клапана вестгейта.
- Демонтируют и разбирают турбокомпрессор, проводят визуальную дефектовку.
- Разобранную турбину отправляют на чистку. Для начала ее отмывают в паровой высокотемпературной камере и в ультразвуковой ванне. Это снимает все масляные отложения и позволяет выявить образовавшиеся трещины. Затем неповрежденные детали турбокомпрессора отправляют на обработку в пескоструйную камеру. Мощная струя мелкодисперсного песка может удалить самые сложные загрязнения и налет. В конце проводится полировка деталей.
- Прошедшую все уровни очистки турбину отправляют на сборку. При необходимости вышедшие из строя детали заменяют на новые.
- Затем турбокомпрессор проходит три этапа балансировки. Сначала балансируется ротор, потом ротор с колесом и в последнюю очередь сам картридж.
- Далее турбину тестируют на специализированных стендах. Чтобы сымитировать рабочие условия двигателя, турбокомпрессор вращают до 180 000 оборотов в минуту при одновременной подаче масла под давлением. На данном этапе происходит выявление остаточного дисбаланса ротора.
- С помощью прибора-тестера анализируют состояние актуаторов — электронных или механических клапанов.
- Отремонтированную турбину устанавливают на автомобиль, проверяют патрубки и интеркулер на герметичность с помощью дымогенератора. На всех этапах ремонта турбокомпрессора должна соблюдаться идеальная чистота, ведь даже мельчайшие частицы грязи могут привести к быстрому износу запчастей.
- Проводят повторную компьютерную диагностику.
В процессе ремонта бензиновых турбин могут быть выявлены неполадки в работе катализатора. Как правило, это происходит из-за его постепенного засорения продуктами переработки топлива. Вышедший из строя катализатор необходимо в первую очередь демонтировать. Далее можно заменить неисправный агрегат на новый. Однако катализатор стóит очень дорого, так что автовладельцы в основном прибегают к более бюджетному способу решения проблемы — после удаления агрегата блок управления двигателем перепрошивается [1] . На этапе ремонта турбин дизельных двигателей такой же процедуре подвергается сажевый фильтр.
Важным условием для правильной работы турбокомпрессора является исправность клапана ЕГР. ЕГР (от англ. Exhaust Gas Recirculation) — это система, отвечающая за снижение уровня выброса оксидов азота. Как и в случае с катализаторами и сажевыми фильтрами, клапан ЕГР тоже подвержен засорению. Также причиной ухудшения его работы может быть неисправность датчика положения или протечка охладителя системы. Своевременные мероприятия по уходу за катализатором или сажевым фильтром, клапаном ЕГР значительно продлят срок службы турбокомпрессора и предотвратят многие возможные причины поломки.
Можно ли самому отремонтировать турбину
Некоторые владельцы авто считают, что ремонт турбины двигателя не требует обращения в специализированные сервисы. Обладая элементарными навыками автомеханика, можно испробовать вариант восстановления турбокомпрессора в «домашних» условиях. В идеале грамотное устранение неполадок начинается с их обнаружения. Но без специального оборудования допустить ошибку крайне легко. Выше мы описали весь перечень действий, которые проводят технически оснащенные сервисы. Понятное дело, что самостоятельно получится воспроизвести далеко не все этапы, требуемые для ремонта турбины.
Как правило, «домашний» ремонт включает в себя демонтаж, разборку, очистку специальным раствором, визуальную дефектовку, замену необходимых деталей, сборку и монтаж. Успех такого мероприятия имеет место, но далеко не во всех случаях. Например, если проблема заключалась в загрязнении и закоксовке некоторых деталей, самостоятельное восстановление может дать положительный результат. Но в любом случае при сборке, не имея специализированного стенда, можно допустить серьезные ошибки в балансировке ротора и картриджа. К тому же не получится произвести необходимую компьютерную диагностику для выявления общей картины неполадок.
Водителю, решившемуся на самостоятельный ремонт турбокомпрессора, лучше не спешить и взвесить все за и против. Желание сэкономить может обернуться еще бóльшими финансовыми тратами. Неправильно отлаженная турбина способна нанести значительный урон двигателю, вплоть до его полного выхода из строя. Даже имея хорошие знания автомеханики, легко допустить ошибку из-за отсутствия необходимого оборудования. Риск нанести двигателю еще больший вред и отсутствие гарантий — серьезные аргументы не в пользу непрофессионального вмешательства.
Ремонт и восстановление турбин — неизбежная процедура для каждого автолюбителя, использующего турбированный двигатель. В этом деле не стоит рисковать с самостоятельным ремонтом или обращаться в сомнительные СТО. Оптимальным вариантом будет доверить автомобиль квалифицированным сервисам.
Принцип работы турбонаддува — бензин и дизель
Турбонаддув – устройство, призванное увеличить мощность двигателя внутреннего сгорания. Оно стало настоящим прорывом в моторостроении ХХ века, но широкое распространение приобрело значительно позже. Автором данного изобретения является Альфред Бьюхи.
Принцип работы и устройство турбонаддува.
Принцип работы турбонаддува при всей его значимости в приросте мощности двигателя весьма прост: на одном валу закреплены крыльчатки двух улиток-турбин, задача одной части посредством потока отработанных газов раскручиваться и приводить в действие вторую часть, которая работает нагнетателем воздуха в двигатель. Именно в увеличении объема воздуха, посылаемого в камеру сгорания, и кроется секрет увеличения мощности движка.
Но, как уже отмечалось выше, при всей своей логической простоте устройство набирало значимость довольно долго – более полувека. Причины:
- требовательность к точности изготовления,
- необходимость в жаропрочных качественных материалах,
- отсутствие в массовом производстве высокооктанового топлива.
Последнее к слову ограничивало применение турбонаддува только на бензиновых двигателях.
Благо, наука не стоит на месте и с годами появлялись более качественные материалы, позволившие турбонаддуву начать проникать сперва в мир автогонок, где он позволял без увеличения веса двигателя увеличивать его мощность и достигать командам высоких позиций в финальных таблицах, а после и на потребительский рынок.
Теперь немного подробнее о том, как работает турбонаддув на бензиновых и дизельных двигателях, а точнее – об особенностях его работы, ведь принцип действия у них практически идентичен.
Особенности работы турбонаддува дизельного двигателя.
Дизель с турбонаддувом сегодня можно встретить гораздо чаще, чем его собрата – бензиновый агрегат. Так происходит потому, что применение турбины в дизеле позволяет решить его главную проблему – низкую эффективность на высоких оборотах – раз и навсегда.
Также аргументом в пользу использования турбины в дизельных ДВС можно назвать невысокую стоимость подобного внедрения за счет меньшей температуры выхлопных газов и более низких оборотов, которые, в сравнении все с тем же бензиновым мотором, требуют применения менее качественных материалов. Отсюда такая популярность турбонаддува у производителей дизельных авто и владельцев последних. В то же время массовость применения данного устройства в дизелях позволяет развиваться самому надуву в принципе, делая его все доступнее для бензиновых транспортных средств.
Особенности работы турбонаддува бензинового двигателя.
Если речь идет об использовании турбонаддува на бензиновых двигателях, то она в первую очередь касается высоконагруженных моторов, комплектующих спорткары и некоторые люксовые автомобили.
Такое классовое различие кроется в том, что прирост мощности в бензиновом двигателе требует больших капиталовложений, как в саму турбину двигателя, так и в обслуживание авто: на дорогое высокооктановое топливо и его количество (турбонаддув всегда ведет к увеличенному расходу), которые не всегда оправданы.
Дело в том, что в турбированном бензиновом ДВС прирост мощности достигается при высоких оборотах, при этом, таков принцип работы турбонаддува, сама мощность возрастает весьма стремительно, что для обычного среднестатистического водителя бензинового автомобиля не всегда необходимо, скорее, даже наоборот… а переплачивать за то, что вся эта мощность никогда не будет использоваться, не имеет смысла.
Видео.
Рекомендую прочитать:
Как работают газотурбинные электростанции
Турбины внутреннего сгорания (газовые), устанавливаемые на многих современных электростанциях, работающих на природном газе, представляют собой сложные машины, но в основном они состоят из трех основных частей:
- Компрессор , который втягивает воздух в двигатель, нагнетает давление его и подает в камеру сгорания со скоростью сотни миль в час.
- Система сгорания , обычно состоящая из кольца топливных форсунок, которые впрыскивают постоянный поток топлива в камеры сгорания, где оно смешивается с воздухом.Смесь сжигается при температуре более 2000 градусов по Фаренгейту. При сгорании образуется высокотемпературный газовый поток под высоким давлением, который входит и расширяется через турбинную секцию.
- Турбина представляет собой сложный набор чередующихся неподвижных и вращающихся лопастей с профилем крыла. Когда горячий газ сгорания расширяется через турбину, он раскручивает вращающиеся лопасти. Вращающиеся лопасти выполняют двойную функцию: они приводят в действие компрессор, чтобы втянуть больше сжатого воздуха в секцию сгорания, и вращают генератор для выработки электроэнергии.
Наземные газовые турбины бывают двух типов: (1) двигатели с тяжелой рамой и (2) авиационные двигатели. Двигатели с тяжелой рамой характеризуются более низким коэффициентом давления (обычно ниже 20) и имеют тенденцию быть физически большими. Степень давления — это отношение давления нагнетания компрессора к давлению воздуха на входе. Двигатели на базе авиационных двигателей являются производными от реактивных двигателей, как следует из названия, и работают с очень высокими степенями сжатия (обычно превышающими 30). Двигатели на базе авиационных двигателей имеют тенденцию быть очень компактными и полезны там, где требуется меньшая выходная мощность.Поскольку турбины с большой рамой имеют более высокую выходную мощность, они могут производить большее количество выбросов и должны быть спроектированы таким образом, чтобы обеспечивать низкие выбросы загрязняющих веществ, таких как NOx.
Одним из ключевых факторов удельного расхода топлива турбины является температура, при которой она работает. Более высокие температуры обычно означают более высокую эффективность, что, в свою очередь, может привести к более экономичной эксплуатации. Газ, протекающий через турбину типичной электростанции, может иметь температуру до 2300 градусов по Фаренгейту, но некоторые из критических металлов в турбине могут выдерживать температуры только от 1500 до 1700 градусов по Фаренгейту.Следовательно, воздух из компрессора может использоваться для охлаждения основных компонентов турбины, что снижает конечный тепловой КПД.
Одним из главных достижений программы передовых турбин Министерства энергетики было преодоление прежних ограничений по температурам турбин с использованием комбинации инновационных технологий охлаждения и современных материалов. Усовершенствованные турбины, появившиеся в результате исследовательской программы Департамента, смогли повысить температуру на входе турбины до 2600 градусов по Фаренгейту — почти на 300 градусов выше, чем в предыдущих турбинах, и достичь КПД до 60 процентов.
Еще одним способом повышения эффективности является установка рекуператора или парогенератора с рекуперацией тепла (HRSG) для рекуперации энергии из выхлопных газов турбины. Рекуператор улавливает отходящее тепло в выхлопной системе турбины, чтобы предварительно нагреть воздух на выходе компрессора перед его поступлением в камеру сгорания. ПГРТ вырабатывает пар за счет улавливания тепла из выхлопных газов турбины. Эти котлы также известны как парогенераторы-утилизаторы. Пар высокого давления из этих котлов можно использовать для выработки дополнительной электроэнергии с помощью паровых турбин, такая конфигурация называется комбинированным циклом.
Газовая турбина простого цикла может достигать КПД преобразования энергии в диапазоне от 20 до 35 процентов. С учетом более высоких температур, достигнутых в турбинной программе Министерства энергетики, будущие газотурбинные установки с комбинированным циклом, работающие на водороде и синтез-газе, вероятно, достигнут КПД 60 процентов или более. Когда отработанное тепло улавливается из этих систем для отопления или промышленных целей, общая эффективность энергетического цикла может приближаться к 80 процентам.
Газотурбинный двигатель | Британника
Полная статья
Газотурбинный двигатель , любой двигатель внутреннего сгорания, использующий газ в качестве рабочего тела, используемого для вращения турбины.Термин также обычно используется для описания полного двигателя внутреннего сгорания, состоящего, по меньшей мере, из компрессора, камеры сгорания и турбины.
Общие характеристики
Полезная работа или тяга может быть получена от газотурбинного двигателя. Он может приводить в действие генератор, насос или воздушный винт или, в случае чисто реактивного авиационного двигателя, развивать тягу, ускоряя поток выхлопных газов турбины через сопло. Такой двигатель, который при той же мощности намного меньше и легче поршневого двигателя внутреннего сгорания, может производить большую мощность.Возвратно-поступательные двигатели зависят от движения поршня вверх и вниз, которое затем должно быть преобразовано во вращательное движение с помощью механизма коленчатого вала, тогда как газовая турбина передает мощность вращающегося вала напрямую. Хотя концептуально газотурбинный двигатель представляет собой простое устройство, компоненты эффективного агрегата должны быть тщательно спроектированы и изготовлены из дорогостоящих материалов из-за высоких температур и напряжений, возникающих во время работы. Таким образом, установки газотурбинных двигателей обычно ограничиваются крупными установками, где они становятся рентабельными.
Циклы газотурбинного двигателя
Большинство газовых турбин работают в открытом цикле, в котором воздух забирается из атмосферы, сжимается в центробежном или осевом компрессоре, а затем подается в камеру сгорания. Здесь топливо добавляется и сжигается при практически постоянном давлении с частью воздуха. Дополнительный сжатый воздух, который обходится вокруг секции горения и затем смешивается с очень горячими газами сгорания, необходим для поддержания температуры на выходе из камеры сгорания (фактически, на входе в турбину) на достаточно низком уровне, чтобы турбина могла работать непрерывно.Если установка должна производить мощность на валу, продукты сгорания (в основном воздух) расширяются в турбине до атмосферного давления. Большая часть мощности турбины требуется для работы компрессора; только остальная часть доступна для обеспечения работы вала генератора, насоса или другого устройства. В реактивном двигателе турбина предназначена для обеспечения мощности, достаточной для привода компрессора и вспомогательных устройств. Затем поток газа выходит из турбины с промежуточным давлением (выше местного атмосферного давления) и проходит через сопло для создания тяги.
В первую очередь рассматривается идеализированный газотурбинный двигатель, работающий без потерь по этому простому циклу Брайтона. Если, например, воздух поступает в компрессор при 15 ° C и атмосферном давлении и сжимается до одного мегапаскаль, он затем поглощает тепло от топлива при постоянном давлении до тех пор, пока температура не достигнет 1100 ° C, прежде чем расширится через турбину обратно до атмосферного. давление. Этот идеализированный блок потребует выходной мощности турбины 1,68 киловатт на каждый киловатт полезной мощности с 0.68 киловатт потребляется для работы компрессора. Тепловой КПД установки (чистая произведенная работа, разделенная на энергию, добавленную через топливо) составит 48 процентов.
Получите подписку Britannica Premium и получите доступ к эксклюзивному контенту. Подпишитесь сейчасФактическая производительность простого открытого цикла
Если для агрегата, работающего в пределах одного и того же давления и температуры, компрессор и турбина имеют КПД только на 80 процентов (, т.е. , работа идеального компрессора равна 0.В 8 раз больше фактической работы, в то время как фактическая мощность турбины в 0,8 раза больше идеальной мощности), ситуация кардинально меняется, даже если все остальные компоненты остаются идеальными. На каждый киловатт производимой полезной мощности турбина теперь должна производить 2,71 киловатт, а работа компрессора становится 1,71 киловатт. Тепловой КПД снижается до 25,9 процента. Это демонстрирует важность высокоэффективных компрессоров и турбин. Исторически сложность разработки эффективных компрессоров, даже более эффективных, чем эффективных турбин, задерживала разработку газотурбинного двигателя.Современные агрегаты могут иметь КПД компрессора 86–88 процентов и КПД турбины 88–90 процентов при проектных условиях.
КПД и выходную мощность можно увеличить за счет повышения температуры на входе в турбину. Однако все материалы теряют прочность при очень высоких температурах, а поскольку лопатки турбины движутся с высокой скоростью и подвергаются серьезным центробежным напряжениям, температура на входе в турбину выше 1100 ° C требует специального охлаждения лопаток. Можно показать, что для каждой максимальной температуры на входе в турбину существует также оптимальное соотношение давлений.Современные авиационные газовые турбины с охлаждением лопаток работают при температурах на входе в турбину выше 1370 ° C и соотношении давлений около 30: 1.
Промежуточное охлаждение, повторный нагрев и регенерация
В авиационных газотурбинных двигателях необходимо обращать внимание на вес и диаметр. Это не позволяет добавлять дополнительное оборудование для повышения производительности. Соответственно, двигатели коммерческих самолетов работают по простому циклу Брайтона, идеализированному выше. Эти ограничения не применяются к стационарным газовым турбинам, в которые могут быть добавлены компоненты для повышения эффективности.Усовершенствования могут включать (1) уменьшение работы сжатия за счет промежуточного охлаждения, (2) увеличение мощности турбины за счет повторного нагрева после частичного расширения или (3) уменьшение расхода топлива за счет регенерации.
Первое усовершенствование будет заключаться в сжатии воздуха почти постоянной температуры. Хотя это не может быть достигнуто на практике, это можно приблизить с помощью промежуточного охлаждения ( т. Е. путем сжатия воздуха в два или более этапов и его водяного охлаждения между этапами до его начальной температуры).Охлаждение уменьшает объем обрабатываемого воздуха и, соответственно, необходимую работу по сжатию.
Второе усовершенствование включает повторный нагрев воздуха после частичного расширения через турбину высокого давления во втором наборе камер сгорания перед подачей его в турбину низкого давления для окончательного расширения. Этот процесс аналогичен повторному нагреву, используемому в паровой турбине.
Оба подхода требуют значительного дополнительного оборудования и используются реже, чем третье улучшение.Здесь горячие выхлопные газы турбины проходят через теплообменник или регенератор для повышения температуры воздуха, выходящего из компрессора перед сгоранием. Это уменьшает количество топлива, необходимое для достижения желаемой температуры на входе в турбину. Однако повышение эффективности связано со значительным увеличением начальной стоимости и будет экономичным только для агрегатов, которые работают почти непрерывно.
Газотурбинный двигатель | Британника
Полная статья
Газотурбинный двигатель , любой двигатель внутреннего сгорания, использующий газ в качестве рабочего тела, используемого для вращения турбины.Термин также обычно используется для описания полного двигателя внутреннего сгорания, состоящего, по меньшей мере, из компрессора, камеры сгорания и турбины.
Общие характеристики
Полезная работа или тяга может быть получена от газотурбинного двигателя. Он может приводить в действие генератор, насос или воздушный винт или, в случае чисто реактивного авиационного двигателя, развивать тягу, ускоряя поток выхлопных газов турбины через сопло. Такой двигатель, который при той же мощности намного меньше и легче поршневого двигателя внутреннего сгорания, может производить большую мощность.Возвратно-поступательные двигатели зависят от движения поршня вверх и вниз, которое затем должно быть преобразовано во вращательное движение с помощью механизма коленчатого вала, тогда как газовая турбина передает мощность вращающегося вала напрямую. Хотя концептуально газотурбинный двигатель представляет собой простое устройство, компоненты эффективного агрегата должны быть тщательно спроектированы и изготовлены из дорогостоящих материалов из-за высоких температур и напряжений, возникающих во время работы. Таким образом, установки газотурбинных двигателей обычно ограничиваются крупными установками, где они становятся рентабельными.
Циклы газотурбинного двигателя
Большинство газовых турбин работают в открытом цикле, в котором воздух забирается из атмосферы, сжимается в центробежном или осевом компрессоре, а затем подается в камеру сгорания. Здесь топливо добавляется и сжигается при практически постоянном давлении с частью воздуха. Дополнительный сжатый воздух, который обходится вокруг секции горения и затем смешивается с очень горячими газами сгорания, необходим для поддержания температуры на выходе из камеры сгорания (фактически, на входе в турбину) на достаточно низком уровне, чтобы турбина могла работать непрерывно.Если установка должна производить мощность на валу, продукты сгорания (в основном воздух) расширяются в турбине до атмосферного давления. Большая часть мощности турбины требуется для работы компрессора; только остальная часть доступна для обеспечения работы вала генератора, насоса или другого устройства. В реактивном двигателе турбина предназначена для обеспечения мощности, достаточной для привода компрессора и вспомогательных устройств. Затем поток газа выходит из турбины с промежуточным давлением (выше местного атмосферного давления) и проходит через сопло для создания тяги.
В первую очередь рассматривается идеализированный газотурбинный двигатель, работающий без потерь по этому простому циклу Брайтона. Если, например, воздух поступает в компрессор при 15 ° C и атмосферном давлении и сжимается до одного мегапаскаль, он затем поглощает тепло от топлива при постоянном давлении до тех пор, пока температура не достигнет 1100 ° C, прежде чем расширится через турбину обратно до атмосферного. давление. Этот идеализированный блок потребует выходной мощности турбины 1,68 киловатт на каждый киловатт полезной мощности с 0.68 киловатт потребляется для работы компрессора. Тепловой КПД установки (чистая произведенная работа, разделенная на энергию, добавленную через топливо) составит 48 процентов.
Получите подписку Britannica Premium и получите доступ к эксклюзивному контенту. Подпишитесь сейчасФактическая производительность простого открытого цикла
Если для агрегата, работающего в пределах одного и того же давления и температуры, компрессор и турбина имеют КПД только на 80 процентов (, т.е. , работа идеального компрессора равна 0.В 8 раз больше фактической работы, в то время как фактическая мощность турбины в 0,8 раза больше идеальной мощности), ситуация кардинально меняется, даже если все остальные компоненты остаются идеальными. На каждый киловатт производимой полезной мощности турбина теперь должна производить 2,71 киловатт, а работа компрессора становится 1,71 киловатт. Тепловой КПД снижается до 25,9 процента. Это демонстрирует важность высокоэффективных компрессоров и турбин. Исторически сложность разработки эффективных компрессоров, даже более эффективных, чем эффективных турбин, задерживала разработку газотурбинного двигателя.Современные агрегаты могут иметь КПД компрессора 86–88 процентов и КПД турбины 88–90 процентов при проектных условиях.
КПД и выходную мощность можно увеличить за счет повышения температуры на входе в турбину. Однако все материалы теряют прочность при очень высоких температурах, а поскольку лопатки турбины движутся с высокой скоростью и подвергаются серьезным центробежным напряжениям, температура на входе в турбину выше 1100 ° C требует специального охлаждения лопаток. Можно показать, что для каждой максимальной температуры на входе в турбину существует также оптимальное соотношение давлений.Современные авиационные газовые турбины с охлаждением лопаток работают при температурах на входе в турбину выше 1370 ° C и соотношении давлений около 30: 1.
Промежуточное охлаждение, повторный нагрев и регенерация
В авиационных газотурбинных двигателях необходимо обращать внимание на вес и диаметр. Это не позволяет добавлять дополнительное оборудование для повышения производительности. Соответственно, двигатели коммерческих самолетов работают по простому циклу Брайтона, идеализированному выше. Эти ограничения не применяются к стационарным газовым турбинам, в которые могут быть добавлены компоненты для повышения эффективности.Усовершенствования могут включать (1) уменьшение работы сжатия за счет промежуточного охлаждения, (2) увеличение мощности турбины за счет повторного нагрева после частичного расширения или (3) уменьшение расхода топлива за счет регенерации.
Первое усовершенствование будет заключаться в сжатии воздуха почти постоянной температуры. Хотя это не может быть достигнуто на практике, это можно приблизить с помощью промежуточного охлаждения ( т. Е. путем сжатия воздуха в два или более этапов и его водяного охлаждения между этапами до его начальной температуры).Охлаждение уменьшает объем обрабатываемого воздуха и, соответственно, необходимую работу по сжатию.
Второе усовершенствование включает повторный нагрев воздуха после частичного расширения через турбину высокого давления во втором наборе камер сгорания перед подачей его в турбину низкого давления для окончательного расширения. Этот процесс аналогичен повторному нагреву, используемому в паровой турбине.
Оба подхода требуют значительного дополнительного оборудования и используются реже, чем третье улучшение.Здесь горячие выхлопные газы турбины проходят через теплообменник или регенератор для повышения температуры воздуха, выходящего из компрессора перед сгоранием. Это уменьшает количество топлива, необходимое для достижения желаемой температуры на входе в турбину. Однако повышение эффективности связано со значительным увеличением начальной стоимости и будет экономичным только для агрегатов, которые работают почти непрерывно.
Газовая турбина / Дизельные двигатели / Газовые двигатели | Ресурсы, энергия и окружающая среда | Продукция | IHI Corporation
IHI предлагает широкий спектр продукции для выработки электроэнергии, включая газовые турбины, дизельные двигатели и газовые двигатели с энергосистемами простого цикла, когенерации и комбинированного цикла.Мы также предоставляем удаленный мониторинг, техническое обслуживание двигателя и другие услуги на протяжении всего жизненного цикла продукта. Мы добиваемся сокращения выбросов NOx и CO2 за счет использования газовых турбин с высоким КПД и низким уровнем выбросов. Поставляем газовые турбины для быстроходных судов и других морских судов. Мы также поставляем полный спектр дизельных двигателей, от больших двигателей, способных работать на средней и низкой скорости, до моделей малого и среднего размера, обеспечивающих низкие, средние и высокие скорости. В наш разнообразный модельный ряд входят дизельные двигатели для наземных генераторов.
Газотурбинные системы выработки энергии
Газотурбинная электростанция «ЛМ6000»
Это электростанции класса 100 МВт, которые сочетают в себе две газовые турбины LM6000, два парогенератора с рекуперацией тепла и одну паровую турбину, чтобы производить самую эффективную в мире выработку электроэнергии, а также обеспечивать наилучшие экологические характеристики и надежность.
Газотурбинная электростанция «ЛМ2500»
Это электростанции класса 20–30 МВт, в которых используется высокоэффективная и очень надежная газовая турбина LM2500, созданная на основе легкого и компактного авиадвигателя.
Системы когенерации
Газотурбинная когенерационная установка «ИМ270»
Это типичные энергосберегающие системы, которые вырабатывают 2 МВт мощности и 6 тонн пара в час за счет сочетания нашей оригинальной спроектированной и разработанной газовой турбины IM270 с высоким КПД и низким уровнем выбросов NOx и парогенератора-утилизатора.
Когенерационная система «IM400 IHI-FLECS»
Это системы когенерации класса 4–6 МВт и оригинальные системы когенерации IHI, которые могут изменять выработку как электроэнергии, так и тепла (пара) в соответствии с потребностями.Если есть избыток пара, он может быть преобразован в выработку электроэнергии для рекуперации энергии.
Двигатели среднего / большого размера
Двухтопливный двигатель «DU-WinGD 6X72DF»
Это двухтопливный двигатель, использующий технологии сгорания с предварительным смешиванием и обедненной смесью, которые считались технически сложными для низкооборотного двухтактного двигателя.
Это большая особенность, позволяющая существенно снизить количество выбросов NOx двигателем.
Дизельный двигатель «DU-Win GD 9X82»
Двигатели X — это двигатели нового поколения, которые разработаны и спроектированы с высокой эксплуатационной гибкостью, чтобы адаптироваться к различным условиям работы двигателя и удовлетворять требованиям более низкого расхода топлива.Двигатели 9X82 устанавливаются на контейнеровозы компании NYK 14 000 TEU в качестве главного двигателя. Эти двигатели 9X82 оснащены «двойной рейтинговой системой», которая включает функции оптимизации двух диапазонов мощности для работы с высокой и низкой нагрузкой. Эта «Двойная рейтинговая система» — лучшая в мире технология, которая позволяет судам значительно снизить потребление топлива и сократить выбросы CO2 для обоих диапазонов, что значительно способствует экономии эксплуатационной энергии при эксплуатации судна.
DU-S.E.M.T. Дизельный двигатель Pielstick
Четырехтактный среднеоборотный двигатель, используемый в качестве основного двигателя для больших паромов и патрульных катеров береговой охраны, а также в качестве генератора для наземных электростанций.
Дизельный двигатель NIIGATA «28AHX»
Дизельный двигатель — это «экологичный» среднеоборотный дизельный двигатель (от 2070 до 6660 кВт) следующего поколения, который, очевидно, соответствует нормам IMO Tier II NOx, а также ориентирован на будущее судовых двигателей.
Используемый на земле для генераторов (от 2000 до 6300 кВт), дизельный двигатель обеспечивает высокий КПД и низкий расход топлива мирового класса, используя как DO, так и HFO.
Двухтопливный двигатель NIIGATA «28AHX-DF»
28AHX-DF — это экологически чистый двигатель, соответствующий нормам IMO Tier III NOx в газовом режиме.В нем используется сжигание чистого газа, что позволяет соблюдать новые правила без селективного каталитического восстановления (SCR).
Системы выработки энергии на газовых двигателях
НИИГАТА Газовый двигатель «28АГС»
Газовый двигатель вносит значительный вклад в сокращение выбросов CO2 за счет высокоэффективной работы с использованием природного и городского газа, а также низкокалорийных газов, таких как те, которые образуются в плавильных печах с газификацией.
2000–6000 кВтэ, серия AGS с зажиганием от свечи зажигания и серия AG с микропилотным зажиганием поставляются как в пределах Японии, так и за границу в качестве стационарных электрогенераторов.
Силовые установки
Азимутальное подруливающее устройство NIIGATA «Z-PELLER®»
Z-PELLER® — самая популярная силовая установка на мировом рынке буксиров.Заказчики высоко оценивают этот силовой агрегат за его высокое качество и долговечность.
Наша линейка Z-PELLER® предлагает непрерывную мощность от 735 кВт (1000 л.с.) до 3310 кВт (4500 л.с.), что позволяет нам реагировать на различные потребности клиентов.
Оборудование для впрыска топлива
Оборудование для впрыска топлива
NICO производит и поставляет так называемое оборудование для впрыска топлива, клапан впрыска топлива и насос впрыска топлива для 4-тактного двигателя Deisel для производителей двигателей, таких как отечественные производители двигателей, европейцы, корейцы и китайцы, а также компания Niigatra Power Systems, которая занимается производством двигателей. Материнская компания NICO.NICO также разрабатывает FIE с электрическим управлением (то есть CRS: Common Rail System), а также обычные механические FIE.
Ссылки
Запросы на продукцию
Прочие товары
Продукты
границ | Мониторинг вибрации газотурбинных двигателей: подходы к машинному обучению и их проблемы
Введение
Измерения вибрации обычно считаются надежным индикатором общего состояния машины (глобальный мониторинг).Общий принцип, лежащий в основе использования данных о вибрации, заключается в том, что, когда начинают развиваться неисправности, динамика системы изменяется, в результате чего модели вибрации отличаются от тех, которые наблюдаются в исправном состоянии контролируемой системы. В последние годы производители газотурбинных двигателей обратили свое внимание на повышение надежности и доступности своего парка, используя подходы к мониторингу состояния на основе данных и вибрации (King et al., 2009). Эти методы, как правило, предпочтительнее для стратегий онлайн-мониторинга по сравнению с подходом к моделированию, основанным на физике, при котором разрабатывается общая теоретическая модель и при ее разработке используются несколько допущений.В случае подходов к мониторингу состояния на основе данных модель, основанная на данных двигателя, может быть построена таким образом, чтобы можно было зафиксировать неотъемлемые линейные и нелинейные зависимости, в зависимости от метода, которые характерны для отслеживаемой системы. По этой причине производители двигателей видят необходимость внедрения таких подходов во время промежуточных испытаний, когда необходимо выявлять возможные дефекты на ранней стадии, до того, как произойдет полный отказ компонентов.
Из-за сложных процессов, происходящих в газотурбинном двигателе, и поскольку режимы отказа таких систем редко наблюдаются на практике, парадигма обнаружения новизны обычно применяется для разработки модели, управляемой данными (Тарасенко и др., 2009), поскольку в этом случае для обучения нужны только данные, поступающие из работоспособного состояния системы. С другой стороны, традиционные подходы мультиклассовой классификации не так просто реализовать, поскольку невозможно получить данные и / или понимание (метки) для всех классов отказов. Основная концепция метода обнаружения новизны описана Pimentel et al. (2014): обучающие данные из одного класса используются для построения управляемой данными модели, описывающей распределение, к которому они принадлежат.Данные, не принадлежащие к этому классу, являются новыми / выбросами. В контексте газотурбинного двигателя разработана модель «нормального» состояния двигателя (класс 𝒩), поскольку данные доступны только из этого класса. Затем эта модель используется для определения того, классифицируются ли новые невидимые точки данных как нормальные или «новые» (класс 𝒜), путем сравнения их с распределением, полученным из данных класса 𝒩. Такая модель должна быть достаточно чувствительной, чтобы на очень ранней стадии идентифицировать потенциальные предвестники локальных неисправностей компонентов, которые могут привести к полному отказу двигателя.Затраты на стратегию непрерывного обслуживания (т.е. вывод оборудования из эксплуатации после отказа для замены) исключительно высоки, но, что наиболее важно, критически важны требования безопасности, и, следовательно, в таких системах требуются надежные механизмы сигнализации.
Подходы к обнаружению новинок используют машинное обучение и статистику. В этом исследовании мы будем использовать непараметрический подход, специфичный для отслеживаемого двигателя и основанный исключительно на данных для разработки модели. Область обнаружения новинок составляет значительную часть дисциплины машинного обучения, поэтому здесь будет упомянуто лишь несколько примеров литературы, посвященной применению мониторинга состояния двигателя с использованием машинного обучения.Некоторые из самых ранних работ в этой области стали возможными благодаря сотрудничеству Оксфордского университета и Rolls Royce (Hayton et al., 2000). Авторы в этой статье использовали данные вибраций для обучения одноклассной опорной векторной машины (OCSVM). Так называемые отслеживаемые приказы (определяемые как амплитуды вибрации, сосредоточенные на основе частоты вращения вала двигателя и ее гармоник) использовались в качестве обучающих функций для OCSVM. OCSVM также был реализован для обнаружения приближающейся нестабильности горения в промышленных системах сгорания с использованием измерений давления сгорания и высокоскоростных изображений сгорания в качестве входных обучающих данных (Clifton et al., 2007). Этот метод также был расширен в Clifton et al. (2014) для калибровки оценок новизны OCSVM в условных вероятностях.
Выбор функции ядра, используемой в OCSVM, значительно влияет на точность классификации. Поскольку ядро определяет сходство между двумя точками, его выбор в основном зависит от данных. Однако ширина ядра является более важным фактором, чем выбор конкретной функции ядра, поскольку ее можно выбрать таким образом, чтобы гарантировать наилучшее описание данных (Scholkopf and Smola, 2001).Хотя методы ядра считаются хорошим способом внедрения специфических знаний в такой алгоритм, как OCSVM, выбор функции ядра и настройка ее параметров не так просты. В этом исследовании авторы следуют относительно простому подходу к определению как параметра функции ядра, так и параметра штрафа за оптимизацию для OCSVM. Параметр функции ядра, который был изменен, представляет собой ширину ядра радиальной базисной функции (RBF) γ вместе с параметром штрафа за оптимизацию ν.В общем, γ управляет сложностью описания обучающих примеров, а ν определяет верхнюю границу доли точек обучающих данных, которые находятся за пределами границы, определенной для данных класса 𝒩. Используя эти два параметра, можно найти компромисс между хорошей возможностью обобщения модели и хорошим описанием данных (обучающий набор данных) для получения точных и надежных прогнозов.
Схема обнаружения новизны, которая представлена в следующих разделах, была разработана для газотурбинного двигателя, который работает на ряде альтернативных видов топлива с различным соотношением воздуха к топливу.Этот двигатель используется для изучения влияния таких рабочих параметров на его характеристики (например, выбросы выхлопных газов), и, таким образом, важно обеспечить раннее обнаружение надвигающихся неисправностей, которые могут иметь место во время этих испытаний. Поскольку мы применяем обнаружение новизны в глобальной системе, для мониторинга должен использоваться весь частотный спектр вибрации, а не конкретные полосы частот, соответствующие компонентам двигателя. Как будет показано ниже, можно ожидать больших амплитуд колебаний в любой области спектра.
Экспериментальная установка и описание данных
Экспериментальные данные, использованные в этой работе, были взяты из более крупного проекта, целью которого было охарактеризовать различные альтернативные виды топлива с точки зрения характеристик двигателя, например, расхода топлива и выбросов выхлопных газов. Альтернативные виды топлива, состоящие из обычного керосинового топлива Jet-A1 и биотоплива, показали многообещающие результаты с точки зрения сокращения выбросов парниковых газов и других показателей эффективности. В нескольких исследовательских программах достаточно подробно изучались альтернативные виды топлива для авиации, как описано в Blakey et al.(2011). На установке, которая использовалась для тестирования различных альтернативных видов топлива при различных соотношениях воздух-топливо в двигателе, находится Honeywell GTCP85-129, который является вспомогательной силовой установкой типа турбовального газотурбинного двигателя. Таким образом, принцип работы этого двигателя следует типичному циклу Брайтона. Как показано на принципиальной схеме двигателя на рис. 1, двигатель втягивает окружающий воздух из впускного отверстия (1 атм) через центробежный компрессор C1, где он повышает свое давление, ускоряя жидкость и пропуская ее через расширяющуюся секцию.Давление текучей среды дополнительно повышается во втором центробежном компрессоре C2 перед смешиванием с топливом в камере сгорания (CC) и воспламенением для добавления энергии в систему (в виде тепла) при постоянном давлении. Газы с высокой температурой и давлением распространяются через турбину, которая приводит в действие два компрессора, генератор G мощностью 32 кВт, который обеспечивает электрическую мощность самолета, и вспомогательное оборудование двигателя (EA), например топливные насосы, через редуктор скорости.
Рисунок 1 .Принципиальная схема газотурбинного двигателя экспериментальной установки, изображающая основные особенности.
Выпускной клапан (BV) двигателя позволяет отводить высокотемпературный сжатый воздух (~ 232 ° C при 338 кПа абсолютного давления) в кабину самолета и обеспечивать пневматическую мощность для запуска основных двигателей. Это позволяет испытывать двигатель в различных режимах работы, поскольку массовый расход воздуха к топливу, который поступает в CC, может изменяться в зависимости от положения BV. Когда BV открывается, частота вращения турбины будет снижаться, если не будет добавлено топливо для компенсации потерянной работы.Потери энергии возникают из-за уменьшения выполняемой работы w c 2 рабочей жидкости двигателя, когда она проходит через вторую ступень сжатия. Количество потерянной работы пропорционально массе отводимого воздуха м отвод и может быть выражено как w c 2 = м отвод c p dT , с c p , представляющая теплоемкость рабочей жидкости, и dT — перепад температур на второй ступени сжатия.Поскольку частота вращения вала должна оставаться постоянной на уровне 4356 ± 10,5 рад / с, регулятор расхода топлива достигает этого, регулируя давление в топливной магистрали, нагнетая поток топлива различной массы в CC.
Увеличение массового расхода топлива, поступающего в CC для поддержания постоянной скорости вращения вала без последующего увеличения массового расхода воздуха, приводит к повышению температуры выхлопных газов, как показано в таблице 1. Это можно объяснить тем, что при Это недостаток кислорода, необходимый для полного сгорания поступающего распыленного топлива, больше капель топлива переносятся дальше по потоку от CC, пока они в конечном итоге не сгорят.Это постепенное горение топлива вдоль участка сгорания заставляет связанное с ним пламя распространяться дальше в сторону зоны разбавления. Следовательно, происходит неадекватное охлаждение газового потока, что приводит к более высокому выходу из камеры сгорания и, в свою очередь, к температурам выхлопных газов. Это также означает, что существует верхний и нижний предел температуры выхлопных газов, который контролируется и регулируется электронным регулятором температуры.
Таблица 1 . Усредненные параметры работы двигателя для трех режимов работы на топливе Джет-А1.
Рассмотрены три режима работы при изменении BV на три позиции. Эти режимы типичны для вспомогательного энергоблока и соответствуют конкретной нагрузке турбины и соотношению воздух-топливо. Таким образом, нагрузка турбины зависит исключительно от отводящей нагрузки, в то время как нагрузка на вал (объем работы, необходимый для приведения в действие генератора и ЭП) остается постоянной во всех трех рабочих режимах. При использовании обычного керосинового реактивного топлива Джет-А1 средние значения основных параметров двигателя изменяются на трех режимах работы, как показано в таблице 1.Что касается режима 1, двигатель BV полностью закрыт; нет дополнительной нагрузки на турбину, в то время как режим 2 является настройкой средней мощности и используется, когда главные двигатели выключены и есть требование для работы гидравлических систем самолета. В режиме 3 двигатель BV полностью открыт, что соответствует максимальному уровню нагрузки на турбину и температуре выхлопных газов. Этот режим работы выбирается, когда для запуска главных двигателей самолета требуется пневматическая энергия, за счет подачи воздуха под высоким давлением, достаточного для вращения лопаток турбины, пока не будет достигнута автономная работа на мощности.
Пьезоэлектрический акселерометр с чувствительностью 10 мВ / г был размещен на опорной конструкции двигателя с частотой дискретизации 2 кГц ( f s = 2 кГц). Продолжительность каждого теста составляла 110 с. В качестве топлива рассматривались смеси Jet-A1 и биотоплива для реактивных двигателей [гидрообработанные сложные эфиры и жирные кислоты (HEFA)]. Удельная плотность энергии HEFA составляет 44 МДж / кг, и, таким образом, он может выделять такое же количество энергии для данного количества топлива, что и Jet-A1. Массовые доли биотоплива, смешанного с Jet-A1 в этом исследовании, следующие: 0, 2, 10, 15, 25, 30, 50, 75, 85, 95 и 100%.Для сравнения также рассматривались дополнительные смеси топлив: 50% сжиженный природный газ (СПГ) + 50% Jet-A1, 100% СПГ и 11% толуол + 89% растворитель Banner.
На рисунках 2 и 3 показаны примеры нормированных ускорений во временной и частотной областях соответственно. Нормализация была выполнена путем деления каждой амплитуды ускорения во временной и частотной областях на соответствующее максимальное значение, то есть нормализованную единицу, так что все амплитуды, соответствующие различным наборам данных, изменяются в одном диапазоне [0, 1].Во временной области показано, что существуют определенные условия двигателя, например, 85% Jet-A1 + 15% HEFA, в которых вибрационные характеристики двигателя, работающего в установившемся режиме, демонстрируют сильные нестационарные тенденции. В то время как для таких условий, как 50% Jet-A1 + 50% HEFA, вибрационные характеристики содержат периодические характеристики, что более четко видно на графиках в частотной области. Обратите внимание, что фактическое зарегистрированное время разгона для каждого состояния двигателя составляло 110 с, но для ясности на графиках показаны только 2 с.На Рисунке 3 показано, что при условии 85% Jet-A1 + 15% HEFA двигатель испытывает самый высокий общий уровень амплитуды во всем спектре в режимах 1 и 3. В то время как в режиме 2 двигатель работает при условиях 50% Jet-A1 + 50% HEFA демонстрирует самые высокие уровни вибрации во всем частотном спектре. Вышеизложенное демонстрирует, что изменение соотношения воздух-топливо изменяет статистические свойства наборов данных и, следовательно, частотную характеристику двигателя для различных топливных смесей.Для режимов 1 и 3 при условии 50% Jet-A1 + 50% HEFA присутствует сильная частотная составляющая на частоте 100 Гц. Сильная периодичность также присутствует для 100% СПГ с той же частотой. Следовательно, глядя на данные, мы можем выделить две основные группы, то есть те, которые содержат некоторые сильные периодические шаблоны, и те, которые не разделяют эту характеристику и в этом случае могут быть нестационарными, если соответствующая оценка их статистики во временной области подтверждает тот.
Рисунок 2 .Нормализованные временные графики вибрации двигателя для четырех различных топливных смесей при самом высоком тестируемом соотношении воздух-топливо.
Рисунок 3 . Графики нормализованной спектральной плотности мощности вибрации двигателя на пяти различных топливных смесях от самого низкого (режим 1) до самого высокого (режим 3) отношения воздух-топливо.
Трудно дать теоретическое объяснение физического контекста полученных вибрационных откликов без действительной основанной на физике модели, которая может предсказать вибрационный отклик двигателя как результат системы, в которой, помимо контекста динамики, сложная термохимическая, и имеют место другие физические процессы.В то же время природа проблемы моделирования / мониторинга, если подходить к ней с точки зрения физики, предполагает, что проверка модели будет серьезной проблемой. Выбор стратегии, основанной на данных, решает эту проблему, поскольку исследуемая система (работающий двигатель) рассматривается как черный ящик.
Методы анализа данных
Как упоминалось в разделе «ВВЕДЕНИЕ», в этом исследовании используется структура машинного обучения для мониторинга состояния двигателей с использованием данных о вибрации.Это означает, что для разработки методологии, которая может использоваться для обнаружения новых моделей двигателя на основе данных о вибрации, следует предпринять три последовательных шага после этапа сбора данных. Это, в частности, предварительная обработка данных, извлечение признаков и разработка модели обучения нормальному поведению двигателя (Тарассенко и др., 2009).
Предварительная обработка исходных данных о вибрации
Чтобы улучшить способность схемы обнаружения новизны определять, принадлежит ли точка данных к классу 𝒩 или 𝒜, при удалении абсолютных значений перед извлечением признаков был применен метод предварительной обработки.Как было показано в Clifton et al. (2006), этот шаг имеет большое значение для системы обнаружения новинок, поскольку позволяет лучше различать два разных класса. Масштабирование и нормализация также важны для большинства систем мониторинга состояния для устранения любых нежелательных экологических или эксплуатационных эффектов в анализируемых данных (He et al., 2009). В качестве метода предварительной обработки он рассматривается для повышения производительности одноклассных классификаторов (Juszczak et al., 2002): это очень хорошая практика при работе с алгоритмами машинного обучения для масштабирования анализируемых данных, поскольку большие диапазоны абсолютных значений функций будут иметь тенденцию преобладать над теми, которые имеют меньшие диапазоны значений (Hsu et al., 2016). В этом исследовании цель состоит в том, чтобы увеличить разницу в амплитуде вибрации для классов 𝒩 и 𝒜, и поэтому данные выбираются для масштабирования в различных испытанных условиях (а не во времени).
Сначала была построена матрица размеров D X = { x 1 ,…, x N } класса 𝒩.Индекс i = 1,…, N используется для обозначения различных условий, которые были включены в эту матрицу, то есть различных топливных смесей в трех режимах работы. Отдельная матрица Z = { z 1 ,…, z L }, содержащая данные для обоих классов (25% условий двигателя относятся к классу 𝒜), была также построен. Эта предварительная маркировка двух классов была выполнена путем сборки матрицы со всеми необработанными данными (до предварительной обработки) и уменьшения ее размеров до 2 с помощью анализа главных компонентов (PCA) для ее визуализации.Наблюдаемым точкам данных в двумерном пространстве PCA, которые были далеко от остальных данных, была присвоена метка класса 𝒜, а всем остальным — метка класса. Например, условию 85% Jet-A1 + 15% HEFA в Режиме 1 было присвоено прежнее обозначение.
Масштабированная версия матрицы X получилась следующим образом:
χi = xi − x¯ ∕ σx, (1), где вектор среднего определяется как x¯ = 1N∑Ni = 1 xi, а вектор дисперсии как σx = 1N∑Ni = 1 (xi − x¯) 2.Теперь масштабированная версия матрицы Z с индексом, обозначающим различные условия в матрице j = 1,…, L , содержащая данные из обоих классов, была получена следующим образом:
ζj = zj − x¯ ∕ σx. (2)Функция Извлечение предварительно обработанных необработанных данных о вибрации
Процесс извлечения признаков следует после этапа предварительной обработки данных. Для этого выбрано преобразование вейвлет-пакета (WPT). Все коэффициенты преобразований шкалы времени используются в качестве входных данных для алгоритма, который подходит для линейного или нелинейного уменьшения размерности, анализа основных компонентов ядра (KPCA).Эта процедура преобразования данных с использованием вейвлет-баз и проекции на набор осей меньшей размерности выгодна в случаях, когда нет информации о характеристических частотах контролируемой механической системы.
Вейвлет-коэффициенты
Целью этого этапа является получение набора отличительных признаков из предварительно обработанных необработанных данных о вибрации, чтобы затем обучающая модель могла легко разделить два класса условий двигателя.Ранее на рисунке 3 было показано, что существует определенная степень несходства между условиями двигателя в отношении их амплитуд в частотном спектре. Следовательно, чтобы получить информацию как во временной, так и в частотной области из данных, необходимо использовать частотно-временные методы. Вейвлет-преобразование позволяет включать информацию о времени для частотных компонентов. Следовательно, нестационарные события можно анализировать с помощью вейвлет-преобразования. Ожидается, что данные можно будет описать более эффективно, чем с помощью методов на основе Фурье, где любые нестационарные области стохастического сигнала не локализованы во времени.Выбор частотно-временного подхода, такого как вейвлет-преобразование, может быть лучшим вариантом для типа данных, обрабатываемых в этом исследовании. Простейший метод частотно-временного анализа, кратковременное преобразование Фурье, не будет оптимальным вариантом, поскольку размер окна фиксирован. Следовательно, существуют ограничения разрешения, определяемые принципом неопределенности, которые могут затруднять анализ потенциально нестационарных частей сигнала.
Вейвлет-преобразование решает проблему фиксированного размера окна за счет использования коротких окон для анализа высокочастотных компонентов (хорошая временная локализация) и больших окон для низкочастотных компонентов (хорошая частотная локализация).Пример вейвлет-преобразований, применяемых для приложений мониторинга состояния, был представлен в Fan and Zuo (2006). Существует несколько других частотных методов для приложений мониторинга, например, разложение по эмпирическим модам, как представлено в работе Antoniadou et al. (2015), которые могут предложить аналогичные преимущества вейвлет-преобразованию. Однако в данной работе выбран последний метод, потому что он очень прост в реализации и является проверенной концепцией, которая математически хорошо обоснована. Изначально вейвлет-преобразование было разработано для построения карты параметров расширения и трансляции.Расширение представляет собой масштабы с ≈ 1 / частота, а перенос τ относится к операции сдвига во времени. Рассмотрим состояние двигателя n χ n ( т ), при т = {0,…, 110} с. Соответствующие вейвлет-коэффициенты можно рассчитать следующим образом:
c (s, τ) = ∫χn (t) ψs, τ (t) dt. (3)Функция ψ s , τ представляет семейство высокочастотных функций кратковременной продолжительности и низкой частоты большой длительности функции прототипа функции ψ.Математически это определяется следующим образом:
ψs, τ (t) = 1 | s | ψt − τs, s> 0, (4), когда с <1, функция-прототип имеет меньшую продолжительность во времени, тогда как, когда с > 1, функция-прототип становится больше во времени, что соответствует высокочастотным и низкочастотным характеристикам, соответственно.
В Маллат (1999) дискретная версия уравнения. 3, а именно дискретное вейвлет-преобразование (DWT), было разработано как эффективная альтернатива непрерывному вейвлет-преобразованию.В частности, было доказано, что при использовании шкалы j и трансляции k , которые принимают только значения степеней двойки вместо промежуточных, все же может быть получено удовлетворительное частотно-временное разрешение. Это называется диадической сеткой вейвлет-коэффициентов, и функция, представленная в формуле. 4, становится набором ортогональных вейвлет-функций:
ψj, k (t) = 2j ∕ 2ψ2jt − k, (5), так что избыточность устраняется с использованием этого набора ортогональных вейвлет-баз, как более подробно описано в Farrar and Worden (2012).
На практике коэффициенты DWT получаются путем свертки χ n ( t ) с набором полуполосных (содержащих половину частотного содержания сигнала) фильтров нижних и верхних частот (Mallat, 1989). Это дает соответствующие поддиапазоны низких и высоких частот сигнала. Впоследствии подполоса нижних частот дополнительно разлагается по той же схеме после прореживания на 2 (половина выборок может быть исключена по критерию Найквиста), в то время как подполоса верхних частот не анализируется далее.Сигнал после первого уровня разложения будет иметь разрешение по частоте в два раза выше, чем исходный сигнал, поскольку он имеет половину числа точек. Эта итерационная процедура известна как двухканальное подполосное кодирование (Mallat, 1999) и обеспечивает эффективный способ вычисления вейвлет-коэффициентов с использованием сопряженных квадратурных зеркальных фильтров. Из-за плохого частотного разрешения DWT на высоких частотах для преобразования функций был выбран WPT. Разница между DWT и WPT заключается в том, что последний дополнительно разбивает поддиапазон более высоких частот.Принципиальная схема WPT до 2 уровней разложения показана на рисунке 4. Сначала сигнал χ n ( t ) свертывается с полуполосным фильтром нижних частот h ( k ) и фильтр верхних частот g ( k ). Это дает вектор вейвлет-коэффициентов c 1,1 , который фиксирует низкочастотное содержимое [0, f s /4] Гц и вектор вейвлет-коэффициентов c 2 , 1 , который захватывает высокочастотный контент ( f s /4, f s /2) Гц.После j уровней декомпозиции коэффициенты на выходе каждого фильтра собираются в матрицу c n , что соответствует состоянию n -го двигателя χ n . Обратите внимание, что каждый коэффициент имеет половину количества выборок, например χ n ( t ) на первом уровне разложения. В этом исследовании четыре уровня декомпозиции рассматривались как промежуточное значение.Вышеупомянутый процесс был повторен для остальных условий двигателя N -1, чтобы получить матрицу коэффициентов C = { c 1 ,…, c N }.
Рисунок 4 . Принципиальная схема преобразования вейвлет-пакетов до уровня разложения 2. На каждом уровне частотный спектр разбивается на 2 поддиапазона j .
Низкоразмерные элементы
Матрица вейвлет-коэффициентов C представляет собой матрицу размерности D , т.е.е., он имеет те же размеры, что и исходный набор данных. Следовательно, элементы меньшего размера необходимы для предотвращения переобучения, которое связано с элементами большего размера. В этом исследовании PCA изначально использовался для целей визуализации, например, для наблюдения возможных кластеров точек данных для матрицы X . Его нелинейный эквивалент, KPCA, используется для уменьшения размерности, чтобы можно было зафиксировать нелинейные отношения между элементами.
Анализ главных компонентов — это метод, который можно использовать для получения нового набора ортогональных осей, которые показывают наибольшую дисперсию данных.Следовательно, C было спроецировано на 2 ортогональные оси из своего исходного размера D . В PCA собственные значения λ k и собственные векторы u k ковариационной матрицы S C из C 9024, полученное путем решения следующего собственного значения
C 9024. проблема:, где k = 1,…, D . Собственный вектор u 1 , соответствующий наибольшему собственному значению λ 1 , является первым главным компонентом и так далее.Двумерное представление C , то есть Y (матрица N × k ), может быть вычислено посредством линейной проекции с использованием первых двух собственных векторов:
В Schölkopf et al. (1998), был введен KPCA. Этот метод является обобщенной версией PCA, поскольку скалярные произведения ковариационной матрицы S C заменяются функцией ядра. В KPCA отображение ϕ двух точек данных, например.g., вектор вейвлет-коэффициентов n, и m, c n и c m , соответственно, получается с помощью функции ядра RBF следующим образом :
k (cn, см) = ecn − cm22σKPCA2. (8)Используя приведенное выше отображение, стандартный PCA может быть выполнен в этом новом пространстве признаков ℱ, которое неявно соответствует нелинейному главному компоненту в исходном пространстве. Следовательно, скалярные произведения ковариационной матрицы заменяются ядром RBF следующим образом:
Sϕ = 1 ∕ N∑Ni ϕciTϕci.(9)Однако указанная выше матрица не может использоваться непосредственно для решения проблемы собственных значений, как в формуле. 6 из-за его большого размера. Следовательно, после некоторой алгебраической обработки собственные значения ℓ d и собственные векторы ud могут быть вычислены для матрицы ядра 𝒦 (размера N × N ) вместо ковариационной матрицы (размера ℱ × ℱ). Следовательно, в KPCA вместо этого мы должны найти решение следующей проблемы собственных значений:
, где d = {1,…, N }, поскольку ℱ> N , количество ненулевых собственных значений не может превышать количество рабочих условий двигателя N (Bishop, 2006).Используя собственные векторы матрицы ядра, можно получить новые проекции Y = y1,…, yN отображенных точек данных вейвлет-коэффициентов ϕ ( c i ) на нелинейной поверхности. размерности d , которая может варьироваться от 1 до N .
Модель обучения для обнаружения новинок
Поддержка векторных машин в качестве инструмента для классификации предлагает гибкость искусственной нейронной сети, преодолевая при этом ее недостатки.Использование функции ядра для расширения исходного входного пространства в пространство более высокой размерности для нахождения гиперплоскости линейного решения тесно связано с добавлением дополнительных слоев в искусственную нейронную сеть. Следовательно, алгоритм может быть адаптирован для лучшего соответствия характеристикам наших данных таким образом, чтобы повысить точность прогнозирования. Учитывая, что OCSVM формирует задачу квадратичной оптимизации, он гарантирует нахождение оптимального решения того места, где должна располагаться гиперплоскость линейного решения (Schölkopf et al., 2001; Шоу-Тейлор и Кристианини, 2004 г.). С другой стороны, можно получить локальный оптимум как решение для нахождения среднеквадратичной ошибки в искусственной нейронной сети с использованием алгоритма спуска градиента.
В качестве обучающих данных используется матрица, полученная из KPCA, т.е. 𝒴 . Принимая во внимание, что низкоразмерные представления данных тестирования (из матрицы Z ) получают с помощью того же преобразования признаков, выбора и т. Д.Методология OCSVM позволяет использовать функцию ядра RBF, которая отображает точки данных в 𝒴 таким же образом, как и в KPCA. Однако формулировка в наборе инструментов LIBSVM (Chang and Lin, 2011) немного отличается для ядра RBF. Учитывая две точки данных yn и ym, ядро RBF, реализованное в OCSVM, определяется следующим образом:
k (yn, ym) = e − γyn − ym2. (11)После того, как обучающие данные отображаются через в ядре RBF, источник в этом новом пространстве функций рассматривается как единственный член данных класса.Затем определяется гиперплоскость, так что отображаемые обучающие данные отделяются от исходной точки с максимальным запасом. Гиперплоскость в отображенном пространстве признаков расположена в точке ϕ (yi) −ρ = 0, где ρ — общая переменная поля. Чтобы отделить все отображенные точки данных от начала координат, необходимо решить следующую квадратичную программу:
minw, ρ, ξ 0.5wTw + 1υN∑iξi − ρ при условии: (wϕ (yi)) ≥ρ − ξi, i = 1,…, N, ξi≥0, (12), где w — вектор нормали к гиперплоскости, а ξ называются резервными переменными и используются для количественной оценки ошибки неправильной классификации каждой точки данных отдельно в соответствии с расстоянием от соответствующей границы.Значение ν, которое было упомянуто ранее, отвечает за штрафные санкции за неправильную классификацию и ограничено ν ∈ (0, 1]. Решение, которое определяет, принадлежит ли невидимая точка данных y ∗, т. Е. Из матрицы Z , к любому из два класса условий двигателя могут быть созданы с помощью следующей функции:
gy ∗ = sgnwϕy ∗ −ρ. (13)Для точки данных из класса 𝒜 gy ∗> 0, в противном случае gy ∗ ≤0. Обратите внимание, что из практических соображений проблема оптимизации в формуле. 12 решается введением множителей Лагранжа.Одна из основных причин этого заключается в том, что это позволяет записывать оптимизацию в терминах скалярных произведений. Это приводит к «уловке с ядром», которая позволяет обобщить проблему на нелинейный случай с помощью подходящих ядерных функций, таких как ядро RBF, которое используется в этом исследовании.
Результаты и обсуждение
В этой работе ядро RBF использовалось для отображения точек данных OCSVM в бесконечномерное пространство признаков, где может быть достигнуто линейное разделение двух классов.Применив OCSVM к нашей проблеме, мы получили широкий спектр формулировок функций ядра для использования. Ядро RBF — одно из самых популярных, поскольку оно подразумевает общие свойства гладкости для набора данных, предположение, которое обычно принимается во многих реальных приложениях, как более подробно обсуждается в Scholkopf and Smola (2001). Ядро RBF имеет два параметра, которые необходимо определить, чтобы адаптировать алгоритм OCSVM к характеристикам сигналов вибрации, ожидаемых в этом исследовании.Эти параметры называются шириной ядра γ и штрафом за оптимизацию ν. Наблюдая за изменением точности проверки α ν OCSVM на мелкой сетке значений γ и ν, можно было определить комбинацию этих двух значений, которая максимизирует α ν . Значения γ и ν были выбраны с шагом в 2, как это было предложено в практическом исследовании Hsu et al. (2016). Точность проверки рассчитывалась с использованием 10-кратной схемы перекрестной проверки для предотвращения переобучения данных.Как более подробно описано в Bishop (2006), схема перекрестной проверки используется, когда объем обучающих данных невелик. В таких случаях недостаточно данных, чтобы разделить их на наборы данных для обучения и проверки, чтобы исследовать надежность и точность модели. В нашем исследовании количество режимов работы двигателя относительно невелико по сравнению с количеством измерений в матрице характеристик. Таким образом, схема перекрестной проверки — возможное решение проблемы недостаточного количества обучающих данных.Более подробно, в этой схеме данные сначала делятся на 10 подмножеств одинакового размера. Каждое подмножество используется для последовательного тестирования эффективности классификации модели (которая была обучена на других девяти подмножествах). Каждая точка данных в наборе данных для обучения вибрации прогнозируется один раз. Следовательно, точность перекрестной проверки — это процент правильных классификаций в наборе данных виброобучения.
На рисунке 5 мы представляем два типичных результата изменения точности перекрестной проверки на сеточном пространстве параметров γ и ν.Эти результаты соответствуют точности перекрестной проверки, полученной при обучении OCSVM с помощью набора данных вейвлет-коэффициентов после «сжатия» с помощью PCA (правый график) и KPCA (левый график). Точность перекрестной проверки оценивалась с помощью ν. в диапазоне 0,001 и 0,8 с шагом 0,002, тогда как γ находится в диапазоне 2 −25 и 2 25 с шагом 2. Выбор этого сеточного пространства для ν был сделан на том факте, что этот параметр ограничен, так как представляет собой верхнюю границу доли обучающих данных, которые лежат не по ту сторону гиперплоскости [см. более подробную информацию в Schölkopf et al.(2001)]. В случае γ не было верхнего и нижнего пределов, поэтому был выбран относительно более широкий диапазон. В обоих случаях шаги были определены таким образом, чтобы вычислительные затраты оставались на разумном уровне. Как правило, для определения подходящих границ и размера шага при выборе размера сетки использовалась процедура проб и ошибок для данного набора данных о вибрации. Как видно из контурных графиков, поиск по сетке позволяет нам получить высокую точность проверки, когда выбрана соответствующая комбинация γ и ν.Для нашего набора данных эту комбинацию можно найти в основном при относительно низких значениях γ. По мере уменьшения значения γ попарные расстояния между точками обучающих данных становятся менее важными. Следовательно, граница принятия решения OCSVM становится более ограниченной, а его форма менее гибкой из-за того, что он будет придавать меньшее значение этим расстояниям. Обратите внимание, что примеры на рисунке 5 были получены с d = 100 для 𝒴 и D = 100 для Y (см. Низкоразмерные характеристики), с уровнем декомпозиции WPT j = 4 и (только для KPCA) ширина ядра γ KPCA = 1.Очевидно, что при использовании KPCA с ядром RBF максимальная точность перекрестной проверки составляет около 95%, в то время как при стандартном PCA точность классификации OCSVM относительно низка, то есть около 60%. Следовательно, есть преимущество использования KPCA перед стандартным PCA для конкретного набора данных, который используется в этом исследовании. Это ожидается, поскольку KPCA обнаруживает нелинейные отношения, существующие между элементами данных.
Рисунок 5 . Изменение точности перекрестной проверки с γ и ν для одноклассной опорной векторной машинной модели обучения с использованием функций анализа главных компонент ядра (слева) и стандартного анализа главных компонент.
Метод поиска по сетке для нахождения «подходящих» значений для γ и ν дает преимущество, когда другие параметры, например, ширина ядра KCPA σ KPCA , не могут быть легко определены. Можно продемонстрировать, что α ν может быть значительно увеличено по сравнению с фиксированным набором значений по умолчанию. Набор инструментов LIBSVM предлагает значения по умолчанию: ν = d −1 и γ = 0,5. На рисунке 6 точность проверки показана для различных значений ширины ядра KPCA σ KPCA и количества главных компонентов d для случаев, когда γ и ν были выбраны из поиска по сетке и когда им были заданы фиксированные значения по умолчанию. .Из этих двух графиков ясно, что параметры OCSVM γ и ν можно «настроить» так, чтобы точность проверки могла быть максимальной, независимо от выбора d и σ KPCA . Это наблюдение демонстрирует силу методов на основе ядра в целом, поскольку ширина ядра может иметь большое влияние на описание обучающих данных. В большинстве случаев выбор этого параметра необходим только для получения подходящей адаптации наших алгоритмов (Shawe-Taylor and Cristianini, 2004).Как можно видеть, выбирая каждый раз разные комбинации ν и γ (в соответствии с процедурой поиска по сетке), максимально достижимая точность проверки всегда близка к 100%. Это значительное улучшение по сравнению с соответствующей точностью, которую можно получить с использованием фиксированного набора значений. Более того, это демонстрирует, что «настроить» машину опорных векторов не так сложно, поскольку необходимо найти только два параметра, и это можно сделать с помощью процедуры поиска по сетке. Напротив, искусственная нейронная сеть требует, чтобы ее архитектура, скорость обучения градиентного спуска, среди других параметров, были указаны заранее, что значительно усложняет проблему «настройки» алгоритма.Тем не менее, самой сильной стороной машины опорных векторов является ее способность получить глобальное оптимальное решение для любого выбранного значения γ и ν, которое мы указали, так что ее обобщающая способность всегда максимальна.
Рисунок 6 . Изменение точности перекрестной проверки для различных значений d и σ KPCA для выбранных (слева) и фиксированных (справа) значений γ и ν.
Как было показано ранее на Рисунке 5, выбранное значение γ (из поиска по сетке) было очень маленьким.Это верно для каждого исследованного случая, например, для разных значений d . По этой причине можно сказать, что алгоритм лучше обобщается с менее сложной границей решения. Однако «настройка» OCSVM оказывается сложной задачей, поскольку точность прогнозирования (с использованием набора тестовых данных) ниже ожидаемой, то есть менее 50%. Большинство ошибок произошло для точек данных, ошибочно принятых как происходящие из класса 𝒜, тогда как в действительности они принадлежали классу. Вероятные причины неудовлетворительной работы OCSVM на наборе тестовых данных обсуждаются ниже:
• На этапе проверки OCSVM оцениваются только ошибки ошибочного отклонения данных из класса 𝒩.Можно предположить, что причина такой неправильной классификации может быть связана с ошибками в вычислении параметров γ и ν, оцененных с помощью сеточного поиска. Что касается выбора γ и ν, было несколько попыток решить эту проблему другими способами, чем поиск по сетке. Например, в Xiao et al. (2015) авторы представили методы выбора ширины ядра γ OCSVM с помощью того, что они называют «геометрическими» вычислениями.
• Из-за характера данных существует много различий между условиями двигателя, а также внутри каждого условия.Следовательно, сложно разработать модель с использованием данных класса 𝒩, если характеристики каждого условия в пределах одного класса различны. Выбор подходящих обучающих данных является важным фактором для применяемых подходов, основанных на данных. В этом случае следует выбрать представление данных в областях с соответствующим временным разрешением, а выбранные алгоритмы распознавания образов должны потенциально не зависеть от обучения, а работать в адаптивной структуре.
Заключение
В этом исследовании мы использовали схему обнаружения новинок для мониторинга состояния двигателей с использованием передовых методов машинного обучения, выбранных в соответствии с типом анализируемых данных.Это привело к лучшему описанию основных проблем, с которыми можно столкнуться при следовании стратегии на основе данных для мониторинга данных о вибрации двигателя. Схема обнаружения новизны была выбрана вместо классификационного подхода из-за отсутствия обучающих данных для различных состояний работы двигателя, с которыми обычно сталкиваются в реальных приложениях. Следующие шаги были рассмотрены как фундаментальные, оптимальные методы анализа данных. Модель нормальности, основанная на OCSVM, которая была обучена распознавать сценарии нормальных и новых условий двигателя, была разработана с использованием данных двигателя, работающего в условиях, в которых двигатель испытывал низкие амплитуды вибрации.Выбор этого метода машинного обучения для обнаружения новизны был обусловлен тем фактом, что проблема распознавания образов основана на создании ядра, которое предлагает универсальность, которая может поддерживать анализ более сложных данных. В этом случае, согласно анализу, представленному в исследовании, сильное влияние штрафного параметра ν и ширины ядра γ OCSVM может повлиять на точность проверки. Используя поиск по мелкой сетке для выбора параметров ν и γ, можно достичь точности проверки, близкой к 100%, как показано в результатах.Это значительное преимущество, когда нет методологии выбора других параметров, таких как количество основных компонентов, используемых в KPCA. Это также подчеркивает одну из сильных сторон основанных на ядре методов, а именно адаптируемость к заданному набору данных. В частности, было доказано, что ядро RBF очень эффективно описывает данные из механизма, выбирая соответствующее значение ширины ядра γ.
Ограничения подходов к обнаружению новизны в целом и того, что обсуждается, в частности, в этом исследовании, включают следующие моменты: обучающие данные вибрации, которые могут быть получены от двигателей, и ограничения конкретных рассмотренных алгоритмов.Для последнего обсуждался выбор ν и γ, и для расчета точности классификации с использованием выбранных ν и γ из поиска по сетке использовался независимый набор тестовых данных, который включал 25% условий из нового поведения двигателя. Несмотря на то, что результаты валидации были исключительно хорошими, и модель, похоже, не превышала данные, поскольку граница решения была гладкой, а количество опорных векторов относительно невелико, точность классификации с использованием набора тестовых данных была неудовлетворительной.Наибольшие ошибки возникали при неправильном прогнозировании точек данных на основе условий исправного двигателя как новизны. Несколько возможных причин того, почему это может произойти, были упомянуты в предыдущей части исследования.
Для улучшения схемы обнаружения новизны, представленной в этом исследовании, требуется дальнейшая работа по обучению OCSVM соответствующим образом. Например, вместо выбора ν и γ с использованием подхода поиска по сетке можно использовать методы, которые вычисляют эти параметры более принципиальным образом с использованием простой геометрии.Кроме того, функции вейвлет-преобразования, извлеченные из данных, могли привести к большому разбросу точек данных в пространстве признаков из-за того, что существует высокая изменчивость сигналов от каждого состояния двигателя. Один из способов решения этой проблемы — изучить новый набор потребностей в функциях, которые могут обеспечить лучшую кластеризацию точек данных из условий исправного двигателя, чтобы в пространстве функций можно было сформировать меньшую и более жесткую границу принятия решения. Другим предложением может быть разработка новых алгоритмов машинного обучения, которые не зависят от качества обучающих данных, а могут скорее адаптивно классифицировать различные состояния / условия работы исследуемого двигателя.
Авторские взносы
IM провел анализ машинного обучения и является первым автором исследования. ИА курировал работу (замысел и обзор). Б.К. способствовал проведению экспериментов и сбору проанализированных данных. Все авторы несут ответственность за содержание работы.
Заявление о конфликте интересов
Авторы заявляют, что исследование проводилось при отсутствии каких-либо коммерческих или финансовых отношений, которые могут быть истолкованы как потенциальный конфликт интересов.
Благодарности
Авторы хотели бы поблагодарить сотрудников Центра низкоуглеродного сжигания при Университете Шеффилда за проведение экспериментов с газотурбинным двигателем и за любезно предоставленные данные о вибрации двигателя, использованные в этом исследовании.
Финансирование
IM — аспирант, получивший стипендию от факультета машиностроения Университета Шеффилда. Все авторы выражают признательность за финансирование, полученное от гранта Совета по инженерным и физическим наукам (EPSRC) EP / N018427 / 1.
Список литературы
Антониаду, И., Мэнсон, Г., Сташевски, В. Дж., Барщ, Т., Ворден, К. (2015). Подход частотно-временного анализа для мониторинга состояния редуктора ветряной турбины в условиях изменяющейся нагрузки. мех. Syst. Сигнальный процесс. 64, 188–216. DOI: 10.1016 / j.ymssp.2015.03.003
CrossRef Полный текст | Google Scholar
Бишоп, К. (2006). Распознавание образов и машинное обучение (информатика и статистика) .Нью-Йорк: Спрингер.
Google Scholar
Блейки, С., Рай, Л., и Уилсон, В. (2011). Альтернативные виды топлива для авиационных газовых турбин: обзор. Proc. Комбас. Inst. 33, 2863–2885. DOI: 10.1016 / j.proci.2010.09.011
CrossRef Полный текст | Google Scholar
Чанг, К., Линь, К. (2011). LIBSVM: библиотека для поддержки векторных машин. ACM Trans. Intell. Syst. Technol. 2, 1–27. DOI: 10.1145 / 1961189.1961199
CrossRef Полный текст | Google Scholar
Клифтон, Д.А., Баннистер П. Р., Тарассенко Л. (2006). «Применение интуитивно понятной метрики новизны для мониторинга состояния реактивного двигателя», в Успехах в прикладном искусственном интеллекте , ред. М. Али и Р. Дапуаньи (Берлин, Гейдельберг: Springer), 1149–1158.
Google Scholar
Клифтон, Л., Клифтон, Д. А., Чжан, Ю., Уоткинсон, П., Тарассенко, Л., Инь, Х. (2014). Вероятностное обнаружение новизны с машинами опорных векторов. IEEE Trans. Надежный. 455–467. DOI: 10.1109 / TR.2014.2315911
CrossRef Полный текст | Google Scholar
Клифтон, Л., Инь, Х., Клифтон, Д., и Чжан, Ю. (2007). «Обнаружение новизны комбинированного вектора поддержки для данных о многоканальном сгорании», на Международной конференции IEEE по сетям, зондированию и управлению , Лондон.
Google Scholar
Фан, X., и Цзо, М. (2006). Обнаружение неисправностей коробки передач с использованием преобразования Гильберта и вейвлет-пакетов. мех. Syst. Сигнальный процесс. 20, 966–982.DOI: 10.1016 / j.ymssp.2005.08.032
CrossRef Полный текст | Google Scholar
Фаррар, К., Уорден, К. (2012). Структурный мониторинг работоспособности: перспектива машинного обучения . Чичестер: Джон Уайли и сыновья.
Google Scholar
Hayton, P., Schölkopf, B., Tarassenko, L., and Anuzis, P. (2000). «Обнаружение новинок опорных векторов применительно к спектрам вибрации реактивного двигателя», Ежегодная конференция по системам обработки нейронной информации (NIPS) , Денвер.
Google Scholar
Хе, К., Ян, Р., Конг, Ф., и Ду, Р. (2009). Мониторинг состояния машин с использованием представления главных компонентов. мех. Syst. Сигнальный процесс. 23, 446–466. DOI: 10.1016 / j.ymssp.2008.03.010
CrossRef Полный текст | Google Scholar
Сюй, К., Чанг, К., Линь, К. (2016). Практическое руководство по классификации опорных векторов . Тайбэй: Департамент компьютерных наук, Национальный университет Тайваня.
Google Scholar
Ющак, П., Tax, D., и Duin, R.P.W. (2002). «Масштабирование функций в описании векторных данных поддержки», в Proc. ASCI , Lochem.
Google Scholar
Кинг, С., Баннистер, П. Р., Клифтон, Д. А., и Тарассенко, Л. (2009). Вероятностный подход к мониторингу состояния авиакосмических двигателей. Proc. Inst. Мех. Англ. G J. Aerosp. Англ. 223, 533–541. DOI: 10.1243 / 09544100JAERO414
CrossRef Полный текст | Google Scholar
Маллат, С. (1989). Теория разложения сигнала с разным разрешением: вейвлет-представление. IEEE Trans. Pattern Anal. Мах. Intell. 11, 674–693. DOI: 10.1109 / 34.192463
CrossRef Полный текст | Google Scholar
Маллат, С. (1999). Вейвлет-тур по обработке сигналов (вейвлет-анализ и его приложения) . Нью-Йорк: Academic Press.
Google Scholar
Пиментел М., Клифтон Д., Клифтон Л. и Тарассенко Л. (2014). Обзор обнаружения новинок. Обработка сигналов 99, 215–249. DOI: 10.1016 / j.sigpro.2013.12.026
CrossRef Полный текст | Google Scholar
Шёлкопф, Б., Платт, Дж. К., Шоу-Тейлор, Дж., Смола, А. Дж., И Уильямсон, Р. К. (2001). Оценка поддержки многомерного распределения. Neural Comput. 10, 1443–1471. DOI: 10.1162 / 089976601750264965
PubMed Аннотация | CrossRef Полный текст | Google Scholar
Scholkopf, B., and Smola, A. (2001). Обучение с помощью ядер: поддержка векторных машин, регуляризация, оптимизация и не только .Кембридж: MIT Press.
Google Scholar
Шёлкопф Б., Смола А. и Мюллер К. (1998). Нелинейный компонентный анализ как проблема собственных значений ядра. Neural Comput. 10, 1299–1319. DOI: 10.1162 / 089976698300017467
CrossRef Полный текст | Google Scholar
Шоу-Тейлор, Дж., И Кристианини, Н. (2004). Методы ядра для анализа паттернов . Нью-Йорк: Издательство Кембриджского университета.
Google Scholar
Тарасенко, Л., Клифтон, Д. А., Баннистер, П. Р., Кинг, С., Кинг, Д. (2009). «Глава 35 — Обнаружение новизны» в энциклопедии структурного мониторинга здоровья , , ред. К. Боллер, Ф. Чанг и Ю. Фуджино (Барселона: John Wiley & Sons).
Google Scholar
Газовые турбины
Узнайте об истории и развитии газовой турбины.
г. газовая турбина стала важным, распространенным и надежным устройством в области энергетики, транспорта и других приложений.Газовая турбина — это двигатель внутреннего сгорания, она может сжигать самые разные топлива (что способствует его большой универсальности).
Использует газовых турбин:
Есть Есть много форм газовых турбин от 1 до 10+ метров в длину. Газовые турбины бывают самых разных форм, чтобы удовлетворить самые разные потребности в энергии от управления танками, реактивными самолетами и вертолетами до выработки электроэнергии и промышленное использование энергии.
В На этой странице мы обсуждаем газовые турбины , используемые для производства электроэнергии .
Позже вы можете узнать о многих других сложных формах газовой турбины перечислено в вики страница.
1.
Как это работает
2. Краткая история газовых турбин
3. Разработка газовых турбин в General Electric, Арне
Чердак
4. Системы управления газовой турбиной
1.Как это работает:
Газовая турбина используется для получения механической энергии из горючего топлива. В газе турбины, используемые для превращения промышленной / электрической энергии в механическую. поставляется в виде вращающегося вала (в отличие от находящегося под давлением тяга газотурбинного реактивного двигателя). Этот вал имеет огромное количество мощности и крутящего момента.
Использование газовая турбина с валом:
Вал может быть подключенным к другому оборудованию для выполнения различных видов работ, таких как: вращая ротор вертолета, запуская компрессор (который «давит» газ в конденсированную форму для использования в промышленных приложениях) или генерации электроэнергия.
Газовая турбина полезен в нашем современном мире, потому что он относительно компактен по размеру и делает много энергии. Газовые турбины используются в системах резервного питания. в Манхэттене, например, когда сеть выходит из строя из-за стихийного бедствия, газовые турбины включаются и могут вырабатывать электроэнергию для аварийных нужд.
Газовые турбины используются на нефтяных платформах для выработки энергии. Нефтяная платформа похожа на небольшой город, изолированный от воды, поэтому требует много энергии и не имеет много места.Газовые турбины также используются в масле. нефтеперерабатывающие заводы, чтобы производить мощность для крекинга процесс.
Обвязка мощность взрыва: Как работает устройство:
Оригинальный рисунок вверху: General Electric.
г. газовая турбина сжигает топливо в камере сгорания высокого давления, продукты из них принудительно попадают в турбину. Турбина специально спроектирована лопасти, прикрепленные к центральному валу, и как газы под высоким давлением протекает, вал вращается.Вал вращается с невероятной силой. Вал часто соединен с генератором, который вырабатывает электроэнергию. Иногда вал соединяется с компрессором. Компрессоры используются для сжатия газа или пара для множества промышленных и коммерческих целей.
Наручные часы видео ниже, чтобы узнать подробности о том, как работает газовая турбина:
2.Краткая история газовой турбины:
Газ турбины, разработанные в двух областях техники: паровая турбина, и двигатель внутреннего сгорания. Работа по обоим этим направлениям помогла привели к «Современной газовой турбине» периода после 1940-х годов.
1500 — 1870-е: Леонардо да Винчи, Джионванни Бранка, Джон Барбер и другие. упоминать или проектировать устройства, в которых для создания движения используется горячий газ или пар.Одновременно работают Сэмюэл Браун, Сади Карно, Сэмюэл Морел, Уильям. Барнетт и другие разрабатывают конструкцию двигателя внутреннего сгорания. Базовое понимание и теория горения и поведения газов в закрытых помещениях. пространства развита.
Паровая турбина by GE, нажмите на изображение, чтобы увидеть фотографию большего размера |
|
Реактивные двигатели использовать газотурбинную технологию. Это применение газовых турбин было разработано сначала сэром Фрэнком Уиттлом, Гансом фон Ойаном, доктором Францем Анслемом и другими с 1930-42 годов. Еще одна тема — разработка реактивных двигателей. обсуждается на отдельной странице.
В первая современная газовая турбина:
BCC Коричневый Бовери & Cie (Швейцария) ведет разработку газовых турбин для коммунального хозяйства. производство электроэнергии с 1930-х гг.Рауль Патерас де Пескара, Ханс von Ohain, Max Hahn разрабатывают собственные проекты за пределами BCC Brown Boveri. В 1936 году компания BCC Brown Boveri построила велокотел с наддувом для нефтеперерабатывающего завода. в Пенсильвании, который использовался в процессе каталитического крекинга для масло. В 1939 году установлена газовая турбина мощностью 4 МВт. в Невшателе, Швейцария. Теперь вы можете увидеть эту турбину на выставке Бирр, Швейцария. Работал с 1939 по 2002 год.
Первый коммерчески продана газовая турбина в Западном полушарии, используемая для выработки электроэнергии был установлен в 1949 году на станции Белл-Айл, штат Оклахома, США.Основная группа инженеров General Electric разработали эффективный и мощный дизайн, который лег в основу многомиллиардной индустрии. В дизайн привел к взрывному росту продаж газовых турбин во всем мире. Газовые турбины наконец занял прочное место в надежном производстве электроэнергии после 1950.
Пионеры газовые турбины 1949 года в GE включают: Брюса Бакленда «Мистер Газовая турбина», Нил Старки (GT Control Genius), Арне Лофт *, Энди Смит, Боб Крамер, Боб Хендриксон *, Дик Ноэ, Том МакКоун, Аль Бойко, Билл Тейлор, Голди Голдсворт, Фрэнк Йипл, Джордж Фуснер, Эдди Уимет, Энди Дарджис, Рой Линн, Джон Бак, Фил Белл, Фред Каммингс, Фернан Померло.
* Доступны видеолекции Арне Лофт и Боба Хендриксона
Вверху: инженеры по ракетным и газотурбинным двигателям на Испытательный полигон на Мальте
3. Инженерный форум:
|
4.Системы управления газовой турбиной:
Газ турбины — чрезвычайно сложные устройства, требующие точного контроля работать. Инженеры по управлению в General Electric первыми разработать надежную систему управления. Нил Старки разработал механический контроль, который был надежным в 1940-е годы. Нужна была лучшая система используя компьютеры и электронику (которая сама только что была разработана в это время).Эта первая электронная система была разработана Арне Лофтом, инженер-механик / электрик, работающий в GE в Скенектади, Нью-Йорк. Ниже приводится его история разработки первого Speedtronic Control. Система. (Позже Speedtronic превратился в большую линейку продуктов, не только газовые турбины, но паровые турбины и другие устройства).
Видео на первой системе управления Speedtronic ниже:
1980-е годы:
Газ 7 F Турбина General Electric (видео Youtube):
Связанные темы:
Нравится нас на Facebook
Источники:
-История
Газовая турбина с Бобом Хендриксоном от Фрэнка Хаккерта и Эдисона
Технический центр
-Эдисон представляет: интервью с Арне Лофтом Эдисоном
Технический центр
-Википедия (Двигатель внутреннего сгорания, записи газовой турбины)
-О.com Inventors
-The General Electric Story в Зале истории
— ASME.org -Belle Isle Gas Turbine
— The ABB Group, History web page
Engine на микросхеме обещает лучшую батарею | MIT News
Исследователи Массачусетского технологического института помещают крошечный газотурбинный двигатель в кремниевый чип размером примерно с четверть. Полученное устройство могло работать в 10 раз дольше, чем батарея того же веса, питая ноутбуки, сотовые телефоны, радиоприемники и другие электронные устройства.
Это также может значительно облегчить нагрузку на людей, которые не могут подключиться к электросети, включая солдат, которым теперь приходится нести много фунтов батарей для трехдневной миссии — и все это по разумной цене.
Исследователи говорят, что в долгосрочной перспективе массовое производство может приблизить удельную стоимость энергии микродвигателей к стоимости энергии сегодняшних крупных газотурбинных электростанций.
Создание крошечных вещей — это все в моде. Эта область, называемая микроэлектромеханическими системами или МЭМС, выросла из ошеломляющего успеха компьютерной индустрии в разработке и использовании микротехнологий.«Сорок лет назад компьютер заполнил все здание, — сказал профессор Алан Эпштейн из Департамента аэронавтики и астронавтики. «Теперь у всех нас есть микрокомпьютеры на наших столах, внутри наших термостатов и часов».
В то время как другие создают миниатюрные устройства, начиная от биологических датчиков и заканчивая химическими процессорами, Эпштейн и его команда из 20 преподавателей, сотрудников и студентов стремятся превратить власть в личную силу. «Большие газотурбинные двигатели могут привести в действие город, но маленький может« привести в действие »человека», — сказал Эпштейн, чьи коллеги работают в Лаборатории газовых турбин Массачусетского технологического института, Лабораториях микросистемных технологий и Лаборатории электромагнитных и электронных систем.
Как сделать крошечный двигатель, работающий на топливе? Двигателю нужен компрессор, камера сгорания, вращающаяся турбина и так далее. Изготовить миллиметровые версии этих компонентов из сварных и склепанных металлических частей невозможно. Итак, как и производители компьютерных микросхем, исследователи из Массачусетского технологического института обратились к протравленным кремниевым пластинам.
Их микродвигатель состоит из шести силиконовых пластин, сложенных друг на друга, как блины, и скрепленных вместе. Каждая пластина представляет собой монокристалл с идеально выровненными атомами, поэтому он чрезвычайно прочен.Чтобы получить необходимые компоненты, вафли индивидуально подготавливаются с использованием усовершенствованного процесса травления, чтобы удалить выбранный материал. Когда пластины складываются в стопку, поверхности и промежутки между ними создают необходимые функции и функции.
Создание микродвигателей по одному было бы непомерно дорогостоящим, поэтому исследователи снова последовали примеру производителей компьютерных микросхем. Они делают от 60 до 100 компонентов на большой пластине, которую затем (очень осторожно) разрезают на отдельные части.
Проблемы впереди
Команда MIT теперь использовала этот процесс для изготовления всех компонентов, необходимых для их двигателя, и каждая деталь работает. Внутри крошечной камеры сгорания топливо и воздух быстро смешиваются и сгорают при температуре плавления стали. Лопатки турбины, изготовленные из высокопрочных микроструктурных материалов с низким уровнем дефектов, вращаются со скоростью 20 000 оборотов в секунду — в 100 раз быстрее, чем у реактивных двигателей. Мини-генератор выдает мощность 10 Вт. Небольшой компрессор повышает давление воздуха, готовясь к сгоранию.И охлаждение (всегда проблема в горячих микроприборах) кажется управляемым, направляя сжатый воздух вокруг камеры сгорания.
«Итак, все детали работают…», — сказал Эпштейн. В конечном итоге, конечно, горячие газы из камеры сгорания должны вращать лопатки турбины, которые затем должны приводить в действие генератор, и так далее. «Это оказывается непростой задачей», — сказал он. Их цель — завершить это до конца этого года.
Предсказать, насколько быстро они смогут продвигаться вперед, само по себе непросто. Если процесс соединения выполнен хорошо, каждый микродвигатель представляет собой монолитный кусок кремния, атомарно совершенный и неразделимый. В результате даже крошечная ошибка в одном компоненте потребует начинать с нуля. И если нужно изменить один компонент — скажем, компрессор должен быть на микрон меньше — команде микротехнологий придется переосмыслить весь процесс проектирования.
Несмотря на все трудности, Эпштейн сказал, что проект «доставляет огромное удовольствие», и Массачусетский технологический институт — идеальное место для этого.«В пределах 300 футов от моего офиса я мог найти мировых экспертов по каждой из технологий, необходимых для создания полной системы», — сказал он.
Кроме того, проект дает прекрасную возможность для обучения. «Неважно, чем вы занимаетесь — сжигание, подшипники или микротехнология — это одинаково сложно», — сказал он.