Ремонт коленчатого вала — цена в Москве
Коленчатый вал – запасная часть, которая воспринимает усилия, передаваемые шатуном от поршней, поэтому коленчатый вал должен быть жестким и прочным. Нередко из-за серьёзных нагрузок коленчатый вал выходит из строя и требует профессионального ремонта.
Когда необходим ремонт коленвала
Основные симптомы, указывающие на необходимость производить ремонт коленчатого вала:
- износ шеек и нарушение геометрии вала. Шлифовка шеек возможна в случае выполнения трех условий: наличие вкладышей ремонтного размера,
- отсутствие превышения предельных размеров шеек по износу и отсутствие нарушения продольной оси вала (изгиба),
- нарушение геометрии вала,
- засор каналов подачи смазки,
- падение давления в масляной магистрали,
- увеличение осевого свободного хода детали,
- срыв резьбы под крепление маховика,
- образование глубоких бороздок на посадочных местах коленвала под сальники,
- образование сколов и трещин на поверхности шеек коленчатого вала.
Процесс проведения ремонтных работ
Ремонт коленчатого вала делится на этапы:
- разборка и промывка коленвала. На этом этапе выявляется степень износа деталей и составляется план будущего ремонта, формируется цена ремонта коленчатого вала;
- проведение шлифовки. После этого замеряют габаритные размеры коленчатого вала, они должны быть около 0,0015 мм. Чтобы исключить перекос шеек нужна качественная и точная работа специалиста. Работы по шлифованию проводятся в случае выполнения трех условий: наличие вкладышей ремонтного размера; отсутствие превышения предельных размеров шеек по износу и отсутствие нарушения продольной оси вала (изгиба). При невыполнении хотя бы одного из условий ремонт коленчатого вала становится экономически нецелесообразным. Все предложения по наплавке шеек, правке изгиба, изготовление вкладышей на заказ не имеют под собой никаких гарантий на результат и имеют смысл только при отсутствии возможности заменить вал;
- чистка каналов для подачи смазочных материалов.
Каналы снимают и очищают с помощью сжатого воздуха под высоким давлением. После этого выполняется монтаж новых заглушек;
- после расточки коленчатого вала может быть установка новых ремонтных вкладышей для корректировки наружного диаметра шеек;
- для двигателей старых моделей необходимо провести восстановление маслогонной накатки, чтобы не допустить протечки масла.
Работы по ремонту коленчатого вала требуют высокого профессионализма, поэтому поручить это специалистам технического центра АВТО-Z – верное решение.
Процесс снятия-установки коленчатого вала возможен только после демонтажа двигателя с автомобиля, следовательно цена на ремонт коленчатого вала формируется с учетом этого факта. Чтобы узнать цену замены коленчатого вала в Москве, заполните специальную форму на сайте АВТО-Z или позвоните по одному из указанных номеров.
Методы контроля размеров шеек шлифованного коленчатого вала
Мы неоднократно говорили об инструментальных методах контроля размеров восстановленных деталей. Подобные методы были и остаются самыми правильным и точным способом контроля соответствия размеров восстановленной детали техническим требованиям. Но такая возможность есть не всегда и далеко не у всех: немногие располагают полным комплектом мерительного инструмента для проведения необходимых измерений. Можно ли обойтись без мерительного инструмента и при этом контролировать сопряжения деталей с достаточной точностью? Наш ответ — можно! Рассмотрим конкретный пример.
Во многих, да чего уж скрывать, почти во всех известных мне печатных изданиях по ремонту двигателей есть описание этого — весьма несложного — метода контроля монтажного зазора в подшипниках коленчатого вала. Он описан даже в книге «Автомобили ВАЗ» изданной еще в 1973 году. Его-то мы и покажем, по заведенной здесь традиции в фотографиях. Опишем все поэтапно — благо это просто и недолго.
Для контроля монтажных зазоров в подшипниках коленвала (шатунных или коренных — не важно) имеются пластиковые «нити», назовём их так, различной толщины. В своей работе мы используем продукцию фирмы SEALED POWER от FEDERAL MOGUL и KOLBENSCHMIDT. Под маркой SEALED POWER поставляются нити (plastic gauge) голубого, зелёного и красного цвета («если в обществе нет цветовой дифференциации штанов, у общества нет будущего» — так говорил один из героев известного фильмы), для измерения различных зазоров: голубые — для зазоров 0,102-0,229 мм, зелёные — для зазоров 0,025-0,076 мм и красные — для зазоров 0,05-0,152 мм. У KOLBENSCHMIDT красные нити используются для определения зазоров от 0,025 мм до 0,175 мм.
В нашем примере мы рассмотрим определение величины зазора в шатунном подшипнике двигателя автомобиля ВАЗ 21083, для чего воспользуемся измерителем KOLBENSCHMIDT, проходящими красной нитью через всю статью. Комплект состоит из двух компонентов: полосок со «штрихами» различной ширины (против каждого стоит обозначение размера в миллиметрах и долях дюйма) и несколькиих пластиковых нитей. Полоски многоразовые, а ниточки одноразовые. Однако, пользовать ими значительно проще, чем «мучатсься» с нутромерами и микрометрами. Принцип измерения зазора (контроля) такой: отрезаем кусочек ниточки, кладем его между валом и крышкой (в которую установлен вкладыш), затягиваем крепжные болты надлежащим моментом, затем разбираем детали. Само собой разумеется, что собираемые детали должны быть чистыми — без песка, металлической стружки и прочей грязи. Пластиковая нить-проволочка расплющивается, оставляя на валу след. К этому следу мы прикладываем измерительную полоску, на которой есть цветные прямоугольники-«штрихи» разного размера. Фактически мы замеряем «меру расплющивания» пластиковой нити.
На момент создания материала красные нити SEALED POWER были только в заказе.
Поэтому взяли со склада Plastic Gauga от Kolbernschmidt. На MotorZona.ru есть некоторое количество и других ниточек, например SPR1 STD
Измерительные полоски и «ниточки» (проволчки)
Вот отшлифованный коленчатый вал и пара вкладышей из заказа-наряд №5481. Хозяин даже не предполагает, что его коленвал стал уже звездой рунета
Собираем… И тут же разбираем.
Шаблон из комплекта прикладываем к самому широкому месту расплющенной нити
Измеренный зазор находится в пределах 0,025-0,038 мм, что входит в допустимый диапазон. По заводским требованиям (ВАЗ) монтажный зазор в шатунном подшипнике должен составлять 0,036—0,086 мм.
Когда таких нитей-измерителей в России еще не было (или их трудно было найти), для тех же целей применяли фольгу от сигаретной пачки, которая имела толщину примерно 4 сотых мм (0,04 мм). Методика измерений была точно такой же, только кусочек фольги укладыли не между валом и вкладышем, а между крышкой и тыльной стороной вкладыша. Если после этой процедуры вал не проворачивался, значит зазор меньше или равен 0,04 мм. Если проворачивался — больше. Это конечно не очень научно, но в руках мастера и фольга может быть достаточно точным инструментом. Ну а если Вы не умеете играть в шахматы, то никакая теория не поможет…
Укладка коленчатого вала / НЕВА-диз
Перед укладкой коленчатого вала необходимо убедится в отсутствии деформации верхней поверхности машинной рамы, в сохранении ее плоскости. Укладка вала будет отвечать всем требованиям в том случае, когда все контрольные плоскости и поверхности гнезд рамовых подшипников располагаются правильно относительно оси коленчатого вала.
Укладку коленчатого вала (выравнивание его оси) путем шабрения соответствующих
рамовых подшипников или выравнивания рамы. Для этого необходимо снять раскепы на всех мотылях. Данные заносятся в таблицу. Полученные значения раскепов позволяют построить график «изломанной» оси коленчатого вала.
Если от условной прямой ОО отложить на осях цилиндров 1,2,3, и т. д. в определенном масштабе величины раскепов и нанесенные точки соединить отрезками, то получится ломаная линия, условно изображающая характер расположения оси коленчатого вала. На рисунке-графике с учетом знаков отложены раскепы: -L1; +L2; +L3; L4=0; -L5; -L6.
Из рис.1 видно, что относительно других наиболее низко расположена рамовая шейка №3. Так как подъем нижних вкладышей подшипников за счет подкладок запрещается Правилами Регистра, то выравнивают ось данного вала шабрением баббита нижних половинок вкладышей подшипников в последовательности 6-1-2-5-7-4. Тогда ось коленчатого вала займет положение О’ — O’. В практике укладки коленчатых валов после каждого цикла шабрения снимают раскепы и, сверяя их с предыдущими величинами, соответственно корректируют последующий цикл шабровки.
Для подъема коленчатых валов устанавливают специальное подъемное устройство. При укладке тяжелых валов применяют подъемник с синхронным выбиранием строп, что исключает опасный прогиб вала при подъеме. В целях сокращения числа подъемов коленчатого вала предварительную пригонку вкладышей выполняют по шейкам вала, уложенного на деревянные прокладки. После предварительной пригонки рабочей поверхности нижних вкладышей рамовых подшипников их укладывают в гнезда рамы. Рамовые шейки покрывают тонким слоем краски, коленчатый вал опускают на нижние вкладыши и проворачивают на один оборот. После подъема вала выступающие места баббита вкладыша (окрашенные краской) б мешающие прилеганию шеек, удаляют шабером. Повторяя эту операцию несколько раз, добиваются необходимого прилегания рамовых шеек коленчатого вала к поверхности нижних вкладышей. В процессе пригонки вкладышей следует вести контроль за положением оси вала в вертикальной и горизонтальной плоскостях. Положение оси в вертикальной плоскости определяют по контрольной скобе, в горизонтальной плоскости — при помощи нутромера и микрометра. Просадку вала определяют относительно горизонтальной плоскости рамы, а смещение вала на левый или правый борт проверяют относительно вертикальных плоскостей замка рамовых подшипников.
1. положение вала по скобе;
2. раскепы вала;
3. прилегание рамовых подшипников по шейке вала на краску, поочередно их вынимая.
Все эти работы выполняются при разобщенных фланцах коленчатого вала и упорного вала. При замере просадки шейки вала должны опираться на нижние вкладыши и щуп 0,03 мм не должен проходить между шейкой и вкладышем. Раскепы и измерения скобой дадут прямо противоположные результаты, значит, деформирована фундаментная рама двигателя.
Уклон оси коленчатого вала относительно плоскости рамы допускается до 0,10 мм на 1м длины. Однако общий уклон не должен превышать 0,5 мм на всей длине вала.
P.S.
За исходный (базовый) мотыль целесообразно всегда принять мотыль с нулевым раскепом. Тогда проходящая через рамовые подшипники ось «O — O» и будет той осью, к которой необходимо свести все остальные подшипники, чтобы вывести раскепы в мотылях.
Для удобства пользования графиком и простоты условимся откладывать раскепы от линии О-О вверх со знаком (-), а вниз со знаком (+). В практике редко бывают случаи, когда коленчатый вал имеет хотя бы один нулевой раскеп. Поэтому за базовый раскеп в таких случаях принимают мотыль с наименьшим раскепом по абсолютной величине.
Перед укладкой коленчатого вала, как правило, проверяют крепление рамы двигателя к фундаменту и плотность постановки клиньев между ними. В процессе укладки коленчатого вала должно быть достигнуто равномерное прилегание всех рамовых шеек к их вкладышам, не должно быть не равномерной просадки колен вала и изгиба его оси.
До начала укладки колен вала выполняют ремонт и пригонку затылков нижних рамовых подшипников на краску по постелям машинной рамы и предварительную пригонку вкладышей по фальшвалу.
Зазоры в подшипниках, осевые и радиальные, указываются в формуляре двигателя. Осевой разбег между вкладышами и щеками вала зависит от длины вала. Радиальный масляный зазор при отсутствии данных можно определить по формуле:
S = 0,00078 D + 0,02mm, где D — диаметр шейки вала.
Правилами Регистра установлены следующие величины упругих раскепов в зависимости от хода поршня: монтажные = 0,0001S; допустимые в эксплуатации = 0,00015S; недопустимые = 0,00025S.
Нормальный износ вкладышей за 1000 часов работы составляет: в малооборотных двигателях около 0,01 — 0,015 мм; в высокооборотных около 0,02 — 0,03 мм.
Интенсивный износ и под плавление возникает по двум причинам:
1. нарушение жидкостного трения из-за падения давления масла в системе и уменьшения вязкости при попадании топлива или воды в масло;
2. увеличение удельного давления на отдельные вкладыши из-за неравномерного распределения нагрузки по цилиндрам или уменьшения опорной поверхности вкладыша при деформации фундаментной рамы или самого коленчатого вала.
Задиры и царапины на поверхности вкладышей возникают при попадании вместе с маслом твердых механических частиц. Тщательная очистка масла в фильтрах и сепараторах позволяет избежать этих повреждений.
Растрескивание и выкрашивание антифрикционного слоя появляются в результате усталости металла. Причинами усталости могут быть:
— несоответствие действующих нагрузок прочностным характеристикам сплава;
— неправельная технология заливки подшипников;
— появление ударных нагрузок из-за увеличения радиальных зазоров или чрезмерной овальности шеек вала.
информация с сайта http://www.mygma.narod.ru/
Восстановление коленчатого вала в Новосибирске
Восстановление коленчатого вала – процесс достаточно непростой, зависит от многих факторов и возможен не в каждой компании по ремонту двигателей, так как эта услуга узкоспециализированная. Коленвал представляет собой сложную конструкцию, которая играет важную роль в регулировании усилия шатунов в крутящий момент двигателя. Восстанавливая коленчатый вал, следует сохранять соосность всех механизмов. Для начала замеряются все ремонтные размеры, и проводится геометрия вала. Геометрия позволяет определить, какой именно ремонт детали необходим. Так же следует обратить внимание, какие манипуляции с валом проводились раньше, так как скорей всего появится необходимость в применении нестандартных ремонтных вкладышей. Слабым местом коленчатых валов является изнашивание шеек, которое устраняется шлифовкой под ремонтный размер, либо восстановлением методом детонационного напыления под заданный размер. Восстановление шеек коленвала предотвратит возникновение деформации детали. На этом этапе так же следует произвести запайку трещин с последующей обработкой. Все работы проводятся на специализированных станках, контролирующих баланс детали. По завершению шлифовки шатунных шеек, шлифуются коренные. Восстановление шеек коленчатого вала напылением позволяет не только полностью восстановить геометрию вала, но и значительно повысить срок его службы.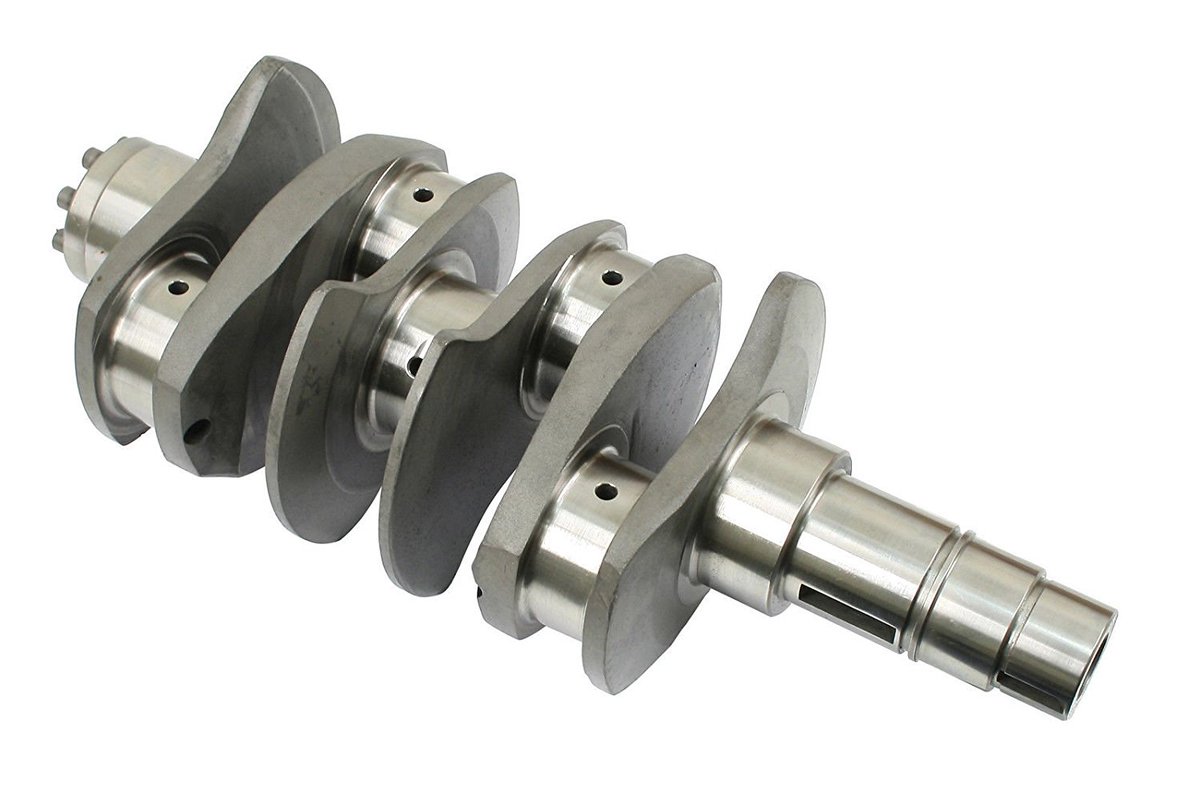
Что такое отклонение коленчатого вала?
Коленвал отклонение происходит со временем, в ходе неоднократных и непрерывное использование коленчатого вала.
Это процесс, который происходит в фоновом режиме, как работает двигатель и, Хотя это может ’ t рассматриваться без обнаружения документа, Это вызывает значительный ущерб к механизму.
- Без устранения сдвигов в коленчатого вала с течением времени, машина будет носить неравномерно, привести к неоправданной нагрузки на вспомогательные компоненты.
- Это будет отвлекать от срока службы двигателя, заставляя его преждевременно изнашивается. Это естественно-происходя проблемы могут быть легко исправлены однако, с небольшой корректировки.
Зная, когда и как настроить коленчатого вала будет продлить его жизни, Экономия времени и денег.
В ДИ-5 и ди — 5C от Prisma Тибро легко для использования и могут быть запрограммированы и перепрограммировать проверить положение каждого механизма в любое время.
С помощью ди-5 или ди — 5C регулярно проверять для коленвала прогиб требуется всего несколько минут вашего времени и может продлить срок службы двигателя по годам.
В прошлом, Датчик шкалы был использован для обнаружения рассогласования коленчатого вала.
Это требует гораздо больше времени, процесс, с подробные показания инженер будет принимать сам.
Она требует чтения коленчатого вала в каждой из пяти позиций (стороны, Вверх, и два по обе стороны от нижней), и затем интерпретировать эти цифры вручную, чтобы увидеть, каким образом следует скорректировать коленчатого вала.
- Глубокое понимание процесса и дотошный измерения необходимы для обеспечения точных измерений, и, даже если процесс был завершен корректно, нет никаких гарантий wouldn датчика ’ t немного скольжения, осадки в чтении.
Кроме того, датчика требуется инженер для доступа к механизму из каждого угла, охватывающий его в грязи и смазки.
Автоматизация и компьютеризация устройство измерения, Этот процесс занимает лишь часть времени, и гораздо более точные измерения.
ДИ-5 и ди — 5C устройств надежно вписывается коленчатого вала и остаться там, без смены или скольжения.
Как удаленного датчика, ДИ-5 / 5C обнаруживает смещения измеряя коленчатого вала в каждой точке. Числа записываются во внутреннюю память устройства. С каждым измерением, устройство затем сравнивает номера друг против друга и обеспечивает измерение смещения без дальнейших вычислений.
ДИ-5 / 5C могут быть запрограммированы бесконечное количество раз и оценивать любое количество коленвалов, используя такой же процесс.
Это устраняет необходимость вручную номера и позволяет инженера для измерения каждого механизма в двигатель и каждой точки быстро и легко. Прилагаемый овальности комплект на ди-5 / 5C будет измерять износ цилиндра вкладыш и показать, где неравномерно цилиндра.
Ремонт коленчатого вала компрессора — Центр защитных покрытий — Урал
Центр защитных покрытий производит восстановление и ремонт коленчатого вала компрессора методом газопламенного напыления. Коленвал служит в оборудовании для передачи момента и преобразования движений, поступательного во вращательное движение или наоборот. Коленчатый вал имеет такие конструктивные элементы: шейки, кулачки, кривошипы, торцы, шпоночные пазы, стыки и отверстия. При эксплуатации компрессора происходит не равномерный износ коренных и мотылевых шеек вала. Шатунные шейки изнашиваются быстрее, чем коренные из-за более тяжелых условий работы.
Ремонт коленчатого вала компрессора
- возникновением овальности шеек вала
- порча шеек задирами, рисками и раковинами
- выбоины шеек
- образованием изломов и трещин
- возникновением остаточных деформаций
Износ шеек вала происходит из-за неравномерности нагрузки вала за один оборот. Неравномерный износ шеек по образующей конусность, по сечению овальность. Важную роль при ремонте коленчатого вала компрессора играет операция дефектовки. При ремонте шатунной шейки коленчатого вала задиры, забоины, риски на поверхностях шеек валов определяются осмотром. Дефекты шеек коленвала, в зависимости от их характера и величины, устраняем шлифованием и полированием на станках. На нашем предприятии у коленчатого вала восстанавливаем расположение, форму, размеры и шероховатость элементов, износостойкость трущихся поверхностей и усталостную прочность.
При больших износах коленчатого вала компрессора приходится протачивать шейки на токарном станке с последующей шлифовкой и подвергать поверхностной металлизации наплавке металла. После наплавки или металлизации производится механическая обработка — коленвал протачивается и шлифуются.
Методом газопламенного напыления производится упрочнение шатунной шейки коленчатого вала компрессора. Гетерогенное многофазное пористое покрытие обладает большой износостойкостью. Толщина износостойкого покрытия может быть обеспечена в пределах от 50 мкм до 10 мм и более.
Исследование предельного состояния коленчатого вала судового среднеоборотного дизеля Текст научной статьи по специальности «Строительство и архитектура»
DOI: 10. 24143/2073-1574-2017-3-53-61 УДК 629.562: 621.83.061.1
Ю. А. Корнейчук
ИССЛЕДОВАНИЕ ПРЕДЕЛЬНОГО СОСТОЯНИЯ КОЛЕНЧАТОГО ВАЛА СУДОВОГО СРЕДНЕОБОРОТНОГО ДИЗЕЛЯ
Предельное состояние коленчатого вала среднеоборотного дизеля наступает вследствие влияния трех основных факторов — кинематической погрешности, изнашивания подшипников скольжения и усталости материала. Кинематическая погрешность вызывает деформацию коленчатого вала, неравномерное изнашивание подшипников и усталостные явления. Деформация контролируется измерением биения рамовых шеек и изменением расстояния между щеками. Допустимые значения деформации определены изготовителем и проверены на практике. По данным литературных источников проведен анализ результатов исследований процесса изнашивания подшипников скольжения коленчатого вала. Основным видом является абразивное изнашивание подшипников скольжения. Неравномерное изнашивание шеек коленчатого вала приводит к появлению овальности и конусности. Нецилиндричность шеек является основной причиной отказов подшипников скольжения. Исследовано явление усталости коленчатого вала. При превышении значений предельной длины трещины и зоны ее расположения на поверхности шейки, указанных в инструкциях по техническому обслуживанию и ремонту среднеоборотного дизеля, рекомендовано менять коленчатые валы с трещинами шеек. Выявлены разные виды усталостного разрушения коленчатого вала. Исследован процесс развития трещин внутри коленчатого вала. Предложены оценки предельной глубины растрескивания шеек по результатам изучения структуры аварийного усталостного излома коленчатого вала с учетом рекомендаций фирм-изготовителей и опыта ремонта. Даны оценки средней скорости растрескивания внутри шеек коленчатого вала на основе изучения аварийных ситуаций. Приведен пример успешного восстановления коленчатого вала с глубокими трещинами. После цветной и магнитопорошковой дефектоскопии для локализации трещины рекомендуется применять электропотенциальный трещиномер RMG 4015. Рассмотрен опыт управления процессом растрескивания поверхности коленчатого вала на дизеле 8№УС48А2-и путем снижения нагрузки на дизель.
Ключевые слова: дизель, коленчатый вал, отказ, излом.
Введение
Предельное состояние коленчатого вала (КВ) среднеоборотного дизеля (СОД) определяется тремя основными факторами — кинематической погрешностью, изнашиванием подшипников скольжения и усталостью материала.
Изнашивание подшипников скольжения КВ. В ходе исследования изнашивания подшипников скольжения получены достоверные результаты предельных значений износа и неравномерного износа шеек в виде овальности и конусности [1]. Основной причиной отказов подшипников скольжения коленчатых валов является абразивное изнашивание, которое обусловлено наличием абразивных частиц в моторном масле. Наибольшее влияние на возникновение задира оказывает величина овальности шеек. При величине овальности 0,14 мм вероятность задира составляет 100 % [1].
У шатунных шеек формируется преимущественно конусообразность, достигающая 0,10 мм. Рамовые шейки в результате износа приобретают по большей части овальную форму. Наиболее опасны катастрофические виды изнашивания: заедание, задир и схватывание. При задире или схватывании шеек с вкладышем, а также расплавлении антифрикционного слоя вкладышей, как правило, происходит деформация коленчатого вала, реже — поломка вала.
Контроль зазора между вкладышем и шейкой дает информацию об износе и смазке подшипников. Применение многослойных вкладышей подшипников скольжения с гальваническим покрытием не допускает измерений зазоров щупом из-за вероятности повреждения рабочей поверхности. Вопрос о простом и эффективном способе измерения этого зазора пока не решен.
Кинематическая погрешность. Кинематическая погрешность вызвана отклонениями формы и размеров КВ, вкладышей и постелей подшипников, фундаментной рамы дизеля и судового фундамента. Контроль кинематической погрешности сводится к оценкам деформации КВ путем измерения биений рамовых шеек, упругого и жесткого раскепов. Нецилиндричность шеек в виде овальности и конусности является следствием неравномерного изнашивания. Предельное значение кинематической погрешности прописано в инструкции каждого конкретного дизеля.
Усталостное разрушение. Отсутствуют исследования предельного состояния КВ СОД с учетом появления и развития трещин. С развитием и появлением новых методов восстановления деталей существует возможность продлить ресурс КВ.
Объекты, цель, средства и методы исследований
Для упрощения разделим трещины по факту их расположения на поверхностные и глубокие. Глубокие усталостные трещины шеек обычно проходят в плоскости под углом около 45° к оси вала. Глубокие трещины щек наблюдаются в местах слияния их с шейками. Поверхностные трещины шеек расположены вдоль оси вала в упрочненном слое.
С появлением приборов и способов контроля глубоких трещин появилась возможность наблюдений за процессом растрескивания. При определенных условиях трещины растут очень медленно. Длительный период подрастания трещины позволяет планировать оптимальный срок службы КВ, его замены или восстановления. Этот принцип контролируемой деградации положен в основу современной концепции проектирования и эксплуатации с допускаемым повреждением damage-tolerant design (DTD). Для применения DTD необходимо знать скорость роста и предельные размеры трещины.
В инструкциях по техническому обслуживанию и ремонту СОД оговариваются максимальная длина поверхностной трещины и зона ее расположения. Небольшие трещины шлифуют до следующего ремонтного размера, одновременно восстанавливая цилиндричность шеек. При превышении указанных значений рекомендовано менять валы с трещинами шеек.
Цель исследования состоит в определении значений показателей предельного состояния КВ СОД с учетом новых технологий диагностирования, ремонта и восстановления КВ.
Усталостные разрушения КВ СОД наблюдаются редко. Количество контролируемых СОД ограничено. Большие размеры КВ СОД затрудняют выполнение испытаний образцов на выносливость. Эти предпосылки обусловливают проведение натурных испытаний и наблюдения за процессом естественной деградации КВ. При усталостном разрушении деталей применяется фрактографический анализ изломов для выявления причин отказов.
Средства дефектоскопии. Электропотенциальный метод определения глубины трещины основан на измерении электрического сопротивления переменному току между двумя точками на поверхности металлических объектов. Трещиномер RMG 4015 фирмы «Karl Deutsch» измеряет падение напряжения по поперечному контуру трещины. В отличие от обычного мульти-метра, в трещиномере используется переменный ток высокой частоты, поэтому ток течет по поверхности проводника под действием скин-эффекта. Стабилизированный переменный ток подается к объекту по двум крайним контактным электродам. Глубина трещины определяется разностью потенциалов между двумя внутренними электродами. Для измерения глубины наклонных трещин частота переменного тока автоматически снижается (для того, чтобы электрический ток покрывал большую площадь контролируемого объекта), и устанавливается дополнительный внешний электрод (рис. 1).
Прибор измеряет глубину трещины, ранее обнаруженной средствами магнитопорошковой или цветной дефектоскопии. Внутренний дефект им не обнаруживается. Быстродействие соответствует одному измерению в секунду. 0 = сош1
(3)
Кривую многоцикловой усталости (рис. 2) описывают степенным уравнением (3), где N0 — базовое число циклов при пределе выносливости о2; N — число циклов разрушающих знакопеременных нагрузок о1; т — экспериментальный параметр, характеризующий крутизну кривой усталости.
с, МПа
Рис. 2. Кривая выносливости испытаний образцов
Формулы (1)—(3) получены экспериментальным путем. В них определены пороговые значения параметров, при которых трещины стабилизированы и не сказываются на прочности конструкции.
Опыт управления процессом растрескивания шеек коленчатого вала
На шейках КВ главного двигателя 8NVD48A-2U сейнер-траулера рефрижераторного проект 503 (СТР-503) наблюдались трещины. После протачивания шеек до ремонтного размера и замены вкладышей дизель отработал 6000 часов. В ходе заводского ремонта магнитным дефектоскопом обнаружены едва заметные трещины на шейках КВ. Их решили оставить без обработки, при условии снижения нагрузки на 20 %. В течение последующих 5 лет трещины не изменились по форме и размерам. Отметим, что восстановление цилиндрической формы шеек КВ и замена вкладышей не решила проблему появления трещин.
Исследование усталостного разрушения коленчатого вала дизеля 8NVD48A-2U
Шестицилиндровый дизель 6NVD48-U (295 кВт при 275 мин- ) обладал достаточной надежностью. После добавления двух цилиндров и применения наддува частота вращения дизеля 8№УВ48А-и увеличилась до 375 мин-1 при мощности 736 кВт. Все основные детали остались без конструктивных изменений, что привело к превышению допустимых норм нагрузок по многим показателям. Надежность дизеля значительно снизилась. Фирма SKL (ГДР) фактически признала конструктивные дефекты и запустила новую модификацию дизеля NVD48. При этом были усилены все основные детали. Например, дизель 8NVD48А-2U имеет коленчатый вал с толщиной щек 98 мм и шириной 395 мм; рамовые и шатунные шейки диаметром 215 мм, тогда как у ранее выпущенных дизелей 8NVD48-U и 8NVD48A-U толщина щек 93 мм, ширина щек 380 мм, диаметр рамовых шеек 210 мм и диаметр шатунных 200 мм. В 2015 г. произошло аварийное разрушение КВ главного двигателя 8NVD48A-2U СТР «Иван Мошляк». Усталостное разрушение КВ произошло из-за действия знакопеременных нагрузок при скручивании и изгибе КВ. Для дизелей NVD характерны отказы КВ, вызванные крутильными колебаниями вала. Часть усталостных разрушений — 60 % — приходится на шейки, остальные 40 % — на разрушение щеки в районе галтели [4].
На рис. 3 показаны зоны усталостного разрушения рамовой шейки КВ дизеля 8№У048А-2и.
1 В настоящее время фирма SKL-Motoren-und Systemtechnik GmbH (Германия).
<
Рис. 3. Усталостное разрушение рамовой шейки КВ
Направление гребня по оси излома и характерные усталостные бороздки (рис. 4) говорят о том, что очаг зарождения трещины находится на поверхности рамовой шейки, а не в зоне галтели, где наблюдаются максимальные напряжения.
Рис. 4. Структура излома рамовой шейки коленчатого вала: 1 — очаг зарождения первой усталостной трещины; 2 — волнообразные следы развития трещины;
3 — зона долома; 4 — отверстие для смазки; 5 — зона второй усталостной трещины
Это указывает на наличие концентратора напряжений на поверхности шейки в виде задира или поверхностной трещины [5].
Усталостное разрушение во времени можно разбить на три зоны:
— зарождение трещины в результате дефекта материала (концентратора напряжений) или фреттинг-коррозии в местах соединений с натягом;
— развитие трещины на поверхности шейки или вглубь в результате действия знакопеременных нагрузок;
— разрушение по критерию снижения площади рабочего сечения;
— разрушение по критерию повышенных динамических нагрузок.
На рис. 4 представлена структура излома рамовой шейки КВ главного двигателя СТР «Иван Мошляк», на котором довольно сложно определить зону зарождения усталостной трещины. Следует определить границы продвижения усталостной трещины, цвета побежалости, зону хрупкого излома, очаг зарождения трещины, фреттинг-коррозию. Место зарождения трещины шейки должно находиться в зоне максимальных напряжений — у галтели. Очевидно, для данного случая (см. рис. 3) у галтели структура излома не соответствует критериям обычной усталостной трещины.
Если предположить наличие следов фреттинг-коррозии и обычной коррозии в районе усталостной трещины, то в левой части снимка (рис. 4) можно обнаружить очаг зарождения усталостной трещины. Это подтверждается мелкозернистой структурой материала, расхождением волновых линий от зоны зарождения трещины и коричневым налетом от фреттинг-коррозии. Для этой стадии усталостного излома (рис. 4, зона 1) характерно наличие волнообразных полос, представляющих собой ряд границ ее последовательного распространения.
Наличие коррозии указывает на долгую историю существования этой трещины. На изломе шейки (рис. 4) имеются два источника усталостных трещин с противоположных сторон поверхности излома. Зоны развития трещин несколько смещены по оси вала. Этим объясняется наличие гребня в изломе шейки вала.
Диаметр рамовой шейки D = 205 мм. Глубина первой трещины hi = 41 мм. Глубина второй трещины h3 = 22 мм. Доля двух трещин от диаметра шейки D
100(h2 + h3)/D = 100(41 + 22)/205 = 30 %.
Остаточная толщина вала 70 %. По данным наблюдений можно сделать вывод о предельном значении относительной глубины трещины [h %] = 25 %, с 5 %-м запасом.
Не имея точных данных о зарождении трещины, предположим, что она появилась в результате задира шейки при проворачивании вкладыша в предыдущем рейсе. От ремонта до ремонта наработка дизеля составила t = 6000 ч. Тогда максимальная скорость роста трещины, мкм/ч, определится как
Vmax = M/t = 41/6000 = 6,8.
Минимальную скорость роста трещины, мкм/ч, определим из назначенного ресурса КВ СОД (R = 80 000 ч)1:
vmin = h2/R = 41/80 000 = 0,5.
На шейке КВ СОД СТР «Иван Мошляк» (рис. 4) трещина глубиной 41 мм; частота вращения дизеля 8NVD48A-2U 375 мин 1 (6,25 с 1). Минимальная скорость растрескивания 0,5 мкм/ч. Если допустить, что трещина растет с начала эксплуатации судна, то средняя скорость роста v = 41/(18108) = 2,28 10-8 мм/цикл.
Опыт восстановления коленчатого вала дизеля 6ЧН40/46
На большом автономном морозильном траулере (БМРТ) проекта 1288 «Oriental Discoverer» установлены два дизеля Pielstik 6ЧН40/46. Через 120 000 часов наработки обнаружены 134 трещины шеек КВ. Применялись магнитопорошковая и ультразвуковая дефектоскопия. 10 ) = 2,24• 10 мм/цикл.
Рис. 5. Восстановленный коленчатый вал дизеля 6ЧН40/46
Отметим, что на дизелях Pielstik 6ЧН40/46 устанавливается один и тот же КВ как для рядного, так и для У-образного дизеля. Диаметр шеек увеличен с 285 до 315 мм. Для рядного дизеля это ведет к дополнительному запасу прочности КВ в случае появления трещин.
Заключение
Предельные значения показателей состояния КВ определены на основании анализа результатов исследований литературных источников, данных фирм-изготовителей и опытным путем. Критические значения глубин трещин шеек коленчатых валов определены опытом естественного разрушения КВ и опытом его восстановления при глубоких трещинах.
Основным видом предельного состояния КВ является неравномерный износ шеек (90 %). Реже встречается предельная деформация КВ, контролируемая по раскепам и биениям шеек рамовых подшипников (8 %). Доля аварийных усталостных разрушений КВ составляет 2 %. Среди усталостных отказов КВ СОД 65 % приходится на шатунные и рамовые шейки и 35 % на разрушение щек.
По результатам двух наблюдений на разных конструкциях дизелей минимальная средняя скорость роста трещины внутрь шейки составила 0,5-0,7 мкм/ч. Если учесть разную частоту вращения наблюдаемых дизелей, то средняя скорость роста трещин оказалась одинаковой: V = 2,2-10 8 мм/цикл.
Экспериментально доказана возможность управления процессом растрескивания шеек КВ путем снижения нагрузки на дизель. Расширена классификация трещин КВ. Трещины разделяются на поверхностные и глубокие. Поверхностная трещина может со временем стать глубокой.
Изучение отказов коленчатых валов СОД выявило необходимость учитывать не только длину трещины на поверхности КВ, но и ее глубину. В ходе изучения аварийных разрушений КВ на основании полученных данных установлено предельное значение глубины трещины: Йдред= 0,25D.
СПИСОК ЛИТЕРА ТУРЫ
1. Леонтьев Л. Б., Леонтьев А. Л., Макаров В. Н. Влияние эксплуатационных факторов на отказы подшипников скольжения коленчатых валов судовых среднеоборотных дизелей и пути повышения их надежности // Вестн. Гос. ун-та мор. и речн. флота им. адм. С. О. Макарова. 2016. № 1 (35). C. 129-138.
2. Griffith A. A. The phenomenon of rupture and flow in solids // Philosophical Transactions of the Royal Society A. 1920. Vol. 221. Р. 163-198.
3. Парис П., Си Дж. Анализ напряженного состояния около трещин // Прикладные вопросы вязкости разрушения. М.: Мир, 1968. С. 64-142.
4. Соболенко А. Н. Исследование причин повреждений рамовых подшипников при вибрации и деформации упругих систем фундаментных рам ВДГ // Науч. тр. Дальрыбвтуза. 2015. T. 35. C. 97-103.
5. Маницын В. В., Соболенко А. Н. Анализ повреждений рамовых подшипников двигателей 8NVD48A-2U на промысловых судах // Вестн. Гос. ун-та мор. и речн. флота им. адм. С. О. Макарова. 2016. № 6 (40). C. 150-155.
Статья поступила в редакцию 05.06.2017
ИНФОРМАЦИЯ ОБ АВТОРЕ
Корнейчук Юрий Алексеевич — Россия, 690087, Владивосток; Дальневосточный государственный технический рыбохозяйственный университет; канд. техн. наук; доцент кафедры судовых энергетических установок; [email protected].
Y. A. Korneychuk
RESEARCH OF THE LIMITING STATE OF THE MARINE MEDIUM-SPEED DIESEL CRANKSHAFT
Abstract. The limiting state of the marine medium speed diesel engine crankshaft occurs as a result of the influence of three basic factors: kinematics error, plain bearings wear, and fatigue of material. A kinematics error causes deformation of the crankshaft, uneven wear of bearings and material fatigue. The crankshaft deformation is monitored by radial runout of the crank journal and change of distance between crankwebs. The legitimate values of deformation are defined by the manufacturer and tested in practice. According to the data taken from the literature, there has been analyzed the process of the crankshaft bearings wearing. The main reason is found an abrasive wear of plain bearings. The uneven wear of crankshaft necks results in their ovality and conicity. Non-cylindrical shape of the neck is the principal reason of plain bearings faults. The phenomenon of the crankshaft fatigue has been studied. Exceeding warning limits of crack length and area on the neck surface, which is mentioned in diesel technical service and repair manual, will result in changing crankshafts with cracked necks. The different types of diesel crankshaft fatigue destruction have been educed. The problem of crack development inside a crankshaft has been studied. The es-
timations of limiting depth of neck craking are offered based on the results of emergency fatigue fracture of crankshaft, taking into account recommendations of firms-manufacturers and experience of repair. The estimations of crankshaft neck cracking average speed have been given on the basis of study of emergency situations. An example of successful renewal of crankshaft with deep cracks has been demonstrated. After magnetic particle or dye penetrant testing it has been recommended to use the crack depth gauge RMG 4015. Crack control experience has been investigated in the course of the process of 8NVD48A2-U diesel crankshaft neck surface cracking by a decreasing of diesel load.
Key words: diesel, crankshaft, failure, fracture.
REFERENCES
1. Leont’ev L. B., Leont’ev A. L., Makarov V. N. Vliianie ekspluatatsionnykh faktorov na otkazy podshipni-kov skol’zheniia kolenchatykh valov sudovykh sredneoborotnykh dizelei i puti povysheniia ikh nadezhnosti [The influence of operational factors on failure of crankshaft bearings of marine medium-speed diesels and ways to improve their reliability]. Vestnik GUMRF, 2016, no. 1 (35), pp. 129-138.
2. Griffith A. A. The phenomenon of rupture and flow in solids. Philosophical Transactions of the Royal Society A, 1920, vol. 221, pp. 163-198.
3. Paris P., Si Dzh. Analiz napriazhennogo sostoianiia okolo treshchin [Analysis of the stress state around the cracks]. Prikladnye voprosy viazkosti razrusheniia. Moscow, Mir Publ., 1968. Pp. 64-142.
4. Sobolenko A. N. Issledovanie prichin povrezhdenii ramovykh podshipnikov pri vibratsii i deformatsii up-rugikh sistem fundamentnykh ram VDG [The study of bedplate bearing damage during vibration and deformation of elastic systems of diesel generator bed frames]. Nauchnye trudy Dal’rybvtuza, 2015, vol. 35, pp. 97-103.
5. Manitsyn V. V., Sobolenko A. N. Analiz povrezhdenii ramovykh podshipnikov dvigatelei 8NVD48A-2U na promyslovykh sudakh [Analysis of bedplate bearings damage of 8NVD48A-2U engines on fishing vessels]. Vestnik Gosudarstvennogo universiteta morskogo i rechnogo flota im. adm. S. O. Makarova, 2016, no. 6 (40), pp. 150-155.
The article submitted to the editors 05.06.2017
INFORMATION ABOUT THE AUTHOR
Korneychuk Yury Alekseevich — Russia, 690087, Vladivostok; Far Eastern State Technical University of Fisheries; Candidate of Technical Sciences; Assistant Professor of the Department of Ship Power Plants; korneych @mail. ru.
Коленчатый вал | Инжиниринг | Fandom
Коленчатый вал, поршни и маховик
Коленчатый вал , иногда сокращенно кривошипно , является той частью двигателя, которая преобразует возвратно-поступательное движение поршня во вращение.
Обычно он соединяется с маховиком для уменьшения характеристики пульсации четырехтактного цикла, а иногда и с демпфером крутильных или вибрационных колебаний на противоположном конце, чтобы уменьшить крутильные колебания, часто вызываемые по длине коленчатого вала цилиндрами, наиболее удаленными от вала. выходной конец действует на упругость металла при кручении.
Большие двигатели обычно являются многоцилиндровыми, чтобы уменьшить пульсации от отдельных тактов зажигания, с более чем одним поршнем, прикрепленным к более сложному коленчатому валу; но многие небольшие двигатели, такие как двигатели мопедов или садовой техники, являются одноцилиндровыми и используют только один поршень, что упрощает конструкцию коленчатого вала. Коленчатый вал имеет линейную ось, вокруг которой он вращается, как правило, с несколькими шейками подшипников, установленными на сменных подшипниках, удерживаемых в блоке двигателя, основных подшипниках.Поскольку коленчатый вал подвергается значительной боковой нагрузке от каждого цилиндра в многоцилиндровом двигателе, он должен поддерживаться несколькими такими подшипниками, а не только по одному на каждом конце; это также было фактором роста автомобильных двигателей V8 с их более короткими коленчатыми валами, а не с прямым восьмёркой. По этой причине двигатели с высокими рабочими характеристиками часто имеют больше коренных подшипников, чем их собратья с более низкими характеристиками.
Кроме того, для преобразования возвратно-поступательного движения во вращение коленчатый вал имеет «ходы кривошипа» или «штифты кривошипа», дополнительные опорные поверхности, ось которых смещена относительно оси кривошипа, к которым относятся «большие концы» шатунов. от каждого цилиндра прикрепить.Расстояние оси кривошипа от оси коленчатого вала определяет измерение хода поршня и, следовательно, рабочий объем двигателя; распространенный способ увеличить мощность двигателя — увеличить ход. Однако это также увеличивает возвратно-поступательную вибрацию, ограничивая возможности двигателя на высоких оборотах; в качестве компенсации это улучшает работу двигателя на низких оборотах, поскольку более длинный ход впуска за счет меньшего (ых) клапана (ов) приводит к большей турбулентности и перемешиванию всасываемого заряда.По этой причине даже такие высокоскоростные производственные двигатели, как современные двигатели Honda, классифицируются как длинноходные, поскольку ход больше диаметра отверстия цилиндра. В серийных V-образных или плоских двигателях соседние шатуны прикрепляются бок о бок к одному ходу кривошипа, что упрощает конструкцию кривошипа.
Конфигурация и количество поршней относительно друг друга и кривошипа приводит к прямым, V-образным или плоским двигателям. Однако один и тот же базовый блок двигателя может использоваться с разными коленчатыми валами для изменения порядка зажигания; например, конфигурация двигателя V6 под углом 90 градусов, обычно получаемая с использованием шести цилиндров двигателя V8 с укороченной версией коленчатого вала V8, создает двигатель с присущей ему пульсацией потока мощности из-за «недостающих» двух цилиндры, часто уменьшенные за счет использования балансирных валов.Однако тот же двигатель можно сделать так, чтобы он обеспечивал равномерно распределенные импульсы мощности, используя коленчатый вал с индивидуальным ходом кривошипа для каждого цилиндра, разнесенный таким образом, чтобы поршни фактически смещены по фазе на 60 градусов друг от друга, как в двигателе GM 3800. Точно так же, в то время как серийные двигатели V8 используют 4 хода кривошипа, разнесенные на 90 градусов, в гоночных двигателях часто используется «плоский» коленчатый вал с разнесением ходов на 180 градусов, что обеспечивает более высокий и плавный звук двигателей IRL по сравнению, например, с двигателями NASCAR. В двигателях, отличных от плоской конфигурации, необходимо предусмотреть противовесы для возвратно-поступательного движения каждого поршня и шатуна; они обычно отливаются как часть коленчатого вала, но иногда их изготавливают на болтах. Это значительно увеличивает вес коленчатого вала; коленчатые валы плоских двигателей Volkswagen, Porsche и Corvair, не имеющие противовесов, легко переносятся вручную, по сравнению с коленчатыми валами рядных или V-образных двигателей, которые необходимо обрабатывать и перевозить как тяжелые куски металла.
Многие ранние авиационные двигатели (и несколько других применений) имели коленчатый вал, прикрепленный к корпусу, а вместо этого вращались цилиндры, известная как конструкция роторного двигателя.
В двигателе Ванкеля роторы приводят в движение эксцентриковый вал, который можно рассматривать как эквивалент коленчатого вала в поршневом двигателе.
Коленчатые валы могут быть коваными или отлитыми из низкоуглеродистой или высокопрочной стали, либо изготовлены из цельной заготовки кованой стали. Низкоуглеродистая сталь используется только для двигателей в моделях или других подобных устройствах, где двигатель работает, но не подает питание.Литые коленчатые валы обычно используются в серийных двигателях, при этом кованые коленчатые валы и коленчатые валы с заготовками более дорогие, но надежные для более высокой производительности. Черновая отливка или поковка обрабатываются по размеру и форме, отверстия просверливаются, шейки коренных и шатунных подшипников прецизионно отшлифованы и закалены, а соответствующие отверстия имеют резьбу.
Анализ напряжений коленчатого вала [править | править источник]
Коленчатый вал подвергается воздействию различных сил, но его необходимо проверять в двух положениях.Во-первых, выход из строя может произойти в положении максимального изгиба. В таком состоянии выход из строя происходит из-за изгиба, а давление в цилиндре максимальное. Во-вторых, кривошип может выйти из строя из-за скручивания, поэтому шатунную шейку необходимо проверить на срез в положении максимального скручивания. Давление в этом положении — это не максимальное давление, а часть максимального давления.
Определение коленчатого вала Merriam-Webster
кривошип · вал | \ ˈKraŋk-ˌshaft \ 1 : вал, приводимый в движение кривошипом. 2 : вал, состоящий из ряда кривошипов и кривошипов, к которым прикреплены шатуны двигателя.Причины отказа и несоосности коленчатого вала судовых двигателей
Коленчатый вал — это промежуточная часть морского двигателя, которая передает мощность рабочего цилиндра от поршневого поршня на вращающийся гребной винт (или генератор переменного тока в случае генератора).
Работа других компонентов двигателя зависит от правильного вращения коленчатого вала, например, распределительного вала для определения времени подачи топлива, порядка запуска агрегатов и т. Д. Отказ одной части коленчатого вала может привести к остановке двигателя, а также корабля.
Как морской инженер, работающий на судне, следует знать различные причины, которые могут привести к выходу из строя этого важного узла.
Причины выхода из строя коленвала
Усталостный отказ: В большинстве случаев стальной коленчатый вал выходит из строя из-за усталостного разрушения, которое может возникнуть при изменении поперечного сечения, например, на кромке масляного отверстия, просверленного в шатунной шейке.
Отказ из-за вибрации : Если двигатель работает с сильной вибрацией, особенно крутильной, это может привести к трещинам в шатунной шейке и шейке
Недостаточная смазка : Недостаточная смазка подшипника коленчатого вала может привести к протиранию подшипника и выходу из строя коленчатого вала.
Цилиндр избыточного давления: Может случиться так, что внутри гильзы есть гидравлический затор (утечка воды), и из-за чрезмерного давления коленчатый вал может проскользнуть или даже погнуться (если предохранительный клапан этого блока не работает).
Трещины : Трещины могут развиваться на галтели между цапфой и перегородкой, особенно между положением, соответствующим 10 часам и 2 часам, когда поршень находится в положении T.D.C.
Причины несоосности коленчатого вала
Коленчатый вал судового двигателя является массивным компонентом, когда он полностью собран в двигателе. Первоначально весь коленчатый вал выравнивается по прямой линии (соединение, проведенное из центра коленчатого вала, образует прямую линию) перед установкой его на верхнюю часть коренных подшипников.
Но со временем из-за различных факторов прямая линия может отклоняться и смещаться. Степень смещения допустима в определенных пределах, но если значение выходит за пределы, указанные производителем; это может привести к повреждению или даже поломке коленчатого вала.
Причины перекоса коленчатого вала —
.- Повреждение или износ коренного подшипника
- Ослабленный фундаментный болт двигателя, приводящий к вибрации
- Деформация корпуса судна
- Трещина в опоре подшипника
- Ослабление болта коренного подшипника, ведущее к повреждению коренного подшипника
- Очень высокий изгибающий момент на коленчатом валу из-за чрезмерного усилия со стороны поршневого узла
- Посадка корабля на мель
- Взрыв или пожар картера
- Неисправные или изношенные подшипники кормовой трубы или промежуточного вала
- Ослабленные или сломанные штуцеры в фундаменте
- Карманы подшипников с трещинами
- Опорная плита деформирована — повреждена поперечная балка
- Стяжные болты ослаблены или сломаны
- Ослабление конструкции из-за коррозии
Таким образом, рекомендуется регулярно проверять картер и отклонение коленчатого вала (для проверки несоосности).
Изображение предоставлено:
максчевый
Новый коленчатый вал для V8
Тесты, которые больше всего выигрывают от Crankshaft, — это Richards, DeltaBlue и Crypto. Это показывает, что мы подняли производительность доступа к свойствам JavaScript, арифметических операций, жестких циклов и вызовов функций на новый уровень. В целом, Crankshaft повышает производительность V8 на 50% по результатам тестов V8. Это самое большое улучшение производительности с момента запуска Chrome в 2008 году.Помимо повышения пиковой производительности, измеренной с помощью набора тестов V8, Crankshaft также улучшает время запуска веб-приложений, таких как GMail.

Crankshaft использует адаптивную компиляцию для улучшения как времени запуска, так и максимальной производительности. Идея состоит в том, чтобы сильно оптимизировать код, который часто выполняется, и не тратить время на оптимизацию кода, который не выполняется.Из-за этого тесты, которые завершаются всего за несколько миллисекунд, такие как SunSpider, не покажут улучшения с Crankshaft. Чем больше работы выполняет приложение, тем больше будет выигрыш.
Коленчатый вал состоит из четырех основных компонентов:
- Базовый компилятор , который изначально используется для всего кода. Базовый компилятор быстро генерирует код без серьезных оптимизаций. Компиляция с базовым компилятором выполняется в два раза быстрее, чем с компилятором V8 в Chrome 9, и генерирует на 30% меньше кода.
- Профилировщик времени выполнения , который контролирует работающую систему и определяет «горячий» код, то есть код, на выполнение которого мы тратим значительную часть времени.
- Оптимизирующий компилятор , который перекомпилирует и оптимизирует горячий код, идентифицированный профилировщиком времени выполнения. Он использует статическую форму одиночного назначения для выполнения таких оптимизаций, как перемещение кода с инвариантным циклом, выделение регистров линейного сканирования и встраивание. Решения по оптимизации основаны на информации о типе, собранной во время выполнения кода, созданного базовым компилятором.
- Поддержка деоптимизации , которая позволяет оптимизирующему компилятору быть оптимистичным в предположениях, которые он делает при генерации кода. С поддержкой деоптимизации можно отказаться от кода, сгенерированного базовым компилятором, если предположения в оптимизированном коде окажутся слишком оптимистичными.
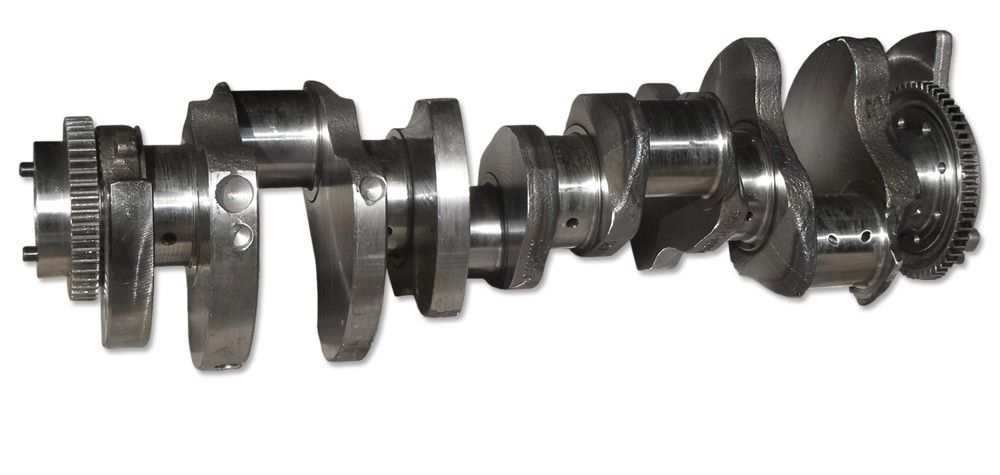
Мы очень рады улучшениям скорости JavaScript, которые мы сегодня доставляем с Crankshaft. Crankshaft обеспечивает отличную инфраструктуру для следующей волны улучшений скорости JavaScript в V8, и мы продолжим повышать производительность JavaScript, чтобы обеспечить следующее поколение веб-приложений.
Кевин Милликин, инженер-программист и Флориан Шнайдер, инженер-программист
Сегодня мы представляем Crankshaft, новую инфраструктуру компиляции для V8, движка JavaScript Google Chrome.Используя агрессивную оптимизацию, Crankshaft значительно улучшает производительность требовательных к вычислениям приложений JavaScript — часто более чем в два раза! Это позволит пользователям быстрее и быстрее реагировать на загрузку веб-страниц и приложений, созданных с использованием сложного JavaScript. Вот сравнение Chrome с коленчатым валом и без него в тестовом наборе V8: Тесты, которые больше всего выигрывают от Crankshaft, — это Richards, DeltaBlue и Crypto. Это показывает, что мы подняли производительность доступа к свойствам JavaScript, арифметических операций, жестких циклов и вызовов функций на новый уровень.В целом, Crankshaft повышает производительность V8 на 50% по результатам тестов V8. Это самое большое улучшение производительности с момента запуска Chrome в 2008 году.Помимо повышения пиковой производительности, измеренной с помощью набора тестов V8, Crankshaft также улучшает время запуска веб-приложений, таких как GMail. Наши тесты цикличности страниц показывают, что Crankshaft улучшает скорость загрузки страниц в Chrome на 12% для страниц, содержащих значительное количество кода JavaScript.
Crankshaft использует адаптивную компиляцию для улучшения как времени запуска, так и максимальной производительности.Идея состоит в том, чтобы сильно оптимизировать код, который часто выполняется, и не тратить время на оптимизацию кода, который не выполняется. Из-за этого тесты, которые завершаются всего за несколько миллисекунд, такие как SunSpider, не покажут улучшения с Crankshaft. Чем больше работы выполняет приложение, тем больше будет выигрыш.
Коленчатый вал состоит из четырех основных компонентов:
- Базовый компилятор , который изначально используется для всего кода. Базовый компилятор быстро генерирует код без серьезных оптимизаций.Компиляция с базовым компилятором выполняется в два раза быстрее, чем с компилятором V8 в Chrome 9, и генерирует на 30% меньше кода.
- Профилировщик времени выполнения , который контролирует работающую систему и определяет «горячий» код, то есть код, на выполнение которого мы тратим значительную часть времени.
- Оптимизирующий компилятор , который перекомпилирует и оптимизирует горячий код, идентифицированный профилировщиком времени выполнения. Он использует статическую форму одиночного назначения для выполнения таких оптимизаций, как перемещение кода с инвариантным циклом, выделение регистров линейного сканирования и встраивание.Решения по оптимизации основаны на информации о типе, собранной во время выполнения кода, созданного базовым компилятором.
- Поддержка деоптимизации , которая позволяет оптимизирующему компилятору быть оптимистичным в предположениях, которые он делает при генерации кода. С поддержкой деоптимизации можно отказаться от кода, сгенерированного базовым компилятором, если предположения в оптимизированном коде окажутся слишком оптимистичными.
Мы очень рады улучшениям скорости JavaScript, которые мы сегодня доставляем с Crankshaft. Crankshaft обеспечивает отличную инфраструктуру для следующей волны улучшений скорости JavaScript в V8, и мы продолжим повышать производительность JavaScript, чтобы обеспечить следующее поколение веб-приложений.
Кевин Милликин, инженер-программист и Флориан Шнайдер, инженер-программист
1W5009 | КОЛЕНВАЛ С ШЕСТЕРНЮ | 3408, 3408B, 3408C, 3408E | 589, 631D, 631E, 631G, 633D, 633E II, 637D, 637E, 637, 69D, 637E, 637 768C, 769C, 769D, 771C, 771D, 834B, 836, 988B, 988F, 988F II, AD40, AD45, AE40, AE40 II, CG137-08 | ||||||||
1W6209 | КОЛЕНЧАТЫЙ ВАЛ С ШЕСТЕРНЯ 34084 | 905 905 , 988B||||||||||
1W6213 | КОЛЕНВАЛ AW / ШЕСТЕРНЯ | 3412, G3412 | D9L | ||||||||
1W9771 | КОЛЕНВАЛ | 3204 926, 931 | |||||||||
1070992 | КОЛЕНЧАТКА В СОСТОЯНИИ | 3046 | 933, 939, 939C, D3C III, D3G, D4C III, D4G, D5C III, D5G | ||||||||
11728 CRANSHA | , 315C, 317B LN, 318B, 933C, 939C | ||||||||||
1253005 | CR Анкерный вал с шестерней | 3066 | 318C, 319C, 320, 320B, 320B L, 320C, 320C FM, 320C L, 320D, 320D LRR, 320N, 321B, 321C, 323D L, 323D LN | ||||||||
1352419 | |||||||||||
1352419 | |||||||||||
1352419 | КОЛЕНВАЛ | 3064 | 311B, 311C, 312B, 312C, 312C L, 314C | ||||||||
1601799 | КОЛЕНВАЛ W ШЕСТЕРНЯ | 3406C, C-15, C-16, 824, 824, C15 , 825G II, 826G II, AD30, MTC835, R2900G | |||||||||
1694187 | КОЛЕНВАЛ | 3176C, C-10 | 345B, 480, 75D, 966G II, D7R II, R1600183 | КОЛЕНВАЛ С ШЕСТЕРНЯ | C-12 | 85D, 972G II | |||||
1894918 | КОЛЕНВАЛ С ШЕСТЕРНЯ | C-18, C18 | 24M, 385C, 385C LH, 385C L, 385C L, 385C L, 385C 390D, 390D L, 631E, 631G, 633E II, 637E, 637G, 657E, 657G, 772, 834H, 836H, 988H, AD45B, AD55, D9T, PM-200, PM-201 | ||||||||
2W4088 901 85 | КОЛЕНВАЛ AW / ШЕСТЕРНЯ | 3412, 3412C, 3412E, G3412, G3412C | 24H, 651E, 657E, 773B, 773D, 775B, 775D, 844, 990, 990 II, 992C, 992D, D10NL, D10R PR-1000, PR-750B, SCT673, SPS342, SPT342 | ||||||||
2327400 | КОЛЕНЧАТЫЙ ВАЛ | 3054C | 414E, 416D, 416E, 420D, 420E, 422E, 424D, 430D, 428D, 428D 432E, 434E, 442D, 442E, 444E, 914G, AP-300, AP-300D, AP-650B, AP-800D, C4.![]() | ||||||||
2611544 | КОЛЕНВАЛ С ШЕСТЕРНЮ | C-9 | 12H, 140M, 140M 2, 160M, 160M 2 , 2290, 2390, 2391, 2491, 2590, 330C, 330C FM, 330C L, 330C MH, 330D, 330D FM, 330D L, 330D LN, 330D MH, 336D, 336D L, 336D LN, 336D2, 336D2 L, 340D L, 340D2 L, 511 | ||||||||
2715658 | КОЛЕНВАЛ С ШЕСТЕРНЮ | 3116, 3126, 3126B, 3126E | 120H, 120H ES, 120H NA, 120K, 120K 2, 12K, 12M, 135H, 135H, 135H 140G, 140K, 140K 2, 140M, 160K, 214B, 30/30, 320B, 322B L, 322B LN, 322C, 322C FM, 324D, 324D FM, 324D FM LL | ||||||||
3133996 | ШЕСТЕРНЯ КОЛЕНЧАТОГО ВАЛА | ВКЛЮЧЕНО | C1114M, 725, 730, 966H, C11, R1600H, R1700G, RM-300, Th45-C11I | ||||||||
3133997 | КОЛЕНВАЛ С ШЕСТЕРНЯ | C13 | 16M, 345C, 345C, 345C 345D, 345D L, 345D L VG, 349D, 349D L, 621H, 621K, 623H, 623K LRC, 627H, 627K LRC, 730 , 730C, 972H, 980C, 980K, 980K HLG, C13, C13 XQ350, CX31-C13I, D8N, Th45-C13I, Th45-C1 | ||||||||
3216442 | КОЛЕНЧАТЫЙ ВАЛ | 33018 | 9019 902|||||||||
3348389 | КОЛЕНВАЛ W ШЕСТЕРНЯ | 3306, 3306B | 12G, 12H ES, 12H NA, 140G, 140H, 140H ES, 140H NA, 143H, 14G, 14H NA, 160G, 160H ES, 160H NA, 163H NA , 1673C, 330, 350, 528B, 530B, 615C, 627E, 627F, 637E, 815B, 966F, 966F II, 970F, 972G | ||||||||
3370201 | КОЛЕНВАЛ | C15 Th | 374 374 -C15T | ||||||||
3370872 | КОЛЕНВАЛ | G3304, G3304B | 120G, 130G, 3304, 3304B, 515, 517, 518C, 525, 527, D4H, D4H XL, D4HTSK III 9018 3442603 | КОЛЕНВАЛ | 3306, 3306B, 3306C | 12H, 12H ES, 12H NA, 140G, 140H, 140H ES, 140H NA, 143H, 14H NA, 160H, 160H ES, 160H NA, 163H NA, 235B, 330, 330B L, 350, 545, 572R, 611, 615C, 627B, 627F, 627G, 637E, 637G, 814F | |||||
3642828 | КОЛЕНВАЛ | 3054, 3054C | 312B, 416C L, 3 416D, 420D, 426C, 428B, 428C, 430D, 436C, 438C, 908, 914G, CB-434B, CB-434C, CB-535B, CB-544, CB-545, CP-433C, CS-323C, CS- 431C, IT14G, M312, M315, PS-150B | ||||||||
3645145 | КОМПЛЕКТ ШАЙБЫ | C7.![]() | 120M 2, 2384C, 2484C, 2570C, 2670C, 312E, 312E L, 314E CR, 314E LCR, 316E L, 318E L, 320D2, 320D2 GC, 320D2 L, 320E, 320E L, 320E LN, 320E LRR, 320E RR, 323D2 L, 323E L, 324E, 324E L, 324E LN, 329E | ||||||||
3849906 | КОЛЕНЧАТЫЙ ВАЛ | 3412, 3412C, 3412E | 24H, 5110BE, 651E 77, 77B, 77B, 77B , 775E, 844, 990, 990 II, 992C, C30, D10N, D10R, D9L, G3412, PM3412, PR-1000, SPS342, SPT342 | ||||||||
4N7692 | КОЛЕНЧАТЫЙ ВАЛ С ШЕСТЕРНЯМИ КОВАНА | , 130G, 215, 215B, 215C, 225, 225D, 229D, 3304, 518, 920, 930, 936, 941, 950, 950B, 950B / 950E, 951B, 955K, 955L, 963, CB-534, D4D, D4E , D5H, E240, FB518, G936 | |||||||||
4N7693 | КОЛЕНЧАТЫЙ ВАЛ С КОВАННОЙ ПЕРЕДАЧЕЙ | 3306, 3306B | 120B, 12G, 140G, 14G, 160G, 1673C, 235, 56C, 528 561D, 571G, 572G, 615, 615C, 627B, 637D, 639D, 814, 814B, 815, 815B, 816, 816B, 966C, 966D, 973, 977K, 977L, 980B, D250B | ||||||||
6I1453 | КОЛЕНЧАТЫЙ ВАЛ / ШЕСТЕРНЯ | 3406, 3406B, 3406C, 3406E | 16G, 16H NA, 245B, 375, 375 L, 5080, 587, 621R, 621R, 621E, 621R , 621G, 623E, 623F, 623G, 627B, 627E, 627F, 627G, 657B, 814B, 824C, 824G, 825G, 826C, 826G, 980C, 980F, 980G | ||||||||
6N2823 | ШАТУНКА ПЕРЕДАЧИ | 342, D342 | D8K | ||||||||
7C4859 | КОЛЕНЧАТЫЙ ВАЛ W / GR-FORGED | 3406, 3406B, G3406 | 16G, 578, 621E, 623E, 6275 9080, 814, 814, 814 | ||||||||
8M4505 | КОЛЕНЧАТЫЙ ВАЛ СТД | D330A | 955H, 955K, D4D | ||||||||
9M2337 | КОЛЕНЧАТЫЙ ВАЛ | 1673, 1673B18B62 9018 9018 9018, КОЛЕНЧАТЫЙ ВАЛ 9018 5 3208 | 225, 3208, 613B, 613C, FB221, PR-1000, PS-500 | ||||||||
6127-31-1012 901 85 | КОЛЕНЧАТЫЙ ВАЛ С ШЕСТЕРНЮ | S6D155, SA6D155 | |||||||||
6211-31-1010 | КОЛЕНЧАТЫЙ ВАЛ С ШЕСТЕРНЯ | S6D140, S6D140E, SA6D140, SA6D6D1401 9018 | |||||||||
6240-31-1101 | КОЛЕНВАЛ С ШЕСТЕРНЮ | SAA6D170E |
Коленчатый вал | История Wiki | Fandom

Коленчатый вал (красный), поршни (серые) в цилиндрах (синий) и маховик (черный)
Коленчатый вал , иногда сокращенно , коленчатый вал , является частью двигателя, которая выполняет возвратно-поступательное поступательное движение поршня. в ротацию. Чтобы преобразовать возвратно-поступательное движение во вращение, коленчатый вал имеет «ходы кривошипа» или «шатунные шейки», дополнительные опорные поверхности, ось которых смещена относительно оси кривошипа, к которым прикреплены «большие концы» шатунов каждого цилиндра.
Обычно он соединяется с маховиком для уменьшения характеристики пульсации четырехтактного цикла, а иногда и с демпфером крутильных колебаний или колебаний на противоположном конце, чтобы уменьшить крутильные колебания, часто вызываемые по длине коленчатого вала наиболее удаленными цилиндрами. от выходного конца, действующего на крутильную упругость металла.
Самое раннее использование кривошипа в машине произошло в веялке с кривошипным приводом из Китая во время династии Хань (202 г. до н.э. — 220 г. н.э.). [1] Кривошипный механизм впервые был использован на водяной мельнице в поздней античности. Доказательства появляются на рельефе конца III века лесопилки из Иераполиса, Малая Азия. [2] Две лесопильные фабрики VI века, раскопанные в Эфесе, Малая Азия, и Герасе, Иордания, работали с аналогичным механизмом. [2] В Китае в 5 веке появились кривошипно-шатунные механизмы, а в 6-м веке — кривошипно-шатунные механизмы со штоком поршня. [3] В 9 веке немеханический кривошип появляется в нескольких гидравлических машинах, описанных братьями Бану Муса в их Книге изобретательных устройств . [4] Эти автоматически приводимые в действие кривошипы присутствуют в нескольких устройствах, описанных в книге, два из которых имеют действие, приближенное к коленчатому валу. Автоматический кривошип братьев Бану Муса не позволил бы полностью вращаться, но потребовалась лишь небольшая модификация, чтобы преобразовать его в коленчатый вал. [5]
Hhhh Устройство, показанное в манускрипте Каролингов в начале 9 века Утрехтский Псалтырь — это рукоятка, используемая с вращающимся точильным камнем. [6] Ученые указывают на использование кривошипных рукояток в трепанационных сверлах в работе 10 века испанского хирурга-мусульманина Абу аль-Касима аль-Захрави (936–1013). [6]
Коленчатый вал [редактировать | править источник]
В 1206 году арабский изобретатель Аль-Джазари описал самый ранний известный коленчатый вал, который он соединил с кривошипно-шатунным механизмом в своем двухцилиндровом насосе. Механизм Аль-Джазари состоял из колеса, приводившего в движение несколько шатунов. [7] В его водяном насосе также использовался первый известный кривошипно-скользящий механизм. [8]
Коленчатые валы позже были описаны Конрадом Кизером (ум. 1405), Франческо ди Джорджио (1439–1502), Леонардо да Винчи (1452–1519) и Таки ад-Дином, который включил их в шестицилиндровый двигатель. Цилиндровый насос в 1551 году. Голландский «фермер» Корнелис Корнелизоон ван Юитгест также описал коленчатый вал в 1592 году. Его ветряная лесопилка использовала коленчатый вал, чтобы преобразовать круговое движение ветряной мельницы в движение вперед и назад, приводящее в действие пилу.Corneliszoon получил патент на коленчатый вал в 1597 году.
Файл: Диаграмма четырехтактного двигателя .jpgКомпоненты типичного четырехтактного поршневого двигателя DOHC. (E) Выпускной распредвал, (I) Впускной распределительный вал, (S) Свеча зажигания, (V) Клапаны, (P) Поршень, (R) Шатун, (C) Коленчатый вал, (W) Водяная рубашка для потока охлаждающей жидкости.
Большие двигатели обычно являются многоцилиндровыми, чтобы уменьшить пульсации от отдельных тактов зажигания, с более чем одним поршнем, прикрепленным к сложному коленчатому валу.Многие небольшие двигатели, такие как двигатели мопедов или садовой техники, являются одноцилиндровыми и используют только один поршень, что упрощает конструкцию коленчатого вала. Этот двигатель также может быть построен без заклепочного шва.
[править | править источник]
Коленчатый вал имеет линейную ось, вокруг которой он вращается, обычно с несколькими шейками подшипников, установленными на сменных подшипниках (основных подшипниках), удерживаемых в блоке двигателя. Поскольку коленчатый вал подвергается значительной боковой нагрузке от каждого цилиндра в многоцилиндровом двигателе, он должен поддерживаться несколькими такими подшипниками, а не только по одному на каждом конце.Это было одним из факторов, способствовавших развитию двигателей V8 с их более короткими коленчатыми валами, по сравнению с двигателями с восьмеркой. Длинные коленчатые валы последних страдали от недопустимой степени прогиба, когда конструкторы двигателей начали использовать более высокие степени сжатия и более высокие скорости вращения. По этой причине двигатели с высокими рабочими характеристиками часто имеют больше коренных подшипников, чем их собратья с более низкими характеристиками.
Ход поршня [править | править источник]
Расстояние, на которое ось кривошипа отклоняется от оси коленчатого вала, определяет измерение хода поршня и, следовательно, рабочий объем двигателя.Обычный способ увеличить крутящий момент двигателя на низких оборотах — увеличить ход. Однако это также увеличивает возвратно-поступательную вибрацию, ограничивая возможности двигателя на высоких скоростях. В качестве компенсации он улучшает работу двигателя на низких оборотах, поскольку более длинный ход впуска за счет меньшего (ых) клапана (ов) приводит к большей турбулентности и перемешиванию всасываемого заряда. По этой причине даже такие высокоскоростные производственные двигатели, как современные двигатели Honda, классифицируются как «малоугольные» или длинноходные, так как их ход больше диаметра отверстия цилиндра.
Конфигурация двигателя [править | править источник]
Конфигурация и количество поршней относительно друг друга и кривошипа позволяет использовать прямые, V-образные или плоские двигатели. Однако один и тот же базовый блок двигателя может использоваться с разными коленчатыми валами для изменения порядка зажигания; например, конфигурация двигателя V6 под углом 90 градусов, которая в прежние времена иногда создавалась с использованием шести цилиндров двигателя V8 с укороченной версией коленчатого вала V8, производит двигатель с присущей ему пульсацией в потоке мощности из-за » отсутствуют «два цилиндра».Однако один и тот же двигатель можно сделать так, чтобы он обеспечивал равномерно распределенные импульсы мощности, используя коленчатый вал с индивидуальным ходом кривошипа для каждого цилиндра, разнесенный таким образом, чтобы поршни фактически смещены по фазе на 120 градусов, как в двигателе GM 3800. В то время как серийные двигатели V8 используют четыре хода кривошипа, разнесенные на 90 градусов, в высокопроизводительных двигателях V8 часто используется «плоский» коленчатый вал с разнесенными на 180 градусов ходами. Разницу можно услышать, поскольку плоские коленчатые валы приводят к тому, что двигатель имеет более плавный и более высокий звук, чем при поперечной плоскости (например, серия IRL IndyCar по сравнению с NASCAR Nextel Cup или Ferrari 355 по сравнению с Chevrolet Corvette) .См. Основную статью о коленчатых валах с крестообразным шлицем
[править | править источник]
Для некоторых двигателей необходимо предусмотреть противовесы для возвратно-поступательного движения каждого поршня и шатуна, чтобы улучшить балансировку двигателя. Обычно они отливаются как часть коленчатого вала, но иногда это детали на болтах. Хотя противовес значительно увеличивает вес коленчатого вала, он обеспечивает более плавную работу двигателя и позволяет достичь более высоких оборотов.
Роторные двигатели [править | править источник]
Многие ранние авиационные двигатели (и несколько других применений) имели коленчатый вал, прикрепленный к корпусу, а вместо этого вращались цилиндры, известная как конструкция роторного двигателя. Роторные двигатели, такие как двигатель Ванкеля, называются бес поршневыми роторными двигателями.
В двигателе Ванкеля, также называемом роторным двигателем, роторы приводят в движение эксцентриковый вал, который можно рассматривать как эквивалент коленчатого вала в поршневом двигателе.
Файл: Marine Crankshafts 8b03602r.jpgEngine Crankshafts, 1942 год
Коленчатые валы могут быть монолитными (цельными) или сборными из нескольких частей. Чаще всего встречаются монолитные коленчатые валы, но в некоторых двигателях меньшего и большего размера используются коленчатые валы в сборе.
Ковка и литье [править | править источник]
Коленчатые валы могут быть выкованы из стального прутка, обычно путем ковки на валках, или отлиты из высокопрочной стали. Сегодня все больше и больше производителей склоняются к использованию кованых коленчатых валов из-за их меньшего веса, более компактных размеров и лучшего демпфирования.В кованых коленчатых валах в основном используются стали с микролегированием ванадием, поскольку эти стали можно охлаждать на воздухе после достижения высокой прочности без дополнительной термообработки, за исключением поверхностного упрочнения поверхностей подшипников. Низкое содержание сплава также делает этот материал дешевле, чем высоколегированные стали. Также используются углеродистые стали, но они требуют дополнительной термообработки для достижения желаемых свойств. Железные коленчатые валы сегодня в основном используются в более дешевых двигателях (например, в дизельных двигателях Ford Focus), где нагрузки ниже.В некоторых двигателях также используются чугунные коленчатые валы для версий с малой мощностью, в то время как в более дорогих версиях с высокой мощностью используется кованая сталь.
Обработка [править | править источник]
Коленчатые валы также могут быть изготовлены из заготовки, часто с использованием прутка из высококачественной стали, переплавленной в вакууме. Несмотря на то, что поток волокна (локальные неоднородности химического состава материала, образующиеся во время литья) не повторяет форму коленчатого вала (что нежелательно), это обычно не проблема, поскольку стали более высокого качества, которые обычно трудно подделать, могут быть использовал. Эти коленчатые валы, как правило, очень дороги из-за снятия большого количества материала, которое необходимо выполнять с помощью токарных и фрезерных станков, высокой стоимости материала и необходимой дополнительной термообработки. Однако, поскольку не требуется дорогостоящая оснастка, этот метод производства позволяет производить небольшие партии коленчатых валов без больших затрат.
Усталостная прочность [править | править источник]
Усталостную прочность коленчатого вала обычно повышают за счет использования радиуса на концах каждого коренного подшипника и подшипника шатунной шейки.Радиус сам по себе снижает напряжение в этих критических областях, но, поскольку радиусы в большинстве случаев прокатываются, это также оставляет некоторое остаточное напряжение сжатия на поверхности, которое предотвращает образование трещин.
Закалка [править | править источник]
В большинстве производимых коленчатых валов используются поверхности подшипников с индукционной закалкой, поскольку этот метод дает хорошие результаты при низких затратах. Это также позволяет переточить коленчатый вал без повторной закалки. Но для высокопроизводительных коленчатых валов, в частности для коленчатых валов с заготовками, вместо этого используется нитридизация.Нитридизация происходит медленнее и, следовательно, дороже, и, кроме того, она предъявляет определенные требования к легирующим металлам в стали, чтобы можно было создавать стабильные нитриды. Преимущество нитридизации заключается в том, что ее можно проводить при низких температурах, она создает очень твердую поверхность, и в результате процесса на поверхности остается некоторое остаточное напряжение сжатия, что хорошо для усталостных свойств коленчатого вала. Низкая температура во время обработки выгодна тем, что не оказывает отрицательного воздействия на сталь, такого как отжиг.В коленчатых валах, которые работают на роликовых подшипниках, предпочтительнее науглероживание из-за высоких контактных напряжений Герца в таком применении. Как и азотирование, науглероживание также оставляет на поверхности некоторые остаточные напряжения сжатия.
Противовесы [править | править источник]
Некоторые дорогие высокопроизводительные коленчатые валы также используют противовесы из тяжелого металла, чтобы сделать коленчатый вал более компактным. В качестве тяжелого металла чаще всего используется вольфрамовый сплав, но также использовался обедненный уран.Более дешевый вариант — использовать свинец, но по сравнению с вольфрамом его плотность намного ниже.
Вал подвергается воздействию различных сил, но обычно его необходимо анализировать в двух положениях. Во-первых, выход из строя может произойти в положении максимального изгиба; это может быть в центре кривошипа или на любом конце. В таком состоянии выход из строя происходит из-за изгиба, а давление в цилиндре максимальное. Во-вторых, кривошип может выйти из строя из-за скручивания, поэтому необходимо проверить шатун на сдвиг в положении максимального скручивания.Давление в этом положении — это максимальное давление, но только часть максимального давления. ==
- ↑ Н. Сивин (август 1968 г.), «Обзор: Наука и цивилизация в Китае Джозефа Нидхэма», Журнал азиатских исследований (Ассоциация азиатских исследований) 27 (4): 859-864 [ 862], http://www.jstor.org/stable/2051584
- ↑ 2,0 2,1 Ритти, Туллия; Греве, Клаус; Кессенер, Пол (2007), «Рельеф водяной каменной пилы на саркофаге в Иераполе и его последствия», Journal of Roman Archeology 20 : 138–163 (161)
- ↑ Джозеф Нидхэм (1975), «История и человеческие ценности: китайский взгляд на мировую науку и технологию», Философия и социальные действия II (1-2): 1-33 [4], http: / / citeseerx.ist.psu.edu/viewdoc/download?doi=10.1.1.122.293&rep=rep1&type=pdf#page=12, получено 13 марта 2010 г.
- ↑ А. Ф.
Л. Бистон, М. Дж. Л. Янг, Дж. Д. Лэтэм, Роберт Бертрам Сержант (1990), Кембриджская история арабской литературы , Cambridge University Press, стр. 266, ISBN 0521327636
- ↑ Бану Муса, Дональд Рутледж Хилл (1979), Книга изобретательных устройств (Китаб аль-Чиял) , Springer, стр. 23-4, ISBN08339
- ↑ 6.0 6,1 Needham 1986, p. 112.
- ↑ Салли Ганчи, Сара Ганчер (2009), Ислам и наука, медицина и технологии , The Rosen Publishing Group, стр. 41, ISBN 1435850661
- ↑ Лотфи Ромдхан и Саид Зеглул (2010), «Аль-Джазари (1136–1206)», История механизмов и машиноведения (Springer) 7 : 1-21, DOI: 10.1007 / 978-90- 481-2346-9, ISBN 978-90-481-2346-9, ISSN 1875-3442
Шаблон: внешние ссылки
T&C Surf — коленчатый вал
Шортборд для малых волн с высокими характеристиками.Более полные очертания с низким входным рокером, позволяющим доске ровно проходить через плоские поверхности, хвостовой качающийся рычаг позволяет доске по-прежнему плотно поворачиваться в кармане. Следует заказывать по крайней мере на дюйм короче и немного шире, чем ваши обычные размеры. У него глубокая одинарная вогнутость с небольшим V-образным вырезом на хвосте.
Размеры
Длина | Нос | Ширина | Хвост | Толщина | Объем |
---|---|---|---|---|---|
5’9 ” | 12.39 | 18 ”1/2 | 14,54 | 2 дюйма 3/16 | 24,4 |
5’11 ” | 12,50 | 19 дюймов | 12,39 | 2 дюйма 5/16 | 27,3 |
6’0 ” | 12,55 | 19 ”1/4 | 14,78 | 2 дюйма 3/8 | 28,9 |
6’1 ” | 12,44 | 19 ”1/4 | 14.![]() |