Ремонт и техническое обслуживание кривошипно-шатунного механизма
Ремонт кривошипно-шатунного механизма заключается в замене или ремонте его деталей. Ремонт, как правило, осуществляется со снятием двигателя с автомобиля. Не снимая двигатель с автомобиля, можно только производить снятие или установку крышки головки блока цилиндров, головки блока цилиндров, поддона масляного картера, а также замену их прокладок. При установке вышеперечисленных деталей затяжка гаек и болтов их крепления осуществляется в определенном порядке в соответствии с общим правилом крепления корпусных деталей: от центра к периферии методом крест-накрест. Такой способ затяжки позволяет обеспечить герметичность креплений и всего механизма.
Крышку головки цилиндров снимают и устанавливают в том случае, если есть необходимость замены или ремонта головки цилиндров двигателя, при подтяжке гаек и болтов ее крепления, при замене прокладки головки блока. Кроме того, крышку головки цилиндров необходимо снимать при техническом обслуживании и ремонте газораспределительного механизма (регулировке зазоров клапанов, замене маслоотражательных колпачков и других деталей газораспределения). Снятие и установка крышки цилиндра производится аккуратно, чтобы не повредить прокладку крышки, кроме того, при ремонте двигателя желательно иметь запасную прокладку крышки для замены в случае повреждения ее при разборке или на тот случай, если старая прокладка окажется поврежденной в процессе эксплуатации двигателя. Кроме этого запасная прокладка может понадобиться в том случае, если старая резиновая прокладка потеряет свои уплотняющие свойства из-за затвердевания.
Снятие и установка головки блока цилиндров осуществляется в том случае, если необходимо произвести ее замену, при замене прокладки головки, ремонте газораспределительного механизма. Кроме этого головку блока цилиндров снимают в том случае, когда осуществляют удаление нагара со стенок камер сгорания и с днища поршней, а также если применение специальных веществ для удаления нагара не приносит результатов. Признаками отложения нагара являются перегрев двигателя и продолжение работы в течение нескольких секунд после выключения зажигания. Для того чтобы снять головку блока цилиндров, необходимо сначала слить охлаждающую жидкость, потом снять приборы, установленные на головке; отвернуть болты, при помощи которых она крепится к двигателю. После этого можно аккуратно снять головку, чтобы не повредить прокладку. В том случае, если прокладка прилипла к головке цилиндров, ее отделяют при помощи тонкой металлической пластины или тупого ножа. При удалении нагара нужно поочередно установить поршни в ВМТ, затем размягчить нагар ветошью, смоченной керосином, и после этого удалить образовавшийся нагар скребком из мягкого металла или из дерева. При удалении нагара со стенок камеры сгорания необходимо проделать те же самые операции.
Установка головки цилиндров производится в обратной последовательности. Перед установкой старой прокладки ее нужно натереть порошкообразным графитом для обеспечения герметичности. Однако лучше всего при каждом снятии-установке головки блока цилиндров производить замену старой прокладки на новую. После установки головки блока цилиндров необходимо произвести затяжку ее креплений к блоку. Затяжка креплений осуществляется на холодном двигателе при помощи динамометрического ключа с определенным моментом и в определенной последовательности. В процессе эксплуатации двигателя головка не нуждается в дополнительном подтягивании крепежных элементов, благодаря применению специальных болтов и установки безусадочной прокладки. Для ремонта и замены остальных деталей кривошипно-шатунного механизма необходимо снять двигатель с автомобиля и произвести полную или частичную его разборку. Для того чтобы определить пригодность детали к ее дальнейшему применению, необходимо произвести проверку технического состояния деталей кривошипно-шатунного механизма.
Проверка технического состояния блока цилиндров заключается в тщательном визуальном контроле целостности блока, в измерении величин его деформации, а также износов поверхностей цилиндров и отверстий под коренные подшипники. Перед проверкой технического состояния блок цилиндров нужно тщательно очистить, а также промыть все его внутренние полости (особенно каналы смазочной системы) горячим раствором каустической соды при температуре 75-85 °С. Если на блоке цилиндров имеются повреждения (трещины, пробоины, сколы), то блок, как правило, подлежит немедленной замене. Небольшие трещины заделывают эпоксидным составом или устраняют при помощи сварки. В процессе определения деформации блока цилиндров осуществляется контроль соосности отверстий под коренные подшипники, а также неплоскостности его разъема с головкой блока цилиндров.
Неплоскостность разъема блока с головкой цилиндров проверяют при помощи набора щупов, линейки или поверочной плиты. Линейку устанавливают по диагоналям плоскости разъема и посередине в продольном и поперечном направлениях. После этого при помощи подложенного под нее щупа определяют величину зазора между щупом и линейкой. Блок считается пригодным для дальнейшего применения, если величина зазоров не превышает 0,1 мм. Если величина зазора.не превышает 0,14 мм, то плоскость разъема необходимо прошлифовать для устранения ее неплоскостности. При зазоре более 0,14 мм блок цилиндров подлежит замене. .
Несоосность отверстий коренных подшипников проверяется при помощи специальной оправки. Для проверки необходимо вставить оправку в отверстие коренного подшипника. Если оправка вставляется одновременно во все отверстия коренных подшипников, то блок считается пригодным для дальнейшего применения, если оправка не вставляется одновременно во все отверстия, то блок цилиндров необходимо заменить на новый.
После этого необходимо провести измерение диаметров цилиндров и отверстий под коренные подшипники. Для этой операции применяют индикаторный нутромер. Если износ отверстий превышает допустимые значения, то блок цилиндров либо меняется на новый, либо растачивается под ближайший ремонтный размер. После такой расточки в блок цилиндров устанавливают поршни и поршневые кольца, соответствующие ремонтному размеру.
Проверка технического состояния коленчатого вала осуществляется для того, чтобы выявить наличие трещин, следы повышенного износа поверхности резьбы. Перед проверкой коленчатый вал необходимо снять с двигателя, тщательно промыть. Кроме этого нужно прочистить и продуть полости масляных каналов, предварительно отвернув пробки масляных каналов. Если в процессе визуального осмотра вала обнаруживаются трещины, вал подлежит замене. При срыве резьбы не более двух ниток производится ее прогонка. После этого производится измерение диаметров коренных и шатунных шеек и делается заключение о дальнейшем использовании вала, о возможности перешлифования шеек под ремонтные размеры или о замене вала на новый. Замер шейки коленчатого вала осуществляется при помощи микрометра по двум поясам в двух взаимно перпендикулярных плоскостях. Перешлифовка всех одноименных шеек осуществляется под один ремонтный размер. Кроме этого при проверке технического состояния коленчатого вала измеряется биение в креплениях маховика и оси вала при помощи микрометрической индикаторной головки при прокручивании коленчатого вала. Эта проверка позволяет контролировать перпендикулярность торцевой поверхности фланца.
Контроль технического состояния маховика осуществляется по состоянию поверхности плоскости прилегания ведомого диска сцепления, а также по состоянию ступицы и зубчатого обода. Плоскость прилегания ведомого диска должна быть без рисок и задиров. Кроме этого проверяется биение плоскости маховика в сборе с коленчатым валом. Оно не должно превышать 0,10 мм на крайних точках. Если биение превышает допустимые значения, нужно прошлифовать плоскость прилегания либо необходимо заменить маховик. Маховик также подлежит замене при наличии на нем трещин. Если на зубьях обода маховика присутствуют забои, то их следует зачистить, а при значительном износе или при повреждении обод маховика меняют на новый. Новый обод необходимо разогреть до температуры в 200-230 °С и затем напрессовать на маховик.
После первых 1500-2000 км пробега необходимо подтянуть гайки шпилек и болты головки блока цилиндров. В дальнейшем эту операцию необходимо проделывать только после снятия головки блока цилиндров, при появлении признаков прорыва газов или подтекания охлаждающей жидкости. Кроме этого вместе с подтяжкой гаек и болтов крепления головки блока цилиндров нужно подтягивать винты или болты крепления поддона картера двигателя.
Через каждые 10 000-15000 км пробега нужно проверять и при необходимости подтягивать болты и гайки крепления опор двигателя, а также очищать их резиновые подушки. Кроме того, по мере накопления пыли и грязи следует протирать поверхность двигателя ветошью, смоченной специальным очистителем.
Ремонт КШМ и ГРМ — Инструкции по эксплуатации и ремонту автомобилей МАЗ на Мазбука.ру
2.3 Ремонт кривошипно-шатунного и газораспределительных механизмов двигателя
Снятие и установка головки цилиндров
Для замены головки цилиндров и её деталей, а также деталей цилиндропоршневой группы, прокладки головки цилиндров, клапанов и сёдел клапанов снятие головки цилиндров необходимо произвести в следующей последовательности:
слить из системы охлаждения двигателя охлаждающую жидкость;
отсоединить все трубопроводы от головки цилиндров и защитить их внутренние полости от попадания пыли и грязи;
снять крышку головки цилиндров, а затем форсунки, предохраняя распылители от ударов и засорения отверстий;
снять ось коромысел вместе с коромыслами и вытянуть штанги;
ослабить гайки крепления головки цилиндров, соблюдая ту же последовательность, что и при затяжке (см. рис 4), а затем отвернуть их;
снять головку цилиндров с двигателя и проверить её состояние;
снять осторожно прокладку головки цилиндров избегая повреждений, при необходимости при сборке заменить прокладку.
Головку цилиндров заменяют при наличие трещин, проходящих через отверстия под направляющие втулки клапанов, отверстия под стаканы форсунок и гнёзда под сёдла клапанов, трещин на стенках рубашки охлаждения в местах, недоступных для ремонта. Наличие трещин определяется внешним осмотром (Старым (дедовским) испытанным способом проверки является обрызгивание топливом поверхности головки цилиндров между клапанами при работающем двигателе. В местах прорыва, трещин головки наблюдается выход воздуха. Но при этом необходимо проявлять осторожность вследствие снятия крышки клапанов и работе двигателя). Также провести проверку головок цилиндров на герметичность водой под давлением 4кгс/см².
Герметичность рубашки охлаждения можно проверить, подведя к ней воздух и опустив головку цилиндров в ванну с водой. Трещины и пробоины на головке цилиндров не допускаются. Допускаются лишь мелкие трещины на привалочных поверхностях между отверстиями под распылители форсунок и клапаны, не захватывающие рабочие фаски впускного клапана и не нарушающие герметичность. Если при испытании головки цилиндров на герметичность обнаружится нарушение уплотнения стакана форсунки, следует подтянуть гайку крепления стакана. Если при этом течь не устраняется, стакан снимают и заменяют уплотнительное кольцо и шайбу, а в случае необходимости и стакан. Гайку крепления стакана форсунки затягивают моментом 9-11кгс.м. Головку цилиндров устанавливают на двигатель в последовательности, обратной разборке. При этом привалочные поверхности головки блока цилиндров и блока необходимо протереть чистой ветошью, обращая внимание на правильность установки прокладки головки цилиндров на штифты и окантовок прокладки на бурты гильз цилиндров. Гайки крепления головок цилиндров затягивают в порядке возрастания номеров, как показано на рис.
4 с приложением момента 22-24 кгс.м. После первой затяжки необходимо повторной операцией проверить требуемый крутящий момент на каждой гайке, соблюдая указанную последовательность.
Замена деталей шатунно-поршневой группы
При нормальных износах деталей цилиндро-поршневой группы (отсутствие трещин, задиров и т. д) поршень, гильзу, палец и кольца, как правило, заменяют одновременно. Поршневые кольца обычно приходится менять чаще, чем весь комплект.
Для снятия поршней и гильз с двигателя необходимо:
установить автомобиль на смотровую канаву и слить масло и охлаждающую жидкость из двигателя;
снять головки цилиндров и поддон картера двигателя;
отогнуть замковые шайбы и отвернуть болты крепления крышек нижних головок шатунов, убедитесь меток спаренности на стыке со стороны длинного болта (при отсутствии меток или плохой видимости, их необходимо нанести вновь). При сборке замены крышек или переустановка их в другие места не допускается:
снять поршень в сборе с шатуном через цилиндр, а затем гильзы из блока цилиндров при помощи приспособления (см. рис 5).
Для разборки комплекта поршень-шатун необходимо:
снять кольца с поршня специальными щипцами (см.рис 6), ограничивающими расширение кольца до диаметра 142,5мм;
вытянуть стопорное кольцо поршневого пальца круглогубцами;
вытянуть поршневой палец, предварительно выдержав поршень в сборе с шатуном в масле в течение 10мин при температуре масла 80-100°С.
После разборки поршень и кольца очищают от нагара и промывают (очищают) отверстия для отвода масла. После очистки детали тщательно промеряют и выявляют дефекты.
Замена поршней и гильз
Номинальный зазор между внутренней поверхностью гильзы и юбкой поршня в холодном состоянии должен быть 0,19-0,22мм. Если зазор превышает 0,45мм поршневую группу нужно заменить. Гильзу цилиндров заменяют, если имеются трещины, обломы, задиры внутренней поверхности, вмятины и забоины на буртике, кавитационные раковины выходящие на канавки под уплотнительные кольца, если внутренний диаметр в результате износа превышает 130,18мм (при установке в гильзу поршня с поршневыми кольцами, которые не работали до разборки, диаметр можно увеличить до 130,25мм), овальность и конусность гильзы превышает 0,06мм. Диаметр следует замерять в двух взаимно перпендикулярных направлениях. Поршень заменяют, если есть задиры на боковой поверхности, выгорания на днище поршня, трещины, если диаметр юбки поршня меньше 129,6мм (замер следует делать в плоскости перпендикулярной поршневым пальцам, на расстоянии 153мм от днища поршня), если есть задиры на поверхности отверстия под поршневой палец, диаметр отверстия под поршневой палец превышает 50,03мм, а овальность и конусность отверстия превышает 0,015 мм, торцевые зазоры между новыми поршневыми кольцами и канавками поршня превышает: для верхнего компрессионного кольца (размер «а» рис. 7) 0,35мм, для второго и третьего компрессионных колец (размер «б») 0,30мм, для масленых колец (размер «в») 0,25мм. Для замеров торцевых зазоров поршень в сборе с новыми кольцами вставляют в калиброванную шайбу с внутреннем диаметром 130,00-130,01мм. Замер нужно производить одновременно с двух диаметрально противоположных сторон поршня.
Замена поршневых колец
Поршневые кольца заменяют при расходе масла двигателем, превышающим 3% расхода топлива и повышенном дымление через сапун. Если вышеуказанные явления не наблюдаются, а двигатель по каким – либо причинам поступил в текущий ремонт, то кольца заменяют только при наработке двигателем более 150тыс. км, полностью или частично сработанных канавках на рабочей поверхности второго и третьего компрессионных колец, наличии задиров на внешне цилиндрической поверхности.
Замена поршневого пальца
Поршневой палец заменяют при наличии грубых рисок, задиров, наволакиваний металлов и прожогах, если наружний диаметр менее 49,98мм, а овальность и конусность превышают 0,015мм.
Замена шатуна
Шатун заменяют при наличии трещин. Если внутренний диаметр отверстия головки шатуна (под втулку), который должен быть не более 56,04мм. Проверять диаметр нужно как при ослаблении посадки, так и при повороте втулки. При запрессовке новой втулки натяг должен быть в пределах 0,5-0,12мм. Внутренний диаметр нижней головки шатуна проверяют после контрольной затяжки шатунных болтов с моментом 20-22кгс. м. Предельно допустимый диаметр должен составлять 92,98-93,05мм, если среднее арифметическое диаметров в плоскости стыка и сечении, перпендикулярном стыку, не выходит за пределы 93,00-93,021мм. Ширина нижней кривошипной головки должна быть не менее 41,25мм. При меньшей ширине нижней головки шатуна следует заменить. Непараллельность осей отверстий верхних и нижней головок шатуна (изгиб) без ремонта допускается не более 0,08мм на длине 100мм, а отклонение осей указанных отверстий от положения одной плоскости (скручивание) не более 0,1мм на длине 100мм. Если не параллельность и скручивание осей верхней и нижней головок шатуна выше допустимых, шатун нужно заменить. Допускается установка новой втулки в отверстие верхней головки с последующей расточкой внутреннего диаметра до 50+0,040мм, обеспечив при этом отклонение от параллельности осей не более 0,04мм на длине 100мм, положение осей в одной плоскости в пределах 0,04мм на длине 100мм и расстояние между указанными осями 265±0,04мм. Правка шатуна не допускается.
При ремонте запрещается установка крышек с другого шатуна. Проверять шатуны и крышки по меткам спаренности.
Сборка шатунно-поршневой группы
Гильзы цилиндров по наименьшему внутреннему диаметру цилиндра, а поршень по наибольшему диаметру юбки делятся на следующие шесть размерных групп обозначаемых индексами А, Б, В, Г, Е, Ж на верхнем торце гильзы и на днище поршня.
При установке поршни и цилиндры подбираются по одноименным размерным группам. Установка не совпадающих по группам узлов может вызвать задиры на поверхности гильз и заклинивание поршня. Втулки шатуна и поршневой палец перед сборкой необходимо смазать моторным маслом. Поршневой палец устанавливают в поршень после его нагрева в течение 10мин в масленой ванне при температуре 80-100ºС, при этом поршневой палец должен заходить в отверстия от усилия большим пальцем руки. Запрессовка поршневого пальца в поршень не допускается. При сборке поршня с шатуном необходимо отследить направление смещения камеры сгорания. Смещение должно быть направлено в сторону большого болта шатунной крышки. В каждый поршень подбирают три компрессионных и два маслосъемных кольца; наружная цилиндрическая поверхность верхнего компрессионного кольца должна быть хромирована, второе компрессионное кольцо имеет луженые канавки.
Компрессионные кольца устанавливаются на поршень скошенной поверхностью в сторону днища поршня. Тепловой зазор в замках поршневых колец, вставленных в гильзу цилиндра должен составлять 0,45-0,65мм. Просветов между стенками гильзы и поверхностью колец не допускается. При величине зазора менее 0,45мм можно пропилить концы стыка, обеспечив параллельность сторон в сжатом состоянии. Тепловой зазор в замках поршневых колец проверяют щупом; поршневое кольцо должно находиться в 25мм от верхней кромки гильзы. Кольца на поршень устанавливают при помощи специальных щипцов (см. рис 6). Замки смежных колец должны располагаться относительно друг друга под углом 180º.
Установка шатунно-поршневой группы
Перед установкой гильзы в блок цилиндров необходимо тщательно протереть все поверхности, а уплотнительные кольца смазать моторным маслом. Гильзу с уплотнительными кольцами устанавливают в блок усилием руки. Буртики гильз цилиндров должны выступать над поверхность блока на 0,065-0,165мм. Перед установкой поршня с шатунами зеркало цилиндра необходимо тщательно протереть и смазать моторным маслом. Поршень устанавливают в цилиндр так, чтобы камера сгорания была смещена внутрь двигателя (в сторону топливного насоса). Поршневые кольца должны быть обжаты обоймой, внутренний диаметр которой должен быть равен диаметру цилиндра (см рис 8). При сборке шатунных подшипников необходимо, чтобы клейма спаренности на шатуне и крышке были одинаковыми, а риски спаренности совпадали. Болты крепления крышки шатунов затягиваются моментом 20-22кгс.м. Затяжку болтов начинают с длинного болта и выполняют в два приёма, сначала половинным усилием, а затем в полным. Замковые шайбы шатунных болтов при каждой сборке заменяют. После установки шатанно-поршневой группы коленчатый вал должен плавно, без заеданий проворачиваться за головку болта крепления шкива коленчатого вала с помощью рычага длиной 550мм.
Ремонт коленчатого вала
Коленчатый вал заменяют при наличии трещин любого размера и расположения, задиров на шатунных или коренных шейках, при биении коренных шеек, не устраняемых методом шлифования под последний ремонтный размер. Биение средних коренных шеек относительно крайних допускается не свыше 0,08мм. Проверка производится индикатором при установленных на призмы крайних коренных шейках. При износе хотя бы одной коренной или шатунной шейки сверх допустимого (табл. 1), а также при наличие хотя бы на одной из шеек глубоких рисок или задиров все коренные или шатунные шейки перешлифовываются под единый размер. Номер ремонтного размера коренных шеек может отличаться от номера ремонтного размера шатунных шеек. Шлифовка шеек коленчатого вала производится в пределах величин указанных в табл. 1.
При этом необходимо выполнить следующие условия:
переход цилиндрических участков шеек в галтели должен быть плавным (радиус галтели 5,5-6,0мм), без подрезов, прожогов, грубых рисок: шероховатость поверхностей шеек не должна превышать 0,20мкм, шероховатость галтелей не ниже 0,32мкм;
величина радиусов осей всех кривошипов вала должна быть 70±0,12мм;
не параллельность средних осей коренных шеек относительно общей оси крайних коренных шеек не должна превышать 0,010мм, не параллельность шатунных шеек относительно общей оси крайних коренных шеек не должна превышать 0,015мм;
овальность, конусность, вогнутость, бочкообразность коренных и шатунных шеек не допускается более 0,01мм.
Отсутствие трещин проверяется магнитным дефектоскопом с обязательным последующим размагничиванием.
При каждом снятии коленчатого вала с двигателя для замены вкладышей полости шатунных шеек рекомендуется очищать, предварительно удалив заглушки, которыми закрыты полости. Повторное использование заглушек не допускается. Перед установкой заглушек вспученный металл у кромок отверстий от предыдущей раскерновки запиливают, промывают вал и прочищаются масленые каналы. Заглушки запрессовывают на 5-6мм и раскернивают внутри отверстия в трех точках, равномерно расположенных по окружности, для предотвращения само производительного выпрессовывания заглушек.
Шестерню коленчатого вала заменяют при контактном разрушении зубьев, сколах, трещинах, выработке в виде канавок, а также при боковом зазоре в зацеплении с шестерней распределительного вала более 0,3мм. Шестерню коленчатого вала можно заменить без снятия коленчатого вала с двигателя. При снятых шкиве и передней крышке блока передний противовес и шестерня спрессовываются при помощи съемника. Перед установкой шестерню и противовес необходимо нагреть до температуры 105°С произвести последовательную на прессовку.
Замена вкладышей коренных и шатунных подшипников
Коленчатые валы двигателей ЯМЗ обладают высокой износостойкостью. После 80-100тыс.км пробега рекомендуется профилактическая замена вкладышей, которая продлит срок службы коленчатого вала до пере шлифовки. Для замены вкладышей коренных и шатунных подшипников двигатель снимают с автомобиля. Вклады необходимо заменять в условиях исключающих попадание грязи. Новые вкладыши должны иметь номинальные размеры. Шатунные вкладыши меняют по порядку, начиная с первого цилиндра. Снятые вкладыши тщательно осматриваю. При наличии повреждений не свойственных естественному износу, выясняют их причину. Масляные каналы коленчатого вала очищают от загрязнённого масла и отложений, протирают шейку и осматриваю её. Перед установкой вкладышей шейку и вкладыши смазываю моторным маслом. Болты крепления шатунных подшипников затягивают моментом 20-22кгс. м. Вкладыши коренных подшипников можно заменить при помощи штифта. Штифт представляет собой стальной стержень длиной 250мм, диаметром 6мм и имеет головку диаметром 15мм, высотой 3мм. Для снятия верхнего вкладыша коренного подшипника, штифт вставляют в отверстие масленого канала коренной шейки. Для выталкивания вкладыша коленчатый вал вращают. Для установки вкладыша в постель его накладывают на шейку и усилием руки частично вводят в зазор между шейкой и постелью. Затем штифт вводят в отверстие масленого канала и проворачивают вал до полной установки вкладыша. Вертикальные болты крышек коренных подшипников затягивают с приложением момента 43-47кгс.м, а горизонтальные – 10-12кгс.м.
Необходимость замены вкладышей определяется величиной износа по толщине и диаметральным зазором в сопряжении (табл. 2). Если износ по толщине превышает 0,05мм или диаметральный зазор более 0,23мм, вкладыши заменяют новыми. Толщина вкладыша измеряется по его середине. Зазор проверяют измерением толщины шейки коленчатого вала и внутреннего диаметра подшипника (после затяжки болтов крепления крышки). Вкладыши также заменяются при наличие механических повреждений.
При повторной установке вкладышей, их устанавливают только на старое место. Верхний вкладыш имеет канал и отверстие для подвода и разбрызгивания масла. Вкладыши нижней головки шатуна взаимозаменяемые.
Для ремонта шатуна предусматривается шесть ремонтных размеров вкладышей. Клеймо размера нанесено на тыльной стороне вкладыша недалеко от стыка. Номер ремонтного размера вкладыша должен соответствовать номеру ремонтного размера шейки коленчатого вала. Вкладыши подшипников коленчатого вала следует менять целиком во всём двигателе.
Восстановление герметичности клапанов
Для восстановления герметичности клапанов нужно снять головку (или головки) блока цилиндров снять с двигателя. Очистить их от грязи и масла, нанести на тарелки клапаном метки для установки их при сборке на старое место. Пользуясь приспособлением (рис. 9) сжать пружины клапанов и вытащить сухари клапанов, снять клапан, тщательно очистить их от нагара, промыть в керосине, определить степень износа. При незначительных износах и раковинах на клапане и седле, клапан восстанавливается притиркой клапана и седла пастой, которая приготавливается перемешиванием 1,5 частей (объема) микропорошок зелёного карбида кремния 63С-М28 ОСТ 2-144-71 с одной частью летнего моторного масла и 0,5 части дизельного топлива Л-0,2-40 ГОСТ 305-82.
Процесс притирки состоит из вращательно-поступательного движения при помощи специального инструмента (притирочная дрель), либо в ручную с использованием зажима. Вращение должно выполняться в различных направлениях по ½ оборота с возможностью поступления пасты под фаску. Внешним признаком нормальной притирки является наличие матового пояска на клапане и седле не менее 1,5мм. Разрывов, рисок на пояске не допускается. После притирки клапан промывают в керосине, вытирают и устанавливают. Проверяют герметичность залив керосин во впускные и выпускные окна и выдержав 3мин. При любом повороте клапана, не должно быть протечек и потёков. Правильность притирки можно проверить при помощи графита. Для этого на фаску мягким грифелем карандаша нанося 10-15 рисок через одинаковые промежутки. Клапан вставляют в седло, сильно нажимают на него и делают поворот на ¼ оборота. Грифель после этого должен быть стёрт. Если не удаётся добиться герметичности притиркой, то производится прошлифовка клапана и седла процедура притирки повторяется. Для шлифовки клапана применяется шлифовочные устройства или электродрели. Шлифовку седел производят специальными головками. Если необходимо произвести замену направляющих втулок клапана, то шлифовку седла производят только после их замены.
Ремонт клапанных седел
Риски, выработки и вмятины от нагара на седле устраняются методом зенкерования и шлифовки фаски седла, обеспечив минимальное снятие металла. Предельное утопание тарелок нового клапана от плоскости головки при восстановлении фаски седла допускается: 2,5мм для впускного клапана; 3,0мм для выпускного. Режущий инструмент должен иметь фиксацию во внутренней втулке клапана, для совмещения соосности клапана и фаски седла в пределах 0,025мм (биение 0,05мм).
Обработку фаски впускного клапана производить в следующем порядке:
фрезеровать рабочую фаску зенкером под углом 120° (рис 10, а) до получения чистой и ровной поверхности;
фрезеровать нижнюю кромку рабочей фаски зенкером под углом 150° (рис 10, б), выдерживая рабочую фаску в пределах 59,4 +0,7мм;
фрезеровать верхнюю кромку фаски зенкером под углом 60° (рис 10, в) до получения ширины фаски, равной 2,0-2,5мм.
Обработку фаски выпускного клапана производить в следующем порядке:
фрезеровать рабочую фаску зенкером под углом 90° (рис 11, а) до получения чистой и ровной поверхности;
фрезеровать нижнюю кромку рабочей фаски зенкером под углом 150° (рис 11, б), до получения ширины фаски, равной 1,5-2,0мм.
Риски и незначительную выработку на сёдлах клапанов устраняется шлифовкой и притиркой. Если невозможно получить ширину рабочей фаски на седле выпускного клапана, равной 1,55-2,0мм, а также при наличии прогара, трещин, раковин и других дефектов седла выпускного клапана, не устраняемых обработкой, седло необходимо заменить. При запрессовке нового седла головку цилиндров нагревают в кипящей воде до 90°С. Запрессовывают седло лёгким ударами молотка через мягкую (медную, латунную) проставку, обеспечив натяг не менее 0,02мм. Прилегание седла к головке цилиндров проверяют щупом. Щуп толщиной 0,05мм проходить не должен. Если необходимо заменить направляющие втулки клапанов, то рабочие фаски на седлах клапанов шлифуют после замены втулок. Направляющие втулки клапана при износе внутреннего диаметров более чем 12,06мм заменяют новыми. После запрессовки новую втулку развертывают на размер 12+0,019мм. Выступание втулки из тела головки должно быть 32±0,5мм.
Замена впускного клапана
На рабочей поверхности тарелки не допускается наличие рисок, раковин, углублений.
Если имеются данные дефекты, то рабочую поверхность клапана необходимо перешлифовать, выдержав толщину цилиндрической тарелки на менее 0,75мм, угол 121-122°, шероховатость поверхности не ниже 1,25мкм, биение рабочей поверхности относительно стержне не более 0,03мм. Износ стержня допускается до 11,92мм.
Замена выпускного клапана
На рабочей поверхности тарелки не допускается наличие рисок, раковин, углублений. Если имеются данные дефекты, то рабочую поверхность клапана необходимо перешлифовать, выдержав толщину пояса цилиндрической поверхности тарелки на менее 1,00мм, угол 91-92°, шероховатость поверхности не ниже 0,63 мкм, биение рабочей поверхности относительно стержне не более 0,03мм. Отклонение при проверке стержня клапана от прямолинейности допускается не более 0,01мм. Износ стержня допускается до 11,68мм.
Замена штанг, коромысел и их осей
Коромысло заменяют при обнаружении трещин или обнаружении облома. При износе отверстия под ось коромысла до диаметра 25,15мм заменяют только втулку. Кроме того, втулку заменяют при прославлении её посадки в коромысле. Посадку проверяют лёгким ударом через медную выколотку. Новая втулка должна утопать в тело коромысла по 1мм с каждой стороны. Масленые отверстия во втулке и коромысле должны совпадать, а стык втулки должен находиться в верхней части отверстия. После запрессовки втулки необходимо развернуть под размер 25+0,025мм.
Ось коромысла бракуют при наличие трещин или облома. Допускается износ оси до диаметра 25,00мм.
Штанга толкателя не должна иметь задиров или выкрашивания цементированного слоя на рабочих поверхности наконечников. Погнутость штанги проверяют индикатором на призмах. Если биение штанги превышает 0,5мм, её необходимо править. После сборки необходимо проверить тепловые зазоры в клапанном механизме и при необходимости отрегулировать их.
Ключи для тяжелых условий эксплуатации из углеродистой стали (метрические) KSHM — NEWMAN TOOLS КОРЗИНА ДЛЯ ПОКУПОК
- 41,75 долл. США долл. США 41,75 долларов США
8 мм x 1,0 — $ 41,75 USD10 мм x 1,5 — 32,13 долл. США 12 мм x 1,75 — 33,17 долл. США 14 мм x 1,5 — 49,85 долл. США, x 2,0 мм x 2,0 — 59,85 долл. США, 1,5 мм, 1,5, 1,5, $ 6, 1,5, $ 6, 1,5, $ 5, 1,5, $ 5, 1,5, 1,5, 1,5, $ 5, 1,5, $ 5, 1,5, $ 5, 1,5, $ 5, 1,5, $ 5, 1,5, $ 5, 1,5, $ 5, 1,5, $ 5, 1,5, $ 5, 1,5, $ 5, $ 5, $ 5, $ 5, $ 5, $ 5, $ 5, $ 5, $ 5, $ 5, $ 5, $ 5, $ 5, $ 59,5, $ 59,5.
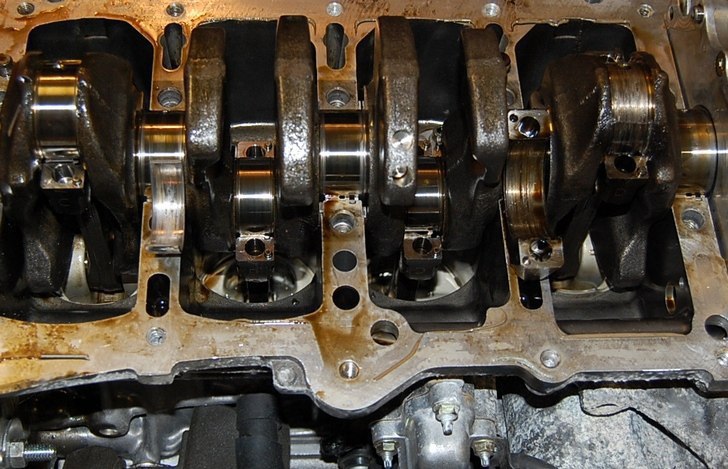
Резьбовые вставки Keysert® Key-Lock
выберите размер из раскрывающегося меню
- Простая установка
Устанавливается со стандартными сверлами и метчиками
Хвостовик не ломается. - Блокировочные ключи обеспечивают надежную механическую блокировку, предотвращают вращение из-за вибрации или кручения.
- Может использоваться с большинством материалов
Алюминий, магний, чугун, холоднокатаная сталь и пластик - Обеспечивают высокую прочность и надежность. Одна длина каждого размера обеспечивает максимальную прочность на отрыв. Разрывает болты класса 8 в тесте за тестом.
- Легко снимается
- Никаких специальных навыков не требуется. Процедуры установки можно изучить за несколько минут
Размер внутренней резьбы | *Размер внешней резьбы (мод.![]() |
КШМ | * Только для справки |
КШМ6х1 | М12х1,25 |
КШМ8х1,25 | М14х1,5 |
КШМ8х1 | |
КШМ10х1,5 | М16х1,5 |
КШМ10х1,25 | |
КШМ12х1,75 | М18х1,5 |
КШМ12х1,25 | |
КШМ14х2,0 | М20×1,5 |
КШМ14х1,5 | |
КШМ16х2 | М22×1,5 |
КШМ16х1,5 | |
КШМ18х1,5 | М24×1,5 |
КШМ20х2,5 | М30×2,0 |
КШМ20х1,5 | |
КШМ22х1,5 | М32×2,0 |
КШМ24х3,0 | М33х2,0 |
КШМ24х2 |
Для получения дополнительной информации
Усиленные ключи из углеродистой стали (дюймовые) KSH
Обычная цена
Из 6,04 долл. США долл. США
6,04 доллара США
Ключи из нержавеющей стали для тяжелых условий эксплуатации (дюймовые) KSSH
Обычная цена Из 11,34 долл. США долл. США 11,34 долларов США
долларов СШАКлючи из нержавеющей стали для тяжелых условий эксплуатации (метрические) KSSHM
Обычная цена Из 15,92 долл. США долл. США 15,92 долларов США
долларов США Тонкостенные ключи из углеродистой стали (дюймы) KSTОбычная цена Из 6,04 долл. США долл. США 6,04 доллара США
долларов СШАКлючи из нержавеющей стали с тонкими стенками (дюймы) KSST
Обычная цена
Из 11,48 долл. США долл. США
11,48 долларов США 9 долларов США0013
Армейский справочник
Бронетранспортер БТР-Д был разработан на основе боевой машины десанта БМД-1, подробно описанной в отдельной статье, для удовлетворения требований Воздушно-десантных войск России к машине с большим внутренним объемом.
БТР-Д имел условное обозначение «Объект 925» и впервые был выпущен в 1974 году. Впервые БТР-Д был замечен во время российского вторжения в Афганистан; НАТО называет эту машину M1979, поскольку она была замечена впервые. Версии с носовыми пулеметами — Объект 9.25г.
БТР-Д — это многоцелевой бронированный транспортер, который используется для различных целей, включая транспортировку войск, буксировку вспомогательного оружия, такого как 23-мм легкая зенитная установка ЗУ-23-2, и техническое обслуживание.
Машина предназначена для десантирования с парашютом и может перевозиться внутри тяжелого вертолета Ми-26.
Заменой БТР-Д может стать БТР «Ракушка», базирующийся на шасси, аналогичном недавно представленной боевой машине десанта БМД-4.
Описание
Бронетранспортер десанта БТР-Д создан на базе компонентов боевой машины десанта БМД-1, но без башни и с дополнительным опорным катком с каждой стороны. Это дает автомобилю больший внутренний объем и повышенную грузоподъемность.
Корпус БТР-Д выполнен из цельносварной алюминиевой броневой конструкции, обеспечивающей защиту пассажиров от огня стрелкового оружия и осколков снарядов.
Водитель сидит в передней части корпуса по центру и имеет цельную крышку люка, открывающуюся вправо. Перед ним расположены три дневных перископа ТНПО-170, обеспечивающие наблюдение за передней частью машины; средний может быть заменен на средство ночного вождения ТНП-350Б/ТВНЭ-4Б. По бокам и сзади водителя есть дополнительное сиденье, и каждый из этих членов экипажа снабжен крышкой люка, открывающейся назад. Перед ним находится поворотный перископ.
С обеих сторон корпуса установлены 7,62-мм пулеметы ПКТ, стреляющие вперед, которые ведут огонь на подавление по лобовой дуге машины.
Командирская башенка расположена позади места механика-водителя и имеет цельную крышку люка, открывающуюся назад, один комбинированный прицел ТКН-3Б и два прибора технического зрения ТНП-170. В корме и по бокам командирской башенки расположены два люка в форме полумесяца. Два дополнительных 7,62-мм пулемета часто несут на крыше для ведения огня на подавление.
Некоторые машины ранних серий имели башню, вооружённую 7,62-мм пулемётом ПКТ. Совсем недавно некоторые из них были оснащены установленным на крыше 30-мм автоматическим гранатометом АГС-17.
Дизельный силовой агрегат находится сзади, а подвеска с обеих сторон состоит из шести сдвоенных опорных катков с резиновыми шинами. Ведущая звездочка находится сзади, направляющее колесо спереди и пять опорных катков с возвратом гусеницы. Подвеска регулируется по высоте.
Стандартное оборудование включает приборы ночного видения и систему NBC. Машина является полностью амфибийной с небольшой подготовкой, приводится в движение двумя водометами, установленными в корме корпуса.
Предусмотрены стеллажи для двух гранатометов, боеприпасов, двух ручных пулеметов РПК, стеллажи для двух переносных зенитных ракет ПЗРК, сигнальных ракет и другого специального оборудования.
В общей сложности пять сферических огневых портов позволяют некоторым посаженным войскам вести огонь из своего оружия изнутри машины.
БТР-Д может быть быстро сконфигурирован для перевозки четырех пациентов на носилках, 12 ящиков с боеприпасами или двух топливных баков по 200 литров.
Натяжение гусеницы может регулироваться водителем, не выходя из машины, а средства связи, изначально установленные на БТР-Д, включают радиостанцию Р-123М и аппаратуру А-1 для переговорного устройства Р-124.
С 1984 года радиостанция Р-123М была заменена новой полупроводниковой радиостанцией Р-173 и приемником Р-173П. На смену переговорному устройству Р-124 пришел новый Р-174.
Варианты
Первое обновление №
С 1979 года машина прошла первую модернизацию, включавшую установку 81-мм дымовых гранатометов Тип 920Г «Туча», состоящих из двух блоков по четыре пусковых установки в каждом. Обычно они располагаются по одному берегу с каждой стороны шасси на одной линии с пятой станцией опорных катков.
Командно-штабная машина БМД-КШМ
Имеет складную антенну «штанга для одежды» вокруг надстройки. В лобовой части корпуса нет 7,62-мм пулеметов, а также огневых портиков. Люк командира смещен влево, пусковые установки дымовых гранат с электроприводом не установлены.
Командно-штабная машина БМД-1Э
Аналогичен предыдущему, но не оснащен антенной того же типа. Вместо этого он оснащен телескопической антенной, которая намного больше, а штыревые антенны теперь установлены на передней стороне автомобиля. Правильное название этой машины — БМД-1Р, она носит имя «Синица».
БМД-1 Р-440 ОДБ Машина связи
Это БТР-Д, оснащенный системой спутниковой связи Р-440. На крыше машины установлена большая круглая тарелка связи. Предполагается, что это мобильная версия Р-440 (кодовое название НАТО «Park Drive»).
БМД-КШМ с ДПЛА «Шмель-1»
Модифицированное шасси БМД-КШМ также используется в качестве основы для пусковой установки и пункта управления для беспилотного летательного аппарата «Шмель-1». Фактическая стартовая платформа называется «Стерх».
Кроме того, платформа также используется для более поздней версии Птцела-1Т (Пчела) системы реактора Строй-П.
Это шасси БТР-Д, модифицированное для использования в качестве центра обнаружения артиллерийского огня, для использования со 120-мм самоходной артиллерийско-минометной системой Анона 2С9 на базе шасси БМД-1.
Обычно развертывается на уровне батареи и оснащен радиолокационным комплексом наземных целей 1РЛ133-1 с дальностью обнаружения 14 км, лазерным дальномером ДАК-2 с дальностью до 8 км, прибором ПВ-1 и прибор ночного видения ННП-21, топоприцел 1Т121-1, ПУО-9прибор управления огнем М, две радиостанции Р-123 и одна радиостанция Р-107М. Этот автомобиль не вооружен.
Предусматривается для 120-мм 2С9, а также других артиллерийских систем, таких как буксируемые 122-мм гаубицы Д-30 и 122-мм реактивные системы залпового огня БМ-21 (40 снарядов).
Робот БТР-РД
Это противотанковый вариант БТР-Д, который также иногда называют БМД-1Д. Экипаж из шести человек, состоящий из командира, механика-водителя и двух противотанковых ракетных расчетов по два человека.
Большая цельная крышка люка расположена в верхней передней части надстройки, которая открывается назад. Справа от открытой крышки люка находится выдвижная пусковая установка ПТРК «Тула» КБП 9К113 «Конкурс» (НАТО АТ-5 «Spandrel»), максимальная дальность действия которой составляет 4000 м. Пусковая установка также может вести огонь ПТУР меньшей дальности 9К111 «Фагот» (НАТО АТ-4 «Штуцер»). Базовая нагрузка этой машины составляет 12 ПТРК. Кроме того, ракета может быть запущена оператором с пульта дистанционного управления на расстоянии до 20 м от машины. Предусмотрены шкворневые крепления, позволяющие устанавливать ракеты и запускать их с крыши.
Ремонтно-эвакуационная машина БрехМ-Д
Базируется на шасси БТР-Д и оснащен специализированным оборудованием для поддержки, ремонта и эвакуации машин типа БМД-1.
Специализированное оборудование, устанавливаемое на транспортное средство, включает: кран с поворотом на 180°; эвакуационная лебедка; комбинированная лопата и бульдозерный отвал; буксировочное оборудование; система электросварки, а также инструменты; и готовые запчасти.
Стандартное оборудование включает 7,62-мм носовой пулемет ПКТ, радиостанцию, систему внутренней связи и систему NBC.
БТР-ЗД
Это представитель ПВО семейства БТР-Д, который может буксировать спаренную 23-мм легкую зенитную установку ЗУ-23-2 или нести такую же систему на крыше и вести огонь.
Для погрузки и выгрузки системы ЗУ-23-2 на автомобиль предусмотрены рампы. Эта версия также оснащена двумя багажниками на крыше для переносных ЗРК типа «выстрелил-забыл», таких как «Игла-1М» (НАТО SA-16 «Гимлет»).