Как сделать шиномонтажный станок своими руками?
Удобнее всего, быстрее и надёжнее производить замену покрышек в специализированной шиномонтажной мастерской. Но обратиться туда получается не всегда и на то может быть масса причин, одна из которых – это стоимость замены. Вот поэтому некоторые автомобилисты и пытаются всё сделать самостоятельно. Только для этого потребуется определённое оборудование. О том, как сделать простой шиномонтажный станок у себя в гараже, мы и расскажем далее.
Нужен ли станок для бортировки колес в гараже?
По сути, если взглянуть со стороны, то процедура замены покрышек не покажется таким уж и сложным занятием. Нужно просто снять старую шину и одеть на диск новую. Но как только вы взялись за демонтаж, возникает одна проблема – банально не хватает физической силы.
Можно приобрести специальный дорожный набор, который облегчит задачу. В него входит набор различных монтировок и специальные клинья.
Вот именно в таких случаях разбортовка колеса может потребовать некоторые самодельные приспособления, что будут сконструированы именно под вашу ситуацию. Одно из таких – это шиномонтажный станок.
Знаете ли вы?Корейский художник Йонг Хо Джи из старых покрышек и их частей изготавливает реалистичные скульптуры различных животных.
Особенности конструкции шиномонтажного станка
Устройство шиномонтажного станка очень простое и схожее с конструкцией реечного домкрата. Он состоит из: рамы, вертикального стояка и трубы с рукоятью.
Рама представляет собой две параллельные трубы из прямоугольного профиля. Они соединятся между собой стальным уголком.
Вертикальный стояк крепится к раме и выполняет ряд задач: крепление рычага и площадка, для фиксирования колёсного диска.
Труба с рукоятью будет работать, как рычаг при снятии покрышки.
Важно! Конструируя все перечисленные выше компоненты, нужно запастись качественным металлопрокатом, ведь при выполнении шиномонтажа станок будет претерпевать большие нагрузки.
Плюсы самодельной конструкции
Станок для разбортовки автомобильных колес, сконструированный своими руками, имеет много преимуществ:
- Небольшая цена расходных материалов и производства. Запчасти для таких станков вполне дешёвые, а в некоторых ситуациях их можно сделать и из переработанного сырья.
- Всегда можно будет провести замену покрышек в своём гараже, плюс появляется возможность дополнительного заработка.
- В силу своей универсальности он может быть адаптирован под любые колёса, даже от грузовых автомобилей.
- В силу своей компактности приспособление для шиномонтажа может храниться в любом удобном месте.
- В силу простоты деталей и элементов креплений конструкция собирается за несколько часов.
Экономия в ремонте автомобилей. Правильное используя такой станок, вы сможете бортировать колёса даже грузовых автомобилей.
Важно! При правильном использовании такого станка колёса не будут повреждены.
Как сделать шиномонтажный станок своими руками?
Когда вы решили соорудить самодельный шиномонтажный станок своими руками, рекомендуем поискать подходящие схемы и чертежи конструкции в интернете.
- Возьмите две крепкие профильные трубы, расположите их параллельно относительно друг друга на расстоянии не менее 70 сантиметров. Так конструкция будет устойчивее.
- Соедините их между собой уголком или меньшей трубой. Дополнительно можно установить ножки, которые будут регулироваться.
- Далее приварите трубу сечением 20 или 30 миллиметров к перекладине. Предварительно на высоте приблизительно 50 сантиметров приварите фланец.
- Приварите крепёжный элемент к вертикальной части. Им послужит стальная пластина.
С её помощью будет установлен рычаг, который потребуется для снятия покрышки с диска колеса. Рычаг будет состоять из двух частей: плеча и лапки.
Советы по бортировке колес
Теперь, когда у вас уже есть станок для шиномонтажа, изготовленный своими руками, вы можете приступать разбортировке колеса. Вам понадобиться также длинная монтировка из дорожного набора. К ней можно приварить ручку.
- Установите колесо на фланец и зафиксируйте хомутом.
- Узким торцом монтировки выведите край резины за наружную часть колёсного диска. Переверните колесо и полностью демонтируйте покрышку.
- Нельзя допустить деформации края обода, так как это затруднит монтаж новой покрышки. Чтобы сохранить бортируемую покрышку и не повредить резину, узкий край монтировки смажьте солидолом.
- Одевая новую резину, используйте мыльную пену.
- Следите, чтобы не было щелей между ободом и одеваемой резиной.
Интересный факт! Работники шиномонтажной мастерской города Электросталь спасли кота, который проехал внутри автомобиля из города Ногинска. К одной молодой девушке на Хёндай Гетц животное забралось в район коробки передач и сидело там всю дорогу. Далее кот испугался и забрался на правый приводной вал, откуда уже не мог сам вылезти. Кота успешно достали целого и невредимого.
Подписывайтесь на наши ленты в таких социальных сетях как, Facebook, Вконтакте, Instagram, Pinterest, Yandex Zen, Twitter и Telegram: все самые интересные автомобильные события собранные в одном месте.
Шиномонтажный станок своими руками (фото, видео)
Содержание статьи:
Многие из автомобилистов задумывались о том, как можно сэкономить время и деньги на шиномонтаже, сделав его своими руками. Плюс к тому же, как мы знаем, не каждый шиномонтаж может предложить качественные услуги. Так иногда после смены шин, мы можем обнаружить погнутые диски, а иногда и сам кузов машины.
На шиномонтаже всегда собирается большая очередь и поэтому, чтобы поменять покрышки, порой следует выстоять длинную очередь. Ну и, конечно же, цена за такие услуги не маленькая, и если учесть то, что переобувать автомобиль, как минимум, нужно два раза в год, сумма получается хорошая. Поэтому многие автомобилисты задумываются о замене шин своими руками.
Для такого действия, нам понадобится самодельный ручной шиномонтажный станок. Конструкция таких станков проста и для их изготовления не нужны чертежи. Ниже мы представим вам всю необходимую информацию, а также обучающее видео, которое продемонстрирует устройство и особенности в построении станка своими руками и его эксплуатации.
Описание конструкции
Самодельный станок по бортировке колес
Если рассмотреть саму процедуру смены покрышек, то на первый взгляд она покажется весьма простой. Для того чтобы сделать замену, вам следует, всего-навсего произвести демонтаж старой покрышки с диска, после чего произвести установку новой. В то же время, шиномонтажа колес, мы сталкиваемся с небольшой проблемой.
Для демонтажа необходимо приложить огромные усилия. Конечно, мы можем использовать специальные инструменты, представленные в виде «дорожного набора». В комплекте такого набора мы найдем несколько монтировок, которые имеют разную форму, а также специальные клинья. Такие инструменты смогут слегка облегчить выполнение бортировки колес. В то же время, если покрышка эксплуатировалась вами довольно длительный период, то отделить ее от колеса будет весьма непросто. Поэтому лучшим выходом из ситуации будет сделать шиномонтажный станок. Этот инструмент поможет вам в решении такой проблемы.
Конструкция такого станка, сделанного своими руками, должна быть представлена в виде таких составляющих, как:
- рама. Зачастую она представлена в виде двух прямоугольных профильных трубы, которые располагаются параллельно одна к другой.
- вертикальный стояк, крепится к раме. Данное приспособление предназначено для выполнения нескольких функций. Он представлен в виде крепления рычага, который предназначается для совершения работ по демонтажу покрышки, а также играет роль площадки, на которую устанавливается диск;
- труба, к которой мы привариваем рукоятку. Эта труба выступает в качестве рычага во время снятия покрышек.
Чтобы изготовить такое оборудование своими руками, мы рекомендуем купить высококачественный металлопрокат. Это связано с тем, что во время использования такой инструмент будет принимать на себя огромную нагрузку.
Изготовления станка для бортировки колес
Первый этап снятия шины с диска
Для производства каркаса, который будет выступать в качестве основания, мы рекомендуем применять профильные трубы. Между этими трубами должно иметься расстояние не меньше 70 сантиметров. Это расстояние понадобится нам для того, чтобы оборудование имело высокий уровень устойчивости.
Две трубы, которые располагаются параллельно по отношению друг к другу, мы соединяем посредством уголка из стали. Также сюда может пойти и профильная конструкция более маленького сечения. В качестве дополнительного компонента, мы можем сделать регулирующиеся ножки.
После того как мы изготовили каркас, нам следует проделать следующее:
- приварить к каркасу трубу. Диаметр такой трубы может варьироваться от двадцати до тридцати миллиметров. Прежде чем приваривать трубу, мы предварительно, на высоту 40-60 сантиметров, привариваем фланец;
- на вертикальной области мы делаем элемент крепления, который выполнен в форме пластины из стали. Эта пластина понадобится нам для того, чтобы установить такой инструмент, как рычаг.
Основное предназначение рычага это проведение демонтажа шин с колес. Рычаг представлен в виде двух основных частей. Тут мы видим плечо рычага и лапу, которой мы будем воздействовать на саму покрышку.
Важные советы
Подготовка к началу установка шины
После того как вы отделили покрышку от колеса, вам следует провести ее полный демонтаж. Для такого дела, лучше всего, как основной инструмент, применять монтировку. Эта монтировка должна иметь довольно большую длину, с приваренной к ней ручкой. После того как вы произвели установку диска на фланце, посредством хомута, мы проводим его фиксацию.
После этого, при помощи узенького конца монтировки мы выводим край покрышки за пределы наружной части диска. После того, как мы перевернули диск, можно провести демонтаж шины с колеса.
На данном этапе работы важно учитывать следующие факторы:
- Краешек ободка не должен быть подвержен деформации. Данный момент способен весьма сильно затруднить проведение монтажа шины на колесо, в особенности, если вы будете использовать бескамерную шину.
- Для того, чтобы сохранить целостность самой демонтируемой шины, нам необходимо смазать узенький краешек обычным солидолом. Данное действие способно уменьшить вероятность по прорыву резины.
- В момент проведения монтажных работ, по установке новой покрышки на колесо, мы рекомендуем пользоваться также мыльным раствором.
Самодельный рычаг для бортировки колес
Также важно заметить, что во время установки шины на колесо, следует с большим вниманием наблюдать за тем, чтобы отсутствовали щелей между шиной и диском. Как дополнение к самодельному станку по шиномонтажу, мы рекомендуем купить специализированный набор инструментов, в котором вы сможете найти жгуты для уплотнения, а также монтировки, имеющие разный размер.
Как вы видите, конструкция такого станка для бортировки колес довольно проста и не требует какой-либо чертеж. Сделать его своими руками очень просто. Так вы сможете сэкономить массу своего времени, а также сэкономить деньги.
чертежи, размеры, как сделать станок для разбортировки колес
На чтение 5 мин. Просмотров 21.9k. Опубликовано
Обновлено
Пробитое колесо на трассе без запаски – классическая ситуация, которая по частоте событийности держит почетное первое место в списке неприятностей автолюбителя. Необъятные просторы нашей Родины добавляют этой проблеме яркости и глубины: вокруг ни одной автомастерской, а если и есть, то с солидной очередью.
Самое естественное решение – делать шиномонтаж самостоятельно, то есть ни от кого не зависеть. Решение отличное, вот только для его реализации нужно иметь кое-какие инструменты и навыки. Где набраться навыков и какими инструментами запастись, читаем здесь и сейчас.
Романтика большой дороги: шиномонтаж на опушке
Шиномонтаж на трассе можно сделать с помощью двух монтажных лопаток и специального устройства, чтобы оторвать покрышку от диска. Но получится удобнее и цивилизованнее, если у вас найдутся домкрат и буксировочный трос. А они у вас найдутся.
Поэтому дальше работаем вот по какому алгоритму:
- Снимаем колесо, чистим и кладем ниппелем вверх.
- Выпускаем из колеса воздух.
- Просовываем буксировочный трос в дисковое отверстие, ставим домкрат вплотную к ободу.
- Трос накидываем на кронштейн домкрата, скрепляем концы троса друг с другом.
- Надо вращать рукоять так, чтобы домкрат тянул трос вверх, а посадочное кольцо перемещалось вниз вплоть до отделения шины от диска.
- Если в починке или замене нуждается камера, нужно поднять боковую часть шины на обод возле штуцера, который вталкиваем внутрь и вынимаем камеру под покрышкой.
- Ниппель вынимаем, воздух удаляем.
- Теперь помещаем ее под покрышкой, но сначала вставляем щтуцер в отверстие внутри.
- Немного подкачиваем вставленную камеру, пока без ниппеля.
- Делаем забортовку, вставляем ниппель в штуцер, полностью накачиваем камеру и ставим колесо на свое место.
Все эти десять пунктов легко описать, но очень трудно сделать. А если погодные условия оставляют желать лучшего, то становится совсем невесело, такой шиномонтаж запомнится вам на всю жизнь. Качество такого монтажа никогда не будет идеальным.
[box type=”info”]Грамотнее будет обзавестись каким-нибудь механизированным устройством для независимого шиномонтажа. Вариантов таких приспособлений много – в сети можно найти самые разнообразные конструктивные решения.[/box]Стоит ли овчинка выделки?
Есть ли смысл тратить время на изготовление кустарного аппарата, когда можно воспользоваться профессиональным сервисом? Решать вам и только вам. Наше дело – дать качественную информацию.
[box type=”fact”]Самодельный ручной шиномонтажный станок выполняет то же самое, что делают в автосервисе. При этом функциональном равенстве кустарный станок обладает рядом преимуществ.[/box]Судите сами:
- надежны и долговечны в эксплуатации;
- оптимальнее и проще по своей конструкции;
- компактные по размерам;
- имеют ручной привод;
- легко разбираются и хранятся, некоторые помещаются даже в багажнике;
- дают полную независимость от мастерских;
- дают оперативность в ремонте;
- одно из главных преимуществ – серьезная экономия финансовых средств.
Сразу заметим, что большинство вариантов механизмов рассчитаны на легковые автомобили. Хотя водителям грузовиков никто не мешает заняться сооружением собственного шиномонтажного аппарата. На тему «как сделать шиномонтажный » имеется огромное количество вполне дельных видеороликов в сети. Они будут отличным подспорьем.
Делаем шиномонтажный комплект самостоятельно
Если вы приняли решение стать самостоятельной персоной в деле забортовки колес, лучшим вариантом будет иметь полноценный самодельный шиномонтажный станок в своем гараже. Его можно сделать в виде комплекта: и устройства для отбивки борта.
[box type=”fact”]Низ станка в виде Н-образной рамы изготовляем из стальной трубы с прямоугольным сечением. Размер рамы примерно 90 см х 60 см. На расстоянии 30-ти см от края к перемычке перпендикулярно с помощью сварки крепится высокая труба круглого сечения.[/box] Схема станка шиномонтажного.Высота трубы около полутора метров. Ее нужно приварить самым устойчивым образом, поэтому для крепости лучше подварить «косынки» из металлических треугольников толщиной не менее 5-ти мм. К круглой трубе приваривается ступица – средняя часть колеса.
На какой высоте приваривать ступицу – меряем сами по своему росту. Нужно, чтобы лежащее на ступице колесо находилось примерно на уровне вашего пояса. Труба должна быть выше лежащего на станке баллона не меньше, чем на 30 см.
Кронштейн для отбивки борта нужно приваривать ниже ступицы. Его лучше всего вырезать из стального листа толщиной в 5 мм, просверлив в нем отверстие для болта. Трубу для этого узла станка нужно найти пошире, ведь в ней будет помещаться рычаг длиной в полтора метра.
Он, в свою очередь, делается из стальной трубы, а наконечники – из стального 20-ти миллиметрового прутка. Длину рычага продумайте сами, она будет зависеть от силы ваших рук и свободного пространства в гараже.
Советы бывалых
Конструкция шиномонтажного станка.Как правильно сделать :
- Угол между наконечником для забортовки и рычагом нужно сделать острым: чем он меньше, тем лучше резина будет надеваться на диск. Но и слишком острым этот угол делать нельзя, в этом случае рычаг будет царапать диск при забортовке. Нужно найти оптимальные градусы угла.
- Самодельный шиномонтажный станок своими руками лучше делать с чертежами. Подготовить их вам вполне по силам.
- Продумайте крепление к полу. легкий, поэтому крепиться он должен надежно. Если пол бетонный, крепите станок анкерными болтами. Если полы деревянные, используйте саморезы.
- Для снижения вреда для дисков и колес наконечники и колесный диск смазывайте густым мыльным раствором. И не забывайте вымыть колесо перед работой.
- Иногда колеса могут различаться по числу отверстий для креплений и расстояниям между ними. Для таких случаев делаем из металла переходники со шпильками с толщина 1 см.
Станок для разбортировки колес
Шиномонтажный станок своими руками… ч.1 — DRIVE2
Шиномонтаж для дома…в принципе на каждом углу открыты эти шиномонтажи, но цены конечно не радуют. Переобуть машину с одного сезона на другой стоит порядки 2тр у нас. Больше всего мне «нравится» вот это…-Сколько стоит поменять резину на 16 радиусе? говорят одну цену, а когда подвез резину и диски для их монтажа, сразу узнаю, что моя машина(дастер), оказывается внедорожник)))…и стоимость услуги сразу поднимается. Первый год менял резину на шиномонтаже!
В итоге купил еще один комплект дисков и последние 6 лет вообще не езжу на шиномонтаж! Многие скажут, а как же балансировка? Да никак, если машина не прыгает на большой скорости, если руль не трясет, то зачем мне эта балансировка. Если конечно, что то не так в поведении машины, то полюбому туда нужно ехать!
Короче, посмотрел кучу роликов по этому самому домашнему шиномонтажу и решил его сделать себе. Есть гараж, есть свой дом и есть металлолом… и почему бы его не сделать! В итоге стал глобально изучать ютуб и 98% роликов -это хрень полная. Но все же нашлись и достойные варианты…больше всего понравился «Армянский шиномонтаж»
так же есть еще пару роликов.
И все… остальное просто ужас. А так как весной буду покупать новую летнюю резину, то решил его сделать к этому времени. Сразу скажу на будущее…после замены резины, конечно придется везти колеса на балансировку. Но эта процедура стоит 500р. А по времени практически будет примерно 30мин разницы. Что потеряете на шиномонтаже при полной смене резины, что сделаете это сами и отвезете, только на балансировку колеса. Но по деньгам у Вас останется в кармане 1-1,5 тр …как то так. Другими словами можно эти 1,5 рубля заработать)))
В итоге, посмотрев, что у меня есть в загашнике, решил делать капитально и на века.

И так, поехали…
Саму колонну решил сделать из 76 трубы.
Полный размер
отрезал кусок 800мм
Торценул трубу обычной болгаркой.
Полный размер
Для тех, кто не знает, как так ровно ее торцевать. Сначала отрезаете болгаркой, как можно ровнее и затем прикладываете отрезной диск к трубе слегка нажимая на болгарку. Зажимная гайка диска болгарки, находится внутри трубы по центру. Получается торец, как на токарном станке!
Далее нашел трубу НКТ 45мм (толстостенную), на ней будет крутится «каретка».
Полный размер
Что бы, как то совместить разные диаметры труб в один центр понадобился конусный переход…
Полный размер
Для держателя колеса решил использовать трубный фланец на 80мм
Полный размер
Все это дело нужно подружить с помощью сварки!
Полный размер
Полный размер
Полный размер
Лишнее отрезаем.
Полный размер
По началу хотел сделать вот так, что бы колесо сразу само центровалось. Но диаметры на разных дисках имеют разные размеры и поэтому от этой идеи отказался.
Полный размер
Все обварил и далее будет стыковаться 76 труба.
Полный размер
Полный размер
На другой конец привариваем еще один фланец.
Полный размер
Колонна готова!
Полный размер
По поводу крепления станка решил сделать так. Если устанавливать в гараже, можно будет засверлить пол и закрутить анкера на М16 и крепить этот станок через фланец. Если устанавливать на улице, то решил сделать крепление через смотровую яму. Для этого будет прикручен кусок трубы к стенкам ямы и с помощью еще одного куска трубы будет крепится колонна!
Вот так…
Полный размер
Взял кусок 76 трубы, выпилил вдоль полоску 2см. Сжал прессом и сварил. Теперь этот кусок трубы, плотно может входить внутрь 76 трубы.
Полный размер
Далее сверлим насквозь сверлом 12 мм под болты и привариваем гайки.

Полный размер
Полный размер
Привариваем кронштейны для крепления к стене.
Полный размер
И устанавливает на место.
Полный размер
Полный размер
Полный размер
Полный размер
В таком положении будет хранится эта вставка.
Полный размер
Так будет стоять колонная во время работы!
Продолжение следует…
www.drive2.ru
Бортировка колес своими руками: инструменты, пошаговая инструкция, видео
Сегодня владельцы автомобилей привыкли обращаться в шиномонтаж в случае появления проблем с колесами. Но такие услуги можно найти только в больших городах, и существует немало «глухих» мест, где трудно найти мастерскую по ремонту шин. В такой ситуации запасное колесо может выручить водителя, но иногда проблемы случаются сразу с несколькими покрышками. Поэтому автовладелец должен знать, как выполняется бортировка колес своими руками. Тем более, что многие водители не доверяют слесарям шиномонтажных сервисов, и предпочитают выполнять подобные работы самостоятельно.
Как бортировать колесо домкратом и тросом
Это один из простых способов самостоятельной разбортировки и бортировки колеса. Если действовать по приведенной ниже инструкции, то можно легко выполнить эту работу своими руками.
- Снимите колесо с автомобиля и очистите от грязи.
- Выкрутите ниппель, спустите воздух.
- Положите колесо ниппелем наверх.
- Буксировочный трос привяжите к диску и домкрату, как показано на фото.
- Установите домкрат ближе к диску на шину. Если она камерная, то нельзя ставить домкрат рядом со штуцером, иначе при разбортировке он оторвется.
- Концы троса надежно закрепите между собой.
- Поднимайте домкрат вверх, натягивая трос и перемещая вниз боковину шины. Делайте это до тех пор, пока покрышка не отойдет от диска.
- Если нужно только заменить или заклеить проколотую камеру, то поднимите боковину шины монтажными лопатками со стороны штуцера и заведите ее на край диска.
- Втолкните штуцер во внутреннюю полость и вытащите камеру из покрышки.
Внимание! Если ниппель исправен, то его можно выкрутить и использовать для новой камеры, либо положить в запас.
Установка новой камеры
Работа по бортировке занимает меньше времени и сил, но выполнять ее нужно также в определенном порядке.
- Возьмите новую камеру и выкрутите из нее ниппель.
- Спустите давление воздуха, выдавив его принудительно.
- Отведите боковину резины со стороны места расположения штуцера.
- Поместите часть камеры со штуцером в покрышку и вставьте его в отверстие диска.
- Установите всю камеру на место.
- Подкачайте слегка камеру без ниппеля, чтобы она расправилась и заняла свое место. Это нужно также для того, чтобы при бортировке не зацепить ее монтировкой и не повредить.
- Монтажными лопатками осторожно забортируйте покрышку по периметру.
Теперь остается установить ниппель, накачать шину до требуемого заводом-изготовителем давления, и поставить колесо на автомобиль.
Разбортировка наездом на колесо
Главная сложность работы заключается в том, что для отделения покрышки от диска даже веса человека недостаточно. На это влияет также снижение эластичности резины со временем. Водители иногда используют наезд автомобилем на дефектное колесо, когда другой возможности ремонта нет.
Чтобы нагрузка распределялась более равномерно, можно использовать отрезок широкой доски длиной не менее 1 метра. Такой способ хорош тем, что отсутствуют ударные нагрузки, однако часто резина приходит в негодность. Эту работу рекомендуется выполнять с помощником, чтобы регулировать скорость наезда и создаваемое усилие.
Разбортировка кувалдой
Наиболее распространенным способом разбортовки колес стал ударный. В нем применяется металлический уголок, кувалда или большой молоток. Таким методом пользовались слесари шиномонтажных мастерских и водители, когда не было специальных приспособлений.
Внимание! Уголок не должен иметь острых кромок, чтобы не повредить резину.
Разбортировка досками
Если под руками нет никакого инструмента и приспособлений, но есть деревянные доски, то можно использовать их. Бруски при этом выполняют роль рычага, который воздействует на покрышку. Большая сила на нее появляется из-за разности длин плеч рычагов, которая отрывают резину от диска.
Шиномонтажный станок своими руками
Для изготовления станка потребуются следующие материалы и инструменты:
- Электродрель.
- Сварочный аппарат.
- Шлифмашинка с абразивным кругом.
- Прямоугольная стальная труба.
- Круглая труба 1,5 метра, диаметром 2 дюйма.
- Старая колесная ступица.
- Стальной лист не менее 4 мм толщиной.
- Пруток диаметром 20 мм.
Все устройство состоит из 2-х частей: отбивка борта и монтаж шины.
Основание рамы делается из профиля прямоугольного сечения.
Круглая 2-дюймовая труба крепится к перемычке сваркой на расстоянии 30 см от края. Высота должна быть около 150 см. Чтобы усилить прочность сварных швов, можно использовать треугольные косынки. Для возможности установки колеса приваривается ступица на высоте пояса человека.
Верхний край трубы должен располагаться над колесом на расстоянии 30 см. Под ступицей необходимо приварить кронштейн для фиксации устройства отбивки. Он делается из листа железа, в котором сверлится отверстие. Труба, которая будет играть роль рычага, должна иметь достаточный диаметр, чтобы в нее можно было воткнуть рычаг-удлинитель. Наконечники для него должны быть из стального круга 20 мм в диаметре.
Они делаются путем выпиливания шлифовальной машинкой, либо вытачиваются на токарном станке.
Все размеры наконечников показаны на фотографиях.
Демонтаж шины
Чтобы снять резину с диска, действуйте в следующем порядке:
- Очистите колесо и спустите воздух.
- Постелите мягкий коврик на низ станка, чтобы диск не повреждался. Положите колесо.
- Поднимите отбойник и установите лапку на бок шины к ободу.
- Смажьте посадочное место раствором мыла.
- Рычагом край покрышки отсоедините по всей окружности колеса.
- Аналогичную работу сделайте, перевернув колесо.
- Установите колесо на ступицу и закрепите болтами.
- Приподнимите монтажкой край покрышки и введите под него наконечник.
- Край диска промажьте мыльным раствором.
- Снимите борт покрышки, потянув рычаг с упором в трубу.
- Вытащите камеру.
- Монтажной лопаткой поднимите другой борт, установите под него рычаг и демонтируйте шину.
Как бортировать колесо
Чтобы установить шину на диск, выполните действия:
- Смажьте раствором мыла монтажный наконечник, край диска и посадочное место резины.
- Наденьте часть покрышки.
- Монтажный наконечник заведите между частью надетого борта и диском. Шарообразный конец должен иметь упор в диск, а посадочный край покрышки должен находиться по центру наконечника.
- Тяните рычаг с упором в трубу, надевая на диск резину.
- Второй борт надевается аналогично первому.
После этого останется только накачать колесо.
Внимание! Чтобы в гараже было удобнее работать на станке, зафиксируйте его на полу болтами или большими саморезами.
Советы профессионалов
Бортирование колес – непростая работа, требующая определенных навыков. Поэтому нужно выполнять рекомендации специалистов для самостоятельной бортировки шин.
- Если требуется заменить только одну шину, то нельзя ставить другой тип резины. Особенно не стоит менять летнюю шину на зимнюю, и наоборот.
- Важно учитывать типоразмер камер, дисков и покрышек.
- После покупки новой резины камеру лучше установить также новую.
- Нельзя допускать грязь во внутреннюю полость шины.
- Для отделения и снятия резины с диска можно использовать домкрат, монтажные лопатки и другой подходящий инструмент, не допуская повреждений колеса.
- Колеса необходимо периодически осматривать, чтобы вовремя обнаружить дефекты и устранить их.
- Не допускается для разбортировки использовать острые предметы, которые могут повредить шину. Например, водители с небольшим опытом иногда применяют для таких целей отвертки. Это приводит к дополнительным расходам.
Если в дороге колесо стало спускать, и Вы обнаружили в нем острый гвоздь, не торопитесь его сразу вытаскивать. Он позволит на некоторое время сохранить давление, и доехать до ближайшей авторемонтной мастерской.
Перебортировка занимает немало времени и сил, и требует наличия удобных монтажных лопаток. Новички часто используют для разбортировки острую отвертку и молоток, что делать категорически запрещено. Вначале повреждения могут быть незаметными, но впоследствии они себя проявят. Монтажки должны иметь закругления на концах, чтобы не повреждать резину.
Внимание! Для ремонта колес удобно использовать отрезок металлического уголка сечением 40х40 мм.
Его используют для вставки между диском и покрышкой.
Особенности монтажа камерных и бескамерных покрышек
Сегодня бескамерные колеса стоят на многих грузовиках и легковых автомобилях, но и камерные шины находят свое применение. Их ставят на велосипеды, мотоциклы, мопеды и скутеры. Колеса со спицами не могут нормально поддерживать необходимое давление и герметичность. Кроме того, к камерам привыкли старые водители, которые считают, что проще заменить ее, или отремонтировать своими силами.
Недостатком камерных шин является больший вес, по сравнению с бескамерной. Также при повреждении она быстро спускает, и доехать до автосервиса или шиномонтажа времени уже не хватит. Чтобы заклеить камеру приходится полностью разбирать колесо.
Достоинства бескамерной резины:
- Медленная потеря давления, что дает возможность доехать до ремонтного пункта.
- Вес колеса меньше, что уменьшает нагруженность подвески.
- Длительный срок службы, так как меньше нагревается, и нет трения покрышки о камеру.
- Мягкая боковина повышает комфорт водителя и пассажиров при движении автомобиля.
Недостатки бескамерных шин:
- Сложный ремонт и установка бескамерки, требующие специального оборудования, трудно установить своими руками.
- При повреждении диска происходит снижение давления в колесе.
- Движение на спущенном колесе часто приводит к разрушению покрышки.
В камерной покрышке камера должна точно соответствовать требуемому размеру. Если он будет больше, то образуются складки, которые способствуют повреждению. Установка камеры в бескамерную покрышку может привести к ее повреждениям, так как между ними появляется воздушный слой. При резком торможении или крутом повороте покрышка может разрушиться. При установке бескамерной шины места соприкосновения с диском необходимо промазывать специальным герметизирующим составом. На камерных колесах этого делать не нужно.
nahybride.ru
Разбортировать колесо самому? Это просто! — журнал За рулем
Переобувка на носу! Поэтому несколько выпусков «Техсреды» мы решили посвятить шиномонтажным темам.

Материалы по теме
В середине-конце осени автовладельцы штурмуют шиномонтажи. Однако разбортировать колеса можно и самостоятельно. Мы покажем, как это сделать. Нам потребуется специальное приспособление, а также отвертка, чтобы вывернуть колесный золотник, и пара монтажек, которые помогут снять шину с диска.
Чтобы избавить диск от шины, мы купили нехитрое, но очень полезное устройство — механический бортировщик колес. На рынке есть несколько вариантов, но мы выбрали то, которое выпускает компания «Сорокин». Стоит недорого. Благодаря возможности регулировать выдвижную тягу можно снимать покрышки с дисков разного диаметра. Требуется лишь выбрать нужное положение тяги и закрутить два удерживающих ее болта, после чего можно приступать к работе.
Подготовка
Материалы по теме
Мы взяли 16-дюймовое колесо. Покрышку удобнее снимать, если положить его на пол. Чтобы в процессе работы не поцарапать алюминиевый диск, подложим под него лист вспененного полиуретана, который используют в строительстве для шумо- и теплоизоляции.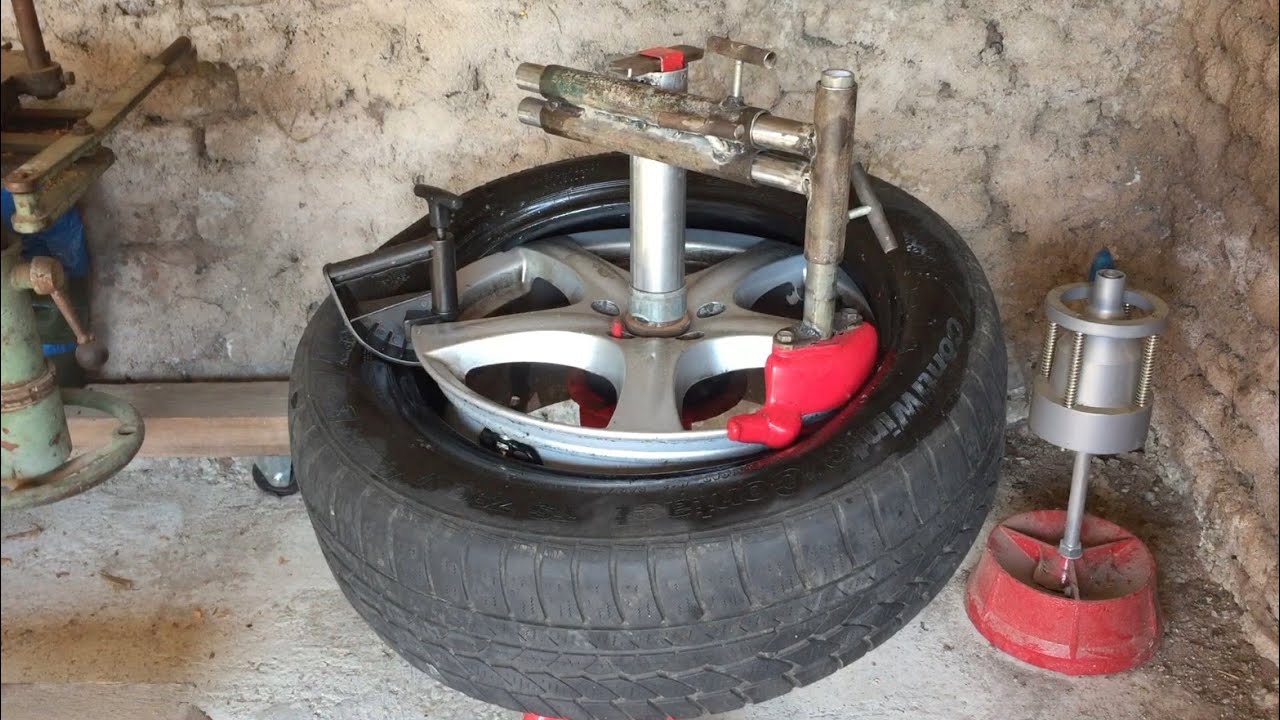
Прежде чем проводить работы с помощью специнструмента, нужно смочить рабочую кромку диска проникающей жидкостью. Иначе мы рискуем повредить диск. Также жидкость, просочившись под кромку, облегчит снятие колеса с хампов.
Эксперимент по разбортировке
Прикладываем наше приспособление к диску. Его крючок в данном случае должен выступать из оправки на 7–8 см. Для ориентира — это одно отверстие на выдвижной тяге. Рукой надавливаем на приспособление с одной стороны, чтобы оно зашло под выступ диска, и заводим крючок под диск с противоположной стороны. Разводим рычаги устройства в разные стороны. Главное — не пытаться скинуть покрышку сразу, а сдвигать ее с хампа постепенно. Иначе шина может пострадать. Учтите, что приспособление не стоит вставлять рядом с колесным вентилем.
Материалы по теме
Вытаскивая и перемещая инструмент, не спеша сдвигаем покрышку с хампа по всей окружности.

Мы сняли покрышку с хампов с каждой стороны. Осталось взять монтажные лопатки и полностью снять шину с диска. Обрабатываем поясок проникающей смазкой. Желательно попасть и на внутреннюю часть колесного диска, это облегчит дело. Заводим первую лопатку под покрышку. Это удобно делать в районе колесного вентиля. Заранее отводим монтажку в сторону, чтобы в ходе работы его не повредить. Придерживаем монтажку ногой. Вставляем рядом вторую лопатку и приподнимаем ею край покрышки. Делаем это по всей внутренней окружности, также постепенно. Мы сняли покрышку с одной стороны диска, осталось сделать то же с другой. Переворачиваем колесо. Заводим лопатку за диск и начинаем его вынимать из шины. Как только нам это удалось, можно считать, что работа окончена.
Разбортировать колеса самостоятельно проще, чем кажется. Главное — запастись нужным инструментом и свободным временем, а также учесть особенности резины.
Все вопросы и предложения по серии выпусков «Техническая среда» присылайте на адрес: [email protected]
Другие выпуски «Технической среды» доступны в нашем спецпроекте, а также на нашем канале в YouTube.
www.zr.ru
Шиномонтажный станок своими руками (фото, видео)
Содержание статьи:
Многие из автомобилистов задумывались о том, как можно сэкономить время и деньги на шиномонтаже, сделав его своими руками. Плюс к тому же, как мы знаем, не каждый шиномонтаж может предложить качественные услуги. Так иногда после смены шин, мы можем обнаружить погнутые диски, а иногда и сам кузов машины.
На шиномонтаже всегда собирается большая очередь и поэтому, чтобы поменять покрышки, порой следует выстоять длинную очередь. Ну и, конечно же, цена за такие услуги не маленькая, и если учесть то, что переобувать автомобиль, как минимум, нужно два раза в год, сумма получается хорошая. Поэтому многие автомобилисты задумываются о замене шин своими руками.
Для такого действия, нам понадобится самодельный ручной шиномонтажный станок. Конструкция таких станков проста и для их изготовления не нужны чертежи. Ниже мы представим вам всю необходимую информацию, а также обучающее видео, которое продемонстрирует устройство и особенности в построении станка своими руками и его эксплуатации.
Описание конструкции
Самодельный станок по бортировке колес
Если рассмотреть саму процедуру смены покрышек, то на первый взгляд она покажется весьма простой. Для того чтобы сделать замену, вам следует, всего-навсего произвести демонтаж старой покрышки с диска, после чего произвести установку новой. В то же время, шиномонтажа колес, мы сталкиваемся с небольшой проблемой.
Для демонтажа необходимо приложить огромные усилия. Конечно, мы можем использовать специальные инструменты, представленные в виде «дорожного набора». В комплекте такого набора мы найдем несколько монтировок, которые имеют разную форму, а также специальные клинья. Такие инструменты смогут слегка облегчить выполнение бортировки колес. В то же время, если покрышка эксплуатировалась вами довольно длительный период, то отделить ее от колеса будет весьма непросто. Поэтому лучшим выходом из ситуации будет сделать шиномонтажный станок. Этот инструмент поможет вам в решении такой проблемы.
Конструкция такого станка, сделанного своими руками, должна быть представлена в виде таких составляющих, как:
- рама. Зачастую она представлена в виде двух прямоугольных профильных трубы, которые располагаются параллельно одна к другой. Соединяются эти трубы посредством уголка из стали;
- вертикальный стояк, крепится к раме. Данное приспособление предназначено для выполнения нескольких функций. Он представлен в виде крепления рычага, который предназначается для совершения работ по демонтажу покрышки, а также играет роль площадки, на которую устанавливается диск;
- труба, к которой мы привариваем рукоятку. Эта труба выступает в качестве рычага во время снятия покрышек.
Чтобы изготовить такое оборудование своими руками, мы рекомендуем купить высококачественный металлопрокат. Это связано с тем, что во время использования такой инструмент будет принимать на себя огромную нагрузку.
Изготовления станка для бортировки колес
Первый этап снятия шины с диска
Для производства каркаса, который будет выступать в качестве основания, мы рекомендуем применять профильные трубы. Между этими трубами должно иметься расстояние не меньше 70 сантиметров. Это расстояние понадобится нам для того, чтобы оборудование имело высокий уровень устойчивости.
Две трубы, которые располагаются параллельно по отношению друг к другу, мы соединяем посредством уголка из стали. Также сюда может пойти и профильная конструкция более маленького сечения. В качестве дополнительного компонента, мы можем сделать регулирующиеся ножки.
После того как мы изготовили каркас, нам следует проделать следующее:
- приварить к каркасу трубу.
Диаметр такой трубы может варьироваться от двадцати до тридцати миллиметров. Прежде чем приваривать трубу, мы предварительно, на высоту 40-60 сантиметров, привариваем фланец;
- на вертикальной области мы делаем элемент крепления, который выполнен в форме пластины из стали. Эта пластина понадобится нам для того, чтобы установить такой инструмент, как рычаг.
Основное предназначение рычага это проведение демонтажа шин с колес. Рычаг представлен в виде двух основных частей. Тут мы видим плечо рычага и лапу, которой мы будем воздействовать на саму покрышку.
Важные советы
Подготовка к началу установка шины
После того как вы отделили покрышку от колеса, вам следует провести ее полный демонтаж. Для такого дела, лучше всего, как основной инструмент, применять монтировку. Эта монтировка должна иметь довольно большую длину, с приваренной к ней ручкой. После того как вы произвели установку диска на фланце, посредством хомута, мы проводим его фиксацию.
После этого, при помощи узенького конца монтировки мы выводим край покрышки за пределы наружной части диска. После того, как мы перевернули диск, можно провести демонтаж шины с колеса.
На данном этапе работы важно учитывать следующие факторы:
- Краешек ободка не должен быть подвержен деформации. Данный момент способен весьма сильно затруднить проведение монтажа шины на колесо, в особенности, если вы будете использовать бескамерную шину.
- Для того, чтобы сохранить целостность самой демонтируемой шины, нам необходимо смазать узенький краешек обычным солидолом. Данное действие способно уменьшить вероятность по прорыву резины.
- В момент проведения монтажных работ, по установке новой покрышки на колесо, мы рекомендуем пользоваться также мыльным раствором.
Самодельный рычаг для бортировки колес
Также важно заметить, что во время установки шины на колесо, следует с большим вниманием наблюдать за тем, чтобы отсутствовали щелей между шиной и диском. Как дополнение к самодельному станку по шиномонтажу, мы рекомендуем купить специализированный набор инструментов, в котором вы сможете найти жгуты для уплотнения, а также монтировки, имеющие разный размер.
Как вы видите, конструкция такого станка для бортировки колес довольно проста и не требует какой-либо чертеж. Сделать его своими руками очень просто. Так вы сможете сэкономить массу своего времени, а также сэкономить деньги.
stanokgid.ru
Бортировка колес сделать самому своими руками
Бортировка колеса может потребоваться в любой момент, при пробое камеры или повреждении диска. Часто автомобилистам приходится обращаться за помощью к другим участникам дорожного движения. Навыки того, как правильно снять и поставить обратно колесо, позволят сэкономить время и обеспечат дальнейшую безопасность передвижения. Рассмотрим особенности этой операции, потребность в инструментарии и этапы работ.
Как и любая другая работа, бортировка колеса требует проведения подготовительной стадии и запаса нужного инструментария. Специальных приспособлений не понадобится, однако одной монтировки и молотка также будет недостаточно для качественного проведения манипуляции. Многие потребители используют именно этот инструмент, чтобы сорвать прикипевшую резину. Такой подход приведет только к повреждению материала, причем дефекты могут проявиться не сразу.
Последовательность действий
Бортировку колеса начинают с подготовки инструмента. Потребуется: набор гаечных ключей, домкрат, монтажные лопатки, молоток, уголок из стали.
Самым важным этапом для правильного демонтажа резины является снятие колеса полностью. Чтобы это осуществить, приподнимают машину на домкрате, отвинчивают фиксирующие гайки, которые желательно заранее отпустить. Затем колесо демонтируется. Далее слегка спускают воздух из камеры, прожимают места контакта обода с шиной. Это дает возможность быстрее и качественнее отделить резину от ободной части. Стоит отметить, что демонтаж колеса начинают со стороны, противоположной золотнику, перемещаясь далее вдоль обода. Без специальных приспособлений и определенных навыков на разборку одного элемента потребуется около получаса.
Основной этап
В бортировке колес своими руками вам поможет подготовленный стальной уголок, который используется для разъединения обода и шины, посредством помещения между указанными элементами с одновременным надавливанием.
Аналогом уголка в процессе могут служить монтажные лопатки, позволяющие провести операцию более точно, не нарушая целостность камеры. Покрышку с обода необходимо снимать внимательно и аккуратно, слегка придавливая ее. После того как одна сторона окажется снаружи, можно приступать к медленному доставанию камеры. В принципе, работу по демонтажу можно считать оконченной. Диск помещается на новую резину, производится сборка в обратной последовательности.
Бескамерная шина
Бортировка колеса с бескамерной шиной имеет свои особенности. Данный элемент не имеет разделения на покрышку и камеру. Внутренняя часть такого колеса полностью заполняется воздушной смесью, которая формирует конфигурацию покрышки, герметично насаженной на дисковое основание. Внутренний слой сделан из специальной каучуковой массы, которая способна при небольшом проколе заполнить образовавшийся дефект, что позволяет сохранить определенное внутреннее давление при движении. Такое решение позитивно сказывается на безопасности езды, особенно на высокой скорости.
Производители «бескамерок» предусмотрели в конструкции специальные выпуклости по краям, позволяющие уплотнить стыки покрышек при повышении внутреннего давления. Называются такие элементы «хампами». Подобная особенность затрудняет самостоятельную разборку. В таком случае используется станок для бортировки колес, создающий преимущественное давление, которое дает возможность сорвать покрышку с места.
Особенности
В дороге водителю смогут помочь специальные комплекты для ремонта шин бескамерного типа. При сильном повреждении добраться до места ремонта можно, если поместить внутрь деформированной «бескамерки» обычную камеру, подходящую по размеру.
Не обязательно использовать приспособление для бортировки колес, чтобы надеть бескамерную шину на диск. В этом процессе поможет силиконовая смазка и тонкая монтажка (для 16-ти дюймовых колес подойдет 300 мм). Проблема возникает при накачке покрышки, необходимо, чтобы борт элемента перескочил через хамп колеса. Сделать это не так просто, поскольку требуется подача значительного объема воздуха, который не обеспечивают стандартные автомобильные компрессоры.
Помочь в решении проблемы может 15-20 грамм эфира, содержащегося в наборе «Быстрый старт». Такой вариант также прекрасно подходит для зимнего периода. При таком способе накачки, главное, не переусердствовать с количеством горючего.
Пошаговая инструкция по самодельной бортировке колес бескамерного типа
Операция проводится в такой последовательности:
- На колесе откручивается клапан.
- Внутрь покрышки заливается немного горючей жидкости (эфир, спирт).
- Также немного воспламеняющего средства помещается на бортик шины, после чего эта смесь поджигается.
- При помощи ударов горящая часть бортика продавливается вовнутрь, чтобы активировались пары горючего, находящегося во внутренней части покрышки.
- Полученный взрыв позволит одеть самопроизвольно покрышку на хампы, одновременно потушив остатки пламени.
- Через несколько секунд, после окончания горючей реакции, можно подсоединять компрессор.
Рекомендации
Имея приспособление для бортировки колес своими руками, может показаться, что данная процедура элементарна для любого пользователя. Однако и здесь есть свои нюансы. Ниже приведены рекомендации специалистов:
- Колесо должно собираться с шинами, камерами и дисками, размеры которых соответствуют друг другу.
- При замене одного колеса, не рекомендуется монтировать другой тип шин. Например, если четыре колеса летнего типа – не следует ставить один зимний вариант.
- При установке шин желательно использовать исключительно новые камеры.
- Не допускайте попадания грязи под покрышку.
- Не используйте для разборки отвертку. Мало того, что так не получится снять резину, так вы еще сможете ее повредить.
Как правило, бортировка грузовых колес проводится при смене резины летнего типа на зимний вариант, или наоборот. Иногда данная процедура требуется в случае прокола камеры либо повреждения диска.
Интересные моменты
Изобретателем первой резины вулканического типа, предназначенной для производства шин, считается Чарльз Гудьир, который создал данный материал в 1844 году.
Автомобильная шина самых крупных габаритов находится в американском городе Детройте, который негласно именуют, как «Поселение моторов». Покрышка была создана в Нью-Йорке конструкторами концерна «Унироял». Ее создание приурочено к показу на Всемирной выставке в 1965 году.
Если резина повредилась в связи с наездом на гвоздь или другой похожий предмет, не спешите вытаскивать его. Элемент перекрывает собой большую поверхность отверстия, что позволяет доехать до гаража или ближайшего пункта по шиномонтажу.
Самодельный станок для бортировки колес
В конструкцию подобного приспособления входят следующие элементы:
- Остов или рама. Эта деталь обычно представляет собой пару прямоугольных труб профильного типа, размещенных параллельно между собой. Между собой элементы соединяются при помощи стального уголка.
- Вертикальная стойка. Она крепится к раме, выполняет функцию крепления рычага, а также играет роль основного наконечника по демонтажу покрышки и площадки для установки диска.
- Труба с приваренной рукояткой. Деталь используется в качестве рычага, когда производится снятие покрышек.
Итог
Провести самостоятельную бортировку колеса не очень просто, но возможно. Следуя указанным рекомендациям, вы сможете провести эту операцию за несколько минут. Существенно облегчает процесс специальный заводской станок или приспособление, сделанное своими руками.
бортировка колёс
О нескольких безударных способах эффективной бортировки колёс автомобиля и о несложных самодельных приспособлениях для этого дела я уже написал вот в этой статье. Ну а эта статья посвящается мотоциклистам и в ней будут описаны несложные, но эффективные приспособления для бортировки шин на мотоциклетные колёса. Кстати, некоторые приспособления, описанные в этой статье, подойдут и для бортировки колёс автомобиля.
Бортировка колёс (или разбортировка) как автомобиля, так и мотоцикла — процесс ответственный и трудоёмкий, но в большинстве регионов разбортировка покрышек мотоциклов так до сих пор и не развита и мотоциклистам всё приходиться делать своими руками. А вот как, и с помощью чего облегчить процесс бортировки колёс мотоцикла и будет подробно описано в этой статье.
Начну с мелочей:
- Первая проблема для новичков — это как вставить вентиль камеры в отверстие обода (особенно если покрышка довольно жёсткая и трудно просунуть руку между ней и ободом).
Но эта проблема решается очень просто, если в запасном колпачке просверлить небольшое сквозное отверстие, и далее в это отверстие пропустить отрезок троса, длиной примерно 20 — 30 см, ну и кончик троса желательно пропаять.
Теперь остаётся накрутить колпачок на вентиль камеры и через отверстие в ободе кончик троса вытаскиваем наружу, а за тросом послушно следует и вентиль. Однако если колпачок достаточно толстый и не пролазит через отверстие обода (на многих ободах отверстие небольшое), значит следует выкрутить золотник и вкрутить вместо него запасную мотоциклетную спицу, которая имеет такую же резьбу, как и внутренняя резьба в вентиле.
Спицу можно использовать и целиком, но это не совсем удобно, значит от спицы следует отрезать лишь резьбовую часть, затем с отрезанной стороны спицу немного расплющиваем и сверлим отверстие для троса, который опять же поможет протянуть вентиль камеры через отверстие в ободе.
- Вторая проблема — это сама бортировка колёс, то есть процесс монтажа покрышки на мотоциклетный обод.
При этом новички зачастую портят камеру монтажными лопатками, а иногда умудряются испортить и закраину покрышки, то есть рвут вживлённый в закраину покрышки её бортовой трос. Чтобы этого избежать, есть несколько вариантов.
Бортировка колеса — доработка лопатки.
1 — монтажная лопатка, 2 — покрышка, 3 — камера, 4 — обод колеса
Первый и самый простой вариант — это доработать монтажные лопатки, как показано на рисунке 1. Кончик лопатки следует нагреть газовой горелкой на длину примерно 10 — 12 мм и после нагрева следует выгнуть кончик лопатки в противоположную сторону, чтобы кончик лопатки получился такой, какой указан красной стрелкой на рисунке 1.
После загиба углубление у самого кончика дорабатываем круглым напильником и далее шлифуем и полируем кончик лопатки. После такой доработки ваша монтажная лопатка 1 (см. рисунок 1) будет плотно ложиться на обод 4 колеса и не соскальзывать с него при монтаже шины 2. Кстати, полезно закраину покрышки и сам обод смочить мыльной водой — это позволит смонтировать покрышку на обод довольно легко.
Самодельные приспособления для бортировки колёс мотоцикла.
Приспособления, которые будут описаны ниже, изготовить своими руками сложнее, но зато они существенно облегчат бортировку колёс вашего байка и будут исправно служить вам долгие годы.
Самое простое приспособление показано на рисунке 2. Как видно из рисунка, оно состоит из двух стальных реек, и оси, которая их соединяет.
Рейки несложно вырезать из профильной трубы 40х20 мм, ну а так же длина реек указана на рисунке 2. Затем следует просверлить на концах рейки отверстия для оси, диаметром 10 мм и соединить рейки осью (в качестве оси можно использовать болт или шпильку на 10). Ну и крючок на длинной рейке, который указан красной стрелкой на рисунке 2, следует сделать без острых граней и обязательно его отполировать, так как он будет давить на закраину покрышки с довольно большой силой.
При монтаже покрышки на обод, как видно из рисунка 2, короткую рейку упираем в кромку ступицы колеса мотоцикла, а с помощью длинной рейки, которая работает как рычаг, перетягиваем закраину покрышки через край обода с помощью крючка (указан красной стрелкой) на конце рейки.
При перетяжке покрышки через край обода, следует обязательно следить за тем, чтобы на противоположной стороне колеса, покрышка была обязательно утоплена в углублении обода (в то углубление, где расположены отверстия спиц). Иначе возможно порвать крючком рычага закраину покрышки, надеюсь это понятно новичкам. Ну и незабываем, что так же не помешает смочить закраины обода и покрышки мыльной водой.
Ниже будут описаны ещё два приспособления для бортировки колёс мотоцикла или автомобиля. Изготовить их ещё сложнее, но зато изготовив их, вы на долгие годы забудете про поиск мотоциклетного шино-монтажа в вашем регионе, так как описанные ниже приспособления будут работать не хуже, чем дорогой шино-монтажный станок в каком нибудь автосервисе.
Только лишь с тем отличием, что для их работы не требуется электроэнергия, а значит эти приспособления можно взять с собой в дальнюю дорогу. К тому же приспособления можно изготовить и для бортировки колёс автомобиля, только лишь делаем всё более мощное (то есть с запасом прочности деталей, ведь автопокрышки имеют более толстые закраины).
Бортировка колёс — ещё два приспособления: 1 — шайба, 2 — ось, 3 — шплинт, 4 — ось вилки, 5 — реечная шестерня (зубья не показаны), 6 — рейка с нажимным сухарём.
Приспособление, показанное на рисунке 3А самое сложное в изготовлении, так как в нём есть детали (например реечная шестерня 5 и рейка 6 с зубцами) которые нужно будет заказать фрезеровщику. Так же потребуется заказать токарю оську 2, и вилку 4, подобрать шайбу 1 и шплинт 3. Все размеры указаны на рисунке 3А.
Вилка 4 имеет такой же диаметр как и ось колеса вашего байка (диаметр вилки 17 мм на рисунке чисто условный), и перед шино-монтажом вилка 4 вставляется вместо оси колеса в подшипники колеса вашего мотоцикла. После этого нажимной сухарь подводится к закраине покрышки (конец сухаря обязательно следует отполировать).
Далее, посредством рычажной шестерни с ручкой нажимаем на закраину шины, пока кромка шины не задвинется за кромку обода колеса (диаметр ручки 11 мм тоже условный и на ручку разумеется можно надеть удлиняющую трубку-рычаг). Далее передвигаем сухарь с рейкой в право или влево и продолжаем давить на кромку покрышки, пока он полностью не надвинется на обод.
Ну и последнее приспособление для бортировки колёс показано на рисунке 3Б. Принцип его работы почти такой же как и у большинства балансировочных станков в шиномонтажных мастерских. Говоря проще, принцип действия заключается в использовании рычага 4 с роликом 1, который давит на кромку последних 15 — 20 см покрышки, пока она не задвинется за кромку обода.
Перед бортировкой колеса, ось колеса вставляют в подшипники ступицы, затем отверстие на конце приспособления одеваем на ось колеса. При этом ролик на оси 2, закреплённый на рычаге с помощью гайки 3, подводим к закраине покрышки и далее продолжаем осторожно перемещать рычаг по радиусу колеса, надавливая роликом на край покрышки до тех пор, пока покрышка не наденется на обод.
Основное преимущество таких приспособлений, как я уже говорил, в том, что они имеют небольшие габариты и не потребляют ни грамма (точнее микроампера) электричества, а значит их можно всегда взять с собой в дорогу и забыть про мученье с монтажными лопатками.
Ну и последний совет. После монтажа другой покрышки (и даже камеры) советую отбалансировать ваше колесо с помощью простого самодельного устройства (о балансировке колёс мотоцикла и о самодельном устройстве для этого дела я подробно написал вот тут). А как выбрать мото-покрышки и о правильной эксплуатации мотоциклетных шин я написал в этой статье.
Вот вроде бы и всё, надеюсь изготовив для себя одно из приспособлений, описанных выше, бортировка колёс вашего мотоцикла, или автомобиля, теперь будет происходить легко и просто, успехов всем.
Как сделать станок шиномонтажный своими руками? :: SYL.ru
В дороге случаются различные неприятности, и пробитое колесо — это одна из них. Но данная ситуация может быть осложнена не отремонтированной вовремя запаской. В этом случае возникает желание сделать шиномонтаж самостоятельно. Конечно, для этого нужны инструменты и определенные навыки. Помочь здесь могут домкрат и буксировочный трос.
Как отремонтировать колесо в дороге
- Сначала нужно снять колесо и очистить его от грязи.
- Спустить воздух с колеса и положить его вверх ниппелем.
- Продеть буксировочный трос в отверстие на диске.
- Поставить домкрат на бок шины, близко к ободу. Если в резине имеется камера, то нужно быть аккуратнее со штуцером.
- После этого трос накинуть на кронштейн и зафиксировать его концы друг с другом.
- Ручку домкрата нужно вращать таким образом, чтобы трос поднимался вверх, а упирающееся в шину основание перемещало вниз посадочное кольцо.
- Как только покрышка отделится от диска, можно выполнять следующую операцию.
- Если идет только ремонт или смена камеры, то с помощью двух монтажек нужно поднять бок шины рядом со штуцером на край обода.
- Штуцер убрать внутрь, а камеру вытащить из-под шины.
- Из хорошей камеры нужно достать ниппель и выдавить из нее воздух.
- Чтобы установить хорошую камеру, надо отогнуть боковину шины и вставить штуцер в специальное отверстие. После чего камера помещается в шину.
- Чтобы не испортить камеру монтировкой, устанавливая шину, нужно немного подкачать камеру, не вставляя ниппель.
- Когда колесо забортовано, ниппель нужно вставить в штуцер. После накачать и установить на место.
Данный способ ремонта подходит лишь в крайнем случае, если шиномонтажная мастерская слишком далеко. Гораздо выгоднее проводить такие манипуляции самостоятельно, а при желании можно сделать станок шиномонтажный своими руками. Такое оборудование не только сэкономит бюджет, но и в осенне-весенний период поможет избежать очереди в автомастерских. В данной статье подробно рассказано, как сделать шиномонтажный станок своими руками.
Самодельный станок для бортировки колес
Сама процедура смены шин на первый взгляд кажется достаточно простой. Для замены нужно всего лишь демонтировать старую шину с диска, после чего установить новую. При этом здесь есть небольшая проблема: чтобы произвести демонтаж, потребуется немало усилий. Конечно, с помощью специальных инструментов, представленных дорожным набором, процедура может пройти легче.
В таком наборе имеются монтировки различной формы, а также несколько специальных клиньев. Эти инструменты облегчают процесс бортировки колес, но все равно сделать это будет непросто, особенно если шины долго находились в эксплуатации. Решить эту проблему поможет шиномонтажный станок. На фото выше вы можете посмотреть, как выглядит чертеж самодельного шиномонтажного станка.
Составляющие шиномонтажного станка
Ручной шиномонтажный станок своими руками проводят с помощью таких деталей:
- Рама. Как правило, это две прямоугольные профильные трубы, располагающиеся параллельно. Такие элементы соединяются стальным уголком.
- Вертикальный стояк. Его крепят к раме. Такой стояк выполняет несколько функций. В первом случае это крепление рычага, предназначенное для демонтажа покрышки, а во втором — площадка, на которую устанавливают диск.
- Труба. К ней приваривается рукоятка. Труба играет роль рычага при снятии покрышек.
Для изготовления такого оборудования самостоятельно лучше запастись заранее высококачественным металлопрокатом, поскольку данный инструмент используется при огромных нагрузках. Важно и то, что можно довольно легко изготовить самодельный шиномонтажный станок своими руками. Чертежи для этого используются простые, а пользы от такого оборудования много.
Изготовление шиномонтажного станка
В данном разделе статьи подробно описывается, как самому сделать шиномонтажный станок своими руками, а точнее — целый комплект.
В него входят два приспособления — сам шиномонтажный станок и устройство отбивки борта, которые объединены в одно. Нижняя часть рамы станка Н-образная, размеры — 90 х 60 см. Для ее изготовления потребуется стальная труба с прямоугольным сечением. На перемычку в 30 см от края приваривают двухдюймовую трубу с круглым сечением. Угол при этом должен быть прямым. Высота привариваемой трубы составляет примерно 1,5 метра. Место сварки усиливают с помощью косынок (прямоугольные треугольники толщиной 5 мм).
На трубу для закрепления колеса нужно надеть старую ступицу и приварить ее. Ступицу устанавливают на определенной высоте, которую подбирают под рост человека. Лежащее на ней колесо должно быть примерно по пояс. Сама труба должна быть примерно на 30 см выше баллона. Немного пониже ступицы нужно приварить кронштейн, чтобы крепить устройство отбивки борта. Его можно сделать из части стального листа толщиной 4-5 мм. В нем просверливается отверстие для болта.
Рычаг, с помощью которого снимают и устанавливают покрышки, изготавливают из стальной трубы. Ее длина — примерно 1,5 метра. Для изготовления наконечников на рычаг потребуется стальной прут диаметром 20 мм. Наконечники делаются на токарном станке или выпиливаются болгаркой. Так выполняется самодельный шиномонтажный станок своими руками.
Как производится снятие шин шиномонтажным станком
- Колесо нужно очистить от грязи и вынуть ниппель.
- Чтобы не поцарапать диск, под колесо можно положить резиновый коврик, под который следует подсунуть основание отбойника.
- Затем лапка отбойника поднимается и устанавливается на бок шины.
- Для смазки посадочного кольца покрышки используется мыльный раствор.
- Рычаг вставляется в трубку отбойника.
- При помощи нажатий на рычаг посадочный борт шины отбивается сначала с одной стороны, потом — с другой.
- Колесо надевается на трубу и присоединяется с помощью болтов к ступице болта.
- С помощью монтажки нужно приподнять борт шины и вставить под него прямой конец рычага.
- Для смазки наконечника, посадочного борта и кромки обода используют также мыльный раствор.
- Нужно сделать упор рычага в трубу над колесом и потянуть рычаг на себя, таким образом, борт шины снимется с диска.
- Камера вынимается из покрышки.
- Покрышка снимается с диска.
Монтаж шин
Станок шиномонтажный своими руками изготавливается достаточно быстро. Монтаж шин с его помощью осуществляется следующим образом:
- С помощью мыльного раствора нужно смазать посадочный борт шины, обод и монтажный наконечник рычага.
- Посадочный борт следует частично надеть на диск.
- Между диском и посадочным бортом вставляется наконечник рычага, при этом шар наконечника должен упираться в диск, а участок посадочного борта должен располагаться примерно посередине наконечника.
- Сделав упор рычага в трубу над колесом, нужно потянуть его на себя, монтажный наконечник при этом будет надевать борт покрышки на диск.
- После этого таким же образом следует надеть нижний посадочный борт и накачать колесо.
Таким образом, станок шиномонтажный своими руками создается без особых финансовых затрат и позволяет без труда сменить резину на автомобиле самостоятельно.
Полезные советы
- Угол приварки наконечника для забортовки к рычагу нужно делать меньше — так резину легче надеть на диск. Здесь главное — не перестараться.
- Станок шиномонтажный своими руками создается быстро и получается довольно легким, поэтому для большего удобства его нужно прикрепить к полу.
- Чтобы облегчить работу и не испортить диски и резину, нужно смазывать все части мыльным раствором.
Искусство копать яму
ТБМ диаметром 18,5 футов по прозвищу «Сэнди» прорывается в одном из водных туннелей главного кольца Лондонского кольца, в рамках проекта, состоящего из почти 50 миль туннелей. |
ТБМ Groene Hart диаметром 48 футов строится компанией NFM Technologies. |
Ловать жесткого рок ТВМ использует расширяющееся упорное кольцо для якоря машины и обеспечить базу, с которой толкающие цилиндрами могут отталкиваться от вождения и режущей головки вперед. |
Ричард и Рик П. Ловаты, президент и вице-президент Lovat Inc., стоят перед машиной, построенной их компанией для рытья линии метро под Лиссабоном, Португалия. Машина грузоподъемностью 1200 тонн использует 1800 кВт для поворота режущей головки. |
Техник из Wirth Tunneling Ltd. в Шотландии исследует канавки в твердой породе, сделанные отрезными дисками TBM. |
Проходческие туннельные машины (ТБМ) могут стать идеальным электроинструментом. Они чудовищны, весят миллионы фунтов и прилагают усилия, измеряемые тысячами тонн, и могут прорваться сквозь самые твердые породы на земле. Кроме того, большинство из них поставляется со всей железной дорогой и поездом в качестве вспомогательного оборудования. Что еще нужно властолюбивым мастерам?
В некоторых случаях, например, в туннеле под Ла-Маншем, машины настолько велики и построены с такими уникальными характеристиками, что по завершении работы их лишают пригодного для использования оборудования и бросают под землю.Компании также ремонтируют и перепродают некоторые ТБМ, обычно это машины более стандартного размера с диаметром от 6,5 до 13 футов. Но для большинства проектов ТБМ изготавливаются по индивидуальному заказу. Как сказал один производитель ТБМ: «Каждая из наших машин — это прототип». Один из наиболее важных критериев при проектировании машины — определить, через что она будет копать.
В твердых породах
ТПМ для твердых пород проще, чем те, что предназначены для мягких грунтов, потому что туннель, однажды вырытый, сам поддерживает себя.Нет необходимости в прокладках для предотвращения обрушения туннеля, а TBM может отталкиваться от стенок, создавая прямое давление. Конечно, есть пределы. Порода с прочностью на сжатие более 30 000 фунтов на квадратный дюйм, такая как плотные кварциты с прочностью до 60 000 фунтов на квадратный дюйм, по-прежнему более экономична для бурения и взрыва, чем для выемки грунта с помощью ТБМ.
В передней части TBM находится режущая головка, вращающийся барабан с свободно вращающимися режущими дисками, установленными на плоской поверхности. Отрезные диски, изобретение компании Robbins Co.В Солоне, штат Огайо, есть бита или обод из карбида вольфрама, которые вращаются по кругу из закаленной инструментальной стали. Диски расположены на расстоянии около 3 дюймов друг от друга и расположены так, чтобы покрывать поверхность туннеля. Колеса вращаются за счет трения, поскольку режущая головка вращается, а гидравлические цилиндры толкаются сзади. Это усилие зависит от количества и размера отрезных дисков.
По словам Джона Тернера, главного инженера Robbins, тяга, которую ТБМ может оказать на диск, увеличивается пропорционально квадрату его диаметра. «И хотя самые большие диски когда-то были всего 12 дюймов., сейчас мы используем в основном 17 и 19 дюймов. диски: «17-дюймовые диски рассчитаны на 60 000 фунтов каждый, а 19-дюймовые диски — на 70 000 фунтов». Но отдельные фрезы могут воспринимать импульсные нагрузки, в 10 раз превышающие их номинальные значения », — отмечает Тернер.
« Каким образом «Диски на самом деле работают, это не совсем понятно», — добавляет Тернер. «Мы думаем, что диски раскалывают камень, когда они вращаются, подобно тому, как стеклорез режет стекло. Диски создают круглые зоны сжатия. Трещины распространяются из одной зоны раздавливания в другую, а затем выпадают стружки. Таким образом, машины измельчают от 20 до 30% породы, а щепа доставляется бесплатно.»
Скорость дисков, измеряемая в периферийной скорости, с годами увеличивалась по мере улучшения подшипников. Когда-то скорость была ограничена до 300 футов / мин, но теперь диски перемещаются до 650 футов / мин. Для режущей головки 11,5 футов , 650 футов / мин означает 18 об / мин, а с дисками, проникающими со скоростью от 0,125 до 0,5 дюйма / об, ТБМ могут туннелировать со скоростью от 11 до 45 футов / ч.
Диски проверяются ежедневно и меняются примерно каждые 500 000–1 500 000 подвижных футов в зависимости от твердости и абразивности породы.Изношенные фрезы заменяют кольцевидные насадки. Сегодняшние туннелеры имеют пространство за режущей головкой, что позволяет проводить техническое обслуживание и замену резца, в то время как TBM все еще прижат к забоям тоннеля.
Регулируемые экраны на лицевой стороне режущей головки определяют, сколько вынутой породы, обычно называемой навозом, проходит за головкой. Винтовой конвейер или лезвия скребка внутри режущей головки поднимают навоз на конвейер, который проходит через главный подшипник. Ремень вынимает навоз из туннеля или переносит в железнодорожный вагон.
В простейших машинах для работы с твердыми породами используется Келли — вертикальная балка, которая выдвигается и прижимается к потолку и полу туннеля для закрепления ТБМ. Основной луч станка, который удерживает режущую головку и основной подшипник, проходит через Келли и использует его в качестве упорного пьедестале. Прижимные цилиндры балки отталкиваются от Келли и прижимают режущую головку к скале. Может быть до 10 цилиндров тяги с ходом от 4 до 25 футов. Когда цилиндры тяги достигают полного выдвижения, Келли перемещается, и процесс повторяется — ход, сброс, ход, сброс — перемещение до 0.6 миль в месяц.
TBM на основе Келли позволяют режущей головке двигаться только вперед и назад. Машиной нельзя управлять во время работы. Поэтому, если кто-то наткнется на особенно твердую породу с левой стороны забоя туннеля, голова и остальная часть TBM захотят согнуться, но не смогут. Это создает огромные изгибающие нагрузки на конструкцию, которые могут разрушить ТПМ.
Роббинс усовершенствовал подход Келли и установил захваты прямо на главную балку. «Мы устанавливаем захваты на цапфах, чтобы обеспечить шесть степеней свободы между машиной и захватами», — говорит Тернер.«Он полностью плавающий, поэтому оператор может поворачивать вверх, вниз, влево, вправо и катить TBM, пока он бурится». Захваты выдвигаются наружу с усилием в 2,4–2,8 раза превышающим общую прямую тягу, приложенную к главной балке. (Общее приложенное усилие рассчитывается путем умножения количества режущих дисков на усилие, которое каждый из них может выдержать, затем прибавляет вес машины, плюс коэффициент трения для учета контакта между TBM и стенками туннеля и дополнительный коэффициент безопасности.)
«По сравнению с машиной Келли, пути загрузки с плавающими захватами более эффективны, но для их работы требуется больше навыков оператора», — добавляет Тернер.
Существуют туннели в твердых породах, которые требуют облицовки, например, туннели для пригородных поездов или шоссе. Никто не хочет, чтобы камень упал на рельсы или сквозь лобовое стекло. Для таких работ некоторые компании строят ТБМ с одной защитой. На них металлическое покрытие или щиток цилиндрической формы окружает оборудование позади режущей головки. За щитом система линейного ремонта аккуратно прикрепляет сборные железобетонные или стальные облицовки по окружности туннеля. Упорные домкраты на задней кромке щита отталкивают последнее кольцо футеровки, вдавливая режущую головку в почву. Проблема с этой установкой в том, что она использует вкладыши для тяги, что означает, что вы не можете растачивать при установке вкладышей, и это тратит время.
«Это привело к ТБМ с двойной защитой, — говорит Тернер. «Эта щитовая проходка имеет второй щит прямо позади режущую головки. Этот второй щит имеет захваты или упорное кольцо, которые распространяются на стены туннеля, так что он не опирается на прокладках для тяги, так экипажи могут установить сегменты во время бурения.»
Управлять этими длинными экранированными TBM стало проще за счет создания шарниров между щитками и, в некоторых случаях, на дополнительной хвостовой части.Они позволяют щитам перемещаться на 2–3 и снижают вероятность того, что БТМ будет «прикованным к железу» — условием, при котором щит прилипает к футеровке, когда оператор меняет курс. Бронированные ТБМ застревают в ловушке и не могут двигаться вперед или назад, что не дает строительным бригадам альтернатив, ни одна из которых не является недорогой или быстрой.
TBM могут делать повороты, но они не совсем уж шпильки. Путем осторожного приложения большего давления к одной стороне режущей головки машины могут изменить курс примерно на 0.125 дюймов / фут. «Типичный радиус поворота составляет от 300 до 400 футов», — говорит Тернер. «Но мы строим специальные ТБМ, если рабочие места требуют более крутых поворотов. Самый узкий радиус, который мы когда-либо выкопали, составлял 90 витков на 75 футов в южноафриканском золотом руднике. Один из наших ТБМ также выкопал ускоритель частиц ЦЕРН в Европе, который представляет собой эллипс. . Его туннель постоянно поворачивается с постоянно изменяющейся скоростью. К счастью, это большой эллипс диаметром семь миль ».
В мягком грунте
«В твердых породах трудность заключается в выемке материала на забое.Стены самонесущие. Однако на мягком грунте трудность заключается не в выемке забоя, а в поддержании туннеля », — говорит Марко Джорелли, менеджер по продукции компании Lovat в Этобико, Канада. Lovat специализируется на ТБМ для мягкого грунта и смешанного забоя, но построила машины для все типы грунта, включая твердые породы.
Подобно машинам для твердых пород, в TBM для мягких грунтов используется вращающаяся режущая головка, но для нее требуется гораздо меньшая сила тяги вперед и не используются режущие диски. Вместо этого на головке установлены рыхлители и зубья лопаты.Рыхлители проникают в почву и выкапывают ее, а зубья лопаты собирают и перемещают ее.
Но ТБМ с мягким грунтом должны поддерживать забой туннеля, а также крышу и стены туннеля до тех пор, пока бригада не сможет установить сегменты хвостовика, удерживающие окружающую землю. Без этой постоянной поддержки ТБМ может создать «пересадку», ситуацию, при которой выкапывается слишком много земли или породы. «Я видел, как в результате перераскрытия были открыты пещеры высотой 300 метров над ТБМ, и вся эта грязь падала прямо на машину», — говорит Тернер.«И обвал может доходить до поверхности, что является настоящей катастрофой. Фермеры раздражаются, когда их коровники исчезают».
«Перераскопки могут быть особенно опасными в городах», — отмечает Джорелли. «Они приводят к заселению, и не нужно много времени, чтобы повредить здания».
Компания Lovat использует навоз в качестве жидкости под давлением в режиме полувысокого давления для удержания забоев в некоторых туннелях с мягким грунтом. Грязь проталкивается в камеру за режущей головкой, где она собирает и создает давление для поддержки забоя.Кольцо для удаления навоза удерживает навоз на месте до тех пор, пока дверь, клапан сброса давления, периодически не открывается, чтобы сбрасывать навоз на конвейер.
Если забой туннеля нуждается в большей опоре, используются противотанковые балки с грунтовым давлением (EPB). Они используют находящуюся под давлением грязь вместе с силой от режущей головки. Шнековый конвейер удаляет грязь, при этом давление внутри головки не падает. Если оператор прикладывает слишком много усилий к голове, грязь собирается и выталкивается вверх к поверхности, создавая волну. Слишком мало нажимайте, и поверхность осядет. Оператор следит за продвижением вперед и давлением на почву, чтобы определить нужный уровень силы.
Альтернативой EPB, заимствованной из буровой промышленности, является перекачка суспензии перед режущей головкой и за ней для обеспечения поддержки. Суспензия обычно содержит бентонит, тиксотропный материал, то есть материал, который течет под давлением, но затвердевает, когда стоит на месте.
Некоторые проекты должны проходить через «выдавливающуюся землю», при которой туннель сжимается, вдавливая до 300 тонн / квадратный метр, по словам Тернера.
Уловка, по его словам, заключается в том, чтобы продолжать движение и не позволять земле захватывать машину. Чтобы помочь, компании создают режущие головки, которые механически расширяются, проходя через туннели, немного превышающие размер ствола TBM. Режущие головки также разработаны с режущими дисками, расположенными ближе друг к другу по внешнему краю и направленными наружу, чтобы сделать отверстие больше, чем TBM.
«Как видите, важно знать, через какую землю вы проходите», — говорит Тернер. «Если машина для обработки твердых пород встречается с мягким грунтом, она застревает, потому что не может оттолкнуться от стен туннеля, если она также не возводит за ней подходящую облицовку.Экипажу придется окопать ТБМ и использовать раствор и цемент для возведения стен, пока они не смогут выдержать давление. В противном случае этот TBM никуда не денется ». Чтобы еще больше проиллюстрировать ценность знания того, что вы будете копать, он говорит о печально известном ирригационном туннеле в Якамбе, Венесуэла.« Они начали работу над ним 25 лет назад и столкнулись с выдавливанием. земля. Последнее, что я слышал, они отказались от проекта ».
Выбор источника питания
Некоторые компании, такие как Lovat, используют гидравлику для привода TBM.«У них высокий крутящий момент на низких скоростях, а это именно то, что нам нужно для проходки туннелей в мягком грунте», — говорит Джорелли. «В некоторых случаях гидравлика также снижает риск возникновения проблем с электричеством во влажной среде под землей».
Инженеры Robbins имеют опыт работы с электроприводами. Они обнаружили, что частотно-регулируемое управление с широтно-импульсной модуляцией позволяет электрическим приводам вести себя так же, как гидравлические. «Мы обычно используем трехфазные двигатели переменного тока с короткозамкнутым ротором, соединенные через муфту с коробкой передач 30: 1.Муфта предотвращает многократный запуск и остановку двигателей и позволяет нам запускать их по очереди, — говорит Тернер. — Мы можем установить дюжину двигателей мощностью 315 кВт на режущую головку TBM. Включение их всех одновременно требует огромной нагрузки и действительно привлекает внимание вашей электрической компании. Двигатели, управляемые ПЛК, соответствуют стандартам, предотвращающим утечки и обеспечивающим защиту от замыкания на землю, поэтому безопасность не является большой проблемой. Гидравлика, с другой стороны, занимает много места, неэффективна и может загрязнить участок.»
Одним из последних достижений в проходке туннелей мягкого грунта является кондиционирование почвы. Строительные бригады вводят мыльную пену или длинноцепочечные полимеры для пластификации песка и других рыхлых грунтов, заставляя их вести себя как глина, по словам Джорелли из Lovat. чтобы сделать его более управляемым. И если бригады подозревают, что впереди есть подземное озеро или ручей, они проверяют это с помощью буров переднего зондирования. Если они обнаруживают слишком много воды, они закачивают раствор и бетон в область, чтобы создать грунт и сделать его водонепроницаемым, затем туннель через него.
Обеспечение безопасности
Когда проект требует наклонных туннелей, бригады предпочитают начинать с забоя и бурить в гору. Он предотвращает скопление воды в буровой части туннеля и упрощает транспортировку навозной навозной породы грузов при спуске с горы. Конечно, ТБМ нужно больше сцепления и тяги, чтобы противостоять гравитации, а также сильные упоры, чтобы ТБМ не выскользнул из туннеля.
«Четыре процента уклона — это предел для большинства стандартных TBM из-за ограничений тягового усилия поездов», — говорит Джорелли. «Но мы сделали машины для более крутых туннелей. Мы построили напорный водовод для подачи воды на гидроэлектростанцию в Сьоне в Швейцарии. Он имеет наклон 35 °. ТБМ очищал около 15 футов в день, что было около 100 футов в день, если скучно по горизонтали «.
Доводя ТБМ до вертикального предела, одна компания во время холодной войны работала с правительством над созданием машины, которая могла бы вести
прямо вверх. План заключался в том, чтобы на шахте стояли машины, готовые пробурить поверхность.Затем, в случае войны, ТБМ прорвутся на поверхность, а шахта будет служить ракетной шахтой, которую нельзя будет уничтожить до запуска своей ракеты.
Другие функции безопасности на TBM включают детекторы газа, которые обнаруживают опасные газы, такие как метан. При обнаружении газа в туннель закачивается больше воздуха, чтобы его разбавить. Также имеются системы пожаротушения для электрошкафов и гидробаков. Гидравлический резервуар также имеет азотный аккумулятор, который поддерживает давление в системе в случае, если гидравлическая система не сможет заблокировать двери и конвейеры.
ТПМ с мягким грунтом и сбалансированным давлением грунта от Ловата была построена для рытья туннелей метро диаметром 18,8 футов в Казани, Россия. Он использует винтовой конвейер длиной 31 фут для перемещения грязи от режущей головки к конвейеру и может использовать бентонит или пену для кондиционирования почвы перед ТБМ. 409-тонная машина имеет длину 230 футов и общую тягу 4400 тонн. Облицовка, которую он возводит, состоит из семи частей и замкового камня, каждая примерно 3 фута в длину и 0,75 фута в толщину.
Микротоннелирование и бестраншейные технологии
Не все ТБМ предназначены для бурения железнодорожных туннелей через горы или прокладки многополосных автомагистралей под реками. При установке труб, бурильные станки с дистанционным управлением прикрепляются с помощью расширяющихся захватов к концу трубы. Буровая головка выкапывает грунт, в то время как грязь попадает в головку через регулируемые дверцы и уносится конвейерными лентами или винтами или смешивается с водой и откачивается. Вся труба, которая действует как футеровка, гидравлически «толкается» вперед, выталкивая режущую головку в новую грязь.В трубах диаметром до фута домкраты развивают тягу до 20 тонн. Отрезки трубы привариваются к исходной трубе, образуя сплошную облицовку. Тщательно настроенный лазерный луч проходит через светочувствительные матрицы и направляет направляющий луч на поверхность выемки.Сигналы от массивов используются для расчета положения TBM, тангажа, рыскания и крена. Пилот, обычно находящийся на поверхности, контролирует эти показания и вносит поправки. В простых мини-ТБМ пилот контролирует, какой участок забоя будет выкапывать и, следовательно, в каком направлении пойдет небольшой ТБМ. В более сложных версиях TBM имеет шарнирно-сочлененную форму, и передняя часть может перемещаться на 5 ° или меньше в любом направлении. Пилот направляет TBM по правильному пути за счет давления режущей головки, прикладывая больше с одной стороны, чем с другой. В больших туннелях, до 168 дюймов в диаметре, микротоннелеры действуют как их более крупные собратья, поднимая сегменты хвостовика, когда они копают мягкий грунт, и нажимая на вкладыши для гидравлического продвижения режущей головки. Бестраншейная технология немного дороже, чем рытье траншеи, если только требования не требуют прокладки труб или инженерных коммуникаций глубже, чем обычно, или через очень влажную почву. «Но это по-прежнему жизнеспособная альтернатива разорению улиц и блокировке движения», — говорит Карл Нигой, исполнительный директор Аккермана.«Городские инженеры не учитывают социальные издержки, связанные с потерей времени и топлива, а также неистовством на дорогах, которые вызывают рытье траншей, поэтому ТБМ всегда кажутся слишком дорогими. Но если бы эти затраты были включены в инженерные расчеты, а общественность знала, что они этого не сделали» не придется мириться со всеми этими неудобствами, ТБМ будут использоваться гораздо чаще для установки утилит ». |
Национальное достояние: Не беспокоить
Когда будет построена линия высокоскоростной железной дороги Thalys к северу от Роттердама, до Амстердама, северного конца линии, будет всего 2 часа езды на поезде от Парижа. На своем пути к северу от Роттерэма железнодорожная линия переходит в Грун-Харт (Зеленое сердце), тысячи акров земли, на которых расположены низменные каналы, каналы и сельская местность, усеянная ветряными мельницами.В этом районе также находится важный птичий заповедник. Команда дизайнеров во главе с Bouygues Construction быстро приняла решение о прокладке туннелей, чтобы свести к минимуму воздействие на окружающую среду и визуальное восприятие. Они также решили построить один туннель диаметром 43,6 фута, а не два туннеля диаметром 30,5 футов. Подход с одним туннелем устраняет необходимость в дорогостоящих проходах безопасности каждые 985 футов, соединяющих две подземные железнодорожные линии.Использование только одного туннеля также сокращает инфраструктуру, необходимую для направления движения в туннель и из него, уменьшает количество выкапываемого материала и означает, что проект будет завершен раньше и будет стоить меньше. Туннель будет иметь длину 4,4 мили с подходами на полмили на каждом конце и проходить на 100 футов ниже поверхности. Чтобы прорыть туннель, NFM Technologies, дочерняя компания Framatome, строит самую большую в мире машину для проходки туннелей под давлением земли. Экологические ограничения при строительстве туннеля включают предельный уровень шума 55 дБ, осадку менее 0.78 дюймов, земляной материал, содержащий менее 2% бентонита, горнодобывающий материал, используемый для поддержания равномерного давления вокруг ТБМ, и абсолютно никакого загрязнения верхнего уровня грунтовых вод. Если все пойдет по графику, ТБМ совершит «прорыв» в мае 2004 г., а строительство железной дороги будет завершено в мае 2005 г. |
Как работает тоннелепроходческий станок?
Как строятся новые туннели метро под таким оживленным городом, как Барселона, Испания? Этот рекламный ролик демонстрирует, как проходческая машина для проходки туннелей, в частности TBM Herrenknecht с защитным щитом для компенсации давления земли, выкапывала 3. 6 километров (2,24 мили) протяженной линии между станциями метро Барселоны Gornal и Zona Universitària :
Во избежание повреждений чувствительных зданий следует избегать проседания, подъема и вибрации любой ценой. Кроме того, воздействие на наземное движение должно оставаться как можно меньшим. S-442 — это классическая машина EPB с внешним диаметром 12,06 метра и общей длиной 95 метров. Благодаря вращающемуся режущему колесу проходческий комбайн отламывает материал из туннельной фазы.Затем материал перемещается в систему ленточных конвейеров в задней части щита через винтовой конвейер, в то время как гидроцилиндры непрерывно толкают машину вперед.
Железобетонные сегменты, известные как сегменты футеровки, устанавливаются под защитой обшивки щита. Когда строительство кольца будет завершено, машина может прижаться к новому кольцу туннеля и просверлить грунт глубже.
Видео выше было размещено на YouTube каналом Central Subway Project в Сан-Франциско в 2011 году.
Спасибо, @akent.
Эта отмеченная наградами видеоколлекция Webby создана для того, чтобы помочь учителям, библиотекарям и семьям пробудить в детях интерес и любопытство. TKSST предлагает более интеллектуальный и значимый контент, чем тот, который обычно используется алгоритмами YouTube, и расширяет круг авторов, создающих этот контент.
Отобранные, адаптированные для детей, независимо изданные. Поддержите эту миссию, став постоянным участником сегодня.
Сохранить это
Посмотреть другие видео о …
Короткая устрашающая поездка в последней идее Илона Маска: The Boring Co.
Все говорят о погоде, но никто ничего не делает. То же и с трафиком.Кроме Илона Маска, который называет это «душераздирающим движением» и решил что-то с этим сделать.
Как и многое другое, Маск видит это в математических терминах. Он видит людей, переходящих от трехмерных домов к двухмерным дорогам, трехмерным офисам и обратно. По его словам, решение — это геометрия.
«Все хотят выйти из своей трехмерной конструкции на двухмерные дороги одновременно», — сказал Маск. «Единственный способ решить эту проблему — перейти в 3D».
Нет, не ракеты — в небе уже слишком людно.Маск собирается использовать туннели. В частности, компания Маска The Boring Co. планирует прокладывать туннели под городами мира с помощью гигантских, сверхэффективных кротовых машин, продвигаясь по спирали сквозь землю и скалы, пока не появится сеть подземных дорог, которая могла бы конкурировать с муравьиной фермой профессионального уровня. Затем автономные электромобили будут перевозить пассажиров по этим туннелям со скоростью до 155 миль в час.
По крайней мере, таков план. Есть несколько вещей, в которых еще нужно разобраться. К примеру, прокладка туннелей исторически была чрезвычайно медленной и дорогой. Современные технологии требуют 1-2 миллиарда долларов и трех-шести месяцев на милю туннеля.
«У вас закончатся деньги, и это займет миллион лет», — сказал Маск.
Итак, Маск собирается сделать все быстрее и дешевле.
Компания Boring Co. решила проблемы по частям. Некоторые из ее решений удивительно просты. Например, заставить сверлильную машину работать быстрее. Используйте извлеченную вами грязь, чтобы сделать бетон, используемый для укрепления стен туннеля (в любом случае бетон на 70 процентов состоит из грязи).Из оставшейся земли сделайте кирпичи, которые вы продаете по 10 центов каждый. Не переставайте скучать, когда кладете бетонные стены на место — продолжайте сверлить. Прямо сейчас туннельные экскаваторы останавливаются через 10 минут для удаления грязи, установки секций стен и удлинения линий электропередач и трубопроводов. Используйте аккумулятор, чтобы управлять всеми транспортными средствами в туннелях. И поместите внешние бамперные колеса на передние колеса автомобилей в туннелях, чтобы любой электрический автономный автомобиль с этими дополнительными бамперными колесами мог пройти через любые стандартные колеса Boring Co. туннели.
Простой, нет?
Проект все еще находится в зачаточном состоянии, но The Boring Co. удалось пройти через 1,14 мили грязи под улицей напротив штаб-квартиры Space X в Южной Калифорнии. Каково пройти через этот туннель? Они подбросили некоторых из нас, болванов из прессы, чтобы выяснить это.
Они погнали нас мимо штабелей бетонных секций стены туннеля, мимо старого бурового станка, мимо нового бурового станка, а затем за угол, и вот он: туннель.Прежде всего, нюанс: туннель не полностью закончен. Это был своего рода демонстрационный туннель. Очевидно, что он находится в грубом, доказательном состоянии.
Tesla Model X была припаркована на том, что выглядело как открытая платформа лифта над падением 40 футов вниз к открытому отверстию туннеля. У Tesla Model X были маленькие колеса на передних углах, которые выглядели как колесные горизонтальные бамперы. Бамперы, казалось, могли удерживать автономные электромобили между бетонными бордюрами так же, как бамперы на автомобилях Autopia в Диснейленде управляли своими автомобилями — своего рода.
Мы спустились по узкой цементной лестнице на уровень самого тоннеля. Там было припарковано еще несколько Model X. (Будучи сообразительным, я подумал, что наша группа собирается сесть в передний X, поэтому я начал пробираться к правому переднему пассажирскому сиденью. Я толкал странную дверную ручку Tesla к тому времени, когда один из местных репортеров новостей кричал бесполезный «Дробовик!» Ха-ха, лохи!)
У нас был водитель, с которым нам было категорически запрещено разговаривать и которому было прямо запрещено говорить с нами.Мы все равно с ним разговаривали. Он просто улыбнулся. Ему удалось сказать: «Пристегнись», что мы все и сделали.
Туннель имеет диаметр 12 футов по внутренней окружности, как нам сказали, и 14 футов по внешней стороне. Поперечное сечение дна имеет цементные выступы, которые простираются на полные 6000 футов. Колеса нашей Model X ехали по этим уступам. Цементный бордюр выстилает края этих выступов, от которых отскакивают колеса бампера. Здесь нет железнодорожных рельсов или чего-то подобного, и наша Model X не была на «коньках», как считалось ранее для туннельного транспорта.В текущей версии гонщики будут ездить на своих электромобилях, пока их управляет автономность.
Когда мы все пристегнулись, Model X начала подниматься по короткой рампе в туннель, но наш водитель держал обе руки возле руля. Потом запустили. То есть запустил . Он оторвался от бетона и спустился по туннелю к первому повороту. Я подумал: «Эй, эта Boring Co. может быть настоящей сделкой». Затем он ударил по тормозам, замедлился, и большие дублирующие щупы передних колес начали стучать по бордюрам.Бетонные выступы, по которым мы ехали, были волнистыми, а не плоскими, и я начал думать, что Model X почти отскочит от них, в то же время ударившись о бордюр. Это было страшнее, чем показалось.
Итак, мы были, подпрыгивая и мчась в сторону подземного транспорта будущего, наш водитель регулярно хватался за руль, чтобы вся конструкция не развалилась на части. Я представил себе заголовок: «Пятеро погибают в туннельной катастрофе — Маск винит в аварии« идиотскую прессу ».«Нашему водителю приходилось все время хвататься за руль, поскольку подпрыгивание и стук становились все более жестокими. Я прикинул, что мы, наверное, разгонялись до 45 миль в час. Испугались ли другие пионеры транспорта так, или они были посмелее, у них хватило смелости, неужели первый паровой автомобиль напугал репортеров, кричащих, как девочки-подростки? Возможно нет.
Затем появился свет в конце туннеля. Мы сделали это. Ух!
Опять же, это грубый прототип. По словам Маска, производственные туннели, по которым будет ездить публика, будут «идеальными».Так что никаких подпрыгиваний или ударов. Действительно.
В конце пути — еще одна лифтовая площадка, на которой работают молодые горные инженеры. Я мог смотреть сквозь большое лобовое стекло и видеть их бородатые кружки, смотрящие на нас. Кто-то нажал кнопку, и платформа поднялась. Мы вышли на самый невзрачный пригородный / промышленный переулок, который вы когда-либо видели, а затем поехали по бездорожью обратно туда, откуда начали. Мы прошли мимо Hyperloop, другой замечательной транспортной идеи Илона, и мимо Space X, который пока может быть единственной из этих безумных идей, приносящих прибыль.
Все ли заработает? Сможем ли нас всех перенести в мусктуннелях на гиперскорости к тому месту, где мы пожелаем? Кто знает? Маск знает. И он говорит: «Да».
Этот контент создается и поддерживается третьей стороной и импортируется на эту страницу, чтобы помочь пользователям указать свои адреса электронной почты. Вы можете найти дополнительную информацию об этом и подобном контенте на сайте piano.io.
T.R.U.D.E — отрезной круг тоннелепроходческого станка 360 Panorama
T.R.U.D.E — отрезной круг тоннелепроходческого станка 360 Панорама | 360Города ОШИБКА: Javascript не активирован |

Нажмите Shift + колесо мыши для увеличения
{{thumb_title}}
T.R.U.D.E — отрезной круг проходческого комбайна
Гамбург
Большой отрезной круг проходческого комбайна, на котором строился автомобильный тоннель под рекой Эльба.Колесо имеет диаметр 14,2 метра и вес 380 тонн. Сейчас в помещениях «Museum der Arbeit» (Музей труда) в Гамбурге.
T.R.U.D.E = «Тиф Рантер Унтер Ди Эльба» (Глубоко под Эльбой)
Авторские права: Ulrich NeitzelТип: Сферический
Разрешение: 12536×6268
Снято: 07.04.2013
Загружено: 13.04.2013
Просмотров:
…
Теги: machine; туннель; музей; промышленность
Подробнее о Гамбурге
Гамбург: второй по величине город Германии, расположенный на севере у реки Эльба, благодаря морскому порту, известному как город купцов. Из-за близлежащего моря у вас всегда будет свежий ветерок, пока вы гуляете по улицам с красивыми частными таунхаусами или плывете по реке Альстер на борту «Альстердампфера».
✖ Похоже, вы создаете заказ.
Если у вас есть какие-либо вопросы перед оформлением заказа, просто дайте нам знать по адресу info@360cities.net, и мы ответим вам. Файлы cookie помогают нам предоставлять вам отличные услуги.Используя этот сайт, вы соглашаетесь на использование файлов cookie. ОКВыйти с этого сайта
Что такое скучная компания?
Что такое скучная компания?
Как и многие самые противоречивые идеи Илона Маска, The Boring Company начиналась с твита. Предположительно, 18 декабря 2016 года Маск сидел в час пик в Лос-Анджелесе, когда написал: «Трафик сводит меня с ума. Я собираюсь построить туннельную машину и просто начать копать …» Если бы Маск был кем угодно, кроме $ 22,1 миллиардов долларов, генеральный директор Tesla, он мог бы оставить все как есть, но буквально через несколько минут казалось, что он серьезно задумался над этой идеей.
«Я действительно собираюсь это сделать. Это будет называться« Скучная компания », — сказал Маск в серии твитов. Но в отличие от его предложений «взять Tesla в частную собственность», создать «сайт доверия СМИ» или пилотировать мини-подводную лодку в Таиланде — идеи, которые были либо ненавистны, либо неудачны, либо и то, и другое — The Boring Company, возможно, просто самая успешная презентация Маска в социальных сетях на свидание. Генеральный директор Tesla официально запустил The Boring Company в январе 2017 года, но не раньше, чем вернулся в Twitter, чтобы придумать слоган компании: «Скучно, это то, что мы делаем.»
The Boring Company открыла землю месяц спустя, в феврале 2017 года, когда рыла пробную яму на территории SpaceX. Как сообщается, пробные раскопки начались в пятницу днем, когда Маск сказал: «Давайте начнем сегодня и посмотрим, какая самая большая яма, которую мы можем выкопать с сегодняшнего дня до полудня воскресенья, работающая 24 часа в сутки». В конце этого периода The Boring Company удалось пробурить яму шириной 30 футов, длиной 50 футов и глубиной 15 футов.
Чем занимается «Скучная компания»?
Хотя Илон Маск проявлял беспокойство по поводу того, что происходит на суше и в космосе, он, похоже, также интересуется тем, что происходит под землей. Всего через два года после своего основания Boring Company представляет собой компанию по строительству инфраструктуры и туннелей с контрактами в Чикаго, Лос-Анджелесе и Хоторне, Калифорния. Самостоятельная цель компании — «решить проблему душераздирающего трафика», построив сеть транспортных коридоров под землей.Как именно они собираются это сделать? Маск предположил, что у него есть технология и средства для увеличения скорости проходки туннелей и снижения затрат в 10 или более раз. Для сравнения: самые дорогие проекты по прокладке туннелей могут стоить до 1 миллиарда долларов за милю в городских районах.
Компания Boring Company предложила перевозить пассажиров из центра Чикаго в аэропорт О’Хара с помощью высокоскоростных капсул.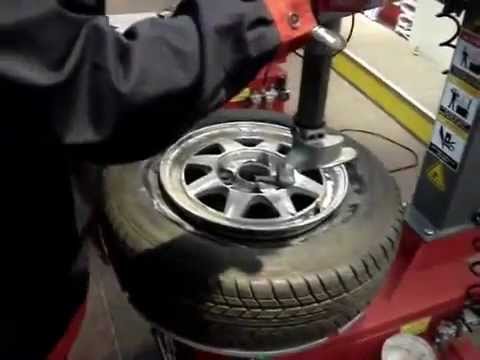
Новый взгляд на общественный транспорт
Boring Company представила свой первый законченный участок подземного туннеля 7 декабря.19 августа 2018 года в Хоторне, Калифорния. Когда проект был впервые предложен, Маск предположил, что капсулы, способные перевозить 16 пассажиров одновременно, будут проходить через туннель со скоростью до 150 миль в час. Но проект, который The Boring Company представила в декабре, выглядел заметно иначе: вместо пассажирских контейнеров Tesla Model X были оснащены «отслеживающими колесами», системой управления, похожей на то, как автомобили перемещаются через автомойку. Первые гонщики сообщили, что следящие колеса делали поездку чрезвычайно ухабистой даже на тестовой скорости примерно 40 миль в час.Спустя почти два года после того, как Маск впервые написал в Твиттере о пробках в Лос-Анджелесе, The Boring Company завершила свой первый туннель длиной 1,14 мили, обойдя его строительство в 10 миллионов долларов.
Нравится вам это или нет, но первый туннель The Boring Company теперь проложит путь для работы компании в Чикаго и Мэриленде, где она заключила контракты на строительство систем общественного транспорта. В феврале 2018 года городские власти Чикаго объявили конкурс на строительство высокоскоростной транспортной сети от центра Чикаго до аэропорта О’Хара.Компания Boring Company участвовала в конкурсе с предложением перевезти пассажиров из центра города в аэропорт за 12 минут на автоматизированных электромобилях. Маск описал использование «петлевой» системы, в которой 16 пассажиров (и их багаж) будут транспортироваться со скоростью от 125 до 150 миль в час в капсулах, которые отправляются каждые полминуты. Это сложная задача, особенно после выступления Маска в Лос-Анджелесе, но в июне 2018 года Чикаго, тем не менее, выбрало The Boring Company из четырех конкурирующих заявок. Если Boring Company успешно завершит строительство тоннеля, оценка частной компании может вырасти до 16 миллиардов долларов.
Продажа развлекательных огнеметов
Илон Маск не смог сдержать некоторые из обещаний, данных им в прошлом, но когда дело доходит до обещания его Boring Company вывести на рынок развлекательный огнемет, генеральный директор Tesla, похоже, выполнил. В декабре 2017 года Маск пообещал создать огнемет Boring Company, если компания сможет продать 50 000 брендовых шляп по 20 долларов за штуку, а в канун Рождества он объявил в Twitter, что цель была достигнута.Вскоре после публикации Маск написал в Твиттере: «По-видимому, некоторые таможенные органы заявляют, что не разрешат отгрузку всего, что называется« огнемет ». Чтобы решить эту проблему, мы переименовали его в« Не огнемет »». Огнемет или нет, но Boring Company продала ограниченным тиражом 20 000 единиц по 500 долларов каждая, что принесло компании беспрецедентное внимание средств массовой информации и 2 миллиона долларов дохода.
История успеха: CEG BGS помогает Simmons Machine Tool Corporation внедрять методы бережливого производства и согласовывать их со своей практикой бухгалтерского учета
Общие, НовостиИстория успеха: CEG BGS помогает Simmons Machine Tool Corporation внедрять методы бережливого производства и согласовывать их с методами бухгалтерского учета
Справа: программируемый робот захватывает подшипник для запрессовки на колесную пару.
В течение 117 лет Simmons Machine Tool Corporation производит специализированные станки и системы автоматизации, которые железнодорожная промышленность использует для обслуживания и производства рельсовых колесных пар. В компании Albany работает около 100 человек на заводе на Северном Бродвее, где она проектирует и производит станки для перепрофилирования колес, токарные станки для осей, расточные станки для колес, прессы для колес и подшипников и другое оборудование для колесных мастерских.
На изготовление типовой машиныSimmons уходит от 3000 до 8000 часов.Такая трудоемкая работа вынудила Симмонс быть консервативным в своем стремлении к новому бизнесу. Поэтому, когда производитель обновил свой стратегический план в 2016 году, он сотрудничал с отделом Business Growth Solutions (BGS) Центра экономического роста, чтобы определить, какой дополнительный бизнес можно продолжить с небольшими корректировками.
Для главного операционного директора Simmons Дэвида У. Дэвиса вопрос звучал так: «Как мы используем набор навыков, в которых участвуем, и как мы применяем их в отраслях, не относящихся к нашей?» Дэвис также задался вопросом, какую уникальную возможность должна использовать его компания из множества доступных.
«Мы не можем сделать все три — мы не можем сделать даже два», — сказал он.
Чтобы найти ответ, BGS помогла Симмонсу получить 12 283 долларов США в рамках грантов Института развития рабочей силы штата Нью-Йорк (WDI) и Национальной программы повышения производительности энергосистем для обучения в рамках программы VIA Revenue Throughput Program (RTP). Программа является инициативой, предложенной BGS и Value Prop Interactive, консалтинговой фирмой по стратегическому планированию в Малверне, штат Пенсильвания.
VIA RTP предназначен для оснащения малых и средних предприятий инструментами, которые помогают им определять возможности получения доходов и приоритеты посредством серии практических встреч с руководителями. Эта программа улучшает внимание руководителей к общим препятствиям на пути роста, таким как отсутствие видимости (слепые пятна), сосредоточенности или приверженности. С помощью VIA RTP компания Simmons также смогла оценить выявленные возможности, чтобы помочь выбрать лучшую из них, вместо того, чтобы полагаться на неофициальные данные для принятия такого решения.
В течение нескольких месяцев несколько членов исполнительной команды Симмонса, включая Дэвиса, прошли курсы VIA RTP. Он быстро понял, что отдел продаж недостаточно общается с клиентами лицом к лицу, чтобы узнать об их меняющихся потребностях в непрофильных сегментах рынка, особенно в Южной Америке.
Дэвис также обнаружил, что Симмонс использовал неправильную модель ценообразования. Традиционно производитель использовал цену «затраты плюс», рассчитанную путем умножения нормы нагрузки на часы производства плюс накладные расходы, чтобы получить общую стоимость, к которой добавляется маржа прибыли. Дэвис понял, что эта модель не принимает во внимание, как другие производители оценивают аналогичное оборудование. Ему нужна была рыночная модель ценообразования, при которой товары его компании имели конкурентоспособные цены.
Убеждению Дэвиса в том, что Simmons необходимо пересмотреть свою модель ценообразования, стал семинар CEG по бережливым финансам и бухгалтерскому учету, на котором присутствовали финансовый директор и контролер компании.Семинар, который проводит известный эксперт по бережливому учету Джерри Соломон, показывает производителям, как традиционные показатели эффективности не согласуются с практиками бережливого производства. В нем также изложены шаги, необходимые для согласованной работы обоих.
Семинар по бережливым финансам и бухгалтерскому учету показал, как ценообразование «затраты плюс», которое использовала Simmons, на самом деле оштрафовало производителя, поскольку он добился успеха во внедрении методов бережливого производства: чем больше компания сокращала количество рабочих часов, тем больше увеличивалась ее нагрузка.В 2016 году директор проекта BGS по технологическим услугам Том Белл помог Симмонсу стать более экономичным производителем, проведя серию семинаров по принципам бережливого производства, составлению карты потока создания ценности, системе 5S и обучению бережливому производству и шести сигмам.
Исследование Партнерства по расширению производства (MEP), проведенное Национальным институтом стандартов и технологий (NIST), показало, что набор услуг, которые Симмонс получил при поддержке BGS, имел следующие экономические последствия:
- Увеличение продаж : 3 миллиона долларов
- Нераспределенные продажи : 2 доллара.5 миллионов
- Создано рабочих мест : 5
- Сохранено рабочих мест : 90
- Экономия затрат : 100 000 долл. США
- Заводское оборудование : 600 000 долл. США
- Кадровые практики : 40 780 долларов США
- Новые продукты и процессы : 50 000 долл. США
«Чтобы быть действительно, действительно бережливой компанией, не только производство производителя должно быть бережливым, наша ценовая политика и разработка продуктов должны быть бережливыми», — сказал Дэвис.
Все члены CEG имеют доступ к услугам BGS, которые включают программирование для систем бережливого предприятия, ускорение технологий, улучшение качества, снижение затрат, расширение рынка, стратегию управления и рост продаж. Чтобы назначить консультацию с директором CEG BGS Майклом Лобсингером, напишите по электронной почте michaell@ceg.org или позвоните по телефону 518-465-8975 X238.
1919 Самостоятельная расточка экономичного типа 9 л.с., тип E — журнал для газовых двигателей
Говард Киттлсон | 7 мая 2009 г.
1/9
Приводной вал, который Ховард Киттлсон создал для расточки цилиндров своего 9-сильного автомобиля Type E 1919 года выпуска. Ховард изготовил инструменты для этого проекта и использовал свой токарный станок Monarch 1942 года выпуска 16 на 102 дюйма, чтобы сделать рез.
2/9
9 HP Type E Economy Ховарда Киттлсона 1919 года.
3/9
Конец механической подачи шестигранного приводного вала прикреплен к подшипнику, который закреплен на держателе токарного инструмента. Затем подача токарного станка протянула шестигранный вал через ступицу звездочки вместе с расточной оправкой и режущим инструментом.
4/9
Шестигранный приводной вал и ступица звездочки, зажатая в патроне, обеспечивает вращение при расточке.
5/9
Передняя опора подшипника, резцедержатель и режущий инструмент завершают резку.
6/9
Опора заднего подшипника с установленным задним центрирующим кольцом. Обратите внимание на изготовленный кронштейн и прокладки, чтобы установить подшипник вертикально. После совмещения стержня центрирующие кольца были удалены.
7/9
Хонингование с хонингованием Sunnen.
8/9
Готовая расточка после расточки и хонингования.
9/9
Старый поршень (слева) и новый поршень.Ховард изготовил новый поршень из стали.
❮ ❯Эта история началась в 1995 году, когда джентльмен из Далтона, штат Миннесота, выставил на продажу несколько двигателей.
Среди этих двигателей был 9-сильный тип E 1919 года выпуска. Двигатель был в основном укомплектован, но отсутствовали инжектор и магнето, а порт воспламенителя был открыт. Он также застрял, поршень был полностью задвинут. Неужели мыши и влага попали в цилиндр? Я понятия не имел.
Рискуя
Хотел двигатель, но не купил. Я посмотрел на него еще раз через год, но все равно никакой сделки. В середине зимы 1997 года я наконец купил двигатель, пожав руки, так как владелец не хотел денег, пока я не забрал его весной. Несколько недель спустя некролог владельца был опубликован в местной газете. Я был уверен, что сделка с экономикой была нарушена, но позже я связался с семьей, и они заверили меня, что знают о соглашении и что двигатель все еще доступен. Побольше хороших паровозиков.
Худшие опасения оправдались.
Когда погода позволила, я поднял двигатель и начал восстановление. На то, чтобы снять голову, ушла неделя, и мои опасения оправдались — там было огромное мышиное гнездо и множество неприятных ямок на дне цилиндра. Я почистил и отполировал отверстие и залил биты двухкомпонентной эпоксидной смолой (LPS Tough Titanium), отточил цилиндр, заново нарезал канавки для поршневых колец, установил набор нестандартных колец Джо Сайкса, а также новые клапаны и прокладки. , воспламенитель и магнето.Он работал, но также разбрызгивал много черного масла на заднюю часть двигателя. Я запускал его таким образом несколько дней, но он потерял сжатие и в конце концов не запустился.
Пришлось починить канал ствола, но, имея ограниченные средства на проект, пришлось рассматривать множество вариантов. У меня есть образование машиниста, и я много лет работал в сфере обслуживания тяжелого оборудования. Обычной работой в то время был ремонт изношенных отверстий тяжелого дорожного и горного оборудования с помощью переносного линейного бурового оборудования. Мы растачивали изношенную область и вдавливали втулку или приваривали отверстие и обрабатывали его до нужного размера.Я решил использовать этот метод для увеличения диаметра отверстия, а затем сделать поршень большего размера. Этот двигатель имеет диаметр цилиндра 6-1 / 2 дюйма и длину цилиндра почти 2 фута, и большинство мастерских по восстановлению двигателей не смогли бы обработать такой длинный цилиндр.
Расточка двигателя своими руками
Мне пришлось изготовить большую часть инструмента для обработки отверстия. Оснастка включала два самоустанавливающихся шарикоподшипника размером 1-15 / 16 дюймов; расточная оправка из холоднокатаного стального вала диаметром 1-15 / 16 дюйма; два кардана; длина шестигранного вала 1-1 / 18 дюйма и ступица звездочки 1-1 / 18 дюйма для прохождения шестигранного вала; еще один самоустанавливающийся подшипник на конце шестигранного вала; резцедержатель с механической обработкой; сверлильный инструмент с твердосплавным припоем на 1/2 дюйма; два центрирующих кольца; разная сталь; и проставки, переходная плита, гайки, болты и т. д.
Центрирующие кольца были изготовлены из пластины диаметром 1/4 дюйма и использовались для выравнивания расточной оправки по центру отверстия цилиндра, а затем были удалены. Наружный диаметр составлял 6.500 дюймов (размер отверстия цилиндра), а внутренний диаметр соответствовал скользящей посадке на расточной оправке 1-15 / 16 дюйма. Головной конец был прикреплен болтами к переходной пластине, которая свободно прилегала к шпилькам головки блока цилиндров. Набор трубных распорок удерживал подшипник достаточно далеко, чтобы можно было снять центрирующее кольцо и обеспечить зазор для расточного инструмента. Все это скреплено гайками и шайбами.Задний подшипник был прикручен к сборному кронштейну, который был прикручен к болтам крышки коренного подшипника и болтам крепления цилиндра. Этот подшипник был установлен регулировочной прокладкой для правильной центровки.
Центрирующие кольца были затем установлены в цилиндр, по одному на каждом конце. Расточная оправка вставлялась в кольца, а подшипники скользили по расточной оправке. Передний подшипник в сборе, проставки, гайки и шайбы были собраны и равномерно затянуты. Требовалось легкое постукивание, чтобы отрегулировать выравнивание так, чтобы штанга могла свободно вращаться, а задний подшипник был установлен прокладками, чтобы штанга могла свободно вращаться.Затем стержень был удален, затем центрирующие кольца и стержень с держателем инструмента был повторно установлен.
Двигатель был припаркован примерно в 10 футах от передней бабки моего токарного станка Monarch размером 16 на 102 дюйма и слева от нее. Приводной вал был соединен с расточной оправкой с помощью универсального шарнира, который был соединен с другим универсальным шарниром, а затем с шестигранным валом диаметром 1-1 / 18 дюйма. Шестигранный вал проходил через шпиндель и ступицу с шестигранной звездочкой размером 1-1 / 18 дюйма, которая была зажата в патроне.Втулка была установлена в левой части отверстия шпинделя, чтобы шестигранник находился на одной линии. Это обеспечивало вращательное движение для питания отверстия. Для обеспечения работы конец шестигранного вала был повернут, чтобы он поместился в шарикоподшипник, который затем был снабжен самоустанавливающимся кольцом, которое было прикреплено болтами к штанге, зажатой к держателю поперечного суппорта. Подача и скорость контролировались с помощью органов управления токарного станка, как при обычной расточной или токарной операции. Поскольку универсальные шарниры не были на одной линии, нам пришлось начать растачку на задней стороне двигателя и потянуть (или подать) его вперед.
Режущий инструмент был установлен и отрегулирован в соответствии с глубиной резания, державка инструмента зажата, подшипники и вал смазаны маслом, подача и скорость были установлены, и токарный станок был запущен. Это сработало как шарм, и тяжелая штанга не дребезжала. Чтобы очистить ямы и получить хорошую отделку, потребовался один черновой пропил, затем легкий чистовой пропил, чтобы получить общий пропил 0,100 дюйма. В целом на его настройку ушло несколько дней и около часа на обработку. В результате получилось прямое и круглое отверстие в пределах 0,001 дюйма от общей длины канала.Затем с помощью хона Sunnen удалили следы инструмента и добились хорошей отделки.
Что касается поршня: на других двигателях с изношенными отверстиями я заточил их с помощью хона Sunnen, пока они не стали прямыми и точными, а затем построил поршень с помощью металлического распылителя Eutectic и изготовил кольца увеличенного размера на заказ. Обычно они были только на 0,015–0,030 дюйма, и они хорошо себя зарекомендовали. Но это отверстие было увеличено на 0,100 дюйма, и металлический спрей обычно плохо работает в таком тяжелом наросте. Итак, я решил сделать новый поршень из стали.
Я начал с куска толстостенной трубы, которую обработал до размеров внутреннего диаметра старого поршня, а затем просверлил поперечное отверстие для бобышек поршневых пальцев. Втулки были изготовлены из стальных труб и имели фаску на одном конце, чтобы обеспечить полную сварку. Их удерживали на одной линии и позиционировали с помощью установочного штифта, а затем приваривали изнутри с обоих концов поршня. Затем были сварены внешние поверхности. Эти сварные швы были зачищены, и головка поршня приварена.Затем поршень нормализовали и охлаждали. Затем его повернули, чтобы подогнать под отверстие, и нарезали кольцевые канавки. Последней операцией была обработка отверстия под поршневой палец, просверливание и нарезание отверстий под установочные винты для зажима пальца. Набор нестандартных колец Niagara +0.100 увеличенного размера завершил работу.
Стоит затраченных усилий
Двигатель теперь работает хорошо, и его использовали для жужжания дров для моего камина. Я установил висконсинский двигатель воздушного охлаждения с редуктором в качестве стартового двигателя.Он установлен на салазках и использует пневматическую шину в качестве привода трения относительно маховика. Это лучше, чем пытаться провернуть двигатель вручную!
Свяжитесь с Говардом Киттлсоном по телефону 13540 Cty. Hwy. 30, Pelican Rapids, MN 56572 • kitts2008@hotmail.com
СТАТЬИ ПО ТЕМЕ
Узнайте больше о свече зажигания, изобретенной Эдмоном Бергером в 1839 году, согласно различным источникам.
Обратите внимание на впечатляющую реставрацию 2-сильного двигателя водяного охлаждения Waterloo Boy K 1921 года, произведенного Эммой Ризе ее покойным отцом.
Примерно в 1910 году Hoosier / Flint и Walling внедряют в свою линейку горизонтальный газовый двигатель меньшего размера, аналогичный двигателям Alamo.
.