Как работает роботизированная коробка передач — ДРАЙВ
Чтобы ответить на этот вопрос, придётся вспомнить устройство обычной механической коробки передач. Основу классической «механики» составляют два вала — первичный (ведущий) и вторичный (ведомый). На первичный вал через механизм сцепления передаётся крутящий момент от двигателя. Со вторичного вала преобразованный момент идёт на ведущие колёса. И на первичный, и на вторичный валы посажены шестерни, попарно находящиеся в зацеплении. Но на первичном шестерни закреплены жёстко, а на вторичном — свободно вращаются. В положении «нейтраль» все вторичные шестерни прокручиваются на валу свободно, то есть крутящий момент на колёса не поступает.
Перед включением передачи водитель выжимает сцепление, отсоединяя первичный вал от двигателя. Затем рычагом КПП через систему тяг на вторичном валу перемещаются специальные устройства — синхронизаторы. При подведении муфта синхронизатора жёстко блокирует на валу вторичную шестерню нужной передачи.
Упрощённая схема работы 5-ступенчатой механической коробки передач.
Принцип действия роботизированных коробок передач абсолютно тот же. Единственное отличие в том, что смыканием/размыканием сцепления и выбором передач в «роботе» занимаются сервоприводы — актуаторы. Чаще всего это шаговый электромотор с редуктором и исполнительным механизмом. Но встречаются и гидравлические актуаторы.
Роботизированная КПП SensoDrive применяется на автомобилях марки Citroen.
Управляет актуаторами электронный блок. По команде на переключение первый сервопривод выжимает сцепление, второй перемещает синхронизаторы, включая нужную передачу. Затем первый плавно отпускает сцепление.
Фирма Ricardo на примере «робота» Easytronic от модели Opel Corsa предложила заменить раздельные актуаторы для сцепления и выбора передачи одиночным электромагнитным актуатором. Благодаря этому уменьшились размеры и масса агрегата. И самое главное — механизм выбора передачи стал работать в восемь раз быстрее, а общий период разрыва потока мощности сократился до 0,35 с. Вверху — серийный Easytronic, внизу — рисунок разработки Ricardo.

Пионером массового использования преселективных коробок стал концерн Volkswagen, использующий DSG (S tronic у Audi) как на переднеприводных, так и на полноприводных моделях с продольно и поперечно установленными двигателями. Аббревиатура DSG (Direct Shift Gearbox — коробка прямого включения) стала нарицательным для коробок с двумя сцеплениями — хотя на самом деле это просто товарный знак.
Революционным решением стала появившаяся в начале 80-х трансмиссия с двумя сцеплениями DCT (dual clutch transmission). Рассмотрим её работу на примере 6-ступенчатой коробки DSG концерна Volkswagen. У коробки два вторичных вала с расположенными на них ведомыми шестернями и синхронизаторами — как у шестиступенчатой «механики» Гольфа.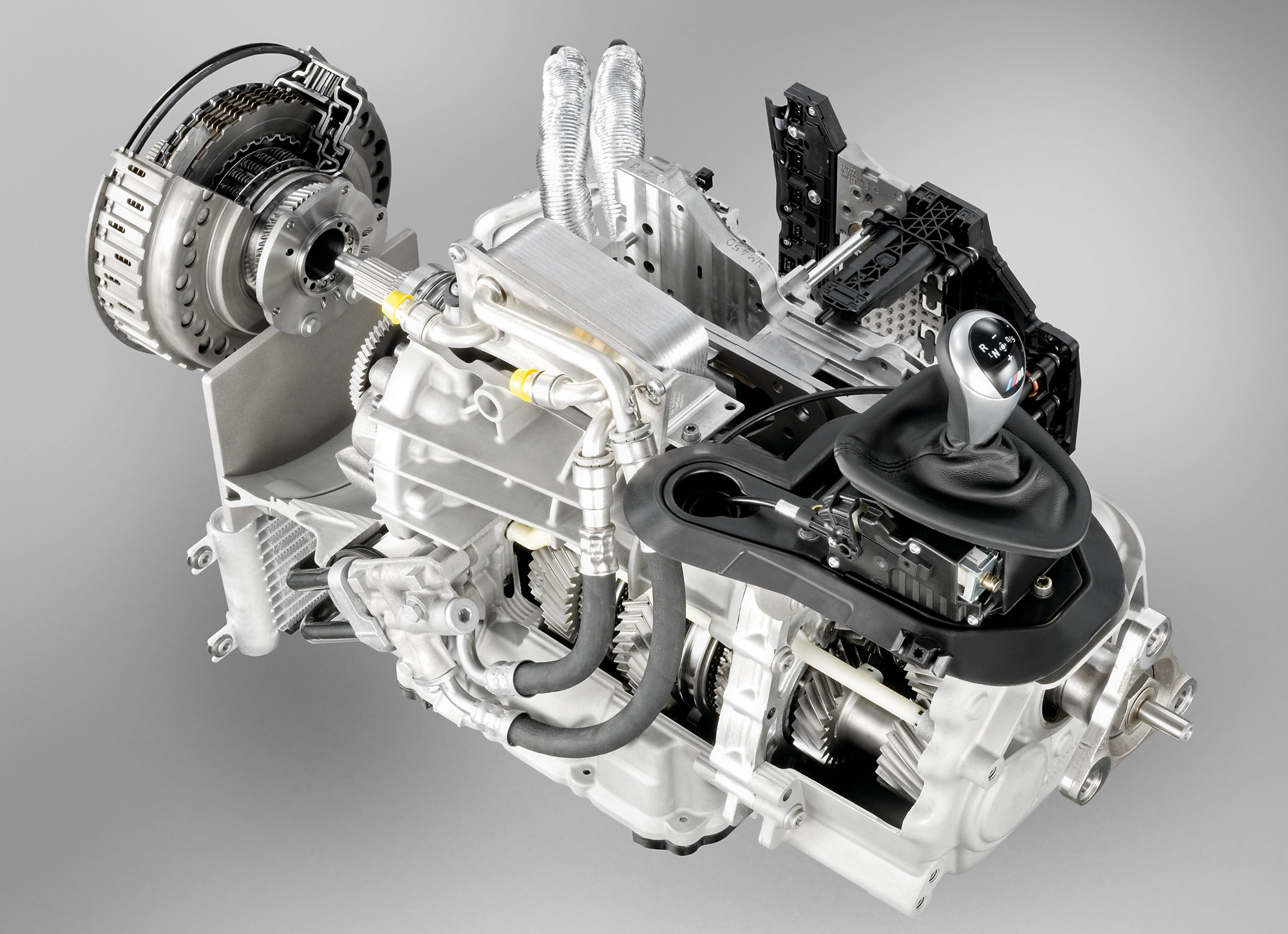
Состояние DSG при движении на первой передаче. Муфтами блокированы шестерни 1-й и 2-й передач.
Когда машина достаточно разгонится и компьютер решит повысить передачу, размыкается первое сцепление и одновременно замыкается второе. Крутящий момент теперь идёт через внешний первичный вал и пару второй передачи. На внутреннем валу уже выбрана третья. При замедлении те же операции происходят в обратном порядке. Переход происходит практически без разрыва потока мощности и с фантастической скоростью. Серийная коробка Гольфа переключается за восемь миллисекунд. Сравните со 150 мс на Ferrari Enzo!
Состояние DSG после переключения на 2-ю передачу. 3-я передача ожидает своей очереди.
Коробки с двойным сцеплением экономичнее и быстрее традиционных механических, а также более комфортны, чем «автоматы». Главный их недостаток — высокая цена. Вторую проблему — неспособность передавать большой крутящий момент — решили с появлением DSG фирмы Ricardo на 1000-сильном купе Bugatti Veyron. Но пока удел большинства суперкаров — «роботы». Хотя, например, коробка Ferrari 599 GTB Fiorano — не чета опелевскому Изитронику: время переключения у суперробота исчисляется десятками миллисекунд.
Роботизированная коробка AMG Speedshift, устанавливаемая на новейший SL 63 AMG, представляет собой модифицированный мерседесовский «автомат» 7G-Tronic. Только крутящий момент вместо тяжёлого и инертного гидротрансформатора передаёт одинарное многодисковое «мокрое» сцепление. Благодаря применению сложных электрогидравлических актуаторов время переключения составляет 0,1 с.
Сегодня коробки DCT есть не только у Фольксвагена, но и у компаний BMW, Ford, Mitsubishi и FIAT. Преселективные коробки признали даже инженеры Porsche, которые используют в своих машинах только проверенные технологии. Аналитики прогнозируют, что в будущем наиболее распространёнными трансмиссиями станут DCT и вариаторы. А дни третьей педали, похоже, сочтены — скоро она исчезнет даже из самых драйверских спорткаров. Человечество выбирает то, что удобнее.
Описание принципов работы роботизированной КПП DCT Хендай
Рассмотрим DCT автомобилей Hyundai: принцип работы, характерные особенности, плюсы и минусы.
Роботизированная трансмиссия — новшество из мира спортивных автокаров
Роботизированная КП (DCT Хендай) — преселиктивная коробка передач, попавшая на любительский рынок в модифицированном виде относительно недавно из автоспорта, оснащенная прямым включением и двумя сцеплениями, на которые возложены разные функции:
- Контроль над нечетными передачами.
- Контроль над четными передачами.
Сравнительно быстрый и, что немаловажно, плавный разгон, в процессе которого скорости переключаются в доли секунды — главные особенности роботизированной трансмиссии автомобиля Hyundai. Кроме этого, сочетание комфортного управления транспортным средством, которое дает автомат, с неоспоримым экономичным режимом и динамикой от МКП — так же отличительная характеристика роботизированной КП, относящиеся к достоинствам этой трансмиссии.
К преимуществам так же можно отнести следующее:
- дешевле автоматической КП;
- небольшая масса робота;
- некоторые модели Hyundai оснащены подрулевыми лепестками — альтернатива традиционному рычагу переключения скоростей, что позволяет быстро поставить необходимую передачу, а значит предать динамичности транспортному средству.
Корейские кроссоверы премиум класса — например, Hyundai Tucson (2016 года), при желании автолюбителя могут комплектоваться 7-ступенчатой роботизированной коробкой с двойным сцеплением и подрулевыми лепестками (несмотря на название, они расположены сразу за рулем). Данная система КПП идет исключительно с силовой установкой мощностью в 175 лошадиных сил.
Категорически противопоказаны пробуксовки, страдает плавность переключения скоростей, при даже кратковременной остановке необходимо переходить в нейтральное положение. Это очевидные недостатки роботизированной коробки. К ним же следует присовокупить дороговизну устройства, как при приобретении, так и в последующем обслуживании и ремонте.
Идеальной коробки передач не существует. Поэтому, выбирая, необходимо расставлять приоритеты. То есть, что предпочтительней: динамика, стоимость, экономичность или комфорт. Определившись, проще осуществить правильный выбор относительно трансмиссии.
РКПП — роботизированная коробка передач, «робот»
РКПП — роботизированная коробка передач (коробка «робот), которая позволяет выбирать и включать необходимую передачу без участия водителя, то есть автоматически. При этом ошибочно полагать, что роботизированная трансмиссия является одной из разновидностей АКПП (гидромеханический автомат).
Прежде всего, чтобы понять, что такое роботизированная коробка передач, для начала необходимо вспомнить устройство и принцип работы обычной механической коробки (МКПП). Так вот, фактически роботизированная коробка является той же «механикой», однако автоматическое переключение передач в данном типе КПП становится возможным благодаря наличию боков управления и электронно-механических исполнительных устройств.
Устройство, особенности и принцип работы роботизированной коробки передач
Как уже было сказано выше, РКПП состоит из механической коробки передач, а также дополнительных устройств для выжима сцепления, выбора и переключения передачи. Данные устройства называются актуаторами (актуатор сцепления, актуатор выбора передачи). Также коробка «робот» имеет собственную систему управления, которая представляет собой ЭБУ коробкой и ряд электронных датчиков, взаимодействующих с блоком.
Получается, данный тип КПП представляет собой механическую коробку с автоматическим управлением и принципиально отличается от классического «автомата», а также бесступенчатого вариатора.
Роботизированная КПП, как и обычная МКПП, имеет сцепление, в ней не используется трансмиссионная жидкость ATF в качестве рабочей для управления и т.д. Добавим, что в современных «роботах» может быть как одно, так и два сцепления. В первом случае следует понимать однодисковый «робот», а во втором преселективную роботизированную коробку передач с двумя сцеплениями.
Если говорить об устройстве коробки — робот, можно выделить следующие базовые составные элементы:
- Коробка передач, которая по устройству напоминает «механику;
- Актуаторы (сервоприводы), отвечающие за выжим сцепления и включение передачи;
- Блок управления коробкой (микропроцессорный ЭБУ) и внешние датчики;
Давайте рассмотрим устройство РКПП на примере 6-и ступенчатой роботизированной коробки передач с двумя сцеплениями. Сама коробка похожа на МКПП, однако имеет сразу два ведущих вала. Если просто, эти валы расположены друг в друге (внешний вал имеет внутреннюю полость, куда вставлен еще один внутренний первичный вал).
На внешнем валу установлены шестерни привода 2, 4 и 6 передачи. На внутреннем валу ставятся шестерни 1, 3, 5 передачи, а также передачи заднего хода. Для каждого из валов имеется отдельное сцепление.
Актуаторы роботизированной коробки представляют собой электрические или гидросервоприводы. Электрический актуатор -электромотор с редуктором, гидравлический является гидроцилиндром, шток которого связан с синхронизатором. Главной задачей как первого, так и второго типа устройств становится механическое перемещение синхронизаторов КПП, а также включение и выключение сцепления.
Блок управления коробкой передач является микропроцессорным ЭБУ, к которому подключены внешние датчики, которые задействованы в ЭСУД автомобиля. Другими словами, контроллер коробки передач взаимодействует с датчиками от двигателя, а также ряда других систем (например, ABS и т.д.). Часто блок управления коробкой совмещен с ЭБУ двигателем, при этом коробка работает по собственному заданному алгоритму.
Как работает роботизированная коробка передач
Что касается принципов работы РКПП, для начала движения и дальнейшего плавного переключения передач необходимо задействовать сцепление (как и в МКПП). Включение сцепления реализует актуатор, который получает сигнал от ЭБУ коробкой и начинает медленно вращать редуктор.
В коробке с двумя сцеплениями сначала включается первое сцепление внутреннего первичного вала. Далее актуатор выбора и включения передачи подводит синхронизатор к шестерне первой передачи. В результате шестерня блокируется на валу и начинает вращаться вторичный вал.
После того, как автомобиль начал движение, водитель продолжает нажимать на педаль газа для разгона. В однодисковых роботах с одним сцеплением для включения второй передачи требуется некоторое время, в результате чего возникает характерный «провал».
Чтобы избавиться от такой задержки и сократить время переключений в конструкцию коробки добавили второе сцепление и еще один вал. В результате появилась так называемая преселективная роботизированная КПП.
Если просто, пока включена первая передача, вторая уже также готова к включению, так как одновременно задействовано второе сцепление. Получается, после сигнала от микропроцессорного блока быстро сработает включение второй передачи.
Подобным образом происходит переключение на последующие высшие передачи, а также понижение передач при езде. При этом время переключения минимально и занимает доли секунды, исключены перегазовки, практически отсутствует разрыв тяги и т.д. Результат — динамичная езда и максимальная топливная экономичность.
Работа в автоматическом режиме становится возможной благодаря тому, что ЭБУ коробкой постоянно анализирует сигналы с внешних датчиков. Блок учитывает нагрузку на ДВС, скорость движения ТС, положение педали газа, пробуксовку колес и т.д.
Также РКПП имеют возможность ручного переключения передач, имитируя работу гидромеханической АКПП в ручном режиме (например, Типтроник). Еще на некоторых «роботах» можно заблокировать включение повышенных передач.
Простыми словами, водитель при помощи селектора выбирает режим, при котором ЭБУ коробкой не будет инициировать включение, например, 3 передачи и выше, что помогает преодолевать сложные участки пути (снег, гололед, грязь и т.д.).
Преимущества и недостатки коробки — робот
Сегодня коробка-робот является достаточно распространенным решением. Например, концерн VAG активно устанавливает подобные коробки, которые знакомы потребителям, как DSG, на разные модели Audi, Volkswagen, Porsche, Skoda и т.д. Также роботизированную трансмиссию массово ставят на модели Ford, Mitsubishi, Honda и машины целого ряда других мировых производителей.
На первый взгляд может показаться, что РКПП имеет только плюсы: надежность и ремонтопригодность «механики», быстрота переключений, топливная экономичность, возможность выдерживать большой крутящий момент и т.д.
При этом по заверениям самих производителей РКПП должны в скором времени полностью вытеснить «классические» АКПП с гидротрансформатором и вариаторные коробки. Однако на практике этого не произошло.
Дело в том, что в плане комфорта работа «однодисковых» роботизированных коробок (с одним сцеплением) далека от АКПП и, тем более, от бесступенчатого вариатора. Автомобиль с такой коробкой дергается при езде, переключения «затянуты», имеются провалы и т.п.
Также ресурс сцепления на «роботе» и актуаторов достаточно низкий (в среднем, около 80-100 тыс. км.). При этом стоимость актуаторов высокая, а ремонтопригодность данных элементов сомнительная. По этой причине многие сервисы практикуют узловую замену, то есть актуатор просто меняется на новый.
Что касается более сложных и дорогих преселективных коробок с двумя сцеплениями, переключения в этом случае более плавные и больше напоминают работу обычной АКПП. Однако ресурс такого «робота» (например, DSG 6 или DSG 7) все равно снижен, нередко возникают проблемы по части механики и электроники, а ремонт в ряде случаев потребует значительных расходов.
В качестве итога отметим, что многие автопроизводители, особенно из Японии, начали постепенно отказываться от установки коробки-робот на свои модели, заменяя ее классической АКПП с гидротрансформатором (ГДТ).
Например, Hondа Civic 8 хэтчбек, который изначально выпускался с РКПП, но в дальнейшем после рестайлинга получил полноценный «автомат». То же самое можно сказать о популярной Toyota Corolla 2007 года, которая позднее получила вместо «робота» автоматическую гидромеханическую коробку.
устройство и принцип работы. Советы по выбору.
Коробка робот похожа на механическую. Единственным отличием от механики является то, что в коробке робот передачи переключает некий исполнительный механизм (робот). Есть два типа исполнительных механизмов:
- • Гидравлический привод;
- • Электрический привод.
Классическая роботизированная коробка передач была сконструирована в 60-х годах 20 века. Основным ее недостатком является большое время переключения передач, что приводит к толчкам и провалам в динамике автомобиля. Для того чтобы сократить время переключения передач, была разработана коробка с двумя сцеплениями. Стоит отметить, что роботизированная коробка передач с двойным сцеплением является самой распространенной на рынке. Например, всем известная коробка DSG от Фольсксваген является роботизированной коробкой передач с двумя сцеплениями.
Такую коробку можно условно представить состоящей из двух коробок (см. рисунок). Каждая из них со своим сцеплением. Одна коробка передач отвечает за нечетные передачи, вторая – за четные. Коробки существует независимо от друг друга.
Давайте рассмотрим процесс переключения передач. Предположим, вы едете на первой передаче. В то время как вы едете на первой, датчики управления сообщают коробке, что происходит разгон автомобиля и заранее включается вторая передача. Т.е. в момент, когда необходимо включить вторую передачу, она уже включена заранее. И коробка просто выключает первую передачу.
Для наглядности давайте рассмотри процесс переключения передач на классической механике.
- 1. Выжимаете сцепление;
- 2. Выключаете передачу;
- 3. Включаете передачу;
- 4. Отпускаете сцепление.
В коробке робот необходимо выполнить всего два действия:
- 1. Выключить сцепление 1
- 2. Включить сцепление 2.
Получается, что в механической коробке передач необходимо выполнить на два действия больше, чем в роботизированной. Поэтому роботизированная коробка передач быстрее переключает передачи, что сказывается на динамике автомобиля, а также на расходе топлива.
Выводы: Современные роботизированные коробки передач имеют два сцепления. Каждое из которых, отвечает за свои передачи. Эти передачи включаются заблаговременно, а в момент непосредственного переключения управление коробкой просто включает или выключает требуемое сцепление.
На рынке существует два вида сцепления:
- • Сухого типа. Для автомобилей с малой мощностью. Недостаток коробок со сцеплением сухого типа – малый ресурс.
- • Мокрого типа. Для автомобилей повышенной мощности. Работают с использованием масла и рассчитаны на более продолжительный срок службы.
Коробка-робот по сравнению с автоматической коробкой передач имеет несколько преимуществ:
- • Низкий расход топлива;
- • Лучшая динамика автомобиля;
- • Стоимость.
К недостаткам можно отнести:
- • низкий ресурс
- • недостаток квалифицированного ремонта роботизированных коробок передач в СНГ.
Если вы спросите, с какой же коробкой нужно покупать автомобиль? Если рассматривайте покупку нового авто, то мы однозначно рекомендуем коробку робот. Однако если вы покупаете бэушный авто с пробегом более 200 тыс., то здесь лучше рассматривать вариант покупки либо механики, либо автоматической акпп.
Роботизированная трансмиссия (РКПП) и принцип работы коробки
РКПП — роботизированная коробка передач (коробка «робот), которая позволяет выбирать и включать необходимую передачу без участия водителя, то есть автоматически. При этом ошибочно полагать, что роботизированная трансмиссия является одной из разновидностей АКПП (гидромеханический автомат).
Прежде всего, чтобы понять, что такое роботизированная коробка передач, для начала необходимо вспомнить устройство и принцип работы обычной механической коробки (МКПП). Так вот, фактически роботизированная коробка является той же «механикой», однако автоматическое переключение передач в данном типе КПП становится возможным благодаря наличию боков управления и электронно-механических исполнительных устройств.
Содержание статьи
Устройство, особенности и принцип работы роботизированной коробки передач
Как уже было сказано выше, РКПП состоит из механической коробки передач, а также дополнительных устройств для выжима сцепления, выбора и переключения передачи. Данные устройства называются актуаторами (актуатор сцепления, актуатор выбора передачи). Также коробка «робот» имеет собственную систему управления, которая представляет собой ЭБУ коробкой и ряд электронных датчиков, взаимодействующих с блоком.
Получается, данный тип КПП представляет собой механическую коробку с автоматическим управлением и принципиально отличается от классического «автомата», а также бесступенчатого вариатора.
Роботизированная КПП, как и обычная МКПП, имеет сцепление, в ней не используется трансмиссионная жидкость ATF в качестве рабочей для управления и т.д. Добавим, что в современных «роботах» может быть как одно, так и два сцепления. В первом случае следует понимать однодисковый «робот», а во втором преселективную роботизированную коробку передач с двумя сцеплениями.
Если говорить об устройстве коробки — робот, можно выделить следующие базовые составные элементы:
- Коробка передач, которая по устройству напоминает «механику;
- Актуаторы (сервоприводы), отвечающие за выжим сцепления и включение передачи;
- Блок управления коробкой (микропроцессорный ЭБУ) и внешние датчики;
Давайте рассмотрим устройство РКПП на примере 6-и ступенчатой роботизированной коробки передач с двумя сцеплениями. Сама коробка похожа на МКПП, однако имеет сразу два ведущих вала. Если просто, эти валы расположены друг в друге (внешний вал имеет внутреннюю полость, куда вставлен еще один внутренний первичный вал).
На внешнем валу установлены шестерни привода 2, 4 и 6 передачи. На внутреннем валу ставятся шестерни 1, 3, 5 передачи, а также передачи заднего хода. Для каждого из валов имеется отдельное сцепление.
Актуаторы роботизированной коробки представляют собой электрические или гидросервоприводы. Электрический актуатор -электромотор с редуктором, гидравлический является гидроцилиндром, шток которого связан с синхронизатором. Главной задачей как первого, так и второго типа устройств становится механическое перемещение синхронизаторов КПП, а также включение и выключение сцепления.
Блок управления коробкой передач является микропроцессорным ЭБУ, к которому подключены внешние датчики, которые задействованы в ЭСУД автомобиля. Другими словами, контроллер коробки передач взаимодействует с датчиками от двигателя, а также ряда других систем (например, ABS и т.д.). Часто блок управления коробкой совмещен с ЭБУ двигателем, при этом коробка работает по собственному заданному алгоритму.
Как работает роботизированная коробка передач
Что касается принципов работы РКПП, для начала движения и дальнейшего плавного переключения передач необходимо задействовать сцепление (как и в МКПП). Включение сцепления реализует актуатор, который получает сигнал от ЭБУ коробкой и начинает медленно вращать редуктор.
В коробке с двумя сцеплениями сначала включается первое сцепление внутреннего первичного вала. Далее актуатор выбора и включения передачи подводит синхронизатор к шестерне первой передачи. В результате шестерня блокируется на валу и начинает вращаться вторичный вал.
После того, как автомобиль начал движение, водитель продолжает нажимать на педаль газа для разгона. В однодисковых роботах с одним сцеплением для включения второй передачи требуется некоторое время, в результате чего возникает характерный «провал».
Чтобы избавиться от такой задержки и сократить время переключений в конструкцию коробки добавили второе сцепление и еще один вал. В результате появилась так называемая преселективная роботизированная КПП.
Если просто, пока включена первая передача, вторая уже также готова к включению, так как одновременно задействовано второе сцепление. Получается, после сигнала от микропроцессорного блока быстро сработает включение второй передачи.
Подобным образом происходит переключение на последующие высшие передачи, а также понижение передач при езде. При этом время переключения минимально и занимает доли секунды, исключены перегазовки, практически отсутствует разрыв тяги и т.д. Результат — динамичная езда и максимальная топливная экономичность.
Работа в автоматическом режиме становится возможной благодаря тому, что ЭБУ коробкой постоянно анализирует сигналы с внешних датчиков. Блок учитывает нагрузку на ДВС, скорость движения ТС, положение педали газа, пробуксовку колес и т.д.
Также РКПП имеют возможность ручного переключения передач, имитируя работу гидромеханической АКПП в ручном режиме (например, Типтроник). Еще на некоторых «роботах» можно заблокировать включение повышенных передач.
Простыми словами, водитель при помощи селектора выбирает режим, при котором ЭБУ коробкой не будет инициировать включение, например, 3 передачи и выше, что помогает преодолевать сложные участки пути (снег, гололед, грязь и т.д.).
Преимущества и недостатки коробки — робот
Сегодня коробка-робот является достаточно распространенным решением. Например, концерн VAG активно устанавливает подобные коробки, которые знакомы потребителям, как DSG, на разные модели Audi, Volkswagen, Porsche, Skoda и т.д. Также роботизированную трансмиссию массово ставят на модели Ford, Mitsubishi, Honda и машины целого ряда других мировых производителей.
На первый взгляд может показаться, что РКПП имеет только плюсы: надежность и ремонтопригодность «механики», быстрота переключений, топливная экономичность, возможность выдерживать большой крутящий момент и т.д.
При этом по заверениям самих производителей РКПП должны в скором времени полностью вытеснить «классические» АКПП с гидротрансформатором и вариаторные коробки. Однако на практике этого не произошло.
Дело в том, что в плане комфорта работа «однодисковых» роботизированных коробок (с одним сцеплением) далека от АКПП и, тем более, от бесступенчатого вариатора. Автомобиль с такой коробкой дергается при езде, переключения «затянуты», имеются провалы и т.п.
Также ресурс сцепления на «роботе» и актуаторов достаточно низкий (в среднем, около 80-100 тыс. км.). При этом стоимость актуаторов высокая, а ремонтопригодность данных элементов сомнительная. По этой причине многие сервисы практикуют узловую замену, то есть актуатор просто меняется на новый.
Что касается более сложных и дорогих преселективных коробок с двумя сцеплениями, переключения в этом случае более плавные и больше напоминают работу обычной АКПП. Однако ресурс такого «робота» (например, DSG 6 или DSG 7) все равно снижен, нередко возникают проблемы по части механики и электроники, а ремонт в ряде случаев потребует значительных расходов.
В качестве итога отметим, что многие автопроизводители, особенно из Японии, начали постепенно отказываться от установки коробки-робот на свои модели, заменяя ее классической АКПП с гидротрансформатором (ГДТ).
Например, Hondа Civic 8 хэтчбек, который изначально выпускался с РКПП, но в дальнейшем после рестайлинга получил полноценный «автомат». То же самое можно сказать о популярной Toyota Corolla 2007 года, которая позднее получила вместо «робота» автоматическую гидромеханическую коробку.
Читайте также
Роботизированная коробка Тойота: принцип работы коробки Toyota
За основу трансмиссии Freetronic была взята традиционная «механика» оснащенная электроприводами. Другое известное название «робота» Freetronic — ММТ (Multimode). Роботизированная трансмиссия может работать как в режиме «автомат», так и в ручном режиме.
Переключение передач в трансмиссии происходит при помощи трех электродвигателей. Один из них отвечает за выключение (выжим) сцепления, а два других за смену передач. Работой приводов управляет электронный блок управления (ТСМ), путем обработки сигналов с бесконтактных датчиков.
Трансмиссией Freetronic комплектовались автомобили марки Toyota с 2005 по 2009 гг. Это такие модели как: Corolla, Auris, Yaris, Aygo,Echo, Prius и другие. На моделях Yaris и Echo концерн Тойота впервые стал устанавливать автоматическое сцепление TFT.
Общее устройство
1 — индикатор в автомобиле, 2 — концевой выключатель рычага КПП, 3 — привод, 4 — датчик 1-2, 5 — датчик заднего хода, 6 — датчик нейтрали, 7 — датчик частоты вращения (КПП), 8 — датчик положения сцепления, 9 — электронный блок управления MMT — Фритроник.
Выключение и включение сцепления TFT в трансмиссии Freetronic происходит путем управления величиной давления жидкости, которая подводится к главному цилиндру сцепления. Коробка переключения передач оснащена датчиками, одни из которых следят за реальным положением селектора передач, а другие измеряют частоту вращения первичного вала КПП. Рычаг переключения оснащен концевыми выключателями упреждающими блок управления о намерениях водителя задействовать рычаг коробки переключения передач. При наличии неисправностей на панели приборов начинает мигать индикатор. Индикатор также сигнализирует водителю при его попытке неверного переключения.
Принцип работы роботизированной коробки Toyota
- До запуска двигателя сцепления всегда включено
- Пуск. После поворота ключа в положение зажигание (положение КПП – нейтраль) блок ММТ выполняет «выжим» сцепления и можно запускать двигатель
- Начало движения. При включении первой передачи или передачи заднего хода и нажатии педали газа, блок ММТ мгновенно получает информацию об этом путем сигнала от датчиков и выдает команду золотниковому клапану на понижение давления, что ведет к включению сцепления и автомобиль трогается. Для плавного включения сцепления клапан золотника открывается постепенно, и полное его включение происходит после выравнивания частоты вращения коленвала и первичного вала КПП. Блок в этот момент дает команду на полное открытие канала главного цилиндра сцепления на слив.
- Смена передач. При отпускании педали газа и изменении положения рычага КПП, соответствующие датчики сообщают об этом в блок ММТ. Блок дает команду на «выжим» сцепления. Дальнейшее включение сцепления происходит после получения сигналов от датчиков нейтрали и «концевиков» рычага.
- Остановка. В момент торможения автомобиля входной вал КПП начинает вращаться с меньшим числом оборотов (ниже заданной нормы) и блок управления TFT выполняет «выжим» сцепления.
- Зуммер. Включается при возникновении внештатных ситуаций: ошибка при переключении вниз, попытка начала движения с передачи выше 3-й, чрезмерная нагрузка на сцепление, попытка запуска при включенной передаче, открыта дверь водителя при запущенном двигателе и положении рычага селектора соответствующее движению вперед или назад ( не нейтраль).
Роботизированная коробка передач (робот) что это? Как работает: плюсы, минусы
Коробка робот: преимущества, недостатки
Еще совсем недавно рядовой автолюбитель не имел свободы выбора трансмиссии с покупкой автомобиля. Технологический прогресс последних лет подарил несколько интересных систем – это и вариатор, и роботизированная коробка. Техническая реализация коробки-робота велась еще в 20 лет назад, однако внедрение этой трансмиссии в массы произошло сравнительно недавно. Первую версию агрегата немецкие инженеры выпустили в 2002 году. С тех пор было придумано немалое количество его разных вариаций и модификаций.
Конструкция и принцип работы роботизированной коробки
В конструктивном плане коробка-робот идентична с обычной «механикой». Вся разница заключается в том, что подбор и переключение передач в ней это полностью автоматизированный процесс. Фактически это значит, что есть некий «мозг», который и отвечает за включение нужной скорости. Причем процесс смыкания/размыкания сцепления практически не заметен и не ощутим. Поэтому водители авто с роботом отмечают высокий уровень комфорта, простоту использования и динамичность.
Особенность робота заключается и в том, что эта коробка может совмещать как одно, так и сразу два сцепления. Внедрив в конструкцию дополнительный механизм разъединения трансмиссии от двигателя, инженеры попытались снизить негативный эффект провалов тяги. Двойное сцепление реализовано в коробках по типу DSG или Powershift. Такие коробки еще называют преселективными или «предварительно выбирающими». Они позволяют при включенной скорости выбрать следующую передачу без перерыва в работе КПП. На авто с такими коробками передача крутящего момента происходит без потерь, так как нет разрыва потока мощности.
Стоит ли приобретать автомобиль с преселективной коробкой?
Как и в случае с автоматической коробкой, функционирование робота невозможно без наличия электронной системы. Датчики следят за определенными рабочими характеристиками коробки, передают информацию блоку управления, где формируются команды исполнительным механизмам с учетом прописанных алгоритмов. Предусмотрен и ручной режим работы (как Типтроник на АКПП), благодаря которому водитель имеет возможность переключать передачи за счет органов управления – селектор или переключатели, расположенные под рулем.
Разновидности роботизированных коробок
Нередко робот является агрегатом, сконструированным на базе готового решения. Часто за основу узла инженеры берут гидромеханический автомат и внедряют фрикционное многодисковое сцепление. Также возможен вариант, когда классическая «механика» получает привод гидравлического или механического типа.
Коробка робот с электрическим приводом считается более простым и дешевым решением. Его основной недостаток – низкая скорость работы (0.3-0.5 с) с одновременным небольшим энергопотреблением. В такой коробке исполнительными механизмами выступают сервоприводы и механическая передача. В гидравлике задействованы специальные гидроцилиндры, которыми управляют электромагнитные клапаны.
Коробка с гидравликой работает шустрее, однако её функционирование подразумевает наличие в системе жидкости под давлением. Поддержка постоянного давления требует серьёзных энергетических затрат. Тем не менее, робот с гидравлическим приводом нашел свое применение на многих спортивных автомобилях, таких как Lamborghini Aventador, Ferrari 599GTO. Также его ставят на машины из среднего и премиум сегмента. Робот с электрическим приводом не составит труда обнаружить на недорогой современной машине. Рассмотрим детально распространенные модификации РКПП с двойным сцеплением.
DSG
Роботизированная коробка DSG считается наиболее «продвинутой» версией автомата. Её легко встретить на автомобилях концерна VAG. Пожалуй, это самая распространенная модификация РКПП с двойным сцеплением. То есть, это преселективная трансмиссия, переключающая передачи крайне быстро (буквально за доли секунд). Эффективность работы DSG значительно выше обычной АКПП. В ней первое сцепление отвечает за нечетные передачи, а второе за четные. В свою очередь коробки DSG принято делить на два вида – «мокрые» и «сухие». Первый вид – «мокрый» – появился первым и характеризуется наличием шести передач. Сцепление в такой DSG находится в масляной ванне, отсюда и название. Спустя время Volkswagen презентовали DSG-7. Это РКПП с «сухим» сцеплением. На практике считается более проблематичным вариантом.
Познакомиться подробнее с DSG (нажмите, чтобы прочитать статью)
Интересное видео на тему того, как работает роботизированная коробка ДСГ
Проблемы
Powershift
Роботизированная трансмиссия Powershift является разработкой компании Ford, поэтому и устанавливается на автомобили североамериканского концерна. Это преселективная КПП с двумя сцеплениями. В качестве исполнительных механизмов выступают сервоприводы, которыми управляет электронный блок, закрепленный на корпусе коробки. Если верить многочисленным отзывам, то Powershift более надежна конкурентной DSG. Однако это не делает её лидером рынка, так как получила те же недостатки, что и роботизированная КПП от Volkswagen.
Познакомиться подробнее с PowerShift (нажмите, чтобы прочитать статью)
S-tronic
Компания Audi входит в состав концерна VAG, но это не мешает ей разрабатывать собственные автомобильные трансмиссии. Так инженеры Audi создали преселективную коробку S-tronic, которая сильно напоминает DSG. Но есть некоторые существенные отличия. Сегодня S-tronic ставят преимущественно на автомобили с передним и полным приводом. В ней также два сцепления, что позволяет роботу работать беспрерывно в одном потоке и без потери мощности. Еще есть R-tronic – другая модификация РКПП от компании Audi. Отличается от S-tronic наличием гидропривода. Такая коробка переключает передачи примерно за 0.8 мс, а это серьёзный показатель динамичности.
Познакомиться с S-Tronic (нажмите, чтобы прочитать статью)
DCT M Drivelogic
Впервые роботом DCT M Drivelogic баварские инженеры оснастили BMW M3. Коробка может работать как в полностью автоматическом, так и в ручном режиме. В обоих случаях передачи переключаются с недостижимой механике и автомату скоростью. Водителю не нужно пользоваться селектором коробки передач. Достаточно переключить лепестковый элемент управления под рулем в нужное положение. Особенность DCT M заключается в наличии функции Drivelogic, которая позволяет водителю самостоятельно переключать передачи и переходить от спокойного стиля вождения к динамичному. Всего предусмотрено 11 программ – 5 для автоматического режима и 6 для ручного.
PDK
Роботизированная КПП от компании Porsche конструктивно является узлов, в корпусе которого помещены две механически коробки. Также конструкцией предусмотрено два сцепления, поэтому PDK относится к сегменту трансмиссий с двойным сцеплением. Функционирует робот за счет гидравлического привода и электронного блока управления. Всего предусмотрено семь передач, последняя с большим передаточным отношением снижает показатель расхода топлива. Пик динамики наблюдается с активной шестой скоростью. Коробка работает в двух режимах – автоматическом и ручном (полуавтоматическом). Сегодня PDK ставят на автомобили с мощными моторами – Porsche Panamera Turbo, Porsche 911 Turbo, Porsche Cayman.
Speedshift DCT
7-ступенчатая роботизированная КПП была разработана специально для мощных автомобилей концерна Mercedes Benz и подразделения AMG. Коробка отличается наличием четырех программ и функции старта Rage AMG Speedshift. Вместо привычного гидротрансформатора в Speedshift DCT задействована компактная муфта сцепления, работающая в масляной ванне – так называемое «мокрое» сцепление. От Других модификаций РКПП этот робот отличается небольшим весом – всего 80 кг. Сделать узел легким удалось за счет применение в его изготовлении его картера легкого магниевого сплава.
TCT
Компания Alfa Romeo недавно презентовала свою версию роботизированной коробки передач – Twin Clutch Transmission. В первую очередь её поставили на модель Giulietta, где она превосходно сочетается с бензиновым и дизельным мотором (разгон до «сотни» всего за 7.7 и 7.9 сек соответственно). Коробка TCT оснащена гидронасосом электрического типа, который обеспечивает работоспособность привода сцепления и механизма переключения передач. Проектировался узел при помощи специалистов компании LuK, имеющих огромный опыт в разработке и производстве автомобильных сцеплений. Некоторые конструктивные элементы TCT также выполнены из легких материалов, что делает коробку на 10 кг легче, чем классическая механика или вариатор.
Twin Clutch SST
Робот с двойным сцеплением Twin Clutch SST ставят на автомобили Mitsubishi, например, на Lancer Evolution и Outlander XL. Это спортивная коробка, в которой вместо гидротрансформатора исправно служат два механизма сцепления, помещенные в один корпус. Отличается тремя режимами работы, которые позволяют адаптироваться автомобилю под разные условия эксплуатации. Для городской езды подходит режим Normal Mode: переключение передач происходит плавнее и мягче, расход топлива минимальный. В режиме Sport Mode переход на высшие скорости происходит на высоких оборотах, что несколько увеличивает расход. Третий режим Super Sport Mode переключает скорости на максимально высоких оборотах. Его целесообразно использовать, когда требуется полностью реализовать динамический потенциал автомобиля.
Плюсы и минусы робота
Сегодня можно найти довольно большое число автовладельцев, положительно отзывающихся о роботизированной коробке. Особенно нравится автоматизированная трансмиссия начинающим водителям. Это и понятно, ведь для управления автомобилем достаточно нажимать педаль тормоза и газа, а электронная система самостоятельно включит нужную передачу. Отсюда вытекают главные преимущества КПП:
- высокий комфорт;
- удобство;
- простота использования;
- высокая скорость переключения передач;
- экономия топлива в городском цикле;
- конструктивная схожесть с механикой, что придает агрегату дополнительную надежность, если сравнивать с тем же вариатором;
- возможность переключения ступеней в ручном режиме.
Как показывает практика, расход бензина автомобилем коробкой-роботом при одинаковых условиях в городском цикле на 20% меньше, чем у транспортного средства с привычным автоматом. Однако такое устройство далеко неидеальное. Также в процессе эксплуатации авто можно ощутить некоторые недостатки узла:
- высокая стоимость обслуживания и ремонта;
- непродолжительные задержки в переключении передач;
- дешевые модели не позволяют провести адаптацию под конкретный стиль вождения.
Специалисты прогнозируют, что по мере увеличения автомобилей с роботом, развитием технологий ремонта и обслуживания этой коробки со временем станет более доступным и дешевым ремонт агрегата. Тот самый электронно-гидравлический блок, или просто «мехатроник», является самой дорогостоящей деталью в DSG. Еще несколько лет назад в случае его даже не самой критичной поломки дилеры, не думая, ставили вердикт – замена устройства. Сейчас хватает специализированных сервисов, выполняющих простые и сложные ремонты «мехатроника».
Основные отличия от автоматической коробки
Автоматическая коробка не утратила актуальности ни с появлением вариатора, ни с появлением роботизированной трансмиссии. Это по-прежнему довольно надежный, а главное хорошо изученный агрегат. Сходство в том, что и автомат, и робот обеспечивают плавный переход с одной передачи на другую. На этом всё. Гораздо больше отличий. Главная разница между этими двумя коробками заключается в следующем:
- В АКПП не предусмотрено жесткое сцепление с двигателем;
- Робот ощутимей снижает нагрузку на мотор за счет максимально коротких переключений передач;
- С автоматической КПП автомобиль уступает в плане динамики;
- Новые РКПП еще недостаточно хорошо изучены, окончательно неизвестен ресурс этих агрегатов, чего нельзя сказать об АКПП.
Возможно, автомат даже накладней обслуживать, а вот что касается ремонта, то здесь и говорить нечего. Автоматическую коробку перебирают на каждом шагу, хватает и грамотных специалистов, способных в кратчайшие сроки восстановить агрегат после серьёзной поломки. В случае с РКПП ситуация ровно обратная.
Заключение
Мы выяснили, что такое коробка робот. Очевидно, что будущее за конструктивно и функционально совершенными автомобильными системами. Но процесс окончательного усовершенствования робота еще не начался. Перед покупкой автомобиля нужно четко уяснить для себя, каким требованиям он должен отвечать. Сказать точно, что лучше – робот или автомат – крайне сложно. И, наверное, никто не возьмется за это. Поэтому каждый автомобилист должен на основании всех плюсов и минусов определить для себя, какой тип трансмиссии удовлетворит все запросы и потребности.
Рассматриваете роботизированные паллетайзеры? Вот преимущества и приложения
Что такое роботизированные штабелеры?
Роботизированные системы укладки на поддоны автоматизируют процесс укладки продукта на поддоны. Их также можно запрограммировать на депаллетирование — неотъемлемую часть многих производственных линий.
Роботизированные паллетоукладчики решают некоторые проблемы, которые не могли решить их более старые аналоги — обычные паллетоукладчики.
Обычные паллетоукладчики существуют уже более полувека.Они состоят из ряда конвейеров и связанных с ними приспособлений. По мере того, как продукт движется по конвейеру, он поворачивается и поворачивается для правильной ориентации перед формированием рядов на концевом упоре. Ряды осторожно помещают на стол для формирования слоев, а затем слои укладывают на поддоны.
Как и их обычные собратья, роботизированные паллетоукладчики часто используют подающий конвейер. Однако они не ориентируют предметы, толкая их по конвейеру. Скорее, робот манипулирует предметами, либо поворачивая их при движении вниз по конвейеру, либо поднимая их прямо на поддон.
Как и у большинства конкурирующих технологий, как у обычных, так и у роботизированных штабелеукладчиков есть свои плюсы и минусы. Обычные паллетоукладчики, производящие до 200 ящиков в минуту, обычно имеют более короткое время цикла. Однако ряд конвейеров, необходимых для ориентации продукта, означает, что им также обычно требуется больше места.
С другой стороны, роботизированные паллетоукладчикиотлично справляются с манипуляциями с продуктом — переворачиванием ящиков для демонстрации с вывешенными этикетками или штабелированием ведер и пакетов, а также с обработкой большого количества SKU в многопоточных операциях.Поскольку им часто приходится выполнять более медленные функции, такие как вращение продукта, их производительность более изменчива, чем у обычных паллетоукладчиков.
При этом эти системы могут быть быстрыми — до 2000 циклов в час. Пример того, как можно использовать скорость, точность и ловкость роботов для сокращения времени выполнения заказа, см. В нашем тематическом исследовании здесь.
Как и в случае с любой другой автоматизацией, для получения окупаемости инвестиций в автоматизированный штабелеукладчик необходимо сначала выбрать подходящее роботизированное решение, а затем его надлежащую реализацию.В PeakLogix наша миссия — понять ваши цели, потребности и стремления, чтобы мы могли применить наш более чем 30-летний опыт работы в сфере погрузочно-разгрузочных работ, чтобы найти лучшее решение, отвечающее вашим потребностям.
Их преимущества
У автоматизированного процесса паллетирования есть много преимуществ. Большинство из них справедливо как для обычного, так и для роботизированного укладывания на поддоны.
Повышенная безопасность
Растяжения, растяжения, разрывы и перенапряжение — самые распространенные производственные травмы в США.Как правило, это вызвано повторяющимися движениями, поднятием больших или тяжелых предметов или и тем, и другим. Ручное штабелирование и разборка продукта на поддоны и снятие с них — это именно та работа, которая может привести к травмам.
Один из способов смягчить это — предоставить работникам достаточное количество перерывов для отдыха, а не только 15 минут, которые требуются в большинстве штатов. Операторы должны соблюдать свои квоты, но компании с сильной культурой безопасности будут реалистичны в отношении человеческих ограничений.
Еще один способ защитить сотрудников от риска — не подвергать их опасности.Роботизированные паллетоукладчики избавляют людей от рисков, связанных с штабелированием продуктов, заменяя их роботами.
Контакт с оборудованием — еще одна частая причина травм. Этого можно избежать за счет использования ограждений и ворот вокруг оборудования для укладки на поддоны. Доступ к рабочему полю робота запрещен, кроме подающего конвейера.
Без повреждений
В повторяющихся задачах, таких как укладка на поддоны, роботы более точны и точны, чем люди. Они каждый раз движутся так, как были запрограммированы.Их не отвлекают громкие звуки на складе, они не спешат и не путают один артикул с другим.
В случае ущерба это означает, что продукт не уронили. Он не уложен на неправильный поддон, в неправильной ориентации или под чем-то слишком тяжелым.
Роботымогут быть оснащены инструментами на конце руки (EOAT), способными работать с мешками, ведрами, картонными коробками, тяжелыми сумками или чем-либо еще. Благодаря технологиям адаптивного захвата — например, комбинируя зажимы и пылесосы — их можно запрограммировать на приложение давления, достаточного для подъема предмета, не ломая его футляр, не порывая сумку или не сгибая коробку.
Своевременное производство
Поскольку роботы быстрее и надежнее людей, их результаты также более предсказуемы. А в культуре, которая все больше и больше движется к производству точно в срок и принципам бережливого производства, предсказуемость является ключевым моментом.
Робот, который выполняет 20 циклов в минуту, может делать это в течение 24 часов без перерыва, как их человеческие коллеги. Это означает, что вы точно знаете, сколько времени потребуется, чтобы сформировать достаточное количество слоев для заполнения одного поддона или целой партии поддонов.
PeakLogix интегрировала несколько роботов-паллетизаторов Fuji Robotics EC-201 в производственную линию национального производителя продуктов питания
Человеческий фактор
Сокращение трудозатрат и связанных с ними затрат — очевидная экономия, которую обеспечивают эти системы.
Но более того, отстранение людей от нежелательной задачи штабелирования предметов на поддонах может положительно сказаться на моральном состоянии всего вашего предприятия. Ощущение того, что у вашей жизни есть цель и что вы движетесь к этой цели, является важной частью самореализованной жизни.И хотя в ручном труде, безусловно, нет ничего плохого, мало кто предпочел бы выполнение квоты штабелированных коробок в течение рабочего дня более значимым задачам.
Удалив эту низкокачественную задачу, сотрудникам могут быть предоставлены возможности для работы с более высокой добавленной стоимостью, что может улучшить их самооценку и их взгляд на жизнь в целом. Что, в свою очередь, улучшит моральный дух и увеличит удержание сотрудников.
Типы
Пьедестал
Роботизированные паллетоукладчики в виде подставки — это машины, похожие на руки, установленные на подставке.Они бывают окрашены в различные цвета, такие как желтый, белый, бежевый, красный и т. Д. — все зависит от того, какой производитель их произвел.
Роботы-палетоукладчики часто представляют собой 4-осевые станки, хотя при необходимости они могут иметь 5 или даже 6 осей. Количество осей определяет степень свободы робота при подъеме и размещении продукта. 4-осевые машины могут поворачиваться вдоль своей базы, дотягиваться до продукта, поднимать / опускать продукт и вращать свои концевые эффекторы для ориентации этого продукта.
Их грузоподъемность варьируется от нескольких фунтов до более тонны.Один блок может быть запрограммирован на укладку нескольких линий на поддоны или, при высокоскоростных операциях, несколько единиц могут укладывать на поддоны одну линию.
Их работа относительно проста. Поддоны размещаются в обозначенном месте вручную или с помощью автоматического дозатора поддонов. Система укладки на поддоны может быть запрограммирована, а может и не быть запрограммирована на размещение разделительного листа на поддоне.
В то же время продукт, который перемещался по подающему конвейеру, ударяется о концевой упор. Используя соответствующий инструмент на конце руки, такой как вакуум или захват, робот поднимает продукт по отдельности или партиями.Он помещает продукт на поддон практически в любой конфигурации, при необходимости чередуя конфигурации слоев для обеспечения устойчивости.
Портальный стиль
Портал — каркасная конструкция с боковыми опорами и надземным пролетом; Роботизированный паллетоукладчик портального типа — это просто паллетоукладчик, подвешенный к порталу. Они лучше всего подходят для тяжелых нагрузок на низких скоростях. Они могут обрабатывать отдельные элементы, но также хорошо работают со слоями, рядами или единичными нагрузками.
Паллетоукладчикипортального типа используют салазки, которые перемещаются по рельсам, нависающим над рабочей площадкой.Концевые эффекторы поднимаются и опускаются, чтобы манипулировать продуктом и перемещать его. В зависимости от системы портальные роботы могут перемещать продукт по 2, 3 или даже 4 осям. Это означает, что они могут поднимать продукт, перемещать его по прямой линии (для 2-осевых роботов) или, возможно, в двух измерениях (для 3-осевых роботов), а в 4-осевых системах переориентировать продукт.
Стиль формирования слоя
Слоистая укладка на поддоны часто включает в себя серию роботов, каждый из которых выполняет свою задачу. В простой системе будет один робот в виде пьедестала, установленный вдоль конвейера.Робот будет перемещать и ориентировать продукт на конвейере таким образом, чтобы при достижении конечного упора он уже имел правильную конфигурацию для своего слоя.
После того, как слой сформирован, концевой упор удаляется, и слой передается роботу, работающему с слоями. Это поднимает слой и перемещает его на поддон.
Смешанные конфигурации корпусов
Роботизированные укладчики смешанных ящиков способны принимать ящики и ящики разных размеров и форм и изготавливать из них стабильные слои. Есть несколько способов сделать это.
Робот в виде пьедестала, установленный на рельсе, может перемещаться между сериями поддонов в зоне подготовки. На каждом поддоне он поднимает продукт и устанавливает его на приемный поддон в заранее определенной стабильной конфигурации.
Другая система может использовать серию конвейеров для доставки товаров на склад. По пути сортировочная обувь, толкатели или роботизированные манипуляторы могут направлять и ориентировать продукт. Затем слои формируются так же, как описано выше: продукт направляется к концевому упору в надлежащей конфигурации, а затем поднимается на поддон с помощью робота-пьедестала.
Соображения и факторы выбора
При интеграции роботизированного штабелера в любую операцию необходимо учитывать множество переменных.
Пропускная способность и количество SKU
Одним из основных факторов при выборе подходящего типа паллетоукладчика является пропускная способность — сколько единиц в минуту необходимо обработать. Обычные паллетоукладчики часто могут обрабатывать более быструю продукцию, но роботизированные паллетоукладчики предлагают некоторые уникальные преимущества. Гибридные системы могут дать вам лучшее из обоих миров.
Другие важные соображения включают различные размеры, вес и формы, с которыми система должна работать, а также упаковочный материал.
В недавнем прошлом некоторые виды упаковки и продуктов не подходили для роботизированных систем укладки на поддоны. Однако технология улучшилась до такой степени, что концевые эффекторы можно использовать практически для любой формы и типа материала. Но знание того, что необходимо, является важной частью процесса планирования.
Наконец, не забудьте учесть любые будущие потребности. Добавление артикулов или изменение упаковки может изменить конец инструмента или даже стиль робота.
Конфигурация поддона
Конфигурация поддона также помогает определить стиль робота и инструменты на конце руки.К важным факторам относятся:
- Количество слоев на поддоне,
- Конфигурация каждого слоя,
- Вращение конфигурации на уровне и
- Использование разделительных листов или ярусных листов.
Расположение на объекте
При выборе места в помещении важно учитывать не только стены и стеллажи. Также нужно продумать, как материал будет поступать на паллетайзер. Существуют ли системы подающих конвейеров, которые необходимо будет адаптировать, или нужно будет добавить новые конвейеры? Как проходит работа в этой зоне, включая продукцию и операторов?
Дополнительное оборудование
Роботизированные паллетоукладчики не являются полноценной системой.Поддоны необходимо доставлять вручную или с помощью дозатора поддонов. Необходимо добавить ярусные и разделительные листы, а поддоны необходимо обернуть в термоусадочную пленку для обеспечения устойчивости и безопасности. Это может происходить вручную или автоматически, в зависимости от потребностей системы.
Законы, постановления и бюджеты
Прежде чем роботизированный штабелеукладчик — или любое другое стационарное оборудование — может быть добавлен к объекту, следует учитывать местные законы и корпоративные правила. Государства, муниципалитеты и корпорации могут регулировать, как оборудование подключается или охраняется.
Возможно, наиболее очевидно, что бюджет — это главная забота. Важно не только реалистично оценивать имеющиеся средства, но и оценивать рост. Как и в большинстве случаев автоматизации, роботизированные паллетоукладчики имеют модульную конструкцию — компоненты системы могут быть добавлены к операции по частям. Поскольку организация получает выгоду от экономии затрат и повышения эффективности каждой единицы, она может реинвестировать в свою систему. Добавление слоев в операцию позволяет достичь оптимального уровня автоматизации при сохранении разумной рентабельности инвестиций.
Однако это возможно только при реалистичных прогнозах бюджета и роста.
В PeakLogix мы имеем 30-летний опыт оказания помощи нашим партнерам в понимании того, какое подъемно-транспортное оборудование может помочь их системам и как это оборудование поможет им расти на долгие годы. Мы гордимся не своей способностью продавать или устанавливать оборудование, а своей способностью настраивать решения, которые оптимизируют ваш рост.
Хотите узнать больше о роботизированных штабелерах? Свяжитесь с нами, чтобы обсудить детали и стратегии.
Control Engineering | Основные принципы коллаборативных роботов
Быстрая установка, простое программирование, гибкое развертывание и безопасная работа — четыре основных принципа, определяющих совместных роботов. Многие люди ошибочно считают, что проектирование коллаборативных роботов связано только с безопасностью; это просто стоимость входа.
Обновление внутренних функций коллаборативного робота усилило каждый из этих четырех основных принципов. Встроенная функция измерения крутящего момента, функции безопасности и повышенная точность позволяют ускорить интеграцию в широкий спектр перспективных приложений.Повышенная повторяемость делает совместных роботов подходящими для точной отделки, сборки и выполнения электронных задач.
Встроенные датчики силы крутящего момента
Коллаборативный робот со встроенными датчиками крутящего момента позволяет сразу же применять крутящий момент и упрощает обучение роботов.
В приложении для полировки с использованием того же инструмента для полировки, что и человек, коллаборативный робот может использовать ручной инструмент. В отдельной демонстрации захват опускается до тех пор, пока не почувствует небольшое сопротивление.Затем открывается и захватывает деталь. Нет необходимости во внешнем датчике для определения контакта со встроенными датчиками крутящего момента силы.
Сотрудничество человека и машины
Производство должно учитывать человеческую ценность и безопасность, мастерство и понимание потребителей, материалов и процессов. Это основные составляющие создания стоимости фабрики. Эту ценность создают не только роботы; люди, работающие с роботами, также создают большую ценность для компании.
Такие тенденции, как массовая персонализация, предполагают использование технологий для получения человеческих ценностей, улучшения производства.Совместные роботы — это то, что нужно компаниям для производства персонализированных продуктов, которые требуются потребителям.
Вдали от отгороженных промышленных роботов, которые заменяют людей автоматизированными процессами, коллаборативные роботы улучшают человеческое мастерство за счет скорости, точности и точности, необходимых для создания современных продуктов. Совместные роботы несут человеческое прикосновение к массам.
Юрген фон Холлен — президент Universal Robots. Под редакцией Марка Т. Хоске, контент-менеджера, Control Engineering, CFE Media , mhoske @ cfemedia.com.
КЛЮЧЕВЫЕ СЛОВА: Коллаборативный робот, определение силы / момента
Роботов для совместной работы проще интегрировать благодаря встроенным функциям измерения силы и крутящего момента.
Люди и роботы могут совместно работать в производственных приложениях.
Роботы для совместной работы могут улучшить человеческое мастерство за счет скорости, точности и точности.
УЧИТЬСЯ
Как коллаборативные роботы могут помочь людям в ваших производственных приложениях?
ОНЛАЙН ЭКСТРА
Universal Robots предоставляет дополнительную информацию о линейке коллаборативных роботов серии e.
См. Соответствующие новые продукты для инженеров на сайте www.controleng.com/NP4E
роботов и их применение | SpringerLink
Достижения в области электроники и механики сделали возможным создание относительно недорогих роботов. Образовательные роботы широко используются в школах, как в классах, так и во внеклассной деятельности. Большое количество обучающих роботов не позволяет дать полный обзор. Здесь мы приводим несколько примеров, которые представляют роботов, обычно используемых в образовании.
Предварительно собранные мобильные роботы
Многие образовательные роботы разработаны как предварительно собранные мобильные роботы. На рис. 1.5a показан робот Thymio от Mobsya, а на рис. 1.5b показан робот Dash от Wonder Workshop. Эти роботы относительно недороги, надежны и содержат большое количество датчиков и выходных компонентов, таких как свет. Важным преимуществом этих роботов является то, что вы можете реализовывать роботизированные алгоритмы «прямо из коробки», не тратя часы на проектирование и строительство механической части.{\ textregistered} \) кирпичи и другие компоненты здания вместе с двигателями и датчиками, а также программируемый блок, который содержит компьютер, который управляет компонентами робота. Преимущество комплектов для робототехники заключается в их гибкости: вы можете спроектировать и построить робота для выполнения конкретной задачи, ограниченного только вашим воображением. Комплект робототехники также можно использовать для обучения студентов механическому проектированию. Недостатки робототехнических комплектов состоят в том, что они более дорогие, чем простые предварительно собранные роботы, и что изучение алгоритмов робототехники зависит от способности человека успешно реализовать надежную механическую конструкцию.{\ textregistered} \) Mindstorms EV3 (любезно предоставлено Ади Шморак, Intelitek), b Poppy Ergo Jr. роботизированное оружие(любезно предоставлено Poppy Project)
Robotic Arms
Чтобы воздействовать на окружающую среду, робот требуется привод , который является компонентом робота, влияющим на окружающую среду. Многие роботы, в частности роботизированные манипуляторы, используемые в промышленности, воздействуют на окружающую среду посредством концевых эффекторов , обычно захватов или аналогичных инструментов (рис.1.3, 14.1 и 15.5b). Приводы мобильных роботов — это двигатели, которые заставляют робота двигаться, а также такие компоненты, как вакуумный насос пылесоса.
Образовательные роботы — это обычно мобильные роботы, единственными исполнительными механизмами которых являются его двигатели и устройства отображения, такие как свет, звуки или экран. Концевые эффекторы могут быть построены с помощью наборов робототехники или с использованием дополнительных компонентов с предварительно собранными роботами, хотя обучающие роботы-манипуляторы существуют (рис. 1.6b). Манипуляция объектами усложняет дизайн; однако, поскольку алгоритмы для конечных эффекторов аналогичны алгоритмам для простых мобильных роботов, большинство действий в книге предполагают только то, что у вашего робота есть двигатели и устройства отображения.
Среда разработки программного обеспечения
Каждая образовательная робототехническая система включает среду разработки программного обеспечения . Язык программирования может быть версией стандартного языка программирования, такого как Java или Python. Программирование упрощается, если используется блочный язык, обычно язык, основанный на Scratch или Blockly (рис. 1.7). 1.7Программное обеспечение Blockly для робота Thymio
Чтобы еще больше упростить программирование робота молодыми студентами, можно использовать полностью графическую нотацию программирования.На рисунке 1.8 показана графическая программная среда VPL (Visual Programming Language) для робота Thymio. Он использует пары событие-действие: когда происходит событие, представленное блоком слева, выполняются действия в следующих блоках. 1.8Программное обеспечение VPL для робота Thymio
На рис. 1.9 показана графическая программная среда для робота Dash. Он также использует события и действия, где действия представлены узлами, а события представлены стрелками между узлами.Рис. 1.9 Программное обеспечениеWonder для робота Dash.
Источник https://www.makewonder.com/mediakit с разрешения Wonder Workshop
Робот-манипулятор для захвата и перемещение, управляемое беспроводным радиочастотным модулем
Робот-манипулятор используется для сбора поднимите объект и поместите его в желаемое место. Это может быть цилиндрический робот, обеспечивающий движение по горизонтальной, вертикальной и вращательной осям, сферический робот, обеспечивающий два вращательных и одно линейное движение, шарнирный робот или робот-скара (неподвижные роботы с вращающимися руками по 3 вертикальным осям).
Преимущества
Прежде чем двигаться дальше, давайте рассмотрим несколько причин, по которым предпочтение отдается роботам, занимающимся подбором и размещением:
- Они быстрее и могут выполнять работу за секунды по сравнению с их коллегами-людьми.
- Они гибкие и имеют соответствующую конструкцию.
- Они точны.
- Они повышают безопасность рабочей среды и никогда не устают.
Детали робота Pick N Place Robot
Pick N Place RobotДавайте посмотрим, из чего на самом деле состоит робот Pick and Place:
- Rover : это основной корпус робота, состоящий из нескольких жестких тела, подобные цилиндру или сфере, соединениям и звеньям.Он также известен как манипулятор.
- Концевой эффектор : Это корпус, соединенный с последним шарниром марсохода, который используется для захвата или перемещения объектов. Это может быть аналогия руки человека.
- Исполнительные механизмы : они являются драйверами робота. Это фактически приводит в действие робота. Это может быть любой двигатель, например серводвигатель, шаговый двигатель, пневматический или гидравлический цилиндр.
- Датчики: Они используются для определения внутреннего, а также внешнего состояния, чтобы убедиться, что робот в целом работает плавно.Датчики включают сенсорные датчики, ИК-датчик и т. Д.
- Контроллер : Он используется для управления исполнительными механизмами на основе обратной связи датчика и, таким образом, управления движением каждого сустава и, в конечном итоге, движением концевого эффектора.
Работа простого робота Pick N Place Robot:
Основная функция робота Pick and Place выполняется его шарнирами. Суставы аналогичны суставам человека и используются для соединения двух последовательных твердых тел в роботе. Они могут быть поворотными или линейными.Чтобы добавить шарнир к любому звену робота, нам нужно знать о степенях свободы и степенях движения для этой части тела. Под степенями свободы понимается линейное и вращательное движение тела, а под градусами движения подразумевается количество осей, по которым тело может перемещаться.
Простой робот для захвата и размещенияПростой робот для захвата и размещения состоит из двух твердых тел на подвижном основании, соединенных между собой поворотным шарниром. Поворотный шарнир — это шарнир, который обеспечивает вращение на 360 градусов вокруг любой из осей.
- Дно или основание крепятся колесами, которые обеспечивают линейное перемещение.
- Жесткий корпус 1 st закреплен и поддерживает второй жесткий корпус, на котором установлен концевой эффектор.
- Жесткий корпус 2 nd имеет движение по всем 3 осям и 3 степени свободы. Он соединен с корпусом 1 st поворотным шарниром.
- Концевой эффектор должен иметь все 6 степеней свободы, чтобы достигать всех сторон компонента и занимать положение на любой высоте.
В целом базовый робот для захвата и размещения работает следующим образом:
- Колеса под основанием помогают перемещать робота в желаемое место.
- Жесткое тело, поддерживающее концевой эффектор, изгибается или выпрямляется, чтобы достичь положения, в котором находится объект.
- Концевой эффектор крепко захватывает объект и помещает его в желаемое положение.
Теперь, когда у нас есть краткое представление о роботе для захвата и размещения, основной вопрос заключается в том, как им фактически управлять.
Простым роботом для захвата и размещения можно управлять, управляя движением его рабочего органа. Движение может быть с использованием гидравлического движения, то есть с использованием гидравлической жидкости под давлением для привода робота, или с использованием пневматического движения, то есть с использованием сжатого воздуха для создания механического движения. Однако наиболее эффективным способом является использование двигателей для обеспечения требуемого движения. Двигатели должны управляться, чтобы обеспечить необходимое движение роботу и рабочему элементу.
Рабочий пример управления роботом Pick N Place
Как насчет управления роботом с помощью всего нескольких кнопок на клавиатуре? Да, это возможно! Просто нажав нужную кнопку, мы можем передать роботу команду, чтобы он двигался в любом направлении для достижения нашей задачи.Более того, этого можно достичь с помощью простой беспроводной связи.
Давайте посмотрим, как это работает на самом деле:
Передатчик состоит из клавиатуры, соединенной с микроконтроллером. Любой номер кнопки в десятичном формате преобразуется микроконтроллером в 4-значное двоичное, и параллельный выход на одном из его портов подается на кодировщик. Кодер преобразует эти параллельные данные в последовательные, и они поступают в передатчик, снабженный антенной для передачи последовательных данных.Блок-схема
, показывающая передатчик робота Pick N PlaceСторона приемника состоит из декодера, соединенного с микроконтроллером. Декодер преобразует полученную команду из последовательного формата в параллельную и передает эти данные микроконтроллеру. На основе этой команды микроконтроллер отправляет соответствующие входные сигналы драйверам двигателей для управления соответствующими двигателями. Блок-схема
, показывающая приемник робота Pick N Place.Система состоит из двух двигателей, обеспечивающих движение всего робота, и двух других двигателей, обеспечивающих движение руки.Необходимо управлять концевым эффектором или захватом, чтобы обеспечить надлежащее давление на объект для эффективного обращения с ним и обеспечения мягкого захвата. Это обеспечивается за счет управления двигателями рычагов с помощью соответствующей команды. Выход двигателей рычага подключен к резистору 10 Ом / 2 Вт, и во время перегрузки двигателя или состояния блокировки на резисторе создается высокое напряжение, которое вызывает высокий логический уровень на выходе оптоизолятора и прерывание. Контакт микроконтроллера, подключенный к выходу оптоизолятора через pnp-транзистор, получает низкий логический сигнал, который останавливает все остальные операции захвата.
Таким образом, с помощью простой радиочастотной связи мы можем фактически управлять роботом для захвата и размещения.
Практическое применение робота для захвата и установки:
- Защитные приложения : Его можно использовать для наблюдения, а также для захвата вредных объектов, таких как бомбы, и их безопасного распространения.
- Промышленное применение : Эти роботы используются в производстве, чтобы подбирать необходимые детали и размещать их в правильном положении, чтобы завершить крепление оборудования.Его также можно использовать для размещения предметов на конвейерной ленте, а также для сбора дефектных продуктов с конвейерной ленты.
- Медицинские приложения : Эти роботы могут использоваться в различных хирургических операциях, таких как операции по замене суставов, ортопедические и внутренние хирургические операции. Он выполняет операции с большей точностью и аккуратностью.
Помимо этих приложений, эти роботы могут также использоваться в различных других приложениях, подходящих для человечества.
Остается вопрос: как далеко наступит день, когда роботы полностью упростят путь людям?
Процесс роботизированной сварки — как работает роботизированная сварка
Процессы роботизированной сварки
21 августа 2019
Роботизированная сварка автоматизирует процесс сварки, повышая точность, безопасность и сокращая время, необходимое для завершения каждого проекта.Эти преимущества делают процесс роботизированной сварки популярной альтернативой ручному соединению металлов. Некоторые отрасли используют преимущества этого автоматизированного процесса, чтобы как можно быстрее получить нужные результаты.
Как работает роботизированная сварка
При использовании роботов для любого процесса метод требует внесения поправок для автоматизации. То же самое можно сказать и о сварке, при которой используются несколько инструментов, которых нет в ручном эквиваленте. Людям не нужно программировать, как сварщики-роботы.
Сам робот имеет руку, которая может перемещаться в трех измерениях для прямолинейных типов и в большем количестве плоскостей для шарнирных версий. Механизм подачи проволоки отправляет присадочную проволоку роботу, так как она нужна ему для сварочных работ. Горючая горелка на конце рычага плавит металл для обеспечения процесса сварки. Поскольку температура достигает тысячи градусов, использование роботов для этого процесса делает людей более безопасными.
Сертифицированные операторы-люди все еще должны оставаться рядом с роботами.Эти рабочие должны иметь сертификаты Американского сварочного общества, AWS, которые сертифицируют не только сварщиков, выполняющих ручную сварку, но и операторов роботизированных сварочных манипуляторов. Операторы программируют контроллер с помощью обучающего пульта. Это устройство устанавливает новые программы, перемещает манипулятор и изменяет параметры процесса. Чтобы начать сварку, оператор использует кнопки на панели управления.
Инструмент в манипуляторе робота нагревается, чтобы расплавить металл, чтобы соединить нужные детали. При необходимости механизм подачи проволоки подает больше металлической проволоки к рычагу и горелке.Ожидая сварки следующих деталей, рычаг перемещает горелку к очистителю, чтобы удалить с рычага любые металлические брызги, которые могут затвердеть на месте без этого процесса.
Поскольку одной из основных причин использования роботов-сварщиков является защита рабочих, эти автоматизированные системы обладают множеством функций безопасности. Дуговые экраны предотвращают смешивание высокотемпературной дуги с кислородом. Закрытые помещения защищают операторов от высоких температур и яркого света.
Роботизированные сварочные процессы
Сварка требует высокого уровня образования и навыков.Однако количество профессиональных сварщиков не соответствует потребностям отрасли. По данным Американского общества сварщиков, к 2022 году отрасль столкнется с нехваткой 450 000 сварщиков. Вместо того, чтобы позволить критически важным проектам, которые эти рабочие завершили, отставать, роботы могут компенсировать это отставание.
Роботыавтоматизируют процесс, что обеспечивает более высокую точность, меньшее количество отходов и более быструю работу. Благодаря широкому спектру доступного оборудования роботы адаптируются к широкому спектру процессов сварки, включая дугу, сопротивление, точечную сварку, TIG и другие.
1. Дуговая сварка
Одним из наиболее распространенных видов роботизированной сварки является дуговой процесс. В этом методе электрическая дуга генерирует сильный нагрев до 6500 градусов по Фаренгейту, который плавит металл. Расплавленный металл соединяет детали вместе, затвердевая в стабильное соединение после охлаждения. Когда проект требует большого объема точно соединенных металлов, дуговая сварка является идеальным вариантом.
2. Сварка сопротивлением
Когда проекты нуждаются в термообработке или снижении затрат, роботы могут использовать контактную сварку.Во время этого процесса электрический ток создает лужу расплавленного металла, проходящего между двумя металлическими основаниями. Этот расплавленный металл соединяет куски металла вместе.
3. Точечная сварка
Некоторые материалы устойчивы к электрическим токам, что исключает их использование в других видах сварки. Такая ситуация часто возникает в автомобильной промышленности при сборке частей автомобильного кузова. Чтобы решить эту проблему, сварщики-роботы используют разновидность контактной сварки для соединения пары тонких металлических листов в одной точке.
4. Сварка TIG
Роботизированная сварка, требующая высокого уровня точности, может потребовать сварки TIG. Этот метод также известен под термином газовая вольфрамовая дуговая сварка или GTAW. Электрическая дуга проходит между вольфрамовым электродом и металлическим основанием.
5. Сварка МИГ
Газовая дуговая сварка металлическим электродом, также известная как GMAW или MIG, — это быстрый и простой метод, использующий высокий уровень наплавки. Проволока непрерывно движется к нагретому наконечнику сварочного аппарата, который плавит проволоку, позволяя большому количеству расплавленного металла капать на основание для соединения основания с другой деталью.
6. Лазерная сварка
Когда сварочные проекты требуют точности для большого объема деталей, лазерная сварка является предпочтительным методом соединения металлов. Для небольших деталей, таких как ювелирные изделия или медицинские компоненты, часто используется лазерная сварка.
7. Плазменная сварка
Плазменная сваркапредлагает наиболее значительную степень гибкости, поскольку оператор может легко изменять как скорость газа, проходящего через сопло, так и температуру.
Свяжитесь с нами
Robotic vs.Ручная сварка
Ручная сварка все еще используется в современном производстве. Для проектов, в которых вам нужен эксперт, чтобы быстро изменить используемые стили сварки, ручная сварка будет вашим лучшим выбором. Профессиональный сварщик может быстро изменить то, что он делает, но роботы не так быстро адаптируются к неопределенным ситуациям.
Поскольку ручная сварка остается процессом, в котором все еще нуждаются многие компании, профессиональные сварщики не исчезнут в ближайшее время. Фактически, из-за нехватки опытных сварщиков, упомянутых выше, те, кто имеет сертификат, легко найдут работу, даже если несколько предприятий инвестируют в роботов.
Замена ручных сварочных аппаратов роботами не приведет к прекращению деятельности AWS по сертификации. Большинству операторов роботов-сварщиков необходимо пройти сертификацию в области робототехники в этой области, для которой AWS также предлагает сертификаты. Наличие экспертов по робототехнике, знающих о сварке, гарантирует, что проекты будут правильно запрограммированы, чтобы завершить их как можно быстрее и с минимальными затратами.
Следует ли использовать роботизированную сварку?
Использование роботизированной сварки во многом зависит от типа проекта, над которым вы работаете.Давайте рассмотрим некоторые плюсы и минусы роботизированной сварки, чтобы помочь вам определить, подходит ли этот метод для вашего проекта.
Плюсы роботизированной сварки
Роботизированная сварка имеет множество положительных качеств, которые убеждают предприятия выбирать этот процесс для своих проектов. Эти преимущества могут повысить производительность и прибыль как для сварочной компании, так и для компаний, которым она поставляет.
1. Повышенная эффективность
В отличие от людей, которым требуются перерывы и отдых, робот может работать в 24-часовую смену.Более продолжительное рабочее время и более высокая скорость позволяют роботизированным сварочным аппаратам выполнять свои проекты намного быстрее, чем это могли бы сделать люди. Благодаря более быстрому завершению работы роботизированные сварочные аппараты намного превосходят все, что может сделать человек.
2. Повышенная безопасность
Роботы-сварщикиоснащены рядом средств безопасности для защиты людей от сварочной дуги, ее температуры и яркости. Эти функции безопасности помогают поддерживать безопасность на рабочем месте. Когда у рабочих будет более безопасное рабочее место, они будут более продуктивными и будут лучше удовлетворены работой.Травмы и повреждение оборудования также обходятся компаниям дорого, поэтому эти меры безопасности также могут сэкономить им деньги.
3. Лучшая точность
Идеальный проект для робота включает повторяющиеся движения, применяемые к большому объему деталей. При выполнении такой работы даже самый опытный работник со временем совершит ошибки. Роботы завершат проект с более высокой степенью точности, потому что машина будет продолжать работать с тем же уровнем внимательности, пока проект не будет завершен.
4. Меньше отходов
Благодаря повышенной точности роботы производят меньше отходов из-за ошибок. Сварщикам, работающим вручную, возможно, придется выбросить детали, которые были ошибочно сварены вместе, или детали со слабыми соединениями. Поскольку роботы работают с большей точностью, они делают меньше ошибок. Без такого количества материала, выбрасываемого из-за ошибок, предприятие, в котором используются роботизированные сварочные аппараты, работает более эффективно и производит меньше отходов.
5. Более низкая стоимость доставки
После установки роботы могут сваривать большое количество деталей.Хотя первоначальные затраты компании, использующей роботизированный сварочный аппарат, могут быть высокими, высокая производительность машины в конечном итоге окупит убытки. Поскольку автоматические сварочные аппараты имеют высокий уровень производства, проекты, выполняемые с их помощью, могут стоить меньше, чем проекты, в которых используется команда людей.
Роботы-сварщикитакже могут сократить расходы на доставку. Сварочная компания может использовать одного оператора вместо бригады сварщиков для выполнения того же объема работы. Сокращая накладные расходы, компания, которую вы нанимаете для сварочных работ, может предложить более низкие цены или дополнительные услуги.
Минусы роботизированной сварки
Роботизированная сварка, хотя и полезна, имеет некоторые недостатки, которые в некоторых ситуациях могут перевесить преимущества.
1. Более высокая первоначальная стоимость
Да, ваши расходы на доставку, вероятно, будут ниже, если вы воспользуетесь услугами компании со сварочными роботами. Однако, если бы вы сами инвестировали в оборудование и обучили операторов, вы, вероятно, сочли бы эти вложения убыточными. Отдельные компании, которые профессионально не предлагают сварочные услуги, могут не использовать роботов-сварщиков в достаточной степени, чтобы оправдать высокую закупочную цену оборудования.
Если вы хотите, чтобы ваш бизнес воспользовался преимуществами роботизированной сварки, передача работы на аутсорсинг будет наиболее финансово ответственным вариантом для вашей компании. Вы получите быстрый результат при больших объемах без необходимости тратить значительную часть своего бюджета на оборудование.
2. Меньшая гибкость
У того, что роботы работают точнее, чем люди, есть и обратная сторона. Люди могут реагировать на неожиданные ситуации не так, как роботы.Когда сварщику-роботу необходимо внести изменения, оператор должен остановить процесс и перепрограммировать его. Для сложных проектов это увеличивает время, необходимое.
3. Невозможно для небольших проектов
Для небольших проектов время, необходимое для программирования манипулятора робота, может быть больше, чем время процесса сварки. Для небольших проектов сварщик-человек мог бы выполнить задачу быстрее, но это время зависит от размера проекта и скорости программирования оператора.
Будущее роботизированной сварки
Сегодня роботизированная сварка составляет лишь небольшую часть сварочных проектов в отрасли, но это, вероятно, изменится с появлением новых технологий.Будущие инновации приведут к появлению сварочных роботов, которые будут проще в использовании, работать с другими машинами и станут популярными.
1. Управляемые разумом сварочные роботы
В настоящее время операторы должны программировать сварочных роботов, чтобы запускать их в процессе. Однако вместо компьютерного терминала или обучающего пульта будущим операторам, возможно, придется думать только о том, что они хотят от робота.
Исследователи из Университета Иллинойса в Урбане-Шампейне создали колпачок, который передает мозговые волны в работу роботизированной сварочной руки.Применительно к отрасли такой процесс мог бы сократить объем обучения, необходимого существующим сварщикам-ручным сварщикам, чтобы стать операторами роботов. Профессионалы могли надеть колпачок и просмотреть планы, чтобы рассказать роботу, как правильно сваривать детали, вместо того, чтобы подключать компьютерную программу.
Поскольку для этих манипуляторов не требуются отдельные компьютерные программы, роботизированные манипуляторы могут выполнять даже небольшие проекты, для которых время программирования в настоящее время слишком велико, чтобы использование роботов имело смысл.
Вероятно, эта технология не появится в ближайшее время. По оценкам исследователей, несмотря на успех прототипа исследовательской группы, разработка крышки для коммерческого использования потребует как минимум пару лет.
2. Коллаборативные роботы
Представьте, что ваш партнер по работе — робот, а не человек. Некоторые компании уже используют совместных роботов. Эти машины имеют удобную для людей конструкцию, которая позволяет легко взаимодействовать с людьми. Датчики делают этих роботов способными собирать информацию и реагировать на меняющиеся ситуации.
Промышленным роботам традиционно требовалось предварительное программирование для выполнения крупномасштабных задач. Эти прочные, но дорогие и громоздкие устройства занимают слишком много места и денег, чтобы быть жизнеспособным вариантом для малых предприятий.
Чтобы решить эту проблему, инженеры создали более надежных роботов для совместной работы, которые могут работать с людьми в промышленных приложениях. Разработчики этих машин надеются сократить на 90% количество задач, которые можно было бы выполнять автоматически, но не делают.
Роботов для совместной работы можно интегрировать в участки ручной сварки, чтобы дополнить работу сварщиков-людей. Ожидайте, что с такими изменениями будет даже больший рост, чем рынок уже демонстрирует.
3. Растущий рынок
Как транспортный, так и автомобильный рынки продолжают внедрять технологические инновации, повышающие производительность. Сварочные роботы — критически важная часть деятельности этих отраслей. В связи с ростом в этих секторах в течение пяти лет с 2018 по 2023 год использование роботов-сварщиков будет расти со средним ежегодным темпом роста 8.91%.
Растущий спрос на автомобили во всем мире заставляет транспортную отрасль и автомобильный сектор увеличивать производство. Увеличение производства потребует инвестиций в оборудование, такое как роботизированные сварочные манипуляторы, которые увеличивают скорость и точность процесса автомобилестроения.
Наши услуги по роботизированной сварке
Вам не нужно вкладывать средства в собственных роботов-сварщиков, чтобы воспользоваться преимуществами их использования. Для этого потребуется гораздо больше времени и денег, чем может потратить большинство предприятий.Вместо этого доверьте свои сварочные проекты профессионалам Summit Steel & Manufacturing. У нас есть предприятие площадью 120 000 квадратных футов в Рединге, штат Пенсильвания, где работает наше роботизированное сварочное оборудование. Все наши специалисты имеют сертификаты AWS, чтобы гарантировать точность сварочных проектов, которые мы выполняем с помощью роботов. Эти автоматизированные службы нуждаются в надзоре и правильном программировании для правильного выполнения работы, а наличие сертифицированных технических специалистов, занимающихся программированием, гарантирует, что роботы правильно выполняют свои задачи.
В Summit Steel мы хотим предложить вашему бизнесу универсальное решение для любого проекта по изготовлению металла или металлообработке. Для получения дополнительной информации о нашей роботизированной сварке или любых наших комплексных услугах свяжитесь с нами сегодня.
Свяжитесь с нами
Брайан Рид — вице-президент по продажам и развитию бизнеса Summit Steel & Manufacturing Inc.
Boston Dynamics представляет Stretch: нового робота, предназначенного для перемещения ящиков на складах
Boston Dynamics наиболее известна своей роботизированной собакой Spot, машиной, предназначенной для работы в различных средах, от морских нефтяных вышек до глубоких подземных шахт.Но в последние годы компания уделяет все больше внимания логистике, и сегодня представляет нового робота, предназначенного только для одного применения: перемещение ящиков на складах.
Робот называется Stretch и выглядит относительно скучно для творения Boston Dynamics. Он не создан по образцу людей или животных, а нацелен на то, чтобы быть максимально практичным. Он имеет квадратную мобильную базу, содержащую набор колес, «мачту восприятия» с камерами и другими датчиками, а также огромную роботизированную руку с семью степенями свободы и набор присосок на конце, который может захватывать и перемещать ящики до 23 килограммы (50 фунтов) в весе.
Что связывает Stretch с другими машинами Boston Dynamics, так это мобильность. Обычно, когда оборудование для автоматизации устанавливается на складах, система крепится болтами в одном месте с моделированием рабочего процесса вокруг этого. Stretch, для сравнения, предназначен для того, чтобы скользить в любое существующее рабочее место, где он может быть полезен при загрузке или разгрузке товаров.
«Все зависит от того, в чем проблема сегодняшнего дня».
«Вот что замечательно в этой системе: она может обеспечить автоматизацию сред, в которых нет инфраструктуры автоматизации», — сказал The Verge вице-президент Boston Dynamics по развитию бизнеса Майкл Перри.«Вы можете воспользоваться этой возможностью, и вы можете переместить ее в кузов грузовика, вы можете переместить ее в проходы, вы можете переместить ее рядом с вашими конвейерами. Все зависит от того, в чем проблема сегодняшнего дня ».
Stretch может работать от батарей в течение восьми часов за раз или переключаться на привязанное питание. Изображение: Boston DynamicsЭто позволит Boston Dynamics ориентироваться на клиентов, которые в противном случае избегали бы автоматизации, поскольку ее интеграция слишком дорога или требует много времени, — говорит Перри.Около 80 процентов складов в мире не имеют оборудования для автоматизации, что дает компании значительный доступный рынок. Но у Stretch пока нет ценника, и вполне возможно, что для предприятий с низкой рентабельностью робот не стоит хлопот, независимо от того, насколько он мобильный.
Boston Dynamics проявляет интерес к логистике с 2019 года, когда она приобрела Kinema Systems, компанию, которая производит программное обеспечение машинного зрения для роботов на складах. Затем он разработал колесного робота под названием Ручка, который мог перемещать ящики с помощью роботизированной руки, балансируя себя с помощью огромного качающегося противовеса, такого как хвост.
Перри говорит, что Handle имеет «подходящую площадь и зону действия» для складских помещений, но не может работать достаточно быстро. Рука робота прикреплена непосредственно к его основному корпусу, что означает, что вся машина должна перемещаться с каждым грузом. Для сравнения, рука Stretch свободно поворачивается благодаря некоторым умным (и запатентованным) противовесам, спрятанным внутри его квадратного основания.
«Это действительно секретный соус», — говорит Перри. «Эта основа способна выдерживать инерционную силу руки, а также коробку, раскачивающуюся под большим весом, без необходимости полагаться на стальную пластину весом в несколько тысяч килограммов, прикрученную к полу.”
Вакуумные захваты Stretch означают, что они могут работать только с коробками с плоскими поверхностями, что ограничивает их полезность на определенных складах. Изображение: Boston Dynamics ПроисхождениеStretch можно проследить до двуногого робота Atlas от Boston Dynamics, который может настолько плавно балансировать свой вес, что может бегать, прыгать, сальто и т. Д. «Атлас, поднимающий коробку, — это не просто вытягивание рук и их перемещение, а координация бедер, ног и туловища», — говорит Перри.«Многое из того же дизайнерского мышления вошло в Stretch».
В результате Boston Dynamics утверждает, что Stretch может перемещать до 800 ящиков в час, что сопоставимо с производительностью человека-сотрудника. Аккумуляторы большой емкости означают, что Stretch может работать в течение восьми часов подряд, прежде чем потребуется подзарядка.
Однако к такой пропускной способности следует относиться скептически. Заставить роботов работать на складах невероятно сложно из-за большого разнообразия этих пространств.Рабочие процессы могут меняться каждый день по мере того, как приходят и уходят разные товары, и часто ценится гибкость. Неспособность машин справиться с этими проблемами до сих пор привела к динамике автоматизации по принципу «все или ничего». Вы либо переделываете весь склад, чтобы он был достаточно регулярным, чтобы его могли понять машины, либо вы остаетесь с людьми, хозяевами неизвестного.
Boston Dynamics заявляет, что Stretch сможет преодолеть этот разрыв. Компания заявляет, что роботом может управлять любой человек, прошедший всего несколько часов обучения, и что его мобильная база означает, что он может размещаться в пространствах, предназначенных для людей.Это будет работать? Мы узнаем об этом только тогда, когда Stretch возьмется за дело. Boston Dynamics заявляет, что в настоящее время ищет клиентов для пилотного тестирования Stretch и планирует коммерческое внедрение в 2022 году.
.www | ГМУНК
Сентябрь 2013 г. ––
Получившийся короткометражный фильм — единственное в своем роде визуальное и технологическое достижение благодаря особому сочетанию таланта и оборудования за дверями предприятия B&D, и был принят во всем мире с неожиданными похвалами и демонстрацией в Интернете и на других ресурсах. фестивальный цикл — все благодаря огромному количеству любви и страсти, вложенных в проект.
Концепция
–– Проекция В основе пьесы лежали Принципы сценической магии с использованием пяти основных категорий иллюзий.Эти категории во многом определили концептуальную и эстетическую основу и были объединены с эстетикой графического дизайна, наполненной минималистичными формами и иллюминированной фрактальной геометрией.
Затем это направление было помещено в проекционную физическую инсталляцию, где вся «магия» была запечатлена вживую и в камере, снята в документальном стиле без пост-эффектов или обработки, чтобы все выглядело аутентично и реально. По сути, огромные технологии за кулисами полностью скрыты от зрителя методами, используемыми для съемки представления.
Подход к проектированию
–– Теория иллюзий в дизайне Подход к дизайну для фильма заключался в том, чтобы Графика была проинформирована Черно-Белым Искусством Оптических Иллюзий в качестве основного визуального катализатора. Было логично, что визуально, если произведение будет основано на принципах магии и иллюзий, графика также впишется в эту теорию иллюзий в дизайне. Эта эстетика была применена ко всем произведениям искусства в КОРОБКЕ, и она эволюционировала на протяжении всего произведения по мере изучения Принципов, чередующихся между затененной объемной графикой и самосветящейся геометрией.
Во-вторых, дизайн освещения и стиль съемок в значительной степени основывались на эстетике «Нуар» 40-х и 50-х годов с использованием черно-белой палитры и стилизованного минимального освещения для создания очень театрального изображения; поскольку с точки зрения эстетики дизайна имело смысл отдать дань уважения тому периоду для произведения, основанного на такой вневременной форме искусства, как магия.
И, наконец, финальная часть головоломки заключалась в создании звуковой среды, которая способствовала психоделической природе дизайна; по сути, выстраивая эмоциональную дугу по всему произведению, когда оно переходит от таинственных объектов внутри Коробки к ярко освещенной и открытой демонстрации технологий и, в конечном итоге, достигает своей кульминации в виде полностью реализованного перформанса.Мириады аналоговых синтезаторов были использованы самим мастером Soviet Rouge, которые идеально вписывались в концептуальные реплики и визуальную палитру пьесы.
Преобразование
–– Глава 01 Первый принцип Магии, исследуемый в этой пьесе, — это Трансформация, где КОРОБКА трансформируется из одного состояния в другое, во многом как шелковый носовой платок, меняющий цвет, или типичный карточный трюк, меняющий одну масть на другую … В данном случае Трансформация было достигнуто за счет того, что КОРОБКА сначала реагировала на прикосновение и жест персонажа, а затем на его движение, в результате чего Геометрия и Объем Коробки разделялись этими действиями.Было исследовано множество визуальных стилей, чередующихся между Затененной графикой, Оп-артом, Освещенными кубами и Каркасами.
Левитация
–– Глава 02Второй принцип Magic — это левитация, где, подобно тому, как фокусник бросает вызов гравитации и парит в нескольких дюймах от пола, холст начинает отрываться от земли и соприкасаться с сюрреалистическим. Появляется еще один холст, и вместе стая сфер взаимодействует с освещенным туннелем, создавая иллюзию левитации объектов и перехода с одного холста на другой.
Ближе к концу раздела сферы возвращаются как одна сверхмощная Электросфера, которая является визуальной кульминацией раздела, затрагивая тему Восстановления, другого Принципа Магии.
Перекресток
–– Глава 03 Третий принцип Magic на самом деле называется «Проникновение», но, поскольку мы все — кучка мальчишек, мы не могли справиться с этим названием, поэтому термин «пересечение» использовался, чтобы все оставались взрослыми. Для этого принципа, который основан на идее прохождения одного объекта через другой — то есть набора стальных колец, соединяющихся и разъединяющихся, или мечей, проходящих через помощника в корзине — графическое решение заключалось в том, чтобы два холста взаимодействовали друг с другом, в то время как визуализация визуального эффекта «Solid-through-Solid».Итак, используя общую центральную область пересечения, было визуализировано множество графических выдавливаний и углублений, чтобы создать глубину и интригу при выполнении этого Принципа Магии.
Телепортация
–– Глава 04 Четвертый принцип магии — это телепортация, когда маг заставляет что-то перемещаться из одного места в другое — заимствованное кольцо находится внутри клубка шерсти, канарейка внутри лампочки, помощник из шкафа в заднюю часть театра, монета из одной руки в другую и т. д.В этом разделе призма постоянно дублирует себя с каждым состоянием внешнего вида, в конечном итоге превращаясь в додекаэдр, который затем переносится между холстами в потоке роботизированного движения.В конце концов, Додекаэдр становится легким объектом и путешествует по длинному глубокому коридору, в конце концов снова распадается на части и падает в глубокую пропасть, выступающую на полу.
Escape
–– Глава 05Пятый и последний Принцип магии, по определению, заключается в том, что мага помещают в ограничивающее устройство (т.е., наручники или смирительную рубашку) или смертельную ловушку, и сбегает в безопасное место. Примеры включают в себя то, что его надевают смирительной рубашкой и помещают в переполненный резервуар с водой, связывают и помещают в автомобиль, проходя через автомобильную дробилку.
В приложении BOX Demo персонаж «захвачен» единой геометрией холста, а затем раскрывается в Box, где персонаж затем перемещается в объеме, поскольку геометрический свет падает позади него. В подходящем крещендо раскрывается гигантский алмазный портал, где персонаж сбегает из объема, путешествуя по коридору, интерактивное освещение освещает его конечности, когда он уносится к Спасению.
Процесс
–– Сочетание отраслей Процесс создания части был довольно сложным, сочетая традиционные инструменты графического дизайна и анимации с роботизированной анимацией, проекционным картированием, автоматизированной кинематографией и другими технологиями, уникальными для студии. Задача заставить графический дизайн сначала интегрироваться с движениями роботов в физическом пространстве, а затем поддерживать его визуальную точность при проецировании, требовала множества итераций, поскольку то, что хорошо выглядит на экране, не всегда переводится в проецируемые и снятые изображения.В конце концов, была разработана довольно сложная система для визуализации дизайна почти в точности так, как задумано; Да и крутой проектор 4K тоже не повредил. Для получения дополнительной информации в The Creator’s Project есть прекрасная короткометражка о проекте, которую стоит посмотреть.
Воспоминания
–– Дети веселятся Эта команда была одной из лучших на сегодняшний день, и не только из-за огромного таланта каждого члена в соответствующем опыте. С дядей Джеффом, многочасовой и сложной креативной работой, эта команда всегда была сплочена, доверяла друг другу и чертовски весело проводила время.
В результате этот восхитительный танцевальный ансамбль был вырезан, чтобы передать дух проекта, мастерски отредактированный единственным и неповторимым Яном Колоном — им действительно понравилась эта калибровочная палочка PhaseSpace. Было очень весело создавать этот невероятно богатый проект; один из лучших когда-либо. Всегда.
BOX Credit List
Производственная компания: BOT & DOLLY
Исполнительные продюсеры: Билл Галуша, Ник Рид
Исполнительный креативный директор: Джефф Линнелл
Креативный и технический директор: Тарик Тарик
Директор по дизайну: Брэдли Дж. Манковиц
Ведущие графические дизайнеры: Брэдли Дж. Манковиц, Джейсон Инглиш Керр
3D-художники: Скотт Пагано, Брэдли Дж. Манковиц, Джейсон Инглиш Керр, Конор Гребель
2D-художники: , Бен Хокинс, Педро Фигера
Оператор-постановщик: Джо Пикард
Художники по свету: Джо Пикард, Фил Рейнери
Проекционный / сенсорный дизайнер: Фил Рейнери
Робототехника Анимация: Тарик Абдель-Гавад, Брэндон Кувад Джордж Бэнкс, Майкл Бердсворт
Оператор робототехники: Майкл Бердсворт, Брэндон Круисман 902 68 Изготовление реквизита: Мэтт Биттерман, Итан Дейл
Руководитель сценария: Ян Колон
Звукорежиссеры: Джо Пикард, Майкл Бердсворт
PAs: Шон Сервис, Дакота Смит, Нико Мизоно, Эрик Вендел 9027, Патрик Уолш
1 Редакторы: Эшли Родхольм, Ян Колон
Музыка / звуковой дизайн: Кейт Руджеро
Звуковое сопровождение: Джоэл Раабе
Исполнители: Тарик Абдель-Гавад, Ирис, Скаут .