Моделирование работы двигателя внутреннего сгорания на конвертерном газе
Ключевые слова: конвертерный газ, двигатель, альтернативное топливо, утилизация, мощность
Аннотация
Впервые рассмотрена возможность утилизации конвертерного газа ПАО «НЛМК» в газопоршневых агрегатах.
Представлена существующая схема работы газоотводящего тракта конверторов, и описан вариант модернизации газоотводящего тракта для сбора и очистки газа. Дан расчет работы двигателя внутреннего сгорания при работе на природном газе на номинальной нагрузке. Смоделирована работа двигателя на конвертерном газе, указаны сравнительные характеристики работы двигателя с колебаниями состава конвертерного газа.
Результаты моделирования показали, что состав газа существенно влияет на работу ДВС. Снижаются основные показатели работы, что указывает на необходимость внесения изменений в конструкцию двигателя.
Литература
1. Курзанов С.Ю. Повышение энергетической эффективности сталеплавильного производства на основе использования конвертерных газов: автореф. дис. …канд. техн. наук. М.: Изд-во МЭИ, 2011.
2. Лотош В.Е. Утилизация вторичных энергетических ресурсов // Ресурсосберегающие технологии. 2003.
№ 9. С. 3—18.
3. Агапитов Е.Б., Максимов А.А. Разработка схемы комбинированного производства газообразного топлива на основе конвертерного газа с целью сбережения энергетических ресурсов металлургического производства // Вопросы технических наук: новые подходы в решении актуальных проблем: Сборник науч.
4. Группа НЛМК — повысить мощности КЦ-2 на 19% [Электрон. ресурс] www.nlmk.com/ru/media-center/news-groups/nlmk-group-to-boost-capacity-of- steelmaking-shop-2-at-lipetsk-site-by-19-/?from=en (дата обращения 18.04.2018).
5. Расщупкин В.П., Корытов М.С. Производство стали. Методика выплавки. Омск: СибАДИ, 2007.
6. Линчевский Б.В., Соболевский А.Л., Кальменев А.А. Металлургия черных металлов. М.: Металлургия, 1986.
7. Ларионов Л.Б., Бураев М.К. Расчет процесса сгорания биогаза в газовом двигателе с искровым зажиганием, конвертированного из дизеля с наддувом // Вестник СВФУ. 2015. Т. 12. № 1. С. 52—58.
8. Карташевич А.Н., Малышкин П.Ю., Плотников С.А., Зубакин А.С. Исследования работы двигателя на альтернативных топливах // Вестник Белорусской гос. сельскохозяйственной академии. 2016. № 4. С. 115—117

10. Европейский опыт утилизации сбросного энергопотенциала промышленных газов [Электрон. ресурс] www.cogeneration.com.ua/ru/analytics/special-gas/ hydrogen-utilization (дата обращения 21.06.2019).
11. Мысник М.И., Свистула А.Е. Анализ теплофизических свойств альтернативных топлив для двигателей внутреннего сгорания // Ползуновский вестник. 2009. № 1—2. C. 37—43.
12. Гичев Ю.А. Проектно-конструкторские решения по использованию конвертерного газа для нагрева металлолома // Современная наука: исследования, идеи, результаты, технологии. 2013. № 5. С. 54—59.
13. Куземко Р.Д., Сущенко А.В. Улучшение теплового баланса конвертерной плавки за счет регенирации теплоты отходящих газов // Вестник Приазовского гос. техн. ун-та. Серия «Технические науки». 1998. № 6. С. 62—69.
14. Гичев Ю.А., Запотоцкая А.Ю. Tехнические решения и эффективность использования конвертерного газа для обжига известняка // Международные конференции: литье, металлургия.

15. Максимов А.А., Агапитов Е.Б. Совершенствование энергоэффективной схемы утилизации конвертерного газа // Теплотехника и информатика в образовании, науке и производстве: Сборник докл. IV Всерос. науч.- практ. конф. студентов, аспирантов и молодых ученых с междунар. участием. Екатеринбург: Изд-во УрФУ, 2015. С. 101—105.
16. Дремов А.Н., Гридин С.В. Использование газов сталеплавильных конвертеров в качестве вторичных энергоресурсов // Металлургия XXI столетия глазами молодых: Сборник докл. Всеукр. науч.-практ. конф. студентов. Донецк: Изд-во ДонНТУ, 2013. С. 143—144.
18. Баптизмаиский В.И., Меджибожский М.Я., Охотский В.Б. Конвертерные процессы производства стали. Теория, технология, конструкции агрегатов.
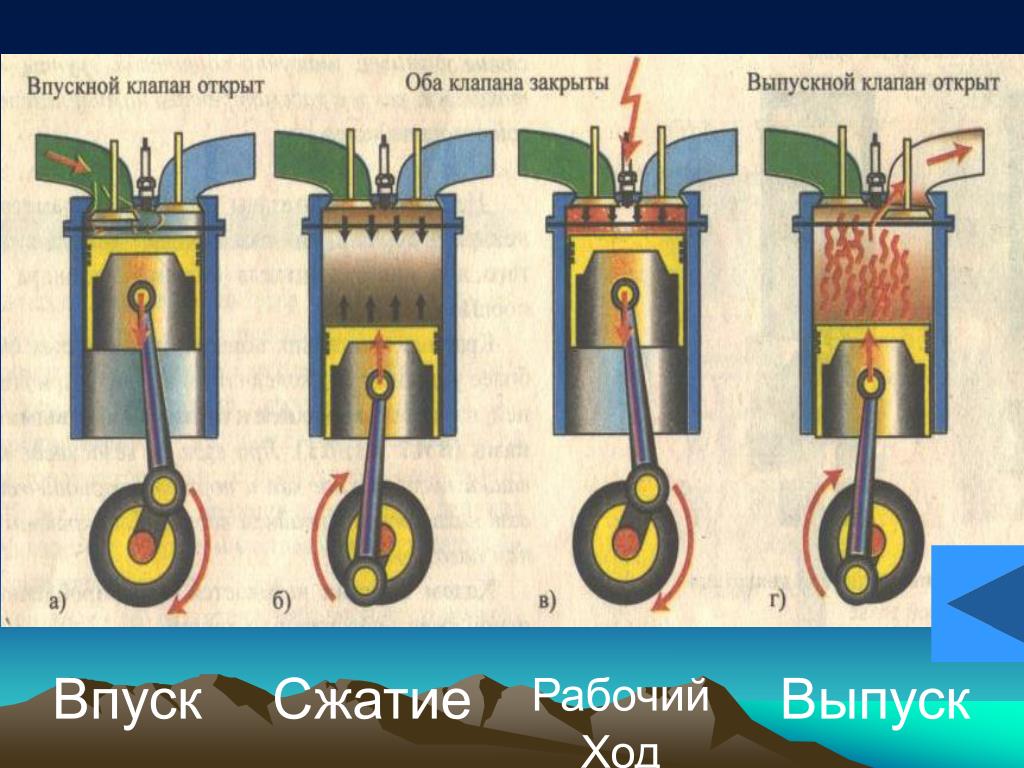
19. Руководство по ремонту двигателей Caterpillar [Электрон. ресурс] www.truckmanualshub.com/caterpillar- workshop-manuals-pdf (дата обращения 21.06.2019).
20. Кулманаков С.П., Кулманаков С.С. Тепловой расчет ДВС. Барнаул: Изд-во АлтГТУ, 2014.
21. Шароглазов Б.А., Шишков В.В. Поршневые двигатели: теория, моделирование и расчет процессов. Челябинск: Издат. центр ЮУрГУ, 2011.
22. Ситтинг М. Процессы окисления углеводородного сырья. М.: Химия, 1970.
23. Калимуллин Р.Ф., Горбачев С.В., Филиппов А.А. Тепловой расчет автомобильных газовых двигателей: методические указания к курсовому проектированию. Оренбург: Изд-во ГОУ ОГУ, 2007.
—
Для цитирования: Губарев В.Я., Спасибин А.Ю. Моделирование работы двигателя внутреннего сгорания на конвертерном газе // Вест- ник МЭИ. 2019. № 6. С. 50—57. DOI: 10.24160/1993-6982-2019-6-50-57.
#
1. Kurzanov S.Yu. Povyshenie Energeticheskoy Effektivnosti Staleplavil’nogo Proizvodstva na Osnove Ispol’zovaniya Konverternykh Gazov: Avtoref.
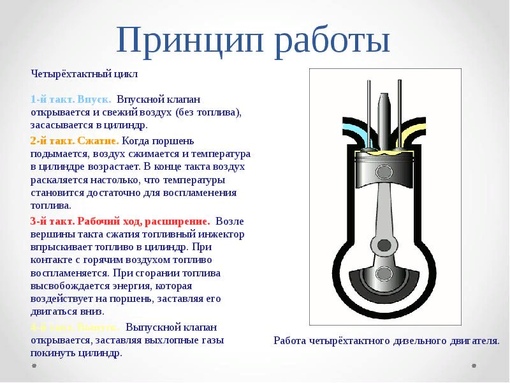
2. Lotosh V.E. Utilizatsiya Vtorichnykh Energeticheskikh Resursov. Resursosberegayushchie Tekhnologii. 2003;9:3—18. (in Russian).
3. Agapitov E.B., Maksimov A.A. Razrabotka Skhemy Kombinirovannogo Proizvodstva Gazoobraznogo Topliva na Osnove Konverternogo Gaza s Tsel’yu Sberezheniya Energeticheskikh Resursov Metallurgicheskogo Proizvodstva. Voprosy Tekhnicheskikh Nauk: Novye Podkhody V Reshenii Aktual’nykh Problem: Sbornik Nauch. Trudov Mezhdunar. Nauch.-prakt. Konf. Kazan’, 2014. (in Russian).
5. Rasshchupkin V.P., Korytov M.S. Proizvodstvo Stali. Metodika Vyplavki. Omsk: SibADI, 2007. (in Russian).
6. Linchevskiy B.V., Sobolevskiy A.

7. Larionov L.B., Buraev M.K. Raschet Protsessa Sgoraniya Biogaza v Gazovom Dvigatele s Iskrovym Zazhiganiem, Konvertirovannogo iz Dizelya s Nadduvom. Vestnik SVFU. 2015;12;1:52—58. (in Russian).
8. Kartashevich A.N., Malyshkin P.Yu., Plotnikov S.A., Zubakin A.S. Issledovaniya Raboty Dvigatelya na Al’ternativnykh Toplivakh. Vestnik Belorusskoy Gos. Sel’skokhozyaystvennoy Akademii. 2016;4:115—117 (in Russian).
9. Levterov A.M., Levterova L.I., Gladkova N.Yu. Ispol’zovanie Al’ternativnykh Topliv v Transportnykh DVS. Avtomobil’nyy transport. 2010;27:61—64. (in Russian).
10. Evropeyskiy Opyt Utilizatsii Sbrosnogo Energopotentsiala Promyshlennykh Gazov [Elektron. Resurs] www.cogeneration.com.ua/ru/analytics/special-gas/hydrogen-utilization (Data Obrashcheniya 21.06.2019). (in Russian).
11. Mysnik M.I., Svistula A.E. Analiz Teplofizicheskikh Svoystv Al’ternativnykh Topliv Dlya Dvigateley Vnutrennego Sgoraniya.

12. Gichev Yu.A. Proektno-konstruktorskie Resheniya po Ispol’zovaniyu Konverternogo Gaza dlya Nagreva Metalloloma. Sovremennaya Nauka: Issledovaniya, Idei, Rezul’taty, Tekhnologii. 2013;5:54—59. (in Russian).
13. Kuzemko R.D., Sushchenko A.V. Uluchshenie Teplovogo Balansa Konverternoy Plavki za Schet Regeniratsii Teploty Otkhodyashchikh Gazov. Vestnik Priazovskogo Gos. Tekhn. Un-ta. Seriya «Tekhnicheskie Nauki». 1998;6:62—69. (in Russian).
14. Gichev Yu.A., Zapototskaya A.Yu. Tekhnicheskie Resheniya i Effektivnost’ Ispol’zovaniya Konverternogo Gaza dlya Obzhiga Izvestnyaka. Mezhdunarodnye Konferentsii: Lit’e, Metallurgiya. Zaporozh’e: Zaporozhskaya Torgovo-promyshlennaya Palata, 2015. (in Russian).
15. Maksimov A.A., Agapitov E.B. Sovershenstvovanie Energoeffektivnoy Skhemy Utilizatsii Konverternogo Gaza. Teplotekhnika i Informatika v Obrazovanii, Nauke i Proizvodstve: Sbornik Dokl. IV Vseros.
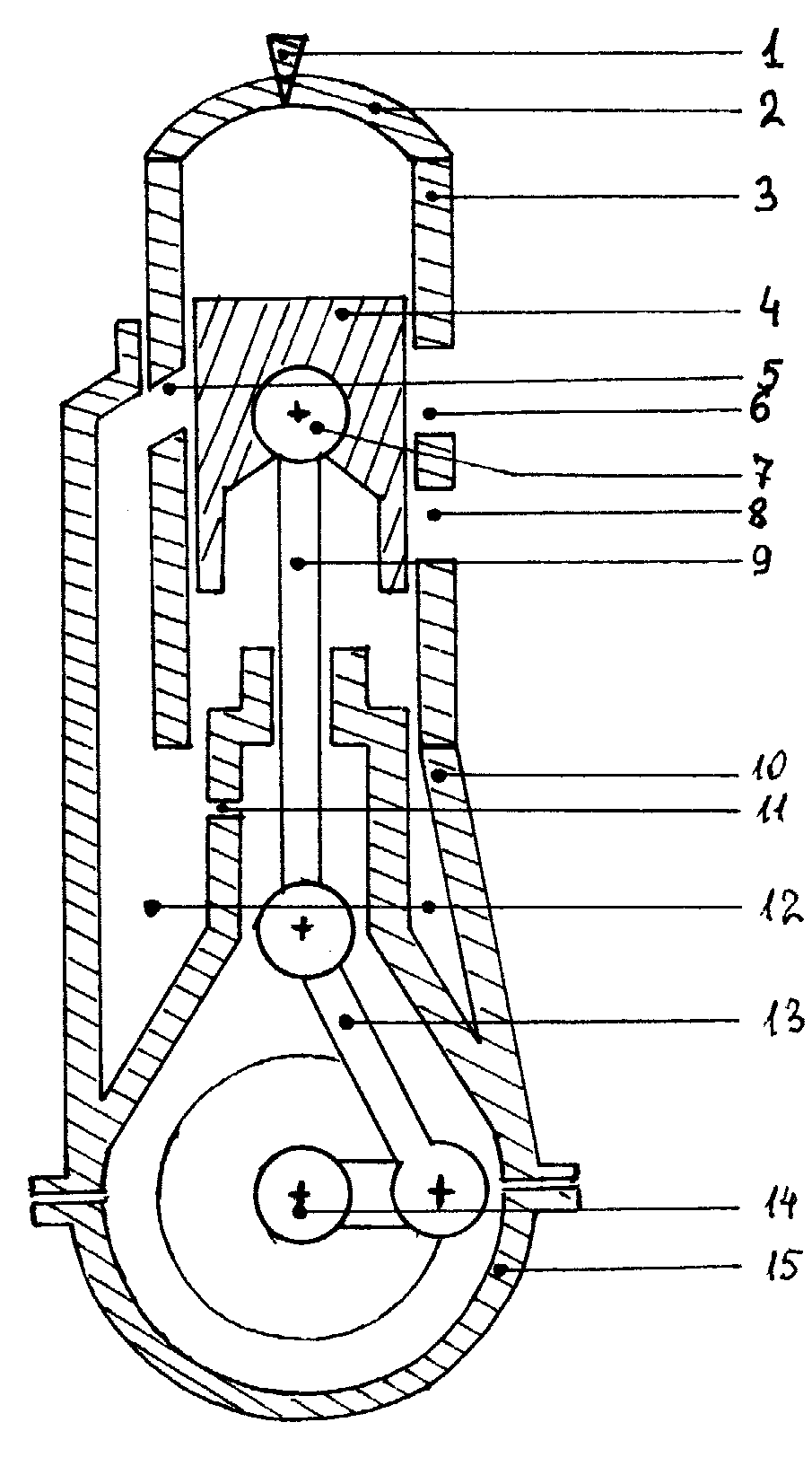
16. Dremov A.N., Gridin S.V. Ispol’zovanie Gazov Staleplavil’nykh Konverterov v Kachestve Vtorichnykh Energoresursov. Metallurgiya XXI Stoletiya Glazami Molodykh: Sbornik Dokl. Vseukr. Nauch.-prakt. Konf. Studentov. Donetsk: Izd-vo DonNTU, 2013:143—144. (in Russian).
17. Stalinskiy D.V. i dr. Puti Povysheniya Effektivnogo Ispol’zovaniya Vtorichnykh Energoresursov (Toplivnykh Gazov) Metallurgicheskogo Proizvodstva. Ekologiya i Promyshlennost’. 2010;3:71—75. (in Russian).
18. Baptizmaiskiy V.I., Medzhibozhskiy M.Ya., Okhotskiy V.B. Konverternye Protsessy Proizvodstva Stali. Teoriya, Tekhnologiya, Konstruktsii Agregatov. Kiev: Vysshaya Shkola, 1984. (in Russian).

20. Kulmanakov S.P., Kulmanakov S.S. Teplovoy Raschet DVS. Barnaul: Izd-vo AltGTU, 2014. (in Russian).
21. Sharoglazov B.A., Shishkov V.V. Porshnevye Dvigateli: Teoriya, Modelirovanie i Raschet Protsessov. Chelyabinsk: Izdat. Tsentr YUUrGU, 2011. (in Russian).
22. Sitting M. Protsessy okisleniya uglevodorodnogo syr’ya. M.: Khimiya, 1970. (in Russian).
23. Kalimullin R.F., Gorbachev S.V., Filippov A.A. Teplovoy Raschet Avtomobil’nykh Gazovykh Dvigateley: Metodicheskie Ukazaniya k Kursovomu Proektirovaniyu. Orenburg: Izd-vo GOU OGU, 2007. (in Russian).
—
For citation: Gubarev V.Ya., Spasibin A.Yu. Simulating the Operation of an Internal Combustion Engine on Converter Waste Gas. Bulletin of MPEI. 2019;6:50—57. (in Russian). DOI: 10.24160/1993-6982-2019-6-50-57.
Короткий ход поршня
Рудольф Дизель родился 18 марта 1858 года в семье Теодора Дизеля и Элис Штробель — эмигрантов из Германии, осевших во Франции и владевших небольшой переплетной мастерской в Париже. С самого раннего детства у Рудольфа проявился интерес к разным машинам и механизмам: излюбленным времяпровождением умного, послушного, аккуратного и трудолюбивого мальчика было посещение парижского Музея искусств и ремесел.
В 1870 году началась Франко-прусская война, и из-за роста антинемецких настроений Дизелям пришлось перебраться в Англию, где вскоре они оказались в нищете. На семейном совете было принято решение отправить Рудольфа в Германию, в семью брата, любезно согласившуюся принять племянника. Дядя Дизеля был профессором и преподавал математику в Королевском земском училище, куда в 1871 году пристроил и Рудольфа, заметив у того склонность к технике, а уже в 1873-м юноша его успешно закончил, опередив по успеваемости всех остальных учеников.
Уже в 12 лет Рудольф испытывал склонность к технике
Иллюстрация: mandieselturbo.com
Затем Рудольф отправляется в Аугсбург, в Техническую школу, а через два года досрочно поступает в престижный Королевский баварский политехнический институт в Мюнхене. Во время учебы произошла судьбоносная для Дизеля встреча — его заметил один из преподавателей, профессор Карл фон Линде, помимо научной работы занимавшийся коммерцией, а именно созданием холодильного оборудования. В 1880 году, когда Дизель окончил институт, Линде пригласил его на работу в свою компанию на должность директора парижского филиала. В наше время Linde — одна из крупнейших и авторитетнейших в мире химических компаний, инжиниринговое подразделение которой занимается строительством «под ключ» крупнотоннажных химических производств, в том числе заводов по сжижению природного газа.
«Инженер все может»
Так ответил студент Рудольф Дизель на вопрос директора Высшей технической школы в Мюнхене профессора Бауэрфайнда о возможности создать двигатель внутреннего сгорания, способный заменить паровой. Теперь амбициозному молодому человеку предстояло доказать это на практике.
К концу XIX века в мире существовало множество поршневых двигателей, однако их КПД не превышал 10–12%, поскольку воспламенение горючей смеси в них производилось либо при помощи электричества, либо за счет тепла, идущего от стенок камеры сгорания. Однако уже в 1824 году французский инженер Сати Карнопредложил более перспективную схему работы двигателя. По его мнению, следовало «сперва сжать воздух насосом, затем пропустить его через вполне замкнутую топку, вводя туда маленькими порциями топливо при помощи приспособления, легко осуществимого; затем заставить воздух выполнять работу в цилиндре с поршнем или в любом другом расширяющемся сосуде и, наконец, выбросить его в атмосферу…». Эта схема, получившая наименование «цикла Карно», стала эталоном цикла теплового двигателя. Ее и попытался на практике реализовать Рудольф Дизель.
Забегая вперед, надо сказать, что у него это получилось не в полной мере: в дизелевском варианте в цилиндре сжималась не топливная смесь, а воздух, причем до запредельных для того времени значений.
Двенадцать лет проб и ошибок
А пока в течение десяти лет, с 1880-го по 1892-й, работая на фирме Линде, он постоянно занимался этим проектом, пытаясь найти такое рабочее тело, которое при соединении с топливом, создавало бы необходимую для воспламенения температуру. В его качестве последовательно использовались аммиак, уголь и бензин, но все было безрезультатно.
Помогла случайность. Использование воздуха в пневматической зажигалке для прикуривания сигар натолкнуло Рудольфа на мысль, что таким рабочим телом может стать сжатый воздух. «Не могу сказать, — писал позже изобретатель, — когда именно возникла у меня эта мысль. В неустанной погоне за целью, в итоге бесконечных расчетов родилась наконец идея, наполнившая меня огромной радостью: нужно вместо аммиака взять сжатый горячий воздух, впрыснуть в него распыленное топливо и одновременно со сгоранием расширить его так, чтобы возможно больше тепла использовать для полезной работы».
Основываясь на этом, Дизель разработал новую схему двигателя, в котором воздух должен был быть сжат с такой силой, чтобы при его соединении с топливом возникшая смесь воспламенилась до температуры 600–650 °С и в цилиндр начало поступать уже готовое для работы двигателя топливо.
Есть прототип!
В 1892 году Рудольф покидает компанию Линде и организовывает собственное предприятие, на котором в течение четырех лет изготавливает несколько опытных образцов. В том же году он получает свой первый патент № 67207 «Рабочий процесс и способ конструирования двигателя внутреннего сгорания для машин», которым закрепил за собой право собственности на «рациональный тепловой двигатель», и издает книгу, в которой дает теоретическое обоснование созданной им конструкции такого двигателя. «Моя идея, — писал он семье в Мюнхен, — настолько опережает все, что создано в данной области до сих пор, что можно смело сказать: я первый в этом новом и наиважнейшем разделе техники на нашем маленьком земном шарике! Я иду впереди лучших умов человечества по обе стороны океана!»
В 1897 году с третьей попытки ему наконец удалось построить готовый к практическому использованию прототип. Современники вспоминали, что это «был двигатель высотой три метра, который развивал 172 об/мин имел диаметр единственного цилиндра 250 мм, ход поршня 400 мм и мощность от 17,8 до 19,8 л. с., расходуя при этом 258 г нефти на 1 л. с. в час. Термический КПД был у него 26,2%, намного выше, чем имели паровые машины». Кроме того, двигатель Дизеля работал на дешевых видах топлива вроде керосина и не имел системы зажигания.
Как удалось достичь такого очень высокого для того времени КПД? Главным образом за счет многократного увеличения давления сжатия с помощью специального компрессора — в двигателе англичанина Герберта Акройда-Стюарта, наиболее похожего по конструкции на дизелевский, оно равнялось шести атмосферам, а в устройстве Рудольфа достигало 36 атмосфер.
#image-kit_1496
В связи с этим неоднократно вставал вопрос: кто первый изобрел ДВС, Стюарт или Дизель? Известно, что основные признаки современного дизельного двигателя — непосредственный впрыск топлива (без применения сжатого воздуха) и компрессионное зажигание. В 1890 году Стюарт получил патент № 7146 «Усовершенствование в работе двигателей при помощи взрыва воспламеняемых паров или смеси газа с воздухом». Но этот патент был дан только на компрессионное зажигание, о применении сжатого воздуха для воспламенения смеси там речи не шло.
Спустя некоторое время Стюарт построил экспериментальный образец устройства, функционировавшего на бензине и проработавшего всего несколько часов. Дизель же патент на компрессионное зажигание получил только в 1892 году, но в отличие от Стюарта в его патент уже была включена идея о сжатом воздухе, которую позже, в 1897 году, он и воплотил. Так что если вести отсчет от идеи, то первенство в изобретении ДВС принадлежит, безусловно, Дизелю. А поскольку идею придумал он и он же построил реально работающий образец, то и сам двигатель стали называть по его фамилии. Топливо такого двигателя, состоит из керосиново-газойлевых фракций переработанной нефти и имеет высокую — 200–350 °С — температуру кипения, в дизельном двигателе оно самовоспламеняется при сильном сжатии. В бензиновом двигателе горючую смесь образуют бензин и воздух, она воспламеняется от искры зажигания.
Развитие изделия
Это был успех. На Всемирной выставке в Париже в 1900 году изделие Дизеля произвело фурор, началась массовая скупка лицензий на производство его двигателей. Однако в начале промышленного изготовления дизелевских двигателей возникли серьезные трудности: первые партии оказывались бракованными, часто ломались и выходили из строя, на многих заводах не было необходимого оборудования и рабочей силы нужной квалификации.
Постепенно болезни роста были преодолены, и двигатель Дизеля стал постепенно использоваться во многих сферах жизнедеятельности, связанных с техникой. А его изобретатель стал миллионером. Дизеля стали приглашать повсюду — во Францию, Швейцарию, Австрию, Бельгию, Россию, Америку… Особый интерес к нему был проявлен в России. Уже в 1898 году Людвиг Нобель, купив у Дизеля лицензию на двигатель, организовал его производство на своем заводе в Санкт-Петербурге (сейчас это известное на всю страну предприятие «Русский дизель»).
Устройство быстро завоевало популярность и стало использоваться всюду — на электростанциях, водонапорном оборудовании, с его помощью освещались крупные магазины и центральные улицы Санкт-Петербурга и других известных городов Российской империи.
Велись работы по его модификации. Известный русский инженер Вадим Аршаулов создал так называемый русский дизель, который, в отличие от своего прототипа, работал на нефти, а не на керосине, и имел топливный насос высокого давления, работавший от сжатого в цилиндре воздуха. На Путиловском заводе инженер Густав Тринклер построил «Тринклер-мотор», который отличался от дизелевского варианта тем, что не имел воздушного компрессора для накачки воздуха, его роль играла гидравлическая система для нагнетания и впрыска топлива.
Дизеля наконец-таки признали и на родине: сам кайзер Вильгельм II вручил ему диплом о присвоении почетного звания доктора-инженера и пригласил в оборонные проекты. Занялся Дизель и совершенствованием конструкции реверсивного судового четырехтактного мотора и созданием двигателя для грузовых автомобилей.
Закат
Дизель жил на широкую ногу. Построил в Мюнхене дворец стоимостью 900 тысяч марок, покупал нефтяные участки в Баварии, где, как выяснялось потом, не было нефти, широко и необдуманно спекулировал акциями, вкладывал деньги в католические лотереи. В итоге финансовые дела стали настолько плохи, что, как пишут его биографы, «пришлось рассчитать почти всю прислугу и заложить дом».
Нервы Дизеля были издерганы постоянными нападками недоброжелателей и конкурентов, среди которых были как малоизвестные инженеры, так и могущественные люди вроде угольных и нефтяных магнатов, постоянно таскавшие его по судам по обвинениям в плагиате и других неблаговидных поступках.
Характерный пример — намерение его ярого противника профессора Людерса издать книгу под названием «Миф Дизеля», пытаясь доказать, что ничего нового в его изобретении нет, поскольку основа работы его двигателя была известна и раньше, а сам Дизель присвоил себе чужие заслуги.
Третьи вспоминали «нобелевскую» историю: незадолго до своей смерти, изобретатель обратился с письмом к председателю Нобелевского комитета Эммануилу Нобелю, в котором намекал на возможность получения Нобелевской премии за свое изобретение, рассчитывая, таким образом, поправить свои финансовые дела и заодно напомнив всем о себе. Но тот отказал. И это ввергло Дизеля в пучину черной депрессии.
К лету 1913 года Дизель стал полным банкротом и, по всей видимости, не видя другого выхода, решился на самоубийство. На это указывает его странное поведение: сначала он вместе с женой объехал всю Европу, как будто прощаясь с ней. Когда он погиб, его жена вспомнила странную фразу, которую он как-то обронил: «Мы можем попрощаться с этими местами. Больше мы их никогда не увидим». Затем он поехал в Баварские Альпы, где участвовал в опасных горных путешествиях и рискованных мероприятиях.
29 сентября 1913 года, в Антверпене 55-летний Рудольф Дизель и еще двое его друзей сели на паром «Дрезден», идущий в Англию, где он собирался работать инженером-консультантом на одном из двигателестроительных заводов. И ночью пропал. А через десять дней в Северном море рыбаки выловили труп. В одежде были найдены некоторые личные вещи, и сын Дизеля подтвердил, что они принадлежали его отцу.
Двигатель внутреннего сгорания — это… Что такое Двигатель внутреннего сгорания?
Дви́гатель вну́треннего сгора́ния (сокращённо ДВС) — это тип двигателя, тепловой машины, в которой химическая энергия топлива (обычно применяется жидкое или газообразное углеводородное топливо), сгорающего в рабочей зоне, преобразуется в механическую энергию.
Несмотря на то, что двигатель внутреннего сгорания относится к относительно несовершенному типу тепловых машин (громоздкость, сильный шум, токсичные выбросы и необходимость системы их отвода, относительно небольшой ресурс, необходимость охлаждения и смазки, высокая сложность в проектировании, изготовлении и обслуживании, сложная система зажигания, большое количество изнашиваемых частей, высокое потребление горючего и так далее), благодаря своей автономности (используемое топливо содержит гораздо больше энергии, чем лучшие электрические аккумуляторы), ДВС очень широко распространены, — например, на транспорте.
История создания
В 1799 году французский инженер Филипп Лебон открыл светильный газ. В 1799 году он получил патент на использование и способ получения светильного газа путём сухой перегонки древесины или угля, однако светильный газ годился не только для освещения.
В 1801 году Лебон взял патент на конструкцию газового двигателя. Принцип действия этой машины основывался на известном свойстве открытого им газа: его смесь с воздухом взрывалась при воспламенении с выделением большого количества теплоты. Продукты горения, стремительно расширяясь, оказывали сильное давление на окружающую среду — таким образом, оставалось только найти способ использования выделившейся энергии. В двигателе Лебона были предусмотрены два компрессора и камера смешивания. Один компрессор должен был накачивать в камеру сжатый воздух, а другой — сжатый светильный газ из газогенератора. Затем газовоздушная смесь поступала в рабочий цилиндр, где воспламенялась. Двигатель был двойного действия, то есть попеременно действовавшие рабочие камеры находились по обе стороны поршня. По существу, Лебон вынашивал мысль о двигателе внутреннего сгорания, однако в 1804 году он погиб, так и не успев воплотить в жизнь своё изобретение.
В последующие годы изобретатели из разных стран пытались создать работоспособный двигатель на светильном газе. Однако все эти попытки не привели к появлению на рынке двигателей, которые могли бы успешно конкурировать с паровой машиной.
Честь создания коммерчески успешного двигателя внутреннего сгорания принадлежит бельгийскому механику Жану Этьену Ленуару. Работая на гальваническом заводе, Ленуар пришёл к мысли, что топливовоздушную смесь в газовом двигателе можно воспламенять с помощью электрической искры, и решил построить двигатель на основе этой идеи. Решив возникшие по ходу проблемы (тугой ход и перегрев поршня, ведущий к заклиниванию) продумав систему охлаждения и смазки двигателя, Ленуар создал работоспособный двигатель внутреннего сгорания. В 1864 году было выпущено более трёхсот таких двигателей разной мощности. Разбогатев, Ленуар перестал работать над дальнейшим усовершенствованием своей машины, и это предопределило её судьбу — она была вытеснена с рынка более совершенным двигателем, созданным немецким изобретателем Августом Отто и получившим патент на изобретение своей модели газового двигателя в 1864 году.
В 1864 году немецкий изобретатель Августо Отто заключил договор с богатым инженером Лангеном для реализации своего изобретения — была создана фирма «Отто и Компания». Ни Отто, ни Ланген не владели достаточными знаниями в области электротехники и отказались от электрического зажигания. Воспламенение они осуществляли открытым пламенем через трубку. Цилиндр двигателя Отто, в отличие от двигателя Ленуара, был вертикальным. Вращаемый вал помещался над цилиндром сбоку. Принцип действия: вращающийся вал поднимал поршень на 1/10 высоты цилиндра, в результате чего под поршнем образовывалось разреженное пространство и происходило всасывание смеси воздуха и газа. Затем смесь воспламенялась. При взрыве давление под поршнем возрастало примерно до 4 атм. Под действием этого давления поршень поднимался, объём газа увеличивался и давление падало. Поршень сначала под давлением газа, а потом по инерции поднимался до тех пор, пока под ним не создавалось разрежение. Таким образом, энергия сгоревшего топлива использовалась в двигателе с максимальной полнотой. В этом заключалась главная оригинальная находка Отто. Рабочий ход поршня вниз начинался под действием атмосферного давления, и после того, как давление в цилиндре достигало атмосферного, открывался выпускной вентиль, и поршень своей массой вытеснял отработанные газы. Из-за более полного расширения продуктов сгорания КПД этого двигателя был значительно выше, чем КПД двигателя Ленуара и достигал 15 %, то есть превосходил КПД самых лучших паровых машин того времени. Кроме того, двигатели Отто были почти в пять раз экономичнее двигателей Ленуара, они сразу стали пользоваться большим спросом. В последующие годы их было выпущено около пяти тысяч штук. Несмотря на это, Отто упорно работал над усовершенствованием их конструкции. Вскоре была применена кривошипно-шатунная передача. Однако самое существенное из его изобретений было сделано в 1877 году, когда Отто получил патент на новый двигатель с четырёхтактным циклом. Этот цикл по сей день лежит в основе работы большинства газовых и бензиновых двигателей.
Типы двигателей внутреннего сгорания
Поршневой ДВС Роторный ДВС Газотурбинный ДВСДВС классифицируют:
а) По назначению — делятся на транспортные, стационарные и специальные.
б) По роду применяемого топлива — легкие жидкие (бензин, газ), тяжелые жидкие (дизельное топливо, судовые мазуты).
в) По способу образования горючей смеси — внешнее (карбюратор, инжектор) и внутреннее (в цилиндре ДВС).
г) По способу воспламенения (с принудительным зажиганием, с воспламенением от сжатия, калоризаторные).
д) По расположению цилиндров разделяют рядные, вертикальные, оппозитные с одним и с двумя коленвалами, V-образные с верхним и нижним расположением коленвала, VR-образные и W-образные, однорядные и двухрядные звездообразные, Н-образные, двухрядные с параллельными коленвалами, «двойной веер», ромбовидные, трехлучевые и некоторые другие.
Бензиновые
Бензиновые карбюраторные
Смесь топлива с воздухом готовится в карбюраторе, далее смесь подаётся в цилиндр, сжимается, а затем поджигается при помощи искры, проскакивающей между электродами свечи. Основная характерная особенность топливо-воздушной смеси в этом случае — гомогенность.
Бензиновые инжекторные
Также, существует способ смесеобразования путём впрыска бензина во впускной коллектор или непосредственно в цилиндр при помощи распыляющих форсунок (инжектор). Существуют системы одноточечного и распределённого впрыска различных механических и электронных систем. В механических системах впрыска дозация топлива осуществляется плунжерно — рычажным механизмом с возможностью электронной корректировки состава смеси. В электронных системах смесеобразование осуществляется под управлением электронного блока управления (ЭБУ), управляющим электрическими бензиновыми вентилями.
Дизельные, с воспламенением от сжатия
Дизельный двигатель характеризуется воспламенением топлива без использования свечи зажигания. В разогретый от сжатия воздух (до температуры, превышающей температуру воспламенения топлива) через форсунку впрыскивается порция топлива. В процессе впрыскивания топлива происходит его распыливание, а затем вокруг отдельных капель топлива возникают очаги сгорания. Т. к. дизельные двигатели не подвержены явлению детонации, характерному для двигателей с принудительным воспламенением, в них допустимо использование более высоких степеней сжатия (до 26), что благотворно сказывается на КПД данного типа двигателей, который может превышать 50% в случае с крупными судовыми двигателями.
Дизельные двигатели являются менее быстроходными и характеризуются большим крутящим моментом на валу. Дизельное топливо является более дешевым, нежели бензин. Также некоторые крупные дизельные двигатели приспособлены для работы на тяжелых топливах, например, мазутах. Запуск крупных дизельных двигателей осуществляется, как правило, за счет пневматической схемы с запасом сжатого воздуха, либо в случае с инверторными генераторными установками, от присоединенной электромашины, которая при обычной эксплуатации выполняет роль генератора.
Вопреки расхожему мнению, современные двигатели, традиционно называемые дизельными, работают не по циклу Дизеля, а по циклу Тринклера-Сабатэ со смешанным подводом теплоты.
Недостатки дизельных двигателей обусловлены особенностями рабочего цикла — более высокой механической напряженностью, требующей повышенной прочности конструкции и, как следствие, увеличения её габаритов, веса и увеличения стоимости за счёт усложнённой конструкции и использования более дорогих материалов. Также дизельные двигатели за счет гетерогенного сгорания характеризуются неизбежными выбросами сажи и повышенным содержанием оксидов азота в выхлопных газах.
Газовые
Двигатель, сжигающий в качестве топлива углеводороды, находящиеся в газообразном состоянии при нормальных условиях:
- смеси сжиженных газов — хранятся в баллоне под давлением насыщенных паров (до 16 атм). Испарённая в испарителе жидкая фаза или паровая фаза смеси ступенчато теряет давление в газовом редукторе до близкого атмосферному, и всасывается двигателем во впускной коллектор через воздушно-газовый смеситель или впрыскивается во впускной коллектор посредством электрических форсунок. Зажигание осуществляется при помощи искры, проскакивающей между электродами свечи.
- сжатые природные газы — хранятся в баллоне под давлением 150—200 атм. Устройство систем питания аналогично системам питания сжиженным газом, отличие — отсутствие испарителя.
- генераторный газ — газ, полученный превращением твёрдого топлива в газообразное. В качестве твёрдого топлива используются:
Газодизельные
Основная порция топлива приготавливается, как в одной из разновидностей газовых двигателей, но зажигается не электрической свечой, а запальной порцией дизтоплива, впрыскиваемого в цилиндр аналогично дизельному двигателю.
Роторно-поршневой
Предложен изобретателем Ванкелем в начале ХХ века. Основа двигателя — треугольный ротор (поршень), вращающийся в камере особой 8-образной формы, исполняющий функции поршня, коленвала и газораспределителя. Такая конструкция позволяет осуществить любой 4-тактный цикл Дизеля, Стирлинга или Отто без применения специального механизма газораспределения. За один оборот двигатель выполняет три полных рабочих цикла, что эквивалентно работе шестицилиндрового поршневого двигателя. Строился серийно фирмой НСУ в Германии (автомобиль RO-80), ВАЗом в СССР (ВАЗ-21018 «Жигули», ВАЗ-416, ВАЗ-426, ВАЗ-526), в настоящее время строится только Маздой (Mazda RX-8). При своей принципиальной простоте имеет ряд существенных конструктивных сложностей, делающих его широкое внедрение весьма затруднительным. Основные трудности связаны с созданием долговечных работоспособных уплотнений между ротором и камерой и с построением системы смазки.
В Германии в конце 70х годов ХХ века существовал анекдот: «Продам НСУ, дам в придачу два колеса, фару и 18 запасных моторов в хорошем состоянии».
- RCV — двигатель внутреннего сгорания, система газораспределения которого реализована за счёт движения поршня, который совершает возвратно-поступательные движения, попеременно проходя впускной и выпускной патрубок.
Комбинированный двигатель внутреннего сгорания
- — двигатель внутреннего сгорания, представляющий собой комбинацию из поршневой и лопаточной машин (турбина, компрессор), в котором обе машины в соотносимой мере участвуют в осуществлении рабочего процесса. Примером комбинированного ДВС служит поршневой двигатель с газотурбинным наддувом (турбонаддув). Большой вклад в теорию комбинированных двигателей внес советский инженер, профессор А. Н. Шелест.
Циклы работы поршневых ДВС
Двухтактный цикл Схема работы четырёхтактного двигателя, цикл Отто1. впуск
2. сжатие
3. рабочий ход
4. выпуск
Поршневые двигатели внутреннего сгорания классифицируются по количеству тактов в рабочем цикле на двухтактные и четырёхтактные.
Рабочий цикл четырёхтактных двигателей внутреннего сгорания занимает два полных оборота кривошипа, состоящий из четырёх отдельных тактов:
- впуска,
- сжатия заряда,
- рабочего хода и
- выпуска (выхлопа).
Изменение рабочих тактов обеспечивается специальным газораспределительным механизмом, чаще всего он представлен одним или двумя распределительными валами, системой толкателей и клапанами, непосредственно обеспечивающими смену фазы. Некоторые двигатели внутреннего сгорания использовали для этой цели золотниковые гильзы (Рикардо), имеющие впускные и/или выхлопные окна. Сообщение полости цилиндра с коллекторами в этом случае обеспечивалось радиальным и вращательным движениями золотниковой гильзы, окнами открывающей нужный канал. Ввиду особенностей газодинамики — инерционности газов, времени возникновения газового ветра такты впуска, рабочего хода и выпуска в реальном четырёхтактном цикле перекрываются, это называется перекрытием фаз газораспределения. Чем выше рабочие обороты двигателя, тем больше перекрытие фаз и чем оно больше, тем меньше крутящий момент двигателя внутреннего сгорания на низких оборотах. Поэтому в современных двигателях внутреннего сгорания всё шире используются устройства, позволяющие изменять фазы газораспределения в процессе работы. Особенно пригодны для этой цели двигатели с электромагнитным управлением клапанами (BMW, Mazda). Имеются также двигатели с переменной степенью сжатия (СААБ), обладающие большей гибкостью характеристики.
Двухтактные двигатели имеют множество вариантов компоновки и большое разнообразие конструктивных систем. Основной принцип любого двухтактного двигателя — исполнение поршнем функций элемента газораспределения. Рабочий цикл складывается, строго говоря, из трёх тактов: рабочего хода, длящегося от верхней мёртвой точки (ВМТ) до 20—30 градусов до нижней мёртвой точки (НМТ), продувки, фактически совмещающей впуск и выхлоп, и сжатия, длящегося от 20—30 градусов после НМТ до ВМТ. Продувка, с точки зрения газодинамики, слабое звено двухтактного цикла. С одной стороны, невозможно обеспечить полное разделение свежего заряда и выхлопных газов, поэтому неизбежны либо потери свежей смеси, буквально вылетающей в выхлопную трубу (если двигатель внутреннего сгорания — дизель, речь идёт о потере воздуха), с другой стороны, рабочий ход длится не половину оборота, а меньше, что само по себе снижает КПД. В то же время длительность чрезвычайно важного процесса газообмена, в четырёхтактном двигателе занимающего половину рабочего цикла, не может быть увеличена. Двухтактные двигатели могут вообще не иметь системы газораспределения. Однако, если речь не идёт об упрощённых дешёвых двигателях, двухтактный двигатель сложнее и дороже за счёт обязательного применения воздуходувки или системы наддува, повышенная теплонапряжённость ЦПГ требует более дорогих материалов для поршней, колец, втулок цилиндров. Исполнение поршнем функций элемента газораспределения обязывает иметь его высоту не менее ход поршня + высота продувочных окон, что некритично в мопеде, но существенно утяжеляет поршень уже при относительно небольших мощностях. Когда же мощность измеряется сотнями лошадиных сил, увеличение массы поршня становится очень серьёзным фактором. Введение распределительных гильз с вертикальным ходом в двигателях Рикардо было попыткой сделать возможным уменьшение габаритов и массы поршня. Система оказалась сложной и дорогой в исполнении, кроме авиации, такие двигатели нигде больше не использовались. Выхлопные клапаны (при прямоточной клапанной продувке) имеют вдвое большую теплонапряжённость в сравнении с выхлопными клапанами четырёхтактных двигателей и худшие условия для теплоотвода, а их сёдла имеют более длительный прямой контакт с выхлопными газами.
Самой простой с точки зрения порядка работы и самой сложной с точки зрения конструкции является система Фербенкс — Морзе, представленная в СССР и в России, в основном, тепловозными дизелями серий Д100. Такой двигатель представляет собой симметричную двухвальную систему с расходящимися поршнями, каждый из которых связан со своим коленвалом. Таким образом, этот двигатель имеет два коленвала, механически синхронизированные; тот, который связан с выхлопными поршнями, опережает впускной на 20—30 градусов. За счёт этого опережения улучшается качество продувки, которая в этом случае является прямоточной, и улучшается наполнение цилиндра, так как в конце продувки выхлопные окна уже закрыты. В 30х — 40х годах ХХ века были предложены схемы с парами расходящихся поршней — ромбовидная, треугольная; существовали авиационные дизели с тремя звездообразно расходящимися поршнями, из которых два были впускными и один — выхлопным. В 20-х годах Юнкерс предложил одновальную систему с длинными шатунами, связанными с пальцами верхних поршней специальными коромыслами; верхний поршень передавал усилия на коленвал парой длинных шатунов, и на один цилиндр приходилось три колена вала. На коромыслах стояли также квадратные поршни продувочных полостей. Двухтактные двигатели с расходящимися поршнями любой системы имеют, в основном, два недостатка: во-первых, они весьма сложны и габаритны, во-вторых, выхлопные поршни и гильзы в зоне выхлопных окон имеют значительную температурную напряжённость и склонность к перегреву. Кольца выхлопных поршней также являются термически нагруженными, склонны к закоксовыванию и потере упругости. Эти особенности делают конструктивное исполнение таких двигателей нетривиальной задачей.
Двигатели с прямоточной клапанной продувкой оснащены распределительным валом и выхлопными клапанами. Это значительно снижает требования к материалам и исполнению ЦПГ. Впуск осуществляется через окна в гильзе цилиндра, открываемые поршнем. Именно так компонуется большинство современных двухтактных дизелей. Зона окон и гильза в нижней части во многих случаях охлаждаются наддувочным воздухом.
В случаях, когда одним из основных требований к двигателю является его удешевление, используются разные виды кривошипно-камерной контурной оконно-оконной продувки — петлевая, возвратно-петлевая (дефлекторная) в разнообразных модификациях. Для улучшения параметров двигателя применяются разнообразные конструктивные приёмы — изменяемая длина впускного и выхлопного каналов, может варьироваться количество и расположение перепускных каналов, используются золотники, вращающиеся отсекатели газов, гильзы и шторки, изменяющие высоту окон (и, соответственно, моменты начала впуска и выхлопа). Большинство таких двигателей имеет воздушное пассивное охлаждение. Их недостатки — относительно невысокое качество газообмена и потери горючей смеси при продувке, при наличии нескольких цилиндров секции кривошипных камер приходится разделять и герметизировать, усложняется и удорожается конструкция коленвала.
Дополнительные агрегаты, требующиеся для ДВС
Недостатком двигателя внутреннего сгорания является то, что он развивает наивысшую мощность только в узком диапазоне оборотов. Поэтому неотъемлемым атрибутом двигателя внутреннего сгорания является трансмиссия. Лишь в отдельных случаях (например, в самолётах) можно обойтись без сложной трансмиссии. Постепенно завоёвывает мир идея гибридного автомобиля, в котором мотор всегда работает в оптимальном режиме.
Кроме того, двигателю внутреннего сгорания необходимы система питания (для подачи топлива и воздуха — приготовления топливо-воздушной смеси), выхлопная система (для отвода выхлопных газов), также не обойтись без системы смазки(предназначена для уменьшения сил трения в механизмах двигателя, защиты деталей двигателя от коррозии, а также совместно с системой охлаждения для поддержания оптимального теплового режима), системы охлаждения(для поддержания оптимального теплового режима двигателя), система запуска (применяются способы запуска: электростартерный, с помощью вспомогательного пускового двигателя, пневматический, с помощью мускульной силы человека), система зажигания (для воспламениня топливо-воздушной смеси, применяется у двигателей с принудительным воспламенением).
См. также
Примечания
Ссылки
Двигатели с изменяемой степенью сжатия: от Saab до Infiniti
Все чаще звучат авторитетные мнения, что сейчас развитие двигателей внутреннего сгорания достигло наивысшего уровня и больше невозможно заметно улучшить их характеристики. Конструкторам остается заниматься ползучей модернизацией, шлифуя системы наддува и впрыска, а также добавляя все больше электроники. С этим не соглашаются японские инженеры. Свое слово сказала компания Infiniti, которая построила двигатель с изменяемой степенью сжатия. Разбираемся, в чем преимущества такого мотора, и какое у него будущее.
В качестве вступления напомним, что степенью сжатия называют отношение объема над поршнем, находящимся в нижней «мертвой» точке, к объему, когда поршень находится в верхней.
Компоненты / Новости
Для бензиновых двигателей этот показатель составляет от 8 до 14, для дизелей — от 18 до 23.
Степень сжатия задается конструкцией фиксировано. Рассчитывается она в зависимости от октанового числа применяемого бензина и наличия наддува.
Возможность динамически изменять степень сжатия в зависимости от нагрузки позволяет поднять КПД турбированного мотора, добившись того, чтобы каждая порция топливовоздушной смеси сгорала при оптимальном сжатии.
При малых нагрузках, когда смесь обедненная, используется максимальное сжатие, а в нагруженном режиме, когда бензина впрыскивается много и возможна детонация, мотор сжимает смесь минимально.
Это позволяет не регулировать «назад» угол опережения зажигания, который остается в наиболее эффективной позиции для снятия мощности. Теоретически система изменения степени сжатия в ДВС позволяет до двух раз уменьшить рабочий объем мотора при сохранении тяговых и динамических характеристик.
Схема двигателя с изменяемым объемом камеры сгорания и шатуны с системой подъема поршней
Одной из первых появилась система с дополнительным поршнем в камере сгорания, который перемещаясь, изменял ее объем. Но сразу возник вопрос о размещении еще одной группы деталей в головке блока, где уже и так теснились распредвалы, клапаны, инжекторы и свечи зажигания. Притом нарушалась оптимальная конфигурация камеры сгорания, отчего топливо сжигалось неравномерно. Поэтому система так и осталась в стенах лабораторий. Не пошла дальше эксперимента и система с поршнями изменяемой высоты. Разрезные поршни были чрезмерно тяжелыми, притом сразу возникли конструктивные трудности с управлением высотой подъема крышки.
Система подъема коленвала на эксцентриковых муфтах FEV Motorentechnik (слева) и траверсный механизм для изменения высоты подъема поршня
Другие конструкторы пошли путем управления высотой подъема коленвала. В этой системе опорные шейки коленвала размещены в эксцентриковых муфтах, приводимых в действие через шестерни электромотором. Когда эксцентрики поворачиваются, коленвал поднимается или опускается, отчего, соответственно, меняется высота подъема поршней к головке блока, увеличивается или уменьшается объем камеры сгорания, и изменяется тем самым степень сжатия. Такой мотор показала в 2000 году немецкая компания FEV Motorentechnik. Система была интегрирована в турбированный четырехцилиндровый двигатель 1.8 л от концерна Volkswagen, где варьировала степень сжатия от 8 до 16. Мотор развивал мощность 218 л.с. и крутящий момент 300 Нм. До 2003 года двигатель испытывался на автомобиле Audi A6, но в серию не пошел.
Не слишком удачливой оказалась и обратная система, также изменяющая высоту подъема поршней, но не за счет управления коленвалом, а путем подъема блока цилиндров. Действующий мотор подобной конструкции продемонстрировал в 2000 году Saab, и также тестировал его на модели 9-5, планируя запустить в серийное производство. Получивший название Saab Variable Compression (SVC) пятицилиндровый турбированный двигатель объемом 1,6 л, развивал мощность 225 л. с. и крутящий момент 305 Нм, при этом расход топлива при средних нагрузках снизился на 30%, а за счет регулируемой степени сжатия мотор мог без проблем потреблять любой бензин — от А-80 до А-98.
Система двигателя Saab Variable Compression, в которой степень сжатия изменяется за счет отклонения верхней части блока цилиндров
Задачу подъема блока цилиндров в Saab решили так: блок был разделен на две части — верхнюю с головкой и гильзами цилиндров, и нижнюю, где остался коленвал. Одной стороной верхняя часть была связана с нижней через шарнир, а на другой был установлен механизм с электроприводом, который, как крышку у сундука, приподнимал верхнюю часть на угол до 4 градусов. Диапазон степени сжатия при поднимании — опускании мог гибко варьироваться от 8 до 14. Для герметизации подвижной и неподвижной частей служил эластичный резиновый кожух, который оказался одним из самых слабых мест конструкции, вместе с шарнирами и подъемным механизмом. После приобретения Saab корпорацией General Motors американцы закрыли проект.
Проект МСЕ-5 в котором применен механизм с рабочим и управляющим поршнями, связаными через зубчатое коромысло
На рубеже веков свою конструкцию мотора с изменяемой степенью сжатия предложили и французские инженеры компании MCE-5 Development S.A. Показанный ими турбированный 1.5-литровый мотор, в котором степень сжатия могла варьироваться от 7 до 18, развивал мощность 220 л. с. и крутящий момент 420 Нм. Конструкция тут довольно сложная. Шатун разделен и снабжен наверху (в части, устанавливаемой на коленвал) зубчатым коромыслом. К нему примыкает другая часть шатуна от поршня, оконечник которой имеет зубчатую рейку. С другой стороной коромысла связана рейка управляющего поршня, приводимого в действие через систему смазки двигателя посредством специальных клапанов, каналов и электропривода. Когда управляющий поршень перемещается, он воздействует на коромысло и высота поднятия рабочего поршня изменяется. Двигатель экспериментально обкатывался на Peugeot 407, но автопроизводитель не заинтересовался данной системой.
Теперь свое слово решили сказать конструкторы Infiniti, представив двигатель с технологией Variable Compression-Turbocharged (VC-T), позволяющей динамически изменять степень сжатия от 8 до 14. Японские инженеры применили траверсный механизм: сделали подвижное сочленение шатуна с его нижней шейкой, которую, в свою очередь, связали системой рычагов с приводом от электромотора. Получив команду от блока управления, электродвигатель перемещает тягу, система рычагов меняет положение, регулируя тем самым высоту подъема поршня и, соответственно, изменяя степень сжатия.
Конструкция системы Variable Compression у мотора Infiniti VC-T: а - поршень, b - шатун, с - траверса, d - коленвал, е - электродвигатель, f - промежуточный вал, g - тяга.
За счет данной технологии двухлитровый бензиновый турбомотор Infiniti VC-T развивает мощность 270 л.с., оказываясь на 27% экономичнее других двухлитровых двигателей компании, имеющих постоянную степень сжатия. Японцы планируют запустить моторы VC-T в серийное производство в 2018 году, оснастив ими кроссовер QX50, а затем и другие модели.
Заметим, что именно экономичность выступает сейчас основной целью разработки моторов с изменяемой степенью сжатия. При современном развитии технологий наддува и впрыска, нагнать мощности в моторе для конструкторов не составляет больших проблем. Другой вопрос: сколько бензина в супернадутом двигателе будет вылетать в трубу? Для обычных серийных моторов показатели расхода могут оказаться неприемлемы, что и выступает ограничителем для надувания мощности. Японские конструкторы решили этот барьер преодолеть. Как считают в компании Infiniti, их бензиновый двигатель VC-T, способен выступить как альтернатива современным турбированным дизелям, показывая тот же расход топлива при лучших характеристиках по мощности и более низкой токсичности выхлопа.
Каков итог?
Работы над двигателями с изменяемой степенью сжатия ведутся уже не один десяток лет — этим направлением занимались конструкторы Ford, Mercedes-Benz, Nissan, Peugeot и Volkswagen. Инженерами исследовательских институтов и компаний по обе стороны Атлантики получены тысячи патентов. Но пока ни один такой мотор не пошел в серийное производство.
Не все гладко и у Infiniti. Как признаются сами разработчики мотора VC-T, у их детища пока остаются общие проблемы: возросла сложность и стоимость конструкции, не решены вопросы с вибрацией. Но японцы надеются доработать конструкцию и запустить ее в серийное производство. Если это произойдет, то будущим покупателям осталось только понять: сколько придется переплатить за новую технологию, насколько такой мотор будет надежен и сколько позволит экономить на топливе.
Устройство двигателя внутреннего сгорания
Автор admin На чтение 6 мин. Просмотров 181
Двигатель внутреннего сгорания – универсальный силовой агрегат, используемый практически во всех видах современного транспорта. Три луча заключенные в окружность, слова «На земле, на воде и в небе» — товарный знак и девиз компании Мерседес Бенц, одного из ведущих производителей дизельных и бензиновых двигателей. Устройство двигателя, история его создания, основные виды и перспективы развития – вот краткое содержание данного материала.
Немного истории
Принцип превращения возвратно-поступательного движения во вращательное, посредством использования кривошипно-шатунного механизма известен с 1769 года, когда француз Николя Жозеф Кюньо показал миру первый паровой автомобиль. В качестве рабочего тела двигатель использовал водяной пар, был маломощным и извергал клубы черного, дурнопахнущего дыма. Подобные агрегаты использовались в качестве силовых установок на заводах, фабриках, пароходах и поездах, компактные же модели существовали в виде технического курьеза.
Все изменилось в тот момент, когда в поисках новых источников энергии человечество обратило свой взор на органическую жидкость — нефть. В стремлении повысить энергетические характеристики данного продукта, ученные и исследователи, проводя опыты по перегонке и дистилляции, получили неизвестное доселе вещество – бензин. Эта прозрачная жидкость с желтоватым оттенком сгорала без образования копоти и сажи, выделяя намного большее, чем сырая нефть, количество тепловой энергии.
Примерно в то же время Этьен Ленуар сконструировал первый газовый двигатель внутреннего сгорания, работавший по двухтактной схеме, и запатентовал его в 1880 году.
В 1885 году немецкий инженер Готтлиб Даймлер, в сотрудничестве с предпринимателем Вильгельмом Майбахом, разработал компактный бензиновый двигатель, уже через год нашедший свое применение в первых моделях автомобилей. Рудольф Дизель, работая в направлении повышения эффективности ДВС (двигателя внутреннего сгорания), в 1897 году предложил принципиально новую схему воспламенения топлива. Воспламенение в двигателе, названном в честь великого конструктора и изобретателя, происходит за счет нагревания рабочего тела при сжатии.
А в 1903 году братья Райт подняли в воздух свой первый самолет, оснащенный бензиновым двигателем Райт-Тейлор, с примитивной инжекторной схемой подачи топлива.
Как это работает
Общее устройство двигателя и основные принципы его работы станут понятны при изучении одноцилиндровой двухтактной модели.
Такой ДВС состоит из:
- камеры сгорания;
- поршня, соединенного с коленвалом посредством кривошипно-шатунного механизма;
- системы подачи и воспламенения топливно-воздушной смеси;
- клапана для удаления продуктов горения (выхлопных газов).
При пуске двигателя поршень начинает путь от верхней мертвой точки (ВМТ) к нижней (НМТ), за счет поворота коленвала. Достигнув нижней точки, он меняет направление движения к ВМТ, одновременно с чем проводится подача топливно-воздушной смеси в камеру сгорания. Движущийся поршень сжимает ТВС, при достижении верхней мертвой точки система электронного зажигания воспламеняет смесь. Стремительно расширяясь, горящие пары бензина отбрасывают поршень в нижнюю мертвую точку. Пройдя определенную часть пути, он открывает выхлопной клапан, через который раскаленные газы покидают камеру сгорания. Пройдя нижнюю точку, поршень меняет направление движения к ВМТ. За это время коленвал совершил один оборот.
Данные пояснения станут более понятными при просмотре видео о работе двигателя внутреннего сгорания.
Два такта
Основным недостатком двухтактной схемы, в которой роль газораспределительного элемента играет поршень, является потеря рабочего вещества в момент удаления выхлопных газов. А система принудительной продувки и повышенные требования к термостойкости выхлопного клапана приводят к увеличению цены двигателя. В противном случае добиться высокой мощности и долговечности силового агрегата не представляется возможным. Основная сфера применения подобных двигателей – мопеды и недорогие мотоциклы, лодочные моторы и бензокосилки.
Четыре такта
Описанных недостатков лишены четырехтактные ДВС, используемые в более «серьезной» технике. Каждая фаза работы такого двигателя (впуск смеси, ее сжатие, рабочий ход и выпуск отработанных газов), осуществляется при помощи газораспределительного механизма.
Разделение фаз работы ДВС очень условно. Инерционность отработавших газов, возникновение локальных вихрей и обратных потоков в зоне выхлопного клапана приводит к взаимному перекрыванию во времени процессов впрыска топливной смеси и удаления продуктов горения. Как результат, рабочее тело в камере сгорания загрязняется отработанными газами, вследствие чего меняются параметры горения ТВС, уменьшается теплоотдача, падает мощность.
Проблема была успешно решена путем механической синхронизации работы впускных и выпускных клапанов с оборотами коленвала. Проще говоря, впрыск топливно-воздушной смеси в камеру сгорания произойдет только после полного удаления отработанных газов и закрытия выхлопного клапана.
Но данная система управления газораспределением так же имеет свои недостатки. Оптимальный режим работы двигателя (минимальный расход топлива и максимальная мощность), может быть достигнут в достаточно узком диапазоне оборотов коленвала.
Развитие вычислительной техники и внедрение электронных блоков управления дало возможность успешно разрешить и эту задачу. Система электромагнитного управления работой клапанов ДВС позволяет на лету, в зависимости от режима работы, выбирать оптимальный режим газораспределения. Анимированные схемы и специализированные видео облегчат понимание этого процесса.
На основании видео не сложно сделать вывод, что современный автомобиль это огромное количество всевозможных датчиков.
Виды ДВС
Общее устройство двигателя остается неизменным достаточно долгое время. Основные различия касаются видов используемого топлива, систем приготовления топливно-воздушной смеси и схем ее воспламенения.
Рассмотрим три основных типа:
- бензиновые карбюраторные;
- бензиновые инжекторные;
- дизельные.
Бензиновые карбюраторные ДВС
Приготовление гомогенной (однородной по своему составу), топливно-воздушной смеси происходит путем распыления жидкого топлива в воздушном потоке, интенсивность которого регулируется степенью поворота дроссельной заслонки. Все операции по приготовлению смеси проводятся за пределами камеры сгорания двигателя. Преимуществами карбюраторного двигателя является возможность регулировки состава топливной смеси «на коленке», простота обслуживания и ремонта, относительная дешевизна конструкции. Основной недостаток – повышенный расход топлива.
Историческая справка. Первый двигатель данного типа сконструировал и запатентовал в 1888 году российский изобретатель Огнеслав Костович. Оппозитная система горизонтально расположенных и двигающихся навстречу друг другу поршней, до сих пор успешно используется при создании двигателей внутреннего сгорания. Самым известным автомобилем, в котором использовался ДВС данной конструкции, является Фольксваген Жук.
Бензиновые инжекторные ДВС
Приготовление ТВС осуществляется в камере сгорания двигателя, путем распыления топлива инжекторными форсунками. Управление впрыском осуществляется электронным блоком или бортовым компьютером автомобиля. Мгновенная реакция управляющей системы на изменение режима работы двигателя обеспечивает стабильность работы и оптимальный расход топлива. Недостатком считается сложность конструкции, профилактика и наладка возможны только на специализированных станциях технического обслуживания.
Дизельные ДВС
Приготовление топливно-воздушной смеси происходит непосредственно в камере сгорания двигателя. По окончании цикла сжатия воздуха, находящегося в цилиндре, форсунка проводит впрыск топлива. Воспламенение происходит за счет контакта с перегретым в процессе сжатия атмосферным воздухом. Всего лишь 20 лет назад низкооборотистые дизеля использовались в качестве силовых агрегатов специальной техники. Появление технологии турбонагнетания открыло им дорогу в мир легковых автомобилей.
Пути дальнейшего развития ДВС
Конструкторская мысль никогда не стоит на месте. Основные направления дальнейшего развития и усовершенствования двигателей внутреннего сгорания – повышение экономичности и минимизация вредных для экологии веществ в составе выхлопных газов. Применение слоистых топливных смесей, конструирование комбинированных и гибридных ДВС – лишь первые этапы долгого пути.
Мне нравится1Не нравитсяЧто еще стоит почитать
Как работает водородный двигатель и какие у него перспективы
Автомобили с водородными двигателями называют главными конкурентами электрокаров. Но у технологии пока что немало минусов, и, например, основатель Tesla Илон Маск называет ее «тупой и бесполезной». Прав он или нет?
С 2018 года в ЕС действует запрет на дизельные автомобили новейшего поколения в населенных пунктах [1]. Это стало поворотным моментом в развитии рынка электрокаров, а также — гибридных и водородных двигателей.
Великобритания еще в 2017-м высказывалась за полный запрет бензиновых авто к 2040 году. Тогда же, если верить исследованию Bloomberg New Energy Finance [2], на электрокары будет приходиться 35% от всех продаж автомобилей. Уже к 2030 году Jaguar и Land Rover планируют довести число электрокаров в своих линейках до 100% [3]. Часть из них тоже работает на водороде.
История развития рынка водородных двигателей
Первый двигатель, работающий на водороде, придумал в 1806 году французский изобретатель Франсуа Исаак де Риваз [4]. Он получал водород при помощи электролиза воды.
Первый патент на водородный двигатель выдали в Великобритании в 1841 году [5]. В 1852 году в Германии построили двигатель внутреннего сгорания (ДВС), который работал на воздушно-водородной смеси. Еще через 11 лет французский изобретатель Этьен Ленуар сконструировал гиппомобиль [6], первые версии которого работали на водороде.
В 1933 году норвежская нефтегазовая и металлургическая компания Norsk Hydro Power переоборудовала [7] один из своих небольших грузовиков для работы на водороде. Химический элемент выделялся за счет риформинга аммиака и поступал в ДВС.
В Ленинграде в период блокады на воздушно-водородной смеси работали около 600 аэростатов. Такое решение предложил военный техник Борис Шепелиц, чтобы решить проблему нехватки бензина. Он же переоборудовал 200 грузовиков ГАЗ-АА для работы на водороде.
Первый транспорт на водороде выпустила в 1959 году американская компания Allis-Chalmers Manufacturing Company — это был трактор [8].
Первым автомобилем на водородных топливных элементах стал Electrovan от General Motors 1966 года. Он был оборудован резервуарами для хранения водорода и мог проехать до 193 км на одном заряде. Однако это был единичный демонстрационный экземпляр, который передвигался только по территории завода.
В 1979-м появился первый автомобиль BMW с водородным двигателем. Толчком к его созданию послужили нефтяные кризисы 1970-х, и по их окончании об идее альтернативных двигателей забыли вплоть до 2000-х годов.
В 2007 году та же BMW выпустила ограниченную серию автомобилей Hydrogen 7, которые могли работать как на бензине, так и на водороде. Но машина была недешевой, при этом 8-килограммового баллона с газом хватало всего на 200-250 км.
Первой серийной моделью автомобиля с водородным двигателем стала Toyota Mirai, выпущенная в 2014 году. Сегодня такие модели есть в линейках многих крупных автопроизводителей: Honda, Hyundai, Audi, BMW, Ford и других.
Toyota Mirai 2016 года выпуска
Как работает водородный двигатель?
На специальных заправках топливный бак заправляют сжатым водородом. Он поступает в топливный элемент, где есть мембрана, которая разделяет собой камеры с анодом и катодом. В первую поступает водород, а во вторую — кислород из воздухозаборника.
Каждый из электродов мембраны покрывают слоем катализатора (чаще всего — платиной), в результате чего водород начинает терять электроны — отрицательно заряженные частицы. В это время через мембрану к катоду проходят протоны — положительно заряженные частицы. Они соединяются с электронами и на выходе образуют водяной пар и электричество.
Схема работы водородного двигателя
По сути, это — тот же электромобиль, только с другим аккумулятором. Емкость водородного аккумулятора в десять раз больше емкости литий-ионного. Баллон с 5 кг водорода заправляется около 3 минут, его хватает до 500 км.
Как работает водородный двигатель внутри Toyota Mirai
Где применяют водородное топливо?
- В автомобилях с водородными и гибридными двигателями. Такие уже выпускают Toyota, Honda, Hyundai, Audi, BMW, Ford, Nissan, Daimler;
- В поездах. Первый такой был выпущен в Германии компанией Alstom и ходит по маршруту Букстехуде — Куксхафен;
- В автобусах: например, в городских низкопольных автобусах марки MAN.
- В самолетах. Первый беспилотник на водороде выпустила компания Boeing, внутри — водородный двигатель Ford;
- На водном транспорте. Siemens выпускает подводные лодки на водороде, а в Исландии планируют перевести на водородное топливо все рыболовецкие суда;
- Во вспомогательном транспорте. Водород используют в электрокарах для гольфа, складских погрузчиках, сервисных автомобилях логистических компаний и аэропортов;
- В энергетике. Электростанции мощностью от 1 до 5 кВт, работающие на водороде, могут обеспечивать теплом и энергией небольшие города и отдельные здания. Например, после аварии на Фукусиме в 2018 году Япония активнее начала переходить на водородную энергетику [9], планируя перевести на водород 1,4 млн электрогенераторов;
- В смесях с обычным топливом. Например, с дизельным или газовым — чтобы удешевить производство.
Плюсы водородного двигателя
- Экологичность при использовании. Водородный транспорт не выбрасывает в атмосферу диоксид углерода;
- Высокий КПД. У двигателя внутреннего сгорания (ДВС) он составляет около 35%, а у водородного — от 45%. Водородный автомобиль сможет проехать на 1 кг водорода в 2,5-3 раза больше, чем на эквивалентном ему по энергоемкости и объему галлоне (3,8 л) бензина;
- Бесшумная работа двигателя;
- Более быстрая заправка — особенно в сравнении с электрокарами;
- Сокращение зависимости от углеводородов. Водородным двигателям не нужна нефть, запасы которой не бесконечны и к тому же сосредоточены в нескольких странах. Это позволяет нефтяным государствам диктовать цены на рынке, что невыгодно для развитых экономик.
Минусы водородного двигателя
- Высокая стоимость. Галлон бензина в США стоит около $3,1 [10], а эквивалентный ему 1 кг водорода — $8,6. Водородные батареи содержат платину — один из самых дорогих металлов в мире. Дополнительные меры безопасности также делают двигатель дорогим: в частности, специальные системы хранения и баки из углепластика, чтобы избежать взрыва.
- Проблемы с инфраструктурой. Для заправки водородом нужны специальные станции, которые стоят дороже, чем обычные.
- Не самое экологичное производство. До 95% сырья для водородного топлива получают из ископаемых [11]. Кроме того, при создании топлива используют паровой риформинг метана, для которого нужны углеводороды. Так что и здесь возникает зависимость от природных ресурсов.
- Высокий риск. Для использования в двигателях водород сжимают в 850 раз [12], из-за чего давление газа достигает 700 атмосфер. В сочетании с высокой температурой это повышает риск самовоспламенения.
Водород обладает высокой летучестью, проникает даже в небольшие щели и легко воспламеняется. Если он заполнит собой весь капот и салон автомобиля, малейшая искра вызовет пожар или взрыв. Так, в июне 2019 года утечка водорода привела к взрыву на заправке в Норвегии. Сила ударной волны была сопоставима с землетрясением в радиусе 28 км. После этого случая водородные АЗС в Норвегии запретили
Водород для топлива можно получать разными способами. В зависимости от того, насколько они безвредны, итоговый продукт называют [13] «желтым» или «зеленым». Желтый водород — тот, для которого нужна атомная энергия. Зеленый — тот, для которого используют возобновляемые ресурсы. Именно на этот водород делают ставку международные организации.
Самый безвредный способ — электролиз, то есть, извлечение водорода из воды при помощи электрического тока. Пока что он не такой выгодный, как остальные (например, паровая конверсия метана и природного газа). Но проблему можно решить, если сделать цепочку замкнутой — пускать электричество, которое выделяется в водородных топливных элементах для получения нового водорода.
Водородный транспорт в России
В России в 2014 году появился свой производитель водородных топливных ячеек — AT Energy. Компания специализируется на аккумуляторных системах для дронов, в том числе военных. Именно ее топливные ячейки использовали для беспилотников, которые снимали Олимпиаду-2014 в Сочи.
В 2019 году Россия подписала Парижское соглашение по климату, которое подразумевает постепенный переход стран на экологичные виды топлива.
Чуть позже «Газпром» и «Росатом» подготовили совместную программу развития водородной технологии на десять лет.
Главный фактор, который может обеспечить России преимущество на рынке водорода — это богатые запасы пресной воды [14] за счет внутренних водоемов, тающих ледников Арктики и снегов Сибири. Вблизи последних уже есть добывающая инфраструктура от «Роснефти», «Газпрома» и «Новатэка».
В конце 2020 года власти Санкт-Петербурга анонсировали [15] запуск каршеринга на водородном топливе совместно с Hyundai. В случае успеха проект расширят и на другие крупные города России.
Перспективы технологии
Вокруг водородных двигателей немало противоречивых заявлений. Одни безоговорочно верят в их будущее — например, Арнольд Шварценеггер еще в 2004 году, будучи губернатором Калифорнии, обещал [16], что к 2010 году весь его штат будет покрыт «водородными шоссе». Но этого так и не произошло. В этом отчасти виноват глобальный экономический кризис: автопроизводителям пришлось выживать в тяжелейших финансовых условиях, а подобные технологии требуют больших и долгосрочных вложений.
Другие, напротив, критикуют технологию за ее очевидные недостатки. Так, основатель Tesla Илон Маск назвал водородные двигатели «ошеломляюще тупой технологией» [17], которая по эффективности заметно уступает электрическим аккумуляторам. Отчасти он прав: сегодня водородным автомобилям приходится конкурировать с электрокарами, гибридами, транспортом на сжатом воздухе и жидком азоте. И пока что до лидерства им очень далеко.
С одной стороны, в Европе Toyota Mirai II стоит несколько дешевле, чем Tesla Model S (€64 тыс. против €77 тыс.) [18]. Полная зарядка водородного автомобиля занимает около 3 минут — против 30-75 минут для электрокара. Однако вся разница — в обслуживании: Toyota Mirai вмещает 5 кг водородного топлива [19] по цене $8-9 за кг. Таким образом, полный бак обойдется в $45, и его хватит на 500 км — получаем около $9 за 100 км пробега. Для Tesla Model S те же 100 км обойдутся всего в $3.
Но у водородного топлива есть существенное преимущество перед электрическими аккумуляторами — долговечность. Если аккумулятора в электрокаре хватает на три-пять лет, то водородной топливной ячейки — уже на восемь-десять лет. При этом водородные аккумуляторы лучше приспособлены для сурового климата: не теряют заряд на морозе, как это происходит с электрокарами.
Есть еще одна перспективная сфера применения водородного топлива — стационарное резервное питание: ячейки с водородом могут снабжать энергией сотовые вышки и другие небольшие сооружения. Их можно приспособить даже для энергоснабжения небольших автономных пунктов вроде полярных станций. В этом случае можно раз в год наполнять газгольдер, экономя на обслуживании и транспорте.
Основной упрек критиков — дороговизна водородного топлива и логистики. Однако Международное энергетическое агентство прогнозирует, что цена водорода к 2030 году упадет минимум на 30% [20]. Это сделает водородное топливо сопоставимым по цене с другими видами [21].
Если вспомнить, как развивался рынок электрокаров, то его росту способствовали три главных фактора:
- Лобби со стороны развитых государств: в США [22], ЕС [23], Японии [24], России [25] и других странах приняты законы в поддержку экологичного транспорта.
- Удешевление аккумуляторов: согласно исследованию Bloomberg New Energy Finance, за последние десять лет цены на литий-ионные аккумуляторы упали с $1200 до $137 за кВт·ч.
- Развитие инфраструктуры: специальные электрозарядные станции и зарядки в крупных бизнес-центрах, на парковках ТЦ и аэропортов.
Водородные двигатели ждет примерно тот же сценарий. В Toyota видят главные перспективы [26] для водородных двигателей в компактных автомобилях, а также в среднем и премиум-классе. Пока что производство не вышло на тот уровень, чтобы бюджетные модели работали на водороде и оставались рентабельными. Современные водородные машины стоят вдвое дороже обычных [27] и на 20% больше, чем гибридные.
Согласно прогнозу Markets&Markets [28], к 2022 году объем мирового производства водорода вырастет со $115 до $154 млрд. Остается главный вопрос: как быть с инфраструктурой? Чтобы водородные двигатели стали массовыми, нужны сети заправок, трубопроводы для топлива, отлаженные логистические цепочки. Все это пока только зарождается. Но и тут есть позитивные сдвиги: например, канадская Ballard Power по заказу китайского Министерства транспорта запустила пилотный проект, в рамках которого водородное топливо можно будет заливать в обычные АЗС.
Авиационные поршневые двигатели XXI века
1 Декабря 2017
До середины прошлого века поршни и цилиндры оставались главным источником лошадиных сил для крылатых машин, но затем пламенные сердца авиации завоевала турбина. Однако старая любовь не ржавеет. На рубеже веков возникла потребность возрождения поршневого авиадвигателестроения в России. И вновь, как и в 1930-х годах, движущей силой этого процесса стал ЦИАМ. О том, что собой представляет авиационный поршневой двигатель (АПД) XXI века, рассказывает начальник отдела «Авиационные поршневые двигатели» ФГУП «ЦИАМ им. П.И. Баранова» (входит в состав НИЦ «Институт имени Н.Е. Жуковского»), кандидат технических наук Лев Аронович Финкельберг.
С чем связана активизация работ по АПД в ЦИАМ?Это направление в ЦИАМ никогда не угасало, хотя, конечно, после перехода Института на реактивную тематику в конце 1940-х годов объем работ по поршневым двигателям резко сократился, и они проводились в основном по двигателям, серийный выпуск которых продолжался. К началу 1980-х годов в производстве остались только АШ-62 для Ан-2 и М-14П для учебно-тренировочных и спортивно-пилотажных самолетов Як-18, Як-52, Су-26.
Однако в 1980-е годы началось развитие беспилотной авиации, в связи с чем в ЦИАМ был создан сектор поршневых двигателей. Они оказались востребованными в беспилотных летательных аппаратах (БЛА) среднего класса со взлетным весом до тонны. Для аэрофотосъемки и мониторинга высокие скорости не нужны, а требуется малый удельный расход топлива, и поршневые двигатели как раз обладают этим качеством. При мощностях до 500 л.с. и при полетном цикле продолжительностью более 5 часов на сегодняшний день они успешно конкурируют с газотурбинными двигателями. Поршневые двигатели немного проигрывают ГТД по массе, но за счет меньшего расхода топлива суммарная масса двигателя и горючего на борту при достаточно длительном полете получается меньше. Еще одним большим преимуществом является то, что час эксплуатации АПД обходится дешевле, чем эксплуатационный час ГТД.
А как выглядят поршневые двигатели в сравнении с электрическими?Хотя сами электродвигатели достаточно компактны, оборудование для их работы — аккумуляторы и другое — пока еще слишком тяжелое. Если полетный цикл короткий, то использование электрического двигателя оправдано, но при длительном цикле АПД выигрывают. Заряда аккумуляторов надолго не хватает, или надо возить на борту тяжелую и сложную энергоустановку для их подзарядки. Перспективным направлением, которым мы сейчас будем заниматься, являются гибридные силовые установки: поршневой двигатель вращает генератор, а тот — питает электродвигатель. Так легче создать распределенную силовую установку: когда несколько электродвигателей с винтами размещаются на крыльях или в других местах на планере. Электрическая трансмиссия в таком случае проще и легче, чем механическая, что дает возможность создавать ЛА любых схем, на которые только хватит фантазии конструкторов.
Еще одна интересная возможность состоит в том, чтобы снабдить поршневой двигатель электромотором, который будет давать дополнительную мощность на взлете и работать как генератор в полете. Благодаря этому не придется делать переразмеренный поршневой двигатель, который на 100% используется только на взлете.
В мире накоплен гигантский опыт по автомобильным поршневым двигателям. Зачем нужны еще какие-то разработки? Чем отличается АПД от обычного автомобильного ДВС?АПД от автомобильных двигателей отличается, прежде всего, режимом работы. Автомобильные ДВС, хотя и рассчитаны до 6000 оборотов, работают в основном в диапазоне до 2500-3000 оборотов, причем в динамике: трогание, разгон, торможение. АПД с точки зрения автомобильного мотора постоянно работает как бы в красной зоне, ведь его крейсерский режим — это 75% от взлетного. И при этих нагрузках необходимо добиться достаточного ресурса и надежности. В авиации другие нормы прочности, необходимо обеспечить ее запас, причем такой, какого нет у автомобилистов.
Кроме того, с точки зрения безопасности системы АПД должны быть дублированными, причем, если одна система отказывает, то вторая должна обеспечить падение характеристик не более чем на 2-3% от максимального режима. Соответственно, конструктивно в АПД многое выполняется иначе. К примеру, устанавливаются две независимые системы зажигания, у которых даже электропитание должно осуществляться от разных источников.
Далее, автомобильные двигатели, как правило, выполняются с масляным поддоном, а в авиации нужно обеспечить работоспособность маслосистемы при крене и тангаже самолета. А уж обеспечение, к примеру, перевернутого полета — это вообще отдельная тема.
В авиации не так просто применить новые материалы. Для этого должна быть проведена большая работа по подтверждению всех характеристик материала, только после этого его вносят в реестр допущенных для использования в авиации. В автомобильной же промышленности это сделать проще.
Авиационный двигатель отличается от автомобильного еще и условиями эксплуатации: к примеру, вся агрегатика в автомобильной промышленности в основном рассчитана на температуру максимум до минус 40°С, а мы должны обеспечить минус 56°С. Это тоже предъявляет повышенные требования, особенно к электронике, резинотехническим изделиям и уплотнениям.
К АПД предъявляются очень жесткие требования, и когда мы приходим к автомобилистам и говорим, что в принципе ваш агрегат нам подходит, но нужно его доработать, то многие оказываются не готовы применять наземную технику в авиации. Для производителей автомобильных агрегатов, которые привыкли к заказам в миллионы единиц, наш рынок все равно достаточно узкий, поскольку мы говорим в лучшем случае о сотнях изделий в год. При этом доработок и испытаний надо проводить много, и ответственность тоже на порядок выше. Поэтому многие отказываются.
Условно говоря, авиационные и автомобильные двигатели схожи по принципу действия, но очень сильно отличаются по исполнению и агрегатам. Поэтому НИР и ОКР по ним нужно проводить отдельно.
Расскажите о работах ЦИАМ по АПД в 1990-е и 2000-е годы.По беспилотникам в эти годы был создан комплекс с небольшим поршневым двигателем П-032 мощностью 32 л.с., который производился в Самаре на фирме «Кузнецов».
Кроме того, мы занимались модернизацией существующих двигателей типа М-14, изучали возможность применения впрысковой системы вместо карбюратора, занимались сертификацией. В то время мы как раз сертифицировали двигатель М-9Ф Воронежского механического завода, современную версию М-14П, которая устанавливалась на спортивных самолетах Су-26М.
Тогда же начиналась работа с «Сухим» по сельхозсамолету Су-38П с поршневым двигателем, но, к сожалению, она не получила логического завершения. Когда было безвременье, то все схватились за идею возрождения малой авиации. Какие-то проекты были даже реализованы: «Молния-1», Ил-103, И-1Л, самолет-амфибия Л-6, тот же Су-38П. В 2000-е годы разрабатывались и вертолеты с поршневыми двигателями: Ми-34 под М-14В26В и «Актай» с роторно-поршневым двигателем ВАЗ-426. Оба вертолета летали.
Было время, когда заговорили о ренессансе малой авиации в России…К сожалению, должного развития это направление не получило. Дело в том, что в 2000-е годы было порушено очень много наземной инфраструктуры, особенно это коснулось небольших аэродромов, которые как раз и нужны малой авиации. Создать летательный аппарат можно в достаточно короткие сроки, а вот быстро восстановить инфраструктуру сложнее. Но в последние годы появилась идея, что перевозки должны базироваться в крупном хабе и осуществляться так, чтобы можно было вернуться без дозаправки. То есть нужна просто взлетная полоса. Здесь тоже становится выгодным применение поршневой авиации, поскольку время полета превышает 4-5 часов.
Каково положение с производством АПД в России сегодня? Какие работы ведутся, и как в них участвует ЦИАМ?На сегодняшний день, кроме М-14 в Воронеже, поршневые двигатели в России серийно не производятся. Однако потребность в них есть. В настоящее время ведутся ОКР по созданию двигателей в классе мощности 50 л.с., 120 л.с. и 300 л.с. По срокам мы немного отстаем, но, я думаю, в конце концов добьемся успеха, потому что АПД в этих классах востребованы и, я надеюсь, их появление даст толчок развитию гражданской малой и беспилотной авиации.
Задержки в разработке происходят по разным причинам, одна из них — отсутствие постоянных соисполнителей по агрегатам. В связи с этим ЦИАМ при проведении НИР фактически занимается налаживанием кооперации по разработке и производству АПД, хотя это не совсем наша обязанность. Но мы вынуждены этим заниматься, поскольку и в 1990-е годы, и сегодня возникает одна и та же проблема: после переориентирования авиации на ГТД потребность в поршневых двигателях сократилась до десятка двигателей в год, а это ударило не только по производителям самих двигателей, но и по поставщикам агрегатов. Никому не интересно производить 10-20 штук в год. Поэтому постепенно поставщики агрегатов в стране пропали. И нам пришлось, с чем мы и до сих пор бьемся, заниматься восстановлением инфраструктуры и кооперации производства АПД.
В 2012 году совместно с Гаврилов-Ямским машиностроительным заводом «Агат» мы сделали двигатель-демонстратор именно для отработки технологии и создания кооперации. Это 4-цилиндровый, 4-тактный двигатель мощностью 90 л.с., объемом 1400 см3 и с маркировкой ПД-1400. На основании этой разработки позже «Агат» открыл ОКР на двигатель этого класса мощности, и в этом проекте используется большая часть налаженной кооперации по агрегатам. Получилось, что ЦИАМ подвиг «Агат» и поставщиков агрегатов на разработку поршневых двигателей, поскольку в 2000-е проблема состояла и в том, что не было предприятий, готовых к работе в этой области.
Мы специально искали относительно небольшое предприятие, для которого эта продукция стала бы основной. К этому времени мы уже имели негативный опыт 1990-х годов, когда за разработку двигателя брались крупные фирмы, такие как Воронежский механический завод или Автоваз. Но потом, когда наладился основной бизнес, это направление им стало не интересно, и свои разработки они просто закрыли. Не потому, что у них что-то не получилось или не было заказчика. А потому, что это нерентабельно. Поэтому мы вынуждены были параллельно с разработкой двигателя искать основных исполнителей. Владимир Алексеевич Скибин, в то время руководивший Институтом, предложил директору завода «Агат» взяться за разработку. Дело пошло и успешно развивается. Так что можно сказать, что ЦИАМ является инициатором возрождения поршневого двигателестроения в России.
Расскажите о вкладе ЦИАМ в разработку АПД в других классах мощности.50-сильный двигатель сейчас разрабатывается АО «КБ «Луч» в Рыбинске. Это двухтактный, двухцилиндровый оппозитный двигатель. К сожалению, у нас сохраняется не очень хорошая традиция: разрабатывать летательный аппарат начали раньше, чем двигатель, соответственно, пока пришлось применять импортный мотор. Сейчас стоит вопрос о его замещении, но конструктивно мы уже на него сориентированы, и другую схему предложить не можем. Мы вынуждены ее повторять, но предлагаем новые системы, ищем свои материалы, датчики, согласуем систему управления с летательным аппаратом. Кроме этого, большой объем работ по АПД ЦИАМ проводит в части испытаний в ожидаемых условиях эксплуатации, то есть в термобарокамере с имитацией высоты, температур и даже скоростей полета. Как правило, мы требуем, чтобы к нам на испытания приходила целиком силовая установка, то есть двигатель с воздушным винтом и капотом. В конце 1990-х годов мы специально для подобных испытаний разработали, изготовили и аттестовали винтовые стенды.
В ЦИАМ создавался и демонстратор дизеля мощностью 300 л.с. Это был НИР для отработки технологий. Необходимо было показать на демонстраторе, что эти технологии работают и доступны для промышленного производства в России. Был предложен вариант дизеля для беспилотного вертолета, по которому тот же «Агат» сейчас ведет ОКР как продолжение работы, начатой ЦИАМ по двигателю-демонстратору. ЦИАМ может вести только НИР, для ведения ОКР и освоения серийного производства необходимо получение дополнительных лицензий. Мы отрабатываем отдельные узлы, технологии, системы и доводим их до 5-го уровня технологической готовности, после чего, в случае получения положительного результата, принимается решение о продолжении работ на одном из предприятий промышленности.
Мы проводим расчеты, подбираем материалы, чтобы обеспечить необходимые надежность и прочность. При нашем участии была создана кооперация по изготовлению демонстратора, мы заказывали компоненты, по нашему техническому заданию их изготавливали, а сборку делали в ЦИАМ. Этими работами мы показали, что создать АПД в России можно.
Чем вызвано применение дизелей в авиации?У дизеля расход топлива еще меньше, чем у бензинового мотора, и гораздо меньше, чем у ГТД. Не менее существенно, что дизель может работать на авиационном керосине, который производится массово, в то время как для бензиновых АПД требуется авиационный бензин. Автомобильным бензином его заправлять нельзя, так как в таком горючем очень много ароматических углеводородов, и на высоте он проявляет склонность к повышенному парообразованию, то есть закипанию. А авиационного бензина в России сейчас не стало, во-первых, потому что запретили добавлять тетраэтилсвинец, то есть этилированные бензины исчезли. Во-вторых, и это основное: нефтеперерабатывающим заводам невыгодно производить его в малых количествах. В результате, кто-то завозит бензин из Финляндии или Польши, и, естественно, он гораздо дороже, чем автомобильный бензин или авиационный керосин. Кто-то на свой страх и риск все же использует автомобильный бензин, но с учетом того, что летать на нем можно только на небольшой высоте. Мы пытались ввести регламент на использование автомобильного бензина на АШ-62 и на М-14. На АШ-62 это не получилось сразу, потому что уже на земле идет перегрев на взлетном режиме из-за более высокой, чем у авиационного бензина, тепловой отдачи.
Интересно, что работы над первым отечественным авиационным дизелем АН-1 велись в ЦИАМ под руководством А.Д. Чаромского еще в 1930-е годы. Наработки по этому проекту были использованы при создании легендарного В-2 для танка Т-34. И вот теперь дизель возвращается в авиацию, но уже в связи с появлением новых технологий с переходом на алюминиевые корпусные детали, которые появились сначала в автомобильной промышленности и позволили значительно облегчить конструкцию дизеля, что открыло ему дорогу к использованию в легковых автомобилях, а далее — в летательных аппаратах.
Чем характеризуется мировой уровень в разработках современных АПД? Есть ли понятие поколений АПД?
В АПД нет такого понятия, как двигатели разных поколений. Поршневой двигатель и у нас, и на Западе остается достаточно консервативной конструкцией, и его схема кардинально не менялась с 1940–50-х годов. Базовые двигатели разработки наиболее известных западных фирм, таких как Lycoming и Teledyne, в течение нескольких десятилетий остаются в том же типоразмере и конфигурации. Единственное, что можно отметить: обновляются обеспечивающие работу двигателя системы, появляются, например, впрысковые системы с электронным управлением с полной ответственностью типа FADEC, которые значительно снижают расход топлива, внедряются новые материалы.
Основное направление развития АПД на Западе — это то, чем занимаемся и мы: переход на новые системы, на новые масла, на новые топлива. В чем мы отстаем, так это в агрегатике, которая у нас не развивалась ни в авиации, ни в автомобильной промышленности. Те же форсунки везде применяются импортные — и в наземной технике, и в авиационной, хотя сейчас ведутся работы по созданию отечественных форсунок и для дизеля, и для бензинового АПД.
Так что говорить о смене поколений или о резком скачке в характеристиках АПД не приходится. Единственное принципиальное новшество состоит в том, что с середины 2000-х годов во всем мире стали внедряться авиационные дизели, использование которых интересно с точки зрения снижения расхода топлива и применения авиационного керосина.
Давайте все же поговорим об АПД нетрадиционных схем. Например, о роторно-поршневых двигателях. В автомобильной промышленности этот тип двигателя не прижился. А какие у него перспективы в авиации?Работы по роторно-поршневым двигателям достаточно успешно ведутся во всем мире. Среди автомобильных компаний в этом направлении преуспела Mazda. Активно занимался этой темой и Автоваз, который вполне успешно оснащал роторно-поршневыми двигателями мощностью 120 л.с. «восьмерки» и «девятки» для МВД. Изготавливались и авиационные варианты, но затем их производство в Тольятти было прекращено. В автомобильной промышленности, прежде чем выпустить продукт на рынок, необходимо обеспечить его сервис в тех точках, где вы намерены его продавать, а эта задача достаточно непростая. Поэтому потеснить поршневые двигатели в наземном транспорте сложно. Роторно-поршневой мотор Mazda несколько лет признавался лучшим в своем классе, однако широкого распространения так и не получил.
Но если говорить об авиационном использовании, то я могу назвать как минимум шесть фирм, которые сейчас делают роторно-поршневые двигатели для беспилотников. БЛА с такими двигателями уже летают в Англии, Германии, Израиле.
У этого типа двигателей много достоинств: он компактен, у него малые вибрации и очень хорошая отдача по весу, он гораздо проще поршневого двигателя по количеству деталей, достаточно экономичен. Еще одно его достоинство — модульность: отработав одну секцию, можно создать унифицированный ряд двигателей, используя одну, две или три секции. Собрать вместе четыре модуля уже сложно, нужно много опор. Мы исследовали роторно-поршневой двигатель Mazda 13B и разработали свою секцию мощностью 90 л.с., что в дальнейшем позволит создать без больших дополнительных затрат двигатели мощностью 180 и 270 л.с.
В ЦИАМ уже создан демонстратор роторно-поршневого двигателя, он прошел на нашем стенде холодную обкатку и в данный момент времени «крутится» уже в горячую.
Важное направление исследований — это применение керамики в двигателях этого типа. ЦИАМ выиграл конкурс Фонда перспективных исследований по применению керамики на базе карбида кремния в роторно-поршневом двигателе для увеличения его ресурса. Будем делать из керамики вставку статора, все уплотнения и напыление на крышке.
Эта работа рассчитана на три года. Мы ее только начинаем, но уже к концу следующего года должен появиться работающий демонстратор для подтверждения заявленных технических характеристик, в том числе по высотности и по температуре окружающего воздуха в термобарокамере.
ЦИАМ на всевозможных выставках не раз демонстрировал поршень и гильзу из композиционного материала. Для роторно-поршневого двигателя будет использован тот же материал?Поршень и гильза из керамики могут работать без смазки, поэтому мы и стремимся их внедрить. Мы испытывали их сначала со смазкой, причем поршни мы делали бесколечные, с минимальными зазорами. Тепловые расширения при использовании композитов посчитать трудно, поскольку применяется достаточно сложный многокомпонентный состав материала. Мы знаем, что цилиндр и поршень из алюминия в результате тепловых напряжений становятся овальными, а как себя поведет керамика, предсказать очень сложно. С первыми образцами у нас сразу ничего не получалось. Но потом мы нашли способ обойти эту трудность за счет изменения структуры материала. Что касается роторно-поршневого двигателя, то сейчас идут исследования и прочностные испытания различных типов материала, который в дальнейшем и будет применен в РПД.
Собственно, это и есть основная работа ЦИАМ: исследования новых технологий, материалов и конструктивных решений, их испытания. Причем испытания сначала идут на наших стендах в наземных условиях, а если они завершаются удачно, то мы переходим к испытаниям в ожидаемых условиях эксплуатации.
Не могу не задать Вам как специалисту по АПД вопрос о бесшатунном двигателе Баландина. Каков все же практический потенциал этого изобретения? Многие считают этот тип двигателя незаслуженно забытым.Это не совсем так. Да, схема интересная. Благодаря отказу от кривошипно-шатунного механизма уменьшается трение между поршнем и цилиндром. Есть энтузиасты, например, в МАИ, которые продолжают развивать эту идею. К нам каждый год приходят несколько изобретателей с новыми вариантами усовершенствования баландинской схемы. Но ее основная проблема в большей степени — технологическая. Она связана с кулисой для передачи усилий со штока на вал. Из-за высоких нагрузок не удается обеспечить приемлемый ресурс этого механизма.
В целом же все схемные решения по поршневым двигателям уже были проверены в 1950–60-е годы: и аксиальная схема, и роторно-поршневой двигатель, и схема Баландина. Сергей Степанович Баландин, кстати, тоже работал в ЦИАМ и здесь создал двигатель, который работал и развивал мощность, но только до 2000 оборотов. В НАМИ много занимались этой схемой в 1980-е годы. Ее не забыли, и государство вкладывало в эти исследования большие деньги, но результата не было. Работоспособную конструкцию создать удалось, но не удалось сделать именно двигатель с нормальным ресурсом и нужными характеристиками.
Расскажите о работах ЦИАМ по турбокомпаундному двигателю.
Турбокомпаундная схема тоже известна уже достаточно давно. В ЦИАМ когда-то занимались и такими двигателями, а созданный при участии Института в 1950 году турбокомпаундный ВД-4К стал вершиной отечественного поршневого двигателестроения. В автомобилях же она в свое время применялась Volvo. Суть ее в том, что энергию от выхлопных газов, чтобы она не пропадала, срабатывают на силовой турбине, от которой мы можем или приводить генератор и получать дополнительную электроэнергию, или использовать эту прибавку непосредственно для увеличения мощности двигателя. Если в традиционном турбонагнетателе мы просто подаем в камеру больший топливный заряд, то здесь речь идет о более полном использовании энергии выхлопных газов, которая позволила бы запитывать, к примеру, бортовые системы, не отбирая мощность у двигателя.
У нас проработано несколько схемных решений использования такой турбины, просчитана сама турбина и электрическая часть. Планируем в этом году доработать математическую модель турбокомпаундного двигателя, посмотреть, какой эффективности мы добьемся в типоразмере на 500 л.с. Мы изучали варианты на 150, 300 и 500 л.с. При 150 л.с. использование этой схемы невыгодно по весовым характеристикам, а вот для 300 и 500 л.с. это уже интересно.
В планах ЦИАМ добиться резкого увеличения характеристик АПД к 2025–30 годам: снизить удельный расход топлива на 20-25%, удельную массу — на 25–30%, повысить ресурс и стоимость эксплуатации в 3–4 раза. За счет чего предполагается достигнуть такого прогресса?За счет применения новых материалов и технологий, новых систем управления, включая систему непосредственного впрыска топлива, работ по применению синтетических масел и топлив, использования методики ЦИАМ по уменьшению масляного зазора между поршнем и цилиндром, позволяющей снизить расход топлива. Ведутся работы по уменьшению веса поршня, шатуна, колец, коленвала за счет использования интерметаллидов и композиционных материалов, по улучшению наполнения цилиндра и снятию большей работы с единицы объема. Оптимизируется геометрия впускного канала и расположения форсунки для улучшения испарения топлива на впуске. Изучаются новые алгоритмы управления рабочим процессом двигателей (стратификация заряда, гомогенное сгорание ТВС) и технологии системы управления с высокими энергиями зажигания и электронной многопараметрической системой управления рабочим процессом. Мы занимаемся отработкой перспективных систем наддува и системы снабжения двигателя воздухом, включая его охлаждение после компрессора. В наших планах — использование альтернативных видов синтетических топлив на основе углеводородных фракций пропан-бутанового ряда. Все эти составляющие дают значительный суммарный эффект, что и позволяет нам рассчитывать на достижение требуемых показателей.
Как работает автомобильный двигатель
Я никогда не был автолюбителем. Мне просто не было никакого интереса копаться под капотом, чтобы понять, как работает моя машина. За исключением замены воздушных фильтров или замены масла время от времени, если у меня когда-либо возникала проблема с моей машиной, я просто отнес ее к механику, и когда он вышел, чтобы объяснить, что случилось, я вежливо кивнул и притворился. как будто я знал, о чем он говорил.
Но в последнее время мне не терпелось изучить основы работы автомобилей.Я не планирую становиться заядлым обезьяной, но я хочу иметь базовое представление о том, как все в моей машине действительно работает. Как минимум, эти знания позволят мне понять, о чем механик говорит в следующий раз, когда я сяду в машину. Кроме того, мне кажется, что мужчина должен уметь понимать основы технологии, которую он использует. ежедневно. Что касается этого веб-сайта, я знаю, как работают кодирование и SEO; пора мне изучить более конкретные вещи в моем мире, например, что находится под капотом моей машины.
Я полагаю, что есть и другие взрослые мужчины, похожие на меня — мужчины, которые не занимаются машинами, но им немного интересно, как работают их машины. Так что я планирую поделиться тем, что я узнал в ходе собственного исследования, и время от времени возьмусь за серию статей, которые мы назовем Gearhead 101. Цель состоит в том, чтобы объяснить самые основы того, как работают различные детали в автомобиле, и предоставить ресурсы о том, где вы можете узнайте больше самостоятельно.
Итак, без лишних слов, мы начнем наш первый урок Gearhead 101 с объяснения всех тонкостей сердца автомобиля: двигателя внутреннего сгорания.
Двигатель внутреннего сгорания
Двигатель внутреннего сгорания называется «двигателем внутреннего сгорания», потому что топливо и воздух сгорают внутри двигателя для создания энергии для перемещения поршней, которые, в свою очередь, перемещают автомобиль (мы покажем вы как это происходит подробно ниже).
Сравните это с двигателем внешнего сгорания, где топливо сжигается за пределами двигателя, и энергия, создаваемая при этом сгорании, является его движущей силой. Паровые двигатели — лучший тому пример.Уголь сжигается за пределами двигателя, который нагревает воду для производства пара, который затем приводит в действие двигатель.
Большинство людей думает, что в мире механизированного движения паровые двигатели внешнего сгорания появились раньше, чем двигатели внутреннего сгорания. Реальность такова, что двигатель внутреннего сгорания был первым. (Да, древние греки возились с паровыми двигателями, но из их экспериментов ничего практического не вышло.) поршней.На самом деле, их двигал не порох. Принцип работы этого раннего двигателя внутреннего сгорания заключался в том, что вы вставляли поршень до самого верха цилиндра, а затем зажигали порох под поршнем. После взрыва образовался вакуум, который засосал поршень в цилиндр. Поскольку этот двигатель полагался на изменения давления воздуха для перемещения поршня, они назвали его атмосферным двигателем. Это было не очень эффективно. К 17 -м годам паровые двигатели были многообещающими, поэтому от двигателей внутреннего сгорания отказались.
Только в 1860 году был изобретен надежный, работающий двигатель внутреннего сгорания. Бельгийский парень по имени Жан Жозеф Этьен Ленуар запатентовал двигатель, который впрыскивал природный газ в цилиндр, который впоследствии воспламенялся постоянным пламенем рядом с цилиндром. Он работал аналогично пороховому атмосферному двигателю, но не слишком эффективно.
Основываясь на этой работе, в 1864 году два немецких инженера по имени Николаус Август Отто и Ойген Ланген основали компанию, которая производила двигатели, аналогичные модели Ленуара.Отто отказался от управления компанией и начал работать над конструкцией двигателя, над которой он играл с 1861 года. Его конструкция привела к тому, что мы теперь знаем как четырехтактный двигатель, и базовая конструкция двигателя до сих пор используется в автомобилях.
Анатомия автомобильного двигателя
Двигатель V-6
Я немного покажу вам, как работает четырехтактный двигатель, но прежде чем я это сделаю, я подумал, что было бы полезно пройти через различные части двигателя, чтобы вы имели представление о том, что и что делает в четырехтактном процессе.В этих объяснениях используется терминология, основанная на других терминах из списка, поэтому не беспокойтесь, если вы сначала запутаетесь. Прочтите все, чтобы получить общее представление, а затем прочтите еще раз, чтобы иметь общее представление о каждой части, о которой идет речь.
Блок цилиндров (блок цилиндров)
Блок двигателя является основой двигателя. Большинство блоков цилиндров отлиты из алюминиевого сплава, но некоторые производители по-прежнему используют железо.Блок двигателя также называют блоком цилиндров из-за большого отверстия или трубок, называемых цилиндрами, которые залиты в интегрированную конструкцию. В цилиндре поршни двигателя скользят вверх и вниз. Чем больше цилиндров в двигателе, тем он мощнее. Помимо цилиндров, в блок встроены другие каналы и каналы, которые позволяют маслу и охлаждающей жидкости течь к различным частям двигателя.
Почему двигатель называется «V6» или «V8»?
Отличный вопрос! Это связано с формой и количеством цилиндров в двигателе.В четырехцилиндровых двигателях цилиндры обычно устанавливаются по прямой линии над коленчатым валом. Эта компоновка двигателя называется рядным двигателем .
Еще одна четырехцилиндровая компоновка называется «плоская четверка». Здесь цилиндры расположены горизонтально двумя рядами, коленчатый вал идет посередине.
Когда двигатель имеет более четырех цилиндров, они делятся на два ряда цилиндров — по три (или более) цилиндра на каждую сторону. Разделение цилиндров на два ряда делает двигатель похожим на букву V.”V-образный двигатель с шестью цилиндрами = двигатель V6. V-образный двигатель с восемью цилиндрами = V8 — по четыре в каждом ряду цилиндров.
Камера сгорания
В камере сгорания двигателя происходит волшебство. Здесь топливо, воздух, давление и электричество объединяются, чтобы создать небольшой взрыв, который перемещает поршни автомобиля вверх и вниз, создавая таким образом силу для движения автомобиля. Камера сгорания состоит из цилиндра, поршня и головки блока цилиндров.Цилиндр действует как стенка камеры сгорания, верхняя часть поршня действует как дно камеры сгорания, а головка цилиндра служит потолком камеры сгорания.
Головка блока цилиндров
Головка блока цилиндров представляет собой кусок металла, который находится над цилиндрами двигателя. В головке блока цилиндров отлиты небольшие закругленные углубления для создания пространства в верхней части камеры сгорания. Прокладка головки герметично закрывает стык между головкой блока цилиндров и блоком цилиндров.Впускные и выпускные клапаны, свечи зажигания и топливные форсунки (эти детали будут объяснены позже) также установлены на головке блока цилиндров.
Поршень
Поршни перемещаются вверх и вниз по цилиндру. Они похожи на перевернутые суповые банки. Когда топливо воспламеняется в камере сгорания, сила толкает поршень вниз, который, в свою очередь, перемещает коленчатый вал (см. Ниже). Поршень прикрепляется к коленчатому валу через шатун, он же шатун. Он соединяется с шатуном через поршневой палец, а шатун соединяется с коленчатым валом через шатунный подшипник.
В верхней части поршня вы найдете три или четыре канавки, отлитые в металле. Внутри канавок вставляются поршневые кольца . Поршневые кольца — это часть, которая фактически касается стенок цилиндра. Они сделаны из железа и бывают двух видов: компрессионные кольца и масляные кольца. Компрессионные кольца — это верхние кольца, они прижимаются наружу к стенкам цилиндра, обеспечивая прочное уплотнение камеры сгорания. Масляное кольцо — это нижнее кольцо на поршне, которое предотвращает просачивание масла из картера в камеру сгорания.Он также вытирает излишки масла со стенок цилиндров и обратно в картер.
Коленчатый вал
Коленчатый вал преобразует движение поршней вверх и вниз во вращательное движение, которое позволяет автомобилю двигаться. Коленчатый вал обычно входит в блок цилиндров вдоль дна. Он простирается от одного конца блока двигателя до другого. В передней части двигателя коленчатый вал соединяется с резиновыми ремнями, которые соединяются с распределительным валом и передают мощность на другие части автомобиля; в задней части двигателя распределительный вал соединяется с трансмиссией, которая передает мощность на колеса.На каждом конце коленчатого вала вы найдете сальники или «уплотнительные кольца», которые предотвращают утечку масла из двигателя.
Коленчатый вал находится в так называемом картере двигателя. Картер находится под блоком цилиндров. Картер защищает коленчатый вал и шатуны от посторонних предметов. Область в нижней части картера называется масляным поддоном, и именно здесь хранится масло вашего двигателя. Внутри масляного поддона вы найдете масляный насос, который прокачивает масло через фильтр, а затем это масло разбрызгивается на коленчатый вал, шатунные подшипники и стенки цилиндра, чтобы обеспечить смазку для движения поршня.В конце концов масло стекает обратно в масляный поддон, но процесс начинается снова.
Вдоль коленчатого вала вы найдете балансировочные выступы, которые действуют как противовесы, чтобы уравновесить коленчатый вал и предотвратить повреждение двигателя из-за колебаний, возникающих при вращении коленчатого вала.
Также вдоль коленчатого вала находятся коренные подшипники. Коренные подшипники обеспечивают гладкую поверхность между коленчатым валом и блоком цилиндров для вращения коленчатого вала.
Распределительный вал
Распределительный вал — это мозг двигателя.Он работает вместе с коленчатым валом через зубчатый ремень, чтобы впускные и выпускные клапаны открывались и закрывались в нужное время для оптимальной работы двигателя. Распределительный вал использует овальные выступы, которые проходят поперек него, чтобы контролировать время открытия и закрытия клапанов.
Большинство распределительных валов проходят через верхнюю часть блока цилиндров непосредственно над коленчатым валом. В рядных двигателях один распределительный вал управляет как впускным, так и выпускным клапанами. На V-образных двигателях используются два отдельных распредвала.Один управляет клапанами на одной стороне V, а другой — клапанами на противоположной стороне. Некоторые V-образные двигатели (например, на нашей иллюстрации) даже имеют два распределительных вала на ряд цилиндров. Один распределительный вал управляет одной стороной клапанов, а другой распределительный вал — другой стороной.
Система синхронизации
Как упоминалось выше, распределительный вал и коленчатый вал координируют свое движение через ремень или цепь ГРМ. Цепь газораспределительного механизма удерживает коленчатый вал и распределительный вал в одном и том же положении относительно друг друга все время во время работы двигателя.Если распредвал и коленчатый вал по какой-либо причине рассинхронизируются (например, цепь ГРМ пропускает зубчатый венец), двигатель не будет работать.
Клапанный механизм
Клапанный механизм — это механическая система, которая установлена на головке блока цилиндров и управляет работой клапанов. Клапанный механизм состоит из клапанов, коромысел, толкателей и подъемников.
Клапаны
Клапаны бывают двух типов: впускные и выпускные. Впускные клапаны подают смесь воздуха и топлива в камеру сгорания, чтобы создать сгорание для питания двигателя.Выпускные клапаны позволяют выхлопным газам, образовавшимся после сгорания, выходить из камеры сгорания.
Автомобили обычно имеют один впускной клапан и один выпускной клапан на цилиндр. Большинство высокопроизводительных автомобилей (Ягуары, Мазерати и др.) Имеют четыре клапана на цилиндр (два впускных, два выпускных). Хотя Honda не считается «высокопроизводительным» брендом, она также использует в своих автомобилях четыре клапана на цилиндр. Есть даже двигатели с тремя клапанами на цилиндр — двумя впускными клапанами, одним выпускным клапаном. Многоклапанные системы позволяют автомобилю лучше «дышать», что, в свою очередь, улучшает характеристики двигателя.
Коромысла
Коромысла — это маленькие рычаги, которые касаются кулачков или кулачков распределительного вала. Когда лепесток поднимает один конец коромысла, другой конец коромысла давит на шток клапана, открывая клапан, чтобы впустить воздух в камеру сгорания или выпустить выхлоп. Это работает как качели.
Толкатели / подъемники
Иногда кулачки распредвала непосредственно касаются коромысла (как вы видите в двигателях с верхним распределительным валом), открывая и закрывая клапан.В двигателях с верхним расположением клапанов выступы распределительного вала не контактируют напрямую с коромыслами, поэтому используются толкатели или толкатели.
Топливные форсунки
Чтобы создать сгорание, необходимое для движения поршней, нам нужно топливо в цилиндрах. До 1980-х годов автомобили использовали карбюраторы для подачи топлива в камеру сгорания. Сегодня все автомобили используют одну из трех систем впрыска топлива: прямой впрыск топлива, впрыск топлива через отверстия или впрыск топлива через корпус дроссельной заслонки.
При непосредственном впрыске топлива каждый цилиндр имеет собственную форсунку, которая впрыскивает топливо прямо в камеру сгорания в самый подходящий момент для сгорания.
При распределенном впрыске топлива, вместо того, чтобы распылять топливо непосредственно в цилиндр, оно распыляется во впускной коллектор сразу за клапаном. Когда клапан открывается, воздух и топливо попадают в камеру сгорания.
Системы впрыска топлива в корпусе дроссельной заслонки работают как карбюраторы, но без карбюратора. Вместо того, чтобы каждый цилиндр получил свою собственную топливную форсунку, есть только одна топливная форсунка, которая идет к корпусу дроссельной заслонки. Топливо смешивается с воздухом в корпусе дроссельной заслонки, а затем распределяется по цилиндрам через впускные клапаны.
Свеча зажигания
Над каждым цилиндром находится свеча зажигания. Когда он загорается, он воспламеняет сжатое топливо и воздух, вызывая мини-взрыв, который толкает поршень вниз.
Четырехтактный цикл
Итак, теперь, когда мы знаем все основные части двигателя, давайте взглянем на механизм, который на самом деле заставляет нашу машину двигаться: четырехтактный цикл.
На приведенном выше рисунке показан четырехтактный цикл в одном цилиндре. То же самое происходит и с другими цилиндрами.Повторите этот цикл тысячу раз в минуту, и вы получите движущуюся машину.
Ну вот. Основы работы автомобильного двигателя. Загляните сегодня под капот вашего автомобиля и посмотрите, сможете ли вы указать на детали, которые мы обсуждали. Если вам нужна дополнительная информация о том, как устроен автомобиль, посмотрите книгу How Cars Work. Это очень помогло мне в моих исследованиях. Автор отлично справляется с переводом вещей на язык, понятный даже новичку.
Теги: АвтомобилиКак работает двигатель внутреннего сгорания?
Двигатель, который использует жидкое топливо для выработки энергии, такой как двигатель внутреннего сгорания, по сути, представляет собой большой воздушный насос.Холодный воздух втягивается, смешивается с выбранным топливом для создания энергии, а затем удаляется в виде горячего выхлопного газа. Чем эффективнее дышит этот «воздушный насос» двигателя, тем эффективнее он вырабатывает мощность.
В этой статье мы сосредоточимся на том, как именно автомобильный двигатель внутреннего сгорания преобразует воздух и топливо в энергию, чтобы двигать ваш автомобиль по дороге. В этой статье мы определяем некоторую терминологию для различных частей, однако вы можете найти нашу статью по теме Глоссарий внутренних деталей двигателя полезен, если вы хотите узнать о других компонентах, не упомянутых здесь.
Имейте в виду, что это сложная тема; Хотя мы сделали все возможное, чтобы объяснить это простым языком, некоторые концепции может быть трудно продемонстрировать в двухмерном формате. Кроме того, некоторые описания функций двигателя были упрощены для ясности.
Каковы основные части двигателя?
Типичный блок двигателя V8.Во-первых, давайте рассмотрим две основные части типичного двигателя внутреннего сгорания. Главный и самый крупный предмет — это блок двигателя, составляющий нижнюю часть двигателя.Это дом для поршни, шатуны, коленчатый вал, масляный насос и распределительный вал, если двигатель имеет конструкцию с верхним расположением клапана. Поскольку эта секция содержит отверстия цилиндра, по которым перемещаются поршни, ее иногда называют блоком цилиндров.
Слева показана головка блока цилиндров, прикрепленная болтами к блоку двигателя. Справа и взломанная схема ГБЦ.К верхней части блока цилиндров привинчена головка (или головки) блока цилиндров. Они содержат выпускные и впускные клапаны, а также распределительные валы, если двигатель имеет конструкцию с верхним кулачком.Рядные двигатели (все цилиндры в один ряд) имеют только одну головку блока цилиндров. Двигатели V-образной или H-образной формы имеют две головки блока цилиндров, по одной на ряд цилиндров.
Типичная секция картера, которая крепится болтами, образуя нижнюю часть блока цилиндров.Как воздух попадает в герметичный блок двигателя?
Прежде чем мы рассмотрим этапы процесса внутреннего сгорания в двигателе, важно понять, как воздух попадает в герметичный блок двигателя.
Это происходит благодаря так называемому впускному коллектору. An Впускной коллектор, сделанный из металла или пластика, представляет собой узел, который находится над двигателем и состоит из ряда труб, которые распределяют воздух и топливо в каждый цилиндр. (Подробнее о впускных коллекторах мы приглашаем вас прочитать наши статья по теме.)
Впускные коллекторы на V-образных двигателях обычно устанавливаются сверху между обоими рядами цилиндров.После того, как воздух сначала проходит через впускную трубку и очищается воздушным фильтром, он попадает во впускной коллектор.Карбюратор, дроссельная заслонка или топливные форсунки впрыскивают соответствующее количество топлива, которое смешивается с этим всасываемым воздухом. Идеальное соотношение для воздушно-топливной смеси составляет 14,7: 1, что означает 14,7 частей воздуха на 1 часть топлива. Теперь нам нужно подать эту топливно-воздушную смесь в каждый цилиндр. Это начало «4-тактного цикла» двигателя нашего автомобиля.
Каковы 4 этапа 4-тактного цикла?
Автомобильные двигатели описываются как «4-тактные», потому что в процессе сгорания участвуют 4 основных этапа.(Существуют «двухтактные» двигатели, но они не использовались в дорожных автомобилях в течение многих десятилетий, и это обсуждение выходит за рамки данной статьи.)
Итак, нам ясно: шаги, описанные ниже, должны выполняться в КАЖДОМ цилиндре двигателя. Для ясности мы опишем четыре хода, как они происходят в ОДНОМ цилиндре.
Первый шаг: ход впуска
Двигателю требуется топливно-воздушная смесь, чтобы попасть в закрытую зону цилиндра.Для этого впускной клапан перемещается из закрытого положения в открытое. Смесь поступает в цилиндр. Поршень, который находится в верхней части цилиндра, начинает двигаться вниз, создавая частичный вакуум, который способствует всасыванию смеси. Выпускной клапан остается закрытым на этом этапе.
- ВПУСКНОЙ ХОД:
- ДВИЖЕНИЕ ПОРШНЯ: ВНИЗ
- ВПУСКНОЙ КЛАПАН: ОТКРЫТ
- ВЫПУСКНОЙ КЛАПАН: ЗАКРЫТО
- ДЕЙСТВИЕ: ВТЯНИЕ В СМЕСИ ВОЗДУХ / ТОПЛИВО
Второй этап: ход сжатия
После того, как поршень достигает нижней части цилиндра (известной как «нижняя мертвая точка»), впускной клапан закрывается, и поршень начинает двигаться вверх, что сжимает топливно-воздушную смесь.Под давлением смеси она воспламеняется с большей силой, чем если бы она не была сжата. Впускные и выпускные клапаны остаются закрытыми, чтобы смесь оставалась в стенках цилиндра. Полное сжатие достигается, когда поршень достигает максимальной точки своего хода (известной как «верхняя мертвая точка»).
- ХОД СЖАТИЯ:
- ДВИЖЕНИЕ ПОРШНЯ: ВВЕРХ
- ВПУСКНОЙ КЛАПАН: ЗАКРЫТО
- ВЫПУСКНОЙ КЛАПАН: ЗАКРЫТО
- ДЕЙСТВИЕ: СМЕСЬ СЖАТОГО ВОЗДУХА / ТОПЛИВА
Третий этап: рабочий ход
Этот ход начинается с поршня в верхней части цилиндра, при закрытых обоих клапанах и сжатой топливно-воздушной смеси.Это момент, когда загорается свеча зажигания, воспламеняя смесь и создавая давление (мощность), которое заставляет поршень опускаться. Оба клапана остаются закрытыми, чтобы сдерживать давление внутри стенок цилиндра.
- СИЛОВОЙ ХОД:
- ДВИЖЕНИЕ ПОРШНЯ: ВНИЗ
- ВПУСКНОЙ КЛАПАН: ЗАКРЫТО
- ВЫПУСКНОЙ КЛАПАН: ЗАКРЫТО
- ДЕЙСТВИЕ: ЗАЖИГАТЬ СМЕСЬ ВОЗДУХ / ТОПЛИВА
Четвертый этап: ход выхлопа
Поршень снова меняет направление и начинает двигаться вверх.Теперь двигатель должен удалить сгоревшие остатки топливно-воздушной смеси. Движение поршня вверх толкает этот выхлопной газ вверх, и выпускной клапан открывается, позволяя ему выйти из цилиндра в выпускной коллектор (и, в конечном итоге, в выхлопную трубу). Впускной клапан остается закрытым, так как двигатель хочет, чтобы все эти газы уходили через выхлопные трубы.
- ХОД ВЫПУСКА:
- ДВИЖЕНИЕ ПОРШНЯ: ВВЕРХ
- ВПУСКНОЙ КЛАПАН: ЗАКРЫТО
- ВЫПУСКНОЙ КЛАПАН: ОТКРЫТЬ
- ДЕЙСТВИЕ: СМЕСЬ ВОЗДУХА / ТОПЛИВА EXPEL
Мы можем суммировать действия четырех штрихов на этой диаграмме:
Как клапаны знают, когда открываться и закрываться?
Здесь впускные и выпускные клапаны (показаны зеленым и красным) приводятся в действие отдельными распределительными валами.Эти клапаны выполняют важную функцию, и их движение точно рассчитано по времени.Назначение клапанов
Двигатель должен иметь как минимум один впускной клапан и один выпускной клапан для каждого цилиндра. Чтобы 4-тактный цикл был успешным, открытие и закрытие этих клапанов точно контролируется — синхронизируется с движением поршней, чтобы каждый клапан выполнял свою работу именно тогда, когда это необходимо. Этот точный контроль известен как «время».
Правильная синхронизация позволяет впускному клапану открываться и впускать топливно-воздушную смесь в цилиндр, когда поршень движется вниз во время такта впуска.А после того, как происходит сгорание, выпускной клапан открывается, так что сгоревшие газы могут выталкиваться из цилиндра, когда поршень движется обратно вверх.
Открытие и закрытие всех клапанов двигателя осуществляется распределительным валом. Каждый распределительный вал содержит несколько «выступов», которые представляют собой детали неправильной формы, расположенные на центральном валу. По мере вращения распределительного вала вращаются и эти выступы, которые контактируют с другими компонентами для перемещения клапанов. Клапаны обычно закрыты и удерживаются закрытыми с помощью клапанных пружин.Лепестки должны преодолевать давление пружины, чтобы открыть клапаны. Поскольку лепесток продолжает вращаться, пружины снова закрывают клапаны. Эти лепестки имеют точную форму и механическую обработку, поэтому они вносят свой вклад в поддержание правильной синхронизации двигателя.
Распределительные валы видны в двигателе с верхним распределительным валом (слева) и в двигателе с верхним расположением клапанов (справа).В двигателях с верхним расположением клапанов распределительные валы расположены в блоке цилиндров и соединены с клапанами с помощью толкателей, толкателей и коромысел (в зависимости от конструкции двигателя).В двигателях с верхним расположением распредвала распредвалы находятся в головке блока цилиндров. По-прежнему существует механическое соединение с клапанами, но поскольку кулачок расположен ближе к клапанам, это более короткое и прямое соединение.
Клапаны и синхронизация двигателя
Без правильного выбора времени клапаны не будут открываться и закрываться, когда они должны это делать. 4-тактный цикл не будет работать должным образом. Хорошее сгорание было бы трудным, если не невозможным, и двигатель не работал бы, потому что это, по сути, гигантский воздушный насос.
Синхронизация движения поршня и клапана достигается за счет механического соединения коленчатого и распределительного валов. Поршни соединены с коленчатым валом (более подробно описано ниже). Коленчатый вал соединяется с распределительным валом одним из трех способов: шестернями ГРМ, цепью ГРМ или ремнем ГРМ (обратите внимание на использование слова «синхронизация»).
Эти иллюстрации демонстрируют, как цепи ГРМ или ремни ГРМ синхронизируют работу коленчатого и распределительного валов.Для наших целей важно то, что малейшее вращательное движение коленчатого вала вызывает его вращение, в результате чего клапаны открываются или закрываются, в зависимости от положения лепестков. Пока синхронизация остается правильной, двигатель будет работать. Если, однако, ремень или цепь ГРМ выскакивает на шестерню или, что еще хуже, щелкает, механическое соединение не синхронизировано или полностью обрывается. Двигатель будет плохо работать или вообще не будет работать.
Количество клапанов зависит от двигателя
Общее количество клапанов в двигателе может быть разным.Старые двигатели имеют 1 впускной и 1 выпускной клапан на цилиндр. У 8-цилиндрового двигателя всего 16 клапанов (2 x 8). Некоторые двигатели имеют 2 впускных клапана и 1 выпускной клапан на цилиндр. 6-цилиндровый двигатель с такой установкой с 3 клапанами на цилиндр будет иметь 18 клапанов (3 x 6). Многие современные двигатели имеют 2 впускных и 2 выпускных клапана на каждый цилиндр. Четырехцилиндровый двигатель с 4 клапанами на цилиндр, конечно, будет иметь в общей сложности 16 клапанов (4 x 4).
Как вы можете видеть из этих примеров, общее количество клапанов НЕ говорит вам, сколько цилиндров в двигателе.
Конфигурации с одним распредвалом и двумя распредвалами
Все двигатели с верхним расположением клапанов (кулачок в блоке) имеют один распределительный вал для двигателя. Двигатели с верхним расположением кулачков с распределительными валами в головках могут иметь один цилиндр на головку или два на головку. Если их два, каждый распределительный вал предназначен для работы впускных или выпускных клапанов.
Терминология двигателя говорит нам, что двигатель с одним распредвалом НА ГОЛОВКУ является двигателем «SOHC» (с одним верхним распредвалом).Точно так же двигатель с двумя кулачками НА ГОЛОВКУ называется двигателем «DOHC» (с двумя верхними кулачками). Будьте осторожны при подсчете распредвалов! V-образный двигатель DOHC с двумя головками цилиндров имеет в общей сложности ЧЕТЫРЕ распредвала (по два на головку).
Как сила от поршней перемещает автомобиль?
Мы узнали, что на этапе 3 4-тактного цикла воспламенение топливно-воздушной смеси внутри цилиндра обеспечивает силу, толкающую поршень вниз. Теперь давайте посмотрим, как двигатель преобразует это движение вверх-вниз во вращательное движение, которое нам нужно для вращения коленчатого вала.
Здесь показан шатун с прилегающими элементами (слева) и сам по себе (справа).Поршень прикреплен к прочной металлической детали, известной как шатун. Шатуны могут поворачиваться в этой точке соединения на поршне.
Нижний конец шатуна крепится к коленчатому валу, который служит выходным валом для всего двигателя. Эта точка крепления на коленчатом валу смещена от средней линии коленчатого вала. Когда шатун перемещается вверх и вниз вместе с поршнем, он вращает коленчатый вал.
Чтобы лучше представить себе это, представьте себе движения ног велосипедиста. Движение вверх-вниз в шарнирном колене очень похоже на то, что происходит с поршнем и верхней частью шатуна. Но голень и ступня велосипедиста вращают педаль велосипеда по кругу. Движение ноги велосипедиста вверх и вниз преобразуется во вращательное движение стопы, которое раскручивает кривошип велосипеда.
На рисунке выше показаны коленчатый вал, шатуны и поршни 4-цилиндрового двигателя.Каждый поршень совершает рабочий ход 4-тактного цикла в разное время. Это позволяет добиться нескольких целей: во-первых, он выравнивает импульсы мощности, чтобы двигатель работал более плавно. Во-вторых, поскольку все поршни соединены друг с другом через кривошип, рабочий ход одного поршня также создает такты впуска, сжатия и выпуска других поршней.
Присмотритесь к типичному коленчатому валу. Обратите внимание на отверстия, через которые проходит смазочное масло. Цапфы коренных подшипников предназначены для прилегания к изогнутым подшипникам картера.Противовесы сглаживают вращательные колебания.Регулярное срабатывание цилиндров создает мощность, необходимую для поддержания постоянного и равномерного вращения коленчатого вала с постоянным крутящим моментом.
Коленчатый вал, если смотреть снизу двигателя, со снятой секцией картера.Сам коленчатый вал находится в нижней части блока цилиндров. Поскольку коленчатый вал вынужден вращаться от мощности, производимой во время 4-тактного цикла, он создает крутящее движение или крутящий момент.Хвостовой конец кривошипа выходит из блока цилиндров сзади, и оттуда он соединяется с маховиком, трансмиссией, приводным и полуосевым валами, в конечном итоге достигая ведущих колес. Это сила, которая продвигает ваш автомобиль вперед.
В задней части двигателя, где коленчатый вал выходит из блока цилиндров, прикреплен маховик.Теперь, когда у вас есть базовое представление о том, как работает двигатель внутреннего сгорания, вы будете знать, какие виды капитального ремонта включают в себя определенные типы.И вы оцените ценность регулярного обслуживания, особенно замены масла, при котором все движущиеся части остаются должным образом смазанными.
Если вы хотите перейти на новый уровень, выполнив перестройку движка (или наняв кого-то для этого), мы рекомендуем прочитать нашу статью по теме ЧТО ВАМ НУЖНО ПРИ ВОССТАНОВЛЕНИИ ИЛИ ЗАМЕНЫ ДВИГАТЕЛЯ, чтобы получить представление об оборудовании и части, которые понадобятся для работы. У нас также есть полностью восстановленные двигатели, готовые к установке.
Если у вас есть какие-либо вопросы о запчастях, которые вам необходимо заказать, мы будем рады вашим запросам — наши компетентные представители находятся здесь семь дней в неделю!
Как работают автомобильные двигатели? — Теперь по всей стране
Несмотря на относительно простое управление, автомобили на самом деле являются очень сложными машинами. Автомобилям для работы требуется топливо, но что на самом деле с ним делает двигатель?
В общем, стандартный двигатель внутреннего сгорания — который сегодня имеет большинство транспортных средств, работающих на топливе, — использует воздух в сочетании с бензином для выработки энергии.[1] Конечно, все становится сложнее.
Компоненты двигателя
Прежде чем углубляться в то, как работает двигатель автомобиля, он поможет изучить его основную анатомию (что также важно, если вам нужно выполнить какое-либо техническое обслуживание автомобиля). Взгляните на схему двигателя автомобиля ниже, затем просмотрите список основных компонентов двигателя и их функции:
- Блок двигателя: Блок двигателя, как правило, изготовлен из железа или алюминия, в нем находится большинство деталей, обеспечивающих работу двигателя, включая цилиндры, поршни, коленчатый вал и распределительный вал.[2] (Если вы открываете капот, на блоке двигателя обычно устанавливается генератор переменного тока.)
- Головка блока цилиндров: В головку блока цилиндров входят компоненты, управляющие потоком всасываемого воздуха и выхлопных газов, такие как клапаны и распределительные валы. [2]
- Коленчатый вал: Коленчатый вал преобразует движение поршней вверх и вниз в соответствующее круговое движение. Он прикреплен к поршням через шатун [2].
- Шатуны: Шатун прикрепляет коленчатый вал к поршням.Он вращается на каждом конце, что дает ему возможность перемещаться вместе с обоими компонентами. [3]
- Поршни: Поршни движутся вверх и вниз внутри цилиндра, передавая энергию коленчатому валу, который, в свою очередь, приводит транспортное средство в движение. Поршневые кольца, расположенные внутри поршней, помогают герметизировать края цилиндра и уменьшают трение во время движения. [2], [3]
- Свечи зажигания: Свечи зажигания вызывают возгорание, создавая искру, воспламеняющую поступающую смесь воздуха и топлива.[3]
- Топливные форсунки : Топливные форсунки снабжают двигатель топливом. В процессе он превращает топливо в крошечные, похожие на туман частицы, так что его легче сжечь двигателем. [4]
- Клапаны: В двигателе есть два типа клапанов: впускные и выпускные. Первый пропускает воздух и газ в двигатель; последний выпускает выхлопные газы. [3]
- Распределительный вал: Распределительный вал контролирует открытие и закрытие клапанов.Для этого он преобразует круговое движение коленчатого вала в движение вверх и вниз, которое открывает и закрывает клапаны. [2]
- Ремень или цепь привода ГРМ: Ремень или цепь привода ГРМ проходят между распределительным валом и коленчатым валом, чтобы гарантировать синхронную работу. [2]
Процесс четырехтактного двигателя
Большинство двигателей внутреннего сгорания работают по четырехступенчатому циклу. Эти шаги формально называются ходами по отношению к четырем движениям, которые поршень совершает для завершения каждого цикла.Такты происходят в следующем порядке: впуск, сжатие, сгорание, выпуск.
При каждом такте поршень движется вверх или вниз в цилиндре, перемещаясь вместе с впуском воздуха и топлива или выпуском выхлопных газов. Вот обзор того, как работает этот процесс [1]:
1. Ход всасывания
Во время такта впуска поршень смещается вниз, а впускной клапан открывается, впуская поток бензина и воздуха. Как только поршень достигает основания цилиндра, клапаны закрываются, герметизируя бензиново-воздушную смесь.(Стоит отметить, что в некоторых современных автомобилях бензин впрыскивается позже во время такта сжатия.)
2. Ход сжатия
В этот момент поршень движется назад вверх, чтобы сжимать газ и воздух к верхней части цилиндра. Выталкивание этой смеси в более ограниченное пространство подготавливает ее к воспламенению в такте сгорания.
3. Ход горения
Также известный как рабочий ход, ход сгорания — это то, что действительно создает мощность вашего двигателя и заставляет автомобиль двигаться.Здесь свеча зажигания загорается, чтобы зажечь газ. Возникающее тепло и расширяющийся газ заставляют поршень опускаться обратно в цилиндр.
4. Ход выпуска
Когда поршень достигает дна цилиндра, выпускной клапан открывается, так что поршень может откачивать отработанные газы из двигателя. Оттуда газы попадают в выхлопную систему и покидают автомобиль. Наконец, выпускной клапан закрывается, и четырехтактный цикл повторяется.
Различные типы автомобильных двигателей
Хотя все двигатели внутреннего сгорания обычно работают одинаково, существует несколько различных типов двигателей.При обсуждении двигателей, которые чаще всего используются в личных транспортных средствах, различия в основном связаны с расположением цилиндров. Например, цилиндры рядных двигателей расположены прямо, в то время как в двигателях V-образного типа цилиндры разделены на две группы и образуют V-образную форму. Другие двигатели будут регулировать определенные механизмы, такие как фазы газораспределения или количество воздуха, добавляемого в четырехтактный цикл, для повышения эффективности или мощности. [1]
Знание того, как работает автомобильный двигатель, может оказаться полезным, когда пришло время покупать следующий автомобиль, особенно если вы получаете его от частного лица, а не от дилера.Узнайте, как купить машину у частного продавца.
[1] «Вот как работает двигатель вашего автомобиля» (17 апреля 2019 г.)
[2] «Car Engine Parts» (по состоянию на 24 сентября 2020 г.)
[3] «Как работают автомобильные двигатели» (по состоянию на 24 сентября 2020 г.)
[4] «Как работают системы впрыска топлива» (по состоянию на 24 сентября 2020 г.)
% PDF-1.4 % 1 0 объект > эндобдж 2 0 obj > / Содержание [5 0 R] >> эндобдж 3 0 obj > эндобдж 4 0 obj > эндобдж 5 0 obj > транслировать конечный поток эндобдж 6 0 obj > транслировать application / pdf
Как работает двигатель мотоцикла?
Это сбивает с толку.Это сбивает с толку. Так что давайте не будем начинать с плоской шестерки 1800 куб.
Современные велосипедные двигатели оснащены множеством технологий — иногда вам нужен словарь, чтобы просто перевести руководство. Но если вы не знаете, как работает двигатель, это может быть немного пугающе.
Во всем виноват он.
Но хорошая новость заключается в том, что современные двигатели по-прежнему работают практически на тех же принципах, что и, когда немец (который, возможно, знал) по имени Николас Отто построил первый из них в 1876 году.И это уже больше, чем знают многие эксперты по пабам, так что у нас хорошее начало.
Основы двигателя мотоцикла
История начинается с взрыва внутри небольшого замкнутого пространства. Взрыв — это не взрыв; это контролируемое сжигание смеси бензина и воздуха — бензин попал в пространство, будучи впрыснутым из инжектора, а воздух поступил из атмосферы. Взрыв / ожог также называется сгоранием, как в «двигателе внутреннего сгорания». А небольшое ограниченное пространство называется камерой сгорания.
Действительно важные детали — ваш базовый двигатель
В крыше камеры сгорания находится свеча зажигания, которая зажигает искру или воспламеняет топливно-воздушную смесь и начинает сгорание. Этот бит называется зажиганием.
Газы, горящие в небольших помещениях, быстро расширяются. Дно камеры сгорания на самом деле является верхом поршня, и, к счастью, он скользит вниз внутри стенок цилиндра, называемого «цилиндром». Говорите, что вам нравится об инженерах, но они логичны.
Поршень соединен со штоком, называемым «шатун» (видите?) — сокращенно шатун или просто шток. Шток соединен с большой вещью типа оси, называемой кривошипом. Когда сгорание толкает поршень и шатун вниз, они поворачивают кривошип.
Импульс в кривошипе (который сравнительно тяжелый) теперь снова отбрасывает шатун и поршень обратно вверх по цилиндру. Это полезно, потому что при этом он выталкивает весь сгоревший выхлопной газ из цилиндра через пару маленьких клапанов, которые только что открылись, и выводит его в выхлоп.Здесь есть один хитрый момент — время открытия и закрытия клапанов контролируется цепью, идущей от кривошипа обратно к шпинделю (или распределительному валу) над клапанами, и заставляет их открываться именно тогда, когда это необходимо.
Уф, пока все хорошо. Но работа наполовину сделана. Нам нужно, чтобы в камеру сгорания попало больше бензина и воздуха.
Полный четырехтактный цикл. Это снотворно.
Теперь поршень снова находится в верхней точке своего хода.Но кривошип все еще имеет импульс и все еще вращается, и он начинает тянуть поршень обратно по цилиндру, что является идеальной возможностью открыть еще одну пару клапанов (управляемых другим распределительным валом) и позволить низкому давлению опускающегося поршня потянуться. свежий импульс топливно-воздушной смеси в цилиндр, немного похожий на набирание крови из шприца.
Еще раз поршень достигает нижней точки своего хода, и цилиндр над ним заполнен завихренной топливно-воздушной смесью. По-прежнему приводимый в действие моментом кривошипа, поршень снова начинает подниматься во второй раз, что сжимает смесь.Когда поршень достигает вершины, свеча зажигания снова зажигает искру, воспламеняя смесь и снова толкая поршень вниз по цилиндру.
Итак, это полный цикл двигателя внутреннего сгорания. Если вы считаете, вы поймете, что поршень фактически совершал два хода вверх и два хода вниз за цикл — вот почему он называется четырехтактным двигателем (есть много других типов двигателей — двухтактные, ванкельные, дизели и т. д. — но почти все современные мотоциклетные двигатели четырехтактные).
Четыре удара часто сокращают до запоминающихся глаголов: в порядке, описанном выше, это будет удар, удар, сосать, сжимать (но чаще приказывают сосать, сжимать, стучать, дуть, потому что он лучше спотыкается о язык. ).
Итак, теперь все, что у нас есть, — это летящий вверх и вниз поршень и вращающийся кривошип. Как это заставляет байк двигаться вперед?
Как вы понимаете, четырехтактный цикл, описанный выше, происходит очень и очень быстро. Невероятно быстро. Когда ваш велосипед тикает, кривошип будет вращаться со скоростью около 1200 оборотов в минуту.Это 600 сосаний, 600 нажатий, 600 ударов и 600 ударов каждую минуту (потому что каждый из них составляет половину оборота рукоятки). И это на цилиндр.
Итак, кривошип вращается очень быстро, но если вы затем просто соедините его цепью с задним колесом, у него будет достаточно силы только для того, чтобы вести мотоцикл очень, очень медленно, и он будет крутить гайки, чтобы сделать Это. Представьте, что вы выбираете первую передачу на мотоцикле, а затем пытаетесь крутить педали при спуске с горы; то же самое.
Что нам нужно сделать, так это как-то выбрать более высокую передачу на нашем мотоцикле.Нам нужна система шестерен, чтобы замедлить скорость вращения кривошипа, и которая затем — из-за явления, называемого механическим преимуществом — фактически увеличивает силу силы (также называемую крутящим моментом) до точки, при которой мы можем управлять двигателем. мотоцикл вперед с приличной скоростью, но с более разумной частотой вращения двигателя. Мы хотим поменять местами высокую частоту вращения коленчатого вала и низкий крутящий момент на низкую частоту вращения коленчатого вала и высокий крутящий момент.
А, как насчет коробки передач? Итак, на конце кривошипа есть зубец или шестерня, которая вращает кучу других шестерен разных размеров — и мы можем выбрать, какую из них хотим, с помощью хитроумного механизма, называемого рычагом переключения передач, — до того, как появится привод, медленнее, но гораздо сильнее, на выходной передаче — и отсюда мы можем зацепить ее цепью и привести в движение заднее колесо.
Теперь у вашего велосипеда работает двигатель, и он движется. Ура!
Это рисунок двигателя Triumph Trophy. Вы можете увидеть три поршня в линию, каждый на конце шатуна и вращающий кривошип под ним. Вы также можете увидеть два распредвала впускных и выпускных клапанов в верхней части двигателя, приводящие в действие клапаны. Большая шестерня сразу за корзиной сцепления принимает привод от кривошипа и передает его в коробку передач — группу шестерен.Выход привода — косозубая коническая шестерня внизу справа. У Trophy есть привод вала, и вы можете видеть, что его косозубая коническая шестерня принимает выходной сигнал коробки передач.
Конечно, все вышесказанное описывает процесс только одного поршня, штока и цилиндра. Вы знаете, что велосипеды могут иметь один, два, три, четыре, не часто пять, но иногда и до шести цилиндров. Они могут быть расположены необычным и чудесным образом — рядом друг с другом (параллельные близнецы или рядные тройки, четверки или шестерки), в форме V (V-образные или V-образные четверки) или лицом друг к другу (плоские двойные, плоские четыре, даже плоская шесть).
Количество цилиндров и способ их расположения играют огромную роль в определении не только характера вашего двигателя (как он вибрирует и как он передает свою мощность при открытии дроссельной заслонки), но и в управлении — и размер — вашего велосипеда. Из-за этого некоторые конфигурации цилиндров подходят для определенных типов езды — поэтому одиночные цилиндры хорошо работают на мотоциклах для бездорожья, но не так хорошо на туристических велосипедах. Из четырехцилиндрового двигателя получаются хорошие двигатели для спортивных мотоциклов, но плохие внедорожные двигатели.
Конечно, это только самое основное описание того, как работает двигатель вашего велосипеда.У каждого двигателя есть свои сильные стороны и свои особенности конструкции; он может быть с наддувом, с регулируемым клапаном или полуавтоматической коробкой передач.
Самое прекрасное в четырехтактном двигателе — это когда вы смотрите на его рисунок или анимацию на Youtube и вдруг впервые понимаете волшебную взаимосвязь поршня, штока, кривошипа, распределительного вала и клапанов. Это особенный момент, который может вдохновить инженеров на всю жизнь. Это тот самый момент Эврики, который когда-то вдохновлял могущественного Соитиро Хонда — и, без сомнения, всех остальных разработчиков двигателей, больших или малых.
ВИДЕО — Как работает двигатель мотоцикла
Мотоциклетные двигатели — как это работает ?!
Как работает двигатель мотоцикла; сосать, сжимать, бухать, дуть.
Проект двигателя внутреннего сгоранияпо JSTOR
АбстрактныйРЕЗЮМЕ Проектирование двигателя внутреннего сгорания — это сложная операция, в которой необходимо учитывать большое количество переменных. В промышленной сфере новый проект двигателя внутреннего сгорания начинается с разработки хорошо зарекомендовавшего себя решения и опыта конструкторов. Целью этого исследования является разработка серии процедур для проектирования и проверки всех основных компонентов двигателя, начиная с глубокого библиографического исследования.Каждый компонент двигателя (коленчатый вал, поршень, поршневой палец, шатун, блок двигателя, головка двигателя, подшипники и клапанный механизм) имеет свой собственный интерфейс для проектирования и проверки. Прежде всего, был проведен глубокий библиографический анализ, чтобы найти лучшие методики проектирования и ряд геометрических и термодинамических данных для типового двигателя внутреннего сгорания. Все эти данные используются в качестве входных данных для расчета. Большое количество входных данных является общим для всех компонентов, и они реализованы в интерфейсе ввода, в то время как другая информация, такая как материал компонентов или типичный геометрический размер, запрашивается в интерфейсе конкретного компонента.
Информация о журналеМеждународный журнал двигателей внутреннего сгорания SAE — это научный рецензируемый исследовательский журнал, посвященный науке и технике по двигателям внутреннего сгорания. Журнал освещает инновационные и архивные технические отчеты по всем аспектам разработки двигателей внутреннего сгорания, включая исследования, проектирование, анализ, контроль и выбросы. Стремясь стать всемирно признанным исчерпывающим источником для исследователей и инженеров в области исследований и разработок двигателей, журнал публикует только те технические отчеты, которые считаются имеющими значительное и долгосрочное влияние на разработку и конструкцию двигателей.
Информация об издателеSAE International — это глобальная ассоциация, объединяющая более 128 000 инженеров и технических экспертов в аэрокосмической, автомобильной и коммерческой промышленности.Основные направления деятельности SAE International — это обучение на протяжении всей жизни и добровольная разработка консенсусных стандартов. Благотворительным подразделением SAE International является SAE Foundation, который поддерживает множество программ, включая A World In Motion® и Collegiate Design Series.
Двигатель внутреннего сгорания — Конструкция двигателя внутреннего сгорания — цилиндр, топливо, коленчатый вал и поршень
Двигатели внутреннего сгорания обычно используют возвратно-поступательное движение, хотя газовая турбина , ракетные и роторные двигатели являются примерами других типов двигателей внутреннего сгорания.Однако поршневые двигатели внутреннего сгорания являются наиболее распространенными и используются в большинстве автомобилей, грузовиков, мотоциклов и других машин с приводом от двигателя.
Самыми основными компонентами двигателя внутреннего сгорания являются цилиндр, поршень и коленчатый вал. К ним прикреплены другие компоненты, которые повышают эффективность возвратно-поступательного движения и преобразуют это движение во вращательное движение коленчатого вала. Топливо должно поступать в цилиндр, а выхлоп, образованный взрывом топлива, должен обеспечивать выход из цилиндра.Также необходимо произвести зажигание или зажигание топлива. В поршневом двигателе внутреннего сгорания это делается одним из двух способов.
Дизельные двигатели также называют двигателями сжатия, поскольку они используют сжатие для самовоспламенения топлива. Воздух сжимается, то есть выталкивается в небольшое пространство цилиндра. Сжатие вызывает нагревание воздуха; когда топливо попадает в горячий сжатый воздух, топливо взрывается. Давление , создаваемое сжатием, требует, чтобы дизельные двигатели были более прочными и, следовательно, тяжелее, чем бензиновые двигатели, но они более мощные и требуют менее дорогостоящего топлива.Дизельные двигатели обычно используются в больших транспортных средствах, таких как грузовики и тяжелая строительная техника, или в стационарных машинах.
Бензиновые двигатели также называют двигателями с искровым зажиганием, потому что они зависят от искры электричества, которая вызывает взрыв топлива в цилиндре. Этот газовый двигатель легче дизельного двигателя и требует более очищенного топлива.
В двигателе цилиндр размещен внутри блока цилиндров, достаточно прочного, чтобы сдерживать взрывы топлива.Внутри цилиндра находится поршень, который точно соответствует цилиндру. Поршни обычно имеют куполообразную форму вверху и полую внизу. Поршень прикреплен через шатун, установленный в полой нижней части, к коленчатому валу, который преобразует движение поршня вверх и вниз в круговое движение. Это возможно, потому что коленчатый вал не прямой, а имеет изогнутую часть (по одной на каждый цилиндр), называемую кривошипом.
Аналогичная конструкция приводит в движение велосипед. При езде на велосипеде верхняя часть ноги человека похожа на поршень.От колена до стопы нога действует как шатун, который прикрепляется к коленчатому валу с помощью кривошипа или педального узла велосипеда. Когда сила прикладывается к верхней части ноги, эти части начинают двигаться. Возвратно-поступательное движение голени преобразуется во вращательное или вращательное движение коленчатого вала.
Обратите внимание, что при езде на велосипеде нога делает два движения, одно вниз и одно вверх, чтобы завершить цикл вращения педалей. Это так называемые удары. Поскольку двигатель также должен всасывать топливо и снова выпускать топливо, большинство двигателей используют четыре хода для каждого цикла, который совершает поршень.Первый ход начинается, когда поршень оказывается в верхней части цилиндра, называемой головкой цилиндра. При его опускании в цилиндре создается разрежение . Это потому, что поршень и цилиндр образуют герметичное пространство. Когда поршень опускается, пространство между ним и головкой блока цилиндров увеличивается, а количество воздуха остается прежним. Этот вакуум помогает подавать топливо в цилиндр, подобно действию легких. Поэтому этот ход называется тактом впуска.
Следующий ход, называемый тактом сжатия, происходит, когда поршень снова подталкивается вверх внутри цилиндра, сжимая или сжимая топливо в более тесное и тесное пространство. Сжатие топлива в верхней части цилиндра вызывает нагревание воздуха, что также нагревает топливо. Сжатие топлива также облегчает воспламенение и делает взрыв более мощным. У расширяющихся газов взрыва меньше места, а это означает, что они будут сильнее давить на поршень, чтобы уйти.
В верхней части такта сжатия топливо воспламеняется, вызывая взрыв, толкающий поршень вниз. Этот ход называется рабочим ходом, и это ход, при котором вращается коленчатый вал. Последний ход, такт выпуска, снова поднимает поршень вверх, который вытесняет выхлопные газы, образовавшиеся в результате взрыва, из цилиндра через выпускной клапан. Эти четыре удара также обычно называют «сосание, сжатие, удар и удар». Двухтактные двигатели исключают такты впуска и выпуска, комбинируя их с тактами сжатия и увеличения мощности.Это позволяет создать более легкий и мощный двигатель — по сравнению с размером двигателя — требующий менее сложной конструкции. Но двухтактный цикл — менее эффективный метод сжигания топлива. Остаток несгоревшего топлива остается внутри цилиндра, что препятствует сгоранию. Двухтактный двигатель также воспламеняет топливо в два раза чаще, чем четырехтактный двигатель, что увеличивает износ деталей двигателя. Поэтому двухтактные двигатели используются в основном там, где требуется двигатель меньшего размера, например, на некоторых мотоциклах, и с небольшими инструментами.
Для горения требуется присутствие кислорода, поэтому для воспламенения топливо необходимо смешать с воздухом. В дизельных двигателях топливо подается непосредственно для реакции с горячим воздухом внутри цилиндра. Однако двигатели с искровым зажиганием сначала смешивают топливо с воздухом вне цилиндра. Это делается либо через карбюратор, либо через систему впрыска топлива. Оба устройства испаряют бензин и смешивают его с воздухом в соотношении , что составляет примерно 14 частей воздуха на каждую часть бензина.Дроссельная заслонка в карбюраторе регулирует количество воздуха, смешиваемого с топливом; на другом конце дроссельная заслонка контролирует, сколько топливной смеси будет отправлено в цилиндр.
Вакуум, создаваемый при движении поршня вниз по цилиндру, втягивает топливо в цилиндр. Поршень должен точно входить в цилиндр, чтобы создать этот вакуум. Резиновые компрессионные кольца, вставленные в канавки поршня, обеспечивают герметичность посадки. Бензин поступает в цилиндр через впускной клапан.Затем бензин сжимается в цилиндр следующим движением поршня в ожидании воспламенения.
Двигатель внутреннего сгорания может иметь от одного до двенадцати или более цилиндров, которые действуют вместе в точно рассчитанной по времени последовательности для приведения в движение коленчатого вала. Велосипедиста на велосипеде можно описать как двухцилиндровый двигатель, каждая нога которого помогает другой, создавая мощность для управления велосипедом и подтягивая друг друга в цикле движений. Автомобили обычно имеют четырех-, шести- или восьмицилиндровые двигатели, хотя также доступны двух- и двенадцатицилиндровые двигатели.Количество цилиндров влияет на рабочий объем двигателя, то есть на общий объем топлива, прошедшего через цилиндры. Больший рабочий объем позволяет сжигать больше топлива, создавая больше энергии для привода коленчатого вала.
Искра попадает через свечу зажигания, расположенную в головке блока цилиндров. Искра вызывает взрыв бензина. Свечи зажигания содержат два конца из металла , называемые электродами, которые проходят вниз в цилиндр. У каждого цилиндра своя свеча зажигания.Когда через свечу зажигания проходит электрический ток , ток перескакивает с одного электрода на другой, создавая искру.
Этот электрический ток исходит от батареи . Однако ток батареи недостаточно силен, чтобы вызвать искру, необходимую для воспламенения топлива. Поэтому он проходит через трансформатор , который значительно увеличивает его напряжение или силу. Затем ток можно направить на свечу зажигания.
Однако в случае двигателя с двумя или более цилиндрами искра должна направляться в каждый цилиндр по очереди.Последовательность срабатывания цилиндров должна быть рассчитана таким образом, чтобы, пока один поршень находился в рабочем такте, другой поршень находился в такте сжатия. Таким образом, сила, действующая на коленчатый вал, может поддерживаться постоянной, что позволяет двигателю работать плавно. Количество цилиндров влияет на плавность работы двигателя; чем больше цилиндров, тем постояннее усилие на коленчатом валу и тем плавнее будет работать двигатель.
Время срабатывания цилиндров регулируется распределителем.Когда ток поступает в распределитель, он направляется к свечам зажигания через провода, по одному на каждую свечу зажигания. Механические распределители — это, по сути, вращающиеся роторы, которые по очереди подают ток в каждый провод. Электронные системы зажигания используют компьютерные компоненты для выполнения этой задачи.
В самых маленьких двигателях используется аккумулятор, который при разряде просто заменяется. Однако в большинстве двигателей предусмотрена возможность перезарядки аккумулятора, используя движение вращающегося коленчатого вала для выработки тока обратно в аккумулятор.
Поршень или поршни давят на коленчатый вал и тянут его вверх, вызывая его вращение. Это преобразование возвратно-поступательного движения поршня во вращательное движение коленчатого вала возможно, потому что для каждого поршня коленчатый вал имеет кривошип, то есть секцию, установленную под углом к движению вверх и вниз положения . На коленчатом валу с двумя или более цилиндрами эти кривошипы также установлены под углом друг к другу, что позволяет им работать согласованно. Когда один поршень толкает кривошип вниз, второй кривошип толкает его поршень вверх.
Большое металлическое колесо, похожее на маховик, прикреплено к одному концу коленчатого вала. Он предназначен для поддержания постоянного движения коленчатого вала. Это необходимо для четырехтактного двигателя, поскольку поршни совершают рабочий ход только один раз на каждые четыре хода. Маховик обеспечивает импульс для переноса коленчатого вала во время его движения до тех пор, пока он не получит следующий рабочий ход. Он делает это с помощью инерции, то есть принципа, согласно которому движущийся объект будет стремиться оставаться в движении.Как только маховик приводится в движение поворотом коленчатого вала, он продолжает двигаться и вращать коленчатый вал. Однако чем больше цилиндров в двигателе, тем меньше ему нужно будет полагаться на движение маховика, потому что большее количество поршней будет поддерживать вращение коленчатого вала.
После того, как коленчатый вал вращается, его движение можно адаптировать для самых разных целей, прикрепив шестерни, , ремни или другие устройства. Колеса можно заставить вращаться, пропеллеры можно заставить вращаться, или двигатель можно использовать просто для выработки электроэнергии.К коленчатому валу также прикреплен дополнительный вал, называемый распределительным валом, который открывает и закрывает впускные и выпускные клапаны каждого цилиндра в последовательности с четырехтактным циклом поршней. Кулачок — это колесо, имеющее более или менее форму яйца, с длинным и коротким концом. К распределительному валу крепится несколько кулачков в зависимости от количества цилиндров двигателя. Сверху кулачков установлены толкатели, по два на каждый цилиндр, которые открывают и закрывают клапаны. Когда распределительный вал вращается, короткие концы позволяют толкателям отойти от клапана, заставляя клапан открываться; длинные концы кулачков толкают стержни назад к клапану, снова закрывая его.В некоторых двигателях, называемых двигателями с верхним расположением кулачка, распределительный вал опирается непосредственно на клапаны, что устраняет необходимость в узле толкателя. Двухтактные двигатели, поскольку впуск и выпуск достигаются за счет движения поршня над портами или отверстиями в стенке цилиндра, не требуют распределительного вала.
Коленчатый вал может приводить в действие еще два компонента: системы охлаждения и смазки. Взрыв топлива создает сильное тепло, которое быстро приведет к перегреву двигателя и даже к расплавлению, если он не будет должным образом рассеян или отведен.Охлаждение достигается двумя способами: через систему охлаждения и, в меньшей степени, через систему смазки.
Есть два типа систем охлаждения. В системе жидкостного охлаждения используется воды, , которую часто смешивают с антифризом для предотвращения замерзания. Антифриз снижает температуру замерзания, а также повышает точку кипения воды. Вода, которая очень хорошо собирает тепло, прокачивается вокруг двигателя через ряд каналов, содержащихся в рубашке.Затем вода циркулирует в радиаторе, который содержит множество трубок и тонких металлических пластин, увеличивающих площадь поверхности воды. Вентилятор, прикрепленный к радиатору, пропускает воздух по трубке, дополнительно снижая температуру воды . И насос, и вентилятор приводятся в действие движением коленчатого вала.
В системах с воздушным охлаждением для отвода тепла от двигателя используется воздух, а не вода. В большинстве мотоциклов, многих небольших самолетов и других машин, движение которых производит большое количество ветра , используются системы с воздушным охлаждением.В них металлические ребра прикреплены к внешней стороне цилиндров, создавая большую площадь поверхности; когда воздух проходит через ребра, тепло, передаваемое к металлическим ребрам от цилиндра, уносится воздухом.
Смазка двигателя жизненно важна для его работы. Движение частей друг относительно друга вызывает сильное трение , которое нагревает и вызывает износ деталей. Смазочные материалы, например масло, образуют тонкий слой между движущимися частями. Прохождение масла через двигатель также помогает отводить часть выделяемого тепла.
Коленчатый вал в нижней части двигателя упирается в картер. Он может быть заполнен маслом, или отдельный масляный поддон под картером служит резервуаром для масла.