Зачем сосед льет масло в пороги автомобиля — эксперт все объяснил — журнал За рулем
LADA
УАЗ
Kia
Hyundai
Renault
Toyota
Volkswagen
Skoda
Nissan
ГАЗ
BMW
Mercedes-Benz
Mitsubishi
Mazda
Ford
Все марки
Говорят, что можно легко предотвратить ржавчину в порогах с помощью слитого, уже использованного моторного масла. Есть и рекомендация, как проще это масло в пороги залить, чтобы не испачкаться.
Материалы по теме
Зачем водители держат в бардачке парафиновые свечи? Проверили лайфхак
Отжившее свое моторное масло — давний и популярный способ сохранения автомобильных порогов от ржавчины, уверяют в интернете. Им пользовались еще наши дедушки. Основная сложность в том, как эту самую отработку залить в пороги. Мы наткнулись на необычный способ: выход нашли… в краскопульте!
В интернете советуют найти использованный флакон от современных эмалей и лаков, который подходит к резьбе краскопульта.
Залить отработку во флакон, присоединить к «пистолету» и заполнить порог через сливные отверстия, которые откроются при снятии пластиковых накладок в дверной нише. Потом нужно поставить накладки на место и немного поездить на машине, чтобы масло равномерным слоем распределилось по нишам полости. Со временем отработка загустеет и превратится в плотную пленку, которая надолго сохранит металл от ржавчины. Такой процедуры хватает лет на семь-десять.
Мнение эксперта
Комментирует эксперт «За рулем» Алексей Ревин:
— Способ известен со времен, когда кузова автомобилей стали несущими, и, соответственно, у них появились силовые пороги коробчатого сечения. Но если в середине прошлого века никаких других способов защиты от коррозии не было, то сейчас существует масса вариантов.
Отработанное моторное масло — оно и есть отработанное. Его щелочное число, определяющее антикоррозионные свойства, уже стало заметно меньше. Оно не способно вытеснить влагу, если она оказалась где-то в щели в нижней части порогов. Ведь вода имеет большую плотность, а налитое сверху масло не даст воде высохнуть. Тем не менее масло ликвидирует доступ окислителя — кислорода, а потому коррозия будет замедлена. Запах после обработки сильным не будет, а вот капать масло на дорогу через малейшие щели может очень долго, пока не закончится, ведь оно не высыхает. Капли будут пачкать пол гаража и попадут на шины.
Материалы по теме
За ними заржавеет. Топ-5 быстро гниющих авто
Гораздо лучше работают специальные антикоррозионные составы, применять которые начали в скандинавских странах еще в начале второй половины прошлого века. Конкретно в пороги, хотя это далеко не все места автомобиля, которые следует защищать от коррозии, состав можно подать двумя способами. Первый — самостоятельно, приобретя аэрозольный баллончик с длинной трубочкой для распыления состава. Ну а второй и самый правильный — это провести комплексную антикоррозионную обработку автомобиля, при которой препараты двух типов профессионалы нанесут в скрытые полости автомобиля (включая пороги) и на его днище.
Материалы по теме
Рыжая смерть: 4 важных вопроса (и ответа) про коррозию
Что касается описанного способа нанесения, то он вызывает много вопросов. Если у человека есть краскопульт, то значит есть и система снабжения сжатым воздухом. Тогда лучше использовать специальное устройство для нанесения антикора, приобрести антикоррозионный препарат и «задуть» его в пороги. Вот это даст результат, близкий к профессиональной обработке.
***
Наш вердикт: советом воспользоваться можно, но зачем? Лучше подобрать более эффективный способ решения проблемы.
- Между прочим, ржавчина может служить и элементом декора. Есть компании, которые на этом специализируются.
- Уберечь пороги от внешнего механического воздействия и одновременно придать автомобилю индивидуальность помогут алюминиевые пороги-площадки турецкой компании Can Otomotiv.
- Не хватает места в салоне авто? Приезжайте в наш магазин — подберем недорогой багажник на крышу, посоветуем автобокс!
- «За рулем» теперь можно читать в Facebook.
Фото: Depositphotos и «За рулем»
Наше новое видео
Тест 9-местной Нивы! И необычной Гранты
3 искренних заблуждения при перевозке детей
50 л/100 км, автомат, пневмоподвеска — тест самого народного автомобиля СССР
Понравилась заметка? Подпишись и будешь всегда в курсе!
За рулем на Яндекс.Дзен
Новости smi2.ru
Как правильно заполнить отработкой пороги, чтобы они не гнили — Лайфхак
- Лайфхак
- Эксплуатация
Фото avto-oblast.ru
Отработка, то есть отжившее свое моторное масло, давний и популярный способ сохранения автомобильных порогов от ржавчины. Наверное, это самый известный метод, однако далеко не все автовладельцы знают, как правильно провернуть эту операцию. Портал «АвтоВзгляд» расставит все точки над «i».
Эдуард Раскин
Гнилые пороги — самая распространенная кузовная проблема в России. Реагенты в тандеме с природой и погодой, забитые стоки и просто повреждения быстро приводят этот кузовной элемент в негодность. Что делать? Правильно, залить отработкой. Казалось бы, чего придумывать велосипед, если этот рецепт придуман и испытан лет 50 назад? Однако не все так просто, как пишут на страницах журналов.
С материалом понятно, набрать старого лубриканта может каждый. Начиная с автосервисов и заканчивая собственным мотором, которому никогда не рано обновить смазку. Другой вопрос, как полученный состав доставить непосредственно внутрь порогов и добиться полного заполнения всех полостей и отверстий, наиболее подверженных коррозии.
Кто-то заливает через воронку, кто-то вводит промышленным шприцем, кто-то использует масленку. Долго, грязно, неприятно. Есть вариант намного проще: краскопульт. Да, вы не ослышались, компрессор с насадкой может сократить время и сделать эту грязную работу намного чище. Но начать стоит не с инструмента.
Фото 7gear.ru
Чтобы провести внутреннюю обработку порогов, нужно выбрать теплый летний день, а если точнее — теплый летний свободный вечер. Дело в том, что кузов автомобиля в целом и пороги в частности, должны быть теплыми. Далее следует отыскать пустой флакон от современных эмалей и лаков, который сделан так, чтобы надеваться непосредственно на резьбу красокопульта. Как вариант, попросить в любом малярном цеху — дадут несколько, еще и отблагодарят.
В полученную тару заливаем отработку, цепляем к «пистолету» — дюзу или сопло можно использовать фактически любое, какое не жалко — и начинаем заполнять порог через сливные отверстия, которые откроются, стоит лишь снять пластиковые накладки в дверной нише. Экономить материал не нужно, лейте от души. Пройдя круг, нужно вернуть пластик на место и завести мотор — впереди завершающая часть процедуры.
После заполнения порогов отработкой, надо на машине как следует прокатиться. Тогда и только тогда масло заполнит все ниши и полости, растечется ровным слоем. Резкие ускорения и спортивное торможение применять не обязательно, но 5—10 раз остановиться и вновь ускориться все же стоит. Отработка — густая, и ее перемещений чувствоваться не будет, сколько бы ее в порог не налили. Но со она загустеет и превратится в толстую и надежную пленку, которая сбережет металл от ржавчины. Кстати, несмотря на многочисленные рекомендации проводить эту процедуру ежегодно смысла нет — достаточно обновлять отработку каждые 4—5 лет.
347188
- Общество
- Социум
Цены на автогаз бьют рекорды
621639
- Общество
- Социум
Цены на автогаз бьют рекорды
621639
Подпишитесь на канал «Автовзгляд»:
- Telegram
- Яндекс.Дзен
подержанные авто, автосервис, ремонт, техническое обслуживание, моторное масло, лайфхак
Грунтовка и защита от ржавчины – 4 совета, как избежать ржавчины в автомобиле
Зимняя защита от ржавчины.
Получите защиту сейчас
Полная защита от ржавчины
Внутреннее покрытиеНанесите аэрозольный антикоррозийный воск на раму автомобиля, крылья, двери и другие детали.
Защита днищаНанесите качественное антикоррозионное покрытие на битумной основе, устойчивое к ударам дорожного мусора.
Позвоните сейчас
616-871-2699
Начните сегодня!
Несмотря на недавние достижения в области материалов и производства транспортных средств, коррозия все еще с нами. Вы вряд ли можете не заметить последствия ржавчины, когда едете на работу и с работы. Вид легковых и грузовых автомобилей с ржавыми крыльями, дверями и рамами сейчас так же обычен, как и десятилетия назад. На самом деле потребность в защите от коррозии стала как никогда актуальной.
Почему это? Многие эксперты по транспорту винят в этом новое поколение химикатов против обледенения дорог, особенно хлорид магния. Это соединение образует на кузове и стеклах автомобилей кристаллическую пленку, которую трудно смыть. «MagChlor» впитывает влагу из воздуха, и остатки на транспортном средстве становятся активно коррозионными при уровне влажности ниже 25 процентов. Угрозу усугубляет тот факт, что многие государственные учреждения используют хлорид магния для борьбы с пылью на грунтовых и гравийных дорогах. Для многих автомобилей, подвергающихся воздействию различных условий вождения, хлорид магния может быть круглогодичной проблемой, а не только сезонной.
К счастью, защита от ржавчины/коррозии все еще возможна. Выполняя регулярную программу нанесения антикоррозионного покрытия, антикоррозионного спрея и другого технического обслуживания, вы сможете поддерживать свой автомобиль в отличном состоянии. Вот как:
Механизм коррозии требует, чтобы электролит, обычно вода, вступал в контакт со сталью. Поэтому все, что вы можете сделать, чтобы предотвратить это взаимодействие, имеет решающее значение для достижения антикоррозионной защиты. Нанесение антикоррозионного аэрозольного воска помогает предотвратить внутреннюю ржавчину. Воск вводится в выбранные полости автомобиля, расположенные в дверях, капоте, раме багажника, крыльях, боковых панелях и панелях порогов. Затем он образует барьер, который предотвращает контакт электролита с металлом.
Нижняя часть автомобиля ежедневно подвергается ударам окружающей среды, что может привести к образованию ржавчины на половицах и тормозных магистралях. Качественное антикоррозионное покрытие на битумной основе, способное противостоять ударам дорожного мусора, может защитить днище и предотвратить образование ржавчины. Ключевым преимуществом продуктов на основе асфальта является то, что, в отличие от прорезиненных покрытий, они не отслаиваются и не отслаиваются.
Краска автомобиля также играет решающую роль в предотвращении коррозии автомобиля. Любые сколы или царапины следует немедленно обработать соответствующей краской для подкрашивания, которую можно приобрести в автосалоне. Если потребуется профессиональный кузовной ремонт, не откладывайте. Кроме того, не забудьте заменить антикоррозионные барьерные покрытия после завершения любого ремонта.
Одним из очень простых способов защиты автомобилей от коррозии является частая мойка автомобиля. Уделите особое внимание удалению всех химикатов с кузова и тщательно промойте колесные арки и днище. Никогда не мойте автомобиль с помощью посудомоечной машины или моющего средства для одежды! Такие продукты могут потускнеть или даже поцарапать краску. Рекомендуется использовать раствор для мойки автомобилей с нейтральным pH. В крайнем случае, детский шампунь сделает эту работу!
Выполняя каждый из этих четырех этапов защиты от коррозии, вы можете защитить свой автомобиль от ржавчины, получить от него больше удовольствия и повысить его стоимость при сдаче в аренду.
Предотвращение коррозии стальных мостов
(Вверху) Маляр наносит защитное покрытие на мост, чтобы защитить его от коррозии.
Исследователи FHWA оценивают точность и надежность трех наборов для тестирования хлоридов, чтобы определить их эффективность и точность.
Ежегодно федеральное правительство и транспортные департаменты штатов (DOT) тратят миллиарды долларов на ремонт и техническое обслуживание мостов из-за коррозии. На мостах коррозия чаще всего возникает, когда сталь подвергается воздействию атмосферных условий, таких как соль, влага и кислород. Чтобы предотвратить коррозию мостов, транспортные агентства наносят на сталь защитное покрытие.
Но, по словам доктора Бернарда Эпплмана, консультанта KTA-Tator, Inc. и бывшего исполнительного директора Общества защитных покрытий, если перед окраской на сталь наносится коррозионное вещество, защитное покрытие может преждевременно выйти из строя. «Растворимые соли, особенно соли хлора, которые не удаляются перед покраской, являются основной причиной раннего и часто катастрофического разрушения краски», — говорит Эпплман. Если краска выйдет из строя преждевременно, возникающая в результате коррозия в конечном итоге нарушит структурную целостность металла. «В конечном счете, это повреждение краски может потребовать капитального ремонта моста, что не только дорого обходится, но и создает неудобства для водителей», — добавляет он. Поэтому, прежде чем маляр моста нанесет защитное покрытие на новый стальной или реабилитированный мост, необходимо оценить чистоту поверхности.
В настоящее время почти все спецификации по окраске основаны на визуальных (или качественных) измерениях для определения готовности к нанесению защитных покрытий. Тем не менее, исследователи из Федерального управления автомобильных дорог (FHWA) ищут более точное количественное измерение, которое можно было бы использовать снова и снова для определения наличия коррозионных элементов на стали до нанесения покрытия. Одним из таких методов может быть проверка на хлорид.
Чтобы помочь инспекторам по покрытию мостов лучше оценить состояние стали перед покраской, FHWA недавно оценила три имеющихся в продаже набора для тестирования хлоридов, которые используются для определения чистоты стальных поверхностей. Цели состояли в том, чтобы оценить точность и прецизионность тестов и определить факторы, влияющие на их характеристики.
От визуальной до количественной оценки
Поскольку загрязняющие вещества могут влиять на характеристики покрытий мостов, инспекторам нужны точные методы для оценки чистоты стальных поверхностей перед покраской. Однако большинство методов, используемых сегодня, в лучшем случае являются качественными или полукачественными.
«Сегодня все стандарты уборки основаны на визуальном восприятии», — говорит Боб Коглер, руководитель исследовательской группы по проектированию и строительству мостов в FHWA. По словам Коглера, оценка чистоты стали с помощью визуальных стандартов может привести к спорам. «Инспектор может посмотреть на сталь и увидеть признаки того, что она недостаточно чистая, в то время как подрядчик может утверждать, что она достаточно чистая», — говорит он. «В какой-то степени, даже если у нас есть стандарты, это почти вопрос мнения, потому что сами стандарты являются качественными».
В 2001 году Центр проверки неразрушающего контроля FHWA завершил исследование, в ходе которого оценивалась точность метода визуального осмотра для определения состояния мостов. Исследование показало, что инспекторы значительно различаются в том, как они проводят плановые проверки. В частности, они различаются по способу присвоения оценок состояния.
«В конце концов, нам нужно сделать нашу оценку чистоты стальной поверхности количественной мерой, потому что это прояснит большую область споров по поводу работ по покраске мостов», — говорит Коглер. «Измерения [полученные с помощью тестовых наборов] скажут нам, насколько химически чистая [поверхность], а не только насколько чистой она выглядит. И это даст нам гораздо более точную оценку потенциальных характеристик краски».
Некоторые приложения, например, в судостроении, уже переходят к количественным методам оценки концентрации хлоридов на стальных поверхностях.
Проблема с хлоридом
Поскольку хлорид является основным загрязнителем поверхности и обычно является наиболее коррозионным агентом для стали, инспекторы могут проверить его на наличие хлорида перед покраской стальных поверхностей. Высокие концентрации хлорида могут привести к преждевременному разрушению покрытия, например, к ржавчине и расслаиванию — процессу, при котором покрытие начинает отделяться от стали. В конечном итоге ржавчина и отслоение покрытия могут разрушить структурную целостность металла. Хлорид представляет особую опасность для конструкций, которые засолены во время операций по борьбе с обледенением или расположены в морской среде, где концентрация хлоридных солей может быть высокой в морской воде и брызгах.
После пескоструйной обработки стальной поверхности или очистки водой под высоким давлением и перед нанесением покрытия инспектор должен оценить или проверить стальную поверхность на наличие хлоридов. Если визуальный осмотр или испытания показывают высокие концентрации хлоридов, металл необходимо снова очистить и провести повторные испытания.
Проведена оценка трех тестовых наборов для определения содержания хлоридов
В настоящее время инспекторы по покрытиям используют один из трех имеющихся в продаже тестовых наборов для количественной оценки уровня содержания хлоридов. Как правило, наборы представляют собой тест на мазок, тест на пластырь и тест на рукаве.
Во всех трех тестах используется жидкость, либо кислая жидкость, либо деионизированная вода, для растворения или извлечения хлоридов с поверхности стали в раствор. Затем инспектор проверяет раствор на концентрацию хлоридов. Тест мазка основан на влажных ватных шариках для извлечения хлорида с поверхности стали. В пластырном тесте используется шприц, содержащий экстракционную жидкость, для забора хлорида из области пластырного теста. А при испытании рукава хлорид извлекается в рукаве, содержащем жидкость, который прикреплен к стали.
По данным государственных DOT и мостовых инспекторов, все три теста показали противоречивые и сильно различающиеся результаты. Эти несоответствия могут быть связаны с различной эффективностью извлечения и чувствительностью обнаружения в тестах, а также с изменчивостью оператора.
Таким образом, исследователи FHWA изучили изменчивость и ограничения методов испытаний, чтобы установить методы, которые можно использовать для получения надежных и точных результатов испытаний концентрации хлоридов.
Экспериментальные процедуры
Исследователи проанализировали стальные панели в вертикальном положении. К панелям применяли четыре различных уровня концентрации хлоридов в диапазоне от 3 до 30 микрограммов на квадратный сантиметр (мг/см2), чтобы определить, влияет ли концентрация хлоридов на достоверность результатов. Согласно отраслевому правилу, после пескоструйной обработки мост должен быть окрашен в течение 4 часов. Поэтому исследователи проводили испытания в трех условиях, попадающих в эти временные рамки: в течение 1 минуты после легирования панелей (то есть искусственного загрязнения хлоридом), после старения легированных панелей при высокой температуре и умеренной влажности в течение 4 часов и после старения легированных панелей при высокой температуре и высокой влажности в течение 4 часов.
Детекторы для тестов тампоном, пластырем и гильзой представляют собой полоску для обнаружения ионов, четыре бутылки с жидкостями для титрования и пробирку для обнаружения ионов соответственно. Поскольку в патч-тесте могут использоваться две разные жидкости, кислая жидкость или деионизированная вода, исследователи провели дополнительные тесты, чтобы определить, какая жидкость содержит больше всего хлоридов. Поскольку исследователи обнаружили, что кислая жидкость извлекает больше хлоридов, чем деионизированная вода, в пластырном тесте использовалась кислая жидкость.
В общей сложности исследователи оценили каждый набор в 12 различных условиях (4 концентрации хлоридов и 3 условия старения), чтобы определить, как концентрации хлоридов и старение влияют на точность теста. Каждое испытание проводилось трижды тремя разными операторами в Лаборатории красок и коррозии Центра исследования автомобильных дорог Тернер-Фэрбэнк FHWA (TFHRC) в Маклине, штат Вирджиния.
Три метода определения содержания хлоридов Ниже приводится подробное описание того, как исследователи проводили тесты с использованием трех наборов. Мазок Тест на заплату Исследователь надежно приклеил заплату на стальную поверхность площадью 12,25 см2 (1,89 дюйма2). Затем исследователь вводил 1,5 мл (0,05 жидких унций) экстракционной жидкости в пластырь, затем извлекал две трети жидкости из пластыря и повторно вводил ее для более тщательного перемешивания жидкости. Затем исследователь тер пластырь пальцем в течение 1 минуты, чтобы улучшить растворимость хлоридов. ![]() Тест рукава |
Сравнение результатов
Исследователи выявили сильные и слабые стороны каждого теста. Исследовательская группа признает, что, поскольку эти тесты проводились в лаборатории, где процедуры тщательно контролировались, результаты экспериментов могут быть лучше, чем можно было бы ожидать в полевых условиях.
Из трех тестов мазок выявил наибольшее количество хлоридов, а также дал наиболее воспроизводимые данные. Для свежелегированной стали (т. е. определенного количества хлорида, нанесенного на сталь для испытаний) при испытании мазком было извлечено приблизительно от 70 до 100 процентов хлорида. Этот тест также имел наименьшую вариабельность.
В тесте мазка используется полоска для обнаружения ионов, которая может определять концентрацию хлорида только выше 30 частей на миллион (ppm). Однако большая площадь экстракции компенсирует предел обнаружения. Исследователи обнаружили, что самый низкий уровень обнаружения хлоридов, возможный в используемых лабораторных условиях, составлял 3 мг/см2.
Одним из недостатков испытания мазком является то, что его необходимо проводить очень осторожно, что может быть затруднительно в полевых условиях, где оператор или инспектор может находиться высоко на лестнице, проверяющей стальные подвесные потолки. Поскольку он проводится в открытой среде, вода может легко капать и испаряться, что приведет к уменьшению извлечения хлоридов и, следовательно, к неточным результатам.
В отличие от мазка, пластырь представляет собой закрытую экстракционную систему, предотвращающую испарение и потерю жидкости. Однако оператор все равно может терять жидкость, если заплата неплотно прилегает к стальной поверхности или если шприц, который используется для забора жидкости, неправильно вставлен в заплату. В любом случае потеря даже небольшого количества экстракционной жидкости приведет к неточным измерениям содержания хлоридов.
Патч-тест с жидкостями для титрования, используемыми в качестве детектора, также обеспечивает высокое извлечение хлоридов. Но результаты оказались самыми ненадежными из трех тестов, о чем свидетельствует более высокая погрешность. Одной из возможных причин ошибки является изменчивость количества капель, необходимых для достижения конечной точки титрования (то есть изменение цвета). Если изменение цвета происходит между двумя каплями, некоторые операторы будут использовать дополнительную каплю, в то время как другие будут использовать на одну каплю меньше. Количество используемых капель может варьироваться в зависимости от оператора, или один и тот же оператор может использовать разное количество капель для каждого проведенного теста. Это изменение количества капель повлияет на концентрацию хлорида.
Дополнительным недостатком патч-теста является то, что он показывает только минимальные и максимальные значения, а не фактические значения. Однако инспектор по покрытиям может быть консервативен и использовать максимальное значение, чтобы определить, следует ли продолжать работу по окраске.
Последний недостаток пластырного теста заключается в том, что для кислой жидкости в качестве одного из титрантов требуется нитрат ртути. Поскольку ртуть является опасным отходом, операторы или инспекторы должны следовать строгим правилам при утилизации жидкости.
Тест рукава, как и тест пластыря, представляет собой закрытую систему с небольшим риском потери жидкости, но экстракционная жидкость может быть потеряна, если рукав не плотно прилегает к стальной поверхности. Если жидкость потеряна, тест приведет к ненадежным измерениям хлоридов.
Тест рукава оказался более эффективным при извлечении хлорида при более высоких концентрациях, чем при более низких концентрациях. Низкая скорость извлечения хлоридов при более низких концентрациях может быть связана с низкой чувствительностью и нечетким разделением цветов на конце трубки для обнаружения ионов с низкими показаниями. Чувствительность можно повысить, если уменьшить объем экстракции или увеличить площадь экстракции. Погрешность теста на рукаве была между погрешностью тампона и теста на пластырь.
Для пластического теста исследователь вводит жидкость для извлечения хлоридов в участок на вертикальной стальной пластине. Для анализа мазка исследователь использует ватный тампон и деионизированную воду для обнаружения и извлечения хлоридов из стальной пластины.Мазок-тест | Патч-тест | Проверка рукава | |
---|---|---|---|
Тип системы | Открыть | закрыто | закрыто |
Метод обнаружения | Полоска для обнаружения ионов | Титрование | Трубка для обнаружения ионов |
Площадь, см2 | 150 | 12,25 | 10 |
Экстракционная жидкость, мл | 15 | 3 | 10 |
Площадь (см2)/объем (мл) | 10 | 4.![]() | 1 |
Значение pH экстракционной жидкости | Деионизированная вода, pH = 6,7 | Кислотный, pH = 3,9 | Кислотный, pH = 4,2 |
В таблице указаны тип системы, метод обнаружения, площадь экстракции, объем экстракционной жидкости, отношение площади к объему жидкости и значение pH экстракционной жидкости для каждого из трех тестовых наборов. Источник: FHWA. |
Влажность влияет на результаты испытаний
Важный вывод исследования заключается в том, что высокая температура и влажность влияют на результаты испытаний. Когда легированные панели подвергались старению при высокой температуре — 37 градусов Цельсия (98,6 градусов по Фаренгейту) — в течение 4 часов в двух различных условиях влажности, восстановление хлоридов было меньше, чем у панелей со свежей добавкой. Однако исследователи отметили значительную разницу между умеренной и высокой влажностью. При относительной влажности 57 процентов извлечение хлоридов снижалось лишь незначительно. Но во всех трех испытаниях извлечение хлоридов значительно снизилось при относительной влажности 78 процентов.

Исследователи предполагают, что низкий уровень ржавчины образовался после того, как сталь подверглась воздействию высокой температуры и влажности в течение 4 часов. Невидимая ржавчина захватила хлорид, что затруднило его извлечение.
Эти результаты предполагают, что инспекторы должны определить концентрацию хлоридов на поверхности как можно скорее после взрывных работ. Любая задержка, особенно в жаркой и влажной среде, может привести к ошибочно заниженным значениям содержания хлоридов. Если эти низкие значения содержания хлоридов находятся в допустимых пределах для защитного покрытия, инспектор может принять решение о нанесении покрытия на стальную поверхность, которая в действительности имеет неприемлемые уровни содержания хлоридов под невидимой ржавчиной.
Использование результатов исследования
Хотя необходимы дополнительные исследования, результаты исследования FHWA могут предоставить ценную информацию, которую инспекторы по покрытиям могут применить в полевых условиях уже сегодня.
Сводка результатов испытаний
Мазок-тест | Патч-тест | Проверка рукава | |
---|---|---|---|
Концентрация хлорида | Высокий (10)a | Средний (4.1) | Низкий (1) |
Потери экстракционной жидкости | Да | Нет, если накладка прочно приклеена к стали | Нет, если заплата плотно прилегает к стали |
Минимальный порог | 3 мкг/см2 | ~ 1 мкг/см2 | ~ 5 мкг/см2 |
Воспроизводимость результатов | Высокий (для тестов выше 30 частей на миллион) | Низкий (даны только минимальные и максимальные значения) | Высокий (для тестов выше 9 частей на миллион) |
Чувствительность обнаружения | > 30 частей на миллион | > 1 мкг/см2 (4 части на миллион) | > 5 частей на миллион |
Диапазон обнаружения | 30–600 частей на миллион | 1 — 50 мкг/см2 | 1–50 частей на миллион (= 1–50 мкг/см2 |
a: Отношение площади извлечения к объему экстрагируемой жидкости.![]() |
«Инспектор по покрытиям может использовать результаты исследования, выбирая метод, основанный на ожидаемых уровнях содержания хлоридов и возникающих условиях окружающей среды», — говорит Эпплман. «Например, если поверхность подвергалась воздействию солнца в жаркий день, инспектор по покрытиям может выбрать другой метод, а не мазок, поскольку этот метод приведет к неточному извлечению хлоридов из-за испарения воды во время экстракции на открытом воздухе. другой пример, если бы критерий приемлемости был низким, например, 3 микрограмма на квадратный сантиметр, инспектор по покрытиям избегал бы использования метода с низкой чувствительностью».
Советы по повышению точности тестов на хлориды
|
Из лаборатории в поле
Следующим шагом будет оценка эффективности тестовых наборов для восстановления хлоридов в полевых условиях, чтобы определить, следует ли включать количественные тесты в спецификации для окраски мостов. «Это исследование [было проведено] в лаборатории в контролируемых условиях, которые подходят для фундаментальных исследований», — говорит Коглер. «[Но] нам необходимо оценить эти методы в полевых условиях в сотрудничестве с владельцами мостов штата, чтобы увидеть, какие улучшения нам нужно внести в эти тесты или процедуры, прежде чем мы включим [их] в наши спецификации».
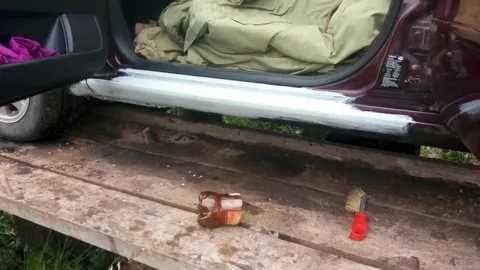
Будущие исследования будут оценивать не только точность и надежность тестов, но и удобство их использования. «Представьте, что вы поднимаетесь по лестнице к опоре моста, а на мосту есть движение», — говорит Коглер. «У вас есть шприц с водой, и вам нужно приклеить эту липкую штуку к мосту и использовать пипетку. Проведение теста занимает некоторое время. Несмотря на то, что [тесты] были разработаны для использования в полевых условиях, мы нужно выяснить, насколько они действительно полезны».
Большой вопрос заключается в том, должны ли инспекторы мостов прямо сейчас требовать проверки на хлориды для всех работ по окраске мостов, и являются ли тесты точными и достаточно удобными для пользователя. В ходе лабораторных испытаний исследователи обнаружили, что тестирование необходимо проводить очень осторожно, чтобы обеспечить согласованность результатов. «Это исследование предоставляет одни из первых реальных объективных данных об этих тестовых наборах», — говорит Коглер. «Анализ дает нам представление о том, где сейчас находится технология и что нам нужно сделать, чтобы улучшить ее».
Шуанг-Линг Чонг, доктор философии, , старший химик-исследователь в FHWA с 1989 года. В обязанности Чонга входило управление Лабораторией красок и коррозии, изучение ускоренных испытаний покрытий мостов и разработка методов определения характеристик покрытий. материалов и неудач. Чонг получила докторскую степень. по физической химии в 1969 г. в Рутгерском государственном университете Нью-Джерси.
Дополнительные сведения об экспериментальных методах, использованных в исследовании, доступны в статье д-ра Чонга «Внутрилабораторная оценка коммерческих тестовых наборов для количественного определения хлоридов на стальных поверхностях», опубликованной в Journal of Protective Coatings and Linings, стр. 42, август 2003 г.