Антикоррозионные покрытия ВМП
Чтобы посмотреть
представительство
в Вашем регионе,
перейдите в раздел контакты.
ВМП в социальных сетях: | |
Любые сооружения подвергаются негативному воздействию климатических и технологических факторов. Осадки, солнечное излучение, перепады температур, конденсация, загрязненная атмосфера ускоряют разрушение конструкционных материалов. В большей степени это касается промышленных объектов, так как они эксплуатируются в высокоагрессивной среде. Между тем длительная бесперебойная и безопасная работа – необходимое условие для всех сооружений. Поэтому выбор способа антикоррозийной защиты объектов – одна из важнейших задач при их строительстве и ремонте.
В ассортименте холдинга ВМП более 50 материалов для антикоррозийной защиты на полиуретановой, эпоксидной, винилово-эпоксидной и других основах, изготовленных по оригинальным рецептурам.
цинкнаполненные композиции,
грунтовки с ингибитором коррозии,
грунтовки с антикоррозионными пигментами,
грунт-эмали,
лаки.
композиции с антикоррозионными пигментами,
композиции с чешуйчатыми пигментами,
УФ-стойкие эмали.
Типовые системы антикоррозионных покрытий ВМП
Система антикоррозионного покрытия может состоять из одного или нескольких слоев лакокрасочных материалов. Для создания толстослойных покрытий применяются грунт-эмали с высоким сухим остатком. Типовые двухслойные системы состоят из грунтовки и эмали, которая создает дополнительный защитный барьер и выполняет декоративную функцию.
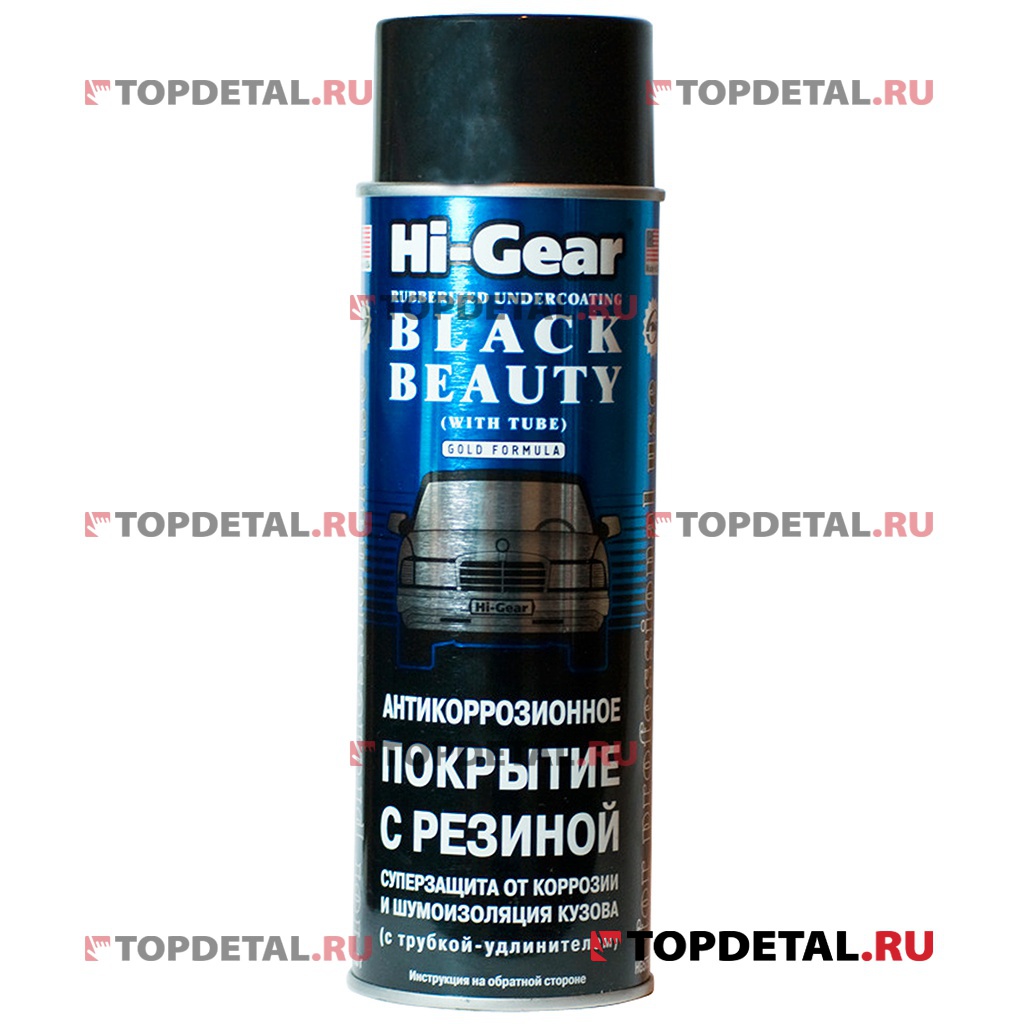
Пример толстослойного антикоррозионного покрытия.
Пример двухслойной системы антикоррозионного покрытия.
Пример трехслойной системы антикоррозионного покрытия.
Отличительные особенности антикоррозионных покрытий ВМП
Системы антикоррозионных покрытий на основе материалов, производимых ВМП, различаются по принципу защитного действия и разработаны для различных условий нанесения.
Особое место в сфере антикоррозионных покрытий ВМП занимают цинкнаполненные грунтовки. Высокое содержание цинкового порошка – до 96 %, позволяет обеспечивать долговременную, до 30 лет, протекторную защиту металла от коррозии. Покрытия на основе цинкнаполненных грунтовок, согласно ISO 12944, обеспечивают наибольший срок службы конструкций в атмосферных условиях.
Грунтовки с ингибиторами замедляют скорость коррозии стали, системы покрытий на их основе обеспечивают высокие и средние сроки службы. Также в ассортименте холдинга широко представлены грунтовки изолирующего типа и грунт-эмали с разными сроками службы.
На случай, когда качественная подготовка поверхности невозможна или экономически нецелесообразна, у ВМП есть материалы, которые можно наносить на поверхность с остатками старой краски и плотно сцепленной ржавчины. Такие материалы позволяют в 1,5 — 2 раза снизить затраты при проведении ремонтных работ за счет уменьшения расходов на подготовку поверхности.
В ассортименте ВМП есть материалы, наиболее эффективные для нанесения в заводских либо в полевых условиях. Первые отличаются коротким временем сушки (20-30 минут). ЛКМ для полевого окрашивания допускается наносить при повышенной влажности воздуха и отрицательных температурах (до -25° С), что позволяет продлить окрасочный сезон. Учет условий нанесения материалов позволяет избежать получения дефектов антикоррозионных покрытий, сократить сроки ввода объектов в эксплуатацию и уменьшить трудо- и энергозатраты при проведении окраски.
В последнее время важным фактором при выборе антикоррозийных материалов становится их технологичность и безопасность нанесения. Большой интерес вызывают ЛКМ, позволяющие набрать требуемую толщину покрытия за минимальное количество слоев. В ассортименте ВМП есть и такие материалы.
Очень часто к антикоррозийному покрытию предъявляются высокие требования по декоративному виду. Покрывные эмали ВМП обеспечивают надежную барьерную защиту от агрессивных внешних факторов и колеруются по каталогу RAL, имеют различную степень блеска, от матового до глянцевого. Высокая УФ-стойкость эмалей позволяет покрытию на длительное время сохранять заданные декоративные свойства.
Материалы ВМП для антикоррозионной защиты удобны в применении. Их нанесение осуществляется общепринятыми методами окраски. Материалы обеспечивают высокую стойкость к промышленной агрессивной среде и воздействиям открытой атмосферы.
Ознакомиться с ассортиментом материалов ВМП Вы можете в каталоге
Антикоррозионные материалы.
История антикоррозионных защитных покрытий
В древности, едва начав использовать металлы в быту, военном деле и производстве, было отмечено, что под действием атмосферной влаги инструменты и оружие начинают постепенно ржаветь и разрушаться. В трудах греческого историка Геродота (V век до нашей эры) находятся упоминания об оловянных покрытиях, предохраняющих железо от ржавчины. Первыми попытками по замедлению коррозийных процессов кроме лужения было также обработка поверхностей маслами и жиром, а также нанесение позолоты и серебрение.
Кроме того, древние уже умели использовать для конструкций материалы, которые менее подвержены коррозии. Например, колонна индийского царя Чандрагупты II изготовлена из практически чистого железа (99,72%). Она была установлена в 415 году нашей эры, и если бы обладала большей долей примесей, то за прошедшие 1600 лет не могла бы сохраниться ни в каком виде. Сейчас же она является одной из достопримечательностей Дели.
С окончанием средневековья в Германии началось промышленное производство белой жести, для этого железные листы погружали в расплавленное олово. В XVIII веке подобное производство было налажено в Англии, еще позже – в России. Возрос спрос также на свинец, потребление которого вызывалось развитием сернокислотного производства. Так в середине XVIII века в Британии впервые была применена свинцовая обшивка для сооружения сернокислотных камер.
В 40-х годах XVIII века был построен первый цинковый завод в Бристоле (Англия). Это способствовало использованию цинка в качестве защитного покрытия для различных сталей. Хотя первые сведения о специальных цинковых покрытиях относятся ко второй половине XVIII века, промышленные масштабы процесс горячего оцинкования получил с 1836 года.
С развитием химии стали применяться другие вариации нанесения защитной пленки, например, оцинковка, хромирование, амальгамирование. Возросший спрос на медь и ее сплавы вызвал увеличение производства олова и цинка, входящих в состав бронз и латуней.
Технологический прогресс (строительство железных дорог, стальных судов и многое другое) вызывал необходимость выработки принципиально новых подходов к защите стальных конструкций, узлов и агрегатов. Так, в 1889 году в Париже было завершено строительство Эйфелевой башни, причем сам изобретатель рассчитывал, что она прослужит как минимум 25 лет.
Долгое время промышленники заботились не об увеличении срока службы металлического изделия, а об увеличения количества произведенного металла. Лишь в 1910 году на Всемирном геологическом конгрессе в Стокгольме была озвучена проблема истощения запасов железной руды. При том, что опасения специалистов оказались преувеличенными и до настоящего времени в мире нет проблемы недостатка сырья, эти угрозы заставили ученых искать варианты более долгой сохранности металлических конструкций.
В 1913 году на основе никель-хромового сплава была получена нержавеющая сталь. В ходе экспериментов была обнаружена способность стальных изделий с высоким содержанием хрома сопротивляться кислотной коррозии. К концу 20-х годов нержавеющая сталь была признана наиболее универсальной и практичной по сравнению со сталью, не содержащей в своем составе хрома.
В начале ХХ века антикоррозийная защита развивалась в сторону покрытий на основе алкидной смолы, льняного масла, в состав которых входил свинцовый сурик. В 40-х годах стали использовать хлоркаучук, а в 50-е – антикоррозионные пигменты на цинковой основе. Эпоха свинцово- и хромосодержащих покрытий закончилась после их исследований экологами и токсикологами. В ходе дальнейших исследований в области защиты от коррозии появлялись все новые способы обработки поверхности металлов, например, воронение и полирование.
В середине XX века были разработаны основные виды и типы лакокрасочных материалов, которые используются до сих пор, в том числе и на столь потенциально опасных объектах как атомные электростанции. Это всевозможные грунты, шпаклевки, преобразователи коррозии. Другим перспективным направлением стало использование полимерных наполнителей, которые широко используются в металлургии вообще, и в производстве труб, в частности.
Выделились два основных варианта антикоррозионной защиты – электрохимический, направленный на повышение сопротивляемости самого изделия, и механический – наружная композитная броня в виде различных покрытий и пленок. Механический метод также применяется к материалам неметаллического типа, например для защиты бетона.
В настоящее время более всего распространены лакокрасочные антикоррозионные покрытия, их применение достигает 95%. Преимущества лакокрасочных материалов заключаются в простоте нанесения, широкой цветовой гамме, практически неограниченных размерах объекта для нанесения, сравнительной дешевизне и возможности быстрого нанесения ремонтного покрытия.
Сейчас на рынке АКЗ представлено множество способов нейтрализации негативного воздействия агрессивной среды, температуры, давления, адгезии и других коррозийных факторов. Для защиты поверхностей промышленных объектов используются различные лаки и краски, эмали и полимеры. Наносятся они также различными способами от «простого» распылителя до использования специальных покрасочных камер. На сегодняшний день это – самый доступный и распространенный способ АКЗ. Используются, как правило, простейшие лакокраски: всевозможные грунтовки и эмали. Стоимость современных высококачественных красок довольно высока, причем на подготовительные работы уходит до 70 – 80% общей стоимости окраски.
Одним из направлений развития технологий производства ЛКМ стала разработка композитных материалов. Наибольшее распространение получили антикоррозийные цинконаполненные краски для технологии так называемого «холодного цинкования». Этот материал имеет существенный недостаток – сравнительно невысокую химстойкость. Вызвано это тем, что металлы являются природными восстановителями, поэтому подобные защитные покрытия сами нуждаются в дополнительной защите в агрессивных средах.
Одной из последних разработок являются защитные покрытия с наполнителями чешуйчатой формы с аморфной или микрокристаллической структурой, такими, как чешуйчатое железо, микрослюда или стекло. При всех их плюсах, массовых работ по АКЗ (например, защиту трубопроводов) с применением этих средств в силу относительной дороговизны осуществлять нецелесообразно.
Проблему цены решает разработка принципиально иного, инновационного материала, который при относительной дешевизне, обладал бы высокой химической стойкостью и таким качеством, как абразивоустойчивость. Всеми этими характеристиками обладают защитные покрытия на основе эпоксидной смолы и базальтового микропластинчатого наполнителя. По своим химико-физическим параметрам он ничем не уступает, а в большинстве случаев – превосходит свои аналоги, при этом стоит существенно дешевле. Связано это с тем, что сырье для производства одного из компонентов этого защитного покрытия – базальт – повсеместно распространено на поверхности Земли.
Антикоррозийные защитные покрытия для резервуаров оптом по РФ
Антикоррозийные защитные покрытия для резервуаров от компании «Ново Коутингс»
Различные емкости, резервуары, цистерны используются повсеместно для хранения и транспортировки жидких и газообразных сред. При этом изготавливаются они из различных материалов, но наиболее распространенным все же является металл. Главной угрозой в его эксплуатации является коррозия. Мы предлагаем все виды антикоррозионных покрытий, обеспечивающих защиту резервуарных поверхностей.
Антикоррозийная защита емкостей – это комплексная работа, обеспечивающая первоначальную подготовку поверхностных слоев и покрытие составами, выбираемыми в зависимости от применения емкостей. При этом осуществляться такие процедуры могут как по вновь вводимым в эксплуатацию объектам, так и уже эксплуатируемым какое-то время.
Особенности покрытий для резервуаров
Антикоррозионные защитные покрытия для емкостей обеспечивают максимальную износостойкость и эффективность в любых условиях эксплуатации. При этом системы и технологии окраски предусматривают множество нюансов, отличающих составы и технику нанесения для внутренних и наружных поверхностей, элементов, соприкасающихся с другими материалами или почвой. Особое внимание следует уделить тем резервуарам, которые обеспечивают хранение или транспортировку пищевых/питьевых жидкостей. Покрытия для них обеспечивают не только защиту от коррозии, но и безопасность для человека.
Компания «Ново Коутингс» предлагает купить антикоррозионное покрытие для металла из первых рук. Мы являемся официальным дистрибьютором TIKKURILA OYJ (Финляндия) и Гамма Индустриальные Краски (г.Санкт-Петербург) и обеспечиваем оптовые поставки по всей территории России. С нами окраска резервуара, металлоконструкций, оборудования, сооружений, техники станет делом не сложным и не дорогим. ревязкой и заделкой швов между кладочными материалами (кирпичом, блоками и т.п.). Эти материалы должны иметь положительную температуру, быть сухими, чистыми, без трещин и поврежденных кромок и углов.
Важное значение придается устройству подслоев под футеровку, обеспечивающих повышенную плотность и химическую стойкость покрытия. Подслои, не проницаемые для жидкостей и газов слабой концентрации, устраивают в виде окрасочных и обмазочных изоляций из битумных, дегтевых, полимерных и других кислотостойких материалов. При более агрессивной среде применяют оклеенную изоляцию, в том числе из полиизобутилено-вых, винипластовых и других стойких полимерных материалов. Технология нанесения таких подслоев аналогична устройству соответствующих видов гидроизоляционных покрытий.
Футеровку выполняют в один и два слоя. Двухслойную выполняют так же, как и однослойную, принимая первый слой в качестве подслоя (основания). Перед эксплуатацией конструкцию хорошо просушивают.
Облицовка кислотоупорным кирпичом выполняется на замазке «Ар-мазит», которую используют как раствор. Для защиты конструкций в агрессивной среде используются кислотоупорные бетоны.
Окраска металлоконструкций лакокрасочными составами также является антикоррозионным защитным покрытием. При окраске лакокрасочными составами поверхность грунтуют битумно-бензиновым раствором.
Лакокрасочные и битумные составы, краски, лаки, эмали на основе полиуретановых, эпоксидных, силикатных и других смол на подготовленные поверхности наносят при температуре воздуха не ниже 10°С с помощью пистолетов-распылителей, кистей и валиков. В некоторых случаях для повышения механической прочности изоляции поверхность армируют стеклотканью.
При использовании перхлорвиниловых красок, лаков и эмалей разрешается наносить покрытие при отрицательной температуре (до -20°С).
Поверхности технологических аппаратов и особо ответственные конструкции изолируют путем наклейки тонких листов’сырой резины, которую потом вулканизируют, получая при этом сплошное противокоррозионное покрытие толщиной до 4 мм.
Гуммирование поверхностей осуществляют сырой рулонной резиной, резиновыми клеями, синтетическим каучуком, нейритом и тиоколовым герметиком с последующей вулканизацией покрытия.
При гуммировании сырой резиной очищенную и обезжиренную поверхность сначала грунтуют тонким слоем резинового клея, затем покрывают рулонной сырой резиной и подвергают тепловой обработке (вулканизации). В результате резина образует сплошное покрытие толщиной 2-4 мм в зависимости от толщины листов сырой резины.
Эта работа выполняется и другим способом. На просохшую грунтовку из резинового клея последовательно с интервалом 45-50 мин краскораспылителем наносят 15-20 слоев растворенной в бензине сырой резины общей толщиной 12-20 мм. Затем покрытие вулканизируют. Так проводят гуммирование и другими материалами. Исключение составляет тиоколовый гер-метик (густой или жидкой консистенции). Густой герметик наносят шпателем по 5-6 слоев, каждый слой толщиной 3 мм. Разжиженный герметик наносят кистью и слоями меньшей толщины. Интервал между нанесением слоев от 20 до 24 ч. При комнатной температуре покрытие готово к эксплуатации через 4-5 суток.
Жидкие резиновые смеси, тиоколовые герметики типа УМС-50 и др. наносят с помощью специальных шприцев, шпателей и волосяных кистей. Металлические конструкции изолируют нанесением 5-6 слоев клея Н-88 или клея СН-57 (толщина слоя 0,5-3 мм). Каждый слой наносят с перерывами 20-24 ч, а при выполнении найритовых покрытий — 4-6 ч.
При приемке поступающих в монтаж готовых конструкций и оборудования, подлежащих защите от коррозии, следует проверять наличие в сопроводительной документации следующих данных:
— для металлических конструкций и оборудования основных технических характеристик нанесенного покрытия или консервирующего материала, данных о числе его слоев, общей толщине, сроках и условиях сохранности;
— для железобетонных и бетонных конструкций данных о прочности и водонепроницаемости бетона, основных характеристик наполнителей бетона, виде цемента и примененных добавках.
Грунтовочные составы, используемые для защиты от коррозии, которые наносятся кистью, должны иметь вязкость в пределах: 30 с — битумные и кремнийорганические грунтовки; 40 с — эпоксидные, глифталевые, фенолформальдегидные, битумнолатексные и полиуретановые грунтовки, а также грунты-преобразователи ржавчины; 70 с — протекторные грунтовки.
Вязкость грунтовок, наносимых краскораспылителем, должна быть вдвое меньше вязкости грунтовок, наносимых кистью, за исключением пер-хлорвиниловых, вязкость которых может быть 20 с.
Шпатлевочные составы должны представлять собой тестообразную однородную, не расслаивающуюся массу, не давать усадки и не образовывать трещин. Для разбавления составов до рабочей консистенции применяют растворители, соответствующие природе смол, на основе которых приготовляют эти составы.
Очень высокие требования предъявляются к подготовке защищаемых поверхностей. Поверхности стальных конструкций и оборудования следует очищать, применяя металлические щетки и скребки, пескоструйные или дробеструйные установки. Открытые поверхности конструкций и оборудования очищают сухим кварцевым песком с зернами размером 0,5-2,5 мм, давление сжатого воздуха при этом должно быть не менее 0,4 МПа. Для очистки закрытых поверхностей конструкций и оборудования допускается применять смесь кварцевого песка с водой.
Внутренние поверхности закрытых стальных аппаратов в случаях, оговоренных проектом, допускается очищать металлической дробью, давление сжатого воздуха при этом должно быть в пределах 0,55-0,6 МПа.
Поверхность, подлежащая защите от коррозии металлизационным покрытием и очищенная с помощью дробе-пескоструйных установок, должна иметь сплошной матовый серый оттенок с ясно видимой шероховатостью до 55 мкм. Поверхности стальных конструкций и оборудования, намечаемые к обработке преобразователями ржавчины или грунтами-преобразователями, должны очищаться только от отслаивающихся пленок ржавчины.
Степень очистки поверхностей стальных конструкций и оборудования при их осмотре должна обеспечивать для покрытий, приготовляемых на основе синтетических смол, отсутствие видимой окалины или ржавчины. А для покрытий, приготовляемых на основе природных смол и жидкого стекла, — наличие окалины или ржавчины в пределах 15% поверхности, но не более 30% на отдельных участках площадью 2,5×2,5 см.
Работы по защите стальных конструкций и оборудования от коррозии следует начинать не позднее чем через 8 ч после окончания сухой очистки поверхностей.
При подготовке поверхностей железобетонных и каменных строительных и технологических конструкций должно быть обеспечено отсутствие раковин и углублений суммарной площадью более 0,2% на 1 м2 поверхности, а поверхностная (на глубине до 20 мм) влажность должна быть в пределах 4%.
При использовании окрасочных, шпатлевочных и вяжущих составов с отвердителями последние вводят в состав непосредственно перед применением. Объем приготовляемого состава должен обеспечивать полное его использование за время пригодности состава. Не допускается использовать или разбавлять затвердевшие или схватывающиеся составы.
Защитные покрытия наносят при температурах окружающего воздуха и защищаемых поверхностей не ниже следующих:
10°С — для окрасочных покрытий материалами, приготовленными на природных смолах; мастичных и шпатлевочных покрытий из силикатных материалов, приготовленных на основе жидкого стекла; подслоев из оклеечных покрытий на основе битумно-рулонных материалов и полиизобутиленовых пластин; гуммировочных покрытий; облицовочных и футеровочных покрытий, устанавливаемых на кислотоупорных силикатных замазках;
15°С — для окрасочных армированных и неармированных покрытий, а также наливных покрытий материалами, приготовленными на синтетических смолах; мастичных покрытий из герметиков, приготовленных на основе синтетических смол; покрытий из листовых полимерных материалов;
18°С — для оклеечных покрытий, выполняемых листовым пластикатом; облицовочных и футеровочных покрытий, выполняемых материалами, устанавливаемыми на замазках, приготовленных на эпоксидных смолах.
Защиту магистральных трубопроводов, стыков и поверхностей конструкций и оборудования, расположенных открыто, оклеечными покрытиями на основе природных смол допускается выполнять при минусовых температурах. При этом защищаемые поверхности должны быть просушены.
В зимнее время через каждые 4 ч следует измерять температуру воздуха, защитных материалов и защищаемых поверхностей. При наличии на защищаемых поверхностях инея, льда или росы поверхности просушивают непосредственно перед нанесением защитных покрытий.
По мере выполнения промежуточных этапов противокоррозионных работ следует проводить их освидетельствование и приемку. К законченным промежуточным этапам работ по защите от коррозии относят: полностью подготовленное основание, огрунтовку поверхности, подслой защитного покрытия, каждое полностью законченное промежуточное защитное покрытие одного вида (независимо от числа нанесенных слоев), специальную обработку поверхности защитного покрытия — обмазку металлического покрытия пастами, вулканизацию гуммировочного покрытия, окисловку швов облицовочного или футеровочного покрытия и т. п.
Во время приемки законченных противокоррозионных покрытий не-обходимо проверять: плотность покрытия, сцепление покрытия с защищаемой поверхностью, затвердение поверхности покрытия, толщину покрытия, полноту полимеризации покрытия или швов, герметичность сварных швов и слоев обкладки, состояние покрытия.
Места вынужденных вскрытий защитных покрытий заделывают покрытиями того же вида. Рулонные и листовые покрытия при этом усиливают дополнительным слоем, перекрывающим не менее чем на 100 мм место вскрытия.
Читать далее:
Антикоррозионные покрытия бетона |
||
ASODUR-TE (АСОДУР-TЕ) Эпоксидное покрытие |
ASODUR-TE- является не содержащей растворителей, тиксотропной двухкомпонентной эпоксидной смолой. Покрытия ASODUR-TE – устойчивы к истиранию, к агрессии чистой и сточных вод, морской воде, а также устойчивы против агрессии разбавленных кислот, щелочей и алифатических углеводородов, как, например, бензин, моторное масло и дизельное топливо. Области применения: ASODUR-TE используется для защиты цементных поверхностей, в частности, в сооружениях, предназначенных для очистки сточных вод, например, в канализационных трубах, метантенках, а также для антикоррозийной покраски шлюзов, портовых хозяйств и стальных шпунтованных стенок. Предварительное грунтование бетонной поверхности осуществляется соответствующими грунтовками: ASODUR-GBM или ASODUR-SG2 – в случае влажной поверхности. |
Schomburg г. Детмольд, Германия |
ASODUR-UBS (АСОДУР-УБС) Универсальное покрытие, кислотостойкое |
ASODUR-UBS является пигментированной двухкомпонентной эпоксидной смолой, не содержащей растворители. ASODUR-UBS отличается высокой стойкостью к воздействию органических и неорганических кислот, щелочей, минеральных масел. ASODUR-UBS стоек к воздействию жидкостей, опасных для воды по испытаниям 3, 8, 9, 10, 11, 12, 13 и 14 DIBt, г. Берлин. ASODUR-UBS соответствует нормам BPG пункту 4.12 DIBt, г. Берлин. Области применения: ASODUR-UBS используется в качестве защитного покрытия железобетонных, бетонных, оштукатуренных поверхностей и поверхностей стяжек в приемных резервуарах и хранилищах жидкостей, загрязняющих водную среду согласно §19 WHG (Закон о водном хозяйстве). ASODUR-UBS является компонентом системы ASOFLOOR-UBS. |
Schomburg г. Детмольд, Германия |
ASODUR-BS (АСОДУР-БC) Покрытие для бетонных и стальных поверхностей |
ASODUR-BS является содержащей растворители, пигментированной эпоксидной смолой. В отверждённом состоянии ASODUR-BS обладает хорошей эластичностью, высокой прочностью и износостойкостью. Покрытия ASODUR-BS устойчивы к воздействию кислот, щелочей, растворителей, масел, воды, морской воды, а также атмосферостойки и устойчивы к воздействию ультрафиолетовых лучей. При длительном атмосферном воздействии покрытие из ASODUR-BS становится слегка мелованным. Области применения: ASODUR-BS применяется для покрытия цементных поверхностей, таких как бетон, стяжки, штукатурки и т.п. в складских помещениях, мастерских, очистных сооружениях, коллекторах, а также для покрытия стальных поверхностей – мостов, ограждений, трубопроводов, резервуаров. |
Schomburg г. Детмольд, Германия |
Антикоррозионные покрытия металла |
||
ASODUR-ZNP (АСОДУР-ЦНП) Антикоррозионное покрытие |
ASODUR-ZNP является содержащей растворители, пигментированной двухкомпонентной твёрдой эпоксидной смолой. В отвержденном состоянии ASODUR-ZNP обладает хорошими вязко-эластичными качествами, высокой твердостью и стойкостью к истиранию. Покрытия ASODUR-ZNP устойчивы к воздействию щелочей, кислот, растворителей, масел, а также воды, в т.ч. морской. Области применения: ASODUR-ZNP предназначен для активной антикоррозионной защиты железных и стальных поверхностей, в частности, перед нанесением материалов группы ASODUR или систем ASOFLOOR. ASODUR-ZNP применяется для антикоррозионной защиты арматурного железа, стальных ёмкостей, силосных башен, стальных мостов и ограждений, а также трубопроводов. ASODUR-ZNP является компонентом системы ASOFLOOR — ZNP/BS. |
Schomburg г. Детмольд, Германия |
ASODUR-BS (АСОДУР-БC) Покрытие для бетонных и стальных поверхностей |
ASODUR-BS является содержащей растворители, пигментированной эпоксидной смолой. В отверждённом состоянии ASODUR-BS обладает хорошей эластичностью, высокой прочностью и износостойкостью. Покрытия ASODUR-BS устойчивы к воздействию кислот, щелочей, растворителей, масел, воды, морской воды, а также атмосферостойки и устойчивы к воздействию ультрафиолетовых лучей. При длительном атмосферном воздействии покрытие из ASODUR-BS становится слегка мелованным. Области применения: ASODUR-BS применяется для покрытия цементных поверхностей, таких как бетон, стяжки, штукатурки и т.п. в складских помещениях, мастерских, очистных сооружениях, коллекторах, а также для покрытия стальных поверхностей – мостов, ограждений, трубопроводов, резервуаров. |
Schomburg г. Детмольд, Германия |
INDUFLOOR-IB 2385 (ИНДУФЛОР-ИВ 2385) Активная защита от коррозии |
INDUFLOOR-IB 2385 является содержащей растворители, пигментированной двухкомпонентной твёрдой эпоксидной смолой. В отвержденном состоянии обладает хорошими вязко-эластичными качествами, высокой твердостью и стойкостью к истиранию. Устойчива к воздействию щелочей, кислот, растворителей, масел, а также воды, в т.ч.морской. Области применения: активная антикоррозионная защита железных и стальных поверхностей антикоррозионная защита арматурного железа |
Schomburg г. Детмольд, Германия |
Антикоррозионные покрытия арматуры |
||
ASODUR-ZNP (АСОДУР-ЦНП) Антикоррозионное покрытие |
ASODUR-ZNP является содержащей растворители, пигментированной двухкомпонентной твёрдой эпоксидной смолой. В отвержденном состоянии ASODUR-ZNP обладает хорошими вязко-эластичными качествами, высокой твердостью и стойкостью к истиранию. Покрытия ASODUR-ZNP устойчивы к воздействию щелочей, кислот, растворителей, масел, а также воды, в т.ч. морской. Области применения: ASODUR-ZNP предназначен для активной антикоррозионной защиты железных и стальных поверхностей, в частности, перед нанесением материалов группы ASODUR или систем ASOFLOOR. ASODUR-ZNP применяется для антикоррозионной защиты арматурного железа, стальных ёмкостей, силосных башен, стальных мостов и ограждений, а также трубопроводов. ASODUR-ZNP является компонентом системы ASOFLOOR — ZNP/BS. |
Schomburg г. Детмольд, Германия |
INDUFLOOR-IB 2385 (ИНДУФЛОР-ИВ 2385) Активная защита от коррозии |
INDUFLOOR-IB 2385 является содержащей растворители, пигментированной двухкомпонентной твёрдой эпоксидной смолой. В отвержденном состоянии обладает хорошими вязко-эластичными качествами, высокой твердостью и стойкостью к истиранию. Устойчива к воздействию щелочей, кислот, растворителей, масел, а также воды, в т.ч.морской. Области применения: активная антикоррозионная защита железных и стальных поверхностей антикоррозионная защита арматурного железа |
Schomburg г. Детмольд, Германия |
ASODUR-TE (АСОДУР-TЕ) Эпоксидное покрытие |
ASODUR-TE- является не содержащей растворителей, тиксотропной двухкомпонентной эпоксидной смолой. Покрытия ASODUR-TE – устойчивы к истиранию, к агрессии чистой и сточных вод, морской воде, а также устойчивы против агрессии разбавленных кислот, щелочей и алифатических углеводородов, как, например, бензин, моторное масло и дизельное топливо. Области применения: ASODUR-TE используется для защиты цементных поверхностей, в частности, в сооружениях, предназначенных для очистки сточных вод, например, в канализационных трубах, метантенках, а также для антикоррозийной покраски шлюзов, портовых хозяйств и стальных шпунтованных стенок. Предварительное грунтование бетонной поверхности осуществляется соответствующими грунтовками: ASODUR-GBM или ASODUR-SG2 – в случае влажной поверхности. |
Schomburg г. Детмольд, Германия |
ASODUR-UBS (АСОДУР-УБС) Универсальное покрытие, кислотостойкое |
ASODUR-UBS является пигментированной двухкомпонентной эпоксидной смолой, не содержащей растворители. ASODUR-UBS отличается высокой стойкостью к воздействию органических и неорганических кислот, щелочей, минеральных масел. ASODUR-UBS стоек к воздействию жидкостей, опасных для воды по испытаниям 3, 8, 9, 10, 11, 12, 13 и 14 DIBt, г. Берлин. ASODUR-UBS соответствует нормам BPG пункту 4.12 DIBt, г. Берлин. Области применения: ASODUR-UBS используется в качестве защитного покрытия железобетонных, бетонных, оштукатуренных поверхностей и поверхностей стяжек в приемных резервуарах и хранилищах жидкостей, загрязняющих водную среду согласно §19 WHG (Закон о водном хозяйстве). ASODUR-UBS является компонентом системы ASOFLOOR-UBS. |
Schomburg г. Детмольд, Германия |
Химзащита |
||
INDUFLOOR-IB 2385 (ИНДУФЛОР-ИВ 2385) Активная защита от коррозии |
INDUFLOOR-IB 2385 является содержащей растворители, пигментированной двухкомпонентной твёрдой эпоксидной смолой. В отвержденном состоянии обладает хорошими вязко-эластичными качествами, высокой твердостью и стойкостью к истиранию. Устойчива к воздействию щелочей, кислот, растворителей, масел, а также воды, в т.ч.морской. Области применения: активная антикоррозионная защита железных и стальных поверхностей антикоррозионная защита арматурного железа |
Schomburg г. Детмольд, Германия |
ASODUR-TE (АСОДУР-TЕ) Эпоксидное покрытие |
ASODUR-TE- является не содержащей растворителей, тиксотропной двухкомпонентной эпоксидной смолой. Покрытия ASODUR-TE – устойчивы к истиранию, к агрессии чистой и сточных вод, морской воде, а также устойчивы против агрессии разбавленных кислот, щелочей и алифатических углеводородов, как, например, бензин, моторное масло и дизельное топливо. Области применения: ASODUR-TE используется для защиты цементных поверхностей, в частности, в сооружениях, предназначенных для очистки сточных вод, например, в канализационных трубах, метантенках, а также для антикоррозийной покраски шлюзов, портовых хозяйств и стальных шпунтованных стенок. Предварительное грунтование бетонной поверхности осуществляется соответствующими грунтовками: ASODUR-GBM или ASODUR-SG2 – в случае влажной поверхности. |
Schomburg г. Детмольд, Германия |
ASODUR-UBS (АСОДУР-УБС) Универсальное покрытие, кислотостойкое |
ASODUR-UBS является пигментированной двухкомпонентной эпоксидной смолой, не содержащей растворители. ASODUR-UBS отличается высокой стойкостью к воздействию органических и неорганических кислот, щелочей, минеральных масел. ASODUR-UBS стоек к воздействию жидкостей, опасных для воды по испытаниям 3, 8, 9, 10, 11, 12, 13 и 14 DIBt, г. Берлин. ASODUR-UBS соответствует нормам BPG пункту 4.12 DIBt, г. Берлин. Области применения: ASODUR-UBS используется в качестве защитного покрытия железобетонных, бетонных, оштукатуренных поверхностей и поверхностей стяжек в приемных резервуарах и хранилищах жидкостей, загрязняющих водную среду согласно §19 WHG (Закон о водном хозяйстве). ASODUR-UBS является компонентом системы ASOFLOOR-UBS. |
Schomburg г. Детмольд, Германия |
ASODUR-BS (АСОДУР-БC) Покрытие для бетонных и стальных поверхностей |
ASODUR-BS является содержащей растворители, пигментированной эпоксидной смолой. В отверждённом состоянии ASODUR-BS обладает хорошей эластичностью, высокой прочностью и износостойкостью. Покрытия ASODUR-BS устойчивы к воздействию кислот, щелочей, растворителей, масел, воды, морской воды, а также атмосферостойки и устойчивы к воздействию ультрафиолетовых лучей. При длительном атмосферном воздействии покрытие из ASODUR-BS становится слегка мелованным. Области применения: ASODUR-BS применяется для покрытия цементных поверхностей, таких как бетон, стяжки, штукатурки и т.п. в складских помещениях, мастерских, очистных сооружениях, коллекторах, а также для покрытия стальных поверхностей – мостов, ограждений, трубопроводов, резервуаров. |
Schomburg г. Детмольд, Германия |
ASODUR®- ZGS (АСОДУР-ЦГС) Вязко-эластичное покрытие бетона для защиты водной среды |
ASODUR-ZGS является не содержащей растворители, пигментированной двухкомпонентной эпоксидной смолой. ASODUR-ZGS устойчив к воздействию органических и неорганических кислот и щелочей, а также минеральных масел, бензина и растворителей. ASODUR-ZGS выдерживает высокие механические нагрузки (по нему можно проезжать). Области применения: ASODUR-ZGS применяется для покрытия поверхностей из железобетона, бетона, штукатурки в производственных и складских помещениях для жидкостей, которые могут быть опасны для воды, согласно §19 ВХГ (закон о водном балансе). Также данный материал применяется для компьютерных помещений, больниц, газо-распределительных станций. ASODUR-ZGS является системным компонентом системы ASODUR-ZGS и ASODUR-ZGS -электропроводящее. |
Schomburg г. Детмольд, Германия |
ASODUR-UBS/Е (АСОДУР-УБС/Е) Универсальное покрытие, кислотостойкое |
ASODUR-UBS/E является не содержащей растворители, двухкомпонентной эпоксидно-полиуретановой смолой с добавками пигмента. ASODUR-UBS/E устойчив против воздействия органических и неорганических кислот и щелочей, а также против воздействия минеральных масел и растворителей. ASODUR-UBS/E является эластифицированным материалом и перекрывает трещины до 0,3 мм. Области применения: ASODUR-UBS/E используется в качестве промежуточного, перекрывающего трещины слоя при покрытии железобетонных, бетонных, оштукатуренных поверхностей и поверхностей стяжек в приемных резервуарах, производственных и складских помещениях для хранения жидкостей, загрязняющих водную среду. Соответствует требованиям параграфа 19 g Закона об использовании воды для бытовых нужд. ASODUR-UBS/E является системным компонентом Системы охраны водной среды ASOFLOOR-HCB/AB. |
Schomburg г. Детмольд, Германия |
INDUFLOOR®-IB 2115 (ИНДУФЛООР-ИБ 2115) Электропроводный лак на водной основе |
INDUFLOOR-IB 2115 — не содержащая растворителей, водоэмульсионная, пигментированная, 2-хкомпонентная эпоксидная смола, обладающая следующими свойствами: Высокая электростатическая проводимость Хорошая адгезия между слоями Области применения: INDUFLOOR-IB 2115 применяется в системе с медной лентой INDU-Leitband в качестве проводящего слоя под антистатическими финишными покрытиями и в качестве системного компонента в системе WHF INDUFLOOR-GWS 3. |
Schomburg г. Детмольд, Германия |
INDUFLOOR®-IB 2360 (ИНДУФЛООР-ИБ 2360) Финишное покрытие для бетона на водной основе |
INDUFLOOR-IB 2360 – Водоэмульсионная, пигментированная, двухкомпоннетная эпоксидная смола, обладающая следующими свойствами: Не содержит органических растворителей Со слабым запахом Устойчиво против разбавленных кислот и щелочей, жидкого топлива и бензина До 10% может быть разбавлена водой (грунтование) Паропроницаема Очень хорошая адгезия к различным поверхностям Эффект шелковой (блестящей) поверхности Под действием УФ, может появиться эффект мелованности, либо изменение цвета . Необходимо проводить собственные испытания , при длительном атмосферном воздействие и длительной влажностной нагрузке. Области применения: INDUFLOOR-IB 2360 применяется как пропиточная мастика на цементных поверхностях: стена и пол, магнезиальных и ангидритных стяжках, коррозионная защита для стальных поверхностей и на хорошо уплотненном асфальтовом покрытии, например, в складских помещениях, мастерских, гаражах, производственных цехах, галереях и т.п. Следует исключить высокую точечную нагрузку. |
Schomburg г. Детмольд, Германия |
INDUFLOOR -IB 2370 (ИНДУФЛОР-ИБ 2370) Сточные воды — герметичная защита |
INDUFLOOR-IB 2370 – герметичная защита от сточных вод со следующими свойствами: не содержащая растворителей тиксотропная устойчива к истиранию устойчива к воде, сточным водам и морской воде устойчива к разбавленным кислотам и щелочам Области применения: INDUFLOOR-IB 2370 используется для защиты цементных поверхностей, в частности, в сооружениях, предназначенных для очистки сточных вод, например: в очистных сооружениях в канализационных трубах биогазовых установках в качестве коррозионной защиты в стальном гидротехническом строительстве, например, в качестве антикоррозионной покраски шлюзов, портовых сооружений и стальных шпунтовых стенок |
Schomburg г. Детмольд, Германия |
INDUFLOOR®-IB 3310 (ИНДУФЛООР-ИБ 3310) (прежнее название ASODUR-UBS, ASODUR-ZGS) Химическая защита — WHG |
INDUFLOOR-IB 3310 является пигментированной двухкомпонентной, не содержащей растворителей эпоксидной смолой, обладающей следующими свойствами: Устойчива к органическим и неорганическим кислотам и щелочам, к минеральным маслам, бензину и растворителям Механически высоконагружаема (непосредственный проезд транспортных средств), обладает антистатическими свойствами Выполняет требования техники лакирования для применения в качестве покрытия в области применения лакировальных установок, например, в автомобильной промышленности После отверждения за счет специального состава в зависимости от подготовки основания, от вида и способа нанесения и климатических условий может сформировываться более или менее неоднородная поверхность, которая однако полностью соответствует нормативным показателям. Области применения: INDUFLOOR-IB 3310 применяется для покрытия железобетонных, бетонных, оштукатуренных поверхностей и поверхностей стяжек в производственных и складских помещениях, подверженных воздействию агрессивных жидкостей (согласно &19 WHG «Закон о водном хозяйстве»). Применяется также в лакокрасочных мастерских, компьютерных залах, больницах, газораспределительных станциях. |
Schomburg г. Детмольд, Германия |
INDUFLOOR-IB® 2380 (ИНДУФЛООР-ИБ 2380) Защита бетона и стали |
INDUFLOOR-IB 2380 является пигментированной двухкомпонентной эпоксидной смолой. Содержит растворители Низковязкая Высокоустойчива к истиранию Устойчива к воде и морской воде Обладает высокой химической стойкостью Склонна к пожелтению Области применения: INDUFLOOR-IB 2380 применяется в наружных и внутренних областях для покрытия цементных поверхностей, таких как бетон, стяжки, штукатурки и т.п. в складских помещениях, мастерских, очистных сооружениях, коллекторах, а также для покрытия стальных поверхностей |
Schomburg г. Детмольд, Германия |
ASOCRET-P/КS (АСОКРЕТ-П/КС) Минеральный антикоррозионный состав |
ASOCRET-P/KS является составом на цементной основе с мелкозернистым наполнителем и синтетическими добавками. К применению ASOCRET-P/KS готовится путем затворения водой. Покрытия из него водонепроницаемы, паропроницаемы, морозостойки, устойчивы к воздействию размораживающих солей и обладают высокой степенью сопротивления карбонизации. ASOCRET-P/KS отверждается без усадки и трещинообразования, в том числе в условиях динамических нагрузок. Области применения: ASOCRET-P/KS находит применение в качестве антикоррозионной защиты при проведении ремонтных работ по следующим категориям поверхностей |
Schomburg г. Детмольд, Германия |
Антикоррозийные защитные покрытия
Антикоррозийные защитные покрытия
Наименование | Фасовка, кг | Цена, руб | ЦИНОЛ | 1,1 кг | 800 руб | ЦИНОЛ | 25 кг | 13690 руб | ЦИНОЛ | 7 кг | 5400 руб | ЦИНОТАН | 1,1 кг | 890 руб | ЦИНОТАН | 25 кг | 15190 руб | ЦИНОТАН | 8 кг | 5550 руб | АЛПОЛ | 0,8 кг | 520 руб | АЛПОЛ | 18 кг | 6890 руб | АЛПОЛ | 2,8 кг | 1080 руб | АЛЮМОТАН | 17 кг | 9745 руб | АЛЮМОТАН | 0,9 кг | 700 руб | ФЕРРОТАН-ПРО | 0,9 кг | 590 руб | ФЕРРОТАН-ПРО | 20 кг | 9850 руб | ФЕРРОТАН | 1,4 кг | 845 руб | ФЕРРОТАН | 15 кг | 6900 руб | СОЛЬВ-УР растворитель | 25 кг | 6300 руб | СОЛЬВ-УР растворитель | 4 кг | 1200 руб |
---|
Коррозийное разрушение изделий и конструкций из железа и стальных сплавов признается большой проблемой во всем мире и решением задач по снижению этого разрушительного воздействия человечество занимается столько времени, сколько прошло с того момента, как люди научились это железо выплавлять.
Люди научились наносить на поверхность металла защитные покрытия из других металлов или лакокрасочных материалов, придумали нержавеющую сталь, используют для своих задач детали и конструкции из неподдающихся воздействию коррозии цветных металлов и сплавов.
Одним из весьма эффективных, недорогих и простых способов защиты металла считается нанесение на поверхность металла защитных композиций на полимерной основе. К таким защитным композициям можно отнести цинксодержащие ЦИНОЛ, ЦИНОТАН, а также АЛПОЛ, АЛЮМОТАН, ФЕРРОТАН, ФЕРРОТАН ПРО.
ЦИНОЛ представляет собой суспензию высокодисперсного порошка цинка в растворе высокомолекулярного синтетического полимера. Поставляется в банках и ведрах массой 1,1; 7,0 и 25 килограмм. Цинкнаполненная композиция применяется, как для нанесения самодостаточного защитного покрытия, так и в качестве грунтовки при нанесении комбинированных защитных покрытий. Рекомендован для совместного использования с алюмонаполненной композицией АЛПОЛ. Также ЦИНОЛ удобен для устранения нарушений цинковых покрытий, наносимых на поверхность конструкций горячим, термодиффузионным или гальваническим способом.
ЦИНОТАН является полиуретановой цинкнаполненной композицией с высоким уровнем содержания нелетучих элементов. Как и ЦИНОЛ, ЦИНОТАН поставляется в банках и ведрах массой 1,1; 7,0 и 25 килограмма. Применяется как в качестве грунтовки, так и в виде самостоятельного покрытия. Рекомендован для применения в комплексных покрытиях как для огневой, так и антикоррозийной защиты.
АЛПОЛ представляет собой защитно-декоративную композицию, состоящую из алюминиевой пудры и высокомолекулярного термопластичного полимера. Применяется АЛПОЛ для антикоррозийной защиты стальных металлоконструкций и металлоизделий, эксплуатируемых в атмосферных условиях. Покрытие устойчиво к водной среде и совместно с ЦИНОЛ допускается для нанесения покрытий в системах водоснабжения. АЛПОЛ не рекомендован для взаимодействия с бензином и некоторыми органическими растворителями.
АЛЮМОТАН — суспензия из порошкообразного алюминия в полиуретановом лаке с добавлением органических растворителей, затвердевает под воздействием влажного воздуха, устойчива к воздействию нефти и нефтепродуктов, морской и пресной воды, водных растворов кислот, щелочей и солей. Применяется для покраски металлоконструкций, монтируемых в атмосферных условиях любых климатических поясов.
ФЕРРОТАН и ФЕРРОТАН ПРО антикоррозийные композиции содержащая полиуретановый лак и железную слюдку, препятствующую появлению коррозии на металлоконструкциях. ФЕРРОТАН устойчив во всех атмосферных зонах, может быть использован для защиты металла от нефтепродуктов, щелочи и кислот, соленой и пресной воды. Применяется индивидуально и в комплексе с другими составами. Служит для защиты металлических, бетонных и железобетонных конструкций.
СОЛЬВ-УР – растворитель, применяемый для обезжиривания поверхностей перед покраской, разбавления полимерных композиций до требуемой консистенции, а также для промывки используемого для покраски инструмента и оборудования.
Уважаемые партнеры, клиенты, заказчики. Для оперативной обработки вашей заявки указывайте в заказе каким образом необходимо подготовить металл к отгрузке. Нужно ли порезать его для транспортировки, на какую длину? Если заказываете доставку нашими силами, укажите по какому адресу и в какой город, какой транспортной компанией или каким отдельным видом транспорта необходимо произвести отправку приобретаемого вами металла.
Защитные покрытия: виды, функции, особенности
Уникальной разновидностью неметаллических защитных покрытий являются антифрикционные материалы. По внешнему виду они напоминают краски, однако вместо пигментов содержат частицы твердых смазочных веществ, которые равномерно распределены в смеси связующих компонентов и растворителей.
В противокоррозионной практике для изоляции металла от воздействия агрессивных сред используются специальные защитные покрытия. Все они подразделяются на металлические и неметаллические.
Металлические – анодные и катодные – покрытия наносятся на поверхности методами газотермического напыления, окунания, гальванизации, плакирования или диффузии.
К неметаллическим защитным покрытиям относятся лакокрасочные составы, полимерные пленки, силикатные эмали, резины, оксиды металлов, соединения фосфора, хрома и др.
Рассмотрим все виды покрытий подробнее.
Металлические защитные покрытия
В качестве анодных металлических покрытий выступают металлы, электрохимический потенциал которых меньше, чем у обрабатываемых материалов. У катодных он, наоборот, выше.
Анодные покрытия обеспечивают электрохимическую защиту металлических поверхностей и выполняют свои функции даже при нарушении целостности слоя.
Катодные покрытия препятствуют проникновению агрессивных сред к основному металлу благодаря образованию механического барьера. Они лучше защищают поверхности от негативных воздействий, но только в случае неповрежденности.
В зависимости от способа нанесения металлические покрытия подразделяются на следующие виды.
Гальванические покрытия
Гальванизация – это электрохимический метод нанесения металлического защитного покрытия для защиты поверхностей от коррозии и окисления, улучшения их прочности и износостойкости, придания эстетичного внешнего вида.
Гальванические покрытия применяются в авиа- и машиностроении, радиотехнике, электронике, строительстве.
В зависимости от назначения конкретных деталей на них наносятся защитные, защитно-декоративные и специальные гальванические покрытия.
Защитные служат для изоляции металлических деталей от воздействия агрессивных сред и предотвращения механических повреждений. Защитно-декоративные предназначены для придания деталям эстетичного внешнего вида и их защиты от разрушительных внешних воздействий.
Специальные гальванические покрытия улучшают характеристики обрабатываемых поверхностей, повышают их прочность, износостойкость, электроизоляционные свойства и т.д.
Разновидностями гальванических покрытий являются меднение, хромирование, цинкование, железнение, никелирование, латунирование, родирование, золочение, серебрение и пр.
Газотермическое напыление
Представляет собой перенос расплавленных частиц материала на обрабатываемую поверхность газового или плазменным потоком. Покрытия, образованные таким методом, отличаются термо- и износостойкостью, хорошими антикоррозионными, антифрикционными и противозадирными свойствами, электроизоляционной или электропроводной способностью. В качестве напыляемого материала выступают проволоки, шнуры, порошки из металлов, керамики и металлокерамики.
Выделяют следующие методы газотермическогого напыления:
- Газопламенное напыление: самый простой и недорогой метод, применяемый для защиты крупных площадей поверхности от коррозии и восстановления геометрии деталей
- Высокоскоростное газопламенное напыление: используется для образования плотных металлокерамических и металлических покрытий
- Детонационное напыление: применяется для нанесения защитных покрытий, восстановления небольших поврежденных участков поверхности
- Плазменное напыление: используется для создания тугоплавких керамических покрытий
- Электродуговая металлизация: для нанесения антикоррозионных металлических покрытий на большие площади поверхности
- Напыление с оплавлением: применяется тогда, когда риск деформации деталей отсутствует или он оправдан
Погружение в расплав
При использовании этого метода обрабатываемые детали окунаются в расплавленный металл (олово, цинк, алюминий, свинец). Перед погружением поверхности обрабатываются смесью хлорида аммония (52-56 %), глицерина (5-6 %) и хлорида покрываемого металла. Это позволяет защитить расплав от окисления, а также удалить оксидные и солевые пленки.
Данный метод нельзя назвать экономичным, так как наносимый металл расходуется в больших количествах. При этом толщина покрытия неравномерна, а наносить расплав в узкие зазоры и отверстия, например, на резьбу, не представляется возможным.
Термодиффузионное покрытие
Данное покрытие, материалом для которого выступает цинк, обеспечивает высокую электрохимическую защиту стали и черных металлов. Оно обладает высокой адгезией, стойкостью к коррозии, механическим нагрузкам и деформации.
Слой термодиффузионного покрытия имеет одинаковую толщину даже на деталях сложных форм и не отслаивается в процессе эксплуатации.
Плакирование
Метод представляет собой нанесение металла термомеханическим способом: путем пластичной деформации и сильного сжатия. Чаще всего таким образом создаются защитные, контактные или декоративные покрытия на деталях из стали, алюминия, меди и их сплавов.
Плакирование осуществляется в процессе горячей прокатки, прессования, экструзии, штамповки или сваривания взрывом.
Виды и особенности неметаллических покрытий
Неметаллические покрытия подразделяются на органические и неорганические. Они создают на обрабатываемых поверхностях тонкую, инертную по отношению к агрессивным веществам пленку, которая предохраняет детали от негативных воздействий окружающей среды.
Лакокрасочные защитные покрытия
В состав таких покрытий входят пленкообразующие вещества, наполнители, пигменты, пластификаторы, растворители и катализаторы. Варьирование состава позволяет получать материалы со специфическими свойствами (токопроводящие, декоративные, особопрочные, жаростойкие и т.п.). Они не только защищают изделия в различных условиях, но и придают им эстетичный внешний вид.
В группу лакокрасочных покрытий входят лаки, краски, грунтовки, олифы, шпаклевки.
Силикатные эмали
Применяются для изделий, работающих при высоких температурах в химически агрессивных средах.
Эмалевое защитное покрытие формируется с помощью порошка или пасты. Процесс проходит в несколько этапов. Сначала на изделие наносится грунтовая эмаль – она улучшает адгезию, уменьшает термические и механические напряжения.
Затем, после спекания первого слоя при температуре +880… + 920 °С, накладывается покровная эмаль, после чего изделие снова подвергается нагреванию до +840… +860 °С.
Если требуется нанести несколько слоев силикатной эмали, вышеописанные операции проводят поочередно несколько раз. Изделия из чугуна, к примеру, обрабатывают в 2-3 подхода.
Застывшая эмаль представляет собой тонкое, похожее на стекло, покрытие. Его основным недостатком является сравнительно низкая прочность – под воздействием ударных нагрузок эмаль может растрескиваться или скалываться.
Полимерные защитные покрытия
В число наиболее распространенных полимеров, применяющихся для защиты металлов от коррозии, входят полистирол, полиэтилен, полипропилен, полиизобутилен, фторопласты, эпоксидные смолы и др.
Полимерное покрытие осуществляется методами окунания, газотермического или вихревого напыления, обычной кистью. Остывая, оно образует на поверхности сплошную защитную пленку толщиной несколько миллиметров.
Разновидностью полимерных являются антифрикционные твердосмазочные покрытия. Внешне эти материалы похожи на краски, однако вместо пигментов они содержат высокодисперсные частицы твердых смазочных веществ, которые равномерно распределены в смеси связующих компонентов и растворителей.
Основу покрытий могут составлять дисульфид молибдена, графит, политетрафторэтилен (ПТФЭ) и прочие твердые смазки. В качестве связующих применяются акриловые, фенольные, полиамид-имидные, эпоксидные смолы, титанат, полиуретан и некоторые другие специальные компоненты.
Антифрикционные твердосмазочные покрытия, а также специальные растворители и очистители для предварительной подготовки поверхностей разрабатывает российская компания «Моденжи».
Материалы MODENGY применяются в средне- и тяжелонагруженных узлах трения скольжения (направляющих, зубчатых передачах, подшипниках и т.д.), на деталях двигателей внутреннего сгорания (юбках поршней, вкладышах валов, дроссельной заслонке), в резьбовом крепеже, трубопроводной арматуре, пластиковых и металлических элементах автомобилей (замках, петлях, пружинах, скобах, механизмах регулировки и т.д.), а также в других парах трения металл-металл, металл-резина, полимер-полимер, металл-полимер.
Покрытия MODENGY наносятся однократно на весь срок службы деталей. С их помощью создаются узлы трения, не требующие дальнейшего обслуживания и применения традиционных смазочных материалов.
Антифрикционные покрытия MODENGY отличаются:
- Высокой несущей способностью
- Работоспособностью в запыленной среде
- Низким коэффициентом трения
- Широким диапазоном рабочих температур
- Высокой износостойкостью
- Противозадирными и антикоррозионными свойствами
- Стойкостью к воздействию кислот, щелочей, растворителей и других химикатов
- Работоспособность в условиях радиации и вакуума
Покрытия ложатся тонким слоем, поэтому практически не меняют исходные размеры деталей, зато обеспечивают им необходимый комплекс триботехнических и защитных свойств.
Применение материалов MODENGY позволяет эффективно управлять трением, повышать ресурс и энергоэффективность оборудования.
Оксидные защитные пленки
Оксидирование – это окислительно-восстановительная реакция металлов, которая возникает благодаря их взаимодействию с кислородом, электролитом или специальными кислотно-щелочными составами. В результате этого процесса на металлических поверхностях образуется защитная пленка, которая увеличивает их твердость, снижает риск образования задиров, улучшает приработку деталей и повышает срок их службы.
Оксидирование используется для получения защитных и декоративных покрытий, а также для формирования диэлектрических слоев. Различают химические, анодные (электрохимические), термические, плазменные и лазерные методы этой обработки.
Резиновые защитные покрытия
Гуммирование, или создание защитных покрытий из резины или эбонита, помогает защитить трубопроводы, химические аппараты, резервуары для перевозки и хранения химических веществ от воздействия агрессивных сред.
Защитное покрытие может быть сформировано из мягкой или твердой резины. Консистенция контролируется добавками серы: мягкая содержит от 2 до 4 % этого вещества, твердая – от 30 до 50 %.
Покрытие наносится на предварительно очищенные и обезжиренные поверхности. Скопившийся после обработки воздух выдавливается валиком. В качестве заключительного этапа гуммирования проводится вулканизация изделий.
Резиновые покрытия являются хорошими диэлектриками, обладают стойкостью ко многим кислотам и щелочам (но не к сильным окислителям). Из существенных недостатков резиновых покрытий можно выделить их старение со временем.
Смазки и пасты
При длительном хранении и перевозке металлоизделий в качестве защитных покрытий могут использоваться специальные смазки и пасты – они препятствуют попаданию на поверхности влаги, пыли и различных газообразных веществ, наносятся кистью или методом распыления.
Консервационные материалы изготавливаются на основе минеральных масел (вазелинового, машинного) и воскообразных веществ (воска, парафина, мыла). Очень популярны смазки, в состав которых входит 5 % парафина и 95 % петролатума (смеси парафинов, масел и минеральных восков – церезинов).
Главный недостаток паст и смазок, применяющихся в качестве защитных покрытий, состоит в том, что целостность образовавшейся пленки легко нарушить. Именно поэтому лучшей альтернативой пластичных составов являются антифрикционные твердосмазочные покрытия.
Антикоррозийные покрытия — Антикоррозийные покрытия
Crossroads Coatings широко известна в отрасли благодаря нашему обширному перечню рецептур коррозионно-стойких покрытий. Эти покрытия защищают металлические компоненты от разрушения из-за влаги, солевого тумана, окисления и воздействия ультрафиолетовых лучей и различных экологических или промышленных химикатов. Наши антикоррозионные покрытия весьма разнообразны по своему применению, но мы обычно продаем их клиентам в нефтяной, автомобильной и горной промышленности.Также к покрытию металлических дверей, декоративного железа и другого металлического оборудования.
МЫ ЯВЛЯЕМСЯ ФОРМУЛЯТОРОМ ТАМОЖЕННЫХ ПОКРЫТИЙ
Мы разрабатываем и производим высококачественные коррозионно-стойкие покрытия для применения во всех отраслях промышленности. Запросите расценки на поставку покрытий по индивидуальному заказу сегодня!
Типы антикоррозионных защитных покрытий
Высококачественные антикоррозионные покрытия, производимые Crossroads, позволяют защитить металлические поверхности, выступая в качестве барьера для окисления.У нас уже есть широкий выбор антикоррозионных покрытий, и их можно настроить для любого применения. Мы поставляем:
- Фторполимер — смеси смолы и смазки, обеспечивающие отличную защиту от коррозии
- Эпоксидная смола, воздушная сушка — экономичное антикоррозийное покрытие
- Эпоксидная смола термического отверждения — отличная ударопрочность, а также устойчивость к коррозии и истиранию
- Фенольный — идеален для сред с низким pH и высокой температурой
- Фосфат — покрытие из черных металлов для защиты от истирания и незначительной коррозионной стойкости
- Полиуретан — глянцевое верхнее покрытие для эпоксидной смолы и неорганического цинка
- Цинк неорганический — защита от коррозии и атмосферных воздействий для стали
- PTFE — оригинальное антипригарное покрытие, выдерживающее высокие температуры
- FEP — ПТФЭ с повышенной стойкостью к истиранию
Многие из этих антикоррозионных защитных покрытий также обеспечивают стойкость к истиранию, антипригарные свойства и химическую защиту.
Применение антикоррозионных покрытий
Мы создаем индивидуальные покрытия для различных областей применения в различных отраслях:
С помощью нашего современного испытательного оборудования каждая партия наших антикоррозионных покрытий проверяется на качество и подтверждает их соответствие установленным стандартам. Свяжитесь с нами сегодня, и мы будем рады помочь вам правильно начать свой проект по нанесению покрытий, предоставив покрытие, идеально соответствующее вашим требованиям.
Нажмите здесь, чтобы запросить ценовое предложение, или позвоните нам по телефону 1.833.724.6816Сравнение 5 коррозионно-стойких металлических покрытий
Легкие металлы стали популярным выбором во многих отраслях промышленности. Такие металлы, как алюминий, титан и теперь даже магний, стали жизненно важными для автомобильной, аэрокосмической и многих других областей применения. Сочетание их изобилия, исключительного отношения прочности к весу и универсальности означает, что они являются предпочтительным выбором для инженеров по продукции во всем мире.
Некоторые легкие сплавы обладают превосходной коррозионной стойкостью даже в необработанном виде, но неизбежно потребуется обработка поверхности готового продукта для обеспечения рабочих характеристик, долговечности и качества.Магний известен своей плохой коррозионной стойкостью, но менее известно то, что некоторые алюминиевые сплавы, такие как 2xxx, 7xxx и другие высокопрочные семейства, содержащие медь или другие переходные металлы, также подвержены такой же чувствительности.
Выбор правильного метода защиты от коррозии важен для успешного проектирования и производства компонентов. Каждый метод имеет уникальный набор преимуществ и потенциальных проблем. Мы собрали это сравнение различных методов лечения, чтобы помочь вам найти наиболее подходящее решение для ваших нужд.
1. Анодирование
Анодирование — самый популярный метод улучшения коррозионной стойкости алюминия. Вообще говоря, он включает в себя четырехэтапный процесс для достижения защиты.
Первый этап включает погружение материала в ванну с проводящим раствором — обычно кислотную ванну с низким pH — и подключение сплава к аноду электрической цепи. При подаче электрического тока на поверхности металла происходит реакция окисления:
2Al (S) + 6OH — (водн.) — 6e — Al 2 O 3 (s) + 3H 2 O (л)
Это вызывает утолщение естественного оксида на поверхности металла, создавая защитный внешний слой оксида алюминия.Толщина покрытия может быть изменена за счет увеличения времени нанесения покрытия, что обеспечивает широкий спектр применения:
- При легком нанесении может обеспечить хорошую предварительную обработку для окраски или
последующих покрытий - При окрашивании можно получить особые цветовые эффекты.
- При нанесении тонким слоем (обычно <20 мкм) он является полупрозрачным, что
сохраняет металлический эстетический вид, при желании
Выбор толщины покрытия играет ключевую роль в определении коррозионной стойкости.В наружных условиях или при интенсивном внутреннем стрессе (например, при постоянном контакте с жидкостью) рекомендуется минимум 20 мкм. Если для слоев требуется толщина 10 мкм, более высокое напряжение может повредить материал, растрескивая защитный оксидный слой и становясь пористым.
Кроме того, механизм роста и столбчатая микроструктура вызывают растрескивание по всей толщине в углах, что ограничивает защиту кромок, обеспечиваемую слоями анодирования. Уплотнения с горячей водой могут использоваться для обеспечения более надежной защиты, но более эффективные уплотнения могут быть достигнуты за счет использования опасных химических растворов, таких как ацетат никеля или бихромат натрия.
В конечном счете, для материалов, требующих определенных эстетических качеств, при сохранении высокой устойчивости к коррозии при контакте с жидкостями, анодирование — не лучший метод повышения коррозионной стойкости.
2. ПЭО
Плазменное электролитическое окисление (ПЭО) включает использование плазменных разрядов для преобразования металлической поверхности легких металлов. Он образует твердый и плотный адгезионный оксидный слой.
Компоненты погружаются в ванну, и электрический ток используется для «выращивания» однородного слоя оксида на поверхности.ПЭО состоит из трех этапов:
- Окисление подложки (как происходит в процессе анодирования)
- Совместное осаждение элементов из электролита в покрытие
- Модификация полученного слоя плазменным разрядом
Хотите узнать больше о методологии Keronite PEO? Щелкните ниже, чтобы загрузить бесплатный информационный документ.
PEO образует твердые, плотные и износостойкие покрытия для легких металлов, таких как алюминий, титан и магний.По сравнению непосредственно с анодированными покрытиями, PEO образует покрытия с более высокой твердостью, химической пассивностью и выгодной нерегулярной структурой пор, которая обеспечивает высокую устойчивость к деформации и более прочную адгезию.
Помимо превосходных физических и химических характеристик, процесс ПЭО можно проводить экологически безопасным методом благодаря доброкачественным электролитам, доступным для использования, и нетоксичным побочным продуктам процесса окисления. Электролиты не содержат кислот, аммиака, тяжелых металлов и хрома, а используемые щелочные растворы с низкой концентрацией не представляют опасности и легко утилизируются.
Это означает более экологичное решение, чем альтернативы, а также ряд других преимуществ.
3. Хроматное конверсионное покрытие
Усиление контроля над производственными процессами со стороны государственных органов и регулирующих органов привело к постепенному отказу от использования хроматных конверсионных покрытий как метода защиты от коррозии, хотя это один из наиболее эффективных методов.
Химические составы конверсии хромата сильно различаются, но многие из них включают применение растворов хромовой кислоты, натрия, хромата или дихромата калия для очистки металлических поверхностей вместе с другими добавками.Использование таких добавок вызывает окислительно-восстановительные реакции на поверхности, оставляя на металле подложки пассивную пленку, содержащую оксид хрома (IV) и гидратированные соединения. Это обеспечивает высокую коррозионную стойкость и хорошо сохраняет последующие покрытия.
Высокая защита от коррозии обусловлена способностью соединений хрома (VI) восстанавливать защитную оксидную пленку на поврежденном участке покрытия, подвергающемся воздействию атмосферного кислорода. Это называется самовосстановлением. Аналогичный механизм используется для создания нержавеющей стали: хром, добавленный к сплаву, естественным образом образует очень тонкий пассивный слой оксида хрома на поверхности, предотвращая окисление железа.Он быстро восстанавливается, если поверхность повреждена, а подповерхностный хром подвергается воздействию атмосферы. Хромат также можно использовать в качестве добавки к краскам или в качестве герметика при анодировании, повышая их защиту от коррозии.
Однако в настоящее время известно, что соединения шестивалентного хрома, используемые при обработке с конверсией хромата, обладают повреждающими и канцерогенными свойствами. Побочные продукты хроматных конверсионных покрытий очень опасны, и поэтому неудивительно, что материалы, использующие этот процесс, занимают жесткую позицию.
Сегодня его использование запрещено во многих отраслях промышленности и строго регулируется. Он по-прежнему широко используется в аэрокосмической отрасли, не склонной к риску, но требует все большего изменения. К сожалению, он остается лучшим методом химической пассивации алюминия благодаря своим самовосстанавливающимся свойствам. В 1980-х годах начались интенсивные исследования, чтобы найти альтернативы самовосстановлению без содержания хрома, но они еще не соответствуют его общему уровню защиты. Инженеры ищут альтернативы, такие как анодирование или обработка на основе ПЭО, для повышения производительности в суровых условиях.
4. Краски
Растворы для поверхностных покрытий, такие как краски, грунтовки и другие полимерные системы, кажутся безграничными как по наличию, так и по разнообразию. Самым привлекательным преимуществом работы с красками является то, что их можно раскрашивать, обрабатывать или наносить разными способами.
Полимерные финишные покрытия также доступны в таком разнообразии и способах нанесения. Могут быть внесены альтернативные химические составы и добавки, которые обеспечивают такие свойства, как блеск, дополнительную твердость, смазывающую способность, определенные текстуры, температурную стабильность и химическую стойкость, и это лишь некоторые из них.
Краскипредставляют собой относительно недорогой метод повышения коррозионной стойкости. Однако задействованные процессы крайне неэффективны; во время нанесения до 50% покрытия может испариться, а при отверждении в печи образуются вредные побочные продукты, которые опасны и дороги в утилизации в больших объемах.
Обладая превосходной химической и особенно коррозионной стойкостью, как и другие полимерные углеводороды, краски мягкие (их твердость оценивается сравнением грифеля карандаша), что означает, что они легко царапаются и истираются.
5. Порошковые покрытия
Порошковые покрытия, как и краски, представляют собой еще один относительно недорогой вариант. Хотя преимущества порошковых покрытий во многом такие же, как у красок, но более толстые защитные слои можно наносить более эффективно и быстрее.
Покрытия толстые, что добавляет объемные слои (обычно вверх до 80 мкм), которые существенно повышают коррозионную стойкость материала. Стоимость этой дополнительной защиты заключается в увеличении толщины, а также в том, что эстетические эффекты не столь привлекательны и неодинаковы для разных материалов.
Заключение
В этой статье мы попытались дать краткий обзор покрытий из легких материалов для улучшения коррозионной стойкости легких сплавов. На самом деле существуют сотни различных методов и процессов, доступных от разных поставщиков, каждый с небольшими вариациями в способах достижения результатов.
Выбор правильного покрытия жизненно важен, но непрост. Примите целостный взгляд на процесс нанесения покрытия, начиная с ранних этапов проектирования компонентов. Геометрия компонентов, обеспечение подходящего дренажа, предотвращение несовместимых комбинаций материалов и выбор сплава — все это решающие факторы.
Для достижения наилучших результатов выберите предварительную обработку, обеспечивающую хорошую адгезию к основанию и любой последующей обработке. Верхние покрытия следует выбирать с учетом их совместимости с предварительной обработкой и требуемых конечных / функциональных / эстетических свойств.
Антикоррозийные покрытия — Мир покрытий
Антикоррозионные покрытия — незаменимый инструмент в борьбе с ржавчиной. Применяемые на всем, от автомобилей до мостов и туннелей, антикоррозионные покрытия защищают конструкции в самых суровых условиях.Сегодня существует ряд направлений роста антикоррозионных покрытий. По словам Андерса Брекке, менеджера группы по категориям отделочных покрытий Jotun Coatings, ключевые рынки включают нефть и газ, энергетику, промышленность и инфраструктуру. «Нефтегазовая промышленность по-прежнему демонстрирует хороший рост, и мы хорошо разбираемся в этой отрасли. Норвежская нефтяная промышленность расположена на пороге Jotun, и это отрасль, которую мы хорошо понимаем», — сказал он. «Мы также считаем очень интересной отрасль альтернативной энергетики.Производство ветряных мельниц — одна из областей, у которых есть потенциал. Это отрасль, в которой мы можем увидеть инновационные решения будущего. Мы надеемся, что новые альтернативные источники энергии будут стараться быть экологически чистыми по всей цепочке создания стоимости, и мы можем ожидать, что в этом виде бизнеса предпочтение будет отдано водным технологиям ». Причина в том, что клиенты не будут жертвовать какими-либо антикоррозийными свойствами, поскольку техническое обслуживание здесь может быть сложно и дорого, например ветряные мельницы, расположенные в море
Еще одним важным направлением антикоррозионных покрытий является транспортная инфраструктура.«Мы выполняем требования по ремонту / восстановлению транспортной инфраструктуры, включая шоссе и мосты, — сказал Джон Стил, президент Substrate, Inc.». «Мы также видим значительные возможности в вооруженных силах. Над наземными резервуарами для хранения нефти и прибрежными нефтяными платформами. также находятся в нашем списке приоритетов «.
Препятствия в развитии
Разработка антикоррозионных покрытий для самых разных областей применения — непростая задача. Покрытия должны соответствовать определенным эксплуатационным требованиям, а также соответствовать все более строгим экологическим нормам.� � �
«Постоянно растущие требования к характеристикам антикоррозионных покрытий в сочетании с расходами и заботой об окружающей среде делают такие важные области, как OEM, ремонт автомобилей, покрытия для тяжелых условий эксплуатации, промышленные и специальные покрытия, ключевыми областями антикоррозионного покрытия. производителей «, — сказал Ларс Кирмайер, менеджер по развитию бизнеса антикоррозионных материалов Heubach GmbH.
Одной из важных тенденций является рост площади лакокрасочных материалов на водной основе и сокращение использования покрытий на основе растворителей.«Похоже, что в будущем произойдет рост количества промышленных защитных покрытий на водной основе из-за ужесточения требований к производству с низким содержанием летучих органических соединений», — сказал Кирмайер. «Эти покрытия удобнее использовать из-за слабого запаха и безопаснее для окружающей среды».
«Летучие органические соединения являются необходимым компонентом всех органических покрытий поверхности», — продолжил Кирмайер. «Из доступных на сегодняшний день технологий окраски с низким содержанием летучих органических соединений только составы с высоким содержанием твердых частиц или водные составы в настоящее время являются практическими предложениями для защитных покрытий.Альтернативы включают покрытия, отверждаемые излучением, и порошковые покрытия. Кроме того, в последнее время в мире защитных покрытий популярным материалом стали тонкие керамические или не содержащие золь покрытия ».
Другими тенденциями на рынке, по словам Кирмайера, являются системы поверхностно-толерантных защитных покрытий или покрытия, обеспечивающие универсальную адгезию. меньше покрытий — до однослойного нанесения — и сочетаются с большой толщиной пленки и высоким глянцем.
Несмотря на все инновации, покрытие может работать наилучшим образом только при правильном нанесении.Правильная подготовка субстрата жизненно важна.
«Подготовка основания — самый важный этап процесса нанесения покрытия», — сказал Мехруз Заманзаде, сертифицированный NACE (Национальная ассоциация инженеров по коррозии) специалист по защите материалов в Matco Associates. «Надлежащая подготовка поверхности основания обеспечит долгий срок службы и высокую производительность при минимальном уходе».
Одним из способов улучшения антикоррозионных свойств защитного покрытия является достижение наилучшей адгезии к основанию.«Соответственно, предварительная обработка является очень важным фактором и сильно влияет на формирование защитного покрытия», — сказал Кирмайер. «Высокие затраты на электроэнергию и экологическое законодательство стимулировали исследования и разработки альтернативных технологий предварительной обработки. Среди них — новые тенденции, такие как нанотехнологии, силановые технологии или предварительная обработка без содержания фосфора».
Крыши Follansbee TCS II возвышаются над двумя основными жилыми зданиями в Stonnington Commons, историческим проектом реставрации, который сформировал многофункциональный комплекс из литейного цеха XIX века в Стоннингтоне, штат Коннектикут. |
Нанотехнологии продолжают предлагать некоторые захватывающие возможности для рынка антикоррозийных материалов».
«Нанотехнологии, скорее всего, будут включать в себя некоторые интересные будущие перспективы для антикоррозионных приложений, но осуществимость этой технологии для промышленного использования, особенно в отношении обработки и затраты еще не полностью доказаны, — сказал Кирмайер. — Heubach находится в тесном контакте и налаживает сотрудничество с различными университетами и институтами, которые занимаются нанотехнологиями, и в настоящее время прилагает много усилий в исследовательской работе, касающейся использования этой технологии для современных антикоррозийное развитие пигмента.«
Для Substrate, Inc. нанотехнологии были и были основой ее антикоррозионных продуктов.« Эта «новая» технология обеспечивает ковалентное сцепление наших антикоррозионных продуктов с подложками, устраняя необходимость в дорогостоящих профилях поверхности », сказал Стил.
Последние предложения продуктов
Существует ряд новых продуктов, в которых используются новейшие технологии для антикоррозионных покрытий. Со стороны поставщика Heubach разработал инновационный антикоррозионный пигмент.
«После успешного маркетинга наших антикоррозионных пигментов широкого спектра на основе модифицированных фосфатов для универсального применения, Heubach недавно разработал не содержащий цинка антикоррозийный пигмент на основе диоксида кремния, который предназначен для использования в тонкопленочных приложениях. , особенно рулонных покрытий, и будут представлены на рынке во втором квартале 2008 года », — сказал Кирмайер.
Substrate, Inc. разработала продукцию TegaTeknology, ряд покрытий с химическим прививанием, в первую очередь ориентированных на антикоррозионные покрытия для стали и алюминия.«Наши продукты содержат тщательно подобранный набор определенных мономеров в сочетании с запатентованной системой прививки / катализатора, что обеспечивает постоянную модификацию субстрата», — сказал Стил. «Основное применение наших продуктов — это грунтовка. Наши продукты требуют минимальной подготовки поверхности без образования накипи и углеводородов, и их можно наносить на плотно склеенную ржавчину. Верхние слои можно наносить непосредственно на наши грунтовки, промежуточные слои не требуются. »
По словам Заманзаде, хромат, который используется в оцинкованной кровле и подъездных путях, и свинцовые покрытия для кровельных материалов подвержены коррозии и вымыванию водой из-за дождя, что может привести к загрязнению подземных вод.«Поэтому эти покрытия следует заменить как можно скорее», — сказал он. Follansbee Steel предлагает кровельные продукты, такие как TCD II, которые представляют собой экологически чистые панели, которые обеспечивают приятный внешний вид, а также защиту от коррозии. Высокоэффективные антикоррозийные оловянно-цинковые покрытия Follansbee для меди, нержавеющей стали и кровельных панелей из углеродистой стали прошли более 17 750 часов испытаний в солевом тумане.
Jotun недавно выпустил на рынок Hardtop Flexi, гибкий полиуретан, и Hardtop XP, традиционный полиуретан с высокой твердостью.Кроме того, компания продолжит разработку экологически чистых продуктов. «Продукты на водной основе будут иметь большее значение, и мы будем уделять этому больше внимания», — сказал Брекке. «В будущем традиционные технологии будут иметь более высокий объем сухого остатка и меньше вредных растворителей».
Покрытия для контроля коррозии — Coatings World
Покрытия для промышленного ухода и защитные покрытия разработаны для защиты внешних и внутренних поверхностей от коррозии, истирания, термического, химического и УФ-разрушения.Эти системы покрытий для защиты от коррозии обычно используются в областях, где существуют экстремальные условия, такие как сильная жара, соленая вода и другие суровые климатические условия, такие как нефтегазовый, химический, инфраструктурный и энергетический сегменты.Хотя эти покрытия ценятся за их защиту от коррозии, клиентам также требуется эстетически привлекательная отделка.
AkzoNobel предлагает широкий ассортимент продукции для защиты от коррозии. «Многие из наших продуктов основаны на технологии двухкомпонентной эпоксидной смолы и наносятся непосредственно на металл (например.г. Intershield, Interseal, Interplus, Interzone, Intergard) », — сказал Ян Флетчер, региональный менеджер по маркетингу — Европа, защитные покрытия, AkzoNobel. «У нас также есть эпоксидные или неорганические цинковые грунтовки с высоким содержанием цинка (Interzinc), которые обеспечивают отличную защиту от коррозии; они обычно являются частью трехслойной схемы, которая включает цинковую грунтовку, эпоксидный промежуточный продукт и, например, полиуретановое (Interthane) или верхнее покрытие, не содержащее изоцианатов (Interfine). Там, где особенно важна стойкость к истиранию или ударам, мы предлагаем толстослойные эпоксидные покрытия, содержащие пигмент чешуйчатого пластинчатого стекла.
«Для защиты от коррозии можно использовать комбинацию грунтовок с высоким содержанием цинка, эпоксидных смол, уретанов и специальных покрытий», — сказал Джейк Охеда, глобальный менеджер по нефтехимическому сегменту PPG. «Важно учитывать тип обслуживания (погружение, атмосферное и т. Д.), Основание (черный, цветной, бетон и т. Д.), Условия окружающей среды (температура, влажность и т. Д.) И время выполнения работ (часы, дни , недель).
При выборе антикоррозионного покрытия необходимо учитывать различные факторы.
«Важны такие факторы, как стойкость к истиранию, ударам и химическому воздействию», — отметил Флетчер. «Также совместимость с катодной защитой критична, например, для некоторые приложения для морских сооружений и трубопроводов. Еще один фактор, который необходимо учитывать, — это рабочая температура стали с покрытием, поскольку только определенные технологии подходят для использования при температуре выше 120 ° C. А также внешний вид покрытия; некоторые конечные пользователи хотят, чтобы покрытие сохраняло свой цвет или блеск на определенном уровне, поэтому в зависимости от конечного использования они часто покрывают их более прочной отделкой.Другие факторы могут включать в себя время высыхания, объем сухих веществ / летучих веществ, задержку и свойства нанесения кистью / валиком ».
Подготовка основания имеет решающее значение при нанесении антикоррозионных покрытий. Эти типы покрытий обычно наносят специально обученные аппликаторы. Их можно применять как часть нового строительства или во время текущего обслуживания, чтобы обеспечить постоянную защиту активов от износа и ухудшения состояния.
«Высококачественное покрытие не будет работать хорошо при плохой подготовке основы», — сказал Флетчер.«От качества подготовки поверхности будет зависеть, как долго покрытие продержится на стали. В идеале сталь следует обезжирить, удалить прокатную окалину и ржавчину, а также подвергнуть абразивоструйной очистке, чтобы получить острый угловой профиль. Доступны и другие методы подготовки поверхности, такие как очистка проволочной щеткой и очистка электроинструментом, но качество покрытия стали не будет таким хорошим, как абразивоструйная очистка, например Sa2.5 ».
«Подготовка основания является ключом к обеспечению надлежащей адгезии и удаления любых загрязнений, которые могут повлиять на характеристики покрытия», — сказал Охеда.«Тем не менее, есть продукты, которые допускают поверхностную толерантность и допускают минимальную подготовку поверхности, но при этом могут обеспечить адекватную защиту.
При выборе систем защиты от коррозии заказчики обращают внимание на различные характеристики. «Все клиенты хотят, чтобы время до первого обслуживания было как можно дольше», — сказал Флетчер. «Обычно основные требования к техническому обслуживанию составляют не менее 15 лет после нанесения покрытия во время нового строительства, но для приложений технического обслуживания заказчики соглашаются примерно на пять лет, в зависимости от уровня подготовки поверхности, прежде чем потребуется повторное техническое обслуживание.«
» «Владельцы ищут продукты и системы, которые могут продлить срок службы их активов, а также увеличить время между графиками регулярного технического обслуживания», — согласился Охеда. «Аппликаторам нужны продукты, которые были бы конкурентоспособными по стоимости, простыми в применении и могли увеличить их производительность».
«Мы видим новые разработки в грунтовках, обеспечивающих катодную защиту, а также в более прочных эпоксидных смолах», — сказал Охеда.
«Большинство технологий, как правило, основываются на новых рецептурах с использованием e.г. существующая эпоксидная технология », — сказал Флетчер. «Появилось несколько новых технологий аминных отвердителей. Полиаспарагиновая кислота является одним из примеров новой химии, обеспечивающей технологию быстрого отверждения с низким содержанием летучих органических соединений, например, для OEM-приложения ».
Инновационный подход к нанесению покрытий обеспечивает долгосрочное решение для борьбы с коррозией в нефтехимических прибрежных активах
В нефтегазовой отрасли защита массивных активов из углеродистой стали от коррозии является постоянной проблемой во всем мире, включая Китай, особенно вдоль береговой линии подвергается воздействию высокой влажности и соленого воздуха вблизи океанов или других водоемов.
Проблема усугубляется тем фактом, что многие нефтеперерабатывающие и нефтехимические предприятия, включая резервуары и технологическое оборудование, а также наземные трубопроводы и железнодорожные вагоны, расположены рядом с портами, что облегчает хранение и транспортировку как сырой нефти, так и продуктов ее переработки.
Типичной превентивной мерой является использование покрытий барьерного типа, которые обычно повторно наносят каждые несколько лет в этих прибрежных зонах высокого риска. Это может быть дорогостоящим и разрушительным для нефтегазового производства, требуя удаления старого покрытия, очистки поверхности и повторного нанесения нескольких покрытий.Несмотря на это дорогостоящее обслуживание, чрезмерная коррозия таких активов из углеродистой стали может привести к утечкам, пожарам и несчастным случаям, а также ускорить преждевременную замену.
Теперь на этих прибрежных нефтехимических активах инновационный подход к нанесению покрытий обеспечивает долгосрочное решение для борьбы с атмосферной коррозией, сводя к минимуму простои производства и повышая безопасность.
Китайский портовый город Нинбо, ограниченный на востоке Восточно-Китайским морем и на севере заливом Ханчжоу, имеет очень влажный, влажный климат, а также соленый воздух, которые вызывают коррозию нефтехимических активов в область конкретной проблемы.В течение десятилетий в регионе выпадало в среднем более 56 дюймов / 1440 мм дождя, а также более 157 дней с осадками и средняя относительная влажность 80% +, не говоря уже о сезоне муссонов.
В этих тяжелых условиях Ningbo Xingang Fuel Storage Company стремилась защитить свои активы от коррозии. Однако коррозия их оборудования из углеродистой стали довольно серьезна. Перед компанией стояла особая задача по защите двух огневых пушек и вспомогательных огневых рубежей на восточной и западной стороне терминала сырой нефти мощностью 50 000 тонн, расположенного в районе Бейлун в Нинбо.
Традиционные методы защиты, такие как нанесение полимерных красок и покрытий резинового типа, оказались неэффективными и теряют свой эффект вскоре после нанесения.
Хотя эти методы могут создавать физический барьер, удерживающий стимуляторы коррозии, такие как вода и кислород, от стальных подложек, они работают только до тех пор, пока краска не поцарапается, не потрескается или не потрескается, а активаторы коррозии не попадут в зазор между подложкой и покрытием. Тогда покрытие может действовать как теплица, задерживая воду, кислород и другие ускорители коррозии, что позволяет коррозии распространяться.
Из-за этих суровых условий компания искала лучшее решение и обратилась к EonCoat, неорганическому покрытию, наносимому распылением от одноименной компании из Роли, Северная Каролина, для использования в проекте защиты от коррозии с целью продления срока службы. водометные пушки и вспомогательные линии огня. EonCoat представляет новую категорию прочной химически связанной фосфатной керамики (CBPC), которая может остановить коррозию, упростить нанесение и сократить время простоя производства.
В отличие от традиционных полимерных покрытий, которые наносятся поверх подложки, коррозионно-стойкое покрытие CBPC связывается посредством химической реакции с подложкой, и небольшое окисление поверхности фактически улучшает реакцию.Образуется слой сплава. По сообщению компании, из-за этого активаторы коррозии, такие как кислород и влажность, не могут проникнуть за покрытие, как это делают обычные краски.
Хотя традиционные полимерные покрытия механически связываются с основами, которые были тщательно подготовлены, при выдолблении влага и кислород будут мигрировать под пленку покрытия со всех сторон канавки.
Напротив, такое же повреждение подложки с керамическим покрытием не приведет к распространению коррозии на предприятиях нефтегазовой отрасли, поскольку поверхность углеродистой стали превращается в сплав стабильных оксидов.Как только поверхность стали становится стабильной (как стабильны благородные металлы, такие как золото и серебро), она больше не вступает в реакцию с окружающей средой и не может подвергаться коррозии.
EonCoat, видимый на фотографиях, сделанных с помощью сканирующего электронного микроскопа, не оставляет зазора между сталью и покрытием, поскольку связь является химической, а не механической. Поскольку зазора нет, даже если влага должна проникнуть в сталь из-за зазубрины, влаге некуда перемещаться. Это эффективно предотвращает атмосферную коррозию прибрежных резервуаров и других нефтехимических объектов.
Барьер от коррозии покрыт керамической оболочкой, которая дополнительно противостоит коррозии, огню, воде, истиранию, ударам, химическим веществам и температурам до 400 ° F. Помимо этого, керамическая оболочка выполняет уникальную роль, помогая завершить дорогостоящий цикл обслуживания, заключающийся в замене типичных покрытий барьерного типа каждые несколько лет.
«На прибрежных нефтехимических объектах, таких как нефтеперерабатывающие заводы и резервуарные парки, если керамическая оболочка и слой сплава когда-либо будут повреждены, керамическая оболочка действует как резервуар фосфата для постоянного повторного плавления стали», — пояснил Меррик Альперт, президент компании EonCoat.«Это« самоизлечивает »разрыв, в зависимости от его размера, и, при необходимости, останавливает коррозию. Эта способность, наряду с другими свойствами покрытия, обеспечивает эффективную защиту от коррозии в течение всего срока службы актива за одно нанесение ».
Проект Ningbo Xingang Fuel Storage Company был успешно покрыт неорганическим покрытием, нанесенным распылением, и добавлен верхний слой. EonCoat совместим с широким спектром обычно используемых финишных покрытий.
Благодаря многослойной защите от коррозии керамического покрытия и способности «самовосстановления» повреждений прибрежный объект находится на пути к обеспечению долгосрочной защиты своего оборудования, эффективно прерывая дорогостоящий цикл взрывных работ и перекраски каждые несколько лет. .
Руководители нефтегазовых операций или инженеры по коррозии, стремящиеся сократить расходы, находят дополнительные преимущества у покрытий CBPC, таких как EonCoat, помимо коррозионной стойкости.
Например, один из способов, которым правительство Китая работает над смягчением негативных последствий загрязнения воздуха, — это обращение к экологически чистым альтернативам, таким как покрытия CBPC, которые являются неорганическими и нетоксичными, поэтому в них нет ЛОС, нет HAP и без запаха. Это означает, что негорючие покрытия можно безопасно наносить даже в ограниченном пространстве.
Такие покрытия состоят из двух безопасных компонентов, которые не взаимодействуют друг с другом до тех пор, пока не будут нанесены с помощью стандартной промышленной системы множественного распыления, подобной тем, которые обычно используются для нанесения покрытий из пенополиуретана или полимочевины.
Одним из важнейших дополнительных преимуществ является быстрое возвращение к работе, что сводит к минимуму время простоя оборудования. Экономия времени на проекте антикоррозионного покрытия с керамическим покрытием достигается как за счет упрощенной подготовки поверхности, так и за счет ускоренного времени отверждения.
При типичном антикоррозийном покрытии для подготовки поверхности требуется струйная очистка почти белого металла (NACE 2 / SSPC-SP 10).Но с керамическим покрытием обычно требуется только промышленная струйная очистка NACE 3 / SSPC-SP 6.
Для проектов защиты от коррозии с использованием типичных полимерных красок, таких как полиуретаны или эпоксидные смолы, время отверждения может составлять дни или недели до нанесения следующего слоя традиционных «трехкомпонентных систем», в зависимости от продукта. Время отверждения необходимо для того, чтобы каждый слой полностью раскрыл свои свойства, даже если он может казаться сухим на ощупь.
При использовании традиционных покрытий требуется тщательная подготовка поверхности, которая проводится постепенно, чтобы избежать окисления поверхности, широко известного как «мгновенная ржавчина», которая может потребовать повторной струйной очистки.
Напротив, коррозионно-стойкое покрытие для углеродистой стали с использованием керамического покрытия в один слой почти не требует времени отверждения. Возврат к работе может быть выполнен всего за один час. Такая скорость возобновления добычи актива может потенциально сэкономить сотни тысяч долларов в день за счет сокращения времени простоя в нефтегазовых приложениях.
Поскольку атмосферная коррозия является постоянной проблемой для нефтегазовых предприятий с массивными конструкциями из углеродистой стали, использование покрытий CBPC, которые могут предотвращать коррозию в течение десятилетий, только поможет чистой прибыли.•
Какие бывают виды антикоррозионных \ антикоррозионных покрытий?
Исследование, проведенное крупной отраслевой ассоциацией NACE (Национальная ассоциация инженеров по коррозии), показало, что ежегодные затраты на борьбу с коррозией в США составляют 279 миллиардов долларов. На тот момент, когда исследование было заказано Федеральным управлением шоссейных дорог, эта цифра составляла 2–3% ВВП США.
Исследователи определили, что до 30% этих затрат — около 83 миллиардов долларов — могут быть устранены, если будут реализованы установленные протоколы защиты от ржавчины и коррозии.С тех пор коррозия остается трудноразрешимой проблемой, но успехи в борьбе с ней были значительными.
Существует несколько различных промышленных покрытий с антикоррозийными свойствами. Многие также обладают другими эксплуатационными качествами, что делает их хорошими универсальными покрытиями для промышленных или коммерческих целей.
Очень важно, чтобы тип покрытия соответствовал основанию и рабочей среде, на которую оно будет наноситься. Имея это в виду, на большинстве рабочих мест потребуется несколько разных типов покрытий.Правильное покрытие снижает коррозию, продлевает срок службы и упрощает техническое обслуживание в будущем. Нередко использование этих покрытий в качестве основы перед нанесением других покрытий для защиты поверхности.
Во многих случаях на одну подложку наносят несколько покрытий или покрытия специально разрабатываются для решения поставленной задачи. Однако есть некоторые широко известные антикоррозионные покрытия, подходящие для ряда распространенных ситуаций.
Некоторые из лучших антикоррозионных покрытий включают:
ФторполимерФторполимер — это смесь высокоэффективных смол в сочетании с фторполимерными смазочными материалами.В их состав входит превосходная твердая пленочная смазка, которая контролирует истирание за счет значительного уменьшения трения. Фторполимер полезен в средах с очень высокими и очень низкими температурами.
Хотя фторполимер выбран в основном из-за коррозионной стойкости, он также устойчив к коррозионным химическим веществам. Он также обладает некоторым электрическим сопротивлением. Такое сочетание характеристик делает его пригодным для крепежа и компонентов OEM, продлевая срок их службы.
ЭпоксиднаяЭпоксидная смола — одно из самых распространенных промышленных покрытий.Это часто обсуждают с точки зрения систем напольных покрытий из эпоксидной смолы. Однако его можно использовать повсюду на производстве. Различные составы эпоксидной смолы имеют радикально разные свойства проводимости и термостойкости.
Существует два основных типа эпоксидного покрытия:
1. Эпоксидное покрытие, высушенное на воздухеЭпоксидное покрытие, сухое на воздухе, применяется исключительно для металлических поверхностей. Обладает высокой антикоррозийной и антихимической стойкостью. Одинарный слой обеспечивает защиту от коррозии при толщине 4-6 миллиметров.Обычно он используется в двух- и трехслойных системах на объектах нефтегазовой отрасли.
2. Expoxy покрытие термического отвержденияЭпоксидные покрытия с термическим отверждением обеспечивают лучшую защиту от коррозии в сложных промышленных условиях. Высокая молекулярная масса означает сосуществование исключительной стойкости к ударам и истиранию. Это популярное покрытие в отраслях, где используются щелочные и щелочные растворы.
ФосфатФосфат — это вид конверсионного покрытия для стали и других металлов.Он имеет кристаллическую структуру, сформированную на подложках из черных металлов. Используется для предварительной обработки перед нанесением покрытия или окраски промышленных поверхностей. Помимо защиты от коррозии, он улучшает фрикционные свойства скользящих компонентов. С соответствующим масляным верхним слоем он может препятствовать образованию ржавчины на резьбовых компонентах.
Цинк неорганическийНеорганический цинк — идеальная форма защиты от коррозии для металлических поверхностей, подвергнутых струйной очистке. Он обеспечивает лучшую защиту от коррозии на рынке и эффективен против атмосферных воздействий, солей и растворителей.В прибрежных установках широко используются покрытия из неорганического цинка. Мы обнаружили, что многие морские суда использовали эту форму защиты.
Неорганический цинк обладает тем преимуществом, что он совместим с широким ассортиментом финишных покрытий, которые могут дополнительно усилить его защиту от коррозии. Он работает с эпоксидными смолами, фенольными смолами, акрилом, силиконом и многими другими. Это следует учитывать для химических заводов и нефтеперерабатывающих заводов, а также для силосов и промышленных резервуаров.
Это всего лишь образец антикоррозионных покрытий, доступных на сегодняшний день.Любой план покраски должен начинаться с комплексной оценки участка с подробным описанием окружающей среды и ее опасностей. Только помня об этом, покрытия можно использовать стратегически для оптимизации их эффектов и преимуществ.
Чтобы узнать больше или начать работу, запросите бесплатную смету проекта у Performance Painting Contractors.
Антикоррозийное защитное покрытие и применение
Антикоррозийные, антикоррозионные покрытия, металлические или защитные покрытия защищают металлические компоненты от разрушительного воздействия промышленных химикатов, факторов окружающей среды, окисления, солевого тумана и влаги.Антикоррозийные защитные покрытия являются дополнительной защитой металлических поверхностей и действуют как барьер, препятствующий контакту между коррозионными материалами и химическими соединениями.
Помимо защиты от коррозии, защитное покрытие обеспечивает химическую защиту, антипригарные свойства и стойкость к истиранию. Покрытия обладают антикоррозийными свойствами, что гарантирует максимально долгий срок службы металлических компонентов.
Применение покрытийРазличные покрытия используются для разных ситуаций, в зависимости от того, как металлы подвергаются воздействию, будь то в агрессивных химических, промышленных или морских средах.Несколько покрытий можно использовать для всех типов ситуаций, даже от экстремальных химикатов, соленой воды и влажности.
- Фторполимер — Смеси смолы и смазки, обеспечивающие высококачественную защиту от коррозии.
- Ксилан — фторполимер, который может продлить срок службы компонентов.
- Дисульфид молибдена — защита от трения при нагрузках под высоким давлением.
- Эпоксидное или воздушно-сухое — экономичное антикоррозийное покрытие.
- Эпоксидное термическое отверждение — Превосходная ударопрочность, стойкость к истиранию и коррозии.
- Фенольный — идеально подходит для сред с низким pH и высокими температурами.
- Фосфат — покрытие из черных металлов для предотвращения заедания и незначительной коррозионной стойкости.
- Цинк неорганический — Защита стали от коррозии и атмосферных воздействий.
- PTFE (политетрафторэтилен) — антипригарное покрытие, способное выдерживать высокие температуры.
- FEP (фторированный этилен-пропилен) — характеристики ПТФЭ с улучшенными абразивными свойствами.
- Химическое эпоксидное покрытие — уникальное стойкое к истиранию покрытие, которое защищает, связывая керамические частицы с системой смолы.
Для других целей металлические покрытия могут использоваться в качестве смазочных материалов или противовращающих средств. Например, крепежные детали, болты и винты, которые являются металлическими, можно обработать металлическими покрытиями, чтобы их было легче затягивать или откручивать.
Пройдитесь по дому, и вы можете найти металлические покрытия на уличной мебели, заборах или принадлежностях для бассейнов. Металлическое покрытие защищает эти металлы от погодных условий, поэтому они не ржавеют, когда им приходится выдерживать ливень.Одной из распространенных форм стального покрытия, обычно распознаваемой вокруг любого дома, является оцинкованная сталь.
Гуляя где угодно, вы можете заметить, что металлические покрытия могут быть составлены и применены как для функциональных, так и для косметических целей. Например, когда на самолет наносится металлическое покрытие, поверхность должна быть гладкой. Черновая отделка негативно повлияет на аэродинамику самолета. Это функционально. Выбор цвета металлического покрытия тяжелого оборудования — это косметический выбор, который можно выбрать по вкусу производителя.
Если у вашей компании есть металлические изделия, для которых может быть полезно нанесение защитных металлических покрытий, таких как покрытие из раствора сополимера поливинилхлорида, позвоните специалистам Unituff. Эксперты Unituff познакомят вас с металлическим покрытием Unituff 452 (ранее Seal‘n’Peel ) и покрытием Unituff OGS, специально разработанным для нержавеющей стали.
Поверхность и антикоррозийное покрытие | Технические спреи | Химическая продукция | Продукция
По фильтру результатов не найдено!
Конвертер ржавчины- Преобразователь ржавчины и базовое покрытие за один процесс
Содержание 0.4 литра (39,98 € / 1 литр)
15,99 €
Спрей из нержавеющей стали- коррозионностойкое и эффективное покрытие поверхности
Содержание 0,4 литра (49,68 € / 1 литр)
19,87 €
Алюминиевый спрей А-100- отличная защита от коррозии
- стойкость к истиранию
Содержание 0,4 литра (44,05 € / 1 литр)
17,62 €
Цинковый спрей- Долговременная катодная защита от коррозии
Содержание 0.4 литра (44,98 € / 1 литр)
17,99 €
Спрей хром-серебро- глянцевое антикоррозионное покрытие поверхности на алюминиевой основе
Содержание 0,4 литра (44,35 € / 1 литр)
17,74 €
Цинк-алюминиевый спрей- Предпочтительно для ремонта поврежденного цинкования
- Цветовой оттенок соответствует горячему цинкованию
Содержание 0,4 литра (39,35 € / 1 литр)
15.74 €
Гальва спрей- Долговечная катодная защита от коррозии, под покраску
- Цвет соответствует горячему цинкованию
- > 450 часов при испытании в солевом тумане согласно DIN EN ISO 9227
Содержание 0,4 литра (39,35 € / 1 литр)
15,74 €
Защита от ржавчины 2000 PLUS- специальное покрытие поверхности, устойчивое к коррозии и атмосферным воздействиям
Содержание 0.4 литра (44,98 € / 1 литр)
17,99 €
Латунный спрейСодержание 0,4 литра (48,73 € / 1 литр)
19,49 €
Золотой спрей- высококачественный и эффективный спрей для металла
Содержание 0,4 литра (50,60 € / 1 литр)
20,24 €
Защита от коррозии- Антикоррозийная защита металлических деталей складских помещений
Содержание 0.4 литра (29,08 € / 1 литр)
11,63 €
Изоляционный спрей- Диэлектрическая прочность Кристально чистый
Содержание 0,4 литра (53,73 € / 1 литр)
21,49 €
Медный спрейСодержание 0,4 литра (48,73 € / 1 литр)
19,49 €
.