Обработка порогов автомобиля – делаем все самостоятельно!
Коррозия, мелкие камушки, песок и соли наносят существенный вред вашему «железному коню», поэтому крайне желательно знать, как именно осуществляется антикоррозийная обработка порогов автомобиля, своими руками вы сможете выполнить ее после прочтения нашей статьи. Первый раз сделать эту процедуру рекомендуется, конечно, у специалистов, а в дальнейшем можно будет обойтись и своими силами, просто поддерживая актуальность защиты.
Обработка порогов – посетить СТО или сделать самостоятельно?
При современном состоянии автопрома антикор для корпуса делают еще на заводе-производителе, но, дабы машина не вышла из строя раньше, чем предполагает гарантийное обслуживание, его следует повторять каждые два года. Благодаря этому вы сможете поддерживать целостность заводского покрытия максимально длительный срок. Таким образом, вы защитите наиболее уязвимые места вашего авто, а ими являются сварные швы, скрытые полости, колесные арки, пороги, днище и загибочные соединения.
Главным отличием между антикоррозионной обработкой, которую вы сделаете дома, и обработкой на специализированной станции является, конечно, наличие профессионального оборудования у вторых. Благодаря этому намного проще тщательно вымыть днище авто, а затем осуществить его принудительную сушку. Кроме того, на станциях производится комплексная обработка несколькими покрытиями, естественно, можно попытаться все это сделать и самостоятельно, но тогда вам такой эксперимент обойдется в копеечку, да и отсутствие опыта возьмет свое, так что экономия будет сомнительной.
Также специалисты обязательно установят брызговики и подкрылки, таким образом, защита наружной части автомобиля от воды песка и гравия будет более надежной.
Антикоррозионная обработка порогов автомобиля своими руками
Повторная обработка порогов авто проводится самостоятельно, для этого понадобятся: антикоррозионное средство ( Otrix, Rand, Novol, Car System, Roberlo и т. д.), средство от ржавчины, наждачная бумага или металлическая щетка, респиратор и перчатки. Покупая антикоррозионное средство, следует обращать внимание на все мелочи: назначение, срок годности, особенности применения. А в дальнейшем важно строго придерживаться инструкции на упаковке.
Для начала тщательно вымойте авто от грязи и просушите. Постарайтесь обеспечить доступ ко всем местам обработки, в случае работы с днищем машину следует установить на эстакаду. Удалите ржавчину при помощи наждачной бумаги или металлической щетки. Теперь обработайте поверхность средством от ржавчины и дайте хорошенько высохнуть.
Приступаем к обработке приобретенным средством. Его равномерно нанесите на пороги автомобиля и другие части, требующие защиты с помощью данного состава. Остается просушить авто в течение суток. Кроме того, чтобы не нанести вред своему здоровью, рекомендуется работать в перчатках и респираторе.
Обработка порогов антигравием – последовательность операций
Обработка порогов антигравием происходит практически аналогично:
- авто тщательно моется и высушивается;
- наждачной бумагой удаляется ржавчина и облущенная краска;
- с помощью газет и скотча закрываем все места, прилегающие к порогам, чтобы не запачкать их. кстати, это необходимо делать в каждом случае, когда используется баллончик с распылителем;
- потрясите баллончик на протяжении 3–5 минут;
- нанесите антигравий с расстояния 25 см;
- дайте нанесенному слою высохнуть на протяжении 5 минут;
- повторите процедуру еще 1-2 раза;
- просушите авто в естественных условиях в течение хотя бы двух часов.
Возможно, вы постоянно слышите, насколько эффективна обработка порогов гравитексом, но, по сути, это тот же антигравий, и, соответственно, все вышеперечисленные операции выполняются в том же порядке. Перед тем как покупать это антикоррозионное средство, просмотрите внимательно его характеристики, так как он бывает окрашиваемым и не окрашиваемым. Тут также не забывайте про безопасность кожи рук и дыхательных путей и внимательно читайте инструкцию перед применением.
Обработка порогов автомобиля — как правильно предотвратить коррозию?

Обработка порогов – посетить СТО или сделать самостоятельно?
Современные производители автомобилей делают антикоррозийную обработку машины в целом прямо на заводе при изготовлении машины. Но Вы часто можете услышать, что такую процедуру желательно повторять один раз в два года, дабы транспортное средство раньше времени не вышло из строя. Если вовремя повторять процедуру антикоррозийной обработки, станет возможным максимально надолго сохранить заводское покрытие в первозданном состоянии. Так самые уязвимые и слабые узлы Вашего автомобиля, то есть скрытые от глаз полости, сварочные швы, колесные арки, днище, пороги, соединения с загибами, будут защищены.
Если сравнить антикоррозийную обработку, выполненную дома и специалистом на станции технического обслуживания, то разница будет заметной по причине того, что профессионалы используют специальное оборудование, разработанное специально для выполнения таких видов работ. Специальные приспособления в разы упрощают процесс мойки днища автомобиля, после чего выполняется принудительная его сушка. Более того, работники станции делают комплексную обработку автомобиля, создавая несколько покрытий.
Подобную работу можно попробовать сделать в домашних условиях, но будьте готовы потратить значительное количество финансовых средств по причине сложности работ и отсутствия опыта. В совокупности такие минусы не позволят в результате сэкономить.
Впервые процедуру антикоррозийной обработки желательно сделать у специалистов, после чего можно будет перейти к самостоятельному выполнению, так как необходимо будет только поддерживать в надлежащем состоянии уже сделанное покрытие. Специалистами в обязательном порядке будут установлены подкрылки и брызговики, которые создадут надежную защиту наружной части машины от повреждений водой, песком и гравием.
Антикоррозионная обработка порогов автомобиля своими руками
Повторно обработать пороги автомобиля можно будет самостоятельно. Для выполнения такой процедуры Вам необходимо будет приобрести антикоррозийное средство типа Novol, Otrix, Car System, Rand, средство против ржавчины, наждачную бумагу или обычную металлическую щетку, а также перчатки и респиратор для индивидуальной защиты. При покупке антикоррозийного средства нужно будет обратить особое внимание на такие характеристики, как срок годности, назначение, а также на особенности и показания к применению. В дальнейшем обязательно нужно будет читать инструкцию на упаковке со средством и выполнять ее.
Перед началом работ машину нужно тщательно вымыть, удалив всю грязь, после чего авто нужно просушить. Попытайтесь открыть доступ к любому труднодоступному месту, а если работа будет выполняться с днищем авто, то машину нужно будет загнать на эстакаду. Ржавчину нужно удалять при помощи наждачной бумаги или металлической щетки. После этого нужно будет покрыть все поверхности средством против ржавчины, после чего машине нужно дать высохнуть.
После таких процедур можно переходить к обработке поверхностей непосредственно антикоррозийным средством, которые Вы приобрели. Наносить его нужно равномерно, пороги и другие требующие защиты элементы авто должны быть покрыты ровным слоем состава. Средство должно сохнуть на протяжении суток. При роботе необходимо будет убрать все близлежащие нагревательные приборы и источники открытого огня по причине того, что антикоррозийные средства склонны к быстрому воспламенению. Дабы не навредить себе и своему здоровью, специалисты рекомендуют использовать средства индивидуальной защиты (респиратор, перчатки).
Обработка порогов антигравием – последовательность операций
Обрабатывать пороги автомобиля антигравием нужно по аналогичной схеме:
— машину нужно тщательно вымыть и просушить;
— ржавчину и облущенную краску нужно удалить наждачной бумагой;
— используя газеты и скотч, нужно закрыть все те области, которые прилегают к порогам, дабы не дать им запачкаться, проделывать подобную процедуру нужно каждый раз, когда Вы работаете с покрытием машины при помощи баллончика с распылителем;
— баллончик нужно встряхнуть 3 – 5 минут;
— далее следует нанесение антигравия, соблюдая дистанцию в 25 см от поверхности;
— созданный слой нужно оставить на 5 минут для высыхания;
— повторить процедуру нужно еще пару раз;
— машину нужно просушить в максимально обычных условиях на протяжении не менее двух часов.
Наверняка при покупке антигравия консультант магазина скажет Вам несколько фраз о том, что существует другое крутое средство для обработки порогов авто – гравитекс, якобы работает оно более эффективно, но стоить может немного дороже. По своей суть гравитект от антигравия не отличается, а процедура нанесения нового средства неизменна. Перед покупкой такого средства против коррозии нужно тщательно изучить упаковку, где будут описаны характеристики субстанции. Следует обратить внимание на то, окрашивает или не окрашивает данное средство ту поверхность, на которую субстанция наносится. В это время следует тщательно защитить дыхательные пути и кожу рук, а перед началом работ нужно изучить инструкцию.
Подписывайтесь на наши ленты в таких социальных сетях как,
Facebook,
Вконтакте,
Instagram,
Pinterest,
Yandex Zen,
Twitter и
Telegram:
все самые интересные автомобильные события собранные в одном месте.
Антикоррозийная обработка порогов автомобиля / Антикор154
Наша компания проводит быструю и качественную антикоррозийную обработку порогов автомобиля. Это позволяет не только защитить от появления ржавчины, но и остановить уже начавшую распространяться порчу. Мы работаем со всеми видами и марками машин, строго соблюдаем сроки и отвечаем на все интересующие клиентов вопросы.
Как проводится обработка порогов против коррозии
Сам порог автомобиля относится к категории особенно уязвимых мест. Причина заключается в высокой интенсивности использования, постоянном механическом воздействии. Расположение также играет свою роль – эта часть кузова периодически намокает, к ней прилипает грязь. Это запускает процесс окисления, который и проявляется как ржавение.
Наша компания отлично разбирается во всех средствах для обработки кузова машин от коррозийного воздействия. Могут использоваться следующие методы:
· Профилактическая обработка. Заключается в использовании специальных составов, которые при нанесении на лакокрасочное покрытие машины создают защитный слой. Он отталкивает влажность и грязь, не дает металлу контактировать с воздухом. Такой слой незаметен на поверхности, долго держится, неподвержен механическому воздействию.
· Обработка пораженных участков. Так часто проводится антикоррозийная обработка порогов автомобиля изнутри. Мы применяем специальные составы, действующие как ингибиторы. Они эффективно останавливают распространение коррозии, отличаются высоким уровнем качества. Если поражение сильное, можно существенно замедлить его распространение.
Решение о том, какую методику нужно применять, принимается на основании детального анализа текущего состояния машины. Оба метода также подойдут и в комбинации. Тогда после зачистки пораженных участков, выполняется нанесение внешнего защитного слоя.
Чтобы оформить заказ на обработку от коррозии, звоните нам по телефону +7 (383) 301‒86‒36. Располагаемся в Новосибирске, по адресу ул. Связистов, 12Б к23.
Антикоррозийная обработка порогов автомобиля своими руками. | Все об автомобиле и не только
В данной статье поговорим о антикоррозийной обработке порогов автомобиля в гаражных условиях. Каждый автолюбитель сталкивался со ржавчиной на порогах, так как это самая уязвимая часть кузова, которая больше всего подвержена механическим воздействиям. Антикоррозийная обработка порогов способна остановить распространение ржавчины, если же этого не сделать, то последствия будут печальными, а ремонт в последующем будет стоить намного дороже.
Перед обработкой антикором необходимо тщательно отмыть пороги, при
этом необходимо снять защитные элементы если таковые присутствуют. Лучше это сделать с применением автохимии и мощного напора воды, далее нужно дать порогам высохнуть.
Следующим этапом является удаление очагов ржавчины, если таковые присутствуют. Для этого необходимо металлической щеткой или специальной насадкой на дрель, пройтись по очагу коррозии. После механического удаления ржавчины следует химический этап, специальным составом на основе ортофосфорной кислоты, нужно покрыть место, зачищенное от коррозии место, когда на данном участке появится светлый налет, свидетельствующий о химической реакции кислоты с оксидом железа, можно приступать к следующему этапу.
Далее необходимо нанести защитный состав. Защитные составы можно разделить на несколько групп по типу нанесения:
- составы которые наносятся аэрозольным способом, такие составы продаются в баллончиках, их отличает простота нанесения и малый расход, но стоимость их выше, чем у составов, которые наносятся вручную. Так же такие составы по мере высыхания немного увеличиваются в объеме и создавая более толстую защитную основу.
- составы которые наносятся вручную, например кистью, наносить такие составы сложнее, но стоимость их меньше.
А так же различают по типу защитной основы:
- пушечное сало.
- битумные мастики.
- автопластилин.
- раст-стоп.
Выбор антикора — это дело каждого, кому что нравится, но даже самый плохой антикор лучше, чем его отсутствие. Далее наносим антикоррозийный состав на пороги, ждем пока состав высохнет, в среднем достаточно 12 часов. Устанавливаем на место защитные элементы крепления.
Кроме защиты от коррозии у антикора есть еще одно положительное свойство это дополнительная шумоизоляция.
Ели Ваша цель заключается в защите порогов от коррозии и сохранении эстетического внешнего вида авто, то можно приобрести цветной антикоррозийный состав, который подходит к цвету кузова например белый, черный, серый. Если цвет антикора не пошел к цвету кузова автомобиля, то можно поверх такого состава нанести слой краски, подходящего цвета.
В заключении хочу сказать, что антикоррозийная обработка — это не разовая процедура, её нужно производить регулярно, хотя бы 1 раз в 3 года.
Спасибо за просмотр!
Антикоррозийная обработка — Центр антикоррозийной обработки Dinitrol66.

Не стоит думать, будто бы на заводе уже позаботились о вашем автомобиле: ни вы, ни компания-дилер, в которой вы приобретали авто — никто не может быть уверен в том, что антикоррозионная обработка, проведенная изготовителем, способна выдерживать огромные нагрузки в виде ливней, снегопадов, солей. Вот почему антикоррозионная обработка бывает актуальной не только для подержанных авто, но и для новых машин.
Нужно ли делать антикоррозионную обработку? Этим вопросом задаются миллионы автомобилистов в нашей стране. Наш ответ однозначен – конечно, нужно! Именно антикоррозионная обработка, которая наносится на днище кузова автомобиля, арки колес, а также на другие внешние и внутренние детали транспортного средства, способна минимизировать негативные воздействия окружающей среды.
Этапы антикоррозийной обработки:
— экспресс мойка кузова;
— профессиональная мойка днища автомобиля со спец-шампунем;
— демонтажмонтаж подкрылок (локеров) и прочих элементов (пластиковые защиты и термоэкраны), препятствующих антикоррозийной обработке;
— обработка днища автомобиля износоустойчивым антикоррозийным средством Dinitrol 4941;
— обработка порогов антикоррозийным покрытием Dinitrol 4941;
— обработка скрытых полостей антикоррозийным покрытием Dinitrol ML.
(Скрытые полости: пороги, лонжероны, стойки кузова, поперечины и усилители днища, места под молдингами и накладками, усилители моторного отсека, усилители капота, усилители крышки багажника)
Цены на антикоррозийную обработку -> ЦЕНЫ.
Используемые материалы ->Антикоррозийные материалы Dinitrol
Защита порогов автомобиля
Лада Приора Седан TheEmerald › Бортжурнал › Антикоррозийная обработка порогов.

Часть 1. Подготовка
Аж год назад я подошёл к антикоррозийной обработке машинки, начиналось это тогда с задних арок, но до последнего времени всё никак не получалось дать продолжение. И вот, наконец, через почти 13 месяцев я вернулся к этой теме. После традиционного прочтения немалого количества записей бортовых журналов, составил список необходимых вещей и отправился в магазин для приобретения недостающих компонентов:
• Мовиль с преобразователем ржавчины и распылителем в аэрозоли 1000мл
• Нейтрализатор ржавчины 330мл
• Полимерно-битумный антикор «Кордон» 2кг
• Перчатки
• Кисть
• Обезжириватель, например бензин-калоша
• Малярный скотч
• Щетка металлическая
Часть 2. Процесс, день 1.
Решил не затягивать до вечера, хоть и стояла сильная по местным меркам жара, а приступил днем или даже утром. Пришёл в гараж, распахнул ворота и выкатил машину, уже чистенькую. Начать решил с левой, водительской стороны.
Открыл дверки, вывернул руль влево, после чего выкрутил 3 болта, скрывавшиеся передней дверью, и также 3 болта, скрывавшиеся дверью задней. Далее выкрутил болт, удерживающий порог возле заднего колеса, 2 болта и 1 гайку под ключ на 10, удерживающие фронтальный брызговик, и последний болт, скрывавшийся под брызговиком. Также можно открутить ещё один болт, соединяющий брызговик и порог между собой, но абсолютно необязательно — разъединять их не имеет практического смысла.
Крепёж, разумеется, выглядел не свежим, а потому сложил его в кучку и полил нейтрализатором ржавчины. Вооружившись плоской отвёрткой, легким, но аккуратным, так как пару раз встречал упоминания у поломках этих штучек, движением руки, удалил 3 клипсы, после чего порог был освобождён и лёг на землю, попутно высвободив немалое количество песка и открыв вид на несколько очагов коррозии.
2 из 3х клипс видны в левой части фото
Малярным скотчем закрыл участок кузова, граничащий с обрабатываемой поверхностью, смыл небольшим количеством воды и губкой всю грязь, скрывавшуюся от глаз долгое время, и вынул 6 втулок под болты, скрывавшиеся дверьми.

Ну а раз уж взялся за баллон с мовилем, решил попутно пропихнуть распылитель в каждое из дренажных отверстий каждой из дверей, и хорошенько всё облить и там. Лил до той поры, пока мовиль не начал выливаться наружу. Я полагаю, хуже не будет.
Умаявшись, в попытках справиться щеткой, достал дрель, одел на неё насадку, родственную ручным металлическим щёткам, и счистил по шву всё до металла, дабы обнаружить и уничтожить максимальное количество проблем.
А вот и дрель с насадкой попала в кадр
Оум… Порог в фокус не попал
Всю обрабатываемую поверхность буквально облил нейтрализатором ржавчины, выждал минут 10-15, обезжирил бензин-калошей и покрыл «Кордон’ом». Потратил примерно половину, может чуток больше, 1кг банки.
И, наконец, вернул предварительно промытый порог, вернее будет сказать облицовку, на место.
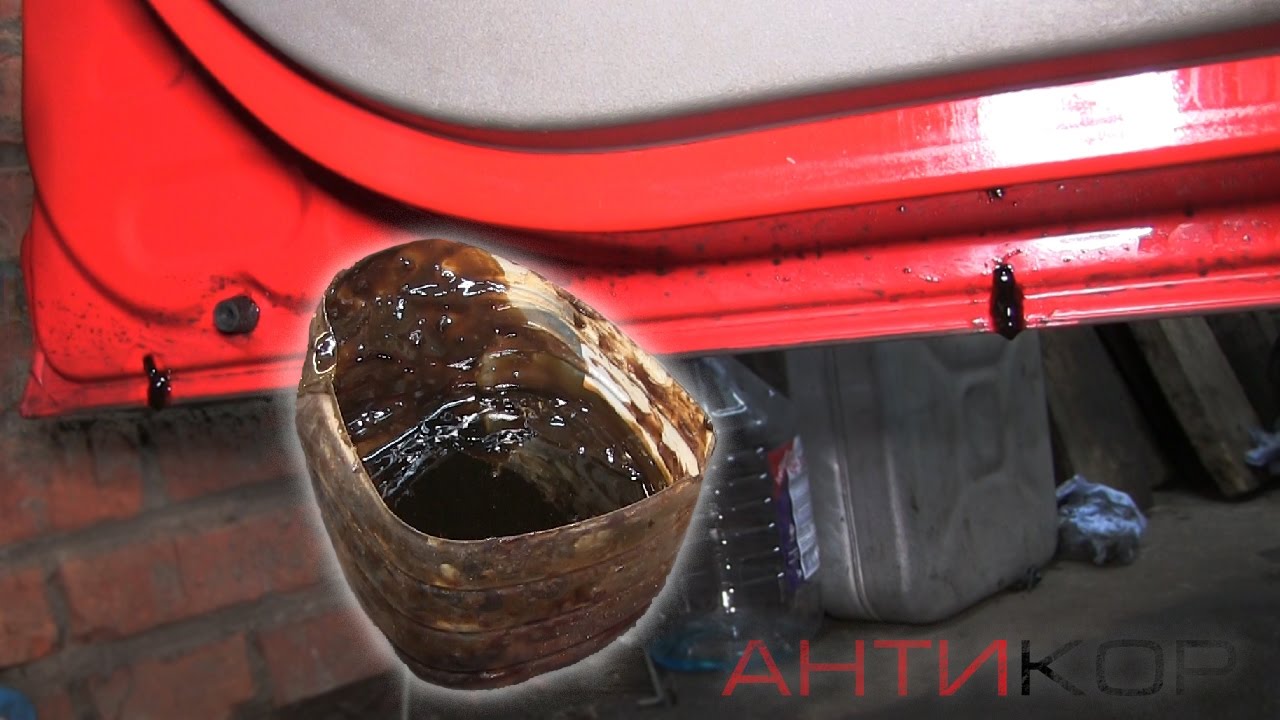
Так закончился первый, утомительный день, длиною в 7 часов…
День 2.
На второй день, я захватил свою маленькую сестру, так как сидеть с ней больше было некому, да и в качестве помощника она всегда может сгодиться — и ей нескучно, и мне веселее. В гараж вышли уже пораньше, чтобы начать работы по сколько-нибудь меньшей жаре.
По знакомому сценарию, выкатываем машинку на удобную позицию, снимаем накладку порога и убираем последнюю в сторону. Справа грязь скрывалась в существенно большем объёме, но, к счастью, очагов зловещей коррозии оказалось меньше — нелогично как-то, но приятно.
Также оклеиваем скотчем малярным, удаляем втулки и омываем небольшим, во избежание попадания во внутренние полости, количеством водички обрабатываемый участок, не забыв влить мовиль и в этот порог.
Обрабатываем дрелью с вышеупомянутой насадкой, периодически смачивая нейтрализатором ржавчины, до момента, пока все подозрительные участки не начнут сиять металлическим блеском.

Обезжириваем всё той же бензин-калошей и обильно обмазываем антикором.
www.drive2.ru
Как обработать пороги автомобиля от коррозии
Все начинается с появления небольших точек ржавчины, а заканчивается тем, что со временем кузовные элементы прогнивают до дыр в полном смысле слова. На некоторых возрастных автомобилях эта проблема ярко выражена и заметна издалека, причем может распространиться на соседние кузовные детали. Если дело дошло до сквозной коррозии, то пороги переваривают или меняют. Разумеется, до подобного лучше не доводить – с опасным явлением лучше бороться методом упреждения, а не решать появившиеся проблемы, грозящие вылиться в большой ремонт, по факту. В группе риска находятся многие отечественные автомобили, «китайцы», некоторые модели японских брендов – у них частенько гниют пороги, а вместе с ними и колесные арки.
Что потребуется для обработки порогов
Процесс можно доверить профессиональным мастерам, осведомленным о всех тонкостях, хотя не возбраняется обработать и замазать пороги от коррозии своими руками – ничего сложного в этом нет. Главное правильно подготовиться самому, серьезно и внимательно подойти к подготовке автомобиля и, конечно, нанести защитный состав, согласно инструкции и рекомендациям.
Для самостоятельной антикоррозийной обработки порогов машины от коррозии непосредственно исполнителю работ желательно иметь при себе рабочую одежду, закрывающую кожу, защитные очки, резиновые перчатки и респиратор. Последним не стоит пренебрегать, так как предстоит работать с химическими веществами. Понадобится металлическая щетка и наждачная бумага, промышленный фен, тряпка для очистки поверхности, обезжириватель «Уайт-Спирит», преобразователь ржавчины, чистая вода и антикоррозийный состав. Как раз последний весьма вреден и его попадание на кожу и слизистые оболочки, мягко говоря, нежелательно.
Чем обработать пороги автомобиля
Покрытие порогов антигравием является обычной практикой. За термином «антигравий» скрывается состав, который не только обеспечивает защиту от коррозии, но также существенно повышает устойчивость порогов к разного рода воздействиям (будь то песок, камни, снег и грязь, климатические особенности, а также неагрессивные вещества) и даже способно снизить уровень шума, проникающего в салон.
autorambler.ru
обработка и защита своими руками
В период эксплуатации автомобиль подвергается воздействию окружающей среды. Повышенная влажность, солевые реагенты, температурный режим и частицы асфальтового покрытия приводит к возникновению повреждений кузова:
- ржавчины;
- потертостей;
- царапин.
Из-за габаритов и расположения, пороги – наиболее уязвимая часть авто. Снаружи и внутри них металл теряет краску и защиту, в связи с чем вероятно появление гнили и дыр. Дальнейшее истощение покрытия приводит к полной замене определенной части днища автомобиля. Предотвращение появления ржавчины и коррозии – один из составляющих ухода за машиной. Частично сохраняют покрытие кузова брызговики и накладки. Полная защита порогов реализовывается обработкой антикоррозийными компонентами.
Первый раз нанесение специальных составов проводят на станциях технического обслуживания. При обработке порогов изнутри и снаружи собственноручно не только продлевается срок эксплуатации автомобиля, но и повышается кругозор и техническая подготовка водителя. Предварительно выполняется подготовка и закупка снаряжения.
Что нужно купить для самостоятельной обработки порогов
Процедуре нанесения антигравийных составов предшествует предварительная закупка:
- Рабочих материалов и компонентов. Нужен антикор или антигравий, преобразователь ржавчины, растворитель для обезжиривания обрабатываемой поверхности, вода, ткань для очистки.
- Средств защиты организма при работе с химическими веществами. Требуется спецодежда для предохранения открытых участков кожи, резиновые перчатки, респиратор или защитная маска, очки.
- Специальных инструментов и вспомогательной оснастки. Необходима щетка по металлу, малярная лента, нож, наждачная бумага, промышленный фен или нагревательный элемент, специальный пистолет при наличии средства в тубе.
- Услуг для качественного и безошибочного проведения работ. Может потребоваться заказ подъемника или аренда эстакады, мойка и сушка автомобиля.
Приобретение определенных товаров следует координировать с выбранным методом, материалами, условиями обработки.
Нюансы выбора покупных средств обработки
При выборе антикоррозийных средств защиты кузова строго проверяются характеристики товара: назначение, срок годности, взаимодействие со вспомогательными материалами, показания к нанесению. Средство поставляется в баллончиках или металлических банках в зависимости от состава и метода нанесения на полости автомобиля.
Химический состав как дорогого, так и более экономичного антикора агрессивен и опасен для организма человека. Поэтому обязательно использование резиновых перчаток и закрытой одежды.
Ассортимент ингибиторов коррозии весьма широк. Они отличаются методами нанесения, компонентами состава, стойкостью к окружающей среде, временем высыхания, ценовыми показателями. Альтернативными вариантами антигравию выступают:
- Отработанное техническое масло. Использовалось в устаревших моделях автомобилей. Отличается резким неприятным запахом и низкими показателями экологичности.
- Мовиль. Антикоррозийный ингибитор жидкой структуры.
Назван в честь двух городов (Москва и Вильнюс). Создан в середине прошлого века как основное средство преодоления ржавчины в узлах автомобиля. В состав входят масла, керосин, олифа и небольшой процент специфических добавок.
- Особые мастики на основе каучука. В состав внедрены отдельные виды смолы. Выделяются повышенной вязкостью, трудоемкостью процесса нанесения, повышенными температурными требованиями к использованию.
Антикоры в удобных баллончиках для распыления являются лучшим вариантом в плане эффективности и рентабельности. При их производстве аккумулируются передовые технологические наработки химической промышленности.
Основные средства по борьбе с коррозией металла производятся на основе нефти и продуктов ее переработки. В качестве усиления эффекта внедряются производные химической промышленности.
Рецепт антикора
Представленные товары сужают поле для деятельности опытных автолюбителей. Лучшее исправление дисбаланса – изготовление антикора своими руками. Комплексное действие составляющих частей, консистенция вещества и объем однозначно удовлетворят владельца автомобиля.
Ценность рецепта заключается в доступности и экономичности большинства ингредиентов. В основе состава – битумные или восковые соединения. Они обволакивают металл кузова, удерживают всю массу на поверхности. Основной вариант – пушечное сало. Это давно выведенное средство, безотказное, малозатратное, доступное в продаже.
Наличие вспомогательных компонентов зависит от потребностей мастера. В состав могут входить:
- Пластилин. Укрепляет структуру, добавляет пластичности и комфорта при обработке.
- Гидроизоляторы. Предохраняют от попадания воды и возникновения ржавчины при эксплуатации.
- Антикоррозийные ингибиторы. Химические замедлители разрушительного процесса гниения металлических частей.
Для повышения эффективности в состав внедряют частицы металлов для прочности (цинк, бронза), пластиковые или каучуковые соединения, клей или герметик для дополнительной защиты проблемных мест.
Поможет ли обычная краска
Состав и свойства обычных лакокрасочных изделий не позволяют использовать их как альтернативу антигравию. Отсутствие антикоррозийных ингибиторов исключает создание защитной пленки, позволяет распространять действие химически агрессивных реагентов и воды. Краска быстро выгорает, не препятствует распространению ржавчины, не устраняет существующие проблемные участки. Водоотталкивающие свойства находятся на низком уровне.
Инструменты и материалы
Обработка порогов изнутри своими руками подразумевает использование подручных вспомогательных средств. Основные инструменты и материалы, сфера их применения:
- Спецодежда. Обязательное условие для начала работы. Предусматривает полное отсутствие открытых участков кожи, наличие защитных очков, резиновых перчаток, респиратора. Предохраняет от пагубного действия химических компонентов рабочего компаунда.
- Металлическая щетка и наждачная бумага. Служат для очистки поверхности металла перед обработкой антикором.
- Ветошь или старая тряпка. Удаляет ненужные элементы с рабочего пространства.
- Средства подготовки кузова к основным процедурам, то есть обезжириватель, преобразователь ржавчины, чистая вода для создания необходимой консистенции.
- Основное средство для антикоррозийной обработки кузова.
- Промышленный фен для заключительного этапа просушки.
- Домкрат или подъемник. Дополнительная оснастка для улучшения условий работы со скрытыми участками днища транспортного средства.
Качество оборудования и материала влияет на износостойкость и долговечность обработанных участков, надежность всего автомобиля.
Подготовка авто к антикору
Прежде чем обработать пороги автомобиля снаружи от коррозии, производится приготовление к процедурам. Перечень предварительных манипуляций:
- Расположить транспортное средство на эстакаде или подъемнике для доступа к поверхности обработки.
- Демонтировать защитные составляющие и части обшивки, создающие помехи.
- Зачистить грязь, ржавчину, коррозийный налет ветошью и водой.
- Просушить обрабатываемые места строительным феном.
- Проклеить прилегающие части малярной лентой для защиты от химических и тепловых последствий нанесения антигравия.
Эффективность процедуры зависит и пропорциональна качеству предшествующей подготовки обшивки к основным манипуляциям.
Обработка порогов автомобиля внутри и снаружи
Процесс нанесения антикора специальным распылительным баллончиком или особым пистолетом трудоемкий, требует концентрации и подготовки. Основные правила покраски металлической поверхности:
- Слой защитного материала наносится равномерно по всей площади.
- Дистанция от места впрыскивания до кузова составляет 15-20 см.
- После каждого распыления возможно подсушивание промышленным феном.
- Количество слоев для оптимального результата не меньше трех.
- Время выдержки между фазами обработки не менее 5 минут.
- Вспомогательная лента убирается.
- Продолжительность подсыхания автомобиля после завершения процедуры до начала эксплуатации не менее 2 часов.
При использовании антикоррозийных смесей на основе мастики применять фен нельзя. Это приводит к противоположному эффекту. Перечень и удельная масса компонентов краски регулируются для достижения эффекта.
Рабочее место обязано быть приспособлено и оборудовано необходимым инвентарем, спецодежда приведена в подобающий вид, инструменты и приспособления – быть в исправном состоянии и удобном расположении.
Восстанавливать целостность окраски автомобиля на станции технического обслуживания надежнее, чем обрабатывать пороги автомобилей от коррозии своими руками в гараже. Но при необходимой сноровке и концентрации владелец авто решает поставленную задачу при минимальных денежных затратах, осваивает положительный опыт в эксплуатации автомобиля.
infokuzov.ru
Обработка порогов автомобиля своими руками
Добрый день, уважаемые читатели и гости блога. Сегодня в статье мы расскажем об обработке порогов автомобиля своими руками для защиты от ржавчины. Все автолюбители сталкивались с проблемой ржавых порогов. Она актуальна для любого автомобиля, эксплуатируемого на дорогах страны.
Антикоррозийная обработка порогов автомобиля способна решить проблему появления ржавчины. Если пустить процесс коррозии на самотёк, то через несколько лет придётся полностью менять пороги машины. Ржавчину проще предотвратить, чем в последующем бороться с её разрушительным действием.
В статье можно увидеть небольшое видео по обработке порогов автомобиля своими руками. Оно может использоваться при выполнении антикоррозийной обработки в режиме реального времени. Достаточно иметь под руками смартфон или планшет.
В конце статьи вас ожидает интересное и увлекательное видео. Покажет разрушительное действие ржавчины на автомобиль.
Антикоррозийная обработка порогов автомобиля своими руками
Пороги автомобиля нуждаются в защите, так как находятся в нижней части автомобиля и подвержены отрицательному воздействию внешних факторов (перепады температуры, солевые реагенты, отрицательная температура, повышенная влажность).
Часто мелкие камни, песок, щебень и гравий способны оставлять на внешней стороне порога небольшие повреждения. Зачастую становятся очагами будущего коррозийного процесса.
Выбор средств антикоррозийной обработки порогов машины широк и разнообразен. Можно найти дешёвые или дорогие средства. Все они получили обобщённое название «антигравий для порогов». Могут продаваться в баллончиках или металлических банках.
Если нет возможности задействовать подъёмник для обработки порогов, то лучше перенести работы на летний период. В летние месяцы можно заехать на эстакаду и работать на открытом воздухе. Зимой или осенью выполнять работы по обработке порогов нельзя.
Процесс обработки порогов автомобиля можно разделить на несколько этапов:
1.Подготовка материалов и спецодежды.
- рабочая одежда, закрывающая все участки кожи;
- резиновые перчатки;
- защитные очки;
- респиратор;
- щётка по металлу;
- наждачная бумага;
- чистая вода;
- средство для антикоррозийной обработки порогов;
- Уайт-Спирит для обезжиривания
- преобразователь ржавчины;
- ветошь;
- строительный фен.
2.Подготовка автомобиля.
- демонтировать защиту;
- тщательная мойка машины с упором на пороги;
- сушка автомобиля;
- заезд на подъёмник или эстакаду;
- удаление всех очагов ржавчины на порогах при помощи наждачной бумаги или специального диска;
- обработка порогов преобразователем ржавчины;
- обезжиривание порогов;
- сушка порогов;
- использование малярной ленты для защиты прилегающих к порогам мест;
3.Нанесение антигравия на пороги.
- баллончик с антигравием следует интенсивно встряхивать неменее 2-3 секунд перед использованием;
- держать баллончик нужно на расстоянии 15-20 сантиметров от поверхности порога;
- следить за равномерностью нанесения средства защиты;
- между слоями надо выдерживать время порядка 5-7 минут;
- оптимальное количество слоёв антигравия не менее 3;
- для ускорений сушки антикоррозийного средства можно воспользоваться строительным феном;
- удаление малярной ленты;
- установка на место защиты;
- использовать автомобиль не раньше чем через 2 часа после обработки.
Ничего сложного в обработке порогов от ржавчины нет. Нужно подготовиться и соблюдать последовательность действий. Не стоит спешить, так как страдает качество работы.
Антикоррозийная обработка порогов автомобиля с использованием мастики
Этот способ обработки порогов машины своими руками пользуется меньшей популярностью. Объясняется всё трудоёмкостью процесса и большим количеством затраченного времени.
Для защиты порогов можно приобрести «Антикор битумный». Представляет собой мастику холодного нанесения. Производится на основе смешивания каучука и смол. Обладает доступной стоимостью и можно с лёгкостью найти в продаже.
Подготовительный этап автомобиля аналогичен, как и в случае использования антигравия. Днище машины надо тщательно вымыть, высушить и очистить от очагов ржавчины. После этого можно приступать к нанесению антикоррозийной мастики.
Перед использованием «Антикора битумного» его лучше немножко подогреть. Это увеличит его текучесть и уровень адгезии. Наносится мастика обыкновенной малярной кистью. Не нужно жалеть мастики. Толщина слоя напрямую влияет на эффективность и долговечность защиты порогов от коррозии.
После нанесения мастики нужно дождаться естественного высыхания антикоррозийного материала. Использование фена для сушки даст обратный эффект. В среднем достаточно 2 часов. По окончании этого времени можно ставить на место защиту и пользоваться автомобилем.
Виды антигравия для порогов автомобиля
Количество средств антикоррозийной обработки порогов автомобиля велико. По большому счёту они мало чем отличаются друг от друга.
Средства защиты порогов машины от ржавчины можно разделить на несколько групп:
1.Период использования.
- постоянная защита;
- временная защита;
2.Упаковка.
- аэрозольный баллончик готовый для применения;
- аэрозольный баллончик под специальный пистолет;
- металлические банки;
- пластиковые ёмкости.
- прозрачный;
- белый;
- чёрный;
- cерый;
- цветной.
- с содержанием преобразователя ржавчины;
- антикоррозийными веществами;
- повышенная адгезия;
- усиленная прочность.
Выбираем средство для обработки порогов автомобиля своими руками
Несмотря на обилие всевозможных средств защиты порогов от коррозии многие автолюбители задаются вопросом: чем обработать пороги? Мы дадим на этот вопрос полный и исчерпывающий ответ. Он поможет автолюбителю сделать правильный выбор.
1.Антикор-спрей BODY-950, ёмкость 400 мл
Антигравий, созданный на основе специальных смол. Обладает высокой адгезией и устойчив к повреждениям. Для нанесения требуется использование специального пистолета. Быстро сохнет. Стоимость 4-6$.
2. Антигравий аэрозоль ЭЛТРАНС, ёмкость от 400 до 1000мл.
Недорогое, но эффективное средство. Не требует использования специального пистолета. Расход одного слоя 400 грамм на 1м². Рекомендуется наносить в 2-3 слоя. Стоимость за 400 мл. 2-3$.
3. Антигравий KERRY, ёмкость 650мл.
Качественный антигравий, обеспечивающий эффективную защиту порогов. Обладает высокой степенью адгезии. Не требует специальных навыков в использовании. Стоимость 3-4$.
Это интересно
www.avtogide.ru
виды, характеристика, установка, плюсы и минусы
Одним из наиболее уязвимых мест в автомобиле являются пороги. Они чаще всего подвергаются воздействию неблагоприятных факторов. И чаще всего ржавчина на кузове автомобиля начинается именно с порогов, быстро расходясь по всему кузову. Как можно этого избежать и какая защита порога существует на данное время, мы расскажем в этой статье.
Что такое автомобильный порог?
Если говорить простым языком, то порог в автомобиле – это полоска, которая проходит под дверью автомобиля между передним и задним крылом. Грубо говоря, чтобы увидеть порог, нужно открыть дверь авто и посмотреть вниз – именно это и является порогом. И именно об их защите мы будем говорить.
Способы защиты порога
- При помощи аэрозольного покрытия.
- При помощи накладок.
- При помощи защитных пленок.
- При помощи мастик и лаков.
- При помощи жидких локеров.
Теперь рассмотрим каждый способ более подробно.
Аэрозольное покрытие
Такой способ защиты порогов своими руками наиболее экономичный, но и не особо долговечный. Насколько аккуратно бы вы ни наносили средство, вам вряд ли удастся добиться идеальной глянцевой поверхности, а это означает, что в малейшие неровности будет постоянно набиваться грязь, которая со временем приведет к тому, что покрытие отслоится.
- BODY-950. Антикоррозийный спрей, который создан на основе смол. Такой спрей довольно устойчивый к внешним повреждениям и быстро высыхает, но наносить его необходимо при помощи специального пистолета.
- «Элтранс». Низкая стоимость этого антигравийного аэрозоля и нанесение сразу из баллона делает его довольно популярным среди автовладельцев. Средство довольно эффективное с экономичным расходом. На один квадратный метр уходит около 400 граммов средства, при условии покраски в один слой. Для большей эффективности рекомендовано наносить два – три слоя.
- Kerry. Довольно качественная защита порогов автомобиля, которая не требует никаких особенных навыков использования. Имеет высокую схватываемость с поверхностью.
Конечно, таких аэрозолей достаточно много, все они имеют как плюсы, так и минусы. Мы привели наиболее известные и заслуживающие внимание. Такая защита порогов может проводиться и как вспомогательная в дополнение к основным способам.
Перед началом обработки пороги следует тщательно вымыть и высушить. Если там имеются следы ржавчины, их необходимо счистить металлической щеткой или наждачкой. И только после этого наносить аэрозоль. Если вы используете антикоррозийную и антигравийную защиту, то средство от ржавчины необходимо наносить первым.
Накладки
Накладки как защита порогов автомобиля имеют не только защитные, но и декоративные свойства. Они эффективно защищают автомобиль от вредных воздействий и являются красивым и эффектным способом тюнинга.
Обычно они изготавливаются из металла, часто из хромированного, но бывает и пластиковая защита порогов. Последний вариант наиболее дешевый, но и самый недолговечный. Кроме того, под пластиковым обвесом металл может ржаветь гораздо сильнее, чем без него вовсе. Это связано с тем, что если нет доступа воздуха, он как бы «потеет», соответственно, повышается риск коррозии.
Металлические накладки же, наоборот, довольно прочные и надежные.
Если говорить в общем, то накладка для защиты порога – это такой «входной коврик», на котором оседает вся уличная грязь, химия с наших дорог и прочий мусор.
Еще один плюс использования накладки в качестве защиты порога — это то, что установить и заменить ее очень легко. Для этого не нужно привлекать специалистов. Согласитесь, лучше периодически менять такие накладки, чем впоследствии платить за полноценный ремонт порогов.
Как видите, плюсов у такой защиты немало, но есть и минусы. Во-первых, это постоянные дополнительные траты. А во-вторых, такие накладки подходят не для всех моделей автомобилей. Порой автолюбители жалуются, что после установки стало неудобно садиться в авто – особенно это касается автомобилей с низкой посадкой. Ну, а третий минус заключается в том, что если проводить монтаж накладок неаккуратно, можно деформировать кузов и повредить пороги, поэтому все действия необходимо выполнять аккуратно и не торопясь.
Еще один из вариантов для защиты порогов – труба, которая действует по принципу накладки-порога, но не требует сверления кузова.
Защитная пленка
Такая пленка применяется не только как защита бампера и порогов, но и для всего кузова, а точнее для тех его частей, которые больше всего подвергаются вредным воздействиям.
Защитная пленка бывает разной, в зависимости от своего предназначения. Для защиты порогов используют обычно антигравийную.
Плюсы такой защиты в том, что монтаж и демонтаж не вызывают никаких повреждений автомобиля. Кроме того, она довольно долговечная и надежно защищает автомобиль от повреждений. Оклеить такой защитой пороги вполне под силу самому автовладельцу. Необходимо лишь терпение и свободное время. Но если вы хотите действительно качественно покрыть весь кузов автомобиля, то лучше обратиться к специалистам.
Минусом такой защиты является то, что:
- Оклейка не нового автомобиля сильнее проявит все сколы и царапины на кузове.
- При некачественной работе высока вероятность того, что пленка быстро слезет.
- Если не мыть автомобиль, то от грязи пленка быстро желтеет.
Пленка бывает виниловой и полиуретановой. Первая недолговечная и защищает автомобиль только за счет своей толщины. Довольно грубая и непластичная, при низких температурах или при сильном ударе может сломаться. Полиуретановая же, наоборот, довольно дорогая, но качественная. Защищает не только от мелких царапин, но и от песка, камней и т. д., очень эластичная и упругая, напоминает резину. Переносит эксплуатацию при низких температурах. По цене полиуретан примерно в пять раз дороже винила.
Лаки и мастики
Защита порогов этим способом под силу самому автовладельцу. Привлечение специалистов СТО обычно не требуется. Порядок работы:
- Тщательно вымыть и высушить пороги автомобиля.
- Снять внешние пороги, чтобы был доступ ко всем частям, которые потребуют обработки. Очистить пороги изнутри.
- Удалить старое антикоррозийное покрытие, слезшую краску. Если есть следы ржавчины, то их нужно счищать до тех пор, пока не появится неповрежденный металл.
- Обезжирить пороги при помощи ацетона или бензина и нанести средство для очистки от ржавчины.
- Малярным скотчем заклеить места, которые не будут подвергаться обработке.
- Нанести протравливающий грунт.
- Обработать защитными средствами пороги.
- Оставить на два – четыре часа до полного высыхания.
Для таких работ чаще всего используются:
- Аэрозольная, битумная, полимерно-битумная мастика.
- Мовиль.
- Битумный лак.
- Материал на масляной основе, обладающий антикоррозийным свойством.
- Антигравийное средство на каучуковой основе.
Жидкий локер
Жидкий локер – это плотная вязкая паста, которая после нанесения на пороги застывает и по свойствам напоминает резину или упругую пластмассу.
Плюсы такого способа защиты:
- Стойкость к механическому воздействию.
- Ее довольно легко наносить, даже на труднодоступные места.
- Локер пластичный и однородный.
- Устойчивость к влаге предохраняет автомобиль от скапливания конденсата.
- Экологически безопасен.
- Хорошо схватывается и имеет высокий порог сцепления с покрытием автомобиля, не образует потеков.
- Хорошо переносит высокие и низкие температуры.
- Обладает шумоизоляционными свойствами.
Такой способ защиты порогов проходит в три этапа:
- При помощи кисточки или шпателя нанести первый слой антикора и просушить.
- Вторым слоем нанести битумную мастику и просушить.
- Третьим финишным слоем распылить антикоррозийную резину.
Каждый слой должен быть толщиной 1,5-2,5 сантиметра. Такое покрытие полностью схватывается примерно через двое суток после нанесения, поэтому на это время лучше воздержаться от использования автомобиля.
Заключение
Как видите, способов защиты порогов достаточно много, и все они имеют свои плюсы и минусы. Какой выбрать – решать вам. Но если вы не уверены в своих силах, то лучше обратитесь на СТО – пусть специалисты сделают работу вам качественно, чтобы не пришлось тратить средства на исправление ваших ошибок.
fb.ru
Защитная антигравийная пленка на пороги автомобиля
Любое транспортное средство в процессе эксплуатации изнашивается. Это вполне логично. Езда по некачественным дорогам, мелкие камни, ветви деревьев и другие внешние факторы становятся причиной повреждений на кузове автомобиля: сколов, царапин, отслаивания лакокрасочного покрытия.
Пороги авто также можно считать зоной повышенного риска. Они находятся в постоянном контакте с обувью, вследствие чего стираются и царапаются. Особенно плохо пороги переносят контакты с женской обувью на шпильках — от неё остаются очень заметные следы. Такие повреждения не только портят внешний вид автомобиля, но и со временем могут стать очагами возникновения коррозийных процессов.
Защитная пленка на пороги автомобиляСовременные технологии успешно решили этот вопрос. Автолюбителям для защиты своего авто предлагаются различные защитные плёнки. Ими можно оклеить проблемные зоны и чувствовать себя гораздо спокойнее.
Бронирование автомобиля пленкой сегодня очень распространено среди тех, кто хочет как можно дольше сохранить целостность лакокрасочного покрытия своего автомобиля.
Что такое бронеплёнка для авто
Бронеплёнка — это прозрачная антигравийная защитная плёнка, с помощью которой можно защитить те зоны автомобиля, которые подвергаются наибольшей опасности повреждения. Не нужно путать её с виниловой плёнкой для оклейки авто — это совершенно другой тип.
Оклейка автомобиля защитной пленкойБронеплёнка отличается от других типов покрытия тем, как она функционирует. При ударе энергия распределяется не в одном месте, а происходит её рассеивание по большой площади. Может появиться вмятина, но нарушения слоя лакокрасочного покрытия не произойдёт. Место деформации современные технологии дают возможность выправить без проблем, а новой покраски повреждённого участка не потребуется.
Антигравийная плёнка изготавливается, как правило, из прочного полиуретана. Она служит не только для защиты порогов, но и:
- фар;
- капота;
- бампера;
- радиаторной решётки;
- лобового стекла;
- зоны ручек дверей.
Защитная антигравийная плёнка помогает уберечь уязвимые зоны авто от следующих негативных факторов:
- Посторонних механических воздействий.
- Ультрафиолетового и инфракрасного излучения.
- Воздействия агрессивной среды.
- Образования коррозионных участков.
Бронеплёнка бывает разной толщины. От последней зависят два таких противоположных фактора, как степень защиты и эластичность. Чем толще материал, тем выше его защитная способность, однако тем сложнее его наклеить на участки со сложной геометрией.
Оклейка антигравийной пленкойЕсли говорить о преимуществах, то антигравийная плёнка имеет следующие сильные стороны:
- Помогает защитить пороги и другие проблемные участки авто от повреждений.
- Со временем сохраняет прозрачность, не мутнеет и не желтеет.
- Хорошо поддаётся мойке и покрытию автомобильным воском.
- Без проблем снимается при необходимости.
- Её можно обрабатывать обыкновенной механической полировкой.
- Практически незаметна на кузове автомобиля и на вид ничем не отличается от тех участков, где её нет.
Бронирование порогов автомобиля защитной плёнкой
Приняв решение обработать пороги вашего авто защитным покрытием, вы можете либо обратиться на станцию технического обслуживания, либо сделать это своими силами. Процесс оклейки порогов автомобиля несложен, и нет никаких сомнений, что вы с ним успешно справитесь.
Для начала вам необходимо знать, что нельзя клеить покрытие на свежеокрашенную поверхность. Для нанесения необходимы высокие температуры, которые могут размягчить новое лакокрасочное покрытие и сделать сцепление с бронеплёнкой оптимально сильным. При её удалении на клейком слое могут остаться элементы краски.
А теперь давайте пошагово рассмотрим, как выглядит сам процесс оклейки порогов автомобиля:
- Для начала снимаем пластиковые накладки, поскольку защиту мы будем ставить под них.
- Поверхность, которую планируем оклеивать, тщательно вымываем, вытираем насухо и обезжириваем.
- Обрызгиваем поверхность порогов авто мыльным средством из пульверизатора. Осуществляем примерку и выкройку на каком-нибудь недорогом материале. Смоченная поверхность даст возможность осуществить это без особых проблем — можем двигать материал столько, сколько нам это необходимо.
Обрызгиваем поверхность порогов авто
- Полученные выкройки прикладываем к плёнке и вырезаем по ним участки, которые будет клеить.
- Вырезанные участки прикладываем к защищаемой поверхности авто и приклеиваем. Можно разогреть материал при помощи фена, особенно в тех участках, где он плохо прилегает.
- Тщательно разглаживаем и избавляемся от жидкости и пузырьков воздуха внутри.
Разглаживаем наклеенную пленку
- Излишки, если таковые имеются, подрезаем ножницами.
- Ставим на место пластиковые накладки на пороги авто.
Пороги с наклеенной пленкой
На этом работу можно считать завершённой. Года на два или три вы обеспечили отличную защиту кузова своего автомобиля в тех местах, где он наиболее подвержен повреждениям вследствие контакта с обувью.
Заключение
Бронирование порогов автомобиля антигравийной защитной плёнкой отлично предохраняет их от повреждений, возникающих от истирания обувью и царапин от женских «шпилек». Это довольно несложная процедура, с которой может справиться практически любой владелец авто. Для этого не нужны специальные знания и навыки. Немного терпения и смекалки — и ваша машина будет надёжно защищена от сколов и царапин, причиняемых подошвами и каблуками.
[democracy]
[democracy]
Автор: Лагода Владислав Федорович
Образование высшее: среднее специальное. Специальность: Автомеханик. Хорошее знание устройства легковых автомобилей иностранного производства. Навыки работы: по замене ремня ГРМ ГБЦ ходовая часть сход-развал ТО. Ремонт…
okuzove.ru
Защита порогов и другого пластика от царапин. — Mazda 6, 2.5 л., 2008 года на DRIVE2
Ну а пока моя красотка в таком вот состоянии… мы немного поработаем с пластиковыми деталями 🙂
Шумоизоляция Mazda 6
Прежний хозяин берег все что под ногами от царапин, оклеил пленкой пороги и прочие мелочи.
Я сдер старую пленку так как она имела уже потрепанный вид, но зато детали под ней как новые!
Демонтирую старую пленку
Пороги хорошо сохранились потому что были в пленке
Почему бы не заклеить их в пленку что бы следующий хозяин машки мне тоже потом спасибо сказал.
Сказано-сделано! )
И снова лента-нож выручает!
Черная структурная матовая пленка на передней консоли
Режем пленку без ножа
Удаляем остатки пленки
Вуаля! )
мелочевку тоже затянул в пленку
Деталь что под ручкой открытия лючка бака
Цена вопроса: $10 Пробег: 85 000 км
www.drive2.ru
Skoda Rapid Стремительный серый › Бортжурнал › #14 Бронирование порогов — самостоятельный опыт! Часть1
В общем негативный опыт бронирования у меня уже есть! На выходные планировал поехать к другому мастеру переклеить на заднем бампере и заклеить пороги, но поскольку выходные выдались дождливые и ни на море, ни на дачу не поедешь, принял решение клеить самостоятельно!
Никогда прежде этим не занимался, пару раз видел из-за спины мастера! Решил подкрепить свои знания на Ютубе — там достаточно много разнообразных роликов, так что посмотрел я с десяток, после чего уже имел более полное представление о том что и как надо!
Первый вопрос, который возник — как клеить — на «сухую» или «мокрую»? Поиск по спецификации пленки(Орагуард 290) результатов не дал, а так как на сухую мне уже клеили, я решил пробовать на мокрую.
Следующий момент — это инструменты и приспособы, которые нужны для работы. За бегая на перед, перечислю то, чем пользовался я:
-Ракель(он же резиновый шнпатель, он же «выгонка»)
-Рулетка
-Металлическая линейка
-Канцелярский или строительный нож(кому чем удобрнее, главное чтобы лезвие плотно сидело, не перекашивалось)
-Опрыскиватель с мыльной водой(я взял от мистер Мускул)
-Промышленный фен(но можно и бытовой)
-Маркер, карандаш и бумага
-Сухая ветошь, салфетки
Профессионалы используют специальные ракили, химию, ножи и пр, чего для разовых работ не накупишься, но в принципе работать можно и непрофессиональным инструментом — не так удобно, поэтому долбаться дольше.
Предварительно составив список чего нужно приобрести, отправился за покупками, по случаю прикупив ништячков для повседневной жизни!
Процесс работы в двух словах:
-Снял мерки, на бумаге зарисовал форму с размерами
-Нарисовал форму на тыльной стороне пленки и вырезал
-Помыл и обезжирил порог
-Далее процесс поклейки — обрызгал порог, снял с подложки пленку и обрызгал ее, прилепил-спозиционировал, далее выгоняешь долго и нудно воду… Когда основные пузыри ушли, взял фен и прошелся еще раз… Ну и все — правда у меня каждый порог по часу времени занял, плюс пока скупился, туда-сюда помотался и вчера успел поклеить только передние пороги. В течении недели поклею задние и багажник, тогда и выложу.
В гараже должно быть хорошее освещение, иначе делать нечего! Фоток мало, тк делал сам — в одной руке ракиль, в другой фонарь — фотать не хватало рук.
Предварительная прикидка формы
Рабочее место для порезки пленки
Тщательно вымываем порог
Финальный вариант — приблизительно очертил форму
Небольшие косяки на пассажирском пороге
Так поклеили профессионалы!((((
Долой позорняк, под пленкой вода и грязь…((((
www.drive2.ru
Русская Артель › Блог › Как самостоятельно установить защитные накладки на внутренние пороги дверей? Инструкция.
Всех приветствуем в нашем блоге.
Сегодня мы хотим вам рассказать, как самостоятельно осуществить установку наших накладок на пороги дверей.
Полный размер
Защитные накладки на внутренние пороги дверей
И так, для начала монтажа вам понадобится
• спиртовая салфетка
• канцелярский нож
• перчатки
• влажная салфетка
Важным условием установки изделия является температура поверхности автомобиля, рабочего помещение и двустороннего скотча на изделии. Она должна быть не ниже 21 градуса тепла!
Так же мы рекомендуем производить работы по монтажу в перчатках. Для очистки и обезжиривания поверхности рекомендуем использовать спиртовые салфетки, либо смесь технического спирта с водой в пропорции 1:1.
Теперь перейдем к главным шагам по установке изделия.
1 шаг. Перед установкой накладок на пороги, для получения максимально прочного соединения, удалите загрязнения с поверхности автомобиля: вымойте и высушите автомобиль.
2. шаг. Затем используя канцелярский нож, аккуратно распакуйте пакет с комплектом накладок и извлеките их.
3 шаг. Далее вам необходимо обезжирить поверхность порогов автомобиля и нанести праймер в местах контакта с изделием. Для обезжиривания, как и писали ранее, советуем использовать спиртовые салфетки, либо смесь технического спирта с водой в пропорции 1:1
4 шаг. Следующий шаг – это примерка накладок на автомобиле. Приложите накладки на пороги авто, принимая за ориентир центр дверного проема вашего автомобиля.
5 шаг. После всех подготовительных работ и примерок можно приступить непосредственно к установке изделий. Для этого необходимо отделить часть защитной пленки с двустороннего скотча так, чтобы она выступала за контур накладки на 30-40 мм. Не отрывая накладку от поверхности порога автомобиля, аккуратно вытяните защитную пленку двустороннего скотча прижимая изделие к порогу.
Настоятельно рекомендуем не открывать сразу всю защитную пленку с двустороннего скотча! Так как при ошибке расположения накладки её будет проблематично отодрать с поверхности и последующая наклейка изделия будет не возможна.
6 шаг. Сильно прижмите накладку по всему периметру к порогам автомобиля. Прочность соединения зависит от степени контакта клейкой ленты с поверхностью. Не мойте авто в течении ближайшего часа.
Рекомендуем выдержать автомобиль в теплом боксе в течении суток по факту установки и не мыть автомобиль в течение суток. Это необходимо для окончательного отверждения клеевого состава двустороннего скотча.
Для примера посмотрите видео инструкцию установки накладок на пороги автомобиля Nissan Juke.
www.drive2.ru
Защита порогов автомобиля от соли
Зима суровое испытание не только для водителей автомобилей, но и работников дорожных служб. Снег, мороз и гололёд создают аварийную ситуацию на дороге. В статье читатели узнают о том, как выполняется защита порогов от соли? Что надо сделать для обработки порогов от соли?
Большую опасность для водителей представляет гололёд. Дорожное полотно при понижении температуры покрывается тонкой плёнкой льда незаметной глазу человека.
Снижается сцепления автомобильных шин с асфальтом. Неосторожные манёвры водителя на покрытой гололёдом дороге часто заканчиваются кюветом или дорожно-транспортным происшествием.
В конце статьи можно увидеть интересное видео о том, как выполняется защита порогов от соли. Оно станет отличным дополнением к тексту и поможет понять тонкости процесса.
Что используют для борьбы с гололёдом?
Для борьбы с гололёдом дорожные службы используют смесь песка с солью. Выбор неслучаен, ведь это дешёвый антигололёдный реагент с неплохим эффектом.
Кроме разрушения корки льда на дороге смесь портит поверхность днища автомобиля и в частности, пороги. Соль ускоряет развитие коррозийных процессов на кузове.
Смесь песка и соли содержит мелкие камешки. При движении автомобиля вылетающие из-под колёс камешки оставляют на поверхности кузова и днища небольшие повреждения. На них попадает соль. Если машина «ночует» в тёплом гараже процесс коррозии быстро развивается.
В начале лета наблюдаются первые последствия солевой «атаки» в виде появления очагов ржавчины. Это портит внешний вид и разрушает металл. Прежде всего страдают пороги.
Как правильно защитить пороги от соли?
1.Перед наступлением зимы проверить днище машины на предмет повреждений и очагов коррозии;
2.Выявленные очаги коррозии и повреждения нужно устранить;
3.Обязательно обрабатывают днище машины мастикой;
4.После поездки перед постановкой машины в гараж нужно смыть снег с элементов кузова;
5.Любые повреждения днища зимой безотлагательно ремонтируются.
Эти незамысловатые советы помогут уберечь кузов машины от ржавых «лап» коррозии.
Это интересно
www.avtogide.ru
Каталог защиты порогов по маркам автомобилей
Выбор по автомобилю
Выберите марку…AcuraAlfa RomeoAudiBMWBrillianceBYDCadillacChanganCheryChevroletChryslerCitroenDaewooDAFDaihatsuDatsunDodgeFAWFiatFordGAZGeelyGreat WallHaimaHavalHinoHondaHummerHyundaiInfinitiIsuzuIvecoJACJeepKiaLadaLand RoverLexusLifanLincolnLuxgenManMazdaMercedesMiniMitsubishiNissanOpelPeugeotPontiacPorscheRavonRenaultRoverSaabScaniaScionSeatSkodaSmartSsangyongSubaruSuzukiTagAZToyotaVolkswagenVolvoVortexZAZZotyeУАЗ
Выберите модель…
Выберите год…
Перейтиwww.caroptics.ru
чем и как делать своими руками
Обеспечить защиту порогов авто от воздействия коррозии позволяет периодическая обработка их качественным антикором, которую несложно провести своими руками.
Почему именно пороги
Покрытие кузовных наружных элементов антигравием и прочими средствами с антикоррозийным эффектом давно доказало свою высокую эффективность. Но перед тем как сделать обработку своими руками, нужно уточнить некоторые моменты.
Пороги выступают важной частью кузова. Они нуждаются в повышенной защите, поскольку располагаются в нижней части кузова автомобиля. Из-за этого на них активно воздействуют различные факторы в виде температурных перепадов, реагентов на зимних дорогах, низкие температуры, усиленная жара, высокая влажность и пр. С дороги летят мелкие камни, песок, кусочки щебня и гравия. Они наносят микроповреждения, разрушают лакокрасочный слой, минимизируют работу заводской антикоррозийной обработки.
Все это приводит к тому, что именно на порогах чаще всего возникают первые очаги коррозии, постепенно превращающиеся в крупные рыжие пятна ржавчины.
Думаю, не стоит лишний раз напоминать, чем опасна ржавчина, и к каким последствиям она способна привести.
Важно понимать, что бороться с коррозией нужно не после ее фактического появления. Своевременная профилактика и качественная консервация металла защитит от ржавчины и не даст ей проявиться на кузове вашего авто.
Существует огромный перечень средств, предназначенных для антикоррозийной обработки. Выбор огромен, потому каждый найдет себе вариант по кошельку и потребностям. На некоторые средства цена очень высокая, другие относятся к бюджетной категории. Но все они называются антигравиями для порогов. Чаще всего выпускаются в специальных баллончиках и металлических емкостях. Причем предпочтение стоит отдать именно баллончикам. Мастики требуют более сложной и длительной процедуры нанесения.
Но вне зависимости от формы выпуска выбранного средства, наносить антигравий нужно правильно, соблюдая определенную последовательность. Вы уже сами для себя решите, чем задуть, замазать или чем залить пороги в своем авто.
Как защитить пороги от ржавчины?
Внешняя обработка.
Как было написано во вступлении – внешняя обработка не так важна как внутренняя, но тем не менее именно внешняя часть порога определяет внешний вид автомобиля. И в целях его улучшения, многие автомобилисты устанавливают пластиковые обвесы. Внешний вид мол лучше и сколы не видны. Коллеги – это огромная ошибка. Нестандартный обвес вредит порогу больше чем отсутствие краски!
Смотрите, что бывает под пластиковыми накладками порогов:
Дело в том, что под накладки неизбежно набивается пыль, естественно, в нашем климате, пыль собирает воду и не просыхает большую часть времени, а при каждом изменении температуры, или проезде неровностей, набившаяся под накладку пыль сдирает краску! Итог – порог гниет не только изнутри, но и снаружи.
Договорились – нестандартные накладки порогов убираем….
Сами пороги, со временем, из-за абразивного действия дорожной грязи лишаются краски. Про то, как покрасить пороги у нас на сайте уже есть отдельная статья, не будем повторятся.
Чтобы снизить абразивное действие дорожной грязи – обязательно установите брызговики на передние колеса. С брызговиками краска на порогах и арках проживет на несколько лет больше, и самое главное, снизится количество воды попадающей внутрь порога.
У автора статьи был случай – на переварку порога приехала волга 3102 эксплуатировавшаяся всю жизнь в Волгограде, но одну зиму прожившая в Петербурге и по стечению обстоятельств, волга была без одного переднего брызговика, так вот – порог и короб на стороне без брызговика СГНИЛИ, в то время как, порог с другой стороны не потребовал даже переварки накладки, хотя и имел повреждение от удара и сколы краски.
Договорились – обязательно ставим брызговики на передние колеса.
Резюмируем, по наружной части:
- убираем нестандартные накладки
- обязательно восстанавливаем заводское лакокрасочное покрытие
- обязательно устанавливаем брызговики
Внутренняя обработка.
В сети полно рекомендаций по материалам для обработки скрытых полостей, от пушсала, отработки и мовиля до современных ингибиторов коррозии, мы тоже дадим свои рекомендации, но прежде чем обрабатывать порог его обязательно надо промыть! Делается это очень просто – убираются заглушки с двух сторон и порог промывается большим количеством воды. Вот вам видео на примере 124 мерседеса:
А вот столько песка мы вытрясли, когда переваривали пороги на мазде 3 2007 г.в.:
Договорились – прежде чем обрабатывать от ржавчины скрытее полости, обязательно промываем порог и несколько дней сушим.
Чем обработать скрытые полости порогов от ржавчины?
Отработка – самый дешевый вариант.
Традиция проливать пороги отработкой, зародилась еще во времена СССР, да действительно 2-3 литра отработки в порог при каждой смене масла продлевают его жизнь на 5-10 лет!
В сети пишут, что отработку лить нельзя, она ускорит коррозию и т.п. – бред! Отработка помогает, автора статьи была волга 1993 г.в. которая имела в 2017 году заводские пороги т.к. её проливали отработкой, при каждой смене масла. Вдумайтесь – самая гниющая волга (31029), имела родные пороги через 25 лет после производства, только благодаря отработке!
Отработка отлично пропитывает ржавчину и перекрывает доступ воздуха к металлу, соответственно скорость гниения замедляется в разы.
Миф о том, что отработка ускоряет коррозию, и если и лить масло в пороги, то только свежее, запустили маркетологи (надо же продавать антикоррозийные составы)…
Отработка не лишена недостатков:
- Она вредна для здоровья т.к. неизвестно из чего она сделана, и какие присадки в ней использовались, а так же что она вымыла из двигателя!
- Отработка, иногда, имеет довольно скверный запах, которой долго выветривается.
- Проливать полости отработкой надо минимум раз в сезон.
Кому интересно – сырая нефть отлично заменяет отработку, куда меньше вредит здоровью, куда хуже смывается водой, но достать её довольно трудно.
Мовиль и пушсало – дешевый вариант.
И то и другое было разработано очень давно. Пушсало используется больше 200 лет для консервации орудий и снарядов, а мовиль (Москва – Вильнюс) был разработан как антикоррозийное средство в начале 70х годов.
И то и другое нефтяные производные: пушсало – загущенное нефтяное масло, мовиль – смесь литола, моторного масла, олифы, керосина и ингибиторов коррозии. Оба антикора имеют одинаковый принцип действия – ограничить доступ кислорода к обработанной поверхности.
Если мовиль – относительно жидкий, и как отработка, смачивает ржавчину (хотя и хуже). То пушечное сало, при нормальной температуре, можно резать ножом и наносят его только горячим, что в антикоррозийной обработке не всегда возможно, соответственно использовать его для защиты порогов – бред, а вот замазать для консервации днище, поверх мастики, на время длительной стоянки – вполне вариант.
Мовиль же – дорогая альтернатива отработке. Так как точно так же скверно пахнет и точно также плохо сказывается на здоровье нюхающих.
Мовиль точно так же нужно периодически обновлять т.к. со временем он высыхает и трескается.
Современные антикоррозийные средства….
Естественно, с течением времени, производители совершенствовали антикоррозийные средства, и кроме «колхозных методов» приведенных выше, есть вполне современные составы:
Большинство из них аналоги мовиля, но отличаются скоростью высыхания и ингибиторами коррозии. Самое главное преимущество – их можно наносить реже, да они дороже стоят при покупке, но и обновления они требуют реже. Согласитесь – большинство людей ездит на машине 2-3 года и гораздо выгоднее 1 раз провести антикоррозийную обработку качественными материалами, чем каждый год обновлять за деньги «мовиль».
Договорились – защита скрытых полостей состоит из 2х этапов:
- Мойка порога от грязи изнутри
- Обработка антикоррозийным составом.
На этом у меня сегодня все. Если у вас остались вопросы про то, как защитить пороги автомобиля от коррозии, или если вы хотите рассказать свой опыт применения антикоррозийных составов – пишите комментарии.
С уважением, администратор https://life-with-cars.ru/
Антикоррозийная обработка порогов автомобиля – для чего нужна?
Антикоррозийная обработка автомобиля впервые проводится на заводе-изготовителе, но, к сожалению, тоже не всегда бывает качественной, поэтому даже автомобиль из салона следует тщательно проверить и сработать на опережение. Проблемными также являются дно автомобиля и колесные арки.
Чтобы защитить автомобильные пороги важно обрабатывать их антикоррозийным составом снаружи и изнутри. Для обработки скрытых полостей используют специальную насадку.
Процесс этот несложный и вполне подойдет для выполнения своими руками.
Для предохранения поверхности автомобиля вполне подойдет мовиль. Он легко наносится и образует стойкую пленку. Наносить можно только на неповрежденную поверхность. Если пороги повреждены, то простой обработки недостаточно.
Способы защиты порога
- При помощи аэрозольного покрытия.
- При помощи накладок.
- При помощи защитных пленок.
- При помощи мастик и лаков.
- При помощи жидких локеров.
Теперь рассмотрим каждый способ более подробно.
Чем обработать пороги изнутри
Чтобы защитить пороги автомобиля от коррозии внутри коробов, нужно выполнить антикоррозийную обработку. При этом можно использовать как готовые антикоррозийные составы (например, Раст-Стоп для скрытых полостей), так и хорошо известный Мовиль в пороги или другие решения.
При этом специалисты рекомендуют использовать профессиональные решения, так как они имеют свойство не пересыхать, обладают хорошей текучестью и укрывистостью поверхностей, содержат в своем составе специальные ингибиторы коррозии и т.д.
Основная задача сводится к тому, чтобы внутри короба эффективно распылить защитное средство, которое затем будет защищать металл (зачастую ничем не обработанный) и вытеснять влагу. Сделать обработку можно через специальные технологические отверстия, которые выполнены в коробах автомобиля для вентиляции (могут быть спрятаны за брызговиками и подкрылками).
Подготовка авто к антикору
Защита авто от ржавчины подразумевает несколько этапов. В первую очередь, автомобиль необходимо подготовить к выполнению процесса. Для этого нужно очистить его от уже имеющейся ржавчины. Чаще всего она скапливается в области днища, поэтому особое внимание уделяют именно его очистке. Чтобы это сделать, следует:
- Тщательно вымыть поверхность машины. Желательно отправиться на автомойку, где автомобиль качественно очистят от любых загрязнений.
- Для удаления ржавчины лучше использовать специальные ершики по металлу. Быстро очистить днище поможет дрель.
- Предварительно следует снять с автомобиля подкрылки, поскольку очень часто ржавчина образуется под ними.
После этого можно обработать днище автомобиля антикоррозийным составом.
Обычно его наносят толстым слоем, для высыхания которого требуется несколько суток. Эксплуатировать машину в этот период запрещается.
Рихтовка порога
В случае небольшого повреждения порогов имеет смысл провести мелкий рихтовочный ремонт. Но если помимо нарушения геометрии кузова или целостности ЛКП обнаружены глубоко поврежденные или прогнившие насквозь участки металла, то целесообразнее приобрести новую деталь. Обычно порог образует единое целое с кузовом, придавая ему дополнительную жесткость, но бывают и съемные пороги.
Съемный порог
Съемный порог автомобиля обычно располагается с наружной боковой стороны от лонжерона. Он оберегает кузов от попадания маленьких камней, которые выскакивают из-под колес.
Рихтовка порога споттером
Рихтовка и последующая покраска съемных порогов автомобиля выполняется намного проще, нежели в случае несъемной детали. Для этого его прежде всего надо демонтировать, выкрутив саморезы, которыми он прикреплен к лонжерону. Затем выполняется рихтовка вмятин, обработка внутренней стороны противокоррозийным грунтом или мазью, подготовка к окрашиванию и покраска. После повторного монтажа порога докрашиваются участки, поврежденные во время установки.
Несъемный порог
При рихтовке таких деталей вмятины вытягиваются снаружи. Для этого удаляется старый слой краски, а к поврежденному участку приваривают особые вытяжные зацепы. Их захватывают специальным инерционным съемником (споттером) и выравнивают вмятину.
Кроме того, можно вырезать поврежденный участок и заменить его на новый, выровняв поверхность последующей шпатлевкой и окрашиванием. Когда рихтовка завершена, переходим к подготовительному этапу, предшествующему покраске порога.
https://youtube.com/watch?v=50hc0VsBYvQ
Методы борьбы с коррозией
Обработка порогов автомобиля напрямую зависит от степени изношенности машины, а также страны-производителя. Так, новые европейские или японские машины на протяжении 3 лет будет защищать от коррозии заводское антикор покрытие. Отечественные или китайские авто даже с конвейера рекомендуется сразу отправить на антикоррозийную обработку. При этом пристальное внимание нужно уделить порогам, защита которых поможет продлить срок службы авто.
Грунтование
Одним из распространенных способов борьбы с коррозией считается грунтование. Это метод позволяет создать прослойку между металлом авто и лакокрасочным покрытием. Грунт выступает в качестве изолятора, препятствуя попаданию воды или кислорода на металл. Но обеспечить полное предотвращение попадания воды на поверхность он не может, поэтому только немного отдаляет образование коррозии.
Ламинирование
Одним из методов защиты порогов от ржавчины считается ламинирование. На участки авто наносится специальная полимерная пленка, прозрачная и абсолютно незаметная на поверхности. Она не отклеивается и не теряет свои свойства при сильных перепадах температуры. Защитная пленка может прослужить до 3 лет, после чего требуется ее повторное нанесение. Многие производители при выпуске своей продукции проводят ламинирование наиболее уязвимых участков автомобиля, к которым относятся и пороги.
Ламинированная пленка не ляжет на поверхность с неровностями, поэтому сначала участок нужно прошлифовать и отполировать.
Процесс обработки
- Если все-таки было решено обрабатывать кузов своими руками, то перед тем, как начать обработку, нужно очистить обрабатываемые элементы от грязи и других ненужных элементов. При правильной очистке кузова перед обработкой, средство может продержаться намного дольше, чем эксплуатационный срок. Для того, чтобы все держалось долгое время, после промывки нужно просушить кузовные части.
- После того, как был просушен кузов, желательно будет его обезжирить. Это еще больше увеличит срок годности покрытия.
- После того, как была проведена подготовка, можно приступать к нанесению слоя антикоррозийного средства. Для того, чтобы нанести слой этого вещества на закрытые элементы, потребуется распылитель. Чаще всего в качестве распылителя используют распылитель краски. Нередко продается средство для скрытых элементов в баллончиках, что еще больше упрощает процедуру. Если средство будет наноситься на арки и днище, то нужно взять кисть или валик.
Наносить нужно в несколько слоев, каждый из которых нужно высушить. Некоторые средства нужно наносить не на голый металл, а на металл, который уже покрыт грунтом. Чаще всего на упаковке таких средств это указано. Поэтому нужно читать инструкции, перед тем как наносить вещество на свой автомобиль.
Виды антигравия для порогов автомобиля
Количество средств антикоррозийной обработки порогов автомобиля велико. По большому счёту они мало чем отличаются друг от друга.
Средства защиты порогов машины от ржавчины можно разделить на несколько групп:
1.Период использования.
- постоянная защита;
- временная защита;
2.Упаковка.
- аэрозольный баллончик готовый для применения;
- аэрозольный баллончик под специальный пистолет;
- металлические банки;
- пластиковые ёмкости.
3.Цвет.
- прозрачный;
- белый;
- чёрный;
- cерый;
- цветной.
4.Дополнительные эффекты.
- с содержанием преобразователя ржавчины;
- антикоррозийными веществами;
- повышенная адгезия;
- усиленная прочность.
Метод 2 мойка автомобиля для предотвращения коррозии
- Регулярно мойте автомобиль. Несмотря на то, что зачастую грязь не вызывает коррозию, осадок и примеси могут просочится через краску, что со временем повреждает кузов.Птичий помет и бензин, который проливается при заправке, могут снизить защиту вашего автомобиля от ржавчины ещё больше. С течением времени они повреждают покрытие и делают его более восприимчивым к появлению коррозии. Промывайте свой автомобиль каждые несколько недель, чтобы песок и грязь не повредили краску.
- Вымойте шасси автомобиля. Если вы живете в заснеженном регионе, соль и химические отложения на нижней части машины могут поставить под угрозу ее способность противостоять коррозии. Учтите, что многие автоматические мойки автомобилей предлагают очистку шасси. Вы также можете поднять свой автомобиль и вымыть днище с помощью шланга.
- Используйте пищевую соду для нейтрализации дорожной соли. Если вы часто сталкиваетесь с этой проблемой, следует добавить немного пищевой соды и мыла в воду. Столовая ложка пищевой соды нейтрализует кислотный эффект соли и других химикатов, используемых на дорогах.Обязательно смешивайте вышеуказанное средство с мылом, и вы сразу заметите положительный результат. Одной столовой ложки пищевой соды достаточно для очистки ходовой части большинства автомобилей.
- Тщательно промойте автомобиль. Оставляя высушенное мыло на вашем транспортном средстве, вы также можете сократить срок службы краски. Удостоверьтесь, что вы смываете все мыло с вашего автомобиля каждый раз, когда вы его чистите.Никогда не мойте его под прямыми солнечными лучами, так как это может привести к тому, что химические составляющие моющего средства высохнут раньше самой краски. Вы можете нанести мыло на ваше транспортное средство на определенные зоны, а затем уже смыть его под сильным напором воды.
- Покрытие вашего автомобиля нуждается в обработке воском. Делать это нужно не реже двух раз в год. Воск обеспечивает ваш автомобиль красивым блеском, а также защищает краску от потери цвета и повреждений.Применение этого средства хотя бы два раза в год обеспечит кузов дополнительным слоем защиты и поможет уменьшить вероятность образования ржавчины. Воск отталкивает воду и создает еще один дополнительный защитный слой для корпуса.
Как и где проводить обработку
Подобная антикоррозийная обработка порогов может выполняться как самостоятельно, так и при помощи специального оборудования в соответствующих автомастерских и сервисах. Отметим, что сегодня используются материалы на основе мастики, которые предполагают их нанесение из специальных распылителей. В то же время можно в продаже найти обычные антигравийки на основе органических средств, которые выпускаются в виде аэрозолей, что упрощает их самостоятельное использование.
Помните о том, что, какое бы качественное средство вы ни использовали, через 2−3 года такая автохимия потеряет часть своих защитных свойств и в последующем могут вновь появиться проблемы с коррозией. Чтобы предупредить подобное, рекомендуется каждые 2−3 года выполнять такую обработку днища и порогов. В дальнейшем вам останется лишь правильно покрасить обработанные пороги и днище авто.
Катодная защита от коррозии автомобиля
Один из самых простых в исполнении и надежных способов замедлить коррозию – использовать электрохимический способ защиты. Для этого корпус автомобиля становится анодом, а расположенные в самых уязвимых местах специальные пластины – катодом. При таком распределении потенциалов разрушаются пластины катода, анод (корпус автомобиля) остается целым.
Электрохимическая защита от коррозии автомобиля — один из самых эффективных методов
Сделать такую электрохимическую защиту от коррозии, легко самостоятельно. Для этого нужно иметь элементарные знания по электронике и навыки владения паяльником. Если таких навыков нет, или возиться не хочется, можно купить готовое устройство.
Комплект электрохимической защиты от коррозии автомобиля
Представляет оно собой небольшой электронный блок с индикаторами и набор электродов. Размещать электроды нужно в самых подверженных воздействию коррозии местах:
- в местах крепления фар и подфарников,
- в передней части днища,
- за щитками передних колес,
- на внутренних частях порогов и дверей,
- в арке заднего колеса,
- на стыке колеса с крылом,
- в задней части днища и т.д.
Места установки электродов при протекторной защите от коррозии автомобиля
Количество пластин и размер пластин может быть разным, но существует определенная закономерность: чем больше размер электродов, тем их меньше. Устанавливать пластины-протекторы (от английского to protect – защищать, потому такой способ еще называют «протекторная защита от коррозии автомобиля») нужно так, чтобы на них как можно интенсивнее попадала влага, а наружную сторону (на ней отсутствует пайка) нельзя покрывать никаким электроизоляционным покрытием (мастикой, лаком и т.д.). Для прикрепления к кузову использовать нужно эпоксидную шпаклевку или клей, крепить электроды к деталям, имеющим лакокрасочное покрытие.
Принцип электрохимическая защита от коррозии автомобиля
Электронный блок катодно-протекторной защиты от коррозии автомобиля устанавливается в салоне и подключается к электросети так, чтобы даже при выключении двигателя он был запитан. Потребляет такое устройство очень мало энергии, а защищает кузов от коррозии тщательно и надежно. Причем (при грамотной установке электродов) даже в самых труднодоступных для обработки местах.
Есть несколько других вариантов анодов для электрохимической защиты автомобиля от коррозии. Можно для этих целей использовать металлический гараж, контур заземления, металлизированный «хвост».
Чтобы использовать металлический гараж для катодной защиты, его нужно подключить проводом через резистор к плюсу аккумуляторной батареи. Особенно эффективна такая защита летом, когда в металлическом гараже часто наблюдается скопление конденсата. Повышенная влажность при использовании катодной защиты от коррозии автомобиля способствует не разрушению защитного покрытия, а наоборот, замедляет процессы окисления металла на корпусе. Чтобы каждый раз не лазить под капот, можно взять «плюс» от прикуривателя (если в режиме стоянки на нем есть потенциал).
Гараж может служить для электрохимической защитыот коррозии автомобиля
Если гараж неметаллический, можно по четырем углам от автомобиля вбить четыре металлических стержня не менее метра длиной, соединить их при помощи проволоки, сохраняя электропроводимость, и подключить к автомобилю точно также как гараж.
Список материалов
Здесь мы отвечаем на вопрос, чем покрасить пороги автомобиля, чтобы защитить их от коррозии. Самый простой вариант – нанести защитный состав, не окрашивая его. Результат будет выглядеть, как показано ниже:
Защита антигравием без окраски
Слой самого антигравия можно покрыть лаком. Так делают, чтобы получить глянцевую поверхность. Кстати, многие антигравийные составы не допускают применения лака и красок – после нанесения образуется плёнка, обладающая упругостью. В общем, нужно точно представлять, что именно должно получиться в финале.
Готовый слой антигравийного покрытия, если он был нанесён несколько дней назад, покрывать лаком нельзя – лучше оставить всё, как есть, или провести окраску.
Перед нанесением антигравия поверхность нужно обезжирить. Для этого применяют растворители, не содержащие ацетона. Используйте сольвент. Также понадобится шлифовальная бумага P400-P1000. Ею проводят матирование.
Есть распространённый совет, что любой антигравий нужно покрывать лаком. Возможно, для некоторых материалов это справедливо на 100%. Однако, выбор остаётся за владельцем. Можно подобрать материал, не требующий дополнительной защиты.
Коррозия закладных материалов
Коррозия арматурной стали и других закладных металлов является основной причиной разрушения бетона. Когда сталь подвергается коррозии, образующаяся ржавчина занимает больший объем, чем сталь. Это расширение создает в бетоне растягивающие напряжения, которые в конечном итоге могут вызвать растрескивание, расслоение и отслаивание.
Сталь подвержена коррозии, потому что это не встречающийся в природе материал. Скорее, железная руда выплавляется и очищается для производства стали. Этапы производства, которые превращают железную руду в сталь, добавляют металлу энергии.
Сталь, как и большинство металлов, за исключением золота и платины, термодинамически нестабильна при нормальных атмосферных условиях, выделяет энергию и возвращается в свое естественное состояние — оксид железа или ржавчину. Этот процесс называется коррозией.
Для возникновения коррозии должны присутствовать следующие элементы:
- Должны быть как минимум два металла (или два участка на одном металле) с разными уровнями энергии
- электролит
- металлическое соединение
В железобетоне арматурный стержень может иметь много отдельных участков с разными уровнями энергии.Бетон действует как электролит, а металлическое соединение обеспечивается проволочными стяжками, опорами стульев или самой арматурой.
Коррозия — это электрохимический процесс, связанный с потоком зарядов (электронов и ионов). В активных участках стержня, называемых анодами, атомы железа теряют электроны и переходят в окружающий бетон в виде ионов железа. Этот процесс называется реакцией окисления полуэлемента или анодной реакцией и представлен как:
2Fe → 2Fe 2+ + 4e —
Электроны остаются в стержне и текут к участкам, называемым катоды, где они соединяются с водой и кислородом в бетоне.Реакция на катоде называется реакцией восстановления. Обычная реакция восстановления:
2H 2 O + O 2 + 4e — → 4OH —
Для поддержания электрической нейтральности ионы двухвалентного железа мигрируют через поры бетона и попадают в них. катодные участки, где они объединяются с образованием гидроксидов железа или ржавчины:
2Fe 2+ + 4OH — → 2Fe (OH)
Этот начальный осажденный гидроксид имеет тенденцию далее реагировать с кислородом с образованием более высоких оксидов.Увеличение объема по мере дальнейшей реакции продуктов реакции с растворенным кислородом приводит к внутреннему напряжению в бетоне, которого может быть достаточно, чтобы вызвать растрескивание и отслаивание бетонного покрытия.
Коррозию закладных металлов в бетон можно значительно снизить, если уложить без трещин бетон с низкой проницаемостью и достаточным покрытием из бетона. Бетон с низкой проницаемостью может быть получен за счет уменьшения отношения воды к вяжущим материалам в бетоне и использования пуццоланов и шлака.Пуццоланы и шлак также увеличивают удельное сопротивление бетона, тем самым снижая скорость коррозии даже после ее возникновения. ACI 318-11, Строительные нормы и правила для конструкционного бетона устанавливает минимальные требования к бетонному покрытию, которые помогут защитить металлические конструкции от коррозионных материалов. Дополнительные меры по снижению коррозии стальной арматуры в бетоне включают использование добавок, замедляющих коррозию, покрытие арматуры (например, эпоксидной смолой) и использование герметиков и мембран на поверхности бетона.Герметики и мембраны, если они используются, необходимо периодически повторно наносить.
Бетон и пассивный слой
Хотя сталь естественным образом склонна подвергаться коррозионным реакциям, щелочная среда бетона (pH от 12 до 13) обеспечивает защиту стали от коррозии. При высоком pH на стали образуется тонкий оксидный слой, предотвращающий растворение атомов металла. Эта пассивная пленка фактически не останавливает коррозию; снижает скорость коррозии до незначительного уровня. Для стали в бетоне скорость пассивной коррозии обычно равна 0.1 мкм в год. Без пассивной пленки скорость коррозии стали бы как минимум в 1000 раз выше (ACI222 2001).
Благодаря присущей бетону защите, арматурная сталь не подвергается коррозии в большинстве бетонных элементов и конструкций. Однако при разрушении пассивного слоя может возникнуть коррозия. Разрушение пассивного слоя происходит при снижении щелочности бетона или повышении концентрации хлоридов в бетоне до определенного уровня.
Роль хлорид-ионов
Воздействие хлорид-ионов на железобетон является основной причиной преждевременной коррозии стальной арматуры. Проникновение хлорид-ионов, присутствующих в солях для борьбы с обледенением и морской воде, в железобетон может вызвать коррозию стали, если кислород и влага также доступны для поддержания реакции. Растворенные в воде хлориды могут проникать через прочный бетон или попадать в сталь через трещины. Примеси, содержащие хлориды, также могут вызывать коррозию.Ни один другой загрязнитель не задокументирован так подробно в литературе как причина коррозии металлов в бетоне, чем ионы хлора. Механизм, с помощью которого хлориды способствуют коррозии, не совсем понятен, но наиболее популярная теория состоит в том, что ионы хлора проникают через защитную оксидную пленку легче, чем другие ионы, что делает сталь уязвимой для коррозии.
Риск коррозии увеличивается с увеличением содержания хлоридов в бетоне. Когда содержание хлоридов на поверхности стали превышает определенный предел, называемый пороговым значением, возникает коррозия, если также доступны вода и кислород.Исследования Федерального управления шоссейных дорог (FHWA) показали, что пороговый предел в 0,20 процента общего (растворимого в кислоте) хлорида от веса цемента может вызвать коррозию арматурной стали в настилах мостов (Clear 1976). Однако только водорастворимые хлориды способствуют коррозии; некоторые растворимые в кислоте хлориды могут быть связаны в агрегатах и, следовательно, не могут способствовать коррозии. Работа в FHWA (Clear 1973) показала, что коэффициент преобразования кислотно-растворимых хлоридов в водорастворимые может варьироваться от 0.От 35 до 0,90, в зависимости от состава и истории бетона. Произвольно было выбрано 0,75, в результате чего предел растворимости в воде хлоридов составляет 0,15% от веса цемента.
Хотя хлориды несут прямую ответственность за возникновение коррозии, они, по-видимому, играют лишь косвенную роль в скорости коррозии после ее возникновения. Основными факторами, регулирующими скорость, являются доступность кислорода, удельное электрическое сопротивление и относительная влажность бетона, а также pH и температура.
Карбонизация
Карбонизация происходит, когда двуокись углерода из воздуха проникает в бетон и вступает в реакцию с гидроксидами, такими как гидроксид кальция, с образованием карбонатов. В реакции с гидроксидом кальция образуется карбонат кальция:Ca (OH) 2 + CO 2 → CaCO 3 + H 2 O
Эта реакция снижает pH порового раствора до 8,5, при котором пассивная пленка на сталь нестабильна.
Карбонизация — обычно медленный процесс. Было подсчитано, что в высококачественном бетоне карбонизация будет происходить со скоростью до 0,04 дюйма в год. Уровень карбонизации значительно увеличивается в бетоне с высоким водоцементным отношением, низким содержанием цемента, коротким периодом отверждения, низкой прочностью и высокопроницаемой или пористой пастой.
Карбонизация сильно зависит от относительной влажности бетона. Самый высокий уровень карбонизации происходит при относительной влажности от 50 до 75 процентов.При относительной влажности ниже 25% степень карбонизации считается незначительной. При относительной влажности выше 75% влага в порах ограничивает проникновение CO2. Коррозия, вызванная карбонизацией, часто возникает на участках фасадов зданий, которые подвергаются воздействию дождя, затенены от солнечного света и имеют низкое бетонное покрытие над арматурой.
Карбонизация бетона также снижает количество ионов хлора, необходимых для ускорения коррозии. В новом бетоне с pH от 12 до 13 требуется от 7000 до 8000 ppm хлоридов, чтобы вызвать коррозию закладной стали.Однако, если pH понижается до диапазона от 10 до 11, пороговое значение хлоридов для коррозии значительно ниже — на уровне или ниже 100 частей на миллион. Однако, как и ионы хлора, карбонизация разрушает пассивную пленку армирования, но не влияет на скорость коррозии.
Пример карбонизации на фасаде здания.
Коррозия разнородных металлов
Когда два разных металла, такие как алюминий и сталь, контактируют в бетоне, может возникнуть коррозия, потому что каждый металл обладает уникальным электрохимическим потенциалом.Знакомый тип коррозии разнородных металлов происходит в обычной батарее фонарика. Цинковый корпус и угольный стержень — это два металла, а влажная паста действует как электролит. Когда углерод и цинк соединены проволокой, течет ток. В железобетоне коррозия разнородных металлов может происходить на балконах, где закладные алюминиевые перила контактируют с арматурной сталью. Ниже приведен список металлов в порядке электрохимической активности:1. Цинк 5. Никель 9.Медь
2. Алюминий 6. Олово 10. Бронза
3. Сталь 7. Свинец 11. Нержавеющая сталь
4. Железо 8. Латунь 12. Золото
Когда металлы контактируют в активном электролите, тем меньше активный металл (нижнее число) в серии корродирует.
Список литературы
Комитет ACI 222, Защита металлов в бетоне от коррозии , ACI 222R-01, Американский институт бетона, Фармингтон-Хиллз, Мичиган, 2001, 41 страница.Комитет ACI 318, Требования строительных норм для конструкционного бетона , ACI 318-05, Американский институт бетона, Фармингтон-Хиллз, Мичиган, 2005 г., 443 страницы.
Клир, К. К. и Хэй, Р. Э., «Время до коррозии арматурной стали в бетонной плите, V.1: Влияние параметров проектирования и строительства смеси», FHWA-RD-73-32, Федеральное управление шоссейных дорог, Вашингтон, Округ Колумбия, апрель 1973 г., 103 страницы.
Clear K.C., «Время до коррозии арматурной стали в бетонных плитах», Федеральное управление шоссейных дорог, PB 258 446, Vol.3, апрель 1976 г.
PCA, Типы и причины разрушения бетона, Portland Cement Association, Skokie, Illinois, 2002, 16 страниц.
Антикоррозия — обзор | Темы ScienceDirect
8.2 Трубопроводы и управление рисками
Нефть и газ в основном транспортируются по трубопроводу или серии трубопроводов, как над землей, так и под землей (рис. 8-3). Трубопроводы проходят между провинциями, штатами и странами. Газ движется по трубопроводам под давлением больших компрессоров.Некоторые компрессоры работают на природном газе, поступающем из самого трубопровода, а некоторые — на электроэнергии. Сырая нефть также перекачивается по трубопроводам, которые часто проходят в экологически уязвимых районах.
Рисунок 8-3. Нефтепровод Аляска.
Фото любезно предоставлено AP News.Трубопроводы, устанавливаемые как под землей, так и над землей, часто могут быть повреждены в результате различных работ. Наиболее частая причина — перфорация трубы или полный перелом. Газ будет выпускаться в окружающую среду со скоростью, зависящей от диаметра отверстия и давления внутри трубы.В конце концов выпуск будет остановлен автоматически с помощью регулятора, как реакция на чрезмерный расход, или даже вручную. Отказ трубопроводов природного газа может произойти из-за стихийных бедствий или техногенных катастроф, таких как землетрясение, ураган, саботаж, избыточное давление, наводнение, коррозия или усталостные отказы. На частоту отказов также влияют проектные факторы, условия строительства, политика технического обслуживания, использование технологий и факторы окружающей среды. Все виды аварий на трубопроводах определяются путем оценки рисков и управления ими (Ramanathan 2001).Оценка риска — это процесс получения количественной оценки риска путем оценки его вероятности и последствий. Риск обычно относится к возможности причинения вреда человеку. Этот риск представляет собой опасный сценарий, который представляет собой физическую или социальную ситуацию. В случае обнаружения это может вызвать ряд нежелательных последствий.
Выход из строя трубопроводов является потенциально опасным событием, особенно в городских районах и вблизи дорог. Следовательно, люди, находящиеся рядом с маршрутами трубопроводов, подвергаются значительному риску выхода из строя трубопровода.Опасное расстояние, связанное с трубопроводом, составляет от менее 20 метров для меньшего трубопровода при более низком давлении до более 300 метров для большего трубопровода при более высоком давлении (Jo and Ahn 2002). Поэтому очень важно изучить уровень безопасности трубопровода для лучшей оценки рисков и управления ими.
Оценка рисков касается безопасности, защиты окружающей среды, финансового управления, разработки проектов или продуктов, а также многих других областей деятельности. В секторе трубопроводов оценки рисков в основном рассматриваются в отношении безопасности трубопроводов, необходимой для защиты жизни людей, окружающей среды и имущества в результате аварийных ситуаций, связанных с отказом трубопровода.Трубопровод может выйти из строя и выбросить нефть или природный газ в окружающую среду, что может вызвать множество проблем, включая ухудшение состояния окружающей среды и гибель людей из-за воспламенения.
Основной причиной оценки риска является оценка вероятности возможных угроз, которые могут привести к отказу в определенном месте на трубопроводе, и возможных последствий. Эта оценка проводится путем определения конкретных характеристик трубопровода в любом заданном месте, а также уникальных характеристик окружающей местности.Восприимчивость трубопровода к отказу и его воздействиям зависит от множества характеристик, таких как тип и состояние покрытия трубы, состояние грунта вокруг трубы, расстояние трубопровода от конкретного места, содержимое трубопровода и т. Д.
To определить индивидуальный риск взрыва, данные о пределах воспламеняемости имеют важное значение в трубопроводе природного газа. Пределы воспламеняемости — это обычно используемые индексы для представления характеристик воспламеняемости газов. Критерий предела воспламеняемости и другие связанные параметры широко обсуждались в литературе (Vanderstraeten et al.1997; Kenneth et al. 2000; Кевин и др. 2000; Pfahi et al. 2000; Wierzba and Ale 2000; Мишра и Рахман 2003; Takahashi et al. 2003 г.).
Hossain et al. (2005) изучали воспламеняемость и оценку индивидуальных рисков для трубопроводов природного газа. Они разработали комплексную модель для индивидуальной оценки риска, для которой были объединены предел воспламеняемости и существующий индивидуальный риск для аварийного сценария. Их модель направлена на определение основной аварийной зоны в местности, окруженной трубопроводами, и для любого сценария оценки рисков газопровода.Hossain et al. (2005) также проверили модель, используя имеющиеся полевые данные. Однако они предполагают 10% -ный риск аварии из-за воспламенения при авариях на трубопроводе природного газа. Сценарий аварии может иметь любой процент в пределах предельного значения. Hossain et al. (2007) применили ту же модель для проверки различных случайных сценариев. Для тематического исследования в этой главе рассматривается уровень аварийности 1–20%, что является консервативным показателем при оценке риска.
В случаях оценки риска Fabbrocino et al.(2005) сообщили, что оценка всегда должна быть как можно более консервативной. Они также добавили, что какой бы ни была окончательность оценки, всегда следует учитывать «худший случай». При возникновении неопределенностей следует принимать во внимание детерминированную оценку, даже в рамках вероятностной оценки безопасности. Этот подход особенно эффективен, когда при оценке риска учитывается допущение о позднем или раннем возгорании.
Оценка риска для здоровья человека определяет, насколько опасна авария на трубопроводе для здоровья человека.Основная цель этой оценки — определить безопасный уровень загрязняющих веществ или выбросов токсичных соединений, таких как нефть и природный газ из трубопровода. В случае отдельных людей это стандарт, при котором вредное воздействие на здоровье маловероятно. Он также оценивает текущие и возможные будущие риски. В этом разделе рассматривается индивидуальный риск воспламенения природного газа для здоровья человека. Целью этого исследования является управление рисками до приемлемых уровней, а также включение информации об оценке рисков для планирования и развития трубопроводных сетей для менеджеров по рискам.
Для определения индивидуального риска взрыва необходимы данные о пределах воспламеняемости в трубопроводе природного газа. Пределы воспламеняемости — это обычно используемые показатели, которые представляют характеристики воспламеняемости газов. Эти пределы могут быть определены как такие отношения топливо-воздух, в пределах которых возможно распространение пламени и за пределами которых пламя не может распространяться. По определению существует два предела воспламеняемости, а именно нижний предел воспламеняемости (LFL) и верхний предел воспламеняемости (UFL).LFL можно определить как наименьший предел топлива, до которого может распространяться пламя, причем наивысший предел — это UFL (Liao et al. 2005). Предел воспламеняемости, критерий и другие связанные параметры широко обсуждались в литературе (Vanderstraeten et al. 1997; Kenneth et al. 2000; Kevin et al. 2000; Pfahi et al. 2000; Wierzba and Ale 2000; Mishra and Rahman). 2003; Такахаши и др. 2003).
8.2.1 Управление рисками трубопроводов
Хотя подземное заглубление трубопроводов рекомендуется, оно не предотвращает возникновения аварий, утечки газа и выхода трубопровода из строя.На входах и выходах трубопроводов с различных объектов должны быть предусмотрены средства аварийной изоляции. Для обеспечения целостности трубопроводы следует регулярно проверять на наличие повреждений и утечек в уязвимых местах, включая сварные соединения и фланцевые соединения. Обычно они проверяются с помощью таких методов тестирования, как ультразвук, рентген и проникающие красители.
Основным фактором, влияющим на опасные происшествия на трубопроводе в нормальных условиях, является коррозия. Поэтому важно заботиться о трубопроводах, используя соответствующие антикоррозионные материалы.Кроме того, отказ трубопровода может быть результатом действий третьих лиц, саботажа или стихийных бедствий. На рис. 8-4 показан подход к управлению рисками для трубопроводов природного газа, состоящий из следующих этапов:
Рис. 8-4. Управление рисками для газопроводов.
- •
Идентификация трубопроводной системы
- •
Операционная информация
- •
Оценка рисков
- •
Стратегия72
Оценка
8.2.2 Оценка риска для здоровья человека
К различным компонентам относятся планирование и определение объема работ, оценка воздействия, острые опасности, токсичность и характеристика риска. Основные компоненты оценки риска для здоровья человека показаны на Рисунке 8-4. Для эффективной оценки рисков необходимо «планирование и анализ» информации и данных. Это должно быть сделано до полевых исследований и определения характеристик участка.
Вторым этапом оценки риска для здоровья человека является «оценка воздействия» (рис. 8-5).Оценка воздействия относится к контакту людей с природным газом. Этот процесс учитывает время, продолжительность и частоту контакта химических веществ с людьми в прошлые, настоящие и будущие периоды времени. В случае оценки риска для человека, «острые опасности» означают условия, которые создают возможность травм или ущерба из-за мгновенного или кратковременного воздействия последствий аварийного выброса. В данном исследовании речь идет в основном о воспламеняемости природного газа.
Рисунок 8-5.Различные компоненты оценки рисков для здоровья человека.
«Идентификация опасностей» — это процесс определения того, может ли воздействие природного газа вызвать увеличение числа случаев конкретного неблагоприятного воздействия на здоровье. Как правило, это достигается за счет реакции на дозу определенных химических веществ. Процесс «характеризации риска» представляет собой синтез результатов всех других шагов и определяет, насколько опасна авария. Также рассматриваются основные предположения и научные суждения. Наконец, есть оценки характеристик риска неопределенностей, заложенных в оценке.
8.2.2.1 Уровни риска для здоровья человека
По трубопроводам транспортируется природный газ, содержащий метан, этан, пропан, изобутан, нормальный бутан, изопентан, нормальный пентан, гексаны плюс, азот, диоксид углерода, кислород, водород и сероводород. Кислый газ содержит большее количество сероводорода. В случае аварии на трубопроводе все эти соединения выбрасываются. Из-за горючести и воздействия всех этих соединений существуют разные уровни риска. Недавно (май 2006 г.) более 150 человек погибли из-за возгорания, вызванного авариями на трубопроводе.
Сообщается, что поврежденный топливопровод взорвался и загорелся недалеко от Лагоса, Нигерия (IRIN 2006). По этому трубопроводу топливо транспортируется со склада в порту Лагос для внутреннего использования внутри страны. Жертвами стали жители бедных рыбацких деревень. Аварии на трубопроводах — обычное дело в странах третьего мира, таких как Нигерия, богатая нефтью африканская страна. В 1998 году также сообщалось, что более 1000 человек погибли из-за аварии с возгоранием в Джесси, недалеко от нефтяного города Варри, в дельте Нигера (IRIN 2006).
В приведенном выше отчете об аварии показано, что из-за сильной воспламеняемости судьба неизбежна, но воздействие других компонентов, таких как сероводород, приводит к разным уровням риска. В Таблице 8-1 показаны различные уровни риска, вызванного сероводородом. Это явление следует серьезно рассматривать в случае высокосернистого газа, где концентрация сероводорода выше. Обычно типичное содержание серы составляет 5,5 мг / м 3 , что включает 4,9 мг / м 3 серы в одоранте (меркаптане), добавленном в газ по соображениям безопасности.
Таблица 8-1. Уровни риска для здоровья человека
Уровни риска | Концентрация (ppm) | Эффекты | |||
---|---|---|---|---|---|
Незначительный или нулевой риск | 0,01–0,3 | Порог запаха (сильно изменчивый) | 1–5 | Умеренный неприятный запах, может быть связан с тошнотой, раздражением глаз, головными болями или бессонницей при длительном воздействии; у здоровых молодых мужчин не наблюдается снижения максимальной физической работоспособности | |
Слегка умеренный риск | 108 ч | Предел профессионального воздействия | |||
Умеренный риск | 20–50 | Предел профессионального воздействия и уровень эвакуации населения, запах очень сильный | |||
Риск | 100 | Раздражение глаз и легких; обонятельный паралич, запах исчезает | |||
Высокий риск | 150–200 | Обоняние парализовано; сильное раздражение глаз и легких | |||
Высокий риск | 250–500 | Может возникнуть отек легких, особенно при длительном | |||
Чрезвычайный риск | 500 | Серьезное повреждение глаз в течение 30 минут; сильное раздражение легких; потеря сознания и смерть в течение 4–8 часов; амнезия на период воздействия; «Нокдаун» | |||
Критический уровень | 1000 | Дыхание может остановиться в течение одного или двух вдохов; немедленное коллапс |
Источник: Guidotti (1994)
Copyright © 1994
8.2.2.2 Горючие свойства природного газа
Как упоминалось ранее, природный газ имеет высокий риск воспламенения из-за своего состава. Чтобы понять риск воспламенения, его горючие свойства представлены в Таблице 8-2. Обратите внимание, что характеристики горения зависят от состава, но общие оценки приведены в этой таблице. Показанные свойства являются средними по системе Union Gas (Union Gas 2006).
Таблица 8-2. Типичные характеристики горения природного газа
Точка воспламенения: | 59 ° C * |
---|---|
Пределы воспламеняемости | 4% –16% (об.% в воздухе) |
Теоретическая температура пламени (стехиометрическое соотношение воздух / топливо) | 1960 ° C (3562 ° F) |
Максимальная скорость пламени | 0,3 м / с |
Относительная плотность (удельный вес ) | 0,585 |
Источник данных: Union Gas (2006)
Copyright © 2006
8.2.3 Оценка риска
Чтобы оценить риск, связанный с трубопроводом природного газа, необходимо оценить вероятные нежелательные последствия, возникшие в результате утечки или разрыва.
Количественный риск можно оценить по пределу воспламеняемости для трубопровода природного газа. Риски были описаны как индивидуальный риск, социальный риск, максимальный индивидуальный риск, средний индивидуальный риск для населения, подвергшегося воздействию, средний индивидуальный риск для всего населения и средний уровень смертности (TNO Purple Book 1999; Jo and Ahn 2002, 2005).
Интенсивность отказов трубопроводов зависит от различных параметров, таких как состояние почвы, тип и свойства покрытия, конструктивные соображения и возраст трубопровода.Итак, протяженный трубопровод разбивается на участки из-за значительного изменения этих параметров. Учитывая постоянную интенсивность отказов, индивидуальный риск может быть записан как (Jo and Ahn 2005):
(8.1) IR = ∑iφi∫l − l + pidl
, где
φ i = Failure норма на единицу длины трубопровода, связанного со сценарием аварии, и , из-за состояния почвы, покрытия, конструкции и возраста
л = длина трубопровода
p i = летальность связанный со сценарием аварии, i
l ± = Концы взаимодействующего участка трубопровода, в котором авария представляет опасность для определенного места
Выброс газа через отверстие в трубопроводе вызывает взрыв и пожар в трубопроводе природного газа и на прилегающей территории.Затронутый участок создает опасное расстояние. Скорость выброса природного газа и опасное расстояние коррелированы (Jo and Ahn, 2002):
(8,2) rh = 10,285Qeff
, где
Q eff = Эффективная скорость выброса из отверстия в трубопровод, по которому проходит природный газ
r h = Опасное расстояние
Опасное расстояние — это расстояние, на котором существует более 1% вероятности смертельного исхода из-за радиационной теплоты струйного огня от разрыва трубопровода.На рис. 8-6 показаны геометрические отношения между переменными в указанном месте трубопровода природного газа. Из этого рисунка, взаимодействующий участок прямого трубопровода, х от указанного места, оценивается уравнением 8.3 (Джо и Ан 2005):
Рисунок 8-6. Индивидуальные переменные риска.
(8,3) l ± = 106Qeff-h3
Джо и Ан (2005) показывают различные причины отказа в зависимости от размера отверстия и других действий. Внешнее вмешательство со стороны сторонних организаций является основной причиной основных аварий, связанных с размером ствола скважины.Следовательно, для анализа внешних помех требуется более подробная концепция. Действия третьих лиц зависят от нескольких факторов, таких как диаметр трубы, глубина покрытия, толщина стенки, плотность населения и методы предотвращения. Частота отказов трубопровода оценивалась некоторыми исследователями (Джо и Ан 2005; Джон и др. 2001).
8.2.4 Влияние состава на предел воспламеняемости
Обычно проводится экспериментальное исследование для изучения эффектов концентрации или разбавления в природном газе — воздушной смеси путем добавления газа CO 2 , N 2 .Диапазон предельных значений составляет 85–90% для N 2 и 15–10% для CO 2 по объему. Это практическое рассмотрение стехиометрического сжигания природного газа при температуре окружающей среды. Эксперименты по воспламеняемости проводились для моделирования реальных взрывов, чтобы выявить и предотвратить опасности в практических приложениях (Liao et al. 2005). В таблице 8-3 приведены данные о предельных значениях воспламеняемости для пламени метан-воздух и природного газа-воздуха (Liao et al. 2005).
Таблица 8-3. Данные о пределе воспламеняемости (об.%) Для пламени метан-воздух и природный газ-воздух (спокойные смеси с искровым зажиганием)
Смесь | Условия испытания | LFL (об.%) | UFL (об.%) | ||
---|---|---|---|---|---|
NG-воздух | 1.Камера 57 л | 5,0 | 15,6 | ||
Правило ЛеШателье | 4,98 | — | |||
Метан-воздух | Камера 8 л | 5,0 | — | 15,9 | |
Камера 120 л | 5,0 | 15,7 | |||
25,5 м 3 сфера | 4,9, 5,1 ± 0,1 | — | |||
Трубка воспламеняемости 4 | 9 | 15,0 |
LFL зависит от состава топливной смеси в воздухе. Это значение можно оценить по правилу Лешателье (Liao et al. 2005):
(8,4) LFL = 100∑ (Ки / LFLi)
, где
LFL = нижний предел воспламеняемости смеси (об.% )
C i = Концентрация компонента i в газовой смеси без содержания воздуха (об.%)
LFL i = Нижний предел воспламеняемости компонента , и (т.%)
Оценка правила Лешателье приведена в Таблице 8-3. Зависимость предела воспламеняемости природного газа от концентрации этана была изучена Liao et al. (2005) (рис. 8-7). Показано, что область воспламеняемости несколько расширяется с увеличением содержания этана в природном газе. LFL составляет почти 5% по объему, а UFL — около 15%. Пределы воспламеняемости составляют от 3% до 12,5% по объему для смеси этан-воздух. Их эквивалентные отношения 0,512 и 2.506. Соотношения для метана составляют 0,486 и 1,707 соответственно. Отмечено, что увеличение содержания этана в природном газе увеличивает коэффициент эквивалентности UFL, но при этом не происходит заметного изменения LFL. Liao et al. (2005) показывает влияние соотношения разбавителей ( φ r ) на коэффициент воспламеняемости. Увеличение соотношения разбавителей уменьшает область воспламеняемости. Причина в том, что добавление разбавителей снижает температуру пламени, что снижает скорость горения.Таким образом, сужается предел воспламеняемости. Обычно CO 2 оказывает большее влияние, чем добавление N 2 . Шебеко и др. (2002) представили аналитическую оценку пределов воспламеняемости тройных газовых смесей топливно-воздушного разбавителя.
Рисунок 8-7. Зависимость пределов воспламеняемости ПГ от этана.
8.2.5 Индивидуальный риск, основанный на воспламеняемости
На рисунке 8-8 показана случайная зона, основанная на базовой гидродинамике. Сценарий аварии представляет эту случайную зону.Если произойдет взрыв, случайная зона будет охвачена метательной теорией гидродинамики. Эта концепция является основным отличием от модели Джо и Ан (2005), которая показана на рис. 8.8. Здесь основной причиной инцидента считается авария из-за воспламенения. OB — это максимальное расстояние, пройденное пламенем, в пределах которого вероятен смертельный исход или травма (Рисунок 8-8). BA и BC — это максимальные расстояния, пройденные пламенем.
Рисунок 8-8. Связь переменных, связанных с IR f .
Скорость природного газа, выходящего через отверстие, может быть записана как
(8,5) u = 1,273qmindhole2
, где
q min = Минимальный расход газа, выделяющийся через отверстие, вызывающий взрыв = f ( u, d отверстие )
d отверстие = Диаметр отверстия, через которое проходит газ.
Опасное расстояние или максимальное расстояние, которое покрывают частицы газа, можно записать как
(8.6) hmax = 12ut cos α
, где
h max = Опасное расстояние
u = Скорость газа
t = Время прохождения до опасного расстояния
α = Угол между скоростью газа и опасным расстоянием
На рисунке 8-8 показаны геометрические отношения между переменными в определенном месте от газопровода. Из этого рисунка, взаимодействующий участок прямого трубопровода l ± из определенного места B и угол α оцениваются как
(8.7) l ± = 12ut sin α
и
(8,8) α = tan-1 (lhmax)
Индивидуальный риск ( IR f ) из-за предела воспламеняемости в естественном трубопроводе можно записать как
(8,9) IRf = ∑iφi100∫-l + l∫0hmax (UFLi-LFLi) dhdl
, где
φ i = интенсивность отказов на единицу длины трубопровода, связанная со сценарием аварии , i из-за воспламеняемости
л = длина трубопровода
UFL = верхний предел воспламеняемости
LFL = нижний предел воспламеняемости
- Концы взаимодействующих участков трубопровода, в которых авария представляет опасность для конкретного места.
На Рис. 8-9 показано количество инцидентов с удалением трубопровода от источника газа. Данные были собраны из сводной статистики инцидентов Управления безопасности трубопроводов США с 1986 по август 2005 г. (Hossain et al. 2006a). Количество инцидентов колеблется в пределах 67 775 и 259 136 миль. Однако за пределами этого расстояния частота инцидентов демонстрирует ненормальную картину. Это может быть вызвано другими факторами, такими как стихийное бедствие, деятельность человека и т. Д.
Рисунок 8-9. Инцидент, связанный с протяженностью трубопровода.
Перерисовано из Hossain et al. (2006a). Авторские права © 2006Нет доступной информации, которая касалась бы как предела воспламеняемости, так и летальности для измерения индивидуального риска. Получить данные сложно из-за воспламеняемости на месте аварии. В этом исследовании предполагается, что 10% аварийных сценариев связаны с воспламеняемостью. Предлагаемая модель (уравнение 8.9) тестируется с использованием 10% случайного сценария. Результаты показывают индивидуальный риск, связанный с воспламеняемостью, с количеством травм (рис. 8-10).Нормальный тренд кривой увеличивается с увеличением количества инцидентов, что приводит к отдельному сценарию аварий из-за воспламеняемости. Эта диаграмма также показывает, что существует большое влияние воспламеняемости на случай аварии.
Рисунок 8-10. Индивидуальный риск из-за воспламеняемости и количества травм.
На рис. 8-10 показана вероятность индивидуального риска из-за воспламеняемости в зависимости от расстояния трубопровода с использованием уравнения 8.9. Здесь предполагается, что UFL и LFL равны 15.6 и 5.0 соответственно. Для расчета данного тематического исследования q мин рассматривается как 1 фута 3 / сек, α = 45 °, t = 1 мин и d отверстие = 0,5 фута. Доступная литература показывает, что максимальное значение h составляет 20 м, а l — 30 м. Здесь расчет показывает, что h составляет 80,5 футов, а l составляет 129,93 футов. Эти значения кажутся разумными. Индивидуальный риск воспламенения снижается по мере удаления трубопровода от центра подачи газа.Тем не менее, эта тенденция имеет тенденцию быть непредсказуемой и более частой в случае аварии на участке трубопровода в 124 931 милю. Этот график также показывает, что существует большое влияние воспламеняемости на случайный сценарий.
Комбинируя уравнения 8.1 и 8.9, получается комбинированный индивидуальный риск в трубопроводе природного газа:
(8.10) IRT = IR + IRf
Это представляет собой реальный сценарий индивидуального риска из-за летальности и воспламеняемости природного газа. . Летальность трубопровода природного газа зависит от рабочего давления, диаметра трубопровода, расстояния от источника газа до трубопровода и длины трубопровода от газоснабжения или компрессорной станции до точки отказа.
Hossain et al. (2006a) продемонстрировали концепцию индивидуального риска из-за воспламеняемости в местности с густонаселенностью. Рисунок 8-8 был перерисован из этой ссылки, где был представлен подробный анализ. Несчастный случай из-за возгорания рассматривается здесь как основная причина происшествия. OB — это максимальное расстояние, пройденное пламенем, в пределах которого возможен смертельный исход или травма. BA и BC — это максимальные расстояния, пройденные пламенем.
Индивидуальный риск ( IR f ), связанный с пределом воспламеняемости в естественном трубопроводе, можно записать как
(8.11) IRf = ∑iφi100∫-l + l∫0hmax (UFLi-LFLi) dhdl
, а общий индивидуальный риск можно записать как
(8.12) IRT = IR + IRf
, где
φ i = интенсивность отказов на единицу длины трубопровода, связанная со сценарием аварии, i из-за воспламеняемости
l = длина трубопровода, фута
UFL = верхний предел воспламеняемости
LFL = Нижний предел воспламеняемости
l ± = Концы взаимодействующего участка трубопровода, в котором авария представляет опасность для указанного места, футов
Таблица 8 -4 показывает различные данные по количеству смертей / травм в результате аварий с возгоранием природного газа на трубопроводе с 1985 по 2005 год.Данные были получены от Министерства безопасности трубопроводов США.
Таблица 8-4. Количество травм и данные о воспламеняемости для различных процентов (Hossain et al. 2006a)
Смертельные исходы / травмы | Смертельные исходы / травмы из-за воспламенения природного газа | |||||||||||||||||||||||||||||||||||||||||||||||||||||||||||||||||||||||||||||||||||||||||||||||||||||||||||||||||||||||||||||||||||||||||||||||||||||||||||||||||
---|---|---|---|---|---|---|---|---|---|---|---|---|---|---|---|---|---|---|---|---|---|---|---|---|---|---|---|---|---|---|---|---|---|---|---|---|---|---|---|---|---|---|---|---|---|---|---|---|---|---|---|---|---|---|---|---|---|---|---|---|---|---|---|---|---|---|---|---|---|---|---|---|---|---|---|---|---|---|---|---|---|---|---|---|---|---|---|---|---|---|---|---|---|---|---|---|---|---|---|---|---|---|---|---|---|---|---|---|---|---|---|---|---|---|---|---|---|---|---|---|---|---|---|---|---|---|---|---|---|---|---|---|---|---|---|---|---|---|---|---|---|---|---|---|---|---|---|---|---|---|---|---|---|---|---|---|---|---|---|---|---|---|
1% | %3% | 6402398% | 10% | 12% | 14% | 16% | 18% | 20% | ||||||||||||||||||||||||||||||||||||||||||||||||||||||||||||||||||||||||||||||||||||||||||||||||||||||||||||||||||||||||||||||||||||||||||||||||||||||||||
97 | 0.97 | 2,91 | 5,82 | 7,76 | 9,7 | 11,64 | 13,58 | 15,52 | 17,46 | 19,4 | ||||||||||||||||||||||||||||||||||||||||||||||||||||||||||||||||||||||||||||||||||||||||||||||||||||||||||||||||||||||||||||||||||||||||||||||||||||||||
102 | 3,02 | 3,0 12,24 | 14,28 | 16,32 | 18,36 | 20,4 | ||||||||||||||||||||||||||||||||||||||||||||||||||||||||||||||||||||||||||||||||||||||||||||||||||||||||||||||||||||||||||||||||||||||||||||||||||||||||||||
103 | 1,03 | 3,09 | 6,18 | 8,24 | 10.3 | 12,36 | 14,42 | 16,48 | 18,54 | 20,6 | ||||||||||||||||||||||||||||||||||||||||||||||||||||||||||||||||||||||||||||||||||||||||||||||||||||||||||||||||||||||||||||||||||||||||||||||||||||||||
109 | 1,09 | 3,27 | 6,54 | 8,72 10242 | 6,54 | 8,72 | 8,72 | 21,8 | ||||||||||||||||||||||||||||||||||||||||||||||||||||||||||||||||||||||||||||||||||||||||||||||||||||||||||||||||||||||||||||||||||||||||||||||||||||||||||
110 | 1,1 | 3,3 | 6,6 | 8,8 | 11 | 13,2 | 15,4 | 17,6 | 19,8 | 22 | 18 | 3,54 | 7,08 | 9,44 | 11,8 | 14,16 | 16,52 | 18,88 | 21,24 | 23,6 | 21,24 | 23,6 | ||||||||||||||||||||||||||||||||||||||||||||||||||||||||||||||||||||||||||||||||||||||||||||||||||||||||||||||||||||||||||||||||||||||||||||
121 902 502 | 121 902 902 | 1,2 14,52 | 16,94 | 19,36 | 21,78 | 24,2 | ||||||||||||||||||||||||||||||||||||||||||||||||||||||||||||||||||||||||||||||||||||||||||||||||||||||||||||||||||||||||||||||||||||||||||||||||||||||||||||
124 | 1,24 | 3,72 | 7,44 | 9,92 | 12.4 | 14,88 | 17,36 | 19,84 | 22,32 | 24,8 | ||||||||||||||||||||||||||||||||||||||||||||||||||||||||||||||||||||||||||||||||||||||||||||||||||||||||||||||||||||||||||||||||||||||||||||||||||||||||
137 | 1,37 | 4,11 | 8,22 | 10,96 | 10,96 | 27,4 | ||||||||||||||||||||||||||||||||||||||||||||||||||||||||||||||||||||||||||||||||||||||||||||||||||||||||||||||||||||||||||||||||||||||||||||||||||||||||||||
141 | 1,41 | 4,23 | 8,46 | 11,28 | 14,1 | 16,92 | 19,74 | 22,56 | 25.38 | 28,2 | ||||||||||||||||||||||||||||||||||||||||||||||||||||||||||||||||||||||||||||||||||||||||||||||||||||||||||||||||||||||||||||||||||||||||||||||||||||||||
142 | 1,42 | 4,26 | 8,52 | 11,36 | 14,2 | 17,04 | 19,88 | 22,72 | 22,72 | 8,76 | 11,68 | 14,6 | 17,52 | 20,44 | 23,36 | 26,28 | 29,2 | |||||||||||||||||||||||||||||||||||||||||||||||||||||||||||||||||||||||||||||||||||||||||||||||||||||||||||||||||||||||||||||||||||||||||||||||||
154 | 1,54 | 629,24 | 12,32 | 15,4 | 18,48 | 21,56 | 24,64 | 27,72 | 30,8 | |||||||||||||||||||||||||||||||||||||||||||||||||||||||||||||||||||||||||||||||||||||||||||||||||||||||||||||||||||||||||||||||||||||||||||||||||||||||||
162 | 1,62 | 162 | 22,68 | 25,92 | 29,16 | 32,4 | ||||||||||||||||||||||||||||||||||||||||||||||||||||||||||||||||||||||||||||||||||||||||||||||||||||||||||||||||||||||||||||||||||||||||||||||||||||||||||||
163 | 1,63 | 4,89 | 9,78 | 13,04 | 16,3 | 19.56 | 22,82 | 26,08 | 29,34 | 32,6 | ||||||||||||||||||||||||||||||||||||||||||||||||||||||||||||||||||||||||||||||||||||||||||||||||||||||||||||||||||||||||||||||||||||||||||||||||||||||||
172 | 1,72 | 5,16 | 10,32 | 13,76 | 17,2 | 17,20 | ||||||||||||||||||||||||||||||||||||||||||||||||||||||||||||||||||||||||||||||||||||||||||||||||||||||||||||||||||||||||||||||||||||||||||||||||||||||||||||
177 | 1,77 | 5,31 | 10,62 | 14,16 | 17,7 | 21,24 | 24,78 | 28,32 | 31,86 | 35.4 | ||||||||||||||||||||||||||||||||||||||||||||||||||||||||||||||||||||||||||||||||||||||||||||||||||||||||||||||||||||||||||||||||||||||||||||||||||||||||
201 | 2,01 | 6,03 | 12,06 | 16,08 | 20,1 | 24,12 | 28,14 | 32,16 | 36,18 | 40,2 данные приведены в Таблице 8-4. Он показывает количество инцидентов с индивидуальным риском из-за воспламеняемости для различных процентов риска воспламенения на трубопроводе. Данные были собраны из сводной статистики инцидентов Министерства безопасности трубопроводов США с 1986 по август 2005 года.На этом рисунке индивидуальный риск увеличивается и демонстрирует гораздо более резкую тенденцию, когда увеличивается риск опасности для здоровья человека из-за травм, вызванных воспламенением. Это означает, что на индивидуальный фактор риска влияет фактор риска воспламенения в пределах контурной местности. Рисунок 8-11. Индивидуальный риск из-за воспламеняемости с количеством травм (Hossain et al. 2006a). В настоящее время существует множество моделей для исследования индивидуального риска (John et al. 2001; Jo et al.2002, 2005; Fabbrocino et al. 2005). Однако нет доступной модели, которая учитывала бы как предел воспламеняемости, так и летальность для измерения индивидуального риска для здоровья человека. Получить данные по аварийному сценарию сложно из-за воспламеняемости. Основываясь на имеющейся информации и данных, касающихся этого вопроса, Hossain et al. (2006a) можно легко использовать для уверенной проверки любых наборов данных. В этом исследовании считается, что 1–20% аварийных сценариев связаны с воспламеняемостью (Hossain et al.2006 г.). Используя эти данные, модель (уравнение 8.1) тестируется, и результаты показаны на рисунках 8-12 и 8-13. Здесь предполагается, что UFL и LFL имеют значения 15,6 и 5,0 соответственно. q мин рассматривается как 1 фута 3 / сек, α = 45 °, t = 1 мин и d скважина = 0,5 фута для тематического исследования. Имеющаяся литература показывает, что максимальное значение h составляет 66 футов, а l — 99 футов (Hossain et al. 2006a).Здесь расчет показывает, что h составляет 80,5 футов, а l составляет 129,93 футов, и эти значения кажутся разумными в данном случае. Рисунок 8-12. Процент индивидуального риска из-за воспламеняемости с расстоянием трубопровода (1–18%). Рисунок 8-13. Процент индивидуального риска из-за воспламеняемости с расстоянием трубопровода (20%). В таблице 8-5 показаны различные индивидуальные риски, связанные с данными о воспламеняемости для разных расстояний трубопровода. Данные воспламеняемости были рассчитаны с использованием уравнения 8.11. Данные о жертвах / травмах от природного газа в авариях на трубопроводах относятся к 1985–2005 гг. Данные были получены от Министерства безопасности трубопроводов США. Таблица 8-5. Индивидуальный риск из-за воспламеняемости с расстоянием трубопровода
На рис. 8-12 показан индивидуальный риск воспламенения в зависимости от расстояния трубопровода.Нормальный тренд кривой уменьшается с увеличением длины трубопровода, что приводит к отдельным сценариям аварий из-за воспламеняемости. График также показывает, что существует большое влияние воспламеняемости на случайные сценарии. Интересным моментом является то, что эта модель показывает, что риск опасности для здоровья человека из-за воспламеняемости в индивидуальных оценках риска природного газа ограничен 18% от общего фактора риска (рисунки 8-12 и 8-13). Эти цифры были получены с использованием данных, приведенных в Таблице 8-6.Результаты, превышающие 18% от общего индивидуального риска, не соответствуют другим процентам риска, и значения, показанные в расчетах, нереалистичны (рис. 8-14). Эта информация просто означает, что индивидуальный риск опасности для здоровья человека из-за воспламеняемости природного газа не превышает 18% индивидуального риска. Таблица 8-6. Распределение природного газа в мире
Источник данных: © 2005 Рисунок 8-14.Процент индивидуального риска из-за воспламеняемости в зависимости от расстояния трубопровода. Обширные трубопроводные сети для системы газоснабжения сопряжены со многими рисками. Для обеспечения безопасности необходимо соблюдать соответствующее управление рисками. Индивидуальный риск — один из важных элементов количественной оценки риска. Учитывая ограничения в традиционной оценке риска, представлен новый метод измерения индивидуального риска, объединяющий все вероятные сценарии и параметры, связанные с практическими ситуациями, с учетом воспламеняемости газа.Эти параметры можно рассчитать напрямую, используя географические и исторические данные трубопровода. Использование предложенного метода может сделать управление рисками более привлекательным с практической точки зрения. Предложенная модель признана новаторской в использовании статистических данных о трубопроводах и инцидентах. Метод может применяться для управления трубопроводом на этапах планирования, проектирования и строительства. Его также можно использовать для обслуживания и модификации трубопроводной сети. Обеспечение долговременной защиты от коррозии за счет подавления электрической активности графенаИз-за своей исключительной непроницаемости для газов, паров и жидкостей графен (G) используется в качестве отличного покрытия для защиты металла.Однако недавние исследования показали, что из-за его высокой проводимости G не предотвращает коррозию металла при длительном воздействии воздуха. Здесь мы получили B-легированный графен (BG) и N-легированный графен (NG) с электронодонорными / отводящими элементами, а затем использовали их для модификации водной полиуретановой (PU) смолы. Наша работа показывает, что внедрение BG в полиуретановую матрицу значительно улучшает антикоррозионные свойства. Результаты показали, что графен (BG), легированный электронно-акцепторными легирующими добавками, демонстрирует долговременную коррозионную стойкость, основанную на подавлении гальванической коррозии, в то время как графен (NG), легированный электронодонорными легирующими добавками, проявляет стимуляцию коррозии из-за своей повышенной проводимости.Как правило, модуль импеданса BG / PU при Z f = 0,01 Гц составлял до 10 8 Ом см 2 , увеличиваясь примерно на три порядка по сравнению с модулем чистого ПУ, Г / ПУ и НГ / ПУ (∼10 6 Ом · см 2 ) после погружения на 240 ч в 3,5 мас.% NaCl (водн.) . Настоящее исследование дает важные результаты в будущем для создания антикоррозионных покрытий на основе графена с превосходной долговечностью. У вас есть доступ к этой статье Подождите, пока мы загрузим ваш контент… Что-то пошло не так. Попробуй еще раз?Ресурсы по защите от коррозии и долговечностиСуществует несколько проверенных способов защиты стальных мостов от коррозии, и ни одно решение не подходит для всех обстоятельств. Первое, что следует учитывать при выборе одного из этих методов, — это, конечно, ожидаемое воздействие на мост коррозионных элементов в течение его срока службы. Кроме того, при выборе подхода к защите от коррозии для конкретного моста команды должны учитывать начальные затраты и затраты на жизненный цикл, изготовление, производительность, а также долгосрочную производительность и техническое обслуживание. Общие ресурсы: Некоторые варианты защиты от коррозии:Атмосферостойкая сталь без покрытия (UWS) предназначена для образования стабильной патины, которая защищает структурную целостность элемента.Атмосферостойкая сталь без покрытия — это широко используемая сегодня система защиты от коррозии, которая хорошо работает, если должным образом детализирована и используется в надлежащем месте и в соответствующих условиях. За дополнительной информацией обращайтесь:
Примечание о туннельных условиях: Раздел 3.4 (стр. 21) Том 19 Руководства по проектированию стальных мостов FHWA обобщает дополнительные коррозионно-стойкие сплавы, такие как A709-50CR. Услуги по нанесению коррозионно-стойких покрытий | Praxair Surface TechnologiesКоррозионно-стойкие покрытия Что такое коррозия?Прежде чем разобраться в возможных решениях по нанесению покрытий, вы должны иметь представление о коррозии. Коррозия возникает, когда металл вступает в химическую или электрохимическую реакцию, в результате которой металл расходуется с образованием металлического соединения, такого как сульфид, гидроксид или оксид. Проще говоря, это когда контакт с окружающей средой приводит к ухудшению качества металла. Что вызывает коррозию?Металл корродирует в результате реакции, в которой обычно участвуют кислород, водород, хлор и / или сера из окружающей среды.Агрессивность коррозии может значительно возрасти в присутствии тепла, электрического тока или механического воздействия. Коррозионное растрескивание стали — хорошо известный пример коррозионного воздействия механического напряжения, которое приводит к взрывам котлов, разрывам газопроводов и обрушению мостов. Какие бывают типы коррозии?
Какие способы предотвращения коррозии?Существует три основных категории антикоррозионных покрытий, обеспечивающих защиту.
Возможные решения по покрытию для обеспечения коррозионной стойкости или защиты?Фторполимеры Среди органических материалов фторполимеры уникальны тем, что сочетают в себе одновременно разные свойства, которые обычно можно найти только по отдельности в разных и различных классах полимеров: среди других различных свойств они проявляют:
По этой причине они широко используются в химической, фармацевтической, энергетической и полупроводниковой отраслях, где необходимо бороться с коррозией в суровых условиях. В частности, фторполимерные покрытия стали играть важную роль в предоставлении инженерам-технологам, специалистам по техническому обслуживанию и производству единственного жизнеспособного решения и альтернативы сплавам с высоким содержанием никеля (Inconel 625, Hastelloy C и т. Д.) Для защиты их технологического оборудования (независимо от того, изготовлены из углеродистой стали), везде, где присутствуют сильные кислотные условия, в частности, выше 60 ° C (когда резиновая футеровка больше не обеспечивает раствор) или где присутствует комбинация растворителей и кислот, смешанных вместе, или когда чистота процесса жидкости из любого металлического катиона, даже на уровне частей на миллиард, должны быть предоставлены, как обычно требуется в фармацевтической или полупроводниковой промышленности. Высокоэффективные покрытия для суспензий Неорганическое металлокерамическое базовое покрытие состоит из водного неорганического связующего в сочетании с частицами алюминия, которые обеспечивают защиту от гальванической коррозии. Его распыляют на подготовленный материал основы с последующим процессом сушки, отверждения и полировки для образования защитного слоя. Связующее на основе хромата-фосфата, фосфата или силиката часто используется для обеспечения химического связывания с субстратом. Иногда поверх базового покрытия используется герметизация, чтобы создать дополнительный барьер от коррозии путем заполнения пор, повышения коррозионной стойкости и повышения эффективности работы в более агрессивных средах.Герметизирующее покрытие, иногда называемое верхним слоем, состоит из систем неорганических связующих или органических связующих с пигментами или без них для усиления защиты от коррозии металлической основы с уже нанесенным покрытием. Диффузионные покрытия Диффузионные покрытия состоят из поверхностного слоя сплава подложки, обогащенного защитными оксидными отложениями Al, Cr, Si или их комбинацией на глубину от 15 до 100 мкм. Эти элементы в сочетании с основными составляющими сплава подложки образуют новый химический состав со значительными высокими уровнями Al, Cr, Si или их комбинаций.Для разных областей применения были разработаны различные диффузионные покрытия. Для защиты от высокотемпературного окисления предпочтительным диффузионным покрытием являются алюминиды, которые образуют защитную окалину из оксида алюминия при воздействии высоких температур на воздухе. Для защиты от горячей коррозии более предпочтительны покрытия из алюминия, модифицированного платиной или хромом, а также хромирующее покрытие. Диффузионное покрытие — это, по сути, вид обогащения поверхности путем химического осаждения из паровой фазы.Как правило, он может быть получен с помощью процесса цементации насадки, процесса суспензии, над или вне процесса насадки и «истинного» процесса химического осаждения из паровой фазы. Покрытия для термического напыления
Накладки для лазерной наплавки и сварки TIG с подогревом Гальванические покрытия (PDF) Феноменологическая модель хлоридного порога питтинговой коррозии стали в смоделированных поровых растворах бетона18 Bamforth (Eds.), Коррозия арматуры в бетоне, Elsevier Applied Science, Лондон, Великобритания, 1990, стр. 49–58. [2] Стратфулл Р. Ф., «Коррозия стали в железобетонном мосту», Corros 1956; 13 (3): 173-178. [3] Гауда, В. К., «Коррозия и ингибирование коррозии арматурной стали», Br Corros J, 1970; 5 (2): 198-202. [4] Гласс, Г. К., Буэнфельд, Н. Р., «Представление порогового уровня хлоридов для коррозии стали в бетоне», Corros Sci, 1997; 39 (5): 1001-1013. [5] Алонсо, К., Андраде, К., Кастеллот, М., Кастро, П., «Пороговые значения хлоридов для Депассивации арматурных стержней, встроенных в стандартизованный раствор OPC», Cem Concr Res, 2000 ; 30 (7): 1047-1055. [6] Гласс, Г. К., Буэнфельд, Н. Р., «Хлоридная коррозия стали в бетоне», Prog Struct Engng Mater, 2000; 2: 448-458. [7] Ангст, У., Элсенер, Б., Ларсен, К. К., Веннесланд, О., «Критическое содержание хлоридов в железобетоне — обзор», Cem Concr Res, 2009; 39: 1122-1138. [8] Энн, К. Ю., Сонг, Х. У., «Пороговый уровень хлоридов для коррозии стали в бетоне », Corros Sci 2007; 49: 4113-4133. [9] Кайяли, О. А., Хейг, М. Н., «Проникновение хлоридов и соотношение Cl- / OH- в порах цементной пасты», Cem Concr Res, 1988; 18: 895-900. [10] Хаусманн Д. А., «Вероятностная модель коррозии стали в бетоне», Mater Perform, 1998; 37 (10): 64-68. [11] Ёнэдзава, Т., Ашворт, В., Проктер, Р. П. М., «Влияние состава порового раствора и хлоридов на коррозию стали в бетоне», Corros, 1988; 44 (7): 489- 493. [12] Брейт В., «Критическое содержание хлоридов — исследования стали в растворах щелочных хлоридов », Mater Corros, 1998; 49 (6): 539-550. [13] Хартт В. Х., Нам Дж. «Влияние щелочности цемента на порог хлоридов и время до коррозии арматурной стали в бетоне», Corros, 2008; 64 (8): 671-680. [14] Дехва, Х.А.Ф., Маслехуддин, М., Остин, С.А., «Влияние щелочности цемента на химический состав порового раствора и коррозию арматуры, вызванную хлоридом», ACI Mater J, 2002; 99 (3): 227-235. [15] Хассейн, С. Э., Аль-Гахтани, А. С., Рашидузафар, М., «Порог хлоридов для коррозии арматуры в бетоне», ACI Mater J, 1996; 93 (6): 1-5. [16] Морено, М., Моррис, В., Альварес, М.Г., Даффо, Г.С., «Коррозия арматурной стали в имитированных поровых растворах бетона — влияние карбонизации и содержания хлоридов », Corros Sci, 2004 ; 46: 2681-2699. [17] Крос, П., Хартт, У.Х., Ю, Х., «Влияние арматуры на проникновение хлоридов в бетон и время до коррозии», Труды 16-го Международного конгресса по коррозии , 22 сентября -26, 2005 г., Пекин, Китай. [18] Ли, Л., Сагес, А. А., «Порог хлоридной коррозии арматурной стали в щелочных растворах — Испытания на погружение в открытом цикле», Corros, 2001; 57 (1): 19-28. [19] Алонсо, К., Кастеллот, М., Андраде, К., «Хлоридная пороговая зависимость питтинга Потенциал армирования», Electrochim Acta, 2002; 47: 3469-3481. [20] Монфор, Г. Э., Вербек, Г. Дж., «Коррозия предварительно напряженной проволоки в бетоне», ACI Mater J, 1960; 57 (5): 491-497. Защита от коррозии | Американская ассоциация гальванизаторовДом » Онлайн-семинар по арматурной стали » Почему арматура HDG? » Защита от коррозии Сталь— это эффективный строительный материал в большом количестве, обеспечивающий свободу выбора при проектировании.Однако для стали, залитой бетоном, очень важно нанести на сталь покрытие для защиты от коррозии. Расчетный срок службы крупных строительных проектов часто составляет 75–125 лет, что подчеркивает необходимость в надежной и долговечной защите от коррозии. Горячее цинкование (HDG) обеспечивает превосходную коррозионную стойкость арматурной стали за счет барьерной защиты, катодной защиты и высокого порога содержания хлоридов. Первая линия защиты от коррозии — барьерная защита. Как и краски, горячеоцинкованное покрытие обеспечивает защиту, изолируя сталь от электролитов в окружающей среде.Пока барьер не поврежден, сталь защищена и коррозия не возникает. Однако если преграда будет нарушена, начнется коррозия. Поскольку барьер должен оставаться неповрежденным для обеспечения коррозионной стойкости, двумя важными свойствами барьерной защиты являются адгезия к основному металлу и стойкость к истиранию. Плотно связанный, непроницаемый характер металлического цинка делает его очень хорошим барьерным покрытием.Покрытия, такие как эпоксидная смола с отверстиями для штифтов, подвержены проникновению элементов, вызывающих быстрое распространение коррозии под пленкой. В дополнение к барьерной защите, горячее цинкование защищает сталь катодно, что означает, что цинк будет предпочтительно подвергаться коррозии, чтобы защитить нижележащую базовую сталь. Гальваническая серия металлов — это список металлов, упорядоченный по их электрохимической активности в морской воде (электролите). Такое расположение металлов определяет, какой металл будет анодом и катодом, когда они будут помещены в электролитическую ячейку.Металлы, расположенные выше в списке, анодны по отношению к металлам под ними, что означает, что они обеспечивают катодную или защитную защиту, когда они соединены. Следовательно, цинк защищает сталь. Фактически, эта катодная защита гарантирует, что даже если покрытие HDG будет повреждено до такой степени, что обнажится оголенная сталь (до дюйма в диаметре), коррозия не начнется до тех пор, пока не будет израсходован весь окружающий цинк. Цинк вступает в реакцию с водой, заливаемой бетоном, с образованием соединений, которые защищают металлическую поверхность от дальнейшей коррозии после высыхания бетона.Соединения также задерживают начало депассивации, не позволяя хлоридам достигать поверхности металла. Порог инициирования высокого содержания хлоридов Механизмы коррозии и характеристики горячеоцинкованной стали в бетоне иные, чем при воздействии на нее в атмосферных условиях. Сталь, заложенная в бетон, подвергается воздействию сильнощелочной среды. Черная сталь является пассивной в щелочном бетоне до тех пор, пока уровень хлоридов не превысит примерно 1 фунт / ярд 3 , когда сталь станет депассивированной и начнет корродировать.Цинк, с другой стороны, может выдерживать концентрацию хлоридов в 2-4 раза выше, чем черная сталь, и в сочетании с его непроницаемой барьерной защитой задерживает начало хлоридной коррозии на оцинкованной арматуре. Хлориды проникают в бетон через мелкие поры и трещины, которые образуются на поверхности в результате использования и погодных условий. В то время как черная сталь в бетоне обычно депассивируется при pH ниже 11,5, оцинкованная арматура может оставаться пассивированной при более низком pH, тем самым обеспечивая существенную защиту от эффектов карбонизации бетона. Миграция продуктов коррозии и уплотнение бетонной матрицыВ дополнение к более высокой толерантности к хлоридам, как только цинковое покрытие действительно начинает депассивацию, образующиеся продукты коррозии цинка становятся менее объемными, чем оксиды железа, и фактически мигрируют из оцинкованного стержня в матрицу бетона. В отличие от образования оксида железа, миграция продуктов коррозии цинка из арматуры предотвращает повышение давления и возможное растрескивание бетона. Продукты коррозии цинка представляют собой рыхлые порошкообразные минералы, которые менее объемны, чем продукты коррозии железа, и способны мигрировать с поверхности оцинкованной арматуры в прилегающую матрицу бетона.В результате коррозия цинкового покрытия практически не разрушает окружающий бетон. Элементная карта (слева) свидетельствует об этой миграции. Белые пятна в бетоне указывают на то, что оксид цинка переместился с поверхности раздела оцинкованная арматура / бетон. Также есть свидетельства того, что диффузия продуктов коррозии цинка помогает заполнить поровые пространства на границе раздела бетон / арматура, делая эту область менее проницаемой и помогает снизить перенос агрессивных веществ, таких как хлориды, через эту зону раздела к цинковому покрытию. .Реакции между цинком и бетоном и возникающая в результате диффузия продуктов коррозии также объясняют, почему оцинкованная арматура имеет такую хорошую прочность сцепления с бетоном. Пример защиты от коррозииРиф — Саутгемптон, Бермудские острова, 2008 г. Расположенный посреди тропического рая, Reef Plaza также подвержен одной из самых агрессивных сред, которые только можно представить.Аквамариновые воды и солнечный пляж, расположенный на бетонном полу площади, подвержены воздействию резкого солнца, проливных дождей и соленой соленой воды, что делает стальную арматуру внутри бетона восприимчивой к эстетическим и структурным повреждениям, таким как растрескивание и скалывание. Используя арматуру из горячеоцинкованной стали, архитектор проекта защитил площадь изнутри. Арматура будет защищена от зазубрин и царапин, полученных во время работы, а это означает, что части войдут в бетон и будут защищены от ржавчины и коррозии, которые могут вызвать растрескивание. |