Алюминиевый кузов – плюсы и минусы – список моделей авто
Все стараются купить машину как можно более современную и полную передовых «наворотов». Но есть некоторые «фишки», которых при покупке подержанного авто желательно избегать. Алюминиевый кузов – в том числе.
Того, кто покупает новый автомобиль премиум-сегмента (или близкий к тому) в автосалоне, вряд ли интересуют методы его ремонта. Кузов из алюминиевого сплава наоборот может быть представлен дилером как дополнительное преимущество модели.
Использование алюминиевых сплавов при изготовлении кузова авто позволяет снизить его массу на четверть, а то и на треть.
Но другое дело – выбор машины после ДТП под восстановление, с американского аукциона. С точки зрения ремонта детали из алюминия оказываются немалой проблемой. Во-первых, крылатый металл рихтуется совсем не так, как сталь. Во-вторых, даже замена легкосплавной детали на новую требует особых технологий: аргонная и лазерная сварка, сварка трением, болты, заклепки, клей и т.
ТАКЖЕ ИНТЕРЕСНО: Рихтовка кузова авто своими руками
Итак, какие модели из популярных на американских аукционах имеют кузов с алюминиевыми деталями:
Audi A6. Популярное на американских аукционах четвертое поколение седана с индексом С7 (2011 – 2018) имеет из алюминия переднюю и заднюю части лонжеронов, опоры, подвески (литье!), двери, передние крылья, капот, багажник и заднюю полку кузова. Остальное – сталь двух сортов.
Audi A8. Считается, что все четыре поколения седана имеют полностью алюминиевый кузов – в том числе и его силовой каркас. Хотя последняя на сегодня генерация D5 (с 2017) имеет уже 40% стали.
Практически все модели Audi, которые сегодня популярны на американских аукционах, имеют алюминий в конструкции кузова.
Audi Q5. Кроссовер первого поколения (2008 – 2016 гг.) не имеет существенных кузовных деталей из алюминия, кроме капота и двери багажника.
Audi Q7. В первом поколении (2005 – 2015 гг.) модель имеет легкосплавные двери багажника и поперечный подрамник задней подвески. Второе поколение Q7 (с 2015 г.) в значительной степени сделано из алюминия, в его кузове до 41% этого металла: передние и задние лонжероны, двери, боковины и др. (см фото).
Audi Q8. У этого новичка рынка – в первую очередь американского – тоже большинство компонентов кузова из крылатого металла, спереди, сзади и снизу (см. фото). Причем несколько из них даже литые, что еще больше усложняет ремонт. Собственно, это касается также и других вышеупомянутых моделей немецкой марки.
ТАКЖЕ ИНТЕРЕСНО: Что делать, чтобы уберечь кузов от коррозии
BMW 5. Передняя часть кузова “пятерки” работы Криса Бэнгла (E60 2003 – 2009 гг.) выполнена из алюминия, остальная – из стали. Под передней частью понимается вся силовая структура – лонжероны, опорные чашки подвески, моторный щит. Следующая генерация F10 (2010 – 2016 гг.) также изрядно “алюминизированная” – почти вся структура крепления передней подвески, капот и четыре двери. Наконец, действующая “пятерка” G30 имеет из этого металла передние и задние лонжероны и опорные силовые элементы обеих подвесок. А также все двери, капот, крышку багажника, крышу и передние крылья.
Передовые автопроизводители кроме алюминия используют в конструкции кузова несколько видов стали и композиты. Есть более десятка способов соединения деталей из различных материалов.
BMW 7. Современная седьмая серия G12 (с 2015 г.) имеет в основе не только алюминий (передняя и задняя силовые части, чашки подвесок), но и сталь, и даже карбон. Двери также алюминиевые.
Chevrolet Corvette. Культовый спорткар Corvette с индексом С7 (2014 – 2019 гг.) построен на алюминиевом каркасе, при том что обвес – карбоновый, что облегчает ремонт.
Porsche Panamera. Первый седан от Porsche (2009 – 2016 гг.) имеет алюминиевые лонжероны передка, капот, крышку багажника и облицовку дверей. Более того – “телевизор” радиатора и рамки дверей сделаны из магниевого сплава, который нельзя варить из-за опасности пожара. В нынешней генерации Panamera (с 2016 г.) кузов почти целиком из алюминия – за исключением боковин и деталей днища.
Большая проблема кузова с деталями из разных материалов – обеспечить одновременно и прочность соединения, и изоляцию деталей друг от друга (для предотвращения коррозии).
Porsche Cayenne/Macan. Второй Cayenne (2010 – 2018 гг.) получил легкосплавный капот и внутренние рамки дверей, а у третьего (с 2018 г.) из стали только моторный щит и несколько силовых деталей на днище. У малыша Macan’а из алюминия только капот и крышка багажника.
Tesla model S. Самая дорогая модель Tesla (с 2012 г.) базируется на алюминиевой раме, из этого же металла отлиты силовые детали, к которым крепится подвеска. Внешние детали кузова также из алюминия. Подобным образом устроены и кузов кроссовера Tesla model X (с 2016 г.).
Tesla model Y. Самая свежая модель Tesla (с 2020) уже поступает в Украину с заокеанских площадок, где продают машины после ДТП. Она не самый плохой вариант для восстановления, так как из алюминия в нее не так уж много деталей: пороги, законцовки передних лонжеронов и огромная литая деталь, которая объединяет задние колесные арки, задние лонжероны и поперечины между ними вместе с полом.
Tesla моделей S и X (первые три фото) имеют алюминиевый кузов и такой же силовой каркас в нижней части. В модели Y (две последние фото) доминирует сталь.
Но несмотря на все сложности с ремонтом, алюминиевые сплавы в конструкции кузова – не приговор. Если у вас есть знакомый мастер, который владеет технологиями правки крылатого металла, то с дополнительной скидкой при торгах алюминиевую машину можно брать. Главное, чтобы мастер перед покупкой подтвердил, что серьезных повреждений нет и он справится с ремонтом.
Напоследок осталось добавить, что некоторые из ведущих автопроизводителей еще несколько лет назад начали понемногу отказываться от алюминия как конструкционного материала. Например, лидер применения крылатого металла Audi уже уменьшает его процент в каркасе кузова – прежде всего, в пользу высокопрочной стали.
Полноценно отремонтировать кузов из различных материалов можно только на официальном СТО, да и там не все виды повреждений признаются пригодными для ремонта.
Но на самых новых – серийных! – моделях вместо стали начали использовать магний и карбон (углепластик). Пройдет немного времени и эти машины станут «битками» и «евробляхами» – поэтому мастера-рихтовщики, готовьтесь…
Рекомендация Авто24
Выбирать подержанный автомобиль с оглядкой на его ремонтопригодность – подход вполне рациональный. Особенно если речь идет о кузове, который является основой всего автомобиля и без восстановления которого невозможно существование последнего. Учтите это, даже если машина покупается без повреждений алюминиевых компонентов – ведь нельзя исключать, что такое случится с ней уже в ваших руках. Тем более, что ремонтировать алюминиевые кузовные детали в условиях неофициального сервиса очень непросто и в любом случае недешево.
ТАКЖЕ ИНТЕРЕСНО: Как навосковать кузов автомобиля своими руками
Алюминий в автопроме
Алюминий впервые начал использоваться в автомобильной промышленности более ста лет назад. В то время он был совсем еще новым и малоизученным металлом, но его свойства – легкость и отсутствие коррозии – делали его очень перспективным для зарождающейся автомобильной промышленности.Первый спортивный автомобиль, корпус которого был сделан из алюминия, был представлен публике на международной выставке в Берлине в 1899 году. А первый двигатель, при создании которого использовался алюминий, был сделан несколькими годами позже. В 1901 году Карл Бенц, впоследствии всемирно известный автомагнат, представил для участия в престижных автогонках в Ницце новый автомобиль с двигателем, части которого были сделаны из алюминия.
«Легкий металл» уменьшал вес автомобиля, делал его маневреннее, но сложность обработки алюминия, нехватка знаний и дороговизна ограничивали возможность массового использования этого металла в начале века. Только в послевоенные годы, когда алюминий стал доступнее и дешевле, британская компания Land Rover всерьез занялась изучением возможностей «крылатого металла» и в 1961 году продемонстрировала и затем запустила в массовое производство модель автомобиля – Buick 215 с восьмицилиндровым (V8) двигателем. Блоки этого мотора были сделанным из алюминия. Новый двигатель сразу же завоевал популярность у автогонщиков: компактный и легкий, он весил всего 144 кг и давал существенное преимущество при ускорении.
В 1962 году Микки Томсон, человек легенда американских автогонок, участвовал в гонках «Индианаполис 500» на авто с двигателем из легкого метала, который превосходно показал себя на тех соревнованиях. Многие фирмы позднее усовершенствовали этот легендарный двигатель и использовали его в различных массовых моделях и гоночных автомобилях, в том числе и в Формуле 1.
В семидесятые годы разразившийся нефтяной кризис заставил автомобильные компании искать пути снижения потребления топлива. Известно, что расход топлива во многом зависит от массы автомобиля. Было подсчитано, что снижение веса небольшого пассажирского легкового автомобиля на 100 кг может сэкономить до 700 литров бензина за все годы эксплуатации этого автомобиля (80.000 км). Поэтому автопроизводители стали заменять многие детали на более легкие из алюминия, тем самым снижая общий вес автомобиля. Сегодня в обычном легковом автомобиле в среднем содержится до 110-145 кг алюминия и с каждым годом доля «легкого металла» увеличивается.
Новые прочные сплавы из алюминия способны полностью заменить сталь, традиционно используемую для производства такого важного элемента автомобиля, как кузов. Это доказали инженеры автоконцерна Audi, который в 1994 году представили модель A8, кузов которой вместо стали был полностью сделан из алюминия. Выигрыш в весе представленной модели составил 239 кг! Результатом почти 20-летних исследований и опытно-конструкторских работ стал выпуск пространственной рамы ASF – высокопрочной алюминиевой структуры, в которую встроены большие алюминиевые панели, принимающие на себя часть нагрузки. Штампованные алюминиевые панели соединяются с помощью многофункциональных литых элементов. Новая конструкция потребовала применения самых передовых технологий. Для этого были разработаны новые легкие сплавы и технологии обработки материалов. Модели с алюминиевым кузовом произвели настоящий фурор среди экспертов и поклонников Audi. Сейчас полностью алюминиевые кузова получают модели Audi А2 (усовершенствованный вариант) и А8 (обновленная версия). С 1993 года компания выпустила 133 тысячи таких A2 и 117 тысяч – А8.
Не отстает от Audi и Rover. Новое поколение внедорожника Land Rover – Range Rover – будет иметь важное отличие от своего предшественника – алюминиевую конструкцию кузова. Алюминиевый кузов позволит снижает массу Range Rover по сравнению с Land Rover порядка на 300 – 400 кг. Тем не менее в модельном ряду Land Rover этот автомобиль по-прежнему будет оставаться самым помпезным и представительным, с максимально просторным и люксовым интерьером. Алюминиевый кузов позволит, в частности, добиться улучшения показателей топливной экономичности, а также снизить уровень выбросов углекислого газа в атмосферу, положительным образом сказаться на динамике и управляемости автомобиля.
Инженеры компании Mazda разработали революционную технологию сварки алюминия со сталью, которая впервые была применена в промышленном производстве комплектующих для новой модели спорткара RX-8. До этого момента сварка алюминия и стали представлялась неразрешимой задачей. Инженеры Mazda решили ее путем разогрева за счет трения верхних слоев алюминия (как это происходит в микроволновой печи) и одновременной гальванизации сварной поверхности стали. Процесс коррозии позволяет частицам алюминия проникать в структуру стали и обеспечивать надежное сцепление.
Новая технология открыла широкие возможности в автомобилестроении для выпуска комбинированных кузовов из алюминия и стали, части которых скрепляются сваркой, а не заклепками. Это повышает долговечность и надежность конструкций, обеспечивая одновременно выигрыш по весу. В рамках разработки новой технологии специалисты Mazda оформили более 20 патентов.
Не так давно компания Jaguar сообщила о появлении первого представителя нового поколения своих спортивных автомобилей – модели Jaguar XK. Следует обратить внимание на технологию производства кузова. Уникальным здесь является первое промышленное использование в автомобилестроении конструкции несущего кузова типа «монокок», состоящей полностью из алюминия. Развив авиационные технологии, где снижение массы является критическим фактором, компании Jaguar удалось внедрить в серийное производство легкую и прочную несущую конструкцию кузова, отдельные элементы которой могут быть скреплены как с помощью заклепок, так и с помощью эпоксидных клеев.
«Пятерка» BMW построена с активным применением алюминиевых деталей – из «крылатого металла» сделаны почти все элементы передней части автомобиля. Как считают специалисты, подобное решение продиктовано желанием инженеров BMW снизить общий вес автомобиля и, одновременно с этим, добиться более равномерной развесовки по осям. Положительное влияние это конструктивное решение оказывает и на управляемость автомобиля.
Сегодня алюминий – второй материал по процентному содержанию в общем весе автомобиля и применяется в производстве кузовов и компонентов подвесок, шасси, а также в блоках цилиндров, и других компонентах двигателя. Более 30% производимого алюминия используется сегодня в автомобилестроении и транспорте. Содержание алюминия в общем весе автомобиля будет увеличиваться год от года. Cчитается, что 1 кг алюминия может заменить до 2 кг стали или чугуна во многих областях применения. Чем больше в автомобиле используется алюминия, тем автомобиль легче, что означает, что он потребляет меньше топлива и выбрасывает меньше вредных газов в атмосферу. Было подсчитано, что в 2006 году в мире было произведено 65 млн. автомобилей. Если бы в каждом из этих автомобилей кузов, двигатель и другие детали были изготовлены из алюминия вместо стали, то в воздух было бы выброшено на 140 миллионов тон меньше CO2, а экономия топлива за все время службы всех автомобилей позволила бы сэкономить 60 млрд. литров сырой нефти.
Mercedes E, S; BMW 5, 7; Peugot 307, 607; Renault Laguna; VW Lupo Eco; Citroеn C5; Volvo V70, S60, S80; Landrover Discover; Range Rover; Audi
Результатом почти 20-летних исследований и опытно-конструкторских работ Audi стал выпуск пространственной рамы ASF – высокопрочной алюминиевой структуры, в которую встроены большие алюминиевые панели, принимающие на себя часть нагрузки.

«Пятерка» (и «семерка) BMW построены с активным применением алюминиевых. Подобное решение позволяет снизить общий вес автомобиля и, одновременно с этим, добиться более равномерной развесовки по осям.
Алюминиевый кузов: плюсы и минусы
Чего больше у «крылатого металла» — достоинств или недостатков в качестве материала для изготовления автомобильного кузова?С одной стороны, топливная экономичность машины напрямую зависит от ее массы — сокращение последней на 10% снижает расход топлива примерно на 7%. Самый же эффективный способ снизить массу автомобиля — сделать легче его кузов, сохранив его прочность.
Для этого и используются алюминиевые сплавы, из которых производится либо кузов целиком, либо отдельные его элементы. Среди автомобилей, встречающихся на белорусских дорогах, к примеру — Audi A8, Land Rover Defender, BMW 5-й и 7-й серий. Как видите, недорогих автомобилей в этом списке нет. Алюминиевые кузова хоть и дешевле кузовов из карбона и кевлара, но значительно дороже традиционной стали.
«Крылатый» металл удорожает не только сам автомобиль, но и его ремонт. Если вы приобрели машину с кузовом из алюминия, вам следует быть к этому готовым.
Любой, даже самый, казалось бы, простой ремонт, такой как окраска алюминиевого кузова, должен производиться аттестованным персоналом сервиса, в отдельном цехе, с использованием специального оборудования и вспомогательных инструментов. Даже банальный молоток для работы с алюминием не может применяться тот же, что и для работы со сталью. Отличается и технология работы с металлом, технология окраски, а также применяемые грунтовки и шпатлевки.
Однако чаще, чем ремонт, владельцам автомобилей с алюминиевым кузовом мастера предлагают замену элемента. В ряде случаев так выйдет даже дешевле. Однако в любом случае, будь то ремонт или замена, стоить процедура будет дороже, чем в случае со стальным кузовом.
Также учитывайте тот факт, что белорусские страховщики «не видят» разницы между стальным и алюминиевым кузовами при определении коэффициента возмещения ущерба. Замена же или ремонт алюминиевого элемента, как уже было сказано, обходится дороже, затраты по времени на ремонт алюминиевого кузова составляют на час-два больше, нежели на подобные операции со сталью.
Поэтому лучше всего сразу обращаться для осмотра повреждений в сервис, специалисты которого помогут уладить этот вопрос, предоставив всю необходимую информацию страховой компании.
Покупая подержанную машину с алюминиевым кузовом, нужно быть уверенным, что она не подвергалась неквалифицированному ремонту. Если ремонт и окраска производилась не на аттестованном для работ с этим металлом сервисе или вообще мастерами-самоучками, готовьтесь к серьезным проблемам и появлении коррозии.
Как Ford будет собирать алюминиевые кузова пикапа F-150
Следуй:
Поделись:
СОЛИХАЛЛ, Англия – Скромные заклепки, вот что ставит во главу угла менеджер подразделения по сборке кузовов Jaguar Land Rover, расположив их близко к вершине списка рисков при сборке алюминиевого кузова Range Rover.
В кузове Range Rover 2014 используется 17 типов заклепок, 3,722 штук на каждый автомобиль. Если одна застрянет в пистолете или будет установлена неправильно, производство остановится.
Перед тем, как заклепка поступит на конвейер, она проверяется по крайней мере два раза, при сортировке и рентгеном. Каждая поставленная партия заклепок имеет свой штрих-код и должна подойти к конкретному пистолету, который затем «стреляет» ими в алюминиевые части кузова скрепляя их.
Итак, чтобы понять какие проблемы ожидает переход Ford F-150 на алюминиевый кузов, нужно обратить внимание на заклепки и множество других взаимосвязанных аспектов подобного производства, которое реализовано на этом конвейере в английском индустриальном центре.
Производство с использованием алюминия как все отлично понимают, очень сложно. Множество шагов спрессованы в тот же промежуток времени, который требуется чтобы собрать стальной кузов.
Инженеры Ford не сильно беспокоятся об этом, так как Ford во многом участвовал в разработке этой системы, когда владел Jaguar и Land Rover.
«Очевидно, что мы сделали много передовых инженерных разработок, когда Jaguar являлся частью группы. Поэтому у нас есть большой опыт», — сказал Automotive News в январе Радж Наир, вице-президент Ford Group по разработке продуктов.
Однако от этого, осенью не станет легче, когда Ford начнет сборку около 650,000 пикапов F-150 в год на двух своих заводах. Для сравнения, в Солихалле, Jaguar Land Rover собирает всего 95,000 автомобилей с алюминиевым кузовом в год.
171 метр клея
Кузов каждого Range Rover имеет 403 отдельных компонента – штампованных и литых элементов, которые нужно скрепить вместе промышленным клеем и заклепками.
В начале сборочного конвейера штампованные алюминиевые панели кузова и литые части берутся роботами и устанавливаются в особые приспособления или рамы. При нанесении клея компоненты четко удерживаются в точном положении.
«Заклепки и клей это наподобии брюк с цепочками и пуговицами», — сказал Марк Вайт, главный технический специалист по алюминию Jaguar Land Rover. «На деле вам не нужны одновременно и цепочки и пуговицы, однако если вы оба используете, ваши брюки никогда не спадут».
В каждом кузове Range Rover используется 171 метр клея, полоска длиной почти в два футбольных поля и шириной с карандаш. Как только кузов собран, он направляется в покрасочный цех, где он держится в течение 20 минут при температуре в 140° С для окончательного затвердевания клея.
Однако наиболее критическим аспектом сборки кузова являются заклепки и сложность управления ими. Заклепочные пистолеты «выстреливают» их сквозь метал, чтобы соединить секции вместе. Однако это не обычные заклепки, которые можно купить в хозяйственном магазине, они намного сложнее.
Некоторые из 17 различных стальных заклепок с использованием бора, покрыты веществом предотвращающим коррозию, и выглядят идентично, имеют такую же ширину, длину, форму, однако отличаются по твердости.
Перед тем, как заклепки поступят на конвейер Range Rover, они просвечиваются рентгеном, чтобы исключить дефектные. Покрытие предохраняет гальваническую коррозию в точке соприкосновения стали и алюминия.
Так как эта задача имеет исключительно критическое значение, лишь четыре специально подготовленных человека из каждой смены имеют право работать с заклепками. Каждая сканируется, чтобы удостовериться, что каждый пистолет заряжен соответствующими заклепками.
В каждом автомобиле Land Rover использует 3,722 заклепки. Ford пока не сообщает таких подробностей о F-150. Однако, если считать, что в каждом пикапе будет использоваться примерно такое же количество заклепок, то получается, что для сборки 650,000 F-150, Ford ежегодно будет использовать 2.4 миллиарда заклепок.
Прочнее сварки
Точечная сварка, применяемая практически во всех стальных кузовах намного проще чем использование заклепок. Обычно, при сварке варьируются только давление, время и интенсивность. Однако при сборке в Солхалле используется 17 типов заклепок и каждый предназначен специально для определенной задачи.
«Аппарат для точечной сварки делает точечную сварку, и с его помощью вы можете делать все сварочные работы». Заклепки прочнее, чем точечная сварка, поэтому в автомобилях с алюминиевым кузовом их нужно меньше. В старом, стальном Range Rover, снятом с производства в 2012 году, использовалось более 6,000 точек сварки, почти вдвое больше, чем количество заклепок, которые скрепляют воедино корпус Range Rover. Однако каждая из заклепок должна быть установлена намного корректнее.
«При разработке технологии сборки кузова, пришлось сделать большую предварительную работу, чтобы понять как работает каждая отдельная заклепка в каждой конкретной позиции, как она будет вести себя и как нужно будет проверять ее установку, чтобы быть уверенным в достижении требуемого качества», — говорит Вайт.
Точные измерения проводятся над каждой заклепкой скрепляющей панели кузова Range Rover. При этом проверяется не только положение заклепки, но и сила, с которой она была забита в алюминий. Некачественные или неверно установленные заклепки могут ослабить кузов и сказаться на качестве и безопасности автомобиля.
Чтобы убедиться в том, что каждый кузов соответствует спецификациям, все измерения по ходу сборки производятся дважды. «Мы имеем ряд камер, которые снимают кузов. Затем фотографии сравниваются с результатами конкретных мастеров и это является измерением. Мы измеряем кузов автомобиля, его ключевые характеристики для каждого отдельного автомобиля.
«Если обнаруживается какя-то поврежденная часть, она тотчас же удаляется, пока процесс не пошел далее. Система сконструирована так, чтобы остановить всю линию. Автомобиль не сможет перейти дальше, пока не будет выяснено, является ли это ошибкой при измерении или это действительно проблема с автомобилем»
Модернизации после 2008 года
Ford продал Jaguar Land Rover индийской Tata Motors в 2008 году. За это время Jaguar Land Rover продолжил улучшение системы и технологии сборки алюминиевых кузовов, разработанной совместно с инженерами Ford в Дирборне.
Например, для внедорожников Range Rover и Range Rover Sport инженеры разработали цельные боковые панели, крупнейшие штампованные детали во всей индустрии в настоящее время. Это позволило ускорить производство.
Land Rover требуется всего 10 часов для сборки алюминиевого кузова каждого Range Rover, и это все еще не настолько быстро, чтобы удовлетворить спрос. Глобальная цель поставленная перед следующим поколением Range Rover-ов, сократить это время до 8-9 часов на кузов. Сокращение количества заклепок и изменение процесса покрытия являются двумя путями для увеличения производства Jaguar Land Rover.
Три смены
Jaguar Land Rover является лидером индустрии по производству автомобилей с алюминиевыми кузовами. В прошлом году компания выпустила 133,000 внедорожников Range Rover, Range Rover Sport и Jaguar XJ, XK и F-Type, все с алюминиевыми монококами или цельными кузовам. Это произошло в рекордный для компании год, когда глобальные продажи превысили 425,000 машин.
Автопроизводитель задействовал для этого три смены. Несмотря на это, дилерам Лендровер некоторых стран приходится ожидать по шесть месяцев, пока заказанный автомобиль не будет поставлен. Конечно можно было бы сделать больше Range Rover-ов и намного быстрее с использованием стали, но как говорит Вайт: «Назад дороги нет».
«То, что мы хотим сделать, это иметь соответствующую технологию, чтобы помочь нашим покупателям получить то, что они хотят. В основном этим обусловлен подобный подход. Внедорожники традиционно тяжелы. Наша цель, сделать их значительно легче, что значительно сократит их расход топлива».
Какие «битые» модели авто лучше не покупать, чтобы не переплачивать за ремонт кузова
14. 08. 2020
При покупке автомобиля большинство стремится выбрать можно крутую модель с набором современных функций. Однако есть определенные моменты, которые следует избегать. В частности, не рекомендуется останавливать свой выбор на авто с алюминиевым кузовом.
Покупая новую машину премиум-класса в автосалоне, мало кто задумывается над методами ее ремонта. Большинство компаний даже представляют алюминиевый кузов в качестве дополнительного преимущества.
Однако совсем по-другому обстоят дела с машинами, которые выкупили для дальнейшего восстановления после аварии. Такие легко можно найти почти на каждом аукционе в США. Ремонт алюминиевых деталей может стать настоящей проблемой для владельца такого автомобиля:
- Алюминиевый сплав рихтуется иначе, чем сталь.
- Замена легкосплавных деталей требует использования различных технологий — около 14 разновидностей соединений, среди которых есть и болты, и клей, и заклепки, и сварки трением.
Итак, рассмотрим наиболее популярные модели авто с алюминиевым кузовом на американских аукционах «битых» машин:
Audi A6 — авто, родом из четвертого поколения седана индекса С7, выпускавшие в течение 2011-2018 годов. Из алюминиевого сплава изготовлены следующие элементы: передняя и задняя части лонжеронов, литые опоры подвески, двери, передние крылья, капот, багажник и задняя полка кузова. Все остальное изготовлено из 2-х сортов стали.
Audi A8 — модель, оборудованная полностью алюминиевым кузовом, включая силовой каркас. Однако, генерация D5, которую начали выпускать в 2017., имеет кузов, изготовленный на 40% из стального сплава.
Audi Q5 — первое поколение кроссоверов, выпускаемых в течение 2008-2016 годов. Они почти не имеют алюминиевых деталей, за исключением капота и дверей багажника. Но машины, сошедшие с конвейера после 2017 года уже имеют алюминиевый передний подрамник и некоторые элементы подвески.
Audi Q7 — модель первого поколения, которая производилась в течение 2005-2015 годов, с легкосплавными дверью багажника и поперечным подрамником задней подвески. Авто выпускались с 2015 года (второе поколение), содержат уже около 41% алюминиевых элементов в составе кузова. В частности, это касается передних и задних лонжеронов, дверей, боковин и тому подобное.
Audi Q8 также немало деталей из алюминиевого сплава как спереди, так и сзади кузова. Некоторые из них цельнолитые, что делает ремонт еще сложнее. Данное осложнение — особенность всех моделей, упомянутых выше.
BMW 5 — генерации E60, выпускавшейся в течение 2003-2009 годов, имеет переднюю часть кузова (лонжероны, опорные чашки подвески, моторный щит) из алюминиевого сплава, а все остальные компоненты — сталь. Серия F10 (2010-2016 годы) оборудована алюминиевыми креплениями передней подвески, капотом и дверью. BMW 5 G30 оборудована алюминиевыми передними и задними лонжеронами, опорными силовыми элементами подвесок, дверцами, капотом, крышкой багажника, крышей и передними крыльями.
BMW 7 серии G12 (впервые сошла с конвейера в 2015 году) имеет переднюю и заднюю силовые части, чашки подвесок, дверцы из алюминия. Однако все остальное изготовлено из стали. В составе отдельных деталей есть даже карбон.
Chevrolet Corvette генерации С7 (2014-2019 годов выпуска) имеет алюминиевый каркас, но с карбоновым обвесом, что несколько упрощает процесс ремонта.
Porsche Panamera (2009-2016 гг.) Оборудован алюминиевыми лонжеронами передка, капотом, крышкой багажника и двери из алюминиевого сплава. Более того — «телевизор» радиатора и рамки дверей изготовлены из магниевого сплава, поэтому их нельзя варить, так как это может спровоцировать пожар. Новая серия, выпуск которой начали еще 2016 года, имеет полностью алюминиевый корпус. Исключение составляют только боковины и детали днища.
Porsche Cayenne — модель второго поколения (2010-2018 годов выпуска) с легкосплавным капотом и внутренними рамками дверей. Серия, которую выпустили с 2018 года, имеет только стальной моторный щит и отдельные силовые элементы днища. Все остальное изготовлено из алюминия. В противоположность этому, Porsche Macan из алюминиевого сплава имеет только капот и крышку багажника.
Tesla model S является самой дорогой моделью Tesla, которая выпускалась с 2012 г.. Ее базу составляет алюминиевая рама. Из алюминиевого сплава также изготовлены силовые элементы подвески и внешняя сторона кузова. Похожую структуру имеет также кузов Tesla model X, которую выпустили в 2016
Tesla model Y — новая модель Tesla, сошла с конвейера в 2020 году. Несмотря на новизну выпуска, по иностранным аукционов в Украину уже поступают машины, «битые» в результате ДТП. Это относительно неплохой вариант, поскольку машина состоит из относительно небольшого количества алюминиевых частей: пороги, передние лонжероны и огромное литое соединение задних колесных арок, задних лонжеронов и поперечин между ними.
Читать также: МВД решило усложнить ввоз автомобилей в Украину
Однако, не стоит считать, что элементы из алюминиевого сплава в составе кузова — приговор. Это совсем не так. Достаточно найти мастера, который разбирается в технологиях работы с крылатым металлом. Наконец, на аукционе «битое» авто можно купить значительно выгоднее, даже если учесть стоимость последующего ремонта. Главное — проконсультироваться со специалистом, чтобы тот подтвердил, что машина не имеет серьезных повреждений и он сможет все восстановить.
Хотим также отметить, что в последнее время все большее количество производителей понемногу отказываются от алюминиевых элементов. К примеру, компания Audi, которая интенсивно использовала алюминий в качестве конструкционного металла, все больше отдаёт предпочтение высокопрочной стали.
Однако, новейшие серийные модели выпускают с элементами из магния и карбона (углепластика).
Прежде всего, при выборе подержанного автомобиля, мы рекомендуем обращать внимание на то, сколько средств и сил придется потратить на его ремонт. Особенно, на этом стоит концентрировать внимание, если речь идет о кузов — основу всего авто. Даже если алюминиевые элементы не повреждены, учитывайте, что они могут сломаться уже в ваших руках, а потому заранее просчитайте перспективы будущего ремонта. Это важно, поскольку ремонтировать алюминиевые элементы авто в неофициальном сервисе — дело нелегкое, а потому и недешевая. Даже не каждый официальная компания в Украине может за это взяться.
Читать также: как осуществить техосмотр автомобиля
Tesla увеличит глобальный спрос на алюминий.
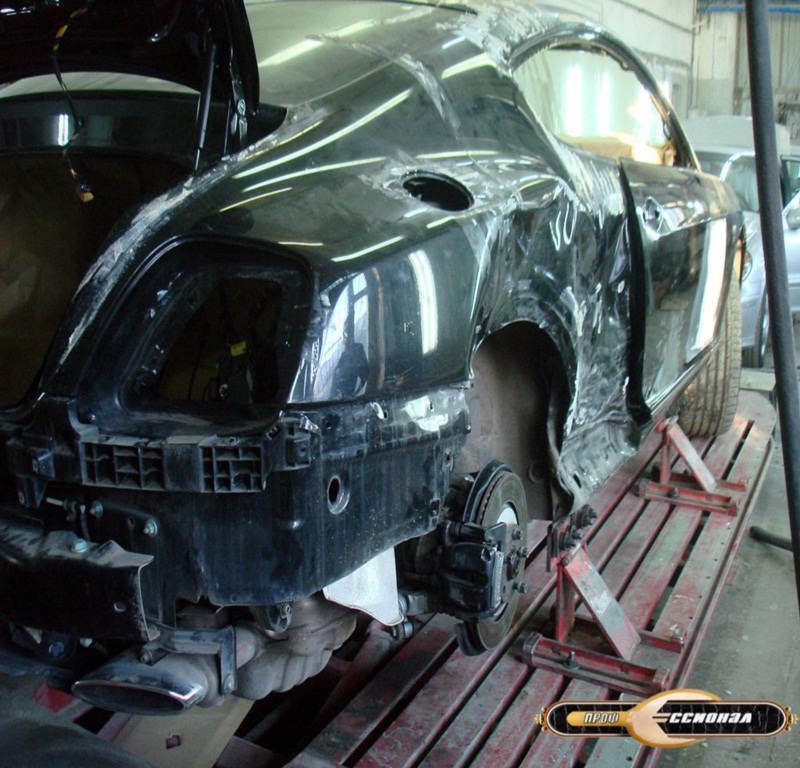
Одним из факторов стремительного роста капитализации Tesla в последние несколько месяцев стало активное расширение производственных мощностей компании, что предполагает существенное увеличение поставок в будущем. Однако есть и другие, на первый взгляд, малозаметные драйверы. Речь идет об увеличении автоматизации и рентабельности производства с одновременным улучшением качества продукции.
Гигафабрика Берлин
В июне 2020 г. Тесла начала строительство Гигафабрики Берлин — своего самого передового завода по производству электрокаров и батарей, первого на территории Европы. Новый завод может заработать уже в 2021 г. и станет площадкой для внедрения новейших технологий в автомобилестроении. В Тесла обещают улучшить сборочный конвейер. Покрасочный цех теперь обеспечит глубину и вариативность окраски автомобиля, чего до сих пор не было ни у одного автопроизводителя. А самое главное — полностью будет переработан кузовной цех.
Литой алюминий вместо стали
Вместо огромного количества сварочных роботов и обслуживающего персонала Тесла поставит гигантские литейные машины — Gigapress, из которых на начальном этапе будут выходить полностью литые алюминиевые задние части Model Y. Производитель обещает в будущем добиться литья практически всей несущей рамы и кузова электрокаров, двигаясь к концепции «машины, которая делает другие машины». Соответствующий патент Tesla подала еще в 2019 г.
Литейный пресс итальянской фирмы IDRA обеспечит выпуск задней части кузова как единого целого, которая заменит предыдущий формат сварки и клепки этой части из 70 стальных деталей. Это существенным образом упростит производство, повысит безопасность и технические характеристики электрокара. Предполагается, что упрощение сборки автомобиля позволит компании сэкономить на рабочей силе.
Преимущества и недостатки
Теперь поговорим об использовании алюминия вместо стали. Алюминий в три раза легче большинства марок стали и не ржавеет. Его вторичная переработка проще и экономичнее. Уменьшение веса и увеличение дальности хода — пожалуй, главный вызов в электромобилестроении.
Последние несколько десятков лет доля алюминия в автомобильном производстве растет, в том числе за счет использования его в конструкции кузова. Тем не менее в среднем на кузов автомобиля приходится не более 20% алюминия. Большее количество, вплоть до 100%, используется преимущественно в спорткарах и некоторых пикапах. Иными словами, большинство выпускаемых автомобилей по-прежнему стальные. Между тем в мире ежегодно выпускается до 100 млн пассажирских и легких коммерческих транспортных средств.
Невысокая популярность этого металла в конструкции кузова обусловлена некоторыми недостатками. Алюминий в 1,5–2 раза менее прочный, чем большинство видов автомобильной стали. Рост его использования тормозится из-за высоких требований безопасности. Однако конструкционные особенности электрокара из-за отсутствия ДВС существенно улучшат этот параметр.
Другая проблема заключалась в скреплении различных частей кузова из алюминия и других видов металла. С появлением литейного пресса и эта проблема будет решена.
Прогнозы по рынку алюминия
Потребление алюминия в мире устойчиво растет с 2009 г. С 2015 до 2020 годы CAGR составляет 2,7%. В 2019 г. потребление алюминия превысило 60 млн тонн. По данным Technavio, среднегодовой рост может ускориться до 5% на горизонте 2019–2023 гг. Предполагалось, что за 4 года прирост потребления мог составить порядка 23 млн тонн. В терминах выручки, по данным Reportlinker, размер рынка алюминия в 2018 г. составил $147 млрд, а к 2026 г. рынок может вырасти до $190 млрд с CAGR 3,2%. Есть и более оптимистичные аналитические оценки. Так, по данным Statista, к 2026 г. рынок может вырасти уже до $250 млрд. С учетом негативного влияния пандемии коронавируса, временной горизонт прогнозов может сдвинуться дальше в будущее, но после восстановления экономики ускорение потребления остается вполне вероятным.
Более 50% использования алюминия приходится на транспортный и строительный сектора. Рост темпов строительства в развивающихся странах и улучшение технологии с переходом на монтаж легких конструкций — все это будет способствовать повышению спроса в соответствующем секторе. Что же касается транспорта, на который в 2019 г. пришлось около 26% спроса, то кроме авиапромышленности высокие темпы прироста может показать использование алюминия в автомобильной отрасли. Около 2/3 потребления алюминия в отрасли приходится на пассажирские автомобили.
Алюминий в автомобильной отрасли
По данным Grand View Research, с 2019 по 2025 гг. рынок алюминия для автомобилестроения покажет среднегодовой рост 8,7%, до $60,5 млрд. Если говорить в терминах выручки, то, по данным за 2018 г., порядка 31% рынка автомобильного алюминия или около 7% всего рынка алюминия ($10,5 млрд) приходилось на конструкцию рамы кузова. Потребление алюминия в этой отрасли может показать опережающий рост с CAGR = 9,3%. Ниже представлена ожидаемая динамика соответствующей отрасли в США.
Литье массивных частей кузова автомобиля из алюминия выглядит перспективной технологией. Можно предположить, что за Tesla по этому пути последуют и другие производители, разгоняя спрос на автомобильный алюминий еще больше.
Кто выиграет от новых технологий, а кто пострадает
Использование литого алюминия в качестве кузова автомобиля поможет улучшить технические характеристики и экономить на процессе сборки электромобиля или авто на ДВС. Если удастся добиться ожидаемой отдачи от новой технологии, выиграть могут первопроходцы в индустрии, в числе которых, конечно, Tesla (TSLA). Из-за относительно невысокого объема выпуска операционная рентабельность производства автомобилей (за вычетом ZEV credits) остается низкой.
Также мы видим высокий потенциал роста спроса на алюминий. Это выгодно таким компаниям, как Rio Tinto, Norsk Hydro, Alcoa, Русал и другим производителям. Акции Русала котируются на Московской Бирже и доступны неквалифицированным инвесторам под тикером RUAL. Акции американской Alcoa доступны на Санкт-Петербургской бирже под тикером AA.
Радикальное увеличение потребления алюминия в автомобильной индустрии приведет к снижению спроса на сталь. Предполагается, что этот процесс будет растянут во времени, влияние на отрасль может оказаться ограниченным. В России основными поставщиками металлургической продукции для автопрома являются ММК и Северсталь, однако тренд на замещение стали алюминием может прийти в страну с большим лагом и касаться только определенного класса автомобилей.
Также можно отметить потенциально негативное влияние на производителей промышленных роботов. К примеру, немецкий производитель KUKA получает примерно 35% выручки от поставок и обслуживания промышленных роботов, в том числе для автоконвейеров. Выручка данного направления стагнирует уже не первый год.
Читайте также: Четыре интересные немецкие акции на Санкт-Петербургской бирже
Пострадать от новых веяний в автомобильном производстве могут компании в странах с сильными позициями профсоюзов. В первую очередь — немецкие и французские производители. Профсоюзы не в восторге от движения рынка в сторону транспорта на полностью электрической тяге, так как конструкция силовой части и трансмиссии автомобиля упрощается, высвобождая существенную часть рабочей силы.
БКС Брокер
Самые прочные и неубиваемые автомобили мира
Прочность четырёхколёсного друга для автомобилиста ассоциируется с безопасностью и надёжностью. Поэтому вопрос износостойкости, долговечности авто – один из основных при его выборе. Ведь такие машины редко ломаются, меньше тратится средств на ремонт, да и ощущать себя в безопасности за рулём – тоже важно. Неуязвимость стального коня – качество обязательное в принципе. Попробуем в данной статье охарактеризовать самые неубиваемые автомобили мира.
Параметры надёжности автомобиляВ понятие «надёжность» вкладывают совокупность качеств автомобиля:
- Безотказность в эксплуатации.
Параметр, который говорит о способности машины служить определённый срок, не нуждаясь в ремонте.
- Долговечность использования. Отвечает за абсолютный срок эксплуатации автомобиля. Рассматриваются машины, которые получали регулярное техническое обслуживание.
- Ремонтопригодность. Возможность восстановить состояние автомобиля путём починки мелких и крупных неполадок.
- Работоспособность. Соответствие реального срока эксплуатации данным, указанным в документации.
В результате изучения 8,5 млн автомобилей 26 различных марок был составлен рейтинг прочности и безопасности машин выпуска не ранее 2015 г.
На первом месте оказался Mercedes SLK. Это родстер небольшой длины от компании, производящей престижные автомобили Mercedes-Benz. Модель, обладающая спортивным характером и просто модель, созданная для удовольствия. Кузов состоит из металла, но не полностью, капот с передними крыльями производитель сделал из алюминия чтобы хоть чуть-чуть сократить расход топлива и улучшить динамические показатели. Крыша изготовлена из пластика, это также уменьшило вес автомобиля, но и сократило время открывания и закрывания крыши. Фары линзованные и оснащены омывателем. Большая радиаторная решётка обладает огромным логотипом, который соединён с хромированной горизонтальной перемычкой. На бампере присутствуют дневные светодиодные ходовые огни. Задний бампер по сути своей прост, под ним находится два огромных патрубка системы выпуска.
Покупатели чаще всего предпочитали 350 версию, но больше хотели 55 AMG. 350-я оборудовалась мотором M276 BlueDIRECT, у которого головки блока получили развал 60 градусов и соответственно вал уравновешивания. Атмосферный V6 выдаёт 306 лошадей, что позволяет кабриолету стартовать до сотни за 5,6 секунды. Минимальный расход в 10 литров обеспечен, по факту он больше. В авто всего два посадочных места, это прекрасные спортивные кожаные кресла с электрорегулировками и отличной боковой поддержкой. Сидеть достаточно удобно, места не так много, но его хватает. Родстер быстрый, красивый и комфортный. Но главное – он надёжный!
Вторую позицию занимает Audi A6. Спортивно изысканная, она отличается инновационными технологиями, широчайшим ассортиментом оборудования, комфортом и прогрессивным дизайном. Автомобиль оснащён мощным турбодизельным двигателем, обеспечивающим уверенный разгон до 100 км/ч всего за 8,2 секунды. Яркий дизайн интерьера достигается за счёт комбинированной обивки Twin Leather, а технологическое оснащение включает регулируемое кресло с электроприводом и функцией памяти, а также информационную систему водителя с цветным TFT дисплеем.
На третьей строчке рейтинга Mercedes GLК (Gelandewagen Luxus Kompaktklasse), люксовый компактный кроссовер немецкой торговой марки Mercedes-Benz, основанный на универсале S204 C-класса. GLK оборудуется бензиновыми и дизельными двигателями. Бензиновые имеют конфигурацию V6 и объём 3 и 3,5 литра. Производит впечатление солидного, хищного и хорошо приспособленного для бездорожья. Всё благодаря широким крыльям и угловатым формам, напоминающим легендарный Гелендваген. Производитель предусмотрел даже Off-Road пакет, который включает в себя несколько дополнений: усиленный передний бампер, защиту двигателя и пластиковые накладки, прикрывающие нижнюю часть кузова. Кроме того, можно изменить характер автомобиля. Рулевое управление становится более раскованным, а реакции на газ – флегматичными. Всё это должно помочь неопытному водителю в преодолении сложных участков. Авто в базовых версиях комплектовался 17-дюймовыми колесными дисками. Спортивный пакет подразумевал 19-дюймовые колеса. Передняя панель выполнена в классическом стиле. Здесь напрасно искать современные формы или дизайнерские изыски. Прямые линии и неуклюжие контуры дают ощущение надежности. Некоторые детали позаимствованы в Мерседес С-класса. В целом, рабочее место водителя хорошо продумано, а приборы легко читаемы. Рулевое колесо, обшитое кожей, можно регулировать в двух плоскостях в достаточно широком диапазоне.
Четвёртое и пятое место делят Porsche 911 и BMW Z4. Первый – знаменитый спорткар, который оставляет на светофоре большинство автомобилей. Базовая версия разгоняется до 100 км/ч всего за 5 секунд, а самый быстрый Порше 911 делает это за время чуть более трёх секунд. Даже самые слабые двигатели позволяют достичь максимальной скорости 280 км/ч, а топовые версии – 320-330 км/ч. Привод в зависимости от модификации может быть как задним, так и полным. На выбор предлагаются три коробки передач: 6-ступенчатая механическая, 5-ступенчатая автоматическая и 7-ступенчатая автоматизированная с двойным сцеплением PDK. На передней оси стойки Макферсон, а на задней система независимых рычагов. На что нужно обратить внимание, – прежде всего, на состояние сцепления и приводных валов. Не отличаются прочностью рулевые наконечники и тяги, но это несерьёзные дефекты. Так же внимательно необходимо исследовать двигатель и трансмиссию на предмет подтеканий, особенно вокруг главной оси RMS (задний сальник коленвала). Кроме того, встречаются утечки масла через масло-охладитель (ослабевает крепление) и проблемы с системой охлаждения (растрескивание патрубков и выход из строя помпы).
BMW Z4 – первый в истории автоконцерна заднеприводный автомобиль. Жёсткая складная крыша двухместного родстера появилась в 2009-м г. Трёхлитровая рядная шестерка М54 – визитная карточка BMW. Она имеет электронную дроссельную заслонку, алюминиевый блок и управляемые фазы газораспределения на обоих распределительных валах. Слабое место – система вентиляции картерных газов. Авто уверенно стартует с места под мощным напором 231-сильного двигателя. Автоматическая коробка аккуратно перебирает передачи, отдавая тягу на заднюю ось. С подвеской возникают проблемы: быстро изнашиваются поперечные рычаги и рулевые тяги. Существует усиленная версия подвески Meyle. BMW Z4 – доступное удовольствие. Сравнительно надёжный, он доставляет немного проблем, хорошо оснащён и красив, как породистый жеребец.
Шестая строчка принадлежит Mercedes E-Klasse C, который с удивительной лёгкостью воплощает в себе современный стиль и утончённую спортивность. Каждая линия следует принципу чувственного лаконизма. Наряду с базовой комплектацией есть три линии исполнения, а также широкий выбор благородных расцветок и материалов позволят автовладельцу индивидуально оформить свой автомобиль. Концепция, которая делает каждую поездку на автомобиле «Мерседес-Бенц» безопасной и уникальной, называется Mercedes-Benz Intelligent Drive. Время, которое водитель проводит за рулём автомобиля, не должно проходить впустую. Это время для отдыха. Время для восстановления сил. Автомобиль надёжно и с комфортом доставляет до места назначения. Соблюдает дистанцию. Активная система экстренного торможения с функцией поддержки при проезде перекрестков предотвращает наезды и помогает избежать столкновений с пересекающими дорогу пешеходами, а также снизить тяжесть аварии.
На седьмом месте Audi Q5 – компактный кроссовер, выпускаемый AUDI AG с ноября 2008 г. Строгий, стильный, функциональный. Всё под рукой. Несмотря на то, что собираются Ауди уже не в Германии, а в Мексике, инженеры концерна гарантируют, что качество не пострадает. В авто широко использован алюминий вкупе с высокопрочными марками стали. Такое сочетание дало возможность уменьшить снаряжённую массу на 90 кг, а значит снизился и расход топлива. Из приятного – возле подлокотника есть место для индукционной (бесконтактной) зарядки смартфонов. Диван оснащён массой регулировок, как подушек, так и спинок. Привод у Audi Q5 – только полный.
На восьмой строчке оказались сразу три модели – Audi A3, Ford Focus и Mercedes C-Klasse. Первое авто оснащается бензиновыми моторами и предлагается с кузовами пятидверный хэтчбек или седан. Базовая версия хэтчбека Audi A3 имеет под капотом двигатель 1.4 TFSI мощностью 150 л. с. Удобен настолько, что в нём можно жить. Ford Focus отличают сегодня новый рельефный кузов и роскошный салон, оснащённый новейшими технологиями. Этот автомобиль является самым эффектным за всю историю модели. Кузов доступен в трёх вариантах хэтчбек, универсал и седан. Бензиновый двигатель являет собой технологичный сплав экономичности и мощности. Его объём 1,5 литра, что позволяет снизить время разгона, расход топлива и объём вредных выбросов. Доступен вариант мощностью 150 л. с. с 6-ступенчатой автоматической коробкой передач. Технология Active City Stop помогает избежать столкновений при движении в плотном городском потоке. За эту технологию Ford удостоилась награды за безопасность Euro NCAP Advanced Reward.
Mercedes C-Klasse впечатляет высоким комфортом, превосходным качеством отделки и техническими инновациями. При желании элегантность, динамику и эффективность можно ещё усилить. Комбинация пакета динамики движения AIRMATIC и 7-ступенчатой АКП 7G-TRONIC обеспечивает максимальный диапазон ходовых качеств – от комфортных до спортивных. Таким образом, седан C-Класса по желанию может превратиться в солидный автомобиль для дальних поездок, защищающий находящихся в нём людей от любых потрясений или в динамичного спортсмена с острым рулевым управлением и жёсткой подвеской, способным привести в восхищение самых амбициозных водителей.
Девятое место рейтинга получила Mazda 2 – субкомпактная «японка», имеет небольшой рельефный капот, небольшую радиаторную решётку, которая отличается хромированной окантовкой, есть крупная оптика с галогенной и светодиодной начинкой. Авто выглядит агрессивно. Форма очень аэродинамична. Задний бампер имеет большую пластиковую вставку, на котором в свою очередь находятся светоотражатели. Водительское место эргономичное, водителю достанется трёхспицевый руль, на котором имеются кнопки управления мультимедийной системой. Панель приборов Mazda 2 – это большой аналоговый тахометр посередине, в который встроен электронный спидометр. Слева и справа находятся бортовые компьютеры, на которых отображается остальная полезная информация об авто. В комплекте четыре подушки безопасности.
Замыкает список Volvo XC60 – это новое поколение легендарного кроссовера родом из Швеции. Там, где яркий дизайн сочетается с элегантным интерьером. Там, где технологии призваны помогать людям. Где каждая поездка – истинное наслаждение. Удлинённый капот сочетается с массивными колёсными арками и укороченными свесами, что всё вместе создаёт невероятное ощущение благородной силы. Внутри натуральное дерево в сочетании с искусно обработанным металлом превращают интерьер в изящно оформленный салон. Удобный интуитивный дисплей. XC60 можно назвать самым безопасным автомобилем во всех категориях. Безопасность в автомобиле Volvo – это тщательно продуманное и выверенное решение. Целостный подход был в основе философии Volvo с самых первых дней работы, таким он остаётся и по сегодняшний день.
Сегодня детище южноафриканской компании Paramount Group под названием Marauder считается самым прочным автомобилем в мире. Изначально эта машина создавалась под специализированные военные задачи: для сопровождения и защиты колонн и групповых перевозок бойцов. В результате Marauder получил множество особенностей. Он умеет плавать и способен переехать и раздавить любую легковушку, которая встретится на пути. «Детка» снабжена противовзрывными креслами, устойчива к взрывам, колёса сделаны с применением пуленепробиваемых материалов. Весит этот броневик 15 тонн, при этом перевезти способен 18 тонн груза со скоростью до 120 км/ч. Его длина более 6 метров, высота 2,5 м, ширина – 2,7 м. Двигатель имеет мощность 300 лошадиных сил. Внутри Marauder размещаются 10 пассажиров. Самый прочный автомобиль в мире устоит при миномётном обстреле и не испугается ракетных ударов. Кирпичная стена для этого «мальца» словно из картона – протаранит, завалит и глазом не моргнёт. Фугасный взрыв способен причинить автотанку только небольшие повреждения корпуса – отряхнётся и уверенно поедет дальше. Бронированный монстр сегодня находится в свободном доступе и купить его может каждый, у кого есть лишние $ 500 тыс. В абсолютном рейтинге безопасности эта машина вне конкуренции.
Однако обычный человек, не воюя и не проживая в местах под названием «горячие точки», в подобном авто не нуждается. Поэтому перейдём к легковым автомобилям повседневного использования.
Лучшим транспортным средством в A-классе является Scion xD. Автомобиль пришёл на смену xA – предшественник оказался чересчур тесным. Габариты новой модели составили 3,93 метра в длину и 1,725 – в ширину. Вес xD оказался на 130 килограммов больше, но на динамичности автомобиля это не сказалось.
Машина оснащается двигателем объёмом 1,8 литра и мощностью 128 лошадиных сил. Комплектуется пятиступенчатой механической или четырёхступенчатой автоматической коробкой передач. Тормоза дополнены антиблокировочной системой. Допускается установка систем стабилизации и предотвращения буксования. Автомобиль также оснащается кондиционером, электропакетом и медиасистемой. Все узлы и техника, а также кузов имеют высокое качество, которое служит дольше любого аналога в классе.
Самое надёжное субкомпактное автоВ классе транспортных средств, занимающем нишу между компактными и средними автомобилями, лучшим представителем является Toyota Corolla. О надёжности автомобиля говорит его распространение – он является самым продаваемым не только в сегменте, но и в мире.
Актуальная версия выпущена в 2013 г. – одиннадцатое поколение классической серии. Внешний вид модели изменился как в плане дизайна, так и габаритов. Интерьер также изменился, но по-прежнему имеет спокойный стиль.
Наилучшим двигателем является 1,8-литровый мощностью 140 л. с. Он дополняется ASR, ESP, антиблокировочной и прочими системами. Доступен также климат-контроль, электропакет и парктроник.
Лучший «европеец» среднего классаВ роли лучшего полноразмерного седана выступает Chevrolet Malibu. Транспортное средство относится к сегменту бизнес-моделей. Последнее поколение имеет обновлённые экстерьер и интерьер, сохраняющие корпоративные черты. В салоне инженеры и дизайнеры создали комфортабельную и эргономичную атмосферу. Единственный двигатель, которым оснащается Малибу – 2,4-литровый агрегат мощностью 167 лошадиных сил. Он дополняется АКПП. В комплектациях можно встретить 6 подушек безопасности, подогрев сидений и электропакет.
В категории дорогостоящих люксовых моделей первое место занимает Mercedes E. Несмотря на то, что автомобиль E-класса отстаёт S в престижности, многие его эксплуатационные свойства, в том числе надёжность, позволили обойти люкс. Кроме того, изменение в дизайне в последнем поколении сделало бизнес-седан ещё более внушительным. В комплектациях автомобиля доступно богатое оснащение – медиасистема с двумя мониторами, адаптивный круиз-контроль, ассистент смены полосы и система предотвращения столкновения с машиной со встречной полосы. Также за дополнительную плату можно получить пневматическую многокамерную подвеску.
Самый стойкий спортивный автомобильСкоростной сегмент в списке представляет Chevrolet Camaro. Последнее, пятое поколение маслкара вышло в 2009 г. Новые автомобили сочетают в дизайне как черты ранних поколений, так и новые линии. В 2013 г. Камаро подлежал рестайлингу, что сделало внешний вид более приближенным к «классике».
Самый надёжный спорткар в классе оснащается восьмицилиндровым двигателем объёмом 6,2 литра и мощностью 405 лошадиных сил, трансмиссией с задним приводом и шестиступенчатой автоматической коробкой передач, системами стабилизации и антиблокировочной. Кроме того, автомобиль имеет климат-контроль, 6 подушек безопасности и встроенный компьютер.
Самый надёжный полноразмерный внедорожникЛучшим джипом в списке является GMC Yukon. Последнее поколение автомобиля вышло в 2006 г. Оно включает в себя весь функционал предыдущей версии: система поддержания устойчивости (в неё входят антиблокировочная и пробуксовочная системы и прочее). Система полного привода может быть настроена, распределяя усилия между осями – можно перенести 100% мощности на одну из них.
Среди нового оснащения самого надёжного кроссовера следует отметить двигатель. Он имеет объём 8,1 литра, восемь цилиндров и мощность 320 лошадиных сил. Доступен мотор в «тяжёлой» версии – Yukon XL 2500. В салоне автомобиля покупатель найдёт климат- и круиз-контроль, электропакет и кожаные сидения с подогревом.
Если у вас ещё нет международного водительского удостоверения, вы можете легко и быстро оформить его на нашем сайте. С международным водительским удостоверением вы сможете брать самый надёжный и безопасный автомобиль в аренду!
15 Automotive Aluminium Warriors — Motor Trend
Ford F-150 2015 доминировал в заголовках газет благодаря своему новому алюминиевому кузову, первому в сегменте полноразмерных грузовиков. Самый продаваемый грузовик Америки присоединяется к элитной группе суперкаров и шикарных роскошных седанов, в которых используется алюминиевая конструкция для снижения веса, но при этом они обладают силой, чтобы конкурировать со стальными аналогами.
Acura NSX
Посмотреть все 16 фотографий Acura NSX первого поколения, представленная в 1990 году, была невероятно сбалансированной и легкой благодаря полностью алюминиевому кузову. Его преемник, Acura NSX 2016 года, будет в основном из алюминия, с добавлением современных композитных материалов для пола и крыльев.
Jaguar F-Type
Посмотреть все 16 фотоJaguar не скупился на создание этой дерзкой британской бомбы. F-Type наделен мощными двигателями с наддувом, заключенными в легкий алюминиевый корпус, который великолепно смотрится как в купе, так и в форме родстера.
Посмотреть все 16 фотографийОколо 90 процентов круизеров Benz с вертикальным расположением кузова изготовлено из алюминия, при этом сталь составляет важные структурные элементы, такие как передняя стойка и крыша.Mercedes использует довольно передовые методы строительства, такие как кокильное литье и сварка трением с перемешиванием, и в конечном результате снижена собственная масса более чем на 200 фунтов по сравнению с предшественником.
Audi A8
Посмотреть все 16 фотографий Audi A8 был одним из первых крупных флагманских седанов с алюминиевым кузовом, и это заметно по его снаряженной массе. Например, A8 L 4.0T весит 4600 фунтов, что делает его примерно на 300 и 200 фунтов легче, чем сопоставимые Mercedes-Benz S-Class и BMW 7 Series соответственно.
Land Rover Range Rover
Посмотреть все 16 фотоОдин из самых больших люксовых внедорожников, доступных сегодня, сел на большую диету, когда в 2013 году перешел на алюминиевый цельный кузов. Несмотря на большие габариты, Land Rover Range Rover (и его более спортивный собрат, Range Rover Sport, изображенный здесь) кажется более спортивным, чем его предшественник, при этом сохраняя знаменитые внедорожные способности Land Rover.
Посмотреть все 16 фотоF12 Berlinetta — последняя модель от Prancing Horse с алюминиевым кузовом, вслед за Ferrari 458 Italia, FF и California T.Высокотехнологичный LaFerrari с гибридным двигателем получил еще более легкий и прочный корпус из углеродного волокна.
Просмотреть все 16 фотографий Нынешний XJ представляет собой радикальную эволюцию флагманского седана Jaguar с точки зрения стиля и характеристик. Большая часть его удивительно спортивного характера обусловлена алюминиевым корпусом, что делает его относительно легким для седана с общей длиной более 200 дюймов. Более того, алюминиевая конструкция XJ просочилась в новый компактный седан XE, который должен сразиться с грозным BMW 3 серии в начале 2016 года.
Audi R8
Посмотреть все 16 фотографийКогда полностью алюминиевый Audi R8 впервые был выпущен в 2008 году, он сразу же стал хитом благодаря выдающемуся стилю и линейке двигателей, включающих в себя приятный по звучанию V-10. Audi уменьшила вес модели второго поколения за счет комбинации алюминия и нескольких композитных панелей.
Tesla Model S
Посмотреть все 16 фото Сборочный завод Tesla Motors в Северной Калифорнии заставлен огромными роботами, которые режут, штампуют и сваривают алюминиевый корпус, в котором находится усовершенствованный электрический силовой агрегат седана Model S.Предстоящий кроссовер Model X появится в выставочных залах с алюминиевым кузовом, дверями типа «сокол» и обновленной версией двухмоторного силового агрегата Model S.
Ford F-150 не новичок в инновациях, и его новый алюминиевый корпус является убедительным доказательством этого. Его снаряженная масса на 700 фунтов легче, чем у модели последнего поколения, и Ford уверен, что грузовик останется таким же долговечным, как и прежде.
Посмотреть все 16 фотографийБлагодаря мощному двигателю V-12 мощностью 510 л.с. и тонкому алюминиевому корпусу Aston Martin DB9 по сути является футбольным бегуном в строгом льняном костюме.Другие Aston также имеют алюминиевые корпуса, в том числе Vantage и Rapide.
Посмотреть все 16 фотографийВ рамках подготовки к выпуску нового Corvette Stingray компания Chevrolet внесла значительные улучшения в сборочный завод в Боулинг-Грин, штат Кентукки, чтобы произвести алюминиевую раму спортивного автомобиля. Легкая, но прочная рама служит основой для шасси и двигателей C7 Corvette, которые продолжают впечатлять на трассе.
Посмотреть все 16 фотоЛегкость была заложена в ДНК Lotus с момента ее создания, поэтому неудивительно, что Evora начинает жизнь с алюминиевой рамы.После короткого отпуска в США Evora вернется в 2016 модельном году с рядом улучшений, включая еще более легкое алюминиевое шасси.
Lamborghini Huracan
Посмотреть все 16 фотоLamborghini Huracan тесно связан со своим немецким братом Audi R8 второго поколения. В дополнение к великолепному V-10, обе машины получили модное и легкое шасси, состоящее в основном из алюминия и нескольких деталей из углеродного композита.
Mercedes-AMG GT S
Посмотреть все 16 фотоНа замену всеми любимому Mercedes-Benz SLS AMG GT придет Mercedes-AMG GT S. будет иметь энергичный твин-турбо V-8 и легкий алюминиевый корпус для снижения веса.
Автомобильный алюминий в легковых и грузовых автомобилях
Быстрое чтение
Алюминий делает автомобиль лучше. Использование алюминия в автомобилях и грузовых автомобилях ускоряется, поскольку он предлагает самый быстрый, безопасный, экологически чистый и экономичный способ повышения производительности, экономии топлива и сокращения выбросов при сохранении или повышении безопасности и долговечности.От автомобилей массового потребления, таких как Ford F-150, до роскошных автомобилей, таких как Audi, Mercedes Benz и Land Rover, алюминий все чаще становится «материалом выбора» для автопроизводителей благодаря своей прочности и экологическим преимуществам. Группа по транспортировке алюминия (ATG) Алюминиевой ассоциации сообщает о преимуществах алюминия при транспортировке через исследовательские программы и связанные с ними информационные мероприятия. Для получения дополнительной информации о том, как алюминий управляет автомобилями сегодняшнего и завтрашнего дня, посетите сайт www.drivealuminium.орг.
Полезные факты
- Постоянный рост использования автомобильной промышленности
Использование автомобильного алюминия непрерывно растет на протяжении 40 лет. В настоящее время алюминий уступает только стали как наиболее часто используемый материал в транспортных средствах. - Переработано на рекордном уровне
В конце срока службы автомобиля почти 90 процентов алюминия в среднем перерабатывается. - Энергоэффективность
По сравнению с парком традиционных стальных автомобилей, использование алюминия позволяет сэкономить 108 миллионов баррелей сырой нефти в виде энергии. - Безопаснее
Фунт за фунт, алюминий поглощает в два раза больше энергии удара, чем низкоуглеродистая сталь. Могут быть спроектированы более крупные зоны раздавливания без соответствующего снижения веса.
Повышение производительности
Поскольку алюминий легче, он позволяет автопроизводителям увеличить сопротивление вмятинам — они могут сделать панели кузова толще, при этом снизив вес. А автомобиль с меньшей массой имеет лучшее ускорение, лучшее торможение и лучшую управляемость. Кроме того, более легкие автомобили могут перевозить и буксировать больше, поскольку двигатель не несет лишнего веса.
Преимущества веса, прочности и безопасности
Применение алюминия для оптимизации конструкции автомобильного кузова позволяет снизить вес до 50 процентов по сравнению с традиционной конструкцией из низкоуглеродистой стали. Алюминиевые конструкции кузова по прочности не уступают стальным и поглощают вдвое больше энергии при столкновении. Снижение веса основной конструкции также позволяет уменьшить размеры других систем автомобиля (включая двигатель, трансмиссию, подвеску и колеса). Во всех отношениях преимущества алюминия по весу, прочности и безопасности очевидны.
Экологические преимущества
Почти 90 процентов автомобильного алюминиевого лома — более полумиллиона тонн в год — рекуперируются и перерабатываются. Для сравнения: переработка 1 тонны алюминия позволяет сэкономить 21 баррель нефти в энергетическом эквиваленте. Экологические победы продолжаются: рецензируемое исследование, проведенное Национальной лабораторией Ок-Ридж при Министерстве энергетики, показало, что автомобиль с интенсивным использованием алюминия может снизить общее потребление энергии в течение всего жизненного цикла на 20 процентов и выбросы CO2 на 17 процентов. .
В ожидании: гонка за топливной экономичностьюПотребители все чаще требуют более экономичные автомобили. Учитывая это наряду с новыми правилами экономии топлива, которые потребуют от автомобильного парка США к 2025 году в среднем 54,5 миль на галлон, автомобильная промышленность реагирует на это. Один из примеров: пикап Ford F-150 с полностью алюминиевым кузовом. Этот переход к алюминию имеет серьезные последствия: Ford F-150 — самый популярный автомобиль любого типа в Соединенных Штатах и одна из самых прибыльных автомобильных линий в мире.Грузовик F-150 2015 похудел на 700 фунтов (примерно 15 процентов от веса автомобиля) благодаря высокопрочному полностью алюминиевому кузову военного класса. Это снижение веса позволяет грузовикам Ford ехать дальше на галлоне бензина и открывает двери для других изменений, таких как двигатели меньшего размера, которые могут еще больше повысить экономию топлива.
История алюминия в автомобиляхСегодня растущий рынок, алюминий с самого начала был ключевым материалом для автопроизводителей. Первый спортивный автомобиль с алюминиевым кузовом был представлен на Берлинском международном автосалоне в 1899 году.Два года спустя Карл Бенц разработал первый двигатель с алюминиевыми деталями. После Второй мировой войны алюминий стал достаточно дешевым, чтобы его можно было использовать в серийных автомобилях. Прорыв произошел в 1961 году, когда британская компания Land Rover выпустила блоки двигателей V-8 с алюминиевыми цилиндрами. Оттуда алюминиевые автомобильные детали закрепились в колесах и картерах трансмиссии, а затем переместились в головки цилиндров и шарниры подвески. Этот металл, пригодный для бесконечной переработки, в настоящее время является ведущим материалом для использования в трансмиссиях и колесах, и продолжает завоевывать долю рынка капотов, багажников, дверей и бамперов, а также целых конструкций транспортных средств.
Интересный факт: четкий выбор автопроизводителей
В 2013 году президент и главный исполнительный директор Ford Алан Мулалли восхвалял автомобильный алюминий в ряде интервью СМИ, посвященных анонсу нового грузовика F-150. Среди других комментариев, сказал Мулалли, «фунт за фунт, алюминий прочнее и жестче, чем сталь» и «[алюминий] будет предпочтительным материалом» для продвижения вперед Ford.
Для получения дополнительной информации об использовании алюминия в автомобильной промышленности: www.drivealuminium.org.
Обозначение сплава | Характеристики | Использование в автомобилях | ||
---|---|---|---|---|
AA | UACJ | |||
1000 Al | 1050 | A50 | Превосходная технологичность и обрабатываемость поверхности. Самый устойчивый к коррозии из всех алюминиевых сплавов. | Теплоизоляторы |
1100 | A30 | Алюминий общего назначения чистотой более 99,0%. Поверхность после анодирования выглядит слегка белой. | Теплоизоляторы, номерные знаки | |
1200 | A0 | Теплоизоляторы | ||
2000 Al-Cu | 2014 | 14S | Для конструктивных элементов используется очень прочный сплав. Из-за относительно более высокого содержания меди низкая коррозионная стойкость. | Ручки для мотоциклов, ABS |
2017 | 17S | Амортизаторы, ручки, спицы, шатуны | ||
2024 | 24С | |||
2219 | B19S | Высокая прочность, отличные свойства при высоких и низких температурах, превосходная свариваемость, но низкая коррозионная стойкость. | Роторы, детали тормоза | |
CG29 | Более высокая прочность при повышенных температурах, чем у 2618. | Шатуны поршневые | ||
CB156 CB256 KS26 | Бессвинцовые легкообрабатываемые сплавы. | AT клапаны | ||
2618 | 2618 | Высокая прочность при высоких температурах. Подходит для ковки и механической обработки. | Колеса компрессора, поршни | |
20A1 | ||||
3000 Al-Mn | 3003 | 303S D3S | на 10% сильнее, чем 1100. Хорошая технологичность и устойчивость к коррозии. | Трубопровод |
3004 | 304S 4S | Прочнее, чем 3003. Отличная способность к глубокой вытяжке и хорошая коррозионная стойкость. | Решетки капота, теплоизоляторы | |
4000 Al-Si | 4032 | 32S | Превосходная термостойкость и стойкость к истиранию. Низкий коэффициент теплового расширения. | Поршни |
SC100 | Превосходная стойкость к истиранию и ковкость.Сильнее 4032. | Корпус гидроусилителя руля, спиральные компрессоры, толкатели клапанов | ||
SC300 | Более сильная версия SC100. | |||
TF06B TF08 TF10B | Превосходная стойкость к истиранию и ковкость. Сильнее 4032. | |||
TF12B | Заэвтектический сплав с повышенной ковкостью. | Роторы компрессора | ||
5000 Al-Mg | 5052 | 52S | Сплав средней прочности.Хорошая коррозионная стойкость и формуемость . Высокая усталостная прочность. | Панели индикации счетчиков, барабаны АКПП, надувные устройства надувных подушек безопасности, крышки |
5454 | D54S | на 20% прочнее, чем 5052. Хорошая коррозионная стойкость. | Колесные диски, детали подвески | |
5083 | 183S | Сплав для использования в сварных конструкциях. Самый прочный из сплавов без термической обработки. | Цистерны, газовые баллоны | |
383S | Версия 183S с высокой формуемостью. Превосходные сверхпластические свойства. | |||
483S NP5 / 6 | Версия 183S из экструдированного сплава. | Крепежные шины | ||
5182 | A82S | Примерно такой же прочный, как 5083. Хорошая обрабатываемость и устойчивость к коррозии. | Пылезащитные чехлы, рамы сидений, кожухи воздухоочистителя, пружинных листов | |
GM145 | Хорошая формуемость и устойчивость к коррозионному растрескиванию под напряжением. | Кузовные панели (внутренние) | ||
5154 | A154S | на 20% сильнее, чем 5052. Хорошая формуемость. | Колеса, детали днища, детали трансмиссии, детали подвески | |
A254S | на 20% прочнее, чем 5052. Хорошие характеристики коррозионного растрескивания под напряжением. | |||
GC32 | Хорошая формуемость и устойчивость к коррозионному растрескиванию под напряжением. | |||
5022 | GC45 | Высокопрочный, легко поддающийся формованию материал панели кузова. Снижение стойкости к спеканию покрытия. | Капоты, крыши, двери, стойки, масляные поддоны, полы, задние крылья, кожухи воздухоочистителя | |
GC150 | Сплав немного прочнее, чем GC45. | Кузовные панели | ||
5110A | 257S | Сплав высокой яркости с такой же прочностью, что и 3003. Хорошая способность к глубокой вытяжке и коррозионная стойкость. | Молдинги, накладки, светоотражающие панели, плафоны для ламп фар | |
5056 | 356S | Нетермообрабатываемый сплав для сварных конструкций. Отличная стойкость к морской воде. | Тормозные поршни, топливопроводы, надувные устройства подушек безопасности | |
6000 Al-Mg-Si | SG712 TM30 | Корпус панели из сплава с высокой способностью к прокаливанию, формуем и высокой подгибаемостью. | Капоты, задние крылья, передние крылья, стойки, колесные арки, крыша, двери | |
TM66 | Корпус из сплава типа BH. Даже сильнее, чем SG112, с хорошей формуемостью. | |||
6061 | 61S 161S | Термообрабатываемые сплавы с хорошей коррозионной стойкостью. | ABS, поперечины, колеса, карданные валы, рычаги, звенья, подушки безопасности, балки, ресиверы | |
561S | Рамы электростанции | |||
6013 | SG210 | Высокопрочный алюминиевый сплав для ковки. | Рычаги подвески | |
6063 | 63S 163S Y63 | Типичные экструзионные сплавы.Прочность ниже, чем у 6061, , но превосходные экструзионные свойства. | Молдинги, каркасы сидений, ворота кузовов грузовиков, перила , трубопроводы | |
6005C | 465S L55 | Промежуточная прочность между 6061 и 6063. Хорошая коррозионная стойкость и свариваемость. | Бамперы, проставки, кронштейны двигателя, каркасы сидений , АБС, пороги, амортизаторы | |
SG109 | Высокопрочный сплав с хорошей изгибаемостью и устойчивостью к коррозии .Возможна полая экструзия. | Усилитель бампера, проставки | ||
SG10 SG310 | Самый прочный из сплавов серии 6000. | Колеса, карданные валы, рычаги, звенья | ||
GT209 KS69S | Бессвинцовый сплав с высокой обрабатываемостью. | AT клапаны | ||
7000 Al-Zn-Mg | 7075 | 75S | Типичный высокопрочный сплав для использования в авиастроении. | Петли, звенья, шпульки, втягивающие ремни ремня безопасности |
7178 | A78S | Самый прочный алюминиевый сплав. | Ключи | |
7003 | ZK60 K73 | Экструзионный сплав для сварных конструкций. Лучше экструзионные свойства, чем у 7204. | Усилитель бампера, ползунки сидений, рамы мотоциклов , ударные балки дверей, диски для мотоциклов | |
7204 | ZK141 K70 | Сплавы для сварных конструкций.Прочность сварной детали восстанавливается почти до такой же, как у исходного материала в результате естественного старения. | Элементы рулевого управления, поперечины, педали тормоза | |
7204 | ZK147 K70Y | Домкраты | ||
ZK55 | Прочнее, чем 7204. Возможна сварка и экструзия полых частей. | Усилитель бампера, противоударные балки, рамы и диски мотоциклов | ||
7046 | ZK170 | |||
7050 | ZG62 | Высокопрочные алюминиевые сплавы. | Передняя вилка мотоцикла | |
ZC88 |
Может ли алюминий быть экономичной альтернативой стали?
Автомобильные кузова: может ли алюминий быть экономичной альтернативой стали?Автомобильные материалы: экономика Аниш Келкар, Ричард Рот и Джоэл Кларк
Хотя использование алюминия в автомобилях увеличивается в за последние два десятилетия прогресс в разработке алюминиевых автомобильных тела.Фактически, большая часть замены алюминия пришла в виде отливок. и поковки в трансмиссии, колесах и т. д. Производители автомобилей разработали полностью алюминиевые автомобили с двумя конкурирующими конструкциями: обычным цельным кузовом и пространственной рамой. Однако алюминий — далеко не лучший выбор для кузовов автомобилей. В замена стали на алюминий частично зависит от нормативных требований для соответствия стандартам топливной экономичности за счет снижения веса автомобиля и соответствия требованиям утилизации стандарты.Ключевыми препятствиями являются высокая стоимость первичного алюминия по сравнению с стали и дополнительные затраты на изготовление алюминиевых панелей. И алюминий, и автомобильная промышленность пыталась сделать алюминий рентабельным альтернатива стали. В данной статье анализируется стоимость изготовления и сборки. из четырех различных конструкций алюминиевых кузовов автомобилей, что позволяет сравнивать их с обычными стальные конструкции по текущим ценам на алюминий и с использованием текущего производства алюминия технология.Затем он пытается определить, может ли алюминий быть альтернативой. производство стали по более низким ценам на первичный алюминий и улучшенные производственные процессы.
ВВЕДЕНИЕ
Автомобиль и алюминий стали коммерчески жизнеспособными в примерно в то же время в конце 19 века; есть ссылки к использованию последних в первых с самого их начала. Несмотря на то что сталь предпочитают большинство автопроизводителей, в последние годы изменилась экономия топлива и правила утилизации активизировали попытки автопроизводителей снизить вес.Алюминий предлагает идеальное инженерное решение: его плотность составляет треть от из стали и удовлетворяет требованиям автомобильной материал. Однако алюминий по весу примерно в пять раз дороже, чем сталь.
Несмотря на высокую стоимость, в последние два десятилетия количество алюминия в автомобилях неуклонно увеличивалась. Проникновение алюминия увеличено с 39 кг (3%). в 1976 г. до примерно 89 кг (7%) в середине 90-х гг. 1 Однако это использование алюминия за счет стали было частичным. основа, а не результат каких-либо радикальных изменений дизайна. Большая часть проникновения алюминия использовался в трансмиссиях, блоках двигателя и колесах, в основном в виде отливок с некоторые поковки и штамповки. Однако проникновение кованого алюминиевого листа ограничивается кондиционерами и несколькими закрывающими панелями для кузова автомобиля. Проще говоря, доказано, что алюминий можно использовать вместо стали, железа и меди для различные детали в автомобиле.Во всех случаях эта замена снижает вес без снижение производительности, но в большинстве случаев стоимость значительно возрастает. Это увеличение можно противодействовать за счет снижения расхода топлива и повышения способности для перевозки безопасного и электронного оборудования и увеличения срока службы автомобиля, если пользователь, производитель и, возможно, самое главное, законодатель считают, что факторы достаточного достоинства.
Использование большого количества алюминия в серийных автомобилях, в отличие от дорогие малотиражные модели часто предсказывались, но пока не приходи.Единственный способ, которым алюминий может хоть как-то вытеснить сталь, — это когда алюминиевый лист заменяет сталь в качестве основного материала в шасси или кузов машины. В течение последнего десятилетия производители автомобилей неоднократно попытался оценить состояние алюминиевых автомобилей. Новые виды сплавов и апробированы передовые технологии производства. Интерес был сосредоточен в основном по тестированию подходящих методов соединения. Хонда NS-X был первым (и единственным) алюминиевым автомобилем, выпущенным ограниченным тиражом. бег.Audi A8 — еще один последний пример роскошной малолитражной полностью алюминиевой космической рамы. дизайн автомобиля.
БЕЛЫЙ КОРПУС
Рисунок 1. Распределение массы легковых автомобилей. |
В то время как алюминий в значительной степени смог победить трансмиссию и теплообменников, шасси, кузов и оборудование должны рассматриваться как области разработки легких конструкций с использованием алюминия.Ключевой вопрос оптимизировала конструкцию, чтобы использовать преимущества алюминия и, в то же время быть рентабельным. Как показано на рисунке 1, белое тело (BIW) составляет около 27% от веса всей средняя машина. Таким образом, именно в BIW происходит масштабное проникновение алюминия. должно произойти.
По частям замена стали алюминием, хотя и обеспечивает свет вес и лучшая коррозионная стойкость алюминия — не оптимальное решение.Поскольку автомобили по-прежнему в основном сделаны из стали, полная переработка автомобиль необходим для оптимального использования алюминия.
Некоторые алюминиевые и автомобильные компании продвигали алюминиевую конструкцию пространственной рамы, с использованием штамповки, литья и штамповки алюминия. Другие разрабатывали традиционная конструкция unibody, которая представляет собой преимущественно штампованный корпус из алюминия. Хотя оба дизайна продемонстрировали свою функциональность и эффективность, неясно, какая конструкция экономически лучше подходит для массового производства.Окончательный успех одного или обоих проектов зависит от прогресса и разработки в области технологий производства алюминия, в частности в алюминиевых штамповках. В этой статье сравниваются и анализируются изготовление и затраты на сборку алюминиевых и стальных автомобильных кузовов двух классов: небольшие, экономичные автомобили и автомобили среднего размера.
МЕТОДОЛОГИЯ
Производство BIW включает две затраты: изготовление деталей.
и сборка деталей.Эти затраты оцениваются с использованием разработанной методики.
в Массачусетском технологическом институте
Лаборатория систем материалов под названием «Моделирование технических затрат». Технический
моделирование затрат — это аналитический инструмент на основе электронных таблиц, который разбивает затраты
производственного процесса на элементарные этапы процесса. 2,3 Затраты, связанные с каждым этапом, определяются комбинацией инженерных разработок.
принципы и эмпирические данные для производственной практики. Факторы включают:
проектные характеристики, параметры материалов (например,г., инженерные свойства, материал
цены), параметры обработки (например, параметры управления оборудованием, требования к пространству,
энергопотребление) и параметры производства (например, объемы производства, лом
ставки, время простоя, время обслуживания). Модели также учитывают экономические
возможность (т.е. стоимость капитала, связанного с владением оборудованием). Входы
преобразуются в оценки постоянных и переменных затрат для каждого производственного
шаг. Переменные затраты включают энергию, материалы и непосредственный труд; фиксированные расходы
покрыть основное оборудование, необходимое для производственного процесса, включая машины,
инструменты для конкретной конструкции, строительные расходы, техническое обслуживание и накладные расходы из косвенных
труд.При отсутствии точных и специфичных для объекта данных станок и инструменты
затраты можно спрогнозировать на основе проектных спецификаций продукта, используя
регрессии, полученные на основе эмпирических данных.
Рисунок 2. Блок-схема методологии оценки стоимости изготовления BIW. |
Рисунок 2 поясняет используемую методологию при оценке затрат на изготовление BIW.По дизайну автомобилей список деталей был подготовлен по детальным разобранным чертежам автомобилей.
В список были включены размеры и вес деталей, которые в то время широко использовались. делятся на две группы. Мелкие детали, которые невозможно было прогнать модели затрат были назначены средние затраты в зависимости от их веса. Больше детали классифицировались в зависимости от процесса изготовления: штамповка, литье, или экструзия. Затем каждый из размеров детали был введен в качестве входных данных в соответствующий модель затрат на основе процесса (штамповка, литье и экструзия) для оценки стоимость изготовления этой части.Процесс повторялся для каждой детали, используя макрос электронной таблицы для оценки стоимости и разбивки затрат (материал, инструменты, стоимость машины, труд) при изготовлении каждой детали. Сумма затрат предоставил общие затраты на изготовление BIW.
Сборочная модель также разработана в Массачусетском технологическом институте. Лаборатория систем материалов использовалась для разработки сметы затрат на сборка BIW. 4 Модель сборки — это TCM, основанная на реляционной базе данных, а не на электронной таблице.BIW собирается путем соединения различных узлов, которые затем соединены вместе на линии окончательной сборки, чтобы сформировать законченный продукт. В модель сборки рассчитывает стоимость с использованием реляционных баз данных для сбора соответствующих информация, необходимая для каждого метода соединения. Затем модель рассчитывает затраты. в зависимости от количества присоединений, которое может быть выполнено на каждой станции во время доступное время. Затем время станции определяет количество станций. что потребуется для указанного объема производства и, следовательно, оборудования и вспомогательные машинные затраты.Для расчета затрат модель сборки выбирает необходимую информацию, хранящуюся в каждой таблице данных для каждого присоединения метод (лазерная сварка, металл в инертном газе [MIG]) сварка, точечная сварка, клепка, клеевое соединение и т. д.) в качестве исходных данных для расчета.
Для сравнения затрат на изготовление и сборку конструкций автомобилей обязательно, чтобы конструкции были одинакового размера. Были проанализированы шесть дизайнов, три из которых являются экономичными компактными автомобилями: полностью стальной Volkswagen Лупо, гибрид Лупо и Audi A2, все они похожи по размеру и габаритам.Сравнение автомобилей среднего размера Форд Контур, Форд P2000 и Audi А8. A8 ориентирован на рынок роскоши и намного больше, чем два других. Чтобы сравнить затраты на изготовление конструкций, относительная разница размеры должны быть учтены, поэтому для данного исследования части A8 сравнивались с габаритами форда Контур. Это было сделано путем уменьшения размеров деталей и панелей Audi. А8 в соотношении внешних габаритов двух конструкций.Вес детали также было уменьшено, если предположить, что толщина листа остается постоянной. Этот Масштабирование позволило сравнить дизайны 1: 1, несмотря на разницу в размерах. Масштабирование нормализует материальные затраты, уменьшая размер инструмента и машина стоит. Эти затраты зависят от размеров детали, полученной опытным путем. производные регрессии.
АНАЛИЗ МАЛЫХ КОНСТРУКЦИЙ АВТОМОБИЛЕЙ
Lupo — это небольшой автомобиль с классическим стальным цельным кузовом.Гибрид Lupo имеет точное внешнее сходство со стальной версией, но двери, капот и крылья изготовлены из алюминия (одна из панелей — из магний). Детали тормозной системы, шасси и колес также изготавливаются из более легкие металлы, чем стальная версия. Внутри машины сохранен вес со специальными сиденьями, рулем и педалями. В Audi A2, конструктивные элементы состоят из профилей и литых узлов, сваренных лазерной сваркой. вместе.Свесные панели изготавливаются из алюминиевого листа, которые затем прикрепляются к космической рамке. В таблице I указано производство детали. и детали веса трех дизайнов.
Таблица I. Данные о деталях для топлива Автомобили эконом-класса | |||
Автомобиль | Количество деталей | Производство | Общий вес детали |
190 | Штампов | 210 кг | |
190 | Штампов | 166 кг | |
210 | Штамповки (120) | 153 кг | |
Рисунок 3, на котором показано изготовление
стоимость трех конструкций, ясно показывает экономию на масштабе, связанную с
изготовление конструкций.Хотя стальные и гибридные кривые Lupo показывают
похожая форма. A2 состоит примерно на 40% из экструдированных и литых деталей, и он сплющивается.
ранее, поскольку он не может использовать эффект масштаба при штамповке.
Гибрид Lupo стоит дорого по сравнению со стальной версией на всем производстве.
объемы, потому что все крышки изготовлены из алюминия, из которого
штраф и дополнительные затраты на инструментальную штамповку всех деталей. A2, на
с другой стороны, он был спроектирован как алюминиевый автомобиль, а пространственная рама была оптимизирована.
за счет консолидации деталей с использованием крупных, экономичных отливок вместо алюминия
штамповки.На рисунке 4 показано абсолютное
стоимостная разбивка затрат на изготовление по категориям для двух объемов производства.
Рисунок 3. Затраты на изготовление деталей три маленькие машины. | Рисунок 4.Разбивка по частичной стоимости для малых автомобилей (60 000 и 195 000 автомобилей ежегодно). | |
Рисунок 5. Стоимость сборки малолитражных автомобилей. | Рисунок 6.Audi Разбивка затрат на сборку А2 по способам стыковки. | |
Рисунки 3 и 4 показать, что затраты на материалы и инструменты являются самыми большими Интерес в этом сравнении. Разбивка показывает, что при средних объемах производства (60 000 в год), общие затраты на гибрид Lupo и Audi А2 сопоставимы, хотя стоимость материала А2 выше.Это смещение высокой стоимостью оснастки гибрида. Добавленные затраты учитываются двумя Факторы: пониженная производительность линии, потому что алюминиевый лист имеет тенденцию к разрыву, что требует медленная штамповка и лишние удары для штамповки; увеличенные затраты на штамп из-за к специальным покрытиям для штампов. При большем объеме производства затраты для Гибрида существенно снизятся, потому что капитальные затраты на штамповку процессы распространяются на большие объемы производства.
В этом анализе только затраты на соединение автомобиля без закрывающих панелей.
считались.Таким образом, затраты на соединение стали и гибрида Lupo являются минимальными.
то же самое в этом анализе. На самом деле, соединение алюминиевых панелей и магния
задняя дверь к стальному unibody приводит к дополнительным расходам, чтобы избежать напряжения и
гальваническая коррозия на стыках. В двух конструкциях используются разные технологии соединения.
и методы для Lupo единственной используемой технологией соединения является сопротивление
точечная сварка. A2 состоит примерно из 35 метров лазерных швов, 20 метров из
сварка швом и 1800 заклепок.
Рисунок 7. Общие производственные затраты маленькие автомобили. |
Как показано на рисунке 5, A2 дешевле собирать, за исключением небольших объемов производства (т.е. менее 20000 автомобилей в год) из-за эффекта масштаба, связанного с процессом лазерной сварки.При малых объемах производства высокие капитальные затраты на аппараты лазерной сварки. несет ответственность за высокие затраты. Однако по мере увеличения уровня производства экономия на масштабе приводит к падению цены ниже Lupo. Единственный расходник При лазерной сварке используется азот, который требует незначительных затрат. Большая часть затрат связана с затратами на станок и лазерную головку. Фигура 6 показана разбивка затрат на соединение по технологиям для A2 в объем производства 60 000 автомобилей в год, где преобладают затраты на лазер. в процессе сборки это хорошо видно (около 52%).
Рисунок 7, на котором показано общее производство стоимость при разных объемах производства, аналогична стоимости изготовления деталей кривые. Гибридные Lupo и A2 конкурентоспособны по цене. Гибридный цельный корпус конструкция намного дороже стального эквивалента, потому что конструкция имеет оптимизирован для стального автомобиля с добавлением алюминия и магния снаружи панелей увеличивает не только материальные затраты, но и затраты на инструменты для штампованные алюминиевые детали.Более того, все не стальные детали в автомобиле штампованы, и поэтому относительно дороже, чем экструдированные профили или литые детали. В при объеме производства 60000 существует разница в стоимости в 510 долларов между А2 и стальной Лупо.
АНАЛИЗ МАШИН СРЕДНИХ РАЗМЕРОВ
Форд Contour — это четырехдверный среднеразмерный стальной цельный автомобиль, использованный в анализе в качестве базовый сценарий. Форд P2000 — это полностью алюминиевый цельный корпус, аналогичный по внешним размерам Форд Контур.Проект P2000 связан с Ford. участие в программе «Партнерство за новое поколение транспортных средств» (PNGV). Конструкция unibody представляет собой сварной алюминиевый лист в конструкции и затворе BIW. панели, литые алюминиевые передняя и задняя стойки амортизаторов, алюминиевая передняя часть подрамник, алюминиевый блок цилиндров и ротор / барабаны из алюминиевого композитного материала.
Таблица II. Данные о деталях для среднего размера Машины | |||
Автомобиль | Количество деталей | Производство | BIW Вес |
200 | Штампов | 215 кг | |
288 | Штампов | 152 кг | |
300 | Штампы (160) | 160 кг | |
Audi
A8, большой роскошный автомобиль, был Audi
конструкция космического корабля первого поколения.A8 имеет экструдированную раму, состоящую из
двух- и трехмерных экструдированных профилей, соединенных алюминиевым литьем под вакуумом
узлы. Используемые методы сборки — это пробивные заклепки, сварка MIG и некоторые
контактная сварка. Хотя этот 1,8-тонный седан не классифицируется как среднеразмерный.
машина для этого анализа, три машины сравнивались из-за наличия данных
и отличительные особенности дизайна трех автомобилей. Как обсуждалось ранее, чтобы
сравните A8 с двумя другими моделями, детали A8 были уменьшены
до габаритов форда
Контур.В таблице II указаны изготовление и вес детали.
(уменьшено для A8) детали трех дизайнов, которые были объединены с
стоимостные модели.
Рис. 8. Стоимость изготовления среднего размера машины. | Рисунок 9.Распределение стоимости запчастей среднего размера автомобилей (60 000 и 195 000 в год). | |
Рисунок 10. Стоимость сборки среднего размера. машины. | Рисунок 11.Общие производственные затраты автомобили среднего размера. | |
На рис. 8 показано изготовление детали в целом. расходы на три машины. Это также показывает, что Ford P2000 и Audi А8 намного дороже стального автомобиля. P2000 дороже производить в меньших объемах, чем аналогичный Audi A8, поскольку он состоит из штампованных алюминиевых деталей.Фигура 9 показана абсолютная разбивка затрат на изготовление при производстве. объемы 60 000 и 195 000 автомобилей в год.
Большая часть стоимости P2000 может быть покрыта инструментами. затраты на штампованные детали. Как видно на рисунке 9, затраты на инструмент составляют более 40% затрат при низком уровне производства. объем.
Модель сборки позволяет анализировать затраты на соединение для сборки этих среднеразмерные автомобили без крышек.В таблице III показаны различные способы соединения и их длина в каждой из машин.
Таблица III. Монтажные технологии Используется в автомобилях среднего размера | ||
Автомобиль | Метод соединения | Длина |
Точечная контактная сварка | 2630 точечных сварных швов | |
Точечная контактная сварка | 2000 точечных сварных швов | |
Точечная сварка | 400 баллов | |
На рисунке 10 показаны затраты на сборку. трех автомобилей при различных объемах производства.Audi А8 — самый дорогой в сборке из трех автомобилей из-за сложности. участвует в использовании различных техник соединения. Капитальные затраты на МИГ сварочное оборудование высокое; однако эффект масштаба можно увидеть в резком снижение затрат с 15 000 до 30 000 автомобилей в год.
Как показано на Рисунке 11, графическая иллюстрация
общей стоимости производства при различных объемах производства имитирует
кривые затрат на изготовление деталей.Стоимость Audi
A8, как правило, выходит за пределы средних объемов производства. В настоящее время
оценка оснастки для штамповки алюминия, конструкция алюминиевого цельного корпуса относительно
дороже, чем эквивалентная конструкция космической рамы, особенно при низких и
средние объемы производства.
ЭКОНОМИКА ЗАМЕНЫ
Анализ затрат на изготовление шести конструкций автомобилей показывает два основных препятствия. превращение алюминия в замену стали: более высокие материальные затраты и более высокие затраты на оснастку алюминиевых панелей.
Производители автомобилей стремятся производить алюминиевый автомобиль с такими же общими производственными характеристиками.
стоит как сталь. Считается, что для этого цена на алюминий должна снизиться.
примерно до 1 доллара за фунт (2,2 доллара за кг). Анализ показывает, что это возможно.
производить алюминий (5ххх) по указанным ценам методом непрерывной разливки и эксплуатации
большая экономия от масштаба. 5 , 6 Тем не менее, большая часть алюминия, используемого в панелях внешнего корпуса, представляет собой сплав 6ххх, что относительно
дорого производить.На рисунке 12 показано
затраты на производство A2, если цена автомобильного алюминиевого листа была
упасть до 1 доллара за фунт. Разница между Audi примерно в 320 долларов.
A2 и сталь Lupo можно было ожидать при текущем целевом объеме производства.
от 60 000 машин (в текущих ценах разница около 510 долларов).
Рисунок 12.Чувствительность продукции А2 затраты на алюминий. | Рисунок 13. Чувствительность производства затраты на цену алюминиевого листа. | Рисунок 14. Чувствительность продукции P2000 затраты при меньших затратах на инструмент. | ||
Аналогичный анализ легковых автомобилей среднего размера объемом 60 000 автомобилей в год показан на рисунке 13.Даже по 1 доллару за фунта, P2000 по-прежнему примерно на 600 долларов дороже, чем Contour.
Дополнительные затраты на инструмент для штамповки алюминия делают алюминий менее выгодным. альтернатива стали, даже по сниженным ценам на материалы, благодаря характеристики алюминия. 7 Например, алюминиевые панели не могут иметь острых фланцев для соединения внутреннего и внешние панели, они имеют тенденцию раскалываться, если углы штамповки слишком острые, и это также обладает большей упругостью, чем сталь, и более чувствителен к загрязнению матрицы так как он относительно мягкий.Как следствие затраты на штамповку алюминия относительно крупнее аналогичной стали по следующим причинам:
- Более высокие затраты на разработку штампа для компенсации упругого возврата
- Разработка и нанесение специальных покрытий и смазок на штампы.
- Более низкая скорость штамповки для предотвращения разрывов и повреждений
На рисунке 14 показан сценарий, в котором это сокращение дополнительных затрат на штамповку алюминия на 50%.В этот оптимистичный сценарий, когда автомобильный алюминиевый лист будет доступен по цене 1 доллар за фунт и 50% -ное сокращение дополнительных затрат на инструмент для штамповки алюминия, P2000 будет примерно на 300 долларов дороже, чем аналогичный стальной автомобильный кузов. Однако по мере развития технологий проектирования и производства и развития отрасли по мере обучения можно ожидать значительного снижения затрат. Собственно, дизайнерские разработки Audi уже привели к значительному снижению затрат между первым и автомобили второго поколения.Это произошло за счет объединения частей, замена процессов и упрощение деталей. 8
ЗАКЛЮЧЕНИЕ
Анализ конструкции шести автомобилей ясно дает представление об экономике замены алюминия в стальных кузовах автомобилей. Анализ показывает, что:
- Гибридные конструкции, такие как Lupo-hybrid, служат хорошим примером транспортных средств. которые могут достичь стандартов экономии топлива или рециркуляции. Однако это не экономически выгодное решение для снижения веса, потому что конструкция автомобиля обычно являются вариантами существующей конструкции, в которых частичная замена некоторых закрытий делается с использованием более легких материалов.Таким образом, метод не позволять производителю в полной мере использовать преимущества одного материала и достичь оптимальной эффективности производства.
- Разбор P2000 и Audi Дизайн A8 (с поправкой на эквивалентный размер) показывает, что при существующем производстве условиях, конструкция космической рамы немного конкурентоспособна по стоимости по сравнению с unibody, в первую очередь из-за более высокой стоимости штамповки алюминия.
- Анализ технологий соединения первого и второго поколения алюминиевые космические рамы показывают, что можно значительно сократить расходы, так как технология созревает.Audi A8 был самым дорогим из трех автомобилей в своем классе для сборки. С другой стороны, Audi второго поколения А2 вообще дешевле в сборке, чем стальной эквивалент, за исключением очень маленьких объемы производства. В первую очередь это можно отнести к развитию в технологии соединения улучшили понимание лазерной сварки алюминия и более быстрые лазерные сварочные аппараты.
Алюминий все еще должен преодолеть серьезные технологические и экономические препятствия прежде, чем он сможет заменить сталь в кузове автомобиля.Однако эти препятствия отнюдь не означает непреодолимое, как показал случай с лазерной сваркой алюминия. Превращение производителей алюминия из простых поставщиков материалов в партнерство с автопроизводителями — шаг в этом направлении. Можно ожидать что в области штамповки алюминия в ближайшее будущее. Это, в сочетании с правильным законодательным давлением с точки зрения цели по экономии топлива и рециркуляции могут сделать алюминий значительным, если не первичный материал в кузове авто.
БЛАГОДАРНОСТИ
Авторы выражают благодарность Ford. Motor Company и McKinsey & Co. за предоставление ценных данных для этого исследования.
Список литературы
1. M.N. Беккер,
Алюминий: новые задачи в сфере переработки и сбыта продукции, JOM ,
51 (11)
(1999), pp. 2638.
2. Дж. П. Кларк, Techno-Economic
Issues in Materials Selection, ASM Handbook Vol.20 Выбор материалов и
Дизайн (Парк материалов, штат Огайо: ASM,
1997), pp. 255265.
3. H.
Хоэх, Экономический анализ алюминиевого листа и перспективы производства алюминия в
Autobody (бакалаврская диссертация, Массачусетский технологический институт,
2000).
4. Ф. Катрак, Д. Полтис и
Дж. Мортон, Сталь против алюминия против полимеров: битва за автомобильный кузов
Приложения в 21 веке (доклад, представленный на Metal
Бюллетени 12-го Междунар. Конф., Сентябрь 1997 г.).
5. А. Келкар, Анализ алюминия
в конструкции кузовов автомобилей и ее стратегическое значение для алюминиевой промышленности
(Докторская диссертация, Массачусетский технологический институт, 2001 г.).
6. A. Kelkar, R. Roth, and J.P.
Кларк, Стоимость обучения при разработке алюминиевых автомобильных кузовов
Проекты, представленные в соответствии с JOM .
7. Х. Марти, Моделирование затрат
сборки автомобильного кузова с использованием реляционных баз данных (Б.С. Диссертация,
Массачусетский технологический институт, 1997 г.).
8. F.W. Ostermann, Алюминий
Технология материалов для автомобилей (German Press, 1987).
Ричард Рот и Джоэл Кларк с материалы Системная лаборатория в Массачусетсе Технологический Институт. Ашиш Келкар работает в Cisco Systems.
За дополнительной информацией обращайтесь к Ричарду Роту, Массачусетский институт.
of Technology, E40-202, 77 Massachusetts Avenue, Cambridge, Massachusetts 02139
СОЕДИНЕННЫЕ ШТАТЫ АМЕРИКИ; электронная почта rroth @ mit.edu.
Авторские права принадлежат The Minerals, Metals & Materials Общество, 2001
Прямой вопросы об этой или любой другой странице JOM по адресу [email protected].
В то время как западные автопроизводители используют алюминий, Азия по-прежнему приваривается к стали
Хёнджу Джин, Мейён Чо
СЕУЛ (Рейтер) — Около четырех лет назад Hyundai Motor рассматривала возможность перехода со стали на алюминиевые детали кузова для своего седана Genesis, чтобы сделать его легче , более экономичный и более конкурентоспособный с немецкими брендами роскоши, сказали два человека, знакомых с этим вопросом.
Завод Hyundai Steel на фотографии из архива 15 июня 2011 года в Данджине, примерно в 130 км (81 милях) к юго-западу от Сеула. REUTERS / Lee Jae-Won / Files
Его дочерняя компания Kia Motors сделала аналогичный шаг, построив тестовые версии своего премиального седана K9, называемого в США K900, с использованием алюминия в панелях кузова, включая дверь, капот и крышку багажника, два другие люди сказали Рейтер.
Но южнокорейский дуэт, который вместе занимает пятое место по мировым продажам автомобилей, предпочел вместо этого сталь, сдерживаемую стоимостью и, по словам двух из этих людей, тесными связями с сестринской сталелитейной компанией Hyundai Steel Co.
Поскольку западные автопроизводители, такие как Audi AG и Ford Motor Co, лидируют в использовании алюминия, который легче, но дороже стали, их азиатские конкуренты неохотно вкладывают средства в дорогостоящее техническое перевооружение, которое могло бы нарушить существующие производственные процессы и отношения с поставщиками. .
«На данный момент действительно большой проблемой для азиатских компаний является определение того, как им следует вести себя в условиях, когда автомобили становятся легче, — сказал Трулс Торстенсен, президент и главный исполнительный директор EFS Business Consultancy.
Автопроизводители в Азии часто предпочитают эволюционные обновления, которые позволяют им использовать существующие заводы и производить несколько моделей на одних и тех же сборочных линиях; западные конкуренты, как правило, вносят изменения в продукцию оптом, что требует реорганизации заводов. Это вынуждает азиатские автомобильные компании искать другие способы снижения веса и выбросов, поскольку ужесточение правил экономии топлива и выбросов в США и Европе стимулирует создание более легких автомобилей.
«Если вы можете делать все, что захотите, возможно, будет проще принять решение в пользу алюминия или легкого веса», — сказал Торстенсен.
В Hyundai отказались комментировать, какие материалы учитывались при разработке продукта. Представитель Kia сказал, что компания не использовала алюминиевые детали кузова в тестовых версиях K9, и отказался комментировать, рассматривает ли компания возможность использования этого материала при разработке автомобиля.
ПОВЫШЕНИЕ СПРОСА
Ожидается, что спрос на алюминий в автомобильной промышленности Азии вырастет на 71 процент к 2016 году, что намного ниже прогнозируемого пятикратного скачка в Северной Америке, согласно внутреннему прогнозу компании Novelis Corp из Атланты [NVLXC.UL], крупнейшего производителя плоского алюминиевого проката и подразделения индийской Hindalco Industries.
В 2016 году на Азию будет приходиться менее десятой части общего потребления алюминия автомобильной промышленностью, в то время как на Северную Америку и Европу будет приходиться около 45 процентов каждая, прогнозирует Новелис. И это несмотря на ожидания, что на Азию по-прежнему будет приходиться более половины мирового производства автомобилей, согласно IHS Automotive.
«Эта замена стали обусловлена в основном строгими правилами выбросов, особенно в Северной Америке, и меняет правила игры для сектора прокатки алюминия», — сказал Чарли Дюрант, старший консультант CRU, консалтинговой компании по металлу.«В Азии нормы выбросов менее строгие, а автомобили, как правило, намного меньше».
«Относительная стоимость алюминиевого листа рассматривается как запретительный фактор, поэтому именно в регионах с самым строгим законодательством … этот материал будет наиболее широко принят», — добавил он в комментариях к этой статье, отправленных Рейтер по электронной почте.
Европейские люксовые бренды, такие как Audi из Volkswagen AG и BMW AG, расширяют использование алюминия в дорогих и высокодоходных автомобилях. Позднее в этом году Ford приступит к созданию своего флагманского пикапа F-150 с алюминиевым кузовом, что сделает его первым подобным автомобилем для массового рынка.
Однако Hyundai, Toyota Motor Corp и другие азиатские автопроизводители в основном производят автомобили для массового рынка на высокоэффективных сборочных линиях, которым часто бывает несколько десятилетий. Они не продают роскошные автомобили в больших объемах и не могут требовать таких цен, как Audi и BMW.
По данным консалтинговой компании Wood Mackenzie, алюминий может стоить примерно в четыре раза дороже стали, хотя алюминий на 30 процентов легче обычной стали и на 15 процентов легче, чем современная высокопрочная сталь.Переход на алюминий увеличивает не только затраты на материалы, но и требует значительных инвестиций для капитального ремонта производственных линий.
«Если вы начнете создавать совершенно другую архитектуру для Lexus от Toyota или Infiniti от Nissan, вы столкнетесь с проблемой стоимости, потому что проданные номера и цена, которую они получают, не похожи на немецкие», — сказал Торстенсен. «Все производители в Азии сталкиваются с той же проблемой. Они не могут получить премиальную цену, поэтому им нужно быть более осторожными ».
HEAVY HYUNDAI
Предыдущая версия Hyundai Genesis имела алюминиевый капот, но компания перешла на сталь для текущей модели, выпущенной в конце 2013 года, что сделало ее более тяжелой и менее топливной, чем ее предшественник, сказали два человека.
По словам Новелиса, алюминиевый капот автомобиля весит примерно половину того, что сделан из стали. По данным Министерства энергетики США, каждые 10 процентов снижения веса автомобиля улучшает экономию топлива на 6-8 процентов.
В 2010 году, когда Hyundai приступила к разработке Genesis текущего поколения, снижение веса и повышение топливной экономичности были проблемой, сказал один из знакомых с этим вопросом.
На встрече в исследовательском центре автопроизводителя на окраине Сеула инженеры предложили расширить использование легкого алюминия от капота до других внешних панелей кузова и даже рам, сказал присутствовавший человек.Но Hyundai пошел в противоположном направлении, заменив алюминий сталью даже на капот из-за его связей с Hyundai Steel и более высоких затрат, связанных с алюминием.
«Это был шаг назад для Hyundai», — сказал этот человек.
Последний Genesis поправился на 390 фунтов (177 кг) по сравнению со своим предшественником, выпущенным в 2008 году, и весит на 181 фунт больше, чем его конкурент 535i.
Глава США Дэйв Зуховски сказал, что Hyundai «добавила дополнительный вес в жесткость конструкции», чтобы пройти более жесткую U.С. краш-тесты. «Раньше мы говорили, что хотим уменьшить вес автомобиля на 10 процентов по мере того, как мы их выводим. В этом мире, с … требованиями к аварийным ситуациям и тому подобным, вы не сможете этого сделать, — сказал он репортерам в Детройте в прошлом месяце.
СИЛЬНАЯ СТАЛЬ
Вместо алюминия азиатские автопроизводители работают с производителями стали над созданием более легкой и прочной стали, одновременно принимая другие меры по повышению топливной эффективности, включая модернизацию обычных двигателей и деталей без необходимости серьезных модификаций производственных мощностей.
«Hyundai Motor находится под огромным давлением, чтобы сократить расходы, поскольку это крупный производитель автомобилей для массового рынка», — сказал Reuters Ву Ю Чол, президент и генеральный директор Hyundai Steel. «Самое главное — оставаться конкурентоспособным на рынке. Они считают, что использование стали для их флагманских моделей намного более конкурентоспособно ».
На данный момент японские автопроизводители ограничивают использование алюминия в основном деталями гибридных автомобилей и автомобилей премиум-класса, таких как Lexus IS от Toyota. Honda Motor разработала технологию комбинирования алюминия и стали для изготовления некоторых деталей в США.S. его версии Acura RLX и Accord. «Когда мы рассматриваем массовое производство, цельналюминиевый корпус по-прежнему затруднен», — сказала Reuters представительница Honda Юка Абэ.
Компания Nissan Motor в прошлом году объявила о плане расширения использования высокопрочной стали, которая прочнее и легче обычной стали, в 20% деталей, устанавливаемых в ее новые серийные модели, начиная с 2017 года.
«Мы продолжаем. для использования алюминия в таких областях транспортных средств, как капоты, двери и багажник некоторых моделей, таких как высокопроизводительные спортивные автомобили GT-R и 370Z.В будущем в ключевых конструкционных областях будет использоваться больше высокопрочной стали », — сказал Крис Киффе, представитель Nissan.
ПРОИЗВОДСТВО СТАЛИ
Азиатские автопроизводители предпочитают сталь отчасти потому, что ее много, причем две трети мировых поставок приходится на этот регион.
Novelis завершит строительство завода по производству листового металла в Китае в конце этого года и получает множество запросов от азиатских автопроизводителей об использовании алюминия, хотя китайским автопроизводителям потребуется 4-5 лет и 2-3 года для корейских и японских фирм. это в значительных количествах, сказал Джефф Ван, директор по продажам автомобилей в Азии.
Он предсказал, что западные автопроизводители, использующие алюминий в автомобилях китайского производства, побудят азиатских конкурентов последовать их примеру.
Wood Mackenzie сказал, что не уверен, что алюминиевый лист кузова найдет свое применение в автомобилях массового потребления.
«Поставщики автомобильных стальных деталей будут сопротивляться привлекательными инновациями и ценами, поскольку это рынок, от которого производители стали вряд ли с готовностью откажутся», — говорится в сообщении.
Дополнительные репортажи Норихико Широузу в ПЕКИНЕ, Мелани Бертон в СИДНЕЕ, Бен Клейман в ДЕТРОЙТ и Йоко Кубота в ТОКИО; Редакция Тони Манро и Яна Геогегана
Почему алюминиевые сплавы используются в автомобильной промышленности? | Howard Precision
Из-за присущих алюминию характеристик и свойств этот металл широко используется как в производстве легковых, так и в грузовых автомобилях.Почему? Прежде всего, алюминий — легкий материал. При использовании в автомобилях он может значительно повысить производительность и снизить расход топлива. Не только это, но и алюминий прочен. Именно из-за соотношения прочности и веса алюминий так ценен в транспортной отрасли. Улучшение характеристик автомобиля не идет в ущерб безопасности. Благодаря высокой прочности и малому весу повышается безопасность водителей и пассажиров. Позвольте команде Howard Precision Metals предоставить вам качественную алюминиевую продукцию, необходимую для удовлетворения ваших требований к автомобилестроению.
Здесь алюминий является вторым наиболее часто используемым металлом в автомобильной промышленности. Обычно используются: спицы, структурные компоненты, калибры, роторы, колеса, роторы и многое, многое другое. Фото любезно предоставлено Бенджамином Чайлдом на Unsplash.Применение в автомобилестроении
Каждый фунт алюминия, используемого в автомобиле вместо стали, снижает общий вес автомобиля на фунт. Этот металл позволяет более безопасным и эффективным транспортным средствам выезжать на проезжие части. С годами популярность алюминия в автомобильной промышленности продолжает расти.В настоящее время это второй наиболее часто используемый металл в транспортных средствах, уступая только стали. Кроме того, этот металл универсален. Его можно использовать для производства двигателей, трансмиссий, подвески, колес, компонентов тормозов, рам, магнитов для тахометров и спидометров, электропроводки, компонентов кондиционеров и даже частей тела. Алюминий прочен, эффективен, безопасен, пригоден для вторичной переработки и его много. По этим и другим причинам он стал обычным материалом в автомобильной промышленности. По оценкам, к 2028 году алюминий будет составлять около 16 процентов от общего веса автомобиля.
Крепкий и безопасный
Алюминий имеет более высокое отношение прочности к массе, чем низкоуглеродистая сталь. Из-за этого алюминий часто используется в более крупных зонах воздействия на автомобили. Использование этих металлов в более крупных зонах раздавливания не только повышает безопасность, но и увеличивает производительность. Во-первых, уменьшение веса позволяет сократить тормозной путь. В конце концов, все мы знаем, что более короткий тормозной путь может быть разницей между близким промахом или смертельным столкновением. Во-вторых, при сравнении отношения прочности металлов к весу характеристики алюминия позволяют ему поглощать в два раза больше энергии удара, чем низкоуглеродистую сталь.Изготавливая зоны деформации автомобиля из алюминия, а не из стали, инженеры могут спроектировать зоны деформации. Это означает, что алюминий можно спроектировать так, чтобы он складывался очень специфическим и предсказуемым образом в случае аварии. Таким образом, алюминий может поглощать энергию столкновения и обеспечивать безопасность пассажиров. Это чрезвычайно важно для легковых автомобилей.
Чем меньше вес автомобиля, тем экологичнее его продукт. Но вы можете быть удивлены почему. Этот «экологичный» продукт возникает не только из-за выхлопных газов.Нет. Он исходит из всего жизненного цикла энергии. Да, выбросы углерода (CO2) снижаются с более легкими автомобилями, а топливная эффективность повышается. Однако использование алюминия в производстве автомобилей приводит к наименьшему углеродному следу «от колыбели до могилы». Как указывалось ранее, большая часть алюминия перерабатывается. Но знаете ли вы, что переработка этого металла требует меньше энергии, чем добыча руды ?! Все это приводит к уменьшению выбросов углекислого газа. Мало того, что для производства этих автомобилей требуется меньше энергии.Но для их работы требуется меньше энергии. Неудивительно, почему алюминий стал таким основным продуктом в автомобильной промышленности.
Перерабатываемые и более энергоэффективные
Алюминий — это не только самый распространенный металл на Земле, но и наиболее переработанный. Период. Фактически, почти 75 процентов всего алюминия, производимого в Соединенных Штатах, все еще используется сегодня. Автомобильная промышленность, безусловно, пользуется этой характеристикой. Почти 90 процентов всего алюминия, включая автомобильный лист, который используется в автомобиле, по окончании срока его службы перерабатывается.Закончится ли когда-нибудь цикл? Скорее всего, не. Алюминий может быть переработан сам по себе в действительно замкнутом цикле. При вторичной переработке свойства алюминия остаются неизменными. Кроме того, энергия, необходимая для рециркуляции алюминия, составляет всего 5 процентов по сравнению с энергией, необходимой для извлечения этого элемента из руды. Изобилие и возможность вторичной переработки — вот причины, по которым алюминий является экологически безопасным вариантом. Особенно по сравнению с другими металлами, например сталью.
2024: хорошее соотношение прочности и веса и сопротивление усталости
Алюминиевые сплавы серии 2000 известны своей прочностью.Сплав 2024 именно такой: прочный. В этом сплаве в качестве основного легирующего элемента используется медь. Таким образом, 2024 год занимает одно из первых мест в категории прочности. Алюминий из сплава 2024 обладает исключительным соотношением прочности и веса и отличным сопротивлением усталости. Однако он имеет более низкую коррозионную стойкость по сравнению с другими алюминиевыми сплавами, такими как 6061. Этот сплав имеет плохую свариваемость и паяемость. Кроме того, 2024 хорошо реагирует на формовку и чистовую обработку в отожженном состоянии.Кроме того, 2024 год станет отличным показателем усталостной прочности. Основные области применения алюминия 2024 года в автомобильной промышленности: роторы, спицы колес, конструктивные элементы и многое, многое другое. Чрезвычайно высокая прочность и отличное сопротивление усталости — две причины, по которым сплав 2024 используется в автомобильной промышленности.
6061: Отличная коррозионная стойкость
Когда к алюминию добавляют марганец и кремний, полученный сплав попадает в серию 6000. Сплав 6061, поставляемый компанией Howard Precision Metals, является термообрабатываемым сплавом с хорошей коррозионной стойкостью.Этот алюминиевый сплав доступен в виде пластин, листов и профилей, в том числе нестандартных форм. Алюминий 6061, обычно используемый в производстве автомобильных компонентов и запчастей, обладает высоким соотношением прочности и веса. Он также обладает хорошей обрабатываемостью в отожженном состоянии. Сплав 6061 также может быть эффективно изготовлен с использованием множества различных распространенных технологий изготовления. Хотя этот сплав не такой прочный, как 2024 год, он определенно более универсален. Благодаря этим свойствам сплав 6061 стал основным сплавом для многих различных компонентов в автомобильной промышленности.Некоторые автомобильные применения сплава 6061 включают: ABS, поперечины, колеса, подушки безопасности, балки и многие другие.
Как 100% поставщик алюминия компания Howard Precision Metals обладает знаниями и опытом для разработки индивидуальных решений для алюминиевых приложений. Чтобы узнать больше об алюминии 2024, алюминии 6061 или запросить ценовое предложение, свяжитесь с нами сегодня по телефону 800.444.0311 или запросите ценовое предложение на нашем веб-сайте.
Какие грузовики Ford имеют алюминиевые кузова?
Первый пикап с алюминиевым кузовом был более смелым изменением, чем некоторые думают.Грузовики символизировали трудолюбивую силу, а сталь считалась неотъемлемой частью этого образа. Тогда Форд решил все поменять. В то время были опасения, что Ford потеряет продажи и постоянных клиентов. Но несколько лет спустя конкуренты Ford тоже начали заниматься алюминием. Вот что вам нужно знать о грузовиках Ford с алюминиевыми кузовами и о том, что этот материал означает сегодня.
Грузовики Ford с алюминиевым кузовом 2020 Серия F Super Duty | FordС 2015 года Ford F-150 имеет алюминиевый кузов.В 2017 году грузовики Super-Duty серии F также получили алюминиевые кузова. По данным The Drive , оба были первыми пикапами в своем классе, корпус которых был сделан из более легкого материала. Тем не менее, серия F по-прежнему сохраняет раму из высокопрочной стали.
На данный момент Ford F-150 и Super Duty серии F являются единственными грузовиками, у которых есть и алюминиевые кузова, и алюминиевые кузова. В 2019 году Chevrolet Silverado заменил некоторые стальные панели кузова алюминиевыми, но не кровать.И хотя GMC Sierra также имеет панели кузова из «смешанных материалов», вместо алюминиевой станины вместо углеродного волокна. Ram также использовал алюминий только выборочно.
При запуске F-150 2015 года критики предположили, что алюминий будет слишком хрупким и дорогостоящим для ремонта. Согласно отчету Autoweek , это все еще преобладающий менталитет некоторых инженеров и дизайнеров. Процитирую старую поговорку велосипедиста: «Сталь настоящая». Но на самом деле? На самом деле это не так.
Что следует знать владельцам об алюминиевых грузовиках Ford: стоимостьБыло выпущено множество видеороликов, демонстрирующих, что алюминиевые панели кузова и станина F-150 не так прочны, как сталь, и что их ремонт стоит дороже. Chevrolet сделал это для одной из своих рекламных роликов «Настоящие люди». Эдмундс на самом деле купил и протестировал F-150 2015 года, чтобы попытаться доказать или опровергнуть это мнение. На YouTube есть бесчисленное количество видеороликов, в которых люди бьют грузовики кувалдами или говорят, что панели сделаны из пивных банок.
Но, как сообщали мы и Automotive News , ремонт алюминия и жизнь с ним не являются дорогостоящими. В 2017 году один техасский дилерский центр был наводнен поврежденными градом алюминиевыми F-150. Но поскольку Ford инвестировал в надлежащее обучение технических специалистов и разработал пикап с модульной структурой, средний ремонт алюминиевого грузовика стоил на 2000 долларов меньше, чем ремонт стали. Это не только уменьшило количество рабочих часов, необходимых для ремонта грузовиков, некоторые алюминиевые детали были фактически дешевле, чем их стальные аналоги.Частично это связано с тем, что алюминий пригоден для вторичной переработки: Ford мог переплавлять оставшийся металл для получения большего количества деталей.
Ford F-150 Raptor 2019 года | Стоимость страховки Fordдля алюминия также не выше, чем для алюминия. сталь. Фактически, из-за простоты ремонта, сообщает Институт данных о потерях на дорогах. Серьезность претензий о столкновении снизилась на 7%. При этом претензии о столкновении в целом выросли на 7%. Это потому, что, честно говоря, алюминий не такой прочный. как сталь.
Что следует знать владельцам об алюминиевых грузовиках Ford: прочностьПри этом грузовики сделаны не из пивных банок.Кроме того, согласно информации из Reading Body, они менее подвержены ржавчине. Как сообщает Car and Driver , Ford потратил более двух десятилетий на исследования производства алюминия. Автопроизводитель использует смесь сплавов, которые широко используются во многих отраслях промышленности, включая военную и аэрокосмическую. Они не совсем «военного», как заявляют в рекламе, но и не так уж и далеко.
Те объявления Chevy, в которых шлакоблоки отскакивают от заднего сиденья? Кто это делает, и без постельного белья? И если вы действительно беспокоились о прочности панели F-150, обратите внимание на недавнюю презентацию Tesla Cybertruck.
Они разбили алюминиевую дверную панель кувалдой, и все, что на ней осталось, это несколько вмятин. Дверь Сильверадо или Ram 1500, вероятно, тоже будет вмятина.
Что следует знать владельцам об алюминиевых грузовиках Ford: снижение веса
В любом случае, экономия веса, несомненно, того стоила. И не только для повышения топливной эффективности. Как объяснил YouTuber Big Truck Big RV, снижение массы тела F-Series означало, что Ford мог увеличить остальную часть грузовика.Благодаря более легкому корпусу и более прочным компонентам это означало, что буксировочная способность и грузоподъемность F-Series могут возрасти. И учитывая, что F-150 и F-Series Super-Duty являются лучшими в своих классах с точки зрения грузоподъемности, это окупилось.
Алюминиевые грузовики по-прежнему вызывают споры?К сожалению, ответ вроде «да». Но это споры, которые больше ни на чем не основаны.
Многие производители грузовиков считают, что переход на полностью алюминиевый что-то как-то ниже их и их клиентов.Дело в том, что многие до сих пор Верить в то, что алюминий — это деликатный и дорогой материал, тоже не помогает.
Ford F-150 Raptor 2019 года | FordТем не менее, F-150 2015 года, самый первый год выпуска алюминиевого кузова, является лучшим модельным годом для покупки. И, как показывают данные, ремонтировать грузовики Ford с алюминиевым кузовом не дороже, чем стальные. И увеличение повреждений при столкновении, вероятно, связано не столько с общим увеличением веса грузовика и внедорожника, сколько со свойствами материалов.Кроме того, если алюминий не является прочным металлом, зачем Ram и GM вообще использовать его в своих грузовиках?
Если вы хотите купить пикап, не чувствуйте себя алюминиевый кузов каким-то образом дискредитирует любой из грузовиков Ford.