Сопло для пескоструйного аппарата: особенности выбора и изготовления
Сопло, которое используется для оснащения пескоструйного аппарата, является важнейшим элементом конструкции такого устройства. Только правильно подобранное сопло позволит вам наиболее эффективно использовать пескоструйный аппарат по его прямому назначению: для очистки различных поверхностей от загрязнений, старых покрытий, следов коррозии, их обезжиривания и подготовке к дальнейшей обработке.
Для каждого применения можно подобрать сопло определенного диаметра, в зависимости от фракции используемого песка
Задачи, которые решает сопло пескоструйное, заключаются в сжатии и разгоне до требуемой скорости смеси, состоящей из воздуха и абразивного материала, а также в формировании рабочего пятна и его насыщении абразивом, воздействующим на поверхность обрабатываемого изделия. В зависимости от размеров поверхности, которую необходимо подвергнуть пескоструйной обработке, в соплах могут быть выполнены отверстия различных типов.
Сущность пескоструйной обработки
Пескоструйная обработка предполагает воздействие на различные поверхности абразивным материалом. В качестве последнего используются песок, дробь, карбид кремния, мелкие шарики из стекла и т.д.
Пескоструйная обработка – это механическое воздействие на поверхность мелких твердых частиц
Перед началом обработки абразив помещают в герметичный бункер. По основному шлангу аппарата под большим давлением подается воздух, поступающий от отдельного компрессора. Проходя мимо отверстия заборного рукава, поток воздуха создает в нем вакуум, что и способствует всасыванию в основной шланг абразива. Уже смешанный с абразивом воздух поступает к пистолету, основным элементом которого является сопло пескоструйное, через которое абразивная смесь подается на обрабатываемую поверхность.
Схема участка пескоструйной обработки
Как уже говорилось выше, для выполнения пескоструйной обработки могут использоваться различные типы абразивных материалов. Выбор здесь зависит от типа поверхности, которую необходимо очистить. Так, обработка с использованием песка эффективна в тех случаях, когда необходимо удалить слой старой краски с бетонной поверхности, очистить кирпичные стены от остатков цемента, подготовить металлические детали к дальнейшей покраске. Такие абразивы, как пластик или пшеничный крахмал, успешно применяют в судостроительной, автомобильной и авиастроительной отраслях, с их помощью эффективно удаляют старые покрытия с композиционных материалов.
Конструктивные особенности сопла для пескоструйного аппарата
Основными параметрами сопла, устанавливаемого на пескоструйный аппарат, являются:
- диаметр и тип отверстия;
- длина;
- материал изготовления.
Абразивоструйные сопла различных конфигураций
Диаметр отверстия в сопле, которое фиксируется на пескоструйном аппарате посредством специального соплодержателя, выбирается в зависимости от того, какой производительностью должно обладать устройство. Производительность любого пескоструйного аппарата – как серийного, так и сделанного своими руками – зависит от мощности струи или объема воздуха, который в состоянии пропускать сопло в единицу времени.
Мощность струи, которую формирует сопло, прямо пропорциональна объему воздуха, который проходит через него в единицу времени. Соответственно, чтобы увеличить мощность пескоструйного аппарата, необходимо сделать в его сопле отверстие большего диаметра. Например, можно оценить мощность сопел, отверстия в которых имеют разные диаметры. Если сопло, диаметр которого соответствует 6 мм (1/4 дюйма), имеет мощность, равную 100%, то изделия с отверстиями больших диаметров будут отличаться следующей величиной данного параметра:
- 8 мм (5/16 дюйма) – 157%;
- 9,5 мм (3/8 дюйма) – 220%;
- 11 мм (7/16 дюйма) – 320%;
- 12,5 мм (1/2 дюйма) – 400%.
Чтобы еще лучше ориентироваться в мощности сопла с тем или иным диаметром внутреннего отверстия, можно принять во внимание, что изделия, диаметр в которых составляет 6 мм (1/4 дюйма), способны обеспечить среднюю мощность струи, равную 30 м
Таблица позволяет примерно оценить влияние диаметра сопла и давления воздуха на производительность и расход абразива
Если вы не собираетесь изготавливать сопло для аппарата пескоструйной обработки своими руками, то следует иметь в виду, что изделия, выпускаемые серийно, имеют стандартные диаметры отверстий, равные 6, 8, 10 и 12 мм.
На выбор такого параметра сопла, как его длина, оказывает влияние степень загрязненности очищаемой поверхности. Для пескоструйной обработки поверхностей, которые имеют незначительные загрязнения, выбираются более короткие сопла (7–8 см). Если же необходимо обработать поверхность, на которой имеются сложные загрязнения, длина сопла должна быть значительной (до 23 см).
Сопла, диаметр которых не изменяется по всей их длине, позволяют обеспечить скорость выхода абразивного материала 320 км/час, при этом давление смеси из воздуха и абразива, поступающей из такого сопла, составляет 6 атм. Сопла с каналом «Вентури» формируют струю абразивной смеси, скорость движения которой может доходить до 720 км/час. Понятно, что сопла с внутренними отверстиями такого типа повышают эффективность пескоструйной обработки.
Очевидно, что площадь потока у сопла типа VENTURI значительно больше, чем у обычного прямолинейного
Использование сопел с внутренними отверстиями, выполненными по типу «Вентури», позволяет предприятиям и специализированным компаниям не только увеличить производительность своего труда, но и значительно повысить качество выполняемой обработки. Что важно, применение изделий с такими каналами не требует приобретения специальных абразивов и не приводит к увеличению расхода сжатого воздуха.
Если сопла с отверстиями обычного типа для пескоструйных аппаратов можно сделать своими руками (хотя это и сложно), то изделия с каналом «Вентури» качественно изготовить в домашних условиях, не располагая специальным оборудованием, практически невозможно.
Устройство сопла пескоструйного с каналом Вентури: d — внутренний диаметр; D — заходной диаметр; Т — присоединительная резьба; L — длина сопла
Для изготовления сопел, в том числе и своими руками, могут быть использованы различные материалы, от выбора которых зависит долговечность изделия. Так, в зависимости от материала изготовления сопла для аппаратов пескоструйной обработки обладают следующей долговечностью:
- керамические изделия, которые в домашних условиях делают из обычных свечей зажигания, – 1–2 часа;
- сопла из чугуна – 6–8 часов;
- изделия, для производства которых был использован карбид вольфрама, – 300 часов;
- сопла, изготовленные из карбида бора, – 750–1000 часов.
Если в качестве абразивного материала в пескоструйном аппарате используется не песок, а стальная дробь, то долговечность сопел любого типа увеличивается в 2–2,5 раза.
Как правильно выбрать сопло для пескоструйной обработки
Выбирая сопло для своего пескоструйного аппарата, учитывайте тот факт, что самые недорогие изделия являются и самыми недолговечными. Такие сопла в итоге обойдутся вам дороже качественной продукции, особенно если вам предстоит выполнить большой объем работ.
Пескоструйные износостойкие сопла из карбида вольфрама
Для бытовых целей подходят сопла из чугуна и керамики. Многие домашние умельцы даже самостоятельно изготавливают керамические сопла, используя для этого отработанные свечи зажигания. Для того чтобы из такой свечи сделать сопло, достаточно удалить из ее керамической оболочки металлический электрод.
Используя для пескоструйного аппарата чугунные и керамические сопла, следует иметь в виду, что из-за своего ускоренного износа они увеличивают расход как воздуха, так и абразива, поэтому их не рекомендуется применять при выполнении масштабных работ.
Применение таких изделий целесообразно во всех ситуациях, когда требуется выполнить большой объем работ по очистке различных поверхностей.
Оценка статьи:
Загрузка…Поделиться с друзьями:
Сопло для пескоструйного аппарата: особенности выбора и изготовления
Сопло, которое используется для оснащения пескоструйного аппарата, является важнейшим элементом конструкции такого устройства. Только правильно подобранное сопло позволит вам наиболее эффективно использовать пескоструйный аппарат по его прямому назначению: для очистки различных поверхностей от загрязнений, старых покрытий, следов коррозии, их обезжиривания и подготовке к дальнейшей обработке.
Для каждого применения можно подобрать сопло определенного диаметра, в зависимости от фракции используемого песка
Задачи, которые решает сопло пескоструйное, заключаются в сжатии и разгоне до требуемой скорости смеси, состоящей из воздуха и абразивного материала, а также в формировании рабочего пятна и его насыщении абразивом, воздействующим на поверхность обрабатываемого изделия. В зависимости от размеров поверхности, которую необходимо подвергнуть пескоструйной обработке, в соплах могут быть выполнены отверстия различных типов. Так, для обработки узких поверхностей применяют сопла с одинаковым диаметром по всей длине, а для очистки поверхностей большой площади используют изделия, отверстия в которых имеют больший диаметр на входе и выходе (тип «Вентури», разработанный в середине прошлого века).
Сущность пескоструйной обработки
Пескоструйная обработка предполагает воздействие на различные поверхности абразивным материалом. В качестве последнего используются песок, дробь, карбид кремния, мелкие шарики из стекла и т.д.
Пескоструйная обработка – это механическое воздействие на поверхность мелких твердых частиц
Перед началом обработки абразив помещают в герметичный бункер. По основному шлангу аппарата под большим давлением подается воздух, поступающий от отдельного компрессора. Проходя мимо отверстия заборного рукава, поток воздуха создает в нем вакуум, что и способствует всасыванию в основной шланг абразива. Уже смешанный с абразивом воздух поступает к пистолету, основным элементом которого является сопло пескоструйное, через которое абразивная смесь подается на обрабатываемую поверхность.
Схема участка пескоструйной обработки
Как уже говорилось выше, для выполнения пескоструйной обработки могут использоваться различные типы абразивных материалов. Выбор здесь зависит от типа поверхности, которую необходимо очистить. Так, обработка с использованием песка эффективна в тех случаях, когда необходимо удалить слой старой краски с бетонной поверхности, очистить кирпичные стены от остатков цемента, подготовить металлические детали к дальнейшей покраске. Такие абразивы, как пластик или пшеничный крахмал, успешно применяют в судостроительной, автомобильной и авиастроительной отраслях, с их помощью эффективно удаляют старые покрытия с композиционных материалов.
Конструктивные особенности сопла для пескоструйного аппарата
Основными параметрами сопла, устанавливаемого на пескоструйный аппарат, являются:
- диаметр и тип отверстия;
- длина;
- материал изготовления.
Абразивоструйные сопла различных конфигураций
Диаметр отверстия в сопле, которое фиксируется на пескоструйном аппарате посредством специального соплодержателя, выбирается в зависимости от того, какой производительностью должно обладать устройство. Производительность любого пескоструйного аппарата – как серийного, так и сделанного своими руками – зависит от мощности струи или объема воздуха, который в состоянии пропускать сопло в единицу времени.
Мощность струи, которую формирует сопло, прямо пропорциональна объему воздуха, который проходит через него в единицу времени. Соответственно, чтобы увеличить мощность пескоструйного аппарата, необходимо сделать в его сопле отверстие большего диаметра. Например, можно оценить мощность сопел, отверстия в которых имеют разные диаметры. Если сопло, диаметр которого соответствует 6 мм (1/4 дюйма), имеет мощность, равную 100%, то изделия с отверстиями больших диаметров будут отличаться следующей величиной данного параметра:
- 8 мм (5/16 дюйма) – 157%;
- 9,5 мм (3/8 дюйма) – 220%;
- 11 мм (7/16 дюйма) – 320%;
- 12,5 мм (1/2 дюйма) – 400%.
Чтобы еще лучше ориентироваться в мощности сопла с тем или иным диаметром внутреннего отверстия, можно принять во внимание, что изделия, диаметр в которых составляет 6 мм (1/4 дюйма), способны обеспечить среднюю мощность струи, равную 30 м3/час.
Таблица позволяет примерно оценить влияние диаметра сопла и давления воздуха на производительность и расход абразива
Если вы не собираетесь изготавливать сопло для аппарата пескоструйной обработки своими руками, то следует иметь в виду, что изделия, выпускаемые серийно, имеют стандартные диаметры отверстий, равные 6, 8, 10 и 12 мм.
На выбор такого параметра сопла, как его длина, оказывает влияние степень загрязненности очищаемой поверхности. Для пескоструйной обработки поверхностей, которые имеют незначительные загрязнения, выбираются более короткие сопла (7–8 см). Если же необходимо обработать поверхность, на которой имеются сложные загрязнения, длина сопла должна быть значительной (до 23 см). Более короткие сопла, устанавливаемые в стандартный соплодержатель, используются и в тех случаях, когда обработке требуется подвергнуть труднодоступные места.
Сопла, диаметр которых не изменяется по всей их длине, позволяют обеспечить скорость выхода абразивного материала 320 км/час, при этом давление смеси из воздуха и абразива, поступающей из такого сопла, составляет 6 атм. Сопла с каналом «Вентури» формируют струю абразивной смеси, скорость движения которой может доходить до 720 км/час. Понятно, что сопла с внутренними отверстиями такого типа повышают эффективность пескоструйной обработки.
Очевидно, что площадь потока у сопла типа VENTURI значительно больше, чем у обычного прямолинейного
Использование сопел с внутренними отверстиями, выполненными по типу «Вентури», позволяет предприятиям и специализированным компаниям не только увеличить производительность своего труда, но и значительно повысить качество выполняемой обработки. Что важно, применение изделий с такими каналами не требует приобретения специальных абразивов и не приводит к увеличению расхода сжатого воздуха.
Если сопла с отверстиями обычного типа для пескоструйных аппаратов можно сделать своими руками (хотя это и сложно), то изделия с каналом «Вентури» качественно изготовить в домашних условиях, не располагая специальным оборудованием, практически невозможно.
Устройство сопла пескоструйного с каналом Вентури: d — внутренний диаметр; D — заходной диаметр; Т — присоединительная резьба; L — длина сопла
Для изготовления сопел, в том числе и своими руками, могут быть использованы различные материалы, от выбора которых зависит долговечность изделия. Так, в зависимости от материала изготовления сопла для аппаратов пескоструйной обработки обладают следующей долговечностью:
- керамические изделия, которые в домашних условиях делают из обычных свечей зажигания, – 1–2 часа;
- сопла из чугуна – 6–8 часов;
- изделия, для производства которых был использован карбид вольфрама, – 300 часов;
- сопла, изготовленные из карбида бора, – 750–1000 часов.
Если в качестве абразивного материала в пескоструйном аппарате используется не песок, а стальная дробь, то долговечность сопел любого типа увеличивается в 2–2,5 раза.
Как правильно выбрать сопло для пескоструйной обработки
Выбирая сопло для своего пескоструйного аппарата, учитывайте тот факт, что самые недорогие изделия являются и самыми недолговечными. Такие сопла в итоге обойдутся вам дороже качественной продукции, особенно если вам предстоит выполнить большой объем работ.
Пескоструйные износостойкие сопла из карбида вольфрама
Для бытовых целей подходят сопла из чугуна и керамики. Многие домашние умельцы даже самостоятельно изготавливают керамические сопла, используя для этого отработанные свечи зажигания. Для того чтобы из такой свечи сделать сопло, достаточно удалить из ее керамической оболочки металлический электрод.
Используя для пескоструйного аппарата чугунные и керамические сопла, следует иметь в виду, что из-за своего ускоренного износа они увеличивают расход как воздуха, так и абразива, поэтому их не рекомендуется применять при выполнении масштабных работ. Дорогостоящие сопла из карбида бора и карбида вольфрама отличаются не только высочайшей долговечностью, но также и тем, что их можно использовать практически с любым абразивным материалом, за исключением карборунда и окиси алюминия. Этим, собственно, и объясняется достаточно высокая стоимость таких сопел для пескоструйного аппарата, которые способны прослужить очень долго, не теряя своих характеристик, не увеличивая расход абразивного материала и воздуха.
Применение таких изделий целесообразно во всех ситуациях, когда требуется выполнить большой объем работ по очистке различных поверхностей.
Оценка статьи:
Загрузка.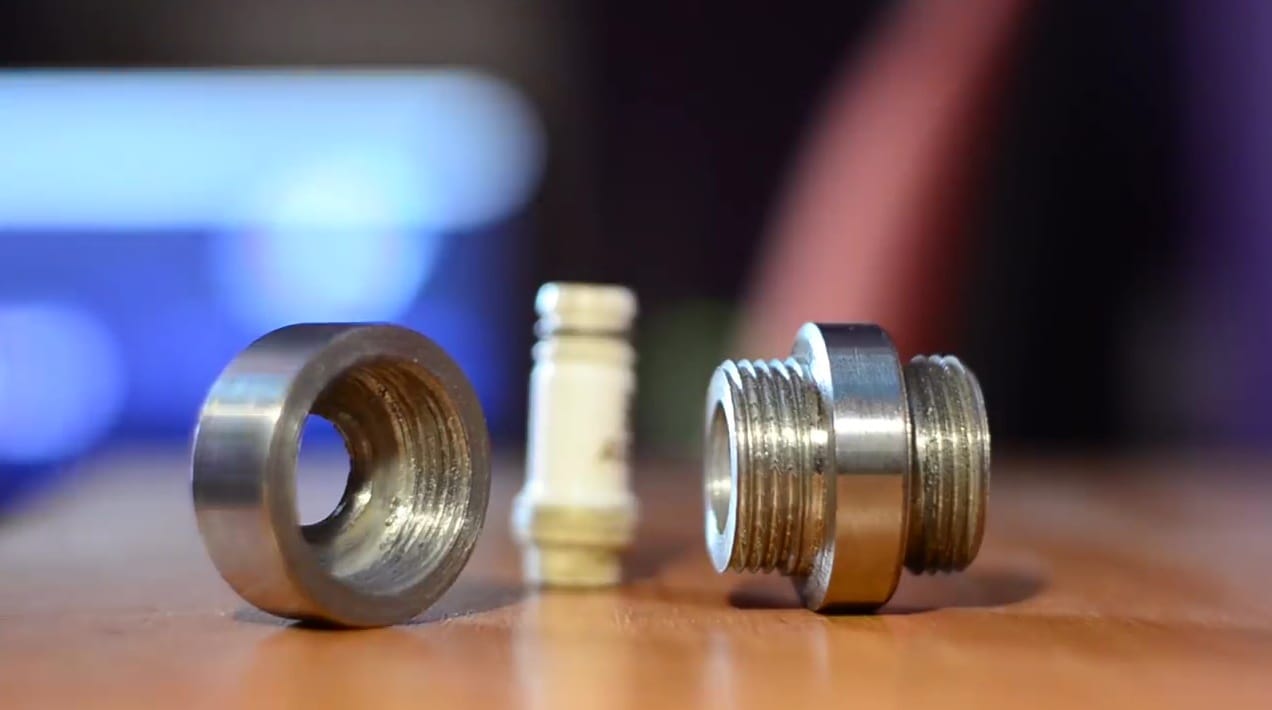
Поделиться с друзьями:
Как сделать пескоструй своими руками в домашних условиях: чертежи и этапы сборки
Обработка песком под высоким давлением позволяет быстро и эффективно очищать поверхности от загрязнений. Для этого применяется специальное устройство – пескоструй, использующийся как в автомастерских, так и в домашних условиях. Основной проблемой такого способа очистки является высокая стоимость оборудования и комплектующих. Если имеется свободное время и желание сэкономить, можно попытаться собрать аппарат самому. Для создания пескоструя своими руками нужен производительный компрессор, остальные части собираются из подручных материалов и элементов, которые легко найдутся в ближайшем хозяйственном магазине. Для работы также требуется изучение чертежей и четкое следование приведенным ниже инструкциям.
Принцип работы пескоструйного аппарата
Пескоструй работает по элементарной системе. Если сравнить чертёж простого аппарата для пескоструйки и базовых моделей краскопульта, наблюдается сходность конструкции. Нагнетённый воздух проходит по воздухопроводам и увлекает материал для абразивной обработки. Небольшие крупинки с большой скоростью направляются на поверхность, выбивая из неё частички.
Пескоструй самодельный разработать можно, а вот создать компрессор будет весьма сложно. Чтобы создать установку достаточного качества, рекомендуется покупать заводской компрессор, у которого будет производительность от 500 л/мин. Для избегания разрушения от перегрева, в нём должна быть устроена система охлаждения. Мощность установки от 3 кВт.
Пескоструй самодельный из ресивера Камаза
Самый простой аппарат – пескоструйный пистолет
Самодельная пескоструйка включает 2 основных элемента: рукоятку со специальным наконечником и 2 штуцера. Перед тем как сделать пескоструйный аппарат своими руками, рекомендуется купить сопло заводского производства. Через него выходит струя воздуха и абразивный материал. Вручную создать сопло приемлемого качества крайне сложно.
С учётом типа сопла изготавливают корпус, в дальнейшем с ним будет соединяться рукоятка и штуцеры. Простейший пескоструй своими руками изготавливают из фитингов водопроводного типа, пластиковой бутылки и тройника. Обязательно устраивается место для крепления шланга от компрессора со сжатым потоком воздуха.
Способ изготовления из краскопульта
Пескоструй можно сделать также и из краскопульта. Для сборки нужно подготовить:
- пистолет, выполняющий функцию смесительного клапана;
- рукоятку с устройством подачи воздуха;
- пластиковую бутылку, играющую роль бачка для абразива;
- тройник;
- шаровой кран для регулирования подачи песка.
Использование аэрографа вместо краскопульта позволит подавать абразив под более высоким давлением за счет меньшей толщины выходного канала.
Сборка выполняется в такой последовательности:
- Пистолет растачивается для увеличения диаметра выходной дюзы.
- Смесительный тройник присоединяется к пистолету.
- Устанавливаются и прикрепляются подающий и циркуляционный шланги.
Выброс абразива происходит после прижатия курка.
Объема небольшой пластиковой бутылки достаточно для очистки поверхностей в течение 30 минут.
Комплектующие для самодельной пескоструйной установки
Перед тем как собирать такое устройство, важно подготовить все комплектующие. Большая часть инструментов и расходных материалов обычно есть в каждой мастерской, но некоторые элементы понадобится купить в строительном магазине.
Начинать создание пескоструйной установки следует с установки ёмкости, в ней будет находиться абразивное вещество. Удобно использовать в качестве резервуара отработанный баллон для хранения газа. Он изготавливается из прочного, высококачественного металла, рассчитанного на большие нагрузки. Баллон герметичный, соответственно, в него сложно вносить абразивное вещество. Для облегчения процесса сверху вваривается небольшой кусок трубы. В неё засыпают материал, через горловину он попадает внутрь.
Отработанный баллон для хранения газа
Важно с осторожностью разбирать ёмкость, так как в старых газовых баллонах чаще всего есть остаток газа.
Наибольшее влияние на качество пескоструя оказывает правильный выбор компрессора. Основная проблема – дороговизна такой установки. Заводские варианты с достаточной мощностью обойдутся дорого, снижая эффект экономии. Альтернативный вариант – сделать своими руками из недорогих комплектующих.
Собрать устройство в домашних условиях можно с помощью компрессорных головок, устанавливаемых на пневмопривод ЗИЛа или МАЗа. Мощности установки с указанными комплектующими будет достаточно для обработки любых автомобильных запчастей. Головки обязательно комплектуются ресивером. Для сокращения расходов его изготавливают из баллона для хранения сжиженного газа. Дополнительно потребуется электрический мотор с приводом и рама для крепления всех элементов.
Перед тем как самому сделать пескоструйный аппарат, следует подготовить:
- краны шарового типа. Они надёжны и долговечны, для уверенности в качестве рекомендуется покупать изделия известных производителей;
- шланг из резины с армированной вставкой от Ø14 мм.
Важно покупать прочный вариант, который способен выдержать повышенное давление и влияние абразива;
- шланг для подачи газа. По нему будет поступать воздух в сжатом состоянии. В месте его установки мелкие крупицы отсутствуют, следовательно, диаметр меньше – от 10 мм;
- штуцеры для фиксации шлангов с другими компонентами системы. Пригодятся и цанговые зажимы;
- ФУМ-лента – она будет использована для создания целостного соединения всей конструкции установки, особенно участков, работающих под давлением.
Фум лента 0.2ммх19ммх15м Sigma
Подобная пескоструйка своими руками без компрессора обойдётся около $35. Экономия существенная, позволяет сохранить большую часть стоимости нового аппарата. Теперь следует переходить к созданию самодельной пескоструйки.
Гидропескоструйка
Гидропескоструйная обработка может производиться регулярно в обычных гаражных условиях или на площадке, с использованием также обычных СИЗ. Кузова старых автомобилей после очистки гидропескоструем вполне пригодны под покраску; удаление площадки или мастерской от указанных выше объектов – от 50 м. Гидропескоструй задействуется без компрессора от портативной автомойки или бытовой «брызгалки» для окон и витрин. Поэтому гидропескоструйной обработке следует уделить особое внимание.
Схема устройства гидропескоструйной установки с приводом от портативного моечного аппарата дана слева на рис.:
Схема устройства гидропескоструйной установки и простая насадка для гидропескоструйной обработки
Чертеж простейшей насадки из деталей водопровода для гидропескоструя – справа; на врезке – ее внешний вид. Принцип действия эжекционный. Однако такая насадка с одними мойками работает, с другими – нет, а пределы регулировки плотности струи и расхода абразива и с подходящим приводом недостаточны. Причина – косая сосредоточенная подача абразивовоздушной смеси в эжектор.
Стабильно работает с любыми авто- и бытовыми моечными установками насадка с коаксиальной подачей воды и абразивовоздушной смеси. Напр., насадка, чертежи которой даны на рис., первоначально разработана для автомойки Кёрхер. Но она годится и для любой другой с резьбой под штатный наконечник G1/4”. А если штатная посадка другая, то достаточно сделать присоединительное гнездо под нее (см. поз. 1).
Чертежи универсальной гидропескоструйной насадки для портативных моечных аппаратов
Примечание: вкладыш сопла из карбида бора (поз. 4) – готовый покупной. Может быть заменен другим, прямым или Вентури; в таком случае диаметр его сужения («горлышка» сопла Вентури – 4,5-6 мм).
Как сделать гидропескоструйную насадку к портативной автомойке, см. также ролик:
Пескоструйная камера
Если пескоструить большие детали, появляется проблема – быстрый расход абразива, большая его часть используется неэффективно, так как разлетается в стороны. Увеличить эффективность прибора позволит особая камера, которая имеет вид ящика, сваренного из металлических листов. Конструкция удобна для обработки небольших деталей автомобиля.
Изготовление камеры является затратной процедурой с точки зрения времени и сил, но оборудование реально сделать даже без особых навыков. Помимо простой конструкции сварного блока, в корпусе устанавливается стекло для контроля над процессом. Спереди просверливается 2 отверстия, к ним фиксируются перчатки несъёмного и грубого типа. Дно изготавливают из решётчатого металла или проволоки. Под дном размещают желоб для отвода использованного материала. Пистолет находится внутри. Для облегчения работ с камерой в неё устанавливают освещение и вентиляцию.
Готовое изделие устанавливают на стол. Инструкция по проведению работ раскрыта в видеороликах в сети.
Пескоструйные аппараты напорного типа
Специалистами разработана схема самодельной напорной установки. Для выполнения работ пригодится бочка из металла, с которой срезается днище. Внутрь устанавливают конус, а снизу крепят затвор и тройник для подключения компрессорного шланга и рукава с соплом.
Передвижной пескоструйный аппарат напорного типа
Гравирование стекла с помощью пескоструйного аппарата
Самый простой способ – использовать обдувочный аппарат с абразивом. Процесс выполняется пошагово:
- Изначально на стеклянную поверхность наносят самоклейку.
- На плёнке рисуют желаемое очертание или рисунок и с помощью строительного ножа вырезают его.
- Незащищённую поверхность обрабатывают пескоструем.
- Плёнка демонтируется, оставляя только выделенное изображение. Оно должно получиться ярким и чётко различимым.
Мастер вручную регулирует желаемую глубину рисунка, по необходимости обрабатывает поверхность 2-3 раза. Даже в подобном виде гравировка придаёт интересный и оригинальный вид, но по желанию к ней добавляют светодиодную ленту. Если сравнивать обычную пескоструйку и профессиональное оборудование, принципиальной разницы видно не будет.
Самый простой аппарат в силах вырезать отверстия в стекле, но для чёткой формы прорези потребуется оградить участок с помощью металла. В листе прорезают отверстие и накладывают на обрабатываемую поверхность. Прорезь внутри является формой для нужного отверстия в стекле. Процедура потребует некоторой выдержки, для создания 1 отверстия уходит около 5 минут и 1 л песка. В результате получают качественную, дешёвую и гладкую прорезь в стекле.
Гравирование стекла с помощью пескоструйного аппарата
Сборка пескоструйного аппарата
Пескоструйный аппарат своими руками требует чертежей, наличия электроинструмента и подготовки материала.
Самый первый этап – это работы с баллоном, из которого поступает абразив. Идеально подойдёт резервуар, который содержал фреон, но другие типы тоже сгодятся. Работы с баллоном:
- С помощью ручной ножовки постепенно и аккуратно срезают латунную насадку.
- Для создания безопасных условий в работе со сварочной установкой потребуется удалить остатки газа из ёмкости. Компрессор без труда выдует его.
- После окончательной очистки просверливают 2 отверстия: снизу для удаления остатка материала и сбоку для поступления абразива к установке.
- В отверстия вводят и приваривают патрубки, они пригодятся для соединения с другими компонентами системы.
Предпочтительно использовать патрубки с наконечниками для резьбы. От мастера требуется создание герметичного контура.
- Для создания мобильности установки и удобства транспортировки к низу привариваются маленькие колёса. Если не планируется перевозить конструкцию, рекомендуется устанавливать треногу.
- По желанию баллон оснащается вибратором, который будет воздействовать на ёмкость и разбивать комки материала. Использование станет более эффективным, и снизится частота забивания патрубков.
Чертеж пескоструйного аппарата
После изготовления резервуара, согласно чертежу, соединяют все элементы:
- На окончания труб фиксируются краны. Соединения осуществляются с помощью резьбы, а герметичность достигается ФУМ-лентой.
- Штуцеры монтируются на выходы тройника: на один шланг 14 мм, второй – 10 мм, но перед его фиксацией вставляется трубка из меди.
- На штуцер 14 мм надевают шланг (закрепляется хомутом), а с другой стороны устанавливают ёмкость для абразива.
В конце устанавливается зажим цангового типа для фиксации сопла.
- В отверстие для воздуха монтируется тройник, затем кран для загрузки песка.
- На первый выход монтируют шланг от компрессора, а во второй – рукав от ёмкости.
- Для управления силой потока в систему вводят специальные дозаторы и краны.
Что такое пескоструй?
Как очистить металл от ржавчины, окалины, наслоений старой смазки, нагара? А если не металл, а дерево или бетон? Специальные химические очистители можно использовать не везде и не всегда, и приходится тереть поверхность наждачкой, металлическими щетками, а затем любоваться сеткой из мелких и не очень царапин.
Альтернативой такой обработке становится пескоструйная очистка. С ее помощью можно без особых проблем убрать с поверхности различные загрязнения, причем обработанный участок очищается гораздо быстрей и эффективней, а грязь удаляется даже из пористого материала (например, с древесины или бетона).
Другой вариант использования пескоструйных аппаратов – работа по дереву или стеклу. Имея определенные навыки, можно делать великолепные витражи с выборочным матированием, гравюры и рельефные узоры.
Пескоструйная машина – это достаточно простой по своему принципу аппарат. Он дает мощный поток воздуха, смешанного с абразивом (обычным песком). Обрабатывать им можно как большую площадь, так и сложные детали со множеством мелких элементов. Поток песка отлично убирает любые наслоения грязи, окислов и нагара, оставляя чистую поверхность без царапин.
Когда пескоструйная машина нужна регулярно, а покупать ее не хочется (чаще всего по финансовым причинам), можно сделать ее своими руками.
Рекомендации специалистов
Все вероятные проблемы с аппаратом сводятся к неграмотному изготовлению установки. При правильном подборе элементов и аккуратной сборке качество устройства будет несущественно уступать серийным моделям.
Несколько дополнительных советов:
- можно включить систему рециркуляции потока воздуха.
Она значительно повысит эффективность работ с аппаратом;
- наибольшее внимание следует уделять выбору сопла и компрессора. Обычное сопло не подходит для пескоструйной установки, рекомендуются вольфрамовые варианты. В зависимости от типа сопла, абразива и обрабатываемой поверхности отличается вид компрессора;
- до окончательной сборки важно проверить герметичность соединений. При малейшем отверстии в баллоне существенно сократится мощность установки.
Самостоятельное изготовление конструкции позволяет сократить расходы в 3–5 раз. Максимальная экономия наступит при использовании самодельного компрессора, но в нём сложно добиться достаточной мощности. Оптимальный вариант – заводской компрессор и самодельный пескоструйный аппарат с баллоном.
Виды пескоструев
Существуют разные виды пескоструев, каждая из которых отличается принципом работы и конструкцией:
- Вакуумные модели. В конструкции такого аппарата присутствует специальная камера, в которую засасывается отработанный абразивный материал для повторного использования.
Нельзя использовать кварцевый песок дважды. Он разбивается в кристаллическую пыль, которая вредна для здоровья.
- Всасывающие модели. Конструкция пескоструйного аппарата идеально подходит для сборки своими руками. Воздух захватывает частицы песка и несёт их к соплу.
- Пневматические модели. Промышленное оборудование, которое предназначено для обработки больших поверхностей. Используются огромные мощности.
Обзор и виды пескоструек.
Всасывающие аппараты считаются самыми популярными и без труда собираются в домашних условиях.
Работа на промышленном пескоструе
Пескоструй своими руками | Компания «БластАнтикор»
Существует два типа классического пескоструйного оборудования — напорного и инжекторного (эжекторного) типа.
Напорный тип — абразив давлением сжатого воздуха из емкости подается по шлангу к соплу, разгоняется в нем и двигается на обрабатываемую поверхность. Это оборудование относится к промышленному, профессиональному и предполагает наличия мощного компрессора (от 5000 литров в минуту), хорошей организации труда и т. п. Это необходимо для обработки мостов, вагонов, кораблей. Такое оборудование предназначено для выполнения больших заказов и объемов.
Инжекторный (эжекторный) тип — абразивный материал засасывается в рукав из открытой емкости благодаря конструкции пистолета. В нем он подхватывается воздушной струей сжатого воздуха и подается в пескоструйное сопло, а уже из него выбрасывается на обрабатываемую поверхность. Вот его-то и будем делать своими руками.
Что для этого понадобится?
1. Инжекторный пистолет.
Если стоит задача отпескоструить легковую машину, то с ней он справится. Если необходимо оказывать услуги по пескоструйной очистке, т.е. будете пользоваться им периодически и не один раз, то стоит задуматься о покупке промышленного пистолета.
Его отличие от одноразового пистолета состоит в материалах изготовления. Сопло воздушное, как правило, делают из инструментальной стали с закалкой либо покрывают износостойким материалом, например полиуретаном. При правильном использовании оно прослужит так же долго, как и пескоструйное. Одноразовые пистолеты не позволяют поворачивать воздушное сопло, и оно быстро изнашивается. Изделие пескоструйное сделано из карбида бора (вернее его внутренняя часть — вставка), и за счет этого имеет повышенную износостойкость. Работоспособность может составлять до 1500 часов непрерывно.
2. Рукав соединения от компрессора до пистолета пескоструйного. Он может быть небольшого сечения (около 9 мм внутреннего диаметра), который можно подсоединить непосредственно от самого компрессора до пистолета пескоструйного. Никаких дополнительных кранов не нужно. Очень часто при использовании поршневых компрессоров имеется очень плохое качество сжатого воздуха. В таких случаях необходимо производить воздухоподготовку. Для пескоструйных работ требуется класс воздуха 13. В принципе это самый простой класс очистки. Отличительная его черта — отсутствие влаги и масла. Другие же классы воздуха не предполагают наличие каких-либо механических примесей.
3. Рукав всасывающий от пистолета до емкости с абразивом. Чем он короче, тем легче абразив будет засасываться. Рекомендуется использовать рукав, длиной не более 3 метров. Диаметр используется 3/4″, т.е. по российским стандартам ДУ20.
Тип рукава должен быть для пескоструйных работ. Можно конечно любой другой, но в таком случае его нужно будет менять раз в неделю.
4. Заборный патрубок. Все дело в том, что если вставить обратный конец рукава в емкость с песком или просто воткнуть его в кучу песка, то забор абразива (его всасывание) происходить не будет. Необходимо сделать подсос воздуха. Берем трубку, по наружному диаметру равную внутренним параметрам всасывающего рукава, прорезаем в ней отверстие и одеваем кусок шланга. Таким образом, при открытии отверстия образуется большой поток воздуха и малый поток всасываемого абразива, а при закрытии всасывание абразива прекратится. Т.е. необходимо прикрывать отверстие до тех пор, пока поток воздушно-абразивной смеси станет равномерным (без пульсаций).
После того как все комплектующие собрали вместе, должно получиться что-то подобное:
Принцип работы очень простой. Открыв кран на пистолете, в его корпусе начнет создаваться разрежение, при помощи которого по пескоструйному рукаву абразив начнет засасываться в пистолет.
Благодаря такому устройству можно произвести пескоструйную обработку с производительностью до 3 кв. м/час.
Примеры работ с подобным устройством — очистка тонколистового металла от старого ЛКП и ржавчины, матирование стекла, искусственное старение дерева.
Расход воздуха зависит от диаметров установленных воздушного и струйного сопел. Посмотреть таблицу с расходами можно здесь >>>
Пескоструй.
Как сделать пескоструй (пескоструйный аппарат) своими руками.
Те мастера, которые хоть раз в жизни пробовали зачистить остатки краски или ржавчину вручную, или даже с помощью болгарки, понимают как это не просто осуществить, особенно в труднодоступных местах, или когда площадь зачищаемого участка металла велика. А кому приходится зачищать детали от коррозии довольно часто, например при ремонтных работах кузова или рамы перед покраской, или кто занимается антикварными машинами, мотоциклами, начинают понимать, что без пескоструйного аппарата в своей мастерской далеко не продвинешься. Некоторые покупают заводские аппараты, но для многих начинающих мастеров и не раскрученных мастерских, цена их довольно высока. В этой статье мы рассмотрим как изготовить вполне работоспособный пескоструйный аппарат своими руками, без особых затрат.
Вообще, прежде чем начать собирать пескоструйный аппарат, нужно приобрести необходимый для этого компрессор, который обязательно должен иметь принудительное охлаждение (так как работать он будет без остановки). А чтобы не ошибиться с его выбором, для начала желательно определиться, что вы собираетесь пескоструить — какую то мелочёвку, или всё же рамы и кузова машин.
Это важно, так как для обработки мелочёвки можно обойтись небольшим компрессором (о компрессорах и какие они бывают читаем вот тут), который выдаёт примерно 250 — 350 литров в минуту, и китайским инжекционным пескоструйным пистолетом (с керамическим соплом), хотя бы таким как на фото слева.
Если же вы собираетесь пескоструить что то более крупное, хотя бы колёса, рамы или особенно кузова машин, тогда вам следует изготовить свой «пистолет» (держатель сопла) для более серьёзного пескоструя, и кроме этого обратить особое внимание на выбор компрессора, то есть на данные опубликованные мной ниже, которые вам помогут определиться с выбором.
И хотя данные опубликованные ниже примерные, но они всё же позволят вам не ошибиться с выбором компрессора при покупке, ведь лучше подкопить ещё денег, но купить более производительный компрессор. Это позволит вам работать быстро и эффективно (без перерывов), то есть в процессе работы не ждать, когда компрессор восстановит необходимое давление в ресивере.
- Детали — свечи зажигания, болты, гайки, крышки бензобака и др. подобные мелкие детали — нужен компрессор производительностью от 300 до 500 литров в минуту, и ресивер (баллон) ёмкостью не менее 50-70 литров .
- Детали — колёса мотоциклов или автомобилей, или вилки, рамы мотоциклов — компрессор производительностью не менее 500 литров в минуту и ресивер не менее 100 -200 литров.
- Детали — рамы автомобилей, кузова автомобилей, цистерны и т.п. — компрессор производительностью 1000 литров в минуту и более, и ресивер емкостью 200 — 500 литров, более не помешает.
Следует учесть, что при пескоструе рам и кузовов, чем больше будет компрессор и ресивер, тем лучше. Ведь имея компрессор производительностью 500 л/мин, с ресивером на 100 литров, и имея сопло на выходе песка диаметром 4 мм, воздух с такого ресивера стравится с давления 8 бар (кг/см²) до давления 2 — 1,5 бара всего за каких то 35 — 45 секунд. Хотя при давлении воздуха в 1,5 бар вполне нормально пескоструить детали, ведь постоянно работающий компрессор в 500 л/мин не даст давлению упасть ниже 1,5 бар при диаметре сопла в 2,5- 3 мм.
Но вот при установке сопла диаметром 4 мм, которое более предпочтительнее, давление может падать ниже и придётся делать небольшие перерывы. И хотя такие перерывы обычно не долгие, и они позволяют немного рассеяться пыли, но всё же больший ресивер и компрессор никогда не помешает. Так как особо стойкие покрытия металла (толстый слой краски и т.п) наиболее эффектно очищать при давлении более чем 1,5 — 2 бара (кг/см²), и поэтому при очистке стойких покрытий, придётся ждать пока давление немного подрастёт (закрывая кран пистолета и делая перерывы).
И поэтому если вы собираетесь профессионально пескоструить кузова машин и зарабатывать на этом, то всё же советую арендовать бокс где нибудь на предприятии, в котором имеется трёхфазная сеть на 380 вольт, а не однофазная на 220 вольт, и объясню почему.
Дело в том, что большинство не больших компрессоров производительностью до 500 л/мин имеющихся в продаже (такой как на фото слева), рассчитаны на сеть в 220 вольт, a вот компрессоры производительностью более 500 л/мин, на 220 вольт вы не найдёте. То есть для эффективного пескоструя кузовов машин, потребуется компрессор на 800 — 1000 л/мин (и больше), но все они рассчитаны только на трёхфазную сеть 380 вольт.
Можно конечно купить такой и переделать его на однофазную сеть 220 вольт (как это сделать читаем вот тут), но мощность электродвигателя после переделки упадёт примерно на 40 %. А кроме этого, вам в гараже нужно будет переделать полностью электропроводку (сделать толще сечение проводов)), так как у компрессоров производительностью более 500 л/мин, электродвигатель имеет мощность более 3-х киловатт.
И при подключении даже переделанного под 220 вольт компрессора производительностью 800 — 1000 л/мин, у которого электромотор имеет 4 — 5 киловатт и более, может начать плавиться штатная гаражная проводка, которая не рассчитана на такую нагрузку. Всё это следует учесть и только когда определитесь с компрессором и его установкой (подключением), только после этого можно начинать изготавливать сам пескоструйный аппарат, о котором ниже.
Есть ещё один вариант для профессионального пескоструя кузовов, на который следует обратить внимание и который позволит получить большую производительность. Покупается большой бэушный советский четырёхцилиндровый компрессор, которых ещё достаточно полно на заброшенных (обанкротившихся) предприятиях, такой, как на фото слева (их раньше называли САК и использовали даже для отбойных молотков, при дорожных работах на выезде).
После покупки он отмывается, перебирается, то есть восстанавливается его поршневая группа (новые детали не так просто найти, но не беда — восстановить поршневую можно с помощью препарата, описанного вот тут), заменяется масло и т.д. При наличии у вас в боксе трёхфазного напряжения в 380 вольт, проблем с его подключением не возникает.
Ну а что делать тем мастерам, у которых в гараже однофазная сеть 220 вольт, бокс снять негде или дорого, но попался такой мощный компрессор за приемлемые деньги. Можно купить его без электродвигателя, который вам не понадобится, что обойдётся намного дешевле, так как электромоторы от от 10 до 20 киловатт стоят не мало.
Далее ищете на ближайшей авто-разборке экономичный дизельный двигатель от какой то иномарки (можно даже от микролитражки), такой мотор можно найти на разборке не дорого, особенно если он без документов. Теперь остаётся подключить такой дизель через ременную передачу, или через резиновую муфту к компрессору, и причём оставив родную коробку передач. И благодаря коробке, можно будет переключая её на нужную скорость, выбирать обороты компрессора, в зависимости от объёма пескоструйных работ.
Конечно электричество дешевле чем дизельное топливо, но этот вариант тоже неплох, и при пескоструе кузовов машин, он всё равно себя окупит. Причём такая установка не зависит от того есть ли свет или нет, и её впоследствии можно будет сделать мобильной. То есть установить на прицеп и уже профессионально пескоструить большие объекты на выезде (например если у клиента машина не на ходу, а нужно отпескоструить её кузов, или цистерны, металлические гаражи и т.п.).
Изготовление пескоструйного аппарата (пескоструй).
Начинать изготовление советую с поиска подходящей ёмкости для песка. Хорошо подойдут для этого баллоны от фреона, пропана, или просто воздушный ресивер (баллон) от воздушной тормозной системы какого то грузовика. Когда найдёте баллон, его естественно следует доработать.
В самом низу баллона, отступив пару сантиметров от сварного шва, нужно отрезать его дно. Если найдёте баллон от пропана, прежде чем резать дно болгаркой, стравите остатки газа, затем выкрутите вентиль вверху и заполните его водой до верху (это предотвратит пожар от искр от болгарки и остатков газа). Когда отрежете дно, прежде чем варить электросваркой, хорошенько пропарьте баллон изнутри паром.
Далее следует сделать (свернуть) из листового металла конус и приварить его вместо нижней отрезанной части баллона. Следует учесть, что чем острее (выше) будет конус, тем лучше — это не позволит песку оставаться внизу на стенках, и он будет полностью расходоваться. Если же не делать конус, то при работе песок будет постоянно лежать по бокам внутри баллона (на его внутренних стенках), а в центре будет небольшая дыра, и придётся постоянно делать перерывы в работе и трясти баллон с песком.
Когда обварите конус, приварите снизу конуса кусок дюймовой трубы, длиной примерно 5 см, на конце которой нарезана резьба. На эту резьбу накрутите дюймовый шаровый кран и закройте его (можно использовать кран на 3/4). Кому удастся раздобыть или изготовить плоский шиберный кран, вместо обычного сантехнического шарового крана, то ещё лучше, такой ставят на заводских профессиональных пескоструйных аппаратах. Затем приварите к баллону три или четыре ножки, которые позволят ему стоять вертикально. Причём чем выше эти ножки, тем лучше.
Наличие острого конуса внизу баллона, позволяет работать по более простой схеме (см схему на рисунке слева) не подавая давление воздуха в баллон с песком дополнительным отводом — шлангом, по которому подводят давление воздуха к верху баллона (как сделано почти у всех), так как песок и так неплохо поступает самотёком.
Если же конус не делать, тогда придётся внизу баллона, перед Т-образным смесителем вкручивать через муфту ещё один Т-образный тройник (см фото слева), от которого нужно будет отводить шланг и подсоединять его вверху баллона, чтобы нагнетать давление в баллон с песком.
И причём даже наличие давления воздуха в баллоне с песком, не гарантирует его нормальную подачу (всё равно песок на стенках будет оставаться), а вот наличие конуса даст гарантию отличной подачи всего песка. Да и при наличии конуса, заморачиваться с дополнительным Т- образным тройником и шлангом не нужно.
После этого, в самой верхней части баллона следует вырезать большой корончатой фрезой отверстие диаметром примерно 50-70 мм, и вварить в это отверстие кусок трубы с резьбой вверху (горловина), на которую накручивается резьбовая крышка (закажите токарю). Под крышку вырежьте из листовой резины толщиной 3-4 мм кружок, который сделает крышку герметичной. В эту горловину будет засыпаться песок, который естественно перед засыпкой нужно просеять через сито, чтобы отделить его от камешков и прочего мусора.
Ещё полезно наварить сверху на крышку кусок прутка или пластину (см фото слева), которая позволит плотно закрутить крышку руками, после засыпки песка в баллон. Недалеко от крышки (сбоку от неё) просверлите отверстие в верхней части баллона и приварите к этому отверстию втулку, с внутренней полдюймовой резьбой на конце.
На резьбу накрутите полдюймовый шаровый кран (или клапан для спуска воздуха как на фото слева), который нужен будет впоследствии для стравливания воздуха.
После сварочных работ, установите баллон на ножках вертикально, залейте в баллон воды и убедитесь, что все сварные швы герметичны и нигде не течёт. Затем откройте кран и слейте воду. Можно проверить герметичность и без воды, если вкрутить в полдюймовый кран (тот который для стравливания воздуха) штуцер для шланга и закачать с компрессора небольшое давление (обычно хватает 1 — 1,5 бар). После этого сварочные швы промазываются кисточкой с мыльной водой, и утечка воздуха обнаруживается по мыльным пузырькам.
Другие детали пескоструя.
Подбор деталей описанных ниже, рассчитан на нормальную работу пескоструйного аппарата, совместно с компрессором производительностью не менее 500 л/мин.
После сварочных работ можно подсоединять к баллону другие детали, показанные на схеме выше. Внизу конуса к дюймовому шаровому крану прикручивается через переходник Т-образный смеситель (см. фото слева), который можно купить там же где и краны — в магазине сантехники.
А с обоих концов в Т-образный смеситель вкручиваются два штуцера под шланги: один шланг от компрессора до смесителя, а второй шланг от смесителя до держателя сопла.
Здесь следует учесть важные нюансы, благодаря которым ваш пескоструй будет работать без проблем с подачей песка, а именно — внутренний диаметр штуцеров под шланги и внутренний диаметр самих шлангов должен быть не менее 16 мм, а лучше всего 18 мм. Это касается и внутренних диаметров используемых кранов и штуцеров.
И именно поэтому нельзя использовать так называемые «быстросъёмы», которые используют маляры, так как они имеют маленький внутренний диаметр (не более 10 мм). Шланги поищите в продаже на тканевой основе (резина армированная капроновыми нитками), такие намного прочнее обычных.
Ещё один важный момент — шланг от Т-образного смесителя (под конусом баллона) до держателя сопла («пистолета») должен быть как можно короче, то есть не более трёх метров, это я написал на схеме выше (с такой длиной, вполне можно работать, но чем меньше, тем лучше), тогда проблем с подачей песка у вас не будет.
А шланг от ресивера компрессора до Т-образного смесителя может быть намного длиннее, вплоть до 8 — 10 метров, тогда можно будет держать компрессор в отдельном помещении и это существенно сократит ваши расходы на воздушный фильтр (ведь пыли очень много при работе), да и вообще существенно увеличит ресурс поршневой группы компрессора.
Шланг, а точнее его штуцер к ресиверу (точнее к крану ресивера) лучше подсоединить через быстросъёмную гайку, называемую у сантехников «американка», чтобы можно было быстро отсоединить пескоструйный аппарат вместе с шлангом от ресивера (компрессора), когда он не нужен. Ведь компрессор в любой мастерской используется не только для пескоструя, но ещё и для покраски, пневмоинструмента и т.д.
Держатель сопла.
После того, как найдёте и подсоедините шланги соответствующих диаметров, останется сделать сам держатель сопла, ну и само сопло. Основа «пистолета» (держателя сопла) всё тот же шаровый кран на 3/4 дюйма, с внутренним диаметром проходного отверстия 20 мм. Кран позволит в любой момент перекрыть доступ к соплу, если например нужно сделать небольшой перерыв, или если упало давление в системе.
Кран с одной стороны «мама» — то есть имеет внутреннюю резьбу, в которую вкрутите штуцер, под 3-х метровый шланг от смесителя (баллона с песком). Не забываем, что диаметр штуцера и шланга должен быть не менее 16 — 18 мм, то есть в четыре раза больше диаметра сопла.
На другом конце крана — «папа», то есть наружная резьба, на которую нужно накрутить накидную гайку, которая будет прижимать сопло к крану, но можно использовать и переходник, если в кране не наружная, а внутренняя труба.
Если хотите, чтобы было удобнее держать так называемый «пистолет » в руках (что бы он был немного длиннее), то после крана следует накрутить переходник из трубы с резьбой, а уже к переходнику накручивать накидную гайку, прижимающую сопло.
Сопло пескоструя.
Сейчас уже можно найти в продаже различные сопла, которые достаточно долговечны, начиная от керамики до карбида бора или карбида вольфрама, которые выдерживает около тысячи часов работы.
Но такие сопла стоят не дёшево и скорей подойдут для профессионального пескоструя, которым пользуются каждый день. И чем твёрже и долговечнее материал сопла, тем естественно они дороже.
Но когда пользуются пескоструйным аппаратом время от времени в гараже, то вполне подойдут более дешёвые керамические сопла, которые выдерживают примерно 100 — 150 часов работы. Но в большинстве некрупных городов купить нормальное сопло не так просто, и на вид многие китайские сопла вроде бы из керамики (непонятно какой), но хватает их примерно так же как и сопла из калёной стали — то есть на пару часов, да и по диаметру оно может быть не то что нужно.
Поэтому есть смысл самостоятельно изготовить сопло из настоящей керамики, которая используется на свечах зажигания. Берётся свеча (лучше советская), отрезается алмазным диском (для резки керамической плитки) металлическая часть, чтобы осталась лишь керамика.
При этом можно не отрезать железо свечи (её железный корпус), а немного сточить его болгаркой или на токарном станке, а потом развальцевать остаток металлического корпуса свечи, который удерживает керамику (см фото слева).
Это предпочтительнее, потому что при таком способе керамика сохраняется полностью, то есть со ступенчатым переходом на более толстый диаметр (см. фото ), и такую керамику удобнее будет прижать к «пистолету» (крану) накидной гайкой (без всяких резиновых прокладок).
Далее из керамики высверливается центральный электрод, и получается отверстие — сопло (см фото слева). Нам требуется сопло с внутренним диаметром 4 мм, этот диаметр наиболее оптимален для компрессора производительностью 500 л/мин, и шлангов с диаметрами описанными выше (16 — 18 мм).
Диаметр сопла больше 4-х мм не даст нормально работать с таким компрессором, так как давление будет часто падать ниже 1,5 бара и придётся делать частые перерывы. Поэтому диаметр сопла в 4 мм самое то.
Но обычные свечи зажигания при высверливании электрода из керамики, имеют диаметр 5 мм, значит нужно купить свечу от бензопилы, у которой диаметр центрального электрода имеет как раз 4 мм. Если у кого то компрессор более производительный, например 800 — 1000 л/мин, и более, то естественно можно использовать и керамику от автомобильной свечи, с диаметром сопла 5 мм.
Вариант бюджетного и долговечного сопла для пескоструя ещё лучше.
А есть ли вариант бюджетных самодельных сопел, но который ещё долговечнее сопел из свечей, описанных выше? Есть !!! Для этого варианта вам придётся поискать на барахолках, строительных рынках или в специализированных магазинах токарно-фрезерного инструмента твёрдосплавные пластинки, примерно такие как я публикую на фото слева.
Пластинки для сопла следует выбирать четырёх, пяти или шестигранные, но в идеале круглые (указаны стрелками, но не все).
В специализированных магазинах такие твёрдосплавные пластинки будут стоить существенно дороже, чем где нибудь на барахолке, но всё же собранное из пластинок сопло всё равно получится ощутимо дешевле какого то фирменного заводского, а по долговечности не особо отличается от фирменных сопел.
Так вот, покупать пластинки лучше всего с диаметром отверстий в центре 4 — 5 мм (внутренний диаметр отверстий в покупаемых вами пластинках конечно же зависит от мощности вашего компрессора), и покупать следует пластинки не треугольные, а четырёх, пяти, или шестиугольные, но лучше всего круглые (смотрите фото).
Так как такие пластинки будет удобнее собирать в пакет и вставлять в самодельный держатель сопла, у которого внутри цилиндрическое отверстие. Держатель следует заказать у токаря (если у вас нет токарного станка), а конструкция его настолько проста, что нет смысла даже публиковать чертёж.
Точится держатель сопла на подобии двух-составной трубки, внутренний диаметр которой следует высверлить таким, чтобы пакет пластинок вставлялся внутрь передней части трубки свободно, но и без ощутимого люфта. Так же в передней части трубки следует завальцевать её край, чтобы пластинки не вываливались наружу спереди, это если пластинки будут использоваться круглые.
А если же твёрдосплавные пластинки вы купили квадратные, или многогранные, то тогда лучше, не завальцевать, а выточить буртик-ступеньку, и отверстие (от ступеньки) на конце держателя должно быть чуть более отверстия в пластинке, то есть перекрывать грани квадратной пластинки (чтобы песок не проходил по бокам квадратной пластинки, а проходил лишь через отверстие в центре пластины — думаю с этим понятно).
Ну и задняя часть трубки должна выкручиваться (или вкручиваться) по резьбе, разделяя держатель сопла пополам, для того чтобы иметь возможность вставить пакет пластинок в переднюю часть трубки и затем вставив ещё одну трубку, чуть меньшего диаметра во внутрь, затем собрать обе части на резьбе и прижать пластинки задней частью и внутренней трубкой, чтобы они не болтались внутри держателя. Ну и на заднюю часть трубки держателя сопла следует надеть песок-подающий шланг и можно начинать пробовать работать.
Сколько пластинок вставлять в держатель зависит от того, сколько вам удалось их купить и от того, какую долговечность сопла вы хотите получить. Так как чем больше количество пластинок, тем долговечнее сопло, но как правило хватает пакета из 5 — 10 штук.
Как повысить эффективность пескоструйных работ?
Если вы хотите повысить эффективность пескоструйных работ, то есть сделать так, чтобы хорошо очищались наиболее толстые и стойкие загрязнения металла, то тогда следует повысить скорость потока песка на выходе из сопла, а как это сделать? Ведь сделанное из свечи сопло имеет одинаковый цилиндрический диаметр по всей длине, и скорость потока воздуха и песка у такого сопла составляет примерно 300 — 350 км/час. Такая скорость позволяет справляться с несильной коррозией, не толстым слоем краски и т.п.
Но вот сопла Вентури (см. фото выше и слева) позволяют отлично очищать даже толстые и стойкие слои на металле, так как скорость песка и воздуха на выходе из такого сопла, составляет в два раза большую скорость — примерно 700 км/час. А всё дело в том, что со стороны поступления песка и воздуха, в таком сопле имеется конус, и в самом сопле диаметр к выходу немного расширяется (см. рисунки) — это и позволяет скорости потока увеличиться на выходе.
Так значит и в керамике от свечи, со стороны входа желательно сделать конусное отверстие, и сделать это возможно, если есть бормашина и несколько тонких конусных насадок (боров) для неё — см фото слева. При растачивании сопла конусным бором, обязательно нужно поливать место обработки водой.
При высверливании конусов повозиться конечно придётся (в этом есть смысл, так как заводские сопла Вентури дорогие), но зато при работе с такими соплами, эффективность очистки намного улучшится. Можно например для особо стойких покрытий использовать сопла с конусом на входе (и выходе), а для обычного не сильно ржавого металла, в целях экономии пользоваться обычными цилиндрическими соплами.
Средства защиты при пескоструйных работах.
При работе с пескоструйным аппаратом очень советую не пользоваться респиратором, а использовать противогаз, особенно если вы работаете в помещении. Если же вы работаете на улице, то тогда всё таки можно не мучится с противогазом, а использовать качественный угольный респиратор от фирмы 3М (стоя при работе спиной к ветру), ну и естественно использовать защитные очки, плотно прилегающие к лицу.
При профессиональных каждодневных работах, очень советую купить маску с автономной подачей воздуха от компрессора (как на самом верхнем фото), на которой к тому же должно меняться стекло, которое со временем будет терять прозрачность от пыли. И хотя автономная маска от авторитетных производителей стоит не дёшево, поверьте, она окупится, ведь лекарства очень дорогие, а здоровье человека вообще бесценно.
Со временем советую потратится на металлический уголок и лист, и сделать камеру для пескоструйных работ (см. фото слева). Такая камера очень удобна, и к тому же под нижний конус можно подложить ведро для песка и воткнув туда шланг от китайского пистолета, использовать песок по кругу (можно до пяти раз).
И если вам часто нужно работать с мелочёвкой, то есть смысл потратиться на изготовление такой камеры, да и пескоструйный аппарат можно в таком случае не использовать, а пользоваться только специальным пистолетом с бачком (как на фото в начале текста). Сейчас уже можно найти в продаже модели, которые довольно неплохо очищают мелочёвку.
Вверху камеры полезно сделать такой же конус как и снизу (см. фото слева), только к верхнему конусу подключается труба от вытяжной вентиляции (вытяжки). Вытяжка вверху камеры позволит очень комфортно работать, и рассматривать при работе деталь будет намного приятнее, так как пыли (тумана) будет намного меньше.
Вот вроде бы и все основные нюансы, которые желательно учесть при изготовлении пескоструйного аппарата, и надеюсь эта статья будет полезна многим мастерам, которые постоянно улучшают свою мастерскую, или просто захотели заняться пескоструем деталей для своей техники, успехов всем.
Как сделать пескоструйный аппарат своими руками
Прежде чем браться за самодельный пескоструй, следует дать ответ на несколько вопросов. Такой подход поможет избежать как лишних расходов, так и известной доли разочарования в будущем. Итак, прежде чем начинать собирать пескоструйный аппарат своими руками, следует определиться с основным назначением устройства.
Содержание
Если планируется пескоструйная декоративная обработка стекла и зеркал — оптимальным представляется вариант пескоструйной камеры. Размеры ее определяются исходя из габаритов изделий, с которыми предполагается работать. Если планируется пескоструйная очистка материалов под окраску и грунтовку, то необходимо изготовление пескоструйного аппарата открытого типа и для работы с ним необходимо отдельное закрытое помещение.
самодельный пескоструйный аппарат из газового балога
На каком уровне будет эксплуатироваться агрегат? На любительском или профессиональном, ориентированном на бизнес? Самодельный аппарат своими руками изготовить можно. И работать он сможет даже при масштабах производства, сравнимых с промышленными. Вот только ресурс, закладываемый в него, должен быть уже совершенно другого плана. Все зависит от качества используемых материалов, размеров установки и ее мощности. Об этом не следует забывать.
От простого к сложному
схема простейшего пескоструйного аппарата
Начнем с самого простого — пескоструйный пистолет. В самом простом варианте это рукоятка с наконечником и двумя штуцерами.
По одному подводится сжатый воздух, через второй засасывается песок. Конечно, пескоструйный пистолет своими руками от начала до конца лучше не делать, а приобрести готовый, особенно если вы планируете интенсивное использование аппарат. Но для домашнего использования вполне можно собрать из того, что есть под рукой.
Прежде всего, нужно выбрать сопло, т. е. насадку, через которую выбрасывается струя воздуха с абразивом. Точить самому или заказывать не имеет смысла, достойного качества и ресурса вы не добьётесь. Лучше купить изготовленное из карбида вольфрама или бора. Срок их работы до износа составляет сотни часов, тогда как керамических или чугунных хватает на два-три часа работы. Высокая абразивность песка, помноженная на высокую скорость подачи, приводят к быстрому износу выходного канала.
Пример самодельно пескоструйного пистолета изготовленного из клапана от краскопульта, тройника, шарового крана и керамического сопла от зуботехнической машины.
Под размеры сопла точится корпус пистолета. К нему присоединяются рукоятка и штуцеры. Простейший вариант собирается из нескольких водопроводных фитингов, тройника и пластиковой емкости для песка — ей может служить обрезанная пластиковая бутылка, закрепленная сверху.
Такая пескоструйная установка собирается буквально своими руками за несколько часов. В бутылку насыпается песок, пистолет подсоединяется к … Да, к пистолету подводится сжатый воздух от компрессора или магистрали.
Это первая, но не последняя сложность, с которой приходится столкнуться начинающему пескоструйщику. Компрессором придется обзавестись, поздно или рано. Можно взять напрокат, конечно, но это будет временной мерой. Как вариант, можно изготовить компрессор своими руками.
Расходный материал
Предположим, что в наличии есть и пистолет и компрессор. Наступает время позаботиться о абразиве, как расходном материале. Песок, в обычном понимании, не очень подходит для поставленной задачи. Состав его разнороден, частицы имеют неодинаковый размер и форму. Отсюда и характер получаемой поверхности. Кроме того, песчинки в процессе разбиваются, превращаясь в пыль. Очень скоро песочная масса становится совершенно непригодной для работы. Короче говоря расходный материал приодеться приобретать.
Дело в том, что для качественного пескоструя нужны специальные виды абразива. Зачастую это даже не песок, а материалы искусственного или естественного происхождения. Выбор их зависит от специфики работы и определяется следующими параметрами:
- твердость
- размеры и форма зерен
После некоторого времени использования, автор понял, что применение его самого по себе довольно ограничено. Для обработки большой площади он не очень эффективен. Декоративная обработка осложняется тем, что песок разлетается в разные стороны. Получается, что нужен немалый запас его или приходится идти на вынужденные остановки. Таким образом, сама собой назрела мысль вести процесс не на открытом воздухе, а в замкнутом пространстве.
Универсальная пескоструйная камера
Таким образом, мы перешли к идее создания камеры для обработки небольших деталей. По конструкции это прямоугольный ящик, сваренный из металлического уголка и обшитый стальным листом толщиной 1 мм. Удобнее всего будет расположить ее на столе или на подставке. По длинной стороне камеры необходимо предусмотреть смотровое окно из стекла.
Для того, чтобы можно было производить внутренние манипуляции, в передней стенке делаются два отверстия диаметром 100 мм. В них закрепляется пара подходящих перчаток. Как стекло, так и камерные перчатки будут подвергаться износу, поэтому следует предусмотреть возможность их замены.
Дно ящика забирается решеткой из проволоки, под ним располагается желоб, выходящий в тару для сбора отработанного песка . К помещенному внутрь пистолету подводится воздух через разъем в стенке. Шланг для песка опускается в емкость с песком. Таким образом, песок при работе ссыпается обратно и не выходит за пределы рабочей зоны. Для внутреннего освещения используются две лампы дневного света подходящих размеров. Конструкция будет более совершенной, если дополнить ее вентиляцией.
Сбоку располагается лючок, через который изделие помещается внутрь. Чтобы обеспечить возможность обработки длинных заготовок, лучше сделать по бокам загрузочные окна. Забранные брезентом, они позволят прогонять через камеру изделия большой длины.
Аппараты напорного типа
При желании, можно изготовить и самодельную пескоструйную установку напорного типа. Конструкция ее не принципиальна. Годится для этой цели металлическая бочка. Дно должно быть обрезано и заменено конусом. В нижней его части крепится песчаный затвор с тройником, к которому с одной стороны присоединяется шланг от компрессора, с другой отходит рукав с соплом.
Автору приходилось встречаться и с конструкцией самодельного пескоструйный аппарат из огнетушителя. От огнетушителя использовался только корпус, через него пропускалась трубка с перфорацией, после чего емкость наполняется песком и подводится сжатый воздух. Что-то вроде инжектора получается. Конструкция простая, но рекомендовать ее можно только в качестве любительского устройства.
Приведенные выше конструкции описывают только общую схему и принцип работы. Если вы решили смастерить самодельный пескоструйный аппарат для долгой эксплуатации, следует задаться конкретными параметры и засесть за расчеты – без этого не обойтись. Хотелось бы пожелать всем самодельщикам успехов, а пескоструйщикам в особенности.
Пескоструйный аппарат своими руками: сборка установки
Пескоструйный аппарат предназначен для абразивной обработки поверхностей металлических, стеклянных, пластиковых и других изделий. Основными преимуществами, определяющими его востребованность, являются возможность обработки изделий сложной формы с криволинейными участками, а также равномерная матовая текстура поверхности с хорошими адгезивными свойствами и способностью рассеивать падающий на нее свет.
Чаще всего такие устройства используются для очистки металлических изделий от ржавчины, окалины, старого покрытия при подготовке к покрасочным работам или гальванической обработке. При обработке участков полированных поверхностей из металла или стекла (пескоструйной гравировке) получается четкий контрастный рисунок, благодаря чему аппарат можно применять в производстве декоративных изделий.
Типы пескоструйных аппаратов и принципы их работы
Высокая стоимость подобных устройств, встречающихся в продаже, и относительная простота их конструкции заставляют задуматься об изготовлении пескоструйного аппарата своими руками. Существует несколько видов пескоструйных аппаратов, отличающихся по принципу действия, но наибольший интерес представляют два из них:
Аппарат всасывающего действия. Конструкция такого пескоструя весьма проста: аппарат состоит из бункера с абразивом, шланга, один конец которого подсоединен к источнику сжатого воздуха, а второй заканчивается соплом. Шланг соединяется с бункером посредством тройника, через который производится подача абразивного материала. Всасывание песка в шланг происходит под действием газового потока. Смешивание воздуха с абразивом происходит на выходе, благодаря чему такая система обладает высокой надежностью и долговечностью. Единственным элементом, нуждающимся в периодической замене, является сопло. Основным недостатком такой конструкции считается ее низкий КПД.
Аппарат нагнетательного действия. Данный пескоструйный аппарат немного сложнее в изготовлении, имеет больше деталей, соответственно, точек отказа. Кроме этого, шланги и сопла нуждаются в более частой замене, чем на всасывающем аппарате. Основным его преимуществом считается высокая производительность. В сравнении с предыдущей схемой, здесь добавлен тройник для разделения потока воздуха, часть которого направляется в бункер для создания в нем положительного давления. Подача воздуха в бункер может осуществляться как через донную, так и через верхнюю часть. Первый вариант более эффективен, поскольку воздушно-песчаная смесь формируется уже в бункере. Одним из элементов, отвечающих за безотказность работы аппарата, является фильтрующий элемент, предназначенный для удаления влаги из сжатого воздуха.
Основные узлы пескоструйных аппаратов и особенности их конструкции
Источник сжатого воздуха. Чаще всего его функции выполняет компрессор. Для автомастерских, где используется ручной пневматический инструмент, проблема его выбора отпадает сама собой, поскольку такие устройства способны создавать достаточное для пескоструйки давление (от 2 до 6 атмосфер). В других случаях его придется купить или взять в аренду, если выполняемые работы имеют разовый или периодический характер.
Бункер. Основные требования к конструкции бункера – это герметичность, достаточный объём и способность выдерживать рабочее давление в системе. Для его изготовления можно использовать подручные материалы, которые можно найти в любом гараже: старая скороварка, отрезки канализационной трубы, корпус от огнетушителя или даже обычная пластиковая бутылка от газированных напитков. Герметизацию стыков и соединений можно выполнить при помощи любого двухкомпонентного состава на основе эпоксидной или полиэфирной смолы. Получаемые таким образом малогабаритные бункеры можно присоединять непосредственно к пескоструйному пистолету.
Стационарную конструкцию можно изготовить из обрезка трубы большого диаметра, старого газового баллона или листового металла при помощи дуговой сварки. Такая емкость подойдет для выполнения постоянных работ, поскольку может иметь большой объем и редко нуждается в перезарядке. Для обеспечения хорошей производительности длина соединительных шлангов от источника до бункера и от бункера до пистолета не должна превышать 10 и 3 метра соответственно.
Пистолет. Простой по конструкции и удобный в работе пистолет, показанный на рисунке выше, можно изготовить из сантехнических фитингов (тройника с накидными гайками и шарового вентиля) и рукоятки с клапаном от краскопульта. Единственный элемент пескоструйного аппарата, который нельзя сделать своими руками, за которым придется идти в магазин, остается износостойкое сопло. Однако, если аппарат будет использоваться редко, его можно выточить из стали или применить отрезок трубки, развальцованной с одного края для крепления накидной гайкой. Также придется выточить фланцевое крепление для присоединения бункера. Включение пистолета производится при помощи клапана, а подача песка регулируется вентилем.
При использовании стационарного бункера к месту крепления съёмного подключается второй шланг. Таким образом несколько снижается вес конструкции и повышается удобство работы.
Камера. Такой элемент вводится в конструкцию для обеспечения возможности работы в закрытых помещениях. Чаще всего он представляет собой цельносварной герметичный короб со стеклянным смотровым окном в верхней части для зрительного контроля и плотно закрывающимися дверями на левой боковине. Габариты камеры и дверей определяются размерами обрабатываемых деталей.
Трубопроводы для подачи песчано-воздушной смеси проходят через правую боковую стенку. На фронтальной стенке вырезаются круглые отверстия для рук, к которым через фланцы прижимаются длинные каучуковые перчатки. Вместо них можно также использовать текстильные рукава из плотной ткани с пришитыми к ним рукавицами.
Каркас камеры можно сварить из уголка (25×25 или 20×20) и обшить листом толщиной не менее 2 мм. В качестве днища камеры можно использовать перфорированный лист (4 – 5 мм) или решетку из прутка, чтобы отработанный песок мог свободно уходить в нижнюю часть камеры пирамидальной формы и через горловину высыпаться в ящик, который размещают на полу. После просеивания отработанный песок можно использовать повторно.
Дверь можно навесить на петли (наружные), а в качестве замков использовать винты с барашковыми гайками, расположенными по ее периметру. В качестве уплотнения подойдет резина от автомобильной камеры, которую можно нарезать полосами и приклеить по периметру проёма любым контактным клеем типа «Момент».
Камеры заводского производства чаще всего снабжены регенераторами и циклонами для очистки отработанного абразива от пыли и автоматической перезарядки бункера. Самостоятельное изготовление таких устройств представляет ряд сложностей. Обязательным элементом системы будет установка вытяжного вентилятора небольшой мощности, создающего разрежение в камере и предотвращающего попадание пыли в помещение.
Уважаемые читатели, если у вас остались вопросы, задавайте их, используя форму ниже. Мы будем рады общению с вами 😉
Рекомендуем другие статьи по теме
Самодельная насадка PAB для переменного управления пескоструйным аппаратом
Если вы еще не знаете, пескоструйный аппарат под давлением никогда не имел отличной настройки сопла и спускового крючка с простой регулировкой для переменного расхода. Раньше форсунки с регулируемой регулировкой спускового крючка производились только для сифонных пескоструйных аппаратов. Это означает, что чем больше вы нажимаете на курок сопла, тем больше выходит абразивный поток. А количество абразива и давление воздуха можно было легко уменьшить, отпустив спусковой крючок.Пружина позволила бы изменять давление в сопле, и это желательно, прежде всего, в пескоструйной промышленности.
Теперь, нагнетательный бак давал больше мощности пескоструйным аппаратам для глубокой резьбы по стеклу в художественной форме, поэтому его обычно использовали. Но проблема заключалась в том, что художники по стеклу хотели также иметь возможность регулировать давление для разных этапов и для более светлых методов затенения. Боб Пикард был единственным человеком, который знал, как изготовить сопло, которое можно было легко отрегулировать и использовать для сосуда под давлением.
Я никогда не использовал насадку Боба Пикарда, но слышал, что она работает очень хорошо. Но так как это было очень дорого, я отправился пробовать самостоятельно из недорогих материалов. На фото ниже вы можете увидеть мой самодельный триггерный пистолет с регулируемым давлением.
Он все еще находится в экспериментальной фазе, и я включу свои планы в учебный курс. Если вас интересуют эти планы, оставьте комментарий ниже.
Я еще не доработал этот дизайн, чтобы выпустить его, но я покажу вам, как сделать аналогичную альтернативную более простую версию, в моей последней загружаемой версии «Сделайте свои собственные планы пескоструйной машины».Это показано в части 2 электронной книги.
Альтернативная система шлангов с пережимным клапаном
Мы также предлагаем более простую систему шлангов с пережимным клапаном, которая работает аналогично PAB на Amazon и способна выдерживать более высокое давление воздуха.
Аналогичная система с педальным клапаном
Кроме того, мы написали планы, в которых обсуждается та же концепция, которая работает так же хорошо, но предотвращает усталость руки от использования ноги вместо того, чтобы управлять включением / выключением, показанным здесь.
Поделитесь этим в социальных сетях или по электронной почте, нажав ниже!
Ознакомьтесь с нашими принадлежностями для пескоструйной обработки
Пескоструйный аппарат с гравитационной подачей
Портативная, быстрая и простая установка
Уникальные держатели сопел и шланговые системы
Ознакомьтесь с нашими долговечными насадками
Выбирайте из керамики или различных карбидов. Большие размеры C1 и обычные размеры C2
Опубликовано в Новости пескоструйных работ | 11 комментариев
Пескоструйный аппарат, Пескоструйный аппарат
Удаление краски
Прочтите об удалении краски с помощью мойки высокого давления и насадки для пескоструйной обработки.
Сетка для песка : сетка для песка — это размер сита, через которое будет проходить песок определенного сорта. Размер сита «16/50» означает, что обычно большая часть этих частиц проходит через сито № 16, а очень небольшой процент проходит через сито № 50.
Примечание. Сито № 16 представляет собой ячейку с 16 отверстиями 0,046 кв. Дюйма (1,19 мм) на дюйм.
Круглый песок : это относится к круглой кромке песчинки. Река — хороший пример того, как вода доходит до размеров песка.
Угловой песок : песчинка с треугольными краями. Обычно к этому типу относятся щебень или песок.
Угол и расстояние струйной очистки : этот угол струи может повлиять на расстояние до сопла. Всегда соблюдайте рекомендуемый угол пескоструйной обработки и надлежащее расстояние от рабочей поверхности для достижения наилучших результатов пескоструйной обработки.
Регулируемое всасывание песка
Для увеличения всасывания песка ослабьте клапан. Чтобы уменьшить поступление песка, затяните клапан.Экспериментируя с различными настройками, вы можете определить, какой из них наиболее экономичен для работы. См. Ниже примерное использование песка в минуту при каждой настройке.
Альтернативная среда для очистки под давлением | |
---|---|
Бикарбонат натрия (сода) | PRO: Мягче песка или ракушек. При ударе рассыпается в пыль. Если вода используется в сочетании с содой, ее можно смыть в канализационные системы как нетоксичный остаток. CON: Не предназначен для многократного использования, так как это может привести к повреждению поверхности. |
Кремнеземный песок: Стеклянная дробленая переработка | PRO: Имеется в наличии. Эффективно. Доступный. CON: Может иметь различный размер / грубость и быть очень абразивным. |
Молотая скорлупа пекана или грецкого ореха | PRO: Мягче песка и менее абразивен для стен и конструкций.При ударе превращается в мелкую пыль, сводя к минимуму повреждение поверхности. CON: Более высокая цена за фунт и сниженная скорость очистки. |
Сухой лед | PRO: Выбрасывается через систему подачи воздуха, распадается при ударе. Как остатки краски, так и сухой лед разрушаются, при этом сухой лед возвращается в атмосферу, а краска превращается в порошок до размера, который невозможно обнаружить в непосредственной близости от места работы.Поставляется в разных размерах для различных применений. CON: Затраты выше, чем традиционные методы взрывных работ. |
Другие варианты: молотые кукурузные початки, каучук, угольный кремень, драгоценные камни | PRO: Новые носители находятся в разработке. CON: Может быть дороже. Непроверено для некоторых приложений. |
Основы струйной печати — 5 советов, как улучшить работу бластера
Размещено: 25 апреля 2012 г. Автор: MattMMedia Blasting — довольно простой процесс, если разбить его на основы.Вы смешиваете абразивный материал с воздухом под высоким давлением и выстреливаете его из небольшого отверстия пистолета / сопла. Обработка носителей чрезвычайно эффективна, если вы будете следовать некоторым довольно простым советам. В этой технической статье мы расскажем об основах, которым необходимо следовать при проведении взрывных работ с помощью бластера под давлением.
1. Правильное оборудование — Причина номер один, которая может привести к неправильной работе носителя, — это компрессор, который не успевает за ним. Обязательно сравните характеристики бластера, который вы покупаете (или владеете), с характеристиками вашего компрессора.В идеале вы не хотите, чтобы ваш компрессор работал на максимальной мощности при работе бластера. Постоянная работа компрессора без отдыха вызывает чрезмерное нагревание, которое приводит к образованию влаги в трубопроводах и может вызвать засорение пескоструйного аппарата (еще одна причина для наличия надлежащей системы управления воздухом). Помните, что струйная очистка носителя требует большого количества постоянного давления для эффективной работы, и если ваш компрессор не может производить требуемый объем, струйный аппарат НЕ будет работать правильно.
— Промышленный стандарт для давления на сопле составляет 80-100 фунтов на квадратный дюйм.Меньше этого, и у материала не будет силы, необходимой для правильного удаления материала. Работа намного выше 100-120 фунтов на квадратный дюйм может превысить максимальное давление бластерного бака и привести к распаду носителя при ударе о поверхность и ухудшении чистящей способности.
2. Длина и форма шланга — Хотя хорошо иметь длинный воздушный шланг, который может дотянуться до любого места в вашем магазине или подъездной дорожке, это может серьезно повлиять на производительность вашего медиаобластера. Старайтесь, чтобы шланг был как можно короче и не имел изгибов и перегибов.Чрезмерная длина и изгибы могут привести к усилению работы компрессора и снижению производительности. Имейте в виду тот же совет и со своим бластерным шлангом. Каждая петля или жесткий изгиб на линии вызывает значительное падение давления (мы видели 5-10 фунтов на квадратный дюйм для каждого жесткого изгиба или перегиба шланга бластера).
3. Вода — враг — Мы намекали на это выше, но мы не можем достаточно подчеркнуть, насколько важно иметь надлежащий воздушный сепаратор или осушитель на линии вашего компрессора. Мы предлагаем добавлять новый встроенный одноразовый воздушный фильтр каждый раз, когда вы начинаете новый проект по очистке.Это дешевая страховка, позволяющая избежать попадания мокрых комков носителя, которые забивают ваш бластер.
4. Правильно отрегулируйте бластер — Большинство бластеров высокого давления имеют аналогичные клапаны типа «мертвец», которые блокируют воздух или среду. Эти клапаны не всегда нужно открывать полностью. Для каждой комбинации носитель / сопло и каждого задания требуются разные настройки. Общее практическое правило заключается в том, что соотношение воздуха и среды должно составлять 90/10. Слишком большое количество носителя снизит давление на конце, когда оно покидает сопло. Мы предлагаем выполнить пробный запуск и медленно открывать клапан среды до тех пор, пока он не начнет удалять материал с испытательного образца.
5. Техника — Один негативный момент, который часто говорят о струйной очистке носителей, заключается в том, что она может деформировать тонкие панели и фактически повредить детали, удалив слишком много материала. Обычно это можно списать на неправильную технику. Вы хотите, чтобы при взрыве было устойчивое движение из стороны в сторону. ЗАПРЕЩАЕТСЯ останавливаться и производить струйную очистку в одной концентрированной зоне в течение длительного периода времени, поскольку это может деформировать более тонкие панели и удалить слишком много материала с некоторых поверхностей. Кроме того, держите сопло под углом 60-45 градусов и направьте его в том направлении, в котором вы движетесь при взрыве.Это поможет очистить носитель более эффективно и поможет не сидеть на одном месте слишком долго.
Следуйте этим советам и сделайте свои взрывные работы максимально гладкими и качественными. Если у вас есть дополнительные вопросы о взрывных работах, напишите нам или зайдите на наш форум и присоединяйтесь к нашим техническим обсуждениям!
Советы, уловки и ссылки Deve по пескоструйной очистке
Советы, приемы и ссылки Deve по пескоструйной очистке
Как и со всем контентом на этом веб-сайте, вы можете просто щелкнуть любое изображение, чтобы получить его самый большой размер.Таким образом, мы можем поддерживать самое четкое определение, чтобы вам было легче видеть детали. Если картина такая большая, ты не сможешь увидеть все это на своем экране, все, что вам нужно сделать, это удерживать CONTROL и перемещать колесико мыши вверх и вниз, чтобы изменить размер!Пескоструйная обработка — это самая неприятная часть процесса восстановления, о которой я могу думать. Вы получаете песок в местах, о которых даже не знали существует, у вас есть горячий капюшон на время, дыхание затруднено с респиратором или без него, и оно медленное независимо от того, какое оборудование у вас есть для работы.Если бы я не верил в это так сильно, я бы не думал об этом ни на минуту. Пескоструйная очистка — лучший и единственный реальный способ удаления краски и ржавчины, который гарантирует, что ваш металл будет правильно подготовлен на долгое время. прочная покраска. Нейтрализаторы ржавчины, средства для покраски ржавчины, чистка проволочной щеткой, ничего не помогает, чтобы действительно проникнуть в металл и глубоко чистая как пескоструйная. Ниже приводится все, что я узнал о предмете, проведя около 800 часов в капюшон.
Существует множество разновидностей абразивно-струйных средств. Я всегда сомневался в необходимости тратить 25 долларов и более на сумку СМИ, поэтому я исследовал и нашел идеальный носитель для 99% всего, что реставратор автомобилей делает со своим пескоструйным оборудованием. Этот включает в себя внутренний абразивный шкаф, а также сифонное и герметичное оборудование.
Секрет в том, чтобы получить супер-тонкий кварцевый песок №1.Я покупаю сумку на 70 фунтов за 4,98 доллара. Это небольшая часть стоимости обычного взрывные носители и работают лучше и служат дольше, чем большинство других. Его преимущества в том, что он не деформирует ваш металл, он быстро режет вплоть до голого металла, его можно использовать повторно, и он не забивает ваше оборудование, как это делает большие носители.
Заявление об отказе от ответственности: Некоторые люди не согласны с тем, что я использую кремнеземный песок по соображениям здоровья. Для получения дополнительной информации о опасности кварцевого песка, посетите веб-сайт CDC.Если вы хотите Альтернативой является продукт под названием StarBlast (от Dupont), который не содержит кремнезема, по цене около 8 долларов за пакет. По слухам, его можно получить через любой дом снабжения стройматериалами.
Внутри или снаружи?
Для мелких деталей можно приобрести абразивоструйный шкаф. Это незаменимый инструмент, которым я пользуюсь довольно часто. Просто не было бы без него можно сделать полноценную реставрацию. Вы можете сделать недорогой шкаф самостоятельно разными способами или купить уже готовый. сделали.Я обнаружил, что лучший ресурс для оборудования для струйной очистки шкафов — это TP Tools из Кантона, штат Огайо. У них есть все, что вы когда-либо будете нужно в том числе планы сделать свои собственные. Я настоятельно рекомендую вам получить их каталог (800)321-9260 или зайти на веб-сайт по адресу tptools.com. У меня есть их дробеструйный шкаф 930, и он работает неплохо, но если бы у меня больше денег, я бы выбрал больше. Чем больше, тем лучше, в зависимости от наличия свободного места. Рециркулируют песок и пол-мешка песок может прослужить очень долго.
Для более крупных деталей вам нужно будет вынести их на улицу. Обычно я коплю кучу работы, а потом делаю из нее ежегодное мероприятие. Это потому что это непросто и весело, а настройка требует времени. Подробнее об этом позже.
Воздушные компрессоры для струйной очистки
Воздушные компрессоры не предназначены для струйной очистки. Независимо от того, какой у вас компрессор, в ту минуту, когда вы начнете взрыв, компрессор начнет бежать и будет продолжать работать, пока вы не отпустите спусковой крючок.Это означает, что компрессору очень тяжело, и вы вы захотите спасти ваше оборудование, периодически делая перерывы, чтобы дать машинам остыть. Я виноват, что делаю этого недостаточно и уже заменили два компрессорных насоса, что дорого. Чтобы правильно запустить абразивоструйный аппарат и не отставать от больших объем воздуха, который используется, подойдет не менее 60 галлонов, 2-ступенчатый компрессор мощностью 7 лошадиных сил. На мой взгляд, это самый минимум. Я работал на том уровне в течение года, пока мне, наконец, не надоест его нехватка воздуха, и я купил второй 60 галлонов, 7 лошадей и поставил их в тандеме.Теперь у меня нет проблем, но дело в том, чтобы получить самый большой и лучший компрессор, который вы можете себе позволить. Если бы я мог все это сделать Опять же, я бы получил двухступенчатую лошадь мощностью 80 галлонов и 15 и надеюсь на лучшее. Два компрессора в тандеме увеличивают вдвое емкость и второй мотор помогает не отставать.
Сифон или под давлением?
Для работы вне дома и только на одном автомобиле можно использовать сифонный бластер. В Sears они стоят около 50 долларов, и я весь Chevy Pickup 50 года с одним.Они медленнее (намного медленнее), чем под давлением, но менее проблематичны, дешевле и требуют меньшее количество сменных форсунок, поскольку они не так быстро изнашиваются. Поскольку песок не выходит со скоростью, близкой к скорости нагнетания, вы можете сохранить больше песка в этом районе для повторного использования. Как видите, сифонная очистка имеет свои преимущества, но если вы серьезный реставратор и буду делать не одно транспортное средство, герметичный однозначно лучше.
Пескоструйные аппараты работают за счет создания давления в резервуаре, заполненном пескоструйным песком.Это выталкивает песок с высокой скоростью и срезает краска и ржавчина намного быстрее. Я считаю, что примерно в 4 раза быстрее, чем сифонная очистка. Достойные бластеры под давлением начинаются примерно от 100 долларов. Я купил 40-фунтовый бластер под давлением Harbour Freight за 79,95 долларов. Это было бы плохой идеей, если бы вы не были готовы поставить еще одну 80 долларов в нее сразу, чтобы ее можно было использовать. Водоотделитель пластиковый и сломался через час, шланг для песка прослужил двое суток, клапан форсунки работал около 2 суток, керамические форсунки — около 5 часов.Я пошел в местный магазин инструментов (не пришлось выкрутил мне руку, чтобы сделать это!) и купил стеклянный водоотделитель и 15-футовый шланг GoodYear с давлением 320 фунтов. Я тогда заказал карбидная насадка от sandblast-nozzles.com (номер детали TL2-1) размером 3/32 дюйма. 3/32 дюйма — действительно лучший размер для песка, который я использую, и давления, которое мне нужно. я мог поддерживайте давление около 80 фунтов с моей установкой с использованием этой насадки. Я остался очень доволен. Убедитесь, что бластер под давлением вы использование идет с дроссельной заслонкой.В дни с высокой влажностью у вас будут проблемы с засорением, и этот дроссельный клапан устраняет эту проблему.
Вкратце …
Если бы мне пришлось делать это снова и снова, я бы купил свою систему под давлением в Brut Mfg. Вы можете позвонить им по телефону (888) 533-2693 или зайти в www.brutmfg.com. Это дороже, но запчасти более доступны. Harbour Freight получает все запасные части из Китая, и им приходится ждать прибытия корабля.Это означает иногда месяцы до того, как ваши запасные части станут доступны. Если вы планируете это, вас устраивает подразделение Harbor Freight, но Brut Mfg ставит более качественное оборудование американского производства. Этим летом я провел 5 недель по 10 часов в день при 100-градусной жаре, взрывая эквивалент двух целых тележек (рама и весь связанный листовой металл). Я очень рада, что все закончилось! Особая благодарность Фреду Цвикеру с покойного Трумэн, Инк.за его понимание и вклад в эту статью.
Проблема решена!
Я получил от моего друга Джона Эрба около двух бочек на 55 галлонов оборудования эпохи Advance Design. Он занимался разборкой грузовиков, чтобы продавать запчасти нашим поставщикам. Он просто бросал оборудование в кучу в углу своего гаража. Когда он был продан, я купил все это потому, что я мог видеть стоимость оборудования на складе.Все было заржавело, смазка / грязь по всем деталям, что делать?
Вы можете купить одну из этих корзин и встряхивать, встряхивать, встряхивать в своем абразивоструйном шкафу или же один из них, положите пистолет в кобуру и отойдите примерно на 30 минут. Это была реальная экономия времени и что-то действительно сделали работу возможной. На данный момент не очень красиво, но свою работу выполняет. Я хочу сделать этот проект мозговым центром. Есть необходимо внести улучшения, но герметичный двигатель и система привода работают очень хорошо.
Фотографии, которые не попали в обрез …
Как правильно выбрать сопло
При выборе сопла необходимо соблюдать баланс, и он начинается с вашего воздушного компрессора . Как только вы поймете, как размер вашего компрессора влияет на производственные возможности, вам нужно будет взглянуть на сопло размером . Выберите сопло со слишком маленьким отверстием, и вы оставите на столе некоторую взрывную мощность.Слишком большой ствол — и вам не хватит давления для продуктивного взрыва.
Далее идет форма сопла . Форсунки двух основных форм: с прямым отверстием и Вентури , с множеством вариаций размера и формы внутри. Наконец, вы захотите рассмотреть материал , из которого изготовлено сопло. В частности, материал, из которого изготовлена накладка внутри канала ствола. Три основных фактора при выборе идеального материала отверстия сопла — это долговечность, ударопрочность и цена.
Правильный выбор сопла может существенно повлиять на рентабельность как малых, так и крупных взрывных работ, и все начинается с вашего воздушного компрессора.
- Забирает более 185 кубических футов воздуха в минуту при атмосферном давлении
- Сжимает воздух до меньшего объема при высоком давлении Сопло
- сжимает воздух до еще меньшего объема (3/8 дюйма — 3/4 дюйма I.D.) при очень высоком давлении
Чем больший объем воздуха вы можете сжать в минуту, тем выше давление в сопле. Это увеличивает производительность двумя способами:
- Высокое давление увеличивает скорость абразивных частиц, обеспечивая большую кинетическую энергию при ударе, создавая более глубокий рисунок якоря. Это позволяет использовать более мелкий абразив, который дает большее количество ударов на единицу объема.
- Увеличенный объем воздуха позволяет использовать сопло с большим диаметром отверстия, что позволяет наносить больше абразива на цель.
Предполагая, что доступная вам мощность воздушного компрессора не безгранична, вам необходимо выбрать сопло с отверстием , достаточно маленькое, чтобы поддерживать производительное давление воздуха при любом объеме, который может подавать ваш компрессор.
Для пароабразивной струйной очистки наиболее часто используемые размеры отверстий сопел находятся в диапазоне от 3/8 дюйма до 3/4 дюйма, увеличиваясь с шагом 1/16 дюйма.Сопло 3/8 дюйма достаточно сужено для создания эффективного давления дутья с компрессором 185 куб. Фут / мин. Сопло 1/2 дюйма достаточно для создания эффективного давления дутья с компрессором 375 куб.
Важно отметить, что , когда вы удваиваете диаметр отверстия, вы в четыре раза увеличиваете размер отверстия и объем воздуха и абразива, которые могут пройти через сопло.
Чтобы подобрать сопло с оптимальной производительностью, определите, какое давление в сопле (PSI) необходимо поддерживать для продуктивной струйной очистки, и какой объем воздуха может подавать имеющийся компрессор в минуту (CFM), а затем обратитесь к следующей таблице, чтобы определить размер отверстия сопла. что соответствует этим параметрам.
Объемная емкость (куб. Фут / мин), необходимая для давления, у сопла
Имейте в виду, что ваш компрессор будет создавать меньшее давление на сопле, чем указано в таблице, в зависимости от состояния и конфигурации вашего оборудования.
Диаметр отверстия | Давление на сопле | Минимум CFM Требуется | ||||||||
Размер сопла | дюймов | мм | 50 | 60 | 70 | 80 | 90 | 100 | 125 | |
№ 6 | 3/8 « | 9.5 | 110 | 124 | 145 | 160 | 175 | 200 | 275 | |
# 7 | 7/16 « | 11 | 150 | 170 | 200 | 215 | 240 | 255 | 315 | |
№ 8 | 1/2 « | 12,7 | 200 | 225 | 250 | 275 | 300 | 340 | 430 | |
# 9 | 5/8 « | 16 | 300 | 350 | 400 | 450 | 500 | 550 | 700 | |
№ 10 | 3/4 « | 19 | 430 | 500 | 575 | 650 | 700 | 800 | 1100 |
Абразивы со временем влияют на давление струи
Форсунки изнашиваются.Абразив, проходящий через сопло, изнашивает футеровку, увеличивая отверстие. Изношенному соплу требуется больший объем в минуту для поддержания целевого давления.
Например, если вы купили сопло № 8 (1/2 дюйма), чтобы получить 100 фунтов на квадратный дюйм с помощью компрессора 375 куб. Футов в минуту, после его износа на 1/8 дюйма диаметр сопла увеличится до следующего размера (№ 9 — 5/8 «), вам повезет, если вы поддержите 65 фунтов на квадратный дюйм, используя тот же компрессор (на линии № 9 компрессор 375 кубических футов в минуту находится в диапазоне от 350 до 400 кубических футов в минуту, поэтому вы можете поддерживать только 65 фунтов на квадратный дюйм), потому что объем воздуха, проходящего через увеличенного отверстия будет недостаточно для поддержания давления.
Однако, если вы купили № 7 (7/16 «), все еще используя компрессор 375 и нацеленный на 100 фунтов на квадратный дюйм, как только он износится до следующего размера (№ 8 — 1/2»), вы все равно будете можно достичь 100 фунтов на квадратный дюйм, но вы пожертвуете некоторой производительностью на более раннем этапе срока службы сопла (по сравнению с соплом № 8 (1/2 дюйма)), потому что количество воздуха и абразива, которые могут пройти через отверстие при 100 фунтов на квадратный дюйм, будет быть меньше, чем может дать ваш компрессор.
Давление может значительно упасть между компрессором и соплом, до одного фунта на квадратный дюйм на 50 футов шланга (1 дюйм I.Д.). Кроме того, давление будет падать при каждом изгибе шланга или изменении направления: самая короткая и прямая конфигурация шланга является наилучшей. Вдобавок ко всему, если в шланге есть плохо подогнанные муфты или утечки, падение давления может быть полным.
Размер отверстия сопла влияет не только на объем и давление, но и на размер формы струи. При каждом увеличении размера сопла ожидайте увеличения размера струи струи до 10%. Но больше всего влияет на размер вашей струи струи форма сопла, а не размер отверстия.
Форсункибывают двух основных форм: с прямым отверстием и Вентури , с несколькими вариантами сопел Вентури.
Когда сжатый воздух входит в сужающийся (левый) конец сопла с прямым отверстием, он ускоряется, ускоряя абразивные частицы, взвешенные в потоке. Частицы выходят из сопла плотной струей и при ударе создают узкую концентрированную струю.
Тип взрыва: 3 дюйма на расстоянии 18 дюймов
Производительность: 4,5 / 5
Вентури имеют сходящийся вход и расходящийся выход. Эта форма предназначена для создания эффекта, который значительно ускоряет воздушный поток и частицы — однако это не эффект Вентури.
Эффект Вентури — это наблюдение, что когда воздушный поток ускоряется, проходя через сужение, происходит соответствующее падение давления.
Это не ключевой принцип работы сопла «Вентури». Технически эти сопла представляют собой сопла де Лаваля, такая же конструкция используется в выхлопных газах. Быстрое ускорение воздушного потока и частиц в сопле де Лаваля происходит из-за эффект, который возникает, когда поток прерывает скорость звука.
Помимо огромного ускорения, наклонная форма расширяющегося конца расширяет поток, создавая большую картину взрыва и более равномерное распределение частиц, чем у сопла со стандартным отверстием.
Форсункис удлиненной трубкой Вентури увеличивают производительность до 40% и потребляют меньше абразива по сравнению с форсунками с прямым отверстием.
Тип взрыва: 3 дюйма на расстоянии 18 дюймов
Производительность: 4/5
Двойное сопло Вентури — это сопло де Лаваля с очень широким выходным отверстием и отверстиями на расходящемся конце.
Согласно эффекту Вентури, когда скорость потока увеличивается, давление падает, создавая вакуум между ударной волной и горловиной, уменьшая скорость абразива.С двойным соплом Вентури атмосферный воздух втягивается через отверстия в зону низкого давления, расширяя воздушный поток и создавая более широкую картину струи.
Тип взрыва: 3 дюйма на расстоянии 18 дюймов
Производительность: 5/5
Форсунки с широким горлом — это сопла де Лаваля с широким горлом и сужающейся секцией сверхширокой 1/4 дюйма. При использовании вместе со шлангом с соответствующим внутренним диаметром (и с соответствующим увеличением объема воздуха) сопло с широким горлом может увеличить производительность до 15% по сравнению с длинной трубкой Вентури.
Схема взрыва: 5 дюймов на расстоянии 48 дюймов
Производительность: 3/5
Эти сверхдлинные сопла ускоряют частицы на большем расстоянии, обеспечивая более высокие скорости на выходе, позволяя бластеру стоять дальше от взрываемой поверхности, создавая более крупную схему взрыва и более высокую производительность.
Третье соображение при выборе сопла — это состав футеровки внутри канала ствола.Более твердые материалы более устойчивы к износу, но их замена дороже, и они склонны к растрескиванию при грубом обращении. Есть три основных типа твердосплавных форсунок.
Прочность: 1/5
Ударопрочность: 5/5
Цена: Низкая
Это наименее прочная из карбидных форсунок, но относительно дешевая и устойчивая к ударам. Подходит для струйной очистки шлака, стекла и минеральных абразивов.
Прочность: 1/5
Ударопрочность: 5/5
Цена: Низкая
Ударопрочный и прочный, как карбид вольфрама, но легче. Вызывает меньшее напряжение оператора.
Прочность: 3/5
Ударопрочность: 1/5
Цена: Высокая
Чрезвычайно твердый и прочный, но хрупкий.Срок службы карбида вольфрама в десять раз превышает срок службы.
Прочность: 5/5
Ударопрочность: 3/5
Цена: Высокая
Некоторые производители производят собственные композитные карбидные форсунки, которые даже тверже, чем карбид бора.
Замена форсунок не из дешевых. Одним из преимуществ пароабразивной очистки является то, что ваши сопла прослужат в 3 раза дольше, чем сопла для сухой струйной очистки, поскольку частицы заключены в водяной рубашке для смазки, что снижает трение между абразивом и футеровкой сопла.
Еще одним важным преимуществом является то, что пароабразивный пескоструйный аппарат отлично контролирует скорость подачи абразива. При пескоструйной очистке регулировку сложнее, с меньшим диапазоном. Переход от сопла №6 к соплу №8 с помощью пескоструйной установки почти удвоит количество потребляемого абразива.
Исследования показали, что производительность струйной очистки постепенно увеличивается с увеличением скорости подачи абразива до достижения критического значения, после чего производительность остается постоянной. Таким образом, после того, как это значение было превышено, потребление большего количества носителя фактически снижает скорость частиц, приводит к потере абразива и снижает эффективность.
Поскольку пароабразивный пескоструйный аппарат может легко регулировать расход абразива для определения этого критического значения, он может достичь оптимальной производительности при более низких давлениях, чем при сухой струйной очистке.
Большой воздух и большие форсунки приводят к большой производительности, но форма отверстия форсунки определяет ускорение частиц и размер струи.
Чтобы максимизировать вашу производительность, выберите самое большое отверстие сопла, которое ваш компрессор будет поддерживать при давлении, которое будет производительным , учитывая характеристики поверхности и технические характеристики задачи, принимая во внимание, что будет значительное снижение давления, поскольку ваша форсунка изнашивается до большего диаметра.Поиск оптимальной точки, в которой ваше сопло может быть продуктивным в течение всего срока его полезного использования, является ключом к получению максимальной отдачи от сопла.
Пистолет содовой
[gravityform id = 1 title = false description = false tabindex = 0]
[gravityform id = 1 title = false description = false tabindex = 0]
Планы пескоструйных аппаратов под давлением
Планы пескоструйных аппаратов
Планы пескоструйных аппаратов на абразивной ржавчине
Строим за ноль $$$$
Самостоятельно под давлением
Вы когда-нибудь думали о покупке пескоструйного аппарата, но не понимали, какой бластер лучший ?? Что ж, не потрудитесь купить один из этих дорогих пескоструйных аппаратов !? Вместо этого создайте супер-средство для удаления ржавчины, монстра, измельчающего ржавчину, из свалок или мусора, извлеченного с обочины!
Бластер, изображенный в этом списке, был построен за? День!
Если вы хотите узнать, насколько быстрым является этот бластер, то посмотрите изображения в конце этого списка (изображение выше до взрыва).? Я взорвал «этот» бластер менее чем за 15 минут. «Это было удаление более двух слоев краски и грунтовки, а также ржавчины.
Вы можете создать дешевый эффективный пескоструйный аппарат, и этот пакет руководств и чертежей покажет вам, как это сделать. Построен из свалок и извлеченных деталей, с которыми вы можете столкнуться каждый день !? Если вы можете найти все детали за бесценок, что вполне возможно, у вас будет только вложение в руководство как ваши затраты (плюс ваше время) !!!? Если вы не можете найти детали в хлам, на обочине или где-то еще,? В руководстве указано, где? Вы можете? Купить их.
Это набор планов по созданию собственного недорогого пескоструйного аппарата с подачей давления. В 67-страничном руководстве есть пошаговые инструкции, фотографии и чертежи о том, как построить пескоструйный аппарат из старого пропанового баллона (конечно, очищенного от газа… ..в планах рассказывается, как произвести продувку). Стоит 10,25 доллара, чтобы узнать, как это сделать!
Я много раз покупал эти цилиндры на местных аукционах менее чем за 50 центов. Вы даже можете использовать небольшой цилиндр от старого гриля для барбекю, если вам нужен бластер меньшего размера.? Часто они свободно сидят на обочине, потому что у них старые клапаны.
Использовать любой имеющийся у вас танк? который будет удерживать давление, которое вы можете создать с помощью компрессора.? Информация может быть адаптирована практически к любому типу танка. Поставляется с картинками на каждом этапе строительства.
Бластер на фото вмещает 275 фунтов. песка.? Это обеспечивает часы непрерывной пескоструйной обработки. Я пропустил более 7000 фунтов песка через этот пескоструйный аппарат, и у меня никогда не было проблем с ним… Никаких засоренных линий или коллекторов, просто бесконечный запас песка и воздуха для вашего удовольствия от пескоструйной обработки!
Используйте этот пескоструйный аппарат для удаления сильных отложений ржавчины на стали — до и после сварки (дуговая, MIG, TIG) перед окраской, он отлично работает при использовании металлолома, металлолома или при ремонте некоторого ржавого или сильно окрашенного оборудования.? Очищает до чистого металла, или вы можете просто протравить поверхность для хорошей адгезии краски. Может также использоваться для травления конструкций на стекле, удаления толстых слоев краски с металла, кирпича или бетона, использования его для восстановления транспортных средств, тракторов или экскаваторов, строительной техники или восстановления прицепов (отлично работает с чугун? И алюминий? Тоже), Восстановление велосипедов, восстановление мотоциклов, восстановление техники. Легко удаляет хромирование с колес или дисков перед повторным покрытием. Независимо от того, занимаетесь ли вы «струйной очисткой деталей для John Deere, Case, Massey Ferguson, Oliver, Allis Chalmers или« Minneapolis Moline », этот бластер удалит ржавчину и нанесет краску на любой из них! Возможности безграничны.
Он способен обрабатывать различные абразивные среды, включая песок, стеклянные шарики, угольный шлак (черный краситель), гранитные абразивные материалы, скорлупу или шелуху грецких орехов, пищевую соду, пластиковые шарики и этот список можно продолжить.
Включает информацию о приобретении деталей и модификациях этих деталей для создания держателя пескоструйных сопел, в котором используются керамические сопла большего размера, которые служат очень долго. Также включает информацию о шлангах, которые служат вечно (мне никогда не приходилось заменять еще один).
Вот пример того, как хорошо работает этот бластер…..Полет шнека перед взрывной ……
… .полет шнека после взрывной обработки ……
Если у вас уже есть пескоструйный аппарат с сифонной подачей, и он не соответствует вашим ожиданиям …… .не проблема, планы показывают, как вы можете преобразовать его в также устройство подачи под давлением, практически исключающее эффект выброса песка. Может быть, у вас есть абразивоструйный шкаф с сифонным устройством подачи внутри,… .. есть ли у вас шанс модернизировать его !? «На фото ниже» — остатки моего оригинального сифона с усилителем давления (шины спущены, а некоторые детали были отобраны у него)….Это было началом моего дизайна 22 года назад.