Коленчатый вал — Энциклопедия журнала «За рулем»
Рис. Коленчатый вал двигателя V6
Коленчатый вал воспринимает усилия, передаваемые от поршней шатуном, и преобразует их в крутящий момент. Поэтому коленчатый вал должен быть прочным и жестким.
В качестве материала для коленчатого вала используют высокопрочный чугун и сталь. Чугунные валы изготавливают методом литья, а стальные — методом ковки. Рабочие поверхности коренных и шатунных шеек коленчатого вала подвергают упрочнению с помощью термической обработки и последующей шлифовке.
Коленчатый вал состоит из нескольких коренных шеек, соединенных щеками с шатунными шейками. Щеки коленчатого вала продолжаются в противоположном от шейки направлении, образуя противовесы. В некоторых двигателях грузовых автомобилей используют съемные противовесы, которые крепятся к коленчатому валу болтами. Коренные шейки всегда больше в диаметре, чем шатунные. Коленчатый вал будет более жестким, если коренные и шатунные шейки перекрывают друг друга при взгляде с торца вала.
В качестве коренных и шатунных подшипников скольжения в настоящее время применяют разъемные, тонкостенные вкладыши. Вкладыши изготавливают из стальной ленты с нанесенным на нее слоем антифрикционного сплава.
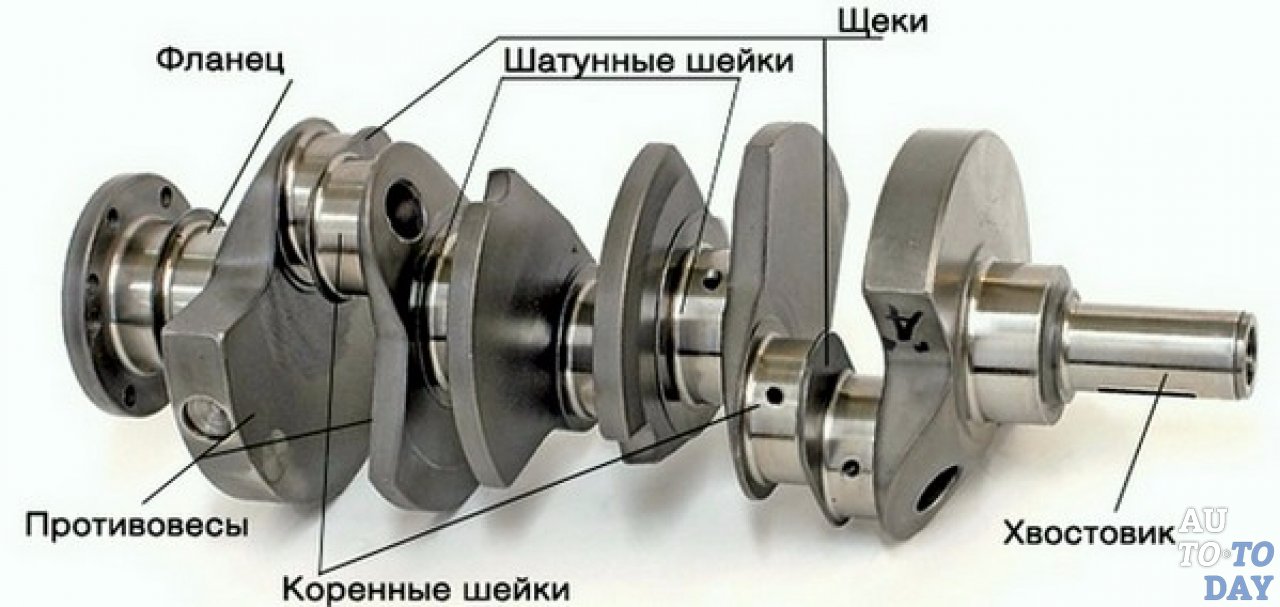
Внутри коленчатого вала, в щеках и шейках коленчатого вала просверлены отверстия для прохода масла. Подшипники коленчатого вала подвергаются значительным нагрузкам, и даже кратковременная работа двигателя без масла приводит к его выходу из строя, поэтому к шейкам коленчатого вала масло подается постоянно под давлением.
К заднему концу коленчатого вала крепится маховик. Маховик служит для уменьшения неравномерности работы двигателя, запасая энергию при рабочем ходе и отдавая ее при других тактах, а также выводит КШМ из мертвых точек. Маховик представляет собой массивный диск, выполненный из чугуна. На внешнюю цилиндрическую поверхность маховика напрессован зубчатый венец, обеспечивающий проворачивание коленчатого вала при пуске двигателя с помощью электрического стартера.
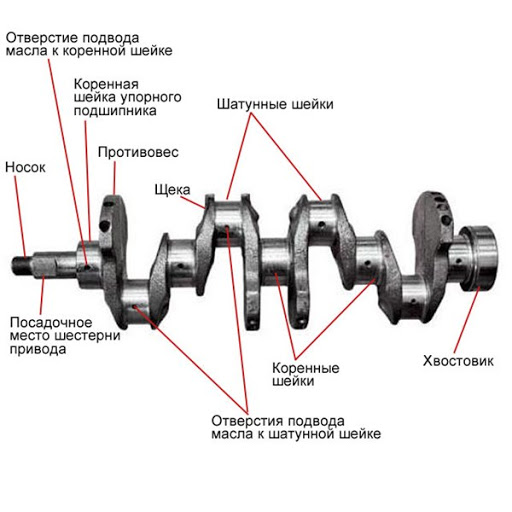
Рис. Двухмассовый маховик двигателя
Каким бы жестким ни был коленчатый вал, он подвергается крутильным колебаниям. Крутильные колебания можно представить как постоянное закручивание с последующим раскручиванием вала, что происходит при работе двигателя с определенной частотой. При совпадении частоты крутильных колебаний с частотой внешних сил может наступить резонанс, который приведет к резкому увеличению нагрузок, действующих на коленчатый вал, и, как следствие, к его поломке. Излом коленчатых валов (обычно в месте соединения щеки с коренной шейкой) был частой причиной выхода из строя двигателей старых конструкций. Современные коленчатые валы имеют высокую жесткость, и резонансные частоты находятся за пределами возможных частот вращения валов этих двигателей. Тем не менее в конструкции двигателей часто применяют гасители крутильных колебаний, которые снижают до нужного уровня виброактивность коленчатого вала. Наиболее распространенный способ: разделить шкив или диск, установленный на коленчатом вале, на внутреннюю и наружную части и соединить их упругим материалом, который поглощает вибрации за счет внутреннего трения.
Прогресс в системах управления может внести дополнительные изменения в конструкцию двигателей. Сегодня разработаны новые тороидные стартер-генераторы, которые не только мгновенно и бесшумно пускают двигатель, но и дают возможность за счет электронного управления гасить всевозможные колебания и вибрации, а также обеспечивают возможность работы двигателя при экстремальных нагрузках.
Шатунные шейки
Создание эффективного и прочного подшипника — это не только вопрос оптимальной конструкции вкладышей подшипника. Шатунные шейки также играют значительную роль, т.к. любое отклонение от допустимой геометрии может вызвать повреждение подшипника.
Осевая погрешность профиля
Радиальная погрешность профиля
Радиальная погрешность профиля возникает в тех местах, где во время изготовления есть вибрации между инструментом и шатунной шейкой. На Рисунке 2 приведены примеры возможных радиальных погрешностей профиля. Степени допустимого отклонения формы зависят от типа отклонения, а также минимальной толщины масляной пленки. Минимальная толщина пленки масла зависит от нагрузки на подшипник.
[Рис. 1] Создают такие погрешности формы шейки коленчатого вала в осевом направлении, как коническое, выпуклое или вогнутое отклонение от идеальной цилиндрической формы. |
[Рис. 2] Типичные отклонения формы шеек коленчатого вала от идеальной круглой формы в радиальном направлении. На иллюстрации показаны отклонения от 1-го по 6-ой порядок. Такие погрешности формы возникают в том случае, если между шлифовальным кругом и проворачивающимся коленчатым валом создаются гармонические колебания. |
Шероховатость поверхности
Вместе с осевыми и радиальными погрешностями формы еще одни важным свойством шатунной шейки является качество обработанной поверхности. Высокое качество обработанной поверхности минимизирует износ шейки и вкладыша.
Коленчатые валы из ЧШГ
В настоящее время коленчатые валы изготавливают либо из стали, либо из чугуна с шаровидным графитом (ЧШГ). ЧШГ содержит включения графита (так называемые «вкрапления» графита), повышающие эластичность материала. При производстве шеек из ЧШГ необходимо учитывать одну специфическую характеристику.
При перешлифовке шейки из чугуна с шаровидным графитом происходит разрезание «вкраплений» графита, а «размазывание» материала во время процесса резки вызывает формирование «крышек», закрывающих «вкрапления» графита. Поэтому даже если поверхность внешне выглядит гладкой, во время работы двигателя напряжения на «крышках» могут вызвать их разрушение, что приведет к повреждению подшипника (см. Рисунки 3 и 4). Формирования «крышек» следует избегать во что бы то ни стало. Для этого существуют два способа. Первый способ заключается в минимизации формирования «крышек» за счет использования полос из кубического нитрида бора (КНБ ).
[Рис. 3] Поверхность «крышек» вкраплений графита на коленчатом вале Схематическое увеличенное изображение шейки коленчатого вала, выполненного из чугуна с шаровидным графитом, в поперечном разрезе. Заштрихованные области представляют собой включения графита в матрицу чугуна. При перешлифовке шейки коленчатого вала включения графита разрезаются. Режущий инструмент «размазывает» сталь по включениям таким образом, что они частично или полностью закрываются «крышкой». Такие «крышки» могут быть опасны для двигателя. Циклическая нагрузка на подшипник может вызвать вибрацию или повреждение «крышек». ![]() |
[Рис. 4] Увеличенное в 300 раз изображение шейки коленчатого вала, выполненного из чугуна с шаровидным графитом, в поперечном разрезе. На нем хорошо видны «крышки», показанные на Рисунке 3. |
По материалам компании Federal-Mogul
Коленчатый вал двигателя
Коленчатый вал двигателя воспринимает действия расширяющихся газов при рабочем ходе поршней, передаваемые шатунами, и преобразуем их в крутяший момент. Кроме того, коленчатый вал обеспечивает движение поршней во время вспомогательных тактов и пуска двигателя.
Коленчатые валы двигателя изготовляются штамповкой из средне углеродистых легированных сталей и литьем из модифицированного магнием чугуна в зависимости от конструктивных и технологических особенностей коленчатых валов.
Коленчатый вал состоит из коренных и шатунных шеек, соединенных щеками, к которым крепятся противовесы (могут быть отлитыми как одно целое с налом) переднего конца коленчатого вала, на котором имеются посадочный поясок крепления газораспределительного зубчатого колеса и шкива. На заднем конце коленчатого вала имеется маслоотражательный гребень, маслосгонная резьба и фланец (может отсутствовать) для крепления маховика. В торце имеется гладкое отверстие иод подшипник дли опоры ведущего вала коробки передач. В коренных шейках для масляных каналов выполнены отверстия пол углом к пустотелым шатунным шейкам, гле масло дополнительно очищается под действием центробежных сил.
Форма коленчатого вала определяется числом и расположением цилиндров, порядком работы и тактностъю двигателя. В большинстве случаев применяют полноопорные коленчатые валы, т. к. каждая шатунная шейка расположена между коренными. Для повышения износостойкости поверхностный слой коренных и шатунных шеек подвергают закалке на глубину 3—4 мм с нагревом ТВЧ. После термической обработки шейки валов, проводят шлифование шеек и полируют. Для повышения жесткости и надежности коленчатых валов применяют перекрытие шеек. Перед капитальным ремонтом двигателя проводят исследование дефектов коленчатого вала. После чего составляют технологическую последовательность ремонта по устранению дефектов коленчатого вала.
Коленчатые валы двигателя:
а — двигателя автомобиля ЗИЛ-130; б — двигателя ЯМЗ — 236; в — КамАЗ-740; 1 — передний конец вала; 2 — грязеуловитель; 3 — шатунная шейка; 4 — противовесы; 5— масло отражатель; 6 — фланец для крепления маховика; 7 — коренная шейка; 8 — щека; 9 — гайка; 10 и 15 — съемные противовесы; 11 — распрелелтельное зубчатое колесо; 12— установочный штифт; 13 — зубчатое колесо привода масляного насоса; 14 — винт: 16 — шпонка; А — величина перекрытия шеек.
Коленчатый вал — что это такое
Коленчатый вал – это одна из самых важных деталей любого двигателя. Она строго индивидуальна для каждой модели автомобиля и в процессе работы притирается к конкретному двигателю.
1. Что такое коленчатый вал, его основные задачи?
Коленчатый вал (коленвал) – это главный элемент двигателя автомобиля, являющийся частью кривошипно-шатунного механизма, который преобразует энергию сгорающих в цилиндрах двигателя газов в механическую энергию.
Главная задача коленчатого вала – преобразовать возвратно-поступательные движения поршней двигателя в крутящий момент, который через трансмиссию передаётся на колёса автомобиля. Одной из основных технических характеристик коленчатого вала, как и всего двигателя, является радиус кривошипа. Это расстояние от осей коренных шеек (шейки, в которых вращается коленвал в цилиндровом блоке) к осям шатунных шеек (шейки, которые вращаются внутри большой головки шатуна). Удвоенный радиус кривошипа являет собой длину хода поршня, которая определяет объём цилиндров. Если изменить длину радиуса кривошипа при неизменном диаметре цилиндра, это приведёт к изменению объёма цилиндров. Эту зависимость часто используют, чтобы менять технические характеристики всего двигателя в определённом направлении.
Подбирая соотношение длины хода поршня и диаметра цилиндра, двигатель можно сделать длиноходным (ход поршня превышает диаметр цилиндра) или короткоходным (диаметр цилиндра больше, чем ход поршня). Короткоходные двигатели дают возможность повысить мощность за счёт увеличения скорости вращения. А длиноходные двигатели более экономичны и обеспечивают высокий крутящий момент на низких оборотах.
При изменении параметров коленчатого вала происходит изменение всех параметров двигателя, поэтому нужно быть предельно осторожным, тюнингуя свой автомобиль, так как технические характеристики часто меняются не в лучшую сторону.
2. Материалы, из которых изготовлен коленчатый вал.
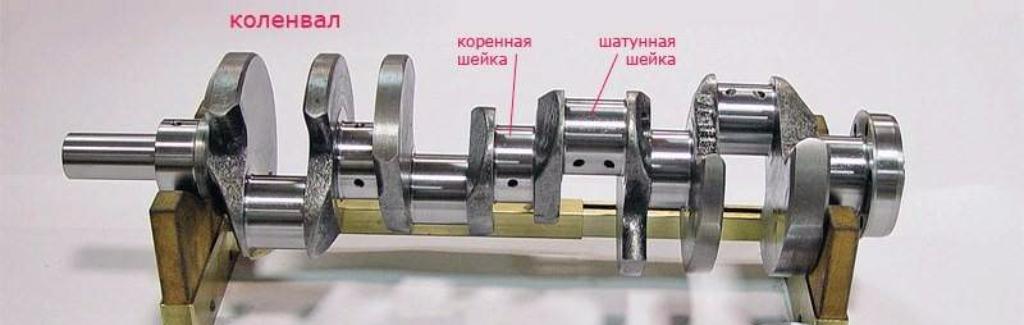
Когда двигатель работает, на коленчатый вал действую сильные нагрузки. Его надёжность определяется конструкцией и материалом, из которого он изготовлен. Этот элемент двигателя, как правило, имеет цельную структуру. А потому материалы для него должны быть максимально прочными, потому что от прочности коленчатого вала будет зависеть работа всей системы.
В качестве материалов для изготовления коленвалов используют углеродистую и легированную сталь либо чугун высокой прочности. Коленвал можно изготовить методом литья, методом ковки из стали или методом точения. Заготовки получают способом горячей штамповки или способом литья. Очень важно, как расположены волокна материалов в заготовках. Чтобы не допустить их перерезания в дальнейшей обработке, применяются гибочные ручьи. Когда заготовка готова, её дополнительно обрабатывают под высокой температурой и очищают от окалины (дробомётной машиной или методом травления).
Материал и способ производства коленвала подбирается в зависимости от типа и класса автомобиля.
1. В серийных моделях коленвал производят из чугуна методом литья. Это даёт возможность уменьшить себестоимость производства и уложиться в указанные расчёты.
2. Более дорогие спортивные модели оснащают кованным стальным коленвалом. Подобные детали имеют множество преимуществ над литыми по габаритам, весу и прочности, а потому всё чаще применяются в автомобилестроении.
3. Для самых дорогих двигателей коленвал вытачивают из цельного стального куска. При этом значительная часть материала попросту становится отходами.
3. Конструкция коленчатого вала.
Конструкция коленчатого вала определяются количеством цилиндров, их конфигурацией и порядком работы, от чего зависит расположение и количество коренных и шатунных шеек. Например, в двигателях V6 присутствует небольшое угловое смещение шатунных шеек по длине вала. В американской версии двигателя V8 коленвал напоминает крест, а в европейской версии V8 для спортивных автомобилей коленвал плоский. Несмотря на всё это, конструкция разных коленчатых валов очень похожа.
Конструктивно коленчатый вал состоит из таких основных элементов:
1. Коренные шейки – опорная шейка, которая находится в коренном подшипнике (располагается в картере двигателя).
2. Шатунные шейки – опорные шейки, которые связывают коленвал с шатунами (в них проходят масленые каналы для смазки) и служат опорой для шатунов.
3. Щёки вала – элемент, который связывает между собой коренные и шатунные шейки.
4. Носок (выходная передняя часть вала) – часть, на которую крепится зубчатое колесо либо шкив отбора мощности, соединяющиеся с газораспределительным механизмом, распределительным валом, гасителем крутильных колебаний, вспомогательными узлами и элементами.
5. Хвостик (выходная задняя часть вала) – часть, которая соединяется с маховиком или шестернёй отбора мощности.
6. Противовесы – элемент коленвала (по сути, продолжение щеки в противоположную сторону от шатунных шеек), который отвечает за разгрузку коренных шеек от сил инерции нижних частей шатунов и неуравновешенных масс кривошипа и обусловливают плавную работу двигателя.
7. Подшипники скольжения – обеспечивают вращение коленчатого вала на опорах. Подшипники являют собой тонкостенные вкладыши, изготовлены из стальной ленты с антифрикционным слоем. Вкладыши фиксируются в опоре выступом, который не позволяет им перекручиваться или за счёт тугой посадки. Наличие смазки обеспечивает простое вращение в подшипниках на протяжении долгого времени.
8. Упорный подшипник скольжение – элемент, который не допускает осевых перемещений коленчатого вала. Он устанавливается на крайнюю коренную шейку или на среднюю коренную шейку.
Количество коренных шеек, обычно, превышает количество шатунных на единицу (такой коленвал называют полноопорным) и они имеют больший диаметр.
Коленом называют шатунную шейку, которая располагается между двумя щеками. Положение колен определяется особенностями работы двигателя, положением его цилиндров и должно обеспечивать его уравновешенность, минимальные колебания и минимальные крутильные моменты.
Место перехода шейки к щеке – это самое нагруженное место в конструкции коленвала. Для того, чтобы снизить напряжение на это место, переход делают с галтелью (радиусом закругления). Галтели увеличивают длину вала и для снижения этого значения их углубляют в шейку или щеку. Все коренные и шатунные шейки интегрированы в смазочную систему двигателя. Эти элементы смазываются под давлением. Подвод масла организован к каждой из коренных шеек от общей магистрали в индивидуальном порядке. А к шатунным шейкам масло попадает по каналам в щеках.
4. Обслуживание коленчатого вала.
Коленчатый вал, как и любая деталь автомобиля требует периодического обслуживания. Для этого нужно уметь его снимать и устанавливать обратно.
Снятие коленчатого вала производится в такой последовательности:
1. Демонтируется двигатель из автомобиля, а потом из него снимаются все элементы.
2. Двигатель переворачивается коленвалом к верху. Крышки коренных подшипников отличаются, поэтому необходимо запомнить их положение.
3. Снимаются крышки коренных подшипников.
4. Поднимается коленвал, а заднее уплотнительное кольцо снимается.
5. Снимаются коренные вкладыши с крышек коренных подшипников и блока цилиндров.
После снятия производится проверка коленчатого вала.
Алгоритм проверки коленчатого вала:
1. Промыть бензином все составляющие и просушить деталь.
2. Тщательно осмотреть коленвал на наличие негативных следов от использования (трещины, сколы, сильный износ). Если же коленвал признан непригодным для дальнейшей эксплуатации, то придётся приобрести новый.
3. Прочистить, промыть и продуть сжатым воздухом все каналы для масла, предварительно открутив пробки.
4. Если на шатунных шейках обнаружены задиры или царапины, то их необходимо отшлифовать и отполировать. После этого опять следует продуть воздухом масляные каналы.
5. Осмотреть вкладыши коренных подшипников. Если на них есть дефекты, то их необходимо заменить на новые.
6. Осмотреть маховик и при обнаружении на нём дефектов, маховик стоит заменить.
7. Осмотреть подшипник носка и, если на нём есть негативные следы эксплуатации, то его нужно выпрессовать и запрессовать новый.
8. Осмотреть сальник, который находится в крышке распределительных звёздочек и при необходимости заменить эту деталь. При большом пробеге автомобиля сальник меняют в обязательном порядке.
9. Сменить и обжать набивку заднего уплотнения коленвала.
10. Проверить резиновые уплотнители, которые расположены в держателе набивки. Если они непригодны для дальнейшего использования, то их нужно заменить.
После проверки коленчатый вал необходимо установить обратно. Установка коленчатого вала производится в обратной последовательности к его снятию. Перед установкой нужно обязательно смазать все шейки и другие элементы коленвала моторным маслом. После установки следует проверить, что коленчатый вал вращается легко и плавно. В противном случае придётся его опять снять и установить заново, добиваясь плавности хода.
Подписывайтесь на наши ленты в таких социальных сетях как, Facebook, Вконтакте, Instagram, Pinterest, Yandex Zen, Twitter и Telegram: все самые интересные автомобильные события собранные в одном месте.
Коренная шейка коленчатого вала – АвтоТоп
Проверка зазора в коренном подшипнике
- Снимите крышку коренного подшипника и нижний вкладыш.
- Очистите подшипник и коренную шейку коленчатого вала.
- Уложите отрезок пластичного калибра на каждую коренную шейку коленчатого вала.
- Установите крышки подшипников и затяните винты крепления. Момент затяжки: 54-59 Нм.
Примечание: не поворачивайте коленчатый вал.
- Снимите крышку и нижний вкладыш подшипника.
- С помощью контрольной шкалы измерьте ширину расплющенного участка калибра в самом широком месте. Номинальный зазор: 0,022-0,040 мм.
20.Если зазор превышает максимально допустимое значение, замените вкладыш коренного подшипника новым с аналогичной маркировкой и повторите проверку.
Внимание: механическая обработка вкладышей или крышки недопустима.
20.Если зазор в новых подшипниках все равно не соответствует требуемой величине, подберите вкладыш большего или меньшего размера (в соответствии с маркировкой) и повторите проверку.
Примечание: если требуемая величина зазора не достигается подбором подшипников, замените коленчатый вал.
Маркировка опор коленчатого вала
Примечание: буквенная маркировка всех пяти опор коленчатого вала выбита на нижней части блока цилиндров.
Метка | Внутренний диаметр, мм |
а | 54,000-54,006 |
b | 54,006-54,012 |
с | 54,012-54,018 |
Маркировка коренных шеек коленчатого вала
Метка | Диаметр шейки, мм |
а | 49,962-49,968 |
b | 49,956-49,962 |
с | 49,950-49,956 |
Примечание: маркировка всех пяти коренных шеек коленчатого вала выбита на переднем противовесе коленчатого вала.
- Буквенная маркировка размерной группы коренных шеек
Маркировка коренного подшипника
Класс | Цветовая |
маркировка
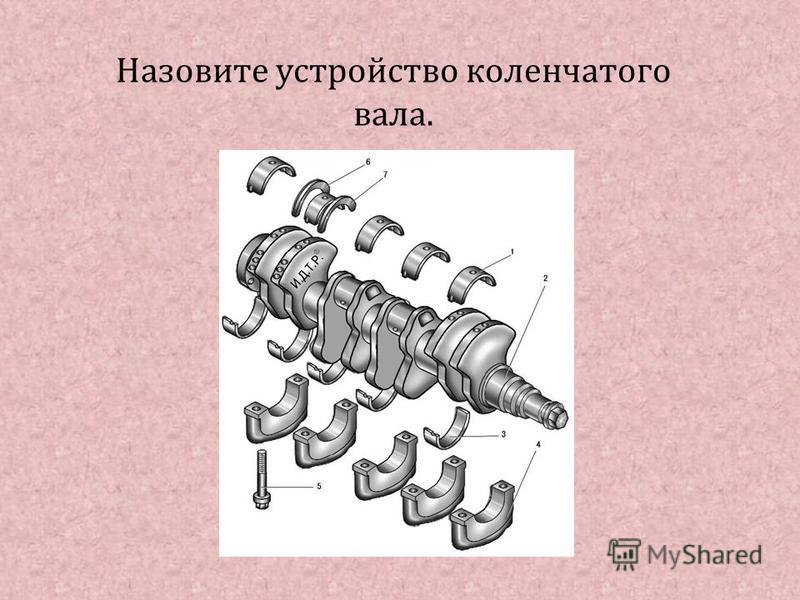
- Буквенная маркировка вкладыша
- Цветовая метка
Таблица для подбора вкладышей коренных подшипников
Маркировка вкладыша коренного подшипника в зависимости от размерной группы посадочного отверстия в блоке цилиндров | ||||
Размерная группа а | Размерная группа b | Размерная группа с | ||
Маркировка размерной группы коренной шейки | а | D(желтый) | С (зеленый) | В(-) |
b | С (зеленый) | В(-) | А (черный) | |
с | В(-) | А (черный) | АА(синий) |
Проверка осевого разбега коленчатого вала
21. Индикатором измерьте осевой разбег коленчатого вала, перемещая его отверткой вперед и назад. Номинальное значение: 0,05-0,175 мм. Предельное значение: 0,2 мм.
22.Если измеренное значение больше предельно допустимого, замените упорный подшипник.
Проверка геометрических параметров
23.Микрометром измерьте диаметр всех коренных и шатунных шеек.
Коренная шатунная шейка – коленчатый вал
Коренные и шатунные шейки коленчатого вала выполняют одинакового диаметра; шатунные шейки обычно имеют меньший диаметр. Коренные и шатунные шейки шлифуют; при этом допуск на диаметр должен быть выдержан в пределах 6 – 10 мкм, отклонение от круглости и цилиндр ич-ности до 3 мкм, параметр шероховатости Ra 0 63 мкм, отклонение от параллельности осей коренных и шатунных шеек 6 – 8 мкм. [2]
Коренные и шатунные шейки коленчатого вала тщательно шлифуют и полируют. [3]
Коренные и шатунные шейки коленчатого вала закаливают и отпускают до требуемой твердости. Режим термической обработки устанавливается в зависимости от марки применяемой стали. Эта операция необходима для обеспечения износоустойчивости коренных и шатунных шеек коленчатого вала. [4]
Коренные и шатунные шейки коленчатого вала ввиду большой их твердости могут обрабатываться только шлифованием. Большая первоначальная глубина закаленного слоя исключает необходимость в термической обработке шеек после их шлифования под ремонтные размеры. Шлифование производится электрокорундовым кругом на керамической связке твердостью СТ2 или СТЗ и зернистостью 46 с обильным охлаждением. Скорость вращения шлифовального-кр – yta – 32 – 35 м / coit – я-коленчатого-вшга-бколо lOV – 12 м / мин для шатунных и 20 – 24 м / мин – для коренныхТПеекТпо – – перечная подача круга не должна превышать 0 006 мм на один оборот вала. На поверхности шеек после шлифования ни в коем случае не должно быть следов цветов побежалости. [5]
Коренные и шатунные шейки коленчатого вала соединены между собой щеками. [6]
Коренные и шатунные шейки коленчатого вала закалены токами высокой частоты. [8]
Коренные и шатунные шейки коленчатых валов просверливают и рарта-чивают насквозь. Шейки и щеки / просверливают также в радиальном направлении для подвода масла, нагнетаемого через полости в вале. Коленчатые валы авиационных двигателей, в отличие-от коленчатых валов других легких двигателей ( автомобильных и тракторных), обрабатывают по воем поверхностям и полируют. [9]
Коренные и шатунные шейки коленчатых валов звездообразных моторов высверливаются и затем растачиваются. В некоторых моторах шатунная шейка растачивается изнутри не насквозь. При этом образуется глухая полость ( фиг. [10]
Шлифование коренных и шатунных шеек коленчатых валов проводят на шлифовальных станках-автоматах. Скорость шлифования ( v 45 м / с) регулируется по мере изнашивания круга. Правка осуществляется алмазным роликом по копирной линейке. [12]
Для коренных и шатунных шеек коленчатых валов автомобильных двигателей овальность, конусность и вогнутость допускаются не больше 0 01 мм; для тракторных двигателей овальность шеек – не больше 0 02 мм и конусность на длине шейки 100 мм – не более 0 03 мм. [13]
При восстановлении коренных и шатунных шеек коленчатого вала под ремонтные размеры план операций технологического процесса может быть следующим: контроль биения и правка вала при необходимости; исправление центровых фасок; нарезание резьбы ремонтного размера под храповик; восстановление шпоночной канавки и шейки под шестерню и ступицу шкива; развертывание отверстий во фланце под болты крепления маховика, под подшипник конца ведущего вала коробки передач; запрессовка втулки; тонкое растачивание отверстия под наружное кольцо шарикоподшипника; шлифование коренных и шатунных шеек; балансировка; суперфиниширование или полирование шеек; промывка масляных каналов; контроль вала. [14]
В этих условиях коренные и шатунные шейки коленчатого вала подвергаются износу. [15]
- Коленчатый вал – что это такое
- 1. Что такое коленчатый вал, его основные задачи?
- 2. Материалы, из которых изготовлен коленчатый вал.
- 3. Конструкция коленчатого вала.
- 4. Обслуживание коленчатого вала.
Коленчатый вал – это одна из самых важных деталей любого двигателя. Она строго индивидуальна для каждой модели автомобиля и в процессе работы притирается к конкретному двигателю.
1. Что такое коленчатый вал, его основные задачи?
Коленчатый вал (коленвал) – это главный элемент двигателя автомобиля, являющийся частью кривошипно-шатунного механизма, который преобразует энергию сгорающих в цилиндрах двигателя газов в механическую энергию.
Подбирая соотношение длины хода поршня и диаметра цилиндра, двигатель можно сделать длиноходным (ход поршня превышает диаметр цилиндра) или короткоходным (диаметр цилиндра больше, чем ход поршня). Короткоходные двигатели дают возможность повысить мощность за счёт увеличения скорости вращения. А длиноходные двигатели более экономичны и обеспечивают высокий крутящий момент на низких оборотах.
При изменении параметров коленчатого вала происходит изменение всех параметров двигателя, поэтому нужно быть предельно осторожным, тюнингуя свой автомобиль, так как технические характеристики часто меняются не в лучшую сторону.
2. Материалы, из которых изготовлен коленчатый вал.
Когда двигатель работает, на коленчатый вал действую сильные нагрузки. Его надёжность определяется конструкцией и материалом, из которого он изготовлен. Этот элемент двигателя, как правило, имеет цельную структуру. А потому материалы для него должны быть максимально прочными, потому что от прочности коленчатого вала будет зависеть работа всей системы.
В качестве материалов для изготовления коленвалов используют углеродистую и легированную сталь либо чугун высокой прочности. Коленвал можно изготовить методом литья, методом ковки из стали или методом точения. Заготовки получают способом горячей штамповки или способом литья. Очень важно, как расположены волокна материалов в заготовках. Чтобы не допустить их перерезания в дальнейшей обработке, применяются гибочные ручьи. Когда заготовка готова, её дополнительно обрабатывают под высокой температурой и очищают от окалины (дробомётной машиной или методом травления).
Материал и способ производства коленвала подбирается в зависимости от типа и класса автомобиля.
1. В серийных моделях коленвал производят из чугуна методом литья. Это даёт возможность уменьшить себестоимость производства и уложиться в указанные расчёты.
2. Более дорогие спортивные модели оснащают кованным стальным коленвалом. Подобные детали имеют множество преимуществ над литыми по габаритам, весу и прочности, а потому всё чаще применяются в автомобилестроении.
3. Для самых дорогих двигателей коленвал вытачивают из цельного стального куска. При этом значительная часть материала попросту становится отходами.
3. Конструкция коленчатого вала.
Конструкция коленчатого вала определяются количеством цилиндров, их конфигурацией и порядком работы, от чего зависит расположение и количество коренных и шатунных шеек. Например, в двигателях V6 присутствует небольшое угловое смещение шатунных шеек по длине вала. В американской версии двигателя V8 коленвал напоминает крест, а в европейской версии V8 для спортивных автомобилей коленвал плоский. Несмотря на всё это, конструкция разных коленчатых валов очень похожа. Конструктивно коленчатый вал состоит из таких основных элементов:
1. Коренные шейки – опорная шейка, которая находится в коренном подшипнике (располагается в картере двигателя).
2. Шатунные шейки – опорные шейки, которые связывают коленвал с шатунами (в них проходят масленые каналы для смазки) и служат опорой для шатунов.
3. Щёки вала – элемент, который связывает между собой коренные и шатунные шейки.
4. Носок (выходная передняя часть вала) – часть, на которую крепится зубчатое колесо либо шкив отбора мощности, соединяющиеся с газораспределительным механизмом, распределительным валом, гасителем крутильных колебаний, вспомогательными узлами и элементами.
5. Хвостик (выходная задняя часть вала) – часть, которая соединяется с маховиком или шестернёй отбора мощности.
6. Противовесы – элемент коленвала (по сути, продолжение щеки в противоположную сторону от шатунных шеек), который отвечает за разгрузку коренных шеек от сил инерции нижних частей шатунов и неуравновешенных масс кривошипа и обусловливают плавную работу двигателя.
7. Подшипники скольжения – обеспечивают вращение коленчатого вала на опорах. Подшипники являют собой тонкостенные вкладыши, изготовлены из стальной ленты с антифрикционным слоем. Вкладыши фиксируются в опоре выступом, который не позволяет им перекручиваться или за счёт тугой посадки. Наличие смазки обеспечивает простое вращение в подшипниках на протяжении долгого времени.
8. Упорный подшипник скольжение – элемент, который не допускает осевых перемещений коленчатого вала. Он устанавливается на крайнюю коренную шейку или на среднюю коренную шейку. Количество коренных шеек, обычно, превышает количество шатунных на единицу (такой коленвал называют полноопорным) и они имеют больший диаметр.
Коленом называют шатунную шейку, которая располагается между двумя щеками. Положение колен определяется особенностями работы двигателя, положением его цилиндров и должно обеспечивать его уравновешенность, минимальные колебания и минимальные крутильные моменты.
Место перехода шейки к щеке – это самое нагруженное место в конструкции коленвала. Для того, чтобы снизить напряжение на это место, переход делают с галтелью (радиусом закругления). Галтели увеличивают длину вала и для снижения этого значения их углубляют в шейку или щеку. Все коренные и шатунные шейки интегрированы в смазочную систему двигателя. Эти элементы смазываются под давлением. Подвод масла организован к каждой из коренных шеек от общей магистрали в индивидуальном порядке. А к шатунным шейкам масло попадает по каналам в щеках.
4. Обслуживание коленчатого вала.
Коленчатый вал, как и любая деталь автомобиля требует периодического обслуживания. Для этого нужно уметь его снимать и устанавливать обратно.
Снятие коленчатого вала производится в такой последовательности:
1. Демонтируется двигатель из автомобиля, а потом из него снимаются все элементы.
2. Двигатель переворачивается коленвалом к верху. Крышки коренных подшипников отличаются, поэтому необходимо запомнить их положение.
3. Снимаются крышки коренных подшипников.
4. Поднимается коленвал, а заднее уплотнительное кольцо снимается.
5. Снимаются коренные вкладыши с крышек коренных подшипников и блока цилиндров.
После снятия производится проверка коленчатого вала.
Алгоритм проверки коленчатого вала:
1. Промыть бензином все составляющие и просушить деталь.
2. Тщательно осмотреть коленвал на наличие негативных следов от использования (трещины, сколы, сильный износ). Если же коленвал признан непригодным для дальнейшей эксплуатации, то придётся приобрести новый.
3. Прочистить, промыть и продуть сжатым воздухом все каналы для масла, предварительно открутив пробки.
4. Если на шатунных шейках обнаружены задиры или царапины, то их необходимо отшлифовать и отполировать. После этого опять следует продуть воздухом масляные каналы.
5. Осмотреть вкладыши коренных подшипников. Если на них есть дефекты, то их необходимо заменить на новые.
6. Осмотреть маховик и при обнаружении на нём дефектов, маховик стоит заменить.
7. Осмотреть подшипник носка и, если на нём есть негативные следы эксплуатации, то его нужно выпрессовать и запрессовать новый.
8. Осмотреть сальник, который находится в крышке распределительных звёздочек и при необходимости заменить эту деталь. При большом пробеге автомобиля сальник меняют в обязательном порядке.
9. Сменить и обжать набивку заднего уплотнения коленвала.
10. Проверить резиновые уплотнители, которые расположены в держателе набивки. Если они непригодны для дальнейшего использования, то их нужно заменить.
После проверки коленчатый вал необходимо установить обратно. Установка коленчатого вала производится в обратной последовательности к его снятию. Перед установкой нужно обязательно смазать все шейки и другие элементы коленвала моторным маслом. После установки следует проверить, что коленчатый вал вращается легко и плавно. В противном случае придётся его опять снять и установить заново, добиваясь плавности хода.
Подписывайтесь на наши ленты в таких социальных сетях как, Facebook, Вконтакте, Instagram, Twitter и Telegram: все самые интересные автомобильные события собранные в одном месте.
Шлифовка шейки коленвала | ООО «ВЭР»
Попробуем разобраться, зачем шлифовать этот узел, как предотвратить его преждевременный выход из строя.
Шлифовка шеек коленчатого вала – одна из самых трудоёмких ремонтных процедур. Её выполнение в условиях домашней мастерской практически невыполнимо, так как требует применения высокоточного инструмента. Также от ремонтников потребуется определённый опыт работы. Довериться частным мастерам скорее всего не получится – оборудование для шлифовки шейки вала найдётся только в крупных мастерских. Попробуем разобраться, зачем шлифовать этот узел, как предотвратить его преждевременный выход из строя и где лучше всего выполнить ремонтные работы.
Зачем проводится шлифовка шейки вала
Коленвал (он же коленчатый вал) – ответственная часть двигателя внутреннего сгорания, отвечающая за передачу возвратно-поступательных движений поршней во вращение. Деталь имеет довольно сложную форму, обточенную с точностью до сотых долей миллиметра. Шатуны поршней закрепляются на шейках коленвала – это цилиндрические опоры, отвечающие за передачу усилия от поршней. Прикрепление выполняется с помощью подшипников скольжения.
Следует отметить, что столь ответственная часть изготавливается из высокопрочной стали, слабо подверженной износу. Тем не менее, износ имеется, а его интенсивность зависит от многих факторов, в том числе от характера вождения автомобиля. Используемые здесь коренные и шатунные подшипники скольжения контактируют с валом посредством сменных вкладышей. В случае ремонта они подлежат замене.
Что же происходит в процессе эксплуатации двигателя внутреннего сгорания? Вкладыши постепенно изнашиваются (даже при самой аккуратной и бережной езде), одновременно с этим изнашиваются и шейки, на которых закрепляются шатуны поршней. В какой-то момент износ становится настолько большим, что дальнейшая эксплуатация двигателя становится невозможной – ему нужен ремонт. При этом менять дорогостоящий вал полностью пока не нужно – его можно отремонтировать:
- Двигатель разбирается, из него извлекается вал;
- Производится шлифовка шеек коленчатого вала;
- Меняются изношенные в процессе эксплуатации вкладыши.
После этого двигатель собирается и проверяется.
За кажущейся простотой ремонтных работ скрывается их сложность. Разобрать двигатель и извлечь коленчатый вал сможет каждый мастер. То же самое относится к съёму шатунов. Но шлифовка шейки коленвала возможно только при наличии токарного станка, способного снимать сотые доли миллиметра металла. Обойтись простым промышленным токарным станком или кустарным оборудованием не получится – здесь требуется высокая точность. Именно поэтому шлифовка шеек коленчатого вала осуществляется только в условиях мастерских, где имеется соответствующее оборудование.
Что нужно учесть при шлифовке шейки вала? Необходимо найти шейку с максимальным износом и отталкиваться от неё, учитывая ремонтные размеры вкладышей. После этого вал закрепляется в токарном станке и протачивается до выбранного размера – снимаются десятые или даже сотые доли миллиметра металла, в зависимости от степени износа. Токарный станок протачивает шейки настолько точно, что готовая поверхность получается идеально ровной. Далее вал промывается, устанавливается на место, производится сборка двигателя. Следующий этап – это бережная обкатка в течение нескольких дней, которая покажет, как ведёт себя ДВС. Если всё хорошо, можно приступать к повседневной эксплуатации в привычном режиме.
Как предотвратить повреждение коленвала
Ключевое воздействие на коленвал оказывает характер езды. Резкие рывки, гонки по трассе, езда на повышенных оборотах – всё это приводит к повышенному износу. При этом многие «гонщики» умудряются удивляться, почему двигатель так быстро вырабатывает свой ресурс. Следует помнить, что даже самые маленькие перегрузки многократно увеличивают износ коленвала, приближая момент дорогостоящего ремонта.
Чтобы продлить жизнь коленвала и двигателя, следуйте рекомендациям:
- Водите автомобиль аккуратно, не нагружайте двигатель – в этом случае он прослужит максимально долго. Типичный пример нагрузки – перевозка грузов, вес которых превышает грузоподъёмность автомобиля;
- Вовремя меняйте масло – стоит это не так уж и дорого, а в большинстве случаев его можно поменять самостоятельно, воспользовавшись инструкциями из интернета.
Интервал замены масла составляет 10-15 тыс. км, в зависимости от марки автомобиля. Езда на отработанном масле приводит к перегреву двигателя и увеличивает трение. Одновременно с этим детали двигателя подвергаются коррозии;
- Пользуйтесь маслами от проверенных производителей и только рекомендованной вязкости. Это поможет сохранить целостность коленвала.
Не производите ремонт самостоятельно – помните, что шлифовка шейки вала должна осуществляться квалифицированными специалистами, обладающими опытом работы на высокоточных фрезерных станках.
Шлифовка коленчатого вала в компании Механика, территория г.Дзержинский
Коленчатый вал – деталь непростая
Коленчатые валы поражают обилием форм и размеров: плоские и пространственные, длинные и короткие, разные по размерам, весу, жесткости, и, конечно же, по числу коренных и шатунных шеек.
Коленчатый вал часто называют не просто деталью, а системой. И вполне оправданно – любое сколь-нибудь существенное воздействие (механическое или термическое) на шейку, щёку, галтель или любой другой участок вызывает реакцию всей детали, отклик. И выражается он в виде деформации тех или иных зон, грозящей вызывать биение и дисбаланс.
Поэтому ремонтировать коленчатый вал необходимо только профессионально, руководствуясь принципом «не навреди». Иначе – выбраковка дорогой детали.
Когда требуется шлифовка
Первый признак необходимости ремонта коленчатого вала замечает водитель – это падение давления масла. Значит, подшипники скольжения скорее всего изношены и масляный клин между шейкой и стенкой вкладыша недостаточно плотный и надежный.
Помогает и взятие пробы масла из картера. Существуют методики, основанные на спектральном анализе таких проб. Если прибор показывает в масле следы меди и некоторых других цветных металлов, можно говорить о вероятном износе вкладышей.
Но окончательный диагноз ставится лишь после разборки двигателя и замеров геометрии коленчатого вала. И тогда выносится вердикт: вал требует шлифовки в ремонтный размер. Именно шлифовки в отличие от расточки блока – ведь шейки имеют закаленный слой, а такая поверхность не для резца. Приносим извинения за столь банальное уточнение, но вдруг кто-то из читателей не знаком с технологией коленчатого вала и металловедением. Знаете, в интернете всякое встречается…
В цехах «Механики». Диагностика
(фото: диагностика состояния коленчатого вала)
Дальнейший разговор поведем, опираясь на опыт компании «Механика». Здесь принимают в ремонт любые коленчатые валы – от автомобильных (бензиновый ДВС, дизель) до громадных тепловозных.
Вал прибывает в ремонт в составе двигателя либо отдельно, если мотор уже разобран самим заказчиком. И сразу попадает на проверку. Первое, что с ним делают – замеряют износ шеек.
Вал устанавливается крайними коренными шейками на призмы. Далее мастер микрометром замеряет диаметры всех шеек в нескольких плоскостях, чтобы проверить – есть ли «эллипс»? До величины 0,01 мм его можно вытерпеть, больше – нет.
Про замеры шеек, как правило, клиенты знают. Это делают во всех мастерских. Но «Механика» выполняет еще один замер – прогиб (биение) вала. К центральной коренной шейке подводят часовой индикатор и вращают вал на призмах. Если стрелка отклоняется в пределах 0,01 мм – прекрасно. Эту «сотку» можно списать на погрешность измерений. Также необходимо проверить биение хвостовика и поверхностей сальников.
А если биение центральной коренной шейки больше «сотки»? По опыту компании, биение до 0,1 (а иногда до 0,2 мм) исправляется шлифовкой. Разумеется, с учетом особенностей данного вала.
В цехах «Механики». Шлифовка
(фото: шлифовка коленчатого вала)
Итак, вал замерен. Принято решение шлифовать шейки – в какой именно размер, зависит от их износа и наличия в каталогах производителя соответствующих вкладышей.
Правда, ухо здесь надо держать востро. В разных каталогах разных производителей вкладышей встречается различные ряды ремонтных размеров. Например, у официалов только 0,25 мм, у Кольбеншмидт (Kolbenschmidt) – 0,25 и 0,5, а у американского Глико (Glyco ) еще и 0,75 мм. Еще нюанс: присутствие вкладышей в каталоге еще не означает, что они есть в природе. Поэтому важно уточнить их фактическое наличие и лишь тогда приступать к работе.
Для шлифовки применяются специализированные шлифовальные станки. Главная их «изюминка» – приспособления, позволяющие смещать зажимные кулачки относительно оси станка. Это позволяет шлифовать шатунные шейки. Точность станков – 5 мкм.
Как закрепляется вал? В «Механике» рассказали, что при шлифовке коренных шеек валов легковых двигателей деталь закрепляется в центрах. При этом необходима подготовка внутренних фасок – их предварительно протачивают на токарном станке.
Когда подпираешь деталь центром, очень важно «не пережать», иначе вал в станке может деформироваться – вспомните, с чего мы начали эту статью.
Если вал «грузовой», тяжелый, его зажимают в патроне по поверхности заднего сальника, а передняя часть подпирается центром. Здесь тоже требуется подготовка фаски на токарном станке.
Что касается шатунных шеек, при их обработке вал фиксируется в патронах с обеих сторон. Разумеется, со смещением на радиус кривошипа и тщательным выставлением оси каждой шатунной шейки в ось вращения станка с помощью индикаторной стойки.
Шлифовка каждой шейки осуществляется, как правило, в два прохода. Например, если вал шлифуется в ремонтный размер 0,25 мм, то сначала снимается слой 0,15 – 0,2 мм. А потом, уже с меньшей подачей, шейка выводится в окончательный размер. Подача смазочно-охлаждающей жидкости (СОЖ) обязательна – иначе шейка перегреется.
Долго ли длится сам процесс, включая переналадку под коренные или шатунные шейки? По опыту компании, на шлифовку вала четырехцилиндрового двигателя легкового автомобиля уходит порядка 40 мин.
Но это время можно и сократить – например, если обрабатывать партию однотипных валов. В этом случае задействуются два станка – на одном шлифуют коренные шейки, на другом шатунные.
Нельзя не сказать и об инструменте – шлифовальных кругах. К ним тоже есть свои требования, и довольно жесткие. Например, биение круга должно быть менее 3-4 мкм, иначе шейка из круглой может превратиться в граненую. Этот дефект называется дроблением.
И еще. Если шейка имеет канавку для выхода круга, никакой особой подготовки инструмента не потребуется. А если ее нет? Тогда галтель будет подрезана, что недопустимо. Ведь в вале появится опасный концентратор напряжений, резко снижающий усталостную прочность детали.
В этом случае шлифовальный круг заправляется специальным алмазным инструментом таки образом, чтобы радиус закругления края был равен радиусу галтели. И тогда шлифовка станет для вала безопасной.
И завершает процесс ремонта полировка шеек. Она не только убирает микронеровности, повышая качество поверхности, но и уничтожает заусенцы в на масляных отверстиях на шейках.
После работ необходимо очистить все масляные каналы от технологической грязи после шлифовки и полировки.
В цехах «Механики». Несколько подробностей
Выходной контроль при передаче отремонтированного вала заказчику – процедура обязательная. Проверка размеров и формы шлифованных шеек – это само собой. А еще вал устанавливается на призмы и проверяется с помощью индикатора на биение. Если уложились в «сотку», прекрасно, деталь можно смело ставить в двигатель.
Правда, и здесь есть свои нюансы. Вал по разным плоскостям имеет не равную жесткость. Тяжелый вал может прогнуться и от собственного веса. Поэтому в ряде случаев допускается прогиб равный монтажному зазору.
Есть еще один подводный камень – состояние посадочного места для подшипника первичного вала коробки. Многие мастерские пренебрегают его проверкой и получают претензии: вы сделали мотор, сделали коробку, почему же коробка выходит из строя?
Загадка в следующем. Гнездо для подшипника может иметь биение. Вина ли это завода или предыдущего некачественного ремонта, неважно. Важно этот дефект устранить. Мастер разворачивает индикаторную стойку, упирает щуп во внутреннюю стенку гнезда и вращает вал. Ага, биение есть.
Вал ставят в токарный станок, базируясь по коренной шейке, и протачивают бьющее отверстие на 2 мм «в плюс». Затем запрессовывают в него стальную втулку и протачивают посадочное место под подшипник первичного вала. Все – теперь подшипник сосен с шейкой, и приключений с коробкой не будет.
Подробности можно приводить еще и еще, но, как говорил Козьма Прутков, нельзя объять необъятное. Поэтому резюмируем: используя отличное знание коленчатых валов, применяя индивидуальный подход к каждому случаю, базируясь на современных технологиях и станочном парке, компания неизменно обеспечивает высокое качество ремонта.
И еще. Качество и опыт – вещи неразделимые. Об опыте «Механики» свидетельствует такая история. Однажды, еще в 90-х (так ли уж важна точная дата?) компанию посетили представители известной фирмы Кольбеншмидт. И среди прочего поинтересовались: а сколько валов вы делаете в своем цехе? Где-то штук пятнадцать, ответили в «Механике». В неделю, уточнили немцы? В день, пояснили в «Механике». Надо было видеть глаза гостей.
И в заключение рекомендуем к просмотру ролики. В них руководитель «Механики» Д.Н. Даньшов рассказывает о тонкостях шлифовальных технологий.
Автор: Юрий Буцкий, к.т.н.
Как проверить зазоры в подшипниках
Проверка и регулировка зазоров подшипников — один из наиболее важных аспектов конструкции двигателя. В этом сегменте мы подробно рассмотрим, как измерить кривошип, шатуны и подшипники.
Простой факт заключается в том, что установка зазора подшипника для высокопроизводительного двигателя — это то, что нельзя сократить. Не существует быстрых и простых способов установить этот критический зазор, независимо от того, является ли двигатель круизным двигателем с костями или дорожным животным, которое выдержит сотни миль жестокого обращения. Мы рассмотрим основы измерения зазора подшипника и покажем, как избежать ошибок. Это также потребует некоторых важных измерительных инструментов. Скажем прямо: измерить зазор в подшипнике мощного двигателя невозможно с помощью Plastigage. Эти маленькие кусочки восковой нити не являются прецизионными измерительными приборами и не должны использоваться для определения зазора подшипника. Это может задеть чувства некоторых людей, но установка зазоров подшипников — процесс, который слишком важен, чтобы позволить что-либо, кроме ваших усилий.
Для начала потребуются несколько инструментов и точных измерительных устройств. Это начинается с точного внешнего микрометра в диапазоне журналов, которые вы будете измерять. Существуют дешевые микрометры, которых следует избегать.Настаивайте на использовании микрометра, который будет измерять с точностью до 0,0001 дюйма. Это абсолютная необходимость.
Для измерения внутреннего диаметра коренного или стержневого подшипника потребуется индикатор внутреннего диаметра. Лучшие из них имеют точность до 0,0001 дюйма. С помощью этих двух инструментов вы можете быстро определить зазоры в любом двигателе.
Измерение зазора подшипника имеет смысл только в том случае, если числа точны, поэтому используйте качественные инструменты. Микрометр должен показывать показания с точностью до четвертого знака после запятой, и необходим калибр с круглой шкалой.Процесс несложный, но требует определенных навыков обращения с микрометром и снятия показаний. Также важно всегда обнулять микрометр перед его использованием. Стандарты обычно поставляются с микрометром вместе с инструментом для точной настройки микрофона. Все стандарты также откалиброваны для использования при температуре 68 градусов F.
Прежде чем мы перейдем к собственно процессу, было бы неплохо поговорить об общих допусках. Общепринятое правило, которое большинство производителей коленчатых валов предпочитают для уличных и высокопроизводительных двигателей — 0.0010 дюймов на каждый 1 дюйм диаметра шейки. Таким образом, для основной шейки малого блока размером 2,45 дюйма зазор подшипника будет составлять 0,0024 дюйма. Для шейки стержня меньшего размера 2,100 дюйма допустимый зазор будет 0,0021 дюйма. Допустимые заводские допуски на стандартном малоблочном Chevy намного шире, чем это.
Начнем с измерения коренной шейки подшипника. Лучше всего измерять цапфу как минимум в двух разных плоскостях, чтобы определить диаметр и округлость. В идеале овальность должна быть нулевая, но можно увидеть отклонение от 0,0001 дюйма, которое может зависеть или не зависеть от точности измерения. В зависимости от области применения новые спецификации коленчатого вала требуют биения и конуса не более 0,0002 дюйма как для шатунов, так и для сети.
Измерьте шейку коленчатого вала и запишите диаметр всех шейек на листе.Для нового коленчатого вала вы должны обнаружить, что шатуны и сеть, вероятно, будут отличаться не более чем на +/- 0,0001 дюйма. Мы измерили коленчатый вал с малым блоком K1, и разница между шейками шатуна составила менее 0,0002 дюйма. Например, большинство наших цапф стержней имели размер 2,09951 дюйма.
После измерения шейки пора установить индикатор внутреннего диаметра подшипников штока. Для начала мы установили наш индикатор диаметром чуть более 2100 дюймов, чтобы установить нагрузку на датчик.Затем мы установили наш микрометр на 2,1000 дюйма и поместили его в защищенные тиски, чтобы удерживать его на месте, пока мы устанавливаем циферблатный индикатор на ноль (0) при этой спецификации 2,100 дюйма.
Лучше использовать тот же микрометр, который использовался для считывания показаний цапф, чтобы установить нулевой зазор на индикаторе внутреннего диаметра.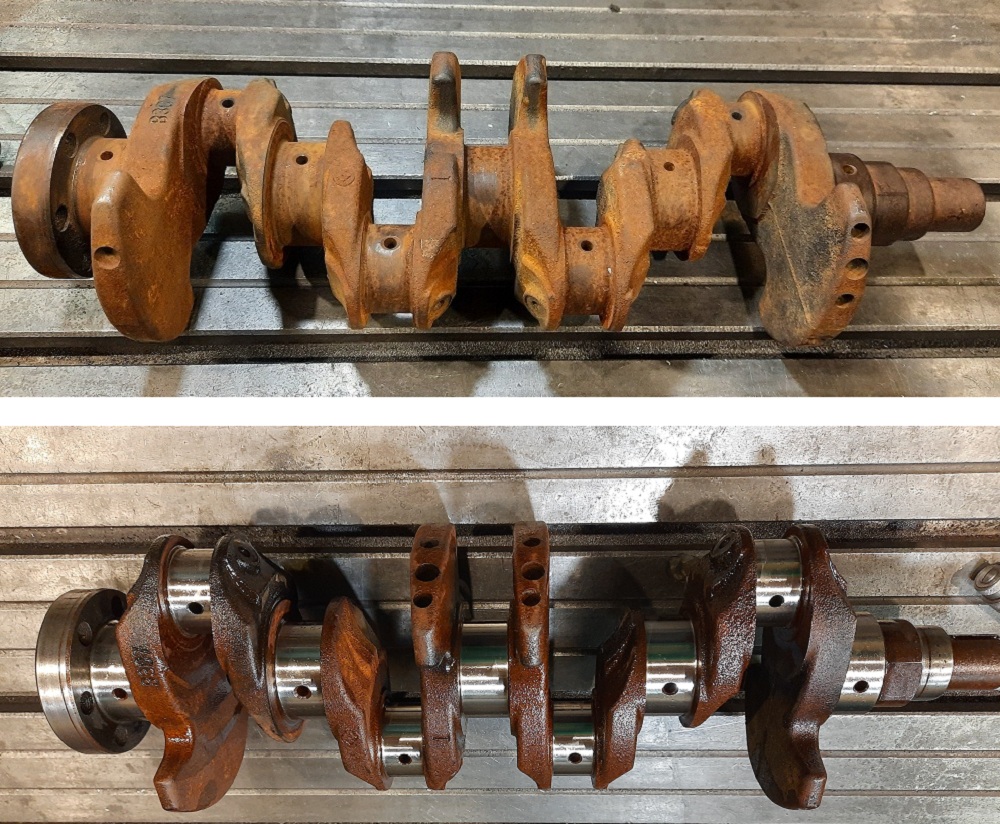
После этого мы поместили стандартный набор шатунных подшипников в шатун и затянули болты до требуемого значения растяжения шатуна (от 0,0055 до 0,0060 дюйма). После того, как оба болта были вытянуты, мы помещаем стрелочный индикатор в отверстие для измерения вертикального масляного зазора прямо на уровне штока.Важно всегда измерять масляный зазор в истинно вертикальной плоскости, так как все подшипники имеют эксцентриситет, обеспечивающий дополнительный зазор на линии разъема подшипников. Это сделано для компенсации нагрузки, поскольку стороны корпуса подшипника будут защемлены внутрь на линии разъема при высокой нагрузке.
Наше первое измерение с использованием стандартного подшипника для этого приложения показало зазор едва 0,0010 дюйма. Мы установили наш циферблатный индикатор на 2,100 дюйма, так как цапфа стержня номер один измеряла 2.0994 дюйма, мы добавили это 0,0006 дюйма к внутреннему диаметру подшипника, указанному на стрелочном индикаторе. Это обеспечило истинный зазор подшипника 0,0016 дюйма, что меньше нашего минимального значения 0,0021. Это может быть связано с проблемой накопления допусков, которая очень распространена. Вот почему мы измеряем зазор подшипника.
К счастью, все производители высокопроизводительных подшипников, такие как Federal-Mogul (Speed-Pro), Mahle-Clevite, King и другие, предлагают вкладыши подшипников различных размеров больше или меньше, чтобы производитель двигателей мог настраивать свои зазоры. В нашем случае Clevite предлагает подшипник 1X, который увеличивает зазор на 0,001 дюйма. Есть несколько методов, которые вы можете использовать, чтобы установить зазоры именно там, где вы хотите.
Например, добавление полного комплекта подшипников 1X теоретически добавит 0,001 дюйма, увеличивая зазор до 0. 0026 дюймов. На этом двигателе мы решили установить зазоры в подшипниках шатуна прямо в соответствии со спецификацией шейки 0,001 дюйма на дюйм, что может быть достигнуто путем добавления только одной из двух половин вкладыша подшипника. Это приемлемая процедура, если вы никогда не смешиваете половинки скорлупы с разницей более 0,001 дюйма. Так, например, никогда не комбинируйте половину 1X (+0,001 дюйма) с половиной -1 (0,001 дюйма), потому что толщина корпуса будет несовместимой.
При смешивании половин гильзы более толстая половина гильзы должна находиться в нагруженной стороне отверстия корпуса. Таким образом, в случае коренного подшипника более толстая половина вкладыша будет помещена в основную крышку, а в шатуне более толстая половина будет помещена в верхнее положение со штоком. Это создает ситуацию, когда под нагрузкой масляный зазор уменьшается на нагруженной стороне, поэтому более тонкая половина кожуха дает больше места для масла, поступающего в зону подшипника и поддерживающего смазку.
После измерения всех восьми зазоров в подшипниках шатунов и использования половин корпуса для установки зазоров, очень часто возникает разброс зазора между шатунами от 0,0004 до 0,0005 дюйма. Допустим, наш самый свободный подшипник штока имел размер 0,0028 дюйма, а самый плотный стержень — 0 мм.0023 дюйма — расширение 0,0005 дюйма. Мы обнаружили, что переключение самых жестких и слабых опор иногда может сблизить разброс. Для нашего двигателя мы измерили разброс всего 0,0003 дюйма.
Установка зазора подшипника не представляет особого труда, если вы работаете осторожно и дважды проверяете правильность всех цифр. Но как только вы это сделаете, вы просто убедитесь, что у двигателя есть большие шансы на выработку мощности в течение очень долгого времени.
Стальные шатуны , такие как кривошипы K1, используют большие радиусы галтелей на шейках шатунов, что требует суженных подшипников.Эти подшипники обычно имеют фаску, которая требует, чтобы подшипник был правильно установлен в стержне, при этом фаска подшипника должна совпадать с фаской на стержне. По этой причине подшипники обычно имеют маркировку «верхний» и «нижний».Спасите чудака | Коленчатый вал Огайо
Гоночный коленчатый вал не обязательно является одноразовым элементом. — Как видно из журнала Drag Racing Scene .
Гоночные шатуны выдерживают самые строгие допуски.Обычно обработанные поверхности на сегодняшних гоночных коленчатых валах выдерживаются с допуском 0,0003 дюйма (или лучше) прямо из коробки производителя. Эти прецизионные допуски на грунт обеспечивают отличные несущие поверхности, что продлевает срок службы кривошипа и опорных поверхностей при огромных скручивающих нагрузках, которые они испытывают в гоночных условиях.
В сфере дрэг-рейсинга нагрузка на коленчатый вал невероятна при преобразовании радиальных сил, действующих на поршень и шток, во вращательное движение коленчатого вала.Лучшие материалы и допуски на обработку в компонентах вашего двигателя находятся в состоянии войны с злоупотреблениями, связанными с высокими оборотами, сцеплениями, преобразователями крутящего момента и запусками. Список сценариев ненависти к коленчатому валу можно продолжать и продолжать.
Станция правки используется много раз в процессе ремонта, чтобы убедиться, что сварка и механическая обработка не приводят к изменению коленчатого вала.
Провала стержень или журнальный подшипник является самым распространенным бедствием в мучительном нижнем конце гоночного двигателя.Другие общие сбои включают площадь опоры тяги, как правило, расположен на заднем журнале блока. Сам коленчатый вал может выйти из строя без выхода из строя подшипника. Общий износ поверхностей коленчатого вала может выходить за рамки допустимых размеров, могут возникать трещины или изгибы.
Отремонтированный шатун затем подвергается механической обработке и повторной шлифовке на том же высокотехнологичном оборудовании, которое использовалось для создания новой линейки продуктов Ohio Crankshaft. Прежде чем бросить поврежденный дорогостоящий коленчатый вал в кучу металлолома, есть очень жизнеспособные методы ремонта для этих описанных сценариев.Конечно, самый простой ремонт — это переточить стандартный стержень и основную шейку до меньшего диаметра, устраняя таким образом повреждения.
Хотя подшипники легко доступны для компенсации уменьшения диаметра шейки кривошипа после «переточки», многие спорят о прочности коленчатого вала за пределами типичной очистки 0,010 / 0,010. Мы сохраним эту дискуссию для другой технической статьи.
На последнем этапе все допуски на размер снова проверяются по всему коленчатому валу, а затем каждая обработанная поверхность полируется в соответствии со спецификацией.Процессы предварительного и последующего нагрева различаются в зависимости от марки и материала кривошипа для нескольких печей Ohio Crank. Для достижения наилучшего результата с каждой рукояткой обращаются по-своему.
В процессе дуговой сварки под флюсом используется гранулированный флюс, который течет по активному сварному шву. Это пример очень популярного варианта ремонта коленчатого вала, выполняемого, когда упорный фланец изнашивается из-за проблем с трансмиссией или муфтой / преобразователем крутящего момента. Затем этот фланец можно приварить и повторно обработать до нужных размеров.
Есть уважаемые специалисты по коленчатым валам, такие как Ohio Crankshaft, у которых есть навыки и оборудование для ремонта ваших дорогих коленчатых валов, поэтому они живут, чтобы сражаться в другой день. Компания Ohio Crankshaft не только имеет более 1200 коленчатых валов для автоспорта и хот-родов, но также проверяет и ремонтирует сотни коленчатых валов в год. Их репутация в области ремонта шатунов варьируется от автоспорта до крупногабаритных шатунов для сельского хозяйства и промышленности. Многие ведущие автореставраторы полагаются на компанию Ohio Crankshaft при восстановлении незаменимых старинных коленчатых валов.
«Гоночные коленчатые валы достаточно просты, когда дело касается используемых материалов и процессов упрочнения», — объясняет Стэн Рэй, владелец коленчатого вала из Огайо. «Мы также ремонтируем коленчатые валы, начиная от огромных воздушных компрессоров и заканчивая кривошипами авиационных двигателей Allison длиной 7 1/2 футов и самолетами WWll. Некоторые из этих ремонтов могут быть сложными из-за уникальных материалов и процессов упрочнения. За годы работы мы освоили множество процессов сварки и термообработки для стольких различных материалов кривошипов ».
Ray рекомендует первым шагом в ремонте коленчатого вала является анализ поврежденного узла.
«Мы всегда рекомендуем клиенту позвонить нам, чтобы подробно описать, какой у него коленчатый вал и какие у него общие повреждения, прежде чем тратить доллары на доставку», — продолжает Рэй. «Хотя мы можем успешно отремонтировать некоторые довольно серьезные повреждения, нам просто неприятно видеть, как кто-то тратит деньги, чтобы отправить нам кривошип, который не подлежит ремонту. Что еще более важно, мы обычно можем послушать, какой у них коленчатый вал, вместе с описанием повреждения, и определить, можем ли мы его отремонтировать. Сегодняшние цифровые фотографии и электронная почта также могут помочь нам в диагностике ремонта ».
Как только кривошип прибывает, его подвергают тщательной проверке с помощью магнитопорошкового испытания, широко известного как процесс «Magnaflux». Кольцо электрического тока создает магнитное поле вокруг коленчатого вала. Жидкий раствор, содержащий мелкодисперсный порошок железа, течет по коленчатому валу.Трещина в металле нарушит магнитное поле, концентрируя таким образом смесь жидкости и металла в трещине. Ультрафиолетовый черный свет четко освещает любые трещины, обычно невидимые невооруженным глазом.
Мы следили за Рэем Дарнером в процессе ремонта. Дарнер имеет более чем 30-летний опыт шлифования и ремонта коленчатых валов в компании Ohio Crankshaft.
«Весь процесс ремонта основан на знании того, какой процесс лучше всего подходит для каждой ремонтируемой кривошипа», — говорит нам Дарнер. «При каждом ремонте учитывается различная сварочная проволока, температура сварки и скорость сварки».
Перед сваркой свариваемые поверхности коленчатого вала слегка шлифуют для удаления посторонних материалов, например материала подшипников, застрявших в кривошипе. Цапфы кривошипа также могут быть некруглыми на поврежденных поверхностях, так что это также обеспечивает ровную шейку при сварке.
На сварочной станции Ohio Crankshaft используется оборудование «подводной дугой», которое считается наиболее эффективным способом обеспечить надлежащее проникновение отложений материала для повторной обработки. Этот процесс сварки позволяет флюсу с гравитационной подачей полностью покрывать точку дуги, создаваемую аппаратом для сварки MIG с высоким током. Как и в любом сварочном процессе, флюс создает газ, который защищает сварочную дугу от примесей в воздухе, которым мы дышим.
Сварочный аппарат устроен аналогично шлифовальному станку коленчатого вала.Если шейка стержня, которая вращается за пределами осевой линии коленчатого вала, требует сварки, сварщик запрограммирован на движение с ходом штока, чтобы поддерживать точное расстояние между наконечником сварочного аппарата и движением шейки.
Ярким примером экономичного ремонта кривошипа является этот узел, в котором были повреждены коренные и шатунные шейки подшипников. Материал подшипника, который вы видите встроенным в кривошип, будет удален перед сваркой, так как он загрязнит процесс сварки.Металлический жидкий раствор пропитывает коленчатый вал, пока проверяемые участки освещаются черным ультрафиолетовым светом.Электрическое поле нарушается вокруг любых трещин, в котором концентрируются мелкие частицы металла, в результате чего становятся видимыми трещины, невидимые невооруженным глазом (стрелка).
«Мы уделяем пристальное внимание прямолинейности кривошипа на протяжении всего процесса ремонта», — описывает Дарнер. «С самого начала и на всех этапах сварки и переточки мы следим за тем, чтобы кривошип оставался прямолинейным. Мы также уделяем очень пристальное внимание ремонту радиуса с каждой стороны журнала в соответствии со спецификациями.Именно в этой части процесса ремонта окупается опыт. Плавность сварного шва может измениться между торцом шейки и закругленными концами. Знание различных марок и материала каждой рукоятки окупается ».
Процесс правки не совсем высокотехнологичный, но продуманный процесс правки — это больше искусство, чем наука.Станция гидравлического кривошипного пресса стратегически расположена между станциями сварки и шлифования на заводе по производству коленчатого вала в Огайо. Эта станция заполнена приспособлениями и множеством циферблатных индикаторов, которые контролируют множество точек по длине рукоятки. Гидравлическое давление применяется для «сгибания» кривошипа до надлежащих допусков.
«Здесь окупается опыт», — улыбается Дарнер. «Мы знаем, сколько обратного изгиба требуется для каждого кривошипа, и ожидаем, что он вернет надлежащий допуск.Это похоже на выпечку печенья; вы просто получите опыт работы с кривошипом 5140, 4340 или заготовкой, чтобы вернуть его в исходное положение одним выстрелом, не заходя слишком далеко.
Станция правки используется много раз в процессе ремонта, чтобы убедиться, что сварка и механическая обработка не приводят к изменению коленчатого вала. Опыт персонала позволяет поддерживать все размеры без излишней коррекции во время операции гидравлической правки.Испытание магнитными частицами, широко известное как «магнитное плавление», происходит, когда кольцо электрического тока создает магнитное поле вокруг коленчатого вала или любого другого металлического компонента двигателя, требующего проверки на наличие трещин.
«Наш опыт учитывает любой нагрев коленчатого вала, необходимый до и / или после процесса ремонта», — отмечает Дарнер. «В зависимости от материала коленчатого вала и того, какую термообработку он получил в качестве нового продукта, мы отслеживаем время до или после печи, чтобы сохранить прочность, которую он имел от производителя».
Особое внимание уделяется отправной точке между шлифовальной машиной и свариваемой поверхностью, чтобы не быть слишком агрессивным или чрезмерно нагреть зону сварки, но сварка кривошипом и ремонт становятся более жизнеспособным вариантом, когда дело доходит до ремонта поврежденного двигателя. чтобы вернуться на полосу, не нарушая банк.
Размеры шейки сдвоенного коленчатого вала Triumph — двигатель Franz and Grubb
Размеры шейки сдвоенного коленчатого вала Triumph
Коленчатый вал — краеугольный камень любого хорошего двигателя. Размер и округлость шейки влияют на давление и расход масла.
Следует проявлять особую осторожность при прикручивании шатунов к кривошипу. Ниже приведены размеры различных сдвоенных шеек и допустимые пределы износа.
ПРЕДВАРИТЕЛЬНАЯ УСТАНОВКА 500 И 650
Большинство кривошипов предварительного агрегата состояли из трех частей, скрепляемых шестью болтами 1/4 дюйма.Подшипники шатуна изготовлены из баббита и не подлежат замене. Хотя некоторые магазины все еще могут переоборудовать баббитовые стержни, ни один из известных нам не будет делать такие маленькие отверстия.
Одним из решений этих кривошипов с «малой шейкой» является установка нового набора шатунов от Thunder Engineering или LF Harris, оба из которых используют вкладыши от двигателя Unit 500. Коленчатый вал необходимо отшлифовать для установки более поздних подшипников. Хотя люди могут предположить, что эти коленчатые валы не являются прочными, в этой конструкции нет ничего плохого, а стоимость производства, скорее всего, позволила отказаться от нее.
1946-1954 Предварительный блок 500 куб. См и 650 куб. См (со стержнями из баббита)
СТАНДАРТ 1.4365–1.4360 дюймов
-010 «1. 4265″ до 1.4260 «
-020 дюймов от 1,4165 до 1,4160 дюймов
СТРОИТЕЛЬСТВО БЛОКА 500
Triumph представил агрегат конструкции 500 в 1959 году. Он имел плоскую втулку для стороны привода ГРМ вместо шарикового подшипника. Поскольку подача масла осуществляется через втулку, необходимо проверить и при необходимости откорректировать зазор и посадку шейки привода ГРМ.
Чтобы упростить задачу, компания Triumph использовала опорную шейку подшипника того же размера, что и шейка штока. Боковые втулки привода ГРМ можно купить с шагом 0,010 дюйма как с металлической основой, так и с твердой бронзой.
В 1968 году компания Triumph представила шариковый подшипник для замены втулки привода ГРМ. Размеры шейки стержня не изменились и составляют:
1959-1974 Агрегат 500cc (со вставными подшипниками)
СТАНДАРТ 1.4380 дюймов до 1.4375 «
-010 «1.4280» до 1.4275 «
-020 дюймов от 1,4180 дюйма до 1,4175 дюйма
-030 «1. 4080″ до 1.4075 «
-040 дюймов от 1,3980 до 1,3975 дюймов
КОНСТРУКЦИЯ БЛОКА 650 И 750
С 1955 по 1972 год компания Triumph сохраняла тот же размер шейки коленчатого вала. Шатуны Pre Unit 650 середины 1950-х годов все еще состояли из трех частей, но имели новый больший размер шейки. Когда были введены двухсекционные кривошипы, остались те же шатуны E6304 с тем же диаметром шейки.
Triumph изменил конструкцию шатуна 650 в 1960-х годах и использовал более короткий стержень для 750, но все двухсекционные коленчатые валы 650 и 750 используют одинаковые подшипники скольжения.
1955-1978 Агрегаты 650 куб. См и 750 куб. См (со вставными подшипниками)
СТАНДАРТ от 1,6240 дюйма до 1,6235 дюйма
-010 дюймов от 1,6140 до 1,6135 дюймов
-020 «1.6040» до 1.6035 «
-030 «1,5940» до 1.5935 «
-040 дюймов от 1,5840 дюймов до 1,5835 дюймов
ЗАПРОС ЗАПРОС
При создании двигателя нужно многое проверить. Один большой недостаток, если вы используете гоночные кулачки или смешивающие детали, — это зазор между кулачком и маховиком. Это необходимо проверить перед сборкой двигателя, так как при сборке исправить это невозможно. Хороший запас прочности для использования — это от распределительного вала до маховика 0,080 дюйма для гонок.
Для печати размеров шейки коленчатого вала в формате PDF нажмите здесь
Что, как и почему — Infinite-Garage
Коленчатый вал — это основа любого двигателя.Что и почему легко понять. Проще говоря, это то, что превращает возвратно-поступательное движение поршня вниз во вращательную силу.
Основная плоскость — это место крепления коленвала к блоку двигателя. Шатунные шейки — это места, где концы шатунов крепятся болтами к кривошипу. Противовесы находятся на противоположных сторонах шейки штока и противодействуют гармоническим силам поршня и штока в сборе. Не заметно на фото масляные каналы. Единственное, что заставляет кривошип свободно вращаться, на чем он движется, — это клин давления масла.Теперь вы знаете, почему нужно проверять масло еженедельно. (Обратите внимание: слишком много значит слишком мало). Как бы то ни было, есть проходы, просверленные насквозь, от главных цапф к шейкам стержней, которые направляют масло под давлением к стержням в соответствующее время (при ходе вниз) и удерживают шейки стержней на клине с маслом. На каждом конце есть фланец для крепления маховика, а на противоположном конце вала, где крепится шкив / гармонический балансир.
Основы окончены. Теперь мы переходим к хорошему. Начну с базовой динамики двигателя.Каждый ICE имеет определенное время срабатывания. Рядная четверка срабатывает при повороте кривошипа на 180 градусов. Шесть, каждые 120. Восемь, каждые 90. Чем ближе время зажигания, тем плавнее будет мощность двигателя. Это объясняет, почему V8 кажется намного более плавным, чем «шумная четверка». Для ротора он запускает каждое вращение ротора. Таким образом, два ротора срабатывают каждые 180 градусов.
Типичный дорожный двигатель имеет так называемый коленчатый вал с поперечной плоскостью. Если вы посмотрите на него вдоль, как на ружье, цапфы стержней не будут в одной плоскости.У четырехцилиндрового двигателя нет другого выбора, кроме как быть тем, что называется плоским кривошипом. Присущее ему время обжига на 180 градусов не позволяет ничего другого. Для нечетверок правилом является поперечная плоскость. Для двигателя с V-образной конфигурацией это становится немного сложнее. Жезлы находятся рядом в общем журнале. V-8 имеет врожденный баланс в конфигурации на 90 градусов. Он идеально настроен для равномерного импульса стрельбы. Для 90-градусного V-6 это становится трудным. Он либо будет использовать общий журнал и будет заметно грубее, либо использовать разделенный журнал для достижения времени в 120 градусов.
Шатуны Buick V-6. Обратите внимание на цапфы разъемных стержней.
Отличие двигателей V-типа от плоского кривошипа. Используемый в основном для повышения производительности, он имеет заметно более грубую выходную мощность, но не используется во многих дорожных двигателях. И те, в которых он используется, сильно зависят от производительности. На ум приходят Lotus Esprit V8 и нынешнее поколение Ferarri V-8. Плоский самолет легче сбалансировать и более долговечен при высоких оборотах.
Способ создания кривошипа так же важен, как и дизайн.Есть три основных метода создания. Отлит первый. Достаточно просто: вы берете горячий металл и заливаете его в отливку. После охлаждения стержень и коренные шейки, а также другие точки крепления обрабатываются с требуемыми допусками. Литые кривошипы используются в 99% двигателей. Они относительно прочные и долговечные. И очень дешево и просто в изготовлении. Но в целом они самые слабые из группы.
Далее идет кованый шатун. Он начинает свою жизнь как литой кривошип из специального сплава.После формирования его подвергают термообработке, а цапфы устанавливают на место. После охлаждения обрабатываются поверхности. Его стоимость подкачивает процесс термообработки, а также специальный сплав.
Окончательная версия — кривошипная заготовка. Он вырезан из цельного блока из специально легированной стали. Благодаря своей конструкции из одного материала и механической обработке, он намного ближе к идеальному балансу, чем другие. Стоимость его намного выше. Из-за затрат на покупку большого патрона из специального сплава, а также большого времени на обработку для удаления всего лишнего металла.Это самый дорогой метод, но некоторые сомневаются, что он все еще лучший.
Используемые металлы обычно сопоставимы. Но дело в том, что металл имеет внутреннюю кристаллическую структуру. Срезание лишнего металла приводит к удалению некоторых внутренних структур, в то время как кованый шатун сохраняет все их. Это дискуссия. Явного победителя нет, но я нахожусь в лагере кузнецов.
Для кривошипа доступно несколько модификаций производительности. Первый — это баланс. Это уменьшает гармоники при работе на высоких оборотах.Это также позволяет, с более легкими поршнем и штоком, более легким вращающимся узлом, что делает двигатель более отзывчивым. Следующая модификация — это следующий шаг в балансировке. Это известно как лезвие ножа противовесов. Передняя сторона противовеса обработана до конуса, чтобы уменьшить сопротивление ветру, а также масляный туман и масляный туман в картере. Это небольшое снижение сопротивления, небольшое увеличение, которое, когда вы создаете двигатель, построенный по правилам конкуренции, может стать решающим фактором для победы.Последняя модификация — кривошипный ходовой. В большинстве случаев это рукоятка с более длинным ходом. В сочетании с более коротким поршнем и более длинным штоком создается большее смещение в отверстии цилиндра. Больший объем двигателя означает большую мощность. Но есть некоторые двигатели, у которых не работает кривошип. Это попытка создать двигатель с более высокими оборотами. Большинство дестрокеров используются в определенных классах дрэг-рейсинга.
Времена индекса являются функцией объема двигателя, поэтому меньшее время лучше.
Итак, это в двух словах. Если у вас есть отзывы или вопросы по другому сегменту, оставьте их в разделе комментариев. Мы до них доберемся.
Смазочные характеристики шатуна и главного подшипника в различных условиях эксплуатации двигателя | Китайский журнал машиностроения
Метод и формула
Орбиты осей шейки шейки всех подшипников рассчитываются динамическим методом при анализе смазки всех шатунных или коренных подшипников [32].{3} \ frac {\ partial p} {\ partial y}} \ right) = 6 \ eta R_ \ text {b} \ left ({u \ frac {\ partial h} {\ partial \ theta} + 2R_ \ текст {b} \ frac {\ partial h} {\ partial t}} \ right), $$
(1)
где p — давление масляной пленки, h — толщина масляной пленки, η — динамическая вязкость смазочного масла, u = u j + u b , u j — скорость поверхности шейки, а u j = R j ω j , R j — радиус шейки, ω j — угловая скорость журнала, у б есть скорость несущей поверхности и у б = R б ω б , R б радиус подшипника, ω b — угловая скорость подшипника.
Уравнение Рейнольдса решается методом конечных разностей.
Толщина масляной пленки [34]
$$ h = c + e \ cos (\ theta — \ psi) + \ delta, $$
(2)
, где c — радиальный зазор подшипника, e — эксцентрическое расстояние подшипника цапфы, ψ — угол наклона подшипника, δ — изменение толщины масляной пленки, вызванное упругой деформацией втулки поверхность подшипника под давлением масляной пленки, а упругая деформация поверхности втулки подшипника под давлением масляной пленки рассчитывается методом матрицы податливости.
Уравнение равновесия нагрузок
Если влияние инерции масляной пленки не учитывается, движение осей шейки подшипника соответствует второму закону Ньютона, то есть
$$ \ varvec {P} + \ varvec { F} = m _ {\ text {j}} \ frac {{{\ text {d}} \ varvec {v}}} {{{\ text {d}} t}}, $$
(3)
, где P — вектор нагрузки подшипника, F — результирующий вектор силы масляной пленки подшипника, v — вектор скорости осей шейки. {2 \ pi} {\ left ({\ frac {h} {2} \ frac {\ partial p} {{R_ \ text {j} \ partial \ theta}} + \ frac {u \ eta} {h}} \ right) R_ \ text {j} \ text {d} \ theta \ text {d} y}}.{720} {(F_ \ text {j}) _ {i} u} /720.$$
(6)
Результаты и обсуждение
Орбиты осей шейки, максимальное давление масляной пленки, минимальная толщина масляной пленки, расход утечки на конце и коэффициенты трения шатунного подшипника и коренного подшипника № 2 в рабочем цикле двигателя при полной нагрузке двигателя при 1200 об / мин и 3200 об / мин показаны на рисунках 5, 6, 7, 8, 9, 10, 11, 12, 13, 14. В различных условиях работы двигателя есть большие различия в смазочных характеристиках подшипников, и есть очевидные различия в изменениях и числовых значениях орбит осей шейки, максимальном давлении масляной пленки, минимальной толщине масляной пленки, расходах утечки на конце и коэффициентах трения подшипников в рабочем цикле двигателя.
Рисунок 5Орбита шейки шатуна
Рисунок 6Орбита шейки оси коренного подшипника № 2
Рисунок 7Максимальное давление масляной пленки шатунного подшипника
Рисунок 8Максимальное давление масляной пленки коренного подшипника № 2
Рисунок 9Минимальная толщина масляной пленки шатунного подшипника
Рисунок 10Минимальная толщина масляной пленки коренного подшипника № 2
Рисунок 11Расход утечки на конце шатунного подшипника
Рисунок 12Расход конечной утечки №2 коренных подшипника
Рисунок 13Коэффициент трения шатунного подшипника
Рисунок 14Коэффициент трения коренного подшипника № 2
Максимальное давление масляной пленки, минимальная толщина масляной пленки и средние потери мощности на трение шатунного подшипника и всех коренных подшипников в рабочем цикле двигателя при полной нагрузке двигателя и при 1200, 1600, 1800, 2000, 2200, 2400, 2800 и 3200 об / мин соответственно показаны в таблицах 4, 5, 6.
При одинаковой нагрузке на двигатель максимальное давление масляной пленки шатунного подшипника в рабочем цикле двигателя обычно снижается с увеличением частоты вращения двигателя, а максимальное давление масляной пленки (372.52 МПа) шатунного подшипника при 1200 об / мин в 4,02 раза больше, чем (92,74 МПа) при 3200 об / мин, что показывает, что максимальное давление масляной пленки шатунного подшипника при более низких оборотах двигателя заметно больше, чем на более высоких оборотах двигателя при той же нагрузке двигателя. Основная причина, по которой максимальное давление масляной пленки в шатунном подшипнике при более низких оборотах двигателя больше, чем при более высоких оборотах двигателя при той же нагрузке двигателя, заключается в том, что при одинаковой нагрузке на двигатель максимальная нагрузка на шатун составляет уменьшается в основном с увеличением оборотов двигателя, а максимальная нагрузка на шатун при 1200 об / мин заметно больше, чем при 3200 об / мин.
При одинаковой нагрузке на двигатель изменения максимального давления масляной пленки всех коренных подшипников в рабочем цикле двигателя отличаются друг от друга при изменении частоты вращения двигателя. Максимальное давление масляной пленки коренных подшипников № 1 и № 5 не претерпевает явных изменений при разных оборотах двигателя, максимальное давление масляной пленки коренных подшипников № 2 и № 4 больше при более низких оборотах двигателя, а максимальное давление. Давление масляной пленки коренных подшипников № 3 больше при более высоких оборотах двигателя.
При одинаковой нагрузке на двигатель минимальная толщина масляной пленки шатунного подшипника и всех коренных подшипников в рабочем цикле двигателя не меняются одинаково при изменении частоты вращения двигателя. Минимальная толщина масляной пленки шатунного подшипника и всех основных подшипников в рабочем цикле двигателя при более высоких оборотах двигателя (3200 об / мин), как правило, меньше в дополнение к индивидуальным обстоятельствам.
При одинаковой нагрузке на двигатель средние потери мощности на трение шатунного подшипника и всех коренных подшипников увеличиваются с увеличением частоты вращения двигателя, а средние потери мощности на трение в шатунном подшипнике и всех коренных подшипниках являются наибольшими при более высокая частота вращения двигателя (3200 об / мин).
Максимальное давление масляной пленки, минимальная толщина масляной пленки и средние потери мощности на трение шатунного подшипника и всех коренных подшипников в рабочем цикле двигателя при 2200 об / мин при 20%, 40%, 60%, 80% и полном Нагрузки на двигатель приведены в таблицах 7, 8, 9.
При одинаковых оборотах двигателя максимальное давление масляной пленки шатунного подшипника и всех основных подшипников в рабочем цикле двигателя обычно увеличивается с увеличением нагрузки на двигатель, но максимальное значение максимального давления масляной пленки, равное No.3 коренной подшипник появляется при меньшей нагрузке двигателя (40%).
При одинаковых оборотах двигателя минимальная толщина масляной пленки шатунного подшипника уменьшается с увеличением нагрузки двигателя, а максимальное значение появляется при полной нагрузке двигателя (100%). Минимальная толщина масляной пленки всех коренных подшипников не изменяется одинаково при изменении нагрузки на двигатель, минимальные значения минимальной толщины масляной пленки коренных подшипников №№ 1, 4, 5 появляются при полной нагрузке двигателя (100 %), а также минимальные значения минимальной толщины масляной пленки №№.2, 3 коренных подшипника появляются при меньшей нагрузке на двигатель.
Когда частота вращения двигателя одинакова, средние потери мощности на трение шатунного подшипника и всех основных подшипников в рабочем цикле двигателя, очевидно, не изменяются с изменением нагрузки двигателя. Средние потери мощности на трение шатунного подшипника и всех коренных подшипников в рабочем цикле двигателя обычно немного увеличиваются с увеличением нагрузки двигателя в дополнение к отдельным нагрузкам двигателя.
Кроме того, соответствующие сравнения между смазочными характеристиками шатунного подшипника и одним из основных подшипников при одном и том же рабочем состоянии двигателя (показаны в таблицах 4, 5, 6, 7, 8, 9) показывают, что максимальное количество масла давление пленки шатунного подшипника в рабочем цикле двигателя больше, чем у всех коренных подшипников, минимальная толщина масляной пленки шатунного подшипника в рабочем цикле двигателя меньше, чем у всех коренных подшипников, а средняя сила трения потери шатунного подшипника в рабочем цикле двигателя меньше, чем у всех коренных подшипников. Кроме того, существует соответствующая разница между характеристиками смазки (максимальное давление масляной пленки, минимальная толщина масляной пленки и средняя потеря мощности на трение в рабочем цикле двигателя) всех основных подшипников друг друга при одинаковых условиях работы двигателя, а некоторая разница больше .
Влияние и анализ углового качения шейки коленчатого вала на биение
[1] Housheng Li.Технология изготовления двигателей внутреннего сгорания [J]. Журнал китайского сельскохозяйственного механического пресса, (1981).
[2]
Гуанхуа Лю. Оценка перспектив применения коленчатого вала из чугуна с шаровидным графитом [J]. Современный чугун, 2005 (1): с.1-7.
[3] Цзин Ван, Цюньхуэй Чжан.Анализ причин поломки коленчатого вала [J]. Журнал угольной техники, 2002 (6): с.41 ~ 42.
[4]
Шисун Сюй. Расчет на прочность коленчатого вала [J]. Журнал двигателя внутреннего сгорания, 1990 (8): с.169 ~ 174.
[5] Даксин Чжу. Процесс прокатки коленчатого вала двигателя [J]. Журнал технологий и материалов, 2001 (6): с.32 по 39.
[6]
Чаохуэй Чжан. ANSYS12. 0 примеры инженерных приложений для анализа структуры объясняют третье издание [M]. Пресса для машиностроительной промышленности, (2010).
[7] Чулин Ли и др. Анализ приложений HyperWorks [M]. Пресса для машиностроительной промышленности, (2008).
[8] Ронгчанг Лю и др. Теория расчета ключевых параметров качения коленчатого вала и численное моделирование [J]. Национальная оборонная пресса, 2010 (2).
Сварка шейки коленчатого вала
Сварка шейки коленчатого вала
Мы специализируемся на качественном восстановлении поврежденных коленчатых валов. Любой размер от 6 дюймов до 40 футов для дизельных, газовых двигателей или компрессоров большего размера и большей мощности. У нас есть современный хромовый цех и самый большой шлифовальный станок в Соединенных Штатах и Канаде, включая множество других станков, способных шлифовать более 30 футов.
Coastal Plating была основана в 1948 году. У нас работают квалифицированные мастера, которые эффективно выполняют свою работу. Более 300 лет ноу-хау в области промышленного хромирования используются в наших процедурах утилизации и восстановления. Специализируясь только на восстановлении изношенных, погнутых, заржавевших или поврежденных коленчатых и распределительных валов, мы можем предложить вам САМЫЕ БЫСТРЫЕ ДОСТУПНЫЕ УСЛУГИ. Вы можете повторно собрать двигатель и вернуть его в эксплуатацию. Ваше время простоя минимально. Наш контроль качества и профессиональное мастерство гарантируют вам БЫСТРЫЙ ОБРАТНЫЙ ОТВЕТ с бескомпромиссным качеством.Мы не хотим извиняться за брелок и не хотим делать это заново. Так что мы делаем это правильно с первого раза. Одновременно мы следим за расходами. Наши цены, пожалуй, самые низкие в бизнесе. В наши дни и это важно. Низкая стоимость плюс вся необходимая надежность и производительность — уникальная комбинация для Coastal Plating. Мы снова отправим вас в путь!
Сварка
Если цапфы выгорели и обнажили трещины, их необходимо отремонтировать дуговой сваркой под флюсом.Каждый радиус, точка напряжения, упорная поверхность и цапфа тщательно проверяются. Каждая трещина шлифуется и сваривается. Мы не завариваем трещины, даже самые маленькие.
КОЛЕНЧАТЫЕ ВАЛЫ БОЛЬШИЕ. ИЗ-ЗА ОСОБЫХ ПОТРЕБНОСТЕЙ И НАПРЯЖЕНИЯ БОЛЬШИХ ВАЛОВ ДЛИНОЙ ДО 40 ФУТОВ В ОБЛАСТИ ПРИБРЕЖЕНИЯ РАЗРАБОТАНЫ ВРАЩАЮЩИЕСЯ ОПОРЫ, ОБЕСПЕЧИВАЮЩИЕ ВОССТАНОВЛЕНИЕ КОЛЕНЧАТОГО ВАЛА НА ПЕРВОНАЧАЛЬНУЮ ВЕРСИЮ, КОТОРЫЕ НЕ ИМЕЮТ РАЗМЕР, ВЕС ИЛИ КОНФИГУРАЦИЯ. СТАНДАРТЫ.
Ремонт коленчатого вала
В области промышленного производства твердого хромирования мы в компании Coastal Plating Company знаем, что для вас важно иметь высокотехнологичное оборудование.