Основные детали двигателей внутреннего сгорания
Фундаментная рама является основанием двигателя и состоит из двух продольных балок коробчатого или двутаврового сечения, на которые устанавливаются стойки и станины, и нескольких поперечных балок необходимой формы для установки рамовых подшипников. Фундаментные рамы могут быть сварными или литыми (стальными, чугунными). Они бывают закрытые и открытые, цельные и составные. Нижняя часть закрытой фундаментной рамы, т. е. поддон, выполнена за одно целое с продольными балками. Между поперечными балками вращаются кривошипы (мотыли) коленчатого вала, поэтому пространства между ними и продольными балками называют мотылевыми колодцами. Поперечные балки в нижней части имеют отверстия для перетекания масла из одного мотылевого колодца в другой. В быстроходных и легких двигателях применяют так называемые картерные рамы, позволяющие устанавливать блок цилиндров непосредственно на раме, в результате чего отпадает необходимость в станине.
Рис. 55. Общий вид фундаментной рамы двигателя.
Станина двигателя устанавливается на фундаментную раму и соединяется с ней болтами. Станины бывают цельными и составными и могут иметь различную конструкцию. Некоторые двигатели большой мощности имеют станины открытого типа в виде соединенных между собой вверху и внизу колонн. Сверху на колонны устанавливают цилиндры двигателя.
На рис. 56 показана литая станина 3 мощного двигателя, которая так называемыми анкерными связями — длинными стяжными шпильками 1 — соединяется с рубашками цилиндров 2 и фундаментной рамой 4 в одно целое.
Рис. 56. Литая станина мощного двигателя. Рабочие цилиндры изготовляют каждый в отдельности или в виде блочной конструкции.
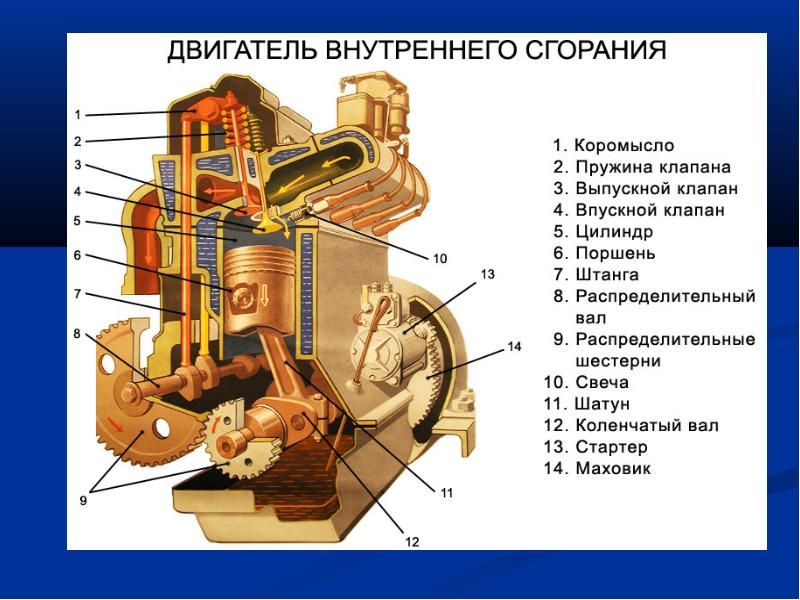
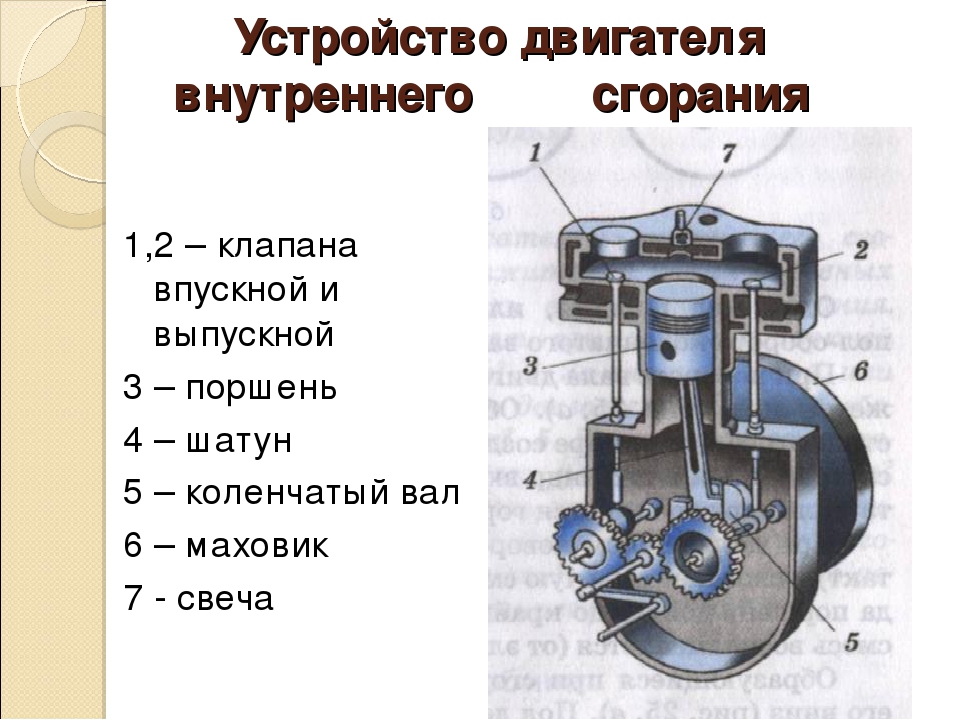
Рис. 57. Цилиндр четырехтактного двигателя.
Рабочие цилиндры двухтактных двигателей отличаются от рабочих цилиндров четырехтактных тем, что имеют окна для подвода продувочного воздуха и удаления отработавших газов. Это приводит к необходимости обеспечивать уплотнение между втулкой и рубашкой не только в нижней ее части, но и в районе окон. В канавки, прилегающие к окнам, закладывают медные кольца, а в остальные канавки— резиновые кольца.
Крышка цилиндра — наиболее ответственная и сложная по конфигурации деталь двигателя. Она должна выдерживать высокое давление и температуру. Если две или более крышек выполнены за одно целое, то такая деталь называется головкой блока. Самой сложной по конфигурации является крышка четырехтактного двигателя, где кроме отверстий для форсунки и клапанов имеются канал для подвода воздуха к пусковому клапану и каналы для газообмена между цилиндром и атмоферой.
Простейшая конструкция крышки цилиндра двухтактного двигателя показана на рис. 58. Крышка имеет центральное отверстие в котором устанавливают объединенные в одном корпусе форсунку и пусковой клапан. В кольцевом пространстве 2 циркулирует охлаждающая вода. Крышка крепится к цилиндру при помощи шпилек 3. Для увеличения жесткости во внутренних полостях крышки имеются ребра 4. Уплотнение крышки осуществляется при помощи буртика 5, входящего в кольцевую выточку фланца цилиндра. В выточку для уплотнения устанавливают медное отожженное кольцо.
Рис. 58. Простейшая конструкция крышки цилиндра двухтактного двигателя.
Основные подвижные детали двигателя входят в состав кривошипно-шатунного механизма, назначение которого — преобразование возвратно-поступательного движения поршня во вращательное движение коленчатого вала. Кривошипно-шатунный механизм тронковых двигателей состоит из поршня, поршневого пальца, поршневых колец, шатуна и коленчатого вала. В крейцкопфных двигателях в состав кривошипно-шатунного механизма входят, кроме того, поршневой шток и поперечина (крейцкопф) с ползунами. Крейцкопфом называется узел, соединяющий нижнюю часть штока с верхней головкой шатуна.
Поршень тронкового двигателя, выполняющий дополнительно функции ползуна, имеет сравнительно длинную направляющую часть, называемую «юбкой» или тронком. Поршень тронкового двигателя соединен с шатуном шарнирно — при помощи поршневого пальца. На рис. 59 показано устройство тронкового поршня, у которого головка 3 и тронк 1 отлиты за одно целое. Применяется наиболее часто такой способ установки поршневого пальца 5 в бобышках направляющей части поршня, когда он может свободно проворачиваться вокруг своей оси, но лишен возможности передвигаться вдоль оси. Такой палец называется плавающим. В верхних канавках 4 поршня установлены уплотнительные поршневые кольца 2, а в нижней части — маслосъемные кольца 6.
Рис. 59. Поршень тронкового двигателя.
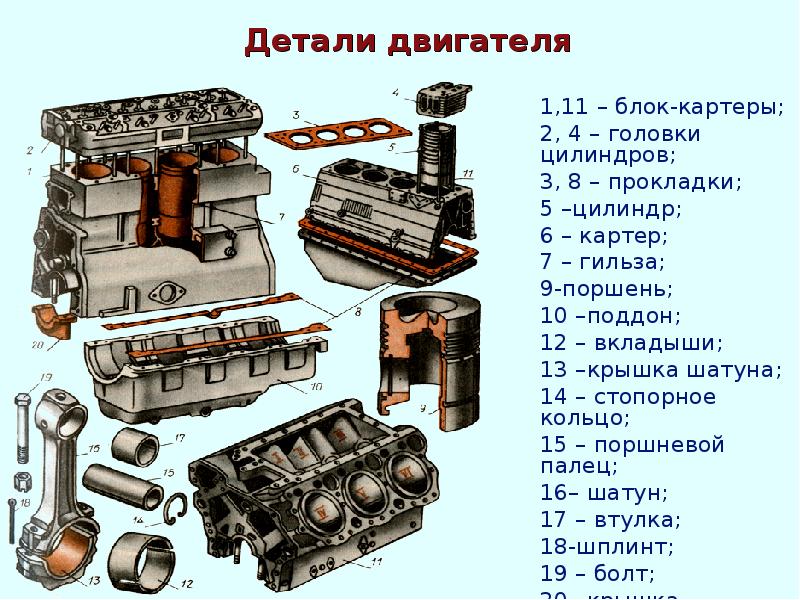
На рис. 60 показана конструкция поршня крейцкопфного двигателя. Вогнутое днище 1 поршня подкреплено ребрами 2. В верхних канавках поршня установлены уплотнительные кольца 3, а в нижней части — маслосъемные кольца 4. Поршень соединен со штоком 6 при помощи шпилек 5 фланцем 7. Диск 8 закрывает внутреннюю полость поршня, охлаждаемую водой.
Рис. 60. Поршень крейцкопфного двигателя.
Поршневые кольца обеспечивают не только уплотнение цилиндра от прорыва газов и воздуха, но и передачу теплоты от головки поршня к стенкам втулки цилиндра. Кольца выполняют самопружинящими. Для надевания на поршень они снабжены косым или ступенчатым разрезом, который называют замком. Разрезные кольца хорошо пружинят и при движении поршня плотно прижимаются к стенкам цилиндра. В четырехтактных двигателях поршневые кольца в канавках обычно не фиксируют. В двухтактных двигателях кольца приходится фиксировать, если имеется опасность попадания их замков в зону продувочных или выпускных окон.
Маслосъемные кольца имеют обычно скос на наружной поверхности. Благодаря этому при ходе поршня вниз маслосъемные кольца удаляют с поверхности цилиндра излишки смазочного масла, а при ходе вверх свободно проскальзывают по масляному слою.
Поршневой шток крейцкопфного двигателя соединен с поперечиной крейцкопфа фланцем или конусным соединением. Для уменьшения массы шток часто выполняют полым.
Крейцкопф состоит из поперечины и присоединенных к ней башмаков (ползунов). Поперечина имеет две цапфы для соединения с вилкой шатуна. Рабочую поверхность башмаков заливают баббитом. Крейцкопфы реверсивных двигателей имеют башмаки с обеих сторон. Для соединения с поршневым штоком поперечина имеет конусное отверстие, соответствующее конусу поршневого штока, или пятку для соединения с фланцем штока.
Шатун двигателя передает усилие от поршня коленчатому валу двигателя. На рис. 61 показан шатун тронкового двигателя.

Рис. 61. Шатун тронкового двигателя.
Шатуны крейцкопфного двигателя отличаются от шатунов тронкового тем, что имеют два головных подшипника, соединяющихся с цапфами поперечины крейцкопфа, если шатун имеет вильчатую форму.
Коленчатый вал — одна из самых ответственных и дорогостоящих деталей двигателя. Валы изготовляют из высококачественной стали, а также отливают из модифицированного и легированного чугуна. В зависимости от конструкции и числа цилиндров коленчатый вал может иметь разное число колен (кривошипов). Кривошипы вала развертывают по отношению друг к другу на определенный угол, который зависит от числа цилиндров и от тактности двигателя. Коленчатые валы чаще всего бывают цельноковаными и реже сборными, состоящими из двух-трех отдельных частей, соединенных между собой фланцами.
Основными элементами коленчатого вала (рис. 62, а) являются рамовые или коренные шейки 1, мотылевые или шатунные шейки 2 и щеки 3, соединяющие шейки между собой. Иногда для уравновешивания сил инерции вращающихся масс к щекам 1 крепят противовесы 2 (рис. 62, б). Мотылевые шейки коленчатого вала охвачены подшипником нижней головки шатуна, а рамовые шейки опираются на рамовые подшипники, установленные в фундаментной раме двигателя. Смазка шеек осуществляется так: к рамовым шейкам масло подается под давлением через отверстие в крышке подшипника и верхнем вкладыше, а затем через сверление в щеке (рис. 62, в) направляется к мотылевой шейке.
Рис. 62. Коленчатый вал двигателя.
В коленчатых валах с полыми шейками масло поступает на рабочие поверхности мотылевых шеек через полости рамовых шеек и радиальные отверстия, выполненные в мотылевых шейках. Для предотвращения утечки масла из полостей шеек последние с торцов закрыты заглушками, стянутыми болтами или шпильками.
Детали ДВС: основы основ
Страницы: 1 2
Все двигатели от прошлых до современных моделей включают в себя: кривошипно-шатунный механизм; механизм газораспределения; систему охлаждения; смазочную систему; систему питания; систему зажигания (у карбюраторных двигателей).
Детали, составляющие двигатель, можно разделить на две группы: подвижные и неподвижные. К неподвижным деталям относятся блок цилиндров, цилиндры, головка блока цилиндров, поддон картера.
Цилиндры двигателя выполнены или установлены в массивном жестком корпусе, называемом блоком цилиндров двигателя. Блок изготавливается из чугуна или алюминиевого сплава. Между цилиндрами в нем выполнены каналы для охлаждающей жидкости, служащей для отвода теплоты от сильно нагревающихся деталей. Сверху на блоке закреплена головка блока цилиндров. Снизу к блоку цилиндров прикреплен поддон картера, служащий емкостью для масла, необходимого для смазывания деталей двигателя во время его работы.
Кривошипно-шатунный механизм. Преобразует прямолинейное (возвратно-поступательное) движение поршня во вращательное движение коленчатого вала. Включает в себя следующие детали, имеющие определенное назначение.
Поршень (рис. 7) изготовлен из алюминиевого сплава и имеет сложную форму. Он состоит из днища, уплотняющей и направляющей частей. На уплотняющей части поршня выполнены кольцевые канавки под поршневые кольца — компрессионные и маслосъемные.
Компрессионные кольца 2 препятствуют проникновению газов из камеры сгорания в зазор между цилиндром и поршнем. Маслосъемные кольца 1 снимают излишки масла со стенок цилиндра. Кольца разрезные, при установке поршня в цилиндр они пружинят и плотно прижимаются к его стенке.
Поршневой палец 3 соединяет поршень с шатуном. Поршневой палец может быть запрессован в теле поршня, при этом он свободно вращается в верхней головке шатуна. Другая конструкция предполагает свободное вращение пальца в бобышках (утолщениях) поршня и запрессовку его в верхнюю головку шатуна. От осевого перемещения в поршне палец удерживается стопорными кольцами 4, установленными в проточках бобышек поршня.
Шатун штампуется из стали. Он состоит из стержня, верхней и нижней головок. В верхнюю головку шатуна запрессована втулка 8, в которой вращается (или запрессован) поршневой палец. Нижняя головка выполнена разъемной и имеет проточки для установки шатунных вкладышей. Части нижней головки соединены между собой специальными шатунными болтами 6.
Коленчатый вал изготавливают из стали или чугуна. Коленчатый вал четырехцилиндрового двигателя состоит из пяти опорных (коренных) шеек, расположенных по одной оси, и четырех шатунных шеек, попарно направленных в противоположные стороны. Коренные шейки вращаются в подшипниках (в виде двух половин вкладышей). Для разгрузки коренных подшипников от действия центробежных сил служат противовесы 10.
На переднем конце вала устанавливается звездочка, шкив или шестерня привода распределительного вала. В торец переднего конца вала ввертывают храповик или болт для проворачивания коленчатого вала вручную при техническом обслуживании. В торце заднего конца вала помещен подшипник первичного вала коробки передач. В задней же части коленчатого вала имеется фланец, к которому прикреплен маховик. На его обод напрессован стальной зубчатый венец, с которым соединяется шестерня стартера при пуске двигателя.
Страницы: 1 2
Порекомендуйте статью друзьям: |
Подвижные детали двигателя
Категория:
Дизельные двигатели
Публикация:
Подвижные детали двигателя
Читать далее:
Подвижные детали двигателя
Кривошипно-шатунный механизм воспринимает давление газов и преобразует прямолинейное возвратно-поступательное движение поршня во вращательное движение коленчатого вала.
В зависимости от типа и размера двигателя детали кривошипно-шатунного механизма отличаются большим разнообразием конструкций. Однако все они рассчитаны на такие условия работы, которые связаны с необходимостью воспринимать и передавать большие нагрузки, вызывающие высокие напряжения в металле, в результате чего они подвержены более значительному износу, чем неподвижные детали.
Для изготовления деталей тихоходных и средней быстроходности дизелей в основном используется углеродистая качественная сталь (ГОСТ 1050—60). Поршневые пальцы, кулачные шайбы и валики изготовляются из стали с малым содержанием углерода (до 0,2%) с цементацией и закалкой рабочих поверхностей.
Рекламные предложения на основе ваших интересов:
Поршень воспринимает давление расширяющихся газов и передает его коленчатому валу через шатун. Поршень обычно изготовляют из серого чугуна (марки СЧ 24-44, ГОСТ 1412—70) или из алюминиевых сплавов, обеспечивающих достаточную прочность при работе в условиях высоких температур.
В поршне различают головку, канавки для поршневых колец, юбку, канавку для стопорного кольца и бобышки. Днище поршня имеет толщину 10—30 мм и с внутренней стороны укрепляется ребрами. Верхняя часть боковых стенок делается такой же толщины, как и днище, а нижняя часть (юбка) — несколько тоньше, но достаточно жесткой. В средней цилиндрической части поршня имеются приливы (бобышки) с отверстиями для установки поршневого пальца 6. Чтобы при тепловом расширении поршень передвигался свободно, он устанавливается в цилиндре с зазором.
На наружной поверхности поршень имеет проточенные канавки для колец: верхние — для компрессионных (газоуплотнительных), а нижние — для маслосъемных. Маслосъемные кольца располагаются одно выше, а другое ниже поршневого пальца. В канавках для маслосъемных колец просверлены сквозные отверстия, через которые масло стекает внутрь поршня.
При работе двигателя поршень у днища нагревается сильнее и, следовательно, больше расширяется, чем у нижней направляющей части. Поэтому для обеспечения необходимого зазора поверхность поршня от оси пальца до днища обработана на конус: с меньшим диаметром у донышка и большим — у пальца. При такой обработке во время работы двигателя форма поршня приближается к цилиндрической, что обеспечивает нормальный зазор между рабочей поверхностью втулки цилиндра и поршнем. У поршней быстроходных двигателей нижняя часть имеет фаску, в которой собирается масло при поступательном движении поршня вниз и затем равномерно распределяется по рабочей поверхности втулки цилиндра, обеспечивая тем самым хорошую его смазку.
Рис. 1. Детали кривошипно-шатунногомеханизма дизеля:
Рис. 2. Поршень. 1 — поршень; 2 — поршневый палец; 3 — шатун; 4 — коленчатый вал
В настоящее время много внимания уделяется качеству материала поршней и их конструкции. Поршни из алюминиевого сплава имеют меньший вес по сравнению с чугунными, следовательно, и меньшие величины сил инерции, вызывающих в двигателях дополнительные напряжения.
Теплопроводность алюминия в 2,0—2,5 раза больше, чем чугуна, а теплоотдача от газов к алюминиевому днищу поршня на 30% меньше, чем к чугунному, т. е. днище алюминиевого поршня имеет более низкую температуру и меньшие температурные напряжения по сравнению с днищем чугунных поршней.
Так как коэффициент линейного расширения алюминия в 2,0— 2,5 раза больше, чем чугуна, во избежание заеданий поршня при расширении его вследствие нагрева зазоры между поршнем и втулкой рабочего цилиндра необходимо делать значительных размеров. С повышением температуры механические качества алюминия резко понижаются, что приводит к быстрой разработке канавок для колец и отверстий в бобышке для пальца поршня. В том случае, когда поршень чугунный, зазор между поршнем и рабочей поверхностью цилиндра, их износ, а также утечка газа не столь значительны. Поэтому при повышении мощности двигателей, вызывающем повышение тепловой и механической нагрузки, приходится отказываться от поршней из алюминиевых сплавов и переходить на чугунные или составные из чугуна и стали и применять внутреннее охлаждение поршня водой или маслом.
Величина монтажного зазора между поршнем и втулкой цилиндра зависит от технологических условий обработки деталей, чистоты обработки их поверхностей, тщательности их пригонки и монтажа двигателя в целом. Особенно большое влияние оказывают неточности при расточке отверстий для поршневых пальцев в приливах поршня. При обмерах поршней необходимо иметь в виду, что на точность обмера оказывает влияние посадка поршневого пальца. При изготовлении поршня окончательная шлифовка до заданного размера производится со вставленным поршневым пальцем. В связи с этим обмеры поршня необходимо также производить с установленным пальцем.
Большое распространение получили поршни, верхняя часть которых выполнена из кованой стали, а нижняя — из чугуна, с охлаждением верхней части маслом (двигатели «Зульцер», МАН, «Гета-веркен» и др.). У некоторых двигателей тронковые поршни снабжены в верхней части медным пояском, чтобы уменьшить зазор и возможность заедания (двигатель МАН). Иногда такой поясок ставится и внизу поршня (двигатель «Зульцер»).
Рис. 3. Поршень дизеля 18Д: 1 — поршень; 2 — компрессионное кольцо; 3 — втулка; 4 — штифт; 5 —заглушка; 6 — палец
Вместо поршней обычной конструкции с бобышками для пальца, ставляемого через боковые отверстия, применяются поршни, в ко-орых палец крепится к приливам (без сквозного отверстия в поршне) что облегчает выемку поршня из цилиндра без шатуна (двигатель «Нордберг»).
На рис. 3 изображен поршень двигателя 18Д, у которого палец может поворачиваться во втулках, запрессованных в бобышки поршня. Втулки предохраняют отверстия бобышек от износа, а потому исключается необходимость их расточки при ремонте или смене поршневого пальца.
Поршень двигателя типа Д6, изготовленный горячей штамповкой из алюминиевого сплава, показан на рис. 4. Для облегчения с наружной стороны бобышек сделаны выемки. В нижней части поршня просверлены отверстия для стока масла. Форма днища образована по контуру струй топлива, впрыскиваемого в цилиндр двигателя. Для увеличения жесткости и лучшего отвода тепла, которое передается воздуху картера, нижняя поверхность днища выполнена ребристой. Для того чтобы впускные и выпускные клапаны свободно открывались и закрывались, на головке поршня сделаны соответствующие выемки. Относительно малая высота поршня позволяет сделать рабочие втулки небольшой длины и в целом уменьшить высоту двигателя.
Рис. 4. Поршень дизеля Дб: 1 — поршень; 2 — палец; 3 — компрессионное кольцо; 4 — маслосъемное кольцо
На рис. 5 показан поршень дизеля Д-54 с плоским днищем, на котором вдоль оси поршневого пальца выфрезерованы выточки для свободного открывания впускного и выпускного клапанов.
Чтобы придать ему большую жесткость и обеспечить интенсивный отвод тепла от головки поршня, с внутренней стороны сделаны восемь радиальных и одно кольцевое ребро. Поршневой палец пустотелый, с плотной посадкой в бобышках поршня.
Рис. 5. Поршень тракторного дизеля Д-54:
Рис. 6. Поршень дизеля 6БК-43: 1 – поршень; 2 – компрессионное кольцо; 3 – палец; 4 – стопор; 5 – шпонка
Рис. 7. Пояса и направления обмеров поршня
Так же замеряют наружный диаметр пальца.
Наружный диаметр тронка поршня замеряют в трех поясах и в двух направлениях (аа и 66). Первый пояс расположен на расстоянии 10 мм от верхней кромки поршня, второй — между верхним краем отверстия бобышки и нижним поршневым кольцом головки поршня, а третий — на расстоянии 10 мм от нижнего края поршня. Данные этого замера использует механик для подсчета зазора втулка — поршень. Высоту канавок для колец записывают по результатам замеров в соответствующие графы.
Поршневые кольца служат для уплотнения поршня в цилиндре, предотвращения попадания масла в камеру сгорания и отвода тепла от поршня в стенку цилиндра. Материалом для изготовления поршневых колец служит чугун, соответствующий маркам СЧ21-40 и СЧ24-44 с повышенным содержанием фосфора (до 0,5— 0-9%) и с присадкой хрома, никеля или других легирующих элементов. Механические качества материала должны удовлетворять требованиям, предъявляемым к кольцам (твердость, упругость и т. д.).
Твердость колец обычно не превышает 190—230 НВ. Готовые кольца подбирают к цилиндрам с допуском единиц по отношению к твердости втулки цилиндра. Если твердость колец несколько превышает твердость втулки, это нельзя считать недостатком. В отношении износа поршневые кольца находятся в худших условиях, чем втулка, так как работа трения, отнесенная к единице поверхности кольца, всегда больше, чем у втулки. Для колец, изготовляемых из модифицированного чугуна и работающих в паре с втулками высокой твердости, задают твердость 220—250 НВ и выше. Иногда при стальных азотированных втулках применяют кольца повышенной твердости порядка 350—400 НВ при сохранении первоначальной прочности.
Для ускорения приработки колец и повышения износостойкости широко применяются разнообразные покрытия: лужение, свинцевание, фосфатирование, оксидирование. Иногда в кольцах предусматривают канавки для антифрикционного материала, например за-вальцовывают в них бронзовые пояски или заполняют канавки массой, содержащей графит, которую затем спекают. Благодаря своей упругости поршневые кольца прижимаются к стенкам цилиндра и создают необходимую плотность соединения.
Поршневые кольца четырехтактных двигателей при движении поршня вниз, во время такта впуска (всасывания воздуха), прижимаются к верхней торцовой поверхности канавки, а во время хода поршня вверх (при сжатии) — к нижней поверхности. Такое перемещение колец в канавках создает насосное действие, способствующее попаданию масла в камеру сгорания. Для того чтобы уменьшить это вредное явление, необходимо стремиться к минимальным зазорам между кольцом и торцовой поверхностью канавки по высоте. У двухтактных двигателей поршневые кольца все время нагружены сверху и прижаты к нижней торцовой поверхности канавки поршня; здесь насосное действие кольца отсутствует.
По назначению они подразделяются на компрессион-н ы е (газоуплотнительные) и маслосъемные. Компрессионные кольца имеют прямоугольное сечение. Число компрессионных колец зависит от давления газов и диаметра цилиндра и обычно составляет 3—5 у быстроходных двигателей и 6—7 У тихоходных.
Маслосъемные кольца служат для удаления избыточного масла со стенок цилиндра и не допускают его попадания в камеру сгорания.
Кольца ставят по одному вверху под компрессионными и внизу тронковой части поршня.
В свободном состоянии наружный диаметр поршневого кольца несколько больше диаметра цилиндра. Чтобы кольцо не заело при нагревании, в замке, образованном разрезом кольца, устанавливается небольшой зазор.
У хромированию. Износ поршневых колец зависит от скорости движения поршня, температуры рабочей среды, нагрузки и режима работы двигателя и степени загрязнения смазочного масла. Они выходят из строя не одновременно: сперва — верхние, а затем —средние и нижние. При одинаковой мощности износ колец в быстроходном дизеле выше, чем в тихоходном.
Очень большое влияние на износ поршней и колец имеют нагрузка и температура двигателя. Высокая температура внутри цилиндра затрудняет смазку его поверхностей, а низкая обычно является причиной ускоренного износа поршней и поршневых колец вследствие коррозии. Попадание пыли из воздуха также является причиной значительного изнашивания поршневых колец. Поэтому необходимо содержать фильтры в исправности и обеспечивать полную герметичность в соединениях.
Рис. 9. Схема насосного Действия поршневых колец
Рис. 10. Замки поршневых колец: а — прямой; б — косой; в — ступенчатый
Наибольшему износу подвержены два верхних поршневых кольца, поэтому для повышения износостойкости их подвергают пористо-
Измерение величины зазора между поршневым кольцом и опорной поверхностью канавки в поршне производится по всей окружности щупом при надетом на поршень кольце.
Износ поршневых колец сверх допустимых размеров наступает значительно раньше предельного износа цилиндра. Поэтому предельный износ поршневых колец определяет сроки профилактического ремонта двигателей. Перед тем как ставить на поршень новые кольца, их концы следует подогнать под соответствующий нормам размер. Суммарная длина просветов между кольцом и втулкой не должна превышать длины дуги 90°, величина просвета должна быть не более 0,05 мм. Во время работы двигателя изнашиваются также торцовые поверхности поршневых колец и канавок поршня. Пригорают поршневые кольца у двухтактных двигателей, работающих при высокой температуре.
Значительные износы колец (увеличение зазоров в стыках), а также пригорание их вызывают ухудшение пусковых качеств двигателя, проникновение отработавших газов в картер, увеличение дымности выпускных газов и удельного расхода топлива и понижение развиваемой двигателем мощности.
Поршневой палец служит для шарнирного сочленения поршня с шатуном. Он воспринимает силу давления газов, действующую на поршень, и передает ее шатуну. Поршневые пальцы для тихоходных двигателей изготовляют из мягкой углеродистой стали, а для быстроходных — из хромоникелевой стали 12ХНЗА. Для повышения прочности и износостойкости поверхность пальцев цементируют на глу-бнну 0,75—1,0 мм и закаляют. Часто поверхность пальцев хромируют.
В зависимости от характера посадки в бобышках поршня пальцы бывают неподвижные и плавающие. Плавающие пальцы, поворачиваясь относительно своей оси при работе двигателя, способствуют уменьшению износа и устраняют возможность односторонней выработки. Для предотвращения осевого перемещения пальцы в бобышке фиксируют пружинными кольцами или алюминиевыми заглушками со сферической головкой. При этом радиус сфер головок несколько меньше диаметра цилиндра. В заглушке просверлено отверстие, через которое выходит воздух из полости пальца при работе двигателя. Если бы отверстия не было, оставшийся внутри пальца воздух при нагреве, расширяясь, прижимал бы заглушку к рабочей поверхности втулки цилиндра, что вызывало бы ее местный износ.
Рис. 11. Плавающий поршневой палец
Рис. 12. Неподвижный поршневой палец
На рис. 12 изображен поршневой палец с неподвижной посадкой в поршне. От проворачивания он удерживается шпонкой, а от осевого перемещения — коническим штифтом. Такое крепление обеспечивает свободное удлинение пальца в одну сторону при нагревании, не вызывая деформации в теле поршня. Чтобы легче было ставить палец на место и вынимать при разборке, он сделан ступенчатым с большим диаметром со стороны шпонки, средним — в месте соединения с шатуном и меньшим — со стороны конического штифта. Поэтому вынимать палец можно только в сторону шпонки.
Учитывая, что поршневые пальцы работают в условиях больших давлений и высоких температур, их, в целях уменьшения износа, шлифуют и полируют с чистотой отделки поверхности 0,1—0,2 мк. Рабочую поверхность пальцев часто хромируют. Внешний диаметр пальца обычно составляет 0,25—0,3 диаметра поршня, а длина вкладыша верхней головки шатуна должна быть максимально возможной с тем, чтобы создать достаточную опорную поверхность.
Втулка верхней головки шатуна, в которой работает палец, должна всегда иметь достаточное количество смазки, которая у большинства дизелей поступает от коленчатого вала — через шатун или разбрызгиванием.
Выработку поршневого пальца и втулки верхней головки шатуна определяет механик, измеряя зазор между поверхностью пальца и втулкой и обмеряя сам палец.
Карта обмера узла «палец — втулка» должна отражать результаты контроля за изменением размеров поршневого пальца и втулки верхней головки шатуна при каждом ремонте двигателя. Техническое состояние головного сочленения определяется изношенностью пальца, втулки верхней головки шатуна и величиной зазора между ними.
Пояса II и III втулки и пальца находятся в одной плоскости замера. Это позволяет определить величину зазора «втулка — палец» вычитанием из замеренного диаметра втулки наружного диаметра пальца. После замеров, проведенных при ремонте двигателя, механик пишет «Заключение о состоянии и необходимом ремонте» (замена, обработка по ремонтным размерам и т. д.) по каждому головному сочленению.
Рис. 13. Пояса обмера деталей головного соединения (поршневого пальца и головной втулки)
Шатун — основная деталь шатунно-кривошипного механизма, преобразующего возвратно-поступательное прямолинейное движение поршня во вращательное движение коленчатого вала. Шатуны изготовляют штамповкой или поковкой из углеродистой стали высокого качества. В малооборотных двигателях применяют главным образом углеродистые стали: для стержней — сталь 35, для головок — сталь 25, 35; для шатунных болтов — сталь 30, а иногда и легированные стали. В многооборотных двигателях в зависимости от степени напряжения для стержней и крышек при меняют углеродистую сталь 45 , легированные стали 40Х, 45Х, 30ХМА,40ХНМА и, наконец, 18Х2Н4ВА, отличающуюся особо высокими показателями прочности и ударной вязкости; для шатунных болтов — сталь 20ХНВА и 18Х2Н4ВА.
Шатуны делают обычно круглого сечения, а в быстроходных двигателях (с целью облегчения) — двутавровыми. Шатун состоит из трех частей: верхней головки, стержня и нижней головки. Верхняя головка
неразъемная. В нее запрессовывается бронзовая втулка с канавками на рабочей поверхности, по которым подводится смазочное масло к средней части поршневого пальца. Втулки верхней головки изготовляются из бронзы. В настоящее время все больше применяются биметаллические втулки, состоящие из слоя бронзы, залитой в стальную втулку. Это объясняется их небольшой стоимостью и возможностью посадки в отверстие с большим натягом.
Нижняя головка шатуна, соединяющая его с шейкой вала, разъемная. Крышка нижней головки шатуна прикрепляется к телу шатуна через установленные в стыках прокладки двумя или четырьмя шатунными болтами с гайками из высококачественной стали. Внутренние поверхности нижней головки шатуна залиты баббитом. Трущиеся поверхности баббита имеют канавки, которые обеспечивают равномерное распределение смазки по мотылевой шейке вала. Прилегание вкладыша нижней головки к шейке коленчатого вала по мере выработки баббита регулируется уменьшением количества прокладок в разъеме подшипника.
Рис. 14. Шатун с круглым сечением стержня: 1 — верхняя головка; 2 — стержень; 3— маслоподводящий канал; 4 — нижняя головка; 5 — крышка подшипника
Стяжные болты нижней головки шатуна подвержены растяжению и разрыву, поэтому по истечении установленного заводом срока их необходимо заменить новыми, даже при отсутствии дефектов.
В V-образных быстроходных двигателях применяют два типа шатунов. В первом случае оба шатуна нижними головками соединяются непосредственно с мотылевой шейкой коленчатого вала; во втором — один шатун (главный) соединяется непосредственно с мотылевой шейкой, а второй (дополнительный) — с проушиной главного шатуна.
Рис. 15. Шатуны с двутавровым сечением стержня с прямым разъемом нижней головки: 1— верхняя головка; 2—головная втулка; 3— стержень; 4 — маслоподводящий канал; 5 — нижняя головка; 6—вкладыш подшипника; 7 — крышка подшипника
Рис. 16. Шатун с двутавровым сечением стержня и с косым разъемом нижней головки: 1 —верхняя головка; 2 — головная втулка; 3 — стержень; 4 — нижняя головка; 5 — вкладыш подшипника; 6 — шатунный болт
Коленчатый вал—наиболее ответственная и сложная по конструкции деталь, срок службы которой часто определяет долговечность двигателя. При работе двигателя коленчатый вал подвергается действию периодически изменяющихся сил давления газов, сил инерции возвратно-поступательно движущихся деталей и центробежных сил вращающихся деталей. Все они вызывают деформации вала (изгиб, скручивание, сжатие и растяжение). Длительная работа коленчатого вала может быть обеспечена только при услозии правильного его положения в подшипниках, исключающих недопустимый прогиб вала при работе. У тихоходных двигателей коленчатые валы чаще всего изготовляют из углеродистой стали, а у быстроходных—из легированной; они состоят из коренных и шатунных шеек, соединенных щеками.
Коленчатые валы характеризуются парностью колен, углом между ними и порядком работы цилиндров. Число колен вала зависит от числа цилиндров. Небольшие валы изготовляют цельными, крупные — составными из двух или трех частей. В шейках вала и щеках просверлены отверстия, по которым к подшипникам подводится смазка.
При выборе угла между коленами исходят из условия необходимости обеспечения наиболее равномерного вращения вала двигателя. Для этого воспламенение топлива в отдельных цилиндрах должно происходить через определенные углы поворота вала и одинаковые промежутки времени. Угол между соседними мотылями определяется числом тактов двигателя и числом его цилиндров и равен количеству градусов поворота вала за весь цикл, разделенному на число цилиндров. Для четырехцилиндрового четырехтактного двигателя угол ф = 720 : 4 = 180°, т. е. все мотыли располагаются в одной плоскости. Для шестицилиндрового двухтактного двигателя Ф = 360 : 6 = 60°.
Его колена расположены относительно друг друга под углом 720 : 6 = 120° и в определенной последовательности (согласно порядку работы цилиндров). Наиболее распространенные порядки работы цилиндров шестицилиндрового двигателя следующие: 1—5—3—6—2—4, 1—4—2—6—3—5, 1—2—3—6—5—4.
Рис. 17. Главный и прицепной шатуны: 1 — главный шатун; 2 — заглушка; 3 — поршневой палец; 4 — поршень; 5 — прицепной шатун; 6 — палец для крепления шатуна; 7 — винт; 8 — шайба; 9 — проушина для крепления прицепного шатуна; 10 — крышка; 11 — вкладыш
Один конец вала имеет фланец для крепления маховика двигателя. На другом конце крепятся шестерни привода компрессора, водяного и масляных насосов.
Рис. 18. Конструкции коленчатых валов: а — прямоугольная форма мотыли; б, «, г —эллиптическая форма мотыля; д,е — со скосами углов мотыля; ж, з— круглая форма мотыля
Для уравновешивания центробежных сил, с которыми вращающиеся массы действуют на подшипники, щеки мотылей снабжены противовесами.
Хорошая жесткость вала достигается при овальной или круглой форме щек мотыля. Для уменьшения износа шейки подвергаются цементации, азотированию или поверхностной закалке токами высокой частоты.
Причиной изнашивания коленчатого вала является, в первую очередь, трение шеек в подшипниках, а также наличие механических примесей в смазочном масле. В результате выработки сечение шейки делается овальным (эллиптичным), а сама шейка — конусовидной. Овальность, или эллиптичность, определяется разностью двух взаимно перпендикулярных диаметров сечения шейки, а конусность — разностью диаметров двух сечений шейки, при условии, что эти диаметры лежат в одной плоскости, проходящей через ось конуса.
Рис. 19. Коленчатый вал шестицилиндрового дизеля
Для свободного вращения шеек коленчатого вала в рамовых подшипниках и для размещения слоя масла необходимой толщины между трущимися поверхностями во вкладышах устанавливаются зазоры определенного размера. Зазоры в подшипниках при работе двигателя не остаются постоянными, особенно в первые часы работы двигателя после ремонта, т. е. в период приработки подшипников. После обкатки двигателя производится подтяжка подшипников с доведением величин монтажных зазоров до эксплуатационных.
В двигателях, не имеющих прокладок в разъемах вкладышей подшипников, монтажные и эксплуатационные зазоры одинаковы.
Зазоры замеряют до и после каждого ремонта двигателя и подтяжки подшипника, раскепы — еще чаще. Эллиптичность и биение рамовых шеек замеряют перед каждым заводским ремонтом двигателя, а уменьшение диаметра шеек — перед капитальным ремонтом.
Диаметр рамовых шеек замеряют микрометром с ценой деления 0,01 мм в двух поясах и в двух взаимно перпендикулярных направлениях, располагаемых по осям ближайшей щеки.
Рис. 20. Коленчатый вал дизеля 24 10,5/13: 1 — шестерня; 2 — болт крепления противовеса; 3—противовес; 4 — заглушка со стяжным болтом; 5 — шейка вала; 6 — шестерня привода распределительного вала; 7 — шпонка; 8 — масляная трубка
Кроме того, при втором заводском (капитальном) ремонте биение рамовых шеек вала обязательно проверяют на стенке, для чего вал предварительно устанавливают по центровой линии. Гнездо рамового подшипника замеряют без крышки в двух поясах (I и II) на расстоянии 1/4 длины гнезда от его края.
Рис. 21. Обмер рамовых шеек коленчатого вала
Рис. 22. Измерение зазора в рамовом подшипнике: 1 — перемычка фундаментной рамы; 2— нижняя половинка вкладыша рамового подшипника; 3 — шейка коленчатого вала: 4 — прутки свинцовой проволоки
Монтажный зазор замеряют при сборке двигателя после ремонта или изготовления, а эксплуатационный — после приработки подшипников и регулировки зазора путем удаления или замены части прокладок. Эллиптичность шеек вала для каждого пояса определяется разностью размеров наибольшего и наименьшего диаметров вала, замеряемых в направлениях аа и бб.
Диаметры мотылевых шеек замеряют микрометром в двух поясах (I и II) и двух взаимно перпендикулярных направлениях (аа и бб). Для четырехтактных двигателей направление аа смещено от оси цилиндра на 10—15° в сторону вращения кривошипа, для двухтактных — против вращения кривошипа. Эллиптичность шеек вала для каждого пояса определяется разностью размеров наибольшего и наименьшего диаметров вала, замеренных в направлениях аа и бб. Внутренний диаметр мотылевого подшипника замеряют микрометрическим или индикаторным нутромером, установленным по микрометру, в двух поясах (I и II) и одном направлении (аа).
Зазор между подшипником и шейкой вала определяют как разность замеров внутреннего диаметра подшипника и диаметра моты-левой шейки либо посредством выжимки свинцовой проволоки. Монтажный зазор замеряют при сборке двигателя после ремонта или изготовления, а эксплуатационный — после приработки подшипников и регулировки зазора путем удаления или замены части прокладок.
зависящие от величины вращающих моментов, сил упругости вала и сил инерции, вызывающих колебания. При совпадении частот и направлений собственных и вынужденных колебаний наступает так называемое состояние резонанса, вызывающее возрастание внутренних напряжений вала. Число оборотов коленчатого вала, при котором наступает явление резонанса, называется критическим, а колебания при этом — критическими колебаниями.
Критические числа оборотов и напряжения, возникающие при них в вале, определяются расчетом и проверяются при помощи специального прибора, называемого торсиографом.
Рис. 23. Пояса и направления обмеров мотылевых шеек
Коленчатый вал и присоединенные к нему валы, передающие крутящий момент к гребному винту, представляют собой упругую систему, способную под действием внешних периодически изменяющихся нагрузок колебаться. Колебания, продолжающиеся и после того, как вызвавшие их силы или моменты сил перестали действовать, называются собственными колебаниями. Характер собственных колебаний и скорость их затухания зависят от внутренних сопротивлений материала вала, внешнего сопротивления окружающей среды и трения в подшипниках. При затухании частота колебаний остается постоянной, а амплитуда колебаний уменьшается.
Колебания, вызванные периодически изменяющимися вращательными моментами, называются вынужденными колебаниями, причем сила скручивания вала непрерывно изменяется на протяжении полного оборота.
Во время работы двигателя собственные колебания практически затухают. Остаются лишь вынужденные крутильные колебания.
Возникновение резонанса при соответствующих ему критических числах оборотов вала сопровождается значительным шумом, сильной вибрацией дизеля и стуками в соединениях подвижных частей. Происходящее при этом скручивание вала приводит к на-рушению балансировки двигателя и регулировки газораспределительных органов.
Дополнительные напряжения вала, возникающие в диапазоне резонансных колебаний, обычно значительно превышают величину тех крутильных напряжений, на которые рассчитан коленчатый вал. В результате может наступить разрушение вала. При этом излом происходит вблизи так называемого вибрационного узла, т. е. у предпоследнего или последнего колена вала, расположенного у маховика. Излом в таких случаях имеет характер повреждения, возникшего от усталости металла.
В двигателях с большим количеством цилиндров и широким диапазоном чисел оборотов при эксплуатации невозможно избежать резонансных колебаний. В этом случае некоторые числа оборотов следует исключить (быстрым переключением). Ширина запрещенного диапазона обычно составляет около 10% от номинального числа оборотов. Если резонанс наступает при номинальном числе оборотов двигателя, то в этом случае иногда приходится изменять размеры промежуточного вала или гребного винта с целью смещения зоны критических чисел оборотов.
Если же интервал критических чисел оборотов невозможно исключить из рабочего диапазона чисел оборотов двигателя, на носке коленчатого вала двигателя закрепляется демпфер (успокоитель колебаний). Работа демпфера заключается в том, что при возникновении колебаний вала дополнительная масса демпфера, вращающаяся вместе с валом, воспринимает часть энергии возмущающих сил, что способствует затуханию колебаний.
Маховик предназначен для накопления энергии во время рабочего хода, когда давление газов на поршень достигает наибольшей величины, и отдачи ее во время нерабочих ходов. Благодаря этому достигается равномерное вращение вала в условиях периодически меняющихся давлений на поршень. Маховик дает также возможность выводить коленчатый вал из мертвых точек и облегчает пуск двигателя. Отливают маховики обычно из стали или чугуна и после обработки проверяют балансировкой. Маховик обычно крепится на фланце коленчатого вала призонными болтами.
Рекламные предложения:
Читать далее: Газораспределительный механизм двигателя
Категория: — Дизельные двигатели
Главная → Справочник → Статьи → Форум
Цилиндр и поршень как основные детали двигателя
Цилиндр и поршень – одни из ключевых деталей любого двигателя. Стенка цилиндра, днище поршня и нижняя плоскость головки блока цилиндра образуют замкнутую полость, в которой происходит сгорание топливно-воздушней смеси.
Поршень, вставленный в цилиндр, воспринимает усилие образовавшихся газов и преобразует их энергию в поступательное движение, которое заставляет вращаться коленчатый вал.
Цилиндр и поршень – индивидуально подобранная пара, которая прирабатывается в ходе эксплуатации автомобиля, обеспечивая наилучшие режимы и эффективность работы двигателя.
В данной статье мы рассмотрим пару «цилиндр-поршень» подробнее: конструкцию и функции этих элементов, условия их работы и возможные проблемы при эксплуатации цилиндро-поршневой группы (ЦПГ).
Что представляют собой цилиндр и поршень?
В двигателях современных автомобилей от 2 до 16 цилиндров, объединенных в единый прочный корпус – блок цилиндров. Количество цилиндров определяет мощность силового агрегата.
Внутренняя часть цилиндра, которая является его рабочей поверхностью, называется гильзой, внешняя часть, составляющая единое целое с корпусом блока, – рубашкой. По каналам рубашки циркулирует охлаждающая жидкость.
Внутри цилиндра совершает возвратно-поступательное движение поршень. Он передает усилие, возникающее от давления газов, на шатун, герметизирует камеру сгорания и отводит от нее излишек тепла.
Поршень имеет вид перевернутого стакана, состоит из головки (днища), уплотняющих колец и направляющей части (юбки).
В бензиновых двигателях используются поршни с плоским днищем – они проще в изготовлении, меньше нагреваются при работе. Иногда в них выполняются канавки, способствующие полному открытию клапанов. Поршни дизельных двигателей имеют выемку заданной формы на дне, чтобы воздух, поступающий в цилиндр, лучше перемешивался с топливом.
Плотность соединения поршня с цилиндром обеспечивают поршневые кольца. Их число и расположение зависит от типа и предназначения двигателя. Чаще всего поршень включает два компрессионных кольца и одно маслосъемное.
Компрессионные кольца уменьшают попадание газов из камеры сгорания в картер двигателя, а также отводят тепло от головки поршня к стенкам цилиндра. По форме они могут быть трапециевидными, бочкообразными и коническими.
Верхнее компрессионное кольцо изнашивается быстрее других, поэтому его наружную поверхность подвергают пористому хромированию или напылению молибдена. Благодаря этим процедурам первое кольцо лучше удерживает смазочный материал и становится более износостойким. Остальные уплотняющие кольца покрывают слоем олова для лучшей приработки к цилиндрам.
Маслосъемное кольцо при движении поршня вверх и вниз удаляет излишки масла со стенок цилиндра, предупреждая тем самым их попадание в камеру сгорания. Через дренажные отверстия в стенках поршня масло попадает внутрь последнего и далее – в картер.
Направляющая часть поршня (юбка) может иметь конусообразную или бочкообразную форму – это позволяет компенсировать расширение при достижении высоких рабочих температур.
На юбке расположено отверстие двумя приливами (бобышками), в котором крепится поршневой палец, соединяющий поршень с шатуном.
Палец поршня имеет трубчатую форму и может устанавливаться по-разному:
- Закрепляться в бобышках поршня, но вращаться в головке шатуна
- Закрепляться в головке шатуна и вращаться в бобышках поршня
- Свободно вращаться в бобышках поршня и в головке шатуна (плавающие пальцы)
Шатун соединяет поршень с коленчатым валом. Его верхняя головка движется возвратно-поступательно, нижняя вращается вместе с шатунной шейкой коленчатого вала, стержень совершает сложное колебательное движение. В процессе работы шатун подвергается сжатию, изгибу и растяжению, поэтому его производят прочным и жестким, а для уменьшения сил инерции – легким.
Конструкционные материалы
Для того, чтобы цилиндры могли выдерживать высокие нагрузки, их изготавливают из высокопрочных материалов – чугуна или стали с различными присадками. В целях снижения веса современные блоки часто производят из алюминия, а внутреннюю часть цилиндра, запрессованную в блок и контактирующую с движущимся поршнем – из стали.
Автомобильные поршни двигаются внутри цилиндра с высокой скоростью, в процессе работы они подвержены воздействию высоких температур и давлений. Именно поэтому изначально их отливали из чугуна. С развитием технологий основным конструкционным материалом стал алюминий, его использование позволило обеспечить меньшую нагрузку на детали, лучшую теплоотдачу, рост оборотов и мощности двигателя.
Сегодня многие автомобили, особенно с дизельными ДВС, оснащаются сборными поршнями из стали. Они легче алюминиевых, за счет меньшей компрессионной высоты позволяют использовать удлиненные шатуны и, тем самым, снизить боковые нагрузки в паре «поршень-цилиндр».
Поршневые кольца производятся, в основном, из специального серого высокопрочного чугуна с легирующими добавками (хромом, молибденом, никелем, вольфрамом). Эти материалы обеспечивают высокую термо- и износостойкость колец, а также их отличную прирабатываемость.
В процессе работы детали ЦПГ подвергаются значительным циклическим, механическим и тепловым нагрузкам, которые повторяются тысячи раз в минуту.
Именно поэтому современные материалы, применяемые для изготовления поршней, обладают:
- Высокой механической прочностью
- Хорошей теплопроводностью
- Малой плотностью
- Незначительным коэффициентом линейного расширения
- Антифрикционными свойствами
- Коррозионной устойчивостью
Некоторые производители автокомпонентов в целях снижения потерь, вызванных трением, покрывают боковую поверхность поршней специальным антифрикционным материалом, содержащим графит или дисульфид молибдена. Однако со временем заводское покрытие разрушается. Во избежание усиленного износа поршня и образования задиров оно требует восстановления.
Для этих целей применяются специальные материалы на основе твердых смазочных частиц. Одним из самых эффективных является антифрикционное твердосмазочное покрытие MODENGY Для деталей ДВС.
Состав на основе высокоочищенного дисульфида молибдена и графита имеет практичную аэрозольную упаковку с оптимальными параметрами распыления.
Материал наносится на юбки поршней быстро и равномерно, для отверждения не требует нагревания в печи, создает на поверхности долговечное сухое покрытие, снижающее его износ и препятствующее появлению задиров.
Охлаждение цилиндро-поршневой группы
При сгорании топлива в надпоршневом пространстве в каждом цикле работы двигателя выделяется огромное количество тепла. Именно поэтому цилиндро-поршневая группа нуждается в эффективном охлаждении.
Для отвода избыточного тепла предусмотрена воздушная или жидкостная система охлаждения.
Воздушное
Цилиндры двигателя с воздушным охлаждением снаружи покрыты множеством ребер, которые обдуваются встречным или искусственно созданным (с помощью воздухозаборников) потоком воздуха.
Жидкостное
При жидкостном (водяном) охлаждении цилиндры снаружи омываются охлаждающей жидкостью, циркулирующей в толще блока. Нагретые цилиндры отдают ей часть тепла, затем жидкость попадает в радиатор, охлаждается и вновь подается к цилиндрам.
Система смазки цилиндров
Если цилиндр не смазан изнутри, поршень будет заклинивать, что рано или поздно приведет к разрушению двигателя. Именно поэтому качественное смазывание стенок – вторая по значимости проблема после отвода тепла.
Для удержания стабильной масляной пленки на внутренние поверхности цилиндров наносят микросетку. Это процесс называется хонингованием. Благодаря наличию такой сетки на стенках всегда присутствует слой масла, что не только снижает трение в паре «поршень-цилиндр», но и способствует отведению излишков тепла внутри ЦПГ.
Неисправности и ресурс ЦПГ
Даже при правильной эксплуатации автомобиля со временем могут возникнуть проблемы с цилиндро-поршневой группой. Их основная причина – в сложных условиях работы ЦПГ.
Под влиянием очень высоких нагрузок и температур происходит:
- Появление пробоин, сколов, трещин на рабочих поверхностях цилиндров
- Деформация посадочных мест под гильзу
- Оплавление или прогар днища поршней
- Разрушение, закоксовывание, залегание колец
- Различные деформации на теле поршней
- Сужение зазора между поршнем и цилиндром, как следствие – задиры на юбках
Эти и другие неисправности цилиндро-поршневой группы неизбежны при перегреве двигателя – из-за отказа термостата, помпы или разгерметизации системы охлаждения, а также при сбоях в работе вентилятора охлаждения радиатора, самого радиатора или его датчика.
Проблемы с деталями ЦПГ можно заподозрить при увеличении расхода масла, ухудшении пусковых качеств двигателя, снижении его мощностных показателей, появлении шума и стука при работе. Не стоит игнорировать эти моменты, так как цилиндро-поршневая группа – основной узел ДВС, и его неисправности неизбежно ведут к дорогостоящему ремонту.
Точно определить состояние цилиндров и поршней помогает специализированная диагностика: как самой цилиндро-поршневой группы (путем ее полной разборки), так и других систем автомобиля (например, воздушного фильтра).
Кроме того, в ходе сервисных работ проводятся различные операции по измерению компрессии в цилиндрах двигателя, берутся пробы картерного масла и пр.
Ресурс цилиндро-поршневой группы зависит от разных факторов: вида ДВС, режима его эксплуатации, регулярности обслуживания и т.д. В отечественных автомобилях срок службы ЦПГ составляет около 200 тыс. км, в иномарках – до 500 тыс. км.
Ремонт цилиндро-поршневой группы двигателя подразумевает замену маслосъемных и компрессионных колец, установку новых поршней и шатунов, восстановление и расточку цилиндров.
Величину износа цилиндров определяют с помощью индикаторного нутрометра. Трещины и сколы на стенках заваривают или заделывают эпоксидными пастами.
Новые поршни нужного диаметра и массы подбирают к гильзам, а поршневые пальцы – к поршням и втулкам верхних головок шатунов. Шатуны предварительно проверяют и при необходимости восстанавливают.
Для того, чтобы цилиндро-поршневая группа полностью вырабатывала свой ресурс, рекомендуется использовать масло, предписанное производителем, и осуществлять его замену строго по регламенту.
Важно следить за температурным режимом работы двигателя, не допускать его перегрева и холодного пуска зимой.
СУДОРЕМОНТ ОТ А ДО Я.: Остов ДВС.
Остов ДВС состоит из следующих основных деталей: фундаментной рамы, станины, рабочих цилиндров и цилиндровых крышек. Все эти детали при помощи болтов и шпилек плотно соединяются между собой, образуя прочную и жесткую конструкцию, воспринимающую нагрузку от массы двигателя и усилия от давления газов, передаваемые через движущиеся детали.Фундаментная рама служит основанием двигателя, на котором устанавливается станина. Она представляет собой опору для рамовых подшипников, на которые укладывается коленчатый вал двигателя. Рама должна выполняться герметичной, так как служит емкостью (картером) для масла, стекающего из системы смазки и охлаждения поршней. Фундаментные рамы в зависимости от их конструкции, технологии изготовления и применяемого материала могут быть цельными или составными, литыми или сварными, чугунными, стальными или из легких сплавов.
Фундаментные рамы судовых ДВС отливаются в основном из серого чугуна. Однако в последнее время нередко применяют стальные сварные конструкции. Рамы длиной более 4— 5 м изготавливают составными из нескольких частей, жестко соединяемых между собой болтами.
На рисунке показана цельная литая чугунная фундаментная рама 4 четырехцилиндрового двигателя, состоящая из двух продольных 6 и пяти поперечных 3 балок. Крепление рамы к судовому фундаменту осуществляется при помощи полок 5, имеющих отверстия для отжимных и крепежных болтов, часть из которых изготавливается калиброванными (призонными). Призонные болты фиксируют раму на фундаменте в строго определенном положении. Рама двигателя устанавливается на судовой фундамент на клиньях, планках и сферических прокладках.
В поперечных балках фундаментной рамы, которые подкрепляются ребрами жесткости, расположены постели для вкладышей рамовых подшипников 2, закрытых крышками 1.
Крышки крепятся к поперечным балкам при помощи шпилек. Снизу фундаментная рама имеет поддон, вместе с поперечными балками образующий отсеки (колодцы), соединенные между собой (для перетока масла). Внутренние полости отсеков отделяются от поддона сетками. Для уменьшения массы рамы поддон изготавливают отдельно из листовой стали толщиной 2—3 мм и прикрепляют к ней болтами или при помощи сварки.
В настоящее время большинство главных двигателей выполняются с сухим картером, а маслосборная цистерна для циркуляционного масла располагается под ним.
Для снижения вредного действия вибрации и уменьшения шума во время работы вспомогательные ДВС часто устанавливают на фундаменте с помощью пружинных или резино-металлических амортизаторов.
Рамовые подшипники служат опорой коленчатого вала и воспринимают усилия, передаваемые шатуном фундаментной раме. Рамовый подшипник показан на рисунке:
Он состоит из верхнего 6 и нижнего 8 вкладышей, залитых антифрикционным сплавом 3 (баббитом Б83). Нижний вкладыш устанавливается в постели, расположенной в фундаментной раме 9, верхний — в крышке 4, крепящейся к раме при помощи шпилек 7 с гайками, которые после затяжки должны быть зашплинтованы. Оба вкладыша имеют заплечики 1, предотвращающие их перемещение в осевом направлении. Между торцами верхнего и нижнего вкладышей устанавливается набор латунных прокладок 2 разной толщины, предназначенных для установки и регулирования зазора между вкладышами и шейкой коленчатого вала. Смазочное масло к рамовому подшипнику подводится по трубке и штуцеру 5, который ввинчивается в крышку 4. Нижним концом штуцер входит в отверстие верхнего вкладыша, тем самым предохраняя его от проворачивания в постели.
Существуют и другие стопорные приспособления от проворачивания вкладышей подшипников. При отсутствии специального упорного подшипника один из рамовых, обычно ближайший к маховику, выполняет его функции. Он называется установочным и предотвращает осевое перемещение коленчатого вала. Длина этого вкладыша равна длине рамовой шейки. Остальные рамовые вкладыши делаются несколько короче для обеспечения беспрепятственного удлинения коленчатого вала при его нагревании. Торцевые поверхности установочного подшипника являются упорными и залиты антифрикционным сплавом. В качестве антифрикционного материала для наплавки вкладышей подшипников, кроме баббита, используется свинцовистая бронза и некоторые другие сплавы на основе алюминия и др.
Наиболее широко в судовых двигателях используются баббиты. Но они надежно работают при сравнительно небольших удельных давлениях (до 20 МПа) и невысоких температурах нагрева (до 100 С). Подшипники из свинцовистой бронзы выдерживают удельные давления до 50 МПа и нагрев до 200 С. Недостатком этих подшипников является плохая их приработка, поэтому необходима точная обработка вкладышей и тщательная их установка. Шейки коленчатого вала должны иметь поверхностную закалку, чего не требуется при заливке вкладышей баббитом.
Станина служит опорой для цилиндров двигателя, скрепляет их в одну жесткую конструкцию и образует закрытую камеру для кривошипно-шатунного механизма. В крейцкопфных двигателях станина, кроме того, воспринимает давление газов через параллели. В зависимости от конструкции и технологии изготовления станины бывают цельные или составные, литые или сварные. Материалом для изготовления станин служит в основном чугун или сталь.
Станины в судовых двигателях применяются двух основных типов: в виде отдельных колонн или стоек, закрытых съемными щитами и люками, и в виде закрытой коробки (картерный тип). Станины первого типа используются в тихоходных судовых крейцкопфных двигателях большой мощности. При такой конструкции литые чугунные колонны располагаются над каждым рамовым подшипником в плоскости, параллельной движению кривошипов, и крепятся внизу к общей фундаментной раме.
Конструкция станины в виде колонн удобна для осмотра и разборки деталей движения и подшипников ДВС. В двигателях тронкового типа станины для увеличения жесткости выполняют в виде коробок, представляющих собой цельную отливку для всех цилиндров. В двигателях малой и средней мощности широко применяется блок-картер, отливаемый заодно с рубашками цилиндров, или общий блок картера с фундаментной рамой. Во время работы двигателя станина и цилиндры (блоки цилиндров) испытывают действие растягивающих усилий в результате давления газов на крышки цилиндров. Для разгрузки этих деталей от растягивающих усилий используют анкерные связи, изготавливаемые из высокосортной стали.
Анкерные связи:
Длинные анкерные связи 1, имеющие резьбу на обоих концах, проходят через отверстия в фундаментной раме 4, станине 3 и цилиндре (блоке цилиндров) 2. Анкерные связи стягивают эти детали при помощи гаек, которые после затяжки шплинтуются.
Рабочие цилиндры являются очень ответственной деталью двигателя. В них совершаются рабочие циклы, в течение которых давление и температура газов изменяются в широких пределах.
Цилиндры судовых двигателей состоят, как правило, из внутренней части (рабочей втулки) и наружной рубашки. Между рабочей втулкой и рубашкой образуется полость, служащая для постоянной циркуляции охлаждающей воды во время работы двигателя. Она называется зарубашечным пространством. Цилиндры двигателей могут быть отлиты и установлены на станину каждый отдельно или в виде одной общей отливки, образующей цилиндровый блок, что значительно повышает жесткость конструкции, одновременно уменьшая ее массу. Одиночные цилиндры применяются сравнительно редко, главным образом в тихоходных двухтактных ДВС большой мощности.
В настоящее время в судовых двигателях наиболее часто используется блочная конструкция цилиндров. Для облегчения изготовления блок цилиндров может быть выполнен из нескольких частей, которые при сборке двигателя жестко соединяются между собой. Рубашки или блоки четырехтактных двигателей отличаются от блоков двухтактных тем, что последние имеют полости для подвода продувочного воздуха и отвода отработавших газов.
Цилиндр тихоходного двухтактного ДВС с прямоточной клапанной продувкой показан на рисунке:
В рубашке 1 установлена съемная рабочая втулка 2, которая своим верхним фланцем плотно садится на кольцевой выступ рубашки, а нижней частью входит в ее отверстие. Для предотвращения попадания охлаждающей воды в картер двигателя в нижней части рабочей втулки с наружной стороны устанавливают уплотнительные резиновые кольца 10. Подача смазочного масла в цилиндры осуществляется по штуцерам 8, которых может быть от двух до восьми. Продувка цилиндра осуществляется через окна 9, а удаление отработавших газов производится через выпускной клапан, установленный в отверстии 4 крышки цилиндра. Осмотр и очистка зарубашечного пространства от осадков и накипи производится через отверстия (с люками) 3.
В нижней части рубашки цилиндра находится отверстие для подвода охлаждающей воды в зарубашечное пространство, поступающей через выходной канал 7 и переливной патрубок 6 в полость охлаждения 5 крышки цилиндра и далее в отливной трубопровод.
Рабочие втулки, непосредственно соприкасающиеся с охлаждаемой водой, называются мокрыми. Сухие втулки (не соприкасающиеся с водой) в судовых двигателях не применяются.
На рисунке показан цилиндр четырехтактного ДВС, состоящий из рубашки 1 и съемной рабочей втулки 2, опирающейся своим буртиком (верхним фланцем) 9 на выточку в верхней части рубашки. Положение рабочей втулки в нижней части фиксируется направляющим пояском 5. Между ним и втулкой устанавливаются уплотнительные резиновые кольца 6 круглого сечения, предотвращающие попадание воды в картер. Рубашка цилиндра имеет фланец 4 для крепления к станине, горловины 7 для осмотра и очистки зарубашечного пространства, а также отверстия 3 и 8 для подвода охлаждающей воды в зарубашечное пространство и отвода ее в полость охлаждения крышки цилиндра.
Материалом для изготовления рубашек отдельных цилиндров и блоков цилиндров служит серый и легированные чугуны, литая сталь и алюминиевые сплавы. Рабочие втулки изготавливаются из легированного чугуна и реже отливаются из стали. Внутреннюю часть рабочей втулки шлифуют до зеркального блеска и подвергают специальной обработке. На зеркало чугунной втулки часто наносят тонкий слой хрома, а зеркало стальной — цементируют, азотируют или закаливают токами высокой частоты.
Крышки рабочих цилиндров служат для плотного их закрытия и образования над поршнем камер сгорания. Они изготовляются отдельно для каждого цилиндра или в виде блока (для быстроходных двигателей малой мощности). Материалом для изготовления крышек служит в основном высококачественный чугун, реже сталь и легкие сплавы. На крышке четырехтактного двигателя устанавливаются форсунка, впускной, выпускной, пусковой и предохранительный клапаны и стойки осей клапанных рычагов. Крышка двухтактного двигателя проще по конструкции, так как на ней размещаются лишь форсунка, пусковой и предохранительный клапаны. Исключение составляют двухтактные двигатели с прямоточной клапанной продувкой, на крышках которых дополнительно устанавливается выпускной клапан.
Внутри крышки имеются полости для циркуляции охлаждающей воды и отверстия для ее подвода и отвода. По форме крышки бывают квадратные, шести- или восьмиугольные, но наиболее часто применяются цилиндрические. К цилиндрам (или блокам) они крепятся шпильками, проходящими через специальные отверстия в крышках.
На рисунке показана крышка цилиндра двухтактного двигателя, в которой имеется отверстие 5 для форсунки, крепящейся при помощи двух шпилек. Справа расположены отверстие 6 для пускового клапана и отверстие (малого диаметра) для крепления патрубка пускового воздуха. Крышка к блоку цилиндров крепится шпильками, для прохода которых имеются восемь отверстий 9. Охлаждающая вода из зарубашечного пространства в полость крышки подводится по переливному патрубку 2 и отводится через сливное отверстие 3 в отводящий трубопровод. Для осмотра и очистки охлаждающей полости крышки предусмотрены четыре люка 7. Отверстие 8 служит для установки индикаторного крана с предохранительным клапаном. Между крышкой и цилиндровой втулкой устанавливается уплотнительная красно-медная прокладка 1. В отверстие 4 устанавливается водяной термометр.
В двухтактных двигателях большой мощности применяются составные крышки, что делается для значительного уменьшения напряжений, возникающих в них под действием больших тепловых нагрузок.
Из чего состоит поршневой двигатель внутреннего сгорания
Большинство автомобилей заставляет перемещаться поршневой двигатель внутреннего сгорания (сокращённо ДВС) с кривошипно-шатунным механизмом. Такая конструкция получила массовое распространение в силу малой стоимости и технологичности производства, сравнительно небольших габаритов и веса.
По виду применяемого топлива ДВС можно разделить на бензиновые и дизельные. Надо сказать, что бензиновые двигатели великолепно работают на газе. Такое деление непосредственно сказывается на конструкции двигателя.
Как устроен поршневой двигатель внутреннего сгорания
Основа его конструкции — блок цилиндров. Это корпус, отлитый из чугуна, алюминиевого или иногда магниевого сплава. Большинство механизмов и деталей других систем двигателя крепятся именно к блоку цилиндров, или располагаются внутри его.
Другая крупная деталь двигателя, это его головка. Она находится в верхней части блока цилиндров. В головке также располагаются детали систем двигателя.
Снизу к блоку цилиндра крепится поддон. Если эта деталь воспринимает нагрузки при работе двигателя, её часто называют поддоном картера, или картером.
Все системы двигателя
- кривошипно-шатунный механизм;
- механизм газораспределения;
- система питания;
- система охлаждения;
- система смазки;
- система зажигания;
- система управления двигателем.
Кривошипно-шатунный механизм состоит из поршня, гильзы цилиндра, шатуна и коленчатого вала.
Кривошипно-шатунный механизм:
1. Расширитель маслосъёмного кольца. 2. Кольцо поршневое маслосъёмное. 3. Кольцо компрессионное, третье. 4. Кольцо компрессионное, второе. 5. Кольцо компрессионное, верхнее. 6. Поршень. 7. Кольцо стопорное. 8. Палец поршневой. 9. Втулка шатуна. 10. Шатун. 11. Крышка шатуна. 12. Вкладыш нижней головки шатуна. 13. Болт крышки шатуна, короткий. 14. Болт крышки шатуна, длинный. 15. Шестерня ведущая. 16. Заглушка масляного канала шатунной шейки. 17. Вкладыш подшипника коленчатого вала, верхний. 18. Венец зубчатый. 19. Болты. 20. Маховик. 21. Штифты. 22. Болты. 23. Маслоотражатель, задний. 24. Крышка заднего подшипника коленчатого вала. 25. Штифты. 26. Полукольцо упорного подшипника. 27. Вкладыш подшипника коленчатого вала, нижний. 28. Противовес коленчатого вала. 29. Винт. 30. Крышка подшипника коленчатого вала. 31. Болт стяжной. 32. Болт крепления крышки подшипника. 33. Вал коленчатый. 34. Противовес, передний. 35. Маслоотрожатель, передний. 36. Гайка замковая. 37. Шкив. 38. Болты.
Поршень расположен внутри гильзы цилиндра. При помощи поршневого пальца он соединен с шатуном, нижняя головка которого крепится к шатунной шейке коленчатого вала. Гильза цилиндра представляет собой отверстие в блоке, или чугунную втулку, вставляемую в блок.
Гильза цилиндров с блоком
Гильза цилиндра сверху закрыта головкой. Коленчатый вал также крепится к блоку в нижней его части. Механизм преобразует прямолинейное движение поршня во вращательное движение коленчатого вала. То самое вращение, которое, в конечном счете, заставляет крутиться колеса автомобиля.
Газораспределительный механизм отвечает за подачу смеси паров топлива и воздуха в пространство над поршнем и удаление продуктов горения через клапаны, открываемые строго в определенный момент времени.
Система питания отвечает в первую очередь за приготовление горючей смеси нужного состава. Устройства системы хранят топливо, очищают его, смешивают с воздухом так, чтобы обеспечить приготовление смеси нужного состава и количества. Также система отвечает за удаление из двигателя продуктов горения топлива.
При работе двигателя образуется тепловая энергия в количестве большем, чем двигатель способен преобразовать в механическую энергию. К сожалению, так называемый термический коэффициент полезного действия, даже лучших образцов современных двигателей не превышает 40%. Поэтому приходится большое количество «лишней» теплоты рассеивать в окружающем пространстве. Именно этим и занимается система охлаждения, отводит тепло и поддерживает стабильную рабочую температуру двигателя.
Система смазки. Это как раз тот случай: «Не подмажешь, не поедешь». В двигателях внутреннего сгорания большое количество узлов трения и так называемых подшипников скольжения: есть отверстие, в нем вращается вал. Не будет смазки, от трения и перегрева узел выйдет из строя.
Система зажигания призвана поджечь, строго в определенный момент времени, смесь топлива и воздуха в пространстве над поршнем. У дизелей такой системы нет. Там топливо самовоспламеняется при определенных условиях.
Видео:
Система управления двигателем при помощи электронного блока управлении (ЭБУ) управляет системами двигателя и координирует их работу. В первую очередь это приготовление смеси нужного состава и своевременное поджигание её в цилиндрах двигателя.
Загрузка…ВЛИЯНИЕ ТЕМПЕРАТУРЫ НА ОТЛОЖЕНИЯ В ДВИГАТЕЛЕ
ВЛИЯНИЕ ТЕМПЕРАТУРЫ НА ОТЛОЖЕНИЯ В ДВИГАТЕЛЕ
Исследование отложений в автомобильных двигателях.
Одним из резервов повышения показателей эксплуатационной надежности ДВС является снижение отложений нагаров, лаков и осадков на поверхностях их деталей, контактирующих с моторным маслом. В основе их образования лежат процессы старения масел (окисление углеводородов, входящих в состав масляной основы). Определяющее влияние на процессы окисления масла в двигателях, на образование отложений и эффективность работы ДВС в целом оказывает тепловой режим теплонагруженных деталей.
Ключевые слова: температура, поршень, цилиндр, моторное масло, отложения, нагар, лак, работоспособность, надежность.
Отложения на поверхностях деталей ДВС делятся на три основных вида – нагары, лаки и осадки (шламы).
Нагар – твердые углеродистые вещества, откладывающиеся во время работы двигателя на поверхностях камеры сгорания (КС). При этом отложения нагаров, главным образом, зависят от температурных условий даже при аналогичном составе смеси и одинаковой конструкции деталей двигателей. Нагар оказывает весьма существенное влияние на протекание процесса сгорания топливовоздушной смеси в двигателе и на долговечность его работы. Почти все виды ненормального сгорания (детонационное сгорание, калильное воспламенение и прочие) сопровождаются тем или иным влиянием нагара на поверхностях деталей, образующих КС.
Лак – продукт изменения (окисления) тонких масляных пленок, растекающихся и покрывающих детали цилиндропоршневой группы (ЦПГ) двигателя под действием высоких температур. Наибольший вред для ДВС наносит лакообразование в зоне поршневых колец, вызывая процессы их закоксовывания (залегания с потерей подвижности). Лаки, откладываясь на поверхностях поршня, контактирующих с маслом, нарушают должную теплопередачу через поршень, ухудшают теплоотвод от него.
На количество осадков (шламов), образующихся в ДВС, решающее влияние оказывает качество моторного масла, температурный режим деталей, конструкционные особенности двигателя и условия эксплуатации. Отложения этого типа наиболее характерны для условий зимней эксплуатации, интенсифицируются при частых пусках и остановках двигателя.
Тепловое состояние ДВС оказывает определяющее влияние на процессы образования различных видов отложений, прочностные показатели материалов деталей, выходные эффективные показатели двигателей, процессы изнашивания поверхностей деталей. В этой связи необходимо знать пороговые значения температур деталей ЦПГ, по крайней мере, в характерных точках, превышение которых приводит к указанным ранее негативным по следствиям.
Температурное состояние деталей ЦПГ ДВС целесообразно анализировать по значениям температур в характерных точках, расположение которых показано на рис. 1 . Значения температур в данных точках следует учитывать при производстве, испытаниях и доводке двигателей для оптимизации конструкций деталей, при выборе моторных масел, при сравнении тепловых состояний различных двигателей, при решении целого ряда других технических проблем конструирования и эксплуатации ДВС.
Рис. 1. Характерные точки цилиндра и поршня ДВС при анализе их температурного состояния для дизельных (а) и бензиновых (б) двигателей
Эти значения имеют критические уровни:
1. Максимальное значение температур в точке 1 (в дизельных двигателях – на кромке КС, в бензиновых – в центре донышка поршня) не должно превышать 350С (кратковременно, 380С) для всех серийно применяемых в автомобильном двигателестроении алюминиевых сплавов, иначе происходит оплавление кромок КС в дизелях и, нередко, прогар поршней в бензиновых двигателях. Ко всему прочему высокие температуры огневой поверхности днища поршня вызывают образование нагаров высокой твердости на этой поверхности. В практике двигателестроения это критическое значение температуры удается повышать путем добавления в поршневой сплав кремния, бериллия, циркония, титана и других элементов.
Недопущение превышения критических значений температур в этой точке, равно как и в объемах деталей ДВС, обеспечивается также путем оптимизации их форм и правильной организацией охлаждения. Превышение температурами деталей ЦПГ двигателей допустимых значений обычно является основным сдерживающим фактором для форсирования их по мощности. По температурным уровням следует иметь определенный запас с учетом возможных экстремальных условий эксплуатации.
2. Критическое значение температур в точке 2 поршня – над верхним компрессионным кольцом (ВКК) – 250…260С (кратковременно, до 290С). При превышении этой величины все массовые моторные масла коксуются (происходит интенсивное лакообразование), что приводит к “залеганию” поршневых колец, то есть потере их подвижности, и в результате – к существенному уменьшению компрессии, увеличению расхода моторного масла и др.
3. Предельное максимальное значение температур в точке 3 поршня (точка расположена симметрично по сечению головки поршня на внутренней его стороне) – 220С. При более высоких температурах на внутренней поверхности поршня происходит интенсивное лакообразование. Лаковые отложения, в свою очередь, являются мощным тепловым барьером, препятствующим теплоотводу через масло. Это автоматически приводит к повышению температур во всем объеме поршня, а значит, и на поверхности зеркала цилиндра.
4. Максимально допустимое значение температур в точке 4 (расположена на поверхности цилиндра, напротив места остановки ВКК в ВМТ) – 200С. При его превышении моторное масло разжижается, что приводит к потере стабильности образования масляной пленки на зеркале цилиндра и «сухому» трению колец по зеркалу. Это вызывает интенсификацию молекулярно-механического изнашивания деталей ЦПГ. С другой стороны, известно, что пониженная температура стенок цилиндра (ниже точки росы отработавших газов) способствует ускорению их коррозионно-механического изнашивания [1,2]. Ухудшается также смесеобразование и уменьшается скорость сгорания топливовоздушной смеси, что снижает эффективность и экономичность работы двигателя, вызывая повышение токсичности отработавших газов. Также следует отметить, что при существенно заниженных температурах поршня и цилиндра сконденсированные водяные пары, проникающие в картерное масло, вызывают интенсивную коагуляцию примесей и гидролиз присадок с образованием осадков – «шламов». Эти осадки, загрязняя масляные каналы, сетки маслоотстойников, масляные фильтры, существенно нарушают нормальную работу смазочной системы.
На интенсивность протекания процессов образования отложений нагаров, лаков и осадков на поверхностях деталей ДВС существенно влияет старение моторных масел при их работе. Старение масел состоит в накоплении примесей (в том числе воды), изменении их физико-химических свойств и окислении углеводородов.
Изменение фракционного состава чистого залитого масла по мере работы двигателя вызывается в основном причинами, изменяющими состав его масляной основы и процентное соотношение присадок по отдельным составляющим (парафиновым, ароматическим, нафтеновым).
К ним относятся:
процессы термического разложения масла в зонах перегрева (например, в клапанных втулках, зонах верхних поршневых колец, на поверхностях верхних поясов зеркала цилиндров). Такие процессы приводят к окислению наиболее легких фракций масляной основы или даже их частичному выкипанию;
добавление к углеводородам основы неиспарившегося топлива, попадающего в начальные периоды пусков (или при резком увеличении подачи топлива в цилиндры для осуществления ускорения автомобиля) в маслосборник картера через зону поршневых уплотнений;
попадание в поддон картера или маслосборник двигателя воды, образующейся при сго-рании топлива в КС цилиндров.
Если система вентиляции картера действует достаточно эффективно, а стенки картера находятся в подогретом состоянии до 90-95°С, вода не конденсируется на них и удаляется в атмосферу системой вентиляции картера. Если температура стенок картера существенно понижена, то попавшая в масло вода будет принимать участие в процессах его окисления. Количество сконденсировавшейся воды при этом может быть весьма значительным [2]. Даже если считать, что только 2% газов могут прорваться через все компрессионные кольца цилиндра, то через картер двигателя с рабочим объемом 2-2,5 л за каждые 1000 км пробега будет прокачиваться по 2 кг воды. Допустим, что 95% воды удаляется системой вентиляции картера, то все равно после пробега в 5000 км на 4,0 л моторного масла будет приходиться около 0,5 л Н2О. Эта вода при работе двигателя преобразуется антиокислительной присадкой, содержащейся в моторном масле, в примеси – кокс и золу.
По указанным ранее причинам необходимо поддерживать при работе двигателя температуру стенок картера достаточно высокой, а в случае необходимости – применять системы смазки с сухим картером и отдельным масляным баком.
Следует отметить, что мероприятия, замедляющие процессы изменения состава масляной основы, существенно замедляют образование нагара, лака и осадков, а также снижают интенсивность изнашивания основных деталей автомобильных двигателей .
Фракционный и химический состав масел может изменяться в достаточно широких
пределах под влиянием различных факторов:
характера сырья, зависящего от месторождения, свойств нефтяной скважины;
Для предварительной оценки свойств нефтепродуктов применяют различные лабораторные методы: определение кривой разгонки, температур вспышки, помутнения и застывания, оценку окисляемости в средах с различной агрессивностью и т.п.
В основе старения автомобильного моторного масла лежат процессы окисления, разложения и полимеризации углеводородов, которые сопровождаются процессами загрязнения масла различными примесями (нагаром, пылью, металлическими частичками, водой, топливом и пр.). Процессы старения существенно изменяют физико-химические свойства масла, приводят к появлению в нѐм разнообразных продуктов окисления и износа, ухудшают его эксплуатационные качества. Различают следующие виды окисления масла в двигателях: в толстом слое – в поддоне картера или в масляном баке; в тонком слое -на поверхностях горячих металлических деталей; в туманообразном (капельном) состоянии – в картере, клапанной коробке и т.п. При этом окисление масла в толстом слое даѐт осадки в виде шлама, а в тонком слое – в виде лака.
Окисление углеводородов подчиняется теории перекисей А.Н. Баха и К.О. Энглера, дополненной П.Н. Черножуковым и С.Э. Крейном. Окисление углеводородов, в частности, в моторных маслах ДВС, может идти по двум основным направлениям, представленным на рис. 2, результаты окисления по которым различны. При этом результатом окисления по первому направлению являются кислые продукты (кислоты, оксикислоты, эстолиды и асфальтогенные кислоты), образующие осадки при пониженных температурах; результатом окисления по второму направлению являются нейтральные продукты (карбены, карбоиды, асфальтены и смолы), из которых образуются в различных пропорциях при повышенных температурах или лаки, или нагары.
Рис. 2. Пути окисления углеводородов в нефтяном продукте (например, в моторном масле для ДВС)
В процессах старения масла весьма значительна роль воды, попадающей в масло при конденсации ее паров из картерных газов или другими путями. В результате этого образуются эмульсии, которые впоследствии усиливают окислительную полимеризацию молекул масла. Взаимодействие оксикислот и других продуктов окисления масла с водомасляными эмульсиями вызывает усиленное образование осадков (шламов) в двигателе.
В свою очередь, образовавшиеся частички шлама, если они не будут нейтрализованы присадкой, служат центрами катализации и ускоряют разложение еще не окислившейся части масла. Если при этом не произвести своевременную замену моторного масла, процесс окисления будет происходить по типу цепной реакции с увеличивающейся скоростью, со всеми вытекающими отсюда последствиями.
Решающее влияние на образование нагаров, лаков и осадков на поверхностях деталей ДВС, контактирующих с моторным маслом, оказывает их тепловое состояние. В свою очередь, конструкционные особенности двигателей, условия их эксплуатации, режимы работы и т.д. определяют тепловое состояние двигателей и влияют, таким образом, на процессы образования отложений.
Не менее важное влияние на образование отложений в ДВС оказывают и характеристики применяемого моторного масла. Для каждого конкретного двигателя важно соответствие рекомендованного заводом-изготовителем масла температуре поверхностей деталей, контактирующих с ним.
В данной работе произведен анализ взаимосвязи температур поверхностей поршней двигателей ЗМЗ-402.10 и ЗМЗ-5234.10 и процессов образования на них отложений нагаров и лаков, а также произведена оценка осадкообразования на поверхностях картера и клапанной крышки двигателей при использовании рекомендованного заводом изготовителем моторного масла М 63/12Г1.
Для исследования зависимостей количественных характеристик отложений в двигателях от их теплового состояния и условий работы можно использовать различные методики, например, Л-4 (Англия), 344-Т (США), ПЗВ (СССР) и др. [2, 3]. В частности, по методике 344-Т, являющейся нормативным документом США, состояние «чистого» неизношенного двигателя оценивается в 0 баллов; состояние предельно изношенного и загрязненного двигателя в 10 баллов. Аналогичной методикой оценки лакообразования на поверхностях поршней является отечественная методика ПЗВ (авторы – К.К. Папок, А.П. Зарубин, А.В. Виппер), цветовая шкала которой имеет баллы от 0 (отсутствие лаковых отложений) до 6 (максимальные отложения лака). Для пересчета баллов шкалы ПЗВ в баллы методики 344-Т показания первой необходимо увеличить в полтора раза. Указанная методика аналогична отечественной методике отрицательной оценки отложений ВНИИ НП (10 балльная шкала).
Для экспериментальных исследований использовались по 10 двигателей ЗМЗ-402.10 и ЗМЗ-5234.10 [2]. Эксперименты по исследованию процессов образования отложений проводились совместно с лабораториями испытаний легковых и грузовых автомобилей УКЭР ГАЗ на моторных стендах. В процессе испытаний, кроме прочего, контролировались расходы воздуха и топлива, давление и температура отработавших газов, температура масла и охлаждающей жидкости. При этом на стендах выдерживались режимы: частота вращения коленчатого вала, соответствующая максимальной мощности (100% нагрузки), и, поочередно, в течение 3,5 часов – 70% нагрузки, 50% нагрузки, 40% нагрузки, 25% нагрузки и без нагрузки (при закрытых дроссельных заслонках), т.е. эксперименты проведены по нагрузочным характеристикам двигателей. При этом температура охлаждающей жидкости выдерживалась в интервале 90…92С, температура масла в главной масляной магистрали – 90…95С. После этого двигатели разбирались и производились необходимые замеры.
Предварительно были проведены исследования по изменению физико-химических параметров моторных масел при испытаниях двигателей ЗМЗ-402.10 в составе автомобилей ГАЗ-3110 на автополигоне УКЭР ГАЗ. При этом выдержаны условия: средняя техническая скорость 30…32 км/ч, температура окружающего воздуха 18…26С, пробег до 5000 км. В результате испытаний получено – при увеличении пробегов автомобилей (времени работы двигателей) увеличивалось количество механических примесей и воды в моторных маслах, его коксовое число и зольность, происходили прочие изменения, что представлено в табл. 1
Нагарообразование на поверхностях днищ поршней двигателей ЗМЗ-5234.10 характеризовалось данными, представленными на рис. 3 (для двигателей ЗМЗ-402.10 результаты подобны). Из анализа рисунка следует, что при повышении температур днищ поршней от 100 до 300С толщина (зона существования) нагара уменьшалась с 0,45…0,50 до 0,10…0,15 мм, что объясняется выжиганием нагара при повышении температуры поверхностей двигателей. Твердость же нагара повышалась с 0,5 до 4,0…4,5 баллов по причине спекания нагара при высоких температурах.
Рис. 3. Зависимости нагарообразования на поверхностях днищ поршней двигателей ЗМЗ-5234.10 от их температур:
а – толщина нагара; б – твердость нагара;
символами нанесены усредненные экспериментальные значения
Оценка величин отложений лаков на боковых поверхностях поршней и их внутренних (нерабочих) поверхностях производилась также по десятибалльной шкале, согласно методике 344-Т, используемой во всех ведущих научно-исследовательских учреждениях страны.
Данные по лакообразованию на поверхностях поршней двигателей представлены на рис. 4 (результаты по исследуемым маркам двигателей совпадают). Режимы испытаний указаны ранее и соответствуют режимам при исследованиях нагарообразования на деталях.
Из анализа рисунка следует, что лакообразование на поверхностях поршней двигателей однозначно увеличивается с увеличением температур их поверхностей. На интенсивность лакообразования влияет не только повышение температур поверхностей деталей, но и длительность ее действия, т.е. продолжительность работы двигателей [3]. При этом, однако, процессы лакообразования на рабочих (трущихся) поверхностях поршней существенно замедляются по сравнению с внутренними (нерабочими) поверхностями, вследствие стирания слоя лака в результате трения.
Рис. 4. Зависимости отложений лака на поверхностях поршней двигателей ЗМЗ-5234.10 от их температур:
а – внутренние поверхности; б – боковые поверхности; символами нанесены усредненные экспериментальные значения
Нагаро- и лакообразование на поверхностях деталей существенно интенсифицируется при применении масел групп «Б» и «В», что подтверждено рядом исследований, проведенных авторами на подобных и других типах автомобильных двигателей.
Планомерное увеличение отложений лаков на внутренних (нерабочих) поверхностях поршней вызывает уменьшение теплоотвода в картерное масло при увеличении наработки двигателей. Это вызывает, например, постепенное увеличение уровня теплового состояния двигателей по мере приближения наработки к смене масла при очередном ТО-2 автомобиля.
Образование осадков (шламов) из моторных масел происходит в наибольшей степени на поверхностях картера и клапанной крышки. Результаты исследований осадкообразования в двигателях ЗМЗ-5234.10 представлены на рис. 5 (для двигателей ЗМЗ-402.10 результаты подобны). Осадкообразование на поверхностях указанных ранее деталей оценивалось в зависимости от их температур, для измерения которых были смонтированы термопары (приварены конденсаторной сваркой): на поверхностях картера по 5 штук у каждого двигателя, на поверхностях клапанных крышек – по 3 штуки.
Как следует из рис. 5, при повышении температур поверхностей деталей двигателей осадкообразование на них уменьшается вследствие уменьшения содержания воды в картерном масле, что не противоречит результатам ранее проведенных экспериментов другими исследователями. Во всех двигателях осадкообразование на поверхностях деталей картера оказались больше, чем на поверхностях клапанных крышек.
На моторных маслах групп форсирования «Б» и «В» осадкообразование на деталях ДВС, контактирующих с моторным маслом, происходит интенсивнее, чем на маслах групп форсирования «Г», что подтверждено рядом исследований [1, 2, 3 и др.].
По сравнению с поверхностями поршней, отложения на зеркалах цилиндров следует считать незначительными. Далее, на рис. 6 приводятся данные по лакообразованию на зеркале цилиндра двигателей ЗМЗ-5234.10 при работе на маслах М-8В («автол») и М6з/12Г1, полученные также по методике 344-Т (для двигателей ЗМЗ-402.10 результаты подобны).
В данной работе исследования отложений на зеркалах цилиндров при эксплуатации двигателей на самых современных маслах не проводилось, однако, можно уверенно предположить, что для исследуемых двигателей они будут не больше, чем при их работе на менее качественных маслах.
Полученные результаты по взаимосвязи изменения температур основных деталей двигателей ЗМЗ-402.10 и ЗМЗ-5234.10 (поршней, цилиндров, клапанных крышек и масляных картеров) и количества отложений позволили выявить закономерности процессов образования нагаров, лаков и осадков на поверхностях указанных деталей. Для этого результаты аппроксимированы функциональными зависимостями методом наименьших квадратов и представлены на рис. 3-5. Полученные закономерности процессов образования отложений на поверхностях деталей автомобильных карбюраторных двигателей должны учитываться и использоваться конструкторами и инженерно-техническими работниками, занимающимися доводкой и эксплуатацией ДВС.
Двигатель автомобиля работает с наибольшей эффективностью лишь при определенных условиях. Оптимальный температурный режим теплонагруженных деталей является одним из таких условий и обеспечивает высокие технические характеристики двигателя с одновременным снижением износов, отложений и, следовательно, повышением показателей его надежности.
Оптимальное тепловое состояние ДВС характеризуется оптимальными температурами поверхностей их теплонагруженных деталей. Анализируя проведенные исследования процессов образования отложений на деталях исследуемых карбюраторных двигателей ЗМЗ и подобные исследования по бензиновым двигателям [1, 2, 3 и др.], можно с достаточной степенью точности определить интервалы оптимальных и опасных температур поверхностей деталей данного класса двигателей. Полученная информация представлена в табл. 2.
При температурах деталей двигателей в опасной высокотемпературной зоне существенно увеличивается твердость нагара на деталях КС цилиндра, что вызывает процессы калильного зажигания топливовоздушных смесей, количество лаковых отложений на поверхностях поршней и цилиндров, а значит, нарушается нормальный тепловой баланс. Рис. 7.
При температурах деталей двигателей в опасной низкотемпературной зоне увеличивается толщина нагара на поверхностях деталей, образующих КС, что приводит к возникновению детонационного сгорания топливовоздушных смесей, а также при низких температурах поверхностей деталей двигателей на них увеличивается количество осадков из моторных масел. Все это нарушает нормальную работу двигателей. В свою очередь отложения приводят к перераспределению тепловых потоков, проходящих через поршни, и повышению температур поршней в критических точках – в центре огневой поверхности днища поршня и в канавке ВКК. Температурное поле поршня двигателя ЗМЗ-5234.10 с учетом отложений нагаров и лаков на его поверхностях представлено на рис. 7.
Задача теплопроводности методом конечных элементов решалась с ГУ 1-рода, полученными при термометрировании поршня на режиме номинальной мощности при стендовых испытаниях двигателя. Термоэлектрические эксперименты проводились с тем же поршнем, для которого предварительно выполнены исследования температурного состояния без учета отложений. Эксперименты осуществлялись при идентичных условиях. Предварительно двигатель работал на стенде более 80 часов, после чего наступает стабилизация нагаров и лаков. В результате, температура в центре днища поршня повысилась на 24°С, в зоне канавки ВКК – на 26°С в сравнении с моделью поршня без учета отложений. Значение температуры поверхности поршня над ВКК 238°С входит в опасную высокотемпературную зону (табл. 2). Близко к опасной высокотемпературной зоне и значение температуры в центре днища поршня.
На этапе проектирования и доводки двигателей влияние отложений нагаров на тепловоспринимающих поверхностях поршней и лаков на их поверхностях, контактирующих с моторным маслом, учитывается крайне редко. Это обстоятельство в совокупности с эксплуатацией двигателей в составе АТС при повышенных тепловых нагрузках увеличивает вероятность отказов – прогары поршней, закоксовывание поршневых колец и т.д.
Н.А Кузьмин, В.В. Зеленцов, И.О. Донато
Нижегородский государственный технический университет им. Р.Е. Алексеева, Управление автомагистрали “Москва — Н.Новгород»
Основные части двигателя внутреннего сгорания
Сегодня мы узнаем об основных частях двигателя или, точнее, двигателя внутреннего сгорания. Двигатель внутреннего сгорания — это тепловой двигатель, в котором сгорание (сжигание топлива) происходит внутри цилиндра двигателя. После сжигания топлива возникает высокая температура и сила давления. Эта сила давления используется для перемещения транспортного средства или вращения колес с помощью какого-либо механизма. В двигателе многие части работают вместе для достижения цели преобразования химической энергии топлива в механическую.Эти части скреплены болтами, и комбинация всех этих частей известна как двигатель. Сегодня я собираюсь рассказать вам об этих частях и о том, как они работают, чтобы вы могли узнать основы автомобильного двигателя.
1. Блок цилиндров
Цилиндр является основным корпусом двигателя внутреннего сгорания. Цилиндр — это часть, в которой происходит забор топлива, сжатие топлива и сжигание топлива. Основная функция цилиндра — направлять поршень. Он находится в прямом контакте с продуктами сгорания, поэтому его необходимо охлаждать.Для охлаждения цилиндра на внешней стороне цилиндра расположена водяная рубашка (для жидкостного охлаждения, используемого в большинстве автомобилей) или ребро (для охлаждения воздуха, используемого в большинстве мотоциклов). На верхнем конце цилиндра, головка цилиндра и на нижнем конце картера закреплены болтами. В верхней части цилиндра находится камера сгорания, в которой горит топливо. Чтобы справиться со всем этим давлением и температурой, возникающими при сгорании топлива, материал цилиндра должен иметь высокую прочность на сжатие. Таким образом, он сделан из высококачественного чугуна.Его изготавливают методом литья и обычно отливают в виде цельного куска.
2. Головка блока цилиндров
Верхний торец цилиндра двигателя закрыт съемной головкой блока цилиндров. На головке блока цилиндров есть два отверстия, одно для впуска топлива, а другое для выпуска. Как впускной, так и выпускной порты закрыты двумя клапанами, известными как впускной и выпускной клапан. Впускной клапан, выпускной клапан, свеча зажигания, форсунка и т. Д. Прикручены к головке блока цилиндров.Основная функция головки блока цилиндров — герметизировать блок цилиндров и не допускать попадания и выхода газов на двигатель с клапаном крышки головки блока цилиндров. Головка блока цилиндров обычно изготавливается из чугуна или алюминия. Его изготавливают методом литья или ковки и, как правило, цельным.
3. Поршень
Поршень установлен на каждом цилиндре как поверхность для приема давления газа и передачи усилия на шатун. Это главный двигатель в двигателе. Основная функция поршня — плотно прилегать к цилиндру через отверстие и свободно скользить внутри цилиндра.Поршень должен быть легким и достаточно прочным, чтобы выдерживать давление газа, возникающее при сгорании топлива. Таким образом, поршень изготовлен из алюминиевого сплава, а иногда и из чугуна, потому что поршень из легкого сплава расширяется больше, чем чугун, поэтому им требуется больше зазоров до отверстия.
4. Поршневые кольца
Поршень должен достаточно свободно входить в цилиндр, чтобы он мог свободно перемещаться внутри цилиндра. Если поршень установлен слишком плотно, он будет расширяться при нагревании и может плотно прилипать к цилиндру, а если он слишком ослаблен, это приведет к утечке давления пара.Чтобы обеспечить хорошее уплотнение и меньшее сопротивление трению между поршнем и цилиндром, поршни оснащены поршневыми кольцами. Эти кольца вставляются в пазы, прорезанные в поршне. Они разделены на одном конце, поэтому они могут расширяться или скользить по концу поршня. Небольшой двухтактный двигатель имеет два поршневых кольца для обеспечения хорошего уплотнения, но четырехтактный двигатель имеет дополнительное кольцо, известное как масляное кольцо. Поршневые кольца изготовлены из мелкозернистого чугуна и высокоэластичного материала, на который не влияет рабочая температура.Иногда его изготавливают из легированной пружинной стали.
5. Шатун
Шатун соединяет поршень с коленчатым валом и передает движение и усилие поршня на коленчатый вал. Он преобразует возвратно-поступательное движение поршня во вращательное движение коленчатого вала. Есть два конца шатуна; один известен как большой конец, а другой как малый конец. Большой конец соединен с коленчатым валом, а малый конец соединен с поршнем с помощью поршневого пальца.Шатуны изготовлены из никелевых, хромовых и хромованадиевых сталей. Для небольших двигателей материалом может быть алюминий.
6. Коленчатый вал
Коленчатый вал двигателя внутреннего сгорания воспринимает усилие или тягу, прилагаемую поршнем к шатуну, и преобразует возвратно-поступательное движение поршня во вращательное движение коленчатого вала. Коленчатый вал устанавливается в подшипник, поэтому он может свободно вращаться. Форма и размер коленчатого вала зависят от количества и расположения цилиндров.Обычно его изготавливают путем ковки стали, но некоторые производители используют специальные типы чугуна, такие как отливки из шаровидного графита или никелевых сплавов, которые дешевле в производстве и имеют хороший срок службы.
7. Подшипник двигателя
Везде, где в двигателе есть вращательное действие, нужны подшипники. Подшипники используются для поддержки движущихся частей. Коленчатый вал опирается на подшипник. Шатун шатуна прикреплен к шатуну на кривошипе коленчатого вала подшипником.Поршневой палец на малом конце используется для прикрепления штока к поршню и также находится в подшипниках. Основная функция подшипников — уменьшить трение между этими движущимися частями. В двигателе внутреннего сгорания используются подшипники скольжения и качения. Подшипник скольжения, который иногда называют втулкой, используется для крепления шатуна к поршню и коленчатому валу. Они разделены, чтобы их можно было установить в двигатель. Подшипник качения и шарикоподшипник
используется для поддержки коленчатого вала, поэтому он может свободно вращаться.Типичная половина подшипника
изготовлена из стали или бронзы, на которую нанесена футеровка из относительно мягкого материала подшипника
.
8. Картер двигателя
Главный корпус двигателя, к которому прикреплен цилиндр и который содержит коленчатый вал и подшипник коленчатого вала, называется картером. Он также служит системой смазки и иногда его называют масляным картером. В него помещается все масло для смазки.
9.Клапаны
Для управления впуском и выпуском двигателя внутреннего сгорания используются клапаны. Количество клапанов в двигателе зависит от количества цилиндров. Для каждого цилиндра используются два клапана: один для впуска топливовоздушной смеси внутрь цилиндра, а другой — для выпуска дымовых газов. Клапаны устанавливаются в порт на головке блока цилиндров с помощью сильной пружины. Этой весной держите их закрытыми. Оба клапана обычно открываются внутрь.
10.Свеча зажигания
Применяется в двигателях с искровым зажиганием. Основная функция свечи зажигания — проводить высокий потенциал от системы зажигания в камеру сгорания для воспламенения топливной смеси сжатого воздуха. Он установлен на головке блока цилиндров. Свеча зажигания состоит из металлической оболочки с двумя электродами, изолированными друг от друга воздушным зазором. При подаче высокого потенциала тока на свечу зажигания она отскакивает от питающего электрода и дает необходимую искру.
11.Форсунка
Форсунка обычно используется в двигателях с воспламенением от сжатия. Он распыляет топливо в камеру сгорания в конце такта сжатия. Он установлен на головке блока цилиндров.
12. Коллектор
Основная функция коллектора — подавать воздушно-топливную смесь и собирать выхлопные газы в равной степени со всех цилиндров. В двигателе внутреннего сгорания используются два коллектора: один для впуска, а другой для выпуска. Обычно они изготавливаются из алюминиевого сплава.
13. Распределительный вал
Распределительный вал используется в двигателе внутреннего сгорания для управления открытием и закрытием клапанов в нужное время. Для обеспечения надлежащей выходной мощности двигателя впускной клапан должен открываться в конце такта выпуска и закрываться в конце такта впуска. Таким образом, для регулирования времени используется кулачок овальной формы, который оказывает давление на клапан для открытия и отпускания для закрытия. Он приводится в движение зубчатым ремнем, который приводится в движение коленчатым валом. Он размещается вверху или внизу цилиндра.
14. Поршневой палец или поршневой палец
Это параллельные шпиндели из закаленной стали, проходящие через бобышки поршня и малые концевые втулки или проушины для обеспечения возможности поворота шатунов. Он соединяет поршень с шатуном. Он сделан полым для легкости.
15. Толкатель
Толкатель используется, когда распределительный вал расположен в нижнем конце цилиндра.
Он передает движение распределительного вала к клапанам, расположенным на головке блока цилиндров.
16. Маховик
Маховик закреплен на коленчатом валу. Основная функция маховика — вращать вал во время подготовительного хода. Это также делает вращение коленчатого вала более равномерным.
Это все об основных частях двигателя. Если у вас есть какие-либо вопросы относительно этой статьи, задавайте их в комментариях. Если вам понравилась эта статья, не забудьте поделиться ею в социальной сети. Подпишитесь на наш сайт, чтобы получить более информативную статью.
Детали двигателя внутреннего сгорания
Читать и знать, как работает двигатель внутреннего сгорания — это нормально, но незнание его компонентов делает его бесполезным.Комбинированный компонент двигателя транспортного средства заставляет магию работать под капотом, что ж, некоторым людям это кажется волшебством.
Автомобильный двигатель состоит из различных компонентов разного размера, выполняющих различные функции. Данная статья ориентирована на распространенный тип автомобильного двигателя « двигатель внутреннего сгорания ».
Современная версия двигателя сочетает в себе как механические, так и электрические компоненты. Прочтите важные статьи о двигателях внутреннего сгорания…
Подробнее: Типы автомобильных двигателей
Автомобильные двигатели заключены в герметичный упругий металлический цилиндр.Он содержит до шестнадцати цилиндров, но большинство современных автомобилей имеют от четырех до восьми цилиндров. Читая мои предыдущие статьи, вы поймете, что функция цилиндра — открываться и закрываться в определенное время, позволяя топливу и воздуху попадать в камеру сгорания и выпускать выхлопные газы. ну, это уже объясненное содержание. Проверьте это по ссылке выше!
В этой статье я распространил список основных частей двигателя внутреннего сгорания, их схемы и их функции.
Подробнее: Понимание работы автомобильного мозга
Компоненты двигателя внутреннего сгорания:
Ниже приведены общие детали двигателя внутреннего сгорания:
1. Цилиндр :Эти детали автомобильного двигателя расположены в блоке двигателя, также известном как блок цилиндров. Он содержит подкладку или рукава вокруг него. Этот лайнер изнашивается во время работы и может быть легко заменен. В цилиндрах есть часть или пространство для поршня, чтобы двигаться вверх и вниз, заставляя происходить сгорание.
Цилиндрыотличаются диаметром и ходом. Отверстие — это внутренний диаметр, а ход — это эффективная длина поршня, совершающего возвратно-поступательное движение, то есть движение поршня от ВМТ к НМТ, они являются самой верхней и самой нижней точками хода.
В блоке цилиндров также есть пустоты вокруг и между отдельными цилиндрами, эти полые части известны как рубашки. Он позволяет охлаждающей жидкости поступать и циркулировать, обеспечивая эффективное рассеивание тепла в двигателях с жидкостным охлаждением.
2. Поршень :Поршень представляет собой цилиндрическую часть, которая движется вверх и вниз в цилиндре, обеспечивая полный цикл сгорания (впуск, сжатие, сгорание, выпуск). Посмотрите, как этот процесс работает ниже.
Диаметр поршня немного меньше диаметра цилиндра, чтобы избежать быстрого износа поверхности поршня. В круглые выемки на поверхностях поршня вставлены три кольца, известные как поршневые кольца. Эти кольца изготовлены из алюминия и имеют прямой контакт с гильзой цилиндра, что предотвращает износ поршня.
Два первых кольца представляют собой компрессионные кольца, у него скошена внешняя часть, что способствует возникновению эффекта продувки (предотвращение попадания отработанных газов внутри камеры сгорания в картер). Третье кольцо известно как масляное кольцо, оно предотвращает попадание масла в камеру сгорания и обеспечивает правильное распределение масла по стенкам цилиндров.
3. Коленчатый вал :Эти детали двигателя помогают преобразовывать скользящее движение поршня во вращательное движение через шатун.Он расположен под блоком цилиндров внутри кожуха, называемого картером. Коленчатый вал имеет выступы, загнутые и смещенные относительно оси вала. В многоцилиндровом двигателе каждый цилиндр снабжен собственной шатунной шейкой, предназначенной для крепления поршня с помощью шатуна.
Часть коленчатого вала, называемая опорным подшипником кривошипа, известна как шатун, имеющий подшипник скольжения. Другая его часть называлась противовесами. Он предназначен для противодействия колебаниям растяжения, испытываемым коленчатым валом из-за возвратно-поступательного дисбаланса движущегося поршня во время процесса сгорания.Баланс кривошипа либо прикреплен болтами к корпусу кривошипа, либо является неотъемлемой частью.
Коленчатые валы производятся как по частям, так и в сборе. Цельная конструкция более предпочтительна, поскольку она не оставляет места для вибрации и обеспечивает лучший поток волокна и хорошую способность выдерживать нагрузки.
Наконец, коленчатые валы обычно изготавливают из стали путем ковки вальцом или из пластичной стали путем литья. цельные коленчатые валы изготавливаются из жаропрочных углеродистых сталей.Некоторые другие стали, такие как микролегированные стали с ванадием, также используются из-за более высокой прочности, которую они могут обеспечить без термической обработки.
4. Шатун :Эти детали двигателя предназначены для соединения поршня с коленчатым валом. Как упоминалось ранее, он преобразует поступательное движение поршня во вращательное движение кривошипа. Одна из его концевых частей прикреплена к поршню через поршневой палец, также известный как поршневой палец и палец для запястья. Другой конец прикреплен к шейке шатунной шейки с помощью болтов для удержания верхней и нижней крышек подшипников, называемых шатуном.
Подшипник выполнен в виде двух полукорпусов, помещенных в шейку кривошипа шатуном шатуна. Оба конца не закреплены жестко, чтобы поворачиваться на угол. Следовательно, оба конца находятся в непрерывном движении и испытывают огромную нагрузку от давления поршня.
Шатун обычно изготавливается из кованой стали, а иногда и из алюминиевого сплава, когда приоритетным является легкий вес и способность поглощать сильные удары. Шатун изготовлен с высокой точностью, так как это чувствительная деталь, склонная к выходу из строя.
5. Головка блока цилиндров :Эти детали двигателя служат крышкой для блока цилиндров, клапана, коромысел и элемента зажигания. Он прикручен к блоку цилиндров с прокладкой головки блока цилиндров между ними.
Головка блока цилиндров изготовлена из чугуна, а иногда и из алюминиевого сплава, когда требуется легкая деталь и поскольку она проводит тепло быстрее, чем чугун.
В двигателе с верхним распределительным валом распределительный вал размещен в головке при отсутствии толкателя для клапанного механизма.Некоторые другие части, такие как впускные, выпускные отверстия и камера сгорания, также имеют пространство под цилиндром, что делает их одним целым компонентом двигателя.
6. Распределительный вал :Этот компонент двигателя внутреннего сгорания представляет собой вал, на котором установлен кулачок. его функции — управлять клапанами непосредственно, сидя над ними или через коромысло и толкатель. Время газораспределения определяется размером распредвала. То есть открытие и закрытие клапанов регулируется распределительным валом, который установлен на коленчатом валу либо непосредственно через редуктор, либо косвенно через шкив и ремень привода ГРМ.
Распределительный вал, соединенный с кривошипом шестерней, требовал толкателя и толкателя вместе с коромыслами. Распределительный вал обычно изготавливается из отливок из закаленного чугуна и стальной заготовки, используемой для изготовления высококачественных. Охлажденный чугун обеспечивает большую износостойкость и твердость поверхности.
7. Клапаны :Клапаны, известные как тарельчатые клапаны в двигателях внутреннего сгорания. Он состоит из длинного тонкого круглого стержня, называемого штоком клапана, и плоского круглого диска, называемого головкой клапана, который сужается вдоль тонкого стержня.Функция клапана состоит в том, чтобы включить клапан для свежего всасывания топлива и воздуха и выпуска отработанных газов (выхлопа). Открытие и закрытие клапана вызывается скользящим движением распределительного вала и связанных с ним рычагов.
Клапаны двигателя изготовлены из стальных сплавов, наполненных натрием для увеличения теплоотдачи. Наконец, клапаны двухсекционные; впускной / впускной клапан, который позволяет свежему заряду поступать в камеру при открытии, а выпускной / выпускной клапан позволяет выходить выхлопным газам.
8. Коромысло :Эта деталь двигателя внутреннего сгорания играет важную роль, поскольку она передает вращательное движение кулачка или коленчатого вала через толкатель / фиксатор и преобразует его в линейное движение штока клапана, помогая прижать головку клапана
Головка коромысла изготовлена из стальных штамповок для двигателей легкой и средней мощности, тогда как головка коромысла тяжелого дизельного двигателя изготовлена из чугуна и кованой углеродистой стали, так как она обеспечивает большую прочность и жесткость.Коромысла колеблются вокруг неподвижного стержня шарнира в головке блока цилиндров.
9. Картер двигателя :Эти компоненты двигателя внутреннего сгорания расположены под блоком цилиндров, содержащим подшипники, вращающие кривошип. Этот коренной подшипник представляет собой подшипник скольжения с достаточной подачей масла. Четырехцилиндровые рядные бензиновые двигатели содержат три подшипника в картере, по одному на каждом конце и один посередине, в то время как дизельные двигатели имеют пять основных подшипников, по одному на каждом конце и по одному между каждым цилиндром.
Картер сделан из чугуна и алюминия, из того же материала, что и блок цилиндров. Картер двигателя служит многим целям двигателя, поскольку помогает защитить его внутренний механизм от пыли, грязи и некоторых других материалов. Он также служит корпусом, в котором заключены коленчатый вал и шатун, удерживая масло и воздух.
10. Масляный насос и поддон :Масляный насос перекачивает масло в различные части двигателя для надлежащей смазки, очистки и охлаждения.Масляный насос в двигателе приводится в действие шестерней коленчатого вала. Масло находится под давлением к различным частям компонентов двигателя, что помогает смазывать и охлаждать систему.
Масляный поддон служит резервуаром, в котором хранится масло. Масло поднимается масляным насосом из поддона через сетку из проволочной сетки, которая предотвращает попадание мусора и грязи в двигатель. Масляный фильтр и маслоохладитель пропускают масло перед его распределением по деталям двигателя. После выполнения своей работы масло возвращается в масляный поддон.
Прочие компоненты автомобильного двигателя — электрические, о которых пойдет речь в другой статье. В электрическую часть двигателя входят:
Мы надеемся, что вам понравился этот пост «Компоненты двигателя внутреннего сгорания», и вы получили удовольствие от чтения. Если да, то поделитесь этим постом со своими друзьями и учениками в социальных сетях. Спасибо!
Основные компоненты двигателя внутреннего сгорания и их функции
Несмотря на то, что существуют разные типы двигателей внутреннего сгорания, и каждый двигатель состоит из сотен компонентов, есть некоторые основные компоненты, которые присутствуют почти во всех двигателях.Те, кто изучает двигатели IC, должны знать этот базовый компонент и часто используемую терминологию в двигателях IC.
На рисунке показан поперечный разрез двигателя SI, различные компоненты и его функции описаны ниже.
🔗Разница между SI Engine и CI Engine
🔗Сравнение двухтактных и четырехтактных двигателей
Блок цилиндров
6-цилиндровый блок BMW |
Блок цилиндров — это основной корпус двигателя.Это основная несущая конструкция, которая удерживает вместе другие компоненты и обеспечивает точки крепления. Блок цилиндров изготавливается методом литья. Используемый материал может быть железом или алюминием. Для многоцилиндрового двигателя блок цилиндров выполнен как единое целое. Головка блока цилиндров плотно закреплена на верхней части блока цилиндров болтом и шпильками. Эти две части снабжены соответствующей системой охлаждения (водяная рубашка, охлаждающие ребра). Прокладка цилиндра используется для уплотнения всех сопрягаемых поверхностей, в том числе между головкой цилиндров и блоком цилиндров.Материал прокладки может быть резиной, бумагой, пробкой или металлом. Нижняя часть блока цилиндров называется картером.
Цилиндр
Цилиндр — это пространство или цилиндрический сосуд, поддерживаемый блоком цилиндров, в котором поршень совершает возвратно-поступательное движение. В процессе работы двигателя объем внутри цилиндра заполняется рабочей жидкостью и подвергается различным термодинамическим процессам.
Поршень
Поршень — это трубчатый элемент, который устанавливается в цилиндр двигателя.Его движение ограничено одним измерением, он совершает возвратно-поступательное движение внутри цилиндра. Поршневые кольца и смазочные материалы, обеспечивающие посадку, являются газонепроницаемыми. Он также действует как связующее звено в передаче сил газа во вращательное движение выходного вала.
Кольца поршневые
На поршне предусмотрены поршневые кольца, обеспечивающие газонепроницаемое уплотнение между поршнем и стенкой цилиндра. Он вставляется в прорези на внешнем диаметре поршня, чтобы предотвратить утечку продуктов сгорания во время работы двигателя.
Камера сгорания
Камера сгорания — это пространство, заключенное между цилиндром и верхней частью поршня во время процесса сгорания. В камере сгорания происходит сгорание топлива, выделение тепловой энергии и повышение давления.
Шатуны
Это металлический стержень, который соединяет поршень и коленчатый вал. Он передает усилие от поршня на коленчатый вал. Малый конец шатуна соединял поршень с поршневым пальцем, а большой конец — с коленчатым валом с помощью шатунной шейки.
Коленчатый вал
Коленчатый вал — это компонент, который заключен в картер и преобразует возвратно-поступательное движение поршня во вращательное движение выходного вала. Подшипники используются для поддержки вала трещины, уменьшения трения и позволяют ему свободно вращаться при различных условиях нагрузки. На них предусмотрены пара кривошипов и балансировочные грузы для статической и динамической балансировки вращающейся системы.
Свеча зажигания
Это компонент двигателя с искровым зажиганием, инициирующий процесс сгорания.Обычно он находится на головке блока цилиндров.
Уплотнения
Уплотнения двигателя расположены на конце вала, который выходит за пределы блока цилиндров. Уплотнения защищают подшипник и предотвращают утечку газа и масла.
Кулачки и распредвал
Кулачки и распредвал — это части двигателя, которые контролируют открытие и закрытие впускных и выпускных клапанов. Кулачок и распределительный вал приводятся в движение коленчатым валом с помощью синхронизирующих шестерен, и они сконструированы таким образом, чтобы открывать клапаны в правильное время и держать их открытыми в течение необходимого времени.Распредвалы также используются для привода системы зажигания.
Впускные и выпускные клапаны
Это клапаны, предусмотренные в головке блока цилиндров для регулирования потока рабочей жидкости в цилиндр и удаления продуктов сгорания в атмосферу.
Впускной коллектор и выпускной коллектор
Трубы, которые соединяют впускную систему с впускным клапаном, известны как впускной коллектор. Воздух, топливовоздушная смесь втягивается в цилиндр через впускной коллектор.
Выпускной коллектор — это патрубок, соединяющий выхлопную систему с выпускными клапанами. Продукты сгорания, такие как CO, NOx и т. Д., Попадают в атмосферу через выпускной коллектор.
Маховик
Чтение: Что такое маховик? функция, приложения и уравнение для накопленной энергии
Крутящий момент на коленчатом валу колеблется в течение одного цикла сгорания и вызывает колебания угловой скорости вала. Маховик — это инерционная масса, прикрепленная к выходному валу, чтобы минимизировать эти колебания и добиться равномерного крутящего момента.
ДВИГАТЕЛЬ IC: КОМПОНЕНТЫ И ИХ ФУНКЦИИ, ВИДЫ И ТЕРМИНОЛОГИЯ
Это двигатель, в котором сгорание топлива происходит внутри двигателя. Когда топливо сгорает внутри цилиндра двигателя, оно создает высокую температуру и давление. Эта сила высокого давления действует на поршень (устройство, которое свободно перемещается внутри цилиндра и передает силу давления на кривошип с помощью шатуна), который используется для вращения колес транспортного средства. В этих двигателях мы можем использовать только газы и топливо с высокой летучестью, такое как бензин, дизельное топливо.Эти двигатели обычно используются в автомобильной промышленности, производстве электроэнергии и т. Д.
Преимущества I.C. двигатель
В целом имеет высокий КПД по сравнению с двигателем E.C.
Эти двигатели компактны и занимают меньше места.
Начальная стоимость I.C. двигатель ниже, чем двигатель E.C.
Этот двигатель легко запускается в холодную погоду, так как в нем используется высоколетучее топливо.
КОМПОНЕНТЫ ДВИГАТЕЛЯ IC
1. Блок цилиндров
Цилиндр является основным корпусом двигателя внутреннего сгорания.Цилиндр — это часть, в которой происходит забор топлива, сжатие топлива и сжигание топлива. Основная функция цилиндра — направлять поршень. Он находится в прямом контакте с продуктами сгорания, поэтому его необходимо охлаждать. Для охлаждения цилиндра на внешней стороне цилиндра расположена водяная рубашка (для жидкостного охлаждения, используемого в большинстве автомобилей) или ребро (для охлаждения воздуха, используемого в большинстве мотоциклов). На верхнем конце цилиндра, головка цилиндра и на нижнем конце картера закреплены болтами. Верхняя часть цилиндра представляет собой камеру сгорания, в которой горит топливо.Чтобы справиться со всем этим давлением и температурой, возникающими при сгорании топлива, материал цилиндра должен иметь высокую прочность на сжатие. Таким образом, он сделан из высококачественного чугуна. Его изготавливают методом литья и обычно отливают в виде цельного куска.
2. Головка блока цилиндров
Верхний торец цилиндра двигателя закрыт съемной головкой блока цилиндров. На головке блока цилиндров есть два отверстия, одно для впуска топлива, а другое для выпуска. Как впускной, так и выпускной порты закрыты двумя клапанами, известными как впускной и выпускной клапан.Впускной клапан, выпускной клапан, свеча зажигания, форсунка и т. Д. Прикручены к головке блока цилиндров. Основная функция головки блока цилиндров — герметизировать блок цилиндров и не допускать попадания и выхода газов на двигатель с клапаном крышки головки блока цилиндров. Головка блока цилиндров обычно изготавливается из чугуна или алюминия. Его изготавливают методом литья или ковки и, как правило, цельным.
3. Поршень
Поршень установлен на каждом цилиндре как поверхность для приема давления газа и передачи усилия на шатун. Это главный двигатель в двигателе.Основная функция поршня — плотно прилегать к цилиндру через отверстие и свободно скользить внутри цилиндра. Поршень должен быть легким и достаточно прочным, чтобы выдерживать давление газа, возникающее при сгорании топлива. Таким образом, поршень изготовлен из алюминиевого сплава, а иногда и из чугуна, потому что поршень из легкого сплава расширяется больше, чем чугун, поэтому им требуется больше зазоров до отверстия.
4. Поршневые кольца
Поршень должен свободно входить в цилиндр, чтобы он мог свободно перемещаться внутри цилиндра.Если поршень установлен слишком плотно, он будет расширяться при нагревании и может плотно прилипать к цилиндру, а если он слишком ослаблен, это приведет к утечке давления пара. Чтобы обеспечить хорошее уплотнение и меньшее сопротивление трению между поршнем и цилиндром, поршни оснащены поршневыми кольцами. Эти кольца вставляются в пазы, прорезанные в поршне. Они разделены на одном конце, поэтому они могут расширяться или скользить по концу поршня. Небольшой двухтактный двигатель имеет два поршневых кольца для обеспечения хорошего уплотнения, но четырехтактный двигатель имеет дополнительное кольцо, известное как масляное кольцо.Поршневые кольца изготовлены из мелкозернистого чугуна и высокоэластичного материала, на который не влияет рабочая температура. Иногда его изготавливают из легированной пружинной стали.
5. Шатун
Шатун соединяет поршень с коленчатым валом и передает движение и усилие поршня на коленчатый вал. Он преобразует возвратно-поступательное движение поршня во вращательное движение коленчатого вала. Есть два конца шатуна; один известен как большой конец, а другой как малый конец. Большой конец соединен с коленчатым валом, а малый конец соединен с поршнем с помощью поршневого пальца.Шатуны изготовлены из никелевых, хромовых и хромованадиевых сталей. Для небольших двигателей материалом может быть алюминий.
6. Коленчатый вал
Коленчатый вал двигателя внутреннего сгорания воспринимает усилие или тягу, прилагаемую поршнем к шатуну, и преобразует возвратно-поступательное движение поршня во вращательное движение коленчатого вала. Коленчатый вал устанавливается в подшипник, поэтому он может свободно вращаться. Форма и размер коленчатого вала зависят от количества и расположения цилиндров.Обычно его изготавливают путем ковки стали, но некоторые производители используют специальные типы чугуна, такие как отливки из шаровидного графита или никелевых сплавов, которые дешевле в производстве и имеют хороший срок службы.
7. Подшипник двигателя
Везде, где в двигателе есть вращательное действие, нужны подшипники. Подшипники используются для поддержки движущихся частей. Коленчатый вал опирается на подшипник. Шатун шатуна прикреплен к шатуну на кривошипе коленчатого вала подшипником. Поршневой палец на малом конце используется для прикрепления штока к поршню и также находится в подшипниках.Основная функция подшипников — уменьшить трение между этими движущимися частями. В двигателе внутреннего сгорания используются подшипники скольжения и качения. Подшипник скольжения, который иногда называют втулкой, используется для крепления шатуна к поршню и коленчатому валу. Они разделены, чтобы их можно было установить в двигатель. Подшипник качения и шарикоподшипник используются для поддержки коленчатого вала, поэтому он может свободно вращаться. Типичная половина подшипника изготовлена из стали или бронзы, на которую нанесена футеровка из относительно мягкого материала подшипника.
8. Картер двигателя
Главный корпус двигателя, к которому прикреплен цилиндр и который содержит коленчатый вал и подшипник коленчатого вала, называется картером. Он также служит системой смазки и иногда его называют масляным картером. В него помещается все масло для смазки.
9. Клапаны
Для управления впуском и выпуском двигателя внутреннего сгорания используются клапаны. Количество клапанов в двигателе зависит от количества цилиндров. Для каждого цилиндра используются два клапана: один для впуска топливовоздушной смеси внутрь цилиндра, а другой — для выпуска дымовых газов.Клапаны устанавливаются в порт на головке блока цилиндров с помощью сильной пружины. Этой весной держите их закрытыми. Оба клапана обычно открываются внутрь.
10. Свеча зажигания
Применяется в двигателях с искровым зажиганием. Основная функция свечи зажигания — проводить высокий потенциал от системы зажигания в камеру сгорания для воспламенения топливной смеси сжатого воздуха. Он установлен на головке блока цилиндров. Свеча зажигания состоит из металлической оболочки с двумя электродами, изолированными друг от друга воздушным зазором.При подаче высокого потенциала тока на свечу зажигания она отскакивает от питающего электрода и дает необходимую искру.
11. Инжектор
Инжектор обычно используется в двигателях с воспламенением от сжатия. Он распыляет топливо в камеру сгорания в конце такта сжатия. Он установлен на головке блока цилиндров.
12. Коллектор
Основная функция коллектора — подавать топливовоздушную смесь и собирать выхлопные газы в равной степени со всех цилиндров. В двигателе внутреннего сгорания используются два коллектора: один для впуска, а другой для выпуска.Обычно они изготавливаются из алюминиевого сплава.
13. Распределительный вал
Распределительный вал используется в двигателе внутреннего сгорания для управления открытием и закрытием клапанов в нужное время. Для обеспечения надлежащей выходной мощности двигателя впускной клапан должен открываться в конце такта выпуска и закрываться в конце такта впуска. Таким образом, для регулирования времени используется кулачок овальной формы, который оказывает давление на клапан для открытия и отпускания для закрытия. Он приводится в движение зубчатым ремнем, который приводится в движение коленчатым валом. Он размещается вверху или внизу цилиндра.
14. Поршневой палец или поршневой палец
Это параллельные шпиндели из закаленной стали, проходящие через бобышки поршня и малые концевые втулки или проушины, позволяющие шатунам поворачиваться. Он соединяет поршень с шатуном. Он сделан полым для легкости.
15. Толкатель
Толкатель используется, когда распределительный вал расположен на нижнем конце цилиндра. Он передает движение распределительного вала к клапанам, расположенным на головке блока цилиндров.
16. Маховик
Маховик закреплен на коленчатом валу.Основная функция маховика — вращать вал во время подготовительного хода. Это также делает вращение коленчатого вала более равномерным.
ВИДЫ ДВИГАТЕЛЕЙ I.C
I.C. Двигатель широко используется в автомобильной промышленности, поэтому он также известен как автомобильный двигатель. Автомобильный двигатель можно классифицировать по-разному.
По количеству ходов:
1. Двухтактный двигатель
В двухтактном двигателе поршень перемещается один раз вверх и вниз внутри цилиндра и совершает один оборот коленчатого вала во время однократного впрыска топлива.Этот тип двигателя имеет более высокий крутящий момент по сравнению с четырехтактным двигателем. Обычно они используются в мотороллерах, насосных агрегатах и т. Д.
2. Четырехтактный двигатель
В четырехтактном двигателе поршень перемещается два раза вверх и вниз внутри цилиндра и совершает два оборота коленчатого вала за одно время сжигания топлива. Этот тип двигателей имеет высокий средний показатель по сравнению с двухтактным двигателем. Обычно они используются в мотоциклах, автомобилях, грузовиках и т. Д.
Согласно конструкции двигателя:
1.Поршневой двигатель (поршневой двигатель)
В поршневом двигателе сила давления создается за счет сгорания топлива, действующего на поршень (устройство, которое может совершать возвратно-поступательное движение внутри цилиндра). Поршень начинает возвратно-поступательное движение (как и движение). Это возвратно-поступательное движение преобразуется во вращательное движение за счет использования коленчатого вала. Таким образом, коленчатый вал начинает вращаться и заставляет вращаться колеса автомобиля. Обычно они используются во всех автомобилях.
2. Роторный двигатель (двигатель Ванкеля)
В роторном двигателе есть ротор, который свободно вращается.Сила давления, создаваемая сгоранием топлива, действует на этот ротор, поэтому ротор вращается и начинает вращать колеса транспортного средства. Этот двигатель разработан Ванкелем в 1957 году. В настоящее время этот двигатель не используется в автомобилях.
В зависимости от используемого топлива:
1. Дизельный двигатель
В этих двигателях в качестве топлива используется дизельное топливо. Они используются в грузовиках, автобусах, легковых автомобилях и т. Д.
2. Бензиновый двигатель
В этих двигателях в качестве топлива используется бензин. Они используются в мотоциклах, спортивных автомобилях, роскошных автомобилях и т. Д.
3. Газовый двигатель
В этих двигателях в качестве топлива используется КПГ и СНГ. Они используются в некоторых легковых автомобилях.
По способу воспламенения:
1. Двигатель с воспламенением от сжатия
В двигателях этого типа нет дополнительного оборудования для воспламенения топлива. В этих двигателях горение топлива начинается из-за повышения температуры при сжатии воздуха. Так он известен как двигатель с воспламенением от сжатия.
2. Двигатель с искровым зажиганием
В этих типах двигателей зажигание топлива начинается от искры, генерируемой внутри цилиндра каким-либо дополнительным оборудованием (свечой зажигания).Так он известен как двигатель с искровым зажиганием.
По количеству цилиндров:
1. Одноцилиндровый двигатель
В двигателях этого типа только один цилиндр и один поршень соединены с коленчатым валом.
2. Многоцилиндровый двигатель
В двигателях этого типа имеется более одного цилиндра и поршень, соединенный с коленчатым валом
По расположению цилиндра:
1. Рядный двигатель
В двигателях этого типа цилиндры расположены по прямой линии один за другим по длине коленчатого вала.
2. V-образный двигатель
Двигатель с двумя рядами цилиндров, наклоненными под углом друг к другу, и с одним коленчатым валом, известный как V-образный двигатель.
3. Двигатель с противоположными цилиндрами
Двигатель с двумя рядами цилиндров, расположенными друг напротив друга на одном коленчатом валу (двигатель V-образного типа с углом между рядами 180 °).
4. Двигатель W-типа
Двигатель такой же, как двигатель V-типа, за исключением трех рядов цилиндров на одном коленчатом валу, известный как двигатель W-типа.
5.Двигатель с противоположным поршнем
В двигателе этого типа в каждом цилиндре установлено по два поршня, а камера сгорания находится в центре между поршнями. В этом двигателе один процесс сгорания вызывает два рабочих хода одновременно.
6. Радиальный двигатель
Это двигатель с поршнями, расположенными в круговой плоскости вокруг центрального коленчатого вала. Шатуны поршней соединены с ведущим штоком, который, в свою очередь, соединен с коленчатым валом.
По воздухозаборному процессу:
1.Безнаддувный
В этом типе двигателей забор воздуха в цилиндр происходит за счет атмосферного давления.
2. Двигатель с наддувом
В этом типе двигателя давление всасываемого воздуха повышается компрессором, приводимым в действие коленчатым валом двигателя.
3. Двигатель с турбонаддувом
В этом типе двигателей давление всасываемого воздуха увеличивается за счет использования турбинного компрессора, приводимого в действие выхлопными газами горящего топлива.
ТЕРМИНОЛОГИЯ ДВИГАТЕЛЯ
1. Верхняя мертвая точка (Т.D.C.)
В поршневом двигателе поршень движется вперед и назад в цилиндре. Когда поршень движется в верхнем направлении в цилиндре, точка, в которой поршень останавливается или меняет свое направление, известна как верхняя мертвая точка. Он расположен в верхнем конце цилиндра.
2. Нижняя мертвая точка (B.D.C.)
Когда поршень движется в направлении вниз, точка, в которой поршень останавливается или меняет свое направление, известная как нижняя мертвая точка. Он расположен в нижней части цилиндра.
3. Ход (L)
Максимальное расстояние, на которое перемещается поршень в одном направлении, называется ходом. Это расстояние между верхней мертвой точкой и нижней мертвой точкой.
4. Отверстие (b)
Внутренний диаметр цилиндра, известный как отверстие цилиндра.
5. Максимальный или общий объем цилиндра (Vtotal)
Это объем цилиндра, когда поршень находится в нижней мертвой точке. Как правило, он измеряется в кубических сантиметрах (куб. См).
6. Минимальный или зазорный объем цилиндра (Vclearance)
Это объем цилиндра, когда поршень находится в верхней мертвой точке.
7. Рабочий или рабочий объем (Vswept)
Это объем, который перемещается поршнем. Разница между общим объемом и зазором называется рабочим объемом.
Рабочий объем = Общий объем — Чистый объем
8. Степень сжатия
Отношение максимального объема цилиндра к минимальному называется степенью сжатия. Оно составляет от 8 до 12 для двигателя с искровым зажиганием и от 12 до 24 для двигателя с воспламенением от сжатия.
Степень сжатия = Общий объем / Свободный объем
9.Задержка зажигания
Это временной интервал между запуском зажигания (запуск свечи зажигания в двигателе S.I. и впрыск топлива в двигателе C.I.) и фактическим началом горения.
10. Передаточное число рабочего диаметра
Передаточное число рабочего диаметра — это отношение внутреннего диаметра (диаметра цилиндра) к длине хода. Обычно он равен единице для маленького двигателя и меньше единицы для большого двигателя.
Отношение внутреннего диаметра цилиндра к длине хода
11. Среднее эффективное давление
Среднее давление, действующее на поршень, называется средним эффективным давлением.Он определяется отношением работы, проделанной двигателем, к общему объему двигателя.
Среднее эффективное давление = Работа, проделанная двигателем / Общий объем цилиндра
15 важных частей двигателя внутреннего сгорания, которые вы должны знать
Двигатель внутреннего сгорания представляет собой комбинацию различных типов деталей. Когда I.C. Детали двигателя функционируют определенным образом, вы преобразуете химическую энергию топлива в механическую энергию.
В основном, автомобильная технология Engineering разрабатывает два типа двигателей внутреннего сгорания.
One — двигатель с искровым зажиганием (двигатель SI), также известный как бензиновый двигатель. Другой — двигатель с воспламенением от сжатия (CI Engine), также известный как Diesel Engine .
Принцип работы и детали обоих двигателей практически одинаковы, разница только в процессе сжигания топлива.
Чтобы получить подробную информацию о работе с бензиновым и дизельным двигателями, прочтите эти статьи.
Работа двигателя: как работает четырехтактный бензиновый двигатель?
Дизельный двигатель : принцип работы четырехтактного дизельного двигателя
В этом посте я подробно поделюсь информацией о деталях двигателя внутреннего сгорания .Таким образом, вы можете лучше понять части двигателя и их функции.
Фото любезно предоставлено SlideshareВы также можете посмотреть и подписаться на наш канал YouTube с обучающими видео по инженерным наукам, нажав здесь https://goo.gl/4jeDFu
Цилиндр или блок цилиндров также известен как блок цилиндров двигателя. Это та часть, где происходит сжигание топлива. Основная функция цилиндра — позволить поршню совершать возвратно-поступательное движение внутри.
Внутри цилиндра зажигается свежий заряд топливовоздушной смеси . Этот заряд сжимается и расширяется, поэтому поршень может работать дальше.
При сгорании топлива выделяется сильное тепло. Так, для проведения генерируемого тепла в двигателе с водяным охлаждением предусмотрена водяная рубашка . В двигателях с воздушным охлаждением ребра предназначены для охлаждения блока цилиндров .
Блок цилиндров двигателя изготовлен из высококачественного чугуна, чтобы выдерживать высокие температуры и давление.Блок двигателя изготавливается в виде единой детали методом литья.
Головка блока цилиндров привинчивается к верхней стороне путем размещения прокладки головки блока цилиндров, в то время как картер закреплен болтами в нижней части блока цилиндров.
Основная функция головки блока цилиндров — уплотнение блока цилиндров с верхней стороны с помощью прокладки головки блока цилиндров. Таким образом, утечка топливовоздушной смеси и сгоревших выхлопных газов полностью прекращена.
Для впуска свежей смеси внутрь блока цилиндров на головке блока цилиндров установлен впускной клапан .При этом установлен выпускной клапан для выхода сгоревших выхлопных газов в атмосферу через глушитель.
Свеча зажигания устанавливается, если двигатель с искровым зажиганием (SI Engine). В двигателе с воспламенением от сжатия (двигатель CI) топливная форсунка установлена на головке блока цилиндров.
Головка блока цилиндров обычно изготавливается методом литья или ковки из цельного чугуна. Также в некоторых случаях он изготовлен из алюминия.
Картер — это корпус, который скрепляет вместе все остальные детали двигателя.Это самая большая часть двигателя, но она должна быть прочной и легкой.
Эта деталь также известна как масляный поддон. Смазочное масло заливается в картер двигателя для смазки двигателя. Также имеется щуп для проверки уровня смазочного масла.
Как упоминалось ранее, блок двигателя установлен на картере. Прокладка двигателя помещается между картером и блоком цилиндров для предотвращения утечки.
Основное назначение картера — вмещать смазочное масло и служить в качестве корпуса для коленчатого вала.
Картер двигателя обычно изготавливается из чугуна в виде одной детали путем литья в песчаные формы. Процесс литья алюминия в песчаные формы используется для изготовления картера из алюминия.
Основная функция коленчатого вала — преобразование линейного движения во вращательное. Это означает, что поступательное движение поршня преобразуется во вращательное движение.
Для завершения преобразования этих двух движений на коленчатом валу имеется шатунная шейка. Шатун также известен как «ход кривошипа».
Большой конец шатунаприкреплен болтами к шатунной шейке, а малый конец фиксируется поршнем с помощью поршневого пальца.
Противовес установлен на коленчатом валу для частичного уравновешивания сил возвратно-поступательного поршня и уменьшения нагрузки на шейки подшипников коленчатого вала.
Также проверьте: Конструкция и функционирование коленчатого вала, используемого в двигателе I.C.
Количество шатунов и противовеса зависит от конструкции двигателя. Инженер-разработчик или инженер-конструктор пытается сохранить минимальную длину коленчатого вала. Следовательно, может быть достигнута максимальная балансировка.
Предусмотрено уплотнение коленчатого вала, позволяющее избежать утечки смазочного масла. Коленчатый вал установлен на подшипнике, который передает свое движение на маховик.
Это цельная деталь, отлитая из высокопрочной стали. В настоящее время используются кованые коленчатые валы из-за меньшего веса, более компактной конструкции и лучшего внутреннего демпфирования.
Как видно из названия, он соединяет поршень с коленчатым валом, так что осуществляется передача мощности. Он преобразует возвратно-поступательное движение поршня во вращательное движение коленчатого вала.
Большой конец шатуна соединяется с коленчатым валом, а меньший конец соединяется с поршнем.
В большинстве случаев шатун является полым или снабжен внутренним литым маслопроводом для подачи смазки на поршневой палец.
В зависимости от требований шатун изготавливается из высококачественного алюминия и микролегированных сталей. Для высокопроизводительного двигателя он сделан из титана.
Шатун лучше изготавливать методом ковки.Кованые шатуны имеют лучшее соотношение прочности и веса и более низкую стоимость, чем спеченные шатуны.
Это цилиндрическая деталь, которая скользит взад и вперед в полом цилиндре. Основная функция поршня — передавать усилие от расширяющегося газа в цилиндре на коленчатый вал через шатун.
Во время такта всасывания всасывает свежий заряд топливовоздушной смеси через впускной клапан. Сжимает во время такта сжатия, а также вытесняет сгоревшие выхлопные газы из цилиндра через выпускной клапан .
Поршень должен быть легким, но достаточно прочным, чтобы выдерживать давление газа, возникающее при сгорании.
Итак, Поршни отлиты из алюминиевых сплавов. Для повышения прочности и долговечности некоторые гоночные поршни могут быть коваными. Иногда поршни также делают из чугуна.
Поршневое кольцо установлено на поршне для хорошего уплотнения и уменьшения трения между стенкой цилиндра и поршнем.
Предотвращает утечку сжатого заряда топливовоздушной смеси на другую сторону поршня.
Поршневые кольцаимеют разрез на одном конце, поэтому они могут расширяться или скользить по концу поршня.
Количество и размер колец определяется мощностью двигателя. Три поршневых кольца рекомендуются для четырехтактного двигателя , а два поршневых кольца — для двухтактного двигателя .
Масляное кольцо используется для удаления смазочного масла из цилиндра после смазки. Это кольцо предотвращает смешивание излишка масла с зарядом.
Основные функции поршневого кольца следующие
- Уплотнение камеры сгорания
- Регулировка расхода моторного масла
- Теплообмен к цилиндру
- Поршень опоры в цилиндре
Важно, чтобы кольца свободно перемещались в своих канавках внутри поршня, чтобы они могли оставаться в контакте с цилиндром.
Большинство поршневых колец изготовлено из очень твердого и несколько хрупкого чугуна . Иногда его также делают из легированной пружинной стали.
Поршневой палец, поршневой палец или поршневой палец соединяет поршень с шатуном. Он подвергается сочетанию срезающих и изгибающих нагрузок.
Поршневой палец должен работать при некоторых из самых высоких температур в двигателе.
Поршневые пальцы имеют трубчатую форму, что обеспечивает достаточную прочность при минимальном весе.
Обычно они изготавливаются из низкоуглеродистой цементированной стали с содержанием углерода 0,15%, кремния 0,3%, марганца 0,55% и остального железа 99%.
Основная функция распределительного вала — открывать и закрывать впускной и выпускной клапаны с правильной синхронизацией .
Итак, для регулирования фаз газораспределения используются кулачки, обычно называемые кулачками. Кулачки имеют овальную форму, и они оказывают давление на клапан для открытия и отпускания для закрытия.
Он принимает движущую силу от коленчатого вала через зубчатую передачу или цепь и управляет впускным клапаном, а также выпускным клапаном с помощью некоторых других частей, таких как толкатели, толкатель и коромысла.
An Производительность двигателя во многом зависит также от конструкции распредвала и его правильного функционирования.
Распредвалы могут изготавливаться из различных материалов. Благодаря этому распредвалы из охлажденного чугуна обладают хорошей износостойкостью, поскольку в процессе охлаждения они затвердевают. Для качественной заготовки распредвала используется сталь.
Основная функция карбюратора — смешивать воздух и топливо в надлежащем соотношении для сгорания в двигателе внутреннего сгорания.
Он превращает бензин в мелкую струю и смешивается с воздухом в надлежащем соотношении в соответствии с требованиями двигателя.
В более старых двигателях использовались карбюраторы с восходящим потоком, в которых воздух поступает снизу карбюратора и выходит через верх. Он был заменен карбюраторами с нисходящим потоком.
В настоящее время карбюратор заменен системой с электронным управлением под названием впрыск топлива для регулирования топливно-воздушной смеси.
Проще говоря, карбюратор — это трубка, по которой воздух и топливо попадают в двигатель через клапаны.
Эта деталь используется только в двигателе Spark Ignition (двигатель SI).Основная функция свечи зажигания — подавать электрический ток от системы зажигания в камеру сгорания. Таким образом, сжатая топливно-воздушная смесь воспламеняется от электрической искры.
Свеча зажигания состоит из металлического кожуха с резьбой, который электрически изолирован от центрального электрода фарфоровым изолятором.
Металлический кожух свечей зажигания ввинчивается в головку блока цилиндров двигателя, следовательно, он электрически заземлен.
Свечи зажигания обычно требуют напряжения 12 000–25 000 В или более для правильного образования искры.
Замена свечи зажигания требуется редко из-за ее прочной конструкции.
В каждом двигателе внутреннего сгорания используются два типа клапанов.
Впускной клапан установлен на головке блока цилиндров для подачи свежего заряда смеси внутрь камеры сгорания.
Выпускной клапан также установлен на головке блока цилиндров, чтобы позволить выхлопным газам выходить из отверстия цилиндра в нужное время.
Количество впускных и выпускных клапанов зависит от количества цилиндров двигателя.
Впускной и выпускной клапаны приводятся в действие распределительным валом. Распределительный вал использует подъемники, толкатели и коромысла для приведения в действие клапанов.
Правильный выбор времени открытия и закрытия клапанов необходим для бесперебойной работы двигателя. Распределительный вал управляет последовательностью и синхронизацией клапана.
Как видно из названия, он регулирует скорость двигателя, контролируя подачу топлива.
Регулировка частоты вращения дизельного двигателя будет осуществляться регулятором при другой нагрузке путем регулирования подачи топлива.
Движение втулки регулятора вверх приводит в действие дроссельную заслонку, уменьшая подачу топлива. Следовательно, скорость двигателя регулируется.
Маховик — это диск, который установлен на одном конце коленчатого вала для обеспечения инерции двигателя.
Маховик сглаживает некоторые обороты и отклонения усилия за счет сопротивления ускорению.
Маховик обеспечивает инерцию, необходимую для предотвращения потери скорости двигателя и возможной остановки вращения коленчатого вала между интервалами сгорания.
Маховики обычно изготавливаются из стали или чугуна.
По сути, форсунка — это одна из частей общей системы подачи топлива.
Топливные форсунки — это механические устройства с электронным управлением, которые отвечают за распыление (впрыск) нужного количества топлива в камеру сгорания двигателя.
Форсункитакже должны распылять топливо под прямым углом, давлением и формой распыления.
Форсунки управляются блоком управления двигателем (ЭБУ).У двигателей есть несколько топливных форсунок, и они часто подключены к топливной рампе.
Топливные форсунки расположены в головке двигателя и ввинчиваются в камеру сгорания форсункой внутри.
Итак, это все части двигателя внутреннего сгорания.
Помимо этой информации, вам предлагается прочитать что-нибудь еще ниже Engineering Books
Итак, здесь вы найдете лучшие инженерные ресурсы для получения более подробной информации
Чтобы получить более подробную информацию о двигателе внутреннего сгорания и его частях, я рекомендую прочитать
Если вам понравился пост, поделитесь им с друзьями, а также в социальных сетях.Нажмите на колокольчик, чтобы подписаться
КОМПОНЕНТОВ И ИХ ФУНКЦИИ, ТИПЫ И
Это двигатель, в котором сгорание топлива происходит внутри двигателя. Когда топливо сгорает внутри цилиндра двигателя, оно создает высокую температуру и давление. Эта сила высокого давления действует на поршень (устройство, которое освобождает движение внутри цилиндра и передает силу давления на кривошип с помощью шатуна), который используется для вращения колес транспортного средства.В этих двигателях мы можем использовать только газы и топливо с высокой летучестью, такое как бензин, дизельное топливо. Эти двигатели обычно используются в автомобильной промышленности, производстве электроэнергии и т. Д.
Преимущества I.C. двигатель
- В целом имеет высокий КПД по сравнению с двигателем E.C.
- Эти двигатели компактны и занимают меньше места.
- Начальная стоимость I.C. двигатель ниже, чем двигатель E.C.
- Этот двигатель легко запускается в холодную погоду, поскольку он использует легколетучий вид топлива.
КОМПОНЕНТЫ ДВИГАТЕЛЯ IC
1. Блок цилиндров
Цилиндр — это основной корпус двигателя внутреннего сгорания. Цилиндр — это часть, в которой происходит забор топлива, сжатие топлива и сжигание топлива. Основная функция цилиндра — направлять поршень. Он находится в прямом контакте с продуктами сгорания, поэтому его необходимо охладить. При охлаждении цилиндра на внешней стороне цилиндра имеется водяная рубашка (когда жидкостное охлаждение используется в большинстве автомобилей) или плавник (для воздушного охлаждения, используемого в большинстве мотоциклов).Головка блока цилиндров и картер на нижнем конце цилиндра закреплены на верхнем конце цилиндра. Верхняя часть цилиндра представляет собой камеру сгорания, в которой горит топливо. Чтобы справиться со всем этим давлением и температурой, возникающими при сгорании топлива, материал цилиндра должен иметь высокую прочность на сжатие. Таким образом, он сделан из высококачественного чугуна. Его изготавливают методом литья и обычно отливают в виде цельного куска.
2. Головка блока цилиндров
Верхний торец цилиндра двигателя закрыт съемной головкой блока цилиндров.В головке блока цилиндров есть два отверстия, одно для впуска топлива, а другое для выпуска. Как впускной, так и выпускной порты закрыты двумя клапанами, известными как впускной и выпускной клапан. Впускной клапан, выпускной клапан, свеча зажигания, форсунка и т. Д. Прикручены к головке блока цилиндров. Основная функция головки блока цилиндров — герметизировать блок цилиндров и не допускать попадания и выхода газов на крышку клапана головки блока цилиндров двигателя. Головка блока цилиндров обычно изготавливается из чугуна или алюминия. Его изготавливают методом литья или ковки и, как правило, цельным.
3. Поршень
Поршень установлен на каждом цилиндре как поверхность для приема давления газа и передачи усилия на шатун. Это главный двигатель в двигателе. Основная функция поршня — плотно прилегать к цилиндру через отверстие и свободно скользить внутри цилиндра. Поршень должен быть легким и достаточно прочным, чтобы выдерживать давление газа, возникающее при сгорании топлива. Таким образом, поршень изготовлен из алюминиевого сплава, а иногда и из чугуна, потому что поршень из легкого сплава расширяется больше, чем чугун, поэтому им требуется больше зазоров до отверстия.
4. Кольца поршневые
Поршень в цилиндре должен иметь достаточно свободную посадку.
Так, чтобы он мог свободно перемещаться внутри цилиндра. Если поршень слишком мал для соответствия требованиям, он будет расширяться при нагревании и может оставаться в цилиндре.
Плотно прилегать к цилиндру, а если он потеряет слишком много,
Давление пара будет уменьшаться. Поршни оснащены поршневыми кольцами для обеспечения хорошего уплотнения.
Посадка и меньшее сопротивление трению между поршнем и соплом.
Эти кольца имеют канавки, вырезанные в поршне.Они разделены на одном конце, чтобы они могли расширяться или скользить по краю поршня. В небольшом двухтактном двигателе
есть два поршневых кольца для обеспечения эффективного уплотнения.
Но четырехтактный двигатель имеет дополнительное кольцо, известное как масляное кольцо.
Поршневые кольца изготовлены из мелкозернистого чугуна и
из высокоэластичного материала, не подверженного воздействию рабочей температуры.
5. Шатун
Шатун соединяет поршень с коленчатым валом и передает движение и усилие поршня на коленчатый вал.Он преобразует возвратно-поступательное движение поршня во вращательное движение коленчатого вала. У шатуна два конца; один известен как большой конец, а другой — как малый конец. Большой конец соединен с коленчатым валом, а малый конец соединен с поршнем с помощью поршневого пальца. Шатуны изготовлены из никелевых, хромовых и хромованадиевых сталей. Для небольших двигателей материалом может быть алюминий.
6. Коленчатый вал
Коленчатый вал двигателя внутреннего сгорания воспринимает усилие или тягу, прилагаемую поршнем к шатуну, и преобразует возвратно-поступательное движение поршня во вращательное движение коленчатого вала.Коленчатый вал устанавливается в подшипник, поэтому он может свободно вращаться. Форма и размер коленчатого вала зависят от количества и расположения цилиндров. Обычно его изготавливают путем ковки стали, но некоторые производители используют специальные типы чугуна, такие как отливки из шаровидного графита или никелевых сплавов, которые дешевле в производстве и имеют хороший срок службы.
7. Подшипник двигателя
Везде, где в двигателе есть вращательное действие, нужны подшипники. Подшипники используются для поддержки движущихся частей.Коленчатый вал опирается на подшипник. Шатун шатуна прикреплен к шатунной шейке на кривошипе коленчатого вала подшипником. Поршневой палец на малом конце используется для прикрепления штока к поршню и также находится в подшипниках. Основная функция подшипников — уменьшить трение между этими движущимися частями. В двигателе внутреннего сгорания используются подшипники скольжения и качения. Подшипник скольжения, который иногда называют втулкой, используется для крепления шатуна к поршню и коленчатому валу. Они разделены, чтобы их можно было установить в двигатель.Подшипник качения и шарикоподшипник используются для поддержки коленчатого вала, поэтому он может свободно вращаться. Типичная половина подшипника изготовлена из стали или бронзы, на которую нанесена футеровка из относительно мягкого материала подшипника.
8. Картер двигателя
Основной корпус двигателя, к которому прикреплен цилиндр и который содержит коленчатый вал и подшипник коленчатого вала, называется картером. Он также служит системой смазки и иногда его называют масляным картером. В него помещается все масло для смазки.
9. Клапаны
Для управления впуском и выпуском двигателя внутреннего сгорания используются клапаны. Количество клапанов в двигателе зависит от количества цилиндров. Для каждого цилиндра используются два клапана: один для впуска топливовоздушной смеси внутрь цилиндра, а другой — для выпуска дымовых газов. Клапаны устанавливаются в порт на головке блока цилиндров с помощью сильной пружины. Этой весной держите их закрытыми. Оба клапана обычно открываются внутрь.
10. Свеча зажигания
Используется в двигателях с искровым зажиганием.Основная функция свечи зажигания — проводить высокий потенциал от системы зажигания в камеру сгорания для воспламенения сжатой топливовоздушной смеси. Он установлен на головке блока цилиндров. Свеча зажигания состоит из металлической оболочки с двумя электродами, изолированными друг от друга воздушным зазором. При подаче высокого потенциала тока на свечу зажигания она отскакивает от питающего электрода и дает необходимую искру.
11. Инжектор
В двигателе с воспламенением от сжатия обычно используется инжектор.Он распыляет топливо в камеру сгорания в конце такта сжатия. Он установлен на головке блока цилиндров.
12. Коллектор
Основная функция коллектора — подавать топливовоздушную смесь и собирать выхлопные газы в равной степени со всех цилиндров. В двигателе внутреннего сгорания используются два коллектора: один для впуска, а другой для выпуска. Обычно они изготавливаются из алюминиевого сплава.
13. Распределительный вал
Распределительный вал используется в двигателе внутреннего сгорания для управления открытием и закрытием клапанов в нужное время.Для обеспечения надлежащей выходной мощности двигателя впускной клапан должен открываться в конце такта выпуска и закрываться в конце такта впуска. Кулачок овальной формы используется для управления синхронизацией и оказывает давление на клапан для открытия и отпускания для закрытия. Он приводится в действие ремнем газораспределительного механизма коленчатого вала. Он устанавливается сверху или снизу цилиндра.
14. Поршневой палец или поршневой палец
Это параллельные шпиндели из закаленной стали, проходящие через бобышки поршня и маленькие концевые втулки или проушины, позволяющие шатунам поворачиваться.Он соединяет поршень с шатуном. Он сделан полым для легкости.
15. Толкатель
Толкатель используется, когда распределительный вал расположен в нижнем конце цилиндра. Он передает движение распределительного вала к клапанам, расположенным на головке блока цилиндров.
16. Маховик
На коленчатом валу закреплен маховик. Основная функция маховика — вращать вал во время подготовительного хода. Это также делает вращение коленчатого вала более равномерным.
ВИДЫ ДВИГАТЕЛЯ I.C
I.C. Двигатель широко используется в автомобильной промышленности, поэтому он также известен как автомобильный двигатель. Автомобильный двигатель можно классифицировать по-разному.
По количеству штрихов:
Какие компоненты 4-тактного двигателя? Клапаны, кулачки, поршень и т. Д.
В этом выпуске «Содержание автомобильных технологий» мы представляем вам общую конструкцию и компоненты обычного двигателя внутреннего сгорания.Цель состоит в том, чтобы дать краткое представление о конструкции и работе всех компонентов внутри двигателя. Все это будет сделано простым для понимания языком, чтобы у человека появился интерес к знаниям о различных процессах, происходящих внутри двигателя внутреннего сгорания. Если вас интересуют такие статьи, подпишитесь на Car Blog India и посетите раздел Автомобильных технологий, чтобы простыми словами познакомиться с некоторыми интересными техническими процессами, связанными с автомобильной инженерией. Давайте сейчас погрузимся в это.
Также прочтите: Что такое векторизация крутящего момента, управление крутящим моментом, недостаточная и избыточная поворачиваемость?
4-тактный двигатель внутреннего сгорания
Практически все автомобили, которые у нас есть сегодня, построены по принципу 4-тактного цикла. Они представляют собой ходы впуска, сжатия, мощности и выпуска. Если нам нужно кратко объяснить каждый из них, мы начнем с такта впуска, который заключается в заполнении цилиндра сгорания двигателя свежим воздухом. В камере сгорания топливо сжигается для выработки энергии, необходимой для движения транспортного средства.Кислород необходим для сгорания, поэтому такт впуска обеспечивает достаточную подачу свежего воздуха (кислорода) для сжигания топлива. Второй штрих представляет собой фазу сжатия. Это означает, что воздух и топливо должны быть сжаты или смешаны вместе, чтобы процесс сгорания или горения происходил чисто. Здесь необходимо отметить, что если есть топливо, которое не было тщательно перемешано, оно выйдет из выхлопной трубы как несгоревшее и вызовет сильное загрязнение. Следовательно, смешивание воздуха с топливом является важным аспектом двигателей внутреннего сгорания.
Читайте также: Работа синхронных и асинхронных двигателей в электромобилях (электромобилях)!
После этого сгорание топливовоздушной смеси вызывает выделение энергии, которая толкает автомобиль вперед. Это процесс, при котором энергия бензина или дизельного топлива фактически выделяется в виде тепла и преобразуется в механическую энергию или движение. Последний такт — это такт выпуска, который обеспечивает безопасное удаление сгоревших газов и частиц из двигателя и их выброс в атмосферу.Следует отметить, что к выхлопу прикреплена система очистки выхлопных газов, которая обеспечивает минимальную токсичность этих газов перед их выбросом в атмосферу. Эти 4 процесса составляют 1 цикл, что означает, что каждый цикл имеет 1 рабочий ход.
Читайте также: Работа корневых, двухвинтовых, центробежных нагнетателей!
Клапаны
Клапаны обеспечивают управление воздухом или газами внутри различных частей двигателя.Клапаны расположены на впускной стороне двигателя, чтобы впускать свежий воздух в необходимом количестве. Клапаны также присутствуют на выхлопной стороне, чтобы позволить выбрасывать необходимое количество выхлопных газов из двигателя. Кроме того, это важные компоненты другого оборудования, такого как турбокомпрессор, насос или другие механические устройства. Эти клапаны выполняют операции закрытия и открытия в различных устройствах.
Также прочтите: 6 самых актуальных технических характеристик подключенных автомобилей в современных автомобилях!
Распредвалы
Это механически спроектированный компонент, который имеет возвышения на валу для открытия и закрытия впускных и выпускных клапанов.Когда распределительный вал вращается, эти возвышения толкают детали, соединенные с клапанами, и совершают операции закрытия и открытия. Продолжительность и время открытия и закрытия клапанов можно контролировать или изменять с помощью конкретных конструкций распределительных валов. В зависимости от того, когда впускные клапаны открываются, происходит впрыск топлива внутри цилиндра, чтобы обеспечить надлежащее смешивание топлива с воздухом.
Читайте также: Работа рулевого управления с гидравлическим, электрическим и гидроэнергетическим приводом!
Поршни, шатуны и коленчатые валы
Вся энергия камеры сгорания должна передаваться на колеса, чтобы автомобиль мог двигаться.Это требует некоторых дополнительных компонентов для преобразования возвратно-поступательного движения поршней внутри цилиндра во вращательное движение колес. Поршни — это то, что движется вверх и вниз внутри цилиндра для создания тактов впуска, сжатия, мощности и выпуска. Это движущиеся части внутри цилиндра. Они соединены с шатунами внизу, которые заставляют коленчатый вал вращаться. Коленчатые валы соединены с приводным валом, который, в свою очередь, соединен с колесами.Таким образом, движение поршней вверх и вниз преобразуется во вращательное движение колес. Один полный оборот коленчатого вала включает 2 рабочих хода. По сути, можно сделать вывод, что химическая энергия топлива преобразуется в кинетическую энергию транспортного средства в этом 4-тактном цикле с использованием вышеупомянутых компонентов.
Также прочтите: Что такое EGR (рециркуляция выхлопных газов) — принцип и преимущества!
Дифференциалы
Дифференциалы — это механические компоненты, которые получают мощность и крутящий момент от двигателя и распределяют их поровну (в случае 2WD) между колесами.В случае системы полного привода дифференциалы допускают непропорционально большие крутящие моменты для любого из четырех колес, которое требует этого больше всего. Основная цель дифференциала — обеспечить разную скорость разных колес. Например, за углом внешние колеса автомобиля должны преодолеть большее расстояние по сравнению с внутренними колесами. Для сохранения устойчивости эти колеса должны двигаться с разной скоростью, что обеспечивается дифференциалом. В частности, более сложные внедорожники имеют несколько дифференциалов, чтобы обеспечить гибкость в отношении того, какие колеса должны получать какой крутящий момент.Это зависит от тяги конкретного колеса.
Также прочтите: Как работают ABS, EBD, Brake Assist, Hill-Start Assist, Traction Control и ESP?
Турбокомпрессоры и промежуточные охладители
По сути, турбокомпрессоры и промежуточные охладители можно рассматривать как усилители производительности транспортных средств. У них есть определенные цели, которые действуют как катализатор для увеличения мощности, снижения выбросов, топливной эффективности или теплового КПД. Турбокомпрессор увеличивает мощность и крутящий момент автомобиля за счет использования энергии выхлопных газов.Выхлопные газы заставляют вращаться турбину турбонагнетателя, которая вращает компрессор, установленный на том же валу. Это заставляет свежий воздух сжиматься, и количество свежего воздуха, которое может быть упаковано внутри цилиндра, увеличивается. Это позволяет впрыскивать больше топлива в камеру сгорания, что равняется большей мощности. Интеркулеры следят за тем, чтобы температура всей системы (или свежего воздуха) оставалась низкой. В частности, после сжатия воздуха воздух становится горячим и его необходимо охладить перед входом в камеру сгорания.Более высокие температуры вызывают более высокие уровни NOx (оксидов азота), которые должны быть ниже предела, чтобы быть законными на улице. Улучшен эмиссионный аспект.
Также прочтите: Что такое пневматическая подвеска — использование мягких и жестких пружин!
Система очистки выхлопных газов
Наконец, выхлопные газы двигателя обрабатываются в выхлопной системе автомобиля. Нормы выбросов становятся жестче с каждым днем, а двигатели внутреннего сгорания должны быть более эффективными и чистыми, чтобы продолжать работу.Поэтому в системах очистки выхлопных газов используются современные технологии, которые развиваются изо дня в день, чтобы гарантировать, что уровень загрязнения, вызываемого транспортными средствами, остается допустимым пределом.