Повреждения подшипников скольжения: Коррозия · Technipedia · Motorservice
Оценка
Если вкладыш подшипника неправильно установлен в постели, то наблюдается относительное движение (микродвижение скольжения), из-за которого возникает коррозия от трения. Тепло, образующееся при трении в процессе движения подшипника, не отводится смазочным материалом, как внутри подшипника, а приводит к локальному перегреву стальной основы. В результате этого перегрева образуются места наплавления, а поверхность покрывается типичными ямками. Происходит перенос материалов между обратной стороной вкладыша подшипника и корпусом. Окружающая среда может проникнуть в уже ставшие шероховатыми и химически активными поверхности и ускорить коррозию. Коррозия от трения снижает усталостную прочность материала из-за содействия образованию микротрещин. Возможны усталостные повреждения, вследствие которых возникают трещины и усталостные изломы.
Возможныe причины
- недостаточный предварительный натяг из-за слишком большого отверстия под подшипник или слишком малого вкладыша подшипника
- выступ вкладыша подшипника слишком мал: выступ вкладыша подшипника обеспечивает глухую посадку за счет достаточной прессовой посадки
- деформация корпуса: у изготовленных из алюминия картеров двигателей под действием значительной температуры корпус и вкладыш подшипника могут деформироваться по-разному, из-за чего больше не обеспечивается глухая посадка подшипника
- изгиб коленчатого вала: вследствие изгиба коленчатого вала на рабочей поверхности подшипника остается особое пятно контакта
- недостаточная затяжка болтов
- колебания или вибрации корпуса или коленчатого вала, которые вызывают микродвижение (возможно также усиление колебаний или вибраций за счет частиц или, соответственно, пустот на обратной стороне вкладыша)
Меры по устранению
Если распознаются признаки контактной коррозии, то подшипник необходимо заменить, так как уже возможно снижение усталостной прочности.
- отверстие под подшипник и наружный диаметр вкладыша подшипника должны быть в пределах допусков, чтобы обеспечить соблюдение заданного зазора в подшипнике
- выступ: для обеспечения глухой посадки вкладыша подшипника за счет надлежащей прессовой посадки требуется достаточное значение выступа вкладыша
- проверить отверстие под подшипник и корпус на наличие возможных деформаций
- отбалансировать коленчатый вал при монтаже и проверить нагрузку на вал
- затянуть болты с соблюдением данных изготовителя относительно моментов и последовательности затяжки
- проверить работающий двигатель на вибрации и колебания
Оценка
Химическую коррозию вызывают реакции между вкладышем подшипника и моторным маслом. Причинами химической реакции являются агрессивные присадки к маслу или загрязнение масла во время эксплуатации. В результате химического воздействия снижается усталостная прочность материала, из-за чего ускоряется развитие усталостных повреждений даже при малой нагрузке.
Возможныe причины
- износ, кавитация и эрозия могут способствовать появлению коррозии из-за разрушения и химической активации поверхности материала
- образование кислот и солей металлов вследствие старения масла
- недопустимые, агрессивные присадки к маслу
- агрессивные продукты сгорания (сера, сероводород)
- загрязнение масла водой или антифризом
- высокие рабочие температуры ускоряют химические процессы, например, старение масла
Меры по устранению
Пораженные коррозией подшипники необходимо заменить.
- смену масла всегда выполнять согласно предписаниям изготовителя
- использовать только качественные масла, не содержащие агрессивных присадок
- обеспечивать достаточное охлаждение двигателя
Подшипники коренные и шатунные — Справочник химика 21
Подготовка вкладышей в отверстия коренных подшипников и шатунов. [c.419] Гильзы. . . Поршни. . Подшипники коренные шатунные Шейки [c.61]
Двигатель в коренных подшипниках В шатунных подшипниках Двигатель в коренных подшипниках в шатунных подшипниках [c.74]
Смазка механизма движения — циркуляционная под давлением, от масляного насоса (шестеренчатого или винтового) с приводом от индивидуального электродвигателя. Система смазки обслуживает коренные подшипники, вкладыши шатунов, направляющие крейцкопфа. [c.12]
Коренные подшипники кривошипно-шатунных механизмов компрессоров, электродвигателей до 100 кВт, турбин [c.329]
Коренные подшипники служат для восприятия нагрузок от переменных поршневых сил. Подшипники, на которые опирается коленчатый вал, называются коренными. В соединениях шатуна с коленчатым валом и пальцем крейцкопфа или поршня устанавливаются подшипники, называемые шатунными. Для многоколейных валов, как правило, применяют подшипники скольжения, воспринимающие большие по величине нагрузки.
Как правило, баббит Б83 используют для коренных, шатунных и выносных подшипников тяжелых и средних компрессоров. [c.68]
Механизм движения включает коренной вал, шатуны, крейцкопфы и подшипники. Коренной вал кривошипного типа [ 1 ] представляет собой кованую конструкцию, состоящую из вала кривошипов, пальцев кривошипа и противовесов (могут быть литыми из стали). Средняя часть вала утолщена в месте насадки ротора электродвигателя, фиксируемого двумя тангенциальными шпонками. Кривошип насажен на цапфу вала по горячей посадке аналогично крепится и палец кривошипа. При двухрядном исполнении кривошипы закреплены под углом 90—110° друг к другу, что соответствует более благоприятному распределению тангенциальных сил.
На правой стороне компрессора расположены цилиндры второй 6, четвертой 8 и шестой 9 ступеней, имеющих соответственно диаметры 690, 335 и 115 мм. На левой стороне расположены цилиндры первой 13, третьей И п пятой 10 ступеней, которые имеют соответственно диаметры 1080, 620 и 195 мм. Цилиндры первой и второй ступеней двойного действия установлены на весу между двумя промежуточными фонарями 14 п 12, 5 и 7. Цилиндры третьей и четвертой ступеней прикреплены к промежуточным фонарям 12 я 7 п опираются на качающиеся опоры. Цилиндры пятой и шестой ступеней выполнены консольно, присоединены только одной стороной к соседним цилиндрам. Между III—V и IV—VI ступенями находятся уравнительные полости. Все промежуточные фонари установлены на качающихся опорах. Поршни первой и второй ступеней компрессора выполнены подвешенными, а поршни остальных — скользящими. Вал 19 компрессора кривошипного типа опирается на коренные подшипники 1, шатуны 18 с закрытой кривошипной головкой.
Баббит ВН по антифрикционным свойствам незначительно уступает баббиту Б83. Рекомендуется для заливки коренных, шатунных и головных подшипников двигателей внутреннего сгорания и компрессоров. С целью экономии дорогостоящего баббита Б83 в двухтактных двигателях допускается заливка верхних вкладышей шатунных подшипников баббитом ВН, а нижних баббитом В83. На твердость баббита БН температура влияет меньше, чем на баббит В83. От воздействия смазочного масла коррозия незначительна. [c.211]
На текущих ремонтах ТР-2 производят внешний осмотр подшипников нижнего коленчатого вала с измерением щупом зазоров на масло и провисания коренных шеек вала (кроме 8, 9 и 10-го подшипников). Все шатунные подшипники разбирают для осмотра. Верхний коленчатый вал снимают, осматривают коренные подшипники и определяют их ступенчатость, которая должна быть не больше значения, указанного в табл.

При первом пуске компрессора шатуны отсоединяют (если ротор электродвигателя насажен непосредственно на коренной вал компрессора). Таким образом проверяют работу электродвигателя и коренных подшипников. Затем шатуны соединяют с коренным валом и компрессор для проверки работы его узлов и систем обкатывают вхолостую при снятых клапанах. Замеченные неисправности устраняют при остановках компрессора. После того как проверена надежность работы компрессора на холостом ходу, проводят непрерывное испытание компрессора на этом ходу в течение 10 ч (для газовых и воздушных компрессоров) или 24 ч (для компрессоров холодильных установок). В соответствии с правилами производства и приемки монтажных работ горизонтальные поршневые компрессоры (кроме компрессоров холодильных установок) до сдачи в комплексные испытания подвергают непрерывным испытаниям под нагрузкой в течение 48 ч.
Компрессор фреоновый транспортный сальниковый бескрейцкопфный, блок-картерный, одноступенчатый, двухцилиндровый, непрямоточный ФВ2 (лист 84) имеет холодопроизводительность при стандартных условиях 2,71 кВт.
Компрессор фреоновый сальниковый бескрейцкопфный, блок-картерный, одноступенчатый, четырехцилиндровый, непрямоточный, с регулированием производительности 4U (Швеция) (листы 106, 107). Хладагент — фреон-12, холодопроизводительность при стандартных условиях 110 кВт.
После пригонки всех коренных подшипников монтируют шатунно-поршневую группу. Крейцкопфы заводят через окна рамы на направляющие параллели и проверяют прилегание башмаков к нижней направляющей. Нижние башмаки должны прилегать плотно на всей длине направляющей. Зазор между башмаком и верхней направляющей должен быть 0,2—0,3 мм. Зазоры проверяют путем перемещения крейцкопфа из одного Крайнего положения в другое. Величину зазоров регулируют с помощью прокладок, устанавливаемых между корпусом крейцкопфа и башмаком. [c.444]
Отсутствие третьего коренного подшипника делает конструкцию вала статически определенной. Надежность расчета вала создает предпосылки для снижения запаса прочности. Кроме того, двухопорный вал является более надежным в сборке и монтаже, так как его незначительные перекосы компенсируются за счет радиальных и аксиальных зазоров в подшипниках качения. Шатуны стальные, облегченного типа, двутаврового сечения, с нижней разъемной головкой, залитой баббитом, и с бронзовой втулкой в верхней головке. Поршни компрессора чугунные прямоточные, тронковые, с тремя уплотнительными и одним маслослизывающим кольцом.
Деформации нодшипника, вызванные перестановкой крышки коренных и шатунных подшипников на другие шейки валов и гнезда или перестановкой в перевернутом положении, или же от неравномерного натяжения гаек и шпильки, являются другой обычной причиной чрезмерных местных напряжений и преждевременного разрушения подшипника. Все крышки подшипников и шатунов перед разборкой должны быть помечены, чтобы при сборке они были поставлены в первоначальное положение. Универсальный гаечный ключ является необходимым инструментом для правильной установки подшипника, все гайки и шпильки должны быть затянуты в соответствии с инструкцией но эксплуатации данного мотора. Гайки и шпильки следует затягивать равномерно, а не сначала на одной, а потом на другой стороне. Если для затягивания обеих гаек применяется не один и тот же ключ, или если они затягиваются не попеременно, гнездо может потерять цилиндричность. Точно так же применение торцовых ключей большого внешнего диаметра может вызвать перекашивание крышек. Ошибки в выполнении этих сравнительно простых. операций могут легко привести к сокращению срока службы подшипника.
Разборку ремонтируемого компрессора начинают с демонтажа трубопроводов, подводящих воду, воздух, смазку. Разбираемые трубы для облегчения последующей сборки маркируют, затем вскрывают коренные подшипники, снимают шатуны, ползуны и крышки цилиндров, разбирают клапаны.
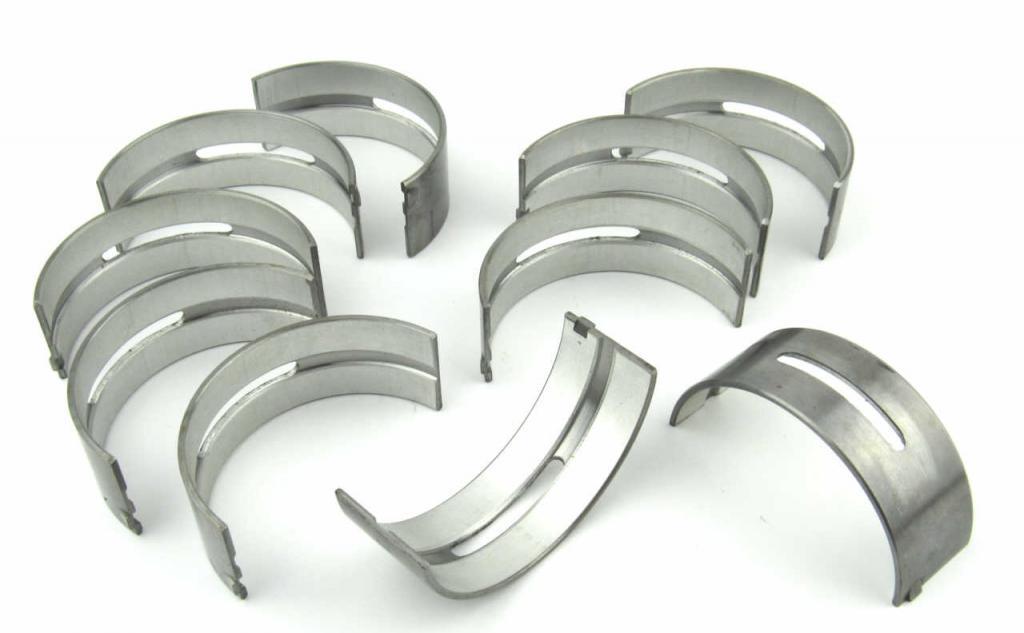
Компрессор аммиачный сальниковый бес1фейцкопфный У-образный, бустерный, прямоточный, четырехцилиндровый, с отъемными цилиндрами 4БАУ19 (лист 112) предназначен для работы в составе двухступенчатых систем в качестве I (низкой) ступени при температуре кипения не ниже —70° С. Хладагент—аммиак. Компрессор имеет развал цилиндров 90°. Вал коленчатый, горизонтальный, двухопорный с двумя шатунными шейками, расположенными под углом 180°, опирается на коренные подшипники качения. Шатуны изготовлены с разъемной нижней головкой и толстостенными вкладышами, залитыми баббитом. Механизм движения смазывается от шестеренчатого насоса затопленной конструкции, расположенного в специальном отсеке картера. Цилин- [c.48]
Система смазки механизма йеижения — циркуляционная, под давлением масло подается от насоса к коренным подшипникам, вкладышам шатунов и направляющим крейцкопфов. [c.12]
В двигателях внутреннего сгорания масло служит для смазки коренных подшипников вала, шатунных подшипников, подшипников поршневого пальца и т. д. Кроме того, масло подается на стенки цилиндра двигателя для уменьшения износа поршневых лолец и для уплотнения рабочей камеры цилиндра. [c.39]
На рис. 11 показана принципиальная схема смазки авиационного двигателя. Из масляного бака 1 масло забирается насосом и под давлением в несколько атмосфер подается к подшипникам (коренным и шатунным), системам передач и другим узлам трения. Вытекающее из подшипников масло забрызгивается центробежной силой в область поршневой и цилиндровой грзгпн. [c.40]
Проверяют ностунление масла ко всем смазываемым точкам — на коренные, шатунные и выносные подшипники, направляюн1ие ползунов. О.тиовременно проверяют уплотнение всех стыков маслопроводов и устраняют выявленные дефекты. Перепускной клапан в этот период регулируют на максимальное давление 0,5 МПа, Затем подают воду в масляные. холодильники и проверяют герметичность системы. Проверяют работу конт-рольно-нзмерительны.х приборов (манометров, термометров), уровень масла, срабатыван[ е реле давления на отключение компрессора при давлении и масла ниже нормального. Фильтр грубой очистки периодически переключают и очиш,ают отключенную секцию. Систему промывают до прекращения загрязнения фильтров грубой очистки (3—4ч), Затем регулируют давление перепускного клапана на 0,2—0,4 МПа (минимальное рабочее давление 0,15 МПа, давление срабатывания блокировки 0,12 МПа) и несколько раз проворачивают коленчатый вал компрессора. В горизонтальных машинах контролируют сток масла из картера в бак. Скопление масла в картере свидетельствует о засорении маслопровода или недостаточном его сечении. Если при прокачке масло нагревается, включают масляные холодильники. По окончании промывки масло сливают из системы, масляный бак и фильтры очищают от осадков. Заправляют чистое масло и готовят систему к работе компрессора. [c.78]
Коленчатый вал стальной, кованы11. Поверхность шатунных и коренных ншек закалена. Вал имеет косые отверстия для подвода смазки от коренных подшипников к шатунным. Мас.по к коренным подшипникам подводится по каналам в перегородках картера. [c.48]
Коленчатый вал кованный из углеродистой стали, имеет пять шатунных и шесть коренных шеек. На каждой щеке вала установлен противовес. Вал имеет отверстия для подвода масла от коренных подшипников к шатунным. На коренных шейках между подшипниками размещены разъемные кулачковые шайбы привода газовпускных клапанов. [c.247]
По сроку службы детали делятся на три группы I) быстроизнашивающиеся сменные — поршмевые кольца, набивка сальника, клапанные пластины и пружины 2) со средним сроком службы — вкладыши коренных подшипников и шатуна, пальцы шатуна и крейцкопфа 3) с длительным сроком службы — коленчатый вал, шатун, крейцкопф, цилиндры, поршни. [c.376]
Шейка коренная — подшипник1. . . Станина (корпус) — подшипник . . . Шейка шатунная — вкладыш шатуна . Вал— втулка сальникового уплотнения Расстояние между торцовыми буртами Длина вкладыша………. [c.88]
Коренные, шатунные и крейцкопфные подшипники перезаливают при выработке, более допустимой, и при отставании заливки более чем на 10% поверхности. [c.166]
Рамы обоих рядов машины являются зеркальным отображением друг друга. Левая рама отличается от правой только наличием площадки с шестеренчатым маслонасосом, подающим масло для смазки механизма движения машины. Рама — байонетного типа с круглыми параллелями 0500 мм и коренными подшипниками й—280 мм и I—420 мм. Коренные подшипники состоят из четырех вкладышей. Боковые вкладыши могут быть поджаты клиньями, с помощью которых регулируется износ подшипника. Кривошипно-шатунный механизм состоит из двух кривошипов/ — 250мм, насаженных непосредственно на коренной вал компрессора двух шатунов I — 1625 мм к й — Ъ мм 0. головками закрытого типа и клиновой подтяжкой вкладышей двух крейцкопфов закрытого типа с башмаками длиной 605 мм, шириной 340 мм и диаметром 500 мм. [c.210]
Типы вкладышей
По направлению восприятия нагрузки:
- Радиальные подшипники скольжения.
- Осевые (упорные) подшипники скольжения.
По назначению вкладыши делятся:
-
Коренные вкладыши коленвала.
Коренные вкладыши коленчатого вала. Это подшипник скольжения, обеспечивающий вращение коренных шеек коленчатого вала в постели блока цилиндров. Наши поставщики, изготавливают коренные вкладыши как комплектом на весь двигатель, так и поштучно на каждую шейку. Для удобства при монтаже выпускаются комплекты коренных вкладышей, в комплект которых входит одна опора, в которой соединены фланец упорного подшипника (полукольцо) с самим коренным вкладышем.
- Шатунные вкладыши коленвала. Шатунные вкладыши обеспечивают свободное вращение шатуна относительно шатунной шейки.
- Упорные полукольца /кольца (упорный подшипник коленвала). Это упорные подшипники скольжения, предназначенные для ограничения коленчатого вала от осевых перемещений.
-
Втулки (вкладыши) распредвала.
Втулки распредвала предназначены обеспечения вращения распределительного вала в блоке или головке блока цилиндров.
- Втулки верхней головки шатуна (ВГШ) .Втулки ВГШ обеспечивают вращение поршневого пальца относительно верхней головки шатуна.
- Втулки привода вспомогательных агрегатов. Втулки которые обеспечивают вращение, дополнительных валов ( балансирного вала , вала привода вспомогательных агрегатов, вала привода масляного насоса) в блоке цилиндров.
- Втулки вала привода коромысел клапана (оси коромысел). Втулки, обеспечивающие защиту от износа оси коромысел и сами коромысла.
По типу покрытия:
-
Цельный подшипник (вкладыш)
.
Цельные подшипники сделаны полностью из одного материала, обладающего достаточной жесткостью и износостойкостью.
- Двухслойный подшипник (биметаллический). Самый распространенный тип подшипников скольжения. Такие подшипники используются для снижения нагрузки в бензиновых и безнаддувных дизельных двигателях в легковых автомобилях. Они состоят из стальной основы, и среднего слоя, слоя антифрикционного покрытия.
- Подшипники, состоящие из трех материалов. Эти вкладыши используются, главным образом в двигателях с более тяжелой нагрузкой. Трехслойные вкладыши состоят из стального слоя являющегося основанием, слоя заливки (изоляционной прокладки) обеспечивающего оптимальные условия для прилегания третьего слоя -антифрикционного.
-
В отдельную группу выделяют трехслойные подшипники скольжения изготовленные с помощью технологии ионно-плазменного напыления (SPUTTER).
Источник: motorzona.ru
полный обзор, особенности и виды
Совершенно любой двигатель – это достаточно сложный механизм, который состоит из множества различных компонентов. Каждая деталь этого механизма обеспечивает слаженную и правильную работу всей системы в целом. При этом одни детали в большом механизме могут играть серьезные роли, а другие не настолько функциональны. Коленчатый вал, как и прочие узлы и детали, которые имеют к нему прямое отношение – это наиболее значимая часть ДВС. Именно он обеспечивает вращение маховика путем превращения энергии горения топливной смеси в механическую работу.
Одна из важных деталей в устройстве двигателя – коренной подшипник. Это небольшая деталь в форме полукольца из металла средней жесткости, имеющая специальное антифрикционное покрытие. Когда двигатель эксплуатируется в течение длительного времени, эти подшипники или вкладыши подвергаются сильному износу. В статье подробнее рассмотрим эти небольшие, но очень важные элементы ДВС.
Общее описание
Коренной подшипник двигателя или вкладыш – это не что иное, как подшипник скольжения, обеспечивающий возможность вращения коленчатого вала. Процесс вращения проходит, как результат сгорания топливной смеси в камере сгорания. При активной работе двигателя детали испытывают трение – усиленные нагрузки, а также высокий скоростной режим может вывести мотор из строя. Чтобы предотвратить эту ситуацию и максимально снизить степень трения, главные значимые элементы покрыты тонким слоем смазки – в данном случае это моторное масло. Смазываются коренные подшипники коленчатого вала посредством штатной смазочной системы. При этом масляная пленка образуется только под воздействием высокого давления масла. На рабочей поверхности вкладышей имеются отверстия, а также кольцевые канавки для подачи смазочной жидкости к шейкам коленчатого вала.
Назначение
В двигателях любой конструкции и любого типа коленчатые валы постоянно подвержены огромным нагрузкам – физическим и температурным. В процессе работы двигателя коренной подшипник удерживает коленчатый вал на оси. Работа кривошипно-шатунного механизма поддерживается и обеспечивается только этими вкладышами. Шейки коленчатого вала представлены в форме внутренних обойм, а коренные вкладыши – наружные. Эти детали, как уже было замечено, смазываются через маслоканалы.
Устройство в подробностях
Итак, тонкостенным вкладышем является изогнутая в форму полукольца стальная лента. На рабочую поверхность детали нанесен специальный антифрикционный слой. Это оловянисто-алюминиевые сплавы. В моторах с повышенными нагрузками в качестве антифрикционного покрытия применяется свинцовистая бронза.
Материалы
Коренной подшипник изготавливается из нескольких слоев. Первый слой преимущественно медный – процент содержания меди составляет от 69 до 75 процентов. Второй изготавливают из свинца – он содержится в количестве от 21 до 25 процентов. В качестве третьего слоя применяется олово – не более 4 процентов.
Размеры
Толщина коренного подшипника-вкладыша составляет около 1,5-2 миллиметров. Нужно отметить, что иногда в качестве материалов для производства этой детали может применяться другой состав – вместо меди и свинцово-оловянных сплавов используют специальные сплавы на основе алюминия.
Но стандартизация материалов для изготовления этих изделий отсутствует – каждый производитель изготавливает вкладыш по своим уникальным формулам. Единственное, что объединяет изделия между собой – это стальная лента.
Практика показывает, что используются следующие размеры слоев при производстве подшипников скольжения. Так, толщина стальной основы составляет от 0,9 миллиметра и более. Основной слой имеет толщину до 0,75 миллиметра. Слой никеля – 0,001. Слой сплава олова и свинца – 0,02-0,04 миллиметра. Оловянный слой — 0,005.
Любые сплавы, использующиеся в производстве, индивидуально подбираются для каждого мотора и рассчитываются, учитывая твердость материалов, из которых изготавливается коленчатый вал. Для повышения ресурса и работоспособности новых или ремонтных моторов рекомендуется применять только те детали, которые советует использовать производитель.
Чем тоньше коренной подшипник, тем более высокими характеристиками он обладает. Более тонкие изделия гораздо лучше лежат на постели, обладают лучшим отводом тепла, зазоры в них ниже. В современных моторах производители стараются использовать более тонкие подшипники скольжения.
Вкладыш должен быть изготовлен не только из правильно подобранных компонентов. Также очень важна и форма. Дело в том, что для правильного монтажа необходимо, чтобы подшипник имел натяг на диаметре постели коленчатого вала.
Натяг делают не только по диаметру изделия, но и по его длине. Так удается достичь отличного контакта между вкладышем-подшипником и постелью. Для валов диаметром до 40 миллиметров натяг должен составлять от 0,03 до 0,05 миллиметра. Для более крупных валов (70 миллиметров) и выше натяг составляет от 0,06 до 0,08 миллиметра.
В устройстве этой детали также имеется верхняя часть – это крышки коренных подшипников. Они фиксируются болтами или же шпильками на картере двигателя.
Производится данная деталь, а именно вкладыш, методом штамповки из стальной ленты. Штамп придает детали форму. А затем выполняется обработка торцевых частей и рабочей поверхности. Данная деталь очень точная. Допуск от номинального размера до 0,02 миллиметра на длину и до 0,005 по толщине.
Канавка и ее особенности
Чтобы к детали постоянно подавалась смазка, на всю длину коренного подшипника коленвала прорезана канавка – ширина ее составляет 3,0-4,5 миллиметров, а глубина – до 1,2. На двигателях старой конструкции данная канавка выполнялась на вкладыше и на его крышке. В современных моторах нижний вкладыш канавки не имеет. Если канавка все же имеется, тогда он отличается сниженной максимальной нагрузкой.
Отказ от нарезания канавки ведет к тому, что уровень максимальных нагрузок существенно повышается. Это позволяет снизить площадь подшипника.
Замок
Зачастую при штамповке этих деталей на нем делается замок. Устройство коренных подшипников предусматривает замок около середины. Чтобы замок был прочным, он выполняется без разрывов.
По традициям конструирования двигателей внутреннего сгорания, замки расположены в зависимости от того, в какую сторону вращается коленчатый вал. На коренном вкладыше он нужен больше для центровки при его монтаже и для подстраховки от проворачивания. Когда двигатель испытывает масляное голодание, подшипник интенсивно нагревается, и тогда его не спасут никакие замки – вкладыш проворачивается.
Основные виды
Вкладыши изготавливаются для каждого типа двигателя. Однако они различаются по внутреннему диаметру. В зависимости от модели мотора, диаметр вкладышей будет разным даже для одного конкретного мотора. Шаг размера составляет 0,25 мм. Размерный ряд – 0,25 мм, 0,5 мм, 0,75 мм и далее.
Подбирают те или иные виды подшипников по тому, в каком состоянии находятся шейки коленчатого вала. Со временем, вследствие естественного износа, шейки стачиваются. Для компенсации этого износа производителями выпускаются так называемые ремонтные коренные подшипники. Для подгонки шейки коленчатого вала под тот или иной подшипник вал шлифуют до следующего размера.
Проверка и замена
Так как коленчатый вал работает в тяжелых условиях под воздействием высоких температурных и других нагрузок, то на оси его могут удерживать только эти подшипники. Шейки выполняют роль внутренней обоймы, а вкладыши – наружных. Как и прочие элементы двигателя, эти детали также нужно периодически менять.
Меняют вкладыши чаще по причине износа, а также по причине проворота. Провернуть вкладыш может по следующим причинам. Это вязкое масло, попадание в масло абразива, малый натяг при установке крышки, недостаточная вязкость смазочного материала, эксплуатация в условиях перегрузок.
Признаки необходимости замены
Чтобы определить необходимость замены коренных подшипников, понадобится провести измерения микрометром. Но нередко удается выявить поломку визуально. Если вкладыши проворачиваются, то снятие и установка вместо них новых должна проводиться очень быстро. О том, нужна ли замена, можно понять по громкому стуку вала, снижению мощности, попыткам мотора заглохнуть.
Заключение
Итак, мы выяснили, что собой представляет коренной подшипник. Как видите, это очень важный элемент в кривошипно-шатунном механизме. От его состояния зависит работоспособность всего двигателя автомобиля. Поэтому подшипник должен быть максимально надежным и иметь высокий ресурс эксплуатации.
Справочная и техническая информация о деталях двигателей
Вкладыши и втулки (подшипники скольжения) условно можно разделить следующим образом:
- По направлению восприятия нагрузки:
- Радиальные подшипники скольжения.
- Осевые (упорные) подшипники скольжения.
- По назначению:
- Шатунные вкладыши коленвала. Это подшипники скольжения, обеспечивающие вращение шатуна относительно шатунной шейки.
- Коренные вкладыши коленвала. Это подшипники скольжения, обеспечивающие вращение коренных шеек коленчатого вала в постели блока цилиндров. Наши поставщики, изготавливают коренные вкладыши как комплектом на весь двигатель, так и поштучно на каждую шейку. Для удобства при монтаже выпускаются комплекты коренных вкладышей, в комплект которых входит одна опора, в которой соединены фланец упорного подшипника (полукольцо) с самим коренным вкладышем.
- Упорные полукольца/кольца (упорный подшипник коленвала). Это подшипники скольжения, предназначенные для ограничения осевого перемещения коленчатого вала.
- Втулки (вкладыши) распредвала. Втулки распредвала предназначены для обеспечения вращения распределительного вала в блоке или головке блока цилиндров.
- Втулки верхней головки шатуна (ВГШ). Втулки ВГШ обеспечивают вращение поршневого пальца относительно верхней головки шатуна.
- Втулки привода вспомогательных агрегатов. Втулки, которые обеспечивают вращение дополнительных валов (балансирного вала, вала привода вспомогательных агрегатов, вала привода масляного насоса) в блоке цилиндров.
- Втулки вала привода коромысел клапана (оси коромысел). Втулки, обеспечивающие защиту от износа оси коромысел и сами коромысла.
- По типу покрытия:
- Цельнометаллический (монометаллический) подшипник (вкладыш). Сделаны полностью из одного материала, обладающего достаточной жесткостью и износостойкостью.
- Двухслойный подшипник (биметаллический). Самый распространенный тип подшипников скольжения. Такие подшипники используются для снижения нагрузки в бензиновых и безнадувных дизельных двигателях в легковых автомобилях. Состоят из стальной основы, среднего слоя и слоя антифрикционного покрытия.
- Трехслойные. Вкладыши используются, главным образом, в двигателях с более тяжелой нагрузкой. Трехслойные вкладыши состоят из стального слоя являющегося основанием, слоя заливки (изоляционной прокладки) обеспечивающего оптимальные условия для прилегания третьего слоя — антифрикционного.
- SPUTTER. В отдельную группу выделяют трехслойные подшипники скольжения изготовленные с помощью технологии ионно-плазменного напыления (SPUTTER)
Зазор подшипника — ua.MotoFocus.eu
Факторы, влияющие на зазор подшипника
Зазор подшипника зависит от трех факторов: размерного допуска компонента, износа подшипника за время эксплуатации и свойств материалов, из которых изготовлен компонент.
Материалы, из которых изготавливают коленчатый вал, подшипники и картер имеют разные коэффициенты теплового расширения, что может значительно сказаться на зазоре подшипника при высоких и низких температурах. Обычно тугая посадка подшипника приводит к незначительному расширению посадочного гнезда.
Размер и допуски зазора подшипника
Допуск зазора подшипника определяется суммой допусков отдельных частей. Типичные значения допусков в случае с двигателем легкового автомобиля составляют 19 микрон для посадочного гнезда, 19 микрон для диаметра коленчатого вала и 10 микрон для толщины стенки подшипника. На легковых автомобилях также допускается минимальный зазор в 20 микрон для шатунного подшипника и в 25 микрон для коренного подшипника.
Таким образом, получаем зазор от 20 до 78 микрон для шатунного подшипника и от 25 до 83 микрон для коренного подшипника. На Рисунке 20 приведено сравнение минимального зазора шатунного подшипника легкового автомобиля с человеческим волосом. Это подтверждает тот факт, что даже мельчайшие частицы грязи, попавшие в подшипник двигателя, могут вызвать его повреждение.
Последствия зазора подшипника для двигателя
Величина зазора подшипника имеет последствия для работы двигателя. Минимальный зазор обеспечивает хорошую прилегаемость между подшипником и шейкой коленчатого вала. Такая прилегаемость является результатом износа материала в некоторых частях подшипника порядка нескольких микрон. Этот процесс приводит к снижению локального напряжения на слое скольжения, лучшей амортизации ударных нагрузок и снижению износа. Меньший зазор также снижает шумы двигателя. Недостаток маленького зазора заключается в том, что через меньший смазочный зазор проходит меньшее количество масла, т.е. подшипник охлаждается хуже, чем при большем зазоре.
Для улучшения охлаждения подшипников применяется больший зазор. В качестве примера можно привести двигатели спортивных автомобилей, использование большего зазора на которых значительно сокращает срок их эксплуатации. Не стоит и говорить о том, что после каждой гонки двигатели спортивных автомобилей перебирают полностью.
[Рис. 1]
Зазор подшипника представляет собой разность между внутренним диаметром подшипника, собранного в картере, и наружным диаметром шейки коленчатого вала. Диаметры посадочного гнезда и шейки коленчатого вала, а также и толщина стенки подшипника, должны быть пределах определенных допусков. Эт и допуски указывают на чертежах компонентов. Общая сумма максимальных допусков составляет максимальный зазор подшипника. Например, сумма минимальной толщины стенки с максимальным диаметром посадочного гнезда и минимальным диаметром шейки коленчатого вала составляет максимальный зазор подшипника. Сумма максимальной толщины стенки с минимальным диаметром посадочного гнезда и максимальным диаметром шейки коленчатого вала составляет минимальный зазор подшипника. Нормальный минимальный зазор равен 20 микрон для шатунных подшипников и 25 микрон для коренных подшипников.
ЗАЗОР : C = Di + ΔD — 2w — dw
ДОПУСК : Доп. C = Доп. Di + 2 x Доп. w + Доп. dw
Влияние температуры масла на зазор подшипника
Если картер и вал изготовлены из одного и того же материала, то по мере роста температуры масла компоненты расширяются равномерно. В этом случае при повышении температуры масла зазор подшипника остается неизменным.
Однако в том случае, если картер изготовлен из алюминия, а вал из стали, ситуация меняется (Рисунок 3). При повышении температуры алюминий расширяется больше стали, поэтому в данном случае с ростом температуры зазор увеличивается. Более того, снижается и тугая посадка. Такое явление можно компенсировать за счет увеличения припуска на длину вкладыша, который необходимо учитывать еще на этапе разработки двигателя.
При крайне низких температурах зазор может уменьшиться даже до нуля, что сделает невозможным запуск двигателя.
[Рис. 2]
Человеческий волос в сравнении с минимальным допустимым зазором в 20 микрон шатунного подшипника.
[Рис. 3]
Если картер и коленчатый вал изготовлены из одного и того же материала, то при повышении температуры масла зазор подшипника остается постоянным. Ситуация изменяется при использовании различных материалов, так как различные материалы имеют разные коэффициенты теплового расширения. На диаграмме приведены два примера для коленчатого вала, выполненного из стали. Если блок двигателя изготовлен из алюминия, то при повышении температуры масла зазор увеличивается (непрерывная линия). Если шатун изготовлен из титана (например, в двигателе гоночного автомобиля), то при повышении температуры масла зазор уменьшается (прерывистая линия).
По материалам компании Federal-Mogul
Назначение и место применения подшипников коленвала | Общество (август 2015)
Коленчатый вал является одной из самых главных деталей любого автомобиля. И в случае, когда он выходит из строя все сказывается на работе машины. Сразу начинаются стуки под капотом, снижается давление масла, падает мощность и много других негативных последствий. Основным элементом этого устройства являются подшипники коленвала, которые заставляют его вращаться и приводят в действие.
В общем, подшипники используются не только в автомобилях, а и во многих других устройствах и технике.
Что же касается именно коленвала, то в нем и нем используется два вида подшипников (выбрать их можно на сайте):
— шатунные подшипники;
— коренные подшипники.
Каждый из этих видов выполняет свои задачи.
Коренные подшипники предназначены для обеспечения свободного вращения и одновременно упора коленвала. Также они применяются для герметизации гнезд в каретке двигателя. В большинстве случаев на коленвалах двигателей устанавливаются подшипники скольжения. Они выдерживают более высокие нагрузки и могут устанавливаться способом разъемной установки, что дает им преимущество перед подшипниками качения. Если смазка подается на коленвал постоянно и без перебоев, то они могут прослужить многие годы тем самым обеспечив вам надежную работу и длительный срок эксплуатации вашего коленвала.
Подшипники качения в качестве подшипников для коленвала используются редко. В основном они устанавливаются в малолитражных автомобилях, мотоциклах, скутерах и прочей техники типа бензопил и мотоблоков.
Подшипники скольжения используются только на шатунных шейках. Все по той причине, что они могут быть разъемными и имеют небольшую толщину вкладыша.
Смазка подшипников коленвала происходит через систему смазки двигателя, так что необходимо проверять, как она работает ведь случает плохой работы подшипники не будут получать нужной смазки, а значит быстрее сносятся и выйдут из строя.
Подводя итог можно сказать, что долговечность и стабильность работы двигателя любого автомобиля напрямую зависит от коленвала и качества подшипников, которые в нем установлены. Они также наибольше со всех деталей подвергаются нагрузке и быстрому сносу, поэтому стоит покупать только качественную и проверенную продукцию, которая не подведет вас в нужный момент.
Повреждение подшипников двигателя из-за воздействия частиц · Technipedia · Motorservice
Когда инородные частицы попадают в смазочный зазор между подшипником и шейкой вала, существует большой риск повреждения подшипника. Из-за очень малой толщины смазочной пленки даже мелкие частицы могут нарушить работу и вызвать полусухое трение. Они могут застрять в скользящем слое и, следовательно, стать «безвредными». Края, созданные в процессе, сглаживаются при контакте с валом.Частицы, размер которых превышает толщину скользящего слоя, не могут быть полностью погружены. Выступающая часть вызывает износ шейки вала в виде канавок. Сильно выраженные канавки сокращают ожидаемый срок службы и могут способствовать заклиниванию подшипников. Даже во время производства или ремонта двигателя частицы могут попасть в блок двигателя и застрять. Это может иметь место, например, при очистке блока цилиндров песком или стеклом. Однако частицы грязи также могут «возникать» во время работы (например, сажа или углерод) или попадать внутрь.
Неправильное обслуживание смазочной системы или экстремальные внешние воздействия также способствуют попаданию грязи в смазочный контур. Поврежденные соседние подшипники или другие поврежденные компоненты двигателя также могут
попадать в масляный контур. Как правило, опасность повреждения из-за воздействия частиц в коренном подшипнике выше, чем в шатунном подшипнике. В шатунные подшипники подается масло
из коренных подшипников через отверстия в коленчатом валу, что означает, что масло сначала проходит через коренные подшипники (см.рис.). Более крупные частицы оседают в основном подшипнике и поэтому обычно не достигают шатунного подшипника.
Чтобы понять, откуда пришли частицы, может быть полезно проанализировать подшипник и взять образец масла.
Возможные причины
- Установка не была чистой: из-за небрежности или недостаточной очистки компонентов двигателя во время установки в блок двигателя может попасть грязь
- Остатки, такие как металлическая стружка или остатки взрывчатого вещества от производства или ремонта, могут образовывать отложения в блок двигателя, который затем отключается во время работы — часто это также отложения от навесного оборудования, такого как масляный радиатор, которые не были должным образом очищены во время ремонта двигателя
- Повреждение уплотнений в области двигателя: если уплотнение чрезмерно нагруженный или поврежденный во время установки, он больше не выполняет свою функцию, и частицы могут попасть в систему
- Отсутствие обслуживания системы смазки: превышение интервалов проверки или засорение масляных фильтров может привести к увеличению загрязнения масла
- Кавитация: частицы отламываются от материала подшипника и уносятся маслом — в зависимости от размера se может вызвать задиры или мелкое застревание в подшипнике или соседнем подшипнике
- Задиры: заедание деталей двигателя (поршни, вкладыши подшипников) приводит к попаданию большого количества частиц в смазочный контур, что, в свою очередь, может вызвать повреждение других компонентов
- Усталостное повреждение : если материал откололся от компонентов двигателя, этот отколовшийся материал может быть перенесен маслом в подшипники и может привести к их повреждению.
Однако это зависит от степени повреждения. Если, например, имеется множество крупных вмятин от частиц с начальными отметками полусухого трения из-за скопления материала, рекомендуется заменить подшипник. Вмятины из мелких частиц не ухудшают работу подшипника. В обоих случаях в любом случае следует выяснить причину:
- Очистка всех компонентов перед установкой: важно промыть все масляные отверстия в валу и корпусе перед первым запуском.Также важно очистить посадочные места подшипников, чтобы удалить мелкую стружку и частицы от производства и / или ремонта — масляные каналы навесного оборудования, такого как масляный радиатор и турбокомпрессор, также должны быть тщательно очищены.
- Проверьте уплотнения на работоспособность.
- Всегда заменяйте масляный фильтр и масло в соответствии с указаниями производителя: убедитесь, что соблюдаются интервалы проверок и используются только масло и масляные фильтры, соответствующие стандартам.
- Фильтрация всасываемого воздуха: регулярно обслуживайте фильтры; при необходимости заменить
- Проверить другие компоненты двигателя на наличие повреждений, таких как кавитация, усталость или заедание — повреждение подшипников двигателя из-за воздействия частиц часто является косвенным повреждением
- Если влияние частиц не может быть установлено, анализ поврежденных вкладышей подшипников и образец масла может дать представление: если частицы все еще находятся в подшипнике или присутствуют в масле, их химический состав может быть определен — например, если это материал из коленчатого вала, более точная проверка на наличие повреждений может выполняется здесь
Установка стержня и главного подшипника с подшипниками King Engine
Сборка двигателя— один из тех процессов, который по понятным причинам пугает большинство энтузиастов DIY-типа, и не зря.
Вы собираете воедино сердце своего двигателя, компоненты которого вращаются сотни раз в секунду , при этом подшипники двигателя и другие зазоры измеряются с точностью до тысячных и даже десятых долей дюйма в некоторых случаях! Излишне говорить, что здесь первостепенное значение имеют точность и терпение.
При установке подшипников главного двигателя и шатунных подшипников соблюдение правильных процедур снизит чрезмерный износ и трение, чтобы гарантировать долгую и здоровую жизнь вращающегося узла вашего двигателя.Для тех из вас, кто делает все возможное, чтобы сделать это самостоятельно или просто интересно узнать больше о том, что при этом задействовано, компания King Engine Bearings создала простое двенадцатиступенчатое руководство по установке стержневых и коренных подшипников!
В этой статье мы рассмотрим несколько основных шагов, описанных в руководстве King Bearing, и немного углубимся в каждую тему.
Подходящие колпачки
Один из наиболее важных шагов (и первый, упомянутый в руководстве), важность которого многие энтузиасты могут даже не осознавать, — это убедиться, что каждый шатун и крышка коренного подшипника правильно идентифицированы по положению и ориентации.
Это связано с тем, что каждая крышка идеально обработана, чтобы соответствовать сопрягаемой поверхности блока, а также форме самого отверстия подшипника. Если не будут приняты надлежащие меры предосторожности для идентификации каждой крышки, чтобы убедиться, что они не перепутались, произойдет чрезмерный износ подшипников и шейки цапфы и, возможно, даже серьезное повреждение двигателя.
Поддержание чистоты
Поддержание чистоты поверхностей, таких как коленчатый вал, сопрягаемые поверхности блока цилиндров и шейки, также чрезвычайно важно для долговечности двигателя.King рекомендует сначала использовать проволочную щетку для очистки масляных каналов и удаления любого осадка или мусора, которые накопились с течением времени, а затем очищать каждый компонент в горячей мыльной воде. После того, как деталь будет тщательно очищена, просто используйте сжатый воздух, чтобы высушить деталь и удалить остатки мусора.
Невыполнение очистки этих компонентов, вероятно, приведет к тому, что отстой и мусор будут смещаться во время демонтажа или установки, задирать поверхности подшипников и шейки, а также засорять соленоиды или масляные каналы, что приведет к повреждению или чрезмерному износу из-за масляного голодания при следующем запуске двигателя.
Затяжка колпачков и проверка люфта
Очистив и правильно смазав все компоненты, поместите коленчатый вал на верхние главные подшипники, установите главные крышки на место (убедившись, что каждая крышка вернулась в правильное положение и ориентацию), затем слегка постучите по крышке, чтобы она встала на место. до полной фиксации и затягивайте только что очищенные застежки от руки.
Чтобы выровнять упорный подшипник (который используется для ограничения осевого люфта), используйте монтировку или резиновый молоток для перемещения кривошипа вперед и назад, так чтобы он находился в крайнем переднем положении; затем, начиная с центральной главной крышки и продвигаясь оттуда, осторожно начните затягивать каждую застежку крышки с нагрузкой, указанной производителем.При правильной установке коленчатый вал должен по-прежнему свободно вращаться после затяжки каждой крышки.
Перед установкой шатунов проверка того, что осевой люфт коленчатого вала (осевой люфт) находится в пределах допуска, является одним из последних и наиболее важных шагов в закреплении вашего вращающегося узла.
Неспособность проверить осевой люфт может привести к целому ряду проблем — будет оставлено слишком мало места для расширения металлов при нагревании, что приведет к повышению температуры масляной пленки, полному отсутствию смазки или даже заедание самой рукоятки; слишком свободно, и коленчатый вал будет буквально подпрыгивать, вызывая проблемы с синхронизацией и чрезмерный износ подшипников и коленчатого вала.
Опять же, установив коленчатый вал в крайнее переднее положение, установите циферблатный индикатор на торце коленчатого вала и обнулите его. Если у вас есть алюминиевый блок, просто прикрутите небольшую стальную пластину где-нибудь в пределах досягаемости к блоку, чтобы на нее можно было установить магнитное основание циферблатного индикатора. Затем, используя монтировку или резиновый молоток, надавите на коленчатый вал в другом направлении до упора, а затем снимите показания с шкалы.
Люфт в конце от 0,002 до 0,008 дюйма обычно является предпочтительным для большинства приложений, но это значение может быть больше или меньше в зависимости от специфики вашей сборки, приложения и того, как оно будет работать.
Поэтому обязательно сверьте свои показания с заводским руководством по обслуживанию или производителем коленчатого вала для справки.
Полное руководство из двенадцати шагов, а также ряд других технических описаний, связанных с подшипниками двигателя, можно найти в полном техническом репозитории на веб-сайте King Engine Bearing.
Обслуживание коренных подшипников. (Автомобиль)
Рис. 20.49. Измерение люфта коленчатого вала.
20,7.Упор конца коленчатого вала воспринимается кромками, расположенными на одной из вкладышей коренных подшипников, которые прилегают к краю шейки коренных подшипников. Зазор между этими кромками подшипника и стороной шейки подшипника обеспечивает осевой люфт коленчатого вала. Коленчатый вал сжимается в одном направлении, так что шейка соприкасается с выступом подшипника, затем измеряется концевая пластина коленчатого вала между другой стороной шейки и выступом подшипника с помощью щупа (рис.
Измерение зазора подшипника.20,49).
Альтернативный метод измерения осевого люфта коленчатого вала заключается в том, чтобы расположить циферблатный индикатор напротив передней части коленчатого вала, а затем коленчатый вал перемещать вперед и назад. Если осевой люфт
превышает спецификации производителя, то либо кромка подшипника, либо коленчатый вал изношены. Когда устанавливается новый коренной подшипник и осевой люфт оказывается чрезмерным, то сторона шейки коленчатого вала изнашивается.Зазор шатуна или коренного подшипника проверяется полоской Plastigage на опорной поверхности коленчатого вала по всей ширине подшипника и примерно в 6 мм от центра подшипника (рис.20,50).
После установки Plastigage устанавливается крышка подшипника и затягивается до указанного значения. Коленчатый вал нельзя вращать во время установки Plastigage. После снятия крышки подшипника следует использовать шкалу на упаковке Plastigage для измерения зазора подшипника (рис.20.51).
Полоса Plastigage должна измеряться в самом широком месте, чтобы получить минимальный зазор в подшипнике. В случае изменения ширины Plastigage полоса в самом узком месте должна быть
Рис.20,50. Установка Plastigage.
Рис. 20.51. Измерение зазора подшипника с помощью шкалы Plastigage.
, что указывает максимальный зазор подшипника. Разница между двумя показаниями указывает на конусность шейки коленчатого вала или шатунного подшипника. Подшипник необходимо заменить, если зазор подшипника превышает данные производителя. Если подшипник стандартного размера не обеспечивает указанный зазор, необходимо отшлифовать шейки коренного подшипника и шатуна меньшего размера.После того, как шейки были отшлифованы до максимального занижения, необходимо заменить коленчатый вал. Вкладыши подшипников, размер которых меньше 0,254 мм, могут быть установлены, если они поддерживают зазоры подшипников в пределах спецификаций. Однако, если зазор подшипника слишком велик, или если шейки коленчатого вала неровные, шейки должны иметь меньший размер.
Хонингование линии.Внутреннее напряжение, возникающее в результате непрерывного нагрева и охлаждения из-за длительной работы двигателя, может вызвать деформацию блока, что приведет к смещению коренного подшипника.Из-за чрезмерно высоких рабочих нагрузок двигателя крышки коренных подшипников могут растягиваться. За двигателем
Рис. 20.52. Смещенные и растянутые отверстия коренных подшипников.
, главные подшипники необходимо восстановить до идеально круглого и точно выровненного состояния, чтобы обеспечить долгий срок службы подшипников. Коренные подшипники могут заедать за коленчатый вал и вращаться вместе с валом, что приведет к повреждению отверстия коренного подшипника. Смещенные и растянутые отверстия коренных подшипников — это
, показанные на рис.20,52.Для измерения конуса отверстия коренного подшипника щуп помещается под линейку, которая устанавливается на отверстия коренного подшипника в блоке.
Установка вкладыша подшипника и уплотнения.При измерении овального отверстия подшипника с помощью калибра необходимо установить крышки коренных подшипников и затянуть их в соответствии со спецификациями, отверстия хонинговать на станке для хонингования. Если отверстия коренных подшипников имеют некруглую форму, небольшое количество металла стачивается с крышек коренных подшипников с помощью специальной насадки на шатун и болгарку крышек.После установки крышек подшипников и их затяжки в соответствии со спецификациями отверстия коренных подшипников хонингуются до их первоначального диаметра.
Рис. 20.53. Установка манжетного уплотнения заднего коренного подшипника.
Многие вкладыши коренных подшипников имеют смазочную канавку в верхнем вкладыше подшипника. Масляный канал в верхнем вкладыше подшипника должен быть совмещен с масляным отверстием в отверстии коренного подшипника. В некоторых двигателях используется уплотнение заднего главного подшипника с кромкой, которое можно снять, поддев его отверткой.
При установке манжетного уплотнения внешний диаметр уплотнения должен быть покрыт подшипником Loctite Stud N ’Bearing Mount или аналогичным. Специальный установочный инструмент прижимается к задней части коленчатого вала, в то время как уплотнение устанавливается на место с помощью пластикового молотка (рис. 20.53).
В некоторых двигателях используется уплотнение заднего коренного подшипника канатного типа. Этот тип уплотнения можно врезать в верхнее отверстие коренного подшипника и крышку подшипника с помощью специального инструмента и молотка (рис. 20.54).
После установки двух половин уплотнения излишки материала уплотнения должны быть удалены промывкой с металлическими отливками.Установлен коленчатый вал и на заднюю шейку коренного коленчатого вала накладывается планка Plastigage. Болты задней крышки коренного подшипника затянуты с указанным значением. Крышка подшипника снимается и проверяется зазор подшипника. Фигуры 20,50
Рис. 20.54. Установка уплотнения коренного подшипника канатного типа.
Рис. 20.55. Анаэробный герметик на крышке заднего коренного подшипника.
Рис. 20.56. Установка крышки коренного подшипника и момент затяжки болтов.
и 20.51 можно использовать для измерения зазора подшипников Plastigage. Если зазор подшипника слишком велик, проверяется материал уплотнения между задней крышкой коренного подшипника и поверхностью блока. Перед окончательной установкой крышки заднего коренного подшипника на крышку подшипника следует нанести анаэробный герметик (рис. 20.55).
Крышки коренных подшипников должны всегда устанавливаться на свои первоначальные места с затяжкой болтов крышки до заданного значения (рис. 20.56). После того, как все основные подшипники будут затянуты в соответствии со своими техническими условиями, коленчатый вал должен свободно вращаться.Таблица размеров коренных подшипников VW типа 1 для двигателей VW Beetle и Dune Buggy
В этом посте рассматриваются размеры коренных подшипников для двигателей VW Type 1.
В этом посте есть таблица для калибровки и измерения.
Коренные подшипники — важная часть нижней части вашего двигателя VW с воздушным охлаждением.
Коренной подшипник правильного размера позволяет коленчатому валу двигаться свободно, без излишнего люфта. Коренной подшипник правильного размера также важен для поддержания надлежащего давления масла.
Мы видели, что у многих клиентов возникли проблемы с якобы восстановленными двигателями, в которых подшипники были слишком тугими или слишком ослабленными. И то, и другое в короткие сроки может привести к катастрофическому отказу.
Важно убедиться, что ваши измерения верны и соответствуют заводским спецификациям VW, чтобы ваш восстановленный двигатель выжил после первого запуска.
Измерения кривошипа Измерение диаметра Измерение тяги Фондовая 2. 164
Фондовая 0 мм (2,559 дюйма) Фондовая 0 мм (0,864 дюйма) 0,010 дюйма Меньше 2,154 0,020 «Свыше 0,50 мм (2,579 дюйма) 0,040 «Менее 1.0 мм (0,824 дюйма) 0,020 дюйма Меньше 2,144 0,040 «Более 1 мм (2,599 дюйма) 0,080 «Менее 2,0 мм (0,784 дюйма) 0,030 дюйма Меньше 2,134 0. 060 «Более
1,50 мм (2,619 дюйма) 0,040 дюйма Меньше 2,124 0,080 «Более 2,00 мм (2,639 дюйма) Для правильного определения размеров основных подшипников необходимо выполнить три измерения на корпусе двигателя VW с воздушным охлаждением.В приведенной выше таблице показаны стандартные размеры для этих измерений.
Сначала вы должны определить, повернут ли ваш коленчатый вал или его размер на складе. Если у вас новый коленчатый вал VW типа 1, будь то кривошипный механизм или стандартный коленчатый вал, он будет обработан до стандартного размера 2,164 дюйма. Если ваш коленчатый вал использовался или переточен, рекомендуется измерить его или спросить у вашего Шатуны VW с воздушным охлаждением могут быть обработаны на 0,040 дюйма меньше стандартного размера.
Мы рекомендуем приобретать коленчатый вал как можно ближе к стоковому размеру.
Следующее необходимое измерение — это отверстие коренной шейки картера двигателя. Вы можете измерить это, измерив внутренний диаметр главной шейки картера двигателя без подшипника, когда картер скреплен болтами. Вы также можете измерить шейки одной половины картера, измерив диаметр открытого конца шейки по средней линии картера двигателя.
Большинство корпусов двигателей VW Type 1 изготовлены из магния и алюминия, что делает их мягкими и подверженными деформации после многих лет эксплуатации.Это означает, что им часто требуется центрирующее отверстие, чтобы все основные шейки были идеально круглыми и одинакового размера. Коренные шейки картера двигателя могут изменяться в зависимости от работы машины или износа с годами. Всегда полезно измерить диаметр главного проходного отверстия картера бывшего в употреблении двигателя, который вы хотели бы приобрести, чтобы убедиться, что он пригоден для использования.
Стандартный размер отверстия основной цапфы — 2,559 дюйма. Их можно расточить на 0,080 дюйма. Опять же, мы рекомендуем использовать картер двигателя, из которого удалено наименьшее количество материала, насколько это возможно для увеличения срока службы.
Осевое усилие главной шейки — это последнее измерение, которое необходимо выполнить при выборе размеров коренных подшипников VW с воздушным охлаждением. Измерение тяги определяется путем измерения толщины последней главной шейки со стороны маховика двигателя. Стандартное значение тяги составляет 0,864 дюйма, и его можно уменьшить на 0,080 дюйма.
Упорный коренной подшипник принимает на двигатель переднюю и заднюю нагрузку, также известную как тяга, от сцепления и трансмиссии. Тяга двигателя VW типа 1 или типа 4 может изнашиваться из-за возраста, неправильной настройки осевого люфта маховика или жесткого вождения с тяжелым сцеплением.С учетом сказанного может потребоваться разное количество времени, чтобы так или иначе изнашивать тягу.
Заводские характеристики тяги с установленным маховиком составляют 0,003–0,005 дюйма.
Обычная проверка работоспособности, которую многие производители двигателей и гайки VW любят проводить на двигателе, — это захватить шкив кривошипа двигателя, потянуть его вперед и толкнуть назад, чтобы увидеть, есть ли какой-либо заметный люфт. Если вы чувствуете заметный люфт, скорее всего, упор изношен на подшипник или корпус.
И последнее замечание: размеры коренных подшипников могут измеряться в дюймах или миллиметрах.Таблица преобразования прилагается, чтобы ваши измерения соответствовали метрической или американской системе измерения.
Метрическая система в дюймы Преобразование ,25 мм = 0,010 дюйма 1,00 мм = 0,040 дюйма . 50 ММ = 0,020 дюйма
1,50 мм = 0,060 дюйма .75 MM = .030 « 2,00 мм = 0,080 дюйма Наука, лежащая в основе современных подшипников двигателя
Они выглядят достаточно просто. Это просто полукруги из тонкого металла, обычно с полуматовой отделкой.В настоящее время на некоторых даже нанесено покрытие. На самом деле эти простые на вид подшипники двигателя являются результатом сложных научных исследований и производственных процессов. Понимание функции, истории и способов оптимизации работы и надежности этих подшипников является обязательным условием для любого серьезного разработчика программы двигателя.
Автор: Майкл Феррара // Изображения предоставлены ACL Distribution, MAHLE Clevite и King Race Bearings
ДСПОРТ Выпуск № 150Каковы ваши функции?
Тонкостенные разъемные радиальные подшипники скольжения, или то, что мы называем «стержневыми» и «коренными подшипниками», выполняют в двигателе три важные функции.
Прежде всего, эти подшипники обеспечивают заменяемую поверхность износа. Если бы двигатель был спроектирован для работы без этих подшипников, блок цилиндров, коленчатый вал и шатуны испытали бы износ. Коренные шейки блока, коренные и шатунные штифты коленчатого вала, а также шейка шатуна большого конца шатуна будут не только изнашиваться, но и иметь большую вероятность заедания (заедание всегда более вероятно, когда похожие металлы соприкасаются друг с другом. ). Ремонт двигателя без коренного и стержневого подшипников просто невозможен.Помимо обеспечения заменяемой поверхности износа, стержень и основные подшипники также обеспечивают оптимальную поверхность для масла под давлением, позволяющего выдерживать нагрузки вращающегося узла. Когда в двигателе течет масло, именно масляная пленка между штифтами и подшипниками фактически выдерживает нагрузку. Поверхность подшипника должна быть достаточно прочной, чтобы сохранять правильную геометрию и выдерживать усталость (растрескивание или отслаивание).
Наконец, подшипники также должны иметь возможность захватывать твердые частицы, которые в противном случае повредили бы шток или основные штифты коленчатого вала.Для этого необходимо, чтобы поверхность подшипника была достаточно мягкой, чтобы более твердые частицы могли оставаться на своих местах.
История подшипников двигателя
В 1839 году Исаак Бэббит из Массачусетса разработал уникальный металлический сплав, обладающий высокой устойчивостью к истиранию (заедание и растяжение двух металлических поверхностей, контактирующих друг с другом). Его баббитовый материал стал основным материалом для подшипников скольжения, используемых в различных сферах. Материал обладал отличной податливостью (способность обходить ограничения производственного оборудования той эпохи) и отличной способностью к заливке (способность отбрасывать более твердые частицы на поверхности подшипника, а не повредить штифт).[pullquote] ЧЕМ ТОНЧЕ СЛОЙ МЯГКОГО МАТЕРИАЛА БЭББИТТА, ТЕМ ДЛИННЕЕ БУДЕТ ИЗНОСИТЬСЯ.
[/ pullquote] У суперсплава действительно была слабость. «Мягкий» материал изнашивается. Фактически, ранние штанги и главные крышки должны были быть оснащены прокладками, которые удалялись, чтобы уменьшить зазор. Это было время, когда в двигателе тоже не хватало масляных фильтров. Со временем выяснилось, что чем тоньше слой мягкого баббитового материала, тем дольше он изнашивается. Реализация привела к разработке подшипников с промежуточным слоем между стальным несущим вкладышем и тонким верхним слоем баббита.
Все коренные и стержневые подшипники имеют стальную основу. Промежуточный слой медь / свинец либо отливают, либо спекают на стальном слое. Перед слоем баббита часто бывает пограничный слой никеля (не показан). Большинство подшипников на этом останавливаются, но некоторые даже добавляют сверху слой молибденового / графитового покрытия.
Уровни производительности
Все подшипники современных двигателей имеют многослойную конструкцию. Каждый слой различается по составу и толщине для достижения желаемых результатов.
Стальной поддерживающий слой обеспечивает плотную посадку с натягом на шейку и помогает определить форму подшипника. На подшипнике, имеющем общую толщину 1,5 мм, стальная основа обычно составляет около 0,70–0,75 мм (45–50% от общей толщины). Промежуточный слой по толщине аналогичен стальной оболочке. Фактически, этот слой обычно заливается (иногда спекается в более дешевых подшипниках) на стальной корпус. При поставке изготовителю подшипника непрерывный рулон этого материала основы и промежуточного материала будет использоваться для изготовления подшипника.Рулон будет разрезан на полоски, которые штампуются в формы, чтобы они приняли нужную форму. Примерно после семи или восьми операций механической обработки подшипник с соответствующими размерами будет готов для гальванических операций, на которые будут нанесены барьерный и верхний (баббитовый) слои. Барьерный слой из никелевого сплава предотвращает диффузию свинца из верхнего слоя в промежуточный слой, обеспечивая покрытие (баббит) предсказуемого состава.
Почти все подшипники содержат этот барьерный слой, за исключением стержневых подшипников Vandervell / Clevite серии V.В этих подшипниках используется уникальная свинцово-индийская накладка (большинство накладок — это свинец, олово и медь), на которую не влияет диффузия свинца между промежуточным слоем и накладкой.
В основном подшипники скольжения в автомобилях используются для подшипников коленчатого вала, шарниров поршневых пальцев, балансирных валов и коленчатых валов. Это могут быть либо половинки вкладышей, в которых для сборки требуется разъем (например, подшипники коленчатого вала), либо втулки, которые могут быть вставлены без разъема (например, подшипники коленчатого вала).g., шарниры поршневых пальцев). Для подшипников двигателя масло обычно подается под давлением от масляного насоса через узел фильтра / охладителя в главный масляный канал, который проходит вдоль двигателя, а затем в главный подшипник, как показано на рисунке 8.1. Отверстие для подачи масла в верхнем основном подшипнике обычно входит в канавку, так что отверстие в шейке коленчатого вала может транспортировать масло к подшипнику шатуна в шатуне.
Подача масла к узкому концу шарнирного соединения и бобышке поршневого пальца обычно осуществляется за счет «брызг» с боков или через внутренние отверстия в шатуне или поршне.В процессе проектирования сборка должна рассматриваться как «система» с адекватной подачей смазки и формой зазора — подшипники часто являются «предохранителями», где любые недостатки становятся очевидными при повреждении, например, заедании двигателя. Нормальный проектный диапазон для опорных подшипников обозначается следующим образом:
• Максимальная удельная нагрузка (MSL): MSL — это приложенная нагрузка, деленная на расчетную площадь (длина × диаметр). Типичные значения составляют 30–70 МПа для «биметаллических» подшипников и 60–100 МПа для «триметаллических» подшипников.Перегрузка может привести к потере футеровки из-за механизмов усталости или «обжатия» / пластического течения материала вблизи краев.
• Минимальная толщина масляной пленки: Здесь масляная пленка не может полностью разделить поверхности, а противоположные поверхности скольжения или вершины неровностей поверхности начинают контактировать друг с другом с возможным износом, температурой вспышки или заеданием.
Типичные значения шероховатости поверхности ( Ra ) составляют приблизительно 0,2 мкм для шейки коленчатого вала и 0.05 мкм для поршневых / поршневых пальцев. Высокие температуры могут быть результатом «смешанных» или «граничных» условий смазки, поскольку коэффициент трения для смазываемого контакта примерно на 1 или 2 порядка меньше, чем для «сухого» трения. При высоких оборотах двигателя (6000–7000 об / мин, бензиновые двигатели) локальные участки тонкой пленки могут привести к выделению тепла и возникновению горячих точек в масле из-за сильного сдвига.
• Сдвиг масла в зазоре: Это может привести к дальнейшему увеличению температуры поверхности подшипника примерно на 20–50 ° C по сравнению с температурой подачи, что может привести к перегреву подшипника.Во время работы двигателя температура масляного картера или масла в подшипниках может достигать примерно 100–155 ° C. При некоторых условиях скорости нагрузки возможны температуры поверхности подшипника 190 ° C или более, когда некоторые компоненты сплава подшипника, такие как олово, могут начать плавиться, что приведет к заклиниванию двигателя, если поддерживаются высокие температуры.
Продолжительные периоды работы двигателя при высоких температурах также могут привести к ухудшению качества масла, когда сажеобразный материал или лаки могут забивать масляные каналы и оставлять темный осадок на рабочей поверхности подшипника.
(PDF) Анализ гидродинамических нагрузок на рабочие характеристики коренных подшипников двигателя
7. Тан Б. Расчет динамических коэффициентов
коренных подшипников скольжения в шестицилиндровом рядном дизельном двигателе. SAE
Technical Paper 2007-01-1968, 2007.
8. D’Agostino V, Ruggiero A и Senatore A. Неустойчивые
Силы масляной пленки в пористых подшипниках: Анализ влияния проницаемости
на линейный ротор стабильность. Meccanica
2008; 44 (2): 207–214.
9. Зарбане К., Зеглул Т. и Хаджам М. Численное исследование поведения смазочной пленки
при периодической нагрузке
. Tribol Int 2011; 44 (12): 1659–1667.
10. Эбрат О., Мурелатос З.П., Влахопулос Н.
и др. Масляная пленка
динамические характеристики для эластогидродинамического анализа подшипников скольжения
на основе конечно-разностной формулы. Технический документ SAE 2003-01-1669, 2003.
11. Cheng M, Meng G и Jing J.Нелинейная динамика системы
ротор-подшипник-уплотнение. Arch Appl Mech 2006;
76 (3–4): 215–227.
12. Шин Ю.Т. и Лю Ю.Х. Количественный показатель для анализа вибрации подшипников
на основе резонансных мод механической системы
. J Intell Manuf 2009;
23 (2): 189–203.
13. EI-Marhomy AA. Динамика и устойчивость упругих
систем подшипник вал с нелинейными параметрами подшипника
. Тепломассообмен 1999; 35: 334–344.
14. Курка П.Г., Изука Дж. Х. и Паулино КЛГ. Динамические нагрузки
поршневых компрессоров с гибкой опорой —
мин. Mech Mach Theory 2012; 52: 130–143.
15. Cruz RFd и Galli LAF. Сравнение гидродинамического
и эластогидродинамического моделирования применили
к подшипникам скольжения.
Технический документ SAE 2010-36-
0360, 2010.
16. Sun J, Zhao X и Wang H. Анализ смазки подшипников коленчатого вала
с учетом деформации коленчатого вала.
Технический документ SAE 2011-01-0613, 2011.
17. Пинкус О. и Сттернлихт Б. Теория гидродинамической смазки
. Нью-Йорк: McGraw Hill Inc, 1961.
18. Саллес Б., Биттенкур М.Л., Круз Р. и др. Радиальная поверхность
Оптимизация подшипников для двигателей внутреннего сгорания.
Технический документ SAE 2009-36-0191, 2009.
19. Дурак Э., Курбаног
lu C, Bıyıklıog
lu A, et al.
Измерение силы трения и воздействия масляного усилителя
в подшипниках скольжения двигателя в условиях динамической нагрузки.
.Tribol Int 2003; 36 (8): 599–607.
20. Sun J и Gui CL. Влияние состояния смазки подшипника
на прочность коленчатого вала. J Tribol 2007; 129 (4):
887–894.
21. Оффнер Г. Моделирование потерь мощности на трение внутренних двигателей внутреннего сгорания
с учетом смешанной смазки
радиальный ползун, осевой ползун и контакты поршня и гильзы.
Трибол Транс 2013; 56 (3): 503–515.
22. Джагадиша К.М., Нагараджу Т., Шарма С.К. и др.3D
Влияние шероховатости поверхности на переходную неньютоновскую реакцию
динамически нагруженных подшипников скольжения. Трибол
Транс 2012; 55 (1): 32–42.
23. Леопольд Дж. Контроль качества поверхности с использованием биокомпьютерных алгоритмов
. J Intell Manuf 1998; 9: 377–382.
24. Денкена Б. и Хеннинг Х. Многокритериальное определение размеров
операций твердой чистовой обработки с учетом взаимозависимостей между процессами
. J Intell Manuf 2010; 23 (6):
2333–2342.
25. Шао К., Лю CW и Би Фр. Моделирование вибрации дизельного двигателя
на основе многомерной динамики. Appl Mech
Mater 2011; 97–98: 706–711.
26. Озаса Т., Нийзэки М., Сакураи С. и др. Смазка ana-
лизис шатунного подшипника с использованием моделирования цикла бензиновых двигателей
с вариацией A / F.
SAE Technical
Paper 2011-01-2118, 2011.
27. Fatu A, Hajjam M и Bonneau D. Новая модель термоэластогидродинамической смазки
в динамически нагруженных подшипниках скольжения
.J Трибол-Транс ASME 2006;
128: 85–95.
Приложение
Обозначение
Радиальный зазор (м)
Эксцентриситет
F
x
, F
y
динамическая нагрузка, действующая на ось (Н)
gacceleration (смещение / ускорение)
2
)
Толщина пленки жидкости (м)
Безразмерная толщина пленки
h
max
максимальная толщина пленки жидкости (м)
h
min
минимальная толщина пленки жидкости )
фунт Длина подшипника (м)
Масса материала (кг)
n
потери
общий коэффициент трения
безразмерное давление пленки
Давление пленки (Па)
000
qd b
радиус опоры (м)
R
j
радиус шейки (м)
R
x
, R
y
гидродинамическая реакция
tвремя (с)
u, v, wкомпоненты скорости в
окружности
x, y, zкоординаты в окружном, радиальном
и осевом направлении
допуск
«относительный эксцентриситет
» динамическая вязкость масла (кг / мс)
!
b
Угловая скорость подшипника (рад / с)
!
j
угловая скорость шейки (рад / с)
‘угол положения (град) (рисунок 1)
плотность масла (кг / м
3
)
угловая координата (рисунок 1)
Подписи
bBearing
jjournal
676 Proc IMechE Part J: J Engineering Tribology 229 (6)
в TULANE UNIV 29 июня 2015 г.