ΠΡΠΎ ΡΠ°ΠΌΡΠΉ ΡΠΌΠ½ΡΠΉ ΠΊΠΈΡΠ°ΠΉΡΠΊΠΈΠΉ ΠΊΡΠΎΡΡΠΎΠ²Π΅Ρ Π½Π°Β ΠΌΠΎΠ΅ΠΉ ΠΏΠ°ΠΌΡΡΠΈ: Π½Π°ΠΏΡΠΈΠΌΠ΅Ρ, Π»ΡΠΊ Π²Β ΠΊΡΡΡΠ΅ Π°Π²ΡΠΎΠΌΠ°ΡΠΈΡΠ΅ΡΠΊΠΈ Π·Π°ΠΊΡΠΎΠ΅ΡΡΡ ΠΏΡΠΈ ΠΏΠ΅ΡΠ²ΡΡ ΠΊΠ°ΠΏΠ»ΡΡ Π΄ΠΎΠΆΠ΄Ρ, Π°Β Π½Π°Β ΡΠ΅Π½ΡΡΠ°Π»ΡΠ½ΠΎΠΌ Π΄ΠΈΡΠΏΠ»Π΅Π΅ ΠΌΠΎΠΆΠ½ΠΎ ΠΎΡΠ·Π΅ΡΠΊΠ°Π»ΠΈΡΡ Π―Π½Π΄Π΅ΠΊΡ.ΠΠ°Π²ΠΈΠ³Π°ΡΠΎΡ ΡΠΎΒ ΡΠΌΠ°ΡΡΡΠΎΠ½Π°.
ΠΡΠΎ ΡΠ΅ΡΠ²Π΅ΡΡΡΠΉ ΠΊΡΠΎΡΡΠΎΠ²Π΅Ρ, ΠΊΠΎΡΠΎΡΡΠΉ ΠΊΠΎΠΌΠΏΠ°Π½ΠΈΡ Changan ΠΏΡΠΈΠ²ΠΎΠ·ΠΈΡ Π²Β Π ΠΎΡΡΠΈΡ. ΠΡΠ·ΠΎΠ² Π½ΠΎΠ²ΠΎΠ³ΠΎ CS55 ΡΠΈΡΠΎΠ²Π°Π»ΠΈ ΠΈΡΠ°Π»ΡΡΠ½ΡΠΊΠΈΠ΅ Π΄ΠΈΠ·Π°ΠΉΠ½Π΅ΡΡ, ΠΈΒ ΠΏΠΎΠ»ΡΡΠΈΠ»ΠΎΡΡ Ρ ΠΎΡΠΎΡΠΎ. ΠΠΊΡΡΠ΅ΡΡΠ΅Ρ ΡΠ΄Π΅ΡΠΆΠ°Π½Π½ΡΠΉΒ β ΡΠ°ΠΊΠΎΠΉ Π΄ΠΎΠ»Π³ΠΎ Π½Π΅ ΡΡΡΠ°ΡΠ΅Π΅Ρ. ΠΠΎΒ Β«ΠΏΠ΅ΡΠ΅ΡΒ» Π΅ΡΡΡ: Π΄ΠΈΡΡΡΠ·ΠΎΡ ΠΏΠΎΠ΄Β Π·Π°Π΄Π½ΠΈΠΌ Π±Π°ΠΌΠΏΠ΅ΡΠΎΠΌ, ΡΠΏΠΎΠΉΠ»Π΅Ρ Π½Π°Β ΠΊΡΡΡΠ΅, Π°ΠΊΡΠ»ΠΈΠΉ ΠΏΠ»Π°Π²Π½ΠΈΠΊ Π°Π½ΡΠ΅Π½Π½Ρ ΠΈΒ 18-Π΄ΡΠΉΠΌΠΎΠ²ΡΠ΅ ΠΊΠΎΠ»Π΅ΡΠ°.
ΠΠ½ΡΠ΅ΡΡΠ΅Ρ
ΠΠ°ΡΠ΅ΡΠΈΠ°Π»Ρ ΠΏΠΎΒ ΡΠ΅ΠΌΠ΅
ΠΠ½, ΠΊΠ°ΠΊ ΠΈΒ Π²Π½Π΅ΡΠ½ΠΎΡΡΡ, Π²ΡΠ΄Π΅ΡΠΆΠ°Π½ Π²Β Π»Π°ΠΊΠΎΠ½ΠΈΡΠ½ΠΎΠΌ ΠΊΠ»ΡΡΠ΅. Π Π΅ΡΠΏΠ΅ΠΊΡ Π·Π°Β ΠΏΡΠΈΡΡΠ½ΡΠ΅ Π³Π»Π°Π·Ρ ΠΊΡΠ°ΡΠ½ΡΠ΅ Π°ΠΊΡΠ΅Π½ΡΡ, ΡΠ°Π·Π±Π°Π²Π»ΡΡΡΠΈΠ΅ ΡΠ΅ΡΠ½ΡΠΉ Π΄ΠΎΠΌΠΈΠ½ΠΈΡΡΡΡΠΈΠΉ ΡΠ²Π΅Ρ. ΠΡΠ³ΠΊΠΈΠΉ ΠΏΠ»Π°ΡΡΠΈΠΊ Π²Β ΠΎΡΠ΄Π΅Π»ΠΊΠ΅, ΠΊΠΎΠ½Π΅ΡΠ½ΠΎ, Π²ΡΡΡΠ΅ΡΠ°Π΅ΡΡΡ Π½Π΅Β Π²Π΅Π·Π΄Π΅, Π½ΠΎΒ Π·Π°ΡΠΎ ΡΠ°ΠΌ, Π³Π΄Π΅ Π½Π°Π΄ΠΎ: Π²Π΅ΡΡ Π½ΡΡ ΡΠ°ΡΡΡ ΠΏΠ΅ΡΠ΅Π΄Π½Π΅ΠΉ ΠΏΠ°Π½Π΅Π»ΠΈ, ΠΏΠΎΠ΄Π»ΠΎΠΊΠΎΡΠ½ΠΈΠΊΠΈ ΠΈΒ Π±ΠΎΠΊΠΎΠ²ΡΠ΅ ΡΠ΅Π³ΠΌΠ΅Π½ΡΡ ΡΠ΅Π½ΡΡΠ°Π»ΡΠ½ΠΎΠ³ΠΎ ΡΡΠ½Π½Π΅Π»Ρ.ΠΠΏΠ΅ΡΠ°ΡΠ»ΠΈΠ»ΠΎ ΠΊΠΎΠ»ΠΈΡΠ΅ΡΡΠ²ΠΎ Π΅ΠΌΠΊΠΎΡΡΠ΅ΠΉ ΠΈΒ Π½ΠΈΡ: ΡΒ Π½Π°ΡΡΠΈΡΠ°Π» 35Β (!) ΡΡΡΠΊ. ΠΡΠ΄Π΅Π»ΡΠ½ΠΎΠ΅ ΡΠΏΠ°ΡΠΈΠ±ΠΎ Π·Π°Β ΠΎΠ³ΡΠΎΠΌΠ½ΡΠΉ Π±ΠΎΠΊΡ Π½Π°Π΄Β ΡΠ΅Π½ΡΡΠ°Π»ΡΠ½ΠΎΠΉ ΠΊΠΎΠ½ΡΠΎΠ»ΡΡ ΠΈΒ ΠΏΡΡΠΌΠΎ-ΡΠ°ΠΊΠΈ ΠΏΠ΅ΡΠ΅ΡΡ Π²Β Π½Π΅Π΄ΡΠ°Ρ ΠΏΠΎΠ΄Π»ΠΎΠΊΠΎΡΠ½ΠΈΠΊΠ°. ΠΡΠΈΡΠ΅ΠΌ Π΄Π½ΠΎ ΡΡΡΠ»Π°Π½ΠΎ ΠΌΡΠ³ΠΊΠΈΠΌ ΠΌΠ°ΡΠ΅ΡΠΈΠ°Π»ΠΎΠΌ, ΡΠ°ΠΊ ΡΡΠΎ ΠΌΠ΅Π»ΠΎΡΠ΅Π²ΠΊΠ° Π½Π΅Β Π±ΡΠ΅Π½ΡΠΈΡ. ΠΡΡΡΠΊΠ° ΠΏΠ΅ΡΡΠ°ΡΠΎΡΠ½ΠΎΠ³ΠΎ ΡΡΠΈΠΊΠ° ΠΈΒ ΠΏΠΎΡΠΎΠ»ΠΎΡΠ½ΡΠ΅ ΡΡΡΠΊΠΈΒ β ΡΒ ΠΌΠΈΠΊΡΠΎΠ»ΠΈΡΡΠΎΠΌ.
Π§Π΅Π³ΠΎ ΡΒ Π±ΠΎΠ»ΡΡΠΈΠ½ΡΡΠ²Π° ΠΎΠ΄Π½ΠΎΠΊΠ»Π°ΡΡΠ½ΠΈΠΊΠΎΠ² Π½Π΅Ρ, ΡΠ°ΠΊ ΡΡΠΎ Π΄Π²ΡΡ Π·ΠΎΠ½Π½ΠΎΠ³ΠΎ ΠΊΠ»ΠΈΠΌΠ°Ρ-ΠΊΠΎΠ½ΡΡΠΎΠ»Ρ ΠΈΒ Π»ΡΠΊΠ° Π²Β ΠΊΡΡΡΠ΅. ΠΠ°Β Π½Π΅ ΠΏΡΠΎΡΡΠΎΠ³ΠΎ, Π°Β ΡΠΌΠ½ΠΎΠ³ΠΎ: ΡΒ ΠΏΠ΅ΡΠ²ΡΠΌΠΈ ΠΊΠ°ΠΏΠ»ΡΠΌΠΈ Π΄ΠΎΠΆΠ΄Ρ ΠΎΠ½Β Π°Π²ΡΠΎΠΌΠ°ΡΠΈΡΠ΅ΡΠΊΠΈ Π·Π°ΠΊΡΡΠ²Π°Π΅ΡΡΡ… ΡΠ°ΠΌ!
ΠΠ½ΡΠ΅ΡΡΠ΅Ρ ΠΏΠΎΠ΄ΠΊΡΠΏΠ°Π΅Ρ Π½Π΅Β ΡΠΎΠ»ΡΠΊΠΎ ΡΠΎΠ²ΡΠ΅ΠΌΠ΅Π½Π½ΠΎΠΉ Π°ΡΡ ΠΈΡΠ΅ΠΊΡΡΡΠΎΠΉ, Π½ΠΎΒ ΠΈΒ Π±ΠΎΠ³Π°ΡΡΠΌ ΠΎΡΠ½Π°ΡΠ΅Π½ΠΈΠ΅ΠΌ.ΠΠ½ΡΠ΅ΡΡΠ΅Ρ ΠΏΠΎΠ΄ΠΊΡΠΏΠ°Π΅Ρ Π½Π΅Β ΡΠΎΠ»ΡΠΊΠΎ ΡΠΎΠ²ΡΠ΅ΠΌΠ΅Π½Π½ΠΎΠΉ Π°ΡΡ ΠΈΡΠ΅ΠΊΡΡΡΠΎΠΉ, Π½ΠΎΒ ΠΈΒ Π±ΠΎΠ³Π°ΡΡΠΌ ΠΎΡΠ½Π°ΡΠ΅Π½ΠΈΠ΅ΠΌ.
ΠΠ΄ΠΎΡΠΎΠ²ΠΎ, ΡΡΠΎ Changan ΠΎΡΡΠ°Π»ΡΡ Π²Π΅ΡΠ΅Π½ ΠΎΠ»Π΄ΡΠΊΡΠ»ΡΠ½ΡΠΌ Π°Π½Π°Π»ΠΎΠ³ΠΎΠ²ΡΠΌ ΠΏΡΠΈΠ±ΠΎΡΠ°ΠΌ. ΠΒ ΡΠΈΡΠ°Π΅ΠΌΠΎΡΡΠΈ ΡΡΠΈΡΡΠΎΠ² ΠΈΒ ΡΠ°ΡΠΏΠΎΠ»ΠΎΠΆΠ΅Π½ΠΈΡ ΡΠΊΠ°Π» Π½Π΅ ΠΏΡΠΈΠ΄Π΅ΡΠ΅ΡΡΡΡ. ΠΠ΄ΠΎΡΠΎΠ²ΠΎ, ΡΡΠΎ Changan ΠΎΡΡΠ°Π»ΡΡ Π²Π΅ΡΠ΅Π½ ΠΎΠ»Π΄ΡΠΊΡΠ»ΡΠ½ΡΠΌ Π°Π½Π°Π»ΠΎΠ³ΠΎΠ²ΡΠΌ ΠΏΡΠΈΠ±ΠΎΡΠ°ΠΌ. ΠΒ ΡΠΈΡΠ°Π΅ΠΌΠΎΡΡΠΈ ΡΡΠΈΡΡΠΎΠ² ΠΈΒ ΡΠ°ΡΠΏΠΎΠ»ΠΎΠΆΠ΅Π½ΠΈΡ ΡΠΊΠ°Π» Π½Π΅Β ΠΏΡΠΈΠ΄Π΅ΡΠ΅ΡΡΡΡ. | Π Π°Π·Π΄Π΅Π»ΡΠ½ΡΠΉ ΠΊΠ»ΠΈΠΌΠ°Ρ-ΠΊΠΎΠ½ΡΡΠΎΠ»Ρ ΡΠ½Π°Π±ΠΆΠ΅Π½ ΠΈΠΎΠ½ΠΈΠ·Π°ΡΠΎΡΠΎΠΌ Π²ΠΎΠ·Π΄ΡΡ Π°Β β Π²Β ΡΠ°Π»ΠΎΠ½Π΅ CS55 Π²ΡΠ΅Π³Π΄Π° Π΄ΡΡΠΈΡΡΡ Π»Π΅Π³ΠΊΠΎ. Π Π°Π·Π΄Π΅Π»ΡΠ½ΡΠΉ ΠΊΠ»ΠΈΠΌΠ°Ρ-ΠΊΠΎΠ½ΡΡΠΎΠ»Ρ ΡΠ½Π°Π±ΠΆΠ΅Π½ ΠΈΠΎΠ½ΠΈΠ·Π°ΡΠΎΡΠΎΠΌ Π²ΠΎΠ·Π΄ΡΡ Π°Β β Π²Β ΡΠ°Π»ΠΎΠ½Π΅ CS55 Π²ΡΠ΅Π³Π΄Π° Π΄ΡΡΠΈΡΡΡ Π»Π΅Π³ΠΊΠΎ. | ΠΡΠΎΡΠ΅Π·ΠΈ Π½Π°Β ΡΡΠ½Π½Π΅Π»Π΅ Π»Π΅Π³ΠΊΠΎ ΠΏΠΎΠ³Π»ΠΎΡΠ°ΡΡ ΠΏΠ°ΡΠΊΠΎΠ²ΠΎΡΠ½ΡΠ΅ ΡΠ°Π»ΠΎΠ½Ρ, Π²ΠΈΠ·ΠΈΡΠΊΠΈ ΠΈΒ ΡΠ°Π·Π½ΠΎΠΎΠ±ΡΠ°Π·Π½ΡΠ΅ ΠΏΠ»Π°ΡΡΠΈΠΊΠΎΠ²ΡΠ΅ ΠΊΠ°ΡΡΠΎΡΠΊΠΈ. ΠΡΠΎΡΠ΅Π·ΠΈ Π½Π°Β ΡΡΠ½Π½Π΅Π»Π΅ Π»Π΅Π³ΠΊΠΎ ΠΏΠΎΠ³Π»ΠΎΡΠ°ΡΡ ΠΏΠ°ΡΠΊΠΎΠ²ΠΎΡΠ½ΡΠ΅ ΡΠ°Π»ΠΎΠ½Ρ, Π²ΠΈΠ·ΠΈΡΠΊΠΈ ΠΈΒ ΡΠ°Π·Π½ΠΎΠΎΠ±ΡΠ°Π·Π½ΡΠ΅ ΠΏΠ»Π°ΡΡΠΈΠΊΠΎΠ²ΡΠ΅ ΠΊΠ°ΡΡΠΎΡΠΊΠΈ. |
Π‘Π²ΡΠ·Ρ ΡΒ ΡΠ΅Π»Π΅ΡΠΎΠ½ΠΎΠΌ
ΠΠΎΡΠ°Π΄ΠΊΡ Π·Π°Β ΡΡΠ»Π΅ΠΌ ΡΒ Π½Π°ΡΠ΅Π» Π±ΡΡΡΡΠΎ. ΠΒ ΠΎΡΠ»ΠΈΡΠΈΠ΅ ΠΎΡΒ Π±ΠΎΠ»ΡΡΠΈΠ½ΡΡΠ²Π° ΠΊΠΈΡΠ°ΠΉΡΠΊΠΈΡ ΠΊΠΎΠ½ΠΊΡΡΠ΅Π½ΡΠΎΠ², ΡΡΠ»Π΅Π²Π°Ρ ΠΊΠΎΠ»ΠΎΠ½ΠΊΠ° Π·Π΄Π΅ΡΡ ΡΠ΅Π³ΡΠ»ΠΈΡΡΠ΅ΡΡΡ Π²Β Π΄Π²ΡΡ ΠΏΠ»ΠΎΡΠΊΠΎΡΡΡΡ . Π‘ΠΈΠ΄Π΅Π½ΡΠ΅ ΠΏΡΡΡΡ ΠΈΒ Π±Π΅Π· ΡΠ»Π΅ΠΊΡΡΠΎΠΏΡΠΈΠ²ΠΎΠ΄ΠΎΠ², Π½ΠΎΒ Π΄ΠΈΠ°ΠΏΠ°Π·ΠΎΠ½Ρ ΡΠ΅Π³ΡΠ»ΠΈΡΠΎΠ²ΠΎΠΊ ΡΠ°ΡΡΡΠ½ΡΡΡΠ΅. Π₯ΠΎΡΠΎΡΠ° ΠΈΒ ΠΎΠ±Π·ΠΎΡΠ½ΠΎΡΡΡ: ΡΡΠ°Π²Π½ΠΈΡΠ΅Π»ΡΠ½ΠΎ ΡΠΎΠ½ΠΊΠΈΠ΅ ΡΡΠΎΠΉΠΊΠΈ ΠΊΡΡΡΠΈ, ΠΊΡΡΠΏΠ½ΡΠ΅ Π±ΠΎΠΊΠΎΠ²ΡΠ΅ Π·Π΅ΡΠΊΠ°Π»Π° ΡΒ ΡΠΈΡΠΎΠΊΠΈΠΌ ΠΎΡ Π²Π°ΡΠΎΠΌ, ΠΊΠ°ΠΌΠ΅ΡΠ° Π·Π°Π΄Π½Π΅Π³ΠΎ Π²ΠΈΠ΄Π° ΡΒ Π΄ΠΈΠ½Π°ΠΌΠΈΡΠ΅ΡΠΊΠΈΠΌΠΈ Π»ΠΈΠ½ΠΈΡΠΌΠΈ ΠΏΠΎΠ΄ΡΠΊΠ°Π·ΠΊΠ°ΠΌΠΈ.
ΠΠ½ΡΠ΅ΡΠ΅ΡΠ½Π°Ρ ΠΎΠΏΡΠΈΡΒ β ΠΏΡΠ°Π²Π°Ρ Π±ΠΎΠΊΠΎΠ²Π°Ρ ΠΊΠ°ΠΌΠ΅ΡΠ°, Π±Π»Π°Π³ΠΎΠ΄Π°ΡΡ ΠΊΠΎΡΠΎΡΠΎΠΉ ΠΌΠΎΠΆΠ½ΠΎ ΠΏΠ°ΡΠΊΠΎΠ²Π°ΡΡΡΡ Π²ΠΏΡΠΈΡΠΈΡΠΊΡ ΠΊΒ Π±ΠΎΡΠ΄ΡΡΠ°ΠΌ. ΠΠ°ΠΌΠ΅ΡΠ° Π°ΠΊΡΠΈΠ²ΠΈΡΡΠ΅ΡΡΡ ΠΏΡΠΈΠ½ΡΠ΄ΠΈΡΠ΅Π»ΡΠ½ΠΎ ΠΊΠ½ΠΎΠΏΠΊΠΎΠΉ ΡΡΠ΄ΠΎΠΌ ΡΒ ΡΠ΅Π»Π΅ΠΊΡΠΎΡΠΎΠΌ ΡΡΠ°Π½ΡΠΌΠΈΡΡΠΈΠΈ. ΠΡΡΡ ΡΠ°ΡΠΏΡΠ΅Π΄Π»ΠΎΠΆΠ΅Π½ΠΈΠ΅: ΠΎΡΡΠ΅Π³ΠΎΒ Π±Ρ ΠΏΡΠΎΠΈΠ·Π²ΠΎΠ΄ΠΈΡΠ΅Π»Ρ Π½Π΅Β ΡΠ΄Π΅Π»Π°ΡΡ ΡΠ°ΠΊ (ΠΏΡΠΎΠ³ΡΠ°ΠΌΠΌΠ½ΠΎ ΡΡΠΎ Π²ΠΎΠ·ΠΌΠΎΠΆΠ½ΠΎ), ΡΡΠΎΠ±Ρ ΠΊΠ°ΠΌΠ΅ΡΠ° Π°Π²ΡΠΎΠΌΠ°ΡΠΈΡΠ΅ΡΠΊΠΈ Π°ΠΊΡΠΈΠ²ΠΈΡΠΎΠ²Π°Π»Π°ΡΡ ΠΏΡΠΈ Π²ΠΊΠ»ΡΡΠ΅Π½ΠΈΠΈ ΠΏΡΠ°Π²ΠΎΠ³ΠΎ ΠΏΠΎΠ²ΠΎΡΠΎΡΠ½ΠΈΠΊΠ°?
ΠΡΠ»ΡΡΠΈΠΌΠ΅Π΄ΠΈΠΉΠΊΠ° ΠΏΠΎΠ½Π°ΡΠ°Π»Ρ ΡΠΌΡΡΠΈΠ»Π° ΠΎΡΡΡΡΡΡΠ²ΠΈΠ΅ΠΌ Apple CarPlay ΠΈΒ Android Auto, Π½ΠΎΒ ΠΏΠΎΠΌΠΎΠ³Π»ΠΎ ΠΏΡΠΈΠ»ΠΎΠΆΠ΅Π½ΠΈΠ΅ Easy Connection. Π‘ΠΊΠ°ΡΠΈΠ²Π°Ρ, ΠΏΠΎΠ΄ΠΊΠ»ΡΡΠ°ΡΡΡ ΠΏΠΎΒ ΠΏΡΠΎΠ²ΠΎΠ΄ΡΒ β ΠΈΒ ΡΡΡ ΠΆΠ΅Β Π½Π°Β ΡΠΊΡΠ°Π½Π΅ ΠΏΠΎΡΠ²Π»ΡΠ΅ΡΡΡ ΠΈΠ·ΠΎΠ±ΡΠ°ΠΆΠ΅Π½ΠΈΠ΅ ΡΠ°Π±ΠΎΡΠ΅Π³ΠΎ ΡΡΠΎΠ»Π° ΠΌΠΎΠ΅Π³ΠΎ ΡΠΌΠ°ΡΡΡΠΎΠ½Π°. ΠΡΠΈΡΠ΅ΠΌ Π²Β ΠΎΡΠ»ΠΈΡΠΈΠ΅ ΠΎΡΒ Apple CarPlay ΠΈΒ Android Auto ΡΡΠ° ΡΠΈΡΡΠ΅ΠΌΠ° ΡΡΠ°Π½ΡΠ»ΠΈΡΡΠ΅Ρ Π―Π½Π΄Π΅ΠΊΡ.ΠΠ°Π²ΠΈΠ³Π°ΡΠΎΡ.
ΠΡΠΈΠ»ΠΎΠΆΠ΅Π½ΠΈΠ΅ Easy Connection Π·Π΅ΡΠΊΠ°Π»ΠΈΡ ΡΠΊΡΠ°Π½ ΡΠΌΠ°ΡΡΡΠΎΠ½Π° ΠΈΒ ΠΏΠΎΠ·Π²ΠΎΠ»ΡΠ΅Ρ Π²ΡΠ²Π΅ΡΡΠΈ Π½Π°Β ΡΠΊΡΠ°Π½ Π΄Π°Π½Π½ΡΠ΅, Π½Π°ΠΏΡΠΈΠΌΠ΅Ρ, ΡΒ Π―Π½Π΄Π΅ΠΊΡ.ΠΠ°Π²ΠΈΠ³Π°ΡΠΎΡΠ°.ΠΡΠΈΠ»ΠΎΠΆΠ΅Π½ΠΈΠ΅ Easy Connection Π·Π΅ΡΠΊΠ°Π»ΠΈΡ ΡΠΊΡΠ°Π½ ΡΠΌΠ°ΡΡΡΠΎΠ½Π° ΠΈΒ ΠΏΠΎΠ·Π²ΠΎΠ»ΡΠ΅Ρ Π²ΡΠ²Π΅ΡΡΠΈ Π½Π°Β ΡΠΊΡΠ°Π½ Π΄Π°Π½Π½ΡΠ΅, Π½Π°ΠΏΡΠΈΠΌΠ΅Ρ, ΡΒ Π―Π½Π΄Π΅ΠΊΡ.ΠΠ°Π²ΠΈΠ³Π°ΡΠΎΡΠ°.
ΠΠ°ΠΌΠ΅ΡΠ° Π·Π°Π΄Π½Π΅Π³ΠΎ Π²ΠΈΠ΄Π° Π΄ΠΎΠΏΠΎΠ»Π½Π΅Π½Π° Π΄ΠΈΠ½Π°ΠΌΠΈΡΠ΅ΡΠΊΠΈΠΌΠΈ Π»ΠΈΠ½ΠΈΡΠΌΠΈ-ΠΏΠΎΠ΄ΡΠΊΠ°Π·ΠΊΠ°ΠΌΠΈ, ΠΏΠΎΠΌΠΎΠ³Π°ΡΡΠΈΠΌΠΈ Π²ΡΠ±ΠΈΡΠ°ΡΡ ΡΡΠ°Π΅ΠΊΡΠΎΡΠΈΡ. ΠΠ°ΠΌΠ΅ΡΠ° Π·Π°Π΄Π½Π΅Π³ΠΎ Π²ΠΈΠ΄Π° Π΄ΠΎΠΏΠΎΠ»Π½Π΅Π½Π° Π΄ΠΈΠ½Π°ΠΌΠΈΡΠ΅ΡΠΊΠΈΠΌΠΈ Π»ΠΈΠ½ΠΈΡΠΌΠΈ-ΠΏΠΎΠ΄ΡΠΊΠ°Π·ΠΊΠ°ΠΌΠΈ, ΠΏΠΎΠΌΠΎΠ³Π°ΡΡΠΈΠΌΠΈ Π²ΡΠ±ΠΈΡΠ°ΡΡ ΡΡΠ°Π΅ΠΊΡΠΎΡΠΈΡ. | ΠΠΎΠΊΠΎΠ²Π°Ρ ΠΊΠ°ΠΌΠ΅ΡΠ°Β β Π½Π°ΡΡΠΎΡΡΠ΅Π΅ ΡΠΏΠ°ΡΠ΅Π½ΠΈΠ΅ ΠΎΡΒ Π²ΡΡΠΎΠΊΠΈΡ
Π±ΠΎΡΠ΄ΡΡΠΎΠ². ΠΠΎΠΊΠΎΠ²Π°Ρ ΠΊΠ°ΠΌΠ΅ΡΠ°Β β Π½Π°ΡΡΠΎΡΡΠ΅Π΅ ΡΠΏΠ°ΡΠ΅Π½ΠΈΠ΅ ΠΎΡΒ Π²ΡΡΠΎΠΊΠΈΡ Π±ΠΎΡΠ΄ΡΡΠΎΠ². |
Π‘Π°Π»ΠΎΠ½ ΠΈΒ Π±Π°Π³Π°ΠΆΠ½ΠΈΠΊ
ΠΠ°ΡΡΠ°ΠΆΠΈΡΠ°ΠΌ Π²ΡΠΎΡΠΎΠ³ΠΎ ΡΡΠ΄Π° ΠΌΠ΅ΡΡΠ° Ρ Π²Π°ΡΠ°Π΅Ρ ΠΏΠΎΒ Π²ΡΠ΅ΠΌ Π½Π°ΠΏΡΠ°Π²Π»Π΅Π½ΠΈΡΠΌ. ΠΠ°ΠΆΠ΅ Π½Π°Β ΡΠ΅Π½ΡΡΠ°Π»ΡΠ½ΠΎΠΌ ΡΠΈΠ΄Π΅Π½ΡΠ΅ Ρ ΠΎΡΠΎΡΠΎΒ β ΡΠΏΠ°ΡΠΈΠ±ΠΎ ΠΌΡΠ³ΠΊΠΎΠΉ ΠΏΠΎΠ΄ΡΡΠΊΠ΅ ΠΈΒ ΡΠΈΡΡΠΎ ΡΠΈΠΌΠ²ΠΎΠ»ΠΈΡΠ΅ΡΠΊΠΎΠΌΡ Π½Π°ΠΏΠΎΠ»ΡΠ½ΠΎΠΌΡ ΡΡΠ½Π½Π΅Π»Ρ. ΠΡΡΡ ΠΈΒ ΠΊΡΡΠ° ΡΠΈΡΠ΅ΠΊ, ΠΊΠΎΡΠΎΡΡΡ Π²Β ΠΌΠ°ΡΠΈΠ½Π΅ Π·Π°Β ΡΠ°ΠΊΠΈΠ΅ Π΄Π΅Π½ΡΠ³ΠΈ (ΠΎΡΒ 1Β 149Β 900) Π²ΡΡΡΠ΅ΡΠΈΡΡ Π½Π΅ ΡΠ°ΡΡΠΎ: USB-ΠΏΠΎΡΡ, Π²Π΅ΡΡ Π½ΠΈΠ΅ Π΄Π΅ΡΠ»Π΅ΠΊΡΠΎΡΡ Π²Π΅Π½ΡΠΈΠ»ΡΡΠΈΠΈ, ΡΠ΅Π½ΡΡΠ°Π»ΡΠ½ΡΠΉ ΠΏΠΎΠ΄Π»ΠΎΠΊΠΎΡΠ½ΠΈΠΊ ΡΒ ΠΏΠ°ΡΠΎΠΉ ΠΏΠΎΠ΄ΡΡΠ°ΠΊΠ°Π½Π½ΠΈΠΊΠΎΠ², Π°Β ΡΠ°ΠΊΠΆΠ΅ Π²ΠΎΠ·ΠΌΠΎΠΆΠ½ΠΎΡΡΡ ΠΌΠ΅Π½ΡΡΡ ΡΠ³ΠΎΠ» Π½Π°ΠΊΠ»ΠΎΠ½Π° ΡΠΏΠΈΠ½ΠΊΠΈ.
ΠΡΠΎΡΡΠΎΡΠ½ΡΠΉ ΡΠ°Π»ΠΎΠ½Β β Π·Π½Π°ΡΠΈΡ ΠΊΡΡΡΠΉ Π±Π°Π³Π°ΠΆΠ½ΠΈΠΊ. Π’Π°ΠΊ Π±ΡΠ²Π°Π΅Ρ, Π½ΠΎΒ Π½Π΅Β Π²Β ΡΡΠΎΡ ΡΠ°Π·. Π’ΡΡΠΌ Π½Π΅Β ΡΠΎΠ»ΡΠΊΠΎ Π±ΠΎΠ»ΡΡΠΎΠ³ΠΎ ΠΎΠ±ΡΠ΅ΠΌΠ° (505Β Π»), Π½ΠΎΒ ΠΈΒ Π½Π΅ΠΏΠ»ΠΎΡ ΠΎ ΠΏΡΠΎΠ΄ΡΠΌΠ°Π½. Π’ΡΡ ΠΈΒ ΠΏΠ΅ΡΠ»ΠΈ Π΄Π»ΡΒ ΠΊΡΠ΅ΠΏΠ»Π΅Π½ΠΈΡ Π³ΡΡΠ·Π°, ΠΈΒ 12-Π²ΠΎΠ»ΡΡΠΎΠ²Π°Ρ ΡΠΎΠ·Π΅ΡΠΊΠ°. ΠΒ ΡΠΎΡΠ»ΡΠ΅ Π²ΠΎΠ΄ΠΈΡΠ΅Π»ΠΈ ΠΎΡΠ΅Π½ΡΡ Π²ΡΡΠΎΠΊΠΎ ΠΏΠΎΠ΄Π½ΠΈΠΌΠ°ΡΡΡΡΡΡ ΠΏΡΡΡΡ Π΄Π²Π΅ΡΡΒ β Π΄ΠΎΒ 185Β ΡΠΌ. ΠΠ»Ρ ΡΡΠ°ΡΡΡΡ Π½Π΅ Ρ Π²Π°ΡΠ°Π΅Ρ ΡΠ°Π·Π²Π΅ ΡΡΠΎ ΡΠ»Π΅ΠΊΡΡΠΎΠΏΡΠΈΠ²ΠΎΠ΄Π° Β«ΠΊΠ°Π»ΠΈΡΠΊΠΈΒ».
ΠΠ°Β Π²ΡΠΎΡΠΎΠΌ ΡΡΠ΄Ρ ΡΠΈΠ΄Π΅Π½ΠΈΠΉ Π±Π΅Π· ΠΏΡΠΎΠ±Π»Π΅ΠΌ ΡΠ°ΡΠΏΠΎΠ»ΠΎΠΆΠΈΡΡΡ ΡΠ΅Π»ΠΎΠ²Π΅ΠΊ ΡΠΎΡΡΠΎΠΌ 190Β ΡΠΌ. ΠΠΎΠΌΡΠΎΡΡΡ ΡΠΏΠΎΡΠΎΠ±ΡΡΠ²ΡΡΡ Π²Π΅ΡΡ Π½ΠΈΠ΅ Π΄Π΅ΡΠ»Π΅ΠΊΡΠΎΡΡΒ β ΠΏΡΠ΅ΡΠΎΠ³Π°ΡΠΈΠ²Π° ΡΠΎΠΏ-Π²Π΅ΡΡΠΈΠΈ Luxe.ΠΠ°Β Π²ΡΠΎΡΠΎΠΌ ΡΡΠ΄Ρ ΡΠΈΠ΄Π΅Π½ΠΈΠΉ Π±Π΅Π· ΠΏΡΠΎΠ±Π»Π΅ΠΌ ΡΠ°ΡΠΏΠΎΠ»ΠΎΠΆΠΈΡΡΡ ΡΠ΅Π»ΠΎΠ²Π΅ΠΊ ΡΠΎΡΡΠΎΠΌ 190Β ΡΠΌ. ΠΠΎΠΌΡΠΎΡΡΡ ΡΠΏΠΎΡΠΎΠ±ΡΡΠ²ΡΡΡ Π²Π΅ΡΡ Π½ΠΈΠ΅ Π΄Π΅ΡΠ»Π΅ΠΊΡΠΎΡΡΒ β ΠΏΡΠ΅ΡΠΎΠ³Π°ΡΠΈΠ²Π° ΡΠΎΠΏ-Π²Π΅ΡΡΠΈΠΈ Luxe.
ΠΠ°Π³Π°ΠΆΠ½ΠΈΠΊ ΡΠ°Π΄ΡΠ΅Ρ Π½Π΅Β ΡΠΎΠ»ΡΠΊΠΎ Π²ΠΌΠ΅ΡΡΠΈΡΠ΅Π»ΡΠ½ΠΎΡΡΡΡ, Π½ΠΎΒ ΠΈΒ ΠΏΠΎΠ³ΡΡΠ·ΠΎΡΠ½ΠΎΠΉ Π²ΡΡΠΎΡΠΎΠΉ. ΠΠΎΠ΄ ΠΏΠΎΠ»ΠΎΠΌΒ β Π΄ΠΎΠΊΠ°ΡΠΊΠ° ΠΈΒ ΠΎΡΠ³Π°Π½Π°ΠΉΠ·Π΅Ρ. ΠΠ°Π³Π°ΠΆΠ½ΠΈΠΊ ΡΠ°Π΄ΡΠ΅Ρ Π½Π΅Β ΡΠΎΠ»ΡΠΊΠΎ Π²ΠΌΠ΅ΡΡΠΈΡΠ΅Π»ΡΠ½ΠΎΡΡΡΡ, Π½ΠΎΒ ΠΈΒ ΠΏΠΎΠ³ΡΡΠ·ΠΎΡΠ½ΠΎΠΉ Π²ΡΡΠΎΡΠΎΠΉ. ΠΠΎΠ΄ ΠΏΠΎΠ»ΠΎΠΌΒ β Π΄ΠΎΠΊΠ°ΡΠΊΠ° ΠΈΒ ΠΎΡΠ³Π°Π½Π°ΠΉΠ·Π΅Ρ. |
ΠΠ²ΠΈΠ³Π°ΡΠ΅Π»Ρ ΠΈΒ ΠΊΠΎΡΠΎΠ±ΠΊΠ° ΠΏΠ΅ΡΠ΅Π΄Π°Ρ
ΠΒ Π ΠΎΡΡΠΈΠΈ CS55 ΠΏΡΠ΅Π΄Π»Π°Π³Π°ΡΡ ΡΒ ΠΏΠΎΠ»ΡΡΠΎΡΠ°Π»ΠΈΡΡΠΎΠ²ΡΠΌ Π±Π΅Π½Π·ΠΈΠ½ΠΎΠ²ΡΠΌ Π΄Π²ΠΈΠ³Π°ΡΠ΅Π»Π΅ΠΌ ΡΠΎΠ±ΡΡΠ²Π΅Π½Π½ΠΎΠΉ ΡΠ°Π·ΡΠ°Π±ΠΎΡΠΊΠΈ. ΠΠΎΠ½ΡΡΡΡΠΊΡΠΈΡ ΡΠΎΠ²ΡΠ΅ΠΌΠ΅Π½Π½Π°Ρ: Π°Π»ΡΠΌΠΈΠ½ΠΈΠ΅Π²ΡΠΉ Π±Π»ΠΎΠΊ, ΡΡΡΠ±ΠΎΠ½Π°Π΄Π΄ΡΠ², Π½Π΅ΠΏΠΎΡΡΠ΅Π΄ΡΡΠ²Π΅Π½Π½ΡΠΉ Π²ΠΏΡΡΡΠΊ, Π΄Π²Π° ΡΠ°Π·ΠΎΠ²ΡΠ°ΡΠ°ΡΠ΅Π»Ρ. ΠΠΎΡΠ½ΠΎΡΡΡ Π΄ΠΎΡΡΠΈΠ³Π°Π΅Ρ Π΄ΠΎΡΡΠΎΠΉΠ½ΡΡ 143 Π».Ρ., ΠΊΡΡΡΡΡΠΈΠΉ ΠΌΠΎΠΌΠ΅Π½ΡΒ β 210Β ΠΠΌ. ΠΠ²ΠΈΠ³Π°ΡΠ΅Π»Ρ ΡΠ°Π±ΠΎΡΠ°Π΅Ρ Π³Π»Π°Π΄ΠΊΠΎ ΠΈΒ ΠΌΠ°Π»ΠΎΡΡΠΌΠ½ΠΎ ΠΈΒ ΡΠΏΠΎΡΠΎΠ±Π΅Π½ Π΄Π°ΡΡ ΠΆΠ°ΡΡ! ΠΠΎΒ Π½Π°ΡΠΈΠΌ Π·Π°ΠΌΠ΅ΡΠ°ΠΌ, Π΄ΠΎΒ ΡΠΎΡΠ½ΠΈ CS55 ΡΠ°Π·Π³ΠΎΠ½ΡΠ΅ΡΡΡ Π·Π°Β 10,3Β Ρ. ΠΠΎΠ»ΡΡΠΈΠ½ΡΡΠ²ΠΎ ΠΎΠ΄Π½ΠΎΠΊΠ»Π°ΡΡΠ½ΠΈΠΊΠΎΠ² ΡΠ²Π΅ΡΠΎΡΠΎΡΠ½ΡΠ΅ Π³ΠΎΠ½ΠΊΠΈ Π΅ΠΌΡ ΠΏΡΠΎΠΈΠ³ΡΠ°ΡΡ.
Π‘Π°ΠΌΠΎΠ΅ ΠΏΡΠΈΡΡΠ½ΠΎΠ΅ Π²Β ΡΡΠΎΠΉ ΠΌΠ°ΡΠΈΠ½Π΅Β β Π³ΡΠ°ΠΌΠΎΡΠ½ΡΠ΅ Π½Π°ΡΡΡΠΎΠΉΠΊΠΈ ΡΠ΅ΡΡΠΈΡΡΡΠΏΠ΅Π½ΡΠ°ΡΠΎΠ³ΠΎ Π°Π²ΡΠΎΠΌΠ°ΡΠ° (ΠΊΠ»Π°ΡΡΠΈΡΠ΅ΡΠΊΠ°Ρ Π³ΠΈΠ΄ΡΠΎΠΌΠ΅Ρ Π°Π½ΠΈΠΊΠ°). ΠΒ ΡΡΠ°Π½Π΄Π°ΡΡΠ½ΠΎΠΌ ΡΠ΅ΠΆΠΈΠΌΠ΅ ΠΎΠ½Β ΠΏΠ΅ΡΠ΅ΠΊΠ»ΡΡΠ°Π΅ΡΡΡ ΠΌΡΠ³ΠΊΠΎ ΠΈΒ ΠΏΠΎΡΡΠΈ Π½Π΅Π·Π°ΠΌΠ΅ΡΠ½ΠΎ, ΡΡΠΎ ΠΏΠΎΠ½ΡΠ°Π²ΠΈΡΡΡ ΠΏΠΎΡΡΠΈ Π²ΡΠ΅ΠΌ. Π₯ΠΎΡΠΈΡΠ΅ ΠΏΠΎΠΎΡΡΡΠ΅Π΅? ΠΠ΅ΡΠ΅Π²ΠΎΠ΄ΠΈΡΠ΅ ΠΊΠΎΡΠΎΠ±ΠΊΡ Π²Β ΡΠΏΠΎΡΡΡΠ΅ΠΆΠΈΠΌΒ β ΠΏΠΎΠ»ΡΡΠΈΡΠ΅ ΠΎΡΡΡΡΠ΅ ΠΎΡΠΊΠ»ΠΈΠΊΠΈ ΠΈΒ ΠΏΠ΅ΡΠ΅ΠΊΠ»ΡΡΠ΅Π½ΠΈΡ Π²Β Π±ΠΎΠ»Π΅Π΅ Π²ΡΡΠΎΠΊΠΎΠΉ Π·ΠΎΠ½Π΅ ΠΎΠ±ΠΎΡΠΎΡΠΎΠ².
Π£ ΠΊΠ°ΠΊΠΈΡ ΠΌΠ°ΡΠΈΠ½ Π°Π»ΡΠΌΠΈΠ½ΠΈΠ΅Π²ΡΠΉ ΠΊΡΠ·ΠΎΠ²: ΡΠΎΡΠΎ ΠΈ ΠΎΠΏΠΈΡΠ°Π½ΠΈΠ΅
ΠΠ²ΡΠΎΡ ΠΠ»Π°Π΄ΠΈΠΌΠΈΡΠΎΠ²ΠΈΡ75 ΠΠ° ΡΡΠ΅Π½ΠΈΠ΅ 3 ΠΌΠΈΠ½. ΠΡΠΎΡΠΌΠΎΡΡΠΎΠ² 2.2k. ΠΠΏΡΠ±Π»ΠΈΠΊΠΎΠ²Π°Π½ΠΎ
ΠΡΠΏΠΎΠ»ΡΠ·ΠΎΠ²Π°Π½ΠΈΠ΅ Π°Π»ΡΠΌΠΈΠ½ΠΈΡ Π² ΠΏΡΠΎΠΈΠ·Π²ΠΎΠ΄ΡΡΠ²Π΅ Π°Π²ΡΠΎΠΌΠΎΠ±ΠΈΠ»ΡΠ½ΠΎΠ³ΠΎ ΠΊΡΠ·ΠΎΠ²Π° β ΡΡΠΎ ΡΠ΅Ρ Π½ΠΎΠ»ΠΎΠ³ΠΈΡ, ΠΊΠΎΡΠΎΡΠΎΠΉ ΠΎΡΠ΄Π°Π²Π°Π»ΠΎΡΡ ΠΏΡΠ΅Π΄ΠΏΠΎΡΡΠ΅Π½ΠΈΠ΅ Π³ΠΈΠ³Π°Π½ΡΠ°ΠΌΠΈ ΠΌΠ°ΡΠΈΠ½ΠΎΡΡΡΠΎΠ΅Π½ΠΈΡ Π΅ΡΡ Π² ΠΏΠ΅ΡΠ²ΠΎΠΉ ΠΏΠΎΠ»ΠΎΠ²ΠΈΠ½Π΅ Π΄Π²Π°Π΄ΡΠ°ΡΠΎΠ³ΠΎ Π²Π΅ΠΊΠ°. ΠΠΎΡΡΠ°ΡΠΎΡΠ½ΠΎ ΡΠ°ΡΡΠΎ Π°Π²ΡΠΎΠ»ΡΠ±ΠΈΡΠ΅Π»Π΅ΠΉ Π²ΠΎΠ»Π½ΡΠ΅Ρ Π²ΠΎΠΏΡΠΎΡ, Ρ ΠΊΠ°ΠΊΠΈΡ ΠΌΠ°ΡΠΈΠ½ Π°Π»ΡΠΌΠΈΠ½ΠΈΠ΅Π²ΡΠΉ ΠΊΡΠ·ΠΎΠ². Π’Π°ΠΊΠΎΠΉ ΠΈΠ½ΡΠ΅ΡΠ΅Ρ ΡΠΎΠ²ΡΠ΅ΠΌ Π½Π΅ΠΏΡΠ°Π·Π΄Π½ΡΠΉ ΠΈ Π²ΡΠ·Π²Π°Π½ ΠΆΠ΅Π»Π°Π½ΠΈΠ΅ΠΌ ΠΎΡΠ΅Π½ΠΈΡΡ Ρ Π°ΡΠ°ΠΊΡΠ΅ΡΠΈΡΡΠΈΠΊΠΈ ΠΊΠΎΡΠΏΡΡΠ° ΡΡΠ°Π½ΡΠΏΠΎΡΡΠ½ΠΎΠ³ΠΎ ΡΡΠ΅Π΄ΡΡΠ²Π°.
Audi A2
Π‘ΡΠΏΠ΅Ρ ΡΠΊΠΎΠ½ΠΎΠΌΠΈΡΠ½ΡΠΉ, Π±Π΅Π· ΠΏΠΎΡΠ΅ΡΠΈ Π΄ΠΈΠ½Π°ΠΌΠΈΠΊΠΈ Π°Π²ΡΠΎΠΌΠΎΠ±ΠΈΠ»Ρ, ΠΎΠ±Π»Π°Π΄Π°Π΅Ρ Π½Π΅Π±ΠΎΠ»ΡΡΠΈΠΌΠΈ ΡΠ°Π·ΠΌΠ΅ΡΠ°ΠΌΠΈ, Π½ΠΎ ΠΎΡΠ½Π°ΡΡΠ½ ΡΠ°ΠΌΡΠΌΠΈ ΡΠΎΠ²ΡΠ΅ΠΌΠ΅Π½Π½ΡΠΌΠΈ ΡΠΈΡΡΠ΅ΠΌΠ°ΠΌΠΈ Π΄Π»Ρ ΠΊΠΎΠΌΡΠΎΡΡΠ° ΠΈ Π±Π΅Π·ΠΎΠΏΠ°ΡΠ½ΠΎΡΡΠΈ ΠΈ ΠΏΠ΅ΡΠ΅Π΄Π²ΠΈΠΆΠ΅Π½ΠΈΡ.
Audi R8 (ASF)
Π’Π΅Ρ Π½ΠΎΠ»ΠΎΠ³ΠΈΡΠ½Π°Ρ ΠΌΠΎΠ΄Π΅Π»Ρ Ρ Π½ΠΎΠ²ΡΠΌ Π²Π·Π³Π»ΡΠ΄ΠΎΠΌ Π½Π° ΠΊΡΠ·ΠΎΠ²ΠΎΡΡΡΠΎΠ΅Π½ΠΈΠ΅ ΠΌΠΈΠ½ΠΈΠΌΠΈΠ·ΠΈΡΡΠ΅Ρ Π²Π΅Ρ Π°Π²ΡΠΎΠΌΠΎΠ±ΠΈΠ»Ρ, Π±Π»Π°Π³ΠΎΠ΄Π°ΡΡ ΡΠ΅ΠΌΡ ΠΎΠΊΠ°Π·ΡΠ²Π°Π΅ΡΡΡ ΡΠΈΠ»ΡΠ½ΠΎΠ΅ Π²Π»ΠΈΡΠ½ΠΈΠ΅ Π½Π° Ρ Π°ΡΠ°ΠΊΡΠ΅ΡΠΈΡΡΠΈΠΊΡ Π΄ΠΈΠ½Π°ΠΌΠΈΡΠ΅ΡΠΊΠΈΡ ΠΏΠΎΠΊΠ°Π·Π°ΡΠ΅Π»Π΅ΠΉ ΠΈ ΡΡΠΎΠ²Π΅Π½Ρ ΡΠ°ΡΡ ΠΎΠ΄Π° ΡΠΎΠΏΠ»ΠΈΠ²Π°.
Aston Martin DB9
ΠΠ°Π΄Π½Π΅ΠΏΡΠΈΠ²ΠΎΠ΄Π½ΠΎΠΉ ΡΠ΅ΡΡΡΡΡ ΠΌΠ΅ΡΡΠ½ΡΠΉ ΡΠΏΠΎΡΡΠΊΠ°Ρ ΠΎΠ±Π»Π°Π΄Π°Π΅Ρ Π½Π΅ ΡΠΎΠ»ΡΠΊΠΎ ΠΎΡΠ»ΠΈΡΠ½ΡΠΌΠΈ Ρ Π°ΡΠ°ΠΊΡΠ΅ΡΠΈΡΡΠΈΠΊΠ°ΠΌΠΈ ΠΈ ΡΡΡΠ΅ΡΠΈΡΠ½ΡΠΌ Π²Π½Π΅ΡΠ½ΠΈΠΌ Π²ΠΈΠ΄ΠΎΠΌ, Π½ΠΎ ΠΈ ΡΠΎΠ²ΡΠ΅ΠΌΠ΅Π½Π½ΡΠΌΠΈ ΠΊΡΠ·ΠΎΠ²Π½ΡΠΌΠΈ ΠΏΠ°ΡΠ°ΠΌΠ΅ΡΡΠ°ΠΌΠΈ.
Ferrari 612 Scaglietti
ΠΡΠΎΠ±Π΅Π½Π½ΠΎΡΡΡ Π΄Π°Π½Π½ΠΎΠΉ ΠΌΠΎΠ΄Π΅Π»ΠΈ ΠΏΡΠ΅Π΄ΡΡΠ°Π²Π»Π΅Π½Π° Π΄Π»ΠΈΠ½Π½ΡΠΌ ΠΊΠ°ΠΏΠΎΡΠΎΠΌ ΠΈ ΠΏΠ»Π°Π²Π½ΠΎ Π½ΠΈΡΠΏΠ°Π΄Π°ΡΡΠ΅ΠΉ ΠΊΡΡΡΠ΅ΠΉ Π°Π»ΡΠΌΠΈΠ½ΠΈΠ΅Π²ΠΎΠ³ΠΎ ΠΊΠΎΡΠΏΡΡΠ°, ΡΡΠΎ Π΄ΠΎΠΏΠΎΠ»Π½Π΅Π½ΠΎ ΡΠΎΠ²ΡΠ΅ΠΌΠ΅Π½Π½ΡΠΌΠΈ ΡΠ΅Ρ Π½ΠΎΠ»ΠΎΠ³ΠΈΡΠΌΠΈ, Π° ΡΠ°ΠΊΠΆΠ΅ Π΄ΠΎΠ»Π³ΠΎΠ²Π΅ΡΠ½ΠΎΡΡΡΡ Π°Π²ΡΠΎΠΌΠΎΠ±ΠΈΠ»ΡΠ½ΠΎΠ³ΠΎ ΠΊΡΠ·ΠΎΠ²Π°.
Honda NSX
Π‘ΠΏΠΎΡΡΠΈΠ²Π½ΠΎΠ³ΠΎ ΡΠΈΠΏΠ° Π°Π²ΡΠΎΠΌΠΎΠ±ΠΈΠ»Ρ, ΠΈΠΌΠ΅ΡΡΠΈΠΉ ΡΡΠ΅Π΄Π½Π΅ΠΌΠΎΡΠΎΡΠ½ΡΡ ΠΊΠΎΠΌΠΏΠΎΠ½ΠΎΠ²ΠΊΡ, ΠΏΡΠΎΠΈΠ·Π²ΠΎΠ΄ΠΈΠ»ΡΡ ΠΊΠΎΠΌΠΏΠ°Π½ΠΈΠ΅ΠΉ Honda Π΄ΠΎ 2005 Π³ΠΎΠ΄Π°, Π½ΠΎ Π΄ΠΎ ΡΠΈΡ ΠΏΠΎΡ Π½Π΅ ΠΏΠΎΡΠ΅ΡΡΠ» ΡΠ²ΠΎΠ΅ΠΉ Π°ΠΊΡΡΠ°Π»ΡΠ½ΠΎΡΡΠΈ ΠΈ ΠΏΠΎΠΏΡΠ»ΡΡΠ½ΠΎΡΡΠΈ.
Jaguar XJ
ΠΠ°ΡΠΈΠ½Π° ΠΏΡΠ΅ΠΌΠΈΡΠΌ-ΠΊΠ»Π°ΡΡΠ° β ΡΡΠΎ Π½Π΅ ΠΈΠ½Π½ΠΎΠ²Π°ΡΠΈΠΎΠ½Π½ΡΠ΅ ΡΠ΅Ρ Π½ΠΎΠ»ΠΎΠ³ΠΈΠΈ, ΠΊΠΎΠΌΡΠΎΡΡ ΠΈ ΡΠΎΡΠΊΠΎΡΠ½ΡΠΉ Π²Π½Π΅ΡΠ½ΠΈΠΉ Π²ΠΈΠ΄, Π° ΡΠ°ΠΊΠΆΠ΅ ΠΎΡΠ»ΠΈΡΠ½ΡΠ΅ Ρ ΠΎΠ΄ΠΎΠ²ΡΠ΅ ΠΊΠ°ΡΠ΅ΡΡΠ²Π°, Π΄ΠΎΠΏΠΎΠ»Π½Π΅Π½Π½ΡΠ΅ Π²ΡΡΠΎΠΊΠΎΠΉ ΡΠΊΠΎΠ½ΠΎΠΌΠΈΡΠ½ΠΎΡΡΡΡ ΠΈ ΠΈΠ½ΠΆΠ΅Π½Π΅ΡΠ½ΠΎΠΉ Π±Π΅Π·ΡΠΏΡΠ΅ΡΠ½ΠΎΡΡΡΡ ΠΊΠΎΠ½ΡΡΡΡΠΊΡΠΈΠΈ ΠΊΡΠ·ΠΎΠ²Π°.
Lamborghini Gallardo (ASF)
Π‘Π°ΠΌΠ°Ρ ΠΏΡΠΎΠ΄Π°Π²Π°Π΅ΠΌΠ°Ρ ΠΈ ΠΎΠ΄Π½Π° ΠΈΠ· Π½Π°ΠΈΠ±ΠΎΠ»Π΅Π΅ ΡΠΎΠ²Π΅ΡΡΠ΅Π½Π½ΡΡ ΠΌΠΎΠ΄Π΅Π»Π΅ΠΉ Π±ΡΠ΅Π½Π΄Π° LΠ°mborghini Π±ΡΠ»Π° ΠΏΡΠ΅Π·Π΅Π½ΡΠΎΠ²Π°Π½Π° Π½Π° ΠΈΠ·Π²Π΅ΡΡΠ½ΠΎΠΌ ΠΆΠ΅Π½Π΅Π²ΡΠΊΠΎΠΌ Π°Π²ΡΠΎΠΌΠΎΠ±ΠΈΠ»ΡΠ½ΠΎΠΌ ΡΠ°Π»ΠΎΠ½Π΅ Π² ΠΌΠ°ΡΡΠ΅ 2003 Π³ΠΎΠ΄Π°, Π½ΠΎ Π΄ΠΎ ΡΠΈΡ ΠΏΠΎΡ ΡΠΎΡ ΡΠ°Π½ΠΈΠ»Π° ΡΠ²ΠΎΡ ΠΏΠΎΠΏΡΠ»ΡΡΠ½ΠΎΡΡΡ.
Lotus Elise
ΠΠΎΠΏΡΠ»ΡΡΠ½ΡΠΉ ΡΠΎΠ΄ΡΡΠ΅Ρ ΡΠ΅Π³ΠΎΠ΄Π½Ρ ΠΎΡΠ½ΠΎΡΠΈΡΡΡ ΠΊ ΠΊΠ°ΡΠ΅Π³ΠΎΡΠΈΠΈ ΡΠ°ΠΌΡΡ Π΄ΠΎΡΡΡΠΏΠ½ΡΡ ΠΏΠΎ ΡΠ΅Π½Π΅ ΡΡΠΏΠ΅ΡΠΊΠ°ΡΠΎΠ² Π½Π° ΠΎΡΠ΅ΡΠ΅ΡΡΠ²Π΅Π½Π½ΠΎΠΌ Π°Π²ΡΠΎΠΌΠΎΠ±ΠΈΠ»ΡΠ½ΠΎΠΌ ΡΡΠ½ΠΊΠ΅ ΠΈ Ρ Π°ΡΠ°ΠΊΡΠ΅ΡΠΈΠ·ΡΠ΅ΡΡΡ ΡΡΠΈΠ»ΡΠ½ΡΠΌ Π²Π½Π΅ΡΠ½ΠΈΠΌ Π²ΠΈΠ΄ΠΎΠΌ, Π° ΡΠ°ΠΊΠΆΠ΅ ΠΏΡΠ΅Π²ΠΎΡΡ ΠΎΠ΄Π½ΠΎΠΉ Π΄ΠΈΠ½Π°ΠΌΠΈΠΊΠΎΠΉ ΡΠ°Π·Π³ΠΎΠ½Π°.
Melkus RS2000
ΠΠΎΠΌΠΏΠ°ΠΊΡΠ½ΡΠΉ ΡΠΏΠΎΡΡΠΈΠ²Π½ΡΠΉ Π°Π²ΡΠΎΠΌΠΎΠ±ΠΈΠ»Ρ, ΠΎΠ±Π»Π°Π΄Π°ΡΡΠΈΠΉ ΠΈΠ½Π΄ΠΈΠ²ΠΈΠ΄ΡΠ°Π»ΡΠ½ΠΎΡΡΡΡ ΠΈ Π½Π΅ΠΎΠ±ΡΠΊΠ½ΠΎΠ²Π΅Π½Π½ΠΎΠΉ Ρ Π°ΡΠΈΠ·ΠΌΠΎΠΉ, ΠΏΠ΅ΡΠ΅ΡΡΠ°Π» Π²ΡΠΏΡΡΠΊΠ°ΡΡΡΡ Π² 2012 Π³ΠΎΠ΄Ρ, ΡΠ΅ΠΌΡ ΡΠΏΠΎΡΠΎΠ±ΡΡΠ²ΠΎΠ²Π°Π»ΠΎ Π±Π°Π½ΠΊΡΠΎΡΡΡΠ²ΠΎ ΠΈ ΠΎΡΡΡΠΆΠ΄Π΅Π½ΠΈΠ΅ ΠΏΡΠΎΠΈΠ·Π²ΠΎΠ΄ΡΡΠ²Π΅Π½Π½ΡΡ Π°ΠΊΡΠΈΠ²ΠΎΠ², ΠΏΡΠΈΠ½Π°Π΄Π»Π΅ΠΆΠ°ΡΠΈΡ ΠΊΠΎΠΌΠΏΠ°Π½ΠΈΠΈ-ΠΏΡΠΎΠΈΠ·Π²ΠΎΠ΄ΠΈΡΠ΅Π»Ρ.
Mercedes SLS AMG
Π‘ΠΎΠ²ΡΠ΅ΠΌΠ΅Π½Π½ΡΠΉ ΡΠΏΠΎΡΡΠΊΠ°Ρ, ΠΎΡΠ½ΠΎΡΡΡΠΈΠΉΡΡ ΠΊ Π»ΠΈΠ½Π΅ΠΉΠΊΠ΅ ΠΊΡΡΠΏΠ½Π΅ΠΉΡΠ΅Π³ΠΎ Π°Π²ΡΠΎΠΌΠΎΠ±ΠΈΠ»ΡΠ½ΠΎΠ³ΠΎ ΠΊΠΎΠ½ΡΠ΅ΡΠ½Π° ΠΠ΅ΡΡΠ΅Π΄Π΅Ρ-ΠΠ΅Π½Ρ, Π΄ΠΎΠ²Π΅ΡΠΈΠ» ΡΠ°Π·ΡΠ°Π±ΠΎΡΠΊΡ ΠΏΡΠΎΠ΅ΠΊΡΠ° ΡΡΠ½ΠΈΠ½Π³Π° ΠΈΠ·Π²Π΅ΡΡΠ½ΠΎΠΉ ΠΊΠΎΠΌΠΏΠ°Π½ΠΈΠΈ ΠΠΠ, Π±Π»Π°Π³ΠΎΠ΄Π°ΡΡ ΡΠ΅ΠΌΡ ΠΌΠΎΠ΄Π΅Π»Ρ ΠΏΠΎΠ»ΡΡΠΈΠ»Π° ΡΠ΅Ρ Π½ΠΈΡΠ½ΡΠΉ ΠΈ ΠΏΡΠΈΠ²Π»Π΅ΠΊΠ°ΡΠ΅Π»ΡΠ½ΡΠΉ ΠΊΠΎΡΠΏΡΡ.
Morgan Aero 8
ΠΠΎΠ²ΠΈΠ½ΠΊΠ° ΠΈΠ·Π²Π΅ΡΡΠ½ΠΎΠ³ΠΎ Π±ΡΠΈΡΠ°Π½ΡΠΊΠΎΠ³ΠΎ Π°Π²ΡΠΎΠΏΡΠΎΠΈΠ·Π²ΠΎΠ΄ΠΈΡΠ΅Π»Ρ Π² ΠΏΠ»Π°Π½Π΅ ΡΡΠΈΠ»ΠΈΡΡΠΈΡΠ΅ΡΠΊΠΈΡ ΡΠ΅ΡΠ΅Π½ΠΈΠΉ β ΡΡΠΎ ΠΈΠ½ΠΎΡΡΡΠ°Π½Π½ΡΠΉ ΡΠΎΠ΄ΡΡΠ΅Ρ, ΠΎΠ±Π»Π°Π΄Π°ΡΡΠΈΠΉ ΡΠ½ΠΈΠΊΠ°Π»ΡΠ½ΠΎΠΉ Π²Π½Π΅ΡΠ½ΠΎΡΡΡΡ, Π° ΡΠ°ΠΊΠΆΠ΅ ΠΎΡΠΌΠ΅Π½Π½ΡΠΌΠΈ Π°ΡΡΠΎΠ΄ΠΈΠ½Π°ΠΌΠΈΡΠ΅ΡΠΊΠΈΠΌΠΈ ΡΠ²ΠΎΠΉΡΡΠ²Π°ΠΌΠΈ.
Opel Speedster
ΠΠ΅ΡΠΌΠΎΡΡΡ Π½Π° ΡΠΎ ΡΡΠΎ ΡΠΏΡΠΎΡ Π°Π²ΡΠΎΠ»ΡΠ±ΠΈΡΠ΅Π»Π΅ΠΉ Π½Π° ΡΠΏΠΎΡΡΠΈΠ²Π½ΡΠΉ ΡΠΎΠ΄ΡΡΠ΅Ρ Π±ΡΠ» Π½Π΅Π²ΡΡΠΎΠΊΠΈΠΌ, Π°Π²ΡΠΎΠΌΠΎΠ±ΠΈΠ»Ρ Ρ ΡΠ°ΠΊΠΈΠΌΠΈ ΠΊΠ°ΡΠ΅ΡΡΠ²Π΅Π½Π½ΡΠΌΠΈ ΠΈ ΡΠ΅Ρ Π½ΠΈΡΠ΅ΡΠΊΠΈΠΌΠΈ Ρ Π°ΡΠ°ΠΊΡΠ΅ΡΠΈΡΡΠΈΠΊΠ°ΠΌΠΈ Π²ΠΏΠΎΠ»Π½Π΅ ΠΎΠΆΠΈΠ΄Π°Π΅ΠΌΠΎ Π·Π°ΡΠ»ΡΠΆΠΈΠ» ΠΊ ΡΠ΅Π±Π΅ ΠΏΠΎΠ²ΡΡΠ΅Π½Π½ΠΎΠ΅ Π²Π½ΠΈΠΌΠ°Π½ΠΈΠ΅.
Spyker C8
ΠΠ½Π°ΠΌΠ΅Π½ΠΈΡΡΠΉ Β«Π‘ΠΏΠ°ΠΉΠΊΠ΅ΡΒ» ΠΎΡΠ½Π°ΡΡΠ½ ΡΠ΅Π½ΡΡΠ°Π»ΡΠ½ΡΠΌ ΡΠ°ΡΠΏΠΎΠ»ΠΎΠΆΠ΅Π½ΠΈΠ΅ΠΌ Π΄Π²ΠΈΠ³Π°ΡΠ΅Π»Ρ, Π·Π°ΠΈΠΌΡΡΠ²ΠΎΠ²Π°Π½Π½ΡΠΌ Ρ ΠΈΠ·Π²Π΅ΡΡΠ½ΠΎΠΉ ΠΊΠΎΠΌΠΏΠ°Π½ΠΈΠΈ Audi, ΡΡΠΎ ΡΠ΄Π΅Π»Π°Π»ΠΎ ΠΌΠΎΠ΄Π΅Π»Ρ Π²ΠΎΡΡΡΠ΅Π±ΠΎΠ²Π°Π½Π½ΠΎΠΉ Π½Π° Π·Π°ΡΡΠ±Π΅ΠΆΠ½ΠΎΠΌ ΠΈ ΠΎΡΠ΅ΡΠ΅ΡΡΠ²Π΅Π½Π½ΠΎΠΌ Π°Π²ΡΠΎΠΌΠΎΠ±ΠΈΠ»ΡΠ½ΠΎΠΌ ΡΡΠ½ΠΊΠ΅.
Tesla Roadster
Π‘Π΅ΡΠΈΡ Π½Π΅ ΡΡΠ°Π»Π° ΡΠ΅ΠΌ-ΡΠΎ Π½ΠΎΠ²ΡΠΌ Π² Ρ ΠΎΡΠΎΡΠΎ ΠΈΠ·Π²Π΅ΡΡΠ½ΠΎΠΌ Π°Π²ΡΠΎΠΌΠΎΠ±ΠΈΠ»ΠΈΡΡΠ°ΠΌ ΠΌΠΎΠ΄Π΅Π»ΡΠ½ΠΎΠΌ ΡΡΠ΄Ρ Tesla, Π½ΠΎ ΡΠ°ΠΊΠΈΠ΅ Π°Π²ΡΠΎΠΌΠΎΠ±ΠΈΠ»ΠΈ ΠΎΡΠ»ΠΈΡΠΈΠ»ΠΈΡΡ ΡΡΠΈΠ»ΡΠ½ΡΠΌ ΠΈ ΠΎΡΠΈΠ³ΠΈΠ½Π°Π»ΡΠ½ΡΠΌ Π΄ΠΈΠ·Π°ΠΉΠ½ΠΎΠΌ, Π° ΡΠ°ΠΊΠΆΠ΅ Π²Π½ΡΡΠΈΡΠ΅Π»ΡΠ½ΠΎΠΉ ΡΠΈΠ»ΠΎΠ²ΠΎΠΉ ΡΡΡΠ°Π½ΠΎΠ²ΠΊΠΎΠΉ.
ΠΠ΅ΡΠΌΠΎΡΡΡ Π½Π° ΡΠΎ ΡΡΠΎ Π°Π²ΡΠΎΠΌΠΎΠ±ΠΈΠ»ΠΈ Ρ Π°Π»ΡΠΌΠΈΠ½ΠΈΠ΅Π²ΡΠΌΠΈ ΠΊΡΠ·ΠΎΠ²Π°ΠΌΠΈ Ρ Π±ΠΎΠ»ΡΡΠΈΠ½ΡΡΠ²Π° ΠΎΠ±ΡΠ²Π°ΡΠ΅Π»Π΅ΠΉ ΡΠ°ΡΠ΅ Π²ΡΠ΅Π³ΠΎ Π°ΡΡΠΎΡΠΈΠΈΡΡΡΡΡΡ Ρ ΠΌΠ°ΡΠΊΠΎΠΉ Audi, Π±ΠΎΠ»ΡΡΠΎΠ΅ ΠΊΠΎΠ»ΠΈΡΠ΅ΡΡΠ²ΠΎ Π΄ΡΡΠ³ΠΈΡ Π·Π°ΡΡΠ±Π΅ΠΆΠ½ΡΡ ΠΌΠΎΠ΄Π΅Π»Π΅ΠΉ Π²ΠΏΠΎΠ»Π½Π΅ ΡΠ΄Π°ΡΠ½ΠΎ ΡΠΎΠ²ΠΌΠ΅ΡΠ°ΡΡ ΡΠ°ΠΊΠΎΠΉ Π²Π°ΡΠΈΠ°Π½Ρ ΠΊΠΎΡΠΏΡΡΠ° Ρ ΠΎΡΠ»ΠΈΡΠ½ΡΠΌΠΈ ΡΠ΅Ρ Π½ΠΈΡΠ΅ΡΠΊΠΈΠΌΠΈ Ρ Π°ΡΠ°ΠΊΡΠ΅ΡΠΈΡΡΠΈΠΊΠ°ΠΌΠΈ.
ΠΡΠ΅Π½ΠΈΡΠ΅ ΡΡΠ°ΡΡΡ: ΠΠΎΠ΄Π΅Π»ΠΈΡΠ΅ΡΡ Ρ Π΄ΡΡΠ·ΡΡΠΌΠΈ!ΠΡΠ±ΠΎΠΏΡΡΠ½ΠΎ, ΡΡΠΎ ΡΠ΅Ρ Π½ΠΎΠ»ΠΎΠ³ΠΈΡ ΠΏΠΎΠ»ΡΡΠ΅Π½ΠΈΡ Π΄Π΅ΡΠ΅Π²ΠΎΠ³ΠΎ Π°Π»ΡΠΌΠΈΠ½ΠΈΡ, Π±ΡΠ»Π° ΡΠ°Π·ΡΠ°Π±ΠΎΡΠ°Π½Π° Π² 1886 Π³ΠΎΠ΄Ρ, ΡΠΎ Π΅ΡΡΡ, Π² ΡΠΎΡ Π³ΠΎΠ΄, ΠΊΠΎΠ³Π΄Π° ΠΠ΅Π½Ρ Π·Π°ΠΏΠ°ΡΠ΅Π½ΡΠΎΠ²Π°Π» ΡΠ²ΠΎΠΉ ΡΠ°ΠΌΠΎΠ΄Π²ΠΈΠΆΡΡΠΈΠΉΡΡ ΡΠΊΠΈΠΏΠ°ΠΆ. Π Π΅Π³ΠΎ ΠΌΠ°ΡΠΈΠ½Π΅ Π°Π»ΡΠΌΠΈΠ½ΠΈΡ Π½Π΅ Π±ΡΠ»ΠΎ, Π½ΠΎ Π±ΡΠ»ΠΎ ΠΌΠ½ΠΎΠΆΠ΅ΡΡΠ²ΠΎ ΠΌΠ΅Π΄Π½ΡΡ ΠΈ ΠΆΠ΅Π»Π΅Π·Π½ΡΡ Π΄Π΅ΡΠ°Π»Π΅ΠΉ. ΠΡΠ΅Π΄ΡΡΠ°Π²Π»ΡΠ΅ΡΠ΅, ΠΊΠ°ΠΊΠΈΠ΅ ΡΠ΅Π·Π΅ΡΠ²Ρ ΠΏΠΎ ΡΠΌΠ΅Π½ΡΡΠ΅Π½ΠΈΡ ΠΌΠ°ΡΡΡ ΡΡΠ°Π½ΡΠΏΠΎΡΡΠ½ΠΎΠ³ΠΎ ΡΡΠ΅Π΄ΡΡΠ²Π° ΠΎΡΠΊΡΡΠ»ΠΈΡΡ ΠΏΠ΅ΡΠ΅Π΄ ΠΊΠΎΠ½ΡΡΡΡΠΊΡΠΎΡΠ°ΠΌΠΈ, ΠΊΠΎΠ³Π΄Π° Π°Π»ΡΠΌΠΈΠ½ΠΈΠΉ Π²ΡΠ΅-ΡΠ°ΠΊΠΈ Π½Π°ΡΠ΅Π» ΠΏΡΠΈΠΌΠ΅Π½Π΅Π½ΠΈΠ΅ Π² Π°Π²ΡΠΎΠΌΠΎΠ±ΠΈΠ»Π΅.
Π ΠΏΡΠΎΠΈΠ·ΠΎΡΠ»ΠΎ ΡΡΠΎ Π² Π‘Π¨Π Π² 1906 Π³ΠΎΠ΄Ρ. ΠΠΎΠΌΠΏΠ°Π½ΠΈΡΒ βMormonβ ΠΏΡΠ΅Π΄ΡΡΠ°Π²ΠΈΠ»Π° Π°Π²ΡΠΎΠΌΠΎΠ±ΠΈΠ»Ρ Ρ Π°Π»ΡΠΌΠΈΠ½ΠΈΠ΅Π²ΡΠΌ Π±Π»ΠΎΠΊΠΎΠΌ ΡΠΈΠ»ΠΈΠ½Π΄ΡΠΎΠ². Π‘Π²ΠΎΠ΅ Π·Π°Π²ΠΎΠ΅Π²Π°Π½ΠΈΠ΅ Π°Π²ΡΠΎΠΌΠΎΠ±ΠΈΠ»Π΅ΠΉ Π»Π΅Π³ΠΊΠΈΠΉ ΠΌΠ΅ΡΠ°Π»Π» Π½Π°ΡΠ°Π» ΠΈΠΌΠ΅Π½Π½ΠΎ Ρ Π΄Π²ΠΈΠ³Π°ΡΠ΅Π»Π΅ΠΉ. ΠΡΡΡΠΎΠΉ Π½Π΅ΠΎΠ±Ρ ΠΎΠ΄ΠΈΠΌΠΎΡΡΠΈ Π΅Π³ΠΎ ΠΈΡΠΏΠΎΠ»ΡΠ·ΠΎΠ²Π°Π½ΠΈΡ, ΠΊΠ°ΠΊΠ°Ρ Π²ΠΎΠ·Π½ΠΈΠΊΠ»Π° Π² Π°Π²ΠΈΠ°ΡΠΈΠΈ, Π² Π°Π²ΡΠΎΠΌΠΎΠ±ΠΈΠ»Π΅ΡΡΡΠΎΠ΅Π½ΠΈΠΈ Π½Π΅ Π±ΡΠ»ΠΎ.
Π‘Π΅ΡΡΠ΅Π·Π½ΡΠΉ ΠΈΠΌΠΏΡΠ»ΡΡ ΠΎΡΡΠ°ΡΠ»Ρ ΠΏΠΎΠ»ΡΡΠΈΠ»ΠΈ ΡΠΎΠ»ΡΠΊΠΎ ΠΏΠΎΡΠ»Π΅ ΠΡΠΎΡΠΎΠΉ ΠΌΠΈΡΠΎΠ²ΠΎΠΉ Π²ΠΎΠΉΠ½Ρ. ΠΠ°ΠΌΡΡΠ΅Π½ ΠΏΡΠΈΠΌΠ΅Ρ Π±ΡΠΈΡΠ°Π½ΡΠΊΠΎΠΉ ΡΠΈΡΠΌΡ Β«Land RoverΒ», Π½Π°ΡΠ°Π²ΡΠ΅ΠΉ Π²ΡΠΏΡΡΠΊ Π²Π΅Π·Π΄Π΅Ρ ΠΎΠ΄ΠΎΠ², Π½Π° ΠΊΡΠ·ΠΎΠ²Π° ΠΊΠΎΡΠΎΡΡΡ ΠΏΠΎΡΠ»Π° ΠΎΠ±Π»ΠΈΡΠΎΠ²ΠΊΠ° ΠΎΡ Π±ΠΎΠΌΠ±Π°ΡΠ΄ΠΈΡΠΎΠ²ΡΠΈΠΊΠΎΠ². Π Π°Π·ΡΠΌΠ΅Π΅ΡΡΡ, ΡΠ°ΠΊΠΎΠΉ Π°Π²ΡΠΎΠΌΠΎΠ±ΠΈΠ»Ρ ΠΌΠΎΠ³ ΠΏΠΎΡΠ²ΠΈΡΡΡΡ ΡΠΎΠ»ΡΠΊΠΎ ΠΏΡΠΈ ΡΡΠ»ΠΎΠ²ΠΈΠΈ ΠΆΠ΅ΡΡΠΎΡΠ°ΠΉΡΠ΅Π³ΠΎ Π΄Π΅ΡΠΈΡΠΈΡΠ° ΡΡΠ°Π»ΠΈ. ΠΠΎ Π΄ΡΡΠ³ΡΡ ΡΡΠΎΡΠΎΠ½Ρ ΠΡΠ»Π°Π½ΡΠΈΠΊΠΈ, Π³Π΄Π΅ ΠΏΡΠ°Π²ΠΈΡΠ΅Π»ΡΡΡΠ²ΠΎ Π»ΠΈΠΌΠΈΡΠΈΡΠΎΠ²Π°Π»ΠΎ Π΅Π΅ ΠΏΡΠΎΠ΄Π°ΠΆΡ, Π°Π²ΡΠΎΠΌΠΎΠ±ΠΈΠ»ΡΠ½ΡΠ΅ ΠΊΠΎΠΌΠΏΠ°Π½ΠΈΠΈ Π²ΡΡ ΠΎΠ΄ΠΈΠ»ΠΈ ΠΈΠ· ΠΏΠΎΠ»ΠΎΠΆΠ΅Π½ΠΈΡ, Π²ΡΠΏΡΡΠΊΠ°Ρ ΠΌΠ°ΡΠΈΠ½Ρ Ρ Π΄Π΅ΡΠ΅Π²ΡΠ½Π½ΡΠΌΠΈ ΠΊΡΠ·ΠΎΠ²Π°ΠΌΠΈ.
ΠΡΠ»ΠΈ Π² 1985 Π³ΠΎΠ΄Ρ Π² ΡΠΎΠ²ΡΠ΅ΠΌΠ΅Π½Π½ΠΎΠΌ Π°Π²ΡΠΎΠΌΠΎΠ±ΠΈΠ»Π΅ ΠΏΡΠΈΠΌΠ΅Π½ΡΠ»ΠΎΡΡ 60 ΠΊΠ³ Π°Π»ΡΠΌΠΈΠ½ΠΈΡ, ΡΠΎ ΡΠ΅Π³ΠΎΠ΄Π½Ρ ΡΡΠ° ΡΠΈΡΡΠ° ΠΏΡΠ΅ΠΎΠ΄ΠΎΠ»Π΅Π»Π° ΡΠ΅Π½ΡΠ½Π΅Ρ. ΠΠ΄ΠΎΠ±Π°Π²ΠΎΠΊ Π°Π»ΡΠΌΠΈΠ½ΠΈΠΉ ΡΡΠ°Π»ΠΈ ΠΈΡΠΏΠΎΠ»ΡΠ·ΠΎΠ²Π°ΡΡ Π΄Π»Ρ ΠΎΡΠ½ΠΎΠ²Ρ ΠΊΠΎΠ½ΡΡΡΡΠΊΡΠΈΠΈ ΠΊΡΠ·ΠΎΠ²Π°. ΠΠ° Π΅ΡΠ΅ ΠΈΠ· Π½Π΅Π³ΠΎ ΡΡΠ°ΠΌΠΏΡΡΡ ΠΊΠ°ΠΏΠΎΡΡ, ΠΊΡΡΠ»ΡΡ ΠΈ Π΄Π²Π΅ΡΠΈ. Π‘ΠΏΠ΅ΡΠΈΠ°Π»ΠΈΡΡΡ ΠΏΡΠΎΠ³Π½ΠΎΠ·ΠΈΡΡΡΡ, ΡΡΠΎ ΠΊ 2020 Π³ΠΎΠ΄Ρ ΠΈΡΠΏΠΎΠ»ΡΠ·ΠΎΠ²Π°Π½ΠΈΠ΅ Π°Π»ΡΠΌΠΈΠ½ΠΈΡ Π²ΠΎΠ·ΡΠ°ΡΡΠ΅Ρ Π΄ΠΎ 150 ΠΊΠ³. ΠΡΠ΅ΠΆΠ΄Π΅ Π²ΡΠ΅Π³ΠΎ ΡΡΠΎ ΠΊΠ°ΡΠ°Π΅ΡΡΡ ΠΏΠΎΠ΄Π²Π΅ΡΠΎΠΊ. ΠΡΠΈΠΌΠ΅Π½Π΅Π½ΠΈΠ΅ Π»Π΅Π³ΠΊΠΎΠ³ΠΎ ΠΌΠ΅ΡΠ°Π»Π»Π° Π² ΠΏΠΎΠ΄Π²Π΅ΡΠΊΠ΅ BMW ΠΏΠΎΠ·Π²ΠΎΠ»ΠΈΠ»ΠΎ ΡΠΎΠΊΡΠ°ΡΠΈΡΡ ΠΌΠ°ΡΡΡ ΡΠ·Π»ΠΎΠ² Π½Π° 36%.
ΠΠΏΡΠΎΡΠ΅ΠΌ, ΠΊΠ°ΠΊ ΠΌΡ Π²ΠΈΠ΄ΠΈΠΌ, ΠΏΡΠΈΠΌΠ΅ΡΡ ΠΈΡΠΏΠΎΠ»ΡΠ·ΠΎΠ²Π°Π½ΠΈΡ Π°Π»ΡΠΌΠΈΠ½ΠΈΡ, ΠΏΡΠ΅ΠΈΠΌΡΡΠ΅ΡΡΠ²Π΅Π½Π½ΠΎ Π½Π° Π΄ΠΎΡΠΎΠ³ΠΈΡ ΠΌΠΎΠ΄Π΅Π»ΡΡ . ΠΠ΄Π΅ Π½Π° ΠΎΠ±ΡΠ΅ΠΌ ΡΠΎΠ½Π΅ Π·Π°ΡΡΠ°Ρ Π½Π΅ ΡΡΠΎΠ»Ρ Π·Π°ΠΌΠ΅ΡΠ½Π° Π΄ΠΎΠ»Ρ ΡΠ°ΡΡ ΠΎΠ΄ΠΎΠ², ΡΠ²ΡΠ·Π°Π½Π½ΡΡ Ρ ΠΏΡΠΈΠΌΠ΅Π½Π΅Π½ΠΈΠ΅ΠΌ Π°Π»ΡΡΠ΅ΡΠ½Π°ΡΠΈΠ²Π½ΠΎΠΉ ΡΠ΅Ρ Π½ΠΎΠ»ΠΎΠ³ΠΈΠΈ. ΠΡΠ΅Π²ΠΈΠ΄Π½ΠΎ, ΡΡΠΎ ΠΏΡΡΠΌΠΎΠΉ Π²ΡΠ³ΠΎΠ΄Ρ ΠΎΡ ΡΡΠΎΠ³ΠΎ ΠΌΠ°ΡΠ΅ΡΠΈΠ°Π»Π°, ΠΆΠ΄Π°ΡΡ Π½Π΅ ΠΏΡΠΈΡ ΠΎΠ΄ΠΈΡΡΡ. ΠΡΡΠ΄ Π»ΠΈ Π°Π»ΡΠΌΠΈΠ½ΠΈΠΉ Π±ΡΠ΄Π΅Ρ Π΄Π΅ΡΠ΅Π²Π΅ΡΡ ΡΡΠΎΠ»Ρ ΠΆΠ΅ ΡΡΡΠ΅ΠΌΠΈΡΠ΅Π»ΡΠ½ΠΎ, ΠΊΠ°ΠΊ ΡΠ΅Ρ Π½ΠΎΠ»ΠΎΠ³ΠΈΡ Π΅Π³ΠΎ ΠΏΡΠΈΠΌΠ΅Π½Π΅Π½ΠΈΡ, ΠΊΠΎΡΠΎΡΠ°Ρ ΡΡΠ°Π½ΠΎΠ²ΠΈΡΡΡ Π±ΠΎΠ»Π΅Π΅ ΠΏΡΠΎΡΡΠΎΠΉ ΠΈ Π΄ΠΎΡΡΡΠΏΠ½ΠΎΠΉ. Π₯ΠΎΡΡ Π²Π΅Π΄Ρ Π‘ΠΎΠ²Π΅ΡΡΠΊΠΈΠΉ Π‘ΠΎΡΠ· Π²ΡΠΏΠ»Π°Π²Π»ΡΠ» ΠΏΡΠΈΠΌΠ΅ΡΠ½ΠΎ Π΄Π²Π° Ρ ΠΏΠΎΠ»ΠΎΠ²ΠΈΠ½ΠΎΠΉ ΠΌΠΈΠ»Π»ΠΈΠΎΠ½Π° ΡΠΎΠ½ ΠΊΡΡΠ»Π°ΡΠΎΠ³ΠΎ ΠΌΠ΅ΡΠ°Π»Π»Π° Π² Π³ΠΎΠ΄. ΠΠ½ΡΠ΅ΡΠ΅ΡΠ½ΠΎ, ΠΏΡΠ΅Π²Π·ΠΎΡΠ»Π° Π»ΠΈ Audi, Π²ΡΠΏΡΡΠΊΠ°ΡΡΠ°Ρ Π°Π²ΡΠΎΠΌΠΎΠ±ΠΈΠ»ΠΈ Ρ Π°Π»ΡΠΌΠΈΠ½ΠΈΠ΅Π²ΡΠΌ Π½Π΅ΡΡΡΠΈΠΌ ΠΊΡΠ·ΠΎΠ²ΠΎΠΌ, ΡΠΈΡΠ°ΠΆ Π²ΡΠΏΡΡΠ΅Π½Π½ΡΡ Π² Π½Π°ΡΠ΅ΠΉ ΡΡΡΠ°Π½Π΅ Π±ΠΎΠ΅Π²ΡΡ ΠΌΠ°ΡΠΈΠ½, ΠΈΠΌΠ΅ΡΡΠΈΡ Π°Π»ΡΠΌΠΈΠ½ΠΈΠ΅Π²ΡΠ΅ Π±ΡΠΎΠ½Π΅ΠΊΠΎΡΠΏΡΡΠ°.
ΠΠ»ΡΠΌΠΈΠ½ΠΈΠ·ΠΈΡΠΎΠ²Π°ΡΡ Π°Π²ΡΠΎΠΌΠΎΠ±ΠΈΠ»Ρ ΠΏΡΡΠ°Π»ΠΈΡΡ ΠΌΠ½ΠΎΠ³ΠΈΠ΅. ΠΡΠ΄Π°ΡΡΠΈΠΉΡΡ ΡΡΠ°Π½ΡΡΠ·ΡΠΊΠΈΠΉ Π°Π²ΡΠΎΠΌΠΎΠ±ΠΈΠ»ΡΠ½ΡΠΉ ΠΈΠ½ΠΆΠ΅Π½Π΅Ρ ΠΠ°ΠΊ ΠΠ»ΡΠ±Π΅Ρ ΠΡΠ΅Π³ΡΠ°Ρ Π² 1934 Π³ΠΎΠ΄Ρ Π²ΡΡΡΡΠΏΠΈΠ» Ρ Π½ΠΎΠ²ΠΎΠΉ ΠΊΠΎΠ½ΡΡΡΡΠΊΡΠΈΠ΅ΠΉ β Π½Π΅ΡΡΡΠΈΠΌ ΠΊΠ°ΡΠΊΠ°ΡΠΎΠΌ ΠΈΠ· Π°Π»ΡΠΌΠΈΠ½ΠΈΡ. ΠΡΠΈ Π½Π°ΡΠ°Π±ΠΎΡΠΊΠΈ ΠΎΠ½ ΠΈΡΠΏΠΎΠ»ΡΠ·ΠΎΠ²Π°Π» Π² ΡΠ΅ΡΠΈΠΉΠ½ΠΎΠΌ Π°Π²ΡΠΎΠΌΠΎΠ±ΠΈΠ»ΡΡΠΈΠΊΠ΅, ΠΊΠΎΡΠΎΡΡΠΉ ΠΈΠΌΠ΅Π» ΠΌΠ°ΡΡΡ 750 ΠΊΠ³.
Π‘ΠΏΠΈΡΠΎΠΊ Π°Π²ΡΠΎΠΌΠΎΠ±ΠΈΠ»Π΅ΠΉ Ρ ΠΎΡΠΈΠ½ΠΊΠΎΠ²Π°Π½Π½ΡΠΌ ΠΊΡΠ·ΠΎΠ²ΠΎΠΌ. Π’Π΅Ρ Π½ΠΎΠ»ΠΎΠ³ΠΈΠΈ ΡΠΈΠ½ΠΊΠΎΠ²Π°Π½ΠΈΡ, ΠΏΠ»ΡΡΡ ΠΈ ΠΌΠΈΠ½ΡΡΡ ΠΊΠ°ΠΆΠ΄ΠΎΠΉ.
ΠΠΎ Π΄Π΅Π»ΠΎ ΠΊΠ°ΠΊ-ΡΠΎ Π½Π΅ ΠΏΠΎΡΠ»ΠΎ. ΠΠΎΡΠ»Π΅ Π²ΠΎΠΉΠ½Ρ ΠΡΠ΅Π³ΡΠ°Ρ ΡΠ°Π·ΡΠ°Π±ΠΎΡΠ°Π» Π΄Π»Ρ ΡΠΈΡΠΌΡ Β«PanardΒ» Π½Π΅Π±ΠΎΠ»ΡΡΠΎΠΉ Π°Π²ΡΠΎΠΌΠΎΠ±ΠΈΠ»ΡΡΠΈΠΊ Dina. ΠΠ΅ Π²ΡΠΏΡΡΡΠΈΠ»ΠΈ Π² ΠΎΡΠ΅Π½Ρ Π½Π΅Π±ΠΎΠ»ΡΡΠΈΡ ΠΊΠΎΠ»ΠΈΡΠ΅ΡΡΠ²Π°Ρ .
ΠΡΡΠ°Π²ΠΈΠ»Π° ΡΠ²ΠΎΠΉ ΡΠ»Π΅Π΄ ΠΈ ΠΈΡΠ°Π»ΡΡΠ½ΡΠΊΠ°Ρ ΡΠΈΡΠΌΠ° ΠΠ°ΡΡΠΎΡΠΈΡΠΈ Π’ΡΡΠΈΠ½Π³, Π²ΡΠΏΡΡΠΊΠ°Π²ΡΠ°Ρ Π² 30-Ρ β 50-Ρ Π³ΠΎΠ΄Π°Ρ Π΄ΠΎΡΠΎΠ³ΠΈΠ΅ ΡΠΏΠΎΡΡΠΈΠ²Π½ΡΠ΅ Π°Π²ΡΠΎΠΌΠΎΠ±ΠΈΠ»ΠΈ Ρ ΠΊΡΠ·ΠΎΠ²Π°ΠΌΠΈ, Π½Π° ΠΊΠΎΡΠΎΡΡΡ Π°Π»ΡΠΌΠΈΠ½ΠΈΠ΅Π²ΡΠ΅ Π½Π°ΡΡΠΆΠ½ΡΠ΅ ΠΏΠ°Π½Π΅Π»ΠΈ ΠΊΡΠ΅ΠΏΠΈΠ»ΠΈΡΡ Π½Π° ΡΡΠ°Π»ΡΠ½ΠΎΠΌ ΡΡΡΠ±ΡΠ°ΡΠΎΠΌ ΠΊΠ°ΡΠΊΠ°ΡΠ΅. ΠΠΎΠ·Π΄Π½Π΅Π΅ ΡΡΡ ΠΈΡΠ°Π»ΡΡΠ½ΡΠΊΡΡ ΡΠ΅Ρ Π½ΠΎΠ»ΠΎΠ³ΠΈΡ ΠΏΡΠΈΠΎΠ±ΡΠ΅Π» Aston Martin.
Π‘Π΅Π³ΠΎΠ΄Π½Ρ ΠΈ ΡΠΎ ΠΈ Π΄ΡΡΠ³ΠΎΠ΅ Π½Π°Π·Π²Π°Π½ΠΈΠ΅, ΠΏΡΠΎΠΈΠ·Π½Π΅ΡΠ΅Π½Π½ΠΎΠ΅ ΠΏΡΠΈΠΌΠ΅Π½ΠΈΡΠ΅Π»ΡΠ½ΠΎ ΠΊ Π°Π²ΡΠΎΠΌΠΎΠ±ΠΈΠ»Ρ, Π·Π°ΡΡΠ°Π²Π»ΡΠ΅Ρ ΡΡΠ΅ΠΏΠ΅ΡΠ°ΡΡ ΡΠ΅ΡΠ΄ΡΠ° ΠΊΠΎΠ»Π»Π΅ΠΊΡΠΈΠΎΠ½Π΅ΡΠΎΠ².
ΠΡΠ·ΠΎΠ² ΡΠ²Π»ΡΠ΅ΡΡΡ ΠΎΠ΄Π½ΠΎΠΉ ΠΈΠ· ΡΠ°ΠΌΡΡ Π½Π°ΠΈΠ²Π°ΠΆΠ½Π΅ΠΉΡΠΈΡ Π΄Π΅ΡΠ°Π»Π΅ΠΉ Π°Π²ΡΠΎΠΌΠΎΠ±ΠΈΠ»Ρ. Π Π΅Π³ΠΎ ΠΎΡΠ½ΠΎΠ²Π½ΡΠ΅ ΠΊΠ°ΡΠ΅ΡΡΠ²Π° Π² ΠΏΠ΅ΡΠ²ΡΡ ΠΎΡΠ΅ΡΠ΅Π΄Ρ Π΄ΠΎΠ»ΠΆΠ½Ρ Π²Ρ ΠΎΠ΄ΠΈΡΡ Π±Π΅Π·ΠΎΠΏΠ°ΡΠ½ΠΎΡΡΡ, ΠΏΡΠΎΡΠ½ΠΎΡΡΡ, ΠΎΡΠ½ΠΎΡΠΈΡΠ΅Π»ΡΠ½Π°Ρ ΠΏΡΠΈ ΡΡΠΎΠΌ Π΄Π΅ΡΠ΅Π²ΠΈΠ·Π½Π°, Π½ΠΎ Π² ΡΠΎΠΆΠ΅ Π²ΡΠ΅ΠΌΡ ΠΎΠ½ Π΄ΠΎΠ»ΠΆΠ΅Π½ Π±ΡΡΡ ΠΎΠΏΡΠΈΠΌΠ°Π»ΡΠ½ΠΎ ΡΠ΄ΠΎΠ±Π½ΡΠΌ Π΄Π»Ρ Π²ΡΠ΅Ρ ΠΏΠ°ΡΡΠ°ΠΆΠΈΡΠΎΠ² ΡΠ°Π»ΠΎΠ½Π° Π°Π²ΡΠΎ ΠΈ ΠΎΡΠ»ΠΈΡΠ°ΡΡΡΡ ΡΡΠΈΠ»Π΅ΠΌ ΠΈ Π΄ΠΈΠ·Π°ΠΉΠ½ΠΎΠΌ. Π‘ΠΎΠ³Π»Π°ΡΠΈΡΠ΅ΡΡ, ΡΡΠΎ ΠΊΠ°ΡΠ΅ΡΡΠ²Π° ΡΡΠΈ ΠΏΠΎΡΠΎΠΉ ΠΏΡΠΎΡΠΈΠ²ΠΎΡΠ΅ΡΠΈΠ²Ρ, ΠΏΠΎΡΡΠΎΠΌΡ ΠΌΠ΅ΠΆΠ΄Ρ ΠΏΡΠΎΠΈΠ·Π²ΠΎΠ΄ΠΈΡΠ΅Π»ΡΠΌΠΈ Π½Π΅Ρ Π΅Π΄ΠΈΠ½ΠΎΠ³ΠΎ ΠΌΠ½Π΅Π½ΠΈΡ, ΠΊΠ°ΠΊΠΎΠΉ ΠΈΠ· ΠΊΡΠ·ΠΎΠ²Π½ΡΡ ΠΌΠ°ΡΠ΅ΡΠΈΠ°Π»ΠΎΠ² Π½Π°ΠΈΠ±ΠΎΠ»Π΅Π΅ Π»ΡΡΡΠ΅ ΠΏΠΎΠ΄Ρ ΠΎΠ΄ΠΈΡ Π΄Π»Ρ ΠΏΡΠΎΠΈΠ·Π²ΠΎΠ΄ΡΡΠ²Π°.
ΠΡ ΡΠ°ΡΡΠΊΠ°ΠΆΠ΅ΠΌ Π²Π°ΠΌ ΠΎ ΡΠΎΠ²ΡΠ΅ΠΌΠ΅Π½Π½ΡΡ
ΠΊΡΠ·ΠΎΠ²Π½ΡΡ
ΠΌΠ°ΡΠ΅ΡΠΈΠ°Π»Π°Ρ
ΠΈ ΡΠ°ΡΡΠΌΠΎΡΡΠΈΠΌ ΠΈΡ
ΠΏΠ»ΡΡΡ ΠΈ ΠΌΠΈΠ½ΡΡΡ.
Π‘ΡΠ°Π»ΡΠ½ΠΎΠΉ ΠΊΡΠ·ΠΎΠ²
Π‘ΡΠ°Π»ΡΠ½ΠΎΠΉ ΠΊΡΠ·ΠΎΠ² ΠΌΠΎΠΆΠ΅Ρ Π±ΡΡΡ ΡΠ°Π·Π»ΠΈΡΠ½ΠΎΠΉ Π²Π°ΡΠΈΠ°Π½ΡΠ½ΠΎΡΡΠΈ ΡΠΏΠ»Π°Π²Π°, ΡΡΠΎ Π΄Π°Π΅Ρ ΡΠΎΠ²Π΅ΡΡΠ΅Π½Π½ΠΎ Π½Π΅ΠΏΠΎΡ ΠΎΠΆΠΈΠ΅ ΡΠ²ΠΎΠΉΡΡΠ²Π° Π΅Π³ΠΎ ΡΠ°Π·Π½ΠΎΠ²ΠΈΠ΄Π½ΠΎΡΡΡΠΌ. Π’Π°ΠΊ, ΠΊ ΠΏΡΠΈΠΌΠ΅ΡΡ, ΠΎΡΠ»ΠΈΡΠ½ΠΎΠΉ ΠΏΠ»Π°ΡΡΠΈΡΠ½ΠΎΡΡΡΡ ΠΎΠ±Π»Π°Π΄Π°Π΅Ρ Π»ΠΈΡΡΠΎΠ²Π°Ρ ΡΡΠ°Π»Ρ, ΠΎΠ½Π° ΠΆΠ΅ ΠΈ ΠΏΠΎΠ·Π²ΠΎΠ»ΡΠ΅Ρ ΠΏΡΠΎΠΈΠ·Π²ΠΎΠ΄ΠΈΡΡ ΠΈΠ· ΡΠ΅Π±Ρ Π½Π°ΡΡΠΆΠ½ΡΠ΅ ΠΏΠ°Π½Π΅Π»ΠΈ Π΄Π΅ΡΠ°Π»Π΅ΠΉ ΠΊΡΠ·ΠΎΠ²Π°, ΠΊΠΎΡΠΎΡΡΠ΅ ΠΏΠΎΡΠΎΠΉ ΠΌΠΎΠ³ΡΡ ΠΈΠΌΠ΅ΡΡ Π΄ΠΎΠ²ΠΎΠ»ΡΠ½ΠΎ Π½Π΅ΠΎΠ±ΡΡΠ½ΡΡ ΠΈ ΡΠ»ΠΎΠΆΠ½ΡΡ ΡΠΎΡΠΌΡ. ΠΠΎΠ³ΠΈΡΠ½ΠΎ, ΡΡΠΎ Π²ΡΡΠΎΠΊΠΎΠΏΡΠΎΡΠ½ΡΠ΅ ΡΠΎΡΡΠ° ΠΎΠ±Π»Π°Π΄Π°ΡΡ ΠΈΠ·ΡΡΠ΄Π½ΠΎΠΉ ΡΠ½Π΅ΡΠ³ΠΎΠ΅ΠΌΠΊΠΎΡΡΡΡ ΠΈ ΠΎΡΠ»ΠΈΡΠ½ΠΎΠΉ ΠΏΡΠΎΡΠ½ΠΎΡΡΡΡ, ΠΏΠΎΡΡΠΎΠΌΡ ΡΡΠΎΡ Π²ΠΈΠ΄ ΡΡΠ°Π»ΠΈ ΠΏΡΠΈΠΌΠ΅Π½ΡΡΡ Π² ΠΏΡΠΎΠΈΠ·Π²ΠΎΠ΄ΡΡΠ²Π΅ ΡΠΈΠ»ΠΎΠ²ΡΡ Π΄Π΅ΡΠ°Π»Π΅ΠΉ ΠΊΡΠ·ΠΎΠ²Π°.
ΠΡΠ³ΠΎΠ΄Π½ΠΎ Π΅ΡΠ΅ ΠΈ ΡΠΎ, ΡΡΠΎ Π·Π° Π²ΡΡ ΠΈΡΡΠΎΡΠΈΡ Π°Π²ΡΠΎΠΌΠΎΠ±ΠΈΠ»Π΅ΡΡΡΠΎΠ΅Π½ΠΈΡ ΠΏΡΠΎΠΈΠ·Π²ΠΎΠ΄ΠΈΡΠ΅Π»ΡΠΌ ΡΠ΄Π°Π»ΠΎΡΡ ΡΠΏΡΠΎΡΡΠΈΡΡ ΠΈ ΠΎΡΠ»Π°Π΄ΠΈΡΡ ΠΌΠ°ΡΡΠ΅ΡΡΡΠ²ΠΎ ΠΈΠ·Π³ΠΎΡΠΎΠ²Π»Π΅Π½ΠΈΡ ΡΡΠ°Π»ΡΠ½ΡΡ ΠΊΡΠ·ΠΎΠ²ΠΎΠ², ΡΡΠΎ Π΄Π΅Π»Π°Π΅Ρ ΠΈΡ Π΄ΠΎΠ²ΠΎΠ»ΡΠ½ΠΎ Π½Π΅Π΄ΠΎΡΠΎΠ³ΠΈΠΌΠΈ.
ΠΠΌΠ΅Π½Π½ΠΎ ΡΡΠΎΡ ΡΠ°ΠΊΡΠΎΡ ΡΠ΄Π΅Π»Π°Π» ΡΡΠ°Π»ΡΠ½ΡΠ΅ ΠΊΡΠ·ΠΎΠ²Π° Π½Π° ΡΠ΅Π³ΠΎΠ΄Π½ΡΡΠ½ΠΈΠΉ Π΄Π΅Π½Ρ ΡΠ°ΠΌΡΠΌΠΈ ΠΏΠΎΠΏΡΠ»ΡΡΠ½ΡΠΌΠΈ Π½Π° Π°Π²ΡΠΎΠΌΠΎΠ±ΠΈΠ»ΡΠ½ΠΎΠΌ ΡΡΠ½ΠΊΠ΅.
ΠΡΠΈ Π²ΡΠ΅Ρ ΡΡΠΈΡ ΠΏΠ»ΡΡΠ°Ρ Π½Π΅Π΄ΠΎΡΡΠ°ΡΠΊΠΈ Ρ ΡΡΠ°Π»ΠΈ Π²ΡΠ΅ ΠΆΠ΅ ΠΈΠΌΠ΅ΡΡΡΡ ΠΈ ΡΡΡΠ΅ΡΡΠ²Π΅Π½Π½ΡΠ΅. Π’Π°ΠΊ, Π½Π°ΠΏΡΠΈΠΌΠ΅Ρ, Π½Π΅ΡΠ΄ΠΎΠ±Π½ΠΎ ΡΠΎ, ΡΡΠΎ ΡΡΠ°Π»ΡΠ½ΡΠ΅ Π΄Π΅ΡΠ°Π»ΠΈ ΠΈΠΌΠ΅ΡΡ Π½Π΅ ΠΌΠ°Π»ΡΠΉ Π²Π΅Ρ, Π° ΡΠ°ΠΊΠΆΠ΅ ΠΏΠΎΠ΄Π²Π΅ΡΠΆΠ΅Π½Ρ ΠΊΠΎΡΡΠΎΠ·ΠΈΠΉΠ½ΡΠΌ ΠΏΡΠΎΡΠ΅ΡΡΠ°ΠΌ, ΡΡΠΎ Π²ΡΠ½ΡΠΆΠ΄Π°Π΅Ρ ΠΏΡΠΎΠΈΠ·Π²ΠΎΠ΄ΠΈΡΠ΅Π»Π΅ΠΉ ΠΈΡΠΏΠΎΠ»ΡΠ·ΠΎΠ²Π°ΡΡ ΠΏΡΠΈΠ΅ΠΌΡ ΠΎΡΠΈΠ½ΠΊΠΎΠ²ΠΊΠΈ ΡΡΠ°Π»ΡΠ½ΡΡ Π΄Π΅ΡΠ°Π»Π΅ΠΉ ΠΈ ΠΏΠ°ΡΠ°Π»Π»Π΅Π»ΡΠ½ΠΎ ΠΈΡΠΊΠ°ΡΡ Π°Π»ΡΡΠ΅ΡΠ½Π°ΡΠΈΠ²Π½ΡΠ΅ Π²Π°ΡΠΈΠ°Π½ΡΡ ΠΊΡΠ·ΠΎΠ²Π½ΡΡ ΠΌΠ°ΡΠ΅ΡΠΈΠ°Π»ΠΎΠ².
ΠΠ»ΡΠΌΠΈΠ½ΠΈΠ΅Π²ΡΠΉ ΠΊΡΠ·ΠΎΠ²
Π‘Π΅Π³ΠΎΠ΄Π½Ρ Π²ΡΠ΅ ΡΠ°ΡΠ΅ ΠΌΠΎΠΆΠ½ΠΎ ΡΡΠ»ΡΡΠ°ΡΡ ΠΎΠ± ΠΈΡΠΏΠΎΠ»ΡΠ·ΠΎΠ²Π°Π½ΠΈΠΈ Π² ΠΏΡΠΎΠΈΠ·Π²ΠΎΠ΄ΡΡΠ²Π΅ ΠΊΡΠ·ΠΎΠ²ΠΎΠ² Π΄Π»Ρ Π°Π²ΡΠΎ ΡΠ°ΠΊΠΎΠ³ΠΎ ΠΌΠ°ΡΠ΅ΡΠΈΠ°Π»Π° ΠΊΠ°ΠΊ Π°Π»ΡΠΌΠΈΠ½ΠΈΠΉ. ΠΡΠΎΡ ΠΌΠ΅ΡΠ°Π»Π», ΠΊΠΎΡΠΎΡΡΠΉ Π² Π½Π°ΡΠΎΠ΄Π΅ Π½Π°Π·Π²Π°Π»ΠΈ Β«ΠΊΡΡΠ»Π°ΡΡΠΌΒ», Π½Π΅ ΠΏΠΎΠ΄Π²Π΅ΡΠΆΠ΅Π½ ΠΎΠ±ΡΠ°Π·ΠΎΠ²Π°Π½ΠΈΡ ΡΠΆΠ°Π²ΡΠΈΠ½Ρ Π½Π° Π΄Π΅ΡΠ°Π»ΡΡ ΠΊΠΎΡΠΏΡΡΠ°, Π° ΡΠ°ΠΌ Π°Π»ΡΠΌΠΈΠ½ΠΈΠ΅Π²ΡΠΉ ΠΊΡΠ·ΠΎΠ² ΠΏΡΠΈ ΡΠ°ΠΊΠΎΠΉ ΠΆΠ΅ ΠΏΡΠΎΡΠ½ΠΎΡΡΠΈ ΠΈ ΠΆΠ΅ΡΡΠΊΠΎΡΡΠΈ Π²Π΅ΡΠΈΡ Π² 2 ΡΠ°Π·Π° ΠΌΠ΅Π½ΡΡΠ΅, ΡΠ΅ΠΌ Π΅Π³ΠΎ ΡΡΠ°Π»ΡΠ½ΠΎΠΉ ΡΠΎΠ±ΡΠ°Ρ. ΠΠΎ ΠΈ ΡΡΡ Π΅ΡΡΡ ΠΏΠΎΠ΄Π²ΠΎΠ΄Π½ΡΠ΅ ΠΊΠ°ΠΌΠ½ΠΈ.
ΠΡΠΈ Π²ΡΠ΅Ρ ΡΠ²ΠΎΠΈΡ ΠΊΠ°ΡΠ΅ΡΡΠ²Π°Ρ Ρ Π°Π»ΡΠΌΠΈΠ½ΠΈΡ ΠΈΠΌΠ΅Π΅ΡΡΡ Π²Π΅ΡΠΎΠΌΡΠΉ Π½Π΅Π΄ΠΎΡΡΠ°ΡΠΎΠΊ β ΡΡΠΎ Ρ ΠΎΡΠΎΡΠ°Ρ ΠΏΡΠΎΠ²ΠΎΠ΄ΠΈΠΌΠΎΡΡΡ ΡΡΠΌΠ° ΠΈ Π²ΠΈΠ±ΡΠ°ΡΠΈΠΈ.
ΠΠΎΡΡΠΎΠΌΡ Π°Π²ΡΠΎΠΏΡΠΎΠΈΠ·Π²ΠΎΠ΄ΠΈΡΠ΅Π»ΡΠΌ ΠΏΡΠΈΡ ΠΎΠ΄ΠΈΡΡΡΡ ΡΡΠΈΠ»ΠΈΠ²Π°ΡΡ ΠΊΡΠ·ΠΎΠ² ΠΏΡΠΎΡΠΈΠ²ΠΎΡΡΠΌΠΎΠ²ΠΎΠΉ ΠΈΠ·ΠΎΠ»ΡΡΠΈΠ΅ΠΉ, ΡΡΠΎ, Π² ΠΊΠΎΠ½Π΅ΡΠ½ΠΎΠΌ ΡΡΠ΅ΡΠ΅, ΠΏΡΠΈΠ²ΠΎΠ΄ΠΈΡ ΠΊ ΡΠ΄ΠΎΡΠΎΠΆΠ°Π½ΠΈΡ ΠΌΠ°ΡΠΈΠ½Ρ, Π΄Π° ΠΈ ΡΠ°ΠΌ ΠΌΠ΅ΡΠ°Π»Π» ΡΡΠΎΠΈΡ Π΄ΠΎΡΠΎΠΆΠ΅ ΡΡΠ°Π»ΠΈ. ΠΡΠΈ ΡΠ°ΠΊΡΠΎΡΡ ΡΠΏΠΎΡΠΎΠ±ΡΡΠ²ΡΡΡ ΡΠΎΠΌΡ, ΡΡΠΎ ΡΠ΅ΠΌΠΎΠ½Ρ ΠΊΡΠ·ΠΎΠ²Π° Π² ΠΏΠΎΡΠ»Π΅Π΄ΡΡΡΠ΅ΠΌ ΠΌΠΎΠΆΠ΅Ρ ΠΏΠΎΡΡΠ΅Π±ΠΎΠ²Π°ΡΡ ΠΈΡΠΏΠΎΠ»ΡΠ·ΠΎΠ²Π°Π½ΠΈΡ ΡΠΏΠ΅ΡΠΈΠ°Π»ΡΠ½ΠΎΠ³ΠΎ ΠΎΠ±ΠΎΡΡΠ΄ΠΎΠ²Π°Π½ΠΈΡ.
Π ΠΈΡΠΎΠ³Π΅, Π²ΡΠ΅ ΡΡΠΎ ΠΏΡΠΈΠ²ΠΎΠ΄ΠΈΡ ΠΊ ΡΠ²Π΅Π»ΠΈΡΠ΅Π½ΠΈΡ ΡΠ΅Π½Ρ ΡΠ°ΠΌΠΎΠ³ΠΎ Π°Π²ΡΠΎΠΌΠΎΠ±ΠΈΠ»Ρ. ΠΠΎΠ»Π½ΠΎΡΡΡΡ Π°Π»ΡΠΌΠΈΠ½ΠΈΠ΅Π²ΡΠΉ ΠΊΡΠ·ΠΎΠ² ΠΌΠΎΠ³ΡΡ ΠΏΠΎΠ·Π²ΠΎΠ»ΠΈΡΡ ΡΠ΅Π±Π΅ Π΄Π°Π»Π΅ΠΊΠΎ Π½Π΅ Π²ΡΠ΅ ΠΏΡΠΎΠΈΠ·Π²ΠΎΠ΄ΠΈΡΠ΅Π»ΠΈ, ΠΎΠ΄ΠΈΠ½ ΠΈΠ· Π½Π΅ΠΌΠ½ΠΎΠ³ΠΈΡ β Audi. ΠΠΎ ΡΠ°ΡΠ΅ Π²ΡΠ΅Π³ΠΎ ΠΏΡΠΈΡ ΠΎΠ΄ΠΈΡΡΡ ΠΈΠ΄ΡΠΈ Π½Π° ΠΊΠΎΠΌΠΏΡΠΎΠΌΠΈΡΡ ΠΈ ΠΊΠΎΠΌΠΏΠΎΠ½ΠΎΠ²Π°ΡΡ Π°Π»ΡΠΌΠΈΠ½ΠΈΠ΅Π²ΡΠ΅ ΠΈ ΡΡΠ°Π»ΡΠ½ΡΠ΅ Π΄Π΅ΡΠ°Π»ΠΈ Π² ΠΎΠ΄Π½ΠΎΠΌ ΠΊΡΠ·ΠΎΠ²Π΅. Π’Π°ΠΊ, ΠΊ ΠΏΡΠΈΠΌΠ΅ΡΡ, Π² ΠΌΠΎΠ΄Π΅Π»ΠΈ BMW ΠΏΡΡΠΎΠΉ ΡΠ΅ΡΠΈΠΈ Π²ΡΡ ΠΏΠ΅ΡΠ΅Π΄Π½ΡΡ ΡΠ°ΡΡΡ ΠΊΡΠ·ΠΎΠ²Π½ΠΎΠ³ΠΎ ΠΊΠΎΡΠΏΡΡΠ° ΠΈΠ·Π³ΠΎΡΠΎΠ²Π»Π΅Π½Π° ΠΈΠ· Π°Π»ΡΠΌΠΈΠ½ΠΈΡ ΠΈ ΡΠ²Π°ΡΠ΅Π½Π° ΡΠΎ ΡΡΠ°Π»ΡΠ½ΡΠΌ ΠΊΠ°ΡΠΊΠ°ΡΠΎΠΌ.
ΠΠ»Π°ΡΡΠΈΠΊΠΎΠ²ΡΠΉ ΠΊΡΠ·ΠΎΠ²
ΠΠ»Π°ΡΡΠΈΠΊ Π½Π΅ ΡΠ°ΠΊ Π΄Π°Π²Π½ΠΎ ΡΡΠΈΡΠ°Π»ΡΡ Π² Π°Π²ΡΠΎΠΌΠΎΠ±ΠΈΠ»Π΅ΡΡΡΠΎΠ΅Π½ΠΈΠΈ Π½Π°ΠΈΠ±ΠΎΠ»Π΅Π΅ ΠΏΠ΅ΡΡΠΏΠ΅ΠΊΡΠΈΠ²Π½ΡΠΌ ΠΊΡΠ·ΠΎΠ²Π½ΡΠΌ ΠΌΠ°ΡΠ΅ΡΠΈΠ°Π»ΠΎΠΌ. ΠΠ½ Π»Π΅Π³ΡΠ΅ Π΄Π°ΠΆΠ΅ Π²ΡΡΠ΅ΡΠΏΠΎΠΌΡΠ½ΡΡΠΎΠ³ΠΎ Π°Π»ΡΠΌΠΈΠ½ΠΈΡ, Π΅ΠΌΡ ΠΌΠΎΠΆΠ½ΠΎ ΠΏΡΠΈΠ΄Π°ΡΡ Π»ΡΠ±ΡΡ, Π΄Π°ΠΆΠ΅ Π²ΡΡΡΡΠ½ΡΡ ΠΈ Π·Π°ΠΌΡΡΠ»ΠΎΠ²Π°ΡΡΡ ΡΠΎΡΠΌΡ, Π΄Π° ΠΈ ΠΏΠΎΠΊΡΠ°ΡΠΊΠ° Π΅Π³ΠΎ ΠΎΠ±Ρ ΠΎΠ΄ΠΈΡΡΡ Π½Π°ΠΌΠ½ΠΎΠ³ΠΎ Π΄Π΅ΡΠ΅Π²Π»Π΅, Π²Π΅Π΄Ρ ΠΏΡΠΎΠ²Π΅ΡΡΠΈ Π΅Π΅ ΠΌΠΎΠΆΠ½ΠΎ ΡΠΆΠ΅ Π½Π° ΡΡΠ°Π΄ΠΈΠΈ ΠΏΡΠΎΠΈΠ·Π²ΠΎΠ΄ΡΡΠ²Π°, ΠΈΡΠΏΠΎΠ»ΡΠ·ΡΡ ΡΠ°Π·Π»ΠΈΡΠ½ΡΠ΅ Ρ ΠΈΠΌΠΈΡΠ΅ΡΠΊΠΈΠ΅ Π΄ΠΎΠ±Π°Π²ΠΊΠΈ.
ΠΠ±ΡΠΎΠ»ΡΡΠ½ΡΠ΅ «Π½Π΅ΡΠΆΠ°Π²Π΅ΠΉΠΊΠΈ». ΠΠ°ΡΠΈΠ½Ρ Π±Π΅Π»ΠΎΡΡΡΡΠΊΠΎΠ³ΠΎ ΡΡΠ½ΠΊΠ° Π±ΡΡΡΠ΅ΠΊ Ρ ΠΊΡΠ·ΠΎΠ²Π°ΠΌΠΈ Π½Π΅ ΠΈΠ· ΡΡΠ°Π»ΠΈ
ΠΡ ΠΈ Π½Π°ΠΊΠΎΠ½Π΅Ρ, ΡΡΠΎΡ ΠΌΠ°ΡΠ΅ΡΠΈΠ°Π» ΡΠΆ ΡΠΎΡΠ½ΠΎ Π½Π΅ Π·Π½Π°Π΅Ρ, ΡΡΠΎ ΡΠ°ΠΊΠΎΠ΅ ΠΊΠΎΡΡΠΎΠ·ΠΈΡ. ΠΠΎ Π½Π΅Π΄ΠΎΡΡΠ°ΡΠΊΠΎΠ² Ρ ΠΏΠ»Π°ΡΡΠΈΠΊΠ° Π³ΠΎΡΠ°Π·Π΄ΠΎ Π±ΠΎΠ»ΡΡΠ΅ ΠΈ ΠΎΠ½ΠΈ Π΄ΠΎΠ²ΠΎΠ»ΡΠ½ΠΎ Π·Π½Π°ΡΠΈΠΌΡΠ΅.
Π’Π°ΠΊ, ΡΠ²ΠΎΠΉΡΡΠ²Π° ΠΏΠ»Π°ΡΡΠΈΠΊΠ° ΠΌΠ΅Π½ΡΡΡΡΡ ΠΏΠΎΠ΄ Π²Π»ΠΈΡΠ½ΠΈΠ΅ΠΌ ΡΠ°Π·Π»ΠΈΡΠ½ΡΡ ΡΠ΅ΠΌΠΏΠ΅ΡΠ°ΡΡΡ β ΠΌΠΎΡΠΎΠ· Π΄Π΅Π»Π°Π΅Ρ ΠΏΠ»Π°ΡΡΠΈΠΊ Π±ΠΎΠ»Π΅Π΅ Ρ ΡΡΠΏΠΊΠΈΠΌ, Π° ΠΆΠ°ΡΠ° ΡΠ°Π·ΠΌΡΠ³ΡΠ°Π΅Ρ ΡΡΠΎΡ ΠΌΠ°ΡΠ΅ΡΠΈΠ°Π».
ΠΠΎ ΡΡΠΈΠΌ ΠΏΡΠΈΡΠΈΠ½Π°ΠΌ ΠΈ ΡΡΠ΄Ρ Π΄ΡΡΠ³ΠΈΡ ΠΈΠ· ΠΏΠ»Π°ΡΡΠΈΠΊΠ° Π½Π΅Π»ΡΠ·Ρ ΠΈΠ·Π³ΠΎΡΠ°Π²Π»ΠΈΠ²Π°ΡΡ ΡΠ΅ Π΄Π΅ΡΠ°Π»ΠΈ, Π½Π° ΠΊΠΎΡΠΎΡΡΠ΅ ΠΎΠΊΠ°Π·ΡΠ²Π°ΡΡΡΡ Π΄ΠΎΠ²ΠΎΠ»ΡΠ½ΠΎ Π²ΡΡΠΎΠΊΠΈΠ΅ ΡΠΈΠ»ΠΎΠ²ΡΠ΅ Π½Π°Π³ΡΡΠ·ΠΊΠΈ, ΡΠ΅ΠΌΠΎΠ½ΡΡ Π½Π΅ΠΊΠΎΡΠΎΡΡΠ΅ ΠΏΠ»Π°ΡΡΠΈΠΊΠΎΠ²ΡΠ΅ Π΄Π΅ΡΠ°Π»ΠΈ ΠΈ Π²ΠΎΠ²ΡΠ΅ Π½Π΅ ΠΏΠΎΠ΄Π΄Π°ΡΡΡΡ, ΠΈ ΡΡΠ΅Π±ΡΡΡ ΠΏΠΎΠ»Π½ΠΎΠΉ ΡΠ²ΠΎΠ΅ΠΉ Π·Π°ΠΌΠ΅Π½Ρ. ΠΠΌΠ΅Π½Π½ΠΎ ΡΡΠΎ ΠΏΡΠΈΠ²Π΅Π»ΠΎ ΠΊ ΡΠΎΠΌΡ, ΡΡΠΎ Π½Π° ΡΠ΅Π³ΠΎΠ΄Π½ΡΡΠ½ΠΈΠΉ Π΄Π΅Π½Ρ ΠΈΠ· ΠΏΠ»Π°ΡΡΠΈΠΊΠ° ΠΈΠ·Π³ΠΎΡΠ°Π²Π»ΠΈΠ²Π°ΡΡ Π»ΠΈΡΡ Π½Π°Π²Π΅ΡΡ, Π±Π°ΠΌΠΏΠ΅ΡΠ° Π΄Π° ΠΊΡΡΠ»ΡΡ.
ΠΠΎΠΌΠΏΠΎΠ·ΠΈΡΠ½ΡΠΉ ΠΊΡΠ·ΠΎΠ²
ΠΡΠ΅ ΠΎΠ΄Π½ΠΈΠΌ Π²ΠΈΠ΄ΠΎΠΌ ΠΌΠ°ΡΠ΅ΡΠΈΠ°Π»Π° Π΄Π»Ρ ΠΈΠ·Π³ΠΎΡΠΎΠ²Π»Π΅Π½ΠΈΡ ΠΊΡΠ·ΠΎΠ²Π° ΡΠ²Π»ΡΡΡΡΡ ΠΊΠΎΠΌΠΏΠΎΠ·ΠΈΡΠ½ΡΠ΅ ΠΌΠ°ΡΠ΅ΡΠΈΠ°Π»Ρ. ΠΡΠΎ Β«Π³ΠΈΠ±ΡΠΈΠ΄Π½ΡΠΉΒ» ΠΌΠ°ΡΠ΅ΡΠΈΠ°Π», ΠΏΠΎΠ»ΡΡΠ°Π΅ΠΌΡΠΉ ΠΈΠ· Π½Π΅ΡΠΊΠΎΠ»ΡΠΊΠΈΡ ΡΠΎΠ΅Π΄ΠΈΠ½Π΅Π½Π½ΡΡ Π²ΠΌΠ΅ΡΡΠ΅. Π’Π°ΠΊΠΎΠ΅ ΠΏΡΠΎΠΈΠ·Π²ΠΎΠ΄ΡΡΠ²ΠΎ Π΄Π΅Π»Π°Π΅Ρ ΠΊΠΎΠΌΠΏΠΎΠ·ΠΈΡΠ½ΡΠΉ ΠΊΡΠ·ΠΎΠ² ΠΎΠΏΡΠΈΠΌΠ°Π»ΡΠ½ΡΠΌ ΠΏΠΎ ΠΊΠ°ΡΠ΅ΡΡΠ²Π°ΠΌ, ΡΠ°ΠΊ ΠΊΠ°ΠΊ Π² Π½Π΅ΠΌ ΡΠΎΠ΅Π΄ΠΈΠ½ΡΠ΅ΡΡΡ Π²ΡΠ΅ Π»ΡΡΡΠ΅Π΅ ΠΎΡ ΠΊΠ°ΠΆΠ΄ΠΎΠ³ΠΎ ΠΊΠΎΠΌΠΏΠΎΠ½Π΅Π½ΡΠ°.
ΠΡΠΎΠΌΠ΅ ΡΠΎΠ³ΠΎ, ΠΊΠΎΠΌΠΏΠΎΠ·ΠΈΡΠ½ΡΠ΅ ΠΌΠ°ΡΠ΅ΡΠΈΠ°Π»Ρ Π±ΠΎΠ»Π΅Π΅ Π΄ΠΎΠ»Π³ΠΎΠ²Π΅ΡΠ½Ρ, ΠΈΠ· Π½ΠΈΡ ΠΌΠΎΠΆΠ½ΠΎ ΠΈΠ·Π³ΠΎΡΠ°Π²Π»ΠΈΠ²Π°ΡΡ ΡΠ°ΠΌΡΠ΅ ΠΊΡΡΠΏΠ½ΡΠ΅ ΠΈ ΡΠΏΠ»ΠΎΡΠ½ΡΠ΅ Π΄Π΅ΡΠ°Π»ΠΈ, ΡΡΠΎ, Π½Π΅ΡΠΎΠΌΠ½Π΅Π½Π½ΠΎ, ΡΠΏΡΠΎΡΠ°Π΅Ρ ΡΠ°ΠΌΠΎ ΠΏΡΠΎΠΈΠ·Π²ΠΎΠ΄ΡΡΠ²ΠΎ.
Π ΠΊΠΎΠΌΠΏΠΎΠ·ΠΈΡΠ½ΡΠΌ ΠΌΠ°ΡΠ΅ΡΠΈΠ°Π»Π°ΠΌ ΠΎΡΠ½ΠΎΡΠΈΡΡΡ, Π½Π°ΠΏΡΠΈΠΌΠ΅Ρ, ΡΠ³Π»Π΅Π²ΠΎΠ»ΠΎΠΊΠ½ΠΎ, ΠΊΠΎΡΠΎΡΠΎΠ΅, ΠΊΡΡΠ°ΡΠΈ, ΠΈΡΠΏΠΎΠ»ΡΠ·ΡΠ΅ΡΡΡ Π² ΠΏΡΠΎΠΈΠ·Π²ΠΎΠ΄ΡΡΠ²Π΅ ΡΠ°ΡΠ΅ Π²ΡΠ΅Π³ΠΎ. ΠΠ· ΡΠ³Π»Π΅Π²ΠΎΠ»ΠΎΠΊΠ½Π° ΠΈΠ·Π³ΠΎΡΠ°Π²Π»ΠΈΠ²Π°ΡΡ ΠΎΡΡΠΎΠ²Ρ ΠΊ ΠΊΡΠ·ΠΎΠ²Π°ΠΌ Π΄Π»Ρ ΡΡΠΏΠ΅ΡΠΊΠ°ΡΠΎΠ².
Π ΠΌΠΈΠ½ΡΡΠ°ΠΌ Π΄Π°Π½Π½ΠΎΠ³ΠΎ ΠΌΠ°ΡΠ΅ΡΠΈΠ°Π»Π° ΠΌΠΎΠΆΠ½ΠΎ ΠΎΡΠ½Π΅ΡΡΠΈ ΡΡΡΠ΄ΠΎΠ΅ΠΌΠΊΠΎΡΡΡ ΠΏΡΠΈ Π΅Π³ΠΎ ΠΈΡΠΏΠΎΠ»ΡΠ·ΠΎΠ²Π°Π½ΠΈΠΈ Π² Π°Π²ΡΠΎΠΌΠΎΠ±ΠΈΠ»Π΅ΡΡΡΠΎΠ΅Π½ΠΈΠΈ. ΠΠ½ΠΎΠ³Π΄Π° Π΄Π°ΠΆΠ΅ Π½Π΅ΠΎΠ±Ρ ΠΎΠ΄ΠΈΠΌ ΡΡΡΠ½ΠΎΠΉ ΡΡΡΠ΄, ΡΡΠΎ, ΠΊΠΎΠ½Π΅ΡΠ½ΠΎ, Π² ΠΈΡΠΎΠ³Π΅ ΡΠΊΠ°Π·ΡΠ²Π°Π΅ΡΡΡ Π½Π° ΡΠ΅Π½Π΅. ΠΡΠ΅ ΠΎΠ΄ΠΈΠ½ Π½Π΅Π΄ΠΎΡΡΠ°ΡΠΎΠΊ β ΡΡΠΎ ΠΏΡΠ°ΠΊΡΠΈΡΠ΅ΡΠΊΠΈ Π½Π΅Π²ΠΎΠ·ΠΌΠΎΠΆΠ½ΠΎΡΡΡ Π²ΠΎΡΡΡΠ°Π½ΠΎΠ²Π»Π΅Π½ΠΈΡ Π΄Π΅ΡΠ°Π»Π΅ΠΉ ΠΈΠ· ΡΠ³Π»Π΅ΠΏΠ»Π°ΡΡΠΈΠΊΠ° ΠΏΠΎΡΠ»Π΅ Π΄Π΅ΡΠΎΡΠΌΠ°ΡΠΈΠΈ ΠΏΡΠΈ Π°Π²Π°ΡΠΈΡΡ . ΠΡΠ΅ ΡΡΠΎ ΡΠΏΠΎΡΠΎΠ±ΡΡΠ²ΡΠ΅Ρ ΡΠΎΠΌΡ, ΡΡΠΎ ΠΌΠ°ΡΡΠΎΠ²ΠΎ Π°Π²ΡΠΎΠΌΠΎΠ±ΠΈΠ»ΠΈ Π² ΡΠ³Π»Π΅ΠΏΠ»Π°ΡΡΠΈΠΊΠΎΠ²ΠΎΠΌ ΠΊΡΠ·ΠΎΠ²Π΅ ΠΏΡΠ°ΠΊΡΠΈΡΠ΅ΡΠΊΠΈ Π½Π΅ Π²ΡΠΏΡΡΠΊΠ°ΡΡΡΡ.
Π£ ΠΊΠ°ΠΆΠ΄ΠΎΠ³ΠΎ ΡΠΈΠΏΠ° ΠΊΡΠ·ΠΎΠ²ΠΎΠ² Π΅ΡΡΡ ΡΠ²ΠΎΠΈ Π΄ΠΎΡΡΠΎΠΈΠ½ΡΡΠ²Π° ΠΈ Π½Π΅Π΄ΠΎΡΡΠ°ΡΠΊΠΈ. Π’ΡΡ ΡΠΆ Π²ΡΠ΅ Π·Π°Π²ΠΈΡΠΈΡ ΠΎΡ Π²ΠΊΡΡΠΎΠ² ΠΏΠΎΡΡΠ΅Π±ΠΈΡΠ΅Π»Π΅ΠΉ, ΡΠΎ Π΅ΡΡΡ Π½Π°Ρ Ρ Π²Π°ΠΌΠΈ.
Π£Π΄Π°ΡΠ½ΡΡ Π²Π°ΠΌ ΠΏΡΠΈΠΎΠ±ΡΠ΅ΡΠ΅Π½ΠΈΠΉ ΠΈ Π±ΡΠ΄ΡΡΠ΅ Π°ΠΊΠΊΡΡΠ°ΡΠ½Ρ!
Π ΡΡΠ°ΡΡΠ΅ ΠΈΡΠΏΠΎΠ»ΡΠ·ΠΎΠ²Π°Π½Ρ ΠΈΠ·ΠΎΠ±ΡΠ°ΠΆΠ΅Π½ΠΈΡ Ρ ΡΠ°ΠΉΡΠΎΠ² www.rul.ua, www.alu-cover.ru, www.tuning-ural.ruwww.torrentino.com
24 ΠΈΡΠ½Ρ, ΠΠ»Π΅Ρ ΠΎΠ² ΠΠΎΠ½ΡΡΠ°Π½ΡΠΈΠ½
Π’Π΅Π³ΠΈ: ΠΠ²ΡΠΎΠΌΠΎΠ±ΠΈΠ»ΠΈ, ΠΡΡΠΎΡΠΈΡ, ΠΡΠ·ΠΎΠ², Π Π΅ΠΌΠΎΠ½Ρ
ΠΠ»ΡΠΌΠΈΠ½ΠΈΠ΅Π²Π°Ρ Π΄Π΅ΡΠ°Π»Ρ
CΡΡΠ°Π½ΠΈΡΠ° 2
ΠΠ° Π°Π»ΡΠΌΠΈΠ½ΠΈΠ΅Π²ΡΠ΅ Π΄Π΅ΡΠ°Π»ΠΈ Π½Π°Π½Π΅ΡΠ΅Π½ΠΎ ΠΏΠΎΠΊΡΡΡΠΈΠ΅ ΠΈΠ· Ρ ΠΈΠΌΠΈΡΠ΅ΡΠΊΠΎΠ³ΠΎ Π½ΠΈΠΊΠ΅Π»Ρ Ρ ΡΠΎΠ΄Π΅ΡΠΆΠ°Π½ΠΈΠ΅ΠΌ 90 Π²Π΅Ρ. ΠΠ½ΠΎΠ΄Π½ΠΎΠ΅ ΡΠ°ΡΡΠ²ΠΎΡΠ΅Π½ΠΈΠ΅ ΡΠ°ΠΊΠΎΠ³ΠΎ ΠΏΠΎΠΊΡΡΡΠΈΡ Π² ΡΠ°ΡΡΠ²ΠΎΡΠ΅ h3SO4 ΠΏΡΠΈ ΠΏΠ»ΠΎΡΠ½ΠΎΡΡΠΈ ΡΠΎΠΊΠ° 20 Π / Π΄ΠΌ2, ΠΏΡΠΎΠ²ΠΎΠ΄ΠΈΠ²ΡΠ΅Π΅ΡΡ Π΄Π»Ρ ΠΎΠΏΡΠ΅Π΄Π΅Π»Π΅Π½ΠΈΡ Π΅Π³ΠΎ ΡΠΎΠ»ΡΠΈΠ½Ρ, ΠΏΡΠΎΠ΄ΠΎΠ»ΠΆΠ°Π»ΠΎΡΡ Π΄ΠΎ ΡΠ½ΡΡΠΈΡ ΠΏΠΎΠΊΡΡΡΠΈΡ 3 ΠΌΠΈΠ½ 10 Ρ. β
ΠΡΠ²Π΅ΡΠ»ΡΡΡ Π°Π»ΡΠΌΠΈΠ½ΠΈΠ΅Π²ΡΠ΅ Π΄Π΅ΡΠ°Π»ΠΈ Π² ΡΠ°ΡΡΠ²ΠΎΡΠ΅ Π±ΡΡΡ ( 50 Π³ / Π») Ρ Π΄ΠΎΠ±Π°Π²Π»Π΅Π½ΠΈΠ΅ΠΌ Π½Π°ΡΠ°ΡΡΡΠ½ΠΎΠ³ΠΎ ΡΠΏΠΈΡΡΠ° ( 5 ΠΌΠ» / Π»), ΠΊΠΎΡΠΎΡΡΠΌ ΠΏΡΠΎΡΠΈΡΠ°ΡΡ ΠΏΠΎΠ²Π΅ΡΡ Π½ΠΎΡΡΡ Π΄Π΅ΡΠ°Π»ΠΈ, Π° ΠΏΠΎΡΠ»Π΅ Π²ΡΡΡΡ Π°Π½ΠΈΡ Π΄Π΅ΡΠ°Π»Ρ ΠΏΡΠΎΡΠΈΡΠ°ΡΡ Π²Π΅ΡΠΎΡΡΡ. ΠΠ΅ΡΠ°Π»ΠΈ ΠΈΠ· ΡΠΈΠ»ΡΠΌΠΈΠ½Π° ( ΡΠΏΠ»Π°Π²Π° Π°Π»ΡΠΌΠΈΠ½ΠΈΡ Ρ ΠΊΡΠ΅ΠΌΠ½ΠΈΠ΅ΠΌ) Π·Π°ΡΠΈΡΠ°ΡΡ, ΠΎΠ±Π΅Π·ΠΆΠΈΡΠΈΠ²Π°ΡΡ ΠΈ ΠΏΠΎΠΌΠ΅ΡΠ°ΡΡ Π½Π° 10 β 20 ΠΌΠΈΠ½ Π² ΡΠ°ΡΡΠ²ΠΎΡ Ρ ΡΠΎΠΌΠΎΠ²ΠΎΠ³ΠΎ Π°Π½Π³ΠΈΠ΄ΡΠΈΠ΄Π° ( 100 Π³ / Π») ΠΈ ΡΠ΅ΡΠ½ΠΎΠΉ ΠΊΠΈΡΠ»ΠΎΡΡ Ρ ΡΠ΄Π΅Π»ΡΠ½ΡΠΌ Π²Π΅ΡΠΎΠΌ 1 84 ( 10 Π³ / Π»), ΠΏΠΎΡΠ»Π΅ ΡΠ΅Π³ΠΎ Π΄Π΅ΡΠ°Π»Ρ ΠΏΡΠΎΠΌΡΠ²Π°ΡΡ ΠΈ ΡΡΡΠ°Ρ. β
ΠΠΎΡΠ΅ΠΌΡ Π°Π»ΡΠΌΠΈΠ½ΠΈΠ΅Π²ΡΠ΅ Π΄Π΅ΡΠ°Π»ΠΈ Π½Π΅Π»ΡΠ·Ρ ΠΏΠ°ΡΡΡ ΠΎΠ±ΡΠΊΠ½ΠΎΠ²Π΅Π½Π½ΡΠΌ ΠΎΠ»ΠΎΠ²ΡΠ½Π½ΡΡ ΠΏΡΠΈΠΏΠΎΠ΅ΠΌ. β
Π‘ΠΊΠ»Π΅ΠΈΠ²Π°ΡΡ Π°Π»ΡΠΌΠΈΠ½ΠΈΠ΅Π²ΡΠ΅ Π΄Π΅ΡΠ°Π»ΠΈ Π½Π΅ΠΎΠ±Ρ ΠΎΠ΄ΠΈΠΌΠΎ ΠΏΠΎΠ΄ Π΄Π°Π²Π»Π΅Π½ΠΈΠ΅ΠΌ 0 2 β 0 6 ΠΊΠ / ΡΠΌ2 ΠΏΡΠΈ ΡΠ΅ΠΌΠΏΠ΅ΡΠ°ΡΡΡΠ΅ Π² ΠΏΠΎΠΌΠ΅ΡΠ΅Π½ΠΈΠΈ 18 β 20 Π‘. ΠΠΏΡΠΈΠΌΠ°Π»ΡΠ½ΠΎΠΉ ΠΏΡΠΈ Ρ ΠΎΠ»ΠΎΠ΄Π½ΠΎΠΌ ΡΠΏΠΎΡΠΎΠ±Π΅ ΡΠΊΠ»Π΅ΠΈΠ²Π°Π½ΠΈΡ ΡΠ²Π»ΡΠ΅ΡΡΡ Π²ΡΠ΄Π΅ΡΠΆΠΊΠ° ΠΏΠΎΠ΄ Π΄Π°Π²Π»Π΅Π½ΠΈΠ΅ΠΌ Π² ΡΠ΅ΡΠ΅Π½ΠΈΠ΅ ΡΡΡΠΎΠΊ. ΠΠ΄Π½Π°ΠΊΠΎ ΠΊΠ»Π΅Π΅Π²ΠΎΠ΅ ΡΠΎΠ΅Π΄ΠΈΠ½Π΅Π½ΠΈΠ΅ ΠΏΡΠΈΠΎΠ±ΡΠ΅ΡΠ°Π΅Ρ Π΄ΠΎΡΡΠ°ΡΠΎΡΠ½ΠΎ Π²ΡΡΠΎΠΊΡΡ ΠΏΡΠΎΡΠ½ΠΎΡΡΡ ΡΠΆΠ΅ ΠΏΠΎΡΠ»Π΅ ΠΈΡΡΠ΅ΡΠ΅Π½ΠΈΡ 12 Ρ Ρ ΠΌΠΎΠΌΠ΅Π½ΡΠ° Π΅Π³ΠΎ ΠΈΠ·Π³ΠΎΡΠΎΠ²Π»Π΅Π½ΠΈΡ. β
ΠΠ° Π°Π»ΡΠΌΠΈΠ½ΠΈΠ΅Π²ΡΠ΅ Π΄Π΅ΡΠ°Π»ΠΈ ΠΌΠ΅ΡΠΎΠ΄ΠΎΠΌ Ρ ΠΈΠΌΠΈΡΠ΅ΡΠΊΠΎΠ³ΠΎ Π½ΠΈΠΊΠ΅Π»ΠΈΡΠΎΠ²Π°Π½ΠΈΡ Π½Π°Π½Π΅ΡΠ΅Π½ΠΎ ΠΏΠΎΠΊΡΡΡΠΈΠ΅ Ρ ΡΠΎΠ΄Π΅ΡΠΆΠ°Π½ΠΈΠ΅ΠΌ 90 % ( ΠΌΠ°Π΅. ΠΠ½ΠΎΠ΄Π½ΠΎΠ΅ ΡΠ°ΡΡΠ²ΠΎΡΠ΅Π½ΠΈΠ΅ ΡΠ°ΠΊΠΎΠ³ΠΎ ΠΏΠΎΠΊΡΡΡΠΈΡ Π² ΡΠ°ΡΡΠ²ΠΎΡΠ΅ h3SO4 ΠΏΡΠΈ ΠΏΠ»ΠΎΡΠ½ΠΎΡΡΠΈ ΡΠΎΠΊΠ° 20 Π / Π΄ΠΌ2, ΠΏΡΠΎΠ²ΠΎΠ΄ΠΈΠ²ΡΠ΅Π΅ΡΡ Π΄Π»Ρ ΠΎΠΏΡΠ΅Π΄Π΅Π»Π΅Π½ΠΈΡ Π΅Π³ΠΎ ΡΠΎΠ»ΡΠΈΠ½Ρ, ΠΏΡΠΎΠ΄ΠΎΠ»ΠΆΠ°Π»ΠΎΡΡ 3 ΠΌΠΈΠ½ 10 Ρ. ΠΡΠΈ ΡΠ°ΡΡΠ²ΠΎΡΠ΅Π½ΠΈΠΈ 15 % ΡΠΎΡΡΠΎΡΠ° ΠΈΠ· ΠΏΠΎΠΊΡΡΡΠΈΡ ΠΎΠΊΠΈΡΠ»ΡΠ»ΠΎΡΡ Π΄ΠΎ ΡΠΎΡΡΠΈΡΠ°, ΠΎΡΡΠ°Π»ΡΠ½Π°Ρ ΡΠ°ΡΡΡ-Π΄ΠΎ ΡΠΎΡΡΠ°ΡΠ°. β
ΠΡΠΎΠΈΠ·Π²ΠΎΠ΄ΡΡΠ²ΠΎ Π°Π»ΡΠΌΠΈΠ½ΠΈΠ΅Π²ΡΡ Π΄Π΅ΡΠ°Π»Π΅ΠΉ ΠΌΠ΅ΡΠΎΠ΄ΠΎΠΌ ΠΊΠΎΠΊΠΈΠ»ΡΠ½ΠΎΠ³ΠΎ Π»ΠΈΡΡΡ ΠΈ Π² Π»ΠΈΡΡΠ΅Π²ΡΡ ΠΌΠ°ΡΠΈΠ½Π°Ρ ΠΎΠ±Π΅ΡΠΏΠ΅ΡΠΈΠ²Π°Π΅Ρ Π²ΡΡΠΎΠΊΡΡ ΠΏΡΠΎΠΈΠ·Π²ΠΎΠ΄ΠΈΡΠ΅Π»ΡΠ½ΠΎΡΡΡ, ΡΠΎΡΠ½ΠΎΡΡΡ ΠΈ ΡΠΊΠΎΠ½ΠΎΠΌΠΈΡ ΠΌΠ΅ΡΠ°Π»Π»ΠΎΠ². β
ΠΠΎΠ΄Π³ΠΎΡΠΎΠ²ΠΊΡ Π°Π»ΡΠΌΠΈΠ½ΠΈΠ΅Π²ΡΡ Π΄Π΅ΡΠ°Π»Π΅ΠΉ ΠΏΠΎΠ΄ ΠΏΠΎΠΊΡΡΡΠΈΠ΅ ΠΊΡΠΈΡΡΠ°Π»Π»ΠΈΡ ( ΠΎΠ±Π΅Π·ΠΆΠΈΡΠΈΠ²Π°Π½ΠΈΠ΅, ΡΡΠ°Π²Π»Π΅Π½ΠΈΠ΅) ΠΏΡΠΎΠΈΠ·Π²ΠΎΠ΄ΡΡ ΠΎΠ±ΡΡΠ½ΡΠΌ ΠΏΡΡΠ΅ΠΌ. β
ΠΡΠΈΠΌΠ΅Π½Π΅Π½ΠΈΠ΅ Π°Π»ΡΠΌΠΈΠ½ΠΈΠ΅Π²ΡΡ Π΄Π΅ΡΠ°Π»Π΅ΠΉ, ΠΎΡΠ»ΠΈΡΡΡ ΠΏΠΎΠ΄ Π΄Π°Π²Π»Π΅Π½ΠΈΠ΅ΠΌ, ΠΏΠΎΠ·Π²ΠΎΠ»ΡΠ΅Ρ ΡΠΎΠ·Π΄Π°ΡΡ ΡΠΎΠ½ΠΊΠΈΠ΅ ΠΈ ΠΏΡΠΎΡΠ½ΡΠ΅ ΡΡΠ΅Π½ΠΊΠΈ ΠΎΡΠ»ΠΈΠ²ΠΎΠΊ. Π ΡΡΠΎΠΌ ΡΠ»ΡΡΠ°Π΅ ΠΏΡΠΈ ΠΏΠ΅ΡΠ΅Ρ ΠΎΠ΄Π΅ ΠΎΡ ΡΡΠ³ΡΠ½Π½ΡΡ Π΄Π΅ΡΠ°Π»Π΅ΠΉ ΠΊ Π°Π»ΡΠΌΠΈΠ½ΠΈΠ΅Π²ΡΠΌ Π·Π½Π°ΡΠΈΡΠ΅Π»ΡΠ½ΠΎ ΡΠΌΠ΅Π½ΡΡΠ°Π΅ΡΡΡ ΠΌΠ°ΡΡΠ° ΠΎΡΠ»ΠΈΠ²ΠΎΠΊ. Π’ΠΎΠ»ΡΠΈΠΏΠ° ΡΡΠ΅Π½ΠΎΠΊ ΡΡΠ³ΡΠ½Π½ΡΡ ΠΎΡΠ»ΠΈΠ²ΠΎΠΊ Π² Π½Π°ΡΡΠΎΡΡΠ΅Π΅ Π²ΡΠ΅ΠΌΡ Π΄ΠΎΠ²Π΅Π΄Π΅Π½Π° Π΄ΠΎ 3 2 β 3 5 ΠΌΠΌ. Π ΡΡΠΎΠΌ ΡΠ»ΡΡΠ°Π΅ ΠΌΠ°ΡΡΡ ΡΡΠ³ΡΠ½Π½ΡΡ Π±Π»ΠΎΠΊ-ΠΊΠ°ΡΡΠ΅ΡΠΎΠ² ΠΏΡΠΈΠ±Π»ΠΈΠΆΠ°ΡΡΡΡ ΠΊ Π°Π»ΡΠΌΠΈΠ½ΠΈΠ΅Π²ΡΠΌ.
ΠΠ²ΡΠΎΠΌΠΎΠ±ΠΈΠ»ΠΈ Ρ Π°Π»ΡΠΌΠΈΠ½ΠΈΠ΅Π²ΡΠΌ ΠΊΡΠ·ΠΎΠ²ΠΎΠΌ
Π ΠΊΠΎΠ½ΡΡΡΡΠΊΡΠΈΡΡ Π±Π»ΠΎΠΊ-ΠΊΠ°ΡΡΠ΅ΡΠΎΠ², ΠΎΡΠΎΠ±Π΅Π½Π½ΠΎ ΠΈΠ· Π°Π»ΡΠΌΠΈΠ½ΠΈΠ΅Π²ΡΡ ΡΠΏΠ»Π°Π²ΠΎΠ², ΠΏΠ΅ΡΠ΅Ρ ΠΎΠ΄Ρ ΠΎΡ ΡΠΎΠ»ΡΡΡΡ ΡΡΠ΅Π½ΠΎΠΊ ΠΊ ΡΠΎΠ½ΠΊΠΈΠΌ Π΄ΠΎΠ»ΠΆΠ½Ρ Π±ΡΡΡ ΠΏΠ»Π°Π²Π½ΡΠΌΠΈ. β
ΠΠ· Π°Π»ΡΠΌΠΈΠ½ΠΈΠ΅Π²ΡΡ Π΄Π΅ΡΠ°Π»Π΅ΠΉ ΡΠ»ΠΎΠΌΠ°Π²ΡΠΈΠ΅ΡΡ ΡΠΏΠΈΠ»ΡΠΊΠΈ ΡΠ΄Π°Π»ΡΡΡ ΠΏΡΡΠ΅ΠΌ ΡΡΠ°Π²Π»Π΅Π½ΠΈΡ, Π΄Π»Ρ ΡΠ΅Π³ΠΎ Π² ΡΠ΅Π»Π΅ ΡΠΏΠΈΠ»ΡΠΊΠΈ Π²ΡΡΠ²Π΅ΡΠ»ΠΈΠ²Π°ΡΡ ΠΎΡΠ²Π΅ΡΡΡΠΈΠ΅, ΠΏΡΠΈ ΡΡΠΎΠΌ Π½Π°Π΄ΠΎ ΠΎΡΡΠ΅ΡΠ΅Π³Π°ΡΡΡΡ ΠΏΠΎΠ²ΡΠ΅ΠΆΠ΄Π΅Π½ΠΈΡ ΡΠ΅Π·ΡΠ±Ρ Π΄Π΅ΡΠ°Π»ΠΈ. Π ΠΊΠ°ΡΠ΅ΡΡΠ²Π΅ ΠΊΠ°ΡΠ°Π»ΠΈΠ·Π°ΡΠΎΡΠ° ΠΏΡΠΈΠΌΠ΅Π½ΡΡΡ ΠΊΡΡΠΎΡΠΊΠΈ ΠΆΠ΅Π»Π΅Π·Π½ΠΎΠΉ ( Π²ΡΠ·Π°Π»ΡΠ½ΠΎΠΉ) ΠΏΡΠΎΠ²ΠΎΠ»ΠΎΠΊΠΈ, ΠΊΠΎΡΠΎΡΡΠ΅ ΠΎΠΏΡΡΠΊΠ°ΡΡ Π² ΡΠ°ΡΡΠ²ΠΎΡ ΠΊΠΈΡΠ»ΠΎΡΡ, Π½Π°Π»ΠΈΡΠΎΠΉ Π² ΠΎΡΠ²Π΅ΡΡΡΠΈΠ΅ ΡΠΏΠΈΠ»ΡΠΊΠΈ. ΠΡΠΎΡΠ΅ΡΡ ΠΏΡΠΎΠ΄ΠΎΠ»ΠΆΠ°Π΅ΡΡΡ Π½Π΅ΡΠΊΠΎΠ»ΡΠΊΠΎ ΡΠ°ΡΠΎΠ², Π΄ΠΎ ΡΠ΅Ρ ΠΏΠΎΡ, ΠΏΠΎΠΊΠ° ΠΌΠ΅ΡΠ°Π»Π» ΡΠΏΠΈΠ»ΡΠΊΠΈ Π½Π΅ Π±ΡΠ΄Π΅Ρ ΠΎΠΊΠΎΠ½ΡΠ°ΡΠ΅Π»ΡΠ½ΠΎ ΡΠ°Π·ΡΡΡΠ΅Π½. ΠΠΎΡΠ»Π΅ ΡΡΠΎΠ³ΠΎ ΠΎΡΡΠ°ΡΠΊΠΈ ΠΊΠΈΡΠ»ΠΎΡΡ ΡΠ΄Π°Π»ΡΡΡ, Π° ΠΎΡΠ²Π΅ΡΡΡΠΈΠ΅ ΠΏΡΠΎΠΌΡΠ²Π°ΡΡ. β
ΠΠ· Π°Π»ΡΠΌΠΈΠ½ΠΈΠ΅Π²ΡΡ Π΄Π΅ΡΠ°Π»Π΅ΠΉ ΡΠ»ΠΎΠΌΠ°Π²ΡΠΈΠ΅ΡΡ ΡΠΏΠΈΠ»ΡΠΊΠΈ ΡΠ΄Π°Π»ΡΡΡ ΠΏΡΡΠ΅ΠΌ ΡΡΠ°Π²Π»Π΅Π½ΠΈΡ, Π΄Π»Ρ ΡΠ΅Π³ΠΎ Π² ΡΠ΅Π»Π΅ ΡΠΏΠΈΠ»ΡΠΊΠΈ Π²ΡΡΠ²Π΅ΡΠ»ΠΈΠ²Π°ΡΡ ΠΎΡΠ²Π΅ΡΡΡΠΈΠ΅, ΠΏΡΠΈ ΡΡΠΎΠΌ Π½Π°Π΄ΠΎ ΠΎΡΡΠ΅ΡΠ΅Π³Π°ΡΡΡΡ ΠΏΠΎΠ²ΡΠ΅ΠΆΠ΄Π΅Π½ΠΈΡ ΡΠ΅Π·ΡΠ±Ρ Π΄Π΅ΡΠ°Π»ΠΈ. Π ΠΊΠ°ΡΠ΅ΡΡΠ²Π΅ ΠΊΠ°ΡΠ°Π»ΠΈΠ·Π°ΡΠΎΡΠ° ΠΏΡΠΈΠΌΠ΅Π½ΡΡΡ ΠΊΡΡΠΎΡΠΊΠΈ ΠΆΠ΅Π»Π΅Π·Π½ΠΎΠΉ ( Π²ΡΠ·Π°Π»ΡΠ½ΠΎΠΉ) ΠΏΡΠΎΠ²ΠΎΠ»ΠΎΠΊΠΈ, ΠΊΠΎΡΠΎΡΡΠ΅ ΠΎΠΏΡΡΠΊΠ°ΡΡ Π² ΡΠ°ΡΡΠ²ΠΎΡ ΠΊΠΈΡΠ»ΠΎΡΡ, Π½Π°ΠΏΠΈΡΠΎΠΉ Π² ΠΎΡΠ²Π΅ΡΡΡΠΈΠ΅ ΡΠΏΠΈΠ»ΡΠΊΠΈ. ΠΡΠΎΡΠ΅ΡΡ ΠΏΡΠΎΠ΄ΠΎΠ»ΠΆΠ°Π΅ΡΡΡ Π½Π΅ΡΠΊΠΎΠ»ΡΠΊΠΎ ΡΠ°ΡΠΎΠ², Π΄ΠΎ ΡΠ΅Ρ ΠΏΠΎΡ, ΠΏΠΎΠΊΠ° ΠΌΠ΅ΡΠ°Π»Π» ΡΠΏΠΈΠ»ΡΠΊΠΈ Π½Π΅ Π±ΡΠ΄Π΅Ρ ΠΎΠΊΠΎΠ½ΡΠ°ΡΠ΅Π»ΡΠ½ΠΎ ΡΠ°Π·ΡΡΡΠ΅Π½. ΠΠΎΡΠ»Π΅ ΡΡΠΎΠ³ΠΎ ΠΎΡΡΠ°ΡΠΊΠΈ ΠΊΠΈΡΠ»ΠΎΡΡ ΡΠ΄Π°Π»ΡΡΡ, Π° ΠΎΡΠ²Π΅ΡΡΡΠΈΠ΅ ΠΏΡΠΎΠΌΡΠ²Π°ΡΡ. β
Π‘Π²Π°ΡΠΊΡ Π°Π»ΡΠΌΠΈΠ½ΠΈΠ΅Π²ΡΡ Π΄Π΅ΡΠ°Π»Π΅ΠΉ ΠΈΠ·-Π·Π° Π²ΡΡΠΎΠΊΠΎΠΉ ΠΆΠΈΠ΄ΠΊΠΎΡΠ΅ΠΊΡΡΠ΅ΡΡΠΈ Π½Π°Π³ΡΠ΅ΡΠΎΠ³ΠΎ Π°Π»ΡΠΌΠΈΠ½ΠΈΡ ΠΏΡΠΎΠΈΠ·Π²ΠΎΠ΄ΡΡ, ΡΡΡΠ°Π½Π°Π²Π»ΠΈΠ²Π°Ρ ΠΏΠΎΠ΄ Π·Π°Π²Π°ΡΠΈΠ²Π°Π΅ΠΌΡΠΌΠΈ ΡΡΠ΅ΡΠΈΠ½Π°ΠΌΠΈ ΡΡΠ°Π»ΡΠ½ΡΠ΅ ΠΈΠ»ΠΈ Π³ΡΠ°ΡΠΈΡΠΎΠ²ΡΠ΅ ΠΏΠΎΠ΄ΠΊΠ»Π°Π΄ΠΊΠΈ. β
Π Π°Π»ΡΠΌΠΈΠ½ΠΈΠ΅Π²ΡΡ Π΄Π΅ΡΠ°Π»ΡΡ ΡΠ΅Π»Π΅ΡΠΎΠΎΠ±ΡΠ°Π·Π½ΠΎ Π·Π°ΠΌΠ΅Π½ΡΡΡ Π±ΠΎΠ»ΡΡ Π½Π° ΡΠΏΠΈΠ»ΡΠΊΡ ΠΈ Π³Π°ΠΉΠΊΡ. Π‘Π½Π°ΡΠ°Π»Π° Π² ΠΊΠΎΡΠΏΡΡΠ΅ ΡΡΡΠ°Π½Π°Π²Π»ΠΈΠ²Π°ΡΡ Π½Π° ΠΊΠ»Π΅ΠΉ ΡΠΏΠΈΠ»ΡΠΊΡ, Π½Π° ΠΊΠΎΡΠΎΡΡΡ Π±ΡΠ΄Π΅Ρ Π½Π°Π΄Π΅Π²Π°ΡΡΡΡ Π΄Π΅ΡΠ°Π»Ρ ΠΈ ΠΊΡΠ΅ΠΏΠΈΡΡΡΡ Π³Π°ΠΉΠΊΠΎΠΉ. Π ΡΡΠΎΠΌ ΡΠ»ΡΡΠ°Π΅ ΠΈΠ·Π½ΠΎΡ ΡΠΎΠ΅Π΄ΠΈΠ½Π΅Π½ΠΈΡ ΠΏΡΠΈ ΡΠ±ΠΎΡΠΊΠ΅ ΠΈ ΡΠ°Π·Π±ΠΎΡΠΊΠ΅ Π·Π½Π°ΡΠΈΡΠ΅Π»ΡΠ½ΠΎ ΡΠΌΠ΅Π½ΡΡΠ°Π΅ΡΡΡ. ΠΡΠ»ΠΈ ΠΏΠΎΠ·Π²ΠΎΠ»ΡΠ΅Ρ ΠΊΠΎΠ½ΡΡΡΡΠΊΡΠΈΡ, Π΄ΠΎΠΏΡΡΠΊΠ°Π΅ΡΡΡ Π²ΠΎΡΡΡΠ°Π½Π°Π²Π»ΠΈΠ²Π°ΡΡ ΡΠ΅Π·ΡΠ±ΠΎΠ²ΠΎΠ΅ ΠΎΡΠ²Π΅ΡΡΡΠΈΠ΅ ΡΠ°ΡΡΠ²Π΅ΡΠ»ΠΈΠ²Π°Π½ΠΈΠ΅ΠΌ Π΄ΠΎ Π±Π»ΠΈΠΆΠ°ΠΉΡΠ΅Π³ΠΎ Π±ΠΎΠ»ΡΡΠ΅Π³ΠΎ Π΄ΠΈΠ°ΠΌΠ΅ΡΡΠ° ΡΠ°Π·ΠΌΠ΅ΡΠ½ΠΎΠ³ΠΎ ΡΡΠ΄Π° ΡΠ΅Π·ΡΠ±Ρ. β
ΠΡΠΈ ΡΡΠΎΠΌ Π°Π»ΡΠΌΠΈΠ½ΠΈΠ΅Π²ΡΠ΅ Π΄Π΅ΡΠ°Π»ΠΈ ΠΏΠΎΠΊΡΡΠ²Π°ΡΡΡΡ ΡΠΎΠ½ΠΊΠΎΠΉ ΠΏΠ»Π΅Π½ΠΊΠΎΠΉ ΡΠΈΠ½ΠΊΠ° ( 0 1 β 0 15 ΠΌΠΊΠΌ), ΠΏΡΠ΅Π΄ΠΎΡ ΡΠ°Π½ΡΡΡΠ΅ΠΉ ΠΏΠΎΠ²Π΅ΡΡ Π½ΠΎΡΡΡ ΠΎΡ ΠΎΠΊΠΈΡΠ»Π΅Π½ΠΈΡ. ΠΠ°ΠΈΠ±ΠΎΠ»Π΅Π΅ ΡΠΏΡΠΎΡΠ½ΠΎΠ΅ ΡΡΠ΅ΠΏΠ»Π΅Π½ΠΈΠ΅ Ρ Π³Π°Π»ΡΠ²Π°Π½ΠΈΡΠ΅ΡΠΊΠΈΠΌΠΈ ΠΏΠΎΠΊΡΡΡΠΈΡΠΌΠΈ ΠΌΠ΅ΡΠ°Π»Π»ΠΎΠ² Π΄ΠΎΡΡΠΈΠ³Π°Π΅ΡΡΡ ΠΏΡΠΈ Π½Π°Π½Π΅ΡΠ΅Π½ΠΈΠΈ Π±ΠΎΠ»Π΅Π΅ ΡΠΎΠ½ΠΊΠΈΡ , ΠΏΠ»ΠΎΡΠ½ΡΡ ΠΈ ΡΠΏΠ»ΠΎΡΠ½ΡΡ ΡΠΈΠ½ΠΊΠΎΠ²ΡΡ ΠΏΠ»Π΅Π½ΠΎΠΊ. Π‘Π½ΠΈΠΆΠ΅Π½ΠΈΠ΅ ΠΊΠΎΠ½ΡΠ΅Π½ΡΡΠ°ΡΠΈΠΈ ΡΠ°ΡΡΠ²ΠΎΡΠ° ΠΏΡΠΈΠ²ΠΎΠ΄ΠΈΡ ΠΊ ΠΎΠ±ΡΠ°Π·ΠΎΠ²Π°Π½ΠΈΡ Π±ΠΎΠ»Π΅Π΅ ΡΠΎΠ»ΡΡΡΡ ΠΈ ΠΌΠ΅Π½Π΅Π΅ ΠΏΠ»ΠΎΡΠ½ΡΡ ΠΎΡΠ°Π΄ΠΊΠΎΠ². β
Π ΠΏΡΠ°ΠΊΡΠΈΠΊΠ΅ Π°Π»ΡΠΌΠΈΠ½ΠΈΠ΅Π²ΡΠ΅ Π΄Π΅ΡΠ°Π»ΠΈ ΠΎΠ±Π΅Π·ΠΆΠΈΡΠΈΠ²Π°ΡΡΡΡ ( ΠΏΠ΅ΡΠ΅Π΄ Π°Π½ΠΎΠ΄ΠΈΡΠΎΠ²Π°Π½ΠΈΠ΅ΠΌ) ΡΡΠ°Π²Π»Π΅Π½ΠΈΠ΅ΠΌ Π² 5Π± β Π½ΠΎΠΌ ΡΠ°ΡΡΠ²ΠΎΡΠ΅ NaOH. ΠΠ»Ρ Π΄Π»ΠΈΡΠ΅Π»ΡΠ½ΠΎΠ³ΠΎ Ρ ΡΠ°Π½Π΅Π½ΠΈΡ Π°Π»ΡΠΌΠΈΠ½ΠΈΠ΅Π²ΡΡ ΠΈΠ·Π΄Π΅Π»ΠΈΠΉ ΠΈΡ ΠΏΡΠΎΠΌΡΠ²Π°ΡΡ 2 % β Π½ΡΠΌ ΡΠ°ΡΡΠ²ΠΎΡΠΎΠΌ ΡΠΌΠ΅ΡΠΈ NaOH, Na2CO3 ΠΈ ΠΆΠΈΠ΄ΠΊΠΎΠ³ΠΎ ΡΡΠ΅ΠΊΠ»Π°, ΠΏΡΠΈΠΌΠ΅Π½ΡΡΡΠ΅Π³ΠΎΡΡ Π² ΠΊΠ°ΡΠ΅ΡΡΠ²Π΅ ΠΈΠ½Π³ΠΈΠ±ΠΈΡΠΎΡΠ°. β
Π‘ΡΡΠ°Π½ΠΈΡΡ: β βββ1 βββ2 βββ3 βββ4
Π‘ΡΠ°ΡΡΠΈ ΠΏΠΎ ΡΠ΅ΠΌΠ΅:
- ΠΠΠ ΠΠΠΠΠ’Π¬ ΠΠΠΠΠ
ΠΠ»ΠΈΠΌΠ°Ρ Ρ Π½Π°Ρ ΠΊΠ°ΠΏΡΠΈΠ·Π½ΡΠΉ. ΠΠ΅ΡΠ΅ΡΠΎΠΌ ΡΠΈΡ Π°Ρ ΠΏΠΎΠ³ΠΎΠ΄Π°, Π° ΡΠΆΠ΅ ΡΠ΅ΡΠ΅Π· ΡΠ°Ρ ΠΏΡΠΈΡΠΎΠ΄Π° ΠΏΡΠ΅ΠΏΠΎΠ΄Π½ΠΎΡΠΈΡ Π½Π°ΠΌ ΡΡΡΠΏΡΠΈΠ·β¦
- ΠΠΠΠΠΠΠΠΠΠΠΠ
ΠΡΠΈΠ½ΡΠΈΠΏ ΡΠ°Π±ΠΎΡΡ ΠΈΠΌΠΌΠΎΠ±ΠΈΠ»Π°ΠΉΠ·Π΅ΡΠ°Π§ΡΠΎ ΡΠ°ΠΊΠΎΠ΅ ΠΈΠΌΠΌΠΎΠ±ΠΈΠ»Π°ΠΉΠ·Π΅Ρ Π² ΠΌΠ°ΡΠΈΠ½Π΅ ΠΈ Π΄Π»Ρ ΡΠ΅Π³ΠΎ ΠΎΠ½ Π½ΡΠΆΠ΅Π½ΠΠΌΠΌΠΎΠ±ΠΈΠ»Π°ΠΉΠ·Π΅Ρ — ΡΡΠΎ ΡΡΠΎβ¦
- ΠΠΠΠ£ΠΠΠΠΠ‘ΠΠΠΠ― ΠΠΠΠΠΠ‘ΠΠ
Π’Π΅Ρ Π½ΠΎΠ»ΠΎΠ³ΠΈΠΈ ΡΠΆΠ΅ Π΄Π°Π²Π½ΠΎ ΠΏΠ΅ΡΠ΅ΡΡΠ°Π»ΠΈ ΡΡΠΎΡΡΡ Π½Π° ΠΌΠ΅ΡΡΠ΅. ΠΠΆΠ΅Π³ΠΎΠ΄Π½ΠΎ Π² ΠΌΠΈΡΠ΅ Π°Π²ΡΠΎΠΌΠΎΠ±ΠΈΠ»Π΅ΠΉ ΠΏΡΠΈΠΌΠ΅Π½ΡΡΡΡΡ Π½ΠΎΠ²ΡΠ΅ ΡΠ΅ΡΠ΅Π½ΠΈΡ Π²β¦
ΠΠ΅ΠΌΠ½ΠΎΠ³ΠΎ ΠΈΠ· ΠΈΡΡΠΎΡΠΈΠΈ
ΠΡΠΏΠΎΠ»ΡΠ·ΠΎΠ²Π°Π½ΠΈΠ΅ Π°Π»ΡΠΌΠΈΠ½ΠΈΡ Π² ΠΏΡΠΎΠΈΠ·Π²ΠΎΠ΄ΡΡΠ²Π΅ ΠΊΡΠ·ΠΎΠ²Π° ΠΊΠ°ΠΆΠ΅ΡΡΡ ΡΡΠΎΠ»Ρ ΡΠΎΠ±Π»Π°Π·Π½ΠΈΡΠ΅Π»ΡΠ½ΠΎΠΉ ΠΈ Π½ΠΎΠ²ΠΎΠΉ ΡΠ΅Ρ Π½ΠΎΠ»ΠΎΠ³ΠΈΠ΅ΠΉ, ΡΡΠΎ Π·Π°Π±ΡΠ²Π°Π΅ΡΡΡ, ΡΡΠΎ ΡΠΎΠ΄ΠΎΠΌ ΠΎΠ½Π° ΠΈΠ· ΠΏΠ΅ΡΠ²ΠΎΠΉ ΠΏΠΎΠ»ΠΎΠ²ΠΈΠ½Ρ Π΄Π²Π°Π΄ΡΠ°ΡΠΎΠ³ΠΎ Π²Π΅ΠΊΠ°. ΠΠ°ΠΊ ΠΊΠΎΠ½ΡΡΡΡΠΊΡΠΈΠ²Π½ΡΠΉ ΠΌΠ°ΡΠ΅ΡΠΈΠ°Π» Π΄Π»Ρ Π°Π²ΡΠΎ Π΅Π³ΠΎ ΠΎΠΏΡΠΎΠ±ΠΎΠ²Π°Π»ΠΈ ΡΡΠ°Π·Ρ, ΠΊΠ°ΠΊ ΡΠΎΠ»ΡΠΊΠΎ Π½Π°ΡΠ°Π»ΠΈ ΠΎΡΠΊΠ°Π·ΡΠ²Π°ΡΡΡΡ ΠΎΡ Π΄Π΅ΡΠ΅Π²Π° ΠΈ ΠΊΠΎΠΆΠΈ, ΠΏΡΠΈΡΠ΅ΠΌ ΠΈΠΌΠ΅Π½Π½ΠΎ Ρ Π΄Π΅ΡΠ΅Π²ΠΎΠΌ ΠΎΠ½ ΠΎΠΊΠ°Π·Π°Π»ΡΡ Π½Π°ΡΡΠΎΠ»ΡΠΊΠΎ Ρ ΠΎΡΠΎΡΠΎ ΡΠΎΠ²ΠΌΠ΅ΡΡΠΈΠΌ, ΡΡΠΎ Π½Π° Π°Π²ΡΠΎΠΌΠΎΠ±ΠΈΠ»ΡΡ Morgan ΠΏΠΎΠ΄ΠΎΠ±Π½Π°Ρ ΡΠ΅Ρ Π½ΠΎΠ»ΠΎΠ³ΠΈΡ ΠΈΡΠΏΠΎΠ»ΡΠ·ΡΠ΅ΡΡΡ Π΄ΠΎ ΡΠΈΡ ΠΏΠΎΡ. ΠΠΎΡ ΡΠΎΠ»ΡΠΊΠΎ Π±ΠΎΠ»ΡΡΠΈΠ½ΡΡΠ²ΠΎ ΠΊΠΎΠΌΠΏΠ°Π½ΠΈΠΉ, ΠΊΠΎΡΠΎΡΡΠ΅ Π² ΡΡΠΈΠ΄ΡΠ°ΡΡΠ΅ Π³ΠΎΠ΄Ρ ΡΡΠΏΠ΅Π»ΠΈ ΠΈΠ·Π³ΠΎΡΠΎΠ²ΠΈΡΡ Π½Π΅ΠΌΠ°Π»ΠΎ Π°Π²ΡΠΎΠΌΠΎΠ±ΠΈΠ»Π΅ΠΉ Ρ ΡΠΈΡΠΎΠΊΠΈΠΌ ΠΈΡΠΏΠΎΠ»ΡΠ·ΠΎΠ²Π°Π½ΠΈΠ΅ΠΌ Π°Π»ΡΠΌΠΈΠ½ΠΈΠ΅Π²ΡΡ Π΄Π΅ΡΠ°Π»Π΅ΠΉ, Π² Π΄Π°Π»ΡΠ½Π΅ΠΉΡΠ΅ΠΌ ΠΎΡ Π»Π΅Π³ΠΊΠΎΠ³ΠΎ ΠΌΠ΅ΡΠ°Π»Π»Π° ΠΎΡΠΊΠ°Π·Π°Π»ΠΈΡΡ. Π ΠΏΡΠΈΡΠΈΠ½ΠΎΠΉ ΡΡΠ°Π» Π½Π΅ ΡΠΎΠ»ΡΠΊΠΎ Π΄Π΅ΡΠΈΡΠΈΡ ΡΡΠΎΠ³ΠΎ ΠΌΠ°ΡΠ΅ΡΠΈΠ°Π»Π° Π² Π³ΠΎΠ΄Ρ ΠΡΠΎΡΠΎΠΉ ΠΌΠΈΡΠΎΠ²ΠΎΠΉ. ΠΠ»Π°Π½Π°ΠΌ ΡΠ°Π½ΡΠ°ΡΡΠΎΠ²-ΡΡΡΡΡΠΈΡΡΠΎΠ² ΠΎ ΡΠΈΡΠΎΠΊΠΎΠΌ ΠΈΡΠΏΠΎΠ»ΡΠ·ΠΎΠ²Π°Π½ΠΈΠΈ Π°Π»ΡΠΌΠΈΠ½ΠΈΡ Π² ΠΊΠΎΠ½ΡΡΡΡΠΊΡΠΈΠΈ ΠΌΠ°ΡΠΈΠ½ Π½Π΅ ΡΡΠΆΠ΄Π΅Π½ΠΎ Π±ΡΠ»ΠΎ ΡΠ±ΡΡΡΡΡ. ΠΠΎ Π²ΡΡΠΊΠΎΠΌ ΡΠ»ΡΡΠ°Π΅, Π΄ΠΎ Π½ΡΠ½Π΅ΡΠ½Π΅Π³ΠΎ ΠΌΠΎΠΌΠ΅Π½ΡΠ°, ΠΊΠΎΠ³Π΄Π° ΡΡΠΎ-ΡΠΎ ΡΡΠ°Π»ΠΎ ΠΌΠ΅Π½ΡΡΡΡΡ.
ΠΠ»ΡΠΌΠΈΠ½ΠΈΠΉ Π² ΠΌΠ΅ΡΠ°Π»Π»ΠΈΡΠ΅ΡΠΊΠΎΠΉ ΡΠΎΡΠΌΠ΅ ΠΈΠ·Π²Π΅ΡΡΠ΅Π½ Π½Π΅ ΡΠ°ΠΊ ΡΠΆ Π΄Π°Π²Π½ΠΎ β Π΅Π³ΠΎ Π²ΡΠ²Π΅Π»ΠΈ ΡΠΎΠ»ΡΠΊΠΎ Π² ΠΊΠΎΠ½ΡΠ΅ XIX Π²Π΅ΠΊΠ°, ΠΈ ΠΎΠ½ ΡΡΠ°Π·Ρ ΡΡΠ°Π» ΡΠ΅Π½ΠΈΡΡΡΡ Π²Π΅ΡΡΠΌΠ° Π²ΡΡΠΎΠΊΠΎ. Π Π²ΠΎΠ²ΡΠ΅ Π½Π΅ ΠΈΠ·-Π·Π° ΡΠ²ΠΎΠ΅ΠΉ ΡΠ΅Π΄ΠΊΠΎΡΡΠΈ, ΠΏΡΠΎΡΡΠΎ Π΄ΠΎ ΠΎΡΠΊΡΡΡΠΈΡ ΡΠ»Π΅ΠΊΡΡΠΎΠ»ΠΈΡΠΈΡΠ΅ΡΠΊΠΎΠ³ΠΎ ΠΌΠ΅ΡΠΎΠ΄Π° Π²ΠΎΡΡΡΠ°Π½ΠΎΠ²Π»Π΅Π½ΠΈΡ ΠΏΡΠΎΠΈΠ·Π²ΠΎΠ΄ΡΡΠ²ΠΎ ΠΎΠ±Ρ ΠΎΠ΄ΠΈΠ»ΠΎΡΡ Π±Π°ΡΠ½ΠΎΡΠ»ΠΎΠ²Π½ΠΎ Π΄ΠΎΡΠΎΠ³ΠΎ, Π°Π»ΡΠΌΠΈΠ½ΠΈΠΉ Π±ΡΠ» Π΄ΠΎΡΠΎΠΆΠ΅ Π·ΠΎΠ»ΠΎΡΠ° ΠΈ ΠΏΠ»Π°ΡΠΈΠ½Ρ. ΠΠ΅Π΄Π°ΡΠΎΠΌ Π²Π΅ΡΡ, ΠΏΠΎΠ΄Π°ΡΠ΅Π½Π½ΡΠ΅ ΠΠ΅Π½Π΄Π΅Π»Π΅Π΅Π²Ρ ΠΏΠΎΡΠ»Π΅ ΠΎΡΠΊΡΡΡΠΈΡ ΠΏΠ΅ΡΠΈΠΎΠ΄ΠΈΡΠ΅ΡΠΊΠΎΠ³ΠΎ Π·Π°ΠΊΠΎΠ½Π°, ΡΠΎΠ΄Π΅ΡΠΆΠ°Π»ΠΈ Π½Π΅ΠΌΠ°Π»ΠΎ Π°Π»ΡΠΌΠΈΠ½ΠΈΠ΅Π²ΡΡ Π΄Π΅ΡΠ°Π»Π΅ΠΉ, Π½Π° ΡΠΎΡ ΠΌΠΎΠΌΠ΅Π½Ρ ΡΡΠΎ Π±ΡΠ» ΠΏΠΎΠΈΡΡΠΈΠ½Π΅ ΠΊΠΎΡΠΎΠ»Π΅Π²ΡΠΊΠΈΠΉ ΠΏΠΎΠ΄Π°ΡΠΎΠΊ. Π‘ 1855 ΠΏΠΎ 1890 Π³ΠΎΠ΄Ρ ΠΈΠ·Π³ΠΎΡΠΎΠ²ΠΈΠ»ΠΈ Π²ΡΠ΅Π³ΠΎ 200 ΡΠΎΠ½Π½ ΠΌΠ°ΡΠ΅ΡΠΈΠ°Π»Π° ΠΏΠΎ ΠΌΠ΅ΡΠΎΠ΄Ρ ΠΠ½ΡΠΈ ΠΡΡΠ΅Π½Π° Π‘Π΅Π½Ρ-ΠΠ»Π΅Ρ ΠΠ΅Π²ΠΈΠ»Ρ, Π·Π°ΠΊΠ»ΡΡΠ°ΡΡΠ΅ΠΌΡΡΒ Π² Π²ΡΡΠ΅ΡΠ½Π΅Π½ΠΈΠΈ Π°Π»ΡΠΌΠΈΠ½ΠΈΡ ΠΌΠ΅ΡΠ°Π»Π»ΠΈΡΠ΅ΡΠΊΠΈΠΌ Π½Π°ΡΡΠΈΠ΅ΠΌ.
Π£ΠΆΠ΅ ΠΊ 1890 Π³ΠΎΠ΄Ρ ΡΠ΅Π½Π° ΡΠΏΠ°Π»Π° Π² 30 ΡΠ°Π·, Π° ΠΊ Π½Π°ΡΠ°Π»Ρ ΠΠ΅ΡΠ²ΠΎΠΉ ΠΌΠΈΡΠΎΠ²ΠΎΠΉ β Π±ΠΎΠ»Π΅Π΅ ΡΠ΅ΠΌ Π² ΡΠΎΡΠ½Ρ. Π ΠΏΠΎΡΠ»Π΅ ΡΡΠΈΠ΄ΡΠ°ΡΡΡ Π³ΠΎΠ΄ΠΎΠ² ΠΏΠΎΡΡΠΎΡΠ½Π½ΠΎ ΡΠΎΡ ΡΠ°Π½ΡΠ»Π° ΠΏΡΠΈΠΌΠ΅ΡΠ½ΡΠΉ ΠΏΠ°ΡΠΈΡΠ΅Ρ Ρ ΡΠ΅Π½Π°ΠΌΠΈ Π½Π° ΡΡΠ°Π»ΡΠ½ΠΎΠΉ ΠΏΡΠΎΠΊΠ°Ρ, Π±ΡΠ΄ΡΡΠΈ Π΄ΠΎΡΠΎΠΆΠ΅ Π² 3-4 ΡΠ°Π·Π°. ΠΠ΅ΡΠΈΡΠΈΡ ΡΠ΅Ρ ΠΈΠ»ΠΈ ΠΈΠ½ΡΡ ΠΌΠ°ΡΠ΅ΡΠΈΠ°Π»ΠΎΠ² ΠΏΠ΅ΡΠΈΠΎΠ΄ΠΈΡΠ΅ΡΠΊΠΈ ΠΈΠ·ΠΌΠ΅Π½ΡΠ» ΡΡΠΎ ΡΠΎΠΎΡΠ½ΠΎΡΠ΅Π½ΠΈΠ΅ Π½Π° Π½Π΅Π±ΠΎΠ»ΡΡΠΎΠΉ ΡΡΠΎΠΊ, Π½ΠΎ ΡΠ΅ΠΌ Π½Π΅ ΠΌΠ΅Π½Π΅Π΅ Π² ΡΡΠ΅Π΄Π½Π΅ΠΌ ΡΠΎΠ½Π½Π° Π°Π»ΡΠΌΠΈΠ½ΠΈΡ Π²ΡΠ΅Π³Π΄Π° ΠΎΠ±Ρ ΠΎΠ΄ΠΈΡΡΡ ΠΌΠΈΠ½ΠΈΠΌΡΠΌ Π² ΡΡΠΈ ΡΠ°Π·Π° Π΄ΠΎΡΠΎΠΆΠ΅ ΠΎΠ±ΡΡΠ½ΠΎΠΉ ΡΡΠ°Π»ΠΈ.
Β«ΠΡΡΠ»Π°ΡΡΠΌΒ» Π°Π»ΡΠΌΠΈΠ½ΠΈΠΉ Π½Π°Π·ΡΠ²Π°ΡΡ Π·Π° ΡΠΎΡΠ΅ΡΠ°Π½ΠΈΠ΅ ΠΌΠ°Π»ΠΎΠΉ ΠΌΠ°ΡΡΡ, ΠΏΡΠΎΡΠ½ΠΎΡΡΠΈ ΠΈ Π΄ΠΎΡΡΡΠΏΠ½ΠΎΡΡΠΈ.Β ΠΡΠΎΡ ΠΌΠ΅ΡΠ°Π»Π» Π·Π°ΠΌΠ΅ΡΠ½ΠΎ Π»Π΅Π³ΡΠ΅ ΡΡΠ°Π»ΠΈ, Π½Π° ΠΊΡΠ±ΠΎΠΌΠ΅ΡΡ ΠΏΡΠΈΡ ΠΎΠ΄ΠΈΡΡΡ ΠΏΡΠΈΠΌΠ΅ΡΠ½ΠΎ 2 700 ΠΊΠ³ ΠΏΡΠΎΡΠΈΠ² 7 800 ΠΊΠ³ Π΄Π»Ρ ΡΠΈΠΏΠΈΡΠ½ΡΡ ΡΠΎΡΡΠΎΠ² ΡΡΠ°Π»ΠΈ. ΠΠΎ ΠΈ ΠΏΡΠΎΡΠ½ΠΎΡΡΡ Π½ΠΈΠΆΠ΅, Π΄Π»Ρ ΡΠ°ΡΠΏΡΠΎΡΡΡΠ°Π½Π΅Π½Π½ΡΡ ΡΠΎΡΡΠΎΠ² ΡΡΠ°Π»ΠΈ ΠΈ Π°Π»ΡΠΌΠΈΠ½ΠΈΡ ΡΠ°Π·Π½ΠΈΡΠ° ΠΏΡΠΈΠΌΠ΅ΡΠ½ΠΎ Π² ΠΏΠΎΠ»ΡΠΎΡΠ°-Π΄Π²Π° ΡΠ°Π·Π° ΡΡΠΎ ΠΏΠΎ ΡΠ΅ΠΊΡΡΠ΅ΡΡΠΈ, ΡΡΠΎ ΠΏΠΎ ΡΠ°ΡΡΡΠΆΠ΅Π½ΠΈΡ. ΠΡΠ»ΠΈ ΠΎ ΠΊΠΎΠ½ΠΊΡΠ΅ΡΠ½ΡΡ ΡΠΈΡΡΠ°Ρ , ΡΠΎ ΠΏΡΠΎΡΠ½ΠΎΡΡΡ Π°Π»ΡΠΌΠΈΠ½ΠΈΠ΅Π²ΠΎΠ³ΠΎ ΡΠΏΠ»Π°Π²Π° ΠΠΠ³3 βΒ 120/230 ΠΠΏΠ°, Π½ΠΈΠ·ΠΊΠΎΡΠ³Π»Π΅ΡΠΎΠ΄ΠΈΡΡΠΎΠΉ ΡΡΠ°Π»ΠΈ ΠΌΠ°ΡΠΊΠΈ 2C10 βΒ 175/315, Π° Π²ΠΎΡ Π²ΡΡΠΎΠΊΠΎΠΏΡΠΎΡΠ½Π°Ρ ΡΡΠ°Π»Ρ HC260BD βΒ ΡΡΠΎ ΡΠΆΠ΅ 240/450 ΠΠΏΠ°.
Π ΠΈΡΠΎΠ³Π΅ ΠΊΠΎΠ½ΡΡΡΡΠΊΡΠΈΠΈ ΠΈΠ· Π°Π»ΡΠΌΠΈΠ½ΠΈΡ ΠΈΠΌΠ΅ΡΡ Π²ΡΠ΅ ΡΠ°Π½ΡΡ Π±ΡΡΡ Π·Π°ΠΌΠ΅ΡΠ½ΠΎ Π»Π΅Π³ΡΠ΅, ΠΌΠΈΠ½ΠΈΠΌΡΠΌ Π½Π° ΡΡΠ΅ΡΡ, Π½ΠΎ Π² ΠΎΡΠ΄Π΅Π»ΡΠ½ΡΡ ΡΠ»ΡΡΠ°ΡΡ ΠΏΡΠ΅Π²ΠΎΡΡ ΠΎΠ΄ΡΡΠ²ΠΎ Π² ΠΌΠ°ΡΡΠ΅ Π΄Π΅ΡΠ°Π»Π΅ΠΉ ΠΌΠΎΠΆΠ΅Ρ Π±ΡΡΡ Π±ΠΎΠ»ΡΡΠ΅, Π²Π΅Π΄Ρ Π°Π»ΡΠΌΠΈΠ½ΠΈΠ΅Π²ΡΠ΅ Π΄Π΅ΡΠ°Π»ΠΈ ΠΈΠΌΠ΅ΡΡ Π±ΠΎΠ»Π΅Π΅ Π²ΡΡΠΎΠΊΡΡ ΠΆΠ΅ΡΡΠΊΠΎΡΡΡ ΠΈ Π·Π°ΠΌΠ΅ΡΠ½ΠΎ Π±ΠΎΠ»Π΅Π΅ ΡΠ΅Ρ Π½ΠΎΠ»ΠΎΠ³ΠΈΡΠ½Ρ Π² ΠΈΠ·Π³ΠΎΡΠΎΠ²Π»Π΅Π½ΠΈΠΈ. ΠΠ»Ρ Π°Π²ΠΈΠ°ΡΠΈΠΈ ΡΡΠΎ ΡΡΡΠΈΠΉ ΠΏΠΎΠ΄Π°ΡΠΎΠΊ, Π²Π΅Π΄Ρ Π±ΠΎΠ»Π΅Π΅ ΠΏΡΠΎΡΠ½ΡΠ΅ ΡΠΈΡΠ°Π½ΠΎΠ²ΡΠ΅ ΡΠΏΠ»Π°Π²Ρ ΠΊΡΠ΄Π°Β Π΄ΠΎΡΠΎΠΆΠ΅, ΠΈ ΠΌΠ°ΡΡΠΎΠ²ΠΎΠ΅ ΠΏΡΠΎΠΈΠ·Π²ΠΎΠ΄ΡΡΠ²ΠΎ ΠΏΠΎΠΏΡΠΎΡΡΡ Π½Π΅Π΄ΠΎΡΡΡΠΏΠ½ΠΎ, Π° ΠΌΠ°Π³Π½ΠΈΠ΅Π²ΡΠ΅ ΡΠΏΠ»Π°Π²Ρ ΠΎΡΠ»ΠΈΡΠ°ΡΡΡΡ Π²ΡΡΠΎΠΊΠΎΠΉ ΠΊΠΎΡΡΠΎΠ·ΠΈΠΉΠ½ΠΎΠΉ Π°ΠΊΡΠΈΠ²Π½ΠΎΡΡΡΡ ΠΈ ΠΏΠΎΠ²ΡΡΠ΅Π½Π½ΠΎΠΉ ΠΏΠΎΠΆΠ°ΡΠΎΠΎΠΏΠ°ΡΠ½ΠΎΡΡΡΡ.
ΠΡΠ°ΠΊΡΠΈΠΊΠ° ΠΈΡΠΏΠΎΠ»ΡΠ·ΠΎΠ²Π°Π½ΠΈΡ Π½Π° Π·Π΅ΠΌΠ»Π΅
Π ΠΌΠ°ΡΡΠΎΠ²ΠΎΠΌ ΡΠΎΠ·Π½Π°Π½ΠΈΠΈ Π°Π»ΡΠΌΠΈΠ½ΠΈΠ΅Π²ΡΠ΅ ΠΊΡΠ·ΠΎΠ²Π° Π² ΠΎΡΠ½ΠΎΠ²Π½ΠΎΠΌ Π°ΡΡΠΎΡΠΈΠΈΡΡΡΡΡΡ Ρ ΠΌΠ°ΡΠΈΠ½Π°ΠΌΠΈ ΠΌΠ°ΡΠΊΠΈ Audi, Ρ ΠΎΡΡ ΠΏΠ΅ΡΠ²Π°Ρ A8 Π² ΠΊΡΠ·ΠΎΠ²Π΅ D2 ΠΏΠΎΡΠ²ΠΈΠ»Π°ΡΡ Π»ΠΈΡΡ Π² 1994 Π³ΠΎΠ΄Ρ. ΠΡΠΎ Π±ΡΠ»Π° ΠΎΠ΄Π½Π° ΠΈΠ· ΠΏΠ΅ΡΠ²ΡΡ ΠΊΡΡΠΏΠ½ΠΎΡΠ΅ΡΠΈΠΉΠ½ΡΡ ΡΠ΅Π»ΡΠ½ΠΎΠ°Π»ΡΠΌΠΈΠ½ΠΈΠ΅Π²ΡΡ ΠΌΠ°ΡΠΈΠ½, Ρ ΠΎΡΡ ΠΈΠ·ΡΡΠ΄Π½Π°Ρ Π΄ΠΎΠ»Ρ ΠΊΡΡΠ»Π°ΡΠΎΠ³ΠΎ ΠΌΠ΅ΡΠ°Π»Π»Π° Π±ΡΠ»Π° ΡΠΈΡΠΌΠ΅Π½Π½ΠΎΠΉ Β«ΡΠΈΡΠΊΠΎΠΉΒ» ΡΠ°ΠΊΠΈΡ ΠΌΠ°ΡΠΎΠΊ, ΠΊΠ°ΠΊ Land Rover ΠΈ Aston Martin Π½Π° ΠΏΡΠΎΡΡΠΆΠ΅Π½ΠΈΠΈ Π΄Π΅ΡΡΡΠΊΠΎΠ² Π»Π΅Ρ, Π½Π΅ Π³ΠΎΠ²ΠΎΡΡ ΡΠΆΠ΅ ΠΎ ΡΠΆΠ΅ ΡΠΏΠΎΠΌΡΠ½ΡΡΠΎΠΌ Morgan, Ρ Π΅Π³ΠΎ Π°Π»ΡΠΌΠΈΠ½ΠΈΠ΅ΠΌ Π½Π° Π΄Π΅ΡΠ΅Π²ΡΠ½Π½ΠΎΠΌ ΠΊΠ°ΡΠΊΠ°ΡΠ΅. ΠΡΠ΅ ΠΆΠ΅ ΡΠ΅ΠΊΠ»Π°ΠΌΠ° ΡΠ²ΠΎΡΠΈΡ ΡΡΠ΄Π΅ΡΠ°.
Π ΠΏΠ΅ΡΠ²ΡΡ ΠΎΡΠ΅ΡΠ΅Π΄Ρ Π² Π½ΠΎΠ²ΠΎΠΉ ΡΠ΅Ρ Π½ΠΎΠ»ΠΎΠ³ΠΈΠΈ ΠΈΠ·Π³ΠΎΡΠΎΠ²Π»Π΅Π½ΠΈΡ ΠΊΡΠ·ΠΎΠ²Π° ΠΏΠΎΠ΄ΡΠ΅ΡΠΊΠΈΠ²Π°Π»Π°ΡΡ Π½ΠΈΠ·ΠΊΠ°Ρ ΠΌΠ°ΡΡΠ° ΠΈ ΡΡΠΎΠΉΠΊΠΎΡΡΡ Π°Π»ΡΠΌΠΈΠ½ΠΈΠ΅Π²ΡΡ ΠΊΡΠ·ΠΎΠ²ΠΎΠ² ΠΊ ΠΊΠΎΡΡΠΎΠ·ΠΈΠΈ. ΠΠ½ΠΎΠ³Π΄Π° ΡΠΏΠΎΠΌΠΈΠ½Π°Π»ΠΈΡΡ ΠΈ Π΄ΡΡΠ³ΠΈΠ΅ ΠΏΡΠ΅ΠΈΠΌΡΡΠ΅ΡΡΠ²Π° Π°Π»ΡΠΌΠΈΠ½ΠΈΠ΅Π²ΡΡ ΠΊΠΎΠ½ΡΡΡΡΠΊΡΠΈΠΉ: Π½Π°ΠΏΡΠΈΠΌΠ΅Ρ, ΠΎΡΠΎΠ±Π΅Π½Π½ΡΠ΅ Π°ΠΊΡΡΡΠΈΡΠ΅ΡΠΊΠΈΠ΅ ΡΠ²ΠΎΠΉΡΡΠ²Π° ΠΊΡΠ·ΠΎΠ²ΠΎΠ² ΠΈ ΠΏΠ°ΡΡΠΈΠ²Π½Π°Ρ Π±Π΅Π·ΠΎΠΏΠ°ΡΠ½ΠΎΡΡΡ ΠΊΠΎΠ½ΡΡΡΡΠΊΡΠΈΠΉ ΠΈΠ· ΠΎΠ±ΡΠ΅ΠΌΠ½ΠΎΠΉ ΡΡΠ°ΠΌΠΏΠΎΠ²ΠΊΠΈ ΠΈ Π»ΠΈΡΡΡ.
Π‘ΠΏΠΈΡΠΎΠΊ ΠΌΠ°ΡΠΈΠ½, Π² ΠΊΠΎΡΠΎΡΡΡ Π°Π»ΡΠΌΠΈΠ½ΠΈΠ΅Π²ΡΠ΅ Π΄Π΅ΡΠ°Π»ΠΈ ΡΠΎΡΡΠ°Π²Π»ΡΡΡ Π½Π΅ ΠΌΠ΅Π½Π΅Π΅ 60% ΠΌΠ°ΡΡΡ ΠΊΡΠ·ΠΎΠ²Π° (Π½Π΅ ΠΏΡΡΠ°ΡΡ Ρ ΠΏΠΎΠ»Π½ΠΎΠΉ ΠΌΠ°ΡΡΠΎΠΉ ΠΌΠ°ΡΠΈΠ½Ρ), Π΄ΠΎΠ²ΠΎΠ»ΡΠ½ΠΎ Π²Π΅Π»ΠΈΠΊ. Π ΠΏΠ΅ΡΠ²ΡΡ ΠΎΡΠ΅ΡΠ΅Π΄Ρ ΠΈΠ·Π²Π΅ΡΡΠ½Ρ ΠΌΠΎΠ΄Π΅Π»ΠΈ Audi, A2, A8, R8 ΠΈ ΡΠΎΠ΄ΡΡΠ²Π΅Π½Π½Π°Ρ R8 Lamborghini Gallardo. ΠΠ΅Π½Π΅Π΅ ΠΎΡΠ΅Π²ΠΈΠ΄Π½Ρ Ferrari F430, F360, 612, ΠΏΠΎΡΠ»Π΅Π΄Π½ΠΈΠ΅ ΠΏΠΎΠΊΠΎΠ»Π΅Π½ΠΈΡ Jaguar XJ X350-X351, XJR, XF, XE ΠΈ F-Pace. Π¦Π΅Π½ΠΈΡΠ΅Π»ΠΈ Π½Π°ΡΡΠΎΡΡΠΈΡ ΡΠΏΠΎΡΡΠΈΠ²Π½ΡΡ ΠΌΠ°ΡΠΈΠ½ Π²ΡΠΏΠΎΠΌΠ½ΡΡ Lotus Elise, Π° ΡΠ°ΠΊΠΆΠ΅ ΡΠΎΠΏΠ»Π°ΡΡΠΎΡΠΌΠ΅Π½Π½ΡΠ΅ Opel Speedster ΠΈ Tesla Roadster. ΠΡΠΎΠ±Π΅Π½Π½ΠΎ Π΄ΠΎΡΠΎΡΠ½ΡΠ΅ ΡΠΈΡΠ°ΡΠ΅Π»ΠΈ ΠΏΡΠΈΠΏΠΎΠΌΠ½ΡΡ Honda NSX, Spyker ΠΈ Π΄Π°ΠΆΠ΅ Mercedes SLS.
Π§Π°ΡΡΠΎ ΠΎΡΠΈΠ±ΠΎΡΠ½ΠΎ ΠΊ ΡΠΈΡΠ»Ρ Π°Π»ΡΠΌΠΈΠ½ΠΈΠ΅Π²ΡΡ ΠΎΡΠ½ΠΎΡΡΡ ΡΠΎΠ²ΡΠ΅ΠΌΠ΅Π½Π½ΡΠ΅ Land Rover, Range Rover, BMW ΠΏΠΎΡΠ»Π΅Π΄Π½ΠΈΡ ΡΠ΅ΡΠΈΠΉ ΠΈ Π½Π΅ΠΊΠΎΡΠΎΡΡΠ΅ Π΄ΡΡΠ³ΠΈΠ΅ ΠΏΡΠ΅ΠΌΠΈΡΠΌ-ΠΌΠΎΠ΄Π΅Π»ΠΈ, Π½ΠΎ ΡΠ°ΠΌ ΠΎΠ±ΡΠ°Ρ Π΄ΠΎΠ»Ρ Π°Π»ΡΠΌΠΈΠ½ΠΈΠ΅Π²ΡΡ Π΄Π΅ΡΠ°Π»Π΅ΠΉ Π½Π΅ ΡΠ°ΠΊ ΡΠΆ Π²Π΅Π»ΠΈΠΊΠ°, Π° ΠΊΠ°ΡΠΊΠ°Ρ ΠΊΡΠ·ΠΎΠ²Π° ΠΏΠΎ-ΠΏΡΠ΅ΠΆΠ½Π΅ΠΌΡ ΠΈΠ· ΡΡΠ°Π»Π΅ΠΉ βΒ ΠΎΠ±ΡΡΠ½ΡΡ ΠΈ Π²ΡΡΠΎΠΊΠΎΠΉ ΠΏΡΠΎΡΠ½ΠΎΡΡΠΈ. Π¦Π΅Π»ΡΠ½ΠΎΠ°Π»ΡΠΌΠΈΠ½ΠΈΠ΅Π²ΡΡ ΠΌΠ°ΡΠΈΠ½ Π½Π΅ΠΌΠ½ΠΎΠ³ΠΎ, ΠΈ Π±ΠΎΠ»ΡΡΠ°Ρ ΡΠ°ΡΡΡ ΠΈΠ· Π½ΠΈΡ βΒ ΡΡΠΎ ΡΡΠ°Π²Π½ΠΈΡΠ΅Π»ΡΠ½ΠΎ ΠΌΠ°Π»ΠΎΡΠ΅ΡΠΈΠΉΠ½ΡΠ΅ ΠΊΠΎΠ½ΡΡΡΡΠΊΡΠΈΠΈ.
ΠΠΎ ΠΊΠ°ΠΊ ΠΆΠ΅ ΡΠ°ΠΊ? ΠΠΎΡΠ΅ΠΌΡ ΠΏΡΠΈ Π²ΡΠ΅Ρ ΡΠ²ΠΎΠΈΡ Π΄ΠΎΡΡΠΎΠΈΠ½ΡΡΠ²Π°Ρ Π°Π»ΡΠΌΠΈΠ½ΠΈΠΉ Π½Π΅ ΠΏΡΠΈΠΌΠ΅Π½ΡΠ΅ΡΡΡ ΠΌΠ°ΠΊΡΠΈΠΌΠ°Π»ΡΠ½ΠΎ ΡΠΈΡΠΎΠΊΠΎ Π² ΡΡΡΠΎΠ΅Π½ΠΈΠΈ ΠΊΡΠ·ΠΎΠ²Π°?
ΠΠ°Π·Π°Π»ΠΎΡΡ Π±Ρ, ΠΌΠΎΠΆΠ½ΠΎ Π²ΡΠΈΠ³ΡΠ°ΡΡ Π½Π° ΠΌΠ°ΡΡΠ΅, Π° ΡΠ°Π·Π½ΠΈΡΠ° Π² ΡΠ΅Π½Π΅ ΠΌΠ°ΡΠ΅ΡΠΈΠ°Π»ΠΎΠ² Π½Π΅ ΡΠ°ΠΊ ΡΠΆ ΠΊΡΠΈΡΠΈΡΠ½Π° Π½Π° ΡΠΎΠ½Π΅ Π΄ΡΡΠ³ΠΈΡ ΡΠΎΡΡΠ°Π²Π»ΡΡΡΠΈΡ ΡΡΠΎΠΈΠΌΠΎΡΡΠΈ Π΄ΠΎΡΠΎΠ³ΠΎΠΉ ΠΌΠ°ΡΠΈΠ½Ρ. Π’ΠΎΠ½Π½Π° Β«ΠΊΡΡΠ»Π°ΡΠΎΠ³ΠΎΒ» ΡΡΠΎΠΈΡ ΡΠ΅ΠΉΡΠ°Ρ 1 600 Π΄ΠΎΠ»Π»Π°ΡΠΎΠ² β ΡΡΠΎ Π½Π΅ ΡΠ°ΠΊ ΡΠΆ ΠΌΠ½ΠΎΠ³ΠΎ, ΠΎΡΠΎΠ±Π΅Π½Π½ΠΎ Π΄Π»Ρ ΠΏΡΠ΅ΠΌΠΈΠ°Π»ΡΠ½ΠΎΠΉ ΠΌΠ°ΡΠΈΠ½Ρ. ΠΡΠ΅ΠΌΡ Π΅ΡΡΡ ΠΎΠ±ΡΡΡΠ½Π΅Π½ΠΈΡ. ΠΡΠ°Π²Π΄Π°, Π΄Π»Ρ ΠΏΠΎΠ½ΠΈΠΌΠ°Π½ΠΈΡ Π²ΠΎΠΏΡΠΎΡΠ° ΠΎΠΏΡΡΡ ΠΏΡΠΈΠ΄Π΅ΡΡΡ Π½Π΅ΠΌΠ½ΠΎΠ³ΠΎ ΡΠ³Π»ΡΠ±ΠΈΡΡΡΡ Π² ΠΏΡΠΎΡΠ»ΠΎΠ΅.
ΠΠ°ΠΊ Π°Π»ΡΠΌΠΈΠ½ΠΈΠΉ ΠΏΡΠΎΠΈΠ³ΡΠ°Π» ΠΏΠ»Π°ΡΡΠΈΠΊΡ ΠΈ ΡΡΠ°Π»ΠΈ
ΠΠΎΡΡΠΌΠΈΠ΄Π΅ΡΡΡΡΠ΅ Π³ΠΎΠ΄Ρ Π΄Π²Π°Π΄ΡΠ°ΡΠΎΠ³ΠΎ Π²Π΅ΠΊΠ° Π²ΠΎΠΉΠ΄ΡΡ Π² ΠΈΡΡΠΎΡΠΈΡ Π°Π²ΡΠΎΠΌΠΎΠ±ΠΈΠ»Π΅ΡΡΡΠΎΠ΅Π½ΠΈΡ ΠΊΠ°ΠΊ Π²ΡΠ΅ΠΌΡ, ΠΊΠΎΠ³Π΄Π° ΡΡΠΎΡΠΌΠΈΡΠΎΠ²Π°Π»ΠΈΡΡ ΠΎΡΠ½ΠΎΠ²Π½ΡΠ΅ Π±ΡΠ΅Π½Π΄Ρ Π½Π° ΠΌΠΈΡΠΎΠ²ΠΎΠΌ ΡΡΠ½ΠΊΠ΅ ΠΈ ΡΠΎΠ·Π΄Π°Π»ΠΎΡΡ ΡΠΎΠΎΡΠ½ΠΎΡΠ΅Π½ΠΈΠ΅ ΡΠΈΠ», ΠΊΠΎΡΠΎΡΠΎΠ΅ ΠΌΠ°Π»ΠΎ ΠΈΠ·ΠΌΠ΅Π½ΠΈΠ»ΠΎΡΡ ΠΈ ΠΏΠΎ ΡΠ΅ΠΉ Π΄Π΅Π½Ρ. ΠΠΎΠ²ΠΎΠΉ ΠΊΡΠΎΠ²ΠΈ Ρ ΡΠ΅Ρ ΠΏΠΎΡ Π΄ΠΎΠ±Π°Π²ΠΈΠ»ΠΈ Π°Π²ΡΠΎΠΌΠΎΠ±ΠΈΠ»ΡΠ½ΠΎΠΌΡ ΡΡΠ½ΠΊΡ Π»ΠΈΡΡ ΠΊΠΈΡΠ°ΠΉΡΠΊΠΈΠ΅ ΠΊΠΎΠΌΠΏΠ°Π½ΠΈΠΈ, Π² ΠΎΡΡΠ°Π»ΡΠ½ΠΎΠΌ ΠΆΠ΅ ΠΈΠΌΠ΅Π½Π½ΠΎ ΡΠΎΠ³Π΄Π° ΠΏΠΎΡΠ²ΠΈΠ»ΠΈΡΡ ΠΎΡΠ½ΠΎΠ²Π½ΡΠ΅ ΡΡΠ΅Π½Π΄Ρ, ΠΊΠ»Π°ΡΡΡ ΠΈ ΡΠ΅Π½Π΄Π΅Π½ΡΠΈΠΈ Π² Π°Π²ΡΠΎΠΌΠΎΠ±ΠΈΠ»Π΅ΡΡΡΠΎΠ΅Π½ΠΈΠΈ. Π’ΠΎΠ³Π΄Π° ΠΆΠ΅ Π½Π°ΠΌΠ΅ΡΠΈΠ»ΡΡ ΠΏΠ΅ΡΠ΅Π»ΠΎΠΌ Π² ΠΈΡΠΏΠΎΠ»ΡΠ·ΠΎΠ²Π°Π½ΠΈΠΈ Π² ΠΊΠΎΠ½ΡΡΡΡΠΊΡΠΈΠΈ ΠΌΠ°ΡΠΈΠ½Ρ Π°Π»ΡΡΠ΅ΡΠ½Π°ΡΠΈΠ²Π½ΡΡ ΠΌΠ°ΡΠ΅ΡΠΈΠ°Π»ΠΎΠ², ΠΏΠΎΠΌΠΈΠΌΠΎ ΡΡΠ°Π»ΠΈ ΠΈ ΡΡΠ³ΡΠ½Π°.
ΠΠ»Π°Π³ΠΎΠ΄Π°ΡΠΈΡΡ Π·Π° ΡΡΠΎ ΡΡΠΎΠΈΡ ΡΠ²Π΅Π»ΠΈΡΠΈΠ²ΡΠΈΠ΅ΡΡ ΠΎΠΆΠΈΠ΄Π°Π½ΠΈΡ ΠΏΠΎ ΡΠ°ΡΡΠΈ Π΄ΠΎΠ»Π³ΠΎΠ²Π΅ΡΠ½ΠΎΡΡΠΈ ΠΌΠ°ΡΠΈΠ½, Π½ΠΎΠ²ΡΠ΅ Π½ΠΎΡΠΌΡ ΠΏΠΎ ΡΠ°ΡΡ ΠΎΠ΄Ρ ΡΠΎΠΏΠ»ΠΈΠ²Π° ΠΈ ΠΏΠ°ΡΡΠΈΠ²Π½ΠΎΠΉ Π±Π΅Π·ΠΎΠΏΠ°ΡΠ½ΠΎΡΡΠΈ. ΠΡ ΠΈ, ΡΡΠ°Π΄ΠΈΡΠΈΠΎΠ½Π½ΠΎ, ΡΠ°Π·Π²ΠΈΡΠΈΠ΅ ΡΠ΅Ρ Π½ΠΎΠ»ΠΎΠ³ΠΈΠΉ, ΠΊΠΎΡΠΎΡΡΠ΅ Π²ΡΠ΅ ΡΡΠΎ ΠΏΠΎΠ·Π²ΠΎΠ»ΠΈΠ»ΠΈ. Π ΠΎΠ±ΠΊΠΈΠ΅ ΠΏΠΎΠΏΡΡΠΊΠΈ ΠΈΡΠΏΠΎΠ»ΡΠ·ΠΎΠ²Π°ΡΡ Π°Π»ΡΠΌΠΈΠ½ΠΈΠΉ Π² ΡΠ·Π»Π°Ρ , ΠΎΡΠ²Π΅ΡΠ°ΡΡΠΈΡ Π·Π° ΠΏΠ°ΡΡΠΈΠ²Π½ΡΡ Π±Π΅Π·ΠΎΠΏΠ°ΡΠ½ΠΎΡΡΡ, Π±ΡΡΡΡΠΎ Π·Π°ΠΊΠΎΠ½ΡΠΈΠ»ΠΈΡΡ Π²Π½Π΅Π΄ΡΠ΅Π½ΠΈΠ΅ΠΌ Π»ΠΈΡΡ ΠΏΡΠΎΡΡΠ΅ΠΉΡΠΈΡ ΡΠ»Π΅ΠΌΠ΅Π½ΡΠΎΠ² Π² Π²ΠΈΠ΄Π΅ Π±ΡΡΡΡΠ΅Π² Π΄Π»Ρ ΡΠΌΠΈΠ½Π°Π΅ΠΌΡΡ Π·ΠΎΠ½ ΠΈ Π΄Π΅ΠΊΠΎΡΠ°ΡΠΈΠ²Π½ΡΡ ΡΠ»Π΅ΠΌΠ΅Π½ΡΠΎΠ², ΠΊΠΎΡΠΎΡΡΠ΅ Π² ΠΎΠ±ΡΠ΅ΠΉ ΠΌΠ°ΡΡΠ΅ ΠΊΡΠ·ΠΎΠ²Π° ΡΠΎΡΡΠ°Π²Π»ΡΠ»ΠΈ Π½Π΅ΡΠΊΠΎΠ»ΡΠΊΠΎ ΠΏΡΠΎΡΠ΅Π½ΡΠΎΠ².
Π Π²ΠΎΡ ΡΡΠ°ΠΆΠ΅Π½ΠΈΠ΅ Π·Π° ΠΊΠΎΠ½ΡΡΡΡΠΊΡΠΈΠΈ ΡΠ°ΠΌΠΎΠ³ΠΎ ΠΊΡΠ·ΠΎΠ²Π° Π±ΡΠ»ΠΎ Π±Π΅Π·Π½Π°Π΄Π΅ΠΆΠ½ΠΎ ΠΏΡΠΎΠΈΠ³ΡΠ°Π½ΠΎ Π½Π° ΡΠΎΡ ΠΌΠΎΠΌΠ΅Π½Ρ. ΠΠΎΠ±Π΅Π΄Ρ ΠΎΠ΄Π½ΠΎΠ·Π½Π°ΡΠ½ΠΎ ΠΎΠ΄Π΅ΡΠΆΠ°Π»ΠΈ ΠΏΡΠΎΠΈΠ·Π²ΠΎΠ΄ΠΈΡΠ΅Π»ΠΈ ΠΏΠ»Π°ΡΡΠΈΠΊΠ°. ΠΡΠΎΡΡΠ°Ρ ΡΠ΅Ρ Π½ΠΎΠ»ΠΎΠ³ΠΈΡ ΠΈΠ·Π³ΠΎΡΠΎΠ²Π»Π΅Π½ΠΈΡ ΠΊΡΡΠΏΠ½ΡΡ Π΄Π΅ΡΠ°Π»Π΅ΠΉ ΠΈΠ· ΠΏΠ»Π°ΡΡΠΈΠΊΠ° ΠΈΠ·ΠΌΠ΅Π½ΠΈΠ»Π° Π΄ΠΈΠ·Π°ΠΉΠ½ Π°Π²ΡΠΎΠΌΠΎΠ±ΠΈΠ»Π΅ΠΉ Π² Π²ΠΎΡΡΠΌΠΈΠ΄Π΅ΡΡΡΡΠ΅. ΠΠ²ΡΠΎΠΏΠ΅ΠΉΡΡ ΡΠ΄ΠΈΠ²Π»ΡΠ»ΠΈΡΡ ΡΠ΅Ρ Π½ΠΎΠ»ΠΎΠ³ΠΈΡΠ½ΠΎΡΡΠΈ ΠΈ Β«ΠΏΡΠΎΠ΄Π²ΠΈΠ½ΡΡΠΎΡΡΠΈΒ» Ford Sierra ΠΈ VW Passat B3 Ρ ΠΈΡ ΡΠ°Π·Π²ΠΈΡΡΠΌ ΠΏΠ»Π°ΡΡΠΈΠΊΠΎΠ²ΡΠΌ ΠΎΠ±Π²Π΅ΡΠΎΠΌ. Π€ΠΎΡΠΌΡ ΠΈ ΠΌΠ°ΡΠ΅ΡΠΈΠ°Π»Ρ ΡΠ°Π΄ΠΈΠ°ΡΠΎΡΠ½ΡΡ ΡΠ΅ΡΠ΅ΡΠΎΠΊ, Π±Π°ΠΌΠΏΠ΅ΡΠΎΠ² ΠΈ Π΄ΡΡΠ³ΠΈΡ ΡΠ»Π΅ΠΌΠ΅Π½ΡΠΎΠ² ΡΠΎ Π²ΡΠ΅ΠΌΠ΅Π½Π΅ΠΌ ΡΡΠ°Π»ΠΈ ΡΠΎΠΎΡΠ²Π΅ΡΡΡΠ²ΠΎΠ²Π°ΡΡ ΠΏΠ»Π°ΡΡΠΈΠΊΠΎΠ²ΡΠΌ Π΄Π΅ΡΠ°Π»ΡΠΌ βΒ Π½Π΅ΡΡΠΎ ΠΏΠΎΠ΄ΠΎΠ±Π½ΠΎΠ΅ ΠΏΡΠΎΡΡΠΎ Π½Π΅ΠΌΡΡΠ»ΠΈΠΌΠΎ ΠΈΠ·Π³ΠΎΡΠΎΠ²ΠΈΡΡ ΠΈΠ· ΡΡΠ°Π»ΠΈ ΠΈΠ»ΠΈ Π°Π»ΡΠΌΠΈΠ½ΠΈΡ.
Π’Π΅ΠΌ Π²ΡΠ΅ΠΌΠ΅Π½Π΅ΠΌ ΠΊΠΎΠ½ΡΡΡΡΠΊΡΠΈΡ ΠΊΡΠ·ΠΎΠ²ΠΎΠ² ΠΌΠ°ΡΠΈΠ½ ΠΎΡΡΠ°Π²Π°Π»Π°ΡΡ ΡΡΠ°Π΄ΠΈΡΠΈΠΎΠ½Π½ΠΎ ΡΡΠ°Π»ΡΠ½ΠΎΠΉ. ΠΠ°Π΄Π°ΡΡ ΠΏΠΎΠ²ΡΡΠ΅Π½ΠΈΡ ΠΏΡΠΎΡΠ½ΠΎΡΡΠΈ ΠΊΡΠ·ΠΎΠ²Π° ΠΈ ΡΠ½ΠΈΠΆΠ΅Π½ΠΈΡ ΠΌΠ°ΡΡΡ Π²ΡΠΏΠΎΠ»Π½ΠΈΠ»ΠΈ ΠΏΠ΅ΡΠ΅Ρ ΠΎΠ΄ΠΎΠΌ Π½Π° Π±ΠΎΠ»Π΅Π΅ ΡΠΈΡΠΎΠΊΠΎΠ΅ ΠΈΡΠΏΠΎΠ»ΡΠ·ΠΎΠ²Π°Π½ΠΈΠ΅ ΡΡΠ°Π»Π΅ΠΉ Π²ΡΡΠΎΠΊΠΎΠΉ ΠΏΡΠΎΡΠ½ΠΎΡΡΠΈ, ΠΈΡ ΠΌΠ°ΡΡΠ° Π² ΡΠΎΡΡΠ°Π²Π΅ ΠΊΡΠ·ΠΎΠ²Π° Π½Π΅ΠΏΡΠ΅ΡΡΠ²Π½ΠΎ ΡΠ²Π΅Π»ΠΈΡΠΈΠ²Π°Π»Π°ΡΡ, Ρ Π½Π΅ΡΠΊΠΎΠ»ΡΠΊΠΈΡ ΠΏΡΠΎΡΠ΅Π½ΡΠΎΠ² Π² ΠΊΠΎΠ½ΡΠ΅ ΡΠ΅ΠΌΠΈΠ΄Π΅ΡΡΡΡΡ Π³ΠΎΠ΄ΠΎΠ² ΠΈ Π΄ΠΎ ΡΠ²Π΅ΡΠ΅Π½Π½ΡΡ 20-40% ΠΊ ΡΠ΅ΡΠ΅Π΄ΠΈΠ½Π΅ Π΄Π΅Π²ΡΠ½ΠΎΡΡΡΡ Ρ ΠΏΠ΅ΡΠ΅Π΄ΠΎΠ²ΡΡ ΠΊΠΎΠ½ΡΡΡΡΠΊΡΠΈΠΉ Π΅Π²ΡΠΎΠΏΠ΅ΠΉΡΠΊΠΈΡ ΠΌΠ°ΡΠΎΠΊ ΠΈ 10-15% Ρ Π°ΠΌΠ΅ΡΠΈΠΊΠ°Π½ΡΠΊΠΈΡ Π°Π²ΡΠΎ.
ΠΡΠΎΠ±Π»Π΅ΠΌΡ Ρ ΠΊΠΎΡΡΠΎΠ·ΠΈΠ΅ΠΉ ΡΠ΅ΡΠΈΠ»ΠΈ ΠΏΠ΅ΡΠ΅Ρ ΠΎΠ΄ΠΎΠΌ Π½Π° ΠΎΡΠΈΠ½ΠΊΠΎΠ²Π°Π½Π½ΡΠΉ ΠΏΡΠΎΠΊΠ°Ρ ΠΈ Π½ΠΎΠ²ΡΠ΅ ΡΠ΅Ρ Π½ΠΎΠ»ΠΎΠ³ΠΈΠΈ ΠΎΠΊΡΠ°ΡΠΊΠΈ, ΠΊΠΎΡΠΎΡΡΠ΅ ΠΏΠΎΠ·Π²ΠΎΠ»ΠΈΠ»ΠΈ ΡΠ²Π΅Π»ΠΈΡΠΈΡΡ ΡΡΠΎΠΊ Π³Π°ΡΠ°Π½ΡΠΈΠΈ Π½Π° ΠΊΡΠ·ΠΎΠ² Π΄ΠΎ 6-10 Π»Π΅Ρ. ΠΠ»ΡΠΌΠΈΠ½ΠΈΠΉ ΠΆΠ΅ ΠΎΡΡΠ°Π»ΡΡ Π½Π΅ Ρ Π΄Π΅Π», Π΅Π³ΠΎ ΡΠΎΠ΄Π΅ΡΠΆΠ°Π½ΠΈΠ΅ Π² ΠΌΠ°ΡΡΠ΅ ΠΌΠ°ΡΠΈΠ½Ρ Π΄Π°ΠΆΠ΅ ΡΠΌΠ΅Π½ΡΡΠΈΠ»ΠΎΡΡ ΠΏΠΎ ΡΡΠ°Π²Π½Π΅Π½ΠΈΡ Ρ 60-ΠΌΠΈ Π³ΠΎΠ΄Π°ΠΌΠΈ β ΡΡΠ³ΡΠ°Π» ΡΠΎΠ»Ρ Π½Π΅ΡΡΡΠ½ΠΎΠΉ ΠΊΡΠΈΠ·ΠΈΡ, ΠΊΠΎΠ³Π΄Π° Π΄ΠΎΡΠΎΠΆΠ΅ ΡΡΠ°Π»ΠΈ ΡΠ½Π΅ΡΠ³ΠΎΠ½ΠΎΡΠΈΡΠ΅Π»ΠΈ, Π° Π·Π½Π°ΡΠΈΡ ΠΈ ΡΠ°ΠΌ ΠΌΠ΅ΡΠ°Π»Π». ΠΠ΄Π΅ Π²ΠΎΠ·ΠΌΠΎΠΆΠ½ΠΎ, Π΅Π³ΠΎ Π·Π°ΠΌΠ΅Π½ΠΈΠ» ΠΏΠ»Π°ΡΡΠΈΠΊ, Π° Π³Π΄Π΅ ΠΏΠ»Π°ΡΡΠΈΠΊ Π½Π΅ Π³ΠΎΠ΄ΠΈΠ»ΡΡ β ΡΠ½ΠΎΠ²Π° ΡΡΠ°Π»Ρ.
ΠΠ»ΡΠΌΠΈΠ½ΠΈΠΉ Π½Π°Π½ΠΎΡΠΈΡ ΠΎΡΠ²Π΅ΡΠ½ΡΠΉ ΡΠ΄Π°Ρ
ΠΡΠΎΠΈΠ³ΡΠ°Π² Π±ΠΈΡΠ²Ρ Π·Π° ΡΠΊΡΡΠ΅ΡΡΠ΅Ρ, ΡΠ΅ΡΠ΅Π· Π΄Π΅ΡΡΡΠΈΠ»Π΅ΡΠΈΠ΅ Π°Π»ΡΠΌΠΈΠ½ΠΈΠΉ ΠΎΡΡΠ³ΡΠ°Π» ΡΠ²ΠΎΠ΅ ΠΏΠΎΠ΄ ΠΊΠ°ΠΏΠΎΡΠΎΠΌ. Π 90-Π΅ ΠΈ 2000-Π΅ Π³ΠΎΠ΄Ρ ΠΏΡΠΎΠΈΠ·Π²ΠΎΠ΄ΠΈΡΠ΅Π»ΠΈ ΠΌΠ°ΡΡΠΎΠ²ΠΎ ΠΏΠ΅ΡΠ΅Ρ ΠΎΠ΄ΠΈΠ»ΠΈ Π½Π° Π°Π»ΡΠΌΠΈΠ½ΠΈΠ΅Π²ΡΠ΅ ΠΊΠΎΡΠΏΡΡΠ° ΠΠΠ ΠΈ Π±Π»ΠΎΠΊΠΈ ΡΠΈΠ»ΠΈΠ½Π΄ΡΠΎΠ², Π° Π·Π°ΡΠ΅ΠΌ ΠΈ Π΄Π΅ΡΠ°Π»ΠΈ ΠΏΠΎΠ΄Π²Π΅ΡΠΊΠΈ. ΠΠΎ ΡΡΠΎ Π±ΡΠ»ΠΎ ΡΠΎΠ»ΡΠΊΠΎ Π½Π°ΡΠ°Π»ΠΎ.
ΠΠ°Π΄Π΅Π½ΠΈΠ΅ ΡΠ΅Π½ Π½Π° Π°Π»ΡΠΌΠΈΠ½ΠΈΠΉ Π² Π΄Π΅Π²ΡΠ½ΠΎΡΡΡΠ΅ Π³ΠΎΠ΄Ρ ΡΠ΄Π°ΡΠ½ΠΎ ΡΠΎΠ²ΠΏΠ°Π»ΠΎ Ρ ΡΠΆΠ΅ΡΡΠΎΡΠ΅Π½ΠΈΠ΅ΠΌ ΡΡΠ΅Π±ΠΎΠ²Π°Π½ΠΈΠΉ ΠΊ ΡΠΊΠΎΠ½ΠΎΠΌΠΈΡΠ½ΠΎΡΡΠΈ ΠΈ ΡΠΊΠΎΠ»ΠΎΠ³ΠΈΡΠ½ΠΎΡΡΠΈ ΠΌΠ°ΡΠΈΠ½. ΠΠΎΠΌΠΈΠΌΠΎ ΡΠΆΠ΅ ΡΠΏΠΎΠΌΡΠ½ΡΡΡΡ ΠΊΡΡΠΏΠ½ΡΡ ΡΠ·Π»ΠΎΠ², Π°Π»ΡΠΌΠΈΠ½ΠΈΠΉ ΠΏΡΠΎΠΏΠΈΡΠ°Π»ΡΡ Π²ΠΎ ΠΌΠ½ΠΎΠΆΠ΅ΡΡΠ²Π΅ Π΄Π΅ΡΠ°Π»Π΅ΠΉ ΠΈ Π°Π³ΡΠ΅Π³Π°ΡΠΎΠ² ΠΌΠ°ΡΠΈΠ½Ρ, ΠΎΡΠΎΠ±Π΅Π½Π½ΠΎ ΠΈΠΌΠ΅ΡΡΠΈΡ ΠΎΡΠ½ΠΎΡΠ΅Π½ΠΈΠ΅ ΠΊ ΠΏΠ°ΡΡΠΈΠ²Π½ΠΎΠΉ Π±Π΅Π·ΠΎΠΏΠ°ΡΠ½ΠΎΡΡΠΈ β ΠΊΡΠΎΠ½ΡΡΠ΅ΠΉΠ½Π°Ρ ΡΡΠ»Π΅Π²ΠΎΠ³ΠΎ ΡΠΏΡΠ°Π²Π»Π΅Π½ΠΈΡ, Π±Π°Π»ΠΊΠ°Ρ -ΡΡΠΈΠ»ΠΈΡΠ΅Π»ΡΡ , ΠΎΠΏΠΎΡΠ°Ρ ΠΌΠΎΡΠΎΡΠΎΠ²… ΠΡΠΈΠ³ΠΎΠ΄ΠΈΠ»Π°ΡΡ ΠΈ Π΅Π³ΠΎ ΠΏΡΠΈΡΠΎΠ΄Π½Π°Ρ Ρ ΡΡΠΏΠΊΠΎΡΡΡ, ΠΈ ΡΠΈΡΠΎΠΊΠΈΠΉ Π΄ΠΈΠ°ΠΏΠ°Π·ΠΎΠ½ ΠΈΠ·ΠΌΠ΅Π½Π΅Π½ΠΈΡ Π²ΡΠ·ΠΊΠΎΡΡΠΈ, ΠΈ Π½ΠΈΠ·ΠΊΠ°Ρ ΠΌΠ°ΡΡΠ°.
ΠΠ°Π»ΡΡΠ΅ β Π±ΠΎΠ»ΡΡΠ΅, Π°Π»ΡΠΌΠΈΠ½ΠΈΠΉ ΡΡΠ°Π» ΠΏΠΎΡΠ²Π»ΡΡΡΡΡ ΠΈ Π² ΠΊΠΎΠ½ΡΡΡΡΠΊΡΠΈΠΈ ΠΊΡΠ·ΠΎΠ²Π°. ΠΡΠΎ ΡΠ΅Π»ΡΠ½ΠΎΠ°Π»ΡΠΌΠΈΠ½ΠΈΠ΅Π²ΡΠ΅ Audi A8 Ρ ΡΠ°ΡΡΠΊΠ°Π·ΡΠ²Π°Π» ΠΏΠΎΠ΄ΡΠΎΠ±Π½ΠΎ, Π½ΠΎ ΠΈ Π½Π° Π±ΠΎΠ»Π΅Π΅ ΠΏΡΠΎΡΡΡΡ ΠΌΠ°ΡΠΈΠ½Π°Ρ ΡΡΠ°Π»ΠΈ ΠΏΠΎΡΠ²Π»ΡΡΡΡΡ Π²Π½Π΅ΡΠ½ΠΈΠ΅ ΠΏΠ°Π½Π΅Π»ΠΈ ΠΈΠ· Π»Π΅Π³ΠΊΠΎΠ³ΠΎ ΠΌΠ΅ΡΠ°Π»Π»Π°. Π ΠΏΠ΅ΡΠ²ΡΡ ΠΎΡΠ΅ΡΠ΅Π΄Ρ ΡΡΠΎ Π½Π°Π²Π΅ΡΠ½ΡΠ΅ ΠΏΠ°Π½Π΅Π»ΠΈ, ΠΊΠ°ΠΏΠΎΡ, ΠΏΠ΅ΡΠ΅Π΄Π½ΠΈΠ΅ ΠΊΡΡΠ»ΡΡ ΠΈ Π΄Π²Π΅ΡΠΈ Π½Π° Π°Π²ΡΠΎ ΠΏΡΠ΅ΠΌΠΈΠ°Π»ΡΠ½ΡΡ ΠΌΠ°ΡΠΎΠΊ. ΠΠ΅Π³ΠΊΠΎΡΠΏΠ»Π°Π²Π½ΡΠΌΠΈ ΡΡΠ°Π»ΠΈ ΠΏΠΎΠ΄ΡΠ°ΠΌΠ½ΠΈΠΊΠΈ, Π±ΡΡΠ·Π³ΠΎΠ²ΠΈΠΊΠΈ ΠΈ Π΄Π°ΠΆΠ΅ ΡΡΠΈΠ»ΠΈΡΠ΅Π»ΠΈ. ΠΠ° ΡΠΎΠ²ΡΠ΅ΠΌΠ΅Π½Π½ΡΡ BMW ΠΈ Audi Π² ΠΏΠ΅ΡΠ΅Π΄Π½Π΅ΠΉ ΡΠ°ΡΡΠΈ ΠΊΡΠ·ΠΎΠ²ΠΎΠ² ΠΎΡΡΠ°Π»ΡΡ ΠΏΡΠ°ΠΊΡΠΈΡΠ΅ΡΠΊΠΈ ΠΎΠ΄ΠΈΠ½ Π°Π»ΡΠΌΠΈΠ½ΠΈΠΉ ΠΈ ΠΏΠ»Π°ΡΡΠΈΠΊ. ΠΠ΄ΠΈΠ½ΡΡΠ²Π΅Π½Π½ΠΎΠ΅, Π³Π΄Π΅ ΠΏΠΎΠ·ΠΈΡΠΈΠΈ ΡΡΠ°Π»ΠΈ ΠΏΠΎΠΊΠ° Π½Π΅Π·ΡΠ±Π»Π΅ΠΌΡ β ΡΡΠΎ ΡΠΈΠ»ΠΎΠ²ΡΠ΅ ΠΊΠΎΠ½ΡΡΡΡΠΊΡΠΈΠΈ.
ΠΡΠΎ ΠΌΠΈΠ½ΡΡΡ ΠΈ ΠΊΠΎΡΡΠΎΠ·ΠΈΡ
ΠΠ»ΡΠΌΠΈΠ½ΠΈΠΉ β ΡΡΠΎ Π²ΡΠ΅Π³Π΄Π° ΡΠ»ΠΎΠΆΠ½ΠΎΡΡΠΈ ΡΠΎ ΡΠ²Π°ΡΠΊΠΎΠΉ ΠΈ ΠΊΡΠ΅ΠΏΠ΅ΠΆΠΎΠΌ. ΠΠ»Ρ ΡΠΎΠ΅Π΄ΠΈΠ½Π΅Π½ΠΈΡ ΡΠΎ ΡΡΠ°Π»ΡΠ½ΡΠΌΠΈ ΡΠ»Π΅ΠΌΠ΅Π½ΡΠ°ΠΌΠΈ ΠΏΠΎΠ΄Ρ ΠΎΠ΄ΡΡ ΡΠΎΠ»ΡΠΊΠΎ ΠΊΠ»Π΅ΠΏΠΊΠ°, Π±ΠΎΠ»ΡΡ ΠΈ ΡΠΊΠ»Π΅ΠΉΠΊΠ°, Π΄Π»Ρ ΡΠΎΠ΅Π΄ΠΈΠ½Π΅Π½ΠΈΡ Ρ Π΄ΡΡΠ³ΠΈΠΌΠΈ Π°Π»ΡΠΌΠΈΠ½ΠΈΠ΅Π²ΡΠΌΠΈ Π΄Π΅ΡΠ°Π»ΡΠΌΠΈ βΒ Π΅ΡΠ΅ ΡΠ²Π°ΡΠΊΠ° ΠΈ ΡΡΡΡΠΏΡ. ΠΠ΅ΠΌΠ½ΠΎΠ³ΠΈΠ΅ ΠΏΡΠΈΠΌΠ΅ΡΡ ΠΊΠΎΠ½ΡΡΡΡΠΊΡΠΈΠΉ Ρ ΠΈΡΠΏΠΎΠ»ΡΠ·ΠΎΠ²Π°Π½ΠΈΠ΅ΠΌ Π»Π΅Π³ΠΊΠΎΡΠΏΠ»Π°Π²Π½ΡΡ Π½Π΅ΡΡΡΠΈΡ ΡΠ»Π΅ΠΌΠ΅Π½ΡΠΎΠ² ΠΏΡΠΎΡΠ²ΠΈΠ»ΠΈ ΡΠ΅Π±Ρ Π²Π΅ΡΡΠΌΠ° ΠΊΠ°ΠΏΡΠΈΠ·Π½ΡΠΌΠΈ Π² ΡΠΊΡΠΏΠ»ΡΠ°ΡΠ°ΡΠΈΠΈ ΠΈ ΠΎΡΠΌΠ΅Π½Π½ΠΎ Π½Π΅ΡΠ΄ΠΎΠ±Π½ΡΠΌΠΈ Π² Π²ΠΎΡΡΡΠ°Π½ΠΎΠ²Π»Π΅Π½ΠΈΠΈ.
Π’Π°ΠΊ, Π°Π»ΡΠΌΠΈΠ½ΠΈΠ΅Π²ΡΠ΅ ΡΠ°ΡΠΊΠΈ ΠΏΠ΅ΡΠ΅Π΄Π½Π΅ΠΉ ΠΏΠΎΠ΄Π²Π΅ΡΠΊΠΈ Π½Π° ΠΌΠ°ΡΠΈΠ½Π°Ρ BMW ΠΈ Π»ΠΎΠ½ΠΆΠ΅ΡΠΎΠ½Ρ Π΄ΠΎ ΡΠΈΡ ΠΏΠΎΡ ΠΈΠΌΠ΅ΡΡ ΡΠ»ΠΎΠΆΠ½ΠΎΡΡΠΈ Ρ ΡΠ»Π΅ΠΊΡΡΠΎΡ ΠΈΠΌΠΈΡΠ΅ΡΠΊΠΎΠΉ ΠΊΠΎΡΡΠΎΠ·ΠΈΠ΅ΠΉ Π² ΠΌΠ΅ΡΡΠ°Ρ ΡΡΡΠΊΠΎΠ² ΠΈ ΠΏΡΠΎΠ±Π»Π΅ΠΌΡ Ρ Π²ΠΎΡΡΡΠ°Π½ΠΎΠ²Π»Π΅Π½ΠΈΠ΅ΠΌ ΡΠΎΠ΅Π΄ΠΈΠ½Π΅Π½ΠΈΠΉ ΠΏΠΎΡΠ»Π΅ ΠΏΠΎΠ²ΡΠ΅ΠΆΠ΄Π΅Π½ΠΈΠΉ ΠΊΡΠ·ΠΎΠ²Π°.
Π§ΡΠΎ ΠΊΠ°ΡΠ°Π΅ΡΡΡ ΠΊΠΎΡΡΠΎΠ·ΠΈΠΈ Π°Π»ΡΠΌΠΈΠ½ΠΈΡ, ΡΠΎ Π±ΠΎΡΠΎΡΡΡΡ Ρ Π½Π΅ΠΉ Π΄Π°ΠΆΠ΅ ΡΠ»ΠΎΠΆΠ½Π΅Π΅, ΡΠ΅ΠΌ Ρ ΠΊΠΎΡΡΠΎΠ·ΠΈΠ΅ΠΉ ΡΡΠ°Π»ΠΈ. ΠΡΠΈ Π±ΠΎΠ»Π΅Π΅ Π²ΡΡΠΎΠΊΠΎΠΉ Ρ ΠΈΠΌΠΈΡΠ΅ΡΠΊΠΎΠΉ Π°ΠΊΡΠΈΠ²Π½ΠΎΡΡΠΈ Π΅Π³ΠΎ ΡΡΠΎΠΉΠΊΠΎΡΡΡ ΠΊ ΠΎΠΊΠΈΡΠ»Π΅Π½ΠΈΡ ΠΎΠ±ΡΡΡΠ½ΡΠ΅ΡΡΡ Π² ΠΎΡΠ½ΠΎΠ²Π½ΠΎΠΌ ΠΎΠ±ΡΠ°Π·ΠΎΠ²Π°Π½ΠΈΠ΅ΠΌ Π·Π°ΡΠΈΡΠ½ΠΎΠΉ ΠΏΠ»Π΅Π½ΠΊΠΈ ΠΎΠΊΠΈΡΠ»ΠΎΠ² Π½Π° ΠΏΠΎΠ²Π΅ΡΡ Π½ΠΎΡΡΠΈ. Π ΡΡΠΎΡ ΡΠΏΠΎΡΠΎΠ± ΡΠ°ΠΌΠΎΠ·Π°ΡΠΈΡΡ Π² ΡΡΠ»ΠΎΠ²ΠΈΡΡ ΡΠΎΠ΅Π΄ΠΈΠ½Π΅Π½ΠΈΡ Π΄Π΅ΡΠ°Π»Π΅ΠΉ ΠΈΠ· ΠΊΡΡΠΈ ΡΠ°Π·Π½ΡΡ ΡΠΏΠ»Π°Π²ΠΎΠ² ΠΎΠΊΠ°Π·Π°Π»ΡΡ Π±Π΅ΡΠΏΠΎΠ»Π΅Π·Π΅Π½.
Π‘Π»ΠΎΠΆΠ½ΠΎΡΡΠΈ ΡΠΎ ΡΡΠ°Π»ΡΡ, ΠΊΠΎΡΠΎΡΡΠ΅ ΠΌΠΎΠ³ΡΡ ΠΈΠ·ΠΌΠ΅Π½ΠΈΡΡ Π²ΡΠ΅
ΠΠΎΠΊΠ° Π°Π»ΡΠΌΠΈΠ½ΠΈΠΉ Π·Π°Ρ Π²Π°ΡΡΠ²Π°Π» Π½ΠΎΠ²ΡΠ΅ ΡΠ΅ΡΡΠΈΡΠΎΡΠΈΠΈ, ΡΠ΅Ρ Π½ΠΎΠ»ΠΎΠ³ΠΈΠΈ ΠΏΡΠΎΠΈΠ·Π²ΠΎΠ΄ΡΡΠ²Π° ΡΡΠ°Π»ΡΠ½ΠΎΠ³ΠΎ ΠΏΡΠΎΠΊΠ°ΡΠ° Π½Π΅ ΡΡΠΎΡΠ»ΠΈ Π½Π° ΠΌΠ΅ΡΡΠ΅. Π‘ΡΠΎΠΈΠΌΠΎΡΡΡ Π²ΡΡΠΎΠΊΠΎΠΏΡΠΎΡΠ½ΡΡ ΡΡΠ°Π»Π΅ΠΉ ΡΠ½ΠΈΠΆΠ°Π»Π°ΡΡ, ΠΏΠΎΡΠ²ΠΈΠ»ΠΈΡΡ ΠΌΠ°ΡΡΠΎΠ²ΡΠ΅ ΡΡΠ°Π»ΠΈ Π³ΠΎΡΡΡΠ΅ΠΉ ΡΡΠ°ΠΌΠΏΠΎΠ²ΠΊΠΈ, Π°Π½ΡΠΈΠΊΠΎΡΡΠΎΠ·ΠΈΠΉΠ½Π°Ρ Π·Π°ΡΠΈΡΠ° ΠΏΡΡΡΡ ΠΈ Ρ ΠΏΡΠΎΠ±ΡΠΊΡΠΎΠ²ΠΊΠ°ΠΌΠΈ, ΡΠΎΠΆΠ΅ ΡΠ»ΡΡΡΠ°Π»Π°ΡΡ.
ΠΠΎ Π°Π»ΡΠΌΠΈΠ½ΠΈΠΉ Π²ΡΠ΅ ΠΆΠ΅ Π½Π°ΡΡΡΠΏΠ°Π΅Ρ, ΠΈ ΠΏΡΠΈΡΠΈΠ½Ρ ΡΡΠΎΠ³ΠΎ ΠΏΠΎΠ½ΡΡΠ½Ρ Π²ΡΠ΅ΠΌ, ΠΊΡΠΎ Π·Π½Π°ΠΊΠΎΠΌ Ρ ΠΏΡΠΎΡΠ΅ΡΡΠΎΠΌ ΡΡΠ°ΠΌΠΏΠΎΠ²ΠΊΠΈ ΠΈ ΡΠ²Π°ΡΠΊΠΈ ΡΡΠ°Π»ΡΠ½ΡΡ Π΄Π΅ΡΠ°Π»Π΅ΠΉ. ΠΠ°, Π±ΠΎΠ»Π΅Π΅ ΠΏΡΠΎΡΠ½ΡΠ΅ ΡΡΠ°Π»ΠΈ ΠΏΠΎΠ·Π²ΠΎΠ»ΡΡΡ ΠΎΠ±Π»Π΅Π³ΡΠΈΡΡ ΠΊΡΠ·ΠΎΠ² ΠΌΠ°ΡΠΈΠ½Ρ ΠΈ ΡΠ΄Π΅Π»Π°ΡΡ Π΅Π³ΠΎ ΠΊΡΠ΅ΠΏΡΠ΅ ΠΈ ΠΆΠ΅ΡΡΡΠ΅. ΠΠ±ΡΠ°ΡΠ½Π°Ρ ΡΡΠΎΡΠΎΠ½Π° ΠΌΠ΅Π΄Π°Π»ΠΈ β ΠΏΠΎΠ²ΡΡΠ΅Π½ΠΈΠ΅ ΡΡΠΎΠΈΠΌΠΎΡΡΠΈ ΡΠ°ΠΌΠΎΠΉ ΡΡΠ°Π»ΠΈ, ΡΠ²Π΅Π»ΠΈΡΠ΅Π½ΠΈΠ΅Β ΡΠ΅Π½Ρ ΡΡΠ°ΠΌΠΏΠΎΠ²ΠΊΠΈ, ΡΠΎΡΡΒ ΡΠ΅Π½Ρ ΡΠ²Π°ΡΠΊΠΈ ΠΈ ΡΠ»ΠΎΠΆΠ½ΠΎΡΡΠΈ Ρ ΡΠ΅ΠΌΠΎΠ½ΡΠΎΠΌ ΠΏΠΎΠ²ΡΠ΅ΠΆΠ΄Π΅Π½Π½ΡΡ Π΄Π΅ΡΠ°Π»Π΅ΠΉ. ΠΠΈΡΠ΅Π³ΠΎ Π½Π΅ Π½Π°ΠΏΠΎΠΌΠΈΠ½Π°Π΅Ρ? Π’ΠΎΡΠ½ΠΎ, ΡΡΠΎ ΡΠ΅ ΡΠ°ΠΌΡΠ΅ ΠΏΡΠΎΠ±Π»Π΅ΠΌΡ, ΠΊΠΎΡΠΎΡΡΠ΅ ΡΠ²ΠΎΠΉΡΡΠ²Π΅Π½Π½Ρ Π°Π»ΡΠΌΠΈΠ½ΠΈΠ΅Π²ΡΠΌ ΠΊΠΎΠ½ΡΡΡΡΠΊΡΠΈΡΠΌ ΠΎΡ ΡΠΎΠΆΠ΄Π΅Π½ΠΈΡ. Π’ΠΎΠ»ΡΠΊΠΎ Ρ Π²ΡΡΠΎΠΊΠΎΠΏΡΠΎΡΠ½ΠΎΠΉ ΡΡΠ°Π»ΠΈ ΠΈ ΡΡΠ°Π΄ΠΈΡΠΈΠΎΠ½Π½ΡΠ΅ Β«ΠΆΠ΅Π»Π΅Π·Π½ΡΠ΅Β» ΡΠ»ΠΎΠΆΠ½ΠΎΡΡΠΈ Ρ ΠΊΠΎΡΡΠΎΠ·ΠΈΠ΅ΠΉ Π½ΠΈΠΊΡΠ΄Π° Π½Π΅ ΠΈΡΡΠ΅Π·Π°ΡΡ.
ΠΡΠ΅ ΠΎΠ΄ΠΈΠ½ ΠΌΠΈΠ½ΡΡ β ΡΠ»ΠΎΠΆΠ½ΠΎΡΡΠΈ ΡΠ΅ΡΠΈΠΊΠ»ΠΈΠ½Π³Π°. Π Π²Π΅ΠΊ, ΠΊΠΎΠ³Π΄Π° Π²Π΅ΡΠΈ ΡΡΠ°Π½ΠΎΠ²ΡΡΡΡ ΠΎΠ΄Π½ΠΎΡΠ°Π·ΠΎΠ²ΡΠΌΠΈ, ΠΎ ΠΏΠ΅ΡΠ΅ΡΠ°Π±ΠΎΡΠΊΠ΅ Π·Π°Π΄ΡΠΌΡΠ²Π°ΡΡΡΡ Π²ΡΠ΅ ΡΠ°ΡΠ΅ ΠΈ ΡΠ°ΡΠ΅. Π Π²ΡΡΠΎΠΊΠΎΠ»Π΅Π³ΠΈΡΠΎΠ²Π°Π½Π½ΡΠ΅ ΡΡΠ°Π»ΠΈ Π² ΡΡΠΎΠΌ ΠΎΡΠ½ΠΎΡΠ΅Π½ΠΈΠΈ βΒ ΠΏΠ»ΠΎΡ ΠΎΠΉ ΠΏΡΠΈΠΌΠ΅Ρ. Π¦Π΅Π½Π° Π°Π»ΡΠΌΠΈΠ½ΠΈΡ ΠΌΠ°Π»ΠΎ Π·Π°Π²ΠΈΡΠΈΡ ΠΎΡ Π΅Π³ΠΎ ΠΌΠ°ΡΠΊΠΈ, ΡΠΎΠ΄Π΅ΡΠΆΠ°Π½ΠΈΠ΅ Π² ΡΠΏΠ»Π°Π²Π΅ ΡΠ΅Π½Π½ΡΡ ΠΏΡΠΈΡΠ°Π΄ΠΎΠΊ ΡΡΠ°Π²Π½ΠΈΡΠ΅Π»ΡΠ½ΠΎ Π½Π΅Π²Π΅Π»ΠΈΠΊΠΎ, Π° ΠΎΡΠ½ΠΎΠ²Π½ΡΠ΅ Ρ Π°ΡΠ°ΠΊΡΠ΅ΡΠΈΡΡΠΈΠΊΠΈ Π·Π°Π΄Π°ΡΡΡΡ ΡΠΎΠ΄Π΅ΡΠΆΠ°Π½ΠΈΠ΅ΠΌ ΠΊΡΠ΅ΠΌΠ½ΠΈΡ. ΠΡΠΈ ΠΏΠ΅ΡΠ΅ΠΏΠ»Π°Π²ΠΊΠ΅ Π΄ΠΎΠ±Π°Π²ΠΊΠΈ Ρ ΠΎΡΠΎΡΠΎ ΠΈΠ·Π²Π»Π΅ΠΊΠ°ΡΡΡΡ Π΄Π»Ρ Π΄Π°Π»ΡΠ½Π΅ΠΉΡΠ΅Π³ΠΎ ΠΈΡΠΏΠΎΠ»ΡΠ·ΠΎΠ²Π°Π½ΠΈΡ. Π ΡΠΎΠΌΡ ΠΆΠ΅ ΡΡΠ°Π²Π½ΠΈΡΠ΅Π»ΡΠ½ΠΎ ΠΌΡΠ³ΠΊΠΈΠΉ ΠΌΠ΅ΡΠ°Π»Π» Ρ ΠΎΡΠΎΡΠΎ ΠΏΠ΅ΡΠ΅ΡΠ°Π±Π°ΡΡΠ²Π°Π΅ΡΡΡ.
Π Π²ΠΎΡ ΠΎ Π²ΡΡΠΎΠΊΠΎΠΏΡΠΎΡΠ½ΠΎΠΉ ΡΡΠ°Π»ΠΈ ΠΏΠΎΠ΄ΠΎΠ±Π½ΠΎΠ³ΠΎ ΡΠΊΠ°Π·Π°ΡΡ Π½Π΅Π»ΡΠ·Ρ. ΠΠ°ΠΊΠ΅Ρ Π΄ΠΎΡΠΎΠ³ΠΈΡ Π»Π΅Π³ΠΈΡΡΡΡΠΈΡ Π΄ΠΎΠ±Π°Π²ΠΎΠΊ ΠΏΡΠΈ ΠΏΠ΅ΡΠ΅ΡΠ°Π±ΠΎΡΠΊΠ΅ Π½Π΅ΠΈΠ·Π±Π΅ΠΆΠ½ΠΎ ΡΠ΅ΡΡΠ΅ΡΡΡ. ΠΠΎΠ»Π΅Π΅ ΡΠΎΠ³ΠΎ, ΠΎΠ½ Π·Π°Π³ΡΡΠ·Π½ΡΠ΅Ρ Π²ΡΠΎΡΠΈΡΠ½ΠΎΠ΅ ΡΡΡΡΠ΅ ΠΈ ΡΡΠ΅Π±ΡΠ΅Ρ Π΄ΠΎΠΏΠΎΠ»Π½ΠΈΡΠ΅Π»ΡΠ½ΡΡ ΡΠ°ΡΡ ΠΎΠ΄ΠΎΠ² ΠΏΠΎ Π΅Π³ΠΎ ΠΎΡΠΈΡΡΠΊΠ΅. Π¦Π΅Π½Π° Π½Π° ΠΏΡΠΎΡΡΡΠ΅ ΠΌΠ°ΡΠΊΠΈ ΡΡΠ°Π»ΠΈ ΠΈ Π²ΡΡΠΎΠΊΠΎΠΏΡΠΎΡΠ½ΡΠ΅ ΡΠ°Π·Π»ΠΈΡΠ°Π΅ΡΡΡ Π² ΡΠ°Π·Ρ, ΠΈ ΠΏΡΠΈ ΠΏΠΎΠ²ΡΠΎΡΠ½ΠΎΠΌ ΠΈΡΠΏΠΎΠ»ΡΠ·ΠΎΠ²Π°Π½ΠΈΠΈ ΠΆΠ΅Π»Π΅Π·Π° Π²ΡΡ ΡΡΠ° ΡΠ°Π·Π½ΠΈΡΠ° Π±ΡΠ΄Π΅Ρ ΡΡΠ΅ΡΡΠ½Π°.
Π§ΡΠΎ Π΄Π°Π»ΡΡΠ΅?
Π‘ΡΠ΄Ρ ΠΏΠΎ Π²ΡΠ΅ΠΌΡ, Π½Π°Ρ ΠΆΠ΄Π΅Ρ Π°Π»ΡΠΌΠΈΠ½ΠΈΠ΅Π²ΠΎΠ΅ Π±ΡΠ΄ΡΡΠ΅Π΅. ΠΠ°ΠΊ Π²Ρ ΡΠΆΠ΅ ΠΏΠΎΠ½ΡΠ»ΠΈ, ΠΈΡΡ ΠΎΠ΄Π½Π°Ρ ΡΡΠΎΠΈΠΌΠΎΡΡΡ ΡΡΡΡΡ Π½Π΅ ΠΈΠ³ΡΠ°Π΅Ρ ΡΠ΅ΠΉΡΠ°Ρ ΡΠ°ΠΊΠΎΠΉ ΡΠΎΠ»ΠΈ, ΠΊΠ°ΠΊ ΡΠ΅Ρ Π½ΠΎΠ»ΠΎΠ³ΠΈΡΠ½ΠΎΡΡΡ ΠΈ ΡΠΊΠΎΠ»ΠΎΠ³ΠΈΡΠ½ΠΎΡΡΡ. ΠΠ°Π±ΠΈΡΠ°ΡΡΠ΅Π΅ ΡΠΈΠ»Ρ Β«Π·Π΅Π»Π΅Π½ΠΎΠ΅Β» Π»ΠΎΠ±Π±ΠΈ ΡΠΏΠΎΡΠΎΠ±Π½ΠΎ Π²Π»ΠΈΡΡΡ Π½Π° ΠΏΠΎΠΏΡΠ»ΡΡΠ½ΠΎΡΡΡ Π°Π»ΡΠΌΠΈΠ½ΠΈΠ΅Π²ΡΡ ΠΌΠ°ΡΠΈΠ½ Π΅ΡΠ΅ ΠΌΠ½ΠΎΠΆΠ΅ΡΡΠ²ΠΎΠΌ ΡΠΏΠΎΡΠΎΠ±ΠΎΠ², ΠΎΡ ΡΠ΄Π°ΡΠ½ΠΎΠ³ΠΎ ΠΏΠΈΠ°ΡΠ° Π΄ΠΎ ΡΠΌΠ΅Π½ΡΡΠ΅Π½Π½ΠΎΠ³ΠΎ ΡΠ±ΠΎΡΠ° Π½Π° ΡΡΠΈΠ»ΠΈΠ·Π°ΡΠΈΡ. Π ΠΈΡΠΎΠ³Π΅ ΠΈΠΌΠΈΠ΄ΠΆ ΠΏΡΠ΅ΠΌΠΈΠ°Π»ΡΠ½ΡΡ Π±ΡΠ΅Π½Π΄ΠΎΠ² ΡΡΠ΅Π±ΡΠ΅Ρ Π±ΠΎΠ»Π΅Π΅ ΡΠΈΡΠΎΠΊΠΎΠ³ΠΎ ΠΈΡΠΏΠΎΠ»ΡΠ·ΠΎΠ²Π°Π½ΠΈΡ Π°Π»ΡΠΌΠΈΠ½ΠΈΡ ΠΈ ΠΏΠΎΠΏΡΠ»ΡΡΠΈΠ·Π°ΡΠΈΠΈ ΡΠ΅Ρ Π½ΠΎΠ»ΠΎΠ³ΠΈΠΉ Π² ΠΌΠ°ΡΡΠ°Ρ , Ρ ΠΌΠ°ΠΊΡΠΈΠΌΠ°Π»ΡΠ½ΠΎΠΉ Π²ΡΠ³ΠΎΠ΄ΠΎΠΉ Π΄Π»Ρ ΡΠ΅Π±Ρ, ΡΠ°Π·ΡΠΌΠ΅Π΅ΡΡΡ.
Π‘ΡΠ°Π»ΡΠ½ΡΠ΅ ΠΊΠΎΠ½ΡΡΡΡΠΊΡΠΈΠΈ ΠΎΡΡΠ°ΡΡΡΡ ΡΠ΄Π΅Π»ΠΎΠΌ Π΄Π΅ΡΠ΅Π²ΡΡ ΠΏΡΠΎΠΈΠ·Π²ΠΎΠ΄ΠΈΡΠ΅Π»Π΅ΠΉ, Π½ΠΎ ΠΏΠΎ ΠΌΠ΅ΡΠ΅ ΡΠ΄Π΅ΡΠ΅Π²Π»Π΅Π½ΠΈΡ Π°Π»ΡΠΌΠΈΠ½ΠΈΠ΅Π²ΡΡ ΡΠ΅Ρ Π½ΠΎΠ»ΠΎΠ³ΠΈΠΉ ΠΎΠ½ΠΈ, Π½Π΅ΡΠΎΠΌΠ½Π΅Π½Π½ΠΎ, ΡΠΎΠΆΠ΅ Π½Π΅ ΡΡΡΠΎΡΡ ΠΏΠ΅ΡΠ΅Π΄ ΡΠΎΠ±Π»Π°Π·Π½ΠΎΠΌ, ΡΠ΅ΠΌ Π±ΠΎΠ»Π΅Π΅ ΡΡΠΎ ΡΠ΅ΠΎΡΠ΅ΡΠΈΡΠ΅ΡΠΊΠΎΠ΅ ΠΏΡΠ΅ΠΈΠΌΡΡΠ΅ΡΡΠ²ΠΎ Π°Π»ΡΠΌΠΈΠ½ΠΈΡ ΠΌΠΎΠΆΠ½ΠΎ ΠΈ Π΄Π°ΠΆΠ΅ Π½ΡΠΆΠ½ΠΎ ΡΠ΅Π°Π»ΠΈΠ·ΠΎΠ²Π°ΡΡ. ΠΠΎΠΊΠ° Π°Π²ΡΠΎΠΏΡΠΎΠΈΠ·Π²ΠΎΠ΄ΠΈΡΠ΅Π»ΠΈ Π½Π΅ ΠΏΡΡΠ°ΡΡΡΡ ΡΠΎΡΡΠΈΡΠΎΠ²Π°ΡΡ ΡΡΠΎΡ ΠΏΠ΅ΡΠ΅Ρ ΠΎΠ΄ βΒ ΠΊΠΎΠ½ΡΡΡΡΠΊΡΠΈΠΈ ΠΊΡΠ·ΠΎΠ²ΠΎΠ² Π±ΠΎΠ»ΡΡΠΈΠ½ΡΡΠ²Π° ΠΌΠ°ΡΠΈΠ½ ΡΠΎΠ΄Π΅ΡΠΆΠ°Ρ Π½Π΅ Π±ΠΎΠ»ΡΡΠ΅ 10-20% Π°Π»ΡΠΌΠΈΠ½ΠΈΡ.
Π’ΠΎ Π΅ΡΡΡ Β«Π°Π»ΡΠΌΠΈΠ½ΠΈΠ΅Π²ΠΎΠ΅ Π±ΡΠ΄ΡΡΠ΅Π΅Β» Π½Π΅ ΠΏΡΠΈΠ΄Π΅Ρ Π½ΠΈ Π·Π°Π²ΡΡΠ°, Π½ΠΈ ΠΏΠΎΡΠ»Π΅Π·Π°Π²ΡΡΠ°.
Π£ ΡΡΠ°Π΄ΠΈΡΠΈΠΎΠ½Π½ΠΎΠ³ΠΎ ΡΡΠ°Π»ΡΠ½ΠΎΠ³ΠΎ ΠΊΡΠ·ΠΎΠ²ΠΎΡΡΡΠΎΠ΅Π½ΠΈΡ Π²ΠΏΠ΅ΡΠ΅Π΄ΠΈ Π²ΠΈΠ΄Π½Π΅Π΅ΡΡΡ ΠΊΡΠ·ΠΎΠ²ΠΎΡΡΡΠΎΠΈΡΠ΅Π»ΡΠ½ΡΠΉ ΡΡΠΏΠΈΠΊ, ΠΈΠ·Π±Π΅ΠΆΠ°ΡΡ ΠΊΠΎΡΠΎΡΠΎΠ³ΠΎ ΠΌΠΎΠΆΠ½ΠΎ, ΡΠΎΠ»ΡΠΊΠΎ ΠΏΠ΅ΡΠ΅Π»ΠΎΠΌΠΈΠ² ΡΡΠ΅Π½Π΄Ρ Π½Π° Π²ΡΠ΅ΠΌΠ΅ΡΠ½ΠΎΠ΅ ΡΠΏΡΠΎΡΠ½Π΅Π½ΠΈΠ΅ ΠΈ ΠΎΠ±Π»Π΅Π³ΡΠ΅Π½ΠΈΠ΅ ΠΊΠΎΠ½ΡΡΡΡΠΊΡΠΈΠΉ.
ΠΠΎΠΊΠ° ΠΏΡΠΎΠ³ΡΠ΅ΡΡ ΡΠΎΡΠΌΠΎΠ·ΠΈΡ ΡΠ΅Ρ Π½ΠΎΠ»ΠΎΠ³ΠΈΡΠ½ΠΎΡΡΡ ΠΏΡΠΎΡΠ΅ΡΡΠΎΠ² ΡΠ²Π°ΡΠΊΠΈ ΠΈ Π½Π°Π»ΠΈΡΠΈΠ΅ Ρ ΠΎΡΠΎΡΠΎ ΠΎΡΠ»Π°ΠΆΠ΅Π½Π½ΡΡ ΠΏΡΠΎΠΈΠ·Π²ΠΎΠ΄ΡΡΠ²Π΅Π½Π½ΡΡ ΠΏΡΠΎΡΠ΅ΡΡΠΎΠ², ΠΊΠΎΡΠΎΡΡΠ΅ ΠΏΠΎΠΊΠ° ΠΌΠΎΠΆΠ½ΠΎ Π½Π΅Π΄ΠΎΡΠΎΠ³ΠΎ Π°Π΄Π°ΠΏΡΠΈΡΠΎΠ²Π°ΡΡ ΠΊ Π½ΠΎΠ²ΡΠΌ ΠΌΠ°ΡΠΊΠ°ΠΌ ΡΡΠ°Π»Π΅ΠΉ. Π£Π²Π΅Π»ΠΈΡΠΈΡΡ ΡΠΎΠΊ ΡΠ²Π°ΡΠΊΠΈ, Π²Π²Π΅ΡΡΠΈ ΡΠΎΡΠ½ΡΠΉ ΠΊΠΎΠ½ΡΡΠΎΠ»Ρ ΠΏΠ°ΡΠ°ΠΌΠ΅ΡΡΠΎΠ², ΡΠ²Π΅Π»ΠΈΡΠΈΡΡ ΡΡΠΈΠ»ΠΈΡ ΡΠΆΠ°ΡΠΈΡ, Π²Π²Π΅ΡΡΠΈ ΡΠ²Π°ΡΠΊΡ Π² ΠΈΠ½Π΅ΡΡΠ½ΡΡ ΡΡΠ΅Π΄Π°Ρ β¦ ΠΠΎΠΊΠ° ΡΠ°ΠΊΠΈΠ΅ ΠΌΠ΅ΡΠΎΠ΄Ρ ΠΏΠΎΠΌΠΎΠ³Π°ΡΡ, ΡΡΠ°Π»Ρ ΠΎΡΡΠ°Π½Π΅ΡΡΡ ΠΎΡΠ½ΠΎΠ²Π½ΡΠΌ ΡΠ»Π΅ΠΌΠ΅Π½ΡΠΎΠΌ ΠΊΠΎΠ½ΡΡΡΡΠΊΡΠΈΠΈ. ΠΠ΅ΡΠ΅ΡΡΡΠ°ΠΈΠ²Π°ΡΡ ΠΏΡΠΎΠΈΠ·Π²ΠΎΠ΄ΡΡΠ²ΠΎ ΡΠ»ΠΈΡΠΊΠΎΠΌ Π΄ΠΎΡΠΎΠ³ΠΎ, Π³Π»ΠΎΠ±Π°Π»ΡΠ½ΡΠ΅ ΠΈΠ·ΠΌΠ΅Π½Π΅Π½ΠΈΡ ΠΎΡΠ΅Π½ΡΒ ΡΡΠΆΠ΅Π»Ρ Π΄Π»Ρ Π½Π΅ΠΏΠΎΠ²ΠΎΡΠΎΡΠ»ΠΈΠ²ΠΎΠ³ΠΎ Π»ΠΎΠΊΠΎΠΌΠΎΡΠΈΠ²Π° ΠΏΡΠΎΠΌΡΡΠ»Π΅Π½Π½ΠΎΡΡΠΈ.
Π ΡΡΠΎ ΠΆΠ΅ ΡΡΠΎΠΈΠΌΠΎΡΡΡ Π²Π»Π°Π΄Π΅Π½ΠΈΡ Π°Π²ΡΠΎΠΌΠΎΠ±ΠΈΠ»Π΅ΠΌ? ΠΠ°, ΠΎΠ½Π° ΡΠ°ΡΡΠ΅Ρ, ΠΈ Π±ΡΠ΄Π΅Ρ ΡΠ°ΡΡΠΈ Π΄Π°Π»ΡΡΠ΅. ΠΠ°ΠΊ ΠΌΡ ΡΠΆΠ΅ Π½Π΅ΠΎΠ΄Π½ΠΎΠΊΡΠ°ΡΠ½ΠΎ Π³ΠΎΠ²ΠΎΡΠΈΠ»ΠΈ, ΡΠΎΠ²ΡΠ΅ΠΌΠ΅Π½Π½ΡΠΉ Π°Π²ΡΠΎΠΏΡΠΎΠΌ ΡΠ°Π·Π²ΠΈΡΡΡ ΡΡΡΠ°Π½ Π·Π°ΡΠΎΡΠ΅Π½ ΠΏΠΎΠ΄ Π±ΡΡΡΡΠΎΠ΅ ΠΎΠ±Π½ΠΎΠ²Π»Π΅Π½ΠΈΠ΅ Π°Π²ΡΠΎΠΏΠ°ΡΠΊΠ° ΠΈ ΡΠΎΡΡΠΎΡΡΠ΅Π»ΡΠ½ΠΎΠ³ΠΎ ΠΏΠΎΠΊΡΠΏΠ°ΡΠ΅Π»Ρ Ρ Π΄ΠΎΡΡΡΠΏΠΎΠΌ ΠΊ Π΄Π΅ΡΠ΅Π²ΡΠΌ ΠΊΡΠ΅Π΄ΠΈΡΠ°ΠΌ ΠΏΠΎΠ΄ 2-3% Π³ΠΎΠ΄ΠΎΠ²ΡΡ . ΠΡΠΎ ΡΡΡΠ°Π½Ρ Ρ ΡΠ΅Π°Π»ΡΠ½ΠΎΠΉ ΠΈΠ½ΡΠ»ΡΡΠΈΠ΅ΠΉ 10-15% ΠΈ Π·Π°ΡΠΏΠ»Π°ΡΠ°ΠΌΠΈ Β«ΡΡΠ΅Π΄Π½Π΅Π³ΠΎ ΠΊΠ»Π°ΡΡΠ°Β» Π² ΡΠ°ΠΉΠΎΠ½Π΅ 1 000 Π΄ΠΎΠ»Π»Π°ΡΠΎΠ² ΡΠΏΡΠ°Π²Π»Π΅Π½ΡΡ ΠΊΠΎΡΠΏΠΎΡΠ°ΡΠΈΠΉ Π΄ΡΠΌΠ°ΡΡ Π΄Π°Π»Π΅ΠΊΠΎ Π½Π΅ Π² ΠΏΠ΅ΡΠ²ΡΡ ΠΎΡΠ΅ΡΠ΅Π΄Ρ. ΠΡΠΈΠ΄Π΅ΡΡΡ ΠΏΠΎΠ΄ΡΡΡΠ°ΠΈΠ²Π°ΡΡΡΡ.
ΠΠΎΡΠ΅ΠΌΡ ΡΠΆΠ°Π²Π΅ΡΡ ΠΎΡΠΈΠ½ΠΊΠΎΠ²Π°Π½Π½ΡΠ΅ ΠΈ Π°Π»ΡΠΌΠΈΠ½ΠΈΠ΅Π²ΡΠ΅ ΠΌΠ°ΡΠΈΠ½Ρ
Π§Π°ΡΡΠΎ ΡΡΠ°Π»ΠΊΠΈΠ²Π°ΡΡΡ ΡΒ Π·Π°Π±Π»ΡΠΆΠ΄Π΅Π½ΠΈΠ΅ΠΌ ΠΊΠ°ΡΠ°ΡΠ΅Π»ΡΠ½ΠΎ ΠΎΡΠΈΠ½ΠΊΠΎΠ²Π°Π½Π½ΡΡ ΠΌΠ°ΡΠΈΠ½. ΠΡΠ΄ΠΈ ΡΡΠΈΡΠ°ΡΡ, ΡΡΠΎ, Π΅ΡΠ»ΠΈ ΠΌΠ°ΡΠΈΠ½Π° ΠΎΡΠΈΠ½ΠΊΠΎΠ²Π°Π½Π½Π°Ρ, ΠΎΠ½Π° Π½Π΅Β Π±ΡΠ΄Π΅Ρ Π³Π½ΠΈΡΡ ΠΈΒ ΡΠΆΠ°Π²Π΅ΡΡ. ΠΠΎ, ΠΊΒ ΡΠΎΠΆΠ°Π»Π΅Π½ΠΈΡ, ΡΡΠΎ Π½Π΅Β Π²ΡΠ΅Π³Π΄Π° ΡΠ°ΠΊ.
Π’Π°ΠΊΠ°Ρ ΡΠ°Π·Π½Π°Ρ ΠΎΡΠΈΠ½ΠΊΠΎΠ²ΠΊΠ°
ΠΠ»Ρ Π½Π°ΡΠ°Π»Π° Π½Π°Π΄ΠΎ ΠΏΠΎΠ½ΠΈΠΌΠ°ΡΡ, ΡΡΠΎ ΠΎΡΠΈΠ½ΠΊΠΎΠ²ΠΊΠ° ΠΎΡΠΈΠ½ΠΊΠΎΠ²ΠΊΠ΅ ΡΠΎΠ·Π½Ρ. ΠΠΎΠΆΠ½ΠΎ ΠΎΡΠΈΠ½ΠΊΠΎΠ²Π°ΡΡ ΠΊΡΠ·ΠΎΠ² ΡΠ»ΠΎΠ΅ΠΌ Π²Β 2 ΠΌΠΊΠΌ, Π°Β ΠΌΠΎΠΆΠ½ΠΎ ΡΠ»ΠΎΠ΅ΠΌ Π²Β 20 ΠΌΠΊΠΌΒ β ΡΡΠΎ ΠΏΠ΅ΡΠ²ΠΎΠ΅. ΠΡΠΎΡΠΎΠ΅Β β ΠΌΠ΅ΡΠΎΠ΄ΠΎΠ² ΠΎΡΠΈΠ½ΠΊΠΎΠ²ΠΊΠΈ ΠΊΡΡΠ°. ΠΡΠ΄ΠΆΠ΅ΡΠ½ΡΠ΅ ΠΌΠ°ΡΠΈΠ½Ρ ΠΎΠ±ΡΡΠ½ΠΎ ΠΎΡΠΈΠ½ΠΊΠΎΠ²ΡΠ²Π°ΡΡ ΡΠ°ΠΌΡΠΌ Π±ΡΠ΄ΠΆΠ΅ΡΠ½ΡΠΌ ΡΠΏΠΎΡΠΎΠ±ΠΎΠΌ. ΠΠ°ΠΊ ΠΏΡΠ°Π²ΠΈΠ»ΠΎ, ΡΡΠΎ Ρ ΠΎΠ»ΠΎΠ΄Π½Π°Ρ ΠΎΡΠΈΠ½ΠΊΠΎΠ²ΠΊΠ°. Π¦ΠΈΠ½ΠΊΠΎΠ²Π°Π½ΠΈΠ΅ ΠΏΡΠΎΠΈΡΡ ΠΎΠ΄ΠΈΡ ΠΏΡΡΡΠΌ ΠΎΠΊΡΠ°ΡΠΊΠΈ ΠΊΡΠ·ΠΎΠ²Π° Π°Π½Π°ΡΠΎΡΠ΅Π·Π½ΡΠΌΠΈ Π³ΡΡΠ½ΡΠ°ΠΌΠΈ ΡΒ Π²ΡΡΠΎΠΊΠΈΠΌ ΡΠΎΠ΄Π΅ΡΠΆΠ°Π½ΠΈΠ΅ΠΌ Π²ΡΡΠΎΠΊΠΎΠ΄ΠΈΡΠΏΠ΅ΡΡΠ½ΠΎΠ³ΠΎ ΡΠΈΠ½ΠΊΠΎΠ²ΠΎΠ³ΠΎ ΠΏΠΎΡΠΎΡΠΊΠ° (ΡΠΎΠ΄Π΅ΡΠΆΠ°Π½ΠΈΠ΅ ΡΠΈΠ½ΠΊΠ° Π²Β Π³ΠΎΡΠΎΠ²ΠΎΠΌ ΠΏΠΎΠΊΡΡΡΠΈΠΈ 89β93%). Π’Π°ΠΊΠ°Ρ ΠΎΡΠΈΠ½ΠΊΠΎΠ²ΠΊΠ°, ΠΊΠΎΠ½Π΅ΡΠ½ΠΎ, Π»ΡΡΡΠ΅, ΡΠ΅ΠΌ Π½ΠΈΡΠ΅Π³ΠΎ, Π½ΠΎΒ ΠΏΠΎΒ ΡΠ°ΠΊΡΡ ΠΏΡΠΈ ΠΏΠΎΠ²ΡΠ΅ΠΆΠ΄Π΅Π½ΠΈΠΈ ΠΠΠ ΠΎΡΒ ΠΊΠΎΡΡΠΎΠ·ΠΈΠΈ ΠΎΠ½Π° Π·Π°ΡΠΈΡΠ°Π΅Ρ ΡΠ»Π°Π±ΠΎ.
ΠΡΠΎΠΈΠ·Π²ΠΎΠ΄ΠΈΡΠ΅Π»ΠΈ ΡΠ°ΡΡΠΎ ΠΈΡΠΏΠΎΠ»ΡΠ·ΡΡΡ ΡΠ°ΠΊΠΎΠΉ Π²ΠΈΠ΄ ΠΎΡΠΈΠ½ΠΊΠΎΠ²ΠΊΠΈ, ΠΏΠΎΡΠΎΠΌΡ ΠΎΠ½Π° Π½Π΅Β ΡΠ°ΠΊ ΡΠΈΠ»ΡΠ½ΠΎ ΡΠΊΠ°Π·ΡΠ²Π°Π΅ΡΡΡ Π½Π°Β ΡΠ΅Π½Π΅ Π°Π²ΡΠΎΠΌΠΎΠ±ΠΈΠ»Ρ (Π²Β Π±ΡΠ΄ΠΆΠ΅ΡΠ½ΠΎΠΌ ΡΠ΅Π³ΠΌΠ΅Π½ΡΠ΅ Π±ΠΎΡΡΡΡΡ Π·Π°Β ΠΊΠ°ΠΆΠ΄ΡΡ ΠΊΠΎΠΏΠ΅ΠΉΠΊΡ). ΠΒ ΡΠΎΠΌΡΒ ΠΆΠ΅ ΡΡΠΎ Π΄Π°ΡΡ ΠΏΡΠ°Π²ΠΎ Π³ΠΎΠ²ΠΎΡΠΈΡΡ, ΡΡΠΎ ΠΊΡΠ·ΠΎΠ² ΠΎΡΠΈΠ½ΠΊΠΎΠ²Π°Π½Β β ΡΡΠΎ Π²ΡΠ³ΠΎΠ΄Π½ΠΎ ΠΈΠ·Β ΠΌΠ°ΡΠΊΠ΅ΡΠΈΠ½Π³ΠΎΠ²ΡΡ ΡΠΎΠΎΠ±ΡΠ°ΠΆΠ΅Π½ΠΈΠΉ.
ΠΡΡ ΠΎΠ΄ΠΈΠ½ Π±ΡΠ΄ΠΆΠ΅ΡΠ½ΡΠΉ ΡΠΏΠΎΡΠΎΠ± ΠΎΡΠΈΠ½ΠΊΠΎΠ²ΠΊΠΈΒ β ΡΠΈΠ½ΠΊΡΠΎΠΌΠ΅ΡΠ°Π»Π». ΠΡΠ»ΠΈ ΠΏΡΠΎΡΡΡΠΌΠΈ ΡΠ»ΠΎΠ²Π°ΠΌΠΈ, ΡΠΎΒ ΡΡΠΎ ΠΎΠ±ΡΡΠ½Π°Ρ ΡΡΠ°Π»Ρ, ΠΏΠΎΠΊΡΡΡΠ°Ρ ΡΠΏΠ΅ΡΠΈΠ°Π»ΡΠ½ΡΠΌ ΡΠΈΠ½ΠΊΠΎΡΠΎΠ΄Π΅ΡΠΆΠ°ΡΠΈΠΌ Π³ΡΡΠ½ΡΠΎΠΌ Π½Π°Β ΡΡΠ°Π΄ΠΈΠΈ ΠΏΡΠΎΠΊΠ°ΡΠ°. Π¦ΠΈΠ½ΠΊΡΠΎΠΌΠ΅ΡΠ°Π»Π» Ρ ΠΎΡΠΎΡ Π²Β ΡΠ΅Π³ΠΈΠΎΠ½Π°Ρ , Π³Π΄Π΅ Π½Π΅Ρ Π²ΡΡΠΎΠΊΠΎΠΉ Π²Π»Π°ΠΆΠ½ΠΎΡΡΠΈ, Π½ΠΎΒ Π²Β ΡΠΎΡΡΠΈΠΉΡΠΊΠΈΡ ΡΡΠ»ΠΎΠ²ΠΈΡΡ , ΠΎΡΠΎΠ±Π΅Π½Π½ΠΎ Π΅ΡΠ»ΠΈ ΠΠΠ ΠΏΠΎΠ²ΡΠ΅ΠΆΠ΄Π΅Π½ΠΎ, ΠΌΠ΅ΡΠ°Π»Π» Π²ΡΠ΅ ΡΠ°Π²Π½ΠΎ Π½Π°ΡΠΈΠ½Π°Π΅Ρ ΡΠΆΠ°Π²Π΅ΡΡ. ΠΡΡΡΡ Π½Π΅Β ΡΠ°ΠΊ Π±ΡΡΡΡΠΎ, ΠΊΠ°ΠΊ Π³ΠΎΠ»Π°Ρ ΡΡΠ°Π»Ρ. Π’Π°ΠΊ ΡΡΠΎ ΡΠΏΠΎΠ²Π°ΡΡ Π½Π°Β ΡΠΏΠ°ΡΠΈΡΠ΅Π»ΡΠ½ΡΡ ΠΎΡΠΈΠ½ΠΊΠΎΠ²ΠΊΡ Π²Β Π΄Π°Π½Π½ΠΎΠΌ ΡΠ»ΡΡΠ°Π΅ ΡΠ°ΠΊΠΆΠ΅ Π½Π΅Β ΡΡΠΎΠΈΡ. ΠΡΠΆΠ½ΠΎ Π±ΡΡΡΡΠΎ ΠΏΠΎΠ΄ΠΊΡΠ°ΡΠΈΠ²Π°ΡΡ ΡΠΊΠΎΠ»Ρ ΠΈΒ ΡΠ°ΡΠ°ΠΏΠΈΠ½Ρ.
ΠΠΎΠ²ΠΎΠ»ΡΠ½ΠΎ Ρ ΠΎΡΠΎΡΠΈΠΉ ΡΠΏΠΎΡΠΎΠ± ΠΎΡΠΈΠ½ΠΊΠΎΠ²ΠΊΠΈΒ β Π³Π°Π»ΡΠ²Π°Π½ΠΈΡΠ΅ΡΠΊΠΈΠΉ. ΠΡΠΎ ΠΊΠΎΠ³Π΄Π° ΠΊΡΠ·ΠΎΠ² ΠΊΡΠΏΠ°ΡΡ Π²Β Π²Π°Π½Π½Π΅ ΡΒ ΡΠΈΠ½ΠΊΠΎΡΠΎΠ΄Π΅ΡΠΆΠ°ΡΠΈΠΌ ΡΠ»Π΅ΠΊΡΡΠΎΠ»ΠΈΡΠΎΠΌ. ΠΠΎΠ΄ Π΄Π΅ΠΉΡΡΠ²ΠΈΠ΅ΠΌ ΡΠ»Π΅ΠΊΡΡΠΈΡΠ΅ΡΠΊΠΎΠ³ΠΎ ΡΠΎΠΊΠ° ΡΠΈΠ½ΠΊ ΠΎΡΠ°ΠΆΠ΄Π°Π΅ΡΡΡ Π½Π°Β ΠΌΠ΅ΡΠ°Π»Π»Π΅ ΡΠ°Π²Π½ΠΎΠΌΠ΅ΡΠ½ΡΠΌ ΡΠ»ΠΎΠ΅ΠΌ. ΠΠ±ΡΡΠ½ΠΎ ΡΡΠΎΡ ΡΠ»ΠΎΠΉ ΡΠΎΡΡΠ°Π²Π»ΡΠ΅Ρ 5β20 ΠΌΠΊΠΌ. ΠΡΠΈ ΡΠ°ΠΊΠΎΠΌ ΡΠΏΠΎΡΠΎΠ±Π΅ ΠΎΡΠΈΠ½ΠΊΠΎΠ²ΠΊΠΈ ΠΏΡΠΎΠΈΠ·Π²ΠΎΠ΄ΠΈΡΠ΅Π»ΠΈ, ΠΊΠ°ΠΊ ΠΏΡΠ°Π²ΠΈΠ»ΠΎ, Π΄Π°ΡΡ Π³Π°ΡΠ°Π½ΡΠΈΡ ΠΎΡΒ ΡΠΊΠ²ΠΎΠ·Π½ΠΎΠΉ ΠΊΠΎΡΡΠΎΠ·ΠΈΠΈ ΠΊΡΠ·ΠΎΠ²Π° Π½Π΅Β ΠΌΠ΅Π½Π΅Π΅ 10 Π»Π΅Ρ.
ΠΠ°Π»ΡΠ²Π°Π½ΠΈΡΠ΅ΡΠΊΡΡ ΠΎΡΠΈΠ½ΠΊΠΎΠ²ΠΊΡ ΡΠ΅Π΄ΠΊΠΎ ΠΏΡΠΈΠΌΠ΅Π½ΡΡΡ Π½Π°Β Π±ΡΠ΄ΠΆΠ΅ΡΠ½ΡΡ ΠΌΠ°ΡΠΈΠ½Π°Ρ , ΠΏΠΎΡΠΎΠΌΡ ΡΡΠΎ ΡΡΠΎ Π΄ΠΎΠ²ΠΎΠ»ΡΠ½ΠΎ Π΄ΠΎΡΠΎΠ³ΠΎ, Π°Β Π²ΠΎΡ Π½Π°Β ΠΌΠ°ΡΠΈΠ½Π°Ρ Π‘-ΠΊΠ»Π°ΡΡΠ° ΠΈΒ Π²ΡΡΠ΅ ΠΎΠ½Π° Π²ΡΡΡΠ΅ΡΠ°Π΅ΡΡΡ ΡΠ°ΡΡΠΎ.
ΠΒ Π»ΡΡΡΠΈΠΉ ΡΠΏΠΎΡΠΎΠ± ΠΎΡΠΈΠ½ΠΊΠΎΠ²ΠΊΠΈΒ β Π³ΠΎΡΡΡΠ΅Π΅ ΡΠΈΠ½ΠΊΠΎΠ²Π°Π½ΠΈΠ΅. Π‘ΡΡ ΠΎΠΉ Π·Π°ΡΠ°Π½Π΅Π΅ ΠΏΠΎΠ΄Π³ΠΎΡΠΎΠ²Π»Π΅Π½Π½ΡΠΉ ΠΊΡΠ·ΠΎΠ² Π°Π²ΡΠΎΠΌΠΎΠ±ΠΈΠ»Ρ ΠΎΠΏΡΡΠΊΠ°ΡΡ Π²Β Π²Π°Π½Π½Ρ ΡΒ Π³ΠΎΡΡΡΠΈΠΌ ΡΠΈΠ½ΠΊΠΎΠΌ. Π’Π΅ΠΌΠΏΠ΅ΡΠ°ΡΡΡΠ° ΡΠ°ΡΠΏΠ»Π°Π²Π° ΠΎΠ±ΡΡΠ½ΠΎ ΠΎΡΒ 500 Π΄ΠΎΒ 4000Β Β°C. Π’Π°ΠΊΠΎΠΉ ΡΠ΅ΡΠΌΠΈΡΠ΅ΡΠΊΠΈΠΉ ΡΠΏΠΎΡΠΎΠ± ΠΎΠ±ΡΠ°Π±ΠΎΡΠΊΠΈ ΠΊΡΠ·ΠΎΠ²Π° Π½Π΅Β ΡΠΎΠ»ΡΠΊΠΎ ΡΠ°ΠΌΡΠΉ Π»ΡΡΡΠΈΠΉ, Π½ΠΎΒ ΠΈΒ ΡΠ°ΠΌΡΠΉ Π΄ΠΎΡΠΎΠ³ΠΎΠΉ. ΠΡΠΈΠΌΠ΅Π½ΡΡΡ Π΅Π³ΠΎ Π΄Π°Π»Π΅ΠΊΠΎ Π½Π΅Β Π²ΡΠ΅ ΠΏΡΠΎΠΈΠ·Π²ΠΎΠ΄ΠΈΡΠ΅Π»ΠΈ Π΄Π°ΠΆΠ΅ ΠΏΡΠ΅ΠΌΠΈΡΠΌ-ΠΊΠ»Π°ΡΡΠ°.
Π¦ΠΈΠ½ΠΊΠΎΠ²ΠΎΠ΅ ΠΏΠΎΠΊΡΡΡΠΈΠ΅ Π²Β Π΄Π°Π½Π½ΠΎΠΌ ΡΠ»ΡΡΠ°Π΅ ΠΏΠΎΠ»ΡΡΠ°Π΅ΡΡΡ ΡΠ°ΠΌΡΠΌ ΡΠΎΠ»ΡΡΡΠΌ ΠΈΒ ΠΏΡΠΎΡΠ½ΡΠΌ. ΠΡΠΈ Π½Π΅Π·Π½Π°ΡΠΈΡΠ΅Π»ΡΠ½ΡΡ ΠΏΠΎΠ²ΡΠ΅ΠΆΠ΄Π΅Π½ΠΈΡΡ ΠΠΠ ΠΌΠ΅ΡΡΠΎ ΡΠΊΠΎΠ»Π° ΠΈΠ»ΠΈ ΡΠ°ΡΠ°ΠΏΠΈΠ½Ρ ΠΌΠΎΠ³ΡΡ Π΄Π°ΠΆΠ΅ Π·Π°ΡΡΠ½ΡΡΡΡΡ ΠΎΡΠ»ΠΎΠΆΠ΅Π½ΠΈΡΠΌΠΈ ΡΠΈΠ½ΠΊΠ°Β β ΡΡΠΎΡ ΠΏΡΠΎΡΠ΅ΡΡ Π½Π°Π·ΡΠ²Π°Π΅ΡΡΡ ΡΠ°ΠΌΠΎΠ²ΠΎΡΡΡΠ°Π½ΠΎΠ²Π»Π΅Π½ΠΈΠ΅ΠΌ. ΠΒ ΡΡΠΎΠΌ ΡΠ»ΡΡΠ°Π΅ Π΄Π°ΠΆΠ΅ ΠΏΠΎΠ²ΡΠ΅ΠΆΠ΄Π΅Π½Π½ΡΠΉ ΠΊΡΠ·ΠΎΠ² ΠΌΠΎΠΆΠ΅Ρ Π½Π΅Β ΡΠΆΠ°Π²Π΅ΡΡ 5β8 Π»Π΅Ρ. ΠΠ°ΠΊ ΠΏΡΠ°Π²ΠΈΠ»ΠΎ, Π½Π°Β ΠΌΠ°ΡΠΈΠ½Ρ, ΠΎΡΠΈΠ½ΠΊΠΎΠ²Π°Π½Π½ΡΠ΅ Π³ΠΎΡΡΡΠΈΠΌ ΡΠΏΠΎΡΠΎΠ±ΠΎΠΌ, Π°Π²ΡΠΎΠΏΡΠΎΠΈΠ·Π²ΠΎΠ΄ΠΈΡΠ΅Π»ΠΈ Π΄Π°ΡΡ Π³Π°ΡΠ°Π½ΡΠΈΡ ΠΎΡΒ ΡΠΊΠ²ΠΎΠ·Π½ΠΎΠΉ Π³Π°ΡΠ°Π½ΡΠΈΠΈ 15 Π»Π΅Ρ ΠΈΒ Π±ΠΎΠ»ΡΡΠ΅.
ΠΠ΄Π½Π°ΠΊΠΎ Π½Π°Π΄ΠΎ ΠΏΠΎΠ½ΠΈΠΌΠ°ΡΡ, ΡΡΠΎ Π΄Π°ΠΆΠ΅ ΡΠ°ΠΌΠΎΠ΅ Π»ΡΡΡΠ΅Π΅ ΡΠΈΠ½ΠΊΠΎΠ²Π°Π½ΠΈΠ΅ Π½Π΅Β ΠΌΠΎΠΆΠ΅Ρ Π·Π°ΡΠΈΡΠΈΡΡ ΠΊΡΠ·ΠΎΠ² ΠΎΡΒ ΠΊΠΎΡΡΠΎΠ·ΠΈΠΈ Π½Π°Π²Π΅ΡΠ½ΠΎ. ΠΡΠ»ΠΈ ΠΠΠ ΡΠ΅Π»ΠΎΠ΅, ΡΠΎΒ Π²ΡΡ Ρ ΠΎΡΠΎΡΠΎ, Π½ΠΎΒ Π΅ΡΠ»ΠΈ ΠΏΠΎΡΠ²ΠΈΠ»ΡΡ ΡΠΊΠΎΠ», ΡΠ°ΡΠ°ΠΏΠΈΠ½Π° ΠΈΠ»ΠΈ Π΄ΡΡΠ³ΠΈΠ΅ ΠΏΠΎΡΠ»Π΅Π΄ΡΡΠ²ΠΈΡ ΠΠ’Π, ΡΠΎΒ ΡΠΈΠ½ΠΊΠΎΠ²ΠΎΠ΅ ΠΏΠΎΠΊΡΡΡΠΈΠ΅ Π±ΡΠ΄Π΅Ρ Π·Π°ΡΠΈΡΠ°ΡΡ ΠΌΠ΅ΡΠ°Π»Π» ΠΎΡΒ ΠΊΠΎΡΡΠΎΠ·ΠΈΠΈ Π»ΠΈΡΡ Π΄ΠΎΒ ΠΏΠΎΡΡ Π΄ΠΎΒ Π²ΡΠ΅ΠΌΠ΅Π½ΠΈ.
ΠΡΠ΄Π° ΡΡ ΠΎΠ΄ΠΈΡ ΡΠΈΠ½ΠΊ?
Π‘ΠΊΠΎΡΠΎΡΡΡ ΠΊΠΎΡΡΠΎΠ·ΠΈΠΈ ΡΠΈΠ½ΠΊΠΎΠ²ΠΎΠ³ΠΎ ΠΏΠΎΠΊΡΡΡΠΈΡ Π²Β ΡΡΠ»ΠΎΠ²ΠΈΡΡ Π°ΡΠΌΠΎΡΡΠ΅ΡΡ ΡΠΎΡΡΠ°Π²Π»ΡΠ΅Ρ ΠΎΠΊΠΎΠ»ΠΎ 3 ΠΌΠΊΠΌ Π²Β Π³ΠΎΠ΄. ΠΒ ΡΠ΅Π»ΡΡΠΊΠΎΠΉ ΠΌΠ΅ΡΡΠ½ΠΎΡΡΠΈΒ β ΡΠ°ΠΌ, Π³Π΄Π΅ Π½Π°Β Π΄ΠΎΡΠΎΠ³Π°Ρ Π½Π΅Ρ Π°Π³ΡΠ΅ΡΡΠΈΠ²Π½ΠΎΠΉ Ρ ΠΈΠΌΠΈΠΈ, ΡΠΎΠ»ΠΈ ΠΈΒ ΡΠ΅Π°Π³Π΅Π½ΡΠΎΠ²,Β β ΡΠΈΠ½ΠΊΠΎΠ²ΡΠΉ ΡΠ»ΠΎΠΉ Π΄Π΅ΡΠΆΠΈΡΡΡ Π΄ΠΎΠ»ΡΡΠ΅, ΠΈΒ ΡΠ°Π·ΡΡΡΠ°Π΅ΡΡΡ ΠΏΡΠΈΠΌΠ΅ΡΠ½ΠΎ ΡΠΎΒ ΡΠΊΠΎΡΠΎΡΡΡΡ 1β2 ΠΌΠΊΠΌ Π²Β Π³ΠΎΠ΄. ΠΒ Π±ΠΎΠ»ΡΡΠΈΡ Π³ΠΎΡΠΎΠ΄Π°Ρ ΠΈΒ Π°Π³ΡΠ΅ΡΡΠΈΠ²Π½ΡΡ ΡΡΠ΅Π΄Π°Ρ , Π½Π°ΠΏΡΠΎΡΠΈΠ², ΡΠΊΠΎΡΠΎΡΡΡ ΠΊΠΎΡΡΠΎΠ·ΠΈΠΈ Π²ΡΡΠ΅Β β ΠΎΡΒ 3 Π΄ΠΎΒ 7 ΠΌΠΊΠΌ Π²Β Π³ΠΎΠ΄.
ΠΠ½ΠΎΠ³ΠΈΠ΅ Π΄ΡΠΌΠ°ΡΡ, ΡΡΠΎ ΡΠΈΠ½ΠΊ Π½Π΅Β ΡΠΆΠ°Π²Π΅Π΅Ρ, Π½ΠΎΒ ΡΡΠΎ Π½Π΅Β ΡΠ°ΠΊ: ΠΊΠΎΡΡΠΎΠ·ΠΈΡ ΡΡΠ΅Π΄Π°Π΅Ρ ΡΠΈΠ½ΠΊΠΎΠ²ΠΎΠ΅ ΠΏΠΎΠΊΡΡΡΠΈΠ΅. ΠΡΠ΅Π»Π΅ΡΡΡ ΡΠΈΠ½ΠΊΠΎΠ²ΠΎΠ³ΠΎ ΠΏΠΎΠΊΡΡΡΠΈΡ Π²Β ΡΠΎΠΌ, ΡΡΠΎ ΠΏΠΎΠΊΠ° Π΅ΡΡΡ Ρ ΠΎΡΡ Π½Π΅ΠΌΠ½ΠΎΠ³ΠΎ ΡΠΈΠ½ΠΊΠ°, ΠΌΠ΅ΡΠ°Π»Π» ΡΠΆΠ°Π²Π΅ΡΡ Π½Π΅Β Π±ΡΠ΄Π΅Ρ. ΠΠΎΠ²ΠΎΡΡ ΠΏΡΠΎΡΡΡΠΌ ΡΠ·ΡΠΊΠΎΠΌ, ΡΠΈΠ½ΠΊ ΠΏΡΠΎΡΡΠΎ Π΄Π°ΡΡ Π²Π°ΠΌ Π²ΡΠ΅ΠΌΡ Π½Π°Β ΠΏΠΎΠ΄ΠΊΡΠ°ΡΠΊΡ ΠΈΒ ΡΠ΅ΠΌΠΎΠ½Ρ. ΠΡΠ»ΠΈ ΡΒ Π²Π°Ρ ΠΎΡΡΠ»ΠΎΠΈΠ»Π°ΡΡ ΠΊΡΠ°ΡΠΊΠ°, ΠΏΠΎΡΠ²ΠΈΠ»ΡΡ ΡΠΊΠΎΠ» ΠΈΠ»ΠΈ ΡΠ°ΡΠ°ΠΏΠΈΠ½Π°, ΠΎΠ½Π° ΠΌΠΎΠΆΠ΅Ρ Π½Π΅Β ΡΠΆΠ°Π²Π΅ΡΡ Π½Π΅ΡΠΊΠΎΠ»ΡΠΊΠΎ ΠΌΠ΅ΡΡΡΠ΅Π² ΠΈΠ»ΠΈ Π΄Π°ΠΆΠ΅ Π»Π΅Ρ. ΠΠΎΒ ΠΏΠΎΡΠΎΠΌ ΠΎΠ±ΡΠ·Π°ΡΠ΅Π»ΡΠ½ΠΎ Π·Π°ΡΠ²Π΅ΡΠ΅Ρ, ΡΠ°ΠΊ ΡΡΠΎ ΡΒ ΠΏΠΎΠΊΡΠ°ΡΠΊΠΎΠΉ Π²ΡΡ-ΡΠ°ΠΊΠΈ Π»ΡΡΡΠ΅ Π½Π΅Β ΡΡΠ½ΡΡΡ, ΠΏΠΎΡΠΎΠΌΡ ΡΡΠΎ ΡΠ΅Π΄ΠΊΠΎ ΠΌΠΎΠΆΠ½ΠΎ Π·Π½Π°ΡΡ Π½Π°Π²Π΅ΡΠ½ΡΠΊΠ°, ΠΊΠ°ΠΊ ΠΈΠΌΠ΅Π½Π½ΠΎ ΠΎΡΠΈΠ½ΠΊΠΎΠ²Π°Π½ ΠΊΡΠ·ΠΎΠ².
ΠΠΎΠΊΠ°Π·Π°ΡΡ ΠΈΠ»ΠΈ ΠΎΠΏΡΠΎΠ²Π΅ΡΠ³Π½ΡΡΡ Π½Π°Π»ΠΈΡΠΈΠ΅ ΠΎΡΠΈΠ½ΠΊΠΎΠ²ΠΊΠΈ ΠΌΠΎΠΆΠ½ΠΎ ΡΠΎΠ»ΡΠΊΠΎ ΡΠΊΡΠΏΠ΅ΡΠΈΠΌΠ΅Π½ΡΠ°Π»ΡΠ½ΡΠΌ ΠΏΡΡΠ΅ΠΌ ΠΈΠ»ΠΈ ΡΒ ΠΏΠΎΠΌΠΎΡΡΡ Π΄ΠΎΡΠΎΠ³ΠΎΡΡΠΎΡΡΠΈΡ Π»Π°Π±ΠΎΡΠ°ΡΠΎΡΠ½ΡΡ ΠΈΡΡΠ»Π΅Π΄ΠΎΠ²Π°Π½ΠΈΠΉ. ΠΡΠΎΠΈΠ·Π²ΠΎΠ΄ΠΈΡΠ΅Π»ΠΈ ΠΎΡΠ΅Π½Ρ ΡΠ΅Π΄ΠΊΠΎ ΠΎΡΠΊΡΡΠ²Π°ΡΡ ΡΡΡ ΠΈΠ½ΡΠΎΡΠΌΠ°ΡΠΈΡ. ΠΠ°ΠΊ ΠΏΡΠ°Π²ΠΈΠ»ΠΎ, ΠΎΠ½ΠΈ ΠΎΠ³ΡΠ°Π½ΠΈΡΠΈΠ²Π°ΡΡΡΡ ΠΎΠ±ΡΠΈΠΌΠΈ ΡΡΠ°Π·Π°ΠΌΠΈ ΠΎΒ ΡΠΎΠΌ, ΡΡΠΎ ΠΊΡΠ·ΠΎΠ² ΠΎΡΠΈΠ½ΠΊΠΎΠ²Π°Π½. Π, ΠΊΠ°ΠΊ ΠΎΡΠΈΠ½ΠΊΠΎΠ²Π°Π½, Π½Π΅Β Π³ΠΎΠ²ΠΎΡΡΡ.
ΠΒ Π²Π΅Π΄Ρ Π±ΡΠ²Π°Π΅Ρ ΠΎΠ΄Π½ΠΎΡΡΠΎΡΠΎΠ½Π½ΡΡ ΠΈΠ»ΠΈ Π΄Π²ΡΡ ΡΡΠΎΡΠΎΠ½Π½ΡΡ ΠΎΡΠΈΠ½ΠΊΠΎΠ²ΠΊΠ°. ΠΠ½ΠΎΠ³Π΄Π° ΡΠΈΠ½ΠΊΡΡΡ ΡΠΎΠ»ΡΠΊΠΎ Π½Π΅ΠΊΠΎΡΠΎΡΡΠ΅ Π²Π½Π΅ΡΠ½ΠΈΠ΅ ΠΏΠ°Π½Π΅Π»ΠΈ ΠΊΡΠ·ΠΎΠ²Π°, Π°Β Π²Π½ΡΡΡΠΈ ΡΠΈΠ½ΠΊΠ° Π½Π΅Ρ. Π§Π°ΡΡΠΎ ΡΒ Π±ΡΠ΄ΠΆΠ΅ΡΠ½ΠΈΠΊΠΎΠ² ΡΠΈΠ½ΠΊΡΡΡΡΡ ΡΠΎΠ»ΡΠΊΠΎ ΡΠ°ΠΌΡΠ΅ ΡΡΠ·Π²ΠΈΠΌΡΠ΅ ΠΌΠ΅ΡΡΠ°. ΠΠ΅ΡΠ΅Π΄ΠΊΠΎ ΠΏΡΠΈ ΠΎΠ±ΡΠ΅ΠΉ ΠΎΡΠΈΠ½ΠΊΠΎΠ²ΠΊΠ΅ ΠΊΡΡΡΠ° ΠΎΡΡΠ°Π΅ΡΡΡ Π½Π΅Β ΠΎΡΠΈΠ½ΠΊΠΎΠ²Π°Π½Π½ΠΎΠΉ.
ΠΠΎΡΠΎΠΉ ΠΌΠ°ΡΠΈΠ½Ρ ΡΠ»ΠΈΡΠΊΠΎΠΌ Π°ΠΊΡΠΈΠ²Π½ΠΎ ΡΠ»ΠΈΡΡΡΡ Π½Π°Β ΠΏΡΠΎΠΈΠ·Π²ΠΎΠ΄ΡΡΠ²Π΅ ΠΈΒ ΡΠΈΠ½ΠΊΠΎΠ²ΡΠΉ ΡΠ»ΠΎΠΉ ΡΡΠΈΡΠ°Π΅ΡΡΡ. ΠΠ½ΠΎΠ³Π΄Π° ΡΠΈΠ½ΠΊΠ° Π½Π΅Ρ Π½Π°Β ΡΠ²Π°ΡΠ½ΡΡ ΡΠ²Π°Ρ . ΠΡΠ°Π½ΡΠΎΠ² ΠΎΡΠ΅Π½Ρ ΠΌΠ½ΠΎΠ³ΠΎ. ΠΡΠΎΠΈΠ·Π²ΠΎΠ΄ΠΈΡΠ΅Π»Ρ Π²ΡΠ΅Π³Π΄Π° ΠΏΡΡΠ°Π΅ΡΡΡ ΡΡΠΊΠΎΠ½ΠΎΠΌΠΈΡΡ, ΡΡΠΎΠ±Ρ ΠΊΠΎΠ½Π΅ΡΠ½Π°Ρ ΡΠ΅Π½Π° Π½Π°Β Π°Π²ΡΠΎΠΌΠΎΠ±ΠΈΠ»Ρ Π±ΡΠ»Π° ΠΌΠ°ΠΊΡΠΈΠΌΠ°Π»ΡΠ½ΠΎ ΠΏΡΠΈΠ²Π»Π΅ΠΊΠ°ΡΠ΅Π»ΡΠ½ΠΎΠΉΒ β ΡΡΠΎ Π½Π°Π΄ΠΎ ΠΏΠΎΠ½ΠΈΠΌΠ°ΡΡ.
ΠΡΠ»ΠΈ ΡΠ΅ΡΡ ΠΈΠ΄Π΅Ρ ΠΎΒ ΠΏΠΎΠΊΡΠΏΠΊΠ΅ ΠΏΠΎΠ΄Π΅ΡΠΆΠ°Π½Π½ΠΎΠΉ ΠΌΠ°ΡΠΈΠ½Ρ, ΡΠΎΒ ΡΠΏΠΎΠ²Π°ΡΡ Π½Π°Β ΠΎΡΠΈΠ½ΠΊΠΎΠ²ΠΊΡ Π½Π΅Β ΡΡΠΎΠΈΡ ΡΠ΅ΠΌ Π±ΠΎΠ»Π΅Π΅. ΠΡΠ»ΠΈ ΠΌΠ°ΡΠΈΠ½Π° Π±ΡΠ»Π° Π²Β Π°Π²Π°ΡΠΈΡΡ , ΡΠΎΒ ΡΠ°ΡΡΠΎ ΡΠ°ΠΌΠΈΒ ΠΆΠ΅ Π²Π»Π°Π΄Π΅Π»ΡΡΡ ΡΠΊΠΎΠ½ΠΎΠΌΡΡ ΠΈΒ ΠΏΠΎΠΊΡΠΏΠ°ΡΡ Π΄Π΅ΡΠ΅Π²ΡΠ΅ Π·Π°ΠΏΡΠ°ΡΡΠΈ ΠΈΠ·Β Π΄Π΅ΡΠ΅Π²ΠΎΠ³ΠΎ ΠΌΠ΅ΡΠ°Π»Π»Π° Π±Π΅Π· Π²ΡΡΠΊΠΎΠΉ ΠΎΡΠΈΠ½ΠΊΠΎΠ²ΠΊΠΈ.
ΠΡΠΎΠ±Π»Π΅ΠΌΠ½ΡΠΉ Π°Π»ΡΠΌΠΈΠ½ΠΈΠΉ
Π§ΡΠΎ ΠΊΠ°ΡΠ°Π΅ΡΡΡ Π°Π»ΡΠΌΠΈΠ½ΠΈΠ΅Π²ΡΡ ΠΌΠ°ΡΠΈΠ½, ΡΒ Π½ΠΈΠΌΠΈ Π²ΡΡ Π΅ΡΡ ΡΠ»ΠΎΠΆΠ½Π΅Π΅. ΠΠ½ΠΈ Π½Π΅Β ΡΠΆΠ°Π²Π΅ΡΡ ΠΏΡΠΈΠ²ΡΡΠ½ΡΠΌ ΡΡΠΆΠΈΠΌ ΡΠ²Π΅ΡΠΎΠΌ. ΠΠ½ΠΈ ΠΏΠΎΠ΄Π²Π΅ΡΠΆΠ΅Π½Ρ ΡΠ»Π΅ΠΊΡΡΠΎΡ ΠΈΠΌΠΈΡΠ΅ΡΠΊΠΎΠΉ ΠΊΠΎΡΡΠΎΠ·ΠΈΠΈ. ΠΠ½Π° Π²ΠΎΠ·Π½ΠΈΠΊΠ°Π΅Ρ Π²Β ΠΌΠ΅ΡΡΠ°Ρ ΠΊΠΎΠ½ΡΠ°ΠΊΡΠ° ΡΠ°Π·Π½ΡΡ ΠΌΠ΅ΡΠ°Π»Π»ΠΎΠ². ΠΠ°ΠΏΡΠΈΠΌΠ΅Ρ, Π°Π»ΡΠΌΠΈΠ½ΠΈΡ ΠΈΒ ΡΡΠ°Π»ΠΈ.
ΠΠΎΠ»Π½ΠΎΡΡΡΡ Π°Π»ΡΠΌΠΈΠ½ΠΈΠ΅Π²ΡΠ΅ Π°Π²ΡΠΎΠΌΠΎΠ±ΠΈΠ»ΠΈΒ β Π²ΡΡ Π΅ΡΡ ΡΠ΅Π΄ΠΊΠΎΡΡΡ. Π§Π°ΡΡΠΎ ΠΈΡΠΏΠΎΠ»ΡΠ·ΡΡΡΡΡ Π°Π»ΡΠΌΠΈΠ½ΠΈΠ΅Π²ΡΠ΅ ΠΏΠ°Π½Π΅Π»ΠΈ, Π°Β ΠΊΠ°ΡΠΊΠ°Ρ ΡΡΠ°Π»ΡΠ½ΠΎΠΉ. ΠΠ»ΠΈ Π°Π»ΡΠΌΠΈΠ½ΠΈΠ΅Π²ΡΠ΅ ΡΠΎΠ»ΡΠΊΠΎ ΠΊΠ°ΠΏΠΎΡ, ΠΊΡΡΠ»ΡΡ, ΠΊΡΡΡΠ° ΠΈΒ ΡΠ°ΠΊ Π΄Π°Π»Π΅Π΅. ΠΠΎΡ Π²Β ΡΡΠΈΡ ΠΌΠ΅ΡΡΠ°Ρ ΠΊΡΠ·ΠΎΠ² Π±ΡΠ΄Π΅Ρ ΡΠ°Π·ΡΡΡΠ°ΡΡΡΡ ΠΈΒ ΡΡΠΏΠ°ΡΡΡΡ Π²Β ΠΏΠ΅ΡΠ²ΡΡ ΠΎΡΠ΅ΡΠ΅Π΄Ρ. ΠΠ΅Π· ΡΡΠΆΠ΅Π³ΠΎ ΡΠ²Π΅ΡΠ°Β β Π²Π΅Π΄Ρ ΠΊΠΎΡΡΠΎΠ·ΠΈΡ Π°Π»ΡΠΌΠΈΠ½ΠΈΡ ΠΏΠΎΡ ΠΎΠΆΠ° Π½Π°Β ΠΌΠ΅ΡΠ°Π»Π»ΠΈΡΠ΅ΡΠΊΡΡ ΠΏΠ΅ΡΡ ΠΎΡΡ.
ΠΠ°Β ΠΊΠΎΠ»Π΅ΡΠ°Ρ : ΠΠ°ΠΊ ΠΆΠΈΠ»ΠΎΡΡ Π΄Π°Π»ΡΠ½ΠΎΠ±ΠΎΠΉΡΠΈΠΊΠ°ΠΌ Π²Β Π‘Π‘Π‘Π
ΠΠ±Π·ΠΎΡ ΡΡΠ½ΠΊΠ°: 5 Π΄ΠΎΡΠΎΠ³ΠΈΡ ΠΎΠΏΡΠΈΠΉ, Π·Π°Β ΠΊΠΎΡΠΎΡΡΠ΅ ΡΠΎΡΠ½ΠΎ Π½Π΅Β ΡΡΠΎΠΈΡ ΠΏΠ΅ΡΠ΅ΠΏΠ»Π°ΡΠΈΠ²Π°ΡΡ
ΠΠ²ΡΠΎ Ρ Π°Π»ΡΠΌΠΈΠ½ΠΈΠ΅Π²ΡΠΌ ΠΊΡΠ·ΠΎΠ²ΠΎΠΌ ΡΠΏΠΈΡΠΎΠΊ
E551MM βΊ ΠΠ»ΠΎΠ³ βΊ ΠΡΠΈΠ½ΠΊΠΎΠ²Π°Π½Π½ΡΠΉ ΠΊΡΠ·ΠΎΠ². ΠΠ»ΡΠΌΠΈΠ½ΠΈΠ΅Π²ΡΠΉ ΠΊΡΠ·ΠΎΠ². ΠΠ°ΠΊΠΎΠΉ ΡΠ³ΠΎΠ΄Π½ΠΎ ΡΠΈΠΏΠ° «Π½Π΅ΡΠΆΠ°Π²Π΅ΡΡΠΈΠΉ» ΠΊΡΠ·ΠΎΠ².
ΠΠΎ ΠΏΠ΅ΡΠ²ΡΡ β¦<ΠΌΠ°ΡΠ΅ΡΠ½ΠΎΠ΅ ΡΠ»ΠΎΠ²ΠΎ> ΠΊΡΠΎ Π²Π°ΠΌ ΡΠΊΠ°Π·Π°Π», ΡΡΠΎ ΡΠΈΠ½ΠΊ <ΠΌΠ°ΡΠ΅ΡΠ½ΠΎΠ΅ ΡΠ»ΠΎΠ²ΠΎ> Π½Π΅ ΡΠΆΠ°Π²Π΅Π΅Ρ ?
ΠΠ΅ΡΠ½Π΅Π΅ Π½Π΅Ρβ¦ Π²ΠΎ ΠΏΠ΅ΡΠ²ΡΡ , ΡΡΠΎ ΡΠ°ΠΊΠΎΠ΅ ΡΠΆΠ°Π²Π΅Π½ΠΈΠ΅ / ΠΊΠΎΡΡΠΎΠ·ΠΈΡ ΠΌΠ΅ΡΠ°Π»Π»Π°? ΠΡΠΎ ΠΏΡΠΎΡΠ΅ΡΡ ΠΎΠ±ΡΠ°Π·ΠΎΠ²Π°Π½ΠΈΡ ΠΎΠΊΡΠΈΠ΄Π° ΠΌΠ΅ΡΠ°Π»Π»Π° ΠΈΠ· ΡΠΈΡΡΠΎΠ³ΠΎ ΠΌΠ΅ΡΠ°Π»Π»Π°.
ΠΠΎΡΡΠΎΠ·ΠΈΡ ΡΠΈΠ½ΠΊΠ° ΠΌΠΎΠΆΠ΅Ρ ΠΏΡΠΎΡ ΠΎΠ΄ΠΈΡΡ ΠΊΠ°ΠΊ Ρ Π²ΠΎΠ΄ΠΎΡΠΎΠ΄Π½ΠΎΠΉ, ΡΠ°ΠΊ ΠΈ ΠΊΠΈΡΠ»ΠΎΡΠΎΠ΄Π½ΠΎΠΉ Π΄Π΅ΠΏΠΎΠ»ΡΡΠΈΠ·Π°ΡΠΈΠ΅ΠΉ.
ΠΠΎΡΡΠΎΠ·ΠΈΡ ΡΠΈΠ½ΠΊΠ° Π² Π²ΠΎΠ΄Π΅ Π½Π°Π±Π»ΡΠ΄Π°Π΅ΡΡΡ ΠΏΡΠΈ ΡΠ΅ΠΌΠΏΠ΅ΡΠ°ΡΡΡΠ΅ Π²ΡΡΠ΅ 55 Β°C. Π‘ ΠΏΠΎΠ²ΡΡΠ΅Π½ΠΈΠ΅ΠΌ ΡΠ΅ΠΌΠΏΠ΅ΡΠ°ΡΡΡΡ ΡΠΊΠΎΡΠΎΡΡΡ ΠΊΠΎΡΡΠΎΠ·ΠΈΠΈ ΡΠ²Π΅Π»ΠΈΡΠΈΠ²Π°Π΅ΡΡΡ, ΠΌΠ°ΠΊΡΠΈΠΌΡΠΌ Π½Π°Π±Π»ΡΠ΄Π°Π΅ΡΡΡ ΠΏΡΠΈ ΡΠ΅ΠΌΠΏΠ΅ΡΠ°ΡΡΡΠ΅ 70 Β°C. ΠΠΎΡΠ»Π΅ ΡΡΠΎΠ³ΠΎ ΡΠ°Π·ΡΡΡΠ΅Π½ΠΈΠ΅ ΠΌΠ΅ΡΠ°Π»Π»Π° ΠΏΡΠΎΡ ΠΎΠ΄ΠΈΡ ΠΎΡΠ΅Π½Ρ ΠΌΠ΅Π΄Π»Π΅Π½Π½ΠΎ. ΠΡΠΎ ΡΠ²ΡΠ·Π°Π½ΠΎ Ρ ΠΎΠ±ΡΠ°Π·ΠΎΠ²Π°Π½ΠΈΠ΅ΠΌ Π² Π²ΠΎΠ΄Π΅ Π½Π° ΠΏΠΎΠ²Π΅ΡΡ Π½ΠΎΡΡΠΈ ΡΠΈΠ½ΠΊΠ° ΠΏΡΠΎΠ΄ΡΠΊΡΠΎΠ² ΠΊΠΎΡΡΠΎΠ·ΠΈΠΈ. ΠΡΠΈ ΡΠ΅ΠΌΠΏΠ΅ΡΠ°ΡΡΡΠ°Ρ Π΄ΠΎ 55 Β°C ΠΈ Π²ΡΡΠ΅ 90 β 95 Β°C ΠΏΡΠΎΠ΄ΡΠΊΡΡ ΠΊΠΎΡΡΠΎΠ·ΠΈΠΈ ΠΎΠ±Π»Π°Π΄Π°ΡΡ Π΄ΠΎΡΡΠ°ΡΠΎΡΠ½ΠΎ Π²ΡΡΠΎΠΊΠΈΠΌΠΈ Π·Π°ΡΠΈΡΠ½ΡΠΌΠΈ ΡΠ²ΠΎΠΉΡΡΠ²Π°ΠΌΠΈ, ΠΎΠ±ΡΠ°Π·ΡΡ Π½Π° ΠΏΠΎΠ²Π΅ΡΡ Π½ΠΎΡΡΠΈ ΠΏΠ»ΠΎΡΠ½ΡΡ ΡΠΏΠ»ΠΎΡΠ½ΡΡ ΠΏΠ»Π΅Π½ΠΊΡ. ΠΠ°ΠΊΡΠΈΠΌΠ°Π»ΡΠ½Π°Ρ ΡΠΊΠΎΡΠΎΡΡΡ ΠΊΠΎΡΡΠΎΠ·ΠΈΠΈ ΡΠΈΠ½ΠΊΠ° ΠΎΠ±ΡΡΡΠ½ΡΠ΅ΡΡΡ ΠΎΠ±ΡΠ°Π·ΠΎΠ²Π°Π½ΠΈΠ΅ΠΌ ΡΡΡ Π»ΠΎΠΉ ΠΏΠ»Π΅Π½ΠΊΠΈ, ΡΠΎΡΡΠΎΡΡΠ΅ΠΉ Ρ Zn(OH)2, ΠΊΠΎΡΠΎΡΠ°Ρ Π½Π΅ ΠΈΠΌΠ΅Π΅Ρ Ρ ΠΎΡΠΎΡΠΈΡ Π·Π°ΡΠΈΡΠ½ΡΡ ΡΠ²ΠΎΠΉΡΡΠ², Ρ.ΠΊ. Π»Π΅Π³ΠΊΠΎ ΠΎΡΡΠ»Π°ΠΈΠ²Π°Π΅ΡΡΡ.
Π Π½Π΅ΠΉΡΡΠ°Π»ΡΠ½ΡΡ ΡΠ°ΡΡΠ²ΠΎΡΠ°Ρ ΠΊΠΎΡΡΠΎΠ·ΠΈΡ ΡΠΈΠ½ΠΊΠ° ΠΏΡΠΎΡ ΠΎΠ΄ΠΈΡ Ρ ΠΊΠΈΡΠ»ΠΎΡΠΎΠ΄Π½ΠΎΠΉ Π΄Π΅ΠΏΠΎΠ»ΡΡΠΈΠ·Π°ΡΠΈΠ΅ΠΉ.
ΠΡΠΈ ΠΊΠΎΠ½ΡΠ°ΠΊΡΠ΅ ΡΠΈΠ½ΠΊΠ° Ρ ΠΌΠ΅ΡΠ°Π»Π»ΠΎΠΌ, ΠΈΠΌΠ΅ΡΡΠΈΠΌ Π±ΠΎΠ»Π΅Π΅ ΡΠ»Π΅ΠΊΡΡΠΎΠΏΠΎΠ»ΠΎΠΆΠΈΡΠ΅Π»ΡΠ½ΡΠΉ ΠΏΠΎΡΠ΅Π½ΡΠΈΠ°Π», ΡΠΊΠΎΡΠΎΡΡΡ ΠΊΠΎΡΡΠΎΠ·ΠΈΠΈ ΡΠΈΠ½ΠΊΠ° Π·Π½Π°ΡΠΈΡΠ΅Π»ΡΠ½ΠΎ Π²ΠΎΠ·ΡΠ°ΡΡΠ°Π΅Ρ. (ΠΠ΅Π»Π΅Π·ΠΎ Π±ΠΎΠ»Π΅Π΅ ΡΠ»Π΅ΠΊΡΡΠΎΠΏΠΎΠ»ΠΎΠΆΠΈΡΠ΅Π»ΡΠ½ΡΠΉ ΠΌΠ΅ΡΠ°Π»Π».)
Π₯ΠΎΡΡ ΡΠΈΠ½ΠΊ ΠΈ ΡΠ²Π»ΡΠ΅ΡΡΡ Π΄ΠΎΡΡΠ°ΡΠΎΡΠ½ΠΎ ΠΊΠΎΡΡΠΎΠ·ΠΈΠΎΠ½Π½ΠΎΡΡΠΎΠΉΠΊΠΈΠΌ ΠΌΠ΅ΡΠ°Π»Π»ΠΎΠΌ β ΠΎΠ½ Π½Π΅ Π½Π°ΡΠ΅Π» ΠΏΡΠΈΠΌΠ΅Π½Π΅Π½ΠΈΡ Π² ΠΏΠΈΡΠ΅Π²ΠΎΠΉ ΠΏΡΠΎΠΌΡΡΠ»Π΅Π½Π½ΠΎΡΡΠΈ, Ρ.ΠΊ. ΠΏΡΠΈ ΠΊΠΎΠ½ΡΠ°ΠΊΡΠ΅ Ρ ΠΊΠΈΡΠ»ΡΠΌΠΈ ΠΏΠΈΡΠ΅Π²ΡΠΌΠΈ ΠΏΡΠΎΠ΄ΡΠΊΡΠ°ΠΌΠΈ ΠΎΠ±ΡΠ°Π·ΡΠ΅Ρ ΡΠΎΠΊΡΠΈΡΠ½ΡΠ΅ ΡΠΎΠ»ΠΈ. (Ρ.Π΅. ΠΎΠΏΡΡΡ ΠΆΠ΅ ΠΎΡΠΈΠ³Π΅Π½Π½ΠΎ ΡΠΆΠ°Π²Π΅Π΅Ρ! Π§ΡΠΎ Π½Π΅ ΠΌΠ΅ΡΠ°Π΅Ρ ΠΊΠΈΡΠ°ΠΉΡΠ°ΠΌ ΠΈ Π²ΡΠ΅ΡΠ½Π°ΠΌΡΠ°ΠΌ Π·Π°ΡΠΎΠ²ΡΠ²Π°ΡΡ Π°Π½Π°Π½Π°ΡΡ Π² Π±Π°Π½ΠΊΠΈ Ρ ΠΎΡΠΈΠ½ΠΊΠΎΠ²ΠΊΠΎΠΉ ΠΈΠ·Π½ΡΡΡΠΈ)
ΠΠ°ΡΡΠ±ΠΈΡΠ΅ ΡΠ΅Π±Π΅ Π½Π° Π½ΠΎΡΡβ¦ ΠΠ Π ΠΠΠΠ«Π ΠΌΠ΅ΡΠ°Π»Π» Π²ΡΠ³Π»ΡΠ΄ΠΈΡ Π²ΠΎΡ ΡΠ°ΠΊ:
ΠΠΎΠ»Π½ΡΠΉ ΡΠ°Π·ΠΌΠ΅Ρ
Π£ ΠΌΠ΅ΡΠ°Π»Π»Π° Π΅ΡΡΡ ΠΌΠ΅ΡΠ°Π»Π»ΠΈΡΠ΅ΡΠΊΠΈΠΉ ΠΠΠΠ‘Π!
ΠΠ½ ΠΎΡΡΠ°ΠΆΠ°Π΅Ρ ΡΠ²Π΅Ρ! ΠΡΠΏΠΎΠΌΠ½ΠΈΡΠ΅ Π·Π΅ΡΠΊΠ°Π»ΠΎ! ΠΡΠΎ ΡΠ»ΠΎΠΉ ΡΠΈΡΡΠΎΠ³ΠΎ ΡΠ΅ΡΠ΅Π±ΡΠ°!
ΠΠΎΠ»ΠΎΡΡΡ ΠΌΠΎΠ½Π΅ΡΡ Π²ΠΈΠ΄Π΅Π»ΠΈ? ΠΠ½Π° ΠΊΠ°ΠΊΠ°Ρ? Π£ΠΊΡΠ°ΡΠ΅Π½ΠΈΡ Ρ ΠΆΠ΅Π½Ρ ΠΊΠ°ΠΊΠΈΠ΅ ?
Π§ΡΠΎ Π½Π΅ Π±Π»Π΅ΡΡΠΈΡ β ΡΠΎ Π½Π΅ ΠΌΠ΅ΡΠ°Π»Π»! (ΠΎΠ±ΡΠ°ΡΠ½ΠΎΠ΅ β Π½Π΅ Π²Π΅ΡΠ½ΠΎ. ΠΠΎ Π΅ΡΠ»ΠΈ ΡΡΠΎ-ΡΠΎ Π½Π΅ ΠΈΠΌΠ΅Π΅Ρ Π±Π»Π΅ΡΠΊΠ° β Π²Ρ ΡΠΌΠΎΡΡΠΈΡΠ΅ Π½Π΅ Π½Π° ΠΌΠ΅ΡΠ°Π»Π», Π° ΡΠΆΠ΅ Π½Π° Π΅Π³ΠΎ ΠΎΠΊΡΠΈΠ΄, ΡΡΠ»ΡΡΠΈΠ΄ ΠΈΡΠ΄. Π½ΠΎ Π½Π΅ Π½Π° ΡΠ°ΠΌ ΠΌΠ΅ΡΠ°Π»Π».)
ΠΠ°Π»Π΅Π΅, ΠΏΡΠΎΡΠΈΡΠΈΡΡΠ΅ΠΌ ΡΠ°ΠΉΡ. Autogener.ru
ΠΠ°Π±Π΅Π³Π°Ρ Π²ΠΏΠ΅ΡΠ΅Π΄ β ΠΎΡ
ΠΎΡΠ΅Π½ΠΎΡΠ½ΡΠ΅ ΡΡΠΆΠ΄Π΅Π½ΠΈΡ Π½Π΅ ΡΠΎΠ²ΡΠ΅ΠΌ Π²Π΅ΡΠ½ΡΠ΅.
1. ΠΠΎΡΡΡΠ°Ρ ΠΎΡΠΈΠ½ΠΊΠΎΠ²ΠΊΠ°
ΠΡΡΡΠΈΠΉ Π²ΠΈΠ΄ ΡΠΈΠ½ΠΊΠΎΠ²Π°Π½ΠΈΡ. ΠΠ°Π½Π½Π°Ρ ΡΠ΅ΡΠΌΠΈΡΠ΅ΡΠΊΠ°Ρ ΡΠ΅Ρ
Π½ΠΎΠ»ΠΎΠ³ΠΈΡ Π½Π°ΠΈΠ±ΠΎΠ»Π΅Π΅ ΡΡΡΠΎΠΉΡΠΈΠ²Π° ΠΊ ΠΊΠΎΡΡΠΎΠ·ΠΈΠΈ Π² ΠΏΡΠΎΡΠ΅ΡΡΠ΅ ΡΠΊΡΠΏΠ»ΡΠ°ΡΠ°ΡΠΈΠΈ ΠΌΠ°ΡΠΈΠ½Ρ Ρ ΡΠ°ΠΊΠΎΠΉ ΠΎΡΠΈΠ½ΠΊΠΎΠ²ΠΊΠΎΠΉ.
ΠΠ°ΡΠ°Π½Π΅Π΅ ΠΏΠΎΠ΄Π³ΠΎΡΠΎΠ²Π»Π΅Π½Π½ΡΠΉ ΠΈ ΡΡΡ
ΠΎΠΉ ΠΊΡΠ·ΠΎΠ² ΠΎΠΏΡΡΠΊΠ°ΡΡ Π² Π²Π°Π½Π½Ρ Ρ ΡΠ°ΡΠΏΠ»Π°Π²ΠΎΠΌ ΡΠΈΠ½ΠΊΠ° ΡΠ΅ΠΌΠΏΠ΅ΡΠ°ΡΡΡΠ° ΠΊΠΎΡΠΎΡΠΎΠ³ΠΎ ΠΎΡ 500 Π΄ΠΎ 4000 Π³ΡΠ°Π΄ΡΡΠΎΠ² Π‘.
ΠΠ°ΡΠ°Π½ΡΠΈΡ ΠΏΡΠΎΠΈΠ·Π²ΠΎΠ΄ΠΈΡΠ΅Π»Ρ Π½Π° ΠΊΡΠ·ΠΎΠ² ΠΌΠ°ΡΠΈΠ½Ρ Ρ ΡΠ°ΠΊΠΈΠΌ Π²ΠΈΠ΄ΠΎΠΌ ΠΎΠ±ΡΠ°Π±ΠΎΡΠΊΠΈ Π½Π°ΡΠΈΠ½Π°Π΅ΡΡΡ ΠΎΡ 15 Π»Π΅Ρ ΠΈ Π²ΡΡΠ΅.
ΠΠ°β¦ Ρ
ΠΎΡΠΎΡΠΈΠΉ ΠΌΠ΅ΡΠΎΠ΄β¦ ΠΌΠΎΠΊΠ½ΡΡΡ ΠΊΡΠ·ΠΎΠ² Π² ΡΠ°ΡΠΏΠ»Π°Π²Π»Π΅Π½Π½ΡΠΉ ΡΠΈΠ½ΠΊ. Π ΠΏΠΎΡΠΎΠΌ Π½Π°ΠΏΠΈΠ»ΡΠ½ΠΈΠΊΠΎΠΌ ΡΠ΄ΠΈΡΠ°ΡΡ Π²ΡΠ΅ ΠΏΠΎΡΡΠΊΠΈ ΠΈ ΠΊΠ°ΠΏΠ»ΠΈ.
Π‘Π»ΠΎΠΉ ΡΠΈΠ½ΠΊΠ° Π²ΡΠΉΠ΄Π΅Ρ ΠΊΠΎΠ½Π΅ΡΠ½ΠΎ Π°Π΄ΡΠΊΠΈΠΉ. ΠΠΎΠΆΠ½ΠΎ Π΄Π΅ΠΉΡΡΠ²ΠΈΡΠ΅Π»ΡΠ½ΠΎ Π½Π΅ ΠΌΠ΅Π½Π΅Π΅ 15 Π»Π΅Ρ Π³Π°ΡΠ°Π½ΡΠΈΡΠΎΠ²Π°ΡΡ.
ΠΠ! Π½ΠΈΠΊΡΠΎ ΡΠ°ΠΊ Π½Π΅ Π΄Π΅Π»Π°Π΅Ρ ΡΠ΅ΠΉΡΠ°Ρ. ΠΡΠΎ Π΄ΠΎΡΠΎΠ³ΠΎ ΠΈ Π½Π΅ ΡΠ΅Ρ
Π½ΠΎΠ»ΠΎΠ³ΠΈΡΠ½ΠΎ. ΠΡΠΎΡΠ΅ ΡΠ΄Π΅Π»Π°ΡΡ ΡΡΠ°Π·Ρ ΠΈ
Π‘ΡΠ°Π»Ρ Π΄ΠΎ ΡΠΈΡ
ΠΏΠΎΡ Π΄ΠΎΠΌΠΈΠ½ΠΈΡΡΠ΅Ρ ΠΏΡΠΈ ΡΠΎΠ·Π΄Π°Π½ΠΈΠΈ ΠΊΡΠ·ΠΎΠ²ΠΎΠ² Π°Π²ΡΠΎΠΌΠΎΠ±ΠΈΠ»Π΅ΠΉ Ρ Π±ΠΎΠ»ΡΡΠΈΠ½ΡΡΠ²Π° Π°Π²ΡΠΎΠΌΠΎΠ±ΠΈΠ»ΡΠ½ΡΡ
ΠΊΠΎΠ½ΡΠ΅ΡΠ½ΠΎΠ². Π ΡΠΎ ΠΆΠ΅ Π²ΡΠ΅ΠΌΡ, ΠΌΠ΅Π΄Π»Π΅Π½Π½ΠΎ, Π½ΠΎ ΡΠ²Π΅ΡΠ΅Π½Π½ΠΎ ΡΠΊΠ»Π°Π΄ΡΠ²Π°Π²ΡΠΈΠ΅ΡΡ Π΄Π΅ΡΡΡΠΈΠ»Π΅ΡΠΈΡΠΌΠΈ ΠΊΠΎΠ½ΡΠ΅ΡΠ²Π°ΡΠΈΠ²Π½ΡΠ΅ ΡΡΡΠΎΠΈ ΡΠ°Π·ΡΡΡΠ°Π΅Ρ Π°Π»ΡΠΌΠΈΠ½ΠΈΠΉ. Π’ΠΎΡΠ½Π΅Π΅ Π΅Π³ΠΎ ΡΠΏΠ»Π°Π²Ρ.
ΠΠ΅ΡΠ²ΡΠΌ ΡΠ΅Π²ΠΎΠ»ΡΡΠΈΠΎΠ½Π½ΡΠΉ ΡΠ°Π³ ΡΠ΄Π΅Π»Π°Π» Π°Π²ΡΠΎΠΌΠΎΠ±ΠΈΠ»ΡΠ½ΡΠΉ ΠΊΠΎΠ½ΡΠ΅ΡΠ½ Β«ΠΡΠ΄ΠΈΒ». ΠΠ°ΠΊ ΠΈΠ·Π²Π΅ΡΡΠ½ΠΎ, Π°Π΄ΠΌΠΈΠ½ΠΈΡΡΡΠ°ΡΠΈΡ ΡΡΠΎΠΉ ΠΊΠΎΠΌΠΏΠ°Π½ΠΈΠΈ ΠΈΠΌΠ΅Π΅Ρ ΠΎΠΏΡΠ΅Π΄Π΅Π»Π΅Π½Π½ΡΠΉ Π±Π·ΠΈΠΊ Π² ΠΎΡΠ½ΠΎΡΠ΅Π½ΠΈΠΈ Π±Π΅Π·ΠΎΠΏΠ°ΡΠ½ΠΎΡΡΠΈ.
ΠΠΌΠ΅Π½Π½ΠΎ ΡΡΠΎΡ ΡΠ°ΠΊΡΠΎΡ ΠΈ ΠΎΠ±ΡΡΠ»ΠΎΠ²ΠΈΠ» ΠΏΡΠΈΠΌΠ΅Π½Π΅Π½ΠΈΠ΅ Π°Π»ΡΠΌΠΈΠ½ΠΈΠ΅Π²ΡΡ
ΡΠΏΠ»Π°Π²ΠΎΠ² ΠΊΠΎΠ³Π΄Π° ΡΠ°Π·ΡΠ°Π±Π°ΡΡΠ²Π°Π»ΡΡ ΡΠ°ΠΊΠΎΠΉ ΠΊΡΠ·ΠΎΠ² Π°Π²ΡΠΎΠΌΠΎΠ±ΠΈΠ»Ρ. Π Π°Π·ΡΠΌΠ΅Π΅ΡΡΡ, ΡΡΠ°Π·Ρ Π½ΡΠΆΠ½ΠΎ ΡΠΏΠΎΠΌΡΠ½ΡΡΡ ΠΎ Π³Π»Π°Π²Π½ΠΎΠΌ ΠΌΠΈΠ½ΡΡΠ΅ ΠΊΡΠ·ΠΎΠ²Π½ΠΎΠΉ ΠΊΠΎΠ½ΡΡΡΡΠΊΡΠΈΠΈ ΠΈΠ· Π°Π»ΡΠΌΠΈΠ½ΠΈΡ β ΡΡΠΎ Π΄ΠΎΡΠΎΠ³ΠΎΠ²ΠΈΠ·Π½Π°. Π ΡΠ΅ΠΏΠ΅ΡΡ ΠΏΠΎΠ³ΠΎΠ²ΠΎΡΠΈΠΌ ΠΎ ΠΏΠ»ΡΡΠ°Ρ
.
Π‘Π΅Π³ΠΎΠ΄Π½Ρ Π°Π²ΡΠΎΠΌΠΎΠ±ΠΈΠ»ΡΠ½Π°Ρ ΠΊΠΎΠΌΠΏΠ°Π½ΠΈΡ Β«ΠΡΠ΄ΠΈΒ» β Π»ΠΈΠ΄Π΅Ρ ΠΏΠΎ ΠΏΡΠΈΠΌΠ΅Π½Π΅Π½ΠΈΡ Π»Π΅Π³ΠΊΠΈΡ
ΡΠΏΠ»Π°Π²ΠΎΠ² Π² ΠΊΠΎΠ½ΡΡΡΡΠΊΡΠΈΠΈ ΠΊΡΠ·ΠΎΠ²ΠΎΠ². Π ΡΠ°ΠΊΠ°Ρ ΡΠ΅Π½Π΄Π΅Π½ΡΠΈΡ Π²ΠΏΠΎΠ»Π½Π΅ ΠΎΠ±ΠΎΡΠ½ΠΎΠ²Π°Π½Π°.
Π‘ΡΠ°Π²Π½Π΅Π½ΠΈΠ΅ Π²Π΅ΡΠ° ΠΊΡΠ·ΠΎΠ²Π°
ΠΡΠ»ΠΈ ΡΡΠ°Π²Π½ΠΈΠ²Π°ΡΡ Π²Π΅Ρ Β«Π°Π»ΡΠΌΠΈΠ½ΠΈΠ΅Π²ΠΎΠ³ΠΎΒ» Π°Π²ΡΠΎ ΡΠΎ Β«ΡΡΠ°Π»ΡΠ½ΡΠΌΒ», ΠΏΡΠ΅ΠΈΠΌΡΡΠ΅ΡΡΠ²ΠΎ Π±ΡΠ΄Π΅Ρ Π² ΠΏΠΎΠ»ΡΠ·Ρ ΠΏΠ΅ΡΠ²ΠΎΠ³ΠΎ. ΠΡΠΎ ΠΎΡΠ΅Π²ΠΈΠ΄Π½ΠΎ, Π½ΠΎ, ΡΡΠΎ ΡΡΠΎ Π΄Π°Π΅Ρ? ΠΠΏΡΡΠ½ΡΠΉ Π°Π²ΡΠΎΠ»ΡΠ±ΠΈΡΠ΅Π»Ρ ΡΡΠ°Π·Ρ ΠΎΡΠ²Π΅ΡΠΈΡ β Π»Π΅Π³ΠΊΠΈΠΉ ΠΊΡΠ·ΠΎΠ² Π΄Π°Π΅Ρ Π»ΡΡΡΠΈΠ΅ Ρ Π°ΡΠ°ΠΊΡΠ΅ΡΠΈΡΡΠΈΠΊΠΈ ΡΠ°Π·Π³ΠΎΠ½Π° ΠΈ ΡΠΎΡΠΌΠΎΠΆΠ΅Π½ΠΈΡ, ΡΠΏΡΠ°Π²Π»ΡΠ΅ΠΌΠΎΡΡΠΈ ΠΈ ΡΡΡΠΎΠΉΡΠΈΠ²ΠΎΡΡΠΈ ΠΏΡΠΈ Π²Ρ ΠΎΠΆΠ΄Π΅Π½ΠΈΠΈ Π² ΠΏΠΎΠ²ΠΎΡΠΎΡΡ. ΠΠ° ΠΈ ΡΠΊΠΎΠ½ΠΎΠΌΠΈΡΠ½ΠΎΡΡΡ Π°Π²ΡΠΎΠΌΠΎΠ±ΠΈΠ»Ρ Π²ΠΎΠ·ΡΠ°ΡΡΠ°Π΅Ρ.
Π§ΡΠΎΠ±Ρ Π½Π΅ Π±ΡΡΡ Π³ΠΎΠ»ΠΎΡΠ»ΠΎΠ²Π½ΡΠΌ, ΠΏΡΠ΅Π΄Π»Π°Π³Π°Π΅ΠΌ ΡΠ²Π΅Π΄ΡΡΠΈΠΌ ΡΠΈΡΠ°ΡΠ΅Π»ΡΠΌ ΡΡΠ°Π²Π½ΠΈΡΡ Π΄Π²Π΅ ΠΏΡΠΈΠΌΠ΅ΡΠ½ΠΎ ΡΠ°Π²Π½ΠΎΠ·Π½Π°ΡΠ½ΡΡ ΠΏΠΎ Π³Π°Π±Π°ΡΠΈΡΠ°ΠΌ ΠΈ ΠΌΠΎΡΠ½ΠΎΡΡΠΈ ΠΌΠΎΠ΄Π΅Π»ΠΈ Π°Π²ΡΠΎΠΌΠΎΠ±ΠΈΠ»Π΅ΠΉ β Β«ΠΡΠ΄ΠΈ Π8Β» ΠΈ Β«Π€ΠΎΠ»ΡΠΊΡΠ²Π°Π³Π΅Π½-Π€Π°ΡΡΠΎΠ½Β». ΠΠ΅ΡΠΌΠΎΡΡΡ Π½Π° ΠΈΠ΄Π΅Π½ΡΠΈΡΠ½ΠΎΡΡΡ, ΡΠΊΡΠΏΠ»ΡΠ°ΡΠ°ΡΠΈΠΎΠ½Π½ΡΠ΅ ΠΊΠ°ΡΠ΅ΡΡΠ²Π° ΠΏΠ΅ΡΠ²ΠΎΠ³ΠΎ Π·Π½Π°ΡΠΈΡΠ΅Π»ΡΠ½ΠΎ Π»ΡΡΡΠ΅ ΡΠΎΠ»ΡΠΊΠΎ ΠΏΠΎΡΠΎΠΌΡ, ΡΡΠΎ Π8 Π½Π° 300 ΠΊΠ³ Π»Π΅Π³ΡΠ΅ Β«Π€Π°ΡΡΠΎΠ½Π°Β».
Π‘ΡΠ°Π²Π½Π΅Π½ΠΈΠ΅ ΠΏΠΎ ΠΏΡΠΈΠ·Π½Π°ΠΊΠ°ΠΌ Π±Π΅Π·ΠΎΠΏΠ°ΡΠ½ΠΎΡΡΠΈ
ΠΡΠ»ΠΈ ΠΆΠ΅ Π³ΠΎΠ²ΠΎΡΠΈΡΡ ΠΎ Π±Π΅Π·ΠΎΠΏΠ°ΡΠ½ΠΎΡΡΠΈ, ΡΠΎ Β«ΠΡΠ΄ΠΈΒ» ΠΈ Π²ΠΎΠ²ΡΠ΅ Π²ΡΡΠ΅ Π² ΡΡΠΎΠΌ ΠΏΠ»Π°Π½Π΅ Π½Π° ΡΠ΅Π»ΡΡ Π³ΠΎΠ»ΠΎΠ²Ρ. ΠΡΠΈΡΠΈΠ½Π° Π² ΡΠΏΠΎΡΠΎΠ±Π½ΠΎΡΡΠΈ Π°Π»ΡΠΌΠΈΠ½ΠΈΡ ΠΏΡΠΎΡΠΈΠ²ΠΎΡΡΠΎΡΡΡ ΡΠΊΡΡΡΠΈΠ²Π°ΡΡΠΈΠΌ Π½Π°Π³ΡΡΠ·ΠΊΠ°ΠΌ. ΠΠ»ΡΠΌΠΈΠ½ΠΈΠ΅Π²ΡΠΉ Π°Π²ΡΠΎΠΌΠΎΠ±ΠΈΠ»ΡΠ½ΡΠΉ ΠΊΡΠ·ΠΎΠ² ΠΆΠ΅ΡΡΡΠ΅, Π½ΠΎ ΠΏΡΠΈ ΡΡΠΎΠΌ Π³ΠΎΡΠ°Π·Π΄ΠΎ Π»ΡΡΡΠ΅ ΠΏΠΎΠ³Π»ΠΎΡΠ°Π΅Ρ ΡΠ΄Π°ΡΠ½ΡΡ ΡΠ½Π΅ΡΠ³ΠΈΡ.
ΠΡΠΎΡΠ΅ Π³ΠΎΠ²ΠΎΡΡ, ΡΠ°ΠΌ, Π³Π΄Π΅ Π΄Π΅ΡΠΎΡΠΌΠΈΡΡΠ΅ΡΡΡ ΡΠΎΠ»ΡΠΊΠΎ ΠΏΠ΅ΡΠ΅Π΄Π½ΡΡ ΡΠ°ΡΡΡ Π°Π»ΡΠΌΠΈΠ½ΠΈΠ΅Π²ΠΎΠ³ΠΎ ΠΊΡΠ·ΠΎΠ²Π°, ΡΡΠ°Π»ΡΠ½ΠΎΠΉ Π±ΡΠ΄Π΅Ρ ΠΈΡΠΊΠΎΡΠ΅ΠΆΠ΅Π½ Π²ΠΌΠ΅ΡΡΠ΅ Ρ ΡΠ°Π»ΠΎΠ½ΠΎΠΌ.
Π ΠΊΠΎΠ½ΡΡΡΡΠΊΡΠΈΠΈ ΠΊΡΠ·ΠΎΠ²Π°
Π ΠΊΠΎΠ½ΡΡΡΡΠΊΡΠΈΠΈ ΠΊΠ°ΠΆΠ΄ΠΎΠ³ΠΎ ΠΊΡΠ·ΠΎΠ²Π°, Π½Π΅Π·Π°Π²ΠΈΡΠΈΠΌΠΎ ΠΎΡ ΠΌΠ°ΡΠ΅ΡΠΈΠ°Π»Π°, ΠΏΡΠΈΡΡΡΡΡΠ²ΡΠ΅Ρ ΡΠΈΠ»ΠΎΠ²ΠΎΠΉ ΠΊΠ°ΡΠΊΠ°Ρ, ΠΎΠ±Π΅ΡΠΏΠ΅ΡΠΈΠ²Π°ΡΡΠΈΠΉ ΠΆΠ΅ΡΡΠΊΠΎΡΡΡ. Π Π°Π»ΡΠΌΠΈΠ½ΠΈΠ΅Π²ΠΎΠΌ ΠΊΡΠ·ΠΎΠ²Π΅ ΡΡΠΎΡ ΠΊΠ°ΡΠΊΠ°Ρ ΡΠΎΡΡΠΎΠΈΡ ΠΈΠ· Π»ΠΈΡΡΡ ΡΠ»Π΅ΠΌΠ΅Π½ΡΠΎΠ² Π² ΠΊΠΎΠΌΠ±ΠΈΠ½Π°ΡΠΈΠΈ Ρ ΠΏΡΠΎΡΠΈΠ»ΠΈΡΠΎΠ²Π°Π½Π½ΡΠΌΠΈ. ΠΡΡ ΡΠ°Π·ΡΠ°Π±ΠΎΡΠ°Π½ΠΎ ΡΠ°ΠΊ, ΡΡΠΎΠ±Ρ ΠΏΡΠΈ ΡΡΠΎΠ»ΠΊΠ½ΠΎΠ²Π΅Π½ΠΈΠΈ ΠΊΡΠ·ΠΎΠ² Π΄Π΅ΡΠΎΡΠΌΠΈΡΠΎΠ²Π°Π»ΡΡ ΠΏΠΎΡΡΠ°ΠΏΠ½ΠΎ. Π Π½Π° ΠΊΠ°ΠΆΠ΄ΠΎΠΌ ΡΡΠ°ΠΏΠ΅ ΡΠ΄Π°ΡΠ½Π°Ρ ΡΠ½Π΅ΡΠ³ΠΈΡ ΠΏΠΎΠ³Π»ΠΎΡΠ°Π΅ΡΡΡ ΠΌΠ°ΠΊΡΠΈΠΌΠ°Π»ΡΠ½ΠΎ.
ΠΠΎΠ·ΡΠΌΠ΅ΠΌ Π΄Π»Ρ ΠΏΡΠΈΠΌΠ΅ΡΠ° ΡΠΎΠ²ΡΠ΅ΠΌΠ΅Π½Π½ΡΠ΅ ΠΌΠΎΠ΄Π΅Π»ΠΈ Β«ΠΡΠ΄ΠΈΒ». ΠΡΠ»ΠΈ Π²Ρ ΡΠ°Π·Π³ΠΎΠ½ΠΈΡΠ΅ Π°Π²ΡΠΎ Π΄ΠΎ ΡΠΊΠΎΡΠΎΡΡΠΈ Π² 12 ΠΊΠΌ/Ρ ΠΈ Π½Π°ΠΏΡΠ°Π²ΠΈΡΠ΅ Π΅Π³ΠΎ Π² Π±Π΅ΡΠΎΠ½Π½ΡΡ ΡΡΠ΅Π½Ρ, ΡΠΎ ΠΏΡΠΈ ΡΠ΄Π°ΡΠ΅ Π΄Π΅ΡΠΎΡΠΌΠΈΡΡΡΡΡΡ Π»ΠΈΡΡ ΡΡΠΈΠ»ΠΈΡΠ΅Π»ΠΈ Π±Π°ΠΌΠΏΠ΅ΡΠ°. ΠΡΠ·ΠΎΠ² ΠΎΡΡΠ°Π½Π΅ΡΡΡ ΡΠ΅Π»Π΅Ρ ΠΎΠ½ΡΠΊΠΈΠΌ. ΠΡΠΈ ΡΠ°Π·Π³ΠΎΠ½Π΅ Π΄ΠΎ 30 ΠΊΠΌ/Ρ ΡΠ΄Π°Ρ Π±ΡΠ΄Π΅Ρ ΠΊΠΎΠΌΠΏΠ΅Π½ΡΠΈΡΠΎΠ²Π°Π½ Π²Π½Π΅ΡΠ½Π΅ΠΉ ΡΡΡΠ±ΡΠ°ΡΠΎΠΉ ΡΠ΅ΠΊΡΠΈΠ΅ΠΉ. Π Π»ΠΈΡΡ ΠΏΡΠΈ Π±ΠΎΠ»Π΅Π΅ Π²ΡΡΠΎΠΊΠΈΡ ΡΠΊΠΎΡΠΎΡΡΡΡ Π² Β«ΡΠ°Π±ΠΎΡΡΒ» Π½Π°ΡΠΈΠ½Π°Π΅Ρ Π²ΡΡΡΠΏΠ°ΡΡ ΡΠΈΠ»ΠΎΠ²ΠΎΠΉ ΠΊΠ°ΡΠΊΠ°Ρ ΠΊΡΠ·ΠΎΠ²Π° Π°Π²ΡΠΎΠΌΠΎΠ±ΠΈΠ»Ρ.
ΠΡΠ²ΠΎΠ΄Ρ ΠΏΠΎΡΠ»Π΅ ΡΡΠ°Π²Π½Π΅Π½ΠΈΡ
ΠΡΡ ΠΎΠ΄Ρ ΠΈΠ· Π²ΡΡΠ΅ΡΠΊΠ°Π·Π°Π½Π½ΠΎΠ³ΠΎ, ΠΌΠΎΠΆΠ½ΠΎ ΡΠ΄Π΅Π»Π°ΡΡ Π²ΡΠ²ΠΎΠ΄ β Π΅ΡΠ»ΠΈ Π²Ρ ΡΠ΅ΡΠΈΠ»ΠΈ ΠΊΡΠΏΠΈΡΡ Π°Π²ΡΠΎΠΌΠΎΠ±ΠΈΠ»Ρ Ρ Π°Π»ΡΠΌΠΈΠ½ΠΈΠ΅Π²ΡΠΌ ΠΊΡΠ·ΠΎΠ²ΠΎΠΌ, ΡΠΎ Π²Ρ Π°Π²ΡΠΎΠΌΠ°ΡΠΈΡΠ΅ΡΠΊΠΈ ΠΏΠΎΠ²ΡΡΠ°Π΅ΡΠ΅ ΡΠΎΠ±ΡΡΠ²Π΅Π½Π½ΡΡ Π±Π΅Π·ΠΎΠΏΠ°ΡΠ½ΠΎΡΡΡ. ΠΠΎ, ΠΊΡΠΎΠΌΠ΅ Π±ΠΎΠ»Π΅Π΅ Π²ΡΡΠΎΠΊΠΎΠΉ ΡΡΠΎΠΈΠΌΠΎΡΡΠΈ ΡΠ°ΠΌΠΎΠ³ΠΎ Π°Π²ΡΠΎ, Π²Π°ΠΌ ΠΏΡΠΈΠ΄Π΅ΡΡΡ Π±ΠΎΠ»ΡΡΠ΅ ΠΏΠ»Π°ΡΠΈΡΡ ΠΈ Π·Π° ΠΊΡΠ·ΠΎΠ²Π½ΠΎΠΉ ΡΠ΅ΠΌΠΎΠ½Ρ, ΠΊΠΎΠ³Π΄Π° ΡΠ°ΠΊΠΎΠ²ΠΎΠΉ ΠΏΠΎΠ½Π°Π΄ΠΎΠ±ΠΈΡΡΡ. Π£Π²Ρ, ΡΡΡ ΠΏΠΎΠΊΠ° Π΄Π΅ΠΉΡΡΠ²ΡΠ΅Ρ ΠΈΠ·Π²Π΅ΡΡΠ½ΡΠΉ Π·Π°ΠΊΠΎΠ½ ΡΠΎΡ ΡΠ°Π½Π΅Π½ΠΈΡ ΡΠ½Π΅ΡΠ³ΠΈΠΈ β Π³Π΄Π΅ ΡΠ΅Π³ΠΎ-ΡΠΎ ΠΏΡΠΈΠ±ΡΠ΄Π΅Ρ, ΡΠΎ Π² Π΄ΡΡΠ³ΠΎΠΌ ΠΌΠ΅ΡΡΠ΅ ΠΎΠ±ΡΠ·Π°ΡΠ΅Π»ΡΠ½ΠΎ ΡΡΠΎΠ»ΡΠΊΠΎ ΠΆΠ΅ ΡΠ±ΡΠ΄Π΅Ρ. Π Π½Π°ΠΎΠ±ΠΎΡΠΎΡ.
Π‘ ΠΌΠΎΠΌΠ΅Π½ΡΠ° ΠΈΠ·ΠΎΠ±ΡΠ΅ΡΠ΅Π½ΠΈΡ Π°Π²ΡΠΎΠΌΠΎΠ±ΠΈΠ»Ρ, ΠΌΠ°ΡΠ΅ΡΠΈΠ°Π»Ρ ΠΊΡΠ·ΠΎΠ²Π°, Π½Π°ΡΠΈΠ½Π°Ρ ΠΎΡ ΡΡΠ°Π»ΠΈ, ΠΆΠ΅Π»Π΅Π·Π° ΠΈ Π΄ΡΡΠ³ΠΈΡ ΠΌΠ΅ΡΠ°Π»Π»ΠΎΠ² Π΄ΠΎ ΠΏΠ»Π°ΡΡΠΌΠ°ΡΡ, ΠΊΠΎΠΌΠΏΠΎΠ·ΠΈΡΠΎΠ² ΠΈ Π΄Π°ΠΆΠ΅ Π΄Π΅ΡΠ΅Π²Π°, ΡΡΠ°Π»ΠΈ ΠΏΡΠ΅ΡΠ΅Π½Π΄ΠΎΠ²Π°ΡΡ Π½Π° Π·Π²Π°Π½ΠΈΠ΅ ΠΎΡΠ½ΠΎΠ²Π½ΠΎΠ³ΠΎ ΠΊΠΎΠ½ΡΡΡΡΠΊΡΠΈΠΎΠ½Π½ΠΎΠ³ΠΎ ΠΌΠ°ΡΠ΅ΡΠΈΠ°Π»Π° Π°Π²ΡΠΎΠΌΠΎΠ±ΠΈΠ»Ρ. Π ΠΏΠΎΡΠ»Π΅Π΄Π½Π΅Π΅ Π²ΡΠ΅ΠΌΡ Π² Π½ΠΎΠ²ΠΎΡΡΡΡ Π°Π²ΡΠΎΠΌΠΎΠ±ΠΈΠ»ΡΠ½ΠΎΠΉ ΠΏΡΠΎΠΌΡΡΠ»Π΅Π½Π½ΠΎΡΡΠΈ Π²ΡΠ΅ ΡΠ°ΡΠ΅ ΠΏΠΎΡΠ²Π»ΡΠ΅ΡΡΡ Π°Π»ΡΠΌΠΈΠ½ΠΈΠΉ, ΡΠ΅ΠΊΠ»Π°ΠΌΠΈΡΡΠ΅ΠΌΡΠΉ ΠΊΠ°ΠΊ ΠΌΠ°ΡΠ΅ΡΠΈΠ°Π» Π²ΡΠ±ΠΎΡΠ° Π΄Π»Ρ ΡΠΎΠ²ΡΠ΅ΠΌΠ΅Π½Π½ΡΡ Π°Π²ΡΠΎΠΌΠΎΠ±ΠΈΠ»Π΅ΠΉ Π½ΠΎΠ²ΠΎΠ³ΠΎ ΠΏΠΎΠΊΠΎΠ»Π΅Π½ΠΈΡ ΠΎΡ ΡΠ»Π΅ΠΊΡΡΠΎΠΌΠΎΠ±ΠΈΠ»Π΅ΠΉ Π΄ΠΎ ΠΏΠΈΠΊΠ°ΠΏΠΎΠ². Π― Π³ΠΎΠ²ΠΎΡΠΈΠ» Ρ Π΄ΠΎΠΊΡΠΎΡΠΎΠΌΠΠΆΠΎΠ΄ΠΈ Π₯ΠΎΠ»Π», Π²ΠΈΡΠ΅-ΠΏΡΠ΅Π·ΠΈΠ΄Π΅Π½Ρ ΠΏΠΎΠ΄ΡΠ°Π·Π΄Π΅Π»Π΅Π½ΠΈΡ Π°Π²ΡΠΎΠΌΠΎΠ±ΠΈΠ»ΡΠ½ΠΎΠ³ΠΎ ΡΡΠ½ΠΊΠ° SMDI ΠΎ ΠΌΠ΅ΡΡΠ΅ ΡΡΠ°Π»ΠΈ Π½Π° ΡΡΠ½ΠΊΠ΅ Π°Π²ΡΠΎΠΌΠΎΠ±ΠΈΠ»ΡΠ½ΡΡ ΠΌΠ°ΡΠ΅ΡΠΈΠ°Π»ΠΎΠ².
Β«ΠΠ΅ΠΆΠ΄Ρ ΠΌΠ°ΡΠ΅ΡΠΈΠ°Π»Π°ΠΌΠΈ Π²ΡΠ΅Π³Π΄Π° Π±ΡΠ»ΠΎ ΠΌΠ½ΠΎΠ³ΠΎ ΠΊΠΎΠ½ΠΊΡΡΠ΅Π½ΡΠΈΠΈΒ», — ΡΠΊΠ°Π·Π°Π»Π° ΠΎΠ½Π°. Β«ΠΠ° ΠΏΡΠΎΡΡΠΆΠ΅Π½ΠΈΠΈ Π²ΡΠ΅ΠΉ ΠΈΡΡΠΎΡΠΈΠΈ Π°Π²ΡΠΎΠΌΠΎΠ±ΠΈΠ»Ρ ΡΡΠΎ ΠΏΡΠΎΠΈΡΡ ΠΎΠ΄ΠΈΠ»ΠΎ Π½Π° Π·Π°Π΄Π½Π΅ΠΌ ΠΏΠ»Π°Π½Π΅. Π ΠΏΠΎΡΠ»Π΅Π΄Π½Π΅Π΅ Π²ΡΠ΅ΠΌΡ, ΠΊΠ°ΠΊ ΡΡΠΎΡ ΠΊΠΎΠ½ΠΊΡΡΡ Π±ΡΠ» Π² Π‘ΠΠ, ΡΡΠΎ Π½ΠΎΠ²ΠΎΠ΅ ΡΠ²Π»Π΅Π½ΠΈΠ΅. Π― ΡΠΆΠ΅ 30 Π»Π΅Ρ ΡΠ°Π±ΠΎΡΠ°Ρ Π² ΡΡΠΎΠΉ ΠΎΡΡΠ°ΡΠ»ΠΈ ΠΌΠ΅ΡΠ°Π»Π»ΡΡΠ³ΠΎΠΌ, ΠΈ Ρ Π½ΠΈΠΊΠΎΠ³Π΄Π° Π½Π΅ Π²ΠΈΠ΄Π΅Π», ΡΡΠΎΠ±Ρ Π°Π²ΡΠΎΠΏΡΠΎΠΈΠ·Π²ΠΎΠ΄ΠΈΡΠ΅Π»ΠΈ ΠΏΡΠ΅Π΄ΡΡΠ°Π²Π»ΡΠ»ΠΈ Π½ΠΎΠ²ΡΠ΅ Π°Π²ΡΠΎΠΌΠΎΠ±ΠΈΠ»ΠΈ ΠΈ Π³ΠΎΠ²ΠΎΡΠΈΠ»ΠΈ ΠΎ ΠΌΠ°ΡΠ΅ΡΠΈΠ°Π»Π°Ρ , ΠΈΠ· ΠΊΠΎΡΠΎΡΡΡ ΠΈΠ·Π³ΠΎΡΠΎΠ²Π»Π΅Π½Π° ββΠΊΠΎΠ½ΡΡΡΡΠΊΡΠΈΡ ΠΊΡΠ·ΠΎΠ²Π°.ΠΡΠΎ Π½Π΅ΡΠ»ΡΡ Π°Π½Π½ΠΎ.
ΠΡΠ°ΠΊ, Π΅ΡΠ»ΠΈ Π²ΡΠ±ΠΎΡ ΠΌΠ°ΡΠ΅ΡΠΈΠ°Π»Π° ΡΡΠ°Π½ΠΎΠ²ΠΈΡΡΡ Π²ΡΠ΅ Π±ΠΎΠ»Π΅Π΅ ΠΈ Π±ΠΎΠ»Π΅Π΅ Π²Π°ΠΆΠ½ΡΠΌ Π΄Π»Ρ ΠΏΠΎΠΊΡΠΏΠ°ΡΠ΅Π»Π΅ΠΉ ΠΈ ΠΏΡΠΎΠΈΠ·Π²ΠΎΠ΄ΠΈΡΠ΅Π»Π΅ΠΉ Π°Π²ΡΠΎΠΌΠΎΠ±ΠΈΠ»Π΅ΠΉ, ΠΊΠ°ΠΊΠΎΠΉ ΠΌΠ°ΡΠ΅ΡΠΈΠ°Π» Π΄Π΅ΠΉΡΡΠ²ΠΈΡΠ΅Π»ΡΠ½ΠΎ Π»ΡΡΡΠ΅?

ΡΡΠ»ΠΎΠ½ΠΎΠ² Π»ΠΈΡΡΠΎΠ²ΠΎΠΉ ΡΡΠ°Π»ΠΈ Π½Π° Π·Π°Π²ΠΎΠ΄Π΅-ΠΈΠ·Π³ΠΎΡΠΎΠ²ΠΈΡΠ΅Π»Π΅.
ΠΠ΅Π³ΠΊΠΈΠΉ Π²Π΅Ρ: Π°Π»ΡΠΌΠΈΠ½ΠΈΠΉ ΠΏΡΠΎΡΠΈΠ² Π²ΡΡΠΎΠΊΠΎΠΏΡΠΎΡΠ½ΠΎΠΉ ΡΡΠ°Π»ΠΈ
Π ΠΏΠ΅ΡΠΈΠΎΠ΄ΠΈΡΠ΅ΡΠΊΠΎΠΉ ΡΠ°Π±Π»ΠΈΡΠ΅ Π°Π»ΡΠΌΠΈΠ½ΠΈΠΉ ΠΏΡΠΈΠΌΠ΅ΡΠ½ΠΎ Π²Π΄Π²ΠΎΠ΅ ΠΌΠ΅Π½ΡΡΠ΅, ΡΠ΅ΠΌ ΠΆΠ΅Π»Π΅Π·ΠΎ. ΠΠΎ ΠΎΠ·Π½Π°ΡΠ°Π΅Ρ Π»ΠΈ Π»Π΅Π³ΠΊΠΎΡΡΡ Π² ΡΡΠΎΠΌ Π±ΡΠΊΠ²Π°Π»ΡΠ½ΠΎΠΌ ΡΠΌΡΡΠ»Π΅ Π»Π΅Π³ΠΊΠΈΠ΅ Π²Π΅ΡΠ° ΡΡΠ°Π½ΡΠΏΠΎΡΡΠ½ΡΡ ΡΡΠ΅Π΄ΡΡΠ²?
ΠΠ»ΡΠΌΠΈΠ½ΠΈΠ΅Π²Π°Ρ ΠΏΡΠΎΠΌΡΡΠ»Π΅Π½Π½ΠΎΡΡΡ Π³ΠΎΠ²ΠΎΡΠΈΡ Β«Π΄Π°Β», ΡΠΊΠ°Π·ΡΠ²Π°Ρ Π½Π° ΡΠΎ, ΡΡΠΎ Π°Π²ΡΠΎΠΏΡΠΎΠΈΠ·Π²ΠΎΠ΄ΠΈΡΠ΅Π»ΠΈ, ΡΠ°ΠΊΠΈΠ΅ ΠΊΠ°ΠΊ Tesla ΠΈ Ford, Π²ΡΠ±ΠΈΡΠ°ΡΡ Π°Π»ΡΠΌΠΈΠ½ΠΈΠ΅Π²ΡΠ΅ ΠΊΡΠ·ΠΎΠ²Π° Π΄Π»Ρ ΠΏΡΠ΅ΠΎΠ±ΡΠ°Π·ΠΎΠ²Π°Π½ΠΈΡ ΡΠΊΠΎΠ½ΠΎΠΌΠΈΠΈ Π²Π΅ΡΠ° Π² Π΅ΠΌΠΊΠΎΡΡΡ Π°ΠΊΠΊΡΠΌΡΠ»ΡΡΠΎΡΠ° ΠΈΠ»ΠΈ ΠΏΠΎΠ»Π΅Π·Π½ΡΡ Π½Π°Π³ΡΡΠ·ΠΊΡ.ΠΠ΄Π½Π°ΠΊΠΎ Π΄ΠΎΠΊΡΠΎΡ Π₯ΠΎΠ»Π» Π½Π΅ ΡΠΎΠ³Π»Π°ΡΠ΅Π½.
ΠΡΠ·ΠΎΠ² ΠΈ Ρ ΠΎΠ΄ΠΎΠ²Π°Ρ ΡΠ°ΡΡΡ ΡΠΎΡΡΠ°Π²Π»ΡΡΡ Π±ΠΎΠ»Π΅Π΅ ΠΏΠΎΠ»ΠΎΠ²ΠΈΠ½Ρ Π²Π΅ΡΠ° ΡΡΠ΅Π΄Π½Π΅Π³ΠΎ ΡΡΠ°Π½ΡΠΏΠΎΡΡΠ½ΠΎΠ³ΠΎ ΡΡΠ΅Π΄ΡΡΠ²Π°, ΠΏΠΎΡΡΠΎΠΌΡ ΠΌΠ°ΡΠ΅ΡΠΈΠ°Π» ΠΌΠΎΠΆΠ΅Ρ ΡΡΡΠ΅ΡΡΠ²Π΅Π½Π½ΠΎ ΠΏΠΎΠ²Π»ΠΈΡΡΡ Π½Π° Π²Π΅Ρ, ΠΆΠ΅ΡΡΠΊΠΎΡΡΡ ΠΈ ΠΏΡΠΎΡΠ½ΠΎΡΡΡ Π°Π²ΡΠΎΠΌΠΎΠ±ΠΈΠ»Ρ. ΠΠΎ ΡΠ»ΠΎΠ²Π°ΠΌ Π΄ΠΎΠΊΡΠΎΡΠ° Π₯ΠΎΠ»Π»Π°, ΠΏΡΠ΅Π΄Π΅Π» ΠΏΡΠΎΡΠ½ΠΎΡΡΠΈ ΡΡΠ°Π»ΠΈ Π΄ΠΎ 2000 ΠΠΠ° (290 000 ΡΡΠ½ΡΠΎΠ² / ΠΊΠ². ΠΡΠΉΠΌ), ΡΡΠΎ ΠΏΡΠΈΠΌΠ΅ΡΠ½ΠΎ Π² ΡΠ΅ΡΡΡΠ΅ ΡΠ°Π·Π° Π²ΡΡΠ΅, ΡΠ΅ΠΌ Ρ ΡΠ°ΠΌΡΡ ΠΏΡΠΎΡΠ½ΡΡ Π°Π»ΡΠΌΠΈΠ½ΠΈΠ΅Π²ΡΡ ΡΠΏΠ»Π°Π²ΠΎΠ², Π΄ΠΎΡΡΡΠΏΠ½ΡΡ ΡΠ΅Π³ΠΎΠ΄Π½Ρ.
ΠΡΠ° ΡΠ°Π·Π½ΠΈΡΠ° Π² ΠΏΡΠΎΡΠ½ΠΎΡΡΠΈ Π½Π° ΡΠ°ΡΡΡΠΆΠ΅Π½ΠΈΠ΅ ΠΎΠ·Π½Π°ΡΠ°Π΅Ρ, ΡΡΠΎ Π°Π»ΡΠΌΠΈΠ½ΠΈΠ΅Π²ΡΠ΅ Π΄Π΅ΡΠ°Π»ΠΈ Π΄ΠΎΠ»ΠΆΠ½Ρ ΡΠ²Π΅Π»ΠΈΡΠΈΠ²Π°ΡΡ ΡΠΎΠ»ΡΠΈΠ½Ρ, ΡΡΠΎΠ±Ρ ΡΠΎΠΎΡΠ²Π΅ΡΡΡΠ²ΠΎΠ²Π°ΡΡ ΡΡΠ°Π½Π΄Π°ΡΡΠ°ΠΌ Π±Π΅Π·ΠΎΠΏΠ°ΡΠ½ΠΎΡΡΠΈ, Π² ΡΠΎ Π²ΡΠ΅ΠΌΡ ΠΊΠ°ΠΊ ΡΡΠΎΠ²Π΅ΡΡΠ΅Π½ΡΡΠ²ΠΎΠ²Π°Π½Π½Π°Ρ Π²ΡΡΠΎΠΊΠΎΠΏΡΠΎΡΠ½Π°Ρ ΡΡΠ°Π»Ρ (AHSS) ΠΌΠΎΠΆΠ΅Ρ Π±ΡΡΡ ΡΠ΄Π΅Π»Π°Π½Π° Π±ΠΎΠ»Π΅Π΅ ΡΠΎΠ½ΠΊΠΎΠΉ, ΡΡΠΎ ΡΠ½ΠΈΠΆΠ°Π΅Ρ Π²Π΅Ρ.ΠΠΎΠ½Π΅ΡΠ½ΠΎ, ΡΡΠΈ Π±ΠΎΠ»Π΅Π΅ ΡΠΎΠ»ΡΡΡΠ΅ Π°Π»ΡΠΌΠΈΠ½ΠΈΠ΅Π²ΡΠ΅ Π΄Π΅ΡΠ°Π»ΠΈ ΠΌΠΎΠ³ΡΡ Π²ΡΠ΅ ΠΆΠ΅ ΠΏΠΎΠ»ΡΡΠ°ΡΡΡΡ Π»Π΅Π³ΡΠ΅, ΡΠ΅ΠΌ ΠΈΡ ΡΡΠ°Π»ΡΠ½ΡΠ΅ Π°Π½Π°Π»ΠΎΠ³ΠΈ.
Β«Π‘ Π°Π»ΡΠΌΠΈΠ½ΠΈΠ΅ΠΌ Π²Ρ ΠΌΠΎΠΆΠ΅ΡΠ΅ ΠΏΠΎΠ»ΡΡΠΈΡΡ ΠΌΠ΅Π½ΡΡΡΡ ΠΌΠ°ΡΡΡ, Π½ΠΎ ΡΡΠΎ ΠΎΡΠ½ΠΎΡΠΈΡΠ΅Π»ΡΠ½ΠΎ Π½Π΅Π±ΠΎΠ»ΡΡΠ°Ρ ΡΠ°Π·Π½ΠΈΡΠ°, ΠΈ Π²Ρ ΠΏΠ»Π°ΡΠΈΡΠ΅ Π·Π° ΡΡΠΎ ΡΠΌΠ΅Π½ΡΡΠ΅Π½ΠΈΠ΅ ΠΌΠ°ΡΡΡ ΠΈΠ·-Π·Π° Π±ΠΎΠ»Π΅Π΅ Π²ΡΡΠΎΠΊΠΎΠΉ ΡΡΠΎΠΈΠΌΠΎΡΡΠΈ ΠΌΠ°ΡΠ΅ΡΠΈΠ°Π»Π°Β», — ΡΠΊΠ°Π·Π°Π» Π΄ΠΎΠΊΡΠΎΡ Π₯ΠΎΠ»Π».
ΠΠ°ΠΊ ΠΏΡΠ°Π²ΠΈΠ»ΠΎ, Π°Π²ΡΠΎΠΏΡΠΎΠΈΠ·Π²ΠΎΠ΄ΠΈΡΠ΅Π»ΠΈ Π² Π·Π½Π°ΡΠΈΡΠ΅Π»ΡΠ½ΠΎΠΉ ΡΡΠ΅ΠΏΠ΅Π½ΠΈ ΡΠ½ΠΈΠΆΠ°ΡΡ ΡΡΠΎΠΈΠΌΠΎΡΡΡ Π°Π»ΡΠΌΠΈΠ½ΠΈΠ΅Π²ΡΡ ΠΌΠ°ΡΠ΅ΡΠΈΠ°Π»ΠΎΠ² Π² Π΄Π²Π°-ΡΡΠΈ ΡΠ°Π·Π° Π½Π° ΠΊΠΈΠ»ΠΎΠ³ΡΠ°ΠΌΠΌ, ΡΠ΅ΠΌ ΡΡΠ°Π»Ρ.
ΠΠΎΠΊΡΠΎΡ Π₯ΠΎΠ»Π» ΡΠΊΠ°Π·Π°Π» Π½Π° Π΅ΡΠ΅ ΠΎΠ΄ΠΈΠ½ Π½Π΅Π΄ΠΎΡΡΠ°ΡΠΎΠΊ Π±ΠΎΠ»Π΅Π΅ ΡΠΎΠ»ΡΡΡΡ Π°Π»ΡΠΌΠΈΠ½ΠΈΠ΅Π²ΡΡ Π΄Π΅ΡΠ°Π»Π΅ΠΉ.Β«ΠΡΠ»ΠΈ Π²Ρ ΠΏΠΎΡΠΌΠΎΡΡΠΈΡΠ΅ Π½Π° ΠΏΠ΅ΡΠ΅Π΄Π½ΡΡ ΡΡΠΎΠΉΠΊΡ Π°Π»ΡΠΌΠΈΠ½ΠΈΠ΅Π²ΠΎΠ³ΠΎ Π°Π²ΡΠΎΠΌΠΎΠ±ΠΈΠ»Ρ, ΡΡΠΎ ΡΠ²Π΅Π»ΠΈΡΠ΅Π½Π½Π°Ρ Π³Π΅ΠΎΠΌΠ΅ΡΡΠΈΡΒ», — ΡΠΊΠ°Π·Π°Π»Π° ΠΎΠ½Π°. Β«ΠΠ½ Π΄ΠΎΠ»ΠΆΠ΅Π½ Π±ΡΡΡ ΡΠΈΡΠ΅ Π² ΠΏΠΎΠΏΠ΅ΡΠ΅ΡΠ½ΠΎΠΌ ΡΠ΅ΡΠ΅Π½ΠΈΠΈ, ΡΡΠΎΠ±Ρ ΠΈΠΌΠ΅ΡΡ ΠΎΠ΄ΠΈΠ½Π°ΠΊΠΎΠ²ΡΡ ΠΏΡΠΎΠΈΠ·Π²ΠΎΠ΄ΠΈΡΠ΅Π»ΡΠ½ΠΎΡΡΡ. Π’Π°ΠΊΠΈΠΌ ΠΎΠ±ΡΠ°Π·ΠΎΠΌ, ΠΎΠ½ ΠΌΠΎΠΆΠ΅Ρ Π²ΡΠΏΠΎΠ»Π½ΡΡΡ ΡΠΎ ΠΆΠ΅ ΡΠ°ΠΌΠΎΠ΅ ΠΈ Π²Π΅ΡΠΈΡΡ Π½Π΅ΠΌΠ½ΠΎΠ³ΠΎ ΠΌΠ΅Π½ΡΡΠ΅, Π½ΠΎ Ρ Π²Π°Ρ Π΄ΠΎΠ»ΠΆΠ½Π° Π±ΡΡΡ Π±ΠΎΠ»Π΅Π΅ ΡΠΈΡΠΎΠΊΠ°Ρ ΠΏΠ΅ΡΠ΅Π΄Π½ΡΡ ΡΡΠΎΠΉΠΊΠ°. ΠΡΠΎ ΠΌΠΎΠΆΠ΅Ρ ΠΏΠΎΠ²Π»ΠΈΡΡΡ Π½Π° ΠΎΠΏΡΡ Π²ΠΎΠΆΠ΄Π΅Π½ΠΈΡ, Π° Π΅ΡΠ»ΠΈ Π²ΡΠ΅ Π΄Π΅ΡΠ°Π»ΠΈ Π²ΡΠΏΠΎΠ»Π½Π΅Π½Ρ ΠΈΠ· Π°Π»ΡΠΌΠΈΠ½ΠΈΡ, ΡΡΠΎ ΠΌΠΎΠΆΠ΅Ρ ΡΠ½ΠΈΠ·ΠΈΡΡ ΡΡΡΠ΅ΠΊΡΠΈΠ²Π½ΠΎΡΡΡ ΠΈΡΠΏΠΎΠ»ΡΠ·ΠΎΠ²Π°Π½ΠΈΡ ΠΏΡΠΎΡΡΡΠ°Π½ΡΡΠ²Π° ΡΠ°Π»ΠΎΠ½Π° Π°Π²ΡΠΎΠΌΠΎΠ±ΠΈΠ»Ρ Β».
ΠΠ΅Π·ΠΎΠΏΠ°ΡΠ½ΠΎΡΡΡ Π°Π»ΡΠΌΠΈΠ½ΠΈΠ΅Π²ΠΎΠ³ΠΎ ΡΡΠ°Π½ΡΠΏΠΎΡΡΠ½ΠΎΠ³ΠΎ ΡΡΠ΅Π΄ΡΡΠ²Π° ΠΏΡΠΎΡΠΈΠ² Π²ΡΡΠΎΠΊΠΎΠΏΡΠΎΡΠ½ΠΎΠΉ ΡΡΠ°Π»ΠΈ
ΠΠΎ Π΄Π°Π½Π½ΡΠΌ driveal Aluminum.org, Π°Π²ΡΠΎΠΌΠΎΠ±ΠΈΠ»ΠΈ Ρ Π°Π»ΡΠΌΠΈΠ½ΠΈΠ΅Π²ΡΠΌ ΠΊΡΠ·ΠΎΠ²ΠΎΠΌ Π±Π΅Π·ΠΎΠΏΠ°ΡΠ½Π΅Π΅, ΡΠ΅ΠΌ ΠΈΡ ΡΡΠ°Π»ΡΠ½ΡΠ΅ Π°Π½Π°Π»ΠΎΠ³ΠΈ, Π±Π»Π°Π³ΠΎΠ΄Π°ΡΡ Π»ΡΡΡΠ΅ΠΌΡ ΠΏΠΎΠ³Π»ΠΎΡΠ΅Π½ΠΈΡ ΡΠ½Π΅ΡΠ³ΠΈΠΈ, Π±ΠΎΠ»ΡΡΠΈΠΌ Π·ΠΎΠ½Π°ΠΌ ΡΠ°Π·ΡΡΡΠ΅Π½ΠΈΡ, ΠΊΠΎΡΠΎΡΡΠ΅ ΡΠΊΠ»Π°Π΄ΡΠ²Π°ΡΡΡΡ Π±ΠΎΠ»Π΅Π΅ ΠΏΡΠ΅Π΄ΡΠΊΠ°Π·ΡΠ΅ΠΌΠΎ, ΠΈ Π±ΠΎΠ»ΡΡΠ΅ΠΌΡ Π³Π°Π±Π°ΡΠΈΡΠ½ΠΎΠΌΡ ΡΠ°Π·ΠΌΠ΅ΡΡ.
ΠΠΎΠΊΡΠΎΡ Π₯ΠΎΠ»Π» ΠΏΡΠ΅Π΄Π»Π°Π³Π°Π΅Ρ ΠΈΠ½ΡΠ΅ΡΠ΅ΡΠ½ΡΠΉ ΠΊΠΎΠ½ΡΡΠ°ΠΏΡΠ½ΠΊΡ ΡΡΠΈΠΌ ΠΏΡΠ΅ΠΈΠΌΡΡΠ΅ΡΡΠ²Π°ΠΌ: Π½Π΅ ΡΠΎΡ ΠΌΠ°ΡΠ΅ΡΠΈΠ°Π», ΠΊΠΎΡΠΎΡΡΠΉ ΡΠ°ΠΊ Π²Π°ΠΆΠ΅Π½, ΠΊΠ°ΠΊ ΡΠΎ, ΠΊΠ°ΠΊ Π²Ρ ΡΠ°Π·ΡΠ°Π±Π°ΡΡΠ²Π°Π΅ΡΠ΅ ΡΡΠΎΡ ΠΌΠ°ΡΠ΅ΡΠΈΠ°Π».
Β«ΠΡ ΠΌΠΎΠΆΠ΅ΡΠ΅ ΡΠ°Π·ΡΠ°Π±ΠΎΡΠ°ΡΡ Π±Π΅Π·ΠΎΠΏΠ°ΡΠ½ΡΠΉ Π°Π²ΡΠΎΠΌΠΎΠ±ΠΈΠ»Ρ Ρ ΠΈΡΠΏΠΎΠ»ΡΠ·ΠΎΠ²Π°Π½ΠΈΠ΅ΠΌ Π΄ΡΡΠ³ΠΈΡ ΠΌΠ°ΡΠ΅ΡΠΈΠ°Π»ΠΎΠ² [ΠΊΡΠΎΠΌΠ΅ ΡΡΠ°Π»ΠΈ], Π½ΠΎ ΡΡΠΎ ΡΠΎΡΠ΅ΡΠ°Π½ΠΈΠ΅ ΠΌΠ°ΡΠ΅ΡΠΈΠ°Π»ΠΎΠ² ΠΈ Π΄ΠΈΠ·Π°ΠΉΠ½Π°Β», — ΡΠΊΠ°Π·Π°Π»Π° ΠΎΠ½Π°. Β«ΠΠ±ΡΠΎΠ»ΡΡΠ½ΠΎ, Ρ Π½Π°ΡΡΠ½ΠΎΠΉ ΡΠΎΡΠΊΠΈ Π·ΡΠ΅Π½ΠΈΡ Π½Π΅Π²Π΅ΡΠ½ΠΎ ΡΡΠ²Π΅ΡΠΆΠ΄Π°ΡΡ, ΡΡΠΎ Π°Π»ΡΠΌΠΈΠ½ΠΈΠΉ ΠΊΠ°ΠΊ ΠΌΠ°ΡΠ΅ΡΠΈΠ°Π»Β« Π±ΠΎΠ»Π΅Π΅ Π±Π΅Π·ΠΎΠΏΠ°ΡΠ΅Π½ Β».
ΠΠΎΠ³Π΄Π° Ρ ΠΏΠΎΠ΄Π½ΡΠ» ΡΠΎΡΠΊΡ ΠΎΡΡΡΠ΅ΡΠ°, ΡΡΠΎ ΠΊΠ°ΠΆΠ΄ΡΠΉ Π°Π²ΡΠΎΠΌΠΎΠ±ΠΈΠ»Ρ Ρ Π°Π»ΡΠΌΠΈΠ½ΠΈΠ΅Π²ΡΠΌ ΠΊΡΠ·ΠΎΠ²ΠΎΠΌ Π½Π° Π΄ΠΎΡΠΎΠ³Π΅ ΠΈΠΌΠ΅Π΅Ρ ΠΏΡΡΠΈΠ·Π²Π΅Π·Π΄ΠΎΡΠ½ΡΠΉ ΡΠ΅ΠΉΡΠΈΠ½Π³ Π±Π΅Π·ΠΎΠΏΠ°ΡΠ½ΠΎΡΡΠΈ, ΠΎΠ½Π° ΡΠΊΠ°Π·Π°Π»Π° Π½Π° ΡΠΌΠ΅ΡΠ°Π½Π½ΡΠ΅ ΠΏΠ΅ΡΠ΅ΠΌΠ΅Π½Π½ΡΠ΅, ΠΊΠΎΡΠΎΡΡΠ΅ ΠΌΠΎΠ³ΡΡ ΠΎΠ±ΡΡΡΠ½ΠΈΡΡ, ΠΏΠΎΡΠ΅ΠΌΡ:
Β«ΠΡΠ΅ Π½ΠΎΠ²ΡΠ΅, Π±ΠΎΠ»Π΅Π΅ Π΄ΠΎΡΠΎΠ³ΠΈΠ΅ Π°Π²ΡΠΎΠΌΠΎΠ±ΠΈΠ»ΠΈ.ΠΠ²ΡΠΎΠΌΠΎΠ±ΠΈΠ»ΠΈ ΠΊΠ»Π°ΡΡΠ° Π»ΡΠΊΡ ΠΌΠΎΠ³ΡΡ ΠΏΠΎΠ·Π²ΠΎΠ»ΠΈΡΡ ΡΠ΅Π±Π΅ Π΄ΠΎΠΏΠΎΠ»Π½ΠΈΡΠ΅Π»ΡΠ½ΡΡ ΡΠ°Π·ΡΠ°Π±ΠΎΡΠΊΡ, ΡΡΠΎΠ±Ρ ΠΏΠΎΠ»ΡΡΠΈΡΡ ΡΡΠΎΡ ΡΠ΅ΠΉΡΠΈΠ½Π³, ΠΈ Π² ΡΠ»ΡΡΠ°Π΅ Ρ Ford F-150, Ρ Π΄ΡΠΌΠ°Ρ, ΡΡΠΎ ΠΎΡΠ΅Π½Ρ Π°Π³ΡΠ΅ΡΡΠΈΠ²Π½ΡΠΉ ΠΈ ΡΠΈΡΠΊΠΎΠ²Π°Π½Π½ΡΠΉ ΡΠ°Π³, ΡΡΠΎΠ±Ρ ΠΏΠ΅ΡΠ΅ΠΎΠ±ΠΎΡΡΠ΄ΠΎΠ²Π°ΡΡ ΠΏΠΈΠΊΠ°ΠΏ Π² Π°Π»ΡΠΌΠΈΠ½ΠΈΠΉ. Π― Π΄ΡΠΌΠ°Ρ, ΡΡΠΎ ΠΎΠ½ΠΈ ΡΠ΄Π΅Π»Π°Π»ΠΈ Π°Π±ΡΠΎΠ»ΡΡΠ½ΠΎ Π²ΡΠ΅, ΡΡΠΎ ΠΌΠΎΠ³Π»ΠΈ, ΡΡΠΎΠ±Ρ ΡΠ±Π΅Π΄ΠΈΡΡΡΡ, ΡΡΠΎ ΡΡΠΎ ΡΡΠ°Π±ΠΎΡΠ°Π΅Ρ Β».
Π’Π°ΠΊΠΈΠΌ ΠΎΠ±ΡΠ°Π·ΠΎΠΌ, Π°Π»ΡΠΌΠΈΠ½ΠΈΠΉ ΠΌΠΎΠΆΠ΅Ρ Π±ΡΡΡ ΡΠ°ΠΊΠΈΠΌ ΠΆΠ΅ Π±Π΅Π·ΠΎΠΏΠ°ΡΠ½ΡΠΌ, ΠΊΠ°ΠΊ ΡΡΠ°Π»Ρ, Π½ΠΎ Ρ Π±ΠΎΠ»Π΅Π΅ Π²ΡΡΠΎΠΊΠΈΠΌΠΈ Π·Π°ΡΡΠ°ΡΠ°ΠΌΠΈ.
Π―Π²Π»ΡΠ΅ΡΡΡ Π»ΠΈ Π°Π»ΡΠΌΠΈΠ½ΠΈΠΉ Π±ΠΎΠ»Π΅Π΅ ΡΡΡΠΎΠΉΡΠΈΠ²ΡΠΌ, ΡΠ΅ΠΌ ΡΡΠ°Π»Ρ?
ΠΠ΅ΡΠΌΠΎΡΡΡ Π½Π° ΡΠΎ, ΡΡΠΎ Π°Π»ΡΠΌΠΈΠ½ΠΈΠΉ ΠΌΠΎΠΆΠ½ΠΎ Π»Π΅Π³ΠΊΠΎ ΠΏΠ΅ΡΠ΅ΡΠ°Π±Π°ΡΡΠ²Π°ΡΡ Ρ ΠΏΠΎΠΌΠΎΡΡΡ ΠΏΠ΅ΡΠ΅Π΄ΠΎΠ²ΡΡ ΡΠ΅Ρ Π½ΠΎΠ»ΠΎΠ³ΠΈΠΉ, ΠΏΡΠ΅ΠΈΠΌΡΡΠ΅ΡΡΠ²ΠΎ ΡΡΠ°Π»ΠΈ Π² ΡΠΎΠΌ, ΡΡΠΎ ΠΎΠ½ ΡΠ²Π»ΡΠ΅ΡΡΡ ΡΠ°ΠΌΡΠΌ ΠΏΠ΅ΡΠ΅ΡΠ°Π±ΠΎΡΠ°Π½Π½ΡΠΌ ΠΌΠ°ΡΠ΅ΡΠΈΠ°Π»ΠΎΠΌ Π² ΠΌΠΈΡΠ΅.ΠΡΠΎΡΠ΅ΡΡ ΠΏΠ΅ΡΠ΅ΡΠ°Π±ΠΎΡΠΊΠΈ ΡΡΠ°Π»ΠΈ ΡΠ°ΠΊΠΆΠ΅ ΠΏΡΠΎΡΠ΅: Π΅Π³ΠΎ ΠΆΠ΅Π»Π΅Π·ΠΈΡΡΡΠ΅ ΡΠ²ΠΎΠΉΡΡΠ²Π° ΠΏΠΎΠ·Π²ΠΎΠ»ΡΡΡ Π»Π΅Π³ΠΊΠΎ ΡΠΎΡΡΠΈΡΠΎΠ²Π°ΡΡ ΠΎΡΡ ΠΎΠ΄Ρ, Π° Π²ΡΠ΅ ΡΠΏΠ»Π°Π²Ρ ΡΡΠ°Π»ΠΈ ΠΌΠΎΠΆΠ½ΠΎ ΠΏΠ»Π°Π²ΠΈΡΡ Π²ΠΌΠ΅ΡΡΠ΅ ΠΈ ΡΠΌΠ΅ΡΠΈΠ²Π°ΡΡ Π΄Π»Ρ ΠΏΠΎΠ»ΡΡΠ΅Π½ΠΈΡ Π»ΡΠ±ΠΎΠ³ΠΎ ΡΠΏΠ»Π°Π²Π° ΡΡΠ°Π»ΠΈ. ΠΠ»ΡΠΌΠΈΠ½ΠΈΠΉ, Ρ Π΄ΡΡΠ³ΠΎΠΉ ΡΡΠΎΡΠΎΠ½Ρ, ΡΠ²Π»ΡΠ΅ΡΡΡ Π±ΠΎΠ»Π΅Π΅ Π΄ΠΎΡΠΎΠ³ΠΎΡΡΠΎΡΡΠΈΠΌ Π΄Π»Ρ ΠΏΠ΅ΡΠ΅ΡΠ°Π±ΠΎΡΠΊΠΈ, ΡΡΠ΅Π±ΡΡ ΡΠ°Π·Π΄Π΅Π»Π΅Π½ΠΈΡ ΡΠ°Π·Π»ΠΈΡΠ½ΡΡ ΠΌΠ°ΡΠΎΠΊ ΠΏΠ΅ΡΠ΅Π΄ ΠΏΠ»Π°Π²Π»Π΅Π½ΠΈΠ΅ΠΌ Π΄Π»Ρ ΡΠΎΡ ΡΠ°Π½Π΅Π½ΠΈΡ ΠΌΠ°ΡΠΎΠΊ.
ΠΏΡΠΈΠ³ΠΎΠ΄Π½ΠΎΡΡΡ ΡΡΠ°Π»ΠΈ ΠΏΡΠΎΡΠΈΠ² Π°Π»ΡΠΌΠΈΠ½ΠΈΡ
Π₯ΠΎΡΡ Ρ Π½Π΅ΠΊΠΎΡΠΎΡΡΠΌΠΈ ΠΌΠ°ΡΠΊΠ°ΠΌΠΈ AHSS ΠΌΠΎΠΆΠ΅Ρ Π±ΡΡΡ ΡΠ»ΠΎΠΆΠ½ΠΎ ΡΠ°Π±ΠΎΡΠ°ΡΡ, ΡΡΠ°Π»Ρ ΡΠΈΡΠΎΠΊΠΎ ΠΈΠ·Π²Π΅ΡΡΠ½Π° Π±ΠΎΠ»Π΅Π΅ Π²ΡΡΠΎΠΊΠΈΠΌ Π²ΡΡ ΠΎΠ΄ΠΎΠΌ ΠΈ ΠΏΠ»Π°ΡΡΠΈΡΠ½ΠΎΡΡΡΡ, ΡΠ΅ΠΌ Π°Π»ΡΠΌΠΈΠ½ΠΈΠ΅Π²ΡΠ΅ ΡΠΏΠ»Π°Π²Ρ.ΠΠΎΠΊΡΠΎΡ Π₯ΠΎΠ»Π» ΡΠΊΠ°Π·ΡΠ²Π°Π΅Ρ Π½Π° ΠΎΠ΄Π½ΠΎ ΠΊΠΎΠ½ΡΡΡΡΠΊΡΠΈΠ²Π½ΠΎΠ΅ ΠΎΡΠ»ΠΈΡΠΈΠ΅, ΠΊΠΎΡΠΎΡΠΎΠ΅ ΠΌΠΎΠΆΠ΅Ρ ΡΠ΄Π΅Π»Π°ΡΡ Π²ΡΠ±ΠΎΡ Π΄Π»Ρ ΠΎΠΏΡΠ΅Π΄Π΅Π»Π΅Π½Π½ΡΡ ΠΏΡΠΎΠΈΠ·Π²ΠΎΠ΄ΠΈΡΠ΅Π»Π΅ΠΉ ΠΌΠ΅ΠΆΠ΄Ρ Π°Π»ΡΠΌΠΈΠ½ΠΈΠ΅ΠΌ ΠΈ ΡΡΠ°Π»ΡΡ:
Β«ΠΠΎΠ½ΡΡΡΡΠΊΡΠΈΡ ΠΊΠΎΡΠΏΡΡΠ° Cadillac, Π½Π°ΠΏΡΠΈΠΌΠ΅Ρ, Ρ Π°Π»ΡΠΌΠΈΠ½ΠΈΠ΅ΠΌ Π½Π΅Π²ΠΎΠ·ΠΌΠΎΠΆΠ½Π° ΠΈΠ·-Π·Π° Π±ΠΎΠ»Π΅Π΅ Π½ΠΈΠ·ΠΊΠΎΠΉ ΠΏΠ»Π°ΡΡΠΈΡΠ½ΠΎΡΡΠΈ ΠΌΠ°ΡΠ΅ΡΠΈΠ°Π»Π°. ΠΠ»ΡΠΌΠΈΠ½ΠΈΠΉ ΠΈΠΌΠ΅Π΅Ρ ΠΌΠ΅Π½ΡΡΠ΅Π΅ ΡΠ΄Π»ΠΈΠ½Π΅Π½ΠΈΠ΅, ΡΡΠΎ ΡΠ²Π»ΡΠ΅ΡΡΡ ΠΏΠΎΠΊΠ°Π·Π°ΡΠ΅Π»Π΅ΠΌ ΡΠΎΡΠΌΡΠ΅ΠΌΠΎΡΡΠΈ.
ΠΠΎΠ²ΡΠ΅ ΡΠΏΠ»Π°Π²Ρ AHSS ΠΈΠΌΠ΅ΡΡ Π΄ΡΡΠ³ΠΈΠ΅ ΡΠ²ΠΎΠΉΡΡΠ²Π° ΠΌΠ°ΡΠ΅ΡΠΈΠ°Π»Π°, ΡΠ΅ΠΌ Ρ 20-30 Π»Π΅Ρ Π½Π°Π·Π°Π΄.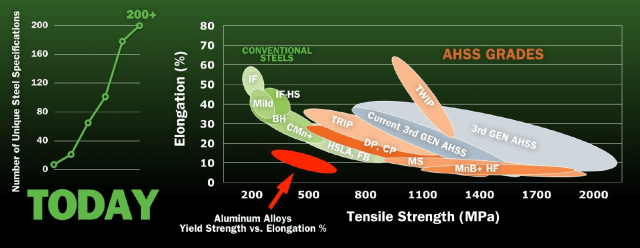
ΠΠ·ΠΎΠ±ΡΠ°ΠΆΠ΅Π½ΠΈΠ΅ ΠΏΡΠ΅Π΄ΠΎΡΡΠ°Π²Π»Π΅Π½ΠΎ SMDI.
Β«Π‘ΡΠ°Π»ΡΠ½Π°Ρ ΠΏΡΠΎΠΌΡΡΠ»Π΅Π½Π½ΠΎΡΡΡ ΠΏΡΠΎΠ΄ΠΎΠ»ΠΆΠ°Π΅Ρ Π²Π½Π΅Π΄ΡΡΡΡ ΠΈΠ½Π½ΠΎΠ²Π°ΡΠΈΠΈΒ», Π΄ΠΎΠΊΡΠΎΡΠ₯ΠΎΠ»Π» ΡΠΊΠ°Π·Π°Π». Β«Π 1970-Ρ Π³ΠΎΠ΄Π°Ρ ΠΌΡ Π½Π°ΡΠ°Π»ΠΈ Ρ ΠΏΡΠΈΠΌΠ΅ΡΠ½ΠΎ ΡΠ΅ΠΌΠΈ ΠΌΠ°ΡΠΎΠΊ ΡΡΠ°Π»ΠΈ. ΠΠ° ΠΏΠΎΡΠ»Π΅Π΄Π½ΠΈΠ΅ Π½Π΅ΡΠΊΠΎΠ»ΡΠΊΠΎ Π΄Π΅ΡΡΡΠΈΠ»Π΅ΡΠΈΠΉ ΡΡΠΎ ΡΠΈΡΠ»ΠΎ Π²ΠΎΠ·ΡΠΎΡΠ»ΠΎ Π΄ΠΎ Π±ΠΎΠ»Π΅Π΅ ΡΠ΅ΠΌ 200 ΠΊΠ»Π°ΡΡΠΎΠ² Β».
ΠΡΠΈ Π½ΠΎΠ²ΡΠ΅ ΡΠΎΡΡΠ° ΡΡΠ°Π»ΠΈ Π±ΡΠ»ΠΈ ΡΠ°Π·ΡΠ°Π±ΠΎΡΠ°Π½Ρ ΠΏΠΎΡΡΠ°Π²ΡΠΈΠΊΠ°ΠΌΠΈ Π΄Π»Ρ ΡΠΎΠ³ΠΎ, ΡΡΠΎΠ±Ρ Π°Π²ΡΠΎΠΏΡΠΎΠΈΠ·Π²ΠΎΠ΄ΠΈΡΠ΅Π»ΠΈ ΠΌΠΎΠ³Π»ΠΈ ΠΊΠΎΠ½ΠΊΡΡΠΈΡΠΎΠ²Π°ΡΡ Π² ΡΠΎΠΎΡΠ²Π΅ΡΡΡΠ²ΠΈΠΈ Ρ ΠΏΠΎΡΡΠΎΡΠ½Π½ΠΎ ΡΠΆΠ΅ΡΡΠΎΡΠ°ΡΡΠΈΠΌΠΈΡΡ ΠΏΡΠ°Π²ΠΈΠ»Π°ΠΌΠΈ ΡΠΊΠΎΠ½ΠΎΠΌΠΈΠΈ ΡΠΎΠΏΠ»ΠΈΠ²Π°. ΠΠ²ΡΠΎΠΏΡΠΎΠΈΠ·Π²ΠΎΠ΄ΠΈΡΠ΅Π»ΠΈ ΡΠΆΠΈΠΌΠ°ΡΡΡΡ Ρ ΠΎΠ±Π΅ΠΈΡ ΡΡΠΎΡΠΎΠ½, Ρ ΡΠ΅ΠΊΠΎΠΌΠ΅Π½Π΄Π°ΡΠΈΡΠΌΠΈ ΠΏΠΎ ΡΡΡΠ΅ΠΊΡΠΈΠ²Π½ΠΎΡΡΠΈ, ΠΏΡΠ΅Π΄Π½Π°Π·Π½Π°ΡΠ΅Π½Π½ΡΠΌΠΈ Π΄Π»Ρ Π±ΠΎΠ»Π΅Π΅ Π»Π΅Π³ΠΊΠΈΡ ΡΡΠ°Π½ΡΠΏΠΎΡΡΠ½ΡΡ ΡΡΠ΅Π΄ΡΡΠ², ΠΈ ΠΏΡΠ°Π²ΠΈΠ»Π°ΠΌΠΈ ΠΏΠΎ Π±Π΅Π·ΠΎΠΏΠ°ΡΠ½ΠΎΡΡΠΈ, ΡΡΠ΅Π±ΡΡΡΠΈΠΌΠΈ Π±ΠΎΠ»Π΅Π΅ ΡΠΈΠ»ΡΠ½ΡΡ , ΠΆΠ΅ΡΡΠΊΠΈΡ ΠΈ Π±ΠΎΠ»ΡΡΠΈΡ ΡΡΠ°Π½ΡΠΏΠΎΡΡΠ½ΡΡ ΡΡΠ΅Π΄ΡΡΠ². ΠΡΠΎ ΠΌΠΎΠΆΠ΅Ρ ΠΎΠ±ΡΡΡΠ½ΠΈΡΡ Π½Π΅Π΄Π°Π²Π½ΠΈΠΉ ΡΠΎΡΡ ΡΠΏΡΠΎΡΠ° Π½Π° Π°Π»ΡΠΌΠΈΠ½ΠΈΠΉ, ΠΊΠΎΡΠΎΡΡΠΉ ΠΌΠΎΠΆΠ΅Ρ ΡΠ΄ΠΎΠ²Π»Π΅ΡΠ²ΠΎΡΠΈΡΡ ΡΡΠΈ ΡΡΠ΅Π±ΠΎΠ²Π°Π½ΠΈΡ, Π½ΠΎ ΠΎΠ½ ΡΠ°ΠΊΠΆΠ΅ Π·Π°ΠΆΠ΅Π³ ΠΎΠ³ΠΎΠ½Ρ Π² ΡΡΠ°Π»Π΅Π»ΠΈΡΠ΅ΠΉΠ½ΠΎΠΉ ΠΏΡΠΎΠΌΡΡΠ»Π΅Π½Π½ΠΎΡΡΠΈ, ΡΡΠΎΠ±Ρ ΡΠΎΠ·Π΄Π°ΡΡ ΡΠΏΠ»Π°Π²Ρ, ΠΊΠΎΡΠΎΡΡΠ΅ ΠΌΠΎΠ³ΡΡ ΠΊΠΎΠ½ΠΊΡΡΠΈΡΠΎΠ²Π°ΡΡ ΠΈ ΠΏΡΠ΅Π²ΠΎΡΡ ΠΎΠ΄ΠΈΡΡ Π΄ΡΡΠ³ΠΈΠ΅ ΠΌΠ°ΡΠ΅ΡΠΈΠ°Π»Ρ.ΠΠΎ ΠΊΠΎΠ³Π΄Π° Π΄Π΅Π»ΠΎ Π΄ΠΎΡ ΠΎΠ΄ΠΈΡ Π΄ΠΎ Π²ΠΎΠΏΡΠΎΡΠ° ΠΎ ΡΠΎΠΌ, ΠΎΡΡΠ°Π½Π΅ΡΡΡ Π»ΠΈ ΠΊΠΎΠ³Π΄Π°-Π½ΠΈΠ±ΡΠ΄Ρ ΡΡΠ°Π»Ρ ΠΊΠ°ΠΊ ΠΊΠΎΡΠΎΠ»Ρ ΠΌΠ°ΡΠ΅ΡΠΈΠ°Π»ΠΎΠ² Π΄Π»Ρ ΠΊΡΠ·ΠΎΠ²ΠΎΠ², Π΄ΠΎΠΊΡΠΎΡ Π₯ΠΎΠ»Π» Π½Π΅ Π±Π΅ΡΠΏΠΎΠΊΠΎΠΈΡΡΡ.
Β«Π― Π΄Π΅ΡΠΆΡ ΠΆΡΡΠ½Π°Π» Π² ΡΠ²ΠΎΠ΅ΠΌ ΠΎΡΠΈΡΠ΅, Π²ΡΠΏΡΡΠΊ 1953 Π³ΠΎΠ΄Π°. Π Π½Π΅ΠΌ ΡΡΠ²Π΅ΡΠΆΠ΄Π°Π΅ΡΡΡ, ΡΡΠΎ ΠΊ 1960 Π³ΠΎΠ΄Ρ ΡΡΠ°Π»Ρ Π±ΠΎΠ»ΡΡΠ΅ Π½Π΅ Π±ΡΠ΄Π΅Ρ ΠΌΠ°ΡΠ΅ΡΠΈΠ°Π»ΠΎΠΌ Π² Π°Π²ΡΠΎΠΌΠΎΠ±ΠΈΠ»ΡΡ . ΠΡΠ΅Π²ΠΈΠ΄Π½ΠΎ, ΡΡΠΎΠ³ΠΎ Π½Π΅ ΠΏΡΠΎΠΈΠ·ΠΎΡΠ»ΠΎΒ», — ΡΠΊΠ°Π·Π°Π»Π° ΠΎΠ½Π°. Β«ΠΠ° ΡΠ²ΠΎΡ 30-Π»Π΅ΡΠ½ΡΡ ΠΊΠ°ΡΡΠ΅ΡΡ Π² GM Ρ Π²ΠΈΠ΄Π΅Π», ΠΊΠ°ΠΊ Π·Π°ΠΊΡΡΠ²Π°ΡΡΠΈΠ΅ ΠΏΠ°Π½Π΅Π»ΠΈ ΠΊΡΠ·ΠΎΠ²Π° Π±ΡΠ»ΠΈ ΡΠΏΡΠΎΠ΅ΠΊΡΠΈΡΠΎΠ²Π°Π½Ρ Π΄Π»Ρ Π°Π»ΡΠΌΠΈΠ½ΠΈΡ, ΠΏΠΎΡΠΎΠΌΡ ΡΡΠΎ ΠΎΠ½ΠΈ ΠΈΠΌΠ΅Π»ΠΈ ΠΌΠ΅Π½ΡΡΡΡ ΠΌΠ°ΡΡΡ, Π° Π±ΡΠΊΠ²Π°Π»ΡΠ½ΠΎ ΡΠ΅ΡΠ΅Π· Π½Π΅ΡΠΊΠΎΠ»ΡΠΊΠΎ ΠΌΠ΅ΡΡΡΠ΅Π² ΠΈΡ Π·Π°ΠΌΠ΅Π½ΠΈΠ»ΠΈ ΡΡΠ°Π»ΡΡ ΠΈΠ·-Π·Π° ΠΈΡ ΡΡΠΎΠΈΠΌΠΎΡΡΠΈ.ΠΠ°ΡΡΠ° Π±ΡΠ»Π° ΡΠ΄Π°Π»Π΅Π½Π° Π΄ΡΡΠ³ΠΈΠΌ ΡΠΏΠΎΡΠΎΠ±ΠΎΠΌ, Π»ΠΈΠ±ΠΎ ΠΈΠ· ΡΡΠ°Π»ΡΠ½ΡΡ ΠΊΠΎΠΌΠΏΠΎΠ½Π΅Π½ΡΠΎΠ², Π»ΠΈΠ±ΠΎ ΠΈΠ· Π΄ΡΡΠ³ΠΈΡ ΠΎΠ±Π»Π°ΡΡΠ΅ΠΉ Β».
Π’Π°ΠΊΠΎΠΉ ΠΆΠ΅ ΠΏΡΠΎΠ³Π½ΠΎΠ· ΠΏΡΠΎΠΈΠ·ΠΎΡΠ΅Π» Π² 2014 Π³ΠΎΠ΄Ρ, ΠΊΠΎΠ³Π΄Π° ΠΎΠΏΡΠΎΡ Ducker Worldwide ΠΏΡΠ΅Π΄ΡΠΊΠ°Π·Π°Π», ΡΡΠΎ 7 ΠΈΠ· 10 ΠΏΠΈΠΊΠ°ΠΏΠΎΠ² ΠΏΠΎΠΉΠ΄ΡΡ ΠΏΠΎ ΡΡΠΎΠΏΠ°ΠΌ Ford F-150. Π‘ ΡΠ΅Ρ ΠΏΠΎΡ Chevrolet Silverado Π±ΡΠ» Π΅Π΄ΠΈΠ½ΡΡΠ²Π΅Π½Π½ΡΠΌ ΠΏΡΠΈΠΌΠ΅ΡΠΎΠΌ, ΠΈ ΠΎΠ½ ΠΈΡΠΏΠΎΠ»ΡΠ·ΡΠ΅Ρ ΡΠΎΠ»ΡΠΊΠΎ Π°Π»ΡΠΌΠΈΠ½ΠΈΠΉ Π΄Π»Ρ ΠΏΠΎΠ²ΠΎΡΠΎΡΠ½ΡΡ ΠΏΠ°Π½Π΅Π»Π΅ΠΉ, ΠΊΠ°ΠΏΠΎΡΠ°, Π΄Π²Π΅ΡΠ΅ΠΉ ΠΈ Π·Π°Π΄Π½Π΅ΠΉ Π΄Π²Π΅ΡΠΈ.
Π Π±ΠΎΡΡΠ±Π΅ Π·Π° ΡΠ½ΠΈΠΆΠ΅Π½ΠΈΠ΅ Π²Π΅ΡΠ° Π°Π²ΡΠΎΠΌΠΎΠ±ΠΈΠ»Ρ ΠΈΠ»ΠΈ ΠΏΠΎΠ²ΡΡΠ΅Π½ΠΈΠ΅ ΠΏΡΠΎΠΈΠ·Π²ΠΎΠ΄ΠΈΡΠ΅Π»ΡΠ½ΠΎΡΡΠΈ Π°Π²ΡΠΎΠΏΡΠΎΠΈΠ·Π²ΠΎΠ΄ΠΈΡΠ΅Π»ΠΈ ΠΎΠ±ΡΠ°ΡΠ°ΡΡΡΡ ΠΊ Π°Π»ΡΡΠ΅ΡΠ½Π°ΡΠΈΠ²Π½ΡΠΌ ΠΌΠ°ΡΠ΅ΡΠΈΠ°Π»Π°ΠΌ ΠΈ Π½ΠΎΠ²ΡΠΌ ΡΠ΅Ρ Π½ΠΎΠ»ΠΎΠ³ΠΈΡΠΌ.ΠΠΎ ΠΊΠ°ΠΊ ΡΠΎΠ»ΡΠΊΠΎ ΠΎΠ½ΠΈ Π΄ΠΎΡΡΠΈΠ³Π½ΡΡ Π½Π΅ΠΎΠ±Ρ ΠΎΠ΄ΠΈΠΌΠΎΠ³ΠΎ ΡΠ½ΠΈΠΆΠ΅Π½ΠΈΡ ΠΌΠ°ΡΡΡ, ΡΠ»Π΅Π΄ΡΡΡΠΈΠΌ ΡΠ°Π³ΠΎΠΌ Π±ΡΠ΄Π΅Ρ ΡΠ½ΠΈΠΆΠ΅Π½ΠΈΠ΅ Π·Π°ΡΡΠ°Ρ.
Β«Chevy Silverado — Π»ΠΎΠ³ΠΈΡΠ΅ΡΠΊΠΈΠΉ ΠΏΡΠΈΠΌΠ΅Ρ ΠΈΡΠΏΠΎΠ»ΡΠ·ΠΎΠ²Π°Π½ΠΈΡ Π°Π»ΡΠΌΠΈΠ½ΠΈΡΒ», — ΠΏΡΠΈΠ·Π½Π°Π» Π΄ΠΎΠΊΡΠΎΡ Π₯ΠΎΠ»Π». Β«ΠΠ°ΡΠ°ΡΡΠΈΠ΅ΡΡ ΠΏΠ°Π½Π΅Π»ΠΈ Π½Π΅ΡΡΡΡΠΊΡΡΡΠ½Ρ, ΠΏΠΎΡΡΠΎΠΌΡ ΠΎΠ½ΠΈ ΡΠ²Π»ΡΡΡΡΡ Ρ ΠΎΡΠΎΡΠΈΠΌ Π²Π°ΡΠΈΠ°Π½ΡΠΎΠΌ Π΄Π»Ρ ΡΠ½ΠΈΠΆΠ΅Π½ΠΈΡ ΠΌΠ°ΡΡΡ, Π΅ΡΠ»ΠΈ Π²Ρ ΠΌΠΎΠΆΠ΅ΡΠ΅ ΠΏΠΎΠ·Π²ΠΎΠ»ΠΈΡΡ ΡΠ΅Π±Π΅ ΡΠ°ΠΊΡΡ ββΡΡΠΎΠΈΠΌΠΎΡΡΡΒ».
ΠΠΎΠΊΡΠΎΡ Π₯ΠΎΠ»Π», Π½Π΅ΡΠΌΠΎΡΡΡ Π½Π° ΡΠ²ΠΎΠΉ ΠΎΠΏΡΡ ΡΠ°Π±ΠΎΡΡ Π² Π°Π²ΡΠΎΠΌΠΎΠ±ΠΈΠ»ΡΠ½ΠΎΠΉ ΠΏΡΠΎΠΌΡΡΠ»Π΅Π½Π½ΠΎΡΡΠΈ, Π΄ΠΎΠ»Π³ΠΎΠ΅ Π²ΡΠ΅ΠΌΡ Π½Π°Π±Π»ΡΠ΄Π°Π»Π° Π·Π° ΡΡΠΎΠΉ Π±ΠΈΡΠ²ΠΎΠΉ. ΠΠ½Π° ΠΏΠΎΠ΄Π²Π΅Π»Π° ΠΈΡΠΎΠ³ ΡΠ°ΠΊ:
Β«Π― Π΄ΡΠΌΠ°Ρ, ΡΡΠΎ Π³ΠΎΠ²ΠΎΡΠΈΡ ΠΎ ΡΠΎΠΌ, ΡΡΠΎ Ρ Π² ΡΠ΅ΡΠ΅Π½ΠΈΠ΅ 30 Π»Π΅Ρ ΠΎΡΠ²Π΅ΡΠ°Π»Π° Π·Π° ΠΏΠ΅ΡΠ΅Π΄ΠΎΠ²ΡΠ΅ ΡΠ΅Ρ Π½ΠΎΠ»ΠΎΠ³ΠΈΠΈ Π² ΠΎΠ±Π»Π°ΡΡΠΈ ΡΡΠ°ΠΌΠΏΠΎΠ²ΠΊΠΈ ΠΈ ΡΡΠ°ΠΌΠΏΠΎΠ²ΠΊΠΈ Π² GM, ΡΠ°Π±ΠΎΡΠ°Ρ ΡΠΎ ΡΡΠ°Π»ΡΡ ΠΈ Π°Π»ΡΠΌΠΈΠ½ΠΈΠ΅ΠΌ, ΠΈ ΠΏΡΠΈΡΠ»Π° ΡΠ°Π±ΠΎΡΠ°ΡΡ Π² ΡΡΠ°Π»Π΅Π»ΠΈΡΠ΅ΠΉΠ½ΡΡ ΠΏΡΠΎΠΌΡΡΠ»Π΅Π½Π½ΠΎΡΡΡΒ», — ΡΠΌΠ΅Π΅ΡΡΡ ΠΎΠ½Π°.
ΠΠ»ΡΠΌΠΈΠ½ΠΈΠ΅Π²Π°Ρ ΡΡΠΎΡΠΎΠ½Π° ΡΡΠΎΠΉ ΠΈΡΡΠΎΡΠΈΠΈ: Β«Π ΠΎΡΡ ΡΠΏΡΠΎΡΠ° Π½Π° Π°Π»ΡΠΌΠΈΠ½ΠΈΠΉ Π² Π°Π²ΡΠΎΠΌΠΎΠ±ΠΈΠ»ΡΠ½ΠΎΠΉ ΠΏΡΠΎΠΌΡΡΠ»Π΅Π½Π½ΠΎΡΡΠΈ: ΡΡΠΎ ΡΡΠΎ Π·Π½Π°ΡΠΈΡ Π΄Π»Ρ ΡΡΠΎΠ²Π½ΡΒ».
,
Quick Read
ΠΠ»ΡΠΌΠΈΠ½ΠΈΠΉ ΡΠΎΠ·Π΄Π°Π΅Ρ Π»ΡΡΡΠΈΠΉ Π°Π²ΡΠΎΠΌΠΎΠ±ΠΈΠ»Ρ. ΠΡΠΏΠΎΠ»ΡΠ·ΠΎΠ²Π°Π½ΠΈΠ΅ Π°Π»ΡΠΌΠΈΠ½ΠΈΡ Π² Π°Π²ΡΠΎΠΌΠΎΠ±ΠΈΠ»ΡΡ ΠΈ ΠΊΠΎΠΌΠΌΠ΅ΡΡΠ΅ΡΠΊΠΈΡ ΡΡΠ°Π½ΡΠΏΠΎΡΡΠ½ΡΡ ΡΡΠ΅Π΄ΡΡΠ²Π°Ρ ΡΡΠΊΠΎΡΡΠ΅ΡΡΡ, ΠΏΠΎΡΠΊΠΎΠ»ΡΠΊΡ ΠΎΠ½ ΠΏΡΠ΅Π΄Π»Π°Π³Π°Π΅Ρ ΡΠ°ΠΌΡΠΉ Π±ΡΡΡΡΡΠΉ, Π±Π΅Π·ΠΎΠΏΠ°ΡΠ½ΡΠΉ, ΡΠΊΠΎΠ»ΠΎΠ³ΠΈΡΠ½ΡΠΉ ΠΈ ΡΠΊΠΎΠ½ΠΎΠΌΠΈΡΠ½ΡΠΉ ΡΠΏΠΎΡΠΎΠ± ΠΏΠΎΠ²ΡΡΠΈΡΡ ΠΏΡΠΎΠΈΠ·Π²ΠΎΠ΄ΠΈΡΠ΅Π»ΡΠ½ΠΎΡΡΡ, ΠΏΠΎΠ²ΡΡΠΈΡΡ ΡΠΊΠΎΠ½ΠΎΠΌΠΈΡ ΡΠΎΠΏΠ»ΠΈΠ²Π° ΠΈ ΡΠΎΠΊΡΠ°ΡΠΈΡΡ Π²ΡΠ±ΡΠΎΡΡ ΠΏΡΠΈ ΡΠΎΡ ΡΠ°Π½Π΅Π½ΠΈΠΈ ΠΈΠ»ΠΈ ΠΏΠΎΠ²ΡΡΠ΅Π½ΠΈΠΈ Π±Π΅Π·ΠΎΠΏΠ°ΡΠ½ΠΎΡΡΠΈ ΠΈ Π΄ΠΎΠ»Π³ΠΎΠ²Π΅ΡΠ½ΠΎΡΡΠΈ. ΠΡ Π°Π²ΡΠΎΠΌΠΎΠ±ΠΈΠ»Π΅ΠΉ ΠΌΠ°ΡΡΠΎΠ²ΠΎΠ³ΠΎ ΡΠΏΡΠΎΡΠ°, ΡΠ°ΠΊΠΈΡ ΠΊΠ°ΠΊ Ford F-150, Π΄ΠΎ ΡΠΎΡΠΊΠΎΡΠ½ΡΡ Π°Π²ΡΠΎΠΌΠΎΠ±ΠΈΠ»Π΅ΠΉ, ΡΠ°ΠΊΠΈΡ ΠΊΠ°ΠΊ Audi, Mercedes Benz ΠΈ Land Rover, Π°Π»ΡΠΌΠΈΠ½ΠΈΠΉ Π²ΡΠ΅ ΡΠ°ΡΠ΅ ΡΡΠ°Π½ΠΎΠ²ΠΈΡΡΡ Β«ΠΌΠ°ΡΠ΅ΡΠΈΠ°Π»ΠΎΠΌ Π²ΡΠ±ΠΎΡΠ°Β» Π΄Π»Ρ Π°Π²ΡΠΎΠΏΡΠΎΠΈΠ·Π²ΠΎΠ΄ΠΈΡΠ΅Π»Π΅ΠΉ Π±Π»Π°Π³ΠΎΠ΄Π°ΡΡ ΡΠ²ΠΎΠ΅ΠΉ ΠΏΡΠΎΡΠ½ΠΎΡΡΠΈ ΠΈ ΡΠΊΠΎΠ»ΠΎΠ³ΠΈΡΠ΅ΡΠΊΠΈΠΌ ΠΏΡΠ΅ΠΈΠΌΡΡΠ΅ΡΡΠ²Π°ΠΌ.ΠΠ»ΡΠΌΠΈΠ½ΠΈΠ΅Π²Π°Ρ ΡΡΠ°Π½ΡΠΏΠΎΡΡΠ½Π°Ρ Π³ΡΡΠΏΠΏΠ° (ATG) ΠΠ»ΡΠΌΠΈΠ½ΠΈΠ΅Π²ΠΎΠΉ Π°ΡΡΠΎΡΠΈΠ°ΡΠΈΠΈ ΡΠ°ΡΡΠΊΠ°Π·ΡΠ²Π°Π΅Ρ ΠΎ ΠΏΡΠ΅ΠΈΠΌΡΡΠ΅ΡΡΠ²Π°Ρ Π°Π»ΡΠΌΠΈΠ½ΠΈΡ ΠΏΡΠΈ ΡΡΠ°Π½ΡΠΏΠΎΡΡΠΈΡΠΎΠ²ΠΊΠ΅ Π² ΡΠ°ΠΌΠΊΠ°Ρ ΠΈΡΡΠ»Π΅Π΄ΠΎΠ²Π°ΡΠ΅Π»ΡΡΠΊΠΈΡ ΠΏΡΠΎΠ³ΡΠ°ΠΌΠΌ ΠΈ ΡΠ²ΡΠ·Π°Π½Π½ΡΡ Ρ Π½ΠΈΠΌΠΈ ΠΌΠ΅ΡΠΎΠΏΡΠΈΡΡΠΈΠΉ. ΠΠ»Ρ ΠΏΠΎΠ»ΡΡΠ΅Π½ΠΈΡ Π΄ΠΎΠΏΠΎΠ»Π½ΠΈΡΠ΅Π»ΡΠ½ΠΎΠΉ ΠΈΠ½ΡΠΎΡΠΌΠ°ΡΠΈΠΈ ΠΎ ΡΠΎΠΌ, ΠΊΠ°ΠΊ Π°Π»ΡΠΌΠΈΠ½ΠΈΠΉ ΡΠΏΡΠ°Π²Π»ΡΠ΅Ρ Π°Π²ΡΠΎΠΌΠΎΠ±ΠΈΠ»ΡΠΌΠΈ ΡΠ΅Π³ΠΎΠ΄Π½Ρ ΠΈ Π·Π°Π²ΡΡΠ°, ΠΏΠΎΠΆΠ°Π»ΡΠΉΡΡΠ°, ΠΏΠΎΡΠ΅ΡΠΈΡΠ΅ www.drivealumin.org.
Π€Π°ΠΊΡΡ Π½Π° Π²ΡΠ½ΠΎΡ
- ΠΠ΅ΠΏΡΠ΅ΡΡΠ²Π½ΡΠΉ ΡΠΎΡΡ ΠΈΡΠΏΠΎΠ»ΡΠ·ΠΎΠ²Π°Π½ΠΈΡ Π°Π²ΡΠΎΠΌΠΎΠ±ΠΈΠ»Π΅ΠΉ
ΠΡΠΏΠΎΠ»ΡΠ·ΠΎΠ²Π°Π½ΠΈΠ΅ Π°Π²ΡΠΎΠΌΠΎΠ±ΠΈΠ»ΡΠ½ΠΎΠ³ΠΎ Π°Π»ΡΠΌΠΈΠ½ΠΈΡ Π½Π΅ΠΏΡΠ΅ΡΡΠ²Π½ΠΎ ΡΠΎΡΠ»ΠΎ Π½Π° ΠΏΡΠΎΡΡΠΆΠ΅Π½ΠΈΠΈ 40 Π»Π΅Ρ. ΠΠ»ΡΠΌΠΈΠ½ΠΈΠΉ ΡΠ΅ΠΉΡΠ°Ρ ΡΡΡΡΠΏΠ°Π΅Ρ ΡΠΎΠ»ΡΠΊΠΎ ΡΡΠ°Π»ΠΈ Π² ΠΊΠ°ΡΠ΅ΡΡΠ²Π΅ Π½Π°ΠΈΠ±ΠΎΠ»Π΅Π΅ ΠΈΡΠΏΠΎΠ»ΡΠ·ΡΠ΅ΠΌΠΎΠ³ΠΎ ΠΌΠ°ΡΠ΅ΡΠΈΠ°Π»Π° Π² Π°Π²ΡΠΎΠΌΠΎΠ±ΠΈΠ»ΡΡ . - Π£ΡΠΈΠ»ΠΈΠ·ΠΈΡΠΎΠ²Π°Π½ΠΎ Π½Π° ΡΠ΅ΠΊΠΎΡΠ΄Π½ΡΡ
ΡΡΠΎΠ²Π½ΡΡ
Π ΠΊΠΎΠ½ΡΠ΅ ΡΡΠΎΠΊΠ° ΡΠ»ΡΠΆΠ±Ρ Π°Π²ΡΠΎΠΌΠΎΠ±ΠΈΠ»Ρ Π² ΡΡΠ΅Π΄Π½Π΅ΠΌ ΠΏΠ΅ΡΠ΅ΡΠ°Π±Π°ΡΡΠ²Π°Π΅ΡΡΡ ΠΏΠΎΡΡΠΈ 90 ΠΏΡΠΎΡΠ΅Π½ΡΠΎΠ² Π°Π»ΡΠΌΠΈΠ½ΠΈΡ. - ΠΠ½Π΅ΡΠ³ΠΎΡΡΡΠ΅ΠΊΡΠΈΠ²Π½ΠΎΡΡΡ
ΠΠΎ ΡΡΠ°Π²Π½Π΅Π½ΠΈΡ Ρ ΠΏΠ°ΡΠΊΠΎΠΌ ΡΡΠ°Π΄ΠΈΡΠΈΠΎΠ½Π½ΡΡ ΡΡΠ°Π»ΡΠ½ΡΡ ΡΡΠ°Π½ΡΠΏΠΎΡΡΠ½ΡΡ ΡΡΠ΅Π΄ΡΡΠ², ΠΈΡΠΏΠΎΠ»ΡΠ·ΠΎΠ²Π°Π½ΠΈΠ΅ Π°Π»ΡΠΌΠΈΠ½ΠΈΡ ΠΏΠΎΠ·Π²ΠΎΠ»ΡΠ΅Ρ ΡΡΠΊΠΎΠ½ΠΎΠΌΠΈΡΡ Π² ΡΠΊΠ²ΠΈΠ²Π°Π»Π΅Π½ΡΠ΅ 108 ΠΌΠΈΠ»Π»ΠΈΠΎΠ½ΠΎΠ² Π±Π°ΡΡΠ΅Π»Π΅ΠΉ ΡΡΡΠΎΠΉ Π½Π΅ΡΡΠΈ. - ΠΠ΅Π·ΠΎΠΏΠ°ΡΠ½Π΅Π΅
Π€ΡΠ½Ρ Π·Π° ΡΡΠ½Ρ, Π°Π»ΡΠΌΠΈΠ½ΠΈΠΉ ΠΌΠΎΠΆΠ΅Ρ Π²Π΄Π²ΠΎΠ΅ ΠΏΠΎΠ³Π»ΠΎΡΠ°ΡΡ ΡΠ½Π΅ΡΠ³ΠΈΡ ΡΠ΄Π°ΡΠ° ΠΌΡΠ³ΠΊΠΎΠΉ ΡΡΠ°Π»ΠΈ. ΠΠΎΠ»ΡΡΠΈΠ΅ Π·ΠΎΠ½Ρ ΡΠ°Π·Π΄Π°Π²Π»ΠΈΠ²Π°Π½ΠΈΡ ΠΌΠΎΠ³ΡΡ Π±ΡΡΡ ΡΠ°Π·ΡΠ°Π±ΠΎΡΠ°Π½Ρ Π±Π΅Π· ΡΠΎΠΎΡΠ²Π΅ΡΡΡΠ²ΡΡΡΠΈΡ ΡΡΡΠ°ΡΠΎΠ² Π·Π° Π²Π΅Ρ.
ΠΡΠ΅ΠΈΠΌΡΡΠ΅ΡΡΠ²Π° ΠΏΡΠΎΠΈΠ·Π²ΠΎΠ΄ΠΈΡΠ΅Π»ΡΠ½ΠΎΡΡΠΈ
ΠΠΎΡΠΊΠΎΠ»ΡΠΊΡ Π°Π»ΡΠΌΠΈΠ½ΠΈΠΉ Π»Π΅Π³ΡΠ΅, ΠΎΠ½ ΠΏΠΎΠ·Π²ΠΎΠ»ΡΠ΅Ρ Π°Π²ΡΠΎΠΏΡΠΎΠΈΠ·Π²ΠΎΠ΄ΠΈΡΠ΅Π»ΡΠΌ ΠΏΠΎΠ²ΡΡΠΈΡΡ ΡΡΠΎΠΉΠΊΠΎΡΡΡ ΠΊ Π²ΠΌΡΡΠΈΠ½Π°ΠΌ — ΠΎΠ½ΠΈ ΠΌΠΎΠ³ΡΡ ΡΠ΄Π΅Π»Π°ΡΡ ΠΏΠ°Π½Π΅Π»ΠΈ ΠΊΡΠ·ΠΎΠ²Π° ΡΠΎΠ»ΡΠ΅, Π½ΠΎ ΠΏΡΠΈ ΡΡΠΎΠΌ ΡΠ½ΠΈΠ·ΠΈΡΡ Π²Π΅Ρ. Π Π°Π²ΡΠΎΠΌΠΎΠ±ΠΈΠ»Ρ ΠΌΠ΅Π½ΡΡΠ΅Π³ΠΎ Π²Π΅ΡΠ° ΠΈΠΌΠ΅Π΅Ρ Π»ΡΡΡΠ΅Π΅ ΡΡΠΊΠΎΡΠ΅Π½ΠΈΠ΅, Π»ΡΡΡΠ΅Π΅ ΡΠΎΡΠΌΠΎΠΆΠ΅Π½ΠΈΠ΅ ΠΈ Π»ΡΡΡΡΡ ΡΠΏΡΠ°Π²Π»ΡΠ΅ΠΌΠΎΡΡΡ. ΠΡΠΎΠΌΠ΅ ΡΠΎΠ³ΠΎ, Π±ΠΎΠ»Π΅Π΅ Π»Π΅Π³ΠΊΠΈΠ΅ ΡΡΠ°Π½ΡΠΏΠΎΡΡΠ½ΡΠ΅ ΡΡΠ΅Π΄ΡΡΠ²Π° ΠΌΠΎΠ³ΡΡ ΠΏΠ΅ΡΠ΅Π²ΠΎΠ·ΠΈΡΡ ΠΈ Π±ΡΠΊΡΠΈΡΠΎΠ²Π°ΡΡ Π±ΠΎΠ»ΡΡΠ΅, ΠΏΠΎΡΠΎΠΌΡ ΡΡΠΎ Π΄Π²ΠΈΠ³Π°ΡΠ΅Π»Ρ Π½Π΅ Π½Π΅ΡΠ΅Ρ Π½Π΅Π½ΡΠΆΠ½ΠΎΠ³ΠΎ Π²Π΅ΡΠ°.
ΠΠ΅Ρ, ΠΏΡΠΎΡΠ½ΠΎΡΡΡ ΠΈ Π±Π΅Π·ΠΎΠΏΠ°ΡΠ½ΠΎΡΡΡ
ΠΡΠΈ ΠΏΡΠΈΠΌΠ΅Π½Π΅Π½ΠΈΠΈ ΠΊ ΠΎΠΏΡΠΈΠΌΠΈΠ·ΠΈΡΠΎΠ²Π°Π½Π½ΠΎΠΉ Π°Π²ΡΠΎΠΌΠΎΠ±ΠΈΠ»ΡΠ½ΠΎΠΉ ΠΊΠΎΠ½ΡΡΡΡΠΊΡΠΈΠΈ ΠΊΡΠ·ΠΎΠ²Π° Π°Π»ΡΠΌΠΈΠ½ΠΈΠΉ ΠΌΠΎΠΆΠ΅Ρ ΠΎΠ±Π΅ΡΠΏΠ΅ΡΠΈΡΡ ΡΠ½ΠΈΠΆΠ΅Π½ΠΈΠ΅ Π²Π΅ΡΠ° Π΄ΠΎ 50 ΠΏΡΠΎΡΠ΅Π½ΡΠΎΠ² ΠΏΠΎ ΡΡΠ°Π²Π½Π΅Π½ΠΈΡ Ρ ΡΡΠ°Π΄ΠΈΡΠΈΠΎΠ½Π½ΠΎΠΉ ΠΊΠΎΠ½ΡΡΡΡΠΊΡΠΈΠ΅ΠΉ ΠΈΠ· ΠΌΡΠ³ΠΊΠΎΠΉ ΡΡΠ°Π»ΠΈ.ΠΠ»ΡΠΌΠΈΠ½ΠΈΠ΅Π²ΡΠ΅ ΠΊΠΎΠ½ΡΡΡΡΠΊΡΠΈΠΈ ΠΊΡΠ·ΠΎΠ²Π° ΠΏΠΎ ΠΏΡΠΎΡΠ½ΠΎΡΡΠΈ ΡΠ°Π²Π½Ρ ΠΈΠ»ΠΈ ΠΏΡΠ΅Π²ΠΎΡΡ ΠΎΠ΄ΡΡ ΡΡΠ°Π»Ρ ΠΈ ΠΏΠΎΠ³Π»ΠΎΡΠ°ΡΡ Π²Π΄Π²ΠΎΠ΅ Π±ΠΎΠ»ΡΡΠ΅ ΡΠ½Π΅ΡΠ³ΠΈΠΈ, Π²ΡΠ·Π²Π°Π½Π½ΠΎΠΉ ΡΡΠΎΠ»ΠΊΠ½ΠΎΠ²Π΅Π½ΠΈΠ΅ΠΌ. Π‘Π½ΠΈΠΆΠ΅Π½ΠΈΠ΅ Π²Π΅ΡΠ° ΠΎΡΠ½ΠΎΠ²Π½ΠΎΠΉ ΠΊΠΎΠ½ΡΡΡΡΠΊΡΠΈΠΈ ΡΠ°ΠΊΠΆΠ΅ ΠΏΠΎΠ·Π²ΠΎΠ»ΡΠ΅Ρ ΡΠΌΠ΅Π½ΡΡΠΈΡΡ ΡΠ°Π·ΠΌΠ΅ΡΡ Π΄ΡΡΠ³ΠΈΡ ΡΠΈΡΡΠ΅ΠΌ Π°Π²ΡΠΎΠΌΠΎΠ±ΠΈΠ»Ρ (Π²ΠΊΠ»ΡΡΠ°Ρ Π΄Π²ΠΈΠ³Π°ΡΠ΅Π»Ρ, ΡΡΠ°Π½ΡΠΌΠΈΡΡΠΈΡ, ΠΏΠΎΠ΄Π²Π΅ΡΠΊΡ ΠΈ ΠΊΠΎΠ»Π΅ΡΠ°). Π‘ ΡΠΎΡΠΊΠΈ Π·ΡΠ΅Π½ΠΈΡ Π²Π΅ΡΠ°, ΠΏΡΠΎΡΠ½ΠΎΡΡΠΈ ΠΈ Π±Π΅Π·ΠΎΠΏΠ°ΡΠ½ΠΎΡΡΠΈ ΠΏΡΠ΅ΠΈΠΌΡΡΠ΅ΡΡΠ²Π° Π°Π»ΡΠΌΠΈΠ½ΠΈΡ ΠΎΡΠ΅Π²ΠΈΠ΄Π½Ρ.
ΠΠΊΠΎΠ»ΠΎΠ³ΠΈΡΠ΅ΡΠΊΠΈΠ΅ ΠΏΡΠ΅ΠΈΠΌΡΡΠ΅ΡΡΠ²Π°
ΠΠΎΡΡΠΈ 90 ΠΏΡΠΎΡΠ΅Π½ΡΠΎΠ² Π°Π²ΡΠΎΠΌΠΎΠ±ΠΈΠ»ΡΠ½ΠΎΠ³ΠΎ Π°Π»ΡΠΌΠΈΠ½ΠΈΠ΅Π²ΠΎΠ³ΠΎ Π»ΠΎΠΌΠ° — Π±ΠΎΠ»Π΅Π΅ ΠΏΠΎΠ»ΡΠΌΠΈΠ»Π»ΠΈΠΎΠ½Π° ΡΠΎΠ½Π½ Π² Π³ΠΎΠ΄ — ΠΈΠ·Π²Π»Π΅ΠΊΠ°Π΅ΡΡΡ ΠΈ ΠΏΠ΅ΡΠ΅ΡΠ°Π±Π°ΡΡΠ²Π°Π΅ΡΡΡ.Π§ΡΠΎΠ±Ρ ΡΠ°ΡΡΠΌΠΎΡΡΠ΅ΡΡ ΡΡΠΎ Π² ΠΏΠ΅ΡΡΠΏΠ΅ΠΊΡΠΈΠ²Π΅: ΠΏΠ΅ΡΠ΅ΡΠ°Π±ΠΎΡΠΊΠ° 1 ΡΠΎΠ½Π½Ρ Π°Π»ΡΠΌΠΈΠ½ΠΈΡ ΡΠΊΠΎΠ½ΠΎΠΌΠΈΡ ΡΠ½Π΅ΡΠ³ΠΈΡ, ΡΠΊΠ²ΠΈΠ²Π°Π»Π΅Π½ΡΠ½ΡΡ 21 Π±Π°ΡΡΠ΅Π»Ρ Π½Π΅ΡΡΠΈ. ΠΠΊΠΎΠ»ΠΎΠ³ΠΈΡΠ΅ΡΠΊΠΈΠ΅ ΠΏΠΎΠ±Π΅Π΄Ρ ΠΏΡΠΎΠ΄ΠΎΠ»ΠΆΠ°ΡΡΡΡ: ΡΠ΅ΡΠ΅Π½Π·ΠΈΡΡΠ΅ΠΌΠΎΠ΅ ΠΈΡΡΠ»Π΅Π΄ΠΎΠ²Π°Π½ΠΈΠ΅, ΠΏΡΠΎΠ²Π΅Π΄Π΅Π½Π½ΠΎΠ΅ ΠΠ°ΡΠΈΠΎΠ½Π°Π»ΡΠ½ΠΎΠΉ Π»Π°Π±ΠΎΡΠ°ΡΠΎΡΠΈΠ΅ΠΉ ΠΠΊ-Π ΠΈΠ΄ΠΆΠ° ΠΠΈΠ½ΠΈΡΡΠ΅ΡΡΡΠ²Π° ΡΠ½Π΅ΡΠ³Π΅ΡΠΈΠΊΠΈ Π‘Π¨Π, ΠΏΠΎΠΊΠ°Π·Π°Π»ΠΎ, ΡΡΠΎ Π°Π²ΡΠΎΠΌΠΎΠ±ΠΈΠ»Ρ Ρ Π²ΡΡΠΎΠΊΠΈΠΌ ΡΠΎΠ΄Π΅ΡΠΆΠ°Π½ΠΈΠ΅ΠΌ Π°Π»ΡΠΌΠΈΠ½ΠΈΡ ΠΌΠΎΠΆΠ΅Ρ ΡΠ½ΠΈΠ·ΠΈΡΡ ΠΎΠ±ΡΠ΅Π΅ ΠΏΠΎΡΡΠ΅Π±Π»Π΅Π½ΠΈΠ΅ ΡΠ½Π΅ΡΠ³ΠΈΠΈ Π² ΡΠ΅ΡΠ΅Π½ΠΈΠ΅ ΠΆΠΈΠ·Π½Π΅Π½Π½ΠΎΠ³ΠΎ ΡΠΈΠΊΠ»Π° Π΄ΠΎ 20 ΠΏΡΠΎΡΠ΅Π½ΡΠΎΠ² ΠΈ ΡΠΎΠΊΡΠ°ΡΠΈΡΡ Π²ΡΠ±ΡΠΎΡΡ CO2 Π΄ΠΎ 17 ΠΏΡΠΎΡΠ΅Π½ΡΠΎΠ². ,
ΠΠ°Π³Π»ΡΠ΄ΡΠ²Π°Ρ Π²ΠΏΠ΅ΡΠ΅Π΄: Π³ΠΎΠ½ΠΊΠ° Π·Π° ΡΠΎΠΏΠ»ΠΈΠ²Π½ΠΎΠΉ ΡΡΡΠ΅ΠΊΡΠΈΠ²Π½ΠΎΡΡΡΡ
ΠΡΠ΅ ΡΠ°ΡΠ΅ ΠΏΠΎΡΡΠ΅Π±ΠΈΡΠ΅Π»ΠΈ ΡΡΠ΅Π±ΡΡΡ Π±ΠΎΠ»Π΅Π΅ ΡΠΊΠΎΠ½ΠΎΠΌΠΈΡΠ½ΡΡ ΡΡΠ°Π½ΡΠΏΠΎΡΡΠ½ΡΡ ΡΡΠ΅Π΄ΡΡΠ².Π£ΡΠΈΡΡΠ²Π°Ρ ΡΡΠΎ, Π½Π°ΡΡΠ΄Ρ Ρ Π½ΠΎΠ²ΡΠΌΠΈ ΠΏΡΠ°Π²ΠΈΠ»Π°ΠΌΠΈ ΡΠΊΠΎΠ½ΠΎΠΌΠΈΠΈ ΡΠΎΠΏΠ»ΠΈΠ²Π°, ΠΊΠΎΡΠΎΡΡΠ΅ ΠΏΠΎΡΡΠ΅Π±ΡΡΡ, ΡΡΠΎΠ±Ρ Π°Π²ΡΠΎΠΌΠΎΠ±ΠΈΠ»ΡΠ½ΡΠΉ ΠΏΠ°ΡΠΊ Π‘Π¨Π ΡΠΎΡΡΠ°Π²Π»ΡΠ» Π² ΡΡΠ΅Π΄Π½Π΅ΠΌ 54,5 ΠΌΠΈΠ»Ρ Π½Π° Π³Π°Π»Π»ΠΎΠ½ ΠΊ 2025 Π³ΠΎΠ΄Ρ, Π°Π²ΡΠΎΠΌΠΎΠ±ΠΈΠ»ΡΠ½Π°Ρ ΠΏΡΠΎΠΌΡΡΠ»Π΅Π½Π½ΠΎΡΡΡ ΡΠ΅Π°Π³ΠΈΡΡΠ΅Ρ. ΠΠ΄ΠΈΠ½ ΠΈΠ· ΠΏΡΠΈΠΌΠ΅ΡΠΎΠ²: ΠΏΠΈΠΊΠ°ΠΏ F-150 Ρ Π°Π»ΡΠΌΠΈΠ½ΠΈΠ΅Π²ΡΠΌ ΠΊΡΠ·ΠΎΠ²ΠΎΠΌ Ford. ΠΡΠΎΡ ΡΠ°Π³ Π² Π½Π°ΠΏΡΠ°Π²Π»Π΅Π½ΠΈΠΈ Π°Π»ΡΠΌΠΈΠ½ΠΈΡ ΠΈΠΌΠ΅Π΅Ρ ΡΠ΅ΡΡΠ΅Π·Π½ΡΠ΅ ΠΏΠΎΡΠ»Π΅Π΄ΡΡΠ²ΠΈΡ — Ford F-150 ΡΠ²Π»ΡΠ΅ΡΡΡ ΡΠ°ΠΌΡΠΌ ΠΏΠΎΠΏΡΠ»ΡΡΠ½ΡΠΌ Π°Π²ΡΠΎΠΌΠΎΠ±ΠΈΠ»Π΅ΠΌ Π»ΡΠ±ΠΎΠ³ΠΎ Π²ΠΈΠ΄Π° Π² Π‘ΠΎΠ΅Π΄ΠΈΠ½Π΅Π½Π½ΡΡ Π¨ΡΠ°ΡΠ°Ρ ΠΈ ββΠΎΠ΄Π½ΠΎΠΉ ΠΈΠ· ΡΠ°ΠΌΡΡ ΠΏΡΠΈΠ±ΡΠ»ΡΠ½ΡΡ Π°Π²ΡΠΎΠΌΠΎΠ±ΠΈΠ»ΡΠ½ΡΡ Π»ΠΈΠ½ΠΈΠΉ Π² ΠΌΠΈΡΠ΅. ΠΡΡΠ·ΠΎΠ²ΠΈΠΊ F-150 2015 Π³ΠΎΠ΄Π° ΠΏΠΎΡΠ΅ΡΡΠ» 700 ΡΡΠ½ΡΠΎΠ² (ΠΏΡΠΈΠΌΠ΅ΡΠ½ΠΎ 15 ΠΏΡΠΎΡΠ΅Π½ΡΠΎΠ² ΠΏΠΎ ΠΌΠ°ΡΡΠ΅ ΠΊΡΠ·ΠΎΠ²Π°) Ρ Π²ΡΡΠΎΠΊΠΎΠΏΡΠΎΡΠ½ΡΠΌ, ΠΏΠΎΠ»Π½ΠΎΡΡΡΡ Π°Π»ΡΠΌΠΈΠ½ΠΈΠ΅Π²ΡΠΌ ΠΊΠΎΡΠΏΡΡΠΎΠΌ Π²ΠΎΠ΅Π½Π½ΠΎΠ³ΠΎ ΠΊΠ»Π°ΡΡΠ°.ΠΡΠΎ ΡΠ½ΠΈΠΆΠ΅Π½ΠΈΠ΅ Π²Π΅ΡΠ° ΠΏΠΎΠ·Π²ΠΎΠ»ΡΠ΅Ρ Π³ΡΡΠ·ΠΎΠ²ΠΈΠΊΠ°ΠΌ Ford Π΄Π²ΠΈΠ³Π°ΡΡΡΡ Π΄Π°Π»ΡΡΠ΅ Π½Π° Π³Π°Π»Π»ΠΎΠ½Π΅ Π±Π΅Π½Π·ΠΈΠ½Π° ΠΈ ΠΎΡΠΊΡΡΠ²Π°Π΅Ρ Π΄Π²Π΅ΡΠΈ Π΄Π»Ρ Π΄ΡΡΠ³ΠΈΡ ΠΈΠ·ΠΌΠ΅Π½Π΅Π½ΠΈΠΉ, ΡΠ°ΠΊΠΈΡ ΠΊΠ°ΠΊ Π±ΠΎΠ»Π΅Π΅ ΠΌΠ΅Π»ΠΊΠΈΠ΅ Π΄Π²ΠΈΠ³Π°ΡΠ΅Π»ΠΈ, ΠΊΠΎΡΠΎΡΡΠ΅ ΠΌΠΎΠ³ΡΡ Π΅ΡΠ΅ Π±ΠΎΠ»ΡΡΠ΅ ΠΏΠΎΠ²ΡΡΠΈΡΡ ΡΠΊΠΎΠ½ΠΎΠΌΠΈΡ ΡΠΎΠΏΠ»ΠΈΠ²Π°.
ΠΡΡΠΎΡΠΈΡ Π°Π»ΡΠΌΠΈΠ½ΠΈΡ Π² Π°Π²ΡΠΎΠΌΠΎΠ±ΠΈΠ»ΡΡ
Π‘Π΅Π³ΠΎΠ΄Π½Ρ ΡΠ°ΡΡΡΡΠΈΠΉ ΡΡΠ½ΠΎΠΊ, Π°Π»ΡΠΌΠΈΠ½ΠΈΠΉ Π±ΡΠ» ΠΊΠ»ΡΡΠ΅Π²ΡΠΌ ΠΌΠ°ΡΠ΅ΡΠΈΠ°Π»ΠΎΠΌ Π΄Π»Ρ Π°Π²ΡΠΎΠΏΡΠΎΠΈΠ·Π²ΠΎΠ΄ΠΈΡΠ΅Π»Π΅ΠΉ Ρ ΡΠ°ΠΌΠΎΠ³ΠΎ Π½Π°ΡΠ°Π»Π°. ΠΠ΅ΡΠ²ΡΠΉ ΡΠΏΠΎΡΡΠΈΠ²Π½ΡΠΉ Π°Π²ΡΠΎΠΌΠΎΠ±ΠΈΠ»Ρ Ρ Π°Π»ΡΠΌΠΈΠ½ΠΈΠ΅Π²ΡΠΌ ΠΊΡΠ·ΠΎΠ²ΠΎΠΌ Π±ΡΠ» ΠΏΡΠ΅Π΄ΡΡΠ°Π²Π»Π΅Π½ Π½Π° ΠΠ΅ΡΠ»ΠΈΠ½ΡΠΊΠΎΠΌ ΠΌΠ΅ΠΆΠ΄ΡΠ½Π°ΡΠΎΠ΄Π½ΠΎΠΌ Π°Π²ΡΠΎΡΠ°Π»ΠΎΠ½Π΅ Π² 1899 Π³ΠΎΠ΄Ρ. ΠΠ²Π° Π³ΠΎΠ΄Π° ΡΠΏΡΡΡΡ ΠΏΠ΅ΡΠ²ΡΠΉ Π΄Π²ΠΈΠ³Π°ΡΠ΅Π»Ρ Ρ Π°Π»ΡΠΌΠΈΠ½ΠΈΠ΅Π²ΡΠΌΠΈ Π΄Π΅ΡΠ°Π»ΡΠΌΠΈ Π±ΡΠ» ΡΠ°Π·ΡΠ°Π±ΠΎΡΠ°Π½ ΠΠ°ΡΠ»ΠΎΠΌ ΠΠ΅Π½ΡΠ΅ΠΌ.ΠΠΎΡΠ»Π΅ ΠΡΠΎΡΠΎΠΉ ΠΌΠΈΡΠΎΠ²ΠΎΠΉ Π²ΠΎΠΉΠ½Ρ Π°Π»ΡΠΌΠΈΠ½ΠΈΠΉ ΡΡΠ°Π» Π΄ΠΎΡΡΠ°ΡΠΎΡΠ½ΠΎ Π½Π΅Π΄ΠΎΡΠΎΠ³ΠΈΠΌ, ΡΡΠΎΠ±Ρ Π΅Π³ΠΎ ΠΌΠΎΠΆΠ½ΠΎ Π±ΡΠ»ΠΎ ΠΈΡΠΏΠΎΠ»ΡΠ·ΠΎΠ²Π°ΡΡ Π² ΡΠ΅ΡΠΈΠΉΠ½ΡΡ Π°Π²ΡΠΎΠΌΠΎΠ±ΠΈΠ»ΡΡ . ΠΡΠΎΡΡΠ² ΠΏΡΠΎΠΈΠ·ΠΎΡΠ΅Π» Π² 1961 Π³ΠΎΠ΄Ρ, ΠΊΠΎΠ³Π΄Π° Π±ΡΠΈΡΠ°Π½ΡΠΊΠ°Ρ ΠΊΠΎΠΌΠΏΠ°Π½ΠΈΡ Land Rover Π²ΡΠΏΡΡΡΠΈΠ»Π° Π±Π»ΠΎΠΊΠΈ V-8 Ρ Π°Π»ΡΠΌΠΈΠ½ΠΈΠ΅Π²ΡΠΌΠΈ ΡΠΈΠ»ΠΈΠ½Π΄ΡΠ°ΠΌΠΈ. ΠΡΡΡΠ΄Π° Π°Π»ΡΠΌΠΈΠ½ΠΈΠ΅Π²ΡΠ΅ Π°Π²ΡΠΎΠΌΠΎΠ±ΠΈΠ»ΡΠ½ΡΠ΅ Π΄Π΅ΡΠ°Π»ΠΈ Π·Π°ΠΊΡΠ΅ΠΏΠΈΠ»ΠΈΡΡ Π² ΠΊΠΎΠ»Π΅ΡΠ°Ρ ΠΈ ΠΊΠΎΠΆΡΡ Π°Ρ ΡΡΠ°Π½ΡΠΌΠΈΡΡΠΈΠΈ, Π° Π·Π°ΡΠ΅ΠΌ ΠΏΠ΅ΡΠ΅ΠΌΠ΅ΡΡΠΈΠ»ΠΈΡΡ Π² Π³ΠΎΠ»ΠΎΠ²ΠΊΠΈ ΡΠΈΠ»ΠΈΠ½Π΄ΡΠΎΠ² ΠΈ ΡΠ°ΡΠ½ΠΈΡΡ ΠΏΠΎΠ΄Π²Π΅ΡΠΊΠΈ. ΠΡΠΎΡ ΠΌΠ΅ΡΠ°Π»Π», ΠΏΡΠΈΠ³ΠΎΠ΄Π½ΡΠΉ Π΄Π»Ρ Π±Π΅ΡΠΊΠΎΠ½Π΅ΡΠ½ΠΎΠΉ ΠΏΠ΅ΡΠ΅ΡΠ°Π±ΠΎΡΠΊΠΈ, Π² Π½Π°ΡΡΠΎΡΡΠ΅Π΅ Π²ΡΠ΅ΠΌΡ ΡΠ²Π»ΡΠ΅ΡΡΡ Π²Π΅Π΄ΡΡΠΈΠΌ ΠΌΠ°ΡΠ΅ΡΠΈΠ°Π»ΠΎΠΌ Π΄Π»Ρ ΠΏΡΠΈΠΌΠ΅Π½Π΅Π½ΠΈΡ Π² ΡΡΠ°Π½ΡΠΌΠΈΡΡΠΈΠΈ ΠΈ ΠΊΠΎΠ»Π΅ΡΠ°Ρ ΠΈ ΠΏΡΠΎΠ΄ΠΎΠ»ΠΆΠ°Π΅Ρ Π·Π°Π²ΠΎΠ΅Π²ΡΠ²Π°ΡΡ ΡΡΠ½ΠΎΡΠ½ΡΡ Π΄ΠΎΠ»Ρ Π² ΠΊΠ°ΠΏΠΎΡΠ°Ρ , Π±Π°Π³Π°ΠΆΠ½ΠΈΠΊΠ°Ρ , Π΄Π²Π΅ΡΡΡ ΠΈ Π±Π°ΠΌΠΏΠ΅ΡΠ°Ρ , Π° ΡΠ°ΠΊΠΆΠ΅ Π² ΠΊΠΎΠΌΠΏΠ»Π΅ΠΊΡΠ°ΡΠΈΡΡ Π°Π²ΡΠΎΠΌΠΎΠ±ΠΈΠ»Π΅ΠΉ.
ΠΠ½ΡΠ΅ΡΠ΅ΡΠ½ΡΠΉ ΡΠ°ΠΊΡ: ΡΠ΅ΡΠΊΠΈΠΉ Π²ΡΠ±ΠΎΡ Π°Π²ΡΠΎΠΏΡΠΎΠΈΠ·Π²ΠΎΠ΄ΠΈΡΠ΅Π»Π΅ΠΉ
Π 2013 Π³ΠΎΠ΄Ρ ΠΏΡΠ΅Π·ΠΈΠ΄Π΅Π½Ρ ΠΈ Π³Π΅Π½Π΅ΡΠ°Π»ΡΠ½ΡΠΉ Π΄ΠΈΡΠ΅ΠΊΡΠΎΡ Ford ΠΠ»Π°Π½ ΠΡΠ»Π°Π»Π»ΠΈ Π²ΡΡΠΎΠΊΠΎ ΠΎΡΠ΅Π½ΠΈΠ» Π°Π²ΡΠΎΠΌΠΎΠ±ΠΈΠ»ΡΠ½ΡΠΉ Π°Π»ΡΠΌΠΈΠ½ΠΈΠΉ Π² ΡΡΠ΄Π΅ ΠΈΠ½ΡΠ΅ΡΠ²ΡΡ Π΄Π»Ρ Π‘ΠΠ, ΠΏΠΎΡΠ²ΡΡΠ΅Π½Π½ΡΡ Π°Π½ΠΎΠ½ΡΡ Π½ΠΎΠ²ΠΎΠ³ΠΎ Π³ΡΡΠ·ΠΎΠ²ΠΈΠΊΠ° F-150. Π‘ΡΠ΅Π΄ΠΈ Π΄ΡΡΠ³ΠΈΡ ΠΊΠΎΠΌΠΌΠ΅Π½ΡΠ°ΡΠΈΠ΅Π², ΡΠΊΠ°Π·Π°Π» ΠΡΠ»Π°Π»Π»ΠΈ, Β«ΡΡΠ½Ρ Π·Π° ΡΡΠ½Ρ, Π°Π»ΡΠΌΠΈΠ½ΠΈΠΉ ΠΏΡΠΎΡΠ½Π΅Π΅ ΠΈ ΠΏΡΠΎΡΠ½Π΅Π΅ ΡΡΠ°Π»ΠΈΒ» ΠΈ Β«[Π°Π»ΡΠΌΠΈΠ½ΠΈΠΉ] Π±ΡΠ΄Π΅Ρ ΠΏΡΠ΅Π΄ΠΏΠΎΡΡΠΈΡΠ΅Π»ΡΠ½ΡΠΌ ΠΌΠ°ΡΠ΅ΡΠΈΠ°Π»ΠΎΠΌΒ» Π΄Π»Ρ ΠΏΡΠΎΠ΄Π²ΠΈΠΆΠ΅Π½ΠΈΡ Ford Π²ΠΏΠ΅ΡΠ΅Π΄.
ΠΠ»Ρ ΠΏΠΎΠ»ΡΡΠ΅Π½ΠΈΡ Π΄ΠΎΠΏΠΎΠ»Π½ΠΈΡΠ΅Π»ΡΠ½ΠΎΠΉ ΠΈΠ½ΡΠΎΡΠΌΠ°ΡΠΈΠΈ ΠΎΠ± ΠΈΡΠΏΠΎΠ»ΡΠ·ΠΎΠ²Π°Π½ΠΈΠΈ Π°Π»ΡΠΌΠΈΠ½ΠΈΡ Π² Π°Π²ΡΠΎΠΌΠΎΠ±ΠΈΠ»ΡΠ½ΠΎΠΉ ΠΏΡΠΎΠΌΡΡΠ»Π΅Π½Π½ΠΎΡΡΠΈ: www.drivealuminum.org.
,Π’ΠΈΠΏ Π±ΠΈΠ·Π½Π΅ΡΠ°: | ΠΡΠΎΠΈΠ·Π²ΠΎΠ΄ΠΈΡΠ΅Π»Ρ / Factory |
ΠΡΠ½ΠΎΠ²Π½Π°Ρ ΠΏΡΠΎΠ΄ΡΠΊΡΠΈΡ: | ΠΠ΅Π½Π·ΠΈΠ½ΠΎΠ²ΡΠΉ Π³Π΅Π½Π΅ΡΠ°ΡΠΎΡ, ΠΠ΅Π½Π·ΠΈΠ½ΠΎΠ²ΡΠΉ Π΄Π²ΠΈΠ³Π°ΡΠ΅Π»Ρ , ΠΠ΅Π½Π·ΠΈΠ½ΠΎΠ²ΡΠΉ Π²ΠΎΠ΄ΡΠ½ΠΎΠΉ Π½Π°ΡΠΎΡ, ΠΠΎΠ΄ΡΠ½ΠΎΠΉ Π½Π°ΡΠΎΡ, ΠΠΈΠ·Π΅Π»ΡΠ½ΡΠΉ Π³Π΅Π½Π΅ΡΠ°ΡΠΎΡ |
Mgmt.Π‘Π΅ΡΡΠΈΡΠΈΠΊΠ°ΡΠΈΡ: | ISO9001: 2015 |
Π²Π»Π°Π΄Π΅Π½ΠΈΠ΅ ΡΠ°Π±ΡΠΈΠΊΠΎΠΉ: | ΠΠ±ΡΠ΅ΡΡΠ²ΠΎ Ρ ΠΎΠ³ΡΠ°Π½ΠΈΡΠ΅Π½Π½ΠΎΠΉ ΠΎΡΠ²Π΅ΡΡΡΠ²Π΅Π½Π½ΠΎΡΡΡΡ |
R & D ΠΠΌΠΊΠΎΡΡΡ: | Π‘ΠΎΠ±ΡΡΠ²Π΅Π½Π½Π°Ρ ΠΌΠ°ΡΠΊΠ°, ODM, OEM |
Π Π°ΡΠΏΠΎΠ»ΠΎΠΆΠ΅Π½ΠΈΠ΅: | Π€ΡΡΠΆΠΎΡ, Π€ΡΡΠ·ΡΠ½Ρ |
Π’ΠΈΠΏ Π±ΠΈΠ·Π½Π΅ΡΠ°: | ΠΡΠΎΠΈΠ·Π²ΠΎΠ΄ΠΈΡΠ΅Π»Ρ / Factory |
ΠΡΠ½ΠΎΠ²Π½Π°Ρ ΠΏΡΠΎΠ΄ΡΠΊΡΠΈΡ: | Π¨ΡΠ°ΠΌΠΏΠΎΠ²Π°Π½Π½ΡΠ΅ Π΄Π΅ΡΠ°Π»ΠΈ, Π·ΡΠ±ΡΠ°ΡΡΠ΅ ΠΊΠΎΠ»Π΅ΡΠ°, ΠΏΡΠΎΡΠΎΡΠΈΠΏΡ, ΠΎΠ±ΡΠ°Π±Π°ΡΡΠ²Π°ΡΡΠΈΠ΅ Π΄Π΅ΡΠ°Π»ΠΈ Ρ Π§ΠΠ£, ΡΡΠ΅Π·Π΅ΡΠ½ΡΠ΅ Π΄Π΅ΡΠ°Π»ΠΈ Ρ Π§ΠΠ£ |
Mgmt.Π‘Π΅ΡΡΠΈΡΠΈΠΊΠ°ΡΠΈΡ: | ISO 9001, ISO 9000, IATF16949, ISO 13485 |
Π²Π»Π°Π΄Π΅Π½ΠΈΠ΅ ΡΠ°Π±ΡΠΈΠΊΠΎΠΉ: | ΠΠ±ΡΠ΅ΡΡΠ²ΠΎ Ρ ΠΎΠ³ΡΠ°Π½ΠΈΡΠ΅Π½Π½ΠΎΠΉ ΠΎΡΠ²Π΅ΡΡΡΠ²Π΅Π½Π½ΠΎΡΡΡΡ |
R & D ΠΠΌΠΊΠΎΡΡΡ: | OEM, ODM |
Π Π°ΡΠΏΠΎΠ»ΠΎΠΆΠ΅Π½ΠΈΠ΅: | ΠΡΠ½Π³ΡΠ°Π½Ρ, ΠΡΠ°Π½Π΄ΡΠ½ |
Π’ΠΈΠΏ Π±ΠΈΠ·Π½Π΅ΡΠ°: | ΠΡΠΎΠΈΠ·Π²ΠΎΠ΄ΠΈΡΠ΅Π»Ρ / Factory ΠΠΎΡΠΏΠΎΡΠ°ΡΠΈΡ ΠΡΡΠΏΠΏ |
ΠΡΠ½ΠΎΠ²Π½Π°Ρ ΠΏΡΠΎΠ΄ΡΠΊΡΠΈΡ: | ΠΠΈΡΡΠ΅, Π»ΠΈΡΡΠ΅ Π² ΠΏΠ΅ΡΡΠ°Π½ΡΠ΅ ΡΠΎΡΠΌΡ, ΡΠΎΡΠ½ΠΎΠ΅ Π»ΠΈΡΡΠ΅, ΡΡΠ°Π»ΡΠ½ΠΎΠ΅ Π»ΠΈΡΡΠ΅, ΡΡΠ³ΡΠ½Π½ΠΎΠ΅ Π»ΠΈΡΡΠ΅ |
Mgmt.Π‘Π΅ΡΡΠΈΡΠΈΠΊΠ°ΡΠΈΡ: | ISO 9001, IATF16949 |
Π²Π»Π°Π΄Π΅Π½ΠΈΠ΅ ΡΠ°Π±ΡΠΈΠΊΠΎΠΉ: | ΠΠ±ΡΠ΅ΡΡΠ²ΠΎ Ρ ΠΎΠ³ΡΠ°Π½ΠΈΡΠ΅Π½Π½ΠΎΠΉ ΠΎΡΠ²Π΅ΡΡΡΠ²Π΅Π½Π½ΠΎΡΡΡΡ |
R & D ΠΠΌΠΊΠΎΡΡΡ: | OEM, ODM |
Π Π°ΡΠΏΠΎΠ»ΠΎΠΆΠ΅Π½ΠΈΠ΅: | Π¦ΠΈΠ½Π΄Π°ΠΎ, Π¨Π°Π½ΡΠ΄ΡΠ½ |
Π’ΠΈΠΏ Π±ΠΈΠ·Π½Π΅ΡΠ°: | ΠΡΠΎΠΈΠ·Π²ΠΎΠ΄ΠΈΡΠ΅Π»Ρ / Factory , Π’ΠΎΡΠ³ΠΎΠ²Π°Ρ ΠΊΠΎΠΌΠΏΠ°Π½ΠΈΡ |
ΠΡΠ½ΠΎΠ²Π½Π°Ρ ΠΏΡΠΎΠ΄ΡΠΊΡΠΈΡ: | ΠΠ΅ΡΠ°Π»ΠΈ Ρ Π§ΠΠ£, ΠΠ±ΡΠ°Π±Π°ΡΡΠ²Π°ΡΡΠΈΠ΅ Π΄Π΅ΡΠ°Π»ΠΈ, ΠΠ±ΡΠ°Π±Π°ΡΡΠ²Π°Π΅ΠΌΡΠ΅ Π΄Π΅ΡΠ°Π»ΠΈ, Π’ΠΎΠΊΠ°ΡΠ½ΡΠ΅ Π΄Π΅ΡΠ°Π»ΠΈ, Π€ΡΠ΅Π·Π΅ΡΠ½ΡΠ΅ Π΄Π΅ΡΠ°Π»ΠΈ |
Mgmt.Π‘Π΅ΡΡΠΈΡΠΈΠΊΠ°ΡΠΈΡ: | ISO 9001 |
Π²Π»Π°Π΄Π΅Π½ΠΈΠ΅ ΡΠ°Π±ΡΠΈΠΊΠΎΠΉ: | Π§Π°ΡΡΠ½ΡΠΉ Π²Π»Π°Π΄Π΅Π»Π΅Ρ |
R & D ΠΠΌΠΊΠΎΡΡΡ: | OEM |
Π Π°ΡΠΏΠΎΠ»ΠΎΠΆΠ΅Π½ΠΈΠ΅: | Π£ΡΠΈ, Π¦Π·ΡΠ½ΡΡ |
Π’ΠΈΠΏ Π±ΠΈΠ·Π½Π΅ΡΠ°: | ΠΡΠΎΠΈΠ·Π²ΠΎΠ΄ΠΈΡΠ΅Π»Ρ / Factory |
ΠΡΠ½ΠΎΠ²Π½Π°Ρ ΠΏΡΠΎΠ΄ΡΠΊΡΠΈΡ: | ΠΠΈΡΡΠ΅ ΠΏΠΎΠ΄ Π΄Π°Π²Π»Π΅Π½ΠΈΠ΅ΠΌ ΠΈΠ· ΠΏΡΠ΅ΡΠΈΠ·ΠΈΠΎΠ½Π½ΡΡ ΠΌΠ΅ΡΠ°Π»Π»ΠΎΠ², Π»ΠΈΡΡΠ΅ ΠΈΠ· Π°Π»ΡΠΌΠΈΠ½ΠΈΠ΅Π²ΠΎΠ³ΠΎ ΡΠΏΠ»Π°Π²Π°, Π»ΠΈΡΡΠ΅ ΠΈΠ· ΡΠΈΠ½ΠΊΠΎΠ²ΠΎΠ³ΠΎ ΡΠΏΠ»Π°Π²Π°, Π΄Π΅ΡΠ°Π»ΠΈ Π΄Π»Ρ Π°Π²ΡΠΎΠΌΠΎΠ±ΠΈΠ»Π΅ΠΉ ΠΈ Π΄Π²ΠΈΠ³Π°ΡΠ΅Π»Π΅ΠΉ, Π΄Π΅ΡΠ°Π»ΠΈ Π΄Π»Ρ ΡΠ²Π΅ΡΠΎΠ΄ΠΈΠΎΠ΄Π½ΠΎΠ³ΠΎ ΠΎΡΠ²Π΅ΡΠ΅Π½ΠΈΡ |
Mgmt.Π‘Π΅ΡΡΠΈΡΠΈΠΊΠ°ΡΠΈΡ: | ISO 9001, IATF16949 |
Π²Π»Π°Π΄Π΅Π½ΠΈΠ΅ ΡΠ°Π±ΡΠΈΠΊΠΎΠΉ: | ΠΠ±ΡΠ΅ΡΡΠ²ΠΎ Ρ ΠΎΠ³ΡΠ°Π½ΠΈΡΠ΅Π½Π½ΠΎΠΉ ΠΎΡΠ²Π΅ΡΡΡΠ²Π΅Π½Π½ΠΎΡΡΡΡ |
R & D ΠΠΌΠΊΠΎΡΡΡ: | OEM, ODM |
Π Π°ΡΠΏΠΎΠ»ΠΎΠΆΠ΅Π½ΠΈΠ΅: | ΠΡΠ½Π³ΡΠ°Π½Ρ, ΠΡΠ°Π½Π΄ΡΠ½ |